కస్టమ్ ప్లాస్టిక్ ఇంజెక్షన్ మౌల్డింగ్
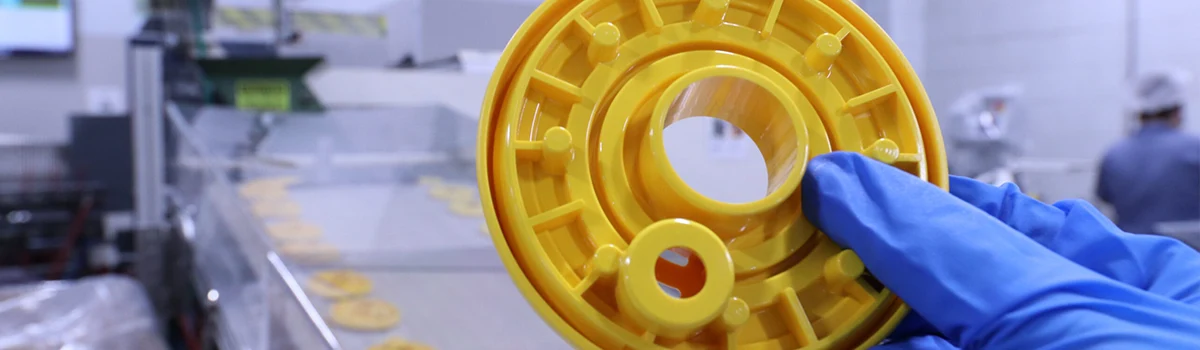
నిర్దిష్ట యాంత్రిక లేదా సౌందర్య లక్షణాలను సాధించడంపై విజయం ఆధారపడి ఉండే ప్లాస్టిక్ భాగాలకు అనుకూల ఇంజెక్షన్ మౌల్డింగ్ అనువైనది. DJmolding ప్లాస్టిక్ ఇంజెక్షన్ మోల్డింగ్ అనేది కస్టమర్లు ఉత్తమమైన ప్లాస్టిక్ భాగాలను ఉత్పత్తి చేయడంలో సహాయపడే ప్రాథమిక లక్ష్యంతో నడపబడుతుంది. సంక్లిష్టతకు కొత్తేమీ కాదు, డిజైన్ సవాళ్లు నిజంగా మీ కోసం ఆవిష్కరణ చేయాలనే మా కోరికను రేకెత్తిస్తాయి. ముందుగా మమ్మల్ని ఇన్వాల్వ్ చేయడం వల్ల డిజైన్ ప్రాసెస్లో విలువను జోడించవచ్చు.
ప్లాస్టిక్ ఇంజెక్షన్ మౌల్డింగ్ యొక్క ప్రయోజనాలు
వివరణాత్మక లక్షణాలు
మీ బ్రాండ్ను మెరుగుపరచడానికి సౌందర్య లేదా క్రియాత్మక వివరాలను పరిగణించండి: ముద్రించిన వచనం, కాస్మెటిక్ లేదా ఆకృతి ఉపరితలాలు, ఇన్-మోల్డ్ డెకరేటింగ్, స్నాప్ ఫిట్లు, ఫ్లెక్సిబుల్ హింగ్లు, విభిన్న కాఠిన్యం.
అధిక సమర్థత
ప్లాస్టిక్ ఇంజెక్షన్ మౌల్డింగ్ యొక్క సామర్థ్యం సరిపోలలేదు. మేము మీ భాగం మరియు సాధనం నుండి అనవసరమైన ఖర్చులను ఇంజినీర్ చేస్తాము. మా దీర్ఘకాల డిజైన్ ఇంజనీర్లు మరియు మాస్టర్ మోల్డర్లు ఇందులో నిజంగా రాణిస్తారు.
మెరుగైన పనితీరు
మెటీరియల్ సైన్స్, డిజైన్ సూత్రాలు, విశ్లేషణాత్మక సాధనాలు మరియు ప్రక్రియ నియంత్రణలను ఉపయోగించడం ద్వారా మీ భాగానికి ఉద్దేశించిన పనితీరును అర్థం చేసుకోవడానికి మరియు మీ ముఖ్య లక్ష్యాలను చేరుకోవడానికి మేము కృషి చేస్తాము.
మెటీరియల్ వెరైటీ
200 కంటే ఎక్కువ పదార్థాలు, వస్తువులు మరియు ఇంజనీరింగ్ రెసిన్ల నుండి ఎంచుకోండి. మేము మీకు పనితీరు మరియు ధరను సమతుల్యం చేయడంలో సహాయం చేస్తాము మరియు ఖర్చులను తగ్గించడానికి ప్రత్యామ్నాయ మెటీరియల్ సమానమైన వాటిని గుర్తించడంలో సహాయం చేస్తాము.
ఇంజెక్షన్ మౌల్డింగ్ ప్రక్రియ
ప్లాస్టిక్ ఇంజెక్షన్ మౌల్డింగ్ అనేది ప్లాస్టిక్లను తయారు చేసే పురాతన పద్ధతుల్లో ఒకటి మరియు ఉత్పత్తి తయారీదారుల కోసం భాగాల అభివృద్ధిలో కీలకమైన దశ. హెవీ మెటల్ భాగాలను ప్లాస్టిక్గా మార్చాలని చూస్తున్న తయారీదారులకు ఇది గొప్ప పరిష్కారం. దాని సరళమైన రూపంలో వివరించబడింది, ప్రక్రియ పాలిమర్లు లేదా ప్లాస్టిక్ రెసిన్లను ఉపయోగిస్తుంది, వీటిని వేడిచేసినప్పుడు, కరిగించి, కస్టమ్ అచ్చులోకి అధిక పీడనంతో ఇంజెక్ట్ చేసినప్పుడు, ఉత్పత్తి తయారీలో ఉపయోగించబడే ప్లాస్టిక్ భాగాలను ఉత్పత్తి చేస్తుంది.
ఆ ప్రక్రియ సూటిగా అనిపించినప్పటికీ, వాస్తవానికి ఇది చాలా క్లిష్టంగా ఉంటుంది మరియు మీ ప్రత్యేక పరిశ్రమ అవసరాలు, స్పెసిఫికేషన్లు, తుది ఉపయోగాలు మరియు సమయం/బడ్జెట్ పరిమితులను తీర్చగల ఇంజక్షన్ మోల్డర్ భాగస్వామి నుండి అధిక స్థాయి అనుభవం అవసరం. ప్లాస్టిక్ మౌల్డింగ్ ప్రక్రియ యొక్క ప్రాథమిక జ్ఞానాన్ని పొందడం మరియు ఉత్తమ అభ్యాసాలను రూపొందించడం ద్వారా ప్రారంభించడానికి ఉత్తమమైన ప్రదేశం.
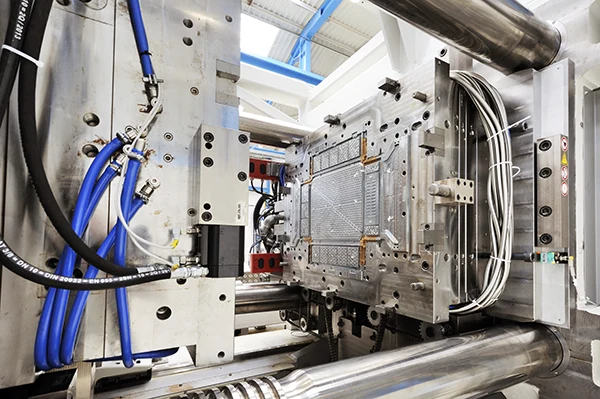
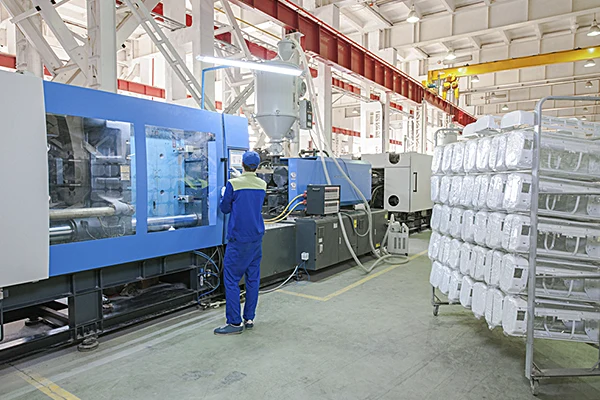
సైంటిఫిక్ మోల్డింగ్
నిర్దిష్ట పనితీరు మరియు అధిక ఖచ్చితత్వాన్ని డిమాండ్ చేసే క్లిష్టమైన భాగాల ఉత్పత్తికి శాస్త్రీయ అచ్చు విధానం ప్రయోజనం చేకూరుస్తుంది. మా అధునాతన అచ్చు సాంకేతికత పునరావృతం మరియు స్థిరత్వాన్ని నిర్ధారిస్తుంది. అంటే ఈరోజు మేము మీ కోసం తయారుచేసే ఉత్పత్తి, రేపు మీ కోసం తయారు చేసే ఉత్పత్తి.
టూలింగ్ డెవలప్మెంట్ సమయంలో సైంటిఫిక్ ఇంజెక్షన్ మౌల్డింగ్ ప్రారంభమవుతుంది. పీడనం, ఉష్ణోగ్రత, కుహరం పూరించే సమయం వంటి అంశాలు ఆప్టిమైజ్ చేయబడతాయి, తద్వారా అచ్చు రూపకల్పన వైవిధ్యానికి అవకాశాలను తగ్గిస్తుంది. అచ్చు ప్రవాహ విశ్లేషణ పూరించవలసిన భాగం యొక్క చివరి ప్రాంతాలను చూపుతుంది, పదార్థం అచ్చుతో ఎలా ఓరియంట్ అవుతుంది మరియు సంభావ్య వార్ప్ మరియు ఒత్తిడి పాయింట్లను బహిర్గతం చేస్తుంది. ఇది ఇంజినీరింగ్ ప్రిడిక్టివ్ అనాలిసిస్ మరియు మెజర్మెంట్ను అందించే చురుకైన దశ మరియు ఒక భాగం లేదా ప్రాజెక్ట్ యొక్క విజయం లేదా వైఫల్యాన్ని సులభంగా నిర్ణయించడానికి అనుమతిస్తుంది.
దృఢమైన ఉత్పత్తి ప్రక్రియలు స్క్రాప్ మరియు ప్రాసెసింగ్ సమయాన్ని తగ్గించే పర్యవేక్షణ మరియు స్వయంచాలక ప్రక్రియ నియంత్రణల ద్వారా శాస్త్రీయ విధానాన్ని మరింత ఉపయోగించుకుంటాయి. వైవిధ్యం లేదా పనిచేయకపోవడం సంభవించినట్లయితే, అది వేగంగా గుర్తించబడుతుంది మరియు అసంబద్ధమైన భాగాలను తయారు చేయడానికి ముందు వేరుచేయబడుతుంది.
ఓవర్మోల్డింగ్
రెండు (లేదా అంతకంటే ఎక్కువ) పదార్థాలను ఓవర్మోల్డింగ్తో ఒకే భాగానికి కలపవచ్చు. ఈ ప్రక్రియ తరచుగా మృదువైన గ్రిప్ ప్రాంతం వంటి ప్రత్యేకమైన స్పర్శ ఉపరితలం కోసం ఉపయోగించబడుతుంది. ఓవర్మోల్డింగ్ అనేది ప్లాస్టిక్ సబ్స్ట్రేట్పై ప్లాస్టిక్ లేదా ప్లాస్టిక్ సబ్స్ట్రేట్పై రబ్బరు కావచ్చు, సాధారణంగా రెండు-షాట్ ఇంజెక్షన్ మోల్డింగ్ ప్రక్రియ ద్వారా సాధించబడుతుంది. రెసిన్ సూత్రీకరణ మరియు రంగులు మారవచ్చు. ఓవర్మోల్డింగ్ యొక్క సౌందర్య ప్రయోజనాలు గమనించడం సులభం, కానీ అవి ద్వితీయ కార్యకలాపాలను కూడా తొలగిస్తాయి. ఓవర్మోల్డింగ్ అనేది హ్యాండ్గ్రిప్లు, హ్యాండ్హెల్డ్ ఆబ్జెక్ట్లు, రబ్బరు గ్రిప్లు అవసరమయ్యే రోబోటిక్లు లేదా విభిన్న రంగులతో ఒక భాగం యొక్క రూపాన్ని మెరుగుపరచడానికి సరైనది.
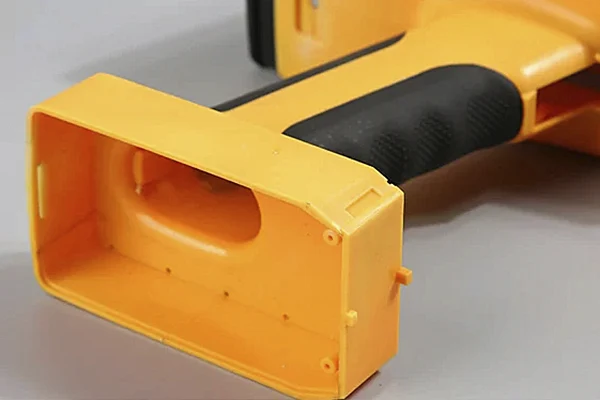
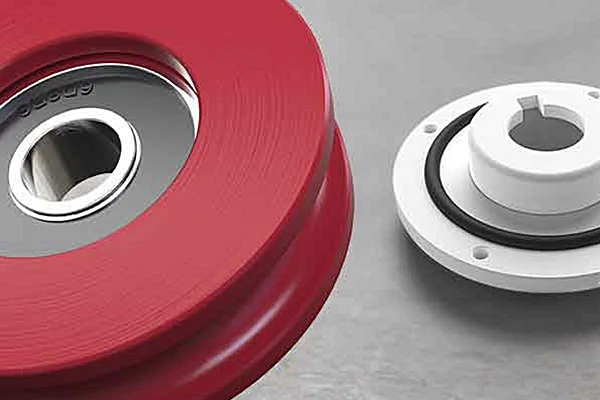
అచ్చును చొప్పించండి
ఇన్సర్ట్ మౌల్డింగ్ అనేది ఓవర్మోల్డింగ్ మాదిరిగానే ఉంటుంది కానీ అచ్చు కుహరంలో ఉంచబడిన వస్తువును కలిగి ఉంటుంది. సాధారణంగా మెటల్ లేదా ప్లాస్టిక్ ఇన్సర్ట్లకు అచ్చు బంధాలను ప్లాస్టిక్ని చొప్పించండి. థ్రెడ్ ఇన్సర్ట్లు సాధారణం. ఫాస్టెనర్లు, అడ్హెసివ్స్ లేదా హీట్-స్టాకింగ్లకు ప్రత్యామ్నాయంగా ఉపయోగించినప్పుడు ఇది శ్రమను తొలగిస్తుంది. ఇన్సర్ట్లు కూడా భాగాన్ని బలోపేతం చేస్తాయి. ఇన్సర్ట్లు మాన్యువల్గా లేదా రోబోటిక్ ఆటోమేషన్తో లోడ్ చేయబడతాయి.
పార్ట్ అలంకరణ మరియు లేబులింగ్
ఇన్-మోల్డ్ డెకరేషన్ (IMD) మరియు ఇన్-మోల్డ్ లేబులింగ్ (IML) గ్రాఫిక్స్ లేదా లేబుల్లతో దృశ్యపరంగా విశేషమైన రూపాన్ని సృష్టించడానికి ఉపయోగించబడతాయి. రోబోటిక్స్ మరియు ఎలెక్ట్రోస్టాటిక్ లేదా వాక్యూమ్ గ్రిప్ ద్వారా సులభతరం చేయబడిన, కరిగిన ప్లాస్టిక్ రెసిన్ను ఇంజెక్షన్ చేయడానికి ముందు అచ్చు కుహరానికి ప్రింటెడ్ ఫిల్మ్ ఓవర్లే జోడించబడుతుంది. ఈ ప్రక్రియ లేబుల్ మరియు పూర్తయిన భాగానికి మధ్య శాశ్వత బంధాన్ని ఏర్పరుస్తుంది, సాధారణంగా పోస్ట్-ప్రాసెసింగ్ కార్యకలాపాల కోసం ఏదైనా అవసరాన్ని తొలగిస్తుంది. విస్తృత శ్రేణి ఆకృతి, రంగు మరియు ఉపరితల పూత ఎంపికలు సృజనాత్మక అవకాశాల కోసం తలుపులు తెరిచి ఉంచుతాయి. మీ బ్రాండ్ను మెరుగుపరచడానికి ఎంపికల గురించి మీ ప్రాజెక్ట్ మేనేజర్తో మాట్లాడమని మేము మిమ్మల్ని ప్రోత్సహిస్తున్నాము.
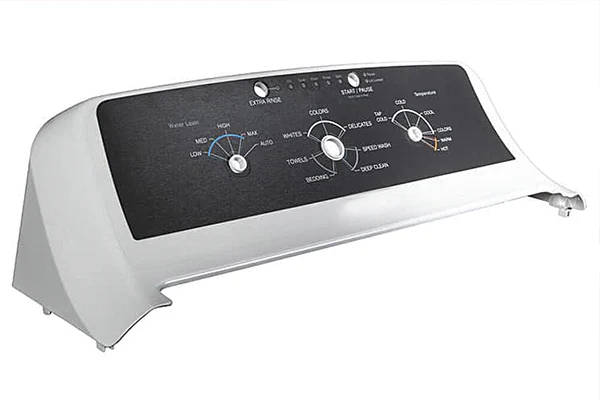
కస్టమ్ ప్లాస్టిక్ ఇంజెక్షన్ మోల్డింగ్ సర్వీస్ చైనా
DJmolding 2010 నుండి ఆపరేటింగ్ | AFAQ ISO/TS 16949, UL మరియు ISO ధృవపత్రాలు, ప్రస్తుతం ప్రపంచంలోని అనేక 3D ప్రింటింగ్ కంపెనీలకు సరఫరా చేస్తున్నాయి.
Djmolding వద్ద మేము అధిక-నాణ్యత ప్లాస్టిక్ ఇంజెక్షన్ అచ్చు భాగాలు మరియు అచ్చు సాధనాలను ఉత్పత్తి చేయడంలో ప్రత్యేకత కలిగి ఉన్నాము. మేము ప్రధానంగా ప్రపంచంలోని అనేక 3D ప్రింట్ కంపెనీలకు మా ప్లాస్టిక్ ఇంజెక్షన్ తయారీని సరఫరా చేస్తాము. మా వద్ద రోబోటిక్స్ మరియు ఆటోమేటిక్ ప్లాస్టిక్ ఇంజెక్షన్ తయారీ కోసం 55 మెషీన్లు ఉన్నాయి. మేము వివిధ రకాల మెటీరియల్ల నుండి టూల్స్ చేయడానికి అన్ని మ్యాచింగ్ మరియు ఫినిషింగ్ సేవలను అందిస్తాము మరియు అన్ని ప్రధాన ప్లాస్టిక్లలో 100 నుండి 200k+ పూర్తి చేసిన భాగాలను ఉత్పత్తి చేయగలము. మా అధునాతన మెటీరియల్ వెరిఫికేషన్, తనిఖీ మరియు మీ భాగాలు మీ అత్యధిక అంచనాలను అందుకోవడానికి మరియు మించి ఉండేలా చూసుకోవడానికి నిజంగా మమ్మల్ని వేరుగా ఉంచుతుంది. ఈ రోజు ఉచిత కోట్ కోసం మా అంతర్జాతీయ ఇంజెక్షన్ మోల్డింగ్ నిపుణులను సంప్రదించండి.
DJmolding ప్లాస్టిక్ ఇంజెక్షన్ మౌల్డింగ్ ప్రక్రియ
మీ ప్లాస్టిక్ ఇంజెక్షన్ అచ్చు సాధనాలు సిద్ధమైన తర్వాత, అచ్చు ప్రక్రియ క్రింది ప్రాథమిక దశలను కలిగి ఉంటుంది:
దశ 1. ప్లాస్టిక్ రెసిన్ ముడి గుళికలలో వస్తుంది. వీటిని సరైన తేమతో ఎండబెట్టి, అవసరమైతే వాటిని వర్ణద్రవ్యం లేదా మాస్టర్ బ్యాచ్ రంగులతో కలపవచ్చు.
దశ 2. ఎండిన గుళికలు అచ్చు యంత్రం యొక్క తొట్టిలో పోస్తారు. యంత్రం యొక్క బారెల్ లోపల ఒక రెసిప్రొకేటింగ్ స్క్రూ ఈ గుళికలను అచ్చు వైపుకు రవాణా చేస్తుంది.
దశ 3. బారెల్ లోపల, గుళికలు పూర్తిగా కరిగిపోయే వరకు మిశ్రమంగా మరియు వేడి చేయబడి, ద్రవ రెసిన్ను ఏర్పరుస్తాయి.
దశ 4. వేడిచేసిన అచ్చు స్వయంచాలకంగా మూసివేయబడుతుంది మరియు రెసిన్, గొప్ప ఒత్తిడిలో, ఒక గేట్ ద్వారా మరియు అచ్చు కుహరంలోకి ఇంజెక్ట్ చేయబడుతుంది.
దశ 5. లోపల భాగాన్ని పటిష్టం చేయడానికి అచ్చు చల్లబడుతుంది.
దశ 6. అచ్చు తెరుచుకుంటుంది మరియు కొత్త చక్రాన్ని ప్రారంభించడానికి భాగం బయటకు తీయబడుతుంది.
ప్లాస్టిక్ ఇంజెక్షన్ మోల్డింగ్ టాలరెన్స్
అన్ని ప్లాస్టిక్ పదార్థాలు వేడి మరియు తేమ ప్రభావంతో విస్తరిస్తాయి మరియు కుదించబడతాయి. మా టాలరెన్స్ గైడ్ విలక్షణమైన పార్ట్ ఫీచర్ల కోసం అత్యంత సాధారణ రెసిన్ రకాల లక్షణాలపై మరింత సాధారణ సమాచారాన్ని అందిస్తుంది.
తయారీ కోసం మీ డిజైన్లను ఆప్టిమైజ్ చేయడానికి మేము మీతో కలిసి పని చేస్తాము. పేలవమైన డిజైన్ థర్మల్ స్ట్రెస్, సంకోచం, వార్పింగ్ మొదలైనవాటిని కలిగించే ఏవైనా ప్రాంతాలను మేము సూచిస్తాము. సాధారణ లోపాలు మరియు వాటిని ఎలా నివారించాలో మరింత సమాచారం కోసం మా డిజైన్ గైడ్ని సంప్రదించండి.
పేర్కొనకపోతే, ప్లాస్టిక్ ఇంజెక్షన్ మోల్డింగ్ల కోసం మేము DIN 16742 స్టాండర్డ్ టాలరెన్స్లకు కట్టుబడి ఉంటాము. మేము ఇంజెక్షన్ అచ్చు భాగాలకు వర్తించే దృశ్య నాణ్యత ప్రమాణాల గురించి చదవండి.
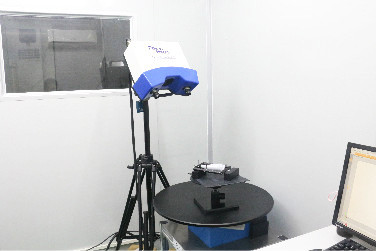
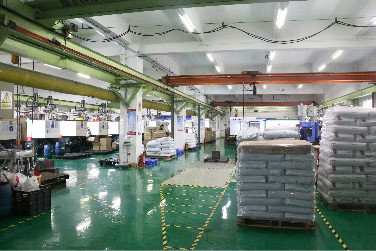
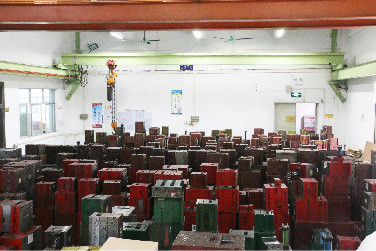
ప్లాస్టిక్ ఇంజెక్షన్ మౌల్డింగ్ మెటీరియల్స్
Djmolding ఇంజక్షన్ మోల్డింగ్ సాధనాలను తయారు చేస్తుంది మరియు అల్యూమినియం 7075, P20 మరియు NAK80 సెమీ-హార్డెన్డ్ స్టీల్స్ మరియు H13 పూర్తిగా గట్టిపడిన స్టీల్తో చనిపోతుంది. అదనంగా, మేము ప్రామాణిక SPI ముగింపులు, EDM టెక్స్చరింగ్ మరియు ఎచెడ్ టెక్చర్ల శ్రేణిని అందిస్తాము.
ఈ మెటీరియల్ రకాల్లో ప్రతి ఒక్కటి నిర్దిష్ట అనువర్తనాలకు ప్రత్యేక ప్రయోజనాలను కలిగి ఉంటాయి. *పరిగణనలు ఉన్నాయి:
* ముడిసరుకు ధర
* మన్నిక మరియు తుప్పు లేదా రాపిడికి నిరోధకత
*యంత్ర సామర్థ్యం
* అధిక ఉపరితల పాలిష్ తీసుకునే సామర్థ్యం
* వేడి చికిత్స కోసం సమయం అవసరం
* ఆశించిన సాధనం జీవితం
మీకు ఏది సరైనది అనే దాని గురించి మరింత తెలుసుకోవడానికి మా సాంకేతిక నిపుణులను సంప్రదించండి.
ప్లాస్టిక్ ఇంజెక్ట్ భాగాలు
మీ ప్రాజెక్ట్ కోసం ఎంచుకోవడానికి వేలాది థర్మోఫార్మింగ్ మరియు థర్మోసెట్టింగ్ ప్లాస్టిక్లు ఉన్నాయి. అదనంగా, గ్లాస్ ఫైబర్స్, UV స్టెబిలైజర్లు మరియు కందెనలు వంటి సంకలితాలతో మెకానికల్ మరియు రసాయన లక్షణాలను కూడా మెరుగుపరచవచ్చు. మా మెటీరియల్స్ షీట్ మీకు ప్రామాణిక రకాలు మరియు ప్రతిదానితో ఆశించే సహనాల గురించి మరింత వివరణాత్మక సమాచారాన్ని అందిస్తుంది.
మీ రెసిన్ల ఎంపిక క్రింది పరిశీలనలలో ఒకటి లేదా అంతకంటే ఎక్కువ ఆధారపడి ఉండవచ్చు:
*UV, రసాయన, రాపిడి మరియు ప్రభావ నిరోధకత
* ముడిసరుకు ధర
* యాంత్రిక బలం
* బరువు మరియు సాంద్రత
*వశ్యత
* పారదర్శకత
*పునర్వినియోగం
మెటీరియల్ లక్షణాల గురించి మరింత తెలుసుకోవడానికి మా సాంకేతిక నిపుణులలో ఒకరిని సంప్రదించండి.
DJmolding ఇంజక్షన్ షాప్:
ప్రముఖ ప్లాస్టిక్ ఇంజెక్షన్ అచ్చు మరియు వేగవంతమైన ప్రోటోటైపింగ్ సర్వీస్ తయారీదారు
Djmolding అనేది చైనాలో బాగా తెలిసిన ప్లాస్టిక్ ఇంజెక్షన్ మోల్డింగ్ కంపెనీలలో ఒకటి. మా ఇంజెక్షన్ మౌల్డింగ్ షాప్లో 50 టన్నుల నుండి 30 టన్నుల వరకు 800 సెట్ల హై ప్రెసిషన్ ఇంజెక్షన్ మోల్డింగ్ మెషీన్లు ఉన్నాయి, అవి ఎక్కువగా తైవాన్ మరియు జపాన్ నుండి దిగుమతి చేయబడతాయి, మా ఇంజెక్షన్ షాప్ రోజుకు 24 గంటలు, వారానికి 7 రోజులు నడుస్తుంది మరియు ఉత్పత్తిని అందిస్తుంది సేవలు.
ఆటోమోటివ్, మెడికల్, లైటింగ్, స్పోర్ట్స్ పరికరాలు, గృహోపకరణాలు మరియు వ్యవసాయంతో సహా అనేక పారిశ్రామిక రంగాలకు సంబంధించిన వివిధ ప్లాస్టిక్ ఉత్పత్తులతో మాకు అనుభవం ఉంది. Djmolding 16949 నుండి AFAQ ISO/TS 9001, UL మరియు ISO 2010 సర్టిఫికేషన్లను కలిగి ఉంది, మా ఉత్పత్తిని నిరంతరం చూస్తూ పార్ట్ క్వాలిటీని తనిఖీ చేసే 15 మంది IPQC వ్యక్తులు కూడా ఉన్నారు, ఇది మా ఉత్పత్తి అత్యున్నత స్థాయి నాణ్యతను నిర్వహిస్తుందని నిర్ధారిస్తుంది. గత 9 సంవత్సరాలలో, Djmolding అధిక నాణ్యత సాధనం మరియు భాగాన్ని సమంజసమైన ధరతో ఉత్పత్తి చేయడంలో బలమైన కీర్తిని నెలకొల్పింది. మేము appxతో బలమైన వ్యాపార సంబంధాలను కొనసాగిస్తున్నాము. 50 మంది కస్టమర్లు, ప్రధానంగా USA మరియు యూరప్ నుండి.
కస్టమ్ ప్లాస్టిక్ ఇంజెక్షన్ మౌల్డింగ్
కస్టమ్ ప్లాస్టిక్ ఇంజెక్షన్ మోల్డింగ్ అనేది అధిక-నాణ్యత ప్లాస్టిక్ భాగాలను ఉత్పత్తి చేయడానికి ఒక వినూత్నమైన మరియు సమర్థవంతమైన మార్గం. ఈ తయారీ ప్రక్రియ ప్లాస్టిక్ పదార్థాలను సంక్లిష్టమైన ఆకారాలు మరియు పరిమాణాలలో ఆకృతి చేయడానికి ఒక అచ్చును ఉపయోగిస్తుంది, ఇది వివిధ పరిశ్రమలకు ఆదర్శవంతమైన పరిష్కారం. ఈ బ్లాగ్ పోస్ట్ కస్టమ్ ప్లాస్టిక్ ఇంజెక్షన్ మౌల్డింగ్లో లోతుగా డైవ్ చేస్తుంది మరియు దాని ప్రయోజనాలు, అప్లికేషన్లు మరియు ఉత్తమ పద్ధతులను అన్వేషిస్తుంది.
అనుకూల ఇంజెక్షన్ మౌల్డింగ్ ప్రక్రియను అర్థం చేసుకోవడం
కస్టమ్ ఇంజెక్షన్ మౌల్డింగ్ అనేది పెద్ద పరిమాణంలో ప్లాస్టిక్ భాగాలను ఉత్పత్తి చేయడానికి ఉపయోగించే తయారీ ప్రక్రియ. ఇది ప్లాస్టిక్ గుళికలు లేదా కణికలను కరిగించి, అధిక పీడనం కింద వాటిని ఒక అచ్చులోకి ఇంజెక్ట్ చేయడం, అక్కడ అవి చల్లబడి, కావలసిన ఆకృతిని ఏర్పరుస్తాయి. ఇంజెక్షన్ మోల్డింగ్ ప్రక్రియ ఎలా పనిచేస్తుందో ఇక్కడ ఉంది:
- బిగింపు: "సాధనం" అని పిలువబడే అచ్చు యొక్క రెండు భాగాలు ఇంజెక్షన్ ఒత్తిడిని తట్టుకునేంత శక్తితో బిగించబడతాయి.
- ఇంజెక్షన్: ప్లాస్టిక్ గుళికలను వేడిచేసిన బారెల్లో కరిగించి, అధిక పీడనం కింద రన్నర్ సిస్టమ్ ద్వారా అచ్చులోకి ఇంజెక్ట్ చేస్తారు. ప్లాస్టిక్ అచ్చు కుహరాన్ని నింపుతుంది మరియు అచ్చు ఆకారాన్ని తీసుకుంటుంది.
- శీతలీకరణ: కావలసిన ఆకారాన్ని నిర్వహించడానికి ప్లాస్టిక్ అచ్చు లోపల చల్లబరుస్తుంది మరియు ఘనీభవిస్తుంది.
- ఎజెక్షన్: ప్లాస్టిక్ చల్లబడిన తర్వాత అచ్చు తెరుచుకుంటుంది మరియు పూర్తయిన భాగాన్ని బయటకు తీస్తుంది.
- పునరావృతం: అనేక సారూప్య భాగాలను సృష్టించడానికి ప్రక్రియ పునరావృతమవుతుంది.
ఇంజెక్షన్ మౌల్డింగ్ ప్లాస్టిక్ ఉత్పత్తులను ఉత్పత్తి చేస్తుంది, చిన్న భాగాల నుండి ఆటోమోటివ్ భాగాలు మరియు గృహోపకరణాల వంటి పెద్ద వస్తువుల వరకు. ప్రక్రియ అత్యంత ప్రభావవంతంగా ఉంటుంది మరియు సంక్లిష్ట జ్యామితులు మరియు గట్టి సహనంతో భాగాలను ఉత్పత్తి చేయగలదు మరియు ఇది కనిష్ట వ్యర్థాలు మరియు తక్కువ స్క్రాప్ రేట్లతో కూడా ఖచ్చితమైనది.
ఈ ప్రక్రియకు ఖచ్చితమైన మరియు స్థిరమైన ఫలితాలను నిర్ధారించడానికి అచ్చు, ఇంజెక్షన్ మోల్డింగ్ మెషిన్ మరియు నియంత్రణ వ్యవస్థతో సహా ప్రత్యేక పరికరాలు అవసరం. అచ్చు సాధారణంగా ఉక్కుతో తయారు చేయబడుతుంది మరియు బహుళ-కుహరం అచ్చును ఉపయోగించి బహుళ భాగాలను ఉత్పత్తి చేయడానికి రూపొందించబడుతుంది.
ఇంజెక్షన్ మౌల్డింగ్ను థర్మోప్లాస్టిక్లు, థర్మోసెట్లు మరియు ఎలాస్టోమర్లతో సహా వివిధ పదార్థాలతో కూడా ఉపయోగించవచ్చు. ప్రతి పదార్థం ప్రత్యేక లక్షణాలను కలిగి ఉంటుంది మరియు నిర్దిష్ట అనువర్తనాలకు అనుగుణంగా ఉంటుంది.
మొత్తంమీద, ఇంజెక్షన్ మౌల్డింగ్ అనేది అనేక పరిశ్రమలలో విస్తృతంగా ఉపయోగించే అత్యంత బహుముఖ మరియు సమర్థవంతమైన తయారీ ప్రక్రియ.
కస్టమ్ ప్లాస్టిక్ ఇంజెక్షన్ మౌల్డింగ్ యొక్క ప్రయోజనాలు
కస్టమ్ ప్లాస్టిక్ ఇంజెక్షన్ మౌల్డింగ్ అనేది పెద్ద వాల్యూమ్లలో కస్టమ్ ప్లాస్టిక్ భాగాలను రూపొందించడానికి ఉపయోగించే తయారీ ప్రక్రియ. ఈ ప్రక్రియ యొక్క కొన్ని ప్రయోజనాలు ఇక్కడ ఉన్నాయి:
అధిక సామర్థ్యం మరియు ఉత్పాదకత: కస్టమ్ ప్లాస్టిక్ ఇంజెక్షన్ మౌల్డింగ్ అనేది అత్యంత సమర్థవంతమైన ప్రక్రియ, ఇది పెద్ద పరిమాణంలో ఒకేలాంటి భాగాలను త్వరగా మరియు స్థిరంగా ఉత్పత్తి చేయగలదు. ఇది ప్లాస్టిక్ భాగాల భారీ ఉత్పత్తికి ఆదర్శవంతమైన ఎంపికగా చేస్తుంది.
పాండిత్యము: థర్మోప్లాస్టిక్లు, థర్మోసెట్లు మరియు ఎలాస్టోమర్లతో సహా అనేక రకాల ప్లాస్టిక్ పదార్థాలతో ఈ ప్రక్రియను ఉపయోగించవచ్చు. ఇది అనేక రకాలైన పార్ట్ డిజైన్లు మరియు అప్లికేషన్లను అనుమతిస్తుంది.
స్థిరత్వం మరియు ఖచ్చితత్వం: ఇంజెక్షన్ మౌల్డింగ్ గట్టి సహనం మరియు భాగాల మధ్య కనిష్ట వైవిధ్యంతో స్థిరమైన మరియు ఖచ్చితమైన ఫలితాలను అందిస్తుంది. ఇది ప్రతి భాగం తదుపరి దానితో సమానంగా ఉండేలా చేస్తుంది, ఇది అనేక అనువర్తనాలకు అవసరం.
ఖర్చుతో కూడుకున్నది: అధిక-వాల్యూమ్ ఉత్పత్తి పరుగుల కోసం అనుకూల ప్లాస్టిక్ ఇంజెక్షన్ మౌల్డింగ్ ఖర్చుతో కూడుకున్నది. ప్రారంభ సాధన ఖర్చులు ఎక్కువగా ఉండవచ్చు, అయితే వాల్యూమ్ పెరిగేకొద్దీ ఒక్కో భాగానికి ధర తగ్గుతుంది.
సంక్లిష్టత: ఇంజెక్షన్ మౌల్డింగ్ సన్నని గోడలు మరియు క్లిష్టమైన లక్షణాలతో సహా సంక్లిష్ట ఆకారాలు మరియు జ్యామితితో భాగాలను ఉత్పత్తి చేస్తుంది. ఇది ఎక్కువ డిజైన్ సౌలభ్యాన్ని అనుమతిస్తుంది మరియు ఇతర పద్ధతులను ఉపయోగించి ఉత్పత్తి చేయడం కష్టతరమైన లేదా అసాధ్యమైన కారకాల ఉత్పత్తిని అనుమతిస్తుంది.
కనిష్ట వ్యర్థాలు: ఇంజెక్షన్ మౌల్డింగ్ ఇతర తయారీ ప్రక్రియలతో పోలిస్తే తక్కువ వ్యర్థాలను ఉత్పత్తి చేస్తుంది, ఎందుకంటే ఏదైనా అదనపు ప్లాస్టిక్ను రీసైకిల్ చేయవచ్చు మరియు తిరిగి ఉపయోగించుకోవచ్చు.
ఉపరితల ముగింపు: ఇంజెక్షన్ మోల్డింగ్ అదనపు పోస్ట్-ప్రాసెసింగ్ లేదా ఫినిషింగ్ ఆపరేషన్లు లేకుండా అధిక-నాణ్యత ఉపరితల ముగింపుతో భాగాలను ఉత్పత్తి చేస్తుంది. ఇది మృదువైన మరియు మెరుగుపెట్టిన రూపాన్ని కలిగి ఉన్న ముక్కలను సృష్టించడానికి ఇది ఖర్చుతో కూడుకున్న పరిష్కారంగా చేస్తుంది.
ఆటోమేషన్: రోబోట్లు అచ్చు నుండి భాగాలను లోడ్ చేయడం మరియు అన్లోడ్ చేయడం మరియు లక్షణాలను తనిఖీ చేయడం మరియు క్రమబద్ధీకరించడం ద్వారా ఇంజెక్షన్ మౌల్డింగ్ను సులభంగా ఆటోమేట్ చేయవచ్చు. ఇది మాన్యువల్ లేబర్ అవసరాన్ని తగ్గిస్తుంది మరియు సామర్థ్యాన్ని పెంచుతుంది.
కస్టమ్ ప్లాస్టిక్ ఇంజెక్షన్ మౌల్డింగ్ అనేది ఇతర పద్ధతుల కంటే అనేక ప్రయోజనాలను అందించే అత్యంత బహుముఖ మరియు సమర్థవంతమైన తయారీ ప్రక్రియ. పెద్ద మొత్తంలో ఒకేలాంటి భాగాలను త్వరగా మరియు కచ్చితంగా ఉత్పత్తి చేయగల సామర్థ్యం ఆటోమోటివ్, ఏరోస్పేస్, మెడికల్ మరియు వినియోగ వస్తువులతో సహా అనేక పరిశ్రమలకు ఆదర్శంగా నిలిచింది.
ఇంజెక్షన్ మౌల్డింగ్ యొక్క అప్లికేషన్లు
ఇంజెక్షన్ మౌల్డింగ్ అనేది వివిధ పారిశ్రామిక ప్లాస్టిక్ ఉత్పత్తులను రూపొందించడానికి విస్తృతంగా ఉపయోగించే తయారీ ప్రక్రియ. ఇంజెక్షన్ మోల్డింగ్ యొక్క అత్యంత సాధారణ అనువర్తనాల్లో కొన్ని ఇక్కడ ఉన్నాయి:
- ఆటోమోటివ్ పరిశ్రమ: ఇంజెక్షన్ మోల్డింగ్ వివిధ ఆటోమోటివ్ భాగాలను ఉత్పత్తి చేస్తుంది, వీటిలో ఇంటీరియర్ మరియు ఎక్స్టీరియర్ ట్రిమ్, డాష్బోర్డ్ భాగాలు, డోర్ హ్యాండిల్స్ మరియు ఇంజిన్ పార్ట్లు ఉన్నాయి. ఇది అధిక బలం మరియు డైమెన్షనల్ ఖచ్చితత్వంతో లక్షణాలను కలిగి ఉంటుంది కాబట్టి ఇది ప్రాధాన్యతనిస్తుంది.
- వినియోగదారు వస్తువులు: ఇంజెక్షన్ మౌల్డింగ్ బొమ్మలు, గృహోపకరణాలు మరియు ఎలక్ట్రానిక్ పరికరాలతో సహా వివిధ వినియోగదారు ఉత్పత్తులను సృష్టిస్తుంది. ఇది సంక్లిష్టమైన ఆకారాలు మరియు జ్యామితులు మరియు అధిక-నాణ్యత ఉపరితల ముగింపులను ఉత్పత్తి చేయడానికి అనుమతిస్తుంది.
- వైద్య పరికరాలు: సిరంజిలు, IV భాగాలు మరియు రోగనిర్ధారణ పరికరాలతో సహా వివిధ రకాల వైద్య పరికరాలను ఉత్పత్తి చేయడానికి ఇంజెక్షన్ మౌల్డింగ్ ఉపయోగించబడుతుంది. ఇది అధిక ఖచ్చితత్వం, శుభ్రమైన తయారీ మరియు సంక్లిష్ట జ్యామితితో భాగాలను ఉత్పత్తి చేయగల సామర్థ్యాన్ని అందిస్తుంది, ఇవి వైద్య పరిశ్రమలో అవసరం.
- ప్యాకేజింగ్ పరిశ్రమ: ఇంజెక్షన్ మౌల్డింగ్ అనేది సీసాలు, పాత్రలు మరియు మూతలతో సహా ప్యాకేజింగ్ పదార్థాలను ఉత్పత్తి చేస్తుంది. ఇది తేలికైన మరియు మన్నికైన కంటైనర్లను సృష్టించడానికి మరియు రంగులు, అల్లికలు మరియు ఆకారాలను అనుకూలీకరించడానికి అనుమతిస్తుంది.
- ఏరోస్పేస్ పరిశ్రమ: నిర్మాణ అంశాలు మరియు అంతర్గత అమరికలతో సహా ఏరోస్పేస్ భాగాల యొక్క వివిధ భాగాలను ఉత్పత్తి చేయడానికి ఇంజెక్షన్ మౌల్డింగ్ ఉపయోగించబడుతుంది. ఇది తీవ్రమైన ఉష్ణోగ్రతలు మరియు ఒత్తిళ్లను తట్టుకోగల అధిక-పనితీరు గల పదార్థాలను రూపొందించడానికి అనుమతిస్తుంది.
- నిర్మాణ పరిశ్రమ: ఇంజెక్షన్ మౌల్డింగ్ PVC పైపులు, గట్టర్ సిస్టమ్లు మరియు రూఫింగ్ పదార్థాలతో సహా వివిధ నిర్మాణ సామగ్రిని ఉత్పత్తి చేస్తుంది. ఇది అధిక మన్నిక, వాతావరణం మరియు రసాయనాలకు నిరోధకత మరియు పెద్ద పరిమాణంలో భాగాలను ఉత్పత్తి చేసే సామర్థ్యాన్ని అందిస్తుంది.
- ఎలక్ట్రానిక్స్ పరిశ్రమ: ఇంజెక్షన్ మౌల్డింగ్ హౌసింగ్, కనెక్టర్లు మరియు స్విచ్లతో సహా వివిధ ఎలక్ట్రానిక్ భాగాలను ఉత్పత్తి చేస్తుంది. ఇది అధిక ఖచ్చితత్వం, ఏకరూపత మరియు సంక్లిష్ట జ్యామితితో భాగాలను ఉత్పత్తి చేయగల సామర్థ్యాన్ని అందిస్తుంది, ఇది ఎలక్ట్రానిక్స్ పరిశ్రమలో అవసరం.
మొత్తంమీద, ఇంజెక్షన్ మౌల్డింగ్ అనేది అనేక పరిశ్రమలకు అనేక ప్లాస్టిక్ భాగాలను ఉత్పత్తి చేయగల బహుముఖ తయారీ ప్రక్రియ. సంక్లిష్ట జ్యామితి, అధిక ఖచ్చితత్వం మరియు స్థిరమైన నాణ్యతతో భాగాలను ఉత్పత్తి చేయగల దాని సామర్థ్యం చాలా మంది తయారీదారులకు ఇది ఒక ప్రసిద్ధ ఎంపిక.
ఇంజెక్షన్ మౌల్డింగ్లో ఉపయోగించే పదార్థాల రకాలు
ఇంజెక్షన్ మౌల్డింగ్ అనేది ఒక నిర్దిష్ట ఆకారాన్ని సృష్టించడానికి ఒక అచ్చు కుహరంలోకి కరిగిన ప్లాస్టిక్ను ఇంజెక్ట్ చేయడంతో కూడిన తయారీ ప్రక్రియ. తుది ఉత్పత్తి యొక్క కావలసిన లక్షణాలపై ఆధారపడి, ఇంజెక్షన్ మౌల్డింగ్లో వివిధ పదార్థాలను ఉపయోగించవచ్చు. ఇంజెక్షన్ మోల్డింగ్లో ఉపయోగించే కొన్ని సాధారణ రకాల పదార్థాలు ఇక్కడ ఉన్నాయి:
- థర్మోప్లాస్టిక్స్: ఇంజెక్షన్ మౌల్డింగ్లో ఇవి సాధారణంగా ఉపయోగించే పదార్థాలు. అవి ఒక రకమైన ప్లాస్టిక్, ఇవి వేడిచేసినప్పుడు మృదువుగా మరియు మలచబడతాయి మరియు చల్లబడినప్పుడు గట్టిపడతాయి. థర్మోప్లాస్టిక్లను వాటి లక్షణాలను కోల్పోకుండా అనేకసార్లు అచ్చు మరియు రీమోల్డ్ చేయవచ్చు. ఇంజెక్షన్ మౌల్డింగ్లో ఉపయోగించే సాధారణ థర్మోప్లాస్టిక్లలో పాలీప్రొఫైలిన్, పాలిథిలిన్, పాలీస్టైరిన్ మరియు నైలాన్ ఉన్నాయి.
- థర్మోసెట్లు: ఇవి ఒక్కసారి మాత్రమే అచ్చు వేయగల ప్లాస్టిక్లు. అవి వేడి చేయబడి, నిర్దిష్ట ఆకృతిలో అభివృద్ధి చెందుతాయి మరియు అవి గట్టిపడిన తర్వాత, వాటిని పునర్నిర్మించలేము. అధిక బలం మరియు మన్నిక అవసరమయ్యే అనువర్తనాల కోసం థర్మోసెట్లు ఉపయోగించబడతాయి. ఇంజెక్షన్ మౌల్డింగ్లో ఉపయోగించే సాధారణ థర్మోసెట్లలో ఎపోక్సీ, మెలమైన్ మరియు ఫినోలిక్ రెసిన్లు ఉన్నాయి.
- ఎలాస్టోమర్లు: ఈ పదార్థాలు సాగే లక్షణాలను కలిగి ఉంటాయి మరియు వాటి అసలు ఆకృతిని సాగదీయవచ్చు మరియు తిరిగి పొందవచ్చు. వశ్యత మరియు షాక్ శోషణ అవసరమయ్యే అనువర్తనాల కోసం ఎలాస్టోమర్లు ఉపయోగించబడతాయి. ఇంజెక్షన్ మౌల్డింగ్లో ఉపయోగించే ప్రామాణిక ఎలాస్టోమర్లలో రబ్బరు, సిలికాన్ మరియు పాలియురేతేన్ ఉన్నాయి.
- బయోడిగ్రేడబుల్ పదార్థాలు: ఇవి హానికరమైన అవశేషాలను వదిలివేయకుండా పర్యావరణంలో సహజంగా విచ్ఛిన్నమవుతాయి. పర్యావరణ స్థిరత్వం ఆందోళన కలిగించే అనువర్తనాల కోసం అవి ఉపయోగించబడతాయి. ఇంజెక్షన్ మౌల్డింగ్లో ఉపయోగించే సాధారణ బయోడిగ్రేడబుల్ మెటీరియల్స్లో పాలిలాక్టిక్ యాసిడ్ (PLA) మరియు పాలీహైడ్రాక్సీల్కనోయేట్స్ (PHAలు) ఉన్నాయి.
- నిర్దిష్ట లక్షణాలతో కొత్త పదార్థాన్ని సృష్టించడానికి రెండు లేదా అంతకంటే ఎక్కువ విభిన్న పదార్థాలను కలపడం ద్వారా తయారు చేయబడిన పదార్థాలు మిశ్రమాలు. అధిక బలం మరియు దృఢత్వం అవసరమయ్యే అనువర్తనాల కోసం మిశ్రమాలు ఉపయోగించబడతాయి. ఇంజెక్షన్ మోల్డింగ్లో ఉపయోగించే ప్రామాణిక మిశ్రమాలలో గ్లాస్ ఫైబర్-రీన్ఫోర్స్డ్ ప్లాస్టిక్లు (GRP) మరియు కార్బన్ ఫైబర్-రీన్ఫోర్స్డ్ ప్లాస్టిక్లు (CFRP) ఉన్నాయి.
- మెటల్-నిండిన ప్లాస్టిక్లు అధిక విద్యుత్ మరియు ఉష్ణ వాహకత మరియు ఇతర నిర్దిష్ట లక్షణాలతో పదార్థాలను రూపొందించడానికి లోహ కణాలతో నింపబడిన ప్లాస్టిక్లు. అవసరమైన విద్యుత్ లేదా ఉష్ణ వాహకత కలిగిన అనువర్తనాల కోసం మెటల్-నిండిన ప్లాస్టిక్లను ఉపయోగిస్తారు. ఇంజెక్షన్ మౌల్డింగ్లో ఉపయోగించే సాధారణ మెటల్-నిండిన ప్లాస్టిక్లలో రాగితో నిండిన ప్లాస్టిక్లు మరియు నికెల్-నిండిన ప్లాస్టిక్లు ఉన్నాయి.
మొత్తంమీద, ఇంజెక్షన్ మౌల్డింగ్ మెటీరియల్ ఎంపిక బలం, వశ్యత, వాహకత మరియు మన్నికతో సహా తుది ఉత్పత్తి యొక్క నిర్దిష్ట అవసరాలపై ఆధారపడి ఉంటుంది. తయారీదారులు తరచుగా ఖర్చు, లభ్యత, ప్రాసెసింగ్ సౌలభ్యం మరియు తుది ఉత్పత్తికి అవసరమైన లక్షణాల ఆధారంగా పదార్థాలను ఎంచుకుంటారు.
ఇంజెక్షన్ మౌల్డింగ్ మెటీరియల్ను ఎంచుకునేటప్పుడు పరిగణించవలసిన అంశాలు
ఇంజెక్షన్ మౌల్డింగ్ విషయానికి వస్తే తగిన పదార్థాన్ని ఎంచుకోవడం చాలా ముఖ్యం, ఎందుకంటే ఇది తుది ఉత్పత్తి యొక్క లక్షణాలు మరియు పనితీరును ప్రభావితం చేస్తుంది. ఇంజెక్షన్ మౌల్డింగ్ మెటీరియల్ను ఎంచుకునేటప్పుడు పరిగణించవలసిన కొన్ని అంశాలు ఇక్కడ ఉన్నాయి:
- యాంత్రిక లక్షణాలు: పదార్థాన్ని ఎన్నుకునేటప్పుడు పరిగణించవలసిన ముఖ్యమైన అంశాలలో ఒకటి దాని యాంత్రిక లక్షణాలు. ఇది దాని బలం, దృఢత్వం, మొండితనం మరియు ధరించడానికి మరియు కన్నీటికి నిరోధకతను కలిగి ఉంటుంది. తుది ఉత్పత్తికి అవసరమైన యాంత్రిక లక్షణాలు అప్లికేషన్ మరియు ఉత్పత్తి బహిర్గతమయ్యే ఒత్తిళ్లపై ఆధారపడి ఉంటాయి.
- థర్మల్ లక్షణాలు: పదార్థం యొక్క ఉష్ణ లక్షణాలు కూడా ముఖ్యమైనవి, ప్రత్యేకించి తుది ఉత్పత్తి అధిక ఉష్ణోగ్రతలు లేదా థర్మల్ సైక్లింగ్కు గురైనట్లయితే. ఇందులో పదార్థం యొక్క ద్రవీభవన స్థానం, ఉష్ణ వాహకత మరియు ఉష్ణ విస్తరణ గుణకం ఉన్నాయి.
- రసాయన నిరోధకత: తుది ఉత్పత్తి రసాయనాలకు గురైనట్లయితే, రసాయన క్షీణతను నిరోధించగల పదార్థాన్ని ఎంచుకోవడం చాలా అవసరం. పదార్థం దాని లక్షణాలను విచ్ఛిన్నం చేయకుండా లేదా కోల్పోకుండా ఆమ్లాలు, క్షారాలు, ద్రావకాలు మరియు ఇతర రసాయనాలకు గురికావడాన్ని తట్టుకోవాలి.
- పర్యావరణ కారకాలు: తేమ మరియు UV ఎక్స్పోజర్ వంటి పర్యావరణ కారకాలు కూడా పదార్థం యొక్క లక్షణాలు మరియు పనితీరును ప్రభావితం చేయవచ్చు. తుది ఉత్పత్తి యొక్క పర్యావరణ పరిస్థితులను పరిగణనలోకి తీసుకోవడం మరియు వాటిని తట్టుకోగల పదార్థాన్ని ఎంచుకోవడం చాలా అవసరం.
- ఖర్చు: పదార్థం యొక్క ధర కూడా ఒక ముఖ్యమైన అంశం, ముఖ్యంగా అధిక-వాల్యూమ్ ఉత్పత్తి పరుగుల కోసం. తుది ఉత్పత్తికి ఇది ఖర్చుతో కూడుకున్న ఎంపిక అని నిర్ధారించడానికి పదార్థం యొక్క ధర దాని పనితీరు మరియు లక్షణాలతో తూకం వేయాలి.
- ప్రాసెసింగ్ అవసరాలు: మెటీరియల్ కోసం ప్రాసెసింగ్ అవసరాలు కూడా ఎంపిక ప్రక్రియను ప్రభావితం చేయవచ్చు. కొన్ని మెటీరియల్స్ నిర్దిష్ట ప్రాసెసింగ్ పరికరాలు లేదా సాంకేతికతలు అవసరం కావచ్చు మరియు కొన్ని ప్రాసెస్ చేయడం చాలా కష్టంగా ఉండవచ్చు. ఇంజెక్షన్ మౌల్డింగ్ ప్రక్రియలో మెటీరియల్ విజయవంతంగా ఉపయోగించబడుతుందని నిర్ధారించడానికి ప్రాసెసింగ్ అవసరాలను పరిగణించాలి.
- రెగ్యులేటరీ సమ్మతి: చివరగా, తుది ఉత్పత్తి తప్పనిసరిగా తీర్చవలసిన ఏవైనా నియంత్రణ అవసరాలను పరిగణనలోకి తీసుకోవడం చాలా అవసరం. వైద్య మరియు ఆహార పరిశ్రమల వంటి కొన్ని పరిశ్రమలు తమ ఉత్పత్తులలో ఉపయోగించే పదార్థాలకు నిర్దిష్ట నిబంధనలను కలిగి ఉంటాయి. తుది ఉత్పత్తి సురక్షితంగా మరియు సమ్మతంగా ఉందని నిర్ధారించుకోవడానికి ఈ నియంత్రణ అవసరాలకు అనుగుణంగా ఉండే మెటీరియల్ని ఎంచుకోవడం చాలా అవసరం.
మొత్తంమీద, ఇంజెక్షన్ మౌల్డింగ్ కోసం తగిన మెటీరియల్ని ఎంచుకోవడానికి మెకానికల్ మరియు థర్మల్ లక్షణాలు, రసాయన నిరోధకత, పర్యావరణ కారకాలు, ఖర్చు, ప్రాసెసింగ్ అవసరాలు మరియు నియంత్రణ సమ్మతి వంటి వివిధ అంశాలను జాగ్రత్తగా పరిశీలించడం అవసరం. తుది ఉత్పత్తికి ఉత్తమంగా సరిపోయే పదార్థాన్ని ఎంచుకోవడానికి తయారీదారులు ఈ కారకాలను ఒకదానికొకటి తూకం వేయాలి.
ఇంజెక్షన్ మౌల్డింగ్లో అచ్చు రూపకల్పన యొక్క ప్రాముఖ్యత
ఇంజెక్షన్ మౌల్డింగ్ ప్రక్రియలో అచ్చు రూపకల్పన ఒక కీలకమైన అంశం. అచ్చు రూపకల్పన తుది ఉత్పత్తి యొక్క నాణ్యతను, అలాగే తయారీ ప్రక్రియ యొక్క సామర్థ్యం మరియు వ్యయ-ప్రభావాన్ని ప్రభావితం చేస్తుంది. ఇంజెక్షన్ మౌల్డింగ్లో అచ్చు రూపకల్పన అవసరం కావడానికి ఇక్కడ కొన్ని కారణాలు ఉన్నాయి:
- ఉత్పత్తి నాణ్యత: అచ్చు రూపకల్పన తుది ఉత్పత్తి నాణ్యతను ప్రభావితం చేస్తుంది. అచ్చు సరిగ్గా రూపొందించబడకపోతే, అది వార్పింగ్, సింక్ మార్కులు మరియు ఫ్లాష్ వంటి లోపాలను కలిగిస్తుంది. ఈ లోపాలు తుది ఉత్పత్తిని నిరుపయోగంగా చేస్తాయి, పనితీరును తగ్గిస్తాయి మరియు స్క్రాప్ రేట్లు మరియు ఉత్పత్తి ఖర్చులను పెంచుతాయి.
- తయారీ సామర్థ్యం: అచ్చు రూపకల్పన కూడా తయారీ ప్రక్రియ యొక్క సామర్థ్యాన్ని ప్రభావితం చేస్తుంది. అచ్చు సరైన ప్రవాహం మరియు శీతలీకరణ కోసం రూపొందించబడకపోతే, ఇది ఎక్కువ చక్రాల సమయాలను, శక్తి వినియోగం పెరగడానికి మరియు తగ్గిన నిర్గమాంశకు దారితీస్తుంది. ఆప్టిమైజ్ చేయబడిన అచ్చు డిజైన్ సామర్థ్యాన్ని మెరుగుపరుస్తుంది మరియు ఉత్పత్తి ఖర్చులను తగ్గిస్తుంది.
- ఖర్చు-ప్రభావం: మోల్డ్ డిజైన్ ఇంజెక్షన్ మోల్డింగ్ ప్రక్రియ యొక్క వ్యయ-ప్రభావాన్ని కూడా ప్రభావితం చేస్తుంది. బాగా రూపొందించిన అచ్చు పదార్థ వ్యర్థాలను తగ్గిస్తుంది, పార్ట్ క్వాలిటీని మెరుగుపరుస్తుంది మరియు ఉత్పత్తి ఖర్చులను తగ్గిస్తుంది. అదనంగా, అధిక-వాల్యూమ్ ఉత్పత్తి కోసం రూపొందించిన అచ్చు ఒక్కో భాగానికి ఖర్చును తగ్గిస్తుంది మరియు పెట్టుబడిపై రాబడిని పెంచుతుంది.
- అనుకూలీకరణ: తుది ఉత్పత్తి యొక్క అనుకూలీకరణలో మోల్డ్ డిజైన్ కూడా కీలక పాత్ర పోషిస్తుంది. నిర్దిష్ట ఆకారాలు మరియు లక్షణాల కోసం అచ్చును రూపొందించడం ద్వారా, తయారీదారులు తమ వినియోగదారుల అవసరాలకు అనుగుణంగా ఉత్పత్తులను సృష్టించవచ్చు. ఇది మార్కెట్లో ఎక్కువ సౌలభ్యం మరియు భేదం కోసం అనుమతిస్తుంది, ఇది కస్టమర్ సంతృప్తి మరియు విధేయతను పెంచుతుంది.
- మెటీరియల్ ఎంపిక: అచ్చు డిజైన్ ఇంజెక్షన్ మోల్డింగ్లో ఉపయోగించే పదార్థం యొక్క ఎంపికను కూడా ప్రభావితం చేస్తుంది. అచ్చు పద్ధతి మెటీరియల్ ఫ్లో మరియు శీతలీకరణను ప్రభావితం చేస్తుంది, ఇది తుది ఉత్పత్తి యొక్క యాంత్రిక మరియు ఉష్ణ లక్షణాలను ప్రభావితం చేస్తుంది. సరైన అచ్చు రూపకల్పనను ఎంచుకోవడం ద్వారా, తయారీదారులు మెటీరియల్ ఎంపికను ఆప్టిమైజ్ చేయవచ్చు మరియు తుది ఉత్పత్తి కావలసిన పనితీరు అవసరాలకు అనుగుణంగా ఉండేలా చూసుకోవచ్చు.
మొత్తంమీద, ఇంజెక్షన్ మౌల్డింగ్ ప్రక్రియలో అచ్చు రూపకల్పన ఒక కీలకమైన అంశం. బాగా డిజైన్ చేయబడిన అచ్చు ఉత్పత్తి నాణ్యత, తయారీ సామర్థ్యం, ఖర్చు-ప్రభావం, అనుకూలీకరణ మరియు మెటీరియల్ ఎంపికను మెరుగుపరుస్తుంది. ఇంజెక్షన్ మోల్డింగ్ ప్రక్రియలో సాధ్యమైనంత ఉత్తమమైన ఫలితాలను సాధించడానికి తయారీదారులు తమ నిర్దిష్ట అవసరాల కోసం ఆప్టిమైజ్ చేసిన అచ్చులను రూపొందించడానికి సమయం మరియు వనరులను పెట్టుబడి పెట్టాలి.
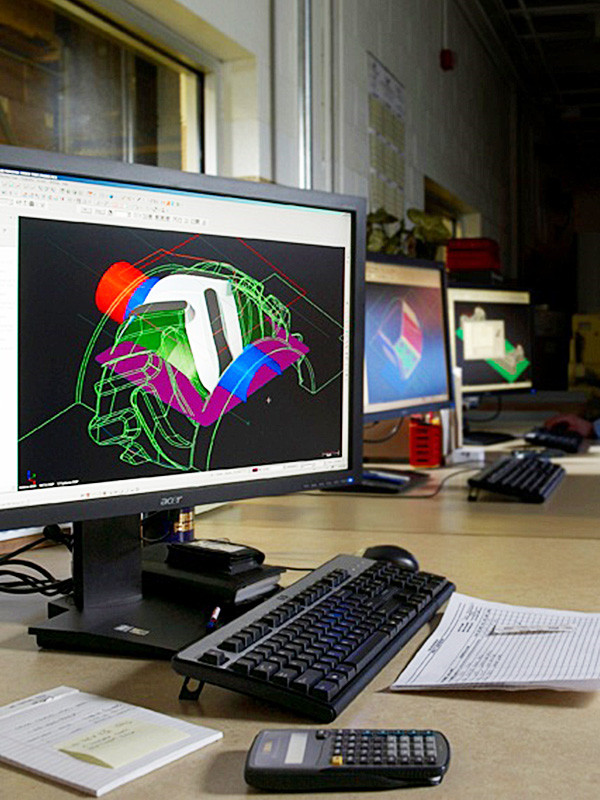
ఇంజెక్షన్ మౌల్డింగ్లో ఉపయోగించే వివిధ రకాల అచ్చులు
ఇంజెక్షన్ మౌల్డింగ్ అనేది వివిధ ప్లాస్టిక్ ఉత్పత్తులను ఉత్పత్తి చేయగల బహుముఖ తయారీ ప్రక్రియ. ఇంజక్షన్ మోల్డింగ్ యొక్క నాణ్యత మరియు సామర్థ్యాన్ని నిర్ణయించే ఒక క్లిష్టమైన అంశం ఉపయోగించే అచ్చు రకం. ఇంజెక్షన్ మోల్డింగ్లో ఉపయోగించే వివిధ రకాల అచ్చులు ఇక్కడ ఉన్నాయి:
- రెండు-ప్లేట్ అచ్చు: రెండు-ప్లేట్ అచ్చులు ఇంజెక్షన్ మోల్డింగ్లో ఉపయోగించే అత్యంత సాధారణ అచ్చు. అవి అచ్చు కుహరం ద్వారా వేరు చేయబడిన రెండు పలకలను కలిగి ఉంటాయి. ప్లాస్టిక్ పదార్థం కుహరంలోకి ఇంజెక్ట్ చేయబడుతుంది, రెండు ప్లేట్లను కలిపి తుది ఉత్పత్తిని ఏర్పరుస్తుంది.
- మూడు-ప్లేట్ అచ్చు: మూడు-ప్లేట్ అచ్చులు రెండు-ప్లేట్ అచ్చులను పోలి ఉంటాయి కానీ రన్నర్ సిస్టమ్ను అచ్చు భాగం నుండి వేరుచేసే అదనపు ప్లేట్ను కలిగి ఉంటాయి. ఇది భాగాన్ని సులభంగా ఎజెక్షన్ చేయడానికి అనుమతిస్తుంది మరియు సైకిల్ సమయాన్ని తగ్గిస్తుంది.
- హాట్ రన్నర్ అచ్చు: హాట్ రన్నర్ అచ్చులు అధిక-వాల్యూమ్ ఉత్పత్తి పరుగుల కోసం ఉపయోగించబడతాయి, ఎందుకంటే అవి సైకిల్ సమయం మరియు పదార్థ వ్యర్థాలను తగ్గించగలవు. అచ్చు వేడిచేసిన రన్నర్ వ్యవస్థను కలిగి ఉంటుంది, ఇది కరిగిన ప్లాస్టిక్ను నేరుగా అచ్చు కుహరానికి పంపిణీ చేస్తుంది, కోల్డ్ రన్నర్ అవసరాన్ని తొలగిస్తుంది.
- కోల్డ్ రన్నర్ అచ్చు: కోల్డ్ రన్నర్ అచ్చులు అత్యంత ప్రాథమిక రకం అచ్చు మరియు స్ప్రూ, రన్నర్లు మరియు అచ్చు కుహరాన్ని కలిగి ఉంటాయి. కరిగిన ప్లాస్టిక్ స్ప్రూలోకి ఇంజెక్ట్ చేయబడుతుంది, ఇది ప్లాస్టిక్ను రన్నర్స్లోకి మరియు తరువాత అచ్చు కుహరంలోకి ఫీడ్ చేస్తుంది.
- కుటుంబ అచ్చు: కుటుంబ అచ్చులు ఒకే చక్రంలో బహుళ భాగాలను ఉత్పత్తి చేస్తాయి. అచ్చు బహుళ కావిటీలను కలిగి ఉంటుంది, వీటిలో ప్రతి ఒక్కటి వేరే భాగాన్ని కలిగి ఉంటుంది. కుటుంబ అచ్చులను తరచుగా చిన్న, అధిక-వాల్యూమ్ భాగాల కోసం ఉపయోగిస్తారు.
- స్టాక్ అచ్చు: స్టాక్ అచ్చులు ఒకే చక్రంలో బహుళ పొరల ప్లాస్టిక్ను ఉత్పత్తి చేస్తాయి. అచ్చు అనేక పొరల కావిటీలను కలిగి ఉంటుంది, ఇవి ఒకదానిపై ఒకటి పేర్చబడి ఉంటాయి. ప్లాస్టిక్ను రంధ్రాలలోకి ఇంజెక్ట్ చేస్తారు, ఆపై పొరలు ఒకే, బహుళ-లేయర్డ్ ఉత్పత్తిని ఏర్పరుస్తాయి.
- అచ్చును చొప్పించండి: అచ్చు ప్రక్రియలో అచ్చు వేయబడిన భాగంలో మెటల్ లేదా ప్లాస్టిక్ భాగాలను చొప్పించడానికి ఇన్సర్ట్ అచ్చులను ఉపయోగిస్తారు. ప్లాస్టిక్ను ఇంజెక్ట్ చేయడానికి ముందు ఇన్సర్ట్ అచ్చు కుహరంలో ఉంచబడుతుంది మరియు ప్లాస్టిక్ ఇన్సర్ట్ను చుట్టుముడుతుంది.
మొత్తంమీద, ఇంజెక్షన్ మౌల్డింగ్లో ఉపయోగించే అచ్చు రకం ఉత్పత్తి చేయబడిన ఉత్పత్తి యొక్క నిర్దిష్ట అవసరాలపై ఆధారపడి ఉంటుంది. సరైన రకమైన అచ్చును ఎంచుకోవడం ద్వారా, తయారీదారులు ఇంజెక్షన్ మోల్డింగ్ ప్రక్రియ యొక్క సామర్థ్యం, నాణ్యత మరియు వ్యయ-ప్రభావాన్ని ఆప్టిమైజ్ చేయవచ్చు.
ఇంజెక్షన్ మౌల్డింగ్ కోసం ఉత్తమ పద్ధతులు
ఇంజెక్షన్ మౌల్డింగ్ అనేది సంక్లిష్టమైన తయారీ ప్రక్రియ, ఇది ఆశించిన ఫలితాలను సాధించడానికి జాగ్రత్తగా ప్రణాళిక మరియు అమలు అవసరం. ఇంజక్షన్ మోల్డింగ్ కోసం ఇక్కడ కొన్ని ఉత్తమ పద్ధతులు ఉన్నాయి, ఇవి సరైన నాణ్యత, సామర్థ్యం మరియు ఖర్చు-ప్రభావాన్ని నిర్ధారించడంలో సహాయపడతాయి:
- ఉత్పాదకత కోసం డిజైన్: ఇంజెక్షన్ మోల్డింగ్ కోసం ఉత్పత్తి రూపకల్పనను ఆప్టిమైజ్ చేయాలి. ఇది భాగాల సంఖ్యను తగ్గించడం, ఏకరీతి గోడ మందాన్ని నిర్ధారించడం మరియు అండర్కట్లు మరియు అచ్చును క్లిష్టతరం చేసే ఇతర లక్షణాలను నివారించడం వంటివి కలిగి ఉంటుంది.
- మెటీరియల్ ఎంపిక: ఇంజెక్షన్ మౌల్డింగ్లో ఉపయోగించే పదార్థాన్ని ఉత్పత్తి అవసరాల ఆధారంగా ఎంచుకోవాలి. యాంత్రిక లక్షణాలు, ఉష్ణ లక్షణాలు మరియు పర్యావరణ నిరోధకత వంటి అంశాలను పరిగణించాలి.
- అచ్చు రూపకల్పన: నిర్దిష్ట ఉత్పత్తి కోసం అచ్చు రూపకల్పనను ఆప్టిమైజ్ చేయాలి. ఇది సరైన శీతలీకరణ, వెంటిటింగ్ మరియు గేటింగ్ను నిర్ధారించడం, అలాగే తగిన రకమైన అచ్చును ఎంచుకోవడం.
- ఇంజెక్షన్ పారామితులు: ఇంజెక్షన్ పీడనం, ఉష్ణోగ్రత మరియు వేగం వంటి ఇంజెక్షన్ పారామితులు సరైన నాణ్యత మరియు స్థిరత్వాన్ని నిర్ధారించడానికి జాగ్రత్తగా నియంత్రించబడాలి మరియు పర్యవేక్షించబడాలి.
- నిర్వహణ: సాధారణ ఇంజెక్షన్ మోల్డింగ్ మెషిన్ మరియు అచ్చు నిర్వహణ సరైన పనితీరును నిర్ధారించడానికి మరియు పనికిరాని సమయాన్ని నిరోధించడానికి కీలకం.
- నాణ్యత నియంత్రణ: ఇన్కమింగ్ మెటీరియల్ తనిఖీ నుండి తుది ఉత్పత్తి తనిఖీ వరకు ఇంజెక్షన్ మోల్డింగ్ ప్రక్రియ అంతటా నాణ్యత నియంత్రణను అమలు చేయాలి. ఇందులో వార్పేజ్, సింక్ మార్క్లు మరియు ఫ్లాష్ వంటి పర్యవేక్షణ లోపాలు ఉన్నాయి.
- ప్రాసెస్ ఆప్టిమైజేషన్: నిరంతర ప్రక్రియ మెరుగుదల అనేది ఇంజెక్షన్ మోల్డింగ్ కార్యకలాపాలలో కీలకమైన అంశంగా ఉండాలి. ఇందులో సైకిల్ సమయం, స్క్రాప్ రేట్ మరియు మెషిన్ వినియోగం వంటి ప్రక్రియ పనితీరు కొలమానాలను పర్యవేక్షించడం మరియు సామర్థ్యం మరియు నాణ్యతను ఆప్టిమైజ్ చేయడానికి అవసరమైన సర్దుబాట్లు చేయడం వంటివి ఉంటాయి.
మొత్తంమీద, ఇంజెక్షన్ మౌల్డింగ్కు వివరాలపై శ్రద్ధ వహించడం మరియు నిరంతర అభివృద్ధిపై దృష్టి పెట్టడం అవసరం. ఇంజెక్షన్ మౌల్డింగ్ కోసం ఉత్తమ పద్ధతులను అనుసరించడం ద్వారా, తయారీదారులు సరైన నాణ్యత, సామర్థ్యం మరియు వ్యయ-ప్రభావాన్ని నిర్ధారించవచ్చు మరియు వారి వినియోగదారుల అవసరాలను తీర్చే అధిక-నాణ్యత ప్లాస్టిక్ ఉత్పత్తులను ఉత్పత్తి చేయవచ్చు.
ఇంజెక్షన్ మౌల్డింగ్ కోసం నాణ్యత నియంత్రణ చర్యలు
ఇంజెక్షన్ మౌల్డింగ్కు నాణ్యత నియంత్రణ కీలకం, ఎందుకంటే తుది ఉత్పత్తి అవసరమైన లక్షణాలు మరియు ప్రమాణాలకు అనుగుణంగా ఉండేలా చేస్తుంది. ఇంజెక్షన్ మోల్డింగ్ కోసం ఇక్కడ కొన్ని నాణ్యత నియంత్రణ చర్యలు ఉన్నాయి:
- ఇన్కమింగ్ మెటీరియల్ ఇన్స్పెక్షన్: ఇంజెక్షన్ మోల్డింగ్ కోసం ఉపయోగించే ముడి పదార్థం యొక్క సమీక్షతో నాణ్యత నియంత్రణ ప్రక్రియ ప్రారంభం కావాలి. మెటీరియల్ సరైన రకం, గ్రేడ్ మరియు రంగు మరియు అవసరమైన మెకానికల్ మరియు థర్మల్ ప్రాపర్టీస్ స్పెసిఫికేషన్లకు అనుగుణంగా ఉందని ధృవీకరించడం ఇందులో ఉంటుంది.
- ప్రక్రియలో తనిఖీ: ఇంజెక్షన్ మోల్డింగ్ సమయంలో, నాణ్యత నియంత్రణ సిబ్బంది ఉత్పత్తి సరిగ్గా అచ్చు వేయబడిందని నిర్ధారించుకోవడానికి క్రమం తప్పకుండా తనిఖీ చేయాలి. సింక్ మార్కులు, వార్పింగ్ మరియు ఫ్లాష్ వంటి లోపాలను పర్యవేక్షించడం మరియు ఉత్పత్తి అవసరమైన డైమెన్షనల్ టాలరెన్స్లకు అనుగుణంగా ఉందని ధృవీకరించడం ఇందులో ఉంటుంది.
- తుది ఉత్పత్తి తనిఖీ: ఇంజెక్షన్ మౌల్డింగ్ ప్రక్రియ పూర్తయిన తర్వాత, తుది ఉత్పత్తి అవసరమైన లక్షణాలు మరియు ప్రమాణాలకు అనుగుణంగా ఉందని నిర్ధారించుకోవడానికి తనిఖీ చేయాలి. ఉత్పత్తి పగుళ్లు, బుడగలు మరియు శూన్యాలు వంటి లోపాలు లేకుండా మరియు అవసరమైన డైమెన్షనల్ టాలరెన్స్లకు అనుగుణంగా ఉందని ధృవీకరించడం ఇందులో ఉంది.
- స్టాటిస్టికల్ ప్రాసెస్ కంట్రోల్: స్టాటిస్టికల్ ప్రాసెస్ కంట్రోల్ (SPC) అనేది స్థిరంగా అధిక-నాణ్యత ఫలితాలను ఉత్పత్తి చేసేలా ఒక ప్రక్రియను పర్యవేక్షించే మరియు నియంత్రించే పద్ధతి. SPC అనేది ఇంజెక్షన్ ఒత్తిడి మరియు ఉష్ణోగ్రత వంటి క్లిష్టమైన ప్రక్రియ పారామితులపై డేటాను సేకరించడం మరియు ప్రక్రియ వైవిధ్యాన్ని సూచించే ట్రెండ్లు మరియు నమూనాలను గుర్తించడానికి గణాంక విశ్లేషణను ఉపయోగించడం.
- నిరంతర అభివృద్ధి: నాణ్యత నియంత్రణ అనేది స్థిరమైన మెరుగుదల యొక్క కొనసాగుతున్న ప్రక్రియగా ఉండాలి. ప్రాసెస్ పనితీరుపై డేటాను విశ్లేషించడం, మెరుగుదల కోసం ప్రాంతాలను గుర్తించడం మరియు నాణ్యత మరియు సామర్థ్యాన్ని ఆప్టిమైజ్ చేయడానికి ప్రక్రియలో మార్పులు చేయడం ఇందులో ఉన్నాయి.
- డాక్యుమెంటేషన్ మరియు ట్రేస్బిలిటీ: ప్రాసెస్ పారామితులు, తనిఖీ ఫలితాలు మరియు దిద్దుబాటు చర్యలతో సహా ఇంజెక్షన్ మోల్డింగ్ ప్రక్రియ యొక్క వివరణాత్మక డాక్యుమెంటేషన్ను నాణ్యత నియంత్రణ సిబ్బంది నిర్వహించాలి. ఈ డాక్యుమెంటేషన్ ట్రేస్బిలిటీని అందిస్తుంది మరియు ఏవైనా నాణ్యత సమస్యలను త్వరగా గుర్తించి సరిదిద్దగలదని నిర్ధారించడంలో సహాయపడుతుంది.
మొత్తంమీద, నాణ్యత నియంత్రణ అనేది ఇంజెక్షన్ మౌల్డింగ్లో కీలకమైన అంశం మరియు తయారీ ప్రక్రియలోని ప్రతి అంశంలో ఏకీకృతం చేయబడాలి. ఈ నాణ్యత నియంత్రణ చర్యలను అమలు చేయడం ద్వారా, తయారీదారులు తమ వినియోగదారుల అవసరాలను తీర్చే అధిక-నాణ్యత ప్లాస్టిక్ ఉత్పత్తులను ఉత్పత్తి చేయవచ్చు.
ఇంజెక్షన్ మౌల్డింగ్లో సాధారణ లోపాలు మరియు వాటిని ఎలా నివారించాలి
ఇంజెక్షన్ మౌల్డింగ్ అనేది ఒక సంక్లిష్ట ప్రక్రియ, ఇది సరిగ్గా అమలు చేయకపోతే లోపాలను కలిగిస్తుంది. ఇంజెక్షన్ మౌల్డింగ్లో కొన్ని సాధారణ లోపాలు మరియు వాటిని ఎలా నివారించాలో ఇక్కడ ఉన్నాయి:
- సింక్ మార్కులు ఉత్పత్తి యొక్క ఉపరితలంపై డిప్రెషన్లు లేదా డెంట్లు. అవి అసమాన శీతలీకరణ లేదా తగినంత ప్యాకింగ్ ఒత్తిడి కారణంగా సంభవిస్తాయి. అచ్చు రూపకల్పనలో ఏకరీతి గోడ మందం మరియు సింక్ గుర్తులను నిరోధించడానికి తగిన డ్రాఫ్ట్ కోణాలు ఉన్నాయని నిర్ధారించుకోండి. ప్యాకింగ్ ఒత్తిడి మరియు శీతలీకరణ సమయాన్ని సర్దుబాటు చేయడం కూడా సింక్ మార్కులను నిరోధించడంలో సహాయపడుతుంది.
- వార్పేజ్: వార్పేజ్ అనేది అచ్చు నుండి తొలగించబడిన తర్వాత ఉత్పత్తి యొక్క వక్రీకరణ. ఉత్పత్తిలో అసమాన శీతలీకరణ లేదా అంతర్గత ఒత్తిళ్ల వల్ల ఇది సంభవిస్తుంది. వార్పేజ్ను నిరోధించడానికి, మోల్డ్ డిజైన్లో ఏకరీతి గోడ మందం మరియు తగినంత శీతలీకరణ సమయం ఉండేలా చూసుకోండి. పదునైన మూలలు లేదా ఉత్పత్తి జ్యామితిలో ఆకస్మిక మార్పులను నివారించండి, ఇది ఒత్తిడి పాయింట్లను సృష్టించగలదు.
- ఫ్లాష్: ఫ్లాష్ అనేది అదనపు ప్లాస్టిక్, ఇది ఉత్పత్తి సరిహద్దులకు మించి విస్తరించి ఉంటుంది, సాధారణంగా అచ్చు అంచుల చుట్టూ ఉంటుంది. ఇది అధిక ఇంజెక్షన్ ఒత్తిడి, తగినంత బిగింపు శక్తి లేదా అరిగిన అచ్చు కారణంగా సంభవిస్తుంది. ఫ్లాష్ను నిరోధించడానికి, ఇంజెక్షన్ ప్రెజర్ మరియు బిగింపు శక్తిని సర్దుబాటు చేయండి మరియు దుస్తులు ధరించే సంకేతాల కోసం అచ్చును క్రమం తప్పకుండా తనిఖీ చేయండి.
- చిన్న షాట్లు: అచ్చును పాక్షికంగా ప్లాస్టిక్తో నింపినప్పుడు చిన్న షాట్లు ఏర్పడతాయి. ఇది తగినంత ఇంజెక్షన్ ఒత్తిడి లేదా ఉష్ణోగ్రత లేదా బ్లాక్ చేయబడిన లేదా నిరోధిత ప్రవాహ ఛానల్ వల్ల సంభవించవచ్చు. చిన్న షాట్లను నివారించడానికి, ఇంజెక్షన్ ఒత్తిడి మరియు ఉష్ణోగ్రతను సర్దుబాటు చేయండి మరియు ఫ్లో ఛానల్ స్పష్టంగా మరియు అడ్డంకులు లేకుండా ఉండేలా చూసుకోండి.
- బర్న్ మార్క్స్: బర్న్ మార్క్స్ అనేది అచ్చులో వేడెక్కడం లేదా అధిక రాపిడి వల్ల ఉత్పత్తి యొక్క ఉపరితలంపై ముదురు రంగు మారడం. కాలిన గుర్తులను నివారించడానికి, అచ్చు తగినంతగా చల్లబడి మరియు లూబ్రికేట్ చేయబడిందని నిర్ధారించుకోండి మరియు ఇంజెక్షన్ వేగం మరియు ఒత్తిడిని అవసరమైన విధంగా సర్దుబాటు చేయండి.
- శూన్యాలు మరియు బుడగలు: శూన్యాలు మరియు బుడగలు అనేది మెటీరియల్ లేని లేదా గాలి పాకెట్లను కలిగి ఉన్న ఉత్పత్తి ప్రాంతాలు. అవి అచ్చులో చిక్కుకున్న గాలి లేదా వాయువు లేదా తగినంత పదార్థ ప్రవాహం వల్ల సంభవిస్తాయి. శూన్యాలు మరియు బుడగలు నిరోధించడానికి, అచ్చు సరిగ్గా వెంట్ చేయబడిందని మరియు ఏకరీతి పదార్థం ప్రవాహాన్ని నిర్ధారించడానికి ఇంజెక్షన్ వేగం మరియు ఒత్తిడి సరిపోతుందని నిర్ధారించుకోండి.
ఇంజక్షన్ మోల్డింగ్ పరికరాల నిర్వహణ చిట్కాలు
ఇంజెక్షన్ మౌల్డింగ్ పరికరాలు తయారీదారులకు ముఖ్యమైన పెట్టుబడి, మరియు సరైన పనితీరు మరియు దీర్ఘాయువును నిర్ధారించడానికి సరైన నిర్వహణ అవసరం. ఇంజెక్షన్ మోల్డింగ్ పరికరాల కోసం ఇక్కడ కొన్ని నిర్వహణ చిట్కాలు ఉన్నాయి:
- క్రమం తప్పకుండా తనిఖీలు నిర్వహించండి: ఏదైనా దుస్తులు మరియు కన్నీటి, నష్టం లేదా ఇతర సమస్యలను గుర్తించడానికి పరికరాలను క్రమం తప్పకుండా తనిఖీ చేయండి. హైడ్రాలిక్ గొట్టాలు, సీల్స్ మరియు ఇతర క్లిష్టమైన భాగాలు మంచి స్థితిలో ఉన్నాయని నిర్ధారించుకోవడానికి వాటిని తనిఖీ చేయండి.
- పరికరాలను శుభ్రపరచండి మరియు ద్రవపదార్థం చేయండి: తుప్పు మరియు ధరించకుండా నిరోధించడానికి పరికరాలను క్రమం తప్పకుండా శుభ్రపరచండి మరియు ద్రవపదార్థం చేయండి. సిఫార్సు చేయబడిన క్లీనింగ్ మరియు లూబ్రికేషన్ ఉత్పత్తులను ఉపయోగించండి మరియు తయారీదారు సూచనలను అనుసరించండి.
- హైడ్రాలిక్ ఆయిల్ను పర్యవేక్షించండి మరియు నిర్వహించండి: ఇది శుభ్రంగా మరియు సరైన స్నిగ్ధతతో ఉండేలా క్రమం తప్పకుండా పర్యవేక్షించండి. అవసరమైన విధంగా నూనెను మార్చండి మరియు సిఫార్సు చేయబడిన నూనె రకాన్ని ఉపయోగించండి.
- హీటర్ బ్యాండ్లను నిర్వహించండి: అవి మంచి స్థితిలో ఉన్నాయని మరియు సరిగ్గా వేడెక్కుతున్నాయని నిర్ధారించుకోవడానికి వాటిని క్రమం తప్పకుండా తనిఖీ చేయండి. దెబ్బతిన్న లేదా అరిగిపోయిన హీటర్ బ్యాండ్లను వెంటనే మార్చండి.
- శీతలీకరణ వ్యవస్థను పర్యవేక్షించండి మరియు నిర్వహించండి: ఇంజెక్షన్ మౌల్డింగ్కు ఇది కీలకం, ఎందుకంటే ఇది వేడెక్కడం మరియు వార్పేజ్ను నిరోధిస్తుంది. శీతలీకరణ వ్యవస్థ సరిగ్గా పనిచేస్తుందని నిర్ధారించుకోవడానికి క్రమం తప్పకుండా పర్యవేక్షించండి మరియు అవసరమైన విధంగా శీతలీకరణ ఛానెల్లను శుభ్రం చేయండి.
- రైలు ఆపరేటర్లు: నష్టాన్ని నివారించడానికి మరియు సరైన పనితీరును నిర్ధారించడానికి సరైన పరికరాల ఆపరేషన్ మరియు నిర్వహణ విధానాలపై రైలు ఆపరేటర్లు.
- సాధారణ నిర్వహణను షెడ్యూల్ చేయండి: నిర్వహణ షెడ్యూల్ను ఏర్పాటు చేయండి మరియు దానికి కట్టుబడి ఉండండి. సరళత మరియు చమురు మార్పులు వంటి సాధారణ నిర్వహణ పనులను షెడ్యూల్ చేయండి మరియు అన్ని నిర్వహణ కార్యకలాపాలను డాక్యుమెంట్ చేయండి.
- విడిభాగాలను చేతిలో ఉంచండి: హైడ్రాలిక్ గొట్టాలు, సీల్స్ మరియు హీటర్ బ్యాండ్లు వంటి విడి భాగాలను అందించండి. ఇది త్వరగా దెబ్బతిన్న లేదా అరిగిపోయిన భాగాలను భర్తీ చేస్తుంది మరియు పనికిరాని సమయాన్ని తగ్గిస్తుంది.
ఇంజెక్షన్ మౌల్డింగ్ పరికరాల సరైన నిర్వహణ అది సమర్ధవంతంగా పనిచేస్తుందని, అధిక-నాణ్యత ఉత్పత్తులను ఉత్పత్తి చేయడానికి మరియు సుదీర్ఘ జీవితకాలం కలిగి ఉండేలా చూసుకోవడం చాలా అవసరం. ఈ నిర్వహణ చిట్కాలను అనుసరించడం ద్వారా, తయారీదారులు తమ పరికరాలను అత్యుత్తమ స్థితిలో ఉంచవచ్చు మరియు పనికిరాని సమయం మరియు మరమ్మత్తు ఖర్చులను తగ్గించవచ్చు.
సరైన ఇంజెక్షన్ మోల్డింగ్ తయారీదారుని ఎలా ఎంచుకోవాలి
సరైన ఇంజెక్షన్ మోల్డింగ్ తయారీదారుని ఎంచుకోవడం అనేది మీ ఉత్పత్తుల నాణ్యత మరియు ధరను గణనీయంగా ప్రభావితం చేసే ముఖ్యమైన నిర్ణయం. ఇంజెక్షన్ మోల్డింగ్ తయారీదారుని ఎన్నుకునేటప్పుడు పరిగణించవలసిన కొన్ని అంశాలు ఇక్కడ ఉన్నాయి:
- అనుభవం మరియు నైపుణ్యం: ఇంజెక్షన్ మౌల్డింగ్లో విస్తృతమైన అనుభవం మరియు నైపుణ్యం కలిగిన తయారీదారు కోసం చూడండి. వాటి తయారీ ప్రక్రియలు, నాణ్యత నియంత్రణ చర్యలు మరియు ధృవపత్రాల గురించి అడగండి.
- సాంకేతికత మరియు పరికరాలు: ఆధునిక సాంకేతికత మరియు పరికరాలను ఉపయోగించే తయారీదారు కోసం చూడండి. ఇది స్థిరమైన నాణ్యత, తక్కువ లీడ్ టైమ్లు మరియు ఖర్చు-ప్రభావాన్ని నిర్ధారించడంలో సహాయపడుతుంది.
- మెటీరియల్స్ మరియు సామర్థ్యాలు: తయారీదారు పని చేయగల పదార్థాల రకాలు మరియు వాటి సామర్థ్యాలను పరిగణించండి. ప్రత్యేకమైన మెటీరియల్లతో సహా విస్తృత శ్రేణి పదార్థాలను నిర్వహించగల మరియు వివిధ రకాల ఉత్పత్తి పరిమాణాలు మరియు ఆకృతులను ఉత్పత్తి చేయగల తయారీదారు కోసం చూడండి.
- నాణ్యత నియంత్రణ చర్యలు: నాణ్యత నియంత్రణపై గట్టిగా దృష్టి సారించే తయారీదారు కోసం చూడండి. తనిఖీ మరియు పరీక్షా విధానాలు మరియు వారు కలిగి ఉన్న ఏవైనా ధృవపత్రాలు వంటి వారి నాణ్యత నియంత్రణ చర్యల గురించి అడగండి.
- కస్టమర్ సేవ: అద్భుతమైన కస్టమర్ సేవను అందించే తయారీదారు కోసం చూడండి. మీ నిర్దిష్ట అవసరాలను తీర్చడానికి ప్రతిస్పందన, కమ్యూనికేషన్ మరియు మీతో కలిసి పని చేయడానికి సుముఖతను పరిగణించండి.
- ఖర్చు మరియు ప్రధాన సమయం: మీ ప్రాజెక్ట్ కోసం తయారీదారు ధర మరియు ప్రధాన సమయాన్ని పరిగణించండి. మీ అవసరాలకు అనుగుణంగా పోటీ ధర మరియు వాస్తవిక లీడ్ టైమ్లను అందించే తయారీదారు కోసం చూడండి.
- సూచనలు మరియు సమీక్షలు: సూచనల కోసం అడగండి మరియు తయారీదారు యొక్క ఆన్లైన్ సమీక్షలను తనిఖీ చేయండి. ఇది వారి ఖ్యాతిని మరియు ఇతర కస్టమర్ల అనుభవాలను మెరుగ్గా అర్థం చేసుకోవడానికి మీకు సహాయపడుతుంది.
మీరు ఈ అంశాలను పరిగణలోకి తీసుకొని మరియు సమగ్ర పరిశోధన చేయడం ద్వారా మీ ప్రాజెక్ట్ కోసం సరైన ఇంజెక్షన్ మోల్డింగ్ తయారీదారుని ఎంచుకోవచ్చు. సరైన అనుభవం, సామర్థ్యాలు మరియు నాణ్యత పట్ల నిబద్ధత కలిగిన ప్రసిద్ధ తయారీదారు మీ ఉత్పత్తులను సమర్ధవంతంగా, తక్కువ ఖర్చుతో మరియు మీ ఖచ్చితమైన స్పెసిఫికేషన్లకు అనుగుణంగా ఉత్పత్తి చేయడంలో సహాయపడగలరు.
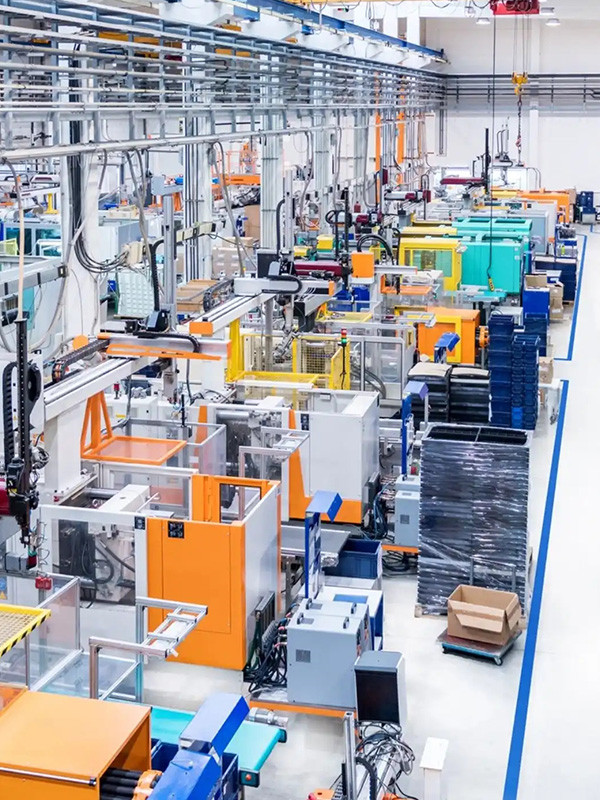
కస్టమ్ ప్లాస్టిక్ ఇంజెక్షన్ మౌల్డింగ్లో ఖర్చు పరిగణనలు
కస్టమ్ ప్లాస్టిక్ ఇంజెక్షన్ మౌల్డింగ్ అనేది అత్యంత బహుముఖ తయారీ ప్రక్రియ, ఇది స్కేల్లో సంక్లిష్టమైన, అధిక-నాణ్యత భాగాలను ఉత్పత్తి చేయగలదు. అయితే, ఈ తయారీ ప్రక్రియను ఉపయోగించడంలో వ్యయ పరిగణనలు కీలకమైన అంశం. కస్టమ్ ప్లాస్టిక్ ఇంజెక్షన్ మౌల్డింగ్లో కొన్ని కీలక వ్యయ పరిగణనలు ఇక్కడ ఉన్నాయి:
- మెటీరియల్ ఖర్చులు: ఇంజెక్షన్ మోల్డింగ్ ప్రక్రియలో ఉపయోగించే పదార్థం యొక్క రకం మరియు పరిమాణం ధరను ప్రభావితం చేస్తుంది. అధిక-పనితీరు గల ఇంజనీరింగ్ ప్లాస్టిక్ల వంటి కొన్ని పదార్థాలు ఇతరులకన్నా ఖరీదైనవి. సరఫరా గొలుసు అంతరాయాలు, మార్కెట్ డిమాండ్ మరియు ధరల హెచ్చుతగ్గుల వల్ల పదార్థాల ధర కూడా ప్రభావితమవుతుంది.
- టూలింగ్ ఖర్చులు: కస్టమ్ ప్లాస్టిక్ ఇంజెక్షన్ మోల్డింగ్లో టూలింగ్ ఖర్చు లేదా భాగాలను ఉత్పత్తి చేయడానికి ఉపయోగించే అచ్చులు గణనీయమైన వ్యయం. భాగం యొక్క సంక్లిష్టత, అచ్చులోని కావిటీస్ సంఖ్య మరియు అచ్చును రూపొందించడానికి ఉపయోగించే పదార్థం అన్నీ సాధన ఖర్చును ప్రభావితం చేస్తాయి. టూలింగ్ ముందస్తుగా ఖరీదైనది కావచ్చు కానీ ఉత్పత్తి సామర్థ్యాన్ని పెంచడం ద్వారా కాలక్రమేణా యూనిట్ ఖర్చులను తగ్గించడంలో సహాయపడుతుంది.
- ఉత్పత్తి పరిమాణం: ఉత్పత్తి చేయబడిన భాగాల పరిమాణం ఇంజెక్షన్ మోల్డింగ్ ధరను ప్రభావితం చేస్తుంది. అధిక-వాల్యూమ్ ఉత్పత్తి యూనిట్ ఖర్చులను తగ్గించడంలో సహాయపడుతుంది, అయితే తక్కువ-వాల్యూమ్ ఉత్పత్తికి ఎక్కువ టూలింగ్ మరియు సెటప్ సమయం అవసరం కారణంగా యూనిట్ ఖర్చులు ఎక్కువగా ఉండవచ్చు.
- లేబర్ ఖర్చులు: ఇంజక్షన్ మౌల్డింగ్లో లేబర్ ఖర్చులు ఒక ముఖ్యమైన అంశం, ప్రత్యేకించి ఎక్కువ మాన్యువల్ లేబర్ అవసరమయ్యే క్లిష్టమైన భాగాలకు. ఆపరేటర్ల నైపుణ్యం స్థాయి మరియు భాగం యొక్క సంక్లిష్టత డెలివరీ ధరను ప్రభావితం చేస్తుంది.
- నాణ్యత నియంత్రణ ఖర్చులు: భాగాల సమగ్రతను నిర్ధారించడానికి నాణ్యత నియంత్రణను నిర్వహించడం చాలా అవసరం. నాణ్యత నియంత్రణ ధరలో తనిఖీ పరికరాలు, పరీక్ష మరియు శ్రమ ఉంటుంది.
- షిప్పింగ్ ఖర్చులు: కస్టమర్కు లేదా ఇతర ప్రదేశాలకు విడిభాగాలను రవాణా చేయడం అనేది ఒక ముఖ్యమైన వ్యయం, ప్రత్యేకించి పెద్ద లేదా భారీ వివరాల కోసం.
తయారీదారులు ఈ వ్యయ కారకాలను పరిగణనలోకి తీసుకోవడం ద్వారా మరియు ఇంజెక్షన్ మోల్డింగ్ ప్రక్రియను ఆప్టిమైజ్ చేయడం ద్వారా తక్కువ ధరతో అధిక-నాణ్యత భాగాలను ఉత్పత్తి చేయవచ్చు. పదార్థ వ్యర్థాలను తగ్గించడం, ఉత్పత్తి సామర్థ్యాన్ని పెంచడం మరియు సెటప్ మరియు మార్పు సమయాన్ని తగ్గించడం ద్వారా దీనిని సాధించవచ్చు. అనుభవజ్ఞుడైన మరియు పరిజ్ఞానం ఉన్న ఇంజక్షన్ మోల్డింగ్ తయారీదారుతో పని చేయడం కూడా ప్రక్రియను ఆప్టిమైజ్ చేయడంలో మరియు ఖర్చులను తగ్గించడంలో సహాయపడుతుంది.
ఇంజెక్షన్ మోల్డింగ్ టెక్నాలజీలో ట్రెండ్లు మరియు ఆవిష్కరణలు
ఇంజెక్షన్ మౌల్డింగ్ టెక్నాలజీ చాలా సంవత్సరాలుగా ఉంది, అయితే ఈ తయారీ ప్రక్రియ యొక్క భవిష్యత్తును రూపొందించే అనేక ఆవిష్కరణలు మరియు పోకడలు ఇప్పటికీ ఉన్నాయి. ఇంజెక్షన్ మోల్డింగ్ టెక్నాలజీలో కొన్ని అగ్ర పోకడలు మరియు ఆవిష్కరణలు ఇక్కడ ఉన్నాయి:
- 3D ప్రింటింగ్ మరియు సంకలిత తయారీ: 3D ప్రింటింగ్ మరియు సంకలిత తయారీ ఇంజెక్షన్ మోల్డింగ్ పరిశ్రమలో బాగా ప్రాచుర్యం పొందుతున్నాయి. సాంప్రదాయిక ఇంజెక్షన్ మౌల్డింగ్తో సాధించడం కష్టం లేదా అసాధ్యం అయిన సంక్లిష్ట ఆకారాలు మరియు జ్యామితిలను రూపొందించడానికి ఈ సాంకేతికత అనుమతిస్తుంది.
- మల్టీ-మెటీరియల్ ఇంజెక్షన్ మౌల్డింగ్: మల్టీ-మెటీరియల్ ఇంజెక్షన్ మోల్డింగ్ ఒకే షాట్లో బహుళ పదార్థాలు లేదా రంగులతో భాగాలను సృష్టించడానికి అనుమతిస్తుంది. ఈ ప్రక్రియ తయారీ సమయం మరియు ఖర్చులను తగ్గిస్తుంది మరియు ప్రత్యేక లక్షణాలు మరియు ప్రదర్శనలతో ఫంక్షన్లను సృష్టించగలదు.
- ఆటోమేషన్ మరియు ఇండస్ట్రీ 4.0: IoT సెన్సార్లు మరియు రోబోటిక్స్ వంటి ఆటోమేషన్ మరియు ఇండస్ట్రీ 4.0 టెక్నాలజీలు ఇంజెక్షన్ మోల్డింగ్ మెషీన్లు మరియు ప్రాసెస్లలో విలీనం చేయబడుతున్నాయి. ఇది ఉత్పత్తి సామర్థ్యాన్ని మెరుగుపరుస్తుంది, కార్మిక వ్యయాలను తగ్గిస్తుంది మరియు నాణ్యత నియంత్రణను మెరుగుపరుస్తుంది.
- స్థిరమైన పదార్థాలు మరియు ప్రక్రియలు: కంపెనీలు తమ పర్యావరణ ప్రభావాన్ని తగ్గించడానికి ప్రయత్నిస్తున్నందున, ఇంజెక్షన్ మోల్డింగ్ పరిశ్రమలో స్థిరమైన పదార్థాలు మరియు పద్ధతులు మరింత ముఖ్యమైనవి. వ్యర్థాలు మరియు శక్తి వినియోగాన్ని తగ్గించే బయోడిగ్రేడబుల్ లేదా రీసైకిల్ పదార్థాలు మరియు ప్రక్రియలను ఉపయోగించడం ఇందులో ఉంటుంది.
- స్మార్ట్ మాన్యుఫ్యాక్చరింగ్ మరియు ప్రిడిక్టివ్ మెయింటెనెన్స్: మెషిన్ లెర్నింగ్ మరియు ప్రిడిక్టివ్ మెయింటెనెన్స్ వంటి స్మార్ట్ మాన్యుఫ్యాక్చరింగ్ టెక్నాలజీలు ఇంజెక్షన్ మోల్డింగ్ ప్రక్రియలను ఆప్టిమైజ్ చేయడానికి మరియు పనికిరాని సమయాన్ని తగ్గించడానికి ఉపయోగించబడుతున్నాయి. ఇది మొత్తం సామర్థ్యాన్ని మెరుగుపరుస్తుంది మరియు నిర్వహణ ఖర్చులను తగ్గిస్తుంది.
- అధిక-పనితీరు గల పదార్థాలు: ఇంజక్షన్ మౌల్డింగ్ కోసం కొత్త అధిక-పనితీరు గల పదార్థాలు అభివృద్ధి చేయబడుతున్నాయి, ఇందులో మెరుగైన బలం, మన్నిక మరియు వేడి నిరోధకత కలిగిన పదార్థాలు ఉన్నాయి. ఈ పదార్థాలను ఆటోమోటివ్ భాగాల నుండి వైద్య పరికరాల వరకు వివిధ అనువర్తనాల్లో ఉపయోగించవచ్చు.
ఈ పోకడలు మరియు ఆవిష్కరణలపై తాజాగా ఉండటం ద్వారా, ఇంజెక్షన్ మోల్డింగ్ తయారీదారులు పోటీతత్వంతో ఉంటారు మరియు వారి వినియోగదారులకు అధిక-నాణ్యత భాగాలను అందించడం కొనసాగించవచ్చు. కొత్త సాంకేతికతలు మరియు మెటీరియల్స్ అభివృద్ధి చేయబడినందున, ఇంజెక్షన్ మోల్డింగ్ పరిశ్రమ అభివృద్ధి చెందుతూనే ఉంటుంది మరియు వినియోగదారులు మరియు వ్యాపారాల యొక్క మారుతున్న అవసరాలకు అనుగుణంగా మారుతుంది.
ఇంజెక్షన్ మౌల్డింగ్లో స్థిరత్వం: వ్యర్థాలు మరియు శక్తి వినియోగాన్ని తగ్గించడం
కంపెనీలు తమ పర్యావరణ ప్రభావాన్ని తగ్గించుకోవడానికి మరియు పర్యావరణ అనుకూల ఉత్పత్తుల కోసం పెరుగుతున్న డిమాండ్ను తీర్చడానికి ప్రయత్నిస్తున్నందున ఇంజెక్షన్ మోల్డింగ్ పరిశ్రమలో స్థిరత్వం చాలా ముఖ్యమైనది. ఇంజెక్షన్ మోల్డింగ్ తయారీదారులు వ్యర్థాలు మరియు శక్తి వినియోగాన్ని తగ్గించే కొన్ని మార్గాలు ఇక్కడ ఉన్నాయి:
- స్థిరమైన పదార్థాలను ఉపయోగించండి: పదార్థం యొక్క ఎంపిక స్థిరత్వంలో కీలకమైన అంశం. ఇంజెక్షన్ మోల్డింగ్ తయారీదారులు పర్యావరణ ప్రభావాన్ని తగ్గించడానికి బయోడిగ్రేడబుల్ లేదా రీసైకిల్ పదార్థాలను ఉపయోగించవచ్చు. బయోడిగ్రేడబుల్ ప్లాస్టిక్స్, ఉదాహరణకు, కాలక్రమేణా సహజంగా విచ్ఛిన్నం అవుతాయి మరియు పల్లపు ప్రదేశాలలో వ్యర్థాల మొత్తాన్ని తగ్గిస్తాయి. పోస్ట్-కన్స్యూమర్ రీసైకిల్ ప్లాస్టిక్స్ వంటి రీసైకిల్ పదార్థాలు కూడా వ్యర్థాలు మరియు శక్తి వినియోగాన్ని తగ్గించడంలో సహాయపడతాయి.
- పదార్థ వ్యర్థాలను తగ్గించండి: ఇంజెక్షన్ మోల్డింగ్ తయారీదారులు భాగం మరియు అచ్చు రూపకల్పనను ఆప్టిమైజ్ చేయడం ద్వారా పదార్థాల వ్యర్థాలను కూడా తగ్గించవచ్చు. ఇది ఉపయోగించిన అదనపు పదార్థాన్ని తగ్గించడం, అచ్చులోని కావిటీస్ సంఖ్యను తగ్గించడం మరియు భాగం యొక్క మొత్తం బరువును తగ్గించడం. పదార్థ వ్యర్థాలను తగ్గించడం ద్వారా, తయారీదారులు పదార్థ ఖర్చులను ఆదా చేయవచ్చు మరియు వారి పర్యావరణ ప్రభావాన్ని తగ్గించవచ్చు.
- ఉత్పత్తి సామర్థ్యాన్ని ఆప్టిమైజ్ చేయండి: ఇంజెక్షన్ మోల్డింగ్ తయారీదారులు శక్తి వినియోగాన్ని తగ్గించడానికి వారి ఉత్పత్తి ప్రక్రియలను ఆప్టిమైజ్ చేయవచ్చు. ఇందులో హై-ఎఫిషియన్సీ ఇంజెక్షన్ మోల్డింగ్ మెషీన్లను ఉపయోగించడం, మోల్డింగ్ ప్రాసెస్ పారామితులను ఆప్టిమైజ్ చేయడం మరియు డౌన్టైమ్ను తగ్గించడం వంటివి ఉంటాయి. శక్తి వినియోగాన్ని తగ్గించడం ద్వారా, తయారీదారులు శక్తి ఖర్చులను ఆదా చేయవచ్చు మరియు వారి కార్బన్ పాదముద్రను తగ్గించవచ్చు.
- స్థిరమైన పద్ధతులను అమలు చేయండి: ఇంజెక్షన్ మోల్డింగ్ తయారీదారులు తమ కార్యకలాపాలలో రీసైక్లింగ్ మరియు వ్యర్థాలను తగ్గించే కార్యక్రమాలు, పునరుత్పాదక ఇంధన వనరులను ఉపయోగించడం మరియు వారి ఉద్యోగులు మరియు సరఫరాదారుల మధ్య స్థిరత్వాన్ని ప్రోత్సహించడం వంటి స్థిరమైన పద్ధతులను కూడా అమలు చేయవచ్చు. సరఫరా గొలుసు అంతటా స్థిరమైన పద్ధతులను ప్రోత్సహించడం ద్వారా, తయారీదారులు మరింత స్థిరమైన పరిశ్రమను రూపొందించడంలో సహాయపడగలరు.
- స్థిరమైన ప్యాకేజింగ్ను ఉపయోగించండి: చివరగా, ఇంజెక్షన్ మోల్డింగ్ తయారీదారులు వ్యర్థాలు మరియు పర్యావరణ ప్రభావాన్ని తగ్గించడానికి స్థిరమైన ప్యాకేజింగ్ పదార్థాలు మరియు డిజైన్లను ఉపయోగించవచ్చు. బయోడిగ్రేడబుల్ లేదా రీసైకిల్ చేయగల ప్యాకేజింగ్ మెటీరియల్లను ఉపయోగించడం, ప్యాకేజింగ్ వ్యర్థాలను తగ్గించడం మరియు పునర్వినియోగపరచదగిన లేదా రీఫిల్ చేయగల ప్యాకేజింగ్ను రూపొందించడం వంటివి ఇందులో ఉన్నాయి.
ఈ స్థిరమైన పద్ధతులను అమలు చేయడం ద్వారా, ఇంజెక్షన్ మోల్డింగ్ తయారీదారులు వారి పర్యావరణ ప్రభావాన్ని తగ్గించవచ్చు మరియు మొత్తం మీద మరింత స్థిరమైన పరిశ్రమను సృష్టించవచ్చు. వినియోగదారులకు మరియు వ్యాపారాలకు సుస్థిరత చాలా ముఖ్యమైనదిగా మారినందున, ఇంజెక్షన్ మోల్డింగ్ తయారీదారులు స్థిరత్వానికి ప్రాధాన్యతనిస్తారు, పర్యావరణ అనుకూల ఉత్పత్తుల కోసం పెరుగుతున్న డిమాండ్ను తీర్చడానికి మంచి స్థానంలో ఉంటారు.
కస్టమ్ ప్లాస్టిక్ ఇంజెక్షన్ మౌల్డింగ్ ఇతర తయారీ ప్రక్రియలతో ఎలా పోలుస్తుంది
కస్టమ్ ప్లాస్టిక్ ఇంజెక్షన్ మోల్డింగ్ అనేది అధిక-నాణ్యత ప్లాస్టిక్ భాగాలను పెద్ద పరిమాణంలో ఉత్పత్తి చేయడానికి ఒక ప్రసిద్ధ తయారీ ప్రక్రియ. అయినప్పటికీ, ప్లాస్టిక్ భాగాలను తయారు చేయడానికి అనేక ఇతర తయారీ ప్రక్రియలను ఉపయోగించవచ్చు, వీటిలో ప్రతి ఒక్కటి ప్రయోజనాలు మరియు అప్రయోజనాలు ఉన్నాయి. కస్టమ్ ప్లాస్టిక్ ఇంజెక్షన్ మౌల్డింగ్ని ఇతర తయారీ ప్రక్రియలతో పోల్చడం ఇక్కడ ఉంది:
- 3డి ప్రింటింగ్: 3డి ప్రింటింగ్ అనేది వేగంగా అభివృద్ధి చెందుతున్న సాంకేతికత, ఇది సంక్లిష్టమైన ఆకారాలు మరియు జ్యామితిలను రూపొందించడానికి అనుమతిస్తుంది. 3D ప్రింటింగ్ను చిన్న-స్థాయి ఉత్పత్తికి ఉపయోగించగలిగినప్పటికీ, పెద్ద భాగాలను ఉత్పత్తి చేయడానికి ఇంజెక్షన్ మోల్డింగ్ కంటే ఇంజెక్షన్ మోల్డింగ్ సాధారణంగా తక్కువ ఖర్చుతో కూడుకున్నది మరియు సమర్థవంతమైనది.
- బ్లో మోల్డింగ్: బ్లో మోల్డింగ్ అనేది సీసాలు మరియు కంటైనర్లు వంటి బోలు ప్లాస్టిక్ భాగాలను సృష్టించే తయారీ ప్రక్రియ. బ్లో మోల్డింగ్ అనేది అధిక వాల్యూమ్ల లక్షణాలను ఉత్పత్తి చేయడానికి అనుకూలంగా ఉంటుంది, ఇంజెక్షన్ మౌల్డింగ్ సాధారణంగా ఇంజెక్షన్ మౌల్డింగ్ కంటే తక్కువ ఖచ్చితమైనది మరియు మరింత సంక్లిష్టమైన ఆకారాలు మరియు జ్యామితిలను రూపొందించడానికి అనువైనది కాకపోవచ్చు.
- CNC మ్యాచింగ్: CNC మ్యాచింగ్ అనేది వ్యవకలన తయారీ ప్రక్రియ, ఇది మెటీరియల్ యొక్క ఘన బ్లాక్ నుండి భాగాలను కత్తిరించడం మరియు ఆకృతి చేయడం. తక్కువ పరిమాణంలో అధిక-ఖచ్చితమైన భాగాలను ఉత్పత్తి చేయడానికి CNC మ్యాచింగ్ అనుకూలంగా ఉంటుంది, ఇది సాధారణంగా ఇంజెక్షన్ మోల్డింగ్ వలె ఖర్చుతో కూడుకున్నది లేదా సమర్థవంతమైనది కాదు.
- భ్రమణ మౌల్డింగ్: రొటేషనల్ మోల్డింగ్ అనేది ఒక అచ్చును వేడి చేసేటప్పుడు రెండు లంబ అక్షాల చుట్టూ తిప్పడం వంటి తయారీ ప్రక్రియ. భ్రమణ మౌల్డింగ్ సంక్లిష్ట జ్యామితితో పెద్ద భాగాలను ఉత్పత్తి చేయగలదు, ఇంజెక్షన్ మౌల్డింగ్ సాధారణంగా ఇంజెక్షన్ మోల్డింగ్ కంటే తక్కువ ఖచ్చితమైనది మరియు చిన్న భాగాలను తయారు చేయడానికి తగినది కాదు.
- థర్మోఫార్మింగ్: థర్మోఫార్మింగ్ అనేది ప్లాస్టిక్ షీట్ను వేడి చేయడం మరియు దానిని అచ్చుపై ఆకృతి చేయడం వంటి తయారీ ప్రక్రియ. థర్మోఫార్మింగ్ సాధారణ జ్యామితితో పెద్ద భాగాలను ఉత్పత్తి చేయగలదు, ఇంజెక్షన్ మౌల్డింగ్ సాధారణంగా ఇంజెక్షన్ మోల్డింగ్ కంటే తక్కువ ఖచ్చితమైనది మరియు మరింత సంక్లిష్టమైన ఆకారాలు మరియు జ్యామితులను రూపొందించడానికి తగినది కాదు.
కస్టమ్ ప్లాస్టిక్ ఇంజెక్షన్ మోల్డింగ్ అనేది అధిక-నాణ్యత ప్లాస్టిక్ భాగాలను పెద్ద పరిమాణంలో ఉత్పత్తి చేయడానికి అత్యంత బహుముఖ మరియు ఖర్చుతో కూడుకున్న తయారీ ప్రక్రియ. ఇతర ఉత్పాదక ప్రక్రియలు నిర్దిష్ట అనువర్తనాలు లేదా ఉత్పత్తి వాల్యూమ్లకు బాగా సరిపోతాయి, ఇంజెక్షన్ మౌల్డింగ్ అనేది దాని వేగం, ఖచ్చితత్వం మరియు ఖర్చు-ప్రభావం కారణంగా చాలా మంది తయారీదారులకు సాధారణంగా ఇష్టపడే ఎంపిక. అంతిమంగా, తయారీ ప్రక్రియ ఎంపిక భాగం రూపకల్పన, ఉత్పత్తి పరిమాణం మరియు బడ్జెట్తో సహా వివిధ అంశాలపై ఆధారపడి ఉంటుంది.
అవుట్సోర్సింగ్ ఇంజెక్షన్ మౌల్డింగ్ యొక్క లాభాలు మరియు నష్టాలు
అవుట్సోర్సింగ్ ఇంజెక్షన్ మోల్డింగ్ అనేది తమ స్వంత ఇంజెక్షన్ మోల్డింగ్ పరికరాలు లేదా నైపుణ్యంలో పెట్టుబడి పెట్టకుండా ప్లాస్టిక్ భాగాలను ఉత్పత్తి చేయాలని చూస్తున్న కంపెనీలకు ఒక సాధారణ పద్ధతి. అవుట్సోర్సింగ్ అనేక ప్రయోజనాలను అందించగలిగినప్పటికీ, దీనికి కొన్ని సంభావ్య లోపాలు కూడా ఉన్నాయి. ఔట్సోర్సింగ్ ఇంజెక్షన్ మౌల్డింగ్ యొక్క కొన్ని లాభాలు మరియు నష్టాలు ఇక్కడ ఉన్నాయి:
ప్రోస్:
- ఖర్చు ఆదా: ఔట్సోర్సింగ్ ఇంజెక్షన్ మౌల్డింగ్ అనేది ఇంట్లో ఉత్పత్తి సౌకర్యాన్ని ఏర్పాటు చేయడం కంటే తరచుగా ఖర్చుతో కూడుకున్నది. ఖరీదైన పరికరాలు మరియు సిబ్బందిలో పెట్టుబడి పెట్టడాన్ని సమర్థించడానికి ఎక్కువ డబ్బు లేదా వాల్యూమ్ అవసరమయ్యే చిన్న మరియు మధ్య తరహా కంపెనీలకు ఇది ప్రత్యేకంగా వర్తిస్తుంది.
- నైపుణ్యం: ఇంజెక్షన్ మౌల్డింగ్ కంపెనీలు తయారీలో ప్రత్యేకత కలిగి ఉంటాయి మరియు భాగాలు అధిక-నాణ్యత ప్రమాణానికి ఉత్పత్తి చేయబడేలా చూసుకునే నైపుణ్యాన్ని కలిగి ఉంటాయి. ఇంజక్షన్ మోల్డింగ్ను అవుట్సోర్సింగ్ చేయడం ద్వారా, అనుభవజ్ఞులైన నిపుణుల నైపుణ్యం నుండి కంపెనీలు ప్రయోజనం పొందవచ్చు.
- కెపాసిటీ: ఇంజెక్షన్ మౌల్డింగ్ కంపెనీలు పెద్ద మొత్తంలో భాగాలను త్వరగా మరియు సమర్ధవంతంగా ఉత్పత్తి చేయగలవు. క్రమం తప్పకుండా పెద్ద మొత్తంలో ఫీచర్లను తయారు చేసే కంపెనీలకు ఇది ప్రత్యేకంగా ప్రయోజనకరంగా ఉంటుంది.
- ఫ్లెక్సిబిలిటీ: అవుట్సోర్సింగ్ ఇంజెక్షన్ మోల్డింగ్ కంపెనీలు తమ ఉత్పత్తి షెడ్యూల్లలో మరింత సరళంగా ఉండటానికి అనుమతిస్తుంది. పరికరాలు మరియు అచ్చులను మార్చడం మూలధన ఖర్చుల గురించి చింతించకుండా కంపెనీలు తమ ఉత్పత్తి వాల్యూమ్లను సర్దుబాటు చేయవచ్చు లేదా వివిధ భాగాలకు మారవచ్చు.
కాన్స్:
- కమ్యూనికేషన్: అవుట్సోర్సింగ్ ఇంజెక్షన్ మోల్డింగ్ కస్టమర్ మరియు కంపెనీ మధ్య కమ్యూనికేషన్ సవాళ్లను సృష్టించగలదు. అపార్థాలు లేదా కమ్యూనికేషన్లో జాప్యాలు ఉత్పత్తిలో పొరపాట్లు లేదా జాప్యాలకు దారితీస్తాయి.
- నాణ్యత నియంత్రణ: అవుట్సోర్సింగ్ ఇంజెక్షన్ మోల్డింగ్ అంటే అవసరమైన నాణ్యతా ప్రమాణాలకు భాగాలను ఉత్పత్తి చేయడానికి బయటి కంపెనీపై ఆధారపడటం. బయటి కంపెనీతో పని చేస్తున్నప్పుడు నాణ్యత నియంత్రణ సవాలుగా ఉంటుంది మరియు అవసరమైన స్పెసిఫికేషన్లకు అనుగుణంగా ఉండే లక్షణాలను స్వీకరించే ప్రమాదం ఎల్లప్పుడూ ఉంటుంది.
- డిపెండెన్స్: అవుట్సోర్సింగ్ ఇంజెక్షన్ మోల్డింగ్ అంటే బయటి ఉత్పత్తి సంస్థపై ఆధారపడి ఉంటుంది. ఇది సరఫరాదారు యొక్క విశ్వసనీయత, స్థిరత్వం మరియు డెలివరీ సమయాలకు సంబంధించి ప్రమాదాలను సృష్టించవచ్చు.
- మేధో సంపత్తి: అవుట్సోర్సింగ్ ఇంజెక్షన్ మౌల్డింగ్ మేధో సంపత్తిని రక్షించడానికి ప్రమాదాలను సృష్టించగలదు. కంపెనీలు తమ డిజైన్లు మరియు సాంకేతికతలను తగిన చట్టపరమైన చర్యల ద్వారా రక్షించబడుతున్నాయని నిర్ధారించుకోవాలి.
కస్టమ్ ప్లాస్టిక్ ఇంజెక్షన్ మౌల్డింగ్ కోసం భవిష్యత్తు అవకాశాలు
కస్టమ్ ప్లాస్టిక్ ఇంజెక్షన్ మౌల్డింగ్ అనేక దశాబ్దాలుగా నమ్మదగిన మరియు బహుముఖ తయారీ ప్రక్రియ. ఇటీవలి సంవత్సరాలలో, ఇంజెక్షన్ మౌల్డింగ్ యొక్క సామర్థ్యాలు మరియు సామర్థ్యాన్ని మెరుగుపరచడంలో సాంకేతికత మరియు మెటీరియల్లలో పురోగతి కొనసాగుతోంది. అనుకూల ప్లాస్టిక్ ఇంజెక్షన్ మౌల్డింగ్ కోసం ఇక్కడ కొన్ని భవిష్యత్తు అవకాశాలు ఉన్నాయి:
- పరిశ్రమ 4.0 సాంకేతికతలను స్వీకరించడం: కృత్రిమ మేధస్సు, మెషిన్ లెర్నింగ్ మరియు ఇంటర్నెట్ ఆఫ్ థింగ్స్ (IoT) వంటి పరిశ్రమ 4.0 సాంకేతికతల ఏకీకరణ ఆటోమేషన్ను పెంచుతుందని, నాణ్యత నియంత్రణను మెరుగుపరుస్తుందని మరియు ఇంజెక్షన్ మోల్డింగ్లో ఉత్పత్తి ప్రక్రియలను ఆప్టిమైజ్ చేస్తుందని భావిస్తున్నారు.
- బయోడిగ్రేడబుల్ మెటీరియల్స్ వాడకం పెరగడం: ఇంజెక్షన్ మౌల్డింగ్లో బయోడిగ్రేడబుల్ మెటీరియల్ల స్వీకరణను పర్యావరణ ఆందోళనలు నడిపిస్తాయి. బయోడిగ్రేడబుల్ పదార్థాలు సాంప్రదాయ ప్లాస్టిక్లకు స్థిరమైన ప్రత్యామ్నాయాన్ని అందిస్తాయి మరియు వ్యర్థాలు మరియు పర్యావరణ ప్రభావాన్ని తగ్గించడంలో సహాయపడతాయి.
- వైద్య పరికరాల తయారీకి పెరుగుతున్న డిమాండ్: వృద్ధాప్య జనాభా మరియు వైద్య సాంకేతికతలో పురోగతి కారణంగా వైద్య పరికరాల అవసరం పెరుగుతోంది. ఇంజెక్షన్ మౌల్డింగ్ అనేది దాని ఖచ్చితత్వం, వేగం మరియు ఖర్చు-ప్రభావం కారణంగా వైద్య పరికరాల కోసం ఒక ప్రసిద్ధ తయారీ ప్రక్రియ.
- 3D ప్రింటింగ్ సామర్థ్యాల విస్తరణ: 3D ప్రింటింగ్ టెక్నాలజీ అభివృద్ధి ఇంజెక్షన్ మౌల్డింగ్ని ఉపయోగించి గతంలో తయారు చేయడం సాధ్యంకాని సంక్లిష్టమైన మరియు క్లిష్టమైన భాగాల ఉత్పత్తిని ఎనేబుల్ చేసింది. అయినప్పటికీ, ఇంజెక్షన్ మౌల్డింగ్తో పోలిస్తే 3D ప్రింటింగ్ ఇప్పటికీ చాలా నెమ్మదిగా మరియు ఖరీదైనది, మరియు రెండు సాంకేతికతలు ఒకదానికొకటి భర్తీ కాకుండా ఒకదానికొకటి పూరకంగా కొనసాగుతాయి.
- బహుళ-మెటీరియల్ ఇంజెక్షన్ మౌల్డింగ్ను పెంచడం: మల్టీ-మెటీరియల్ ఇంజెక్షన్ మోల్డింగ్లో ఒకే ఇంజెక్షన్ అచ్చు ప్రక్రియలో రెండు లేదా అంతకంటే ఎక్కువ విభిన్న పదార్థాలను ఉపయోగించడం ఉంటుంది. ఈ సాంకేతికత మెరుగైన పార్ట్ పనితీరు, తగ్గిన బరువు మరియు ఖర్చు ఆదాతో సహా అనేక ప్రయోజనాలను అందిస్తుంది.
- టూలింగ్ టెక్నాలజీలో పురోగతులు: కొత్త టూలింగ్ మెటీరియల్స్ మరియు డిజైన్ల అభివృద్ధి ఇంజెక్షన్ మోల్డింగ్ యొక్క వేగం, సామర్థ్యం మరియు ఖచ్చితత్వాన్ని పెంచుతుందని భావిస్తున్నారు. ఉదాహరణకు, టూలింగ్లోని కన్ఫార్మల్ కూలింగ్ ఛానెల్లు చక్రాల సమయాన్ని మెరుగుపరుస్తాయి మరియు శక్తి వినియోగాన్ని తగ్గిస్తాయి.
ముగింపు:
కస్టమ్ ప్లాస్టిక్ ఇంజెక్షన్ మౌల్డింగ్ అనేది ఒక బలమైన తయారీ ప్రక్రియ, ఇది గొప్ప ఖచ్చితత్వం మరియు సామర్థ్యంతో అధిక-నాణ్యత ప్లాస్టిక్ భాగాల ఉత్పత్తిని అనుమతిస్తుంది. ఇంజెక్షన్ మోల్డింగ్ ప్రక్రియను అర్థం చేసుకోవడం ద్వారా, తగిన పదార్థాలు మరియు అచ్చు డిజైన్లను ఎంచుకోవడం మరియు నాణ్యత నియంత్రణ మరియు పరికరాల నిర్వహణ కోసం ఉత్తమ పద్ధతులను అమలు చేయడం ద్వారా, వ్యాపారాలు వారి ఇంజెక్షన్ మోల్డింగ్ కార్యకలాపాలను ఆప్టిమైజ్ చేయగలవు మరియు అద్భుతమైన విజయాన్ని సాధించగలవు. పరిశ్రమలో కొత్త పోకడలు మరియు ఆవిష్కరణలు ఉద్భవించినందున, కస్టమ్ ప్లాస్టిక్ ఇంజెక్షన్ మోల్డింగ్ యొక్క స్థిరత్వం, సామర్థ్యం మరియు లాభదాయకతను మెరుగుపరచడానికి తాజాగా ఉండటం మరియు కొత్త అవకాశాలను అన్వేషించడం చాలా అవసరం.