ఇంజెక్షన్ మౌల్డింగ్ యొక్క సాధారణ అచ్చు లోపాలకు పరిష్కారాలు
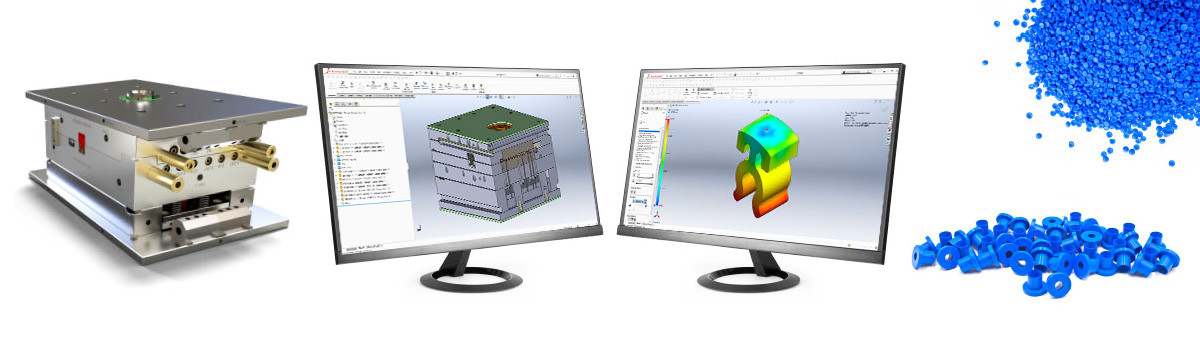
ప్లాస్టిక్ ఇంజెక్షన్ మోల్డింగ్ భాగాలను ప్రాసెస్ చేయడానికి అచ్చులను ఉపయోగిస్తున్నప్పుడు లోపాలు సాధారణం, మరియు ఇది ప్రాసెసింగ్ సామర్థ్యాన్ని ఎక్కువగా ప్రభావితం చేస్తుంది. ప్లాస్టిక్ ఇంజెక్షన్ అచ్చు భాగాలకు సాధారణ అచ్చు లోపాలు మరియు పరిష్కారాలు క్రిందివి.
చిన్న షాట్లు
చిన్న షాట్లు అచ్చులు పూర్తిగా నింపబడనందున అసంపూర్ణంగా తయారైన ఉత్పత్తులను సూచిస్తాయి.
ఈ లోపం సాధారణంగా గేట్కు దూరంగా ఉన్న ప్రదేశంలో లేదా అచ్చుపై ఉన్న ఇరుకైన ప్రాంతాల ద్వారా మాత్రమే చేరుకోగల భాగాలలో కనిపిస్తుంది, ఎందుకంటే ఇరుకైన ప్రాంతాలు కరిగిపోయే ప్రవాహాన్ని ప్రభావితం చేస్తాయి.
షార్ట్ షాట్ మైక్రో ఫ్లో మార్కులకు కారణం కావచ్చు లేదా ఉత్పత్తిలో ఎక్కువ భాగం స్పష్టంగా కనిపించకుండా పోతుంది.
కారణం:
షార్ట్ షాట్లకు గల కారణాలు:
అచ్చులోకి ఇంజెక్ట్ చేసిన ముడి పదార్థం సరిపోదు.
కరిగే నిరోధకత పెద్దది, ఫలితంగా అచ్చు పూర్తిగా నింపబడదు.
అచ్చు యొక్క వెంటింగ్ పేలవంగా ఉంది మరియు కరగకుండా నిరోధించే పుచ్చు ఉత్పత్తికి కారణమవుతుంది, కరుగు అచ్చు యొక్క కొన్ని ప్రాంతాలకు ప్రవహించదు.
burrs
అచ్చు కుహరం నుండి ఉత్పత్తికి వెలికితీసిన అదనపు ముడి పదార్థాల సంశ్లేషణ నుండి బర్ర్స్ ఉత్పత్తి చేయబడతాయి.
ఈ లోపం ఉత్పత్తిపై లేదా అచ్చు యొక్క ప్రతి భాగంపై అంచులపై ఉంటుంది. ముడి పదార్థం అచ్చు నుండి పొంగిపోవచ్చు లేదా కదిలే మరియు ఫిక్సింగ్ అచ్చుల బంధన ప్రదేశాలు.
హైడ్రాలిక్ పీడనం లేదా కోణీయ పిన్ కారణంగా అచ్చు కోర్లో కూడా బర్ర్స్ కనుగొనవచ్చు.
బర్ర్స్ యొక్క తీవ్రత మారుతూ ఉంటుంది, కొన్నిసార్లు సన్నగా, కొన్నిసార్లు మందంగా ఉంటుంది.
కారణం:
బర్ర్స్ యొక్క కారణాలు:
బిగింపు అచ్చు ఉపరితలం దెబ్బతింది లేదా భారీగా ధరిస్తుంది.
మూవింగ్ అచ్చు మరియు ఫిక్సింగ్ అచ్చు లాక్ చేయబడినప్పుడు డిస్-లొకేషన్ అవుతాయి.
అచ్చులో ముడి పదార్థం యొక్క ఒత్తిడి అచ్చు బిగింపు శక్తి కంటే ఎక్కువగా ఉంటుంది.
పైన పేర్కొన్న మూడవ పరిస్థితి వివిధ కారణాల వల్ల ఏర్పడుతుంది. కింది పరిస్థితులలో, ముడి పదార్థం యొక్క ఒత్తిడి అచ్చు బిగింపు శక్తి కంటే ఎక్కువగా ఉంటుంది.
ఇంజెక్షన్ అచ్చు యొక్క మొదటి దశలో (అచ్చు నింపే దశ), చాలా ముడి పదార్థం నిండి ఉంటుంది, ఇది అచ్చు లోపల ఒత్తిడిని పెంచుతుంది.
అచ్చు నింపే ప్రక్రియలో, కరిగే ప్రవాహం యొక్క పెద్ద నిరోధకత అచ్చు లోపల ఒత్తిడిని కూడా పెంచుతుంది.
ప్రెజర్ హోల్డింగ్ దశలో అచ్చు కుహరం ఒత్తిడి చాలా ఎక్కువగా ఉంటుంది.
అచ్చు బిగింపు శక్తి సరిపోదు.
భ్రష్టత
కుళ్ళిపోవడం అనేక ఫలితాలకు దారితీయవచ్చు. సమస్య యొక్క పరిధి మరియు తీవ్రత కూడా మారుతూ ఉంటాయి. అత్యంత తీవ్రమైన సందర్భంలో, ఇది ఉత్పత్తి యొక్క పూర్తి రంగు పాలిపోవడానికి మరియు పేలవమైన యాంత్రిక లక్షణాలను కలిగిస్తుంది. స్థానిక క్షీణత ముదురు చారలు లేదా మచ్చలను మాత్రమే కలిగిస్తుంది.
కారణం:
ముడి పదార్థం దెబ్బతినడం వల్ల క్షీణత ఏర్పడుతుంది. ప్లాస్టిక్లను ఏర్పరిచే పొడవైన గొలుసు అణువులు అధిక వేడి లేదా అధిక కోత ఒత్తిడి ప్రభావంతో కుళ్ళిపోతాయి. అణువుల కుళ్ళిపోయే సమయంలో, అస్థిర వాయువు క్షీణత ప్రక్రియను వేగవంతం చేస్తుంది, ఇది ముడి పదార్థం యొక్క డీ-కలర్కు కారణమవుతుంది. పెద్ద మొత్తంలో అణువుల కుళ్ళిపోవడం చివరకు ముడి పదార్థం యొక్క కంటెంట్ను విచ్ఛిన్నం చేస్తుంది మరియు యాంత్రిక లక్షణాలపై ప్రతికూల ప్రభావాన్ని కలిగిస్తుంది.
మెటీరియల్ బారెల్ యొక్క అసమాన ఉష్ణోగ్రత కారణంగా స్థానిక క్షీణత సంభవించవచ్చు.
కింది పరిస్థితులలో క్షీణత సంభవించవచ్చు:
ముడి పదార్థం మెటీరియల్ బారెల్ లేదా హాట్ రన్నర్ సిస్టమ్లో ఎక్కువగా వేడి చేయబడుతోంది.
ముడి పదార్థం చాలా కాలం పాటు బారెల్లో ఉంటుంది.
ఇంజెక్షన్ మౌల్డింగ్ ప్రక్రియలో, ముడి పదార్థంపై చూపే కోత ఒత్తిడి చాలా పెద్దది. నాజిల్లు బ్లాక్ చేయబడినా, లేదా గేట్లు మరియు రన్నర్ చాలా ఇరుకైనవి అయితే, అది కోత ఒత్తిడిని పెంచుతుంది.
విరూపణ
సాధారణ పరిస్థితుల్లో, ఉత్పత్తుల ఆకారాలు అచ్చులకు అనుగుణంగా ఉండాలి. వైకల్యం ఉత్పత్తుల వైకల్యాన్ని సూచిస్తుంది.
పరిస్థితి మరింత దిగజారినప్పుడు, అచ్చు నుండి బయటకు వచ్చినప్పుడు ఉత్పత్తులు పూర్తిగా వైకల్యం చెందుతాయి. పరిస్థితి తీవ్రంగా లేనప్పుడు, ఉత్పత్తి ఆకారంలో చిన్న అసమానతలు కనిపిస్తాయి.
పొడవాటి కానీ మద్దతు లేని అంచులు లేదా పెద్ద విమానాలు వైకల్యానికి ఎక్కువ అవకాశం ఉన్న ప్రాంతాలు.
కారణం:
వైకల్యానికి కారణాలు:
అచ్చు విడుదలైనప్పుడు ఉష్ణోగ్రత చాలా ఎక్కువగా ఉంటుంది.
శీతలీకరణ సమయం మందపాటి మరియు సన్నని ప్రదేశాలలో భిన్నంగా ఉంటుంది లేదా అచ్చును కదిలించడం మరియు అచ్చును ఫిక్సింగ్ చేయడంలో అచ్చు ఉష్ణోగ్రత వ్యత్యాసం కారణంగా, ఉత్పత్తుల లోపల సంకోచం భిన్నంగా ఉంటుంది.
పూరించేటప్పుడు అచ్చు ప్రవాహం సాఫీగా ఉండదు (దీనిని "ఫ్రీజింగ్ ఓరియంటేషన్" అని పిలుస్తారు) లేదా అచ్చు కుహరం లోపల ఒత్తిడి ఒత్తిడి పట్టుకునే దశలో చాలా ఎక్కువగా ఉంటుంది.
మాలిన్యాలు
మలినాలను తరచుగా వివిధ రంగులు, పాచెస్ లేదా చారలలో మచ్చల రూపంలో కనిపిస్తాయి. అత్యంత సాధారణమైనది నల్ల మచ్చ.
మలినాలు కేవలం చిన్న మచ్చలు మాత్రమే కావచ్చు, కానీ అది తీవ్రంగా ఉన్నప్పుడు స్పష్టమైన చారలు లేదా డి-కలరింగ్లో పెద్ద భాగం కూడా కావచ్చు.
కారణం:
మలినాలను ముడి పదార్థాలతో కలిపిన సాండ్రీస్ వల్ల కలుగుతాయి, అవి:
ముడి పదార్థం బారెల్స్లోకి రవాణా చేయబడినప్పుడు సన్డ్రీలతో కలుపుతారు.
ముడి పదార్థం యొక్క కుళ్ళిపోవడం అనేది ఏదైనా కట్టింగ్ మెకానిజమ్ల నుండి పడిపోయి ఉండవచ్చు మరియు మెషిన్ బోల్ట్లు, డ్రమ్ యొక్క లోపలి గోడ, కీళ్ళు / నాజిల్లు వంటి ముడి పదార్థాలలో మిళితం కావచ్చు.
ల్యామినేషన్
లామినేషన్ ఉత్పత్తుల ఉపరితలంపై "స్కిన్ ఎఫెక్ట్" ను ఉత్పత్తి చేస్తుంది, ఇది ఉత్పత్తులు మరియు ఇతర ముడి పదార్థాల ఉపరితలం యొక్క లక్షణాలు మరియు అల్లికలలో వ్యత్యాసం కారణంగా ఏర్పడుతుంది మరియు ఇది తొలగించబడే చర్మాన్ని ఏర్పరుస్తుంది.
లామినేషన్ తీవ్రంగా ఉన్నప్పుడు, మొత్తం క్రాస్ సెక్షన్ ప్రాంతం వివిధ పొరలతో తయారు చేయబడుతుంది మరియు కలిసి కరిగించబడదు. లోపాలు స్పష్టంగా లేనప్పుడు, ఉత్పత్తుల రూపాన్ని అవసరాలు తీర్చవచ్చు, కానీ ఉత్పత్తుల యొక్క యాంత్రిక లక్షణాలను విచ్ఛిన్నం చేస్తుంది.
కారణం:
లామినేషన్కు రెండు ప్రధాన కారణాలు ఉన్నాయి. మొదటిది ఏమిటంటే, రెండు రకాల ముడి పదార్థాలు తప్పుగా కలిసినప్పుడు. రెండు ముడి పదార్థాలు ఒత్తిడిలో ఒకే సమయంలో బారెల్లోకి రవాణా చేయబడతాయి. అయినప్పటికీ, అచ్చు చల్లబడినప్పుడు కలిసి కరిగించలేనప్పుడు, ఉత్పత్తులను ఏర్పరచడానికి వివిధ పొరలను బలవంతంగా నొక్కినట్లే.
రెండవది: చలిని ఇరుకైన గేటు గుండా బలవంతంగా కరిగిస్తే, కోత ఒత్తిడి ఏర్పడుతుంది. చాలా ఎక్కువ కోత ఒత్తిడి కారణంగా కరిగే పొరను ముందుగానే కరిగించి పూర్తిగా కలపడం సాధ్యం కాదు.
మిక్సింగ్ ప్రమాదం:
తెలుసుకోవలసిన ఒక విషయం ఏమిటంటే, కొన్ని ముడి పదార్థాలను కలిపితే, PVC మరియు Avetal వంటి బలమైన రసాయన ప్రతిచర్యలకు దారి తీస్తుంది.
సిల్వర్ లీనియర్
స్లివర్ లీనియర్ కేవలం స్థానిక దృగ్విషయం కావచ్చు, కానీ అది తీవ్రంగా ఉన్నప్పుడు మొత్తం ఉపరితలం వరకు విస్తరించవచ్చు.
సిల్వర్ లీనియర్ ఉత్పత్తుల రూపాన్ని ప్రభావితం చేస్తుంది మరియు ఉత్పత్తుల యొక్క యాంత్రిక లక్షణాలను కూడా దెబ్బతీస్తుంది.
కారణం:
కింది రెండు పాయింట్లు వెండి రేఖకు కారణమవుతాయి:
ముడి పదార్థం తడిగా ఉంటుంది మరియు వాటిలో కొన్ని గాలిలోని ఆవిరిని గ్రహిస్తాయి. ముడి పదార్థం చాలా తడిగా ఉంటే, బారెల్ యొక్క అధిక ఉష్ణోగ్రత మరియు అధిక పీడనం కింద ఒత్తిడితో కూడిన ఆవిరి ఉత్పత్తి కావచ్చు. ఈ ఆవిరి ఉత్పత్తి యొక్క ఉపరితలం గుండా విరిగిపోతుంది మరియు వెండి చారలను ఏర్పరుస్తుంది.
కరుగు థర్మల్ దెబ్బతింది మరియు స్థానిక క్షీణతను ఉత్పత్తి చేస్తుంది. ఉత్పత్తి చేయబడిన అస్థిర వాయువు అచ్చుపై ఉపరితలంపై నిరోధించబడుతుంది మరియు ఉత్పత్తుల ఉపరితలంపై చారలను ఉత్పత్తి చేస్తుంది.
ఇది అధోకరణం వలె అధ్వాన్నంగా లేదు. కరిగే ఉష్ణోగ్రత ఎక్కువగా ఉన్నంత వరకు లేదా ప్లాస్టిసైజేషన్ సమయంలో కోత ఒత్తిడికి గురైతే లేదా అచ్చులోకి ఇంజెక్ట్ చేసినంత వరకు, ఇది జరగవచ్చు.
గ్లోస్ / నీడ
ఉత్పత్తుల ఉపరితల ముగింపు అచ్చుల మాదిరిగానే ఉండాలి. రెండింటి యొక్క ఉపరితల ముగింపు భిన్నంగా ఉన్నప్పుడు, గ్లోస్/షాడో లోపాలు సంభవించాయి.
లోపాలు సంభవించినప్పుడు ఉపరితలం దిగులుగా ఉంటుంది మరియు కఠినమైన ఉపరితలం మృదువైన మరియు నిగనిగలాడేది.
కారణం:
గ్లోస్/నీడకు కారణాలు:
కరుగు సాఫీగా ప్రవహిస్తుంది లేదా అచ్చు ఉపరితలం యొక్క ఉష్ణోగ్రత తక్కువగా ఉంటుంది, ఫలితంగా మెటీరియల్ మౌల్డింగ్ చేసినప్పుడు అచ్చు ఉపరితల ముగింపు నకిలీ చేయబడదు.
ప్రెజర్ హోల్డింగ్ సమయంలో, కుహరంలోని పీడనం తగినంతగా ఉండదు, శీతలీకరణ ప్రక్రియలో పదార్థం అచ్చు యొక్క ఉపరితలంపై అతుక్కొని, సంకోచం గుర్తులను వదిలివేస్తుంది.
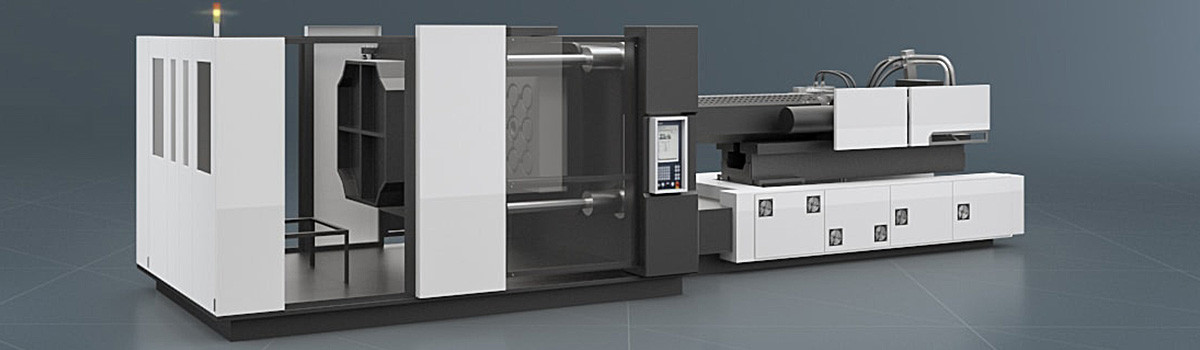
ఫ్లో మార్కులు
బహుళ రూపాల్లో ఉత్పత్తుల ఉపరితలంపై ఫ్లో గుర్తులను కనుగొనవచ్చు. సాధారణంగా, ఇది నీడ ప్రాంతాన్ని ఏర్పరుస్తుంది.
ప్రవాహ గుర్తులు ఉత్పత్తుల ఉపరితలంపై ఎటువంటి ఎంబాసింగ్ లేదా డిప్రెషన్ను ఉత్పత్తి చేయవు, వీటిని వేళ్లతో అనుభూతి చెందలేరు. ఈ లోపాన్ని డ్రాగ్ మార్క్స్, గోస్టింగ్ మరియు షాడోస్ అని కూడా అంటారు.
ప్రవాహ గుర్తులు స్పష్టంగా ఉన్నప్పుడు, అది పొడవైన కమ్మీలను సృష్టిస్తుంది మరియు ఉత్పత్తుల ఉపరితలంపై గుర్తుల వంటి లోపాలను వదిలివేస్తుంది.
కారణం:
ఫ్లో మార్కులను ఎప్పుడు కనుగొనవచ్చు:
కరిగే ప్రవాహ సామర్థ్యం తక్కువగా ఉంటుంది లేదా అచ్చు యొక్క ఉపరితల ఉష్ణోగ్రత తక్కువగా ఉంటుంది, ఫలితంగా అచ్చు నింపే ప్రక్రియలో ప్లాస్టిక్ యొక్క పెద్ద ప్రవాహ నిరోధకత ఏర్పడుతుంది.
మోల్డ్ ఫిల్లింగ్లో, రెసిస్టెన్స్తో కరిగే ప్రవాహం, ఇది డై యొక్క అసమాన ఉపరితలం, డై ఉపరితలంపై ముద్రించిన గుర్తులు లేదా నమూనాలు లేదా ఫిల్లింగ్ ప్రక్రియలో కరిగే ప్రవాహ దిశలో మార్పు వల్ల సంభవించవచ్చు.
జాయింటింగ్ లైన్
మౌల్డ్ ఫిల్లింగ్ సమయంలో రెండు మెల్ట్ ఫ్రంట్లు కలిసినప్పుడు జాయినింగ్ లైన్ ఉత్పత్తి అవుతుంది మరియు ఉత్పత్తి యొక్క ఉపరితలంపై లైన్ లాగా కనిపిస్తుంది.
జాయింటింగ్ లైన్ అనేది ఉత్పత్తుల ఉపరితలంపై క్రాకింగ్ లైన్ లాంటిది, ఇది గుర్తించడానికి స్పష్టంగా లేదు.
అచ్చులను రూపకల్పన చేసేటప్పుడు, కొన్ని కనిపించే జాయింటింగ్ లైన్లు అనివార్యం. ఈ సందర్భంలో, దెబ్బతిన్న ఉత్పత్తుల బలం మరియు రూపాన్ని నిరోధించడానికి వీలైనంత వరకు జాయింటింగ్ లైన్ను తగ్గిస్తుంది.
కారణం:
మెల్ట్ ఫ్రంట్ యొక్క తరానికి చాలా కారణాలు ఉన్నాయి. అత్యంత సాధ్యమైన కారణం అచ్చు కోర్ అంచుల వెంట కరిగే ప్రవాహం కావచ్చు. రెండు కరిగినప్పుడు, అది జాయింటింగ్ లైన్లను ఉత్పత్తి చేస్తుంది. రెండు కరిగే ముందు ఉష్ణోగ్రత వాటిని విజయవంతంగా కలిసిపోయేలా చేయడానికి తగినంత ఎక్కువగా ఉండాలి మరియు ఉత్పత్తుల బలం మరియు రూపాన్ని ప్రభావితం చేయదు.
రెండు కరిగినవి పూర్తిగా కలిసిపోలేనప్పుడు, లోపాలు ఉత్పత్తి అవుతాయి.
లోపాల కారణాలు:
అచ్చు మందంగా మరియు సన్నగా ఉండే భాగాలను కలిగి ఉంటుంది మరియు కరిగే ప్రవాహ వేగం భిన్నంగా ఉంటుంది, కరుగు అచ్చు యొక్క పలుచని భాగం ద్వారా ప్రవహించినప్పుడు, ఉష్ణోగ్రత తక్కువగా ఉంటుంది.
ప్రతి రన్నర్ యొక్క పొడవు భిన్నంగా ఉంటుంది. ఒంటరి రన్నర్లను చల్లబరచడం సులభం అవుతుంది.
అచ్చు కుహరం పీడనం ఒత్తిడిని పట్టుకునే దశలో పూర్తిగా కరిగిపోయేలా చేయడానికి సరిపోదు.
మిగిలిన బుడగలు కరిగే ఫ్రంట్ను ఫ్యూజ్ చేయలేకుండా చేస్తాయి, ఇది దహనానికి కూడా దారి తీస్తుంది.
బర్నింగ్
బర్నింగ్ షార్ట్ షాట్ మాదిరిగానే ఉంటుంది, కానీ సక్రమంగా ఫేడింగ్ అంచులు మరియు కొంచెం మండే వాసనతో ఉంటుంది. పరిస్థితి తీవ్రంగా ఉన్నప్పుడు, ప్లాస్టిక్ బర్నింగ్ వాసనతో పాటు కార్బన్ బ్లాక్ ప్రాంతాలు ఉత్పత్తిపై కనిపిస్తాయి.
లోపాలు తొలగించబడకపోతే, అచ్చుపై తరచుగా నలుపు నిక్షేపణ ఉంటుంది. బర్నింగ్ ద్వారా ఉత్పత్తి చేయబడిన గ్యాస్ లేదా చమురు పదార్థాలను వెంటనే తనిఖీ చేయకపోతే, అవి గాలి రంధ్రాలను నిరోధించవచ్చు. బర్నింగ్ సాధారణంగా మార్గాల చివరలో కనిపిస్తుంది.
కారణం:
అంతర్గత దహన ప్రభావం వల్ల బర్నింగ్ జరుగుతుంది. చాలా తక్కువ సమయంలో గాలిలో ఒత్తిడి తీవ్రంగా పెరిగినప్పుడు, ఉష్ణోగ్రత పెరుగుతుంది మరియు దహనం అవుతుంది. సేకరించిన డేటా ప్రకారం, ఇంజెక్షన్ మౌల్డింగ్ ప్రక్రియలో అంతర్గత దహన ప్రభావం 600 డిగ్రీల వరకు అధిక ఉష్ణోగ్రతను ఉత్పత్తి చేస్తుంది.
బర్నింగ్ ఎప్పుడు ఉత్పత్తి కావచ్చు:
అచ్చు నింపే వేగం వేగంగా ఉంటుంది, తద్వారా అచ్చు కుహరం నుండి గాలిని తొలగించలేరు మరియు ఇన్కమింగ్ ప్లాస్టిక్ బ్లాక్ కారణంగా గాలి బుడగలు ఏర్పడతాయి మరియు కంప్రెస్ చేయబడిన తర్వాత అంతర్గత దహన ప్రభావానికి దారి తీస్తుంది.
గాలి రంధ్రాలు నిరోధించబడ్డాయి లేదా వెంటిలేషన్ మృదువైనది కాదు.
అచ్చులోని గాలిని గాలి రంధ్రాల నుండి తొలగించాలి. స్థానం, సంఖ్య, పరిమాణం లేదా ఫంక్షన్ల ద్వారా వెంటిలేషన్ ప్రభావితమైతే, గాలి అచ్చులో ఉండి దహనానికి దారి తీస్తుంది. పెద్ద అచ్చు బిగింపు శక్తి కూడా పేలవమైన వెంటిలేషన్కు దారి తీస్తుంది.
సంకోచం
సంకోచం అనేది ఉత్పత్తుల ఉపరితలంపై కొంచెం బోలులను సూచిస్తుంది.
లోపాలు తక్కువగా ఉన్నప్పుడు, ఉత్పత్తుల ఉపరితలం అసమానంగా ఉంటుంది. ఇది తీవ్రంగా ఉన్నప్పుడు, ఉత్పత్తుల యొక్క పెద్ద ప్రాంతం కూలిపోతుంది. తోరణాలు, హ్యాండిల్స్ మరియు ప్రోట్రూషన్లతో కూడిన ఉత్పత్తులు తరచుగా సంకోచం లోపాలతో బాధపడుతుంటాయి.
కారణం:
శీతలీకరణ సమయంలో ముడి పదార్థాల పెద్ద-ప్రాంతం సంకోచం కారణంగా సంకోచం ఏర్పడుతుంది.
ఉత్పత్తుల యొక్క మందపాటి ప్రాంతంలో (వంపు వంటిది), పదార్థం యొక్క ప్రధాన సమశీతోష్ణత తక్కువగా ఉంటుంది, కాబట్టి సంకోచం ఉపరితలం కంటే తరువాత సంభవిస్తుంది, ఇది ముడి పదార్థం లోపల సంకోచ శక్తిని ఉత్పత్తి చేస్తుంది మరియు బయటి భాగాన్ని లోపలి మాంద్యంలోకి లాగుతుంది. సంకోచాన్ని ఉత్పత్తి చేయడానికి.
కింది పరిస్థితులలో సంకోచాలు సంభవిస్తాయి:
శీతలీకరణ ప్రక్రియలో ముడి పదార్థం యొక్క సంకోచం నుండి ఉత్పన్నమయ్యే శక్తి కంటే అచ్చు కుహరంలో ఒత్తిడి తక్కువగా ఉంటుంది.
శీతలీకరణ ప్రక్రియలో అచ్చు కుహరం యొక్క తగినంత ఒత్తిడి సమయం ఉండదు, ఫలితంగా ముడి పదార్థం గేట్ నుండి కుహరం నుండి బయటకు వస్తుంది.
మౌల్డింగ్ మరియు ప్రెజర్ హోల్డింగ్ దశలో ముడి పదార్థం తగినంత బఫరింగ్ సామర్థ్యాన్ని కలిగి ఉండదు, ఎందుకంటే అధిక ముడి పదార్థాన్ని ఇంజెక్ట్ చేయడానికి ముందు స్క్రూ పూర్తిగా ఉపసంహరించబడుతుంది.
గేట్లు మరియు రన్నర్ల క్రాస్ సెక్షన్ ప్రాంతాలు ఉత్పత్తుల మందం కంటే చాలా చిన్నవి, అంటే ఉత్పత్తుల వెలికితీత ప్రక్రియకు ముందు గేట్లు ఇప్పటికే స్తంభింపజేయబడ్డాయి.
బుడగలు
వాక్యూమ్ బుడగలు గాలి బుడగలు రూపంలో ప్రదర్శించబడతాయి, ఇవి పారదర్శక ఉత్పత్తులపై సులభంగా కనుగొనబడతాయి. ఇది అపారదర్శక ఉత్పత్తుల యొక్క క్రాస్ సెక్షన్లో కూడా చూడవచ్చు.
కారణం:
గాలి బుడగలు అనేది ఉత్పత్తుల యొక్క వాక్యూమ్ భాగం, ఇది శీతలీకరణ ప్రక్రియలో ముడి పదార్థం తగ్గిపోయినప్పుడు ఉత్పత్తి అవుతుంది.
సంకోచం వలె, ముడి పదార్థం లోపలి భాగం సంకోచ శక్తిని ఉత్పత్తి చేస్తుంది. తేడా ఏమిటంటే, బుడగలు ఏర్పడినప్పుడు ఉత్పత్తుల యొక్క బాహ్య రూపం పటిష్టం చేయబడింది మరియు పతనం లేదు, కాబట్టి బోలు బుడగలు ఉత్పన్నమవుతాయి.
బుడగలు తగ్గడానికి గల కారణాలు, వాటితో సహా:
అసమర్థమైన అచ్చు కుహరం ఒత్తిడి
తగినంత కుహరం ఒత్తిడి సమయం
రన్నర్ మరియు గేట్ పరిమాణం చాలా చిన్నది
స్ప్రేయింగ్ మార్కులు
స్ప్రేయింగ్ మార్కులు గేట్ ఎదురుగా ఉన్న థ్రెడ్ ప్రాంతాన్ని సూచిస్తాయి. స్ప్రేయింగ్ మార్కులు ఉత్పత్తుల రూపాన్ని ప్రభావితం చేయడమే కాకుండా, ఉత్పత్తుల బలాన్ని కూడా ప్రభావితం చేస్తాయి.
కారణం:
స్ప్రేయింగ్ మార్కులు అచ్చు నింపే ప్రక్రియలో నియంత్రణ లేకుండా కరుగుతాయి.
కరిగిన ప్లాస్టిక్ భారీ ఒత్తిడిలో అచ్చులోకి వస్తుంది. అచ్చు నింపే వేగం చాలా ఎక్కువగా ఉంటే, ప్లాస్టిక్ అచ్చు కుహరం యొక్క ఓపెన్ గ్యాప్ నుండి బయటకు వస్తుంది మరియు త్వరగా తిరిగి మరియు చల్లబరుస్తుంది. ఆ సమయంలో, థ్రెడ్లు ఏర్పడతాయి, ఇది గేట్లలోకి ప్రవేశించే కరిగిన ప్లాస్టిక్ను అడ్డుకుంటుంది.
స్ప్రేయింగ్ మార్కులకు ప్రధాన కారణం గేట్ల యొక్క సరికాని స్థానం లేదా గేట్ రూపకల్పన. కింది రెండు పరిస్థితులు లోపాల పరిస్థితిని మరింత తీవ్రతరం చేస్తాయి:
అధిక అచ్చు నింపే వేగం
అచ్చు నింపే సమయంలో పేలవమైన కరిగే ప్రవాహం