Trường hợp ở Ấn Độ
Dịch vụ khuôn ép phun của DJmolidng cho các công ty Ấn Độ
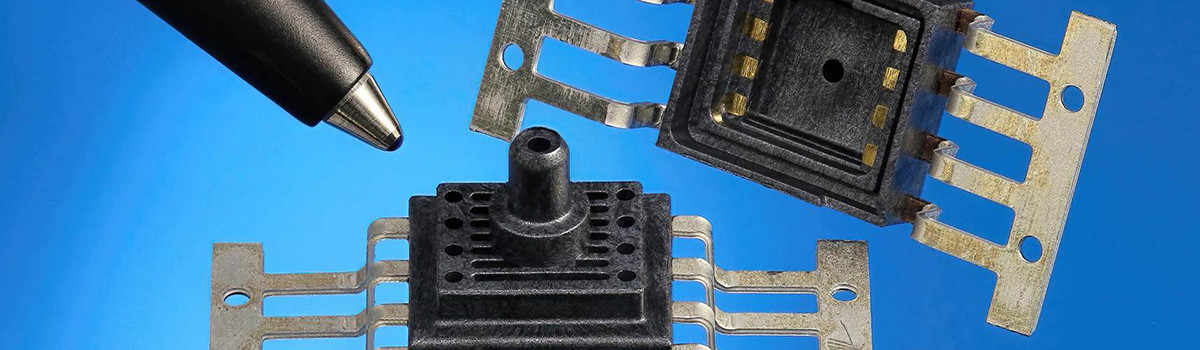
Khuôn chèn nói chung là một loại khuôn dùng để chế tạo đai ốc, các bộ phận kim loại hoặc các bộ phận nhựa cứng cố định bên trong các khoang để ép phun.
DJmolding cung cấp dịch vụ ép phun mlod chèn cho thị trường Ấn Độ và chúng tôi sản xuất rất nhiều bộ phận nhựa của khuôn chèn cho các ngành công nghiệp khác nhau, đặc biệt là cho các nhà sản xuất thiết bị gia dụng. Một số nhà sản xuất thiết bị gia dụng của Ấn Độ đã mua các bộ phận bằng nhựa của khuôn chèn trong một thời gian dài từ DJmolding. Chúng tôi có quan hệ đối tác rất tốt với các công ty của Ấn Độ này.
Chèn ép phun đai ốc: vật liệu đai ốc có thể là thép không gỉ, đồng, đồng và thép, thông thường các loại đai ốc bằng đồng thường được sử dụng. Đồng rất dễ uốn, giúp nối đai ốc và nhựa tốt hơn. Dung sai của các lỗ bên trong đai ốc phải được kiểm soát trong phạm vi 0.02mm, nếu không dung sai vượt quá 0.02mm sẽ dễ gây ra hiện tượng lóe sáng. Khi lắp khuôn, cần lắp đai ốc vào chốt chèn để thử nghiệm. Nếu nó vừa khít giữa các đai ốc và chốt, sẽ khó đẩy chi tiết ra và gây ra các vết đẩy ra hoặc các vấn đề về dính. Nếu nó lắp lỏng lẻo, nó sẽ gây ra đèn flash.
Chèn các bộ phận kim loại ép phun:
Các bộ phận kim loại có thể là thép không gỉ, nhôm, đồng, thép, v.v. Dung sai của các bộ phận kim loại phải được kiểm soát trong phạm vi 0.02mm, nếu không, vật liệu khó bịt kín và dễ có tia chớp. Diện tích của các bộ phận kim loại không thể được thiết kế quá lớn.
Nếu diện tích đổ đầy cho các bộ phận kim loại quá lớn, sẽ rất khó để đạt được sự phun đầy đủ do chênh lệch nhiệt độ lớn giữa các bộ phận kim loại. Vị trí của các bộ phận kim loại thường được thiết kế trong khoang vì khoang không di chuyển, giúp tránh hiện tượng lóe sáng do các bộ phận kim loại bị lỏng khi di chuyển (trong trường hợp nghiêm trọng, có thể làm hỏng khuôn). Trong trường hợp đặc biệt, vị trí của các chi tiết kim loại chỉ được thiết kế ở lõi hoặc mặt bên của sản phẩm.
Chèn khuôn ép nhựa cứng:
Thường chọn các loại nhựa cứng có nhiệt độ nóng chảy cao như PEEK, PA66+30GF, PP+30GF, PA12+30GF, PPS….v.v. Dung sai cho các loại nhựa cứng này phải chính xác. Các khuyết tật như co ngót, vết lõm và biến dạng không thể tồn tại trong khu vực niêm phong. Khi lắp khuôn, nhựa cứng nên được đặt bên trong khuôn để thử nghiệm và để lại 0.05-0.1mm trước khi ép xung quanh khu vực niêm phong để đạt được độ kín tốt hơn.
Phần nhựa cứng không nên thiết kế diện tích quá lớn sẽ gây chênh lệch nhiệt độ và khó đổ đầy vật liệu khi phun. Thường làm cho phần nhựa cứng cố định ở bên cạnh khoang, vì khoang không di chuyển, để tránh flash hoặc thậm chí làm hỏng khuôn khi di chuyển khuôn. Trong trường hợp đặc biệt, chỉ được thiết kế vị trí của các chi tiết kim loại ở lõi hoặc mặt bên của sản phẩm.
Điểm mấu chốt trong thiết kế
1. Thiết kế co rút đối với các sản phẩm có chèn đai ốc, trong khi không cần thiết kế co ngót đối với các sản phẩm có bộ phận kim loại và chèn nhựa cứng. Đối với những khu vực cần dung sai nghiêm ngặt, hãy sửa đổi dung sai kích thước của sản phẩm thành trung bình.
2. Thường sử dụng đế khuôn với cổng chốt tiêu chuẩn trong thiết kế khuôn, và trong quá trình phun thứ cấp, hãy đặt các bộ phận chèn vào khoang càng nhiều càng tốt. Với điều kiện làm cho các hạt dao được cố định trong khoang, hãy xem xét làm thế nào để tạo ra một phần còn lại trong lõi sau khi ép phun, theo cách này, một phần có thể được đẩy ra. Thường thêm các khối đàn hồi trong khoang và keo đàn hồi để giữ một phần trong lõi. Khoảng cách giữa các khối đàn hồi và keo không được quá lớn, nếu không lực đàn hồi sẽ gây biến dạng các bộ phận bằng nhựa cứng hoặc kim loại. Khoảng cách thường được thiết kế trong vòng 2 mm, và tăng số lượng khối đàn hồi và keo đàn hồi một cách thích hợp khi các miếng chèn kim loại hoặc nhựa cứng có diện tích tương đối lớn.
3. Độ dày của vật liệu tốt nhất là trong khoảng 1.3-1.8mm (khoảng 1.5mm là tốt nhất), nếu không, cần kiểm tra bản vẽ sản phẩm và đề nghị khách hàng sửa đổi. Nếu độ dày vật liệu mỏng hơn 1.3mm thì vật liệu khó điền đầy, trong khi độ dày vật liệu dày hơn 1.8mm dễ xảy ra hiện tượng co ngót trong sản xuất.
4.Gating là rất quan trọng trong khuôn. Sự cân bằng của việc lấp đầy vật liệu cho điểm cổng cần được xem xét đầy đủ. Khi vật liệu chạy đến khu vực cố định các bộ phận bằng kim loại hoặc nhựa cứng, tốc độ lấp đầy vật liệu và áp suất sẽ giảm xuống do chênh lệch nhiệt độ và điện trở của vật liệu chèn.
5.Đối với hệ thống đẩy khuôn, phải xem xét sự cân bằng của việc đẩy khuôn nếu không sẽ xảy ra biến dạng sau khi đẩy. Đối với các bộ phận không thể đẩy ra trong trạng thái cân bằng, cần xem xét khả năng thu gọn để cải thiện vấn đề cân bằng trong thiết kế kết cấu.
6. Để đảm bảo chất lượng hình thức của các bộ phận sau khi được đẩy ra trong quá trình ép phun, thiết bị đẩy phải là cục nhựa cứng được chèn bằng ABS hoặc PMMA. Nếu trên khuôn có niêm phong trượt, hãy thiết kế các rãnh trượt trong khoang càng nhiều càng tốt, vì các rãnh trượt trong khoang tạo điều kiện thuận lợi cho việc lắp khuôn.
7. Để đảm bảo độ bền của niêm phong SA (phụ cấp đường may), đối với sản phẩm được tạo ra từ quá trình ép phun hai lần, chiều rộng của niêm phong SA tối thiểu phải là 0.8mm. Đối với vật liệu phun thứ cấp là nhựa cứng, chiều rộng của niêm phong SA tối thiểu phải là 1.0mm, nếu không, cần đề nghị khách hàng sửa đổi sản phẩm.
8. Trong thiết kế khuôn mẫu, chúng ta nên xem xét các máy ép phun để sản xuất xem loại máy nào được sử dụng, dọc hay ngang. Có ý kiến cho rằng không nên thiết kế quá nhiều rãnh, đặc biệt đối với khuôn có rãnh chạy nguội vì quá nhiều rãnh khiến rãnh chạy lâu hơn, gây lãng phí vật liệu và cũng có hại cho việc phun đạt hiệu quả cao. Để phù hợp với máy ép phun, chúng ta phải xem xét liệu nó có nhỏ gọn và hợp lý cho việc sắp xếp sản phẩm hay không. Các sản phẩm phải được cố định để đảm bảo sản phẩm ở tình trạng giống nhau mỗi khi chúng được đưa vào khuôn. Một cách khác là hệ thống phản ứng thiết kế để cảnh báo nếu bộ phận không ở đúng vị trí trước khi đóng khuôn, giúp ngừng đóng khuôn. Bằng cách này, các bộ phận ở trong cùng một tình huống trong khuôn, giúp tăng tỷ lệ chất lượng và hiệu quả sản xuất trong quá trình ép phun.
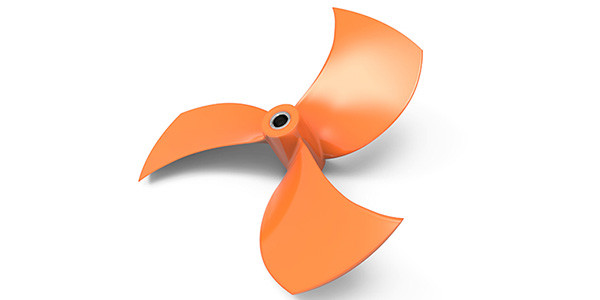
9. Một giá đỡ bằng thép phải được thiết kế vì khu vực phun khuôn chịu áp lực phun lớn (nên lớn hơn 5-10 mm so với hình dạng và kích thước của bộ phận). Không được để khoảng trống giữa các bộ phận xung quanh khu vực Đúc quá mức, nếu không bộ phận đó sẽ không còn hình dạng sau khi phun lần thứ hai. Đối với các bộ phận không có SA (phụ cấp đường may) sẽ cần chú ý nhiều hơn đến khía cạnh này.
10. Đường thoát khí dễ xảy ra Đường thoát khí dễ dàng xảy ra trong quá trình ép phun, vì vậy phải xem xét đầy đủ việc thông hơi trong thiết kế khuôn. Ở tất cả các góc khuất và các vị trí đối với đường nước dài, phải thiết kế các lỗ thoát hơi trên phần nhựa cứng vì ở các góc khuất sẽ khó đổ vật liệu hơn rất nhiều.
11. Để đảm bảo vật liệu được bơm vào và lực đẩy đủ điều kiện được lấp đầy hoàn toàn, một cách là thiết kế một đường cắt ở các góc của bộ phận để tăng cường kết quả kết dính và sau đó làm cho các bộ phận bám chặt hơn.
12. Tại khu vực làm kín và khu vực đường chia khuôn, chúng ta không nên tháo khuôn từ khoang và lõi, vì các đường kẹp trong khuôn và bản nháp tháo khuôn sẽ gây ra hiện tượng lóe sáng khi lắp khuôn. Thử tháo khuôn bằng LISS-OFF.
Các loại điểm cổng của khuôn chèn
Điểm cổng cho khuôn chèn có thể được thiết kế để định hướng cổng van phun nóng, cổng chốt ống dẫn nước nóng, cổng điểm chốt, cổng phụ, cổng cạnh, v.v.
Cổng van xả nóng: thanh khoản tốt, chọn vị trí linh hoạt, điểm cổng nhỏ. Thích hợp cho sản xuất hàng loạt và cho các sản phẩm có độ dày thành dày. Có thể giúp tiết kiệm vật liệu, không lãng phí vật liệu cho cổng, thời gian thực hiện ngắn và chất lượng cao. Khiếm khuyết duy nhất là dấu vết cổng nhỏ.
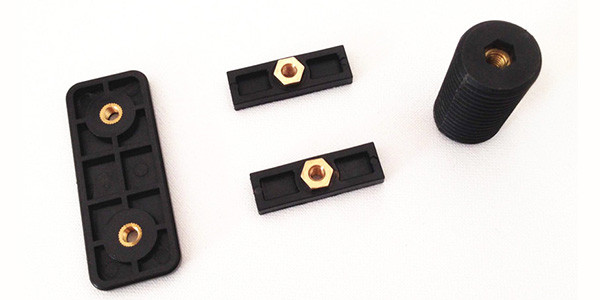
Cổng pin nóng: thanh khoản tốt, chọn vị thế linh hoạt, điểm cửa nhỏ. Thích hợp cho sản xuất hàng loạt và cho các sản phẩm có độ dày thành dày. Có thể giúp tiết kiệm vật liệu, không lãng phí vật liệu cho cổng, thời gian thực hiện ngắn và chất lượng cao. Nhưng có những khiếm khuyết, chẳng hạn như vật liệu còn lại 0.1mm xung quanh điểm cổng và dễ bị bavia. Cần tạo rãnh để phủ vật liệu trái xung quanh điểm cổng.
Cổng chốt: chọn vị trí linh hoạt, thanh khoản yếu, khoảng cách chạy dài, điểm cổng nhỏ. Phù hợp cho sản xuất hàng loạt nhỏ. Nhiều chất thải xung quanh điểm cổng. Cần tay cơ khí để kẹp điểm cổng trong sản xuất. Thời gian dẫn dài. Khiếm khuyết là 0.1-0.2mm vật liệu còn lại xung quanh điểm cổng, cần tạo rãnh để che vật liệu còn lại xung quanh điểm cổng.
Cổng phụ: có thể được thiết kế trên các sườn trong khoang, lõi, thành bên và chốt đẩy. Có thể chọn điểm cổng linh hoạt, cổng rót tự động tách khỏi bộ phận, dấu vết cổng nhỏ. Khuyết điểm: dễ kéo vật liệu ra xung quanh điểm cổng, dễ tạo vết khô ở vị trí cổng, cần gạt vật liệu bằng tay, mất lực ép nhiều từ điểm cổng từ khoang.
Cổng cạnh: nhựa nóng chảy chảy qua cửa, phân bố ngang đều, giảm ứng suất; giảm khả năng lọt khí vào khoang, tránh tạo vệt và bong bóng. Khuyết điểm: cổng rót không thể tự động tách ra khỏi bộ phận, để lại dấu vết phun trên các cạnh của bộ phận, cần dụng cụ để gia công phẳng cổng rót. Cổng cạnh có thể giúp tỷ lệ phun và giữ áp suất, đồng thời cũng tốt cho việc giữ áp suất và cấp liệu, theo cách này, sẽ tốt hơn cho việc cải thiện đường dẫn khí, vạch dòng chảy, v.v.
Gia công và lắp khuôn chèn
1. Trước khi xử lý, hãy tìm ra công nghệ xử lý khuôn. Chọn máy gia công có độ chính xác cao, máy tốc độ cao, máy cắt dây NC tốc độ chậm, máy EDM gương (gia công phóng điện), v.v.
2.Thiết kế chừa 0.05-0.1mm tại vị trí ép trước.
3. Lưu ý các yêu cầu về độ chính xác trong xử lý đế khuôn, kiểm tra dung sai sau khi lấy đế khuôn và không sử dụng nếu dung sai không đủ tiêu chuẩn.
4. Đặt đai ốc, các bộ phận kim loại và các bộ phận nhựa cứng bên trong khuôn để lắp khuôn. Nếu phát hiện có vấn đề trong việc lắp khuôn, hãy kiểm tra các đai ốc, bộ phận kim loại, bộ phận nhựa cứng và khuôn để xem cái nào sai. Gia công phần theo bản vẽ càng nhiều càng tốt, giúp theo dõi dữ liệu trong tương lai.
5.Không thể sử dụng máy mài để lắp khuôn. Chuyển sang máy để sửa những chỗ lắp khuôn chưa tốt.
6. Thực hiện kiểm tra hành động trước khi dùng thử, tránh lắp ráp sai và lắp ráp nhầm. Lắp ráp sai sẽ gây hư hỏng đế khuôn.
Kiểm tra khuôn cho khuôn chèn
1. Trong kiểm tra khuôn, người ta cần biết rõ ràng về trình tự mở, đóng và đẩy khuôn. Hiểu được đặc điểm cấu tạo và tính chất của các chi tiết kim loại và các chi tiết nhựa cứng.
2. Biết rõ về số lượng mẫu mà khách hàng cần, chuẩn bị đủ đai ốc, bộ phận kim loại và nhựa cứng, vì cần nhiều mẫu trong thử nghiệm khuôn.
3. Lưu ý xem có thể kiểm tra khuôn mà không chèn đai ốc, bộ phận kim loại hoặc nhựa cứng hay không. Nếu các đai ốc chèn, các bộ phận kim loại và nhựa cứng không được lắp ráp vào khuôn, bộ phận đó có thể có các khuyết tật như dính vào khuôn hoặc bắn ngắn.
4. Trong nhiều trường hợp, cần điều chỉnh tấm đường nước trên khuôn, nhưng đôi khi không thể điều chỉnh tấm đường nước trong một số khuôn chèn dựa trên cấu trúc của chúng, hoặc thậm chí tệ hơn, khuôn bị kẹt nặng và cần sửa đổi, hoặc khuôn bị hỏng trong khuôn khai mạc.
5. Các vấn đề có thể xảy ra trong quá trình thử nghiệm khuôn, chẳng hạn như bắn ngắn, trượt không khí, nhấp nháy hoặc dính vào khuôn. Nếu các vấn đề có thể được xác minh trên máy ép phun, thì tốt hơn là nên giải quyết nó.
DJmolding có hơn 10 năm kinh nghiệm đúc chèn, nếu bạn có bất kỳ câu hỏi nào, vui lòng liên hệ với chúng tôi.