Formowanie wtryskowe termoplastyczne
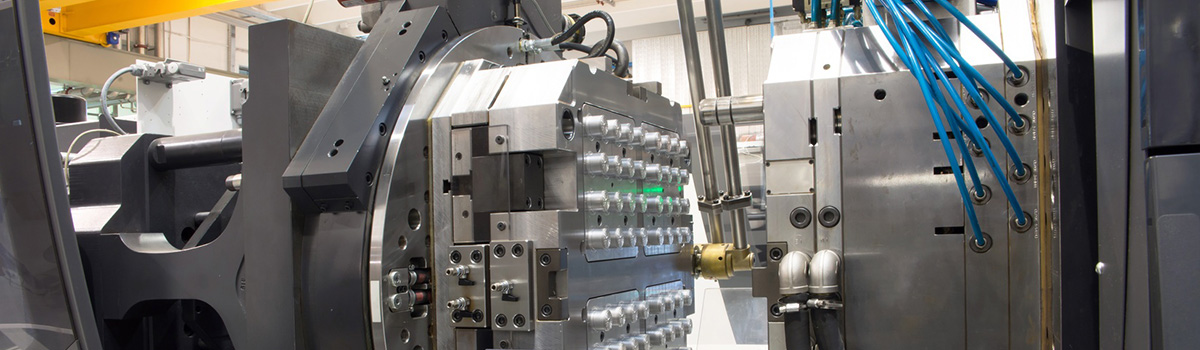
Formowanie wtryskowe tworzyw termoplastycznych jest popularnym procesem produkcyjnym wykorzystywanym do tworzenia różnych części z tworzyw sztucznych dla wielu gałęzi przemysłu. Proces ten polega na stopieniu plastikowych granulek i wstrzyknięciu ich do formy w celu uzyskania trójwymiarowego kształtu. Formowanie wtryskowe tworzyw termoplastycznych jest wysoce wydajne i opłacalne w produkcji dużych ilości wysokiej jakości części z tworzyw sztucznych o wąskich tolerancjach. Ten obszerny przewodnik omawia różne aspekty formowania wtryskowego tworzyw termoplastycznych, w tym jego zalety i wady, rodzaje stosowanych tworzyw termoplastycznych, proces formowania wtryskowego, kwestie projektowe i wiele więcej.
Historia formowania wtryskowego tworzyw termoplastycznych
Historia formowania wtryskowego tworzyw termoplastycznych obejmuje ponad stulecie postępu technologicznego, rozwoju materiałów i zastosowań przemysłowych. Od swoich skromnych początków jako proces formowania celuloidu do współczesnej zaawansowanej technologii, formowanie wtryskowe nadal jest istotną techniką produkcyjną, napędzającą innowacje i kształtującą różne branże.
- Wczesne zmiany:John Wesley Hyatt i jego brat Isaiah opracowali pierwszą praktyczną wtryskarkę, śledząc początki formowania wtryskowego tworzyw termoplastycznych aż do końca XIX wieku. W 19 roku opatentowali urządzenie, które wykorzystywało tłok do wstrzykiwania celuloidu do gniazda formy, tworząc stałe obiekty. Ten przełom położył podwaliny pod nowoczesny proces formowania wtryskowego.
- Postępy w materiałach:Na początku XX wieku wprowadzenie nowych polimerów syntetycznych otworzyło nowe możliwości formowania wtryskowego. Bakelit, żywica fenolowa, stał się popularnym materiałem do formowania ze względu na doskonałe właściwości elektroizolacyjne. W latach trzydziestych i czterdziestych XX wieku postęp w chemii polimerów doprowadził do opracowania innych tworzyw termoplastycznych, takich jak polistyren i polietylen, co dodatkowo rozszerzyło zakres materiałów nadających się do formowania wtryskowego.
- Przyjęcie przemysłowe: Powszechne stosowanie formowania wtryskowego tworzyw termoplastycznych rozpoczęło się w latach pięćdziesiątych XX wieku, gdy producenci uznali jego opłacalność i wszechstronność. Wprowadzenie maszyn wysokociśnieniowych pozwoliło na skrócenie czasu cyklu i zwiększenie wielkości produkcji. W rezultacie powstał różnorodny wybór produktów zarówno do użytku osobistego, jak i przemysłowego. Obejmowały one części samochodowe, sprzęt AGD i zabawki.
- Innowacje technologiczne:Przez dziesięciolecia technologia formowania wtryskowego ewoluowała. W latach 1960. pojawiły się maszyny sterowane komputerowo, umożliwiające precyzyjną kontrolę nad procesem formowania. Wprowadzenie systemów gorących kanałów w latach 1980. zmniejszyło ilość odpadów i poprawiło wydajność, eliminując potrzebę stosowania kanałów i kanałów wlewowych. W ostatnich latach automatyzacja, robotyka i postępy w druku 3D jeszcze bardziej zrewolucjonizowały branżę formowania wtryskowego, umożliwiając złożone projekty i skracając czas produkcji.
- Zrównoważony rozwój i recykling:Wraz z rosnącymi obawami o środowisko branża formowania wtryskowego przyjęła środki na rzecz zrównoważonego rozwoju. Producenci opracowali tworzywa termoplastyczne pochodzenia biologicznego i pochodzące z recyklingu, zmniejszając zależność od materiałów na bazie paliw kopalnych. Ponadto udoskonalone technologie recyklingu umożliwiły ponowne przetwarzanie odpadów poużytkowych i poprzemysłowych, minimalizując wpływ formowania wtryskowego tworzyw termoplastycznych na środowisko.
- Perspektywy na przyszłość:Przyszłość formowania wtryskowego tworzyw termoplastycznych wygląda obiecująco. Branża bada innowacje, takie jak formowanie mikrowtryskowe dla miniaturowych komponentów, techniki wielomateriałowe i overmolding dla złożonych części oraz integracja inteligentnych technologii do monitorowania i optymalizacji procesów. Ponadto naukowcy spodziewają się, że postęp w dziedzinie materiałów biodegradowalnych i wytwarzania przyrostowego zrewolucjonizuje tę dziedzinę, czyniąc formowanie wtryskowe jeszcze bardziej zrównoważonym i wszechstronnym.
Zalety formowania wtryskowego tworzyw termoplastycznych
Formowanie wtryskowe tworzyw termoplastycznych oferuje producentom liczne korzyści. Zapewnia elastyczność projektowania, umożliwiając tworzenie złożonych i skomplikowanych projektów z różnymi funkcjami. Proces jest ekonomiczny, zmniejsza straty materiałowe i obniża koszty jednostkowe. Formowanie wtryskowe tworzyw termoplastycznych obsługuje wiele materiałów, zapewniając wszechstronność w różnych zastosowaniach.
- Elastyczność projektu:Formowanie wtryskowe tworzyw termoplastycznych pozwala na tworzenie skomplikowanych i złożonych projektów z cechami takimi jak podcięcia, cienkie ścianki i różne grubości, zapewniając projektantom ogromną swobodę.
- Efektywność kosztowa: Proces jest bardzo wydajny, zmniejsza straty materiałowe i obniża koszty jednostkowe. Jednoczesne formowanie wielu części i szybkie cykle produkcyjne przyczyniają się do oszczędności kosztów.
- Wszechstronność materiałów: Formowanie wtryskowe tworzyw termoplastycznych obsługuje szeroką gamę materiałów, umożliwiając producentom wybór najbardziej odpowiedniej opcji dla każdego zastosowania, w tym materiałów sztywnych lub elastycznych, przezroczystych lub nieprzezroczystych oraz materiałów odpornych chemicznie.
- Siła i trwałość:Tworzywa termoplastyczne formowane wtryskowo mogą wykazywać doskonałe właściwości mechaniczne, takie jak wysoka wytrzymałość, udarność i odporność na uderzenia. Opcje wzmocnienia, takie jak włókna szklane lub węglowe, dodatkowo poprawiają te właściwości.
- Spójność i jakość:Formowanie wtryskowe zapewnia stałą jakość części i dokładność wymiarową, zapewniając wąskie tolerancje i niezawodne produkty. Proces zapewnia również gładkie i jednolite wykończenie powierzchni, eliminując potrzebę dodatkowych operacji wykańczających.
- Skalowalność i masowa produkcja:Formowanie wtryskowe jest skalowalne od małych do dużych ilości, dzięki czemu nadaje się do masowej produkcji. Gdy producenci utworzą formę, mogą produkować duże ilości identycznych części przy minimalnych różnicach.
- Integracja i montaż:Części formowane wtryskowo mogą zawierać wiele komponentów w jednym kawałku, zmniejszając potrzebę dodatkowych procesów montażowych. Ta integracja zwiększa wydajność produktu, skraca czas montażu i obniża koszty.
- Zrównoważony rozwój:Przemysł formowania wtryskowego wykazuje coraz większy nacisk na zrównoważony rozwój. Dostępność materiałów pochodzenia biologicznego i pochodzących z recyklingu pozwala na wytwarzanie produktów przyjaznych dla środowiska. Efektywne wykorzystanie materiałów i możliwość recyklingu tworzyw termoplastycznych przyczyniają się do bardziej ekologicznego procesu produkcyjnego.
Te korzyści sprawiły, że jest to powszechnie stosowana metoda produkcji w różnych gałęziach przemysłu, zapewniająca wysokiej jakości, opłacalne i przyjazne dla środowiska rozwiązania dla złożonych wymagań produktowych.
Wady formowania wtryskowego tworzyw termoplastycznych
Chociaż termoplastyczne formowanie wtryskowe ma wiele zalet, ma też kilka wad. Producenci muszą dokładnie ocenić te czynniki i porównać je z korzyściami, aby określić przydatność formowania wtryskowego tworzyw termoplastycznych do konkretnych zastosowań.
- Wysoka inwestycja początkowa: Uruchomienie operacji formowania wtryskowego tworzyw termoplastycznych wymaga znacznych inwestycji początkowych w projektowanie i wytwarzanie form oraz zakup specjalistycznych maszyn. Koszty związane z tworzeniem form i oprzyrządowania mogą być znaczne, zwłaszcza w przypadku złożonych i skomplikowanych projektów.
- Ograniczenia projektowe: Chociaż formowanie wtryskowe tworzyw termoplastycznych zapewnia elastyczność projektowania, istnieją pewne ograniczenia. Na przykład uzyskanie jednolitej grubości ścianki w całej części może być wyzwaniem, co prowadzi do różnic w rozmieszczeniu materiału i potencjalnych słabości konstrukcyjnych. Ponadto obecność podcięć lub skomplikowanych geometrii może wymagać zastosowania dodatkowych funkcji formy lub operacji wtórnych, co zwiększa koszty i czas produkcji.
- Długie czasy realizacji:Proces projektowania i wytwarzania form do formowania wtryskowego może być czasochłonny, co prowadzi do dłuższego czasu opracowywania produktu. Proces iteracji projektu, produkcja form i testowanie mogą znacznie wydłużyć ogólny harmonogram produkcji, co może nie być odpowiednie dla projektów o napiętych terminach.
- Ograniczenia wyboru materiałów:Chociaż termoplastyczne formowanie wtryskowe obsługuje szeroką gamę materiałów, istnieją pewne ograniczenia i ograniczenia. Niektóre materiały mogą mieć określone wymagania dotyczące przetwarzania lub ograniczoną dostępność, co wpływa na wybory projektowe i wybór materiałów do konkretnego zastosowania.
- Ograniczenia rozmiaru części:Wtryskarki mają ograniczenia rozmiaru, zarówno pod względem fizycznego rozmiaru urządzenia, jak i rozmiaru form, które mogą pomieścić. Produkcja dużych części może wymagać specjalistycznego sprzętu lub alternatywnych metod produkcji.
- Wpływ środowiska:Podczas gdy przemysł dąży do zrównoważonego rozwoju, proces formowania wtryskowego tworzyw termoplastycznych nadal generuje odpady, w tym złom i nadlewki. Właściwa utylizacja i recykling tych materiałów są niezbędne, aby zminimalizować wpływ na środowisko.
- Złożoność optymalizacji procesów:Osiągnięcie optymalnych parametrów procesu formowania wtryskowego tworzyw termoplastycznych może być skomplikowane i czasochłonne. Producenci muszą dokładnie kontrolować i optymalizować temperaturę, ciśnienie, szybkość chłodzenia i czasy cykli, aby zapewnić stałą jakość części i zminimalizować defekty.
Rodzaje tworzyw termoplastycznych stosowanych w formowaniu wtryskowym
To tylko kilka przykładów tworzyw termoplastycznych powszechnie stosowanych w formowaniu wtryskowym. Każdy materiał ma unikalne właściwości, dzięki czemu nadaje się do określonych zastosowań w oparciu o wytrzymałość, elastyczność, odporność chemiczną, przezroczystość i cenę. Producenci powinni wziąć pod uwagę te właściwości i wymagania przy wyborze odpowiedniego tworzywa termoplastycznego do swoich projektów formowania wtryskowego.
- Polipropylen (PP):Polipropylen jest wszechstronnym tworzywem termoplastycznym powszechnie stosowanym w formowaniu wtryskowym. Oferuje doskonałą odporność chemiczną, niską gęstość i dobrą udarność. PP (polipropylen) ma szerokie zastosowanie w opakowaniach, częściach samochodowych, sprzęcie AGD i urządzeniach medycznych.
- Polietylen (PE):Polietylen jest kolejnym szeroko stosowanym tworzywem termoplastycznym w formowaniu wtryskowym. Jest dostępny w różnych formach, takich jak polietylen o dużej gęstości (HDPE) i polietylen o małej gęstości (LDPE). PE zapewnia dobrą odporność chemiczną, wytrzymałość i elastyczność, dzięki czemu nadaje się do produkcji butelek, pojemników i rur.
- Polistyren (PS):Polistyren jest wszechstronnym tworzywem termoplastycznym znanym ze swojej przejrzystości, sztywności i przystępnej ceny. Znajduje powszechne zastosowanie w opakowaniach, towarach konsumpcyjnych i produktach jednorazowego użytku. PS (polistyren) pozwala na szybką obróbkę i zapewnia dobrą stabilność wymiarową, ale może być kruchy i podatny na pękanie naprężeniowe środowiska.
- Akrylonitrylo-butadieno-styren (ABS): ABS jest popularnym tworzywem termoplastycznym znanym ze swojej doskonałej odporności na uderzenia i trwałości. Łączy właściwości akrylonitrylu, butadienu i styrenu, tworząc wszechstronny materiał odpowiedni do produkcji części samochodowych, obudów elektronicznych i zabawek.
- Polichlorek winylu (PVC): PVC jest szeroko stosowanym tworzywem termoplastycznym znanym ze swojej doskonałej odporności chemicznej, trwałości i niskiego kosztu. Może być sztywny lub elastyczny w zależności od składu i zastosowanych dodatków. PVC (polichlorek winylu) znajduje powszechne zastosowanie w budownictwie, izolacji elektrycznej, produktach ochrony zdrowia i opakowaniach.
- Poliwęglan (PC): Poliwęglan jest przezroczystym tworzywem termoplastycznym o niezwykłej odporności na uderzenia i wysoką temperaturę. Znajduje powszechne zastosowanie w zastosowaniach wymagających przejrzystości optycznej, takich jak komponenty samochodowe, hełmy ochronne i wyświetlacze elektroniczne.
- Nylon (poliamid):Nylon to mocne i trwałe tworzywo termoplastyczne znane ze swoich doskonałych właściwości mechanicznych i odporności chemicznej. Znajduje powszechne zastosowanie w zastosowaniach wymagających wysokiej wytrzymałości, takich jak części samochodowe, komponenty przemysłowe i towary konsumpcyjne.
- Politereftalan etylenu (PET):PET jest popularnym tworzywem termoplastycznym do produkcji butelek, pojemników i materiałów opakowaniowych. Zapewnia dobrą przejrzystość, odporność chemiczną i właściwości barierowe, dzięki czemu nadaje się do zastosowań w żywności i napojach.
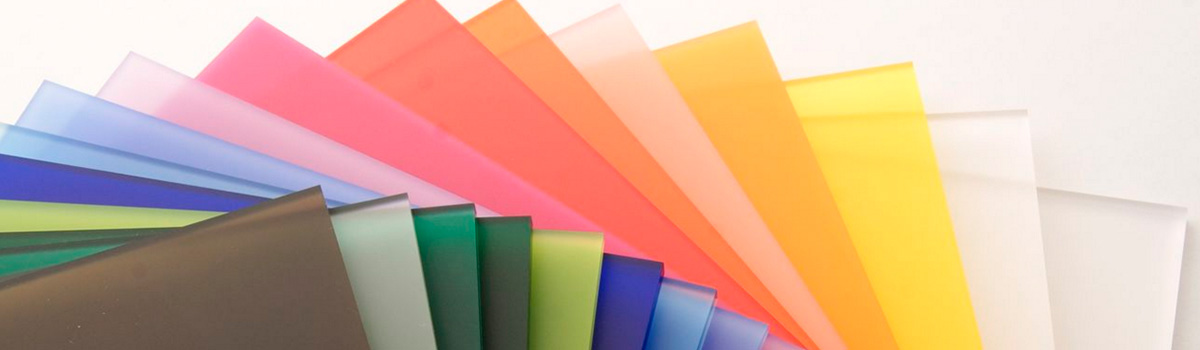
Właściwości tworzyw termoplastycznych stosowanych w formowaniu wtryskowym
Te właściwości tworzyw termoplastycznych odgrywają kluczową rolę w określaniu ich przydatności do określonych zastosowań związanych z formowaniem wtryskowym. Producenci muszą dokładnie rozważyć te właściwości i wybrać odpowiedni materiał termoplastyczny w oparciu o pożądaną wydajność, warunki środowiskowe i wymagania dotyczące kosztów.
- Właściwości mechaniczne:Tworzywa termoplastyczne stosowane w formowaniu wtryskowym mogą wykazywać różne właściwości mechaniczne, w tym wytrzymałość na rozciąganie, udarność i wytrzymałość na zginanie. Te właściwości określają zdolność materiału do wytrzymania przyłożonych sił i jego ogólną trwałość w różnych zastosowaniach.
- Odporność chemiczna:Wiele tworzyw termoplastycznych stosowanych w formowaniu wtryskowym ma niezwykłą odporność na chemikalia, rozpuszczalniki i oleje. Ta właściwość ma kluczowe znaczenie w zastosowaniach, które wiążą się z narażeniem na trudne warunki środowiskowe lub substancje żrące.
- Stabilność termiczna:Stabilność termiczna tworzyw termoplastycznych odnosi się do ich zdolności do wytrzymywania podwyższonych temperatur bez znacznej degradacji. Niektóre tworzywa termoplastyczne wykazują doskonałą odporność na ciepło, dzięki czemu zachowują swoje właściwości mechaniczne nawet w wysokich temperaturach.
- Właściwości elektryczne:Tworzywa termoplastyczne stosowane w formowaniu wtryskowym mogą mieć określone właściwości elektryczne, w tym izolację elektryczną, przewodność lub wytrzymałość dielektryczną. Te właściwości są niezbędne do zastosowań w przemyśle elektrycznym i elektronicznym, gdzie materiały muszą zapewniać niezawodne działanie elektryczne.
- Przejrzystość i przejrzystość:Niektóre tworzywa termoplastyczne, takie jak poliwęglan i PET, zapewniają doskonałą przezroczystość i przejrzystość, dzięki czemu nadają się do zastosowań wymagających właściwości optycznych. Producenci często używają tych materiałów w produktach takich jak przezroczyste okna, soczewki i wyświetlacze.
- Elastyczność i wytrzymałość: Elastyczność i wytrzymałość to podstawowe właściwości tworzyw termoplastycznych stosowanych w zastosowaniach wymagających odporności na uderzenia i trwałości. Niektóre tworzywa termoplastyczne, takie jak ABS i nylon, zapewniają doskonałą wytrzymałość, co pozwala im wytrzymać wielokrotne uderzenia bez pękania.
- Stabilność wymiarowa:Stabilność wymiarowa odnosi się do zdolności tworzywa termoplastycznego do zachowania kształtu i rozmiaru w różnych warunkach, w tym przy zmianach temperatury. Materiały o dobrej stabilności wymiarowej zapewniają spójne wymiary części, minimalizując ryzyko wypaczenia lub zniekształcenia.
- Kompatybilność chemiczna:Kompatybilność chemiczna tworzyw termoplastycznych odnosi się do ich odporności na degradację lub interakcję z różnymi chemikaliami, w tym kwasami, zasadami i rozpuszczalnikami. Aby zapewnić optymalną wydajność, niezbędny jest wybór tworzywa termoplastycznego, które jest w stanie wytrzymać określone środowisko chemiczne, które napotka w zamierzonym zastosowaniu.
- Gęstość: Tworzywa termoplastyczne mają różne grubości, co może wpływać na ich wagę i ogólne właściwości części. Materiały o małej gęstości, takie jak polietylen, zapewniają lekkie rozwiązania, a materiały o dużej gęstości, takie jak polipropylen, zapewniają dodatkową wytrzymałość i sztywność.
Proces formowania wtryskowego: krok po kroku
Proces formowania wtryskowego przebiega zgodnie z tymi etapami, umożliwiając wydajną i precyzyjną produkcję wysokiej jakości części termoplastycznych. Każdy krok wymaga starannej kontroli i monitorowania, aby zapewnić spójne wymiary części, właściwości materiału i ogólną jakość.
- Projektowanie i produkcja form: Pierwszym krokiem w procesie formowania wtryskowego jest zaprojektowanie i wykonanie formy. Producenci muszą stworzyć precyzyjny i szczegółowy projekt formy, aby osiągnąć pożądane specyfikacje części. Następnie producenci wytwarzają formy przy użyciu różnych technik, takich jak obróbka CNC lub obróbka elektroerozyjna (EDM).
- Przygotowanie materiału: Następnym krokiem jest przygotowanie, gdy forma jest gotowa. Pastylki lub granulki termoplastyczne są wybierane na podstawie pożądanych właściwości materiału i topione w zbiorniku. Następnie operatorzy wprowadzają materiał do bębna wtryskarki, gdzie ulega on stopieniu i homogenizacji.
- Wtrysk:Podczas fazy wtrysku operatorzy wtryskują stopione tworzywo termoplastyczne do gniazda formy pod wysokim ciśnieniem. Jednostka wtryskowa maszyny przepycha stopiony materiał przez dyszę do formy. Materiał wypełnia wnękę formy, przyjmując kształt pożądanej części.
- Chłodzenie i zestalanie:Po napełnieniu formy operatorzy pozwalają, aby stopiony plastik ostygł i zestalił się. Chłodzenie ma kluczowe znaczenie dla osiągnięcia stabilności wymiarowej i prawidłowego formowania części. Operatorzy mogą kontrolować proces chłodzenia poprzez cyrkulację chłodziwa w kanałach w formie lub za pomocą płyt chłodzących.
- Otwieranie i wyrzucanie formy:Operatorzy otwierają formę i wyrzucają część z gniazda formy, gdy tworzywo sztuczne stwardnieje. System wyrzucania w maszynie wykorzystuje kołki, płyty wypychaczy lub podmuchy powietrza do usuwania obszaru z formy. Forma jest wtedy gotowa do następnego cyklu wtrysku.
- Przetwarzanie końcowe: Po wyrzuceniu część może zostać poddana obróbce końcowej, takiej jak przycinanie, gratowanie lub wykańczanie powierzchni. Czynności te pomagają usunąć nadmiar materiału, wygładzić ostre krawędzie i poprawić ostateczny wygląd części.
- Kontrola jakości: Ostatnim krokiem jest kontrola jakości wtryskiwanych części i upewnienie się, że spełniają one określone wymagania. W celu sprawdzenia jakości i integralności części można zastosować różne techniki kontroli jakości, w tym pomiar wymiarów, kontrolę wzrokową i testy funkcjonalne.
- Recykling i ponowne wykorzystanie materiałów:Wszelkie nadmiary lub odpady powstające podczas formowania wtryskowego można poddać recyklingowi i ponownie wykorzystać. Ograniczenie użycia nowego materiału termoplastycznego pomaga zminimalizować ilość odpadów i poprawić zrównoważony rozwój.
Sprzęt używany w formowaniu wtryskowym
Te elementy wyposażenia ułatwiają proces formowania wtryskowego, od topienia i wtryskiwania materiału termoplastycznego po kształtowanie, chłodzenie i wyrzucanie gotowej części. Właściwa eksploatacja i konserwacja tych elementów wyposażenia ma kluczowe znaczenie dla osiągnięcia wydajnej, wysokiej jakości produkcji metodą formowania wtryskowego.
- Maszyna do formowania wtryskowego:Podstawowe wyposażenie formowania wtryskowego odpowiada za stopienie materiału termoplastycznego, wtryskiwanie go do formy i kontrolowanie procesu.
- Pleśń: Forma, zaprojektowana na zamówienie w celu uzyskania pożądanego kształtu i cech części z tworzywa sztucznego, składa się z dwóch połówek, wnęki i rdzenia. Operatorzy montują go na jednostce zamykającej wtryskarki.
- Zbiornik:Pojemnik, który przechowuje materiał termoplastyczny w postaci peletek lub granulek i podaje go do bębna wtryskarki w celu stopienia i wtrysku.
- Beczka i śruba: Beczka, cylindryczna komora, topi i homogenizuje materiał termoplastyczny, gdy śruba obraca się w nim w celu stopienia, wymieszania i standaryzacji materiału.
- Systemy ogrzewania i chłodzenia:Wtryskarki posiadają elementy grzejne, takie jak grzałki elektryczne lub grzałki wykorzystujące gorący olej, podnoszące temperaturę cylindra oraz układy chłodzące, takie jak obieg wody lub oleju, w celu schłodzenia formy i zestalenia części z tworzywa sztucznego.
- System wyrzutnika:Usuwa uformowaną część z wnęki formy po zestaleniu, zwykle wykorzystując kołki wypychacza, płyty lub podmuchy powietrza podczas otwierania formy.
- System sterowania:Monitoruje i kontroluje różne parametry procesu formowania wtryskowego, umożliwiając operatorom ustawianie i dostosowywanie parametrów, takich jak prędkość wtrysku, temperatura, ciśnienie i czas chłodzenia.
Maszyny do formowania wtryskowego: rodzaje i charakterystyka
Każdy typ wtryskarki ma swoje cechy i zalety, co pozwala producentom wybrać najbardziej odpowiednie urządzenie do ich specyficznych wymagań produkcyjnych.
- Hydrauliczne wtryskarki: Maszyny te wykorzystują układy hydrauliczne do generowania ciśnienia niezbędnego do wtryskiwania stopionego tworzywa sztucznego do formy. Są znane z dużej siły mocowania, precyzyjnej kontroli i wszechstronności w obsłudze różnych tworzyw termoplastycznych. Maszyny hydrauliczne nadają się do produkcji na dużą skalę i mogą obsługiwać złożone formy.
- Elektryczne maszyny do formowania wtryskowego:Maszyny elektryczne wykorzystują elektryczne serwomotory do obsługi maszyny, w tym systemów wtrysku, zaciskania i wyrzutnika. Oferują precyzyjną kontrolę, efektywność energetyczną i krótszy czas reakcji niż maszyny hydrauliczne. Maszyny elektryczne są idealne do zastosowań związanych z precyzyjnym formowaniem, które wymagają wysokiej powtarzalności i dokładności.
- Wtryskarki hybrydowe:Maszyny hybrydowe łączą zalety urządzeń hydraulicznych i elektrycznych. Wykorzystują kombinację hydraulicznych i elektrycznych układów serwo, aby osiągnąć wysoką precyzję, efektywność energetyczną i opłacalność. Maszyny hybrydowe nadają się do szerokiego zakresu zastosowań, zapewniając równowagę między wydajnością a kosztami operacyjnymi.
- Wtryskarki dwupłytowe: Maszyny dwupłytowe mają unikalną konstrukcję z dwiema oddzielnymi płytami do mocowania formy. Ta konstrukcja zapewnia zwiększoną stabilność, lepszą synchronizację formy i pozwala na większe rozmiary form i większe siły mocowania. Maszyny dwupłytowe nadają się do dużych i złożonych części, które wymagają precyzyjnego formowania.
- Wielokomponentowe wtryskarki:Producenci projektują te maszyny do produkcji części z wielu materiałów lub kolorów w jednym cyklu formowania. Posiadają różne agregaty wtryskowe i formy, umożliwiające jednoczesny wtrysk różnych materiałów. Maszyny wielokomponentowe oferują elastyczność i wydajność w produkcji skomplikowanych części o różnych właściwościach.
- Maszyny do formowania mikrowtryskowego:Zaprojektowane specjalnie do produkcji małych i precyzyjnych części, mikrowtryskiwarki oferują niewiarygodnie wysoką precyzję i dokładność. Mogą wytwarzać skomplikowane detale z wąskimi tolerancjami i minimalnymi stratami materiału. Elektronika, urządzenia medyczne i mikrooptyka powszechnie wykorzystują maszyny do formowania mikrowtrysków.
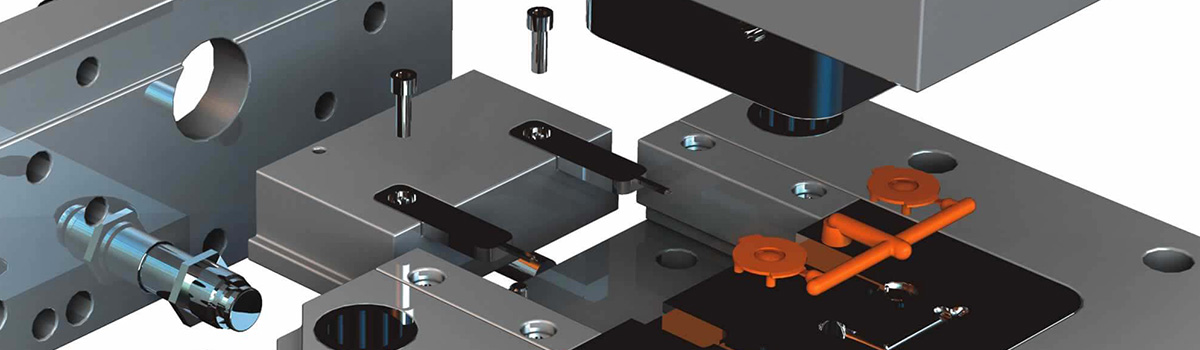
Uwagi dotyczące projektowania form do formowania wtryskowego
Dokładne rozważenie projektu formy jest niezbędne do udanej produkcji metodą formowania wtryskowego.
- Projekt części:Projekt formy powinien uwzględniać specyficzne wymagania części, w tym jej kształt, wymiary i cechy funkcjonalne. Producenci powinni odpowiednio rozważyć kąty pochylenia, grubość ścian, podcięcia i wszelkie niezbędne elementy, aby zapewnić łatwość wyrzucania i jakość części.
- Materiał formy: Wybór materiału formy ma kluczowe znaczenie dla osiągnięcia trwałości, stabilności wymiarowej i odporności na ciepło. Typowe materiały na formy obejmują stopy stali, stopy aluminium i stale narzędziowe. Wybór materiału zależy od czynników, takich jak wielkość produkcji, złożoność części i oczekiwana trwałość narzędzia.
- System chłodzenia:Wydajne chłodzenie jest niezbędne do prawidłowego zestalenia części i zminimalizowania czasu cyklu. Konstrukcja formy powinna obejmować kanały chłodzące lub strategicznie rozmieszczone wkładki, aby zapewnić równomierne chłodzenie formy. Właściwe chłodzenie zmniejsza ryzyko wypaczenia, skurczu i wad części.
- Odpowietrzanie:Konieczne jest odpowiednie odpowietrzenie, aby umożliwić ucieczkę powietrza i gazów podczas procesu wtrysku. Niewystarczające odpowietrzanie może prowadzić do pułapek gazowych, śladów przypaleń lub niepełnego wypełnienia części. Producenci mogą osiągnąć odpowietrzanie poprzez włączenie rowków odpowietrzających, kołków lub innych mechanizmów do konstrukcji formy.
- System wyrzucania:Projekt formy powinien obejmować skuteczny system wyrzucania, aby bezpiecznie i wydajnie usuwać uformowaną część z gniazda formy. System wyrzutnika może składać się ze sworzni wypychacza, tulei lub innych mechanizmów, rozmieszczonych strategicznie, aby uniknąć zakłócenia funkcji lub krytycznych cech.
- Projekt bramy:Brama to miejsce, w którym stopione tworzywo sztuczne wchodzi do gniazda formy. Konstrukcja bramki powinna zapewniać prawidłowe napełnianie części, minimalizować linie przepływu i zapobiegać przedwczesnemu zamarzaniu materiału. Standardowe projekty przewężek obejmują przewężki krawędziowe, przewężki tunelowe i systemy gorących kanałów, w zależności od wymagań części i właściwości materiału.
- Linia podziału:Projekt formy powinien określać odpowiednią linię podziału, czyli linię, w której spotykają się dwie połówki formy. Właściwe umieszczenie linii neutralnej zapewnia minimalne niedopasowanie wypływki i linii neutralnej oraz ułatwia wydajny montaż formy.
- Konserwacja i serwisowanie formy: Producenci powinni wziąć pod uwagę łatwość konserwacji, naprawy i serwisowania form. Elementy formy powinny być łatwo dostępne do czyszczenia, kontroli i wymiany. Włączenie funkcji, takich jak szybkowymienne wkładki lub modułowe konstrukcje form, może poprawić użyteczność formy.
Materiały do form stosowane w formowaniu wtryskowym
Współpraca ze specjalistami od materiałów form i uwzględnienie specyficznych potrzeb związanych z formowaniem może pomóc w określeniu najbardziej odpowiedniego materiału w celu uzyskania optymalnej wydajności formy i jakości części.
- Stopy stali: Stopy stali, takie jak stale narzędziowe (np. P20, H13) i stale nierdzewne, są powszechnie stosowane do form wtryskowych ze względu na ich doskonałą trwałość, odporność na ciepło i odporność na zużycie. Materiały te wytrzymują wysokie temperatury i ciśnienia w procesie formowania wtryskowego i zapewniają dobrą stabilność wymiarową do produkcji wysokiej jakości części.
- Stopy aluminium:Stopy aluminium, takie jak 7075 i 6061, są lekkie i zapewniają dobrą przewodność cieplną, dzięki czemu nadają się do form wymagających wydajnego chłodzenia. Producenci często używają form aluminiowych do prototypowania, produkcji małoseryjnej lub zastosowań, w których redukcja masy ma kluczowe znaczenie. Jednak formy aluminiowe mogą mieć mniejszą trwałość w porównaniu ze stopami stali.
- Stopy miedzi:Stopy miedzi, takie jak miedź berylowa, wykazują wysoką przewodność cieplną i dobrą skrawalność. Znajdują zastosowanie w formach, które wymagają doskonałego przenoszenia ciepła w celu skutecznego chłodzenia. Stopy miedzi mogą pomóc skrócić czas cyklu poprzez szybkie odprowadzanie ciepła z formowanej części, co skutkuje szybszym krzepnięciem.
- stale narzędziowe:Stale narzędziowe, w tym H13, S7 i D2, są przeznaczone do zastosowań narzędziowych o wysokiej wydajności. Stale te oferują połączenie wysokiej wytrzymałości, twardości i odporności na zużycie. Stale narzędziowe nadają się do form o dużej wielkości produkcji, materiałów ściernych lub wymagających warunków formowania.
- Stopy niklu:Stopy niklu, takie jak Inconel i Hastelloy, znane są ze swojej wyjątkowej odporności na korozję, wytrzymałości na wysokie temperatury i stabilności termicznej. Producenci używają tych stopów w formach, które obsługują materiały korozyjne lub wymagają odporności na ekstremalne temperatury i agresywne środowiska formowania.
- Materiały kompozytowe:Materiały kompozytowe, takie jak wzmocnione tworzywa sztuczne lub kompozyty z metalowymi wkładkami, są czasami używane do określonych zastosowań w formowaniu. Materiały te oferują równowagę właściwości, takich jak wysoka wytrzymałość, stabilność termiczna i zmniejszona waga. Formy kompozytowe mogą stanowić opłacalną alternatywę dla określonych wymagań produkcyjnych.
Rodzaje form wtryskowych
Formowanie wtryskowe to wszechstronny i szeroko stosowany proces produkcji części z tworzyw sztucznych.
- Forma dwupłytowa:Forma dwupłytowa jest najczęstszym rodzajem formy wtryskowej. Składa się z dwóch płyt, płyty wnęki i płyty rdzenia, które oddzielają się, aby umożliwić wyrzucenie uformowanej części. Płyta wnęki zawiera stronę wnęki formy, podczas gdy płyta rdzenia zawiera stronę rdzenia. Producenci używają form dwupłytowych do produkcji szerokiej gamy części ze względu na ich stosunkowo prostą konstrukcję.
- Forma trójpłytowa:Forma trójpłytowa to zaawansowana wersja formy dwupłytowej. Zawiera dodatkową płytkę, prowadnicę lub blachę nadlewową. Płyta prowadząca tworzy oddzielny kanał dla wlewu, kanałów prowadzących i bramek, umożliwiając łatwiejsze wyjmowanie formowanej części. Producenci często używają form trójpłytowych do detali ze złożonymi systemami wlewowymi lub gdy pożądane jest uniknięcie pozostałości przewężki na elemencie.
- Forma gorącego kanału:System wlewów i bram jest podgrzewany w formach z gorącymi kanałami, co eliminuje potrzebę krzepnięcia i ponownego topienia materiału podczas każdego cyklu. System gorących kanałów składa się z podgrzewanych kolektorów i dysz, które utrzymują stopiony plastik. Formy z gorącymi kanałami oferują korzyści, takie jak skrócony czas cyklu, mniejsze straty materiału i lepsza jakość części dzięki zminimalizowaniu pozostałości przewężek.
- Forma zimnego biegacza: Formy z zimnymi kanałami mają tradycyjny system kanałów i bramek, w których stopione tworzywo sztuczne przepływa przez zimne kanały, które krzepną w każdym cyklu. Następnie operatorzy usuwają zakrzepłe prowadnice, co powoduje marnotrawstwo materiału. Producenci zazwyczaj używają skomplikowanych form wlewowych do produkcji na mniejszą skalę lub gdy koszty materiałów są mniej krytyczne ze względu na ich prostszą konstrukcję.
- Wstaw formę:Formy wkładane zawierają metalowe lub plastikowe wkładki do wnęki formy podczas formowania wtryskowego. Wkładki można wstępnie umieścić w formie lub wstawić za pomocą zautomatyzowanych procesów. Forma ta pozwala na zintegrowanie dodatkowych elementów lub elementów wzmacniających z wypraską, zwiększając jej funkcjonalność lub wytrzymałość.
- Obtrysk: Overmolding polega na formowaniu jednego materiału na drugim, zazwyczaj łącząc sztywne podłoże z tworzywa sztucznego z bardziej miękkim elastomerem lub tworzywem termoplastycznym. Proces ten pozwala na tworzenie części z wielu materiałów lub tekstur w jednej formie, zapewniając lepszą przyczepność, amortyzację lub cechy estetyczne.
Czynniki wpływające na koszty formowania wtryskowego
Uwzględnienie tych czynników może pomóc producentom oszacować i zoptymalizować koszty formowania wtryskowego, zapewniając równowagę między jakością, wydajnością i opłacalnością dla ich specyficznych wymagań produkcyjnych.
- Złożoność części:Złożoność projektu części odgrywa znaczącą rolę w określaniu kosztów formowania wtryskowego. Skomplikowane geometrie, podcięcia, cienkie ścianki lub złożone elementy mogą wymagać dodatkowego oprzyrządowania, specjalistycznych form lub dłuższych cykli, zwiększając całkowity koszt produkcji.
- Wybór materiału:Wybór materiału termoplastycznego wpływa na koszt formowania wtryskowego. Różne materiały mają różne ceny za kilogram, a czynniki, takie jak dostępność materiału, właściwości i wymagania dotyczące przetwarzania, mogą wpływać na całkowity koszt materiału.
- Projektowanie narzędzi i form: Początkowe koszty oprzyrządowania i projektu formy są znaczące w kosztach formowania wtryskowego. Czynniki takie jak złożoność formy, liczba wnęk, rozmiar formy i materiał formy przyczyniają się do kosztów produkcji oprzyrządowania i formy. Bardziej złożone formy lub formy wymagające zaawansowanych funkcji mogą zwiększyć początkową inwestycję.
- Wielkość produkcji: Wielkość produkcji bezpośrednio wpływa na koszt części w procesie formowania wtryskowego. Wyższe księgi często skutkują korzyściami skali, zmniejszając koszt części. I odwrotnie, serie produkcyjne o małej objętości mogą wiązać się z wyższymi opłatami ze względu na konfigurację, oprzyrządowanie i marnotrawstwo materiałów.
- Czas cyklu: Czas cyklu, który obejmuje fazy chłodzenia i wyrzucania, wpływa na zdolność produkcyjną i całkowity koszt. Dłuższe czasy cykli skutkują zmniejszoną wydajnością produkcji i potencjalnie wyższymi cenami. Optymalizacja projektu formy, systemu chłodzenia i parametrów procesu może skrócić czas cyklu i poprawić wydajność.
- Wymagania jakościowe:Surowe wymagania jakościowe lub określone certyfikaty mogą wpływać na koszt formowania wtryskowego. Spełnienie dokładnych tolerancji, wymagań dotyczących wykończenia powierzchni lub dodatkowych testów może wymagać innych zasobów, procesów lub inspekcji, zwiększając całkowity koszt.
- Operacje drugorzędne:Jeśli formowane części wymagają operacji przetwarzania końcowego, takich jak montaż, malowanie lub dodatkowe etapy wykańczania, operacje te mogą zwiększyć całkowity koszt formowania wtryskowego.
- Dostawca i lokalizacja:Wybór dostawcy form wtryskowych i jego lokalizacji może mieć wpływ na koszty. Koszty pracy, koszty ogólne, koszty logistyki i transportu różnią się w zależności od lokalizacji dostawcy, wpływając na całkowity koszt produkcji.
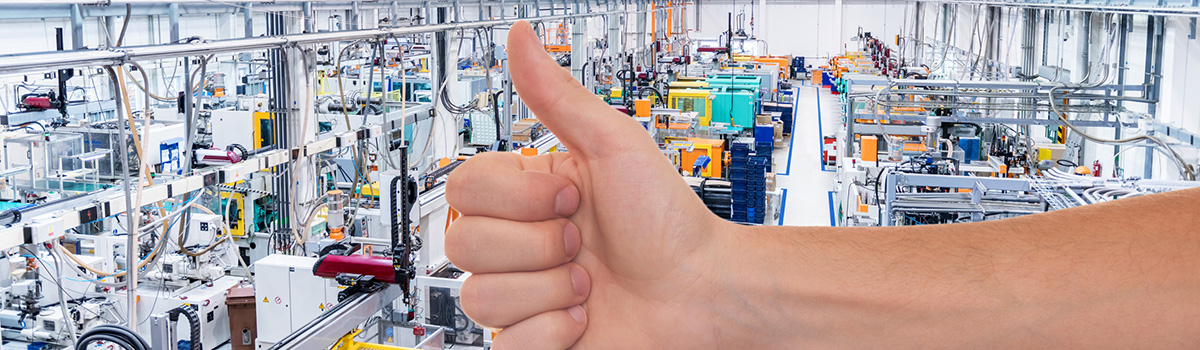
Kontrola jakości w formowaniu wtryskowym
Wdrażanie solidnych środków kontroli jakości w całym procesie formowania wtryskowego pomaga identyfikować i usuwać potencjalne wady, odchylenia lub niespójności, zapewniając produkcję wysokiej jakości części, które spełniają specyfikacje i wymagania klienta.
- Monitorowanie procesu: Ciągłe monitorowanie kluczowych parametrów procesu, takich jak temperatura stopu, ciśnienie wtrysku, czas chłodzenia i czas cyklu, zapewnia spójność i powtarzalność produkcji części. Monitorowanie w czasie rzeczywistym i zautomatyzowane systemy mogą wykrywać zmiany lub odchylenia od ustawionych parametrów, umożliwiając terminową regulację i utrzymanie stabilności procesu.
- Kontrola i pomiar:Regularne przeglądy i pomiary formowanych części są niezbędne do weryfikacji dokładności wymiarowej, jakości części i zgodności ze specyfikacjami. Nasze usługi obejmują szereg metod kontroli jakości, takich jak pomiary wymiarów, analiza jakości powierzchni, przeprowadzanie oględzin, wykonywanie testów funkcjonalnych. Do dokładnej oceny stosuje się różne techniki kontroli, takie jak współrzędnościowe maszyny pomiarowe (CMM) oraz systemy kontroli optycznej i wizualnej.
- Statystyczna kontrola procesu (SPC): SPC obejmuje zbieranie i analizowanie danych procesowych w celu monitorowania i kontrolowania jakości formowania wtryskowego. Metody statystyczne, takie jak wykresy kontrolne i analiza zdolności procesu, pomagają identyfikować trendy, wykrywać odchylenia procesu i zapewniać, że proces pozostaje w określonych granicach kontrolnych. SPC umożliwia proaktywną identyfikację problemów i ułatwia optymalizację procesów.
- Testowanie materiałów: Testowanie surowców, takich jak tworzywa termoplastyczne, dodatki i barwniki, zapewnia ich jakość i przydatność do formowania wtryskowego. Testy materiałowe mogą obejmować analizę wskaźnika płynięcia (MFI), właściwości mechaniczne, właściwości termiczne i skład materiału. Weryfikacja jakości materiału pomaga zapobiegać defektom i niespójnościom formowanych części.
- Konserwacja i kontrola oprzyrządowania:Właściwa konserwacja i regularna kontrola form wtryskowych są kluczowe dla zapewnienia jakości formowania wtryskowego. Regularne czyszczenie, smarowanie i ocena elementów formy pomaga zapobiegać zużyciu, uszkodzeniu lub degradacji, które mogłyby wpłynąć na jakość części. Terminowa naprawa lub wymiana zużytych lub uszkodzonych elementów formy jest niezbędna do utrzymania stałej wydajności formowania.
- Dokumentacja i identyfikowalność:Utrzymywanie obszernej dokumentacji i rejestrów identyfikowalności jest niezbędne do kontroli jakości w formowaniu wtryskowym. Istotne jest, aby rejestrować parametry procesu, wyniki kontroli, informacje o materiałach oraz wszelkie zmiany lub korekty dokonane podczas produkcji. Właściwa dokumentacja umożliwia identyfikowalność części, ułatwia analizę przyczyn źródłowych i zapewnia stałą jakość.
- Szkolenie i rozwój umiejętności: Zapewnienie odpowiedniego szkolenia i programów rozwoju umiejętności dla operatorów, techników i personelu kontroli jakości zwiększa ich zrozumienie procesów formowania wtryskowego, wymagań jakościowych i technik kontroli. Dobrze wyszkolony personel może wykrywać defekty, rozwiązywać problemy i skutecznie wdrażać środki naprawcze, zapewniając wysoką jakość produkcji.
Typowe wady formowania wtryskowego i sposoby ich unikania
Regularna kontrola, monitorowanie i analiza procesów formowania wtryskowego oraz właściwa konserwacja i regulacja sprzętu i form mogą pomóc w identyfikacji i usuwaniu tych typowych wad.
- Znaki zlewu:Ślady zapadnięcia to wgłębienia lub wgniecenia na powierzchni wypraski spowodowane nierównomiernym chłodzeniem lub skurczem. Należy wziąć pod uwagę właściwą lokalizację i projekt przewężki, optymalny projekt systemu chłodzenia i równomierny rozkład grubości ścianek, aby uniknąć śladów zapadnięć. Zwiększenie ciśnienia wtrysku lub dostosowanie czasu chłodzenia może również pomóc zminimalizować ślady zapadnięć.
- Wypaczenie:Wypaczenie odnosi się do odkształcenia lub wygięcia uformowanej części po wypchnięciu z powodu nierównomiernego chłodzenia lub naprężeń szczątkowych. Zachowanie jednolitej grubości ścianek, stosowanie odpowiednich kanałów chłodzących oraz zapewnienie równomiernego napełniania i upakowania formy ma kluczowe znaczenie dla zapobiegania wypaczeniu. Optymalizacja temperatury formy, stosowanie odpowiednich kątów pochylenia oraz kontrolowanie temperatury materiału i prędkości wtrysku może pomóc zminimalizować wypaczenia.
- Migać:Wypływka pojawia się, gdy nadmiar materiału wpływa do linii podziału formy, co skutkuje cienkimi, niechcianymi występami lub dodatkowym materiałem na końcowej części. Można skutecznie zapobiegać wypływce, zapewniając odpowiednią konstrukcję formy, w tym stosując odpowiednią siłę docisku, precyzyjne ustawienie i stosując odpowiednie techniki odpowietrzania. Optymalizacja parametrów procesu, takich jak ciśnienie wtrysku, temperatura i czas cyklu, ogranicza wypływkę.
- Krótki strzał:Szybki strzał ma miejsce, gdy wtryskiwany materiał nie wypełnia wnęki formy, co skutkuje niekompletną częścią. Właściwy dobór materiału, zapewnienie odpowiedniej temperatury i lepkości stopu oraz utrzymanie odpowiedniego ciśnienia i czasu wtrysku są niezbędne, aby uniknąć krótkich zdjęć. Dodatkowo weryfikacja projektu formy pod kątem odpowiedniego rozmiaru prowadnicy i bramy oraz właściwej wentylacji może pomóc w zapobieganiu szybkim strzałom.
- Linie spawalnicze:Linie spawalnicze pojawiają się, gdy dwa lub więcej czoła strumienia stopionego materiału spotykają się i krzepną, co powoduje powstanie widocznej linii lub znaku na powierzchni części. Dobra konstrukcja przewężki i prowadnicy, optymalna temperatura topnienia, prędkość wtrysku oraz dostosowanie przepływu materiału i geometrii części mogą zminimalizować linie spawania. Analiza przepływu formy i optymalizacja rozmieszczenia przewężek mogą również pomóc w zapobieganiu powstawaniu linii spawalniczych lub ich łagodzeniu.
- Ślady oparzeń:Ślady wypalenia to przebarwienia lub czarne plamy na powierzchni wypraski spowodowane nadmiernym nagrzaniem lub przegrzaniem materiału. Unikanie skrajnych temperatur topnienia, stosowanie odpowiednich kanałów chłodzących i optymalizacja czasu cyklu może pomóc w zapobieganiu powstawaniu śladów przypaleń. Odpowiednie odpowietrzanie, właściwa konstrukcja przewężki i kontrolowanie temperatury formy również przyczyniają się do zminimalizowania śladów przypaleń.
Operacje po formowaniu: wykończenie i montaż
Po formowaniu wtryskowym wiele formowanych części może wymagać dodatkowych operacji wykończeniowych i montażowych w celu uzyskania pożądanego produktu końcowego. Te operacje po formowaniu mogą obejmować:
- Lamówka:Usuń nadmiar materiału lub wypływkę wokół formowanej części za pomocą narzędzi do przycinania lub cięcia.
- Obróbka powierzchniowa:Poprawa wyglądu lub funkcjonalności powierzchni części za pomocą różnych technik, takich jak malowanie, powlekanie lub teksturowanie.
- Montaż:Łączenie wielu formowanych części lub dodawanie komponentów, takich jak elementy złączne, wkładki lub etykiety, aby skompletować produkt końcowy.
- Testowanie:Weryfikacja jakości i funkcjonalności części za pomocą różnych metod testowania, takich jak analiza wymiarowa, testowanie właściwości materiałów lub testowanie wydajności.
- Pakowanie i wysyłka:Właściwe pakowanie i etykietowanie gotowego produktu do wysyłki do klientów lub użytkowników końcowych.
Wybór operacji po formowaniu zależy od konkretnego zastosowania i pożądanych właściwości produktu końcowego. Ścisła współpraca między ekspertami w dziedzinie formowania wtryskowego, specjalistami w zakresie wykańczania i montażu oraz klientem ma kluczowe znaczenie dla osiągnięcia pożądanej absolutnej jakości i funkcjonalności produktu. Właściwe planowanie i integracja operacji po formowaniu z procesem produkcyjnym może pomóc w zapewnieniu wydajnej produkcji i terminowej dostawy produktów wysokiej jakości.
Formowanie wtryskowe a inne procesy produkcji tworzyw sztucznych
Każdy proces produkcji tworzyw sztucznych ma zalety i ograniczenia, dzięki czemu nadaje się do różnych zastosowań.
- Formowanie wtryskowe: Formowanie wtryskowe to wysoce wszechstronny i szeroko stosowany proces produkcji części z tworzyw sztucznych. Oferuje takie zalety, jak wysoka wydajność produkcji, precyzyjne odwzorowanie części oraz możliwość tworzenia skomplikowanych geometrii. Formowanie wtryskowe nadaje się do produkcji wielkoseryjnej i pozwala na zastosowanie szerokiej gamy materiałów termoplastycznych. Oferuje doskonałą dokładność wymiarową i wykończenie powierzchni, dzięki czemu idealnie nadaje się do różnych gałęzi przemysłu, takich jak motoryzacja, towary konsumpcyjne i urządzenia medyczne.
- Formowanie z rozdmuchem: Formowanie z rozdmuchiwaniem to proces stosowany głównie do produkcji pustych części z tworzyw sztucznych, takich jak butelki, pojemniki i części samochodowe. Polega na stopieniu tworzywa sztucznego i napompowaniu go do wnęki formy, tworząc pożądany kształt. Formowanie z rozdmuchem nadaje się do produkcji na dużą skalę i może wytwarzać duże, lekkie części o jednolitej grubości ścianek. Jest to jednak ograniczone pod względem złożoności części i wyboru materiału w porównaniu z formowaniem wtryskowym.
- Termoformowanie:Termoformowanie to proces stosowany do produkcji części z tworzyw sztucznych poprzez podgrzewanie arkusza termoplastycznego i kształtowanie go za pomocą form lub formowania próżniowego. Znajduje powszechne zastosowanie w opakowaniach, produktach jednorazowego użytku i produktach na dużą skalę, takich jak tace i pokrywy. Termoformowanie oferuje ekonomiczną produkcję dużych części i pozwala na szybkie tworzenie prototypów. Ma jednak ograniczenia dotyczące złożoności części, wyboru materiału i dokładności wymiarowej w porównaniu z formowaniem wtryskowym.
- Wyrzucenie:Wytłaczanie to ciągły proces produkcji profili, arkuszy, rur i folii z tworzyw sztucznych. Polega na stopieniu plastikowej żywicy i przepchnięciu jej przez matrycę w celu uzyskania pożądanego kształtu. Wytłaczanie jest odpowiednie do wytwarzania długich, ciągłych odcinków wyrobów z tworzyw sztucznych o stałym przekroju. Podczas gdy wytłaczanie zapewnia wysoką wydajność produkcji i opłacalność, jest ono ograniczone pod względem złożonych geometrii części i precyzyjnej kontroli wymiarów w porównaniu z formowaniem wtryskowym.
- Formowanie tłoczne:Formowanie tłoczne polega na umieszczeniu odmierzonej ilości materiału termoutwardzalnego w ogrzanej gnieździe formy i sprasowaniu go pod wysokim ciśnieniem, aż do utwardzenia. Znajduje powszechne zastosowanie w produkcji części o wysokiej wytrzymałości i stabilności wymiarowej, takich jak komponenty samochodowe i izolacje elektryczne. Formowanie tłoczne zapewnia dobrą spójność części, wysoką wydajność produkcji i możliwość stosowania szerokiej gamy materiałów. Jest to jednak ograniczone pod względem złożoności części i czasu cyklu w porównaniu z formowaniem wtryskowym.
Zastosowania termoplastycznego formowania wtryskowego
Różne gałęzie przemysłu szeroko stosują termoplastyczne formowanie wtryskowe ze względu na jego wszechstronność, wydajność i opłacalność. Niektóre zastosowania formowania wtryskowego tworzyw termoplastycznych obejmują:
- Przemysł samochodowy: Przemysł motoryzacyjny szeroko wykorzystuje termoplastyczne formowanie wtryskowe do produkcji różnych elementów, w tym wykończenia wnętrza i nadwozia, desek rozdzielczych, paneli drzwi, zderzaków i złączy elektrycznych. Proces ten pozwala na precyzyjne odwzorowanie części, złożoną geometrię i zastosowanie lekkich materiałów, poprawiając oszczędność paliwa i elastyczność projektowania.
- Dobra konsumpcyjne:Formowanie wtryskowe znajduje szerokie zastosowanie w produkcji towarów konsumpcyjnych, takich jak sprzęt gospodarstwa domowego, urządzenia elektroniczne, pojemniki do pakowania i zabawki. Proces ten umożliwia masową produkcję trwałych, wysokiej jakości produktów o spójnych wymiarach i wykończeniu powierzchni. Pozwala również na opcje dostosowywania i szybkie iteracje produktu.
- Urządzenia medyczne:Formowanie wtryskowe odgrywa kluczową rolę w przemyśle medycznym w produkcji szerokiej gamy urządzeń, w tym strzykawek, narzędzi chirurgicznych, elementów wszczepialnych i systemów dostarczania leków. Proces ten zapewnia produkcję sterylnych, precyzyjnych i biokompatybilnych części, które spełniają surowe wymagania regulacyjne sektora opieki zdrowotnej.
- Przemysł elektroniczny i elektryczny:Przemysł elektroniczny wykorzystuje formowanie wtryskowe do produkcji złączy elektrycznych, obudów, przełączników i innych komponentów. Proces ten zapewnia wysoką dokładność wymiarową, doskonałe wykończenie powierzchni oraz możliwość włączenia funkcji, takich jak formowanie wtryskowe i obtryskiwanie, co pozwala na wydajną produkcję złożonych zespołów elektronicznych.
- Przemysł opakowaniowy:Różne gałęzie przemysłu, w tym żywność i napoje, farmaceutyki i środki higieny osobistej, powszechnie wykorzystują formowanie wtryskowe do produkcji plastikowych pojemników opakowaniowych, nakrętek, zamknięć i butelek. Proces ten umożliwia tworzenie lekkich, trwałych i estetycznych rozwiązań opakowaniowych z wydajnymi cyklami produkcyjnymi.
- Przemysł lotniczy:Sektor lotniczy wykorzystuje formowanie wtryskowe do produkcji lekkich i wysokowydajnych komponentów, takich jak kanały powietrzne, wsporniki, panele wewnętrzne i elementy konstrukcyjne. Proces pozwala na stosowanie zaawansowanych materiałów i skomplikowanych geometrii części, przyczyniając się do redukcji masy i poprawy efektywności paliwowej.
Wpływ termoplastycznego formowania wtryskowego na środowisko
Formowanie wtryskowe tworzyw termoplastycznych jest popularnym procesem produkcyjnym ze względu na wiele zalet, ale należy również wziąć pod uwagę jego wpływ na środowisko. Oto kilka punktów do rozważenia:
- Wydajność materiałowa:Formowanie wtryskowe tworzyw termoplastycznych promuje wydajność materiałową poprzez minimalizację odpadów. Proces wykorzystuje precyzyjną kontrolę nad ilością materiału wtryskiwanego do formy, zmniejszając potrzebę stosowania nadmiaru materiału. Producenci mogą również stosować techniki ponownego szlifowania i recyklingu w celu ponownego wykorzystania złomu lub odrzuconych części, co dodatkowo zmniejsza ilość odpadów materiałowych.
- Zużycie energii:Producenci projektują wtryskarki tak, aby były energooszczędne, a nowoczesne modele wykorzystują zaawansowane technologie, takie jak serwomotory i napędy o zmiennej prędkości. Funkcje te optymalizują zużycie energii poprzez zmniejszenie zużycia energii podczas formowania, co skutkuje niższym zapotrzebowaniem na energię i mniejszym wpływem na środowisko.
- Gospodarowanie odpadami:Minimalizując straty materiałowe, producenci powinni wdrożyć odpowiednie praktyki gospodarowania odpadami, aby poradzić sobie z resztkami materiałów, wlewkami lub kanałami. Producenci mogą ustanowić programy recyklingu w celu zbierania i ponownego wykorzystania odpadów z tworzyw sztucznych powstałych podczas formowania wtryskowego, zmniejszając w ten sposób ilość odpadów wysyłanych na składowiska.
- Redukcja emisji: Formowanie wtryskowe tworzyw termoplastycznych generalnie generuje mniejsze emisje niż inne procesy produkcyjne. Producenci mogą zmniejszyć emisje, stosując materiały przyjazne dla środowiska, wdrażając energooszczędny sprzęt oraz stosując zaawansowane systemy wydechowe i filtrujące do wychwytywania wszelkich uwolnionych emisji.
- Wybór zrównoważonych materiałów:Wybór materiałów termoplastycznych może znacząco wpłynąć na zrównoważenie środowiskowe formowania wtryskowego. Wybór biodegradowalnych lub pochodzenia biologicznego tworzyw sztucznych, a także materiałów pochodzących z recyklingu lub nadających się do recyklingu, może pomóc w zmniejszeniu ogólnego śladu ekologicznego procesu.
Rozważania dotyczące cyklu życia: Uwzględnienie całego cyklu życia uformowanego produktu jest niezbędne do oceny jego wpływu na środowisko. Na etapie projektowania i wyboru materiałów producenci powinni wziąć pod uwagę takie czynniki, jak trwałość części, możliwość jej recyklingu oraz możliwość utylizacji lub ponownego użycia po zakończeniu okresu eksploatacji.
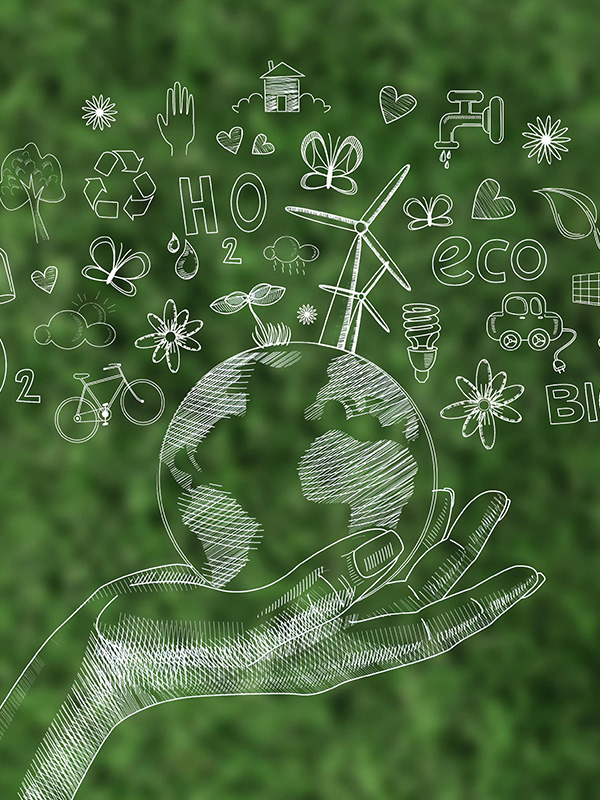
Przyszłość formowania wtryskowego tworzyw termoplastycznych
Przyszłość formowania wtryskowego tworzyw termoplastycznych wygląda obiecująco wraz z ciągłym postępem technologicznym i rosnącym zapotrzebowaniem na wysokiej jakości, precyzyjne części w różnych branżach. Niektóre z kluczowych zmian oczekiwanych w nadchodzących latach obejmują:
- Zwiększone wykorzystanie automatyzacji i robotyki w celu poprawy wydajności i redukcji kosztów.
- Wysiłki koncentrują się na opracowywaniu nowych materiałów i procesów w celu poprawy wydajności części i umożliwienia nowych zastosowań.
- Jest to rosnące przyjęcie zrównoważonych praktyk, takich jak wykorzystanie materiałów pochodzących z recyklingu i optymalizacja zużycia energii, w celu zmniejszenia wpływu formowania wtryskowego na środowisko.
- Większa integracja technologii cyfrowych, takich jak oprogramowanie do drukowania 3D i symulacji, w celu usprawnienia procesów projektowania i produkcji.
Globalny rynek formowania wtryskowego rozwija się, szczególnie w gospodarkach wschodzących, napędzany rosnącym popytem na produkty z tworzyw sztucznych w różnych gałęziach przemysłu.
Wybór odpowiedniego partnera do formowania wtryskowego
Wybór odpowiedniego partnera do formowania wtryskowego ma kluczowe znaczenie dla powodzenia Twojego projektu. Poświęć czas na ocenę wielu opcji, przeprowadź wizyty na miejscu i zaangażuj się w szczegółowe dyskusje, aby zapewnić zgodną i długotrwałą współpracę.
- Wiedza i doświadczenie:Poszukaj partnera do formowania wtryskowego z rozległą wiedzą i doświadczeniem w branży. Powinni mieć udokumentowane doświadczenie w dostarczaniu wysokiej jakości produktów i rozwiązań klientom z różnych sektorów. Weź pod uwagę ich zrozumienie różnych materiałów, projektów form i procesów produkcyjnych.
- Możliwości produkcyjne: Oceń możliwości produkcyjne partnera zajmującego się formowaniem wtryskowym. Upewnij się, że mają dobrze wyposażony obiekt z nowoczesnymi maszynami i technologiami, aby sprostać wymaganiom Twojego projektu. Weź pod uwagę ich zdolność produkcyjną, zdolność do obsługi części o różnych rozmiarach i złożoności oraz zdolność do spełnienia żądanych wielkości produkcji i terminów.
- Zapewnienie jakości:Jakość jest najważniejsza w formowaniu wtryskowym. Oceń systemy kontroli jakości i certyfikaty potencjalnego partnera. Szukaj partnerów, którzy przestrzegają surowych standardów jakości, mają solidne procesy kontroli i przeprowadzają kompleksowe testy, aby zapewnić jakość i spójność części.
- Wsparcie projektowe i inżynieryjne:Niezawodny partner w zakresie formowania wtryskowego powinien oferować wsparcie projektowe i inżynieryjne, aby zoptymalizować projekt części pod kątem możliwości produkcyjnych. Powinni mieć wykwalifikowanych inżynierów, którzy mogą wnieść cenny wkład w dobór materiałów, projektowanie form i optymalizację procesów w celu poprawy jakości i wydajności części.
- Konkurencyjność kosztowa:Chociaż koszt nie powinien być jedynym decydującym czynnikiem, niezbędna jest ocena cen i konkurencyjności kosztowej partnera zajmującego się formowaniem wtryskowym. Poproś o szczegółowe oferty i weź pod uwagę koszty oprzyrządowania, koszty materiałów, koszty robocizny i wszelkie dodatkowe usługi świadczone przez nich.
- Komunikacja i współpraca:Skuteczna komunikacja i współpraca są niezbędne dla udanego partnerstwa. Upewnij się, że partner zajmujący się formowaniem wtryskowym ma dobre kanały komunikacji, odpowiada na Twoje zapytania i może regularnie aktualizować projekt. Podejście oparte na współpracy pomoże nam spełnić Twoje wymagania i szybko odpowiedzieć na wszelkie wyzwania.
- Referencje i recenzje klientów:Szukaj referencji klientów lub czytaj recenzje/rekomendacje, aby uzyskać wgląd w doświadczenia innych klientów z partnerem w zakresie formowania wtryskowego. Uzyskanie tych informacji może pomóc określić ich niezawodność, terminowość i ogólny poziom zadowolenia klientów.
Wnioski
Formowanie wtryskowe tworzyw termoplastycznych to wszechstronna i opłacalna metoda produkcji części z tworzyw sztucznych w dużych ilościach. Jego zdolność do tworzenia skomplikowanych kształtów z dużą precyzją i spójnością stała się popularnym wyborem dla różnych branż, w tym motoryzacyjnej, medycznej, elektronicznej i towarów konsumpcyjnych. Dzięki zrozumieniu różnych aspektów formowania wtryskowego tworzyw termoplastycznych, w tym jego zalet, wad i uwarunkowań projektowych, możesz podejmować świadome decyzje dotyczące wyboru odpowiedniego partnera w zakresie formowania wtryskowego dla potrzeb Twojej firmy.