Turnare prin injecție termoplastică
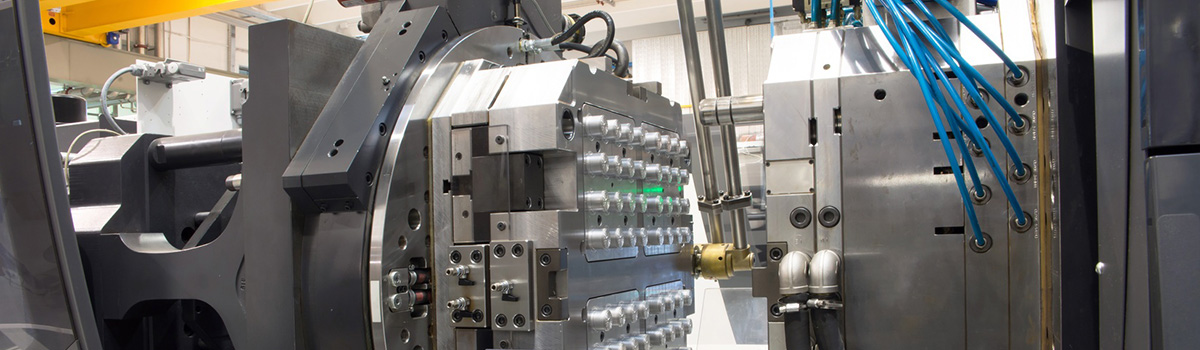
Turnarea prin injecție a termoplasticului este un proces de fabricație popular utilizat pentru a crea diverse piese din plastic pentru mai multe industrii. Acest proces presupune topirea peletelor de plastic și injectarea lor într-o matriță pentru a produce o formă tridimensională. Turnarea prin injecție termoplastică este foarte eficientă și rentabilă pentru producerea unor volume mari de piese din plastic de înaltă calitate, cu toleranțe strânse. Acest ghid cuprinzător va explora diferitele aspecte ale turnării prin injecție a materialelor termoplastice, inclusiv avantajele și dezavantajele acesteia, tipurile de termoplastice utilizate, procesul de turnare prin injecție, considerente de proiectare și multe altele.
Istoria turnării prin injecție a materialelor termoplastice
Istoria turnării prin injecție a materialelor termoplastice se întinde pe peste un secol de progrese tehnologice, dezvoltări materiale și aplicații industriale. De la începuturile sale umile ca proces de turnare a celuloidului până la tehnologia sofisticată actuală, turnarea prin injecție continuă să fie o tehnică de producție vitală, stimulând inovația și modelând diverse industrii.
- Evoluții timpurii:John Wesley Hyatt și fratele său Isaiah au dezvoltat prima mașină practică de turnat prin injecție, urmărind originile turnării prin injecție termoplastic până la sfârșitul secolului al XIX-lea. În 19, au brevetat un dispozitiv care folosea un piston pentru a injecta celuloid într-o cavitate a matriței, creând obiecte solide. Această descoperire a pus bazele procesului modern de turnare prin injecție.
- Progrese în materiale:La începutul secolului al XX-lea, introducerea de noi polimeri sintetici a deschis noi posibilități pentru turnarea prin injecție. Bakelitul, o rășină fenolică, a devenit un material popular pentru turnare datorită proprietăților sale excelente de izolare electrică. De-a lungul anilor 20 și 1930, progresele în chimia polimerilor au condus la dezvoltarea altor materiale termoplastice, cum ar fi polistirenul și polietilena, care au extins și mai mult gama de materiale potrivite pentru turnarea prin injecție.
- Adopție industrială: Adoptarea pe scară largă a turnării prin injecție termoplastic a început în anii 1950, deoarece producătorii i-au recunoscut rentabilitatea și versatilitatea. Introducerea mașinilor de înaltă presiune a permis cicluri mai rapide și volume de producție crescute. Ca urmare, a apărut o selecție diversă de produse atât pentru uz personal, cât și pentru uz industrial. Acestea au inclus componente pentru mașini, electrocasnice și jucării.
- Inovații tehnologice:De-a lungul deceniilor, tehnologia de turnare prin injecție a continuat să evolueze. În anii 1960, au apărut mașini controlate de computer, permițând controlul precis asupra procesului de turnare. Introducerea sistemelor cu canale calde în anii 1980 a redus deșeurile și a îmbunătățit eficiența prin eliminarea nevoii de canale și canale. În ultimii ani, progresele în automatizare, robotică și imprimare 3D au revoluționat și mai mult industria de turnare prin injecție, permițând proiecte complexe și reducând timpul de producție.
- Sustenabilitate și reciclare:Cu preocupările tot mai mari de mediu, industria de turnare prin injecție a adoptat măsuri de durabilitate. Producătorii au dezvoltat materiale termoplastice bio și reciclate, reducând dependența de materialele pe bază de combustibili fosili. În plus, tehnologiile îmbunătățite de reciclare au permis reprocesarea deșeurilor post-consum și post-industriale, reducând la minimum impactul asupra mediului al turnării prin injecție termoplastic.
- Perspective de viitor:Viitorul turnării prin injecție a materialelor termoplastice pare promițător. Industria explorează inovații, cum ar fi turnarea prin micro-injecție pentru componente miniaturale, tehnici multi-materiale și supramulare pentru piese complexe și integrează tehnologii inteligente pentru monitorizarea și optimizarea proceselor. În plus, cercetătorii se așteaptă ca progresele în materialele biodegradabile și fabricarea aditive să revoluționeze domeniul, făcând turnarea prin injecție și mai durabilă și mai versatilă.
Avantajele turnării prin injecție termoplastice
Turnarea prin injecție din termoplastic oferă numeroase avantaje pentru producători. Oferă flexibilitate de proiectare, permițând modele complexe și complicate cu diverse caracteristici. Procesul este eficient din punct de vedere al costurilor, reducând risipa de materiale și scăzând costurile unitare. Turnarea prin injecție din termoplastic acceptă mai multe materiale, oferind versatilitate pentru diferite aplicații.
- Flexibilitate de proiectare:Turnarea prin injecție din termoplastic permite modele complicate și complexe, cu caracteristici cum ar fi tăieturi, pereți subțiri și grosimi diferite, oferind designerilor o libertate imensă.
- Eficiența costurilor: Procesul este foarte eficient, reducând risipa de materiale și scăzând costurile unitare. Turnarea simultană a mai multor piese și ciclurile rapide de producție contribuie la economii de costuri.
- Versatilitatea materialului: Turnarea prin injecție termoplastică acceptă o gamă largă de materiale, permițând producătorilor să aleagă cea mai potrivită opțiune pentru fiecare aplicație, inclusiv materiale rigide sau flexibile, transparente sau opace și rezistente chimic.
- Rezistență și durabilitate:Materialele termoplastice turnate prin injecție pot prezenta proprietăți mecanice excelente, cum ar fi rezistență ridicată, tenacitate și rezistență la impact. Opțiunile de întărire, cum ar fi fibrele de sticlă sau de carbon, îmbunătățesc și mai mult aceste proprietăți.
- Consecvență și calitate:Turnarea prin injecție asigură calitate constantă de la piesă la piesă și precizie dimensională, oferind toleranțe strânse și produse fiabile. Procesul oferă, de asemenea, un finisaj neted și uniform al suprafeței, eliminând necesitatea unor operațiuni suplimentare de finisare.
- Scalabilitate și producție în masă:Turnarea prin injecție este scalabilă de la volume mici la cele mari, ceea ce o face potrivită pentru producția de masă. Odată ce producătorii creează matrița, ei pot produce cantități mari de piese identice cu variații minime.
- Integrare și asamblare:Piesele turnate prin injecție pot încorpora mai multe componente într-o singură piesă, reducând nevoia de procese suplimentare de asamblare. Această integrare îmbunătățește performanța produsului, reduce timpul de asamblare și scade costurile.
- Durabilitate:Industria de turnare prin injecție arată un accent tot mai mare pe durabilitate. Disponibilitatea materialelor bio și reciclate permite producerea de produse ecologice. Utilizarea eficientă a materialelor și reciclabilitatea materialelor termoplastice contribuie la un proces de producție mai ecologic.
Aceste beneficii au făcut din aceasta o metodă de producție adoptată pe scară largă în diverse industrii, oferind soluții de înaltă calitate, rentabile și ecologice pentru cerințele complexe ale produselor.
Dezavantajele turnării prin injecție termoplastice
În timp ce turnarea prin injecție termoplastică oferă numeroase avantaje, există și câteva dezavantaje. Producătorii trebuie să evalueze cu atenție acești factori și să îi cântărească în raport cu beneficiile pentru a determina adecvarea turnării prin injecție a materialelor termoplastice pentru aplicațiile lor specifice.
- Investiție inițială ridicată: Înființarea unei operațiuni de turnare prin injecție a materialelor termoplastice necesită o investiție inițială semnificativă în proiectarea și fabricarea matrițelor și achiziționarea de mașini specializate. Costurile asociate cu crearea matrițelor și sculelor pot fi substanțiale, în special pentru proiectele complexe și complicate.
- Limitări de proiectare: În timp ce turnarea prin injecție termoplastică oferă flexibilitate de proiectare, există anumite limitări. De exemplu, obținerea unei grosimi uniforme a peretelui în întreaga piesă poate fi o provocare, ceea ce duce la variații în distribuția materialului și potențiale slăbiciuni structurale. În plus, prezența decadărilor sau a geometriilor complexe poate necesita utilizarea unor caracteristici suplimentare de matriță sau operațiuni secundare, crescând costurile și timpul de producție.
- Perioade lungi de plumb:Procesul de proiectare și fabricare a matrițelor pentru turnarea prin injecție poate consuma mult timp, ceea ce duce la timpi de livrare mai lungi pentru dezvoltarea produsului. Procesul de iterare a designului, producția de matrițe și testarea pot adăuga timp semnificativ cronologiei generale de producție, care ar putea să nu fie potrivite pentru proiecte cu termene limită strânse.
- Constrângeri de selecție a materialelor:Deși turnarea prin injecție termoplastică acceptă o gamă largă de materiale, există anumite limitări și constrângeri. Unele materiale pot avea cerințe specifice de procesare sau disponibilitate limitată, ceea ce afectează alegerile de proiectare și selecția materialelor pentru o anumită aplicație.
- Limitări privind dimensiunea piesei:Mașinile de turnat prin injecție au limitări de dimensiune, atât în ceea ce privește dimensiunea fizică a dispozitivului, cât și dimensiunea matrițelor pe care le pot găzdui. Producerea de piese uriașe poate necesita echipamente specializate sau metode alternative de fabricație.
- Impact asupra mediului:În timp ce industria lucrează pentru durabilitate, procesul de turnare prin injecție a materialelor termoplastice încă generează deșeuri, inclusiv resturi și spruces. Eliminarea și reciclarea corespunzătoare a acestor materiale sunt necesare pentru a minimiza impactul asupra mediului.
- Complexitatea optimizării proceselor:Atingerea parametrilor optimi de proces pentru turnarea prin injecție a materialelor termoplastice poate fi complexă și consumatoare de timp. Producătorii trebuie să controleze și să optimizeze cu atenție temperatura, presiunea, ratele de răcire și timpii de ciclu pentru a asigura o calitate constantă a pieselor și pentru a minimiza defectele.
Tipuri de termoplastice utilizate în turnarea prin injecție
Acestea sunt doar câteva exemple de termoplastice utilizate în mod obișnuit în turnarea prin injecție. Fiecare material are proprietăți unice, făcându-l potrivit pentru aplicații specifice bazate pe rezistență, flexibilitate, rezistență chimică, transparență și cost. Producătorii ar trebui să ia în considerare aceste proprietăți și cerințe atunci când selectează materialul termoplastic adecvat pentru proiectele lor de turnare prin injecție.
- Polipropilenă (PP):Polipropilena este un termoplastic versatil utilizat în mod obișnuit în turnarea prin injecție. Oferă rezistență chimică excelentă, densitate scăzută și rezistență bună la impact. PP (polipropilena) are o gamă largă de aplicații în ambalaje, componente auto, aparate de uz casnic și dispozitive medicale.
- Polietilenă (PE):Polietilena este un alt termoplastic utilizat pe scară largă în turnarea prin injecție. Este disponibil în diferite forme, cum ar fi polietilena de înaltă densitate (HDPE) și polietilena de joasă densitate (LDPE). PE oferă rezistență chimică bună, duritate și flexibilitate, făcându-l potrivit pentru sticle, recipiente și țevi.
- Polistiren (PS):Polistirenul este un termoplastic versatil cunoscut pentru claritatea, rigiditatea și accesibilitatea sa. Găsește o utilizare comună în ambalaje, bunuri de larg consum și produse de unică folosință. PS (polistirenul) permite o prelucrare rapidă și oferă o bună stabilitate dimensională, dar poate fi fragil și susceptibil la fisurarea prin stres ambiental.
- Acrilonitril Butadien Stiren (ABS): ABS este un termoplastic popular cunoscut pentru rezistența excelentă la impact și durabilitate. Combină proprietățile acrilonitrilului, butadienei și stirenului pentru a crea un material versatil potrivit pentru piese auto, carcase electronice și jucării.
- Clorura de polivinil (PVC): PVC-ul este un termoplastic utilizat pe scară largă, cunoscut pentru rezistența chimică excelentă, durabilitatea și costul scăzut. Poate fi rigid sau flexibil in functie de formula si aditivii folositi. PVC (clorura de polivinil) este utilizat în mod obișnuit în construcții, izolație electrică, produse de îngrijire a sănătății și ambalaje.
- Policarbonat (PC): Policarbonatul este un termoplastic transparent cu impact extraordinar și rezistență ridicată la căldură. Găsește o utilizare obișnuită în aplicațiile care necesită claritate optică, cum ar fi componentele auto, căștile de protecție și afișajele electronice.
- Nailon (poliamida):Nailonul este un termoplastic puternic și durabil, cunoscut pentru proprietățile sale mecanice excelente și rezistența chimică. Găsește o utilizare obișnuită în aplicații care necesită rezistență ridicată, cum ar fi piese auto, componente industriale și bunuri de larg consum.
- Tereftalat de polietilenă (PET):PET-ul este un termoplastic popular pentru producerea de sticle, recipiente și materiale de ambalare. Oferă o claritate bună, rezistență chimică și proprietăți de barieră, făcându-l potrivit pentru aplicații alimentare și băuturi.
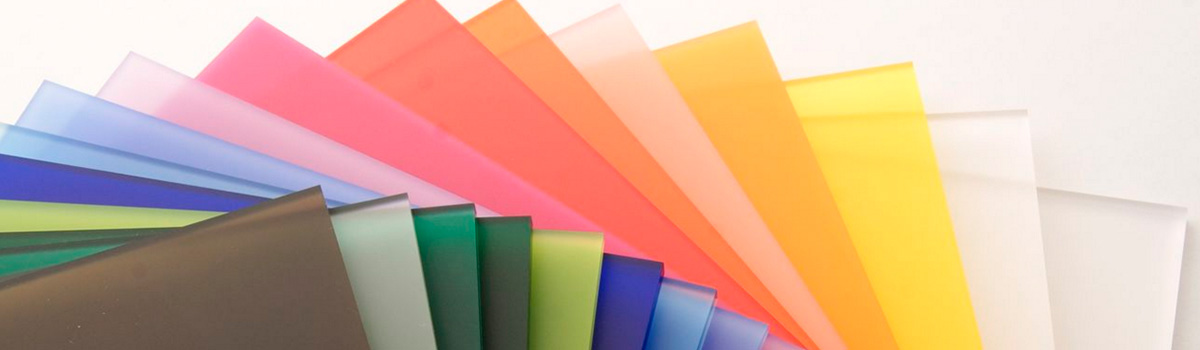
Proprietățile materialelor termoplastice utilizate în turnarea prin injecție
Aceste proprietăți ale materialelor termoplastice joacă un rol crucial în determinarea adecvării lor pentru aplicații specifice de turnare prin injecție. Producătorii trebuie să ia în considerare cu atenție aceste proprietăți și să aleagă termoplasticul potrivit în funcție de performanța dorită, condițiile de mediu și cerințele de cost.
- Proprietăți mecanice:Materialele termoplastice utilizate în turnarea prin injecție pot prezenta diverse proprietăți mecanice, inclusiv rezistența la tracțiune, rezistența la impact și rezistența la încovoiere. Aceste proprietăți determină capacitatea materialului de a rezista forțelor aplicate și durabilitatea sa globală în diferite aplicații.
- Rezistență chimică:Multe materiale termoplastice utilizate în turnarea prin injecție au o rezistență remarcabilă la substanțe chimice, solvenți și uleiuri. Această proprietate este crucială pentru aplicațiile care implică expunerea la medii dure sau substanțe corozive.
- Stabilitate termică:Stabilitatea termică a materialelor termoplastice se referă la capacitatea lor de a rezista la temperaturi ridicate fără degradare semnificativă. Unele materiale termoplastice prezintă o rezistență excelentă la căldură, permițându-le să-și mențină proprietățile mecanice chiar și la temperaturi ridicate.
- Proprietăți electrice:Materialele termoplastice utilizate în turnarea prin injecție pot avea proprietăți electrice specifice, inclusiv izolație electrică, conductivitate sau rigiditate dielectrică. Aceste proprietăți sunt esențiale pentru aplicațiile din industriile electrice și electronice, unde materialele trebuie să ofere performanțe electrice fiabile.
- Transparență și claritate:Anumite materiale termoplastice, cum ar fi policarbonatul și PET, oferă o transparență și claritate excelente, făcându-le potrivite pentru aplicații care necesită proprietăți optice. Producătorii folosesc de obicei aceste materiale în produse precum ferestre transparente, lentile și afișaje.
- Flexibilitate și rezistență: Flexibilitatea și duritatea sunt proprietăți esențiale ale termoplasticelor utilizate în aplicații care necesită rezistență la impact și durabilitate. Unele materiale termoplastice, cum ar fi ABS și nailon, oferă o rezistență excelentă, permițându-le să reziste la impacturi repetate fără a se rupe.
- Stabilitate dimensională:Stabilitatea dimensională se referă la capacitatea unui termoplastic de a-și menține forma și dimensiunea în condiții variate, inclusiv schimbări de temperatură. Materialele cu o bună stabilitate dimensională asigură dimensiuni constante ale pieselor, minimizând riscul deformarii sau deformarii.
- Compatibilitate chimică:Compatibilitatea chimică a materialelor termoplastice se referă la capacitatea lor de a rezista la degradare sau interacțiune cu diferite substanțe chimice, inclusiv acizi, baze și solvenți. Pentru a asigura o performanță optimă, este esențială selectarea unui termoplastic care poate rezista mediului chimic specific pe care îl va întâlni în aplicația prevăzută.
- Densitate: Materialele termoplastice au grosimi diferite, ceea ce le poate afecta greutatea și proprietățile generale ale pieselor. Materialele cu densitate scăzută, cum ar fi polietilena, oferă soluții ușoare, în timp ce materialele cu densitate mare, cum ar fi polipropilena, oferă un plus de rezistență și rigiditate.
Proces de turnare prin injecție: pas cu pas
Procesul de turnare prin injecție urmează acești pași, permițând producția eficientă și precisă a pieselor termoplastice de înaltă calitate. Fiecare pas necesită un control și o monitorizare atentă pentru a asigura dimensiuni constante ale pieselor, proprietățile materialului și calitatea generală.
- Proiectare și fabricare matrițe: Primul pas în procesul de turnare prin injecție este proiectarea și fabricarea matriței. Producătorii trebuie să creeze un design precis și detaliat al matriței pentru a atinge specificațiile dorite ale piesei. Producătorii fabrică apoi matrița folosind diverse tehnici, cum ar fi CNC sau prelucrarea cu descărcare electrică (EDM).
- Pregatirea materialului: Următorul pas este pregătirea odată ce matrița este gata. Granulele sau granulele termoplastice sunt selectate în funcție de proprietățile dorite ale materialului și topite într-un buncăr. Operatorii introduc apoi materialul în cilindrul mașinii de turnat prin injecție, unde se topește și omogenizează.
- Injecţie:În timpul fazei de injecție, operatorii injectează termoplasticul topit în cavitatea matriței la presiune ridicată. Unitatea de injecție a mașinii împinge materialul topit printr-o duză și în matriță. Materialul umple cavitatea matriței, luând forma piesei dorite.
- Răcire și solidificare:După umplerea matriței, operatorii permit plasticului topit să se răcească și să se solidifice. Răcirea este esențială pentru obținerea stabilității dimensionale și formarea corectă a pieselor. Operatorii pot controla procesul de răcire prin circularea lichidului de răcire prin canalele din interiorul matriței sau folosind plăci de răcire.
- Deschiderea și evacuarea matriței:Operatorii deschid matrița și ejectează piesa din cavitatea matriței odată ce plasticul se solidifică. Sistemul de evacuare din interiorul mașinii folosește știfturi, plăci de ejectare sau explozii de aer pentru a îndepărta regiunea din matriță. Matrița este apoi gata pentru următorul ciclu de injecție.
- Post procesare: După evacuare, piesa poate suferi operații de post-procesare, cum ar fi tăierea, debavurarea sau finisarea suprafeței. Acești pași ajută la îndepărtarea excesului de material, la netezirea marginilor aspre și la îmbunătățirea aspectului final al piesei.
- Inspectia calitatii: Pasul final implică inspectarea calității pieselor injectate și asigurarea că acestea îndeplinesc cerințele specificate. Diferite tehnici de control al calității, inclusiv măsurarea dimensională, inspecția vizuală și testarea funcțională, pot fi utilizate pentru a verifica calitatea și integritatea piesei.
- Reciclarea și reutilizarea materialelor:Orice material în exces sau resturi generat în timpul turnării prin injecție poate fi reciclat și reutilizat. Reducerea utilizării noului material termoplastic ajută la minimizarea deșeurilor și la îmbunătățirea durabilității.
Echipamente utilizate în turnarea prin injecție
Aceste componente ale echipamentelor facilitează procesul de turnare prin injecție, de la topirea și injectarea materialului termoplastic până la modelarea, răcirea și ejectarea piesei finale. Operarea și întreținerea corespunzătoare a acestor componente ale echipamentelor sunt cruciale pentru realizarea unei producții eficiente și de înaltă calitate de turnare prin injecție.
- Mașină de turnat prin injecție:Echipamentul primar în turnarea prin injecție este responsabil pentru topirea materialului termoplastic, injectarea acestuia în matriță și controlul procesului.
- Matrite: Matrița, proiectată la comandă pentru a crea forma și caracteristicile dorite ale piesei din plastic, cuprinde două jumătăți, cavitatea și miezul. Operatorii îl montează pe unitatea de prindere a mașinii de turnat prin injecție.
- Buncăr:Container care deține materialul termoplastic sub formă de granule sau granule și îl alimentează în butoiul mașinii de turnat prin injecție pentru topire și injectare.
- Cilindru și șurub: Butoiul, o cameră cilindrică, topește și omogenizează materialul termoplastic pe măsură ce șurubul se rotește în interiorul acestuia pentru a topi, amesteca și standardiza materialul.
- Sisteme de incalzire si racire:Mașinile de turnat prin injecție au elemente de încălzire, cum ar fi încălzitoare electrice sau încălzitoare cu ulei fierbinte, pentru a crește temperatura butoiului, și sisteme de răcire, cum ar fi circulația apei sau a uleiului, pentru a răci matrița și a solidifica piesa de plastic.
- Sistem de evacuare:Îndepărtează piesa turnată din cavitatea matriței după solidificare, utilizând în mod obișnuit știfturi de ejectare, plăci sau explozii de aer în timpul deschiderii matriței.
- Sistem de control:Monitorizează și controlează diferiți parametri ai procesului de turnare prin injecție, permițând operatorilor să seteze și să ajusteze parametri precum viteza de injecție, temperatura, presiunea și timpul de răcire.
Mașini de turnat prin injecție: tipuri și caracteristici
Fiecare tip de mașină de turnat prin injecție are caracteristicile și avantajele sale, permițând producătorilor să aleagă cel mai potrivit dispozitiv pentru cerințele lor specifice de producție.
- Mașini hidraulice de turnat prin injecție: Aceste mașini folosesc sisteme hidraulice pentru a genera presiunea necesară pentru a injecta plastic topit în matriță. Sunt cunoscuți pentru forța lor mare de strângere, controlul precis și versatilitatea în manipularea diferitelor materiale termoplastice. Mașinile hidraulice sunt potrivite pentru producția la scară largă și pot găzdui matrițe complexe.
- Mașini electrice de turnat prin injecție:Mașinile electrice utilizează servomotoare electrice pentru funcționarea mașinii, inclusiv sistemele de injecție, prindere și ejector. Ele oferă control precis, eficiență energetică și timpi de răspuns mai rapidi decât mașinile hidraulice. Mașinile electrice sunt ideale pentru aplicațiile de turnare de precizie care necesită repetabilitate și precizie ridicate.
- Mașini hibride de turnat prin injecție:Mașinile hibride combină beneficiile dispozitivelor hidraulice și electrice. Acestea utilizează o combinație de sisteme servo hidraulice și electrice pentru a obține o precizie ridicată, eficiență energetică și rentabilitate. Mașinile hibride sunt potrivite pentru o gamă largă de aplicații, oferind un echilibru între performanță și costurile operaționale.
- Mașini de turnat prin injecție cu două plăci: Mașinile cu două plăci au un design unic cu două plăci separate pentru prinderea matriței. Acest design oferă o stabilitate sporită, o sincronizare îmbunătățită a matriței și permite dimensiuni mai mari ale matriței și forțe de strângere mai mari. Mașinile cu două plăci sunt potrivite pentru piese mari și complexe care necesită turnare precisă.
- Mașini de turnat prin injecție cu mai multe componente:Producătorii proiectează aceste mașini pentru a produce piese cu mai multe materiale sau culori într-un singur ciclu de turnare. Au diverse unități de injectare și matrițe, permițând injectarea simultană a diferitelor materiale. Mașinile cu mai multe componente oferă flexibilitate și eficiență în fabricarea pieselor complexe cu caracteristici diferite.
- Mașini de turnat cu microinjecție:Proiectate special pentru producerea de piese mici și precise, mașinile de turnat cu microinjecție oferă o precizie și o acuratețe incredibil de ridicate. Ele pot produce detalii complicate cu toleranțe strânse și risipă minimă de material. Electronicele, dispozitivele medicale și micro-optica folosesc în mod obișnuit mașini de turnare cu microinjecție.
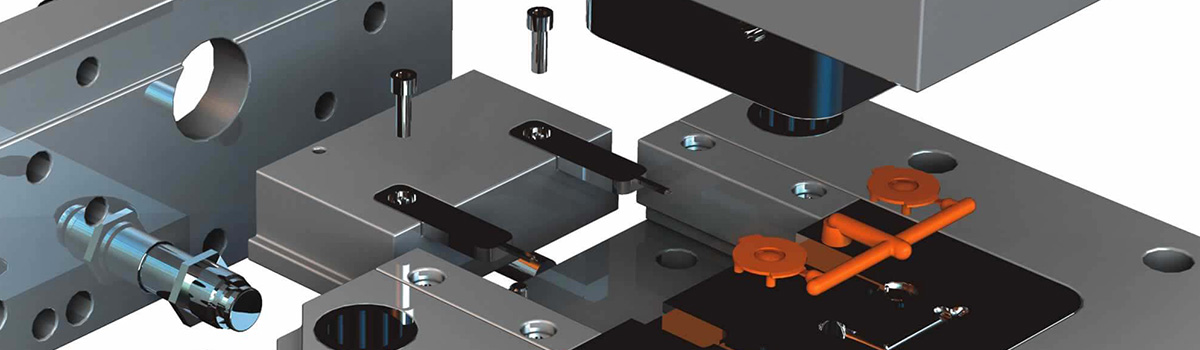
Considerații de proiectare a matriței pentru turnarea prin injecție
Considerațiile atente ale designului matriței sunt esențiale pentru producția de succes a turnării prin injecție.
- Design piese:Designul matriței trebuie să se potrivească cerințelor specifice ale piesei, inclusiv forma, dimensiunile și caracteristicile funcționale ale acesteia. Producătorii ar trebui să ia în considerare în mod corespunzător unghiurile de tragere, grosimea peretelui, decupările și orice elemente necesare pentru a asigura ușurința de evacuare și calitatea pieselor.
- Material matriță: Selectarea materialului matriței este crucială pentru obținerea durabilității, stabilității dimensionale și rezistenței la căldură. Materialele obișnuite ale matriței includ aliaje de oțel, aliaje de aluminiu și oțeluri pentru scule. Alegerea materialului depinde de factori precum volumul producției, complexitatea piesei și durata de viață așteptată a sculei.
- Sistem de răcire:Răcirea eficientă este esențială pentru solidificarea corectă a pieselor și pentru minimizarea timpului de ciclu. Designul matriței trebuie să includă canale de răcire sau inserții poziționate strategic pentru a asigura o răcire uniformă a matriței. Răcirea adecvată reduce riscul deformarii, contracției și defectelor pieselor.
- Aerisire:Este necesară o ventilație adecvată pentru a permite evacuarea aerului și a gazelor în timpul procesului de injecție. Aerisirea insuficientă poate duce la capcane de gaz, urme de arsuri sau umplere incompletă a pieselor. Producătorii pot realiza aerisirea încorporând caneluri de aerisire, știfturi sau alte mecanisme în designul matriței.
- Sistem de evacuare:Designul matriței ar trebui să includă un sistem eficient de evacuare pentru a îndepărta în siguranță și eficient piesa turnată din cavitatea matriței. Sistemul de ejecție poate consta din știfturi, manșoane sau alte mecanisme, poziționate strategic pentru a evita interferența cu funcția sau caracteristicile critice.
- Design poarta:Poarta este locul unde plasticul topit intră în cavitatea matriței. Designul porții trebuie să asigure umplerea corespunzătoare a pieselor, să minimizeze liniile de curgere și să prevină înghețarea prematură a materialului. Modelele standard de porți includ porți de margine, porți de tunel și sisteme cu canal cald, în funcție de cerințele piesei și de proprietățile materialului.
- Linie de despărțire:Designul matriței ar trebui să definească o linie de despărțire adecvată, care este linia în care cele două jumătăți ale matriței se unesc. Amplasarea corectă a liniei de despărțire asigură o nepotrivire minimă a fulgerului și a liniei de despărțire și facilitează asamblarea eficientă a matriței.
- Întreținerea matriței și capacitatea de service: Producătorii ar trebui să ia în considerare ușurința întreținerii, reparațiilor și întreținerii mucegaiului. Componentele matriței trebuie să fie ușor accesibile pentru curățare, inspecție și înlocuire. Încorporarea de caracteristici precum inserții cu schimbare rapidă sau modele de matrițe modulare poate îmbunătăți funcționalitatea matriței.
Materiale de matriță utilizate în turnarea prin injecție
Colaborarea cu specialiști în materiale de matriță și luarea în considerare a nevoilor specifice ale aplicației de turnare poate ajuta la determinarea celui mai potrivit material pentru obținerea performanței optime a matriței și a calității pieselor.
- Aliaje de oțel: Aliajele de oțel, cum ar fi oțelurile pentru scule (de exemplu, P20, H13) și oțelurile inoxidabile, sunt utilizate în mod obișnuit pentru matrițele de turnare prin injecție datorită durabilității excelente, rezistenței la căldură și rezistenței la uzură. Aceste materiale pot rezista la temperaturile și presiunile ridicate din procesul de turnare prin injecție și oferă o bună stabilitate dimensională pentru producerea de piese de înaltă calitate.
- Aliaje de aluminiu:Aliajele de aluminiu, cum ar fi 7075 și 6061, sunt ușoare și oferă o conductivitate termică bună, făcându-le potrivite pentru matrițe care necesită o răcire eficientă. Producătorii folosesc adesea matrițe din aluminiu pentru prototipare, producție de volum redus sau aplicații în care reducerea greutății este critică. Cu toate acestea, matrițele din aluminiu pot avea o durabilitate mai mică în comparație cu aliajele de oțel.
- Aliaje de cupru:Aliajele de cupru, cum ar fi cuprul de beriliu, prezintă o conductivitate termică ridicată și o prelucrabilitate bună. Ei găsesc utilizare în matrițe care necesită un transfer de căldură excelent pentru o răcire eficientă. Aliajele de cupru pot ajuta la reducerea timpilor de ciclu prin disiparea rapidă a căldurii din piesa turnată, rezultând o solidificare mai rapidă.
- Oțeluri pentru scule:Oțelurile pentru scule, inclusiv H13, S7 și D2, sunt proiectate pentru aplicații de scule de înaltă performanță. Aceste oțeluri oferă o combinație de rezistență ridicată, duritate și rezistență la uzură. Oțelurile pentru scule se potrivesc matrițelor cu volume mari de producție, materiale abrazive sau condiții de turnare exigente.
- Aliaje de nichel:Aliajele de nichel, cum ar fi Inconel și Hastelloy, sunt cunoscute pentru rezistența lor excepțională la coroziune, rezistența la temperaturi ridicate și stabilitatea termică. Producătorii folosesc aceste aliaje în matrițe care manipulează materiale corozive sau necesită rezistență la temperaturi extreme și medii de turnare agresive.
- Materiale compozite:Materialele compozite, cum ar fi materialele plastice armate sau compozitele cu inserții metalice, sunt utilizate ocazional pentru aplicații specifice de turnare. Aceste materiale oferă un echilibru de proprietăți, cum ar fi rezistență ridicată, stabilitate termică și greutate redusă. Formele compozite pot fi alternative rentabile pentru cerințe specifice de producție.
Tipuri de matrițe de injecție
Turnarea prin injecție este un proces de fabricație versatil și utilizat pe scară largă pentru piese din plastic.
- matriță cu două plăci:Forma cu două plăci este cel mai comun tip de matriță de injecție. Este alcătuit din două plăci, placa de cavitate și placa de miez, care se separă pentru a permite ejectarea piesei turnate. Placa cu cavitate conține partea cavității matriței, în timp ce placa cu miez găzduiește partea cu miez. Producătorii folosesc matrițe cu două plăci pentru a produce o gamă largă de piese datorită designului lor relativ simplu.
- matriță cu trei plăci:Forma cu trei plăci este o versiune avansată a matriței cu două plăci. Include o placă suplimentară, coloana sau placa de bac. Placa de rulare creează un canal separat pentru canal, canale și porți, permițând îndepărtarea mai ușoară a piesei turnate. Producătorii folosesc în mod obișnuit matrițe cu trei plăci pentru detalii cu sisteme complexe de închidere sau atunci când este de dorit evitarea unui vestigiu de poartă pe piesa.
- Mucegai Hot Runner:Sistemul de canal și poartă este încălzit în matrițe cu canal cald, eliminând nevoia de solidificare și retopire a materialului în timpul fiecărui ciclu. Sistemul de canal cald este format din colectoare și duze încălzite care mențin starea topit a plasticului. Formele cu canal cald oferă avantaje, cum ar fi timpul de ciclu redus, deșeurile de material mai mici și calitatea îmbunătățită a pieselor prin minimizarea vestigiilor de poartă.
- Mucegai Cold Runner: Formele cu canal rece au un sistem tradițional de canal și poartă în care plasticul topit curge prin canale reci care se solidifică cu fiecare ciclu. Operatorii îndepărtează ulterior coloanele solidificate, rezultând deșeuri de material. Producătorii folosesc în mod obișnuit matrițe complexe pentru un volum mai mic de producție sau când costurile materialelor sunt mai puțin critice datorită designului lor mai simplu.
- Inserare matriță:Formele de inserție încorporează inserții de metal sau plastic în cavitatea matriței în timpul turnării prin injecție. Inserțiile pot fi introduse în prealabil în matriță sau introduse prin procese automate. Această matriță permite integrarea unor componente suplimentare sau elemente de armare în piesa turnată, sporind funcționalitatea sau rezistența acesteia.
- Supramulare: Supramularea implică turnarea unui material peste altul, de obicei lipirea unui substrat rigid din plastic cu un elastomer sau termoplastic mai moale. Acest proces permite crearea de piese cu mai multe materiale sau texturi într-o singură matriță, oferind o aderență îmbunătățită, amortizare sau caracteristici estetice.
Factori care afectează costurile de turnare prin injecție
Luarea în considerare a acestor factori poate ajuta producătorii să estimeze și să optimizeze costul turnării prin injecție, asigurând un echilibru între calitate, eficiență și rentabilitate pentru cerințele lor specifice de producție.
- Complexitatea părții:Complexitatea designului piesei joacă un rol semnificativ în determinarea costului turnării prin injecție. Geometriile complicate, decupările, pereții subțiri sau caracteristicile complexe pot necesita scule suplimentare, matrițe specializate sau cicluri mai lungi, crescând costul total de producție.
- Selectarea materialului:Alegerea materialului termoplastic afectează costul turnării prin injecție. Diferitele materiale au prețuri diferite pe kilogram, iar factori precum disponibilitatea materialului, proprietățile și cerințele de procesare pot influența costul total al materialului.
- Design de scule și matrițe: Costurile inițiale de scule și proiectare a matriței sunt semnificative în costurile de turnare prin injecție. Factori precum complexitatea matriței, numărul de cavități, dimensiunea matriței și materialul matriței contribuie la cheltuielile cu sculele și fabricarea matriței. Formele mai complexe sau matrițele care necesită caracteristici avansate pot crește investiția inițială.
- Volumul productiei: Volumul de producție are un impact direct asupra costului pe piesă în turnarea prin injecție. Cărțile mai înalte duc adesea la economii de scară, reducând costul pe piesă. Dimpotrivă, producția de volum redus poate suporta taxe mai mari din cauza instalării, sculelor și deșeurilor de materiale.
- Durata ciclului: Timpul ciclului, care include fazele de răcire și de evacuare, afectează capacitatea de producție și costul total. Cicluri mai lungi au ca rezultat reducerea producției și, potențial, prețuri mai mari. Optimizarea designului matriței, a sistemului de răcire și a parametrilor procesului poate minimiza timpii de ciclu și poate îmbunătăți eficiența.
- Cerințe de calitate:Cerințele stricte de calitate sau certificările specifice pot afecta costul turnării prin injecție. Îndeplinirea toleranțelor exacte, cerințele de finisare a suprafeței sau testarea suplimentară poate necesita alte resurse, procese sau inspecții, adăugând costul total.
- Operatii secundare:Dacă piesele turnate necesită operații de post-procesare, cum ar fi asamblare, vopsire sau etape suplimentare de finisare, aceste operațiuni se pot adăuga la costul total de turnare prin injecție.
- Furnizor și locație:Alegerea furnizorului de turnare prin injecție și locația acestora pot afecta costurile. Costurile cu forța de muncă, cheltuielile generale, logistica și cheltuielile de transport variază în funcție de locația furnizorului, influențând costul total de producție.
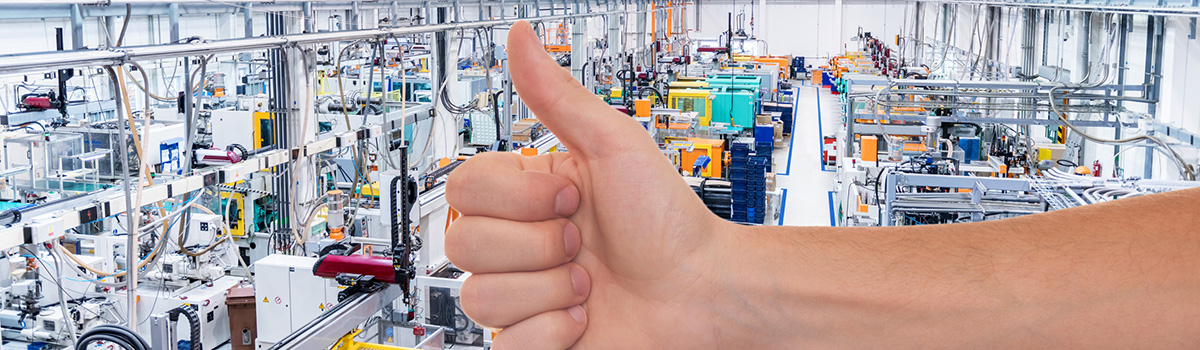
Controlul calității în turnarea prin injecție
Implementarea unor măsuri robuste de control al calității pe tot parcursul procesului de turnare prin injecție ajută la identificarea și abordarea potențialelor defecte, abateri sau inconsecvențe, asigurând producția de piese de înaltă calitate care îndeplinesc specificațiile și cerințele clienților.
- Monitorizarea procesului: Monitorizarea continuă a parametrilor cheie ai procesului, cum ar fi temperatura topiturii, presiunea de injecție, timpul de răcire și timpul ciclului, asigură consistența și repetabilitatea în producția pieselor. Monitorizarea în timp real și sistemele automatizate pot detecta variații sau abateri de la parametrii stabiliți, permițând ajustări în timp util și menținând stabilitatea procesului.
- Inspecție și măsurare:Revizuirea și măsurarea periodică a pieselor turnate sunt esențiale pentru a verifica acuratețea dimensională, calitatea pieselor și respectarea specificațiilor. Serviciile noastre acoperă o gamă largă de metode de control al calității, cum ar fi măsurarea dimensiunilor, analiza calității suprafeței, efectuarea de inspecții vizuale și efectuarea de teste funcționale. Pentru o evaluare precisă sunt utilizate diverse tehnici de inspecție, cum ar fi mașinile de măsurare în coordonate (CMM) și sistemele de inspecție optică și vizuală.
- Controlul statistic al procesului (SPC): SPC implică colectarea și analiza datelor de proces pentru a monitoriza și controla calitatea turnării prin injecție. Metodele statistice, cum ar fi diagramele de control și analiza capacității procesului, ajută la identificarea tendințelor, la detectarea variațiilor procesului și asigură că procesul rămâne în limitele de control definite. SPC permite identificarea proactivă a problemelor și facilitează optimizarea procesului.
- Testarea materialului: Testarea materiilor prime, cum ar fi termoplastele, aditivii și coloranții, asigură calitatea și adecvarea acestora pentru turnarea prin injecție. Testarea materialelor poate include analiza indicelui de curgere a topiturii (MFI), proprietățile mecanice, caracteristicile termice și compoziția materialului. Verificarea calității materialului ajută la prevenirea defectelor și inconsistențelor în piesele turnate.
- Întreținerea și inspecția sculelor:Întreținerea corespunzătoare și inspecția regulată a matrițelor de injecție sunt cruciale pentru asigurarea calității în turnarea prin injecție. Curățarea, lubrifierea și evaluarea regulată a componentelor matriței ajută la prevenirea uzurii, deteriorarea sau degradarea care ar putea afecta calitatea pieselor. Repararea sau înlocuirea în timp util a componentelor matriței uzate sau deteriorate este esențială pentru a menține performanța constantă a turnării.
- Documentare si trasabilitate:Menținerea documentației cuprinzătoare și a înregistrărilor de trasabilitate este esențială pentru controlul calității în turnarea prin injecție. Este vital să se înregistreze parametrii procesului, rezultatele inspecției, informațiile despre materiale și orice modificări sau ajustări efectuate în timpul producției. Documentația adecvată permite trasabilitatea pieselor, facilitează analiza cauzei principale și asigură consecvența calității.
- Formare și dezvoltare a abilităților: Furnizarea de programe adecvate de formare și dezvoltare a abilităților operatorilor, tehnicienilor și personalului de control al calității le îmbunătățește înțelegerea proceselor de turnare prin injecție, cerințele de calitate și tehnicile de inspecție. Personalul bine instruit poate detecta defectele, poate rezolva problemele și poate implementa măsuri corective în mod eficient, asigurând o producție de înaltă calitate.
Defecte comune de turnare prin injecție și cum să le evitați
Inspecția, monitorizarea și analiza regulată a proceselor de turnare prin injecție și întreținerea și reglarea corespunzătoare a echipamentelor și matrițelor pot ajuta la identificarea și rezolvarea acestor defecte comune.
- Semne de scufundare:Urmele de chiuvetă sunt depresiuni sau adâncituri pe suprafața piesei turnate cauzate de răcirea neuniformă sau de contracție. Ar trebui să luați în considerare locația și designul adecvat al porții, designul optim al sistemului de răcire și distribuția uniformă a grosimii peretelui pentru a evita urmele de chiuvetă. Creșterea presiunii de injecție sau reglarea timpului de răcire poate ajuta, de asemenea, la minimizarea urmelor chiuvetei.
- Warpage:Deformarea se referă la deformarea sau îndoirea unei piese turnate după ejectare din cauza răcirii neuniforme sau a tensiunilor reziduale. Menținerea grosimii uniforme a peretelui, utilizarea canalelor de răcire adecvate și asigurarea unei umpleri și ambalări echilibrate a matriței sunt cruciale pentru a preveni deformarea. Optimizarea temperaturii matriței, utilizarea unghiurilor de tragere adecvate și controlul temperaturii materialului și al vitezei de injecție pot ajuta la minimizarea deformarii.
- Flash:Flashul apare atunci când excesul de material curge în linia de despărțire a matriței, rezultând proeminențe subțiri, nedorite sau material suplimentar pe piesa finală. Se poate preveni eficient fulgerul asigurând un design adecvat al matriței, inclusiv aplicarea unei forțe de strângere adecvate, alinierea precisă și utilizarea tehnicilor de aerisire adecvate. Optimizarea parametrilor de proces, cum ar fi presiunea de injecție, temperatura și timpul de ciclu, reduce flash-ul.
- lovitură scurtă:O lovitură rapidă are loc atunci când materialul injectat nu umple cavitatea matriței, rezultând o piesă incompletă. Selectarea corectă a materialului, asigurarea unei temperaturi și vâscozitate adecvate a topiturii și menținerea presiunii și a timpului de injecție adecvate sunt esențiale pentru a evita fotografiile scurte. În plus, verificarea designului matriței pentru o dimensiune suficientă a canalului și a porții și o ventilație adecvată poate ajuta la prevenirea loviturilor rapide.
- Linii de sudare:Liniile de sudură apar atunci când două sau mai multe fronturi de flux de material topit se întâlnesc și se solidifică, rezultând o linie sau un semn vizibil pe suprafața piesei. Designul bun al porții și al canalului, temperatura optimă de topire, viteza de injecție și ajustarea fluxului de material și a geometriei pieselor pot minimiza liniile de sudură. Analiza curgerii matriței și optimizarea plasării porții pot ajuta, de asemenea, la prevenirea sau atenuarea liniilor de sudură.
- Semne de ardere:Urmele de arsură sunt decolorări sau pete negre de pe suprafața piesei turnate cauzate de căldura excesivă sau supraîncălzirea materialului. Evitarea temperaturii extreme de topire, utilizarea canalelor de răcire adecvate și optimizarea duratei ciclului pot ajuta la prevenirea urmelor de arsuri. Aerisirea adecvată, designul adecvat al porții și controlul temperaturii matriței contribuie, de asemenea, la minimizarea urmelor de arsuri.
Operatii post-turnare: finisare si asamblare
După turnarea prin injecție, multe piese turnate pot necesita operațiuni suplimentare de finisare și asamblare pentru a obține produsul final dorit. Aceste operațiuni post-turnare pot include:
- Tundere:Îndepărtați orice exces de material sau fulger din jurul piesei turnate folosind unelte de tăiere sau tăiere.
- Tratament de suprafață:Îmbunătățirea aspectului sau funcționalității suprafeței piesei folosind diverse tehnici, cum ar fi vopsirea, acoperirea sau texturarea.
- Asamblare:Îmbinarea mai multor piese turnate sau adăugarea de componente cum ar fi elemente de fixare, inserții sau etichete pentru a finaliza produsul final.
- Testarea:Verificarea calității și funcționalității pieselor prin diferite metode de testare, cum ar fi analiza dimensională, testarea proprietăților materialelor sau testarea performanței.
- Ambalare și expediere:Ambalarea și etichetarea corespunzătoare a produsului finit pentru expediere către clienți sau utilizatori finali.
Alegerea operațiunilor de post-turnare depinde de aplicația specifică și de caracteristicile dorite ale produsului final. Colaborarea strânsă între experții în turnare prin injecție, specialiștii în finisare și asamblare și client este crucială pentru a obține calitatea și funcționalitatea absolută dorită a produsului. Planificarea corectă și integrarea operațiunilor de post-turnare în procesul de fabricație poate ajuta la asigurarea unei producții eficiente și a livrării la timp a produselor de înaltă calitate.
Turnarea prin injecție vs. alte procese de fabricare a plasticului
Fiecare proces de fabricare a plasticului are avantaje și limitări, făcându-le potrivite pentru diferite aplicații.
- Turnare prin injecție: Turnarea prin injecție este un proces de producție extrem de versatil și utilizat pe scară largă pentru producerea pieselor din plastic. Oferă avantaje precum eficiența ridicată a producției, replicarea precisă a pieselor și capacitatea de a crea geometrii complexe. Turnarea prin injecție este potrivită pentru serii de producție de mare volum și permite utilizarea unei game largi de materiale termoplastice. Oferă o precizie dimensională excelentă și un finisaj al suprafeței, făcându-l ideal pentru diverse industrii, cum ar fi auto, bunuri de larg consum și dispozitive medicale.
- Turnare prin suflare: Turnarea prin suflare este un proces utilizat în principal pentru producerea de piese goale din plastic, cum ar fi sticle, containere și componente auto. Aceasta implică topirea plasticului și umflarea acestuia într-o cavitate a matriței, creând forma dorită. Turnarea prin suflare este potrivită pentru producția de volum mare și poate produce piese mari, ușoare, cu grosime uniformă a peretelui. Cu toate acestea, este limitat în ceea ce privește complexitatea piesei și selecția materialului în comparație cu turnarea prin injecție.
- Termoformare:Termoformarea este un proces folosit pentru a produce piese din plastic prin încălzirea unei foi termoplastice și modelarea acesteia folosind matrițe sau formare în vid. Găsește o utilizare obișnuită în ambalaje, produse de unică folosință și produse la scară largă, cum ar fi tăvi și capace. Termoformarea oferă producție rentabilă pentru piese mari și permite prototiparea rapidă. Cu toate acestea, are limitări în ceea ce privește complexitatea pieselor, selecția materialului și acuratețea dimensională în comparație cu turnarea prin injecție.
- extrudare:Extrudarea este un proces continuu de producere a profilelor, foilor, tuburilor și foliilor din plastic. Aceasta implică topirea rășinii de plastic și forțarea acesteia printr-o matriță pentru a crea forma dorită. Extrudarea este potrivită pentru producerea de lungimi lungi și continue de produse din plastic cu o secțiune transversală consistentă. În timp ce extrudarea oferă rate de producție ridicate și eficiență a costurilor, este limitată în ceea ce privește geometriile complexe ale pieselor și controlul dimensional precis în comparație cu turnarea prin injecție.
- Turnare prin compresie:Turnarea prin compresie implică plasarea unei cantități pre-măsurate de material termorigid într-o cavitate a matriței încălzită și comprimarea acesteia la presiune ridicată până când se întărește. Găsește o utilizare comună în producerea de piese cu rezistență ridicată și stabilitate dimensională, cum ar fi componentele auto și izolația electrică. Turnarea prin comprimare oferă o consistență bună a pieselor, o eficiență ridicată a producției și capacitatea de a utiliza o gamă largă de materiale. Cu toate acestea, este limitat în ceea ce privește complexitatea piesei și timpul ciclului în comparație cu turnarea prin injecție.
Aplicații ale turnării prin injecție a materialelor termoplastice
Diverse industrii folosesc pe scară largă turnarea prin injecție termoplastică datorită versatilității, eficienței și rentabilității sale. Unele dintre aplicațiile turnării prin injecție a materialelor termoplastice includ:
- Industria auto: Industria auto folosește pe scară largă turnarea prin injecție termoplastică pentru a fabrica diverse componente, inclusiv ornamente interioare și exterioare, tablouri de bord, panouri de uși, bare de protecție și conectori electrici. Procesul permite replicarea precisă a pieselor, geometrii complexe și materiale ușoare, îmbunătățind eficiența consumului de combustibil și flexibilitatea designului.
- Bunuri de consum:Turnarea prin injecție își găsește aplicații extinse în producerea de bunuri de larg consum, cum ar fi aparate de uz casnic, dispozitive electronice, recipiente de ambalare și jucării. Procesul permite producerea în masă a produselor durabile, de înaltă calitate, cu dimensiuni și finisaj de suprafață consistente. De asemenea, permite opțiuni de personalizare și iterații rapide ale produsului.
- Dispozitive medicale:Turnarea prin injecție joacă un rol crucial în industria medicală pentru producerea unei game largi de dispozitive, inclusiv seringi, instrumente chirurgicale, componente implantabile și sisteme de livrare a medicamentelor. Procesul asigură producția de piese sterile, precise și biocompatibile care îndeplinesc cerințele stricte de reglementare din sectorul sănătății.
- Industria electronică și electrică:Industria electronică utilizează turnarea prin injecție pentru a produce conectori electrici, carcase, comutatoare și alte componente. Procesul oferă o precizie dimensională ridicată, un finisaj excelent al suprafeței și capacitatea de a încorpora caracteristici precum turnarea prin inserție și supramularea, permițând producția eficientă de ansambluri electronice complexe.
- Industria ambalajelor:Diverse industrii, inclusiv alimente și băuturi, produse farmaceutice și îngrijire personală, folosesc în mod obișnuit turnarea prin injecție pentru producerea de recipiente, capace, capace și sticle de ambalaje din plastic. Procesul permite crearea de soluții de ambalare ușoare, durabile și atractive din punct de vedere estetic, cu cicluri de producție eficiente.
- Industrie aerospatiala:Sectorul aerospațial folosește turnarea prin injecție pentru fabricarea de componente ușoare și de înaltă performanță, cum ar fi conducte de aer, suporturi, panouri interioare și piese structurale. Procesul permite utilizarea materialelor avansate și a geometriilor complicate ale pieselor, contribuind la reducerea greutății și la îmbunătățirea eficienței combustibilului.
Impactul asupra mediului al turnării prin injecție a materialelor termoplastice
Turnarea prin injecție a materialelor termoplastice este un proces de fabricație popular datorită numeroaselor sale beneficii, dar este, de asemenea, esențial să se ia în considerare impactul asupra mediului. Iată câteva puncte de luat în considerare:
- Eficiența materialului:Turnarea prin injecție de termoplastic promovează eficiența materialului prin reducerea la minimum a deșeurilor. Procesul utilizează un control precis asupra cantității de material injectat în matriță, reducând nevoia de material în exces. Producătorii pot folosi, de asemenea, tehnici de reclăcire și reciclare pentru a reutiliza deșeurile sau piesele refuzate, reducând și mai mult deșeurile de materiale.
- Consumul de energie:Producătorii proiectează mașini de turnat prin injecție pentru a fi eficiente din punct de vedere energetic, cu modele moderne care încorporează tehnologii avansate, cum ar fi servomotoare și variatoare de viteză. Aceste caracteristici optimizează utilizarea energiei prin reducerea consumului de energie în timpul turnării, având ca rezultat cerințe mai mici de energie și un impact redus asupra mediului.
- Gestionarea deșeurilor:În timp ce reduc la minimum risipa de materiale, producătorii ar trebui să implementeze practici adecvate de gestionare a deșeurilor pentru a gestiona materialele rămase, sprue sau canale. Producătorii pot stabili programe de reciclare pentru colectarea și reutilizarea deșeurilor de plastic generate în timpul turnării prin injecție, reducând astfel deșeurile trimise la gropile de gunoi.
- Reducerea emisiilor: Turnarea prin injecție a materialelor termoplastice generează, în general, emisii mai mici decât alte procese de fabricație. Producătorii pot reduce emisiile utilizând materiale ecologice, implementând echipamente eficiente din punct de vedere energetic și utilizând sisteme avansate de evacuare și filtrare pentru a capta orice emisii emise.
- Alegeri materiale durabile:Selectarea materialelor termoplastice poate avea un impact semnificativ asupra durabilității ecologice a turnării prin injecție. Optarea pentru materiale plastice biodegradabile sau pe bază de bio, precum și pentru materiale reciclate sau reciclabile, poate ajuta la reducerea amprentei ecologice generale a procesului.
Considerații privind ciclul de viață: luarea în considerare a întregului ciclu de viață al produsului turnat este esențială pentru evaluarea impactului său asupra mediului. În timpul etapelor de proiectare și selecție a materialelor, producătorii ar trebui să ia în considerare factori precum durabilitatea piesei, reciclabilitatea acesteia și potențialul de eliminare sau reutilizare la sfârșitul vieții.
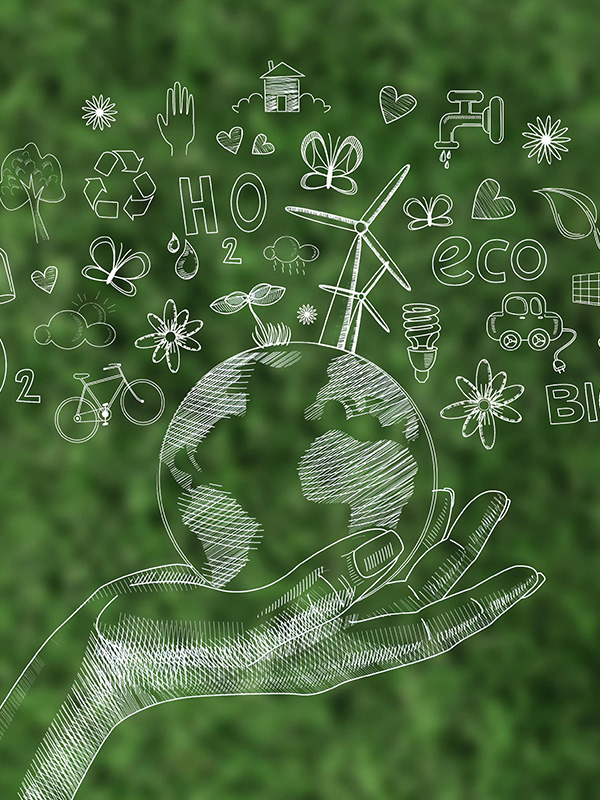
Viitorul turnării prin injecție a materialelor termoplastice
Viitorul turnării prin injecție a materialelor termoplastice pare promițător, cu progrese continue în tehnologie și cerere crescută pentru piese de precizie de înaltă calitate în diverse industrii. Unele dintre evoluțiile cheie așteptate în următorii ani includ:
- Utilizarea sporită a automatizării și a roboticii pentru a îmbunătăți eficiența și a reduce costurile.
- Eforturile sunt concentrate pe dezvoltarea de noi materiale și procese pentru a îmbunătăți performanța pieselor și a permite noi aplicații.
- Este o adoptare în creștere a practicilor durabile, cum ar fi utilizarea materialelor reciclate și optimizarea consumului de energie, pentru a reduce impactul asupra mediului al turnării prin injecție.
- O mai bună integrare a tehnologiilor digitale, cum ar fi software-ul de imprimare și simulare 3D, pentru a îmbunătăți procesele de proiectare și producție.
Piața globală de turnare prin injecție se extinde, în special în economiile emergente, determinată de cererea tot mai mare de produse din plastic în diverse industrii.
Alegerea partenerului potrivit de turnare prin injecție
Alegerea partenerului potrivit de turnare prin injecție este crucială pentru succesul proiectului dumneavoastră. Fă-ți timp să evaluezi mai multe opțiuni, să efectuezi vizite la fața locului și să te angajezi în discuții amănunțite pentru a asigura un parteneriat compatibil și de lungă durată.
- Expertiză și experiență:Căutați un partener de turnare prin injecție cu cunoștințe și experiență vastă în industrie. Ar trebui să aibă o experiență dovedită în furnizarea de produse și soluții de înaltă calitate clienților din diverse sectoare. Luați în considerare înțelegerea lor asupra diferitelor materiale, modele de matrițe și procese de fabricație.
- Capabilitati de productie: Evaluați capacitățile de producție ale partenerului de turnare prin injecție. Asigurați-vă că au o instalație bine echipată cu mașini și tehnologii moderne pentru a face față cerințelor proiectului dumneavoastră. Luați în considerare capacitatea lor de producție, capacitatea de a gestiona diferite dimensiuni și complexități ale pieselor și capacitatea de a îndeplini volumele și termenele de producție dorite.
- Asigurarea calității:Calitatea este primordială în turnarea prin injecție. Evaluează sistemele de control al calității și certificările potențialului partener. Căutați parteneri care respectă standarde stricte de calitate, au procese robuste de inspecție și efectuează teste cuprinzătoare pentru a asigura calitatea și consecvența pieselor.
- Suport pentru proiectare și inginerie:Un partener de încredere de turnare prin injecție ar trebui să ofere suport de proiectare și inginerie pentru a optimiza designul piesei dumneavoastră pentru fabricabilitate. Aceștia ar trebui să aibă ingineri calificați care pot oferi informații valoroase cu privire la selecția materialelor, proiectarea matriței și optimizarea procesului pentru a îmbunătăți calitatea și eficiența pieselor.
- Competitivitatea costurilor:Deși costul nu ar trebui să fie singurul factor determinant, este esențial să se evalueze prețul și competitivitatea costurilor partenerului de turnare prin injecție. Solicitați cotații detaliate și luați în considerare costurile cu sculele, costurile materialelor, costurile cu forța de muncă și orice servicii suplimentare pe care le oferă.
- Comunicare și colaborare:Comunicarea și colaborarea eficientă sunt esențiale pentru un parteneriat de succes. Asigurați-vă că partenerul de turnare prin injecție are canale bune de comunicare, răspunde la întrebările dvs. și poate oferi actualizări regulate ale proiectului. O abordare de colaborare va ajuta să ne asigurăm că îndeplinim cerințele dvs. și răspundem prompt oricăror provocări.
- Referințe și recenzii clienți:Căutați referințe ale clienților sau citiți recenzii/mărturii pentru a obține informații despre experiențele altor clienți cu partenerul de turnare prin injecție. Obținerea acestor informații poate ajuta la determinarea fiabilității, a promptitudinii și a nivelului general de mulțumire a clienților.
Concluzie
Turnarea prin injecție a materialelor termoplastice este o metodă versatilă și rentabilă pentru fabricarea pieselor din plastic în cantități mari. Capacitatea sa de a produce forme complexe cu precizie și consistență ridicată a devenit o alegere populară pentru diverse industrii, inclusiv auto, medical, electronice și bunuri de larg consum. Înțelegând diferitele aspecte ale turnării prin injecție termoplastic, inclusiv avantajele, dezavantajele și considerentele de proiectare ale acesteia, puteți lua decizii informate cu privire la alegerea partenerului potrivit de turnare prin injecție pentru nevoile dvs. de afaceri.