ਇੰਜੈਕਸ਼ਨ ਮੋਲਡਿੰਗ ਦੇ ਆਮ ਮੋਲਡਿੰਗ ਨੁਕਸ ਦੇ ਹੱਲ
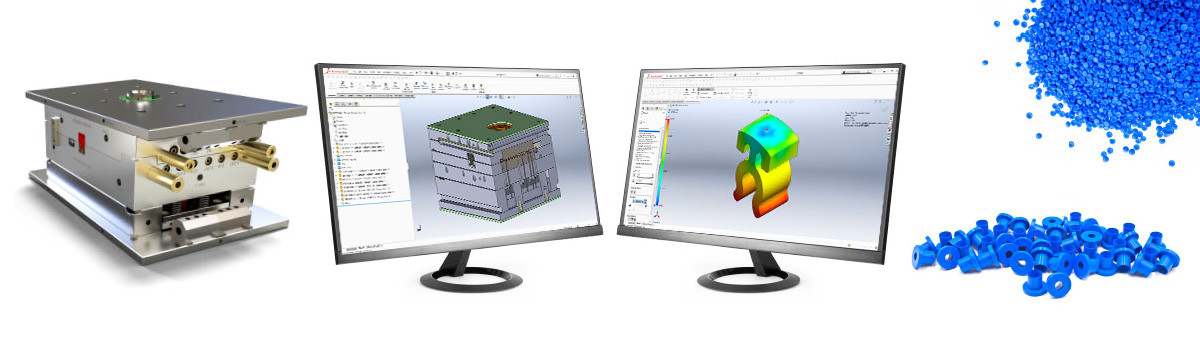
ਪਲਾਸਟਿਕ ਇੰਜੈਕਸ਼ਨ ਮੋਲਡਿੰਗ ਹਿੱਸਿਆਂ ਦੀ ਪ੍ਰਕਿਰਿਆ ਕਰਨ ਲਈ ਮੋਲਡ ਦੀ ਵਰਤੋਂ ਕਰਦੇ ਸਮੇਂ ਨੁਕਸ ਆਮ ਹੁੰਦੇ ਹਨ, ਅਤੇ ਇਹ ਪ੍ਰੋਸੈਸਿੰਗ ਕੁਸ਼ਲਤਾ ਨੂੰ ਵੱਡੇ ਪੱਧਰ 'ਤੇ ਪ੍ਰਭਾਵਿਤ ਕਰਦਾ ਹੈ। ਹੇਠਾਂ ਦਿੱਤੇ ਆਮ ਮੋਲਡਿੰਗ ਨੁਕਸ ਅਤੇ ਪਲਾਸਟਿਕ ਇੰਜੈਕਸ਼ਨ ਮੋਲਡ ਹਿੱਸਿਆਂ ਲਈ ਹੱਲ ਹਨ।
ਛੋਟੇ ਸ਼ਾਟ
ਛੋਟੇ ਸ਼ਾਟ ਤਿਆਰ ਕੀਤੇ ਉਤਪਾਦਾਂ ਦਾ ਹਵਾਲਾ ਦਿੰਦੇ ਹਨ ਕਿਉਂਕਿ ਮੋਲਡ ਪੂਰੀ ਤਰ੍ਹਾਂ ਨਹੀਂ ਭਰੇ ਜਾਂਦੇ ਹਨ।
ਇਹ ਨੁਕਸ ਆਮ ਤੌਰ 'ਤੇ ਗੇਟ ਜਾਂ ਉਹਨਾਂ ਹਿੱਸਿਆਂ ਤੋਂ ਸਭ ਤੋਂ ਦੂਰ ਸਥਾਨ 'ਤੇ ਦਿਖਾਈ ਦਿੰਦਾ ਹੈ ਜਿੱਥੇ ਸਿਰਫ ਮੋਲਡ ਦੇ ਤੰਗ ਖੇਤਰਾਂ ਰਾਹੀਂ ਪਹੁੰਚਿਆ ਜਾ ਸਕਦਾ ਹੈ ਕਿਉਂਕਿ ਤੰਗ ਖੇਤਰ ਪਿਘਲਣ ਦੇ ਪ੍ਰਵਾਹ ਨੂੰ ਪ੍ਰਭਾਵਿਤ ਕਰ ਸਕਦੇ ਹਨ।
ਛੋਟੇ ਸ਼ਾਟ ਕਾਰਨ ਸੂਖਮ ਪ੍ਰਵਾਹ ਚਿੰਨ੍ਹ ਹੋ ਸਕਦੇ ਹਨ ਜਾਂ ਨਤੀਜੇ ਵਜੋਂ ਉਤਪਾਦ ਦਾ ਇੱਕ ਵੱਡਾ ਹਿੱਸਾ ਸਪੱਸ਼ਟ ਤੌਰ 'ਤੇ ਗਾਇਬ ਹੋ ਸਕਦਾ ਹੈ।
ਕਾਰਨ:
ਛੋਟੇ ਸ਼ਾਟ ਦੇ ਕਾਰਨਾਂ ਵਿੱਚ ਸ਼ਾਮਲ ਹਨ:
ਉੱਲੀ ਵਿੱਚ ਟੀਕਾ ਲਗਾਇਆ ਕੱਚਾ ਮਾਲ ਕਾਫ਼ੀ ਨਹੀਂ ਹੈ।
ਪਿਘਲਣ ਦਾ ਵਿਰੋਧ ਵੱਡਾ ਹੁੰਦਾ ਹੈ, ਨਤੀਜੇ ਵਜੋਂ ਉੱਲੀ ਨੂੰ ਪੂਰੀ ਤਰ੍ਹਾਂ ਭਰਿਆ ਨਹੀਂ ਜਾ ਸਕਦਾ।
ਉੱਲੀ ਦਾ ਹਵਾ ਕੱਢਣਾ ਮਾੜਾ ਹੁੰਦਾ ਹੈ ਅਤੇ ਇਸ ਕਾਰਨ ਕੈਵੀਟੇਸ਼ਨ ਪੈਦਾ ਹੁੰਦੀ ਹੈ ਜੋ ਪਿਘਲਣ ਨੂੰ ਰੋਕਦੀ ਹੈ, ਜਿਸ ਨਾਲ ਪਿਘਲਣਾ ਉੱਲੀ ਦੇ ਕੁਝ ਖੇਤਰਾਂ ਵਿੱਚ ਵਹਿ ਨਹੀਂ ਸਕਦਾ।
ਬੁਰਜ਼
ਬਰਰ ਮੋਲਡ ਕੈਵਿਟੀ ਤੋਂ ਉਤਪਾਦ ਤੱਕ ਬਾਹਰ ਕੱਢੇ ਗਏ ਵਾਧੂ ਕੱਚੇ ਮਾਲ ਦੇ ਚਿਪਕਣ ਤੋਂ ਪੈਦਾ ਹੁੰਦੇ ਹਨ।
ਇਹ ਨੁਕਸ ਉਤਪਾਦ ਦੇ ਕਿਨਾਰਿਆਂ ਜਾਂ ਉੱਲੀ ਦੇ ਹਰੇਕ ਬਣੇ ਹਿੱਸੇ 'ਤੇ ਹੋਵੇਗਾ। ਕੱਚਾ ਮਾਲ ਉੱਲੀ ਤੋਂ ਭਰਿਆ ਹੋ ਸਕਦਾ ਹੈ, ਜਾਂ ਮੂਵਿੰਗ ਅਤੇ ਫਿਕਸਿੰਗ ਮੋਲਡਾਂ ਦੀਆਂ ਬੰਧਨ ਵਾਲੀਆਂ ਥਾਵਾਂ।
ਬਰਰ ਮੋਲਡ ਕੋਰ 'ਤੇ ਵੀ ਲੱਭੇ ਜਾ ਸਕਦੇ ਹਨ, ਜੋ ਕਿ ਹਾਈਡ੍ਰੌਲਿਕ ਦਬਾਅ ਜਾਂ ਐਂਗੁਲਰ ਪਿੰਨ ਕਾਰਨ ਹੁੰਦਾ ਹੈ।
ਬੁਰਰਾਂ ਦੀ ਤੀਬਰਤਾ ਵੱਖ-ਵੱਖ ਹੁੰਦੀ ਹੈ, ਕਈ ਵਾਰ ਪਤਲੀ ਹੁੰਦੀ ਹੈ, ਕਦੇ ਮੋਟੀ ਹੁੰਦੀ ਹੈ।
ਕਾਰਨ:
ਬੁਰਸ਼ ਦੇ ਕਾਰਨਾਂ ਵਿੱਚ ਸ਼ਾਮਲ ਹਨ:
ਕਲੈਂਪਿੰਗ ਮੋਲਡ ਸਤਹ ਨੂੰ ਨੁਕਸਾਨ ਪਹੁੰਚਾਇਆ ਜਾਂਦਾ ਹੈ ਜਾਂ ਬਹੁਤ ਜ਼ਿਆਦਾ ਖਰਾਬ ਹੁੰਦਾ ਹੈ।
ਮੂਵਿੰਗ ਮੋਲਡ ਅਤੇ ਫਿਕਸਿੰਗ ਮੋਲਡ ਲਾਕ ਕੀਤੇ ਜਾਣ 'ਤੇ ਡਿਸ-ਸਥਿਤ ਹੁੰਦੇ ਹਨ।
ਉੱਲੀ ਵਿੱਚ ਕੱਚੇ ਮਾਲ ਦਾ ਦਬਾਅ ਮੋਲਡ ਕਲੈਂਪਿੰਗ ਫੋਰਸ ਨਾਲੋਂ ਵੱਧ ਹੁੰਦਾ ਹੈ।
ਉਪਰੋਕਤ ਜ਼ਿਕਰ ਕੀਤੀ ਤੀਜੀ ਸ਼ਰਤ ਵੱਖ-ਵੱਖ ਕਾਰਨਾਂ ਦੇ ਨਤੀਜੇ ਵਜੋਂ ਹੋਵੇਗੀ। ਹੇਠ ਲਿਖੀਆਂ ਸਥਿਤੀਆਂ ਵਿੱਚ, ਕੱਚੇ ਮਾਲ ਦਾ ਦਬਾਅ ਮੋਲਡ ਕਲੈਂਪਿੰਗ ਫੋਰਸ ਨਾਲੋਂ ਵੱਧ ਹੁੰਦਾ ਹੈ।
ਇੰਜੈਕਸ਼ਨ ਮੋਲਡ (ਮੋਲਡ ਫਿਲਿੰਗ ਪੜਾਅ) ਦੇ ਪਹਿਲੇ ਪੜਾਅ 'ਤੇ, ਬਹੁਤ ਜ਼ਿਆਦਾ ਕੱਚਾ ਮਾਲ ਭਰਿਆ ਜਾਂਦਾ ਹੈ, ਜਿਸ ਨਾਲ ਉੱਲੀ ਦੇ ਅੰਦਰ ਦਬਾਅ ਵਧ ਜਾਂਦਾ ਹੈ।
ਉੱਲੀ ਭਰਨ ਦੀ ਪ੍ਰਕਿਰਿਆ ਦੇ ਦੌਰਾਨ, ਪਿਘਲਣ ਦੇ ਪ੍ਰਵਾਹ ਦਾ ਵੱਡਾ ਪ੍ਰਤੀਰੋਧ ਵੀ ਉੱਲੀ ਦੇ ਅੰਦਰ ਦਬਾਅ ਵਧਾਏਗਾ.
ਦਬਾਅ ਰੱਖਣ ਦੇ ਪੜਾਅ ਦੌਰਾਨ ਮੋਲਡ ਕੈਵਿਟੀ ਦਾ ਦਬਾਅ ਬਹੁਤ ਜ਼ਿਆਦਾ ਹੁੰਦਾ ਹੈ।
ਮੋਲਡ ਕਲੈਂਪਿੰਗ ਫੋਰਸ ਕਾਫ਼ੀ ਨਹੀਂ ਹੈ।
ਡੀਗ੍ਰੇਡੇਸ਼ਨ
ਸੜਨ ਨਾਲ ਕਈ ਨਤੀਜੇ ਨਿਕਲ ਸਕਦੇ ਹਨ। ਸਮੱਸਿਆ ਦੀ ਸੀਮਾ ਅਤੇ ਗੰਭੀਰਤਾ ਵੀ ਵੱਖ-ਵੱਖ ਹੁੰਦੀ ਹੈ। ਸਭ ਤੋਂ ਗੰਭੀਰ ਸਥਿਤੀ ਵਿੱਚ, ਇਹ ਉਤਪਾਦ ਦੇ ਪੂਰੀ ਤਰ੍ਹਾਂ ਰੰਗੀਨ ਹੋਣ ਅਤੇ ਖਰਾਬ ਮਕੈਨੀਕਲ ਵਿਸ਼ੇਸ਼ਤਾਵਾਂ ਦਾ ਕਾਰਨ ਬਣ ਸਕਦਾ ਹੈ। ਸਥਾਨਕ ਨਿਘਾਰ ਸਿਰਫ ਹਨੇਰੇ ਧਾਰੀਆਂ ਜਾਂ ਚਟਾਕ ਦਾ ਕਾਰਨ ਬਣੇਗਾ।
ਕਾਰਨ:
ਕੱਚੇ ਮਾਲ ਦੇ ਖਰਾਬ ਹੋਣ ਕਾਰਨ ਇਹ ਪਤਨ ਹੁੰਦਾ ਹੈ। ਲੰਬੀ ਚੇਨ ਦੇ ਅਣੂ ਜੋ ਪਲਾਸਟਿਕ ਬਣਾਉਂਦੇ ਹਨ, ਬਹੁਤ ਜ਼ਿਆਦਾ ਗਰਮੀ ਜਾਂ ਬਹੁਤ ਜ਼ਿਆਦਾ ਸ਼ੀਅਰ ਤਣਾਅ ਦੀ ਕਿਰਿਆ ਦੇ ਅਧੀਨ ਸੜ ਜਾਂਦੇ ਹਨ। ਅਣੂਆਂ ਦੇ ਸੜਨ ਦੇ ਦੌਰਾਨ, ਅਸਥਿਰ ਗੈਸ ਡਿਗਰੇਡੇਸ਼ਨ ਪ੍ਰਕਿਰਿਆ ਨੂੰ ਤੇਜ਼ ਕਰੇਗੀ, ਜਿਸ ਨਾਲ ਕੱਚੇ ਮਾਲ ਦੇ ਡੀ-ਕਲਰਿੰਗ ਦਾ ਕਾਰਨ ਬਣੇਗਾ। ਵੱਡੀ ਮਾਤਰਾ ਵਿੱਚ ਅਣੂਆਂ ਦਾ ਸੜਨ ਅੰਤ ਵਿੱਚ ਕੱਚੇ ਮਾਲ ਦੀ ਸਮੱਗਰੀ ਨੂੰ ਤੋੜ ਦੇਵੇਗਾ ਅਤੇ ਮਕੈਨੀਕਲ ਵਿਸ਼ੇਸ਼ਤਾਵਾਂ 'ਤੇ ਨਕਾਰਾਤਮਕ ਪ੍ਰਭਾਵ ਪੈਦਾ ਕਰੇਗਾ।
ਸਮੱਗਰੀ ਬੈਰਲ ਦੇ ਅਸਮਾਨ ਤਾਪਮਾਨ ਦੇ ਨਤੀਜੇ ਵਜੋਂ ਸਥਾਨਕ ਗਿਰਾਵਟ ਹੋ ਸਕਦੀ ਹੈ।
ਨਿਮਨਲਿਖਤ ਸਥਿਤੀਆਂ ਵਿੱਚ ਵਿਗਾੜ ਹੋ ਸਕਦਾ ਹੈ:
ਮੈਟੀਰੀਅਲ ਬੈਰਲ ਜਾਂ ਹਾਟ ਰਨਰ ਸਿਸਟਮ ਵਿੱਚ ਕੱਚੇ ਮਾਲ ਨੂੰ ਜ਼ਿਆਦਾ ਗਰਮ ਕੀਤਾ ਜਾ ਰਿਹਾ ਹੈ।
ਕੱਚਾ ਮਾਲ ਬਹੁਤ ਦੇਰ ਤੱਕ ਬੈਰਲ ਵਿੱਚ ਰਹਿੰਦਾ ਹੈ।
ਇੰਜੈਕਸ਼ਨ ਮੋਲਡਿੰਗ ਪ੍ਰਕਿਰਿਆ ਦੇ ਦੌਰਾਨ, ਕੱਚੇ ਮਾਲ 'ਤੇ ਸ਼ੀਅਰ ਤਣਾਅ ਬਹੁਤ ਵੱਡਾ ਹੁੰਦਾ ਹੈ। ਜੇ ਨੋਜ਼ਲ ਬਲੌਕ ਹਨ, ਜਾਂ ਗੇਟ ਅਤੇ ਰਨਰ ਬਹੁਤ ਤੰਗ ਹਨ, ਤਾਂ ਇਹ ਸ਼ੀਅਰ ਤਣਾਅ ਨੂੰ ਵਧਾਏਗਾ।
ਵਿਗਾੜ
ਆਮ ਸਥਿਤੀਆਂ ਵਿੱਚ, ਉਤਪਾਦਾਂ ਦੇ ਆਕਾਰ ਮੋਲਡਾਂ ਦੇ ਨਾਲ ਮੇਲ ਖਾਂਦੇ ਹੋਣੇ ਚਾਹੀਦੇ ਹਨ। ਵਿਗਾੜ ਉਤਪਾਦਾਂ ਦੀ ਵਿਗਾੜ ਨੂੰ ਦਰਸਾਉਂਦਾ ਹੈ।
ਜਦੋਂ ਸਥਿਤੀ ਵਿਗੜ ਜਾਂਦੀ ਹੈ, ਜਦੋਂ ਇਹ ਉੱਲੀ ਤੋਂ ਬਾਹਰ ਕੱਢਿਆ ਜਾਂਦਾ ਹੈ ਤਾਂ ਉਤਪਾਦ ਪੂਰੀ ਤਰ੍ਹਾਂ ਵਿਗੜ ਜਾਣਗੇ। ਜਦੋਂ ਸਥਿਤੀ ਗੰਭੀਰ ਨਹੀਂ ਹੁੰਦੀ ਹੈ, ਤਾਂ ਉਤਪਾਦ ਦੀ ਸ਼ਕਲ ਛੋਟੀਆਂ ਬੇਨਿਯਮੀਆਂ ਦਿਖਾਈ ਦੇਵੇਗੀ.
ਲੰਬੇ ਪਰ ਸਪੋਰਟ ਕਿਨਾਰਿਆਂ ਤੋਂ ਬਿਨਾਂ ਜਾਂ ਵੱਡੇ ਜਹਾਜ਼ ਉਹ ਖੇਤਰ ਹਨ ਜੋ ਵਿਗਾੜ ਦਾ ਸਭ ਤੋਂ ਵੱਧ ਖ਼ਤਰਾ ਹਨ।
ਕਾਰਨ:
ਵਿਗਾੜ ਦੇ ਕਾਰਨ:
ਜਦੋਂ ਉੱਲੀ ਨੂੰ ਛੱਡਿਆ ਜਾਂਦਾ ਹੈ ਤਾਂ ਤਾਪਮਾਨ ਬਹੁਤ ਜ਼ਿਆਦਾ ਹੁੰਦਾ ਹੈ।
ਜਿਵੇਂ ਕਿ ਮੋਟੇ ਅਤੇ ਪਤਲੇ ਖੇਤਰਾਂ ਵਿੱਚ ਠੰਢਾ ਹੋਣ ਦਾ ਸਮਾਂ ਵੱਖਰਾ ਹੁੰਦਾ ਹੈ, ਜਾਂ ਉੱਲੀ ਨੂੰ ਹਿਲਾਉਣ ਅਤੇ ਫਿਕਸਿੰਗ ਮੋਲਡ ਵਿੱਚ ਉੱਲੀ ਦੇ ਤਾਪਮਾਨ ਵਿੱਚ ਅੰਤਰ ਹੁੰਦਾ ਹੈ, ਉਤਪਾਦਾਂ ਦੇ ਅੰਦਰ ਸੰਕੁਚਨ ਵੱਖਰਾ ਹੁੰਦਾ ਹੈ।
ਭਰਨ ਵੇਲੇ ਉੱਲੀ ਦਾ ਪ੍ਰਵਾਹ ਨਿਰਵਿਘਨ ਨਹੀਂ ਹੁੰਦਾ (ਅਖੌਤੀ "ਫ੍ਰੀਜ਼ਿੰਗ ਓਰੀਐਂਟੇਸ਼ਨ") ਜਾਂ ਮੋਲਡ ਕੈਵਿਟੀ ਦੇ ਅੰਦਰ ਦਬਾਅ ਦਬਾਅ ਰੱਖਣ ਦੇ ਪੜਾਅ 'ਤੇ ਬਹੁਤ ਜ਼ਿਆਦਾ ਹੁੰਦਾ ਹੈ।
ਅਸ਼ੁੱਧੀਆਂ
ਅਸ਼ੁੱਧੀਆਂ ਅਕਸਰ ਵੱਖ-ਵੱਖ ਰੰਗਾਂ, ਪੈਚਾਂ ਜਾਂ ਧਾਰੀਆਂ ਵਿੱਚ ਚਟਾਕ ਦੇ ਰੂਪ ਵਿੱਚ ਦਿਖਾਈ ਦਿੰਦੀਆਂ ਹਨ। ਸਭ ਤੋਂ ਆਮ ਇੱਕ ਕਾਲਾ ਧੱਬਾ ਹੈ.
ਅਸ਼ੁੱਧੀਆਂ ਸਿਰਫ਼ ਛੋਟੇ ਧੱਬੇ ਹੋ ਸਕਦੀਆਂ ਹਨ, ਪਰ ਇਹ ਗੰਭੀਰ ਹੋਣ 'ਤੇ ਸਪੱਸ਼ਟ ਧਾਰੀਆਂ ਜਾਂ ਡੀ-ਕਲਰਿੰਗ ਦਾ ਵੱਡਾ ਹਿੱਸਾ ਵੀ ਹੋ ਸਕਦੀਆਂ ਹਨ।
ਕਾਰਨ:
ਅਸ਼ੁੱਧੀਆਂ ਕੱਚੇ ਮਾਲ ਦੇ ਨਾਲ ਮਿਲਾਏ ਗਏ ਸੁੰਡੀ ਕਾਰਨ ਹੁੰਦੀਆਂ ਹਨ, ਜਿਵੇਂ ਕਿ:
ਜਦੋਂ ਇਹ ਬੈਰਲਾਂ ਵਿੱਚ ਲਿਜਾਇਆ ਜਾਂਦਾ ਹੈ ਤਾਂ ਕੱਚੇ ਮਾਲ ਨੂੰ ਸੁੰਡੀਆਂ ਨਾਲ ਮਿਲਾਇਆ ਜਾਂਦਾ ਹੈ।
ਕੱਚੇ ਮਾਲ ਦਾ ਸੜਨ ਕਿਸੇ ਵੀ ਕੱਟਣ ਦੀ ਵਿਧੀ ਤੋਂ ਡਿੱਗ ਸਕਦਾ ਹੈ ਅਤੇ ਕੱਚੇ ਮਾਲ ਵਿੱਚ ਮਿਲਾਇਆ ਜਾ ਸਕਦਾ ਹੈ, ਜਿਵੇਂ ਕਿ ਮਸ਼ੀਨ ਦੇ ਬੋਲਟ, ਸੁਕਾਉਣ ਵਾਲੇ ਡਰੱਮ ਦੀ ਅੰਦਰਲੀ ਕੰਧ, ਜੋੜਾਂ/ਨੋਜ਼ਲਾਂ।
ਲੈਮੀਨੇਸ਼ਨ
ਲੈਮੀਨੇਸ਼ਨ ਉਤਪਾਦਾਂ ਦੀ ਸਤ੍ਹਾ 'ਤੇ "ਚਮੜੀ ਦਾ ਪ੍ਰਭਾਵ" ਪੈਦਾ ਕਰੇਗੀ, ਜੋ ਉਤਪਾਦਾਂ ਅਤੇ ਹੋਰ ਕੱਚੇ ਮਾਲ ਦੀ ਸਤਹ ਦੀਆਂ ਵਿਸ਼ੇਸ਼ਤਾਵਾਂ ਅਤੇ ਬਣਤਰ ਵਿੱਚ ਅੰਤਰ ਦੇ ਕਾਰਨ ਹੁੰਦੀ ਹੈ, ਅਤੇ ਇਹ ਇੱਕ ਛਿੱਲ ਵਾਲੀ ਚਮੜੀ ਬਣਾਉਂਦੀ ਹੈ ਜਿਸ ਨੂੰ ਹਟਾਇਆ ਜਾ ਸਕਦਾ ਹੈ।
ਜਦੋਂ ਲੈਮੀਨੇਸ਼ਨ ਗੰਭੀਰ ਹੁੰਦੀ ਹੈ, ਤਾਂ ਸਾਰਾ ਕਰਾਸ ਸੈਕਸ਼ਨ ਖੇਤਰ ਵੱਖ-ਵੱਖ ਲੇਅਰਾਂ ਦਾ ਬਣਿਆ ਹੁੰਦਾ ਹੈ, ਅਤੇ ਇਕੱਠੇ ਪਿਘਲਿਆ ਨਹੀਂ ਜਾਂਦਾ ਹੈ। ਜਦੋਂ ਨੁਕਸ ਘੱਟ ਸਪੱਸ਼ਟ ਹੁੰਦੇ ਹਨ, ਤਾਂ ਉਤਪਾਦਾਂ ਦੀ ਦਿੱਖ ਲੋੜਾਂ ਨੂੰ ਪੂਰਾ ਕਰ ਸਕਦੀ ਹੈ, ਪਰ ਉਤਪਾਦਾਂ ਦੀਆਂ ਮਕੈਨੀਕਲ ਵਿਸ਼ੇਸ਼ਤਾਵਾਂ ਨੂੰ ਤੋੜ ਦੇਵੇਗੀ।
ਕਾਰਨ:
ਲੈਮੀਨੇਸ਼ਨ ਦੇ ਦੋ ਮੁੱਖ ਕਾਰਨ ਹਨ। ਪਹਿਲਾ ਇਹ ਹੈ ਕਿ ਜਦੋਂ ਦੋ ਵੱਖ-ਵੱਖ ਕਿਸਮਾਂ ਦੇ ਕੱਚੇ ਮਾਲ ਨੂੰ ਗਲਤ ਤਰੀਕੇ ਨਾਲ ਮਿਲਾਇਆ ਜਾਂਦਾ ਹੈ। ਦਬਾਅ ਹੇਠ ਦੋ ਕੱਚੇ ਮਾਲ ਨੂੰ ਇੱਕੋ ਸਮੇਂ ਬੈਰਲ ਵਿੱਚ ਲਿਜਾਇਆ ਜਾਵੇਗਾ। ਹਾਲਾਂਕਿ, ਜਦੋਂ ਉੱਲੀ ਨੂੰ ਠੰਡਾ ਹੋਣ 'ਤੇ ਇਕੱਠੇ ਪਿਘਲਿਆ ਨਹੀਂ ਜਾ ਸਕਦਾ, ਉਸੇ ਤਰ੍ਹਾਂ ਜਿਵੇਂ ਵੱਖ-ਵੱਖ ਪਰਤਾਂ ਨੂੰ ਉਤਪਾਦ ਬਣਾਉਣ ਲਈ ਇਕੱਠੇ ਦਬਾਇਆ ਜਾਂਦਾ ਹੈ।
ਦੂਜਾ: ਜੇ ਠੰਡੇ ਪਿਘਲਣ ਨੂੰ ਤੰਗ ਗੇਟ ਵਿੱਚੋਂ ਲੰਘਣ ਲਈ ਮਜਬੂਰ ਕੀਤਾ ਜਾਂਦਾ ਹੈ, ਤਾਂ ਸ਼ੀਅਰ ਤਣਾਅ ਪੈਦਾ ਕੀਤਾ ਜਾਵੇਗਾ. ਬਹੁਤ ਜ਼ਿਆਦਾ ਸ਼ੀਅਰ ਤਣਾਅ ਕਾਰਨ ਪਿਘਲਣ ਵਾਲੀ ਪਰਤ ਪਹਿਲਾਂ ਹੀ ਪਿਘਲ ਜਾਂਦੀ ਹੈ, ਪੂਰੀ ਤਰ੍ਹਾਂ ਫਿਊਜ਼ ਨਹੀਂ ਹੋ ਸਕਦੀ।
ਮਿਸ਼ਰਣ ਦਾ ਜੋਖਮ:
ਇੱਕ ਚੀਜ਼ ਜਿਸ ਬਾਰੇ ਸੁਚੇਤ ਹੋਣਾ ਚਾਹੀਦਾ ਹੈ ਉਹ ਇਹ ਹੈ ਕਿ ਕੁਝ ਕੱਚੇ ਮਾਲ ਨੂੰ ਇਕੱਠੇ ਮਿਲਾਉਣ ਦੇ ਨਤੀਜੇ ਵਜੋਂ ਮਜ਼ਬੂਤ ਰਸਾਇਣਕ ਪ੍ਰਤੀਕ੍ਰਿਆ ਹੋਵੇਗੀ, ਜਿਵੇਂ ਕਿ ਪੀਵੀਸੀ ਅਤੇ ਐਵੇਟਲ ਨੂੰ ਮਿਲਾਇਆ ਨਹੀਂ ਜਾਣਾ ਚਾਹੀਦਾ।
ਸਿਲਵਰ ਰੇਖਿਕ
ਸਲਾਈਵਰ ਲੀਨੀਅਰ ਸਿਰਫ਼ ਸਥਾਨਕ ਵਰਤਾਰੇ ਹੋ ਸਕਦਾ ਹੈ, ਪਰ ਜਦੋਂ ਇਹ ਗੰਭੀਰ ਹੋਵੇ ਤਾਂ ਪੂਰੀ ਸਤ੍ਹਾ ਤੱਕ ਫੈਲਾਇਆ ਜਾ ਸਕਦਾ ਹੈ।
ਸਿਲਵਰ ਲੀਨੀਅਰ ਉਤਪਾਦਾਂ ਦੀ ਦਿੱਖ ਨੂੰ ਪ੍ਰਭਾਵਤ ਕਰੇਗਾ ਅਤੇ ਉਤਪਾਦਾਂ ਦੀਆਂ ਮਕੈਨੀਕਲ ਵਿਸ਼ੇਸ਼ਤਾਵਾਂ ਨੂੰ ਵੀ ਨੁਕਸਾਨ ਪਹੁੰਚਾਏਗਾ।
ਕਾਰਨ:
ਹੇਠਾਂ ਦਿੱਤੇ ਦੋ ਬਿੰਦੂ ਸਿਲਵਰ ਲੀਨੀਅਰ ਦਾ ਕਾਰਨ ਬਣਦੇ ਹਨ:
ਕੱਚਾ ਮਾਲ ਗਿੱਲਾ ਹੈ ਅਤੇ ਉਨ੍ਹਾਂ ਵਿੱਚੋਂ ਕੁਝ ਹਵਾ ਵਿੱਚ ਭਾਫ਼ ਨੂੰ ਜਜ਼ਬ ਕਰ ਲੈਣਗੇ। ਜੇ ਕੱਚਾ ਮਾਲ ਬਹੁਤ ਗਿੱਲਾ ਹੈ, ਤਾਂ ਦਬਾਅ ਵਾਲਾ ਭਾਫ਼ ਉੱਚ ਤਾਪਮਾਨ ਅਤੇ ਬੈਰਲ ਦੇ ਉੱਚ ਦਬਾਅ ਹੇਠ ਪੈਦਾ ਹੋ ਸਕਦਾ ਹੈ। ਇਹ ਵਾਸ਼ਪ ਉਤਪਾਦ ਦੀ ਸਤ੍ਹਾ ਨੂੰ ਤੋੜਦੇ ਹਨ ਅਤੇ ਚਾਂਦੀ ਦੀਆਂ ਧਾਰੀਆਂ ਬਣਾਉਂਦੇ ਹਨ।
ਪਿਘਲਣ ਨਾਲ ਥਰਮਲ ਖਰਾਬ ਹੋ ਗਿਆ ਹੈ ਅਤੇ ਸਥਾਨਕ ਡੀਗਰੇਡੇਸ਼ਨ ਪੈਦਾ ਕਰਦਾ ਹੈ। ਉਤਪੰਨ ਅਸਥਿਰ ਗੈਸ ਨੂੰ ਉੱਲੀ ਦੀ ਸਤ੍ਹਾ 'ਤੇ ਬਲੌਕ ਕੀਤਾ ਜਾਵੇਗਾ ਅਤੇ ਉਤਪਾਦਾਂ ਦੀ ਸਤ੍ਹਾ 'ਤੇ ਧਾਰੀਆਂ ਪੈਦਾ ਕੀਤੀਆਂ ਜਾਣਗੀਆਂ।
ਇਹ ਪਤਨ ਜਿੰਨਾ ਮਾੜਾ ਨਹੀਂ ਹੈ। ਜਿੰਨਾ ਚਿਰ ਪਿਘਲਣ ਦਾ ਤਾਪਮਾਨ ਉੱਚਾ ਹੁੰਦਾ ਹੈ ਜਾਂ ਇਹ ਪਲਾਸਟਿਕਾਈਜ਼ੇਸ਼ਨ ਦੇ ਦੌਰਾਨ ਸ਼ੀਅਰ ਤਣਾਅ ਦੇ ਅਧੀਨ ਹੁੰਦਾ ਹੈ ਜਾਂ ਉੱਲੀ ਵਿੱਚ ਇੰਜੈਕਟ ਕਰਦਾ ਹੈ, ਅਜਿਹਾ ਹੋ ਸਕਦਾ ਹੈ।
ਗਲੋਸ/ਸ਼ੈਡੋ
ਉਤਪਾਦਾਂ ਦੀ ਸਤਹ ਦੀ ਸਮਾਪਤੀ ਮੋਲਡ ਦੇ ਸਮਾਨ ਹੋਣੀ ਚਾਹੀਦੀ ਹੈ। ਜਦੋਂ ਦੋ ਦੀ ਸਤ੍ਹਾ ਦੀ ਸਮਾਪਤੀ ਵੱਖਰੀ ਹੁੰਦੀ ਹੈ, ਤਾਂ ਚਮਕ/ਸ਼ੈਡੋ ਨੁਕਸ ਪੈਦਾ ਹੁੰਦੇ ਹਨ।
ਨੁਕਸ ਆਉਣ 'ਤੇ ਸਤ੍ਹਾ ਉਦਾਸ ਹੋ ਜਾਵੇਗੀ, ਅਤੇ ਖੁਰਦਰੀ ਸਤਹ ਨਿਰਵਿਘਨ ਅਤੇ ਗਲੋਸੀ ਹੋਵੇਗੀ।
ਕਾਰਨ:
ਗਲੋਸ/ਸ਼ੈਡੋ ਦੇ ਕਾਰਨਾਂ ਵਿੱਚ ਸ਼ਾਮਲ ਹਨ:
ਪਿਘਲਣਾ ਅਣ-ਸੁਚਾਰੂ ਢੰਗ ਨਾਲ ਵਹਿੰਦਾ ਹੈ ਜਾਂ ਉੱਲੀ ਦੀ ਸਤ੍ਹਾ ਦਾ ਤਾਪਮਾਨ ਘੱਟ ਹੈ, ਨਤੀਜੇ ਵਜੋਂ ਮੋਲਡ ਸਤਹ ਫਿਨਿਸ਼ ਨੂੰ ਸਮੱਗਰੀ ਦੀ ਢਾਲਣ ਵੇਲੇ ਡੁਪਲੀਕੇਟ ਨਹੀਂ ਕੀਤਾ ਜਾ ਸਕਦਾ।
ਪ੍ਰੈਸ਼ਰ ਹੋਲਡਿੰਗ ਦੇ ਦੌਰਾਨ, ਕੈਵਿਟੀ ਵਿੱਚ ਦਬਾਅ ਇੰਨਾ ਜ਼ਿਆਦਾ ਨਹੀਂ ਹੁੰਦਾ ਹੈ ਕਿ ਸਮੱਗਰੀ ਨੂੰ ਕੂਲਿੰਗ ਪ੍ਰਕਿਰਿਆ ਵਿੱਚ ਉੱਲੀ ਦੀ ਸਤ੍ਹਾ ਨਾਲ ਚਿਪਕਿਆ ਜਾ ਸਕੇ, ਜਿਸ ਨਾਲ ਸੁੰਗੜਨ ਦੇ ਨਿਸ਼ਾਨ ਰਹਿ ਜਾਂਦੇ ਹਨ।
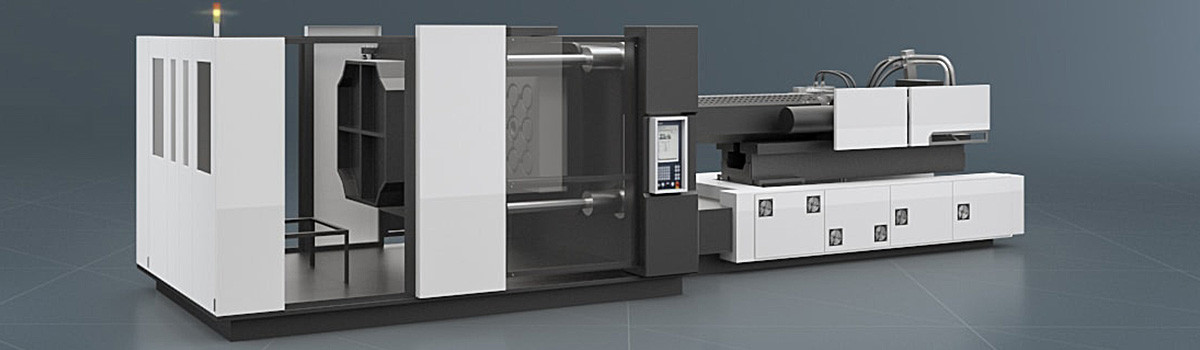
ਵਹਾਅ ਦੇ ਚਿੰਨ੍ਹ
ਵਹਾਅ ਦੇ ਚਿੰਨ੍ਹ ਉਤਪਾਦਾਂ ਦੀ ਸਤ੍ਹਾ 'ਤੇ ਕਈ ਰੂਪਾਂ ਵਿੱਚ ਲੱਭੇ ਜਾ ਸਕਦੇ ਹਨ। ਆਮ ਤੌਰ 'ਤੇ, ਇਹ ਇੱਕ ਸ਼ੈਡੋ ਖੇਤਰ ਬਣਾਏਗਾ.
ਵਹਾਅ ਦੇ ਚਿੰਨ੍ਹ ਉਤਪਾਦਾਂ ਦੀ ਸਤ੍ਹਾ 'ਤੇ ਕੋਈ ਉਭਾਰ ਜਾਂ ਉਦਾਸੀ ਪੈਦਾ ਨਹੀਂ ਕਰਦੇ, ਜਿਸ ਨੂੰ ਉਂਗਲਾਂ ਨਾਲ ਮਹਿਸੂਸ ਨਹੀਂ ਕੀਤਾ ਜਾ ਸਕਦਾ। ਇਸ ਨੁਕਸ ਨੂੰ ਡਰੈਗ ਮਾਰਕ, ਗੋਸਟਿੰਗ ਅਤੇ ਸ਼ੈਡੋ ਵੀ ਕਿਹਾ ਜਾਂਦਾ ਹੈ।
ਜਦੋਂ ਵਹਾਅ ਦੇ ਚਿੰਨ੍ਹ ਸਪੱਸ਼ਟ ਹੁੰਦੇ ਹਨ, ਤਾਂ ਇਹ ਖੰਭਾਂ ਪੈਦਾ ਕਰੇਗਾ, ਅਤੇ ਉਤਪਾਦਾਂ ਦੀ ਸਤ੍ਹਾ 'ਤੇ ਨਿਸ਼ਾਨਾਂ ਵਰਗੇ ਨੁਕਸ ਛੱਡ ਦੇਵੇਗਾ।
ਕਾਰਨ:
ਵਹਾਅ ਦੇ ਚਿੰਨ੍ਹ ਲੱਭੇ ਜਾ ਸਕਦੇ ਹਨ ਜਦੋਂ:
ਪਿਘਲਣ ਦੀ ਵਹਾਅਯੋਗਤਾ ਮਾੜੀ ਹੈ ਜਾਂ ਉੱਲੀ ਦੀ ਸਤਹ ਦਾ ਤਾਪਮਾਨ ਘੱਟ ਹੈ, ਨਤੀਜੇ ਵਜੋਂ ਉੱਲੀ ਭਰਨ ਦੀ ਪ੍ਰਕਿਰਿਆ ਵਿੱਚ ਪਲਾਸਟਿਕ ਦਾ ਇੱਕ ਵੱਡਾ ਵਹਾਅ ਪ੍ਰਤੀਰੋਧ ਹੁੰਦਾ ਹੈ।
ਮੋਲਡ ਫਿਲਿੰਗ ਵਿੱਚ, ਪ੍ਰਤੀਰੋਧ ਦੇ ਨਾਲ ਪਿਘਲਣ ਦਾ ਪ੍ਰਵਾਹ, ਜੋ ਕਿ ਡਾਈ ਦੀ ਅਸਮਾਨ ਸਤਹ, ਡਾਈ ਸਤਹ 'ਤੇ ਛਾਪੇ ਗਏ ਨਿਸ਼ਾਨ ਜਾਂ ਪੈਟਰਨ, ਜਾਂ ਭਰਨ ਦੀ ਪ੍ਰਕਿਰਿਆ ਦੌਰਾਨ ਪਿਘਲਣ ਦੇ ਪ੍ਰਵਾਹ ਦੀ ਦਿਸ਼ਾ ਵਿੱਚ ਤਬਦੀਲੀ ਕਾਰਨ ਹੋ ਸਕਦਾ ਹੈ।
ਜੋੜਨ ਵਾਲੀ ਲਾਈਨ
ਜੁਆਇਨਿੰਗ ਲਾਈਨ ਉਦੋਂ ਉਤਪੰਨ ਹੁੰਦੀ ਹੈ ਜਦੋਂ ਮੋਲਡ ਫਿਲਿੰਗ ਦੌਰਾਨ ਦੋ ਪਿਘਲਣ ਵਾਲੇ ਮੋਰਚੇ ਮਿਲਦੇ ਹਨ, ਅਤੇ ਇੱਕ ਲਾਈਨ ਵਾਂਗ ਉਤਪਾਦ ਦੀ ਸਤ੍ਹਾ 'ਤੇ ਦਿਖਾਈ ਦੇਣਗੇ।
ਜੁਆਇੰਟਿੰਗ ਲਾਈਨ ਉਤਪਾਦਾਂ ਦੀ ਸਤਹ 'ਤੇ ਕ੍ਰੈਕਿੰਗ ਲਾਈਨ ਦੀ ਤਰ੍ਹਾਂ ਹੈ, ਜਿਸਦਾ ਪਤਾ ਲਗਾਉਣਾ ਸਪੱਸ਼ਟ ਨਹੀਂ ਹੈ।
ਮੋਲਡਾਂ ਨੂੰ ਡਿਜ਼ਾਈਨ ਕਰਦੇ ਸਮੇਂ, ਕੁਝ ਦਿਖਾਈ ਦੇਣ ਵਾਲੀਆਂ ਜੋੜਨ ਵਾਲੀਆਂ ਲਾਈਨਾਂ ਅਟੱਲ ਹੁੰਦੀਆਂ ਹਨ। ਇਸ ਸਥਿਤੀ ਵਿੱਚ, ਉਤਪਾਦਾਂ ਦੀ ਤਾਕਤ ਅਤੇ ਦਿੱਖ ਨੂੰ ਨੁਕਸਾਨ ਤੋਂ ਰੋਕਣ ਲਈ ਜਿੰਨਾ ਸੰਭਵ ਹੋ ਸਕੇ ਜੋੜਨ ਵਾਲੀ ਲਾਈਨ ਨੂੰ ਛੋਟਾ ਕਰੋ।
ਕਾਰਨ:
ਪਿਘਲਣ ਵਾਲੇ ਫਰੰਟ ਦੀ ਪੀੜ੍ਹੀ ਦੇ ਕਈ ਕਾਰਨ ਹਨ. ਸਭ ਤੋਂ ਸੰਭਵ ਕਾਰਨ ਮੋਲਡ ਕੋਰ ਦੇ ਕਿਨਾਰਿਆਂ ਦੇ ਨਾਲ ਪਿਘਲਣ ਦਾ ਪ੍ਰਵਾਹ ਹੋ ਸਕਦਾ ਹੈ। ਜਦੋਂ ਦੋ ਪਿਘਲਦੇ ਹਨ, ਇਹ ਜੋੜਨ ਵਾਲੀਆਂ ਲਾਈਨਾਂ ਪੈਦਾ ਕਰਦਾ ਹੈ। ਦੋ ਪਿਘਲਣ ਵਾਲੇ ਫਰੰਟ ਦਾ ਤਾਪਮਾਨ ਇੰਨਾ ਜ਼ਿਆਦਾ ਹੋਣਾ ਚਾਹੀਦਾ ਹੈ ਕਿ ਉਹਨਾਂ ਨੂੰ ਸਫਲਤਾਪੂਰਵਕ ਇਕੱਠੇ ਫਿਊਜ਼ ਕੀਤਾ ਜਾ ਸਕੇ, ਅਤੇ ਉਤਪਾਦਾਂ ਦੀ ਮਜ਼ਬੂਤੀ ਅਤੇ ਦਿੱਖ ਨੂੰ ਪ੍ਰਭਾਵਿਤ ਨਾ ਕਰੇ।
ਜਦੋਂ ਦੋ ਪਿਘਲਣ ਨੂੰ ਪੂਰੀ ਤਰ੍ਹਾਂ ਇਕੱਠਾ ਨਹੀਂ ਕੀਤਾ ਜਾ ਸਕਦਾ, ਤਾਂ ਨੁਕਸ ਪੈਦਾ ਹੋਣਗੇ।
ਨੁਕਸ ਦੇ ਕਾਰਨ:
ਉੱਲੀ ਦੇ ਮੋਟੇ ਅਤੇ ਪਤਲੇ ਹਿੱਸੇ ਹੁੰਦੇ ਹਨ, ਅਤੇ ਪਿਘਲਣ ਦੀ ਗਤੀ ਵੱਖਰੀ ਹੁੰਦੀ ਹੈ, ਜਦੋਂ ਪਿਘਲਣਾ ਉੱਲੀ ਦੇ ਪਤਲੇ ਹਿੱਸੇ ਵਿੱਚੋਂ ਲੰਘਦਾ ਹੈ, ਤਾਪਮਾਨ ਘੱਟ ਹੁੰਦਾ ਹੈ।
ਹਰ ਦੌੜਾਕ ਦੀ ਲੰਬਾਈ ਵੱਖਰੀ ਹੁੰਦੀ ਹੈ। ਇਕੱਲੇ ਦੌੜਾਕਾਂ ਨੂੰ ਠੰਡਾ ਕਰਨਾ ਆਸਾਨ ਹੋਵੇਗਾ.
ਮੋਲਡ ਕੈਵਿਟੀ ਪ੍ਰੈਸ਼ਰ ਇੰਨਾ ਕਾਫ਼ੀ ਨਹੀਂ ਹੈ ਕਿ ਦਬਾਅ ਰੱਖਣ ਦੇ ਪੜਾਅ ਦੌਰਾਨ ਪਿਘਲਣ ਨੂੰ ਪੂਰੀ ਤਰ੍ਹਾਂ ਫਿਊਜ਼ ਕਰਨ ਦਿੱਤਾ ਜਾ ਸਕੇ।
ਬਾਕੀ ਬਚੇ ਬੁਲਬਲੇ ਪਿਘਲਣ ਵਾਲੇ ਫਰੰਟ ਨੂੰ ਫਿਊਜ਼ ਕਰਨ ਵਿੱਚ ਅਸਮਰੱਥ ਬਣਾਉਂਦੇ ਹਨ, ਜਿਸ ਨਾਲ ਜਲਣ ਵੀ ਹੋ ਜਾਂਦੀ ਹੈ।
ਬਰਨਿੰਗ
ਬਰਨਿੰਗ ਸ਼ਾਰਟ ਸ਼ਾਟ ਦੇ ਸਮਾਨ ਹੈ, ਪਰ ਅਨਿਯਮਿਤ ਫੇਡਿੰਗ ਕਿਨਾਰਿਆਂ ਅਤੇ ਮਾਮੂਲੀ ਜਲਣ ਦੀ ਗੰਧ ਦੇ ਨਾਲ। ਕਾਰਬਨ ਬਲੈਕ ਖੇਤਰ ਉਤਪਾਦ 'ਤੇ ਦਿਖਾਈ ਦੇਣਗੇ, ਜਦੋਂ ਸਥਿਤੀ ਗੰਭੀਰ ਹੁੰਦੀ ਹੈ, ਪਲਾਸਟਿਕ ਦੇ ਸੜਨ ਦੀ ਗੰਧ ਦੇ ਨਾਲ।
ਜੇ ਨੁਕਸ ਦੂਰ ਨਹੀਂ ਕੀਤੇ ਜਾਂਦੇ, ਤਾਂ ਉੱਲੀ 'ਤੇ ਅਕਸਰ ਕਾਲਾ ਜਮ੍ਹਾ ਹੁੰਦਾ ਹੈ। ਜੇਕਰ ਜਲਣ ਨਾਲ ਪੈਦਾ ਹੋਣ ਵਾਲੇ ਗੈਸ ਜਾਂ ਤੇਲ ਪਦਾਰਥਾਂ ਦੀ ਤੁਰੰਤ ਜਾਂਚ ਨਾ ਕੀਤੀ ਜਾਵੇ, ਤਾਂ ਉਹ ਹਵਾ ਦੇ ਛੇਕ ਨੂੰ ਰੋਕ ਸਕਦੇ ਹਨ। ਜਲਣ ਆਮ ਤੌਰ 'ਤੇ ਮਾਰਗਾਂ ਦੇ ਸਿਰੇ 'ਤੇ ਪਾਈ ਜਾਂਦੀ ਹੈ।
ਕਾਰਨ:
ਜਲਣ ਅੰਦਰੂਨੀ ਬਲਨ ਪ੍ਰਭਾਵ ਕਾਰਨ ਹੁੰਦੀ ਹੈ. ਜਦੋਂ ਹਵਾ ਵਿੱਚ ਦਬਾਅ ਬਹੁਤ ਘੱਟ ਸਮੇਂ ਵਿੱਚ ਤੇਜ਼ੀ ਨਾਲ ਵਧਦਾ ਹੈ, ਤਾਂ ਤਾਪਮਾਨ ਵਧੇਗਾ ਅਤੇ ਜਲਣ ਦਾ ਕਾਰਨ ਬਣੇਗਾ। ਇਕੱਤਰ ਕੀਤੇ ਡੇਟਾ ਦੇ ਅਨੁਸਾਰ, ਇੰਜੈਕਸ਼ਨ ਮੋਲਡਿੰਗ ਪ੍ਰਕਿਰਿਆ ਵਿੱਚ ਅੰਦਰੂਨੀ ਬਲਨ ਪ੍ਰਭਾਵ 600 ਡਿਗਰੀ ਤੱਕ ਉੱਚ ਤਾਪਮਾਨ ਪੈਦਾ ਕਰ ਸਕਦਾ ਹੈ.
ਜਲਣ ਉਦੋਂ ਪੈਦਾ ਹੋ ਸਕਦੀ ਹੈ ਜਦੋਂ:
ਉੱਲੀ ਭਰਨ ਦੀ ਗਤੀ ਤੇਜ਼ ਹੈ ਤਾਂ ਕਿ ਹਵਾ ਨੂੰ ਉੱਲੀ ਦੇ ਖੋਲ ਤੋਂ ਖਾਲੀ ਨਹੀਂ ਕੀਤਾ ਜਾ ਸਕਦਾ, ਅਤੇ ਆਉਣ ਵਾਲੇ ਪਲਾਸਟਿਕ ਦੇ ਬਲਾਕ ਦੇ ਕਾਰਨ ਹਵਾ ਦੇ ਬੁਲਬੁਲੇ ਪੈਦਾ ਹੁੰਦੇ ਹਨ, ਅਤੇ ਸੰਕੁਚਿਤ ਹੋਣ ਤੋਂ ਬਾਅਦ ਅੰਦਰੂਨੀ ਬਲਨ ਪ੍ਰਭਾਵ ਵੱਲ ਅਗਵਾਈ ਕਰਦੇ ਹਨ.
ਹਵਾ ਦੇ ਛੇਕ ਬੰਦ ਹਨ ਜਾਂ ਹਵਾਦਾਰੀ ਨਿਰਵਿਘਨ ਨਹੀਂ ਹੈ।
ਉੱਲੀ ਵਿਚਲੀ ਹਵਾ ਨੂੰ ਹਵਾ ਦੇ ਛੇਕ ਤੋਂ ਖਾਲੀ ਕਰ ਦੇਣਾ ਚਾਹੀਦਾ ਹੈ। ਜੇ ਹਵਾਦਾਰੀ ਸਥਿਤੀ, ਸੰਖਿਆ, ਆਕਾਰ ਜਾਂ ਫੰਕਸ਼ਨਾਂ ਦੁਆਰਾ ਪ੍ਰਭਾਵਿਤ ਹੁੰਦੀ ਹੈ, ਤਾਂ ਹਵਾ ਉੱਲੀ ਵਿੱਚ ਰਹੇਗੀ ਅਤੇ ਜਲਣ ਵੱਲ ਲੈ ਜਾਵੇਗੀ। ਵੱਡੀ ਮੋਲਡ ਕਲੈਂਪਿੰਗ ਫੋਰਸ ਵੀ ਖਰਾਬ ਹਵਾਦਾਰੀ ਵੱਲ ਲੈ ਜਾਵੇਗੀ।
ਸੁੰਗੜਨ
ਸੁੰਗੜਨ ਦਾ ਮਤਲਬ ਹੈ ਉਤਪਾਦਾਂ ਦੀ ਸਤ੍ਹਾ 'ਤੇ ਮਾਮੂਲੀ ਖੋਖਲੇ।
ਜਦੋਂ ਨੁਕਸ ਮਾਮੂਲੀ ਹੁੰਦੇ ਹਨ, ਤਾਂ ਉਤਪਾਦਾਂ ਦੀ ਸਤਹ ਅਸਮਾਨ ਹੁੰਦੀ ਹੈ। ਜਦੋਂ ਇਹ ਗੰਭੀਰ ਹੁੰਦਾ ਹੈ, ਤਾਂ ਉਤਪਾਦਾਂ ਦਾ ਵੱਡਾ ਖੇਤਰ ਢਹਿ ਜਾਵੇਗਾ। ਕਮਾਨ, ਹੈਂਡਲ ਅਤੇ ਪ੍ਰੋਟ੍ਰੂਸ਼ਨ ਵਾਲੇ ਉਤਪਾਦ ਅਕਸਰ ਸੁੰਗੜਨ ਦੇ ਨੁਕਸ ਤੋਂ ਪੀੜਤ ਹੁੰਦੇ ਹਨ।
ਕਾਰਨ:
ਠੰਢਾ ਹੋਣ ਦੇ ਦੌਰਾਨ ਕੱਚੇ ਮਾਲ ਦੇ ਵੱਡੇ ਖੇਤਰ ਦੇ ਸੁੰਗੜਨ ਕਾਰਨ ਸੁੰਗੜਦਾ ਹੈ।
ਉਤਪਾਦਾਂ ਦੇ ਸੰਘਣੇ ਖੇਤਰ (ਜਿਵੇਂ ਕਿ ਪੁਰਾਲੇਖ) ਵਿੱਚ, ਸਮੱਗਰੀ ਦਾ ਮੁੱਖ ਤਾਪਮਾਨ ਘੱਟ ਹੁੰਦਾ ਹੈ, ਇਸਲਈ ਸੁੰਗੜਨ ਸਤਹ ਨਾਲੋਂ ਬਾਅਦ ਵਿੱਚ ਵਾਪਰਦਾ ਹੈ, ਜੋ ਕੱਚੇ ਮਾਲ ਦੇ ਅੰਦਰ ਇੱਕ ਸੰਕੁਚਨ ਸ਼ਕਤੀ ਪੈਦਾ ਕਰੇਗਾ, ਅਤੇ ਬਾਹਰੀ ਪਾਸੇ ਨੂੰ ਅੰਦਰ ਵੱਲ ਖਿੱਚੇਗਾ। ਸੰਕੁਚਨ ਪੈਦਾ ਕਰਨ ਲਈ.
ਸੰਕੁਚਨ ਹੇਠ ਲਿਖੀਆਂ ਸਥਿਤੀਆਂ ਵਿੱਚ ਵਾਪਰਦਾ ਹੈ:
ਮੋਲਡ ਕੈਵਿਟੀ ਵਿੱਚ ਦਬਾਅ ਕੂਲਿੰਗ ਪ੍ਰਕਿਰਿਆ ਵਿੱਚ ਕੱਚੇ ਮਾਲ ਦੇ ਸੁੰਗੜਨ ਤੋਂ ਪੈਦਾ ਹੋਏ ਬਲ ਨਾਲੋਂ ਘੱਟ ਹੁੰਦਾ ਹੈ।
ਕੂਲਿੰਗ ਪ੍ਰਕਿਰਿਆ ਦੇ ਦੌਰਾਨ ਮੋਲਡ ਕੈਵਿਟੀ ਦਾ ਨਾਕਾਫ਼ੀ ਦਬਾਅ ਸਮਾਂ, ਜਿਸ ਦੇ ਨਤੀਜੇ ਵਜੋਂ ਕੱਚਾ ਮਾਲ ਗੇਟ ਤੋਂ ਕੈਵਿਟੀ ਤੋਂ ਬਾਹਰ ਨਿਕਲਦਾ ਹੈ।
ਮੋਲਡਿੰਗ ਅਤੇ ਪ੍ਰੈਸ਼ਰ ਹੋਲਡਿੰਗ ਪੜਾਅ ਦੌਰਾਨ ਕੱਚੇ ਮਾਲ ਵਿੱਚ ਕਾਫ਼ੀ ਬਫਰਿੰਗ ਸਮਰੱਥਾ ਨਹੀਂ ਹੁੰਦੀ ਹੈ ਕਿਉਂਕਿ ਬਹੁਤ ਜ਼ਿਆਦਾ ਕੱਚੇ ਮਾਲ ਨੂੰ ਟੀਕੇ ਲਗਾਉਣ ਤੋਂ ਪਹਿਲਾਂ ਪੇਚ ਪੂਰੀ ਤਰ੍ਹਾਂ ਵਾਪਸ ਲੈ ਲਿਆ ਜਾਂਦਾ ਹੈ।
ਗੇਟਾਂ ਅਤੇ ਦੌੜਾਕਾਂ ਦੇ ਕਰਾਸ ਸੈਕਸ਼ਨ ਖੇਤਰ ਉਤਪਾਦਾਂ ਦੀ ਮੋਟਾਈ ਤੋਂ ਬਹੁਤ ਛੋਟੇ ਹੁੰਦੇ ਹਨ, ਜਿਸਦਾ ਮਤਲਬ ਹੈ ਕਿ ਉਤਪਾਦਾਂ ਦੀ ਐਕਸਟਰਿਊਸ਼ਨ ਪ੍ਰਕਿਰਿਆ ਤੋਂ ਪਹਿਲਾਂ ਗੇਟ ਪਹਿਲਾਂ ਹੀ ਜੰਮੇ ਹੋਏ ਹਨ।
ਬੁਲਬਲੇ
ਵੈਕਿਊਮ ਬੁਲਬੁਲੇ ਹਵਾ ਦੇ ਬੁਲਬੁਲੇ ਦੇ ਰੂਪ ਵਿੱਚ ਪੇਸ਼ ਕੀਤੇ ਜਾਂਦੇ ਹਨ, ਜੋ ਪਾਰਦਰਸ਼ੀ ਉਤਪਾਦਾਂ 'ਤੇ ਆਸਾਨੀ ਨਾਲ ਲੱਭੇ ਜਾ ਸਕਦੇ ਹਨ। ਇਹ ਅਪਾਰਦਰਸ਼ੀ ਉਤਪਾਦਾਂ ਦੇ ਕਰਾਸ ਸੈਕਸ਼ਨ 'ਤੇ ਵੀ ਦੇਖਿਆ ਜਾ ਸਕਦਾ ਹੈ।
ਕਾਰਨ:
ਹਵਾ ਦੇ ਬੁਲਬੁਲੇ ਉਤਪਾਦਾਂ ਦਾ ਵੈਕਿਊਮ ਹਿੱਸਾ ਹੁੰਦਾ ਹੈ, ਜੋ ਉਦੋਂ ਪੈਦਾ ਹੁੰਦਾ ਹੈ ਜਦੋਂ ਕੂਲਿੰਗ ਪ੍ਰਕਿਰਿਆ ਦੌਰਾਨ ਕੱਚਾ ਮਾਲ ਸੁੰਗੜ ਜਾਂਦਾ ਹੈ।
ਸੁੰਗੜਨ ਵਾਂਗ ਹੀ, ਕੱਚੇ ਮਾਲ ਦਾ ਅੰਦਰਲਾ ਹਿੱਸਾ ਸੰਕੁਚਨ ਸ਼ਕਤੀ ਪੈਦਾ ਕਰਦਾ ਹੈ। ਫਰਕ ਇਹ ਹੈ ਕਿ ਜਦੋਂ ਬੁਲਬਲੇ ਬਣਦੇ ਹਨ ਤਾਂ ਉਤਪਾਦਾਂ ਦੀ ਬਾਹਰੀ ਦਿੱਖ ਮਜ਼ਬੂਤ ਹੋ ਜਾਂਦੀ ਹੈ, ਅਤੇ ਕੋਈ ਢਹਿ ਨਹੀਂ ਜਾਂਦਾ, ਇਸ ਲਈ ਖੋਖਲੇ ਬੁਲਬੁਲੇ ਪੈਦਾ ਹੁੰਦੇ ਹਨ।
ਬੁਲਬਲੇ ਦੇ ਕਾਰਨ ਕਟੌਤੀ ਦੇ ਸਮਾਨ ਹਨ, ਜਿਸ ਵਿੱਚ ਸ਼ਾਮਲ ਹਨ:
ਅਕੁਸ਼ਲ ਮੋਲਡ ਕੈਵਿਟੀ ਪ੍ਰੈਸ਼ਰ
ਨਾਕਾਫ਼ੀ ਕੈਵਿਟੀ ਪ੍ਰੈਸ਼ਰਾਈਜ਼ੇਸ਼ਨ ਸਮਾਂ
ਦੌੜਾਕ ਅਤੇ ਗੇਟ ਦਾ ਆਕਾਰ ਬਹੁਤ ਛੋਟਾ ਹੈ
ਛਿੜਕਾਅ ਦੇ ਨਿਸ਼ਾਨ
ਛਿੜਕਾਅ ਦੇ ਚਿੰਨ੍ਹ ਗੇਟ ਦੇ ਸਾਹਮਣੇ ਥਰਿੱਡਡ ਖੇਤਰ ਨੂੰ ਦਰਸਾਉਂਦੇ ਹਨ। ਛਿੜਕਾਅ ਦੇ ਚਿੰਨ੍ਹ ਨਾ ਸਿਰਫ਼ ਉਤਪਾਦਾਂ ਦੀ ਦਿੱਖ ਨੂੰ ਪ੍ਰਭਾਵਿਤ ਕਰਦੇ ਹਨ, ਸਗੋਂ ਉਤਪਾਦਾਂ ਦੀ ਤਾਕਤ ਨੂੰ ਵੀ ਪ੍ਰਭਾਵਿਤ ਕਰਦੇ ਹਨ।
ਕਾਰਨ:
ਛਿੜਕਾਅ ਦੇ ਨਿਸ਼ਾਨ ਉੱਲੀ ਭਰਨ ਦੀ ਪ੍ਰਕਿਰਿਆ ਦੌਰਾਨ ਪਿਘਲਣ ਦੇ ਪ੍ਰਵਾਹ ਦੇ ਕੰਟਰੋਲ ਤੋਂ ਬਾਹਰ ਹੋਣ ਕਾਰਨ ਹੁੰਦੇ ਹਨ।
ਪਿਘਲਾ ਹੋਇਆ ਪਲਾਸਟਿਕ ਵੱਡੇ ਦਬਾਅ ਹੇਠ ਉੱਲੀ ਵਿੱਚ ਆ ਜਾਂਦਾ ਹੈ। ਜੇ ਉੱਲੀ ਭਰਨ ਦੀ ਗਤੀ ਬਹੁਤ ਜ਼ਿਆਦਾ ਹੈ, ਤਾਂ ਪਲਾਸਟਿਕ ਮੋਲਡ ਕੈਵਿਟੀ ਦੇ ਖੁੱਲ੍ਹੇ ਪਾੜੇ ਤੋਂ ਬਾਹਰ ਨਿਕਲ ਜਾਵੇਗਾ, ਅਤੇ ਜਲਦੀ ਵਾਪਸ ਅਤੇ ਠੰਡਾ ਹੋ ਜਾਵੇਗਾ। ਉਸ ਸਮੇਂ, ਧਾਗੇ ਬਣਦੇ ਹਨ, ਜੋ ਪਿਘਲੇ ਹੋਏ ਪਲਾਸਟਿਕ ਨੂੰ ਗੇਟਾਂ ਵਿੱਚ ਦਾਖਲ ਹੋਣ ਤੋਂ ਰੋਕਦੇ ਹਨ।
ਛਿੜਕਾਅ ਦੇ ਚਿੰਨ੍ਹ ਦਾ ਮੁੱਖ ਕਾਰਨ ਗੇਟਾਂ ਦੀ ਗਲਤ ਸਥਿਤੀ ਜਾਂ ਗੇਟ ਦਾ ਡਿਜ਼ਾਈਨ ਹੈ। ਹੇਠ ਲਿਖੀਆਂ ਦੋ ਸਥਿਤੀਆਂ ਨੁਕਸ ਦੀ ਸਥਿਤੀ ਨੂੰ ਵਿਗਾੜ ਦੇਣਗੀਆਂ:
ਉੱਚ ਉੱਲੀ ਭਰਨ ਦੀ ਗਤੀ
ਉੱਲੀ ਭਰਨ ਦੌਰਾਨ ਖਰਾਬ ਪਿਘਲਣ ਦਾ ਪ੍ਰਵਾਹ