ਇੰਜੈਕਸ਼ਨ ਮੋਲਡਿੰਗ FAQ
ਕੁਸ਼ਨ ਕੀ ਹੈ ਅਤੇ ਮੈਨੂੰ ਇਸਨੂੰ ਰੱਖਣ ਦੀ ਲੋੜ ਕਿਉਂ ਹੈ
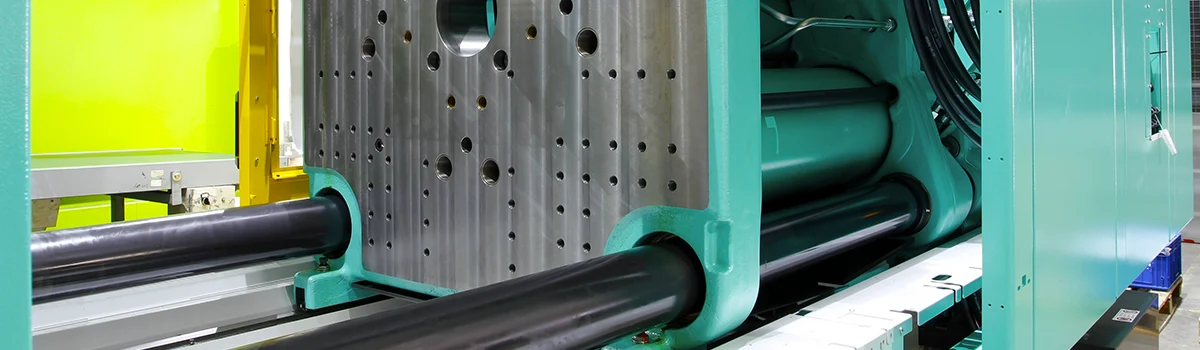
ਇੰਜੈਕਸ਼ਨ ਮੋਲਡਿੰਗ ਦੇ ਬਹੁਤ ਸਾਰੇ ਅਜੀਬ ਆਵਾਜ਼ ਵਾਲੇ ਸ਼ਬਦ ਹਨ. ਭਰਨ ਦਾ ਸਮਾਂ, ਬੈਕ ਪ੍ਰੈਸ਼ਰ, ਸ਼ਾਟ ਦਾ ਆਕਾਰ, ਕੁਸ਼ਨ। ਪਲਾਸਟਿਕ ਜਾਂ ਇੰਜੈਕਸ਼ਨ ਮੋਲਡਿੰਗ ਲਈ ਨਵੇਂ ਲੋਕਾਂ ਲਈ, ਇਹਨਾਂ ਵਿੱਚੋਂ ਕੁਝ ਸ਼ਬਦ ਬਹੁਤ ਜ਼ਿਆਦਾ ਮਹਿਸੂਸ ਕਰ ਸਕਦੇ ਹਨ ਜਾਂ ਤੁਹਾਨੂੰ ਤਿਆਰ ਨਹੀਂ ਮਹਿਸੂਸ ਕਰ ਸਕਦੇ ਹਨ। ਸਾਡੇ ਬਲੌਗ ਦੇ ਟੀਚਿਆਂ ਵਿੱਚੋਂ ਇੱਕ ਹੈ ਨਵੇਂ ਪ੍ਰੋਸੈਸਰਾਂ ਨੂੰ ਉਹਨਾਂ ਸਾਧਨਾਂ ਦੀ ਮਦਦ ਕਰਨਾ ਜੋ ਉਹਨਾਂ ਨੂੰ ਸਫਲ ਹੋਣ ਲਈ ਲੋੜੀਂਦੇ ਹਨ। ਅੱਜ ਅਸੀਂ ਗੱਦੀ 'ਤੇ ਇੱਕ ਨਜ਼ਰ ਮਾਰਾਂਗੇ। ਇਹ ਕੀ ਹੈ, ਅਤੇ “ਇਸ ਨੂੰ ਫੜਨਾ” ਕਿਉਂ ਜ਼ਰੂਰੀ ਹੈ?
ਕੁਸ਼ਨ ਨੂੰ ਸਮਝਣ ਲਈ, ਤੁਹਾਨੂੰ ਮੋਲਡਿੰਗ ਮਸ਼ੀਨਾਂ, ਖਾਸ ਤੌਰ 'ਤੇ ਇੰਜੈਕਸ਼ਨ ਯੂਨਿਟਾਂ ਦੇ ਕਾਰਜਸ਼ੀਲ ਗਿਆਨ ਦੀ ਲੋੜ ਹੈ।
ਇੱਕ ਮੋਲਡਿੰਗ ਪ੍ਰੈਸ ਦੀ ਇੰਜੈਕਸ਼ਨ ਯੂਨਿਟ ਵਿੱਚ ਇੱਕ ਇਲੈਕਟ੍ਰਿਕਲੀ ਗਰਮ ਬੈਰਲ (ਇੱਕ ਲੰਮੀ ਸਿਲੰਡਰ ਵਾਲੀ ਟਿਊਬ) ਹੁੰਦੀ ਹੈ ਜੋ ਇੱਕ ਪਰਸਪਰ ਪੇਚ ਦੇ ਦੁਆਲੇ ਹੁੰਦੀ ਹੈ। ਪਲਾਸਟਿਕ ਦੀਆਂ ਗੋਲੀਆਂ ਨੂੰ ਬੈਰਲ ਦੇ ਇੱਕ ਸਿਰੇ ਵਿੱਚ ਖੁਆਇਆ ਜਾਂਦਾ ਹੈ ਅਤੇ ਜਦੋਂ ਇਹ ਮੋੜਦਾ ਹੈ ਤਾਂ ਪੇਚ ਦੁਆਰਾ ਇਸਦੀ ਲੰਬਾਈ ਨੂੰ ਦੱਸਿਆ ਜਾਂਦਾ ਹੈ। ਪੇਚ ਅਤੇ ਬੈਰਲ ਦੀ ਲੰਬਾਈ ਤੋਂ ਹੇਠਾਂ ਪਲਾਸਟਿਕ ਦੀ ਯਾਤਰਾ 'ਤੇ ਇਸਨੂੰ ਇੱਕ ਗੈਰ-ਰਿਟਰਨ ਵਾਲਵ (ਚੈੱਕ ਰਿੰਗ, ਗੇਂਦ ਦੀ ਜਾਂਚ) ਦੁਆਰਾ ਪਿਘਲਾ, ਸੰਕੁਚਿਤ ਅਤੇ ਜ਼ਬਰਦਸਤੀ ਕੀਤਾ ਜਾਂਦਾ ਹੈ। ਜਿਵੇਂ ਕਿ ਪਿਘਲੇ ਹੋਏ ਪਲਾਸਟਿਕ ਨੂੰ ਨਾਨ-ਰਿਟਰਨ ਵਾਲਵ ਦੇ ਪਾਰ ਧੱਕਿਆ ਜਾਂਦਾ ਹੈ ਅਤੇ ਪੇਚ ਦੀ ਨੋਕ ਦੇ ਸਾਹਮਣੇ ਪਹੁੰਚਾਇਆ ਜਾਂਦਾ ਹੈ, ਪੇਚ ਨੂੰ ਬੈਰਲ ਵਿੱਚ ਵਾਪਸ ਲਿਆ ਜਾਂਦਾ ਹੈ। ਪੇਚ ਦੇ ਸਾਹਮਣੇ ਸਮੱਗਰੀ ਦੇ ਇਸ ਪੁੰਜ ਨੂੰ "ਸ਼ਾਟ" ਕਿਹਾ ਜਾਂਦਾ ਹੈ। ਇਹ ਸਮੱਗਰੀ ਦੀ ਮਾਤਰਾ ਹੈ ਜੋ ਬੈਰਲ ਵਿੱਚੋਂ ਬਾਹਰ ਕੱਢੀ ਜਾਵੇਗੀ ਜੇਕਰ ਪੇਚ ਨੂੰ ਸਾਰੇ ਤਰੀਕੇ ਨਾਲ ਅੱਗੇ ਵਧਾਇਆ ਜਾਂਦਾ ਹੈ।
ਮੋਲਡਿੰਗ ਟੈਕਨੀਸ਼ੀਅਨ ਪੇਚ ਦੇ ਸਟ੍ਰੋਕ ਨੂੰ ਐਡਜਸਟ ਕਰਕੇ ਸ਼ਾਟ ਦੇ ਆਕਾਰ ਨੂੰ ਅਨੁਕੂਲ ਕਰ ਸਕਦਾ ਹੈ. ਇੱਕ ਮੋਲਡਿੰਗ ਪ੍ਰੈਸ ਦੇ ਪੇਚ ਨੂੰ "ਹੇਠਾਂ" ਕਿਹਾ ਜਾਂਦਾ ਹੈ ਜੇਕਰ ਪੇਚ ਪੂਰੀ ਅੱਗੇ ਦੀ ਸਥਿਤੀ ਵਿੱਚ ਹੈ। ਜੇਕਰ ਪੇਚ ਪੂਰੀ ਪਿੱਠ ਵਾਲੀ ਸਥਿਤੀ ਵਿੱਚ ਹੈ ਤਾਂ ਇਸਨੂੰ ਪੂਰੇ ਸਟ੍ਰੋਕ ਜਾਂ ਵੱਧ ਤੋਂ ਵੱਧ ਸ਼ਾਟ ਦੇ ਆਕਾਰ ਵਿੱਚ ਕਿਹਾ ਜਾਂਦਾ ਹੈ। ਇਹ ਆਮ ਤੌਰ 'ਤੇ ਇੰਚ ਜਾਂ ਸੈਂਟੀਮੀਟਰਾਂ ਵਿੱਚ ਇੱਕ ਲੀਨੀਅਰ ਪੈਮਾਨੇ 'ਤੇ ਮਾਪਿਆ ਜਾਂਦਾ ਹੈ ਪਰ ਇਸਨੂੰ ਇੰਚਾਂ ਜਾਂ ਸੈਂਟੀਮੀਟਰਾਂ ਦੀ ਵਰਤੋਂ ਕਰਕੇ ਵੌਲਯੂਮੈਟ੍ਰਿਕ ਤੌਰ 'ਤੇ ਵੀ ਮਾਪਿਆ ਜਾ ਸਕਦਾ ਹੈ।
ਮੋਲਡਿੰਗ ਟੈਕਨੀਸ਼ੀਅਨ ਇਹ ਨਿਰਧਾਰਤ ਕਰਦਾ ਹੈ ਕਿ ਚਲਾਈ ਜਾ ਰਹੀ ਉੱਲੀ ਲਈ ਕਿੰਨੀ ਸ਼ਾਟ ਸਮਰੱਥਾ ਦੀ ਲੋੜ ਹੈ। ਉਦਾਹਰਨ ਲਈ, ਜੇਕਰ ਮੋਲਡ ਕੈਵਿਟੀ ਨੂੰ ਭਰਨ ਅਤੇ ਇੱਕ ਸਵੀਕਾਰਯੋਗ ਹਿੱਸਾ ਪੈਦਾ ਕਰਨ ਲਈ ਲੋੜੀਂਦੇ ਪਲਾਸਟਿਕ ਦੀ ਮਾਤਰਾ 2 ਪੌਂਡ ਹੈ, ਤਾਂ ਟੈਕਨੀਸ਼ੀਅਨ ਪੇਚ ਦੇ ਸਟ੍ਰੋਕ ਨੂੰ ਉਸ ਸਥਿਤੀ ਵਿੱਚ ਸੈੱਟ ਕਰੇਗਾ ਜੋ ਇੱਕ ਥੋੜਾ ਵੱਡਾ ਸ਼ਾਟ ਆਕਾਰ ਪੈਦਾ ਕਰੇਗਾ। 3.5 ਇੰਚ ਸਟ੍ਰੋਕ ਜਾਂ ਸ਼ਾਟ ਦਾ ਆਕਾਰ ਕਹੋ। ਵਧੀਆ ਮੋਲਡਿੰਗ ਅਭਿਆਸਾਂ ਦਾ ਹੁਕਮ ਹੈ ਕਿ ਤੁਸੀਂ ਲੋੜ ਤੋਂ ਥੋੜ੍ਹਾ ਵੱਡਾ ਸ਼ਾਟ ਵਰਤੋ ਤਾਂ ਜੋ ਤੁਸੀਂ ਇੱਕ ਗੱਦੀ ਬਣਾਈ ਰੱਖ ਸਕੋ। ਅੰਤ ਵਿੱਚ, ਅਸੀਂ ਗੱਦੀ ਤੇ ਜਾਂਦੇ ਹਾਂ.
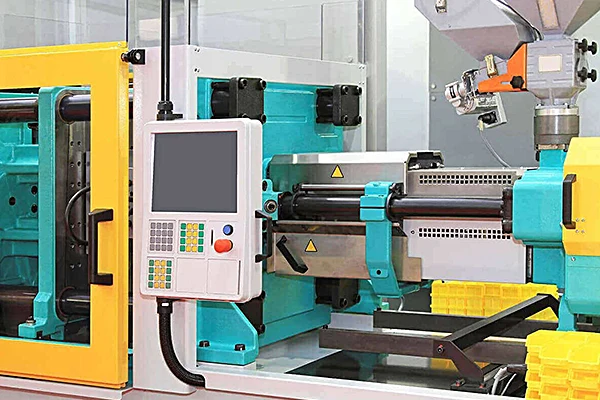
ਵਿਗਿਆਨਕ ਮੋਲਡਿੰਗ ਥਿਊਰੀ ਇਹ ਸਿਫ਼ਾਰਸ਼ ਕਰਦੀ ਹੈ ਕਿ ਇੱਕ ਉੱਲੀ ਨੂੰ ਪਿਘਲੇ ਹੋਏ ਪਲਾਸਟਿਕ ਨਾਲ ਜਿੰਨੀ ਜਲਦੀ ਹੋ ਸਕੇ ਕੁੱਲ ਹਿੱਸੇ ਦੇ ਭਾਰ ਦੇ 90-95% ਤੱਕ ਭਰਿਆ ਜਾਵੇ, ਬਾਕੀ ਦੇ ਭਰੇ ਜਾਣ 'ਤੇ ਵੇਗ ਨੂੰ ਹੌਲੀ ਕਰੋ, ਅਤੇ ਸਥਿਰ ਦਬਾਅ "ਹੋਲਡ" ਪੜਾਅ ਵਿੱਚ ਤਬਦੀਲ ਕਰੋ। ਜਿਵੇਂ ਕਿ ਹਿੱਸਾ ਭਰ ਜਾਂਦਾ ਹੈ ਅਤੇ ਪੈਕ ਕਰਨਾ ਸ਼ੁਰੂ ਕਰਦਾ ਹੈ. ਇਹ ਹੋਲਡ ਪੜਾਅ ਪ੍ਰਕਿਰਿਆ ਦਾ ਇੱਕ ਬਹੁਤ ਮਹੱਤਵਪੂਰਨ ਹਿੱਸਾ ਹੈ. ਇਹ ਉਦੋਂ ਹੁੰਦਾ ਹੈ ਜਦੋਂ ਹਿੱਸੇ ਦੀ ਅੰਤਮ ਪੈਕਿੰਗ ਹੁੰਦੀ ਹੈ ਅਤੇ ਜਦੋਂ ਬਹੁਤ ਜ਼ਿਆਦਾ ਤਾਪ ਮੋਲਡ ਕੀਤੇ ਹਿੱਸੇ ਤੋਂ ਬਾਹਰ ਅਤੇ ਮੋਲਡ ਸਟੀਲ ਵਿੱਚ ਤਬਦੀਲ ਕੀਤਾ ਜਾਂਦਾ ਹੈ। ਹਿੱਸੇ ਨੂੰ ਪੈਕ ਕਰਨ ਲਈ, ਪੇਚ ਦੇ ਸਾਹਮਣੇ ਕਾਫ਼ੀ ਪਿਘਲਾ ਹੋਇਆ ਪਲਾਸਟਿਕ ਬਾਕੀ ਹੋਣਾ ਚਾਹੀਦਾ ਹੈ ਤਾਂ ਜੋ ਰਨਰ ਸਿਸਟਮ ਦੁਆਰਾ ਅਤੇ ਮੋਲਡ ਕੀਤੇ ਹਿੱਸੇ ਦੁਆਰਾ ਹੋਲਡ ਪ੍ਰੈਸ਼ਰ ਨੂੰ ਟ੍ਰਾਂਸਫਰ ਕਰਨ ਦੇ ਯੋਗ ਹੋ ਸਕੇ।
ਇਰਾਦਾ ਹਿੱਸੇ ਦੇ ਵਿਰੁੱਧ ਦਬਾਅ ਨੂੰ ਉਦੋਂ ਤੱਕ ਰੱਖਣ ਦਾ ਹੈ ਜਦੋਂ ਤੱਕ ਇਹ ਢਾਲ ਤੋਂ ਬਾਹਰ ਕੱਢਣ ਵੇਲੇ ਹਿੱਸੇ ਦੇ ਮਾਪ ਅਤੇ ਦਿੱਖ ਨੂੰ ਬਣਾਈ ਰੱਖਣ ਲਈ ਕਾਫੀ ਠੰਡਾ ਨਹੀਂ ਹੋ ਜਾਂਦਾ। ਇਹ ਸਿਰਫ ਪੇਚ ਦੇ ਸਾਹਮਣੇ ਪਲਾਸਟਿਕ ਦੇ ਇੱਕ ਗੱਦੀ ਨਾਲ ਪ੍ਰਾਪਤ ਕੀਤਾ ਜਾ ਸਕਦਾ ਹੈ. ਆਦਰਸ਼ਕ ਤੌਰ 'ਤੇ ਤੁਸੀਂ ਚਾਹੁੰਦੇ ਹੋ ਕਿ ਮਸ਼ੀਨ ਦੇ ਹਰੇਕ ਚੱਕਰ ਤੋਂ ਬਾਅਦ ਬੈਰਲ ਵਿੱਚ ਬਚੀ ਸਮੱਗਰੀ ਦੀ ਮਾਤਰਾ ਨੂੰ ਘੱਟ ਕਰਨ ਲਈ ਤੁਹਾਡਾ ਗੱਦੀ ਛੋਟਾ ਹੋਵੇ। ਕੋਈ ਵੀ ਬਾਕੀ ਸਮੱਗਰੀ ਬੈਰਲ ਵਿੱਚ ਲਗਾਤਾਰ ਗਰਮੀ ਦੇ ਅਧੀਨ ਹੈ ਅਤੇ ਸੰਭਾਵੀ ਤੌਰ 'ਤੇ ਪ੍ਰੋਸੈਸਿੰਗ ਸਮੱਸਿਆਵਾਂ ਜਾਂ ਮਕੈਨੀਕਲ ਵਿਸ਼ੇਸ਼ਤਾਵਾਂ ਦੇ ਨੁਕਸਾਨ ਦਾ ਕਾਰਨ ਬਣ ਸਕਦੀ ਹੈ।
ਨਿਗਰਾਨੀ ਕੁਸ਼ਨ ਤੁਹਾਡੇ ਸਾਜ਼-ਸਾਮਾਨ ਨਾਲ ਸੰਭਾਵੀ ਸਮੱਸਿਆਵਾਂ ਨੂੰ ਦੇਖਣ ਦਾ ਵਧੀਆ ਤਰੀਕਾ ਹੈ। ਇੱਕ ਗੱਦੀ ਜੋ ਲਗਾਤਾਰ ਘਟਦੀ ਰਹਿੰਦੀ ਹੈ ਕਿਉਂਕਿ ਦਬਾਅ ਪੂਰੇ ਹਿੱਸੇ 'ਤੇ ਲਾਗੂ ਹੁੰਦਾ ਹੈ, ਤੁਹਾਡੀ ਪ੍ਰਕਿਰਿਆ ਦੀ ਦੁਹਰਾਉਣਯੋਗਤਾ ਨਾਲ ਸਮੱਸਿਆਵਾਂ ਨੂੰ ਦਰਸਾ ਸਕਦਾ ਹੈ। ਬੈਰਲ ਜਾਂ ਪੇਚ 'ਤੇ ਬਹੁਤ ਜ਼ਿਆਦਾ ਪਹਿਨਣ ਹੋ ਸਕਦੀ ਹੈ। ਗੰਦਗੀ ਦਾ ਕੁਝ ਰੂਪ ਹੋ ਸਕਦਾ ਹੈ ਜੋ ਨਾ-ਵਾਪਸੀ ਵਾਲਵ ਨੂੰ ਸਹੀ ਢੰਗ ਨਾਲ ਬੈਠਣ ਤੋਂ ਰੋਕਦਾ ਹੈ। ਇਹਨਾਂ ਵਿੱਚੋਂ ਕੋਈ ਵੀ ਤੁਹਾਡੇ ਮੋਲਡ ਕੀਤੇ ਹਿੱਸਿਆਂ ਵਿੱਚ ਅਣਚਾਹੇ ਪਰਿਵਰਤਨ ਦਾ ਕਾਰਨ ਬਣੇਗਾ। ਇਹਨਾਂ ਭਿੰਨਤਾਵਾਂ ਦੇ ਨਤੀਜੇ ਵਜੋਂ ਸ਼ਾਰਟਸ, ਸਿੰਕ ਜਾਂ ਹੋਰ ਦਿੱਖ ਮੁੱਦਿਆਂ ਵਾਲੇ ਹਿੱਸੇ ਹੋ ਸਕਦੇ ਹਨ। ਇਹ ਘੱਟ ਪੈਕਿੰਗ ਜਾਂ ਨਾਕਾਫ਼ੀ ਕੂਲਿੰਗ ਦੇ ਕਾਰਨ ਅਯਾਮੀ ਤੌਰ 'ਤੇ ਸਹਿਣਸ਼ੀਲਤਾ ਤੋਂ ਬਾਹਰ ਹੋ ਸਕਦੇ ਹਨ।
ਇਸ ਲਈ, ਯਾਦ ਰੱਖੋ, ਆਪਣੇ ਗੱਦੀ ਵੱਲ ਧਿਆਨ ਦਿਓ. ਇਹ ਤੁਹਾਨੂੰ ਦੱਸੇਗਾ ਕਿ ਤੁਹਾਡੀ ਪ੍ਰਕਿਰਿਆ ਕਿੰਨੀ ਸਿਹਤਮੰਦ ਹੈ।