Giải pháp cho các khuyết tật đúc phổ biến của ép phun
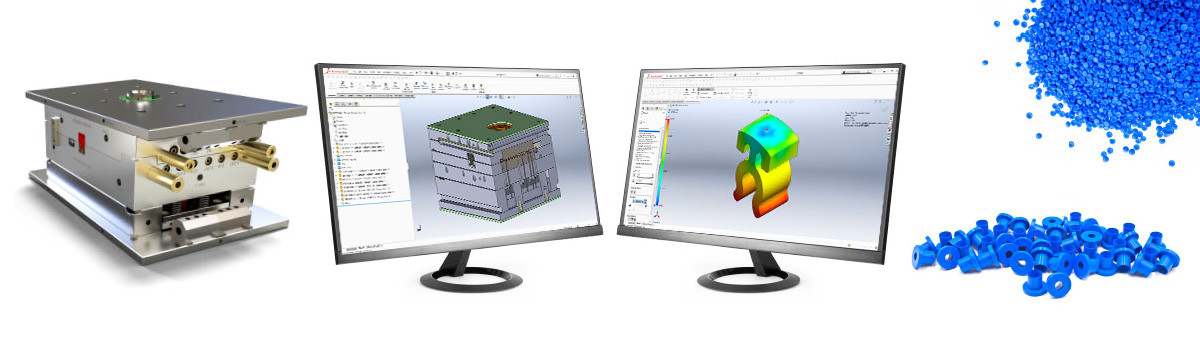
Các lỗi thường gặp khi sử dụng khuôn để xử lý các bộ phận ép phun nhựa và điều này phần lớn ảnh hưởng đến hiệu quả xử lý. Sau đây là các lỗi khuôn phổ biến và giải pháp cho các bộ phận khuôn ép nhựa.
Những cú đánh ngắn
Các bức ảnh ngắn đề cập đến các sản phẩm được tạo ra không đầy đủ do các khuôn không được điền đầy đủ.
Lỗi này thường xuất hiện ở vị trí xa cổng nhất hoặc các bộ phận chỉ có thể tiếp cận qua các khu vực hẹp trên khuôn vì các khu vực hẹp có thể ảnh hưởng đến dòng chảy của tan chảy.
Bắn ngắn có thể gây ra các vết chảy vi mô hoặc dẫn đến một phần lớn sản phẩm bị thiếu rõ ràng.
Nguyên nhân:
Nguyên nhân cho các bức ảnh ngắn bao gồm:
Nguyên liệu thô được đưa vào khuôn là không đủ.
Điện trở của nóng chảy lớn, dẫn đến khuôn không thể được lấp đầy hoàn toàn.
Sự thông hơi của khuôn kém và gây ra hiện tượng xâm thực làm tắc dòng chảy, làm cho dòng chảy không thể chảy đến một số khu vực của khuôn.
gờ
Các gờ được tạo ra do sự bám dính của các nguyên liệu thô dư thừa được ép đùn từ khoang khuôn vào sản phẩm.
Lỗi này sẽ xuất hiện trên các cạnh của sản phẩm hoặc trên từng bộ phận cấu tạo của khuôn. Nguyên liệu thô có thể bị tràn ra khỏi khuôn, hoặc các vị trí liên kết của khuôn di chuyển và khuôn cố định.
Gờ cũng có thể được tìm thấy trên lõi khuôn, do áp suất thủy lực hoặc chốt góc.
Mức độ nghiêm trọng của các gờ khác nhau, đôi khi mỏng, đôi khi dày hơn.
Nguyên nhân:
Nguyên nhân cho burrs bao gồm:
Bề mặt khuôn kẹp bị hư hỏng hoặc mòn nhiều.
Khuôn di chuyển và khuôn cố định bị lệch vị trí khi chúng bị khóa.
Áp suất của nguyên liệu trong khuôn cao hơn lực kẹp khuôn.
Điều kiện thứ ba được đề cập ở trên sẽ xuất phát từ nhiều lý do. Trong các tình huống sau, áp suất của nguyên liệu thô cao hơn lực kẹp khuôn.
Ở giai đoạn đầu tiên của khuôn phun (giai đoạn điền đầy khuôn), quá nhiều nguyên liệu thô được làm đầy, làm tăng áp suất bên trong khuôn.
Trong quá trình điền đầy khuôn, lực cản lớn của dòng chảy nóng chảy cũng sẽ làm tăng áp suất bên trong khuôn.
Áp suất khoang khuôn quá cao trong giai đoạn giữ áp suất.
Lực kẹp khuôn không đủ.
suy thoái
Việc phân tách có thể dẫn đến nhiều kết quả. Mức độ và mức độ nghiêm trọng của vấn đề cũng khác nhau. Trong trường hợp nghiêm trọng nhất, nó có thể khiến sản phẩm bị đổi màu hoàn toàn và tính chất cơ học kém. Sự xuống cấp cục bộ sẽ chỉ gây ra các sọc hoặc đốm sẫm màu.
Nguyên nhân:
Sự xuống cấp là do nguyên liệu thô bị hư hỏng. Các phân tử chuỗi dài tạo thành nhựa sẽ bị phân hủy dưới tác động của nhiệt độ quá cao hoặc ứng suất cắt quá mức. Trong quá trình phân hủy các phân tử, khí dễ bay hơi sẽ đẩy nhanh quá trình phân hủy, điều này sẽ gây ra hiện tượng mất màu của nguyên liệu thô. Sự phân hủy của một lượng lớn các phân tử cuối cùng sẽ phá vỡ thành phần của nguyên liệu thô và gây ra ảnh hưởng tiêu cực đến các tính chất cơ học.
Sự xuống cấp cục bộ có thể do nhiệt độ không đồng đều của thùng vật liệu.
Sự xuống cấp có thể xảy ra trong các trường hợp sau:
Nguyên liệu đang được làm nóng quá mức trong thùng nguyên liệu hoặc hệ thống chạy nóng.
Nguyên liệu ở trong thùng quá lâu.
Trong quá trình ép phun, ứng suất cắt tác dụng lên nguyên liệu quá lớn. Nếu các vòi bị chặn, hoặc cửa và đường dẫn quá hẹp, nó sẽ làm tăng ứng suất cắt.
Biến dạng
Trong các tình huống bình thường, hình dạng của sản phẩm phải phù hợp với hình dạng của khuôn. Sự biến dạng đề cập đến sự biến dạng của sản phẩm.
Khi tình trạng trở nên tồi tệ hơn, sản phẩm sẽ bị biến dạng hoàn toàn khi bị đẩy ra khỏi khuôn. Khi tình trạng không nghiêm trọng, hình dạng sản phẩm sẽ xuất hiện những bất thường nhỏ.
Dài nhưng không có gờ đỡ hoặc mặt phẳng lớn là những vùng dễ bị biến dạng nhất.
Nguyên nhân:
Nguyên nhân biến dạng:
Nhiệt độ quá cao khi khuôn được giải phóng.
Do thời gian làm mát khác nhau ở các khu vực dày và mỏng, hoặc sự khác biệt về nhiệt độ khuôn khi di chuyển khuôn và cố định khuôn, nên sự co ngót bên trong sản phẩm là khác nhau.
Khuôn chảy không trơn tru khi đổ đầy (cái gọi là “Định hướng đóng băng”) hoặc áp suất bên trong khoang khuôn quá cao ở giai đoạn giữ áp suất.
Các tạp chất
Các tạp chất thường xuất hiện dưới dạng các đốm có màu sắc khác nhau, các mảng hoặc sọc. Một trong những phổ biến nhất là đốm đen.
Các tạp chất có thể chỉ là những đốm nhỏ, nhưng cũng có thể là các đường sọc rõ ràng hoặc phần lớn bị mất màu khi nghiêm trọng.
Nguyên nhân:
Các tạp chất được gây ra bởi các đồ lặt vặt trộn với nguyên liệu thô, chẳng hạn như:
Nguyên liệu trộn lẫn với đồ lặt vặt khi nó được vận chuyển vào thùng.
Sự phân hủy của nguyên liệu thô có thể rơi ra từ bất kỳ cơ chế cắt nào và lẫn vào nguyên liệu thô, chẳng hạn như bu-lông máy, thành trong của trống sấy, khớp nối/vòi phun.
Sự ép kim loại
Cán màng sẽ tạo ra “hiệu ứng da” trên bề mặt sản phẩm, nguyên nhân là do sự khác biệt về tính chất và kết cấu của bề mặt sản phẩm và các nguyên liệu thô khác, đồng thời tạo thành lớp da bong tróc có thể loại bỏ được.
Khi cán màng nghiêm trọng, toàn bộ diện tích mặt cắt ngang được tạo thành từ các lớp khác nhau và chưa được nấu chảy với nhau. Khi các khuyết tật ít rõ ràng hơn, bề ngoài của sản phẩm có thể đáp ứng các yêu cầu, nhưng sẽ phá vỡ các tính chất cơ học của sản phẩm.
Nguyên nhân:
Có hai nguyên nhân chính dẫn đến hiện tượng cán màng. Đầu tiên là khi hai loại nguyên liệu thô khác nhau trộn lẫn với nhau không chính xác. Hai nguyên liệu thô sẽ được vận chuyển vào thùng cùng một lúc dưới áp lực. Tuy nhiên, khi khuôn không thể tan chảy với nhau khi nó được làm mát, giống như các lớp khác nhau được ép buộc lại với nhau để tạo thành sản phẩm.
Thứ hai: nếu dòng chảy lạnh buộc phải đi qua cổng hẹp, ứng suất cắt sẽ được tạo ra. Ứng suất cắt quá cao sẽ khiến lớp nóng chảy bị nóng chảy trước không thể hợp nhất hoàn toàn.
Rủi ro trộn lẫn:
Một điều cần lưu ý là một số nguyên liệu thô trộn với nhau sẽ dẫn đến phản ứng hóa học mạnh, chẳng hạn như PVC và Avetal không được trộn lẫn.
bạc tuyến tính
Sliver linear có thể chỉ là hiện tượng cục bộ, nhưng có thể mở rộng ra toàn bộ bề mặt khi nghiêm trọng.
Bạc tuyến tính sẽ ảnh hưởng đến vẻ ngoài của sản phẩm và cũng làm hỏng các tính chất cơ học của sản phẩm.
Nguyên nhân:
Hai điểm sau đây gây ra tuyến tính bạc:
Nguyên liệu ướt và một số trong số chúng sẽ hấp thụ hơi nước trong không khí. Nếu nguyên liệu thô quá ướt, hơi áp suất có thể được tạo ra dưới nhiệt độ cao và áp suất cao của thùng. Những hơi này xuyên qua bề mặt của sản phẩm và tạo thành các sọc bạc.
Sự tan chảy bị hư hỏng do nhiệt và tạo ra sự xuống cấp cục bộ. Khí dễ bay hơi sinh ra sẽ bị chặn lại trên bề mặt khuôn và tạo ra các đường sọc trên bề mặt sản phẩm.
Đây không phải là tồi tệ hơn như sự xuống cấp. Miễn là nhiệt độ nóng chảy cao hoặc nó chịu ứng suất cắt trong quá trình hóa dẻo hoặc bơm vào khuôn, điều này có thể xảy ra.
Bóng/bóng
Bề mặt hoàn thiện của sản phẩm phải giống như bề mặt của khuôn. Khi lớp hoàn thiện bề mặt của hai loại khác nhau, sẽ xảy ra các khuyết tật về độ bóng/bóng.
Bề mặt sẽ ảm đạm khi xuất hiện các khuyết tật, và bề mặt thô ráp sẽ nhẵn và bóng.
Nguyên nhân:
Các nguyên nhân gây bóng/bóng bao gồm:
Dòng chảy không đều hoặc nhiệt độ của bề mặt khuôn thấp, dẫn đến bề mặt khuôn không thể được nhân đôi khi đúc vật liệu.
Trong quá trình giữ áp suất, áp suất trong khoang không đủ cao khiến vật liệu bám vào bề mặt khuôn trong quá trình làm nguội, để lại vết co ngót.
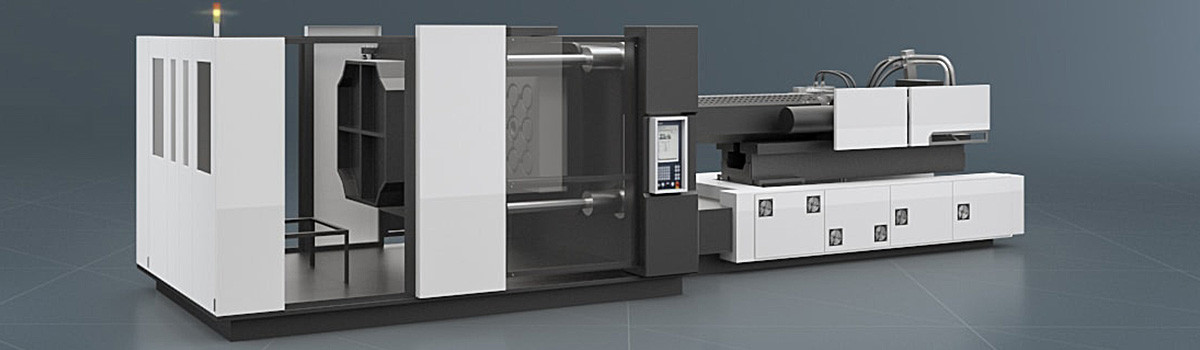
Dòng chảy
Dấu chảy có thể được tìm thấy trên bề mặt sản phẩm dưới nhiều hình thức. Nói chung, nó sẽ tạo thành một vùng bóng tối.
Dấu chảy không tạo ra bất kỳ vết dập nổi hoặc vết lõm nào trên bề mặt sản phẩm, điều mà ngón tay không thể cảm nhận được. Lỗi này còn được gọi là dấu kéo, bóng mờ và bóng.
Khi các vết chảy rõ ràng, nó sẽ tạo ra các rãnh và để lại các khuyết tật như vết hằn trên bề mặt sản phẩm.
Nguyên nhân:
Dấu hiệu dòng chảy có thể được tìm thấy khi:
Khả năng chảy của chất lỏng chảy kém hoặc nhiệt độ bề mặt của khuôn thấp, dẫn đến khả năng chống chảy của nhựa trong quá trình đổ khuôn lớn.
Trong quá trình điền đầy khuôn, dòng chảy nóng chảy có lực cản, có thể do bề mặt khuôn không bằng phẳng, các dấu hoặc hoa văn in trên bề mặt khuôn hoặc do sự thay đổi hướng dòng chảy trong quá trình điền đầy.
đường nối
Đường nối được tạo ra khi hai mặt trước nóng chảy gặp nhau trong quá trình điền đầy khuôn và sẽ xuất hiện trên bề mặt sản phẩm giống như một đường kẻ.
Đường nối giống như đường nứt trên bề mặt sản phẩm, không thể phát hiện rõ ràng.
Khi thiết kế khuôn mẫu, một số đường nối có thể nhìn thấy là không thể tránh khỏi. Trong trường hợp này, hãy rút ngắn đường nối càng nhiều càng tốt để tránh làm hỏng độ bền và vẻ ngoài của sản phẩm.
Nguyên nhân:
Có nhiều lý do cho việc tạo ra mặt trận tan chảy. Lý do khả dĩ nhất có thể là dòng chảy dọc theo các cạnh của lõi khuôn. Khi hai sự tan chảy gặp nhau, nó tạo ra các đường nối. Nhiệt độ của hai mặt trước nóng chảy phải đủ cao để cho phép chúng kết hợp với nhau thành công và không ảnh hưởng đến độ bền và hình thức của sản phẩm.
Khi hai sự tan chảy không thể kết hợp hoàn toàn với nhau, các khuyết tật sẽ được tạo ra.
Nguyên nhân cho các khiếm khuyết:
Khuôn có các phần dày hơn và mỏng hơn, và tốc độ dòng chảy của chất nóng chảy là khác nhau, khi chất lỏng chảy qua phần mỏng của khuôn, nhiệt độ sẽ thấp.
Chiều dài của mỗi người chạy là khác nhau. Kẻ chạy cô độc sẽ dễ nguội lạnh.
Áp suất khoang khuôn không đủ để cho phép tan chảy hoàn toàn trong giai đoạn giữ áp suất.
Các bong bóng còn lại làm cho mặt trước tan chảy không thể hợp nhất, điều này cũng sẽ dẫn đến cháy.
Đốt
Vết cháy tương tự như vết đốt ngắn, nhưng có các cạnh mờ dần không đều và có mùi khét nhẹ. Các vùng đen carbon sẽ xuất hiện trên sản phẩm, khi tình trạng nghiêm trọng, kèm theo mùi khét của nhựa.
Nếu các khuyết tật không được loại bỏ, thường có sự lắng đọng màu đen trên khuôn. Nếu các chất khí hoặc dầu được tạo ra khi đốt cháy không được kiểm tra ngay lập tức, chúng có thể làm tắc các lỗ khí. Đốt cháy thường được tìm thấy ở cuối con đường.
Nguyên nhân:
Đốt cháy là do hiệu ứng đốt cháy bên trong. Khi áp suất trong không khí tăng mạnh trong thời gian rất ngắn, nhiệt độ sẽ tăng cao và gây bỏng. Theo dữ liệu thu thập được, hiệu ứng đốt trong trong quá trình ép phun có thể tạo ra nhiệt độ cao lên đến 600 độ.
Sự cháy có thể xảy ra khi:
Tốc độ điền đầy khuôn nhanh để không khí không thể thoát ra khỏi khoang khuôn và tạo ra bọt khí do khối nhựa đi vào và dẫn đến hiệu ứng đốt cháy bên trong sau khi bị nén.
Các lỗ thoát khí bị bít hoặc thông gió không thông suốt.
Không khí trong khuôn phải được loại bỏ khỏi các lỗ khí. Nếu việc thông gió bị ảnh hưởng bởi vị trí, số lượng, kích thước hoặc chức năng, không khí sẽ ở lại trong khuôn và dẫn đến cháy. Lực kẹp khuôn lớn cũng sẽ dẫn đến thông gió kém.
Sự thu hẹp
Co rút đề cập đến các vết lõm nhẹ trên bề mặt sản phẩm.
Khi các khuyết tật nhẹ, bề mặt của sản phẩm không đồng đều. Khi nghiêm trọng, diện tích lớn sản phẩm sẽ sụp đổ. Các sản phẩm có vòm, tay cầm, phần nhô ra thường bị khuyết tật co ngót.
Nguyên nhân:
Sự co ngót là do nguyên liệu thô bị co lại trên diện rộng trong quá trình làm mát.
Ở khu vực sản phẩm dày (như vòm), nhiệt độ lõi của vật liệu thấp nên sự co ngót sẽ xảy ra muộn hơn so với bề mặt, điều này sẽ tạo ra lực co rút bên trong nguyên liệu thô và kéo mặt ngoài vào trong. để tạo ra sự co ngót.
Co rút xảy ra trong các tình huống sau:
Áp suất trong khoang khuôn thấp hơn lực tạo ra từ sự co ngót của nguyên liệu thô trong quá trình làm mát.
Không đủ thời gian điều áp của khoang khuôn trong quá trình làm mát, dẫn đến nguyên liệu thô chảy ra khỏi khoang từ cổng.
Nguyên liệu thô không có đủ khả năng đệm trong giai đoạn tạo khuôn và giữ áp suất vì vít được rút ra hoàn toàn trước khi lượng nguyên liệu thô dư thừa được bơm vào.
Diện tích mặt cắt ngang của cổng và thanh trượt nhỏ hơn nhiều so với độ dày của sản phẩm, điều đó có nghĩa là cổng đã được đông lạnh trước quá trình ép đùn sản phẩm.
Bubbles
Bong bóng chân không được thể hiện dưới dạng bọt khí, có thể dễ dàng tìm thấy trên các sản phẩm trong suốt. Nó cũng có thể được nhìn thấy trên mặt cắt ngang của các sản phẩm đục.
Nguyên nhân:
Bong bóng khí là phần chân không của sản phẩm, được tạo ra khi nguyên liệu thô co lại trong quá trình làm mát.
Tương tự như sự co ngót, bên trong nguyên liệu thô tạo ra lực co rút. Điều khác biệt là hình thức bên ngoài của sản phẩm đã được đông đặc lại khi các bong bóng được hình thành và không có sự sụp đổ, do đó các bong bóng rỗng được tạo ra.
Nguyên nhân của bong bóng cũng giống như nguyên nhân giảm, bao gồm:
Áp lực khoang khuôn không hiệu quả
Thời gian điều áp khoang không đủ
Kích thước của người chạy và cổng quá nhỏ
vết phun
Dấu phun đề cập đến khu vực ren đối diện với cổng. Các vết phun không chỉ ảnh hưởng đến vẻ ngoài của sản phẩm mà còn ảnh hưởng đến độ bền của sản phẩm.
Nguyên nhân:
Các vết phun là do dòng chảy chảy ra ngoài tầm kiểm soát trong quá trình điền đầy khuôn.
Nhựa nóng chảy vào khuôn dưới áp suất rất lớn. Nếu tốc độ đổ đầy khuôn quá cao, nhựa sẽ văng ra khỏi khe hở của khoang khuôn và nhanh chóng đàn hồi trở lại và nguội đi. Vào thời điểm đó, các sợi được hình thành, chặn nhựa nóng chảy đi vào cổng.
Nguyên nhân chính của các vết phun là do vị trí của cổng không chính xác hoặc thiết kế của cổng. Hai tình huống sau đây sẽ làm trầm trọng thêm tình trạng lỗi:
Tốc độ điền đầy khuôn cao
Dòng chảy kém trong quá trình điền đầy khuôn