భారతదేశంలో కేసు
భారతీయ కంపెనీల కోసం ఇంజెక్షన్ మోల్డింగ్ సేవలో DJmolidng యొక్క ఇన్సర్ట్ మోల్డ్
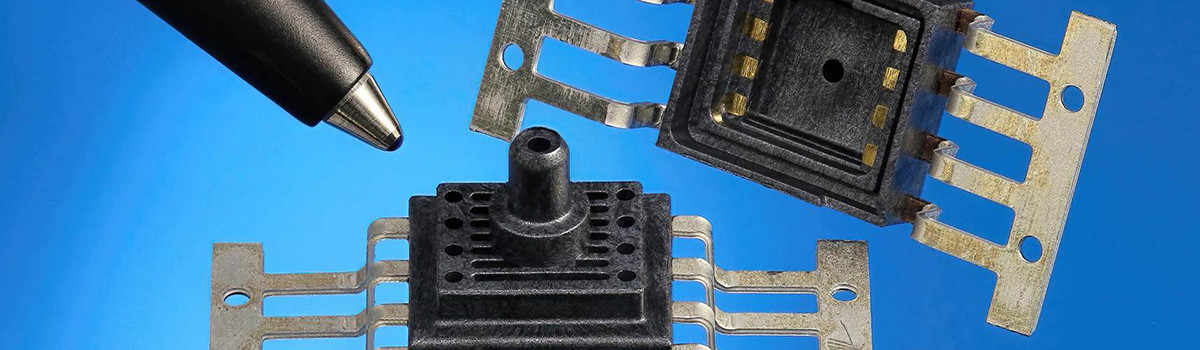
చొప్పించు అచ్చు సాధారణంగా ఒక రకమైన అచ్చు, ఇది ఇంజెక్షన్ మౌల్డింగ్ కోసం కావిటీస్ లోపల స్థిరపడిన గింజలు, లోహ భాగాలు లేదా గట్టి ప్లాస్టిక్ భాగాలను తయారు చేస్తుంది.
DJmolding భారతదేశ మార్కెట్ కోసం ఇన్సర్ట్ mlod ఇంజెక్షన్ మోల్డింగ్ సేవను అందిస్తోంది మరియు మేము వివిధ పరిశ్రమల కోసం, ప్రత్యేకించి గృహోపకరణాల తయారీదారుల కోసం చాలా ఇన్సర్ట్ మోల్డింగ్ యొక్క ప్లాస్టిక్ భాగాలను ఉత్పత్తి చేస్తాము. కొంతమంది భారతీయ గృహోపకరణాల తయారీదారులు ఇన్సర్ట్ మోల్డింగ్ యొక్క ప్లాస్టిక్ భాగాలను చాలా కాలం పాటు DJmolding రూపంలో కొనుగోలు చేస్తారు. ఈ భారత కంపెనీలతో మాకు చాలా మంచి భాగస్వామ్యం ఉంది.
గింజలు ఇంజెక్షన్ మౌల్డింగ్ను చొప్పించండి: గింజల పదార్థం స్టెయిన్లెస్ స్టీల్, రాగి, కాంస్య మరియు ఉక్కు కావచ్చు, సాధారణంగా రాగి గింజలను సాధారణంగా ఉపయోగిస్తారు. గింజలు మరియు ప్లాస్టిక్లు మెరుగ్గా స్ప్లైస్ చేయడానికి రాగి సులువుగా ఉంటుంది. గింజ లోపలి బోర్ల యొక్క సహనాన్ని 0.02mm లోపల నియంత్రించాలి, లేకుంటే 0.02mm మించి ఉంటే సులభంగా ఫ్లాష్ని కలిగిస్తుంది. అచ్చు అమర్చడంలో, పరీక్ష కోసం ఇన్సర్ట్ పిన్స్లో గింజలను సమీకరించడం అవసరం. ఇది గింజలు మరియు పిన్ల మధ్య బిగుతుగా ఉంటే, భాగాన్ని ఎజెక్ట్ చేయడం కష్టంగా ఉంటుంది మరియు ఎజెక్ట్ మార్కులు లేదా అంటుకునే సమస్యలను కలిగిస్తుంది. ఇది వదులుగా ఉంటే, అది ఫ్లాష్కు కారణం అవుతుంది.
లోహ భాగాల ఇంజెక్షన్ మౌల్డింగ్ను చొప్పించండి:
మెటల్ భాగాలు స్టెయిన్లెస్ స్టీల్, అల్యూమినియం, రాగి, ఉక్కు మొదలైనవి కావచ్చు. మెటల్ భాగాల యొక్క సహనం 0.02mm లోపల నియంత్రించబడాలి, లేకుంటే మెటీరియల్ని మూసివేయడం కష్టం మరియు ఫ్లాష్ని కలిగి ఉండటం సులభం. మెటల్ భాగాల విస్తీర్ణం చాలా పెద్దదిగా రూపొందించబడదు.
మెటల్ భాగాలకు పూరించే విస్తీర్ణం చాలా పెద్దది అయితే, మెటల్ భాగాల మధ్య గొప్ప ఉష్ణోగ్రత వ్యత్యాసంగా పూర్తిగా ఇంజెక్షన్ సాధించడం చాలా కష్టం. లోహ భాగాల స్థానాలు సాధారణంగా కుహరంలో రూపొందించబడతాయి, ఎందుకంటే కుహరం కదలదు, ఇది లోహ భాగాలు కదులుతున్నప్పుడు (తీవ్రమైన సందర్భంలో, అచ్చుకు హాని కలిగించవచ్చు) ఫ్లాష్ ఫలితాన్ని నివారించడంలో సహాయపడుతుంది. ప్రత్యేక సందర్భాలలో, మెటల్ భాగాల స్థానాలు ఉత్పత్తి యొక్క కోర్ లేదా సైడ్ ఉపరితలంలో మాత్రమే రూపొందించబడతాయి.
హార్డ్ ప్లాస్టిక్ ఇంజెక్షన్ అచ్చును చొప్పించండి:
సాధారణంగా PEEK, PA66+30GF, PP+30GF, PA12+30GF, PPS....మొదలైన అధిక ద్రవీభవన స్థానం కలిగిన గట్టి ప్లాస్టిక్లను ఎంచుకోండి. ఈ హార్డ్ ప్లాస్టిక్లకు సహనం ఖచ్చితంగా ఉండాలి. సంకోచం, డెంట్ మరియు వైకల్యం వంటి లోపాలు సీలింగ్ ప్రాంతంలో ఉండకూడదు. మోల్డ్ ఫిట్టింగ్లో, గట్టి ప్లాస్టిక్ను పరీక్ష కోసం అచ్చు లోపల ఉంచాలి మరియు మెరుగైన సీలింగ్ సాధించడానికి సీలింగ్ ప్రాంతం చుట్టూ 0.05-0.1mm ముందుగా నొక్కాలి.
గట్టి ప్లాస్టిక్ భాగాన్ని చాలా పెద్ద విస్తీర్ణంలో డిజైన్ చేయకూడదు, ఇది ఉష్ణోగ్రత వ్యత్యాసాన్ని కలిగిస్తుంది మరియు ఇంజెక్షన్లో మెటీరియల్ని నింపడం కష్టతరం చేస్తుంది. సాధారణంగా గట్టి ప్లాస్టిక్ భాగాన్ని కుహరం వైపున అమర్చండి, ఎందుకంటే కుహరం కదలదు , అచ్చు కదులుతున్నప్పుడు ఫ్లాష్ లేదా హాని కలిగించే అచ్చును నివారించడానికి. ప్రత్యేక సందర్భాలలో, మెటల్ భాగాల స్థానాలు ఉత్పత్తి యొక్క కోర్ లేదా సైడ్ ఉపరితలంలో మాత్రమే రూపొందించబడతాయి.
కీలక అంశాలను డిజైన్ చేయండి
1.నట్స్ ఇన్సర్ట్లతో ఉత్పత్తుల కోసం డిజైన్ సంకోచం, మెటల్ భాగాలు మరియు హార్డ్ ప్లాస్టిక్ ఇన్సర్ట్లతో ఉత్పత్తులకు డిజైన్ సంకోచం అవసరం లేదు. కఠినమైన సహనం అవసరమయ్యే ప్రాంతాల కోసం, ఉత్పత్తుల పరిమాణాన్ని మధ్యస్థంగా మార్చండి.
2.సాధారణంగా మోల్డ్ డిజైనింగ్లో స్టాండర్డ్ పిన్-పాయింట్ గేట్తో మోల్డ్ బేస్ని అవలంబించండి మరియు సెకండరీ ఇంజెక్షన్లో, ఇన్సర్టింగ్ పార్ట్లను వీలైనంత వరకు కుహరంలో ఉంచండి. కుహరంలో స్థిరపడిన ఇన్సర్ట్లను తయారు చేసే షరతుపై, ఇంజెక్షన్ మౌల్డింగ్ తర్వాత కోర్లో మిగిలి ఉన్న భాగాన్ని ఎలా తయారు చేయాలో పరిశీలించండి, ఈ విధంగా, భాగాన్ని బయటకు తీయవచ్చు. సాధారణంగా కుహరంలో సాగే బ్లాక్లను మరియు కోర్లో భాగం ఉండేలా సాగే జిగురును జోడించండి. సాగే బ్లాక్లు మరియు జిగురు మధ్య దూరం చాలా పెద్దదిగా ఉండకూడదు, లేకుంటే సాగే శక్తి గట్టి ప్లాస్టిక్ లేదా లోహ భాగాల వైకల్పనానికి కారణమవుతుంది. దూరం సాధారణంగా 2mm లోపల రూపొందించబడింది మరియు మెటల్ లేదా హార్డ్ ప్లాస్టిక్ ఇన్సర్ట్లు సాపేక్షంగా పెద్ద విస్తీర్ణం కలిగి ఉన్నప్పుడు సాగే బ్లాక్లు మరియు సాగే జిగురు పరిమాణాన్ని తగిన విధంగా పెంచండి.
3.మెటీరియల్ యొక్క మందం 1.3-1.8mm (సుమారు 1.5mm ఉత్తమం) లోపల ఉత్తమంగా ఉంటుంది, కాకపోతే, ఉత్పత్తి డ్రాయింగ్ల ద్వారా తనిఖీ చేసి, కస్టమర్ దానిని సవరించమని సూచించాలి. మెటీరియల్ మందం 1.3 మిమీ కంటే సన్నగా ఉంటే, మెటీరియల్ నింపడం కష్టం, అయితే మెటీరియల్ మందం 1.8 మిమీ కంటే మందంగా ఉంటుంది, ఉత్పత్తిలో సంకోచం చాలా సులభం.
4. అచ్చులో గేటింగ్ చాలా ముఖ్యమైనది. గేట్ పాయింట్ కోసం మెటీరియల్ ఫిల్లింగ్ యొక్క బ్యాలెన్స్ను పూర్తిగా పరిగణించాలి.మెటీరియల్ మెటల్ లేదా హార్డ్ ప్లాస్టిక్ పార్ట్లు స్థిరంగా ఉన్న ప్రాంతానికి పరిగెత్తినప్పుడు, ఇన్సర్ట్ల నిరోధకత మరియు ఉష్ణోగ్రత వ్యత్యాసం కారణంగా మెటీరియల్ ఫిల్లింగ్ మరియు పీడనం వేగం తగ్గుతుంది.
5.అచ్చు ఎజెక్టర్ వ్యవస్థ కోసం, ఎజెక్టింగ్ యొక్క సమతుల్యతను తప్పనిసరిగా పరిగణించాలి లేదా ఎజెక్ట్ చేసిన తర్వాత వైకల్యం జరుగుతుంది. భాగాలను బ్యాలెన్స్లో ఎజెక్ట్ చేయడం సాధ్యం కాదు, నిర్మాణ రూపకల్పనలో బ్యాలెన్స్ సమస్యను మెరుగుపరచడానికి కూలిపోవడాన్ని పరిగణించాలి.
6.ఇంజెక్షన్ మౌల్డింగ్లో ఎజెక్ట్ చేయబడిన తర్వాత పార్ట్లు కనిపించే అర్హతను నిర్ధారించడానికి, ఎజెక్టర్ పరికరం తప్పనిసరిగా ABS లేదా PMMAతో చొప్పించిన గట్టి ప్లాస్టిక్ గడ్డ అయి ఉండాలి. ఓవర్ మోల్డ్ స్లయిడ్ సీలింగ్ కలిగి ఉంటే, కుహరంలో స్లయిడ్లను వీలైనంత వరకు డిజైన్ చేయండి, ఎందుకంటే కుహరంలోని స్లయిడ్లు అచ్చును అమర్చడాన్ని సులభతరం చేస్తాయి.
7.సీలింగ్ SA (సీమ్ అలవెన్స్) యొక్క బలాన్ని నిర్ధారించడానికి, రెండుసార్లు ఇంజెక్షన్ మౌల్డింగ్ నుండి తయారు చేయబడిన ఉత్పత్తి కోసం, సీలింగ్ SA యొక్క వెడల్పు కనీసం 0.8mm ఉండాలి. సెకండరీ ఇంజెక్షన్ మెటీరియల్ హార్డ్ ప్లాస్టిక్గా ఉంటుంది, సీలింగ్ SA యొక్క వెడల్పు కనీసం 1.0mm ఉండాలి, లేకపోతే, ఉత్పత్తిని సవరించమని కస్టమర్ను సూచించాలి.
8.అచ్చు రూపకల్పనలో, నిలువుగా లేదా అడ్డంగా ఏ రకమైన యంత్రాన్ని అవలంబిస్తారో చూడడానికి ఉత్పత్తి కోసం ఇంజెక్షన్ మోల్డింగ్ మెషీన్లను పరిగణనలోకి తీసుకోవాలి. చాలా కావిటీలను డిజైన్ చేయవద్దని సూచించబడింది, ముఖ్యంగా కోల్డ్ రన్నర్లతో అచ్చు కోసం చాలా కావిటీలు రన్నర్ను ఎక్కువసేపు చేస్తాయి, పదార్థాన్ని వృధా చేస్తాయి మరియు అధిక సామర్థ్యం గల ఇంజెక్షన్ సాధించడానికి కూడా హానికరం. ఇంజెక్షన్ మౌల్డింగ్ మెషీన్తో సరిపోలడానికి, ఉత్పత్తి ఏర్పాట్లకు ఇది కాంపాక్ట్ మరియు సహేతుకమైనదా కాదా అని మనం పరిగణించాలి. ఉత్పత్తులు అచ్చులో ఉంచబడిన ప్రతిసారీ అదే పరిస్థితిలో ఉన్నాయని నిర్ధారించడానికి ఉత్పత్తులను తప్పనిసరిగా స్థిరపరచాలి. అచ్చు మూసివేయడానికి ముందు భాగం సరైన స్థలంలో లేకుంటే అప్రమత్తం చేయడానికి డిజైన్ రియాక్షన్ సిస్టమ్ మరొక మార్గం, ఇది అచ్చు మూసివేయడాన్ని ఆపడానికి సహాయపడుతుంది. ఈ విధంగా, భాగాలు అచ్చులో అదే పరిస్థితిలో ఉంటాయి, ఇది ఇంజెక్షన్ మోల్డింగ్లో అర్హత కలిగిన రేట్లు మరియు ఉత్పత్తి సామర్థ్యాన్ని పెంచుతుంది.
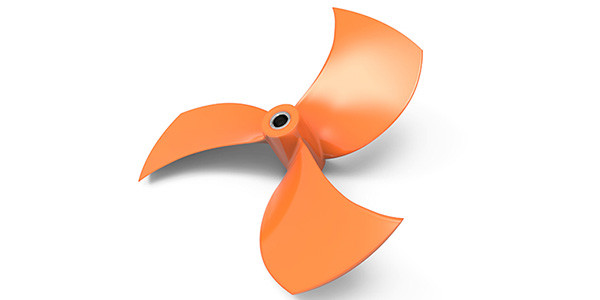
9.అచ్చు ఇంజెక్షన్ ప్రాంతం ఇంజెక్షన్లో అధిక ఒత్తిడిని కలిగి ఉన్నందున ఉక్కు మద్దతును తప్పనిసరిగా రూపొందించాలి (ఆకారం మరియు పరిమాణంలో భాగం కంటే 5-10 మిమీ పెద్దదిగా ఉండాలి). ఓవర్-మోల్డింగ్ ప్రాంతం చుట్టూ భాగాల మధ్య ఖాళీని వదిలివేయకూడదు, లేకుంటే సెకండరీ ఇంజెక్షన్ తర్వాత భాగం ఆకారంలో ఉండదు. SA (సీమ్ అలవెన్స్) లేని భాగాల కోసం ఈ అంశానికి ఎక్కువ శ్రద్ధ అవసరం.
10.ఎయిర్ ట్రిప్ సులభం ఇంజెక్షన్ మోల్డింగ్లో ఎయిర్ ట్రిప్ సులభంగా జరుగుతుంది, కాబట్టి అచ్చు డిజైనింగ్లో వెంటింగ్ను పూర్తిగా పరిగణించాలి. సుదూర నీటి లైన్ కోసం అన్ని బ్లైండ్ యాంగిల్స్ మరియు పొజిషన్లలో, బ్లైండ్ యాంగిల్స్లో మెటీరియల్ని పూరించడం చాలా కష్టం కాబట్టి గట్టి ప్లాస్టిక్ భాగంలో తప్పనిసరిగా వెంటింగు రంధ్రాలను డిజైన్ చేయాలి.
11.ఇంజెక్ట్ చేయబడిన మెటీరియల్ మరియు క్వాలిఫైడ్ థ్రస్ట్ పూర్తిగా నింపబడిందని నిర్ధారించడానికి, అంటుకునే ఫలితాన్ని మెరుగుపరచడానికి భాగం యొక్క మూలల్లో అండర్కట్లను రూపొందించడం మరియు ఆపై భాగాలు మరింత గట్టిగా కట్టుబడి ఉండేలా చేయడం ఒక మార్గం.
12.సీలింగ్ ఏరియా మరియు పార్టింగ్ లైన్ ఏరియాలో, మేము కేవిటీ మరియు కోర్ నుండి డీమోల్డ్ చేయకూడదు, ఎందుకంటే అచ్చులో లైన్లను బిగించడం మరియు డ్రాఫ్ట్ డెమోల్డింగ్ చేయడం వల్ల మోల్డ్ ఫిట్టింగ్లో ఫ్లాష్ ఏర్పడుతుంది. LISS-OFF ద్వారా డెమోల్డ్ చేయడానికి ప్రయత్నించండి.
ఇన్సర్ట్ అచ్చు యొక్క గేట్ పాయింట్ రకాలు
ఇన్సర్ట్ అచ్చు కోసం గేట్ పాయింట్ను హాట్ స్ప్రూ వాల్వ్ గేట్, హాట్ స్ప్రూ పిన్ గేట్, పిన్-పాయింట్ గేట్, సబ్ గేట్, ఎడ్జ్ గేట్... మొదలైన వాటికి డైరెక్ట్ చేయడానికి డిజైన్ చేయవచ్చు.
హాట్ స్ప్రూ వాల్వ్ గేట్: మంచి లిక్విడిటీ, పొజిషన్ ఎంచుకునే సౌకర్యవంతమైన, చిన్న గేట్ పాయింట్. భారీ ఉత్పత్తికి మరియు మందపాటి గోడ మందంతో ఉన్న ఉత్పత్తులకు సూట్లు. మెటీరియల్ని ఆదా చేయడంలో సహాయపడవచ్చు, గేట్కు మెటీరియల్ వేస్ట్ లేదు, తక్కువ లీడ్ టైమ్ మరియు అధిక నాణ్యత. చిన్న గేటింగ్ ట్రేస్ మాత్రమే లోపం.
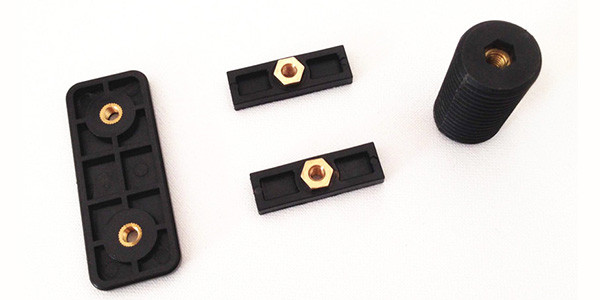
హాట్ స్ప్రూ పిన్ గేట్: మంచి లిక్విడిటీ, పొజిషన్ ఎంచుకునే సౌకర్యవంతమైన, చిన్న గేట్ పాయింట్. భారీ ఉత్పత్తికి మరియు మందపాటి గోడ మందంతో ఉన్న ఉత్పత్తులకు సూట్లు. మెటీరియల్ని ఆదా చేయడంలో సహాయపడవచ్చు, గేట్కు మెటీరియల్ వేస్ట్ లేదు, తక్కువ లీడ్ టైమ్ మరియు అధిక నాణ్యత. కానీ గేట్ పాయింట్ చుట్టూ 0.1mm మెటీరియల్ మిగిలి ఉంది మరియు బర్ర్ చేయడం సులభం వంటి లోపాలు ఉన్నాయి. గేట్ పాయింట్ చుట్టూ ఎడమ మెటీరియల్ను కవర్ చేయడానికి పొడవైన కమ్మీలు తయారు చేయాలి.
పిన్ పాయింట్ గేట్: సౌకర్యవంతమైన, బలహీనమైన లిక్విడిటీ, లాంగ్ రన్నర్ దూరం, చిన్న గేట్ పాయింట్ని ఎంచుకునే స్థానం. చిన్న బ్యాచ్ ఉత్పత్తి కోసం సూట్లు. గేట్ పాయింట్ చుట్టూ ఎక్కువ వ్యర్థ పదార్థాలు. ఉత్పత్తిలో గేట్ పాయింట్ను బిగించడానికి యాంత్రిక ఆయుధాలు అవసరం. లాంగ్ లీడ్ టైమ్. లోపం గేట్ పాయింట్ చుట్టూ 0.1-0.2mm పదార్థం మిగిలి ఉంది, గేట్ పాయింట్ చుట్టూ ఎడమ మెటీరియల్ను కవర్ చేయడానికి పొడవైన కమ్మీలను తయారు చేయాలి.
ఉప ద్వారం: కేవిటీ, కోర్, సైడ్ వాల్స్ మరియు ఎజెక్టర్ పిన్స్లోని పక్కటెముకల మీద డిజైన్ చేయవచ్చు. గేట్ పాయింట్ను ఫ్లెక్సిబుల్గా ఎంచుకోవచ్చు, పోయరింగ్ గేట్ ఆటోమేటిక్గా భాగం నుండి వేరు చేయబడుతుంది, కొంచెం గేటింగ్ ట్రేస్. లోపాలు: గేట్ పాయింట్ చుట్టూ ఉన్న మెటీరియల్ని బయటకు తీయడం సులభం, గేటింగ్ పొజిషన్లో డ్రైయింగ్ మార్క్లను కలిగించడం సులభం, మెటీరియల్ను చేతితో తుడిచివేయడం అవసరం, కావిటీస్ నుండి గేట్ పాయింట్ నుండి చాలా ప్రెస్ లాస్.
ఎడ్జ్ గేట్: కరిగిన ప్లాస్టిక్ గేట్ ద్వారా ప్రవహిస్తుంది, పార్శ్వంగా సమానంగా కేటాయించబడుతుంది, ఒత్తిడిని తగ్గిస్తుంది; గాలి కుహరంలోకి ప్రవేశించే అవకాశాన్ని తగ్గించండి, చారలు మరియు బుడగలు ఏర్పడకుండా నివారించండి. లోపాలు: పోయడం గేట్ స్వయంచాలకంగా భాగం నుండి వేరు చేయబడదు, పార్ట్ అంచులలో స్ప్రూ గుర్తులను వదిలివేయడం, గేట్ ఫ్లాట్గా పోయడాన్ని ప్రాసెస్ చేయడానికి సాధనాలు అవసరం. ఎడ్జ్ గేట్ ప్రొపోర్షన్ ఇంజెక్షన్ మరియు ప్రెజర్ హోల్డింగ్లో సహాయపడుతుంది మరియు ప్రెజర్ హోల్డింగ్ మరియు ఫీడింగ్కి కూడా మంచిది, ఈ విధంగా, ఎయిర్ లైన్లు, ఫ్లో మార్కులు... మొదలైన వాటిని మెరుగుపరచడానికి ఇది ఉత్తమం.
ఇన్సర్ట్ అచ్చు కోసం ప్రాసెసింగ్ మరియు అమర్చడం
1.ప్రాసెసింగ్ చేయడానికి ముందు, అచ్చు యొక్క ప్రాసెసింగ్ టెక్నాలజీని రూపొందించండి. హై-ప్రెసిషన్ ప్రాసెసింగ్ మెషీన్లు, హై-స్పీడ్ మెషిన్, స్లో-ఫీడింగ్ NC వైర్ కట్ మెషిన్, మిర్రర్ EDM(ఎలక్ట్రిక్ డిశ్చార్జ్ మ్యాచింగ్) మెషిన్ మొదలైనవాటిని ఎంచుకోండి.
2.డిజైన్ 0.05-0.1mm ముందుగా నొక్కే ప్రదేశంలో మిగిలి ఉంది.
3.అచ్చు బేస్ ప్రాసెసింగ్లో ఖచ్చితమైన అవసరాలను గమనించండి, మోల్డ్ బేస్ పొందిన తర్వాత సహనాన్ని తనిఖీ చేయండి మరియు టాలరెన్స్ అర్హత లేనిది అయితే దానిని ఉపయోగించవద్దు.
4.అచ్చు అమర్చడం కోసం అచ్చు లోపల గింజలు, మెటల్ భాగాలు మరియు గట్టి ప్లాస్టిక్ భాగాలను ఉంచండి. అచ్చును అమర్చడంలో సమస్యలను కనుగొంటే, గింజలు, లోహ భాగాలు, గట్టి ప్లాస్టిక్ భాగాలు మరియు అచ్చులను పరిశీలించి ఏది తప్పుగా ఉందో చూడండి. సాధ్యమైనంతవరకు డ్రాయింగ్ ప్రకారం భాగాన్ని ప్రాసెస్ చేయండి, ఇది భవిష్యత్తులో డేటాను కనుగొనడంలో సహాయపడుతుంది.
5.అచ్చు అమర్చడం కోసం గ్రైండర్ను ఉపయోగించలేరు. అచ్చు అమర్చడం మంచిది కాని చోట సరిదిద్దడానికి యంత్రాలను ఆశ్రయించండి.
6.ట్రయల్కు ముందు యాక్షన్ టెస్టింగ్ చేయండి, అసెంబ్లింగ్ మిస్ అవ్వడం మరియు తప్పుగా అసెంబ్లింగ్ చేయడాన్ని నివారించండి. తప్పుగా అసెంబ్లింగ్ చేయడం వల్ల అచ్చు బేస్ దెబ్బతింటుంది.
ఇన్సర్ట్ అచ్చు కోసం అచ్చు పరీక్ష
1.అచ్చు పరీక్షలో, అచ్చును తెరవడం, మూసివేయడం మరియు బయటకు తీయడం వంటి క్రమాల గురించి స్పష్టంగా తెలుసుకోవాలి. మెటల్ భాగాలు మరియు హార్డ్ ప్లాస్టిక్ భాగాల నిర్మాణ లక్షణాలు మరియు లక్షణాలను అర్థం చేసుకోండి.
2.కస్టమర్కు అవసరమైన నమూనాల పరిమాణం గురించి స్పష్టంగా తెలుసుకోండి, తగినంత గింజలు, లోహ భాగాలు మరియు గట్టి ప్లాస్టిక్లను సిద్ధం చేయండి, ఎందుకంటే దీనికి అచ్చు పరీక్షలో చాలా నమూనాలు అవసరం.
3.గింజలు, లోహ భాగాలు లేదా గట్టి ప్లాస్టిక్ల ఇన్సర్ట్లు లేకుండా అచ్చును పరీక్షించవచ్చో లేదో గమనించండి. ఇన్సర్ట్ గింజలు, లోహ భాగాలు మరియు గట్టి ప్లాస్టిక్లు అచ్చులో అసెంబుల్ చేయకపోతే, భాగం అచ్చు లేదా షార్ట్ షాట్కు అంటుకోవడం వంటి లోపాలను కలిగి ఉండవచ్చు.
4.అనేక సందర్భాల్లో, వాటర్లైన్ ప్లేట్ను అచ్చుపై సర్దుబాటు చేయాల్సి ఉంటుంది, కానీ కొన్నిసార్లు అది వాటి నిర్మాణం ఆధారంగా కొన్ని ఇన్సర్ట్ అచ్చులో వాటర్లైన్ ప్లేట్ను సర్దుబాటు చేయదు, లేదా అధ్వాన్నంగా, అచ్చు భారీగా ఇరుక్కుపోయి, సవరించాల్సిన అవసరం ఉంది, లేదా అచ్చు దెబ్బతింటుంది. తెరవడం.
5.చిన్న షాట్లు, ఎయిర్ ట్రిప్లు, ఫ్లాష్లు లేదా అచ్చుకు అంటుకోవడం వంటి అచ్చు పరీక్షలో సమస్యలు సంభవించవచ్చు. ఇంజెక్షన్ మోల్డింగ్ మెషీన్లో సమస్యలను ధృవీకరించగలిగితే, దాన్ని పరిష్కరించడం మంచిది.
DJmolding 10+ సంవత్సరాల కంటే ఎక్కువ ఇన్సర్ట్ మోల్డింగ్ అనుభవాన్ని కలిగి ఉంది, మీకు ఏవైనా సందేహాలు ఉంటే, దయచేసి మమ్మల్ని సంప్రదించండి.