ਭਾਰਤ ਵਿੱਚ ਕੇਸ
ਭਾਰਤੀ ਕੰਪਨੀਆਂ ਲਈ ਇੰਜੈਕਸ਼ਨ ਮੋਲਡਿੰਗ ਸੇਵਾ ਵਿੱਚ DJmolidng ਦੀ ਇਨਸਰਟ ਮੋਲਡ
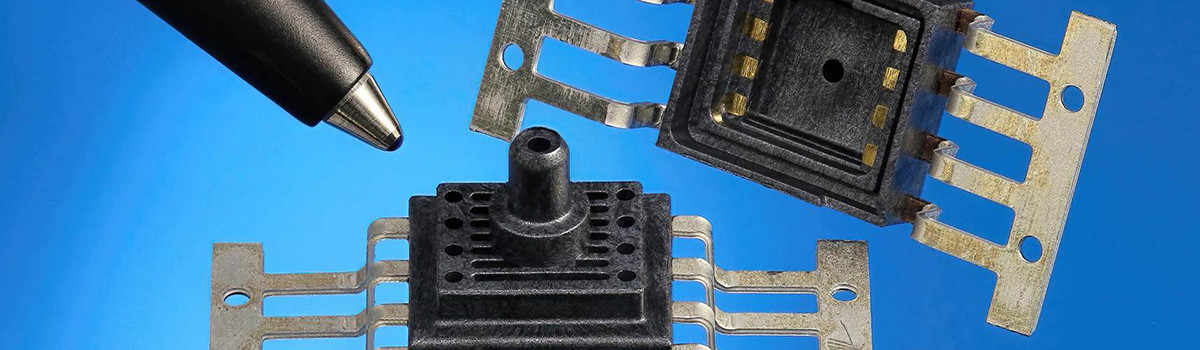
ਇਨਸਰਟ ਮੋਲਡ ਆਮ ਤੌਰ 'ਤੇ ਇੱਕ ਕਿਸਮ ਦਾ ਮੋਲਡ ਹੁੰਦਾ ਹੈ ਜੋ ਨਟ, ਧਾਤ ਦੇ ਹਿੱਸੇ ਜਾਂ ਸਖ਼ਤ ਪਲਾਸਟਿਕ ਦੇ ਹਿੱਸੇ ਨੂੰ ਇੰਜੈਕਸ਼ਨ ਮੋਲਡਿੰਗ ਲਈ ਕੈਵਿਟੀਜ਼ ਦੇ ਅੰਦਰ ਫਿਕਸ ਕਰਦਾ ਹੈ।
ਡੀਜੇਮੋਲਡਿੰਗ ਭਾਰਤ ਦੀ ਮਾਰਕੀਟ ਲਈ ਇਨਸਰਟ ਮਲੋਡ ਇੰਜੈਕਸ਼ਨ ਮੋਲਡਿੰਗ ਸੇਵਾ ਦੀ ਪੇਸ਼ਕਸ਼ ਕਰਦੀ ਹੈ, ਅਤੇ ਅਸੀਂ ਵੱਖ-ਵੱਖ ਉਦਯੋਗਾਂ ਲਈ, ਖਾਸ ਕਰਕੇ ਘਰੇਲੂ ਉਪਕਰਣਾਂ ਦੇ ਨਿਰਮਾਤਾਵਾਂ ਲਈ ਬਹੁਤ ਸਾਰੇ ਇਨਸਰਟ ਮੋਲਡਿੰਗ ਦੇ ਪਲਾਸਟਿਕ ਦੇ ਹਿੱਸੇ ਤਿਆਰ ਕਰਦੇ ਹਾਂ। ਕੁਝ ਭਾਰਤੀ ਘਰੇਲੂ ਉਪਕਰਨਾਂ ਦੇ ਨਿਰਮਾਤਾ ਡੀਜੇ ਮੋਲਡਿੰਗ ਦੇ ਰੂਪ ਵਿੱਚ ਇੰਸਰਟ ਮੋਲਡਿੰਗ ਦੇ ਪਲਾਸਟਿਕ ਦੇ ਹਿੱਸੇ ਲੰਬੇ ਸਮੇਂ ਲਈ ਖਰੀਦਦੇ ਹਨ। ਭਾਰਤ ਦੀਆਂ ਇਨ੍ਹਾਂ ਕੰਪਨੀਆਂ ਨਾਲ ਸਾਡੀ ਬਹੁਤ ਚੰਗੀ ਭਾਈਵਾਲੀ ਹੈ।
ਗਿਰੀਦਾਰ ਇੰਜੈਕਸ਼ਨ ਮੋਲਡਿੰਗ ਪਾਓ: ਗਿਰੀਦਾਰ ਸਮੱਗਰੀ ਸਟੀਲ, ਪਿੱਤਲ, ਕਾਂਸੀ ਅਤੇ ਸਟੀਲ ਹੋ ਸਕਦੀ ਹੈ, ਆਮ ਤੌਰ 'ਤੇ ਤਾਂਬੇ ਦੇ ਗਿਰੀਦਾਰ ਆਮ ਤੌਰ 'ਤੇ ਵਰਤੇ ਜਾਂਦੇ ਹਨ। ਤਾਂਬੇ ਨੂੰ ਘੁੱਟਣਾ ਆਸਾਨ ਹੁੰਦਾ ਹੈ, ਜੋ ਕਿ ਗਿਰੀਦਾਰਾਂ ਅਤੇ ਪਲਾਸਟਿਕ ਨੂੰ ਚੰਗੀ ਤਰ੍ਹਾਂ ਵੰਡਣ ਵਿੱਚ ਮਦਦ ਕਰਦਾ ਹੈ। ਗਿਰੀ ਦੇ ਅੰਦਰਲੇ ਬੋਰਾਂ ਦੀ ਸਹਿਣਸ਼ੀਲਤਾ 0.02mm ਦੇ ਅੰਦਰ ਨਿਯੰਤਰਿਤ ਕੀਤੀ ਜਾਣੀ ਚਾਹੀਦੀ ਹੈ, ਨਹੀਂ ਤਾਂ ਆਸਾਨੀ ਨਾਲ ਫਲੈਸ਼ ਹੋ ਸਕਦੀ ਹੈ ਜੇਕਰ ਸਹਿਣਸ਼ੀਲਤਾ 0.02mm ਤੋਂ ਵੱਧ ਹੈ। ਮੋਲਡ ਫਿਟਿੰਗ ਵਿੱਚ, ਜਾਂਚ ਲਈ ਇਨਸਰਟ ਪਿੰਨ ਵਿੱਚ ਗਿਰੀਆਂ ਨੂੰ ਇਕੱਠਾ ਕਰਨ ਦੀ ਲੋੜ ਹੁੰਦੀ ਹੈ। ਜੇਕਰ ਇਹ ਗਿਰੀਦਾਰਾਂ ਅਤੇ ਪਿੰਨਾਂ ਵਿਚਕਾਰ ਤੰਗ ਫਿਟਿੰਗ ਹੈ, ਤਾਂ ਇਸ ਹਿੱਸੇ ਨੂੰ ਬਾਹਰ ਕੱਢਣਾ ਔਖਾ ਹੋਵੇਗਾ ਅਤੇ ਬਾਹਰ ਕੱਢਣ ਦੇ ਨਿਸ਼ਾਨ ਜਾਂ ਚਿਪਕਣ ਦੀਆਂ ਸਮੱਸਿਆਵਾਂ ਪੈਦਾ ਹੋਣਗੀਆਂ। ਜੇਕਰ ਇਹ ਢਿੱਲੀ ਫਿਟਿੰਗ ਹੈ, ਤਾਂ ਇਹ ਫਲੈਸ਼ ਦਾ ਕਾਰਨ ਬਣੇਗਾ।
ਧਾਤ ਦੇ ਹਿੱਸੇ ਇੰਜੈਕਸ਼ਨ ਮੋਲਡਿੰਗ ਪਾਓ:
ਧਾਤ ਦੇ ਹਿੱਸੇ ਸਟੀਲ, ਅਲਮੀਨੀਅਮ, ਤਾਂਬਾ, ਸਟੀਲ ... ਆਦਿ ਹੋ ਸਕਦੇ ਹਨ। ਧਾਤ ਦੇ ਹਿੱਸਿਆਂ ਦੀ ਸਹਿਣਸ਼ੀਲਤਾ 0.02mm ਦੇ ਅੰਦਰ ਨਿਯੰਤਰਿਤ ਕੀਤੀ ਜਾਣੀ ਚਾਹੀਦੀ ਹੈ, ਨਹੀਂ ਤਾਂ ਸਮੱਗਰੀ ਨੂੰ ਸੀਲ ਕਰਨਾ ਔਖਾ ਹੈ ਅਤੇ ਫਲੈਸ਼ ਹੋਣਾ ਆਸਾਨ ਹੈ। ਧਾਤ ਦੇ ਹਿੱਸਿਆਂ ਦਾ ਰਕਬਾ ਬਹੁਤ ਵੱਡਾ ਡਿਜ਼ਾਈਨ ਨਹੀਂ ਕੀਤਾ ਜਾ ਸਕਦਾ ਹੈ।
ਜੇ ਧਾਤ ਦੇ ਹਿੱਸਿਆਂ ਲਈ ਭਰਾਈ ਦਾ ਰਕਬਾ ਬਹੁਤ ਵੱਡਾ ਹੈ, ਤਾਂ ਧਾਤ ਦੇ ਹਿੱਸਿਆਂ ਦੇ ਵਿਚਕਾਰ ਤਾਪਮਾਨ ਦੇ ਬਹੁਤ ਅੰਤਰ ਦੇ ਰੂਪ ਵਿੱਚ ਪੂਰੀ ਤਰ੍ਹਾਂ ਇੰਜੈਕਸ਼ਨ ਪ੍ਰਾਪਤ ਕਰਨਾ ਬਹੁਤ ਮੁਸ਼ਕਲ ਹੋਵੇਗਾ। ਧਾਤ ਦੇ ਹਿੱਸਿਆਂ ਦੀਆਂ ਸਥਿਤੀਆਂ ਨੂੰ ਆਮ ਤੌਰ 'ਤੇ ਕੈਵਿਟੀ ਵਿੱਚ ਡਿਜ਼ਾਈਨ ਕੀਤਾ ਜਾਂਦਾ ਹੈ ਕਿਉਂਕਿ ਕੈਵਿਟੀ ਹਿੱਲਦੀ ਨਹੀਂ ਹੈ, ਜੋ ਧਾਤ ਦੇ ਹਿੱਸਿਆਂ ਦੇ ਹਿੱਲਣ ਵਿੱਚ ਡਿੱਗਣ ਦੇ ਫਲੈਸ਼ ਨਤੀਜੇ ਤੋਂ ਬਚਣ ਵਿੱਚ ਮਦਦ ਕਰਦੀ ਹੈ (ਗੰਭੀਰ ਸਥਿਤੀ ਵਿੱਚ, ਉੱਲੀ ਨੂੰ ਨੁਕਸਾਨ ਪਹੁੰਚਾ ਸਕਦੀ ਹੈ)। ਖਾਸ ਮਾਮਲਿਆਂ ਵਿੱਚ, ਧਾਤ ਦੇ ਹਿੱਸਿਆਂ ਦੀਆਂ ਸਥਿਤੀਆਂ ਨੂੰ ਉਤਪਾਦ ਦੀ ਕੋਰ ਜਾਂ ਸਾਈਡ ਸਤਹ ਵਿੱਚ ਹੀ ਡਿਜ਼ਾਈਨ ਕੀਤਾ ਜਾ ਸਕਦਾ ਹੈ।
ਹਾਰਡ ਪਲਾਸਟਿਕ ਇੰਜੈਕਸ਼ਨ ਮੋਲਡਿੰਗ ਪਾਓ:
ਆਮ ਤੌਰ 'ਤੇ ਉੱਚ ਪਿਘਲਣ ਵਾਲੇ ਬਿੰਦੂ ਵਾਲੇ ਸਖ਼ਤ ਪਲਾਸਟਿਕ ਦੀ ਚੋਣ ਕਰੋ, ਜਿਵੇਂ ਕਿ PEEK, PA66+30GF, PP+30GF, PA12+30GF, PPS….ਆਦਿ। ਇਹਨਾਂ ਸਖ਼ਤ ਪਲਾਸਟਿਕ ਲਈ ਸਹਿਣਸ਼ੀਲਤਾ ਸਹੀ ਹੋਣੀ ਚਾਹੀਦੀ ਹੈ। ਸੀਲਿੰਗ ਖੇਤਰ ਵਿੱਚ ਸੁੰਗੜਨ, ਡੈਂਟ ਅਤੇ ਵਿਗਾੜ ਵਰਗੇ ਨੁਕਸ ਮੌਜੂਦ ਨਹੀਂ ਹੋ ਸਕਦੇ ਹਨ। ਮੋਲਡ ਫਿਟਿੰਗ ਵਿੱਚ, ਸਖ਼ਤ ਪਲਾਸਟਿਕ ਨੂੰ ਜਾਂਚ ਲਈ ਮੋਲਡ ਦੇ ਅੰਦਰ ਰੱਖਿਆ ਜਾਣਾ ਚਾਹੀਦਾ ਹੈ, ਅਤੇ ਬਿਹਤਰ ਸੀਲਿੰਗ ਪ੍ਰਾਪਤ ਕਰਨ ਲਈ ਸੀਲਿੰਗ ਖੇਤਰ ਦੇ ਦੁਆਲੇ 0.05-0.1mm ਪਹਿਲਾਂ ਤੋਂ ਦਬਾ ਕੇ ਛੱਡ ਦੇਣਾ ਚਾਹੀਦਾ ਹੈ।
ਸਖ਼ਤ ਪਲਾਸਟਿਕ ਦੇ ਹਿੱਸੇ ਨੂੰ ਬਹੁਤ ਜ਼ਿਆਦਾ ਰਕਬੇ ਵਿੱਚ ਡਿਜ਼ਾਈਨ ਨਹੀਂ ਕੀਤਾ ਜਾਣਾ ਚਾਹੀਦਾ ਹੈ, ਜਿਸ ਨਾਲ ਤਾਪਮਾਨ ਵਿੱਚ ਅੰਤਰ ਹੋਵੇਗਾ ਅਤੇ ਇੰਜੈਕਸ਼ਨ ਵਿੱਚ ਸਮੱਗਰੀ ਨੂੰ ਭਰਨਾ ਮੁਸ਼ਕਲ ਹੋ ਜਾਵੇਗਾ। ਆਮ ਤੌਰ 'ਤੇ ਸਖ਼ਤ ਪਲਾਸਟਿਕ ਦੇ ਹਿੱਸੇ ਨੂੰ ਕੈਵਿਟੀ ਦੇ ਪਾਸੇ ਵਿੱਚ ਫਿਕਸ ਕਰੋ, ਕਿਉਂਕਿ ਕੈਵਿਟੀ ਨਹੀਂ ਹਿੱਲਦੀ, ਫਲੈਸ਼ ਤੋਂ ਬਚਣ ਲਈ ਜਾਂ ਉੱਲੀ ਹਿਲਾਉਣ ਵਿੱਚ ਨੁਕਸਾਨਦੇਹ ਉੱਲੀ ਤੋਂ ਬਚਣ ਲਈ। ਖਾਸ ਮਾਮਲਿਆਂ ਵਿੱਚ, ਧਾਤ ਦੇ ਹਿੱਸਿਆਂ ਦੀਆਂ ਸਥਿਤੀਆਂ ਨੂੰ ਉਤਪਾਦ ਦੀ ਕੋਰ ਜਾਂ ਪਾਸੇ ਦੀ ਸਤ੍ਹਾ ਵਿੱਚ ਹੀ ਡਿਜ਼ਾਈਨ ਕੀਤਾ ਜਾ ਸਕਦਾ ਹੈ।
ਮੁੱਖ ਨੁਕਤੇ ਡਿਜ਼ਾਈਨ ਕਰੋ
1. ਨਟਸ ਇਨਸਰਟਸ ਵਾਲੇ ਉਤਪਾਦਾਂ ਲਈ ਡਿਜ਼ਾਇਨ ਸੰਕੁਚਨ, ਜਦੋਂ ਕਿ ਮੈਟਲ ਪਾਰਟਸ ਅਤੇ ਹਾਰਡ ਪਲਾਸਟਿਕ ਇਨਸਰਟਸ ਵਾਲੇ ਉਤਪਾਦਾਂ ਲਈ ਡਿਜ਼ਾਈਨ ਸੁੰਗੜਨ ਦੀ ਕੋਈ ਲੋੜ ਨਹੀਂ ਹੈ। ਉਹਨਾਂ ਖੇਤਰਾਂ ਲਈ ਜਿਨ੍ਹਾਂ ਨੂੰ ਸਖਤ ਸਹਿਣਸ਼ੀਲਤਾ ਦੀ ਲੋੜ ਹੈ, ਉਤਪਾਦਾਂ ਦੇ ਆਕਾਰ ਦੀ ਸਹਿਣਸ਼ੀਲਤਾ ਨੂੰ ਮੱਧਮਾਨ ਵਿੱਚ ਸੋਧੋ।
2. ਆਮ ਤੌਰ 'ਤੇ ਮੋਲਡ ਡਿਜ਼ਾਈਨਿੰਗ ਵਿੱਚ ਸਟੈਂਡਰਡ ਪਿੰਨ-ਪੁਆਇੰਟ ਗੇਟ ਦੇ ਨਾਲ ਮੋਲਡ ਬੇਸ ਨੂੰ ਅਪਣਾਓ, ਅਤੇ ਸੈਕੰਡਰੀ ਇੰਜੈਕਸ਼ਨ ਵਿੱਚ, ਜਿੰਨਾ ਸੰਭਵ ਹੋ ਸਕੇ ਕੈਵਿਟੀ ਵਿੱਚ ਪਾਓ। ਇਨਸਰਟਸ ਨੂੰ ਕੈਵਿਟੀ ਵਿਚ ਫਿਕਸ ਕਰਨ ਦੀ ਸਥਿਤੀ 'ਤੇ, ਵਿਚਾਰ ਕਰੋ ਕਿ ਇੰਜੈਕਸ਼ਨ ਮੋਲਡਿੰਗ ਤੋਂ ਬਾਅਦ ਕੋਰ ਵਿਚ ਖੱਬੇ ਹਿੱਸੇ ਨੂੰ ਕਿਵੇਂ ਬਣਾਇਆ ਜਾਵੇ, ਇਸ ਤਰੀਕੇ ਨਾਲ, ਹਿੱਸੇ ਨੂੰ ਬਾਹਰ ਕੱਢਿਆ ਜਾ ਸਕਦਾ ਹੈ। ਆਮ ਤੌਰ 'ਤੇ ਖੋਲ ਵਿੱਚ ਲਚਕੀਲੇ ਬਲਾਕ ਅਤੇ ਲਚਕੀਲੇ ਗੂੰਦ ਨੂੰ ਜੋੜੋ ਤਾਂ ਜੋ ਹਿੱਸੇ ਨੂੰ ਕੋਰ ਵਿੱਚ ਠਹਿਰਾਇਆ ਜਾ ਸਕੇ। ਲਚਕੀਲੇ ਬਲਾਕਾਂ ਅਤੇ ਗੂੰਦ ਵਿਚਕਾਰ ਦੂਰੀ ਬਹੁਤ ਜ਼ਿਆਦਾ ਨਹੀਂ ਹੋ ਸਕਦੀ, ਨਹੀਂ ਤਾਂ ਲਚਕੀਲੇ ਬਲ ਸਖ਼ਤ ਪਲਾਸਟਿਕ ਜਾਂ ਧਾਤ ਦੇ ਹਿੱਸਿਆਂ ਦੇ ਵਿਗਾੜ ਦਾ ਕਾਰਨ ਬਣੇਗਾ। ਦੂਰੀ ਨੂੰ ਆਮ ਤੌਰ 'ਤੇ 2mm ਦੇ ਅੰਦਰ ਡਿਜ਼ਾਇਨ ਕੀਤਾ ਜਾਂਦਾ ਹੈ, ਅਤੇ ਜਦੋਂ ਧਾਤੂ ਜਾਂ ਸਖ਼ਤ ਪਲਾਸਟਿਕ ਦੇ ਸੰਮਿਲਨਾਂ ਵਿੱਚ ਮੁਕਾਬਲਤਨ ਵੱਡਾ ਰਕਬਾ ਹੁੰਦਾ ਹੈ ਤਾਂ ਲਚਕੀਲੇ ਬਲਾਕਾਂ ਅਤੇ ਲਚਕੀਲੇ ਗੂੰਦ ਦੀ ਮਾਤਰਾ ਨੂੰ ਉਚਿਤ ਢੰਗ ਨਾਲ ਵਧਾਉਂਦਾ ਹੈ।
3. ਸਮੱਗਰੀ ਦੀ ਮੋਟਾਈ 1.3-1.8mm ਦੇ ਅੰਦਰ ਸਭ ਤੋਂ ਵਧੀਆ ਹੈ (ਲਗਭਗ 1.5mm ਸਭ ਤੋਂ ਵਧੀਆ ਹੈ), ਜੇਕਰ ਨਹੀਂ, ਤਾਂ ਉਤਪਾਦ ਦੀਆਂ ਡਰਾਇੰਗਾਂ ਦੀ ਜਾਂਚ ਕਰਨ ਅਤੇ ਗਾਹਕ ਨੂੰ ਇਸ ਨੂੰ ਸੋਧਣ ਦਾ ਸੁਝਾਅ ਦੇਣ ਦੀ ਲੋੜ ਹੈ। ਜੇ ਸਮੱਗਰੀ ਦੀ ਮੋਟਾਈ 1.3mm ਤੋਂ ਪਤਲੀ ਹੈ, ਤਾਂ ਇਹ ਸਮੱਗਰੀ ਭਰਨ ਲਈ ਔਖਾ ਹੈ, ਜਦੋਂ ਕਿ ਸਮੱਗਰੀ ਦੀ ਮੋਟਾਈ 1.8mm ਤੋਂ ਮੋਟੀ ਹੈ, ਉਤਪਾਦਨ ਵਿੱਚ ਸੁੰਗੜਨਾ ਆਸਾਨ ਹੈ।
4. ਮੋਲਡ ਵਿੱਚ ਗੇਟਿੰਗ ਬਹੁਤ ਮਹੱਤਵਪੂਰਨ ਹੈ। ਗੇਟ ਪੁਆਇੰਟ ਲਈ ਸਮੱਗਰੀ ਭਰਨ ਦੇ ਸੰਤੁਲਨ ਨੂੰ ਪੂਰੀ ਤਰ੍ਹਾਂ ਵਿਚਾਰਿਆ ਜਾਣਾ ਚਾਹੀਦਾ ਹੈ। ਜਦੋਂ ਸਮੱਗਰੀ ਉਸ ਖੇਤਰ ਵਿੱਚ ਚਲਦੀ ਹੈ ਜਿੱਥੇ ਧਾਤ ਜਾਂ ਸਖ਼ਤ ਪਲਾਸਟਿਕ ਦੇ ਹਿੱਸੇ ਫਿਕਸ ਕੀਤੇ ਗਏ ਹਨ, ਤਾਂ ਸਮੱਗਰੀ ਭਰਨ ਦੀ ਗਤੀ ਅਤੇ ਦਬਾਅ ਘੱਟ ਜਾਵੇਗਾ ਕਿਉਂਕਿ ਸੰਮਿਲਨ ਪ੍ਰਤੀਰੋਧ ਅਤੇ ਤਾਪਮਾਨ ਵਿੱਚ ਅੰਤਰ ਹੈ।
5. ਮੋਲਡ ਈਜੇਕਟਰ ਸਿਸਟਮ ਲਈ, ਬਾਹਰ ਕੱਢਣ ਦੇ ਸੰਤੁਲਨ ਨੂੰ ਵਿਚਾਰਿਆ ਜਾਣਾ ਚਾਹੀਦਾ ਹੈ ਜਾਂ ਬਾਹਰ ਕੱਢਣ ਤੋਂ ਬਾਅਦ ਵਿਗਾੜ ਹੋਵੇਗਾ। ਭਾਗਾਂ ਨੂੰ ਸੰਤੁਲਨ ਵਿੱਚ ਬਾਹਰ ਨਹੀਂ ਕੱਢਿਆ ਜਾ ਸਕਦਾ ਹੈ, ਇਸ ਲਈ ਢਾਂਚਾ ਡਿਜ਼ਾਈਨ ਵਿੱਚ ਸੰਤੁਲਨ ਦੀ ਸਮੱਸਿਆ ਨੂੰ ਸੁਧਾਰਨ ਲਈ ਢਹਿਣ 'ਤੇ ਵਿਚਾਰ ਕਰਨ ਦੀ ਲੋੜ ਹੈ।
6. ਇੰਜੈਕਸ਼ਨ ਮੋਲਡਿੰਗ ਵਿੱਚ ਬਾਹਰ ਕੱਢਣ ਤੋਂ ਬਾਅਦ ਭਾਗਾਂ ਦੀ ਦਿੱਖ ਦੀ ਯੋਗਤਾ ਨੂੰ ਯਕੀਨੀ ਬਣਾਉਣ ਲਈ, ਈਜੇਕਟਰ ਯੰਤਰ ਨੂੰ ABS ਜਾਂ PMMA ਦੇ ਨਾਲ ਸਖ਼ਤ ਪਲਾਸਟਿਕ ਦਾ ਗੰਢ ਹੋਣਾ ਚਾਹੀਦਾ ਹੈ। ਜੇਕਰ ਉੱਲੀ ਵਿੱਚ ਸਲਾਈਡ ਸੀਲਿੰਗ ਹੈ, ਤਾਂ ਜਿੰਨਾ ਸੰਭਵ ਹੋ ਸਕੇ ਕੈਵਿਟੀ ਵਿੱਚ ਸਲਾਈਡਾਂ ਨੂੰ ਡਿਜ਼ਾਈਨ ਕਰੋ, ਕਿਉਂਕਿ ਕੈਵਿਟੀ ਵਿੱਚ ਸਲਾਈਡ ਮੋਲਡ ਫਿਟਿੰਗ ਦੀ ਸਹੂਲਤ ਦਿੰਦੀਆਂ ਹਨ।
7. ਸੀਲਿੰਗ SA (ਸੀਮ ਭੱਤਾ) ਦੀ ਤਾਕਤ ਨੂੰ ਯਕੀਨੀ ਬਣਾਉਣ ਲਈ, ਦੋ ਵਾਰ ਇੰਜੈਕਸ਼ਨ ਮੋਲਡਿੰਗ ਤੋਂ ਬਣੇ ਉਤਪਾਦ ਲਈ, ਸੀਲਿੰਗ SA ਦੀ ਚੌੜਾਈ ਘੱਟੋ-ਘੱਟ 0.8mm ਹੋਣੀ ਚਾਹੀਦੀ ਹੈ। ਸੈਕੰਡਰੀ ਇੰਜੈਕਸ਼ਨ ਸਮੱਗਰੀ ਲਈ ਸਖ਼ਤ ਪਲਾਸਟਿਕ ਹੈ, ਸੀਲਿੰਗ SA ਦੀ ਚੌੜਾਈ ਘੱਟੋ-ਘੱਟ 1.0mm ਹੋਣੀ ਚਾਹੀਦੀ ਹੈ, ਨਹੀਂ ਤਾਂ, ਉਤਪਾਦ ਨੂੰ ਸੋਧਣ ਲਈ ਗਾਹਕ ਨੂੰ ਸੁਝਾਅ ਦੇਣ ਦੀ ਲੋੜ ਹੈ।
8. ਮੋਲਡ ਡਿਜ਼ਾਇਨ ਵਿੱਚ, ਸਾਨੂੰ ਇਹ ਦੇਖਣ ਲਈ ਕਿ ਇਹ ਕਿਸ ਕਿਸਮ ਦੀ ਮਸ਼ੀਨ ਨੂੰ ਅਪਣਾਉਂਦੀ ਹੈ, ਲੰਬਕਾਰੀ ਜਾਂ ਖਿਤਿਜੀ, ਉਤਪਾਦਨ ਲਈ ਇੰਜੈਕਸ਼ਨ ਮੋਲਡਿੰਗ ਮਸ਼ੀਨਾਂ ਨੂੰ ਧਿਆਨ ਵਿੱਚ ਰੱਖਣਾ ਚਾਹੀਦਾ ਹੈ। ਇਹ ਸੁਝਾਅ ਦਿੱਤਾ ਜਾਂਦਾ ਹੈ ਕਿ ਬਹੁਤ ਜ਼ਿਆਦਾ ਕੈਵਿਟੀਜ਼ ਨੂੰ ਡਿਜ਼ਾਈਨ ਨਾ ਕਰੋ, ਖਾਸ ਤੌਰ 'ਤੇ ਠੰਡੇ ਦੌੜਾਕਾਂ ਵਾਲੇ ਉੱਲੀ ਲਈ ਕਿਉਂਕਿ ਬਹੁਤ ਸਾਰੀਆਂ ਕੈਵਿਟੀਜ਼ ਰਨਰ ਨੂੰ ਲੰਬਾ ਬਣਾਉਂਦੀਆਂ ਹਨ, ਸਮੱਗਰੀ ਨੂੰ ਬਰਬਾਦ ਕਰਦੀਆਂ ਹਨ ਅਤੇ ਉੱਚ-ਕੁਸ਼ਲਤਾ ਵਾਲੇ ਟੀਕੇ ਨੂੰ ਪ੍ਰਾਪਤ ਕਰਨ ਲਈ ਨੁਕਸਾਨਦੇਹ ਵੀ ਹੁੰਦੀਆਂ ਹਨ। ਇੰਜੈਕਸ਼ਨ ਮੋਲਡਿੰਗ ਮਸ਼ੀਨ ਨਾਲ ਮੇਲ ਕਰਨ ਲਈ, ਸਾਨੂੰ ਇਸ ਗੱਲ 'ਤੇ ਵਿਚਾਰ ਕਰਨਾ ਚਾਹੀਦਾ ਹੈ ਕਿ ਕੀ ਇਹ ਉਤਪਾਦ ਪ੍ਰਬੰਧਾਂ ਲਈ ਸੰਖੇਪ ਅਤੇ ਵਾਜਬ ਹੈ। ਉਤਪਾਦਾਂ ਨੂੰ ਇਹ ਯਕੀਨੀ ਬਣਾਉਣ ਲਈ ਫਿਕਸ ਕੀਤਾ ਜਾਣਾ ਚਾਹੀਦਾ ਹੈ ਕਿ ਜਦੋਂ ਵੀ ਉਨ੍ਹਾਂ ਨੂੰ ਮੋਲਡ ਵਿੱਚ ਪਾਇਆ ਜਾਂਦਾ ਹੈ ਤਾਂ ਉਤਪਾਦ ਇੱਕੋ ਸਥਿਤੀ ਵਿੱਚ ਹੁੰਦੇ ਹਨ। ਇੱਕ ਹੋਰ ਤਰੀਕਾ ਹੈ ਡਿਜ਼ਾਇਨ ਪ੍ਰਤੀਕ੍ਰਿਆ ਪ੍ਰਣਾਲੀ ਨੂੰ ਚੇਤਾਵਨੀ ਦੇਣ ਲਈ ਜੇਕਰ ਮੋਲਡ ਬੰਦ ਹੋਣ ਤੋਂ ਪਹਿਲਾਂ ਹਿੱਸਾ ਸਹੀ ਥਾਂ 'ਤੇ ਨਹੀਂ ਹੈ, ਜੋ ਮੋਲਡ ਨੂੰ ਬੰਦ ਹੋਣ ਤੋਂ ਰੋਕਣ ਵਿੱਚ ਮਦਦ ਕਰਦਾ ਹੈ। ਇਸ ਤਰ੍ਹਾਂ, ਹਿੱਸੇ ਮੋਲਡ ਵਿੱਚ ਉਸੇ ਸਥਿਤੀ ਵਿੱਚ ਹੁੰਦੇ ਹਨ, ਜੋ ਟੀਕੇ ਮੋਲਡਿੰਗ ਵਿੱਚ ਯੋਗ ਦਰਾਂ ਅਤੇ ਉਤਪਾਦਨ ਕੁਸ਼ਲਤਾ ਨੂੰ ਵਧਾਉਂਦਾ ਹੈ।
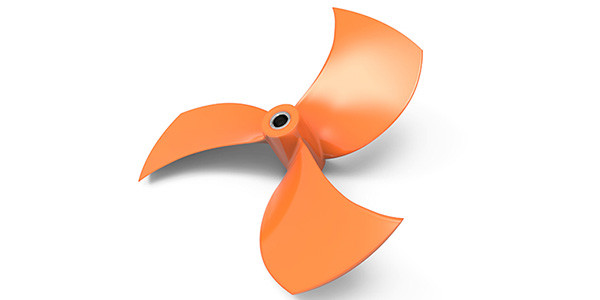
9. ਇੱਕ ਸਟੀਲ ਸਪੋਰਟ ਡਿਜ਼ਾਇਨ ਕੀਤਾ ਜਾਣਾ ਚਾਹੀਦਾ ਹੈ ਕਿਉਂਕਿ ਮੋਲਡ ਇੰਜੈਕਸ਼ਨ ਖੇਤਰ ਟੀਕੇ ਲਗਾਉਣ ਵਿੱਚ ਬਹੁਤ ਦਬਾਅ ਰੱਖਦਾ ਹੈ (ਸ਼ਕਤੀ ਅਤੇ ਆਕਾਰ ਵਿੱਚ ਹਿੱਸੇ ਨਾਲੋਂ 5-10 ਮਿਲੀਮੀਟਰ ਵੱਡਾ ਹੋਣਾ ਚਾਹੀਦਾ ਹੈ)। ਓਵਰ-ਮੋਲਡਿੰਗ ਖੇਤਰ ਦੇ ਆਲੇ ਦੁਆਲੇ ਦੇ ਹਿੱਸਿਆਂ ਦੇ ਵਿਚਕਾਰ ਅੰਤਰ ਨਹੀਂ ਛੱਡਣਾ ਚਾਹੀਦਾ, ਨਹੀਂ ਤਾਂ ਸੈਕੰਡਰੀ ਇੰਜੈਕਸ਼ਨ ਤੋਂ ਬਾਅਦ ਇਹ ਹਿੱਸਾ ਆਕਾਰ ਤੋਂ ਬਾਹਰ ਹੋ ਜਾਵੇਗਾ। SA (ਸੀਮ ਭੱਤੇ) ਤੋਂ ਬਿਨਾਂ ਭਾਗਾਂ ਲਈ ਇਸ ਪਹਿਲੂ 'ਤੇ ਬਹੁਤ ਜ਼ਿਆਦਾ ਧਿਆਨ ਦੇਣ ਦੀ ਲੋੜ ਹੋਵੇਗੀ।
10. ਏਅਰ ਟ੍ਰਿਪ ਅਸਾਨੀ ਨਾਲ ਹੁੰਦਾ ਹੈ ਏਅਰ ਟ੍ਰਿਪ ਇੰਜੈਕਸ਼ਨ ਮੋਲਡਿੰਗ ਵਿੱਚ ਆਸਾਨੀ ਨਾਲ ਹੁੰਦਾ ਹੈ, ਇਸਲਈ ਮੋਲਡ ਡਿਜ਼ਾਈਨਿੰਗ ਵਿੱਚ ਪੂਰੀ ਤਰ੍ਹਾਂ ਵੈਂਟਿੰਗ 'ਤੇ ਵਿਚਾਰ ਕਰਨਾ ਚਾਹੀਦਾ ਹੈ। ਲੰਬੀ-ਦੂਰੀ ਵਾਲੀ ਪਾਣੀ ਦੀ ਲਾਈਨ ਲਈ ਸਾਰੇ ਅੰਨ੍ਹੇ ਕੋਣਾਂ ਅਤੇ ਸਥਿਤੀਆਂ ਵਿੱਚ, ਸਖ਼ਤ ਪਲਾਸਟਿਕ ਵਾਲੇ ਹਿੱਸੇ 'ਤੇ ਵੈਂਟਿੰਗ ਹੋਲ ਡਿਜ਼ਾਈਨ ਕਰਨੇ ਚਾਹੀਦੇ ਹਨ ਕਿਉਂਕਿ ਅੰਨ੍ਹੇ ਕੋਣਾਂ ਵਿੱਚ ਸਮੱਗਰੀ ਨੂੰ ਭਰਨਾ ਵਧੇਰੇ ਮੁਸ਼ਕਲ ਹੁੰਦਾ ਹੈ।
11. ਇਹ ਯਕੀਨੀ ਬਣਾਉਣ ਲਈ ਕਿ ਟੀਕੇ ਵਾਲੀ ਸਮੱਗਰੀ ਅਤੇ ਯੋਗ ਥਰਸਟ ਪੂਰੀ ਤਰ੍ਹਾਂ ਭਰੇ ਹੋਏ ਹਨ, ਇੱਕ ਤਰੀਕਾ ਹੈ ਕਿ ਹਿੱਸੇ ਦੇ ਕੋਨਿਆਂ 'ਤੇ ਇੱਕ ਅੰਡਰਕੱਟ ਡਿਜ਼ਾਈਨ ਕਰਨਾ ਹੈ ਤਾਂ ਜੋ ਚਿਪਕਣ ਵਾਲੇ ਨਤੀਜੇ ਨੂੰ ਵਧਾਇਆ ਜਾ ਸਕੇ ਅਤੇ ਫਿਰ ਹਿੱਸਿਆਂ ਨੂੰ ਹੋਰ ਮਜ਼ਬੂਤੀ ਨਾਲ ਚਿਪਕਿਆ ਜਾ ਸਕੇ।
12. ਸੀਲਿੰਗ ਖੇਤਰ ਅਤੇ ਵਿਭਾਜਨ ਲਾਈਨ ਖੇਤਰ ਵਿੱਚ, ਸਾਨੂੰ ਕੈਵਿਟੀ ਅਤੇ ਕੋਰ ਤੋਂ ਡਿਮੋਲਡ ਨਹੀਂ ਕਰਨਾ ਚਾਹੀਦਾ ਹੈ, ਕਿਉਂਕਿ ਮੋਲਡ ਵਿੱਚ ਕਲੈਂਪਿੰਗ ਲਾਈਨਾਂ ਅਤੇ ਡਰਾਫਟ ਡਿਮੋਲਡ ਕਰਨ ਨਾਲ ਮੋਲਡ ਫਿਟਿੰਗ ਵਿੱਚ ਫਲੈਸ਼ ਹੋ ਜਾਵੇਗਾ। LISS-OFF ਦੁਆਰਾ ਡਿਮੋਲਡ ਕਰਨ ਦੀ ਕੋਸ਼ਿਸ਼ ਕਰੋ।
ਸੰਮਿਲਿਤ ਮੋਲਡ ਦੀਆਂ ਗੇਟ ਪੁਆਇੰਟ ਕਿਸਮਾਂ
ਸੰਮਿਲਿਤ ਮੋਲਡ ਲਈ ਗੇਟ ਪੁਆਇੰਟ ਨੂੰ ਹੌਟ ਸਪ੍ਰੂ ਵਾਲਵ ਗੇਟ, ਹੌਟ ਸਪ੍ਰੂ ਪਿਨ ਗੇਟ, ਪਿੰਨ-ਪੁਆਇੰਟ ਗੇਟ, ਸਬ ਗੇਟ, ਕਿਨਾਰੇ ਗੇਟ… ਆਦਿ ਨੂੰ ਨਿਰਦੇਸ਼ਤ ਕਰਨ ਲਈ ਡਿਜ਼ਾਈਨ ਕੀਤਾ ਜਾ ਸਕਦਾ ਹੈ।
ਗਰਮ ਸਪ੍ਰੂ ਵਾਲਵ ਗੇਟ: ਚੰਗੀ ਤਰਲਤਾ, ਸਥਿਤੀ ਦੀ ਚੋਣ ਲਚਕਦਾਰ, ਛੋਟਾ ਗੇਟ ਪੁਆਇੰਟ। ਵੱਡੇ ਉਤਪਾਦਨ ਲਈ ਅਤੇ ਮੋਟੀ ਕੰਧ ਮੋਟਾਈ ਵਾਲੇ ਉਤਪਾਦਾਂ ਲਈ ਸੂਟ। ਸਮੱਗਰੀ ਨੂੰ ਬਚਾਉਣ ਵਿੱਚ ਮਦਦ ਕਰ ਸਕਦਾ ਹੈ, ਗੇਟ ਲਈ ਕੋਈ ਸਮੱਗਰੀ ਦੀ ਰਹਿੰਦ-ਖੂੰਹਦ, ਛੋਟਾ ਲੀਡ ਟਾਈਮ, ਅਤੇ ਉੱਚ ਗੁਣਵੱਤਾ. ਸਿਰਫ ਨੁਕਸ ਮਾਮੂਲੀ ਗੇਟਿੰਗ ਟਰੇਸ ਹੈ.
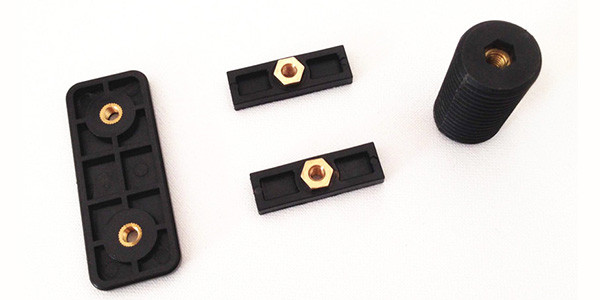
ਗਰਮ ਸਪ੍ਰੂ ਪਿੰਨ ਗੇਟ: ਚੰਗੀ ਤਰਲਤਾ, ਸਥਿਤੀ ਦੀ ਚੋਣ ਲਚਕਦਾਰ, ਛੋਟਾ ਗੇਟ ਪੁਆਇੰਟ। ਵੱਡੇ ਉਤਪਾਦਨ ਲਈ ਅਤੇ ਮੋਟੀ ਕੰਧ ਮੋਟਾਈ ਵਾਲੇ ਉਤਪਾਦਾਂ ਲਈ ਸੂਟ। ਸਮੱਗਰੀ ਨੂੰ ਬਚਾਉਣ ਵਿੱਚ ਮਦਦ ਕਰ ਸਕਦਾ ਹੈ, ਗੇਟ ਲਈ ਕੋਈ ਸਮੱਗਰੀ ਦੀ ਰਹਿੰਦ-ਖੂੰਹਦ, ਛੋਟਾ ਲੀਡ ਟਾਈਮ, ਅਤੇ ਉੱਚ ਗੁਣਵੱਤਾ. ਪਰ ਨੁਕਸ ਹਨ, ਜਿਵੇਂ ਕਿ ਗੇਟ ਪੁਆਇੰਟ ਦੇ ਆਲੇ-ਦੁਆਲੇ 0.1mm ਸਮੱਗਰੀ ਬਚੀ ਹੈ, ਅਤੇ ਬਰਰ ਕਰਨਾ ਆਸਾਨ ਹੈ। ਗੇਟ ਪੁਆਇੰਟ ਦੇ ਆਲੇ-ਦੁਆਲੇ ਖੱਬੀ ਸਮੱਗਰੀ ਨੂੰ ਢੱਕਣ ਲਈ ਟੋਏ ਬਣਾਉਣ ਦੀ ਲੋੜ ਹੈ।
ਪਿੰਨ-ਪੁਆਇੰਟ ਗੇਟ: ਲਚਕਦਾਰ, ਕਮਜ਼ੋਰ ਤਰਲਤਾ, ਲੰਬੀ ਦੌੜ ਦੀ ਦੂਰੀ, ਛੋਟੇ ਗੇਟ ਪੁਆਇੰਟ ਦੀ ਚੋਣ ਕਰਨ ਵਾਲੀ ਸਥਿਤੀ। ਛੋਟੇ ਬੈਚ ਦੇ ਉਤਪਾਦਨ ਲਈ ਸੂਟ. ਗੇਟ ਪੁਆਇੰਟ ਦੇ ਆਲੇ-ਦੁਆਲੇ ਵਧੇਰੇ ਰਹਿੰਦ-ਖੂੰਹਦ ਸਮੱਗਰੀ। ਉਤਪਾਦਨ ਵਿੱਚ ਗੇਟ ਪੁਆਇੰਟ ਨੂੰ ਕਲੈਂਪ ਕਰਨ ਲਈ ਮਕੈਨੀਕਲ ਹਥਿਆਰਾਂ ਦੀ ਲੋੜ ਹੈ। ਲੰਬਾ ਲੀਡ ਟਾਈਮ. ਨੁਕਸ 0.1-0.2mm ਸਮੱਗਰੀ ਹੈ ਜੋ ਗੇਟ ਪੁਆਇੰਟ ਦੇ ਆਲੇ ਦੁਆਲੇ ਬਚੀ ਹੈ, ਗੇਟ ਪੁਆਇੰਟ ਦੇ ਆਲੇ ਦੁਆਲੇ ਖੱਬੀ ਸਮੱਗਰੀ ਨੂੰ ਢੱਕਣ ਲਈ ਗਰੂਵ ਬਣਾਉਣ ਦੀ ਲੋੜ ਹੈ।
ਸਬ ਗੇਟ: ਕੈਵਿਟੀ, ਕੋਰ, ਸਾਈਡ ਵਾਲਾਂ, ਅਤੇ ਇਜੈਕਟਰ ਪਿੰਨਾਂ ਵਿੱਚ ਪੱਸਲੀਆਂ 'ਤੇ ਡਿਜ਼ਾਈਨ ਕੀਤਾ ਜਾ ਸਕਦਾ ਹੈ। ਗੇਟ ਪੁਆਇੰਟ ਨੂੰ ਲਚਕੀਲੇ ਢੰਗ ਨਾਲ ਚੁਣ ਸਕਦਾ ਹੈ, ਡੋਲ੍ਹਣਾ ਗੇਟ ਆਪਣੇ ਆਪ ਹੀ ਹਿੱਸੇ ਤੋਂ ਵੱਖ ਹੋ ਜਾਂਦਾ ਹੈ, ਮਾਮੂਲੀ ਗੇਟਿੰਗ ਟਰੇਸ. ਨੁਕਸ: ਗੇਟ ਪੁਆਇੰਟ ਦੇ ਆਲੇ ਦੁਆਲੇ ਸਮੱਗਰੀ ਨੂੰ ਬਾਹਰ ਕੱਢਣਾ ਆਸਾਨ, ਗੇਟਿੰਗ ਸਥਿਤੀ ਵਿੱਚ ਸੁਕਾਉਣ ਦੇ ਨਿਸ਼ਾਨ ਪੈਦਾ ਕਰਨਾ ਆਸਾਨ, ਹੱਥਾਂ ਨਾਲ ਸਮੱਗਰੀ ਨੂੰ ਪੂੰਝਣ ਦੀ ਲੋੜ ਹੈ, ਗੇਟ ਪੁਆਇੰਟ ਤੋਂ ਕੈਵਿਟੀਜ਼ ਤੋਂ ਬਹੁਤ ਜ਼ਿਆਦਾ ਦਬਾਓ ਨੁਕਸਾਨ।
ਕਿਨਾਰੇ ਗੇਟ: ਪਿਘਲੇ ਹੋਏ ਪਲਾਸਟਿਕ ਗੇਟ ਰਾਹੀਂ ਵਹਿੰਦੇ ਹਨ, ਪਾਸੇ ਵੱਲ ਬਰਾਬਰ ਨਿਰਧਾਰਤ ਕੀਤੇ ਜਾਂਦੇ ਹਨ, ਤਣਾਅ ਘਟਾਉਂਦੇ ਹਨ; ਹਵਾ ਵਿੱਚ ਦਾਖਲ ਹੋਣ ਦੀ ਸੰਭਾਵਨਾ ਨੂੰ ਘਟਾਓ, ਧਾਰੀਆਂ ਅਤੇ ਬੁਲਬਲੇ ਪੈਦਾ ਕਰਨ ਤੋਂ ਬਚੋ। ਨੁਕਸ: ਡੋਲਣ ਵਾਲਾ ਗੇਟ ਆਪਣੇ ਆਪ ਹੀ ਹਿੱਸੇ ਤੋਂ ਵੱਖ ਨਹੀਂ ਹੋ ਸਕਦਾ, ਹਿੱਸੇ ਦੇ ਕਿਨਾਰਿਆਂ 'ਤੇ ਸਪ੍ਰੂ ਦੇ ਨਿਸ਼ਾਨ ਛੱਡੇ ਜਾਂਦੇ ਹਨ, ਡੋਲ੍ਹਣ ਵਾਲੇ ਗੇਟ ਨੂੰ ਫਲੈਟ ਕਰਨ ਲਈ ਸੰਦਾਂ ਦੀ ਲੋੜ ਹੁੰਦੀ ਹੈ। ਕਿਨਾਰੇ ਦਾ ਗੇਟ ਅਨੁਪਾਤ ਇੰਜੈਕਸ਼ਨ ਅਤੇ ਪ੍ਰੈਸ਼ਰ ਹੋਲਡਿੰਗ ਵਿੱਚ ਮਦਦ ਕਰ ਸਕਦਾ ਹੈ, ਅਤੇ ਇਹ ਪ੍ਰੈਸ਼ਰ ਹੋਲਡ ਕਰਨ ਅਤੇ ਫੀਡਿੰਗ ਲਈ ਵੀ ਵਧੀਆ ਹੈ, ਇਸ ਤਰ੍ਹਾਂ, ਇਹ ਏਅਰ ਲਾਈਨਾਂ, ਵਹਾਅ ਦੇ ਨਿਸ਼ਾਨ... ਆਦਿ ਨੂੰ ਬਿਹਤਰ ਬਣਾਉਣ ਲਈ ਬਿਹਤਰ ਹੈ।
ਸੰਮਿਲਿਤ ਮੋਲਡ ਲਈ ਪ੍ਰੋਸੈਸਿੰਗ ਅਤੇ ਫਿਟਿੰਗ
1. ਪ੍ਰੋਸੈਸਿੰਗ ਤੋਂ ਪਹਿਲਾਂ, ਮੋਲਡ ਦੀ ਪ੍ਰੋਸੈਸਿੰਗ ਤਕਨਾਲੋਜੀ ਦਾ ਕੰਮ ਕਰੋ। ਉੱਚ-ਸ਼ੁੱਧਤਾ ਪ੍ਰੋਸੈਸਿੰਗ ਮਸ਼ੀਨਾਂ, ਹਾਈ-ਸਪੀਡ ਮਸ਼ੀਨ, ਹੌਲੀ-ਫੀਡਿੰਗ NC ਵਾਇਰ ਕੱਟ ਮਸ਼ੀਨ, ਮਿਰਰ EDM (ਇਲੈਕਟ੍ਰਿਕ ਡਿਸਚਾਰਜ ਮਸ਼ੀਨਿੰਗ) ਮਸ਼ੀਨ ਆਦਿ ਦੀ ਚੋਣ ਕਰੋ।
2. ਡਿਜ਼ਾਇਨ 0.05-0.1mm ਪ੍ਰੀ-ਪ੍ਰੈਸਿੰਗ ਦੇ ਸਥਾਨ ਵਿੱਚ ਛੱਡ ਦਿੱਤਾ ਗਿਆ ਹੈ।
3. ਮੋਲਡ ਬੇਸ ਪ੍ਰੋਸੈਸਿੰਗ ਵਿੱਚ ਸ਼ੁੱਧਤਾ ਦੀਆਂ ਜ਼ਰੂਰਤਾਂ ਨੂੰ ਨੋਟ ਕਰੋ, ਮੋਲਡ ਬੇਸ ਪ੍ਰਾਪਤ ਕਰਨ ਤੋਂ ਬਾਅਦ ਸਹਿਣਸ਼ੀਲਤਾ ਦੀ ਜਾਂਚ ਕਰੋ ਅਤੇ ਜੇ ਸਹਿਣਸ਼ੀਲਤਾ ਅਯੋਗ ਹੈ ਤਾਂ ਇਸਦੀ ਵਰਤੋਂ ਨਾ ਕਰੋ।
4. ਮੋਲਡ ਫਿਟਿੰਗ ਲਈ ਮੋਲਡ ਦੇ ਅੰਦਰ ਗਿਰੀਦਾਰ, ਧਾਤ ਦੇ ਹਿੱਸੇ ਅਤੇ ਸਖ਼ਤ ਪਲਾਸਟਿਕ ਦੇ ਹਿੱਸੇ ਪਾਓ। ਜੇਕਰ ਮੋਲਡ ਫਿਟਿੰਗ ਵਿੱਚ ਸਮੱਸਿਆਵਾਂ ਮਿਲਦੀਆਂ ਹਨ, ਤਾਂ ਗਿਰੀਦਾਰਾਂ, ਧਾਤੂ ਦੇ ਹਿੱਸਿਆਂ, ਸਖ਼ਤ ਪਲਾਸਟਿਕ ਦੇ ਹਿੱਸਿਆਂ ਅਤੇ ਮੋਲਡਾਂ ਦੀ ਜਾਂਚ ਕਰੋ ਕਿ ਕਿਹੜਾ ਗਲਤ ਹੈ। ਜਿੱਥੋਂ ਤੱਕ ਸੰਭਵ ਹੋਵੇ ਡਰਾਇੰਗ ਦੇ ਅਨੁਸਾਰ ਭਾਗ ਦੀ ਪ੍ਰਕਿਰਿਆ ਕਰੋ, ਜੋ ਭਵਿੱਖ ਵਿੱਚ ਡੇਟਾ ਨੂੰ ਟਰੇਸ ਕਰਨ ਵਿੱਚ ਮਦਦ ਕਰਦਾ ਹੈ।
5. ਮੋਲਡ ਫਿਟਿੰਗ ਲਈ ਗ੍ਰਾਈਂਡਰ ਦੀ ਵਰਤੋਂ ਨਹੀਂ ਕੀਤੀ ਜਾ ਸਕਦੀ। ਠੀਕ ਕਰਨ ਲਈ ਮਸ਼ੀਨਾਂ ਵੱਲ ਮੁੜੋ ਜਿੱਥੇ ਮੋਲਡ ਫਿਟਿੰਗ ਠੀਕ ਨਹੀਂ ਹੈ।
6. ਟ੍ਰਾਇਲ ਤੋਂ ਪਹਿਲਾਂ ਐਕਸ਼ਨ ਟੈਸਟਿੰਗ ਕਰੋ, ਮਿਸ ਅਸੈਂਬਲਿੰਗ ਅਤੇ ਗਲਤ ਅਸੈਂਬਲਿੰਗ ਤੋਂ ਬਚੋ। ਗਲਤ ਅਸੈਂਬਲਿੰਗ ਮੋਲਡ ਬੇਸ ਨੂੰ ਨੁਕਸਾਨ ਪਹੁੰਚਾਏਗੀ।
ਸੰਮਿਲਿਤ ਮੋਲਡ ਲਈ ਮੋਲਡ ਟੈਸਟਿੰਗ
1. ਇੱਕ ਮੋਲਡ ਟੈਸਟਿੰਗ ਵਿੱਚ, ਇੱਕ ਉੱਲੀ ਨੂੰ ਖੋਲ੍ਹਣ, ਬੰਦ ਕਰਨ ਅਤੇ ਬਾਹਰ ਕੱਢਣ ਦੇ ਕ੍ਰਮ ਬਾਰੇ ਸਪਸ਼ਟ ਤੌਰ 'ਤੇ ਜਾਣਨ ਦੀ ਲੋੜ ਹੁੰਦੀ ਹੈ। ਧਾਤ ਦੇ ਹਿੱਸਿਆਂ ਅਤੇ ਸਖ਼ਤ ਪਲਾਸਟਿਕ ਦੇ ਹਿੱਸਿਆਂ ਦੀਆਂ ਸੰਰਚਨਾਤਮਕ ਵਿਸ਼ੇਸ਼ਤਾਵਾਂ ਅਤੇ ਵਿਸ਼ੇਸ਼ਤਾਵਾਂ ਨੂੰ ਸਮਝੋ।
2. ਗਾਹਕ ਨੂੰ ਲੋੜੀਂਦੇ ਨਮੂਨਿਆਂ ਦੀ ਮਾਤਰਾ ਬਾਰੇ ਸਪਸ਼ਟ ਤੌਰ 'ਤੇ ਜਾਣੋ, ਲੋੜੀਂਦੇ ਗਿਰੀਦਾਰ, ਧਾਤ ਦੇ ਹਿੱਸੇ ਅਤੇ ਸਖ਼ਤ ਪਲਾਸਟਿਕ ਤਿਆਰ ਕਰੋ, ਕਿਉਂਕਿ ਇਸ ਨੂੰ ਮੋਲਡ ਟੈਸਟਿੰਗ ਵਿੱਚ ਬਹੁਤ ਸਾਰੇ ਨਮੂਨਿਆਂ ਦੀ ਲੋੜ ਹੁੰਦੀ ਹੈ।
3. ਨੋਟ ਕਰੋ ਕਿ ਕੀ ਗਿਰੀਦਾਰਾਂ, ਧਾਤ ਦੇ ਹਿੱਸਿਆਂ ਜਾਂ ਸਖ਼ਤ ਪਲਾਸਟਿਕ ਦੇ ਸੰਮਿਲਨ ਤੋਂ ਬਿਨਾਂ ਉੱਲੀ ਦੀ ਜਾਂਚ ਕੀਤੀ ਜਾ ਸਕਦੀ ਹੈ। ਜੇਕਰ ਗਿਰੀਦਾਰਾਂ, ਧਾਤ ਦੇ ਹਿੱਸੇ ਅਤੇ ਸਖ਼ਤ ਪਲਾਸਟਿਕ ਨੂੰ ਮੋਲਡ ਵਿੱਚ ਇਕੱਠਾ ਨਹੀਂ ਕੀਤਾ ਜਾਂਦਾ ਹੈ, ਤਾਂ ਹਿੱਸੇ ਵਿੱਚ ਨੁਕਸ ਹੋ ਸਕਦੇ ਹਨ ਜਿਵੇਂ ਕਿ ਉੱਲੀ ਨਾਲ ਚਿਪਕਣਾ ਜਾਂ ਛੋਟਾ ਸ਼ਾਟ।
4. ਬਹੁਤ ਸਾਰੇ ਮਾਮਲਿਆਂ ਵਿੱਚ, ਮੋਲਡ 'ਤੇ ਵਾਟਰਲਾਈਨ ਪਲੇਟ ਨੂੰ ਐਡਜਸਟ ਕਰਨ ਦੀ ਜ਼ਰੂਰਤ ਹੁੰਦੀ ਹੈ, ਪਰ ਕਈ ਵਾਰ ਇਹ ਉਹਨਾਂ ਦੀ ਬਣਤਰ ਦੇ ਅਧਾਰ 'ਤੇ ਕੁਝ ਸੰਮਿਲਿਤ ਮੋਲਡ ਵਿੱਚ ਵਾਟਰ ਲਾਈਨ ਪਲੇਟ ਨੂੰ ਐਡਜਸਟ ਨਹੀਂ ਕਰ ਸਕਦੀ, ਜਾਂ ਇਸ ਤੋਂ ਵੀ ਮਾੜੀ ਗੱਲ ਇਹ ਹੈ ਕਿ ਉੱਲੀ ਬਹੁਤ ਜ਼ਿਆਦਾ ਫਸ ਜਾਂਦੀ ਹੈ ਅਤੇ ਇਸਨੂੰ ਸੋਧਣ ਦੀ ਜ਼ਰੂਰਤ ਹੁੰਦੀ ਹੈ, ਜਾਂ ਉੱਲੀ ਵਿੱਚ ਨੁਕਸਾਨ ਹੁੰਦਾ ਹੈ। ਖੋਲ੍ਹਣਾ
5. ਮੋਲਡ ਟੈਸਟਿੰਗ ਵਿੱਚ ਸਮੱਸਿਆਵਾਂ ਹੋ ਸਕਦੀਆਂ ਹਨ, ਜਿਵੇਂ ਕਿ ਛੋਟੇ ਸ਼ਾਟ, ਏਅਰ ਟ੍ਰਿਪ, ਫਲੈਸ਼, ਜਾਂ ਮੋਲਡ ਨਾਲ ਚਿਪਕਣਾ। ਜੇਕਰ ਕਿਸੇ ਇੰਜੈਕਸ਼ਨ ਮੋਲਡਿੰਗ ਮਸ਼ੀਨ 'ਤੇ ਸਮੱਸਿਆਵਾਂ ਦੀ ਪੁਸ਼ਟੀ ਕੀਤੀ ਜਾ ਸਕਦੀ ਹੈ, ਤਾਂ ਇਸ ਨੂੰ ਹੱਲ ਕਰਨਾ ਬਿਹਤਰ ਹੈ।
DJmolding ਕੋਲ 10+ ਸਾਲਾਂ ਤੋਂ ਵੱਧ ਦਾ ਮੋਲਡਿੰਗ ਦਾ ਤਜਰਬਾ ਹੈ, ਜੇਕਰ ਤੁਹਾਡੇ ਕੋਈ ਸਵਾਲ ਹਨ, ਤਾਂ ਕਿਰਪਾ ਕਰਕੇ ਸਾਡੇ ਨਾਲ ਸੰਪਰਕ ਕਰੋ।