ಇಂಜೆಕ್ಷನ್ ಮೋಲ್ಡಿಂಗ್ನ ಸಾಮಾನ್ಯ ಮೋಲ್ಡಿಂಗ್ ದೋಷಗಳಿಗೆ ಪರಿಹಾರಗಳು
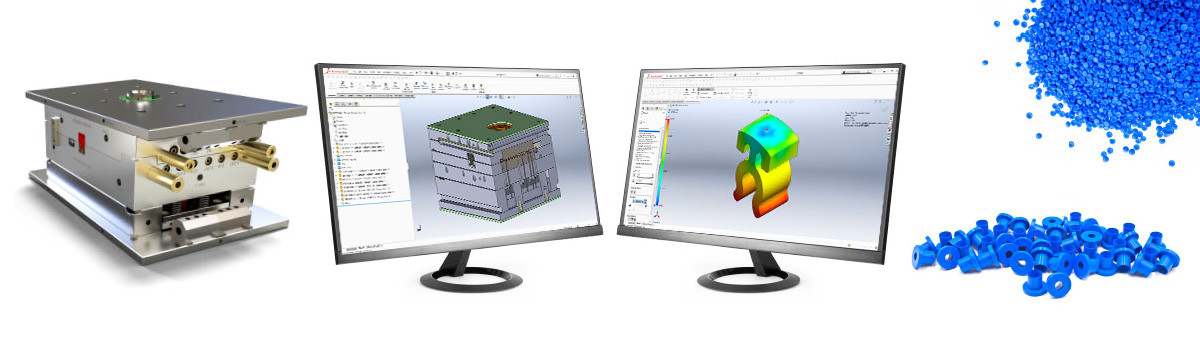
ಪ್ಲಾಸ್ಟಿಕ್ ಇಂಜೆಕ್ಷನ್ ಮೋಲ್ಡಿಂಗ್ ಭಾಗಗಳನ್ನು ಪ್ರಕ್ರಿಯೆಗೊಳಿಸಲು ಅಚ್ಚುಗಳನ್ನು ಬಳಸುವಾಗ ದೋಷಗಳು ಸಾಮಾನ್ಯವಾಗಿದೆ ಮತ್ತು ಇದು ಸಂಸ್ಕರಣೆಯ ದಕ್ಷತೆಯ ಮೇಲೆ ಹೆಚ್ಚಾಗಿ ಪರಿಣಾಮ ಬೀರುತ್ತದೆ. ಕೆಳಗಿನವುಗಳು ಸಾಮಾನ್ಯ ಮೋಲ್ಡಿಂಗ್ ದೋಷಗಳು ಮತ್ತು ಪ್ಲಾಸ್ಟಿಕ್ ಇಂಜೆಕ್ಷನ್ ಅಚ್ಚು ಭಾಗಗಳಿಗೆ ಪರಿಹಾರಗಳಾಗಿವೆ.
ಸಣ್ಣ ಹೊಡೆತಗಳು
ಅಚ್ಚುಗಳು ಸಂಪೂರ್ಣವಾಗಿ ತುಂಬಿಲ್ಲದ ಕಾರಣ ಅಪೂರ್ಣವಾಗಿರುವ ಉತ್ಪನ್ನಗಳನ್ನು ಸಣ್ಣ ಹೊಡೆತಗಳು ಉಲ್ಲೇಖಿಸುತ್ತವೆ.
ಈ ದೋಷವು ಸಾಮಾನ್ಯವಾಗಿ ಗೇಟ್ನಿಂದ ದೂರವಿರುವ ಸ್ಥಳದಲ್ಲಿ ಅಥವಾ ಅಚ್ಚಿನ ಮೇಲಿನ ಕಿರಿದಾದ ಪ್ರದೇಶಗಳ ಮೂಲಕ ಮಾತ್ರ ತಲುಪಬಹುದಾದ ಭಾಗಗಳಲ್ಲಿ ಕಾಣಿಸಿಕೊಳ್ಳುತ್ತದೆ ಏಕೆಂದರೆ ಕಿರಿದಾದ ಪ್ರದೇಶಗಳು ಕರಗುವ ಹರಿವಿನ ಮೇಲೆ ಪರಿಣಾಮ ಬೀರಬಹುದು.
ಶಾರ್ಟ್ ಶಾಟ್ ಮೈಕ್ರೋ ಫ್ಲೋ ಮಾರ್ಕ್ಗಳಿಗೆ ಕಾರಣವಾಗಬಹುದು ಅಥವಾ ಉತ್ಪನ್ನದ ಹೆಚ್ಚಿನ ಭಾಗವು ಸ್ಪಷ್ಟವಾಗಿ ಕಾಣೆಯಾಗಬಹುದು.
ಕಾಸ್:
ಸಣ್ಣ ಹೊಡೆತಗಳಿಗೆ ಕಾರಣಗಳು ಸೇರಿವೆ:
ಅಚ್ಚುಗೆ ಚುಚ್ಚಲಾದ ಕಚ್ಚಾ ವಸ್ತುವು ಸಾಕಾಗುವುದಿಲ್ಲ.
ಕರಗುವಿಕೆಯ ಪ್ರತಿರೋಧವು ದೊಡ್ಡದಾಗಿದೆ, ಇದರ ಪರಿಣಾಮವಾಗಿ ಅಚ್ಚು ಸಂಪೂರ್ಣವಾಗಿ ತುಂಬಲು ಸಾಧ್ಯವಿಲ್ಲ.
ಅಚ್ಚಿನ ಗಾಳಿಯು ಕಳಪೆಯಾಗಿದೆ ಮತ್ತು ಕರಗುವಿಕೆಯನ್ನು ನಿರ್ಬಂಧಿಸುವ ಗುಳ್ಳೆಕಟ್ಟುವಿಕೆಗೆ ಕಾರಣವಾಗುತ್ತದೆ, ಕರಗುವಿಕೆಯು ಅಚ್ಚಿನ ಕೆಲವು ಪ್ರದೇಶಗಳಿಗೆ ಹರಿಯುವುದಿಲ್ಲ.
ಬರ್ರ್ಸ್
ಅಚ್ಚು ಕುಳಿಯಿಂದ ಉತ್ಪನ್ನಕ್ಕೆ ಹೊರತೆಗೆಯಲಾದ ಹೆಚ್ಚುವರಿ ಕಚ್ಚಾ ವಸ್ತುಗಳ ಅಂಟಿಕೊಳ್ಳುವಿಕೆಯಿಂದ ಬರ್ರ್ಸ್ ಉತ್ಪತ್ತಿಯಾಗುತ್ತದೆ.
ಈ ದೋಷವು ಉತ್ಪನ್ನದ ಅಂಚುಗಳ ಮೇಲೆ ಅಥವಾ ಅಚ್ಚಿನ ಪ್ರತಿ ಸಂಯೋಜನೆಯ ಭಾಗವಾಗಿರುತ್ತದೆ. ಕಚ್ಚಾ ವಸ್ತುವು ಅಚ್ಚಿನಿಂದ ಉಕ್ಕಿ ಹರಿಯಬಹುದು, ಅಥವಾ ಚಲಿಸುವ ಮತ್ತು ಫಿಕ್ಸಿಂಗ್ ಅಚ್ಚುಗಳ ಬಂಧದ ಸ್ಥಳಗಳು.
ಹೈಡ್ರಾಲಿಕ್ ಒತ್ತಡ ಅಥವಾ ಕೋನೀಯ ಪಿನ್ ಕಾರಣದಿಂದಾಗಿ ಅಚ್ಚು ಕೋರ್ನಲ್ಲಿ ಬರ್ರ್ಸ್ ಅನ್ನು ಸಹ ಕಾಣಬಹುದು.
ಬರ್ರ್ಸ್ ತೀವ್ರತೆಯು ಬದಲಾಗುತ್ತದೆ, ಕೆಲವೊಮ್ಮೆ ತೆಳುವಾದ, ಕೆಲವೊಮ್ಮೆ ದಪ್ಪವಾಗಿರುತ್ತದೆ.
ಕಾಸ್:
ಬರ್ರ್ಸ್ಗೆ ಕಾರಣಗಳು ಸೇರಿವೆ:
ಕ್ಲ್ಯಾಂಪ್ ಮಾಡುವ ಅಚ್ಚು ಮೇಲ್ಮೈ ಹಾನಿಗೊಳಗಾಗುತ್ತದೆ ಅಥವಾ ಹೆಚ್ಚು ಧರಿಸಲಾಗುತ್ತದೆ.
ಚಲಿಸುವ ಅಚ್ಚು ಮತ್ತು ಫಿಕ್ಸಿಂಗ್ ಅಚ್ಚು ಲಾಕ್ ಮಾಡಿದಾಗ ಅವು ಡಿಸ್-ಲೊಕೇಟೆಡ್ ಆಗಿರುತ್ತವೆ.
ಅಚ್ಚಿನಲ್ಲಿ ಕಚ್ಚಾ ವಸ್ತುಗಳ ಒತ್ತಡವು ಅಚ್ಚು ಕ್ಲ್ಯಾಂಪ್ ಮಾಡುವ ಬಲಕ್ಕಿಂತ ಹೆಚ್ಚಾಗಿರುತ್ತದೆ.
ಮೇಲೆ ತಿಳಿಸಿದ ಮೂರನೇ ಸ್ಥಿತಿಯು ವಿವಿಧ ಕಾರಣಗಳಿಂದ ಉಂಟಾಗುತ್ತದೆ. ಕೆಳಗಿನ ಸಂದರ್ಭಗಳಲ್ಲಿ, ಕಚ್ಚಾ ವಸ್ತುಗಳ ಒತ್ತಡವು ಅಚ್ಚು ಕ್ಲ್ಯಾಂಪ್ ಮಾಡುವ ಬಲಕ್ಕಿಂತ ಹೆಚ್ಚಾಗಿರುತ್ತದೆ.
ಇಂಜೆಕ್ಷನ್ ಅಚ್ಚಿನ ಮೊದಲ ಹಂತದಲ್ಲಿ (ಅಚ್ಚು ತುಂಬುವ ಹಂತ), ಹೆಚ್ಚು ಕಚ್ಚಾ ವಸ್ತುಗಳನ್ನು ತುಂಬಿಸಲಾಗುತ್ತದೆ, ಇದು ಅಚ್ಚಿನೊಳಗೆ ಒತ್ತಡವನ್ನು ಹೆಚ್ಚಿಸುತ್ತದೆ.
ಅಚ್ಚು ತುಂಬುವ ಪ್ರಕ್ರಿಯೆಯಲ್ಲಿ, ಕರಗುವ ಹರಿವಿನ ದೊಡ್ಡ ಪ್ರತಿರೋಧವು ಅಚ್ಚು ಒಳಗೆ ಒತ್ತಡವನ್ನು ಹೆಚ್ಚಿಸುತ್ತದೆ.
ಒತ್ತಡ ಹಿಡಿದಿಟ್ಟುಕೊಳ್ಳುವ ಹಂತದಲ್ಲಿ ಅಚ್ಚು ಕುಹರದ ಒತ್ತಡವು ತುಂಬಾ ಹೆಚ್ಚಾಗಿರುತ್ತದೆ.
ಮೋಲ್ಡ್ ಕ್ಲ್ಯಾಂಪ್ ಮಾಡುವ ಬಲವು ಸಾಕಾಗುವುದಿಲ್ಲ.
ಅವನತಿ
ವಿಭಜನೆಯು ಅನೇಕ ಫಲಿತಾಂಶಗಳಿಗೆ ಕಾರಣವಾಗಬಹುದು. ಸಮಸ್ಯೆಯ ವ್ಯಾಪ್ತಿ ಮತ್ತು ತೀವ್ರತೆಯು ಸಹ ಬದಲಾಗುತ್ತದೆ. ಅತ್ಯಂತ ಗಂಭೀರವಾದ ಪ್ರಕರಣದಲ್ಲಿ, ಇದು ಉತ್ಪನ್ನದ ಸಂಪೂರ್ಣ ಬಣ್ಣ ಮತ್ತು ಕಳಪೆ ಯಾಂತ್ರಿಕ ಗುಣಲಕ್ಷಣಗಳಿಗೆ ಕಾರಣವಾಗಬಹುದು. ಸ್ಥಳೀಯ ಅವನತಿಯು ಕಪ್ಪು ಪಟ್ಟಿಗಳು ಅಥವಾ ಕಲೆಗಳನ್ನು ಮಾತ್ರ ಉಂಟುಮಾಡುತ್ತದೆ.
ಕಾಸ್:
ಕಚ್ಚಾ ವಸ್ತುವು ಹಾನಿಗೊಳಗಾಗುವುದರಿಂದ ಅವನತಿ ಉಂಟಾಗುತ್ತದೆ. ಪ್ಲಾಸ್ಟಿಕ್ಗಳನ್ನು ರೂಪಿಸುವ ದೀರ್ಘ ಸರಪಳಿ ಅಣುಗಳು ಅತಿಯಾದ ಶಾಖ ಅಥವಾ ಅತಿಯಾದ ಬರಿಯ ಒತ್ತಡದ ಕ್ರಿಯೆಯ ಅಡಿಯಲ್ಲಿ ಕೊಳೆಯುತ್ತವೆ. ಅಣುಗಳ ವಿಭಜನೆಯ ಸಮಯದಲ್ಲಿ, ಬಾಷ್ಪಶೀಲ ಅನಿಲವು ಅವನತಿ ಪ್ರಕ್ರಿಯೆಯನ್ನು ವೇಗಗೊಳಿಸುತ್ತದೆ, ಇದು ಕಚ್ಚಾ ವಸ್ತುಗಳ ಡಿ-ಬಣ್ಣವನ್ನು ಉಂಟುಮಾಡುತ್ತದೆ. ದೊಡ್ಡ ಪ್ರಮಾಣದ ಅಣುಗಳ ವಿಭಜನೆಯು ಅಂತಿಮವಾಗಿ ಕಚ್ಚಾ ವಸ್ತುಗಳ ವಿಷಯವನ್ನು ಒಡೆಯುತ್ತದೆ ಮತ್ತು ಯಾಂತ್ರಿಕ ಗುಣಲಕ್ಷಣಗಳ ಮೇಲೆ ನಕಾರಾತ್ಮಕ ಪ್ರಭಾವವನ್ನು ಉಂಟುಮಾಡುತ್ತದೆ.
ವಸ್ತುವಿನ ಬ್ಯಾರೆಲ್ನ ಅಸಮ ತಾಪಮಾನದಿಂದ ಸ್ಥಳೀಯ ಅವನತಿ ಉಂಟಾಗಬಹುದು.
ಕೆಳಗಿನ ಸಂದರ್ಭಗಳಲ್ಲಿ ಅವನತಿ ಸಂಭವಿಸಬಹುದು:
ಕಚ್ಚಾ ವಸ್ತುವನ್ನು ಮೆಟೀರಿಯಲ್ ಬ್ಯಾರೆಲ್ ಅಥವಾ ಹಾಟ್ ರನ್ನರ್ ವ್ಯವಸ್ಥೆಯಲ್ಲಿ ಹೆಚ್ಚು ಬಿಸಿ ಮಾಡಲಾಗುತ್ತಿದೆ.
ಕಚ್ಚಾ ವಸ್ತುವು ಬ್ಯಾರೆಲ್ನಲ್ಲಿ ಹೆಚ್ಚು ಕಾಲ ಉಳಿಯುತ್ತದೆ.
ಇಂಜೆಕ್ಷನ್ ಮೋಲ್ಡಿಂಗ್ ಪ್ರಕ್ರಿಯೆಯಲ್ಲಿ, ಕಚ್ಚಾ ವಸ್ತುಗಳ ಮೇಲೆ ಹೇರಿದ ಬರಿಯ ಒತ್ತಡವು ತುಂಬಾ ದೊಡ್ಡದಾಗಿದೆ. ನಳಿಕೆಗಳು ನಿರ್ಬಂಧಿಸಲ್ಪಟ್ಟಿದ್ದರೆ, ಅಥವಾ ಗೇಟ್ಗಳು ಮತ್ತು ರನ್ನರ್ ತುಂಬಾ ಕಿರಿದಾಗಿದ್ದರೆ, ಅದು ಬರಿಯ ಒತ್ತಡವನ್ನು ಹೆಚ್ಚಿಸುತ್ತದೆ.
ವಿರೂಪ
ಸಾಮಾನ್ಯ ಸಂದರ್ಭಗಳಲ್ಲಿ, ಉತ್ಪನ್ನಗಳ ಆಕಾರಗಳು ಅಚ್ಚುಗಳಿಗೆ ಅನುಗುಣವಾಗಿರಬೇಕು. ವಿರೂಪತೆಯು ಉತ್ಪನ್ನಗಳ ವಿರೂಪತೆಯನ್ನು ಸೂಚಿಸುತ್ತದೆ.
ಪರಿಸ್ಥಿತಿಯು ಹದಗೆಟ್ಟಾಗ, ಅಚ್ಚಿನಿಂದ ಹೊರಹಾಕಲ್ಪಟ್ಟಾಗ ಉತ್ಪನ್ನಗಳು ಸಂಪೂರ್ಣವಾಗಿ ವಿರೂಪಗೊಳ್ಳುತ್ತವೆ. ಪರಿಸ್ಥಿತಿಯು ಗಂಭೀರವಾಗಿಲ್ಲದಿದ್ದಾಗ, ಉತ್ಪನ್ನದ ಆಕಾರವು ಸಣ್ಣ ಅಕ್ರಮಗಳು ಕಾಣಿಸಿಕೊಳ್ಳುತ್ತವೆ.
ಉದ್ದವಾದ ಆದರೆ ಬೆಂಬಲದ ಅಂಚುಗಳು ಅಥವಾ ದೊಡ್ಡ ವಿಮಾನಗಳು ವಿರೂಪಕ್ಕೆ ಹೆಚ್ಚು ಒಳಗಾಗುವ ಪ್ರದೇಶಗಳಾಗಿವೆ.
ಕಾಸ್:
ವಿರೂಪಕ್ಕೆ ಕಾರಣಗಳು:
ಅಚ್ಚು ಬಿಡುಗಡೆಯಾದಾಗ ತಾಪಮಾನವು ತುಂಬಾ ಹೆಚ್ಚಾಗಿರುತ್ತದೆ.
ದಪ್ಪ ಮತ್ತು ತೆಳ್ಳಗಿನ ಪ್ರದೇಶಗಳಲ್ಲಿ ತಂಪಾಗಿಸುವ ಸಮಯವು ವಿಭಿನ್ನವಾಗಿರುತ್ತದೆ, ಅಥವಾ ಅಚ್ಚು ಚಲಿಸುವಲ್ಲಿ ಮತ್ತು ಅಚ್ಚು ಫಿಕ್ಸಿಂಗ್ನಲ್ಲಿನ ಅಚ್ಚು ತಾಪಮಾನ ವ್ಯತ್ಯಾಸದಿಂದಾಗಿ, ಉತ್ಪನ್ನಗಳ ಒಳಗೆ ಕುಗ್ಗುವಿಕೆ ವಿಭಿನ್ನವಾಗಿರುತ್ತದೆ.
ಭರ್ತಿ ಮಾಡುವಾಗ ಅಚ್ಚು ಹರಿವು ಸುಗಮವಾಗಿರುವುದಿಲ್ಲ ("ಫ್ರೀಜಿಂಗ್ ಓರಿಯಂಟೇಶನ್" ಎಂದು ಕರೆಯಲ್ಪಡುತ್ತದೆ) ಅಥವಾ ಒತ್ತಡ ಹಿಡಿದಿಟ್ಟುಕೊಳ್ಳುವ ಹಂತದಲ್ಲಿ ಅಚ್ಚು ಕುಳಿಯೊಳಗಿನ ಒತ್ತಡವು ತುಂಬಾ ಹೆಚ್ಚಾಗಿರುತ್ತದೆ.
ಕಲ್ಮಶಗಳು
ಕಲ್ಮಶಗಳು ಸಾಮಾನ್ಯವಾಗಿ ವಿವಿಧ ಬಣ್ಣಗಳು, ತೇಪೆಗಳು ಅಥವಾ ಪಟ್ಟೆಗಳಲ್ಲಿ ಕಲೆಗಳ ರೂಪದಲ್ಲಿ ಕಾಣಿಸಿಕೊಳ್ಳುತ್ತವೆ. ಅತ್ಯಂತ ಸಾಮಾನ್ಯವಾದದ್ದು ಕಪ್ಪು ಚುಕ್ಕೆ.
ಕಲ್ಮಶಗಳು ಕೇವಲ ಸಣ್ಣ ಕಲೆಗಳಾಗಿರಬಹುದು, ಆದರೆ ಇದು ಗಂಭೀರವಾದಾಗ ಸ್ಪಷ್ಟವಾದ ಪಟ್ಟೆಗಳು ಅಥವಾ ಡಿ-ಬಣ್ಣದ ದೊಡ್ಡ ಭಾಗವಾಗಿರಬಹುದು.
ಕಾಸ್:
ಕಲ್ಮಶಗಳು ಕಚ್ಚಾ ವಸ್ತುಗಳೊಂದಿಗೆ ಮಿಶ್ರಣದಿಂದ ಉಂಟಾಗುತ್ತವೆ, ಅವುಗಳೆಂದರೆ:
ಬ್ಯಾರೆಲ್ಗಳಿಗೆ ಸಾಗಿಸಿದಾಗ ಕಚ್ಚಾ ವಸ್ತುವನ್ನು ಸಂಡ್ರೀಸ್ಗಳೊಂದಿಗೆ ಬೆರೆಸಲಾಗುತ್ತದೆ.
ಕಚ್ಚಾ ವಸ್ತುಗಳ ವಿಘಟನೆಯು ಯಾವುದೇ ಕತ್ತರಿಸುವ ಕಾರ್ಯವಿಧಾನಗಳಿಂದ ಬೀಳಬಹುದು ಮತ್ತು ಯಂತ್ರದ ಬೊಲ್ಟ್ಗಳು, ಡ್ರೈಯಿಂಗ್ ಡ್ರಮ್ನ ಒಳ ಗೋಡೆ, ಕೀಲುಗಳು / ನಳಿಕೆಗಳಂತಹ ಕಚ್ಚಾ ವಸ್ತುಗಳಿಗೆ ಮಿಶ್ರಣವಾಗಬಹುದು.
ವಿಮೋಚನೆ
ಲ್ಯಾಮಿನೇಶನ್ ಉತ್ಪನ್ನಗಳ ಮೇಲ್ಮೈಯಲ್ಲಿ "ಚರ್ಮದ ಪರಿಣಾಮವನ್ನು" ಉಂಟುಮಾಡುತ್ತದೆ, ಇದು ಉತ್ಪನ್ನಗಳ ಮೇಲ್ಮೈ ಮತ್ತು ಇತರ ಕಚ್ಚಾ ವಸ್ತುಗಳ ಗುಣಲಕ್ಷಣಗಳು ಮತ್ತು ಟೆಕಶ್ಚರ್ಗಳಲ್ಲಿನ ವ್ಯತ್ಯಾಸದಿಂದ ಉಂಟಾಗುತ್ತದೆ ಮತ್ತು ಇದು ತೆಗೆದುಹಾಕಬಹುದಾದ ಸಿಪ್ಪೆಸುಲಿಯುವ ಚರ್ಮವನ್ನು ರೂಪಿಸುತ್ತದೆ.
ಲ್ಯಾಮಿನೇಶನ್ ಗಂಭೀರವಾದಾಗ, ಇಡೀ ಅಡ್ಡ ವಿಭಾಗದ ಪ್ರದೇಶವು ವಿವಿಧ ಪದರಗಳಿಂದ ಮಾಡಲ್ಪಟ್ಟಿದೆ ಮತ್ತು ಒಟ್ಟಿಗೆ ಕರಗಿಲ್ಲ. ದೋಷಗಳು ಕಡಿಮೆ ಸ್ಪಷ್ಟವಾಗಿದ್ದಾಗ, ಉತ್ಪನ್ನಗಳ ನೋಟವು ಅವಶ್ಯಕತೆಗಳನ್ನು ಪೂರೈಸಬಹುದು, ಆದರೆ ಉತ್ಪನ್ನಗಳ ಯಾಂತ್ರಿಕ ಗುಣಲಕ್ಷಣಗಳನ್ನು ಮುರಿಯುತ್ತದೆ.
ಕಾಸ್:
ಲ್ಯಾಮಿನೇಶನ್ಗೆ ಎರಡು ಮುಖ್ಯ ಕಾರಣಗಳಿವೆ. ಮೊದಲನೆಯದು ಎರಡು ವಿಭಿನ್ನ ರೀತಿಯ ಕಚ್ಚಾ ಸಾಮಗ್ರಿಗಳು ತಪ್ಪಾಗಿ ಒಟ್ಟಿಗೆ ಮಿಶ್ರಣಗೊಂಡಾಗ. ಒತ್ತಡದ ಅಡಿಯಲ್ಲಿ ಒಂದೇ ಸಮಯದಲ್ಲಿ ಎರಡು ಕಚ್ಚಾ ವಸ್ತುಗಳನ್ನು ಬ್ಯಾರೆಲ್ಗೆ ಸಾಗಿಸಲಾಗುತ್ತದೆ. ಆದಾಗ್ಯೂ, ಅಚ್ಚನ್ನು ತಂಪಾಗಿಸಿದಾಗ ಒಟ್ಟಿಗೆ ಕರಗಿಸಲು ಸಾಧ್ಯವಾಗದಿದ್ದಾಗ, ಉತ್ಪನ್ನಗಳನ್ನು ರೂಪಿಸಲು ವಿವಿಧ ಪದರಗಳನ್ನು ಬಲವಂತವಾಗಿ ಒತ್ತುವಂತೆ.
ಎರಡನೆಯದು: ಶೀತ ಕರಗುವಿಕೆಯು ಕಿರಿದಾದ ಗೇಟ್ ಮೂಲಕ ಹಾದುಹೋಗುವಂತೆ ಒತ್ತಾಯಿಸಿದರೆ, ಬರಿಯ ಒತ್ತಡವು ಉಂಟಾಗುತ್ತದೆ. ತುಂಬಾ ಹೆಚ್ಚಿನ ಕತ್ತರಿ ಒತ್ತಡವು ಕರಗಿದ ಪದರವನ್ನು ಮುಂಚಿತವಾಗಿ ಕರಗಿಸುತ್ತದೆ ಸಂಪೂರ್ಣವಾಗಿ ಬೆಸೆಯಲು ಸಾಧ್ಯವಿಲ್ಲ.
ಮಿಶ್ರಣದ ಅಪಾಯ:
ತಿಳಿದಿರಬೇಕಾದ ಒಂದು ವಿಷಯವೆಂದರೆ ಕೆಲವು ಕಚ್ಚಾ ವಸ್ತುಗಳನ್ನು ಒಟ್ಟಿಗೆ ಬೆರೆಸಿದಾಗ PVC ಮತ್ತು Avetal ನಂತಹ ಬಲವಾದ ರಾಸಾಯನಿಕ ಕ್ರಿಯೆಗೆ ಕಾರಣವಾಗುತ್ತದೆ.
ಬೆಳ್ಳಿ ರೇಖೀಯ
ಸ್ಲಿವರ್ ಲೀನಿಯರ್ ಕೇವಲ ಸ್ಥಳೀಯ ವಿದ್ಯಮಾನವಾಗಿರಬಹುದು, ಆದರೆ ಅದು ಗಂಭೀರವಾಗಿದ್ದಾಗ ಇಡೀ ಮೇಲ್ಮೈಗೆ ವಿಸ್ತರಿಸಬಹುದು.
ಸಿಲ್ವರ್ ಲೀನಿಯರ್ ಉತ್ಪನ್ನಗಳ ನೋಟವನ್ನು ಪರಿಣಾಮ ಬೀರುತ್ತದೆ ಮತ್ತು ಉತ್ಪನ್ನಗಳ ಯಾಂತ್ರಿಕ ಗುಣಲಕ್ಷಣಗಳನ್ನು ಹಾನಿಗೊಳಿಸುತ್ತದೆ.
ಕಾಸ್:
ಕೆಳಗಿನ ಎರಡು ಬಿಂದುಗಳು ಬೆಳ್ಳಿ ರೇಖಾತ್ಮಕತೆಯನ್ನು ಉಂಟುಮಾಡುತ್ತವೆ:
ಕಚ್ಚಾ ವಸ್ತುವು ತೇವವಾಗಿರುತ್ತದೆ ಮತ್ತು ಅವುಗಳಲ್ಲಿ ಕೆಲವು ಗಾಳಿಯಲ್ಲಿ ಹಬೆಯನ್ನು ಹೀರಿಕೊಳ್ಳುತ್ತವೆ. ಕಚ್ಚಾ ವಸ್ತುವು ತುಂಬಾ ತೇವವಾಗಿದ್ದರೆ, ಒತ್ತಡದ ಆವಿಯು ಹೆಚ್ಚಿನ ತಾಪಮಾನ ಮತ್ತು ಬ್ಯಾರೆಲ್ನ ಹೆಚ್ಚಿನ ಒತ್ತಡದ ಅಡಿಯಲ್ಲಿ ಉತ್ಪತ್ತಿಯಾಗಬಹುದು. ಈ ಆವಿಗಳು ಉತ್ಪನ್ನದ ಮೇಲ್ಮೈಯನ್ನು ಭೇದಿಸಿ ಬೆಳ್ಳಿ ಪಟ್ಟೆಗಳನ್ನು ರೂಪಿಸುತ್ತವೆ.
ಕರಗುವಿಕೆಯು ಉಷ್ಣ ಹಾನಿಗೊಳಗಾಗುತ್ತದೆ ಮತ್ತು ಸ್ಥಳೀಯ ಅವನತಿಯನ್ನು ಉಂಟುಮಾಡುತ್ತದೆ. ಉತ್ಪತ್ತಿಯಾಗುವ ಬಾಷ್ಪಶೀಲ ಅನಿಲವು ಅಚ್ಚಿನ ಮೇಲೆ ಮೇಲ್ಮೈಯಲ್ಲಿ ನಿರ್ಬಂಧಿಸಲ್ಪಡುತ್ತದೆ ಮತ್ತು ಉತ್ಪನ್ನಗಳ ಮೇಲ್ಮೈಯಲ್ಲಿ ಪಟ್ಟೆಗಳನ್ನು ಉಂಟುಮಾಡುತ್ತದೆ.
ಇದು ಅವನತಿಯಷ್ಟು ಕೆಟ್ಟದ್ದಲ್ಲ. ಕರಗುವ ಉಷ್ಣತೆಯು ಅಧಿಕವಾಗಿರುವವರೆಗೆ ಅಥವಾ ಪ್ಲಾಸ್ಟಿಸೇಶನ್ ಸಮಯದಲ್ಲಿ ಅದು ಬರಿಯ ಒತ್ತಡಕ್ಕೆ ಒಳಗಾಗುವವರೆಗೆ ಅಥವಾ ಅಚ್ಚಿನೊಳಗೆ ಚುಚ್ಚುವವರೆಗೆ, ಇದು ಸಂಭವಿಸಬಹುದು.
ಹೊಳಪು / ನೆರಳು
ಉತ್ಪನ್ನಗಳ ಮೇಲ್ಮೈ ಮುಕ್ತಾಯವು ಅಚ್ಚುಗಳಂತೆಯೇ ಇರಬೇಕು. ಎರಡರ ಮೇಲ್ಮೈ ಮುಕ್ತಾಯವು ವಿಭಿನ್ನವಾದಾಗ, ಹೊಳಪು/ನೆರಳು ದೋಷಗಳು ಸಂಭವಿಸಿದವು.
ದೋಷಗಳು ಸಂಭವಿಸಿದಾಗ ಮೇಲ್ಮೈ ಕತ್ತಲೆಯಾಗುತ್ತದೆ, ಮತ್ತು ಒರಟಾದ ಮೇಲ್ಮೈ ನಯವಾದ ಮತ್ತು ಹೊಳಪು ಇರುತ್ತದೆ.
ಕಾಸ್:
ಹೊಳಪು / ನೆರಳುಗೆ ಕಾರಣಗಳು ಸೇರಿವೆ:
ಕರಗುವಿಕೆಯು ಸರಾಗವಾಗಿ ಹರಿಯುತ್ತದೆ ಅಥವಾ ಅಚ್ಚು ಮೇಲ್ಮೈಯ ಉಷ್ಣತೆಯು ಕಡಿಮೆಯಾಗಿದೆ, ಇದರ ಪರಿಣಾಮವಾಗಿ ಅಚ್ಚು ಮೇಲ್ಮೈ ಮುಕ್ತಾಯವನ್ನು ವಸ್ತು ಅಚ್ಚೊತ್ತಿದಾಗ ನಕಲು ಮಾಡಲಾಗುವುದಿಲ್ಲ.
ಒತ್ತಡದ ಹಿಡಿತದ ಸಮಯದಲ್ಲಿ, ಕುಳಿಯಲ್ಲಿನ ಒತ್ತಡವು ತಂಪಾಗಿಸುವ ಪ್ರಕ್ರಿಯೆಯಲ್ಲಿ ವಸ್ತುವು ಅಚ್ಚಿನ ಮೇಲ್ಮೈಗೆ ಅಂಟಿಕೊಳ್ಳುವಂತೆ ಮಾಡಲು ಸಾಕಷ್ಟು ಹೆಚ್ಚಿಲ್ಲ, ಕುಗ್ಗುವಿಕೆ ಗುರುತುಗಳನ್ನು ಬಿಡುತ್ತದೆ.
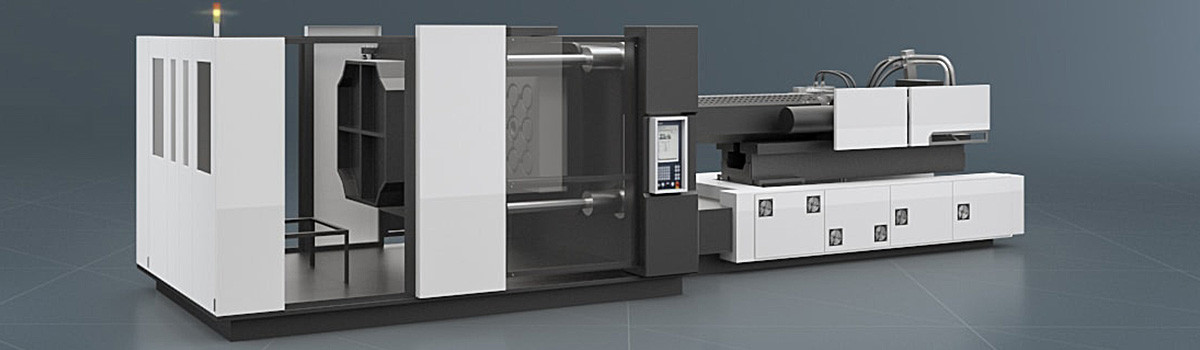
ಹರಿವಿನ ಗುರುತುಗಳು
ಉತ್ಪನ್ನಗಳ ಮೇಲ್ಮೈಯಲ್ಲಿ ಹರಿವಿನ ಗುರುತುಗಳನ್ನು ಬಹು ರೂಪಗಳಲ್ಲಿ ಕಾಣಬಹುದು. ಸಾಮಾನ್ಯವಾಗಿ, ಇದು ನೆರಳು ಪ್ರದೇಶವನ್ನು ರೂಪಿಸುತ್ತದೆ.
ಹರಿವಿನ ಗುರುತುಗಳು ಉತ್ಪನ್ನಗಳ ಮೇಲ್ಮೈಯಲ್ಲಿ ಯಾವುದೇ ಉಬ್ಬು ಅಥವಾ ಖಿನ್ನತೆಯನ್ನು ಉಂಟುಮಾಡುವುದಿಲ್ಲ, ಅದನ್ನು ಬೆರಳುಗಳಿಂದ ಅನುಭವಿಸಲಾಗುವುದಿಲ್ಲ. ಈ ದೋಷವನ್ನು ಡ್ರ್ಯಾಗ್ ಮಾರ್ಕ್ಸ್, ಘೋಸ್ಟಿಂಗ್ ಮತ್ತು ಶಾಡೋಸ್ ಎಂದೂ ಕರೆಯುತ್ತಾರೆ.
ಹರಿವಿನ ಗುರುತುಗಳು ಸ್ಪಷ್ಟವಾಗಿದ್ದಾಗ, ಅದು ಚಡಿಗಳನ್ನು ಉಂಟುಮಾಡುತ್ತದೆ ಮತ್ತು ಉತ್ಪನ್ನಗಳ ಮೇಲ್ಮೈಯಲ್ಲಿ ಗುರುತುಗಳಂತಹ ದೋಷಗಳನ್ನು ಬಿಡುತ್ತದೆ.
ಕಾಸ್:
ಹರಿವಿನ ಗುರುತುಗಳನ್ನು ಯಾವಾಗ ಕಾಣಬಹುದು:
ಕರಗುವಿಕೆಯ ಹರಿವು ಕಳಪೆಯಾಗಿದೆ ಅಥವಾ ಅಚ್ಚಿನ ಮೇಲ್ಮೈ ತಾಪಮಾನವು ಕಡಿಮೆಯಾಗಿದೆ, ಇದು ಅಚ್ಚು ತುಂಬುವ ಪ್ರಕ್ರಿಯೆಯಲ್ಲಿ ಪ್ಲಾಸ್ಟಿಕ್ನ ದೊಡ್ಡ ಹರಿವಿನ ಪ್ರತಿರೋಧವನ್ನು ಉಂಟುಮಾಡುತ್ತದೆ.
ಅಚ್ಚು ತುಂಬುವಿಕೆಯಲ್ಲಿ, ಪ್ರತಿರೋಧದೊಂದಿಗೆ ಕರಗುವ ಹರಿವು, ಡೈನ ಅಸಮ ಮೇಲ್ಮೈ, ಡೈ ಮೇಲ್ಮೈಯಲ್ಲಿ ಮುದ್ರಿಸಲಾದ ಗುರುತುಗಳು ಅಥವಾ ಮಾದರಿಗಳು ಅಥವಾ ಭರ್ತಿ ಪ್ರಕ್ರಿಯೆಯಲ್ಲಿ ಕರಗುವ ಹರಿವಿನ ದಿಕ್ಕಿನ ಬದಲಾವಣೆಯಿಂದ ಉಂಟಾಗಬಹುದು.
ಜೋಡಿಸುವ ಸಾಲು
ಅಚ್ಚು ತುಂಬುವಿಕೆಯ ಸಮಯದಲ್ಲಿ ಎರಡು ಕರಗುವ ಮುಂಭಾಗಗಳು ಭೇಟಿಯಾದಾಗ ಸೇರುವ ರೇಖೆಯನ್ನು ರಚಿಸಲಾಗುತ್ತದೆ ಮತ್ತು ಉತ್ಪನ್ನದ ಮೇಲ್ಮೈಯಲ್ಲಿ ರೇಖೆಯಂತೆ ಕಾಣಿಸುತ್ತದೆ.
ಸಂಯೋಜಕ ರೇಖೆಯು ಉತ್ಪನ್ನಗಳ ಮೇಲ್ಮೈಯಲ್ಲಿ ಬಿರುಕುಗೊಳಿಸುವ ರೇಖೆಯಂತಿದೆ, ಇದು ಪತ್ತೆಹಚ್ಚಲು ಸ್ಪಷ್ಟವಾಗಿಲ್ಲ.
ಅಚ್ಚುಗಳನ್ನು ವಿನ್ಯಾಸಗೊಳಿಸುವಾಗ, ಕೆಲವು ಗೋಚರ ಜಂಟಿ ರೇಖೆಗಳು ಅನಿವಾರ್ಯವಾಗಿವೆ. ಈ ಸಂದರ್ಭದಲ್ಲಿ, ಹಾನಿಗೊಳಗಾಗುವ ಉತ್ಪನ್ನಗಳ ಶಕ್ತಿ ಮತ್ತು ನೋಟವನ್ನು ತಡೆಯಲು ಜಂಟಿ ರೇಖೆಯನ್ನು ಸಾಧ್ಯವಾದಷ್ಟು ಕಡಿಮೆಗೊಳಿಸುತ್ತದೆ.
ಕಾಸ್:
ಕರಗುವ ಮುಂಭಾಗದ ಪೀಳಿಗೆಗೆ ಹಲವು ಕಾರಣಗಳಿವೆ. ಅತ್ಯಂತ ಸಂಭವನೀಯ ಕಾರಣವೆಂದರೆ ಅಚ್ಚು ಕೋರ್ನ ಅಂಚುಗಳ ಉದ್ದಕ್ಕೂ ಕರಗುವ ಹರಿವು ಆಗಿರಬಹುದು. ಇವೆರಡೂ ಕರಗಿದಾಗ ಅದು ಸಂಧಿ ರೇಖೆಗಳನ್ನು ಉಂಟುಮಾಡುತ್ತದೆ. ಎರಡು ಕರಗುವ ಮುಂಭಾಗದ ತಾಪಮಾನವು ಅವುಗಳನ್ನು ಯಶಸ್ವಿಯಾಗಿ ಒಟ್ಟಿಗೆ ಬೆಸೆಯಲು ಅನುಮತಿಸುವಷ್ಟು ಹೆಚ್ಚಿನದಾಗಿರಬೇಕು ಮತ್ತು ಉತ್ಪನ್ನಗಳ ಶಕ್ತಿ ಮತ್ತು ನೋಟವನ್ನು ಪರಿಣಾಮ ಬೀರುವುದಿಲ್ಲ.
ಎರಡು ಕರಗುವಿಕೆಯು ಸಂಪೂರ್ಣವಾಗಿ ಒಟ್ಟಿಗೆ ಸೇರಲು ಸಾಧ್ಯವಾಗದಿದ್ದಾಗ, ದೋಷಗಳು ಉತ್ಪತ್ತಿಯಾಗುತ್ತವೆ.
ದೋಷಗಳ ಕಾರಣಗಳು:
ಅಚ್ಚು ದಪ್ಪ ಮತ್ತು ತೆಳ್ಳಗಿನ ಭಾಗಗಳನ್ನು ಹೊಂದಿದೆ, ಮತ್ತು ಕರಗುವ ಹರಿವಿನ ವೇಗವು ವಿಭಿನ್ನವಾಗಿರುತ್ತದೆ, ಕರಗುವಿಕೆಯು ಅಚ್ಚಿನ ತೆಳುವಾದ ಭಾಗದ ಮೂಲಕ ಹರಿಯುವಾಗ, ತಾಪಮಾನವು ಕಡಿಮೆ ಇರುತ್ತದೆ.
ಪ್ರತಿ ಓಟಗಾರನ ಉದ್ದವು ವಿಭಿನ್ನವಾಗಿರುತ್ತದೆ. ಒಂಟಿ ಓಟಗಾರರು ತಣ್ಣಗಾಗಲು ಸುಲಭವಾಗುತ್ತದೆ.
ಒತ್ತಡ ಹಿಡಿದಿಟ್ಟುಕೊಳ್ಳುವ ಹಂತದಲ್ಲಿ ಕರಗುವಿಕೆಯು ಸಂಪೂರ್ಣವಾಗಿ ಬೆಸೆಯಲು ಅನುಮತಿಸಲು ಅಚ್ಚು ಕುಹರದ ಒತ್ತಡವು ಸಾಕಾಗುವುದಿಲ್ಲ.
ಉಳಿದ ಗುಳ್ಳೆಗಳು ಕರಗುವ ಮುಂಭಾಗವನ್ನು ಫ್ಯೂಸ್ ಮಾಡಲು ಸಾಧ್ಯವಾಗುವುದಿಲ್ಲ, ಅದು ಸುಡುವಿಕೆಗೆ ಕಾರಣವಾಗುತ್ತದೆ.
ಬರ್ನಿಂಗ್
ಸುಡುವಿಕೆಯು ಶಾರ್ಟ್ ಶಾಟ್ನಂತೆಯೇ ಇರುತ್ತದೆ, ಆದರೆ ಅನಿಯಮಿತ ಮರೆಯಾಗುತ್ತಿರುವ ಅಂಚುಗಳು ಮತ್ತು ಸ್ವಲ್ಪ ಸುಡುವ ವಾಸನೆಯೊಂದಿಗೆ. ಉತ್ಪನ್ನದ ಮೇಲೆ ಕಾರ್ಬನ್ ಕಪ್ಪು ಪ್ರದೇಶಗಳು ಕಾಣಿಸಿಕೊಳ್ಳುತ್ತವೆ, ಸ್ಥಿತಿಯು ಗಂಭೀರವಾದಾಗ, ಪ್ಲಾಸ್ಟಿಕ್ ಸುಡುವಿಕೆಯ ವಾಸನೆಯೊಂದಿಗೆ ಇರುತ್ತದೆ.
ದೋಷಗಳನ್ನು ನಿರ್ಮೂಲನೆ ಮಾಡದಿದ್ದರೆ, ಹೆಚ್ಚಾಗಿ ಅಚ್ಚಿನ ಮೇಲೆ ಕಪ್ಪು ಶೇಖರಣೆ ಇರುತ್ತದೆ. ಸುಡುವಿಕೆಯಿಂದ ಉತ್ಪತ್ತಿಯಾಗುವ ಅನಿಲ ಅಥವಾ ತೈಲ ಪದಾರ್ಥಗಳನ್ನು ತಕ್ಷಣವೇ ಪರಿಶೀಲಿಸದಿದ್ದರೆ, ಅವು ಗಾಳಿಯ ರಂಧ್ರಗಳನ್ನು ನಿರ್ಬಂಧಿಸಬಹುದು. ಸುಡುವಿಕೆಯು ಸಾಮಾನ್ಯವಾಗಿ ಮಾರ್ಗಗಳ ಕೊನೆಯಲ್ಲಿ ಕಂಡುಬರುತ್ತದೆ.
ಕಾಸ್:
ಆಂತರಿಕ ದಹನ ಪರಿಣಾಮದಿಂದ ಬರ್ನಿಂಗ್ ಉಂಟಾಗುತ್ತದೆ. ಕಡಿಮೆ ಸಮಯದಲ್ಲಿ ಗಾಳಿಯಲ್ಲಿನ ಒತ್ತಡವು ತೀವ್ರವಾಗಿ ಹೆಚ್ಚಾದಾಗ, ತಾಪಮಾನವು ಹೆಚ್ಚಾಗುತ್ತದೆ ಮತ್ತು ಸುಡುವಿಕೆಗೆ ಕಾರಣವಾಗುತ್ತದೆ. ಸಂಗ್ರಹಿಸಿದ ಮಾಹಿತಿಯ ಪ್ರಕಾರ, ಇಂಜೆಕ್ಷನ್ ಮೋಲ್ಡಿಂಗ್ ಪ್ರಕ್ರಿಯೆಯಲ್ಲಿ ಆಂತರಿಕ ದಹನ ಪರಿಣಾಮವು 600 ಡಿಗ್ರಿಗಳವರೆಗೆ ಹೆಚ್ಚಿನ ತಾಪಮಾನವನ್ನು ಉಂಟುಮಾಡಬಹುದು.
ಯಾವಾಗ ಬರ್ನಿಂಗ್ ಅನ್ನು ಉತ್ಪಾದಿಸಬಹುದು:
ಅಚ್ಚು ತುಂಬುವಿಕೆಯ ವೇಗವು ವೇಗವಾಗಿರುತ್ತದೆ ಆದ್ದರಿಂದ ಗಾಳಿಯನ್ನು ಅಚ್ಚು ಕುಹರದಿಂದ ಅನೂರ್ಜಿತಗೊಳಿಸಲಾಗುವುದಿಲ್ಲ ಮತ್ತು ಒಳಬರುವ ಪ್ಲಾಸ್ಟಿಕ್ನ ಬ್ಲಾಕ್ನಿಂದ ಗಾಳಿಯ ಗುಳ್ಳೆಗಳನ್ನು ಉತ್ಪಾದಿಸುತ್ತದೆ ಮತ್ತು ಸಂಕುಚಿತಗೊಂಡ ನಂತರ ಆಂತರಿಕ ದಹನ ಪರಿಣಾಮಕ್ಕೆ ಕಾರಣವಾಗುತ್ತದೆ.
ಗಾಳಿಯ ರಂಧ್ರಗಳನ್ನು ನಿರ್ಬಂಧಿಸಲಾಗಿದೆ ಅಥವಾ ವಾತಾಯನವು ಸುಗಮವಾಗಿರುವುದಿಲ್ಲ.
ಅಚ್ಚಿನಲ್ಲಿರುವ ಗಾಳಿಯನ್ನು ಗಾಳಿಯ ರಂಧ್ರಗಳಿಂದ ಹೊರಹಾಕಬೇಕು. ವಾತಾಯನವು ಸ್ಥಾನ, ಸಂಖ್ಯೆ, ಗಾತ್ರ ಅಥವಾ ಕಾರ್ಯಗಳಿಂದ ಪ್ರಭಾವಿತವಾಗಿದ್ದರೆ, ಗಾಳಿಯು ಅಚ್ಚಿನಲ್ಲಿ ಉಳಿಯುತ್ತದೆ ಮತ್ತು ಸುಡುವಿಕೆಗೆ ಕಾರಣವಾಗುತ್ತದೆ. ದೊಡ್ಡ ಅಚ್ಚು ಕ್ಲ್ಯಾಂಪ್ ಮಾಡುವ ಬಲವು ಕಳಪೆ ವಾತಾಯನಕ್ಕೆ ಕಾರಣವಾಗುತ್ತದೆ.
ಕುಗ್ಗುವಿಕೆ
ಕುಗ್ಗುವಿಕೆ ಉತ್ಪನ್ನಗಳ ಮೇಲ್ಮೈಯಲ್ಲಿ ಸ್ವಲ್ಪ ಟೊಳ್ಳುಗಳನ್ನು ಸೂಚಿಸುತ್ತದೆ.
ದೋಷಗಳು ಸ್ವಲ್ಪಮಟ್ಟಿಗೆ ಇದ್ದಾಗ, ಉತ್ಪನ್ನಗಳ ಮೇಲ್ಮೈ ಅಸಮವಾಗಿರುತ್ತದೆ. ಇದು ಗಂಭೀರವಾದಾಗ, ಉತ್ಪನ್ನಗಳ ದೊಡ್ಡ ಪ್ರದೇಶವು ಕುಸಿಯುತ್ತದೆ. ಕಮಾನುಗಳು, ಹಿಡಿಕೆಗಳು ಮತ್ತು ಮುಂಚಾಚಿರುವಿಕೆಗಳೊಂದಿಗಿನ ಉತ್ಪನ್ನಗಳು ಸಾಮಾನ್ಯವಾಗಿ ಕುಗ್ಗುವಿಕೆ ದೋಷಗಳಿಂದ ಬಳಲುತ್ತವೆ.
ಕಾಸ್:
ತಂಪಾಗಿಸುವ ಸಮಯದಲ್ಲಿ ಕಚ್ಚಾ ವಸ್ತುಗಳ ದೊಡ್ಡ-ಪ್ರದೇಶದ ಕುಗ್ಗುವಿಕೆಯಿಂದ ಕುಗ್ಗುವಿಕೆ ಉಂಟಾಗುತ್ತದೆ.
ಉತ್ಪನ್ನಗಳ ದಪ್ಪ ಪ್ರದೇಶದಲ್ಲಿ (ಕಮಾನಿನಂತಹವು), ವಸ್ತುವಿನ ಕೋರ್ ಸಮಶೀತೋಷ್ಣವು ಕಡಿಮೆಯಾಗಿದೆ, ಆದ್ದರಿಂದ ಕುಗ್ಗುವಿಕೆ ಮೇಲ್ಮೈಗಿಂತ ನಂತರ ಸಂಭವಿಸುತ್ತದೆ, ಇದು ಕಚ್ಚಾ ವಸ್ತುವಿನೊಳಗೆ ಸಂಕೋಚನ ಬಲವನ್ನು ಉಂಟುಮಾಡುತ್ತದೆ ಮತ್ತು ಹೊರಭಾಗವನ್ನು ಆಂತರಿಕ ಖಿನ್ನತೆಗೆ ಎಳೆಯುತ್ತದೆ. ಕುಗ್ಗುವಿಕೆಯನ್ನು ಉತ್ಪಾದಿಸಲು.
ಕೆಳಗಿನ ಸಂದರ್ಭಗಳಲ್ಲಿ ಕುಗ್ಗುವಿಕೆಗಳು ಸಂಭವಿಸುತ್ತವೆ:
ಅಚ್ಚು ಕುಳಿಯಲ್ಲಿನ ಒತ್ತಡವು ತಂಪಾಗಿಸುವ ಪ್ರಕ್ರಿಯೆಯಲ್ಲಿ ಕಚ್ಚಾ ವಸ್ತುಗಳ ಕುಗ್ಗುವಿಕೆಯಿಂದ ಉತ್ಪತ್ತಿಯಾಗುವ ಬಲಕ್ಕಿಂತ ಕಡಿಮೆಯಾಗಿದೆ.
ತಂಪಾಗಿಸುವ ಪ್ರಕ್ರಿಯೆಯಲ್ಲಿ ಅಚ್ಚು ಕುಹರದ ಸಾಕಷ್ಟು ಒತ್ತಡದ ಸಮಯ, ಇದರ ಪರಿಣಾಮವಾಗಿ ಕಚ್ಚಾ ವಸ್ತುವು ಗೇಟ್ನಿಂದ ಕುಳಿಯಿಂದ ಹೊರಬರುತ್ತದೆ.
ಅತಿಯಾದ ಕಚ್ಚಾ ವಸ್ತುವನ್ನು ಚುಚ್ಚುವ ಮೊದಲು ತಿರುಪು ಸಂಪೂರ್ಣವಾಗಿ ಹಿಂತೆಗೆದುಕೊಳ್ಳಲ್ಪಟ್ಟಿರುವುದರಿಂದ ಕಚ್ಚಾ ವಸ್ತುವು ಮೋಲ್ಡಿಂಗ್ ಮತ್ತು ಒತ್ತಡವನ್ನು ಹಿಡಿದಿಟ್ಟುಕೊಳ್ಳುವ ಹಂತದಲ್ಲಿ ಸಾಕಷ್ಟು ಬಫರಿಂಗ್ ಸಾಮರ್ಥ್ಯವನ್ನು ಹೊಂದಿರುವುದಿಲ್ಲ.
ಗೇಟ್ಗಳು ಮತ್ತು ಓಟಗಾರರ ಅಡ್ಡ ವಿಭಾಗದ ಪ್ರದೇಶಗಳು ಉತ್ಪನ್ನಗಳ ದಪ್ಪಕ್ಕಿಂತ ಚಿಕ್ಕದಾಗಿದೆ, ಅಂದರೆ ಉತ್ಪನ್ನಗಳನ್ನು ಹೊರತೆಗೆಯುವ ಪ್ರಕ್ರಿಯೆಯ ಮೊದಲು ಗೇಟ್ಗಳು ಈಗಾಗಲೇ ಫ್ರೀಜ್ ಆಗಿವೆ.
ಗುಳ್ಳೆಗಳು
ನಿರ್ವಾತ ಗುಳ್ಳೆಗಳನ್ನು ಗಾಳಿಯ ಗುಳ್ಳೆಗಳ ರೂಪದಲ್ಲಿ ಪ್ರಸ್ತುತಪಡಿಸಲಾಗುತ್ತದೆ, ಇದು ಪಾರದರ್ಶಕ ಉತ್ಪನ್ನಗಳಲ್ಲಿ ಸುಲಭವಾಗಿ ಕಂಡುಬರುತ್ತದೆ. ಅಪಾರದರ್ಶಕ ಉತ್ಪನ್ನಗಳ ಅಡ್ಡ ವಿಭಾಗದಲ್ಲಿಯೂ ಸಹ ಇದನ್ನು ಕಾಣಬಹುದು.
ಕಾಸ್:
ಗಾಳಿಯ ಗುಳ್ಳೆಗಳು ಉತ್ಪನ್ನಗಳ ನಿರ್ವಾತ ಭಾಗವಾಗಿದ್ದು, ತಂಪಾಗಿಸುವ ಪ್ರಕ್ರಿಯೆಯಲ್ಲಿ ಕಚ್ಚಾ ವಸ್ತುವು ಕುಗ್ಗಿದಾಗ ಉತ್ಪತ್ತಿಯಾಗುತ್ತದೆ.
ಕುಗ್ಗುವಿಕೆಯಂತೆಯೇ, ಕಚ್ಚಾ ವಸ್ತುಗಳ ಒಳಭಾಗವು ಸಂಕೋಚನ ಶಕ್ತಿಯನ್ನು ಉತ್ಪಾದಿಸುತ್ತದೆ. ವ್ಯತ್ಯಾಸವೆಂದರೆ ಗುಳ್ಳೆಗಳು ರೂಪುಗೊಂಡಾಗ ಉತ್ಪನ್ನಗಳ ಹೊರ ನೋಟವು ಘನೀಕರಿಸಲ್ಪಟ್ಟಿದೆ ಮತ್ತು ಯಾವುದೇ ಕುಸಿತವಿಲ್ಲ, ಆದ್ದರಿಂದ ಟೊಳ್ಳಾದ ಗುಳ್ಳೆಗಳು ಉತ್ಪತ್ತಿಯಾಗುತ್ತವೆ.
ಗುಳ್ಳೆಗಳ ಕಾರಣಗಳು ಕಡಿತದಂತೆಯೇ ಇರುತ್ತವೆ, ಅವುಗಳೆಂದರೆ:
ಅಸಮರ್ಥ ಅಚ್ಚು ಕುಹರದ ಒತ್ತಡ
ಸಾಕಷ್ಟು ಕುಹರದ ಒತ್ತಡದ ಸಮಯ
ಓಟಗಾರ ಮತ್ತು ಗೇಟ್ನ ಗಾತ್ರವು ತುಂಬಾ ಚಿಕ್ಕದಾಗಿದೆ
ಸಿಂಪರಣೆ ಗುರುತುಗಳು
ಸ್ಪ್ರೇಯಿಂಗ್ ಗುರುತುಗಳು ಗೇಟ್ ಎದುರು ಥ್ರೆಡ್ ಪ್ರದೇಶವನ್ನು ಉಲ್ಲೇಖಿಸುತ್ತವೆ. ಸಿಂಪಡಿಸುವಿಕೆಯ ಗುರುತುಗಳು ಉತ್ಪನ್ನಗಳ ನೋಟವನ್ನು ಮಾತ್ರ ಪರಿಣಾಮ ಬೀರುವುದಿಲ್ಲ, ಆದರೆ ಉತ್ಪನ್ನಗಳ ಬಲವನ್ನು ಸಹ ಪರಿಣಾಮ ಬೀರುತ್ತವೆ.
ಕಾಸ್:
ಅಚ್ಚು ತುಂಬುವ ಪ್ರಕ್ರಿಯೆಯಲ್ಲಿ ನಿಯಂತ್ರಣವಿಲ್ಲದೆ ಕರಗುವ ಹರಿವಿನಿಂದ ಸಿಂಪಡಿಸುವಿಕೆಯ ಗುರುತುಗಳು ಉಂಟಾಗುತ್ತವೆ.
ಕರಗಿದ ಪ್ಲಾಸ್ಟಿಕ್ ಭಾರೀ ಒತ್ತಡದ ಅಡಿಯಲ್ಲಿ ಅಚ್ಚುಗೆ ಸೇರುತ್ತದೆ. ಅಚ್ಚು ತುಂಬುವಿಕೆಯ ವೇಗವು ತುಂಬಾ ಹೆಚ್ಚಿದ್ದರೆ, ಪ್ಲಾಸ್ಟಿಕ್ ಅಚ್ಚು ಕುಹರದ ತೆರೆದ ಅಂತರದಿಂದ ಹೊರಹಾಕುತ್ತದೆ ಮತ್ತು ತ್ವರಿತವಾಗಿ ಹಿಂತಿರುಗಿ ತಣ್ಣಗಾಗುತ್ತದೆ. ಆ ಸಮಯದಲ್ಲಿ, ಎಳೆಗಳು ರೂಪುಗೊಳ್ಳುತ್ತವೆ, ಇದು ಕರಗಿದ ಪ್ಲಾಸ್ಟಿಕ್ ಅನ್ನು ಗೇಟ್ಗಳಿಗೆ ಪ್ರವೇಶಿಸುವುದನ್ನು ನಿರ್ಬಂಧಿಸುತ್ತದೆ.
ಗುರುತುಗಳನ್ನು ಸಿಂಪಡಿಸಲು ಮುಖ್ಯ ಕಾರಣವೆಂದರೆ ಗೇಟ್ಗಳ ತಪ್ಪಾದ ಸ್ಥಾನ ಅಥವಾ ಗೇಟ್ನ ವಿನ್ಯಾಸ. ಕೆಳಗಿನ ಎರಡು ಸನ್ನಿವೇಶಗಳು ದೋಷಗಳ ಪರಿಸ್ಥಿತಿಯನ್ನು ಇನ್ನಷ್ಟು ಹದಗೆಡಿಸುತ್ತದೆ:
ಹೆಚ್ಚಿನ ಅಚ್ಚು ತುಂಬುವ ವೇಗ
ಅಚ್ಚು ತುಂಬುವಿಕೆಯ ಸಮಯದಲ್ಲಿ ಕಳಪೆ ಕರಗುವ ಹರಿವು