థర్మోప్లాస్టిక్ ఇంజెక్షన్ మౌల్డింగ్
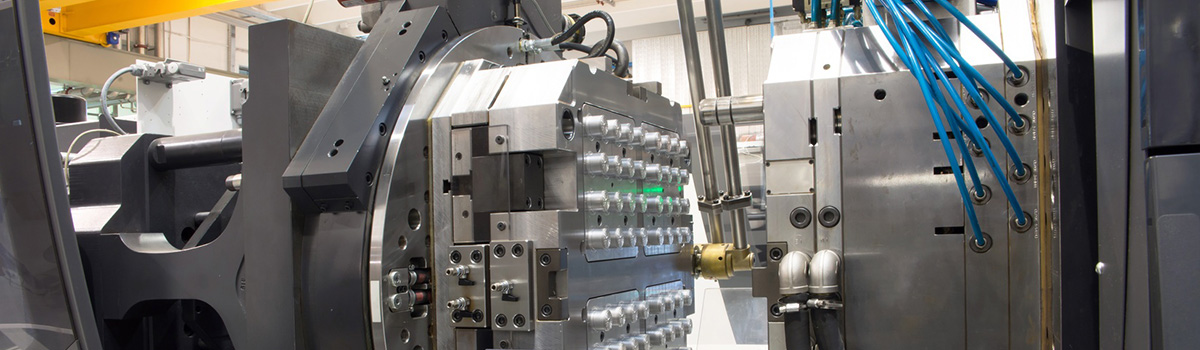
థర్మోప్లాస్టిక్ ఇంజెక్షన్ మోల్డింగ్ అనేది బహుళ పరిశ్రమల కోసం వివిధ ప్లాస్టిక్ భాగాలను రూపొందించడానికి ఉపయోగించే ఒక ప్రముఖ తయారీ ప్రక్రియ. ఈ ప్రక్రియలో ప్లాస్టిక్ గుళికలను కరిగించి, త్రిమితీయ ఆకారాన్ని ఉత్పత్తి చేయడానికి వాటిని అచ్చులోకి ఇంజెక్ట్ చేస్తారు. థర్మోప్లాస్టిక్ ఇంజెక్షన్ మౌల్డింగ్ గట్టి సహనంతో అధిక నాణ్యత కలిగిన ప్లాస్టిక్ భాగాలను పెద్ద పరిమాణంలో ఉత్పత్తి చేయడానికి అత్యంత సమర్థవంతమైనది మరియు ఖర్చుతో కూడుకున్నది. ఈ సమగ్ర గైడ్ థర్మోప్లాస్టిక్ ఇంజెక్షన్ మౌల్డింగ్లోని వివిధ అంశాలను దాని ప్రయోజనాలు మరియు అప్రయోజనాలు, ఉపయోగించిన థర్మోప్లాస్టిక్ల రకాలు, ఇంజెక్షన్ మోల్డింగ్ ప్రక్రియ, డిజైన్ పరిగణనలు మరియు మరెన్నో సహా అనేక అంశాలను అన్వేషిస్తుంది.
థర్మోప్లాస్టిక్ ఇంజెక్షన్ మౌల్డింగ్ చరిత్ర
థర్మోప్లాస్టిక్ ఇంజెక్షన్ మౌల్డింగ్ చరిత్ర ఒక శతాబ్దానికి పైగా సాంకేతిక పురోగతులు, వస్తు పరిణామాలు మరియు పారిశ్రామిక అనువర్తనాలను విస్తరించింది. సెల్యులాయిడ్ మౌల్డింగ్ ప్రక్రియగా దాని వినయపూర్వకమైన ప్రారంభం నుండి నేటి అధునాతన సాంకేతికత వరకు, ఇంజెక్షన్ మౌల్డింగ్ అనేది ఒక ముఖ్యమైన తయారీ సాంకేతికతగా కొనసాగుతోంది, ఆవిష్కరణలను నడిపించడం మరియు వివిధ పరిశ్రమలను రూపొందించడం.
- ప్రారంభ అభివృద్ధి:జాన్ వెస్లీ హయాట్ మరియు అతని సోదరుడు యెషయా 19వ శతాబ్దం చివరిలో థర్మోప్లాస్టిక్ ఇంజెక్షన్ మౌల్డింగ్ యొక్క మూలాలను గుర్తించడం ద్వారా మొదటి ఆచరణాత్మక ఇంజెక్షన్ మౌల్డింగ్ యంత్రాన్ని అభివృద్ధి చేశారు. 1872లో, వారు సెల్యులాయిడ్ను అచ్చు కుహరంలోకి చొప్పించి, ఘన వస్తువులను సృష్టించేందుకు ప్లంగర్ను ఉపయోగించే పరికరానికి పేటెంట్ ఇచ్చారు. ఈ పురోగతి ఆధునిక ఇంజెక్షన్ మౌల్డింగ్ ప్రక్రియకు పునాది వేసింది.
- మెటీరియల్స్లో పురోగతి:20వ శతాబ్దం ప్రారంభంలో, కొత్త సింథటిక్ పాలిమర్లను ప్రవేశపెట్టడం ఇంజక్షన్ మోల్డింగ్కు కొత్త అవకాశాలను తెరిచింది. బేకలైట్, ఒక ఫినాలిక్ రెసిన్, దాని అద్భుతమైన ఎలక్ట్రికల్ ఇన్సులేటింగ్ లక్షణాల కారణంగా మౌల్డింగ్ కోసం ఒక ప్రసిద్ధ పదార్థంగా మారింది. 1930లు మరియు 1940లలో, పాలిమర్ కెమిస్ట్రీలో పురోగతి పాలీస్టైరిన్ మరియు పాలిథిలిన్ వంటి ఇతర థర్మోప్లాస్టిక్ల అభివృద్ధికి దారితీసింది, ఇది ఇంజెక్షన్ మౌల్డింగ్కు అనువైన పదార్థాల పరిధిని మరింత విస్తరించింది.
- పారిశ్రామిక దత్తత: థర్మోప్లాస్టిక్ ఇంజెక్షన్ మౌల్డింగ్ యొక్క విస్తృత స్వీకరణ 1950లలో ప్రారంభమైంది, ఎందుకంటే తయారీదారులు దాని ఖర్చు-ప్రభావం మరియు బహుముఖ ప్రజ్ఞను గుర్తించారు. అధిక పీడన యంత్రాలను పరిచయం చేయడం వలన వేగవంతమైన చక్రాల సమయాలు మరియు ఉత్పత్తి వాల్యూమ్లు పెరిగాయి. తత్ఫలితంగా, వ్యక్తిగత మరియు పారిశ్రామిక ఉపయోగం కోసం ఉత్పత్తుల యొక్క విభిన్న ఎంపిక ఉనికిలోకి వచ్చింది. వీటిలో కారు భాగాలు, గృహోపకరణాలు మరియు ఆట వస్తువులు ఉన్నాయి.
- సాంకేతిక ఆవిష్కరణలు:దశాబ్దాలుగా, ఇంజెక్షన్ మోల్డింగ్ టెక్నాలజీ అభివృద్ధి చెందుతూనే ఉంది. 1960వ దశకంలో, కంప్యూటర్-నియంత్రిత యంత్రాలు ఉద్భవించాయి, అచ్చు ప్రక్రియపై ఖచ్చితమైన నియంత్రణను అందించాయి. 1980లలో హాట్ రన్నర్ సిస్టమ్ల పరిచయం వ్యర్థాలను తగ్గించింది మరియు రన్నర్లు మరియు స్ప్రూల అవసరాన్ని తొలగించడం ద్వారా సామర్థ్యాన్ని మెరుగుపరిచింది. ఇటీవలి సంవత్సరాలలో, ఆటోమేషన్, రోబోటిక్స్ మరియు 3D ప్రింటింగ్ పురోగతులు ఇంజెక్షన్ మోల్డింగ్ పరిశ్రమలో మరింత విప్లవాత్మక మార్పులు చేసాయి, సంక్లిష్టమైన డిజైన్లను ప్రారంభించడం మరియు ఉత్పత్తి సమయాన్ని తగ్గించడం.
- స్థిరత్వం మరియు రీసైక్లింగ్:పెరుగుతున్న పర్యావరణ ఆందోళనలతో, ఇంజెక్షన్ మోల్డింగ్ పరిశ్రమ స్థిరత్వ చర్యలను స్వీకరించింది. తయారీదారులు జీవ-ఆధారిత మరియు రీసైకిల్ థర్మోప్లాస్టిక్లను అభివృద్ధి చేశారు, శిలాజ ఇంధన-ఆధారిత పదార్థాలపై ఆధారపడటాన్ని తగ్గించారు. అదనంగా, మెరుగైన రీసైక్లింగ్ సాంకేతికతలు థర్మోప్లాస్టిక్ ఇంజెక్షన్ మౌల్డింగ్ యొక్క పర్యావరణ ప్రభావాన్ని తగ్గించడం ద్వారా పోస్ట్-కన్స్యూమర్ మరియు పోస్ట్-ఇండస్ట్రియల్ వ్యర్థాలను తిరిగి ప్రాసెస్ చేయడం ప్రారంభించాయి.
- భవిష్యత్ అవకాశాలు:థర్మోప్లాస్టిక్ ఇంజెక్షన్ మౌల్డింగ్ యొక్క భవిష్యత్తు ఆశాజనకంగా ఉంది. పరిశ్రమ సూక్ష్మ భాగాల కోసం మైక్రో-ఇంజెక్షన్ మౌల్డింగ్, సంక్లిష్ట భాగాల కోసం మల్టీ-మెటీరియల్ మరియు ఓవర్మోల్డింగ్ టెక్నిక్లు మరియు ప్రాసెస్ మానిటరింగ్ మరియు ఆప్టిమైజేషన్ కోసం ఇంటెలిజెంట్ టెక్నాలజీలను సమగ్రపరచడం వంటి ఆవిష్కరణలను అన్వేషిస్తోంది. ఇంకా, పరిశోధకులు బయోడిగ్రేడబుల్ మెటీరియల్స్ మరియు సంకలిత తయారీలో పురోగతిని ఈ రంగంలో విప్లవాత్మకంగా మార్చాలని భావిస్తున్నారు, ఇంజెక్షన్ మౌల్డింగ్ను మరింత స్థిరంగా మరియు బహుముఖంగా చేస్తుంది.
థర్మోప్లాస్టిక్ ఇంజెక్షన్ మోల్డింగ్ యొక్క ప్రయోజనాలు
థర్మోప్లాస్టిక్ ఇంజెక్షన్ మౌల్డింగ్ తయారీదారులకు అనేక ప్రయోజనాలను అందిస్తుంది. ఇది డిజైన్ సౌలభ్యాన్ని అందిస్తుంది, వివిధ లక్షణాలతో సంక్లిష్టమైన మరియు క్లిష్టమైన డిజైన్లను అనుమతిస్తుంది. ఈ ప్రక్రియ ఖర్చుతో కూడుకున్నది, పదార్థం వ్యర్థాలను తగ్గించడం మరియు యూనిట్ ఖర్చులను తగ్గించడం. థర్మోప్లాస్టిక్ ఇంజెక్షన్ మౌల్డింగ్ బహుళ పదార్థాలకు మద్దతు ఇస్తుంది, వివిధ అనువర్తనాలకు బహుముఖ ప్రజ్ఞను అందిస్తుంది.
- డిజైన్ ఫ్లెక్సిబిలిటీ:థర్మోప్లాస్టిక్ ఇంజెక్షన్ మోల్డింగ్ అండర్కట్లు, సన్నని గోడలు మరియు వివిధ మందం వంటి లక్షణాలతో క్లిష్టమైన మరియు సంక్లిష్టమైన డిజైన్లను అనుమతిస్తుంది, డిజైనర్లకు అపారమైన స్వేచ్ఛను అందిస్తుంది.
- వ్యయ సామర్థ్యం: ప్రక్రియ అత్యంత ప్రభావవంతంగా ఉంటుంది, పదార్థ వ్యర్థాలను తగ్గిస్తుంది మరియు యూనిట్ ఖర్చులను తగ్గిస్తుంది. బహుళ భాగాల ఏకకాల అచ్చు మరియు వేగవంతమైన ఉత్పత్తి చక్రాలు ఖర్చు ఆదాకు దోహదం చేస్తాయి.
- మెటీరియల్ బహుముఖ ప్రజ్ఞ: థర్మోప్లాస్టిక్ ఇంజెక్షన్ మౌల్డింగ్ విస్తృత శ్రేణి పదార్థాలకు మద్దతు ఇస్తుంది, తయారీదారులు దృఢమైన లేదా సౌకర్యవంతమైన, పారదర్శక లేదా అపారదర్శక మరియు రసాయనికంగా నిరోధక పదార్థాలతో సహా ప్రతి అప్లికేషన్కు అత్యంత అనుకూలమైన ఎంపికను ఎంచుకోవడానికి వీలు కల్పిస్తుంది.
- బలం మరియు మన్నిక:ఇంజెక్షన్-మోల్డ్ థర్మోప్లాస్టిక్లు అధిక బలం, మొండితనం మరియు ప్రభావ నిరోధకత వంటి అద్భుతమైన యాంత్రిక లక్షణాలను ప్రదర్శిస్తాయి. గాజు లేదా కార్బన్ ఫైబర్ల వంటి ఉపబల ఎంపికలు ఈ లక్షణాలను మరింత మెరుగుపరుస్తాయి.
- స్థిరత్వం మరియు నాణ్యత:ఇంజెక్షన్ మౌల్డింగ్ స్థిరమైన పార్ట్-టు-పార్ట్ నాణ్యత మరియు డైమెన్షనల్ ఖచ్చితత్వాన్ని నిర్ధారిస్తుంది, గట్టి సహనం మరియు విశ్వసనీయ ఉత్పత్తులను అందిస్తుంది. ఈ ప్రక్రియ మృదువైన మరియు ఏకరీతి ఉపరితల ముగింపును అందిస్తుంది, అదనపు ముగింపు కార్యకలాపాల అవసరాన్ని తొలగిస్తుంది.
- స్కేలబిలిటీ మరియు మాస్ ప్రొడక్షన్:ఇంజెక్షన్ మౌల్డింగ్ తక్కువ నుండి అధిక వాల్యూమ్ల వరకు స్కేలబుల్, ఇది భారీ ఉత్పత్తికి అనుకూలంగా ఉంటుంది. తయారీదారులు అచ్చును సృష్టించిన తర్వాత, వారు కనిష్ట వైవిధ్యాలతో పెద్ద మొత్తంలో ఒకేలాంటి భాగాలను ఉత్పత్తి చేయవచ్చు.
- ఇంటిగ్రేషన్ మరియు అసెంబ్లీ:ఇంజెక్షన్-అచ్చు భాగాలు బహుళ భాగాలను ఒక ముక్కగా చేర్చగలవు, అదనపు అసెంబ్లీ ప్రక్రియల అవసరాన్ని తగ్గిస్తాయి. ఈ ఏకీకరణ ఉత్పత్తి పనితీరును మెరుగుపరుస్తుంది, అసెంబ్లీ సమయాన్ని తగ్గిస్తుంది మరియు ఖర్చులను తగ్గిస్తుంది.
- స్థిరత్వం:ఇంజెక్షన్ మోల్డింగ్ పరిశ్రమ స్థిరత్వంపై పెరుగుతున్న దృష్టిని చూపుతోంది. జీవ ఆధారిత మరియు రీసైకిల్ పదార్థాల లభ్యత పర్యావరణ అనుకూల ఉత్పత్తులను ఉత్పత్తి చేయడానికి అనుమతిస్తుంది. థర్మోప్లాస్టిక్స్ యొక్క సమర్ధవంతమైన పదార్థ వినియోగం మరియు పునర్వినియోగం అనేది పచ్చని తయారీ ప్రక్రియకు దోహదం చేస్తుంది.
ఈ ప్రయోజనాలు సంక్లిష్ట ఉత్పత్తి అవసరాల కోసం అధిక-నాణ్యత, తక్కువ ఖర్చుతో కూడిన మరియు పర్యావరణ అనుకూల పరిష్కారాలను అందించడం ద్వారా వివిధ పరిశ్రమలలో విస్తృతంగా స్వీకరించబడిన తయారీ పద్ధతిగా మార్చాయి.
థర్మోప్లాస్టిక్ ఇంజెక్షన్ మోల్డింగ్ యొక్క ప్రతికూలతలు
థర్మోప్లాస్టిక్ ఇంజెక్షన్ మౌల్డింగ్ అనేక ప్రయోజనాలను అందించినప్పటికీ, అనేక ప్రతికూలతలు కూడా ఉన్నాయి. తయారీదారులు ఈ కారకాలను జాగ్రత్తగా అంచనా వేయాలి మరియు వారి నిర్దిష్ట అనువర్తనాల కోసం థర్మోప్లాస్టిక్ ఇంజెక్షన్ మౌల్డింగ్ యొక్క అనుకూలతను నిర్ణయించడానికి ప్రయోజనాలతో వాటిని తూకం వేయాలి.
- అధిక ప్రారంభ పెట్టుబడి: థర్మోప్లాస్టిక్ ఇంజెక్షన్ మోల్డింగ్ ఆపరేషన్ను సెటప్ చేయడానికి అచ్చు రూపకల్పన మరియు కల్పన మరియు ప్రత్యేక యంత్రాలను కొనుగోలు చేయడంలో గణనీయమైన ప్రారంభ పెట్టుబడి అవసరం. అచ్చులను మరియు సాధనాలను రూపొందించడానికి సంబంధించిన ఖర్చులు గణనీయంగా ఉంటాయి, ముఖ్యంగా సంక్లిష్టమైన మరియు క్లిష్టమైన డిజైన్ల కోసం.
- డిజైన్ పరిమితులు: థర్మోప్లాస్టిక్ ఇంజెక్షన్ మోల్డింగ్ డిజైన్ సౌలభ్యాన్ని అందిస్తుంది, కొన్ని పరిమితులు ఉన్నాయి. ఉదాహరణకు, భాగం అంతటా ఏకరీతి గోడ మందాన్ని సాధించడం సవాలుగా ఉంటుంది, ఇది మెటీరియల్ పంపిణీలో వైవిధ్యాలు మరియు సంభావ్య నిర్మాణ బలహీనతలకు దారితీస్తుంది. అదనంగా, అండర్కట్లు లేదా సంక్లిష్ట జ్యామితి ఉనికికి అదనపు అచ్చు లక్షణాలు లేదా ద్వితీయ కార్యకలాపాలను ఉపయోగించడం, ఖర్చులు మరియు ఉత్పత్తి సమయాన్ని పెంచడం అవసరం కావచ్చు.
- లాంగ్ లీడ్ టైమ్స్:ఇంజెక్షన్ మోల్డింగ్ కోసం అచ్చులను రూపొందించడం మరియు రూపొందించడం ప్రక్రియ చాలా సమయం తీసుకుంటుంది, ఇది ఉత్పత్తి అభివృద్ధికి ఎక్కువ సమయం పడుతుంది. డిజైన్ పునరుక్తి ప్రక్రియ, అచ్చు ఉత్పత్తి మరియు పరీక్ష మొత్తం ఉత్పత్తి కాలక్రమానికి గణనీయమైన సమయాన్ని జోడించగలవు, ఇది కఠినమైన గడువులతో ప్రాజెక్ట్లకు తగినది కాదు.
- మెటీరియల్ ఎంపిక పరిమితులు:థర్మోప్లాస్టిక్ ఇంజెక్షన్ మౌల్డింగ్ విస్తృత శ్రేణి పదార్థాలకు మద్దతు ఇస్తున్నప్పటికీ, కొన్ని పరిమితులు మరియు పరిమితులు ఉన్నాయి. కొన్ని మెటీరియల్స్ నిర్దిష్ట ప్రాసెసింగ్ అవసరాలు లేదా పరిమిత లభ్యతను కలిగి ఉండవచ్చు, నిర్దిష్ట అప్లికేషన్ కోసం డిజైన్ ఎంపికలు మరియు మెటీరియల్ ఎంపికపై ప్రభావం చూపుతాయి.
- పార్ట్ సైజు పరిమితులు:ఇంజెక్షన్ మౌల్డింగ్ మెషీన్లు పరికరం యొక్క భౌతిక పరిమాణం మరియు అవి అమర్చగలిగే అచ్చుల పరిమాణం రెండింటిలోనూ పరిమాణ పరిమితులను కలిగి ఉంటాయి. భారీ భాగాలను ఉత్పత్తి చేయడానికి ప్రత్యేక పరికరాలు లేదా ప్రత్యామ్నాయ తయారీ పద్ధతులు అవసరం కావచ్చు.
- పర్యావరణ ప్రభావం:పరిశ్రమ స్థిరత్వం కోసం పని చేస్తున్నప్పుడు, థర్మోప్లాస్టిక్ ఇంజెక్షన్ మోల్డింగ్ ప్రక్రియ ఇప్పటికీ స్క్రాప్ మరియు స్ప్రూస్తో సహా వ్యర్థ పదార్థాలను ఉత్పత్తి చేస్తుంది. పర్యావరణ ప్రభావాన్ని తగ్గించడానికి ఈ పదార్థాల సరైన పారవేయడం మరియు రీసైక్లింగ్ అవసరం.
- ప్రాసెస్ ఆప్టిమైజేషన్ సంక్లిష్టత:థర్మోప్లాస్టిక్ ఇంజెక్షన్ మోల్డింగ్ కోసం సరైన ప్రక్రియ పారామితులను సాధించడం సంక్లిష్టమైనది మరియు సమయం తీసుకుంటుంది. స్థిరమైన భాగం నాణ్యతను నిర్ధారించడానికి మరియు లోపాలను తగ్గించడానికి తయారీదారులు ఉష్ణోగ్రత, పీడనం, శీతలీకరణ రేట్లు మరియు చక్రాల సమయాలను జాగ్రత్తగా నియంత్రించాలి మరియు ఆప్టిమైజ్ చేయాలి.
ఇంజెక్షన్ మోల్డింగ్లో ఉపయోగించే థర్మోప్లాస్టిక్ల రకాలు
ఇంజెక్షన్ మౌల్డింగ్లో సాధారణంగా ఉపయోగించే థర్మోప్లాస్టిక్లకు ఇవి కొన్ని ఉదాహరణలు. ప్రతి పదార్థం ప్రత్యేక లక్షణాలను కలిగి ఉంటుంది, ఇది బలం, వశ్యత, రసాయన నిరోధకత, పారదర్శకత మరియు ధర ఆధారంగా నిర్దిష్ట అనువర్తనాలకు అనుకూలంగా ఉంటుంది. తయారీదారులు తమ ఇంజెక్షన్ మోల్డింగ్ ప్రాజెక్ట్ల కోసం తగిన థర్మోప్లాస్టిక్ను ఎంచుకున్నప్పుడు ఈ లక్షణాలను మరియు అవసరాలను పరిగణనలోకి తీసుకోవాలి.
- పాలీప్రొఫైలిన్ (PP):పాలీప్రొఫైలిన్ అనేది ఇంజెక్షన్ మౌల్డింగ్లో సాధారణంగా ఉపయోగించే బహుముఖ థర్మోప్లాస్టిక్. ఇది అద్భుతమైన రసాయన నిరోధకత, తక్కువ సాంద్రత మరియు మంచి ప్రభావ బలాన్ని అందిస్తుంది. PP (పాలీప్రొఫైలిన్) ప్యాకేజింగ్, ఆటోమోటివ్ భాగాలు, గృహోపకరణాలు మరియు వైద్య పరికరాలలో విస్తృత-శ్రేణి అనువర్తనాలను కలిగి ఉంది.
- పాలిథిలిన్ (PE):పాలిథిలిన్ ఇంజక్షన్ మౌల్డింగ్లో విస్తృతంగా ఉపయోగించే మరొక థర్మోప్లాస్టిక్. ఇది అధిక సాంద్రత కలిగిన పాలిథిలిన్ (HDPE) మరియు తక్కువ సాంద్రత కలిగిన పాలిథిలిన్ (LDPE) వంటి వివిధ రూపాల్లో లభ్యమవుతుంది. PE మంచి రసాయన నిరోధకత, దృఢత్వం మరియు వశ్యతను అందిస్తుంది, ఇది సీసాలు, కంటైనర్లు మరియు పైపులకు అనుకూలంగా ఉంటుంది.
- పాలీస్టైరిన్ (PS):పాలీస్టైరిన్ అనేది ఒక బహుముఖ థర్మోప్లాస్టిక్ దాని స్పష్టత, దృఢత్వం మరియు స్థోమత కోసం ప్రసిద్ధి చెందింది. ఇది ప్యాకేజింగ్, వినియోగ వస్తువులు మరియు పునర్వినియోగపరచలేని ఉత్పత్తులలో సాధారణ వినియోగాన్ని కనుగొంటుంది. PS (పాలీస్టైరిన్) శీఘ్ర ప్రాసెసింగ్ కోసం అనుమతిస్తుంది మరియు మంచి డైమెన్షనల్ స్టెబిలిటీని అందిస్తుంది, అయితే ఇది పెళుసుగా మరియు పర్యావరణ ఒత్తిడి పగుళ్లకు గురవుతుంది.
- యాక్రిలోనిట్రైల్ బుటాడిన్ స్టైరీన్ (ABS): ABS అనేది దాని అద్భుతమైన ప్రభావ నిరోధకత మరియు మన్నికకు ప్రసిద్ధి చెందిన ఒక ప్రసిద్ధ థర్మోప్లాస్టిక్. ఇది ఆటోమోటివ్ భాగాలు, ఎలక్ట్రానిక్ హౌసింగ్లు మరియు బొమ్మలకు అనువైన బహుముఖ పదార్థాన్ని రూపొందించడానికి యాక్రిలోనిట్రైల్, బ్యూటాడిన్ మరియు స్టైరీన్ యొక్క లక్షణాలను మిళితం చేస్తుంది.
- పాలీ వినైల్ క్లోరైడ్ (PVC): PVC అనేది దాని అద్భుతమైన రసాయన నిరోధకత, మన్నిక మరియు తక్కువ ధరకు ప్రసిద్ధి చెందిన విస్తృతంగా ఉపయోగించే థర్మోప్లాస్టిక్. ఉపయోగించిన సూత్రీకరణ మరియు సంకలితాలను బట్టి ఇది దృఢంగా లేదా అనువైనదిగా ఉంటుంది. PVC (పాలీ వినైల్ క్లోరైడ్) నిర్మాణం, విద్యుత్ ఇన్సులేషన్, ఆరోగ్య సంరక్షణ ఉత్పత్తులు మరియు ప్యాకేజింగ్లో సాధారణ వినియోగాన్ని కనుగొంటుంది.
- పాలికార్బోనేట్ (PC): పాలీకార్బోనేట్ అనేది అసాధారణ ప్రభావం మరియు అధిక ఉష్ణ నిరోధకత కలిగిన పారదర్శక థర్మోప్లాస్టిక్. ఇది ఆటోమోటివ్ కాంపోనెంట్లు, సేఫ్టీ హెల్మెట్లు మరియు ఎలక్ట్రానిక్ డిస్ప్లేలు వంటి ఆప్టికల్ క్లారిటీ అవసరమయ్యే అప్లికేషన్లలో సాధారణ వినియోగాన్ని కనుగొంటుంది.
- నైలాన్ (పాలిమైడ్):నైలాన్ దాని అద్భుతమైన యాంత్రిక లక్షణాలు మరియు రసాయన నిరోధకతకు ప్రసిద్ధి చెందిన బలమైన మరియు మన్నికైన థర్మోప్లాస్టిక్. ఇది ఆటోమోటివ్ భాగాలు, పారిశ్రామిక భాగాలు మరియు వినియోగ వస్తువులు వంటి అధిక బలం డిమాండ్ చేసే అప్లికేషన్లలో సాధారణ వినియోగాన్ని కనుగొంటుంది.
- పాలిథిలిన్ టెరెఫ్తాలేట్ (PET):PET అనేది సీసాలు, కంటైనర్లు మరియు ప్యాకేజింగ్ పదార్థాలను ఉత్పత్తి చేయడానికి ఒక ప్రసిద్ధ థర్మోప్లాస్టిక్. ఇది మంచి స్పష్టత, రసాయన నిరోధకత మరియు అవరోధ లక్షణాలను అందిస్తుంది, ఇది ఆహారం మరియు పానీయాల అనువర్తనాలకు అనుకూలంగా ఉంటుంది.
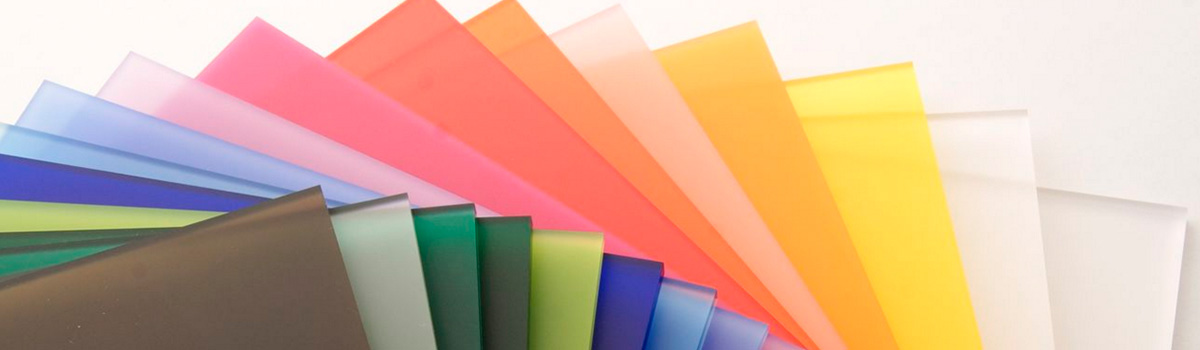
ఇంజెక్షన్ మోల్డింగ్లో ఉపయోగించే థర్మోప్లాస్టిక్ల లక్షణాలు
థర్మోప్లాస్టిక్స్ యొక్క ఈ లక్షణాలు నిర్దిష్ట ఇంజెక్షన్ మౌల్డింగ్ అప్లికేషన్లకు వాటి అనుకూలతను నిర్ణయించడంలో కీలక పాత్ర పోషిస్తాయి. తయారీదారులు ఈ లక్షణాలను జాగ్రత్తగా పరిశీలించాలి మరియు కావలసిన పనితీరు, పర్యావరణ పరిస్థితులు మరియు ఖర్చు అవసరాల ఆధారంగా తగిన థర్మోప్లాస్టిక్ను ఎంచుకోవాలి.
- యాంత్రిక లక్షణాలు:ఇంజెక్షన్ మౌల్డింగ్లో ఉపయోగించే థర్మోప్లాస్టిక్లు తన్యత బలం, ప్రభావ నిరోధకత మరియు ఫ్లెక్చరల్ బలంతో సహా వివిధ యాంత్రిక లక్షణాలను ప్రదర్శిస్తాయి. ఈ లక్షణాలు వివిధ అనువర్తనాల్లో అనువర్తిత శక్తులను మరియు దాని మొత్తం మన్నికను తట్టుకునే పదార్థం యొక్క సామర్థ్యాన్ని నిర్ణయిస్తాయి.
- రసాయన నిరోధకత:ఇంజెక్షన్ మౌల్డింగ్లో ఉపయోగించే అనేక థర్మోప్లాస్టిక్లు రసాయనాలు, ద్రావకాలు మరియు నూనెలకు అద్భుతమైన ప్రతిఘటనను కలిగి ఉంటాయి. కఠినమైన వాతావరణాలు లేదా తినివేయు పదార్థాలకు గురికావడం వంటి అనువర్తనాలకు ఈ ఆస్తి కీలకం.
- ఉష్ణ స్థిరత్వం:థర్మోప్లాస్టిక్స్ యొక్క ఉష్ణ స్థిరత్వం గణనీయమైన క్షీణత లేకుండా అధిక ఉష్ణోగ్రతలను తట్టుకోగల సామర్థ్యాన్ని సూచిస్తుంది. కొన్ని థర్మోప్లాస్టిక్లు అద్భుతమైన ఉష్ణ నిరోధకతను ప్రదర్శిస్తాయి, అధిక ఉష్ణోగ్రతల వద్ద కూడా వాటి యాంత్రిక లక్షణాలను నిర్వహించడానికి వీలు కల్పిస్తుంది.
- ఎలక్ట్రికల్ ప్రాపర్టీస్:ఇంజెక్షన్ మౌల్డింగ్లో ఉపయోగించే థర్మోప్లాస్టిక్లు విద్యుత్ ఇన్సులేషన్, వాహకత లేదా విద్యుద్వాహక బలంతో సహా నిర్దిష్ట విద్యుత్ లక్షణాలను కలిగి ఉంటాయి. ఈ లక్షణాలు ఎలక్ట్రికల్ మరియు ఎలక్ట్రానిక్ పరిశ్రమలలో అనువర్తనాలకు అవసరం, ఇక్కడ పదార్థాలు విశ్వసనీయమైన విద్యుత్ పనితీరును అందించాలి.
- పారదర్శకత మరియు స్పష్టత:పాలికార్బోనేట్ మరియు PET వంటి కొన్ని థర్మోప్లాస్టిక్లు అద్భుతమైన పారదర్శకత మరియు స్పష్టతను అందిస్తాయి, ఇవి ఆప్టికల్ లక్షణాలు అవసరమయ్యే అప్లికేషన్లకు అనుకూలంగా ఉంటాయి. తయారీదారులు సాధారణంగా ఈ పదార్థాలను పారదర్శక కిటికీలు, లెన్సులు మరియు డిస్ప్లేలు వంటి ఉత్పత్తులలో ఉపయోగిస్తారు.
- వశ్యత మరియు దృఢత్వం: ఫ్లెక్సిబిలిటీ మరియు మొండితనం అనేది ప్రభావ నిరోధకత మరియు మన్నిక అవసరమయ్యే అప్లికేషన్లలో ఉపయోగించే థర్మోప్లాస్టిక్స్ యొక్క ముఖ్యమైన లక్షణాలు. ABS మరియు నైలాన్ వంటి కొన్ని థర్మోప్లాస్టిక్లు అద్భుతమైన దృఢత్వాన్ని అందిస్తాయి, అవి పగలకుండా పదే పదే ప్రభావాలను తట్టుకోగలవు.
- డైమెన్షనల్ స్థిరత్వం:డైమెన్షనల్ స్టెబిలిటీ అనేది ఉష్ణోగ్రత మార్పులతో సహా వివిధ పరిస్థితులలో దాని ఆకారాన్ని మరియు పరిమాణాన్ని నిర్వహించడానికి థర్మోప్లాస్టిక్ సామర్థ్యాన్ని సూచిస్తుంది. మంచి డైమెన్షనల్ స్టెబిలిటీ ఉన్న మెటీరియల్స్ స్థిరమైన పార్ట్ డైమెన్షన్లను నిర్ధారిస్తాయి, వార్పింగ్ లేదా వక్రీకరణ ప్రమాదాన్ని తగ్గిస్తుంది.
- రసాయన అనుకూలత:థర్మోప్లాస్టిక్స్ యొక్క రసాయన అనుకూలత అనేది ఆమ్లాలు, స్థావరాలు మరియు ద్రావకాలతో సహా వివిధ రసాయనాలతో అధోకరణం లేదా పరస్పర చర్యను నిరోధించే సామర్థ్యాన్ని సూచిస్తుంది. సరైన పనితీరును నిర్ధారించడానికి, ఉద్దేశించిన అప్లికేషన్లో ఎదుర్కొనే నిర్దిష్ట రసాయన వాతావరణాన్ని తట్టుకోగల థర్మోప్లాస్టిక్ను ఎంచుకోవడం చాలా అవసరం.
- సాంద్రత: థర్మోప్లాస్టిక్లు వేర్వేరు మందాలను కలిగి ఉంటాయి, ఇవి వాటి బరువు మరియు మొత్తం భాగాల లక్షణాలను ప్రభావితం చేస్తాయి. పాలిథిలిన్ వంటి తక్కువ-సాంద్రత పదార్థాలు తేలికైన పరిష్కారాలను అందిస్తాయి, అయితే పాలీప్రొఫైలిన్ వంటి అధిక సాంద్రత కలిగిన పదార్థాలు అదనపు బలం మరియు దృఢత్వాన్ని అందిస్తాయి.
ఇంజెక్షన్ మౌల్డింగ్ ప్రక్రియ: దశల వారీగా
ఇంజెక్షన్ మౌల్డింగ్ ప్రక్రియ ఈ దశలను అనుసరిస్తుంది, ఇది అధిక-నాణ్యత థర్మోప్లాస్టిక్ భాగాల యొక్క సమర్థవంతమైన మరియు ఖచ్చితమైన ఉత్పత్తిని అనుమతిస్తుంది. ప్రతి దశకు స్థిరమైన భాగం కొలతలు, మెటీరియల్ లక్షణాలు మరియు మొత్తం నాణ్యతను నిర్ధారించడానికి జాగ్రత్తగా నియంత్రణ మరియు పర్యవేక్షణ అవసరం.
- మోల్డ్ డిజైన్ మరియు ఫాబ్రికేషన్: ఇంజెక్షన్ మౌల్డింగ్ ప్రక్రియలో మొదటి దశ అచ్చు రూపకల్పన మరియు కల్పన. కావలసిన పార్ట్ స్పెసిఫికేషన్లను సాధించడానికి తయారీదారులు ఖచ్చితమైన మరియు వివరణాత్మక అచ్చు రూపకల్పనను తప్పనిసరిగా సృష్టించాలి. తయారీదారులు CNC లేదా ఎలక్ట్రికల్ డిశ్చార్జ్ మ్యాచింగ్ (EDM) వంటి వివిధ పద్ధతులను ఉపయోగించి అచ్చును తయారు చేస్తారు.
- మెటీరియల్ తయారీ: అచ్చు సిద్ధమైన తర్వాత తదుపరి దశ తయారీ. థర్మోప్లాస్టిక్ గుళికలు లేదా కణికలు కావలసిన పదార్థ లక్షణాల ఆధారంగా ఎంపిక చేయబడతాయి మరియు తొట్టిలో కరిగించబడతాయి. ఆపరేటర్లు ఇంజెక్షన్ మోల్డింగ్ మెషిన్ యొక్క బారెల్లోకి పదార్థాన్ని ఫీడ్ చేస్తారు, అక్కడ అది ద్రవీభవన మరియు సజాతీయీకరణకు లోనవుతుంది.
- ఇంజెక్షన్:ఇంజెక్షన్ దశలో, ఆపరేటర్లు కరిగిన థర్మోప్లాస్టిక్ను అధిక పీడనం కింద అచ్చు కుహరంలోకి ఇంజెక్ట్ చేస్తారు. యంత్రం యొక్క ఇంజెక్షన్ యూనిట్ కరిగిన పదార్థాన్ని నాజిల్ ద్వారా మరియు అచ్చులోకి నెట్టివేస్తుంది. పదార్థం అచ్చు కుహరాన్ని నింపుతుంది, కావలసిన భాగం యొక్క ఆకారాన్ని తీసుకుంటుంది.
- శీతలీకరణ మరియు ఘనీభవనం:అచ్చును నింపిన తర్వాత, ఆపరేటర్లు కరిగిన ప్లాస్టిక్ను చల్లబరచడానికి మరియు పటిష్టం చేయడానికి అనుమతిస్తారు. డైమెన్షనల్ స్టెబిలిటీ మరియు సరైన పార్ట్ ఫార్మేషన్ సాధించడానికి శీతలీకరణ కీలకం. ఆపరేటర్లు శీతలీకరణ ప్రక్రియను అచ్చు లోపల ఛానెల్ల ద్వారా లేదా శీతలీకరణ ప్లేట్లను ఉపయోగించడం ద్వారా శీతలకరణిని నియంత్రించవచ్చు.
- అచ్చు తెరవడం మరియు ఎజెక్షన్:ఆపరేటర్లు అచ్చును తెరిచి, ప్లాస్టిక్ ఘనీభవించిన తర్వాత అచ్చు కుహరం నుండి భాగాన్ని బయటకు తీస్తారు. యంత్రంలోని ఎజెక్షన్ సిస్టమ్ అచ్చు నుండి ప్రాంతాన్ని తొలగించడానికి పిన్స్, ఎజెక్టర్ ప్లేట్లు లేదా ఎయిర్ బ్లాస్ట్లను ఉపయోగిస్తుంది. అచ్చు తదుపరి ఇంజెక్షన్ చక్రం కోసం సిద్ధంగా ఉంది.
- శుద్ధి చేయబడిన తరువాత: ఎజెక్షన్ తర్వాత, భాగం ట్రిమ్మింగ్, డీబరింగ్ లేదా సర్ఫేస్ ఫినిషింగ్ వంటి పోస్ట్-ప్రాసెసింగ్ కార్యకలాపాలకు లోనవుతుంది. ఈ దశలు అదనపు పదార్థాన్ని తీసివేయడానికి, కఠినమైన అంచులను సున్నితంగా చేయడానికి మరియు భాగం యొక్క తుది రూపాన్ని మెరుగుపరచడంలో సహాయపడతాయి.
- నాణ్యత తనిఖీ: చివరి దశలో నాణ్యత కోసం ఇంజెక్ట్ చేయబడిన భాగాలను తనిఖీ చేయడం మరియు అవి పేర్కొన్న అవసరాలకు అనుగుణంగా ఉన్నాయని నిర్ధారించడం. భాగం యొక్క నాణ్యత మరియు సమగ్రతను ధృవీకరించడానికి డైమెన్షనల్ కొలత, దృశ్య తనిఖీ మరియు ఫంక్షనల్ టెస్టింగ్తో సహా వివిధ నాణ్యత నియంత్రణ పద్ధతులు ఉపయోగించబడతాయి.
- రీసైక్లింగ్ మరియు మెటీరియల్ పునర్వినియోగం:ఇంజెక్షన్ మౌల్డింగ్ సమయంలో ఉత్పత్తి చేయబడిన ఏదైనా అదనపు లేదా స్క్రాప్ పదార్థాన్ని రీసైకిల్ చేయవచ్చు మరియు తిరిగి ఉపయోగించవచ్చు. కొత్త థర్మోప్లాస్టిక్ పదార్థాల వినియోగాన్ని తగ్గించడం వ్యర్థాలను తగ్గించడానికి మరియు స్థిరత్వాన్ని మెరుగుపరచడంలో సహాయపడుతుంది.
ఇంజెక్షన్ మోల్డింగ్లో ఉపయోగించే పరికరాలు
ఈ పరికరాల భాగాలు థర్మోప్లాస్టిక్ పదార్థాన్ని కరిగించడం మరియు ఇంజెక్ట్ చేయడం నుండి తుది భాగాన్ని ఆకృతి చేయడం, చల్లబరచడం మరియు బయటకు తీయడం వరకు ఇంజెక్షన్ అచ్చు ప్రక్రియను సులభతరం చేస్తాయి. సమర్థవంతమైన, అధిక-నాణ్యత ఇంజెక్షన్ మోల్డింగ్ ఉత్పత్తిని సాధించడానికి ఈ పరికరాల భాగాల యొక్క సరైన ఆపరేషన్ మరియు నిర్వహణ కీలకం.
- ఇంజెక్షన్ మోల్డింగ్ మెషిన్:ఇంజెక్షన్ మౌల్డింగ్లోని ప్రాథమిక పరికరాలు థర్మోప్లాస్టిక్ పదార్థాన్ని కరిగించడానికి, అచ్చులోకి ఇంజెక్ట్ చేయడానికి మరియు ప్రక్రియను నియంత్రించడానికి బాధ్యత వహిస్తాయి.
- అచ్చు: ప్లాస్టిక్ భాగం యొక్క కావలసిన ఆకారం మరియు లక్షణాలను రూపొందించడానికి అనుకూల-రూపకల్పన చేయబడిన అచ్చు, కుహరం మరియు కోర్ అనే రెండు భాగాలను కలిగి ఉంటుంది. ఆపరేటర్లు ఇంజెక్షన్ మౌల్డింగ్ మెషీన్ యొక్క బిగింపు యూనిట్లో దాన్ని మౌంట్ చేస్తారు.
- హాప్పర్:థర్మోప్లాస్టిక్ పదార్థాన్ని పెల్లెట్ లేదా గ్రాన్యులర్ రూపంలో ఉంచి, కరిగే మరియు ఇంజెక్షన్ కోసం ఇంజెక్షన్ మోల్డింగ్ మెషీన్ యొక్క బారెల్లోకి ఫీడ్ చేసే కంటైనర్.
- బారెల్ మరియు స్క్రూ: బారెల్, ఒక స్థూపాకార గది, థర్మోప్లాస్టిక్ పదార్థాన్ని కరుగుతుంది మరియు సజాతీయంగా మారుస్తుంది, స్క్రూ మెటీరియల్ను కరిగించడానికి, కలపడానికి మరియు ప్రమాణీకరించడానికి దాని లోపల తిరుగుతుంది.
- తాపన మరియు శీతలీకరణ వ్యవస్థలు:ఇంజెక్షన్ మౌల్డింగ్ మెషీన్లు బారెల్ యొక్క ఉష్ణోగ్రతను పెంచడానికి ఎలక్ట్రిక్ హీటర్లు లేదా వేడి నూనెను ఉపయోగించే హీటర్లు మరియు అచ్చును చల్లబరచడానికి మరియు ప్లాస్టిక్ భాగాన్ని పటిష్టం చేయడానికి నీరు లేదా చమురు ప్రసరణ వంటి శీతలీకరణ వ్యవస్థలను కలిగి ఉంటాయి.
- ఎజెక్టర్ సిస్టమ్:ఘనీభవించిన తర్వాత అచ్చు కుహరం నుండి మలచబడిన భాగాన్ని తొలగిస్తుంది, సాధారణంగా అచ్చు తెరుచుకునే సమయంలో ఎజెక్టర్ పిన్స్, ప్లేట్లు లేదా ఎయిర్ బ్లాస్ట్లను ఉపయోగిస్తుంది.
- నియంత్రణ వ్యవస్థ:ఇంజెక్షన్ మోల్డింగ్ ప్రక్రియ యొక్క వివిధ పారామితులను పర్యవేక్షిస్తుంది మరియు నియంత్రిస్తుంది, ఇంజక్షన్ వేగం, ఉష్ణోగ్రత, పీడనం మరియు శీతలీకరణ సమయం వంటి పారామితులను సెట్ చేయడానికి మరియు సర్దుబాటు చేయడానికి ఆపరేటర్లను అనుమతిస్తుంది.
ఇంజెక్షన్ మౌల్డింగ్ యంత్రాలు: రకాలు మరియు లక్షణాలు
ఇంజక్షన్ మౌల్డింగ్ మెషీన్ యొక్క ప్రతి రకం దాని లక్షణాలు మరియు ప్రయోజనాలను కలిగి ఉంది, తయారీదారులు వారి నిర్దిష్ట ఉత్పత్తి అవసరాలకు తగిన పరికరాన్ని ఎంచుకోవడానికి అనుమతిస్తుంది.
- హైడ్రాలిక్ ఇంజెక్షన్ మౌల్డింగ్ యంత్రాలు: ఈ యంత్రాలు కరిగిన ప్లాస్టిక్ను అచ్చులోకి ఇంజెక్ట్ చేయడానికి అవసరమైన ఒత్తిడిని ఉత్పత్తి చేయడానికి హైడ్రాలిక్ వ్యవస్థలను ఉపయోగిస్తాయి. వారు అధిక బిగింపు శక్తి, ఖచ్చితమైన నియంత్రణ మరియు వివిధ థర్మోప్లాస్టిక్లను నిర్వహించడంలో బహుముఖ ప్రజ్ఞకు ప్రసిద్ధి చెందారు. హైడ్రాలిక్ యంత్రాలు పెద్ద-స్థాయి ఉత్పత్తికి అనుకూలంగా ఉంటాయి మరియు సంక్లిష్ట అచ్చులను కలిగి ఉంటాయి.
- ఎలక్ట్రిక్ ఇంజెక్షన్ మౌల్డింగ్ యంత్రాలు:ఎలక్ట్రిక్ యంత్రాలు ఇంజెక్షన్, బిగింపు మరియు ఎజెక్టర్ సిస్టమ్లతో సహా యంత్రం యొక్క ఆపరేషన్ కోసం ఎలక్ట్రిక్ సర్వో మోటార్లను ఉపయోగించుకుంటాయి. అవి హైడ్రాలిక్ మెషీన్ల కంటే ఖచ్చితమైన నియంత్రణ, శక్తి సామర్థ్యం మరియు వేగవంతమైన ప్రతిస్పందన సమయాలను అందిస్తాయి. అధిక రిపీటబిలిటీ మరియు ఖచ్చితత్వం అవసరమయ్యే ఖచ్చితమైన మోల్డింగ్ అప్లికేషన్లకు ఎలక్ట్రిక్ యంత్రాలు అనువైనవి.
- హైబ్రిడ్ ఇంజెక్షన్ మౌల్డింగ్ యంత్రాలు:హైబ్రిడ్ యంత్రాలు హైడ్రాలిక్ మరియు ఎలక్ట్రిక్ పరికరాల రెండింటి ప్రయోజనాలను మిళితం చేస్తాయి. వారు అధిక ఖచ్చితత్వం, శక్తి సామర్థ్యం మరియు వ్యయ-ప్రభావాన్ని సాధించడానికి హైడ్రాలిక్ మరియు ఎలక్ట్రిక్ సర్వో సిస్టమ్ల కలయికను ఉపయోగిస్తారు. హైబ్రిడ్ యంత్రాలు విస్తృత శ్రేణి అనువర్తనాలకు అనుకూలంగా ఉంటాయి, పనితీరు మరియు కార్యాచరణ ఖర్చుల మధ్య సమతుల్యతను అందిస్తాయి.
- రెండు-ప్లాటెన్ ఇంజెక్షన్ మౌల్డింగ్ యంత్రాలు: రెండు-ప్లాటెన్ యంత్రాలు అచ్చును బిగించడానికి రెండు వేర్వేరు ప్లేట్లతో ప్రత్యేకమైన డిజైన్ను కలిగి ఉంటాయి. ఈ డిజైన్ మెరుగైన స్థిరత్వం, మెరుగైన అచ్చు సమకాలీకరణను అందిస్తుంది మరియు పెద్ద అచ్చు పరిమాణాలు మరియు అధిక బిగింపు శక్తులను అనుమతిస్తుంది. రెండు-ప్లాటెన్ యంత్రాలు ఖచ్చితమైన అచ్చు అవసరమయ్యే పెద్ద మరియు సంక్లిష్ట భాగాలకు అనుకూలంగా ఉంటాయి.
- బహుళ-భాగాల ఇంజెక్షన్ మౌల్డింగ్ యంత్రాలు:ఒకే మౌల్డింగ్ చక్రంలో బహుళ పదార్థాలు లేదా రంగులతో భాగాలను ఉత్పత్తి చేయడానికి తయారీదారులు ఈ యంత్రాలను డిజైన్ చేస్తారు. వారు వివిధ ఇంజెక్షన్ యూనిట్లు మరియు అచ్చులను కలిగి ఉంటారు, వివిధ పదార్థాల ఏకకాల ఇంజెక్షన్ను అనుమతిస్తుంది. బహుళ-భాగాల యంత్రాలు విభిన్న లక్షణాలతో సంక్లిష్ట భాగాలను తయారు చేయడంలో వశ్యత మరియు సామర్థ్యాన్ని అందిస్తాయి.
- మైక్రో-ఇంజెక్షన్ మోల్డింగ్ యంత్రాలు:చిన్న మరియు ఖచ్చితమైన భాగాలను ఉత్పత్తి చేయడానికి ప్రత్యేకంగా రూపొందించబడింది, మైక్రో-ఇంజెక్షన్ మోల్డింగ్ మెషీన్లు చాలా ఎక్కువ ఖచ్చితత్వం మరియు ఖచ్చితత్వాన్ని అందిస్తాయి. వారు గట్టి సహనం మరియు కనీస పదార్థ వ్యర్థాలతో క్లిష్టమైన వివరాలను ఉత్పత్తి చేయగలరు. ఎలక్ట్రానిక్స్, వైద్య పరికరాలు మరియు మైక్రో-ఆప్టిక్స్ సాధారణంగా మైక్రో-ఇంజెక్షన్ మోల్డింగ్ మెషీన్లను ఉపయోగిస్తాయి.
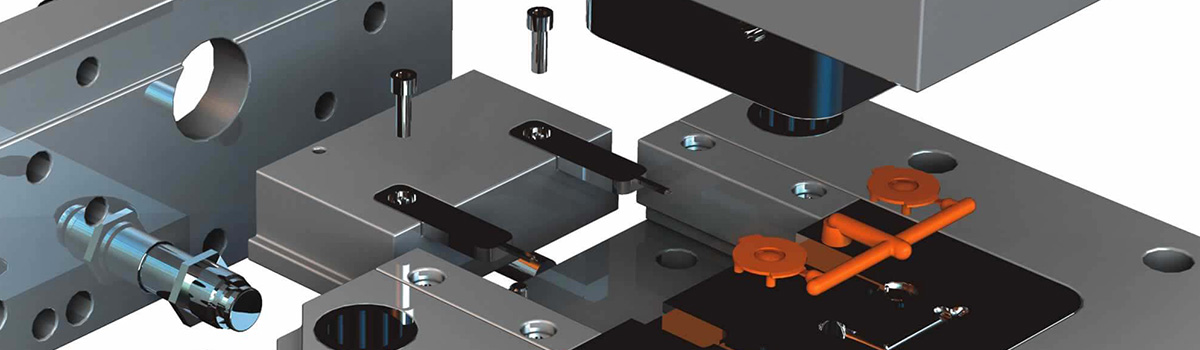
ఇంజెక్షన్ మోల్డింగ్ కోసం మోల్డ్ డిజైన్ పరిగణనలు
విజయవంతమైన ఇంజెక్షన్ మోల్డింగ్ ఉత్పత్తికి జాగ్రత్తగా అచ్చు రూపకల్పన పరిగణనలు అవసరం.
- పార్ట్ డిజైన్:అచ్చు రూపకల్పన దాని ఆకారం, కొలతలు మరియు క్రియాత్మక లక్షణాలతో సహా భాగం యొక్క నిర్దిష్ట అవసరాలకు అనుగుణంగా ఉండాలి. తయారీదారులు డ్రాఫ్ట్ కోణాలు, గోడ మందం, అండర్కట్లు మరియు ఎజెక్షన్ సౌలభ్యం మరియు పార్ట్ క్వాలిటీని నిర్ధారించడానికి అవసరమైన ఏవైనా అంశాలను సరిగ్గా పరిగణించాలి.
- అచ్చు పదార్థం: మన్నిక, డైమెన్షనల్ స్టెబిలిటీ మరియు హీట్ రెసిస్టెన్స్ని సాధించడానికి అచ్చు పదార్థం ఎంపిక కీలకం. సాధారణ అచ్చు పదార్థాలలో ఉక్కు మిశ్రమాలు, అల్యూమినియం మిశ్రమాలు మరియు టూల్ స్టీల్స్ ఉన్నాయి. మెటీరియల్ ఎంపిక ఉత్పత్తి పరిమాణం, భాగం సంక్లిష్టత మరియు ఆశించిన సాధనం జీవితం వంటి అంశాలపై ఆధారపడి ఉంటుంది.
- శీతలీకరణ వ్యవస్థ:సరైన భాగాన్ని పటిష్టం చేయడానికి మరియు చక్రం సమయాన్ని తగ్గించడానికి సమర్థవంతమైన శీతలీకరణ అవసరం. అచ్చు డిజైన్ ఏకరీతి అచ్చు శీతలీకరణను నిర్ధారించడానికి శీతలీకరణ ఛానెల్లను లేదా వ్యూహాత్మకంగా ఉంచబడిన ఇన్సర్ట్లను కలిగి ఉండాలి. సరైన శీతలీకరణ వార్పేజ్, సంకోచం మరియు భాగాల లోపాల ప్రమాదాన్ని తగ్గిస్తుంది.
- venting:ఇంజెక్షన్ ప్రక్రియలో గాలి మరియు వాయువుల నుండి తప్పించుకోవడానికి తగినంత వెంటింగ్ అవసరం. తగినంతగా వెంటింగ్ గ్యాస్ ఉచ్చులు, బర్న్ మార్కులు లేదా అసంపూర్ణ భాగం నింపడానికి దారితీస్తుంది. తయారీదారులు అచ్చు డిజైన్లో వెంటింగ్ గ్రూవ్లు, పిన్స్ లేదా ఇతర మెకానిజమ్లను చేర్చడం ద్వారా వెంటింగ్ను సాధించవచ్చు.
- ఎజెక్షన్ సిస్టమ్:అచ్చు రూపకల్పన అచ్చు కుహరం నుండి అచ్చు భాగాన్ని సురక్షితంగా మరియు సమర్ధవంతంగా తొలగించడానికి సమర్థవంతమైన ఎజెక్షన్ వ్యవస్థను కలిగి ఉండాలి. ఎజెక్షన్ సిస్టమ్ ఎజెక్టర్ పిన్స్, స్లీవ్లు లేదా ఇతర మెకానిజమ్లను కలిగి ఉంటుంది, ఫంక్షన్ లేదా క్లిష్టమైన లక్షణాలతో జోక్యాన్ని నివారించడానికి వ్యూహాత్మకంగా ఉంచబడుతుంది.
- గేట్ డిజైన్:కరిగిన ప్లాస్టిక్ అచ్చు కుహరంలోకి ప్రవేశించే ద్వారం. గేట్ డిజైన్ సరైన భాగాన్ని నింపేలా, ప్రవాహ రేఖలను తగ్గించి, అకాల పదార్థం గడ్డకట్టడాన్ని నిరోధించాలి. ప్రామాణిక గేట్ డిజైన్లలో ఎడ్జ్ గేట్లు, టన్నెల్ గేట్లు మరియు హాట్ రన్నర్ సిస్టమ్లు ఉంటాయి, ఇవి పార్ట్ అవసరాలు మరియు మెటీరియల్ లక్షణాలపై ఆధారపడి ఉంటాయి.
- విభజన రేఖ:అచ్చు రూపకల్పన తగిన విభజన రేఖను నిర్వచించాలి, ఇది అచ్చు యొక్క రెండు భాగాలు కలిసే రేఖ. సరైన పార్టింగ్ లైన్ ప్లేస్మెంట్ కనీస ఫ్లాష్ మరియు పార్టింగ్ లైన్ అసమతుల్యతను నిర్ధారిస్తుంది మరియు సమర్థవంతమైన అచ్చు అసెంబ్లీని సులభతరం చేస్తుంది.
- అచ్చు నిర్వహణ మరియు సేవా సామర్థ్యం: తయారీదారులు నిర్వహణ, మరమ్మత్తు మరియు అచ్చు సర్వీసింగ్ సౌలభ్యాన్ని పరిగణించాలి. అచ్చు భాగాలు శుభ్రపరచడం, తనిఖీ చేయడం మరియు భర్తీ చేయడం కోసం సులభంగా అందుబాటులో ఉండాలి. త్వరిత-మార్పు ఇన్సర్ట్లు లేదా మాడ్యులర్ మోల్డ్ డిజైన్ల వంటి ఫీచర్లను చేర్చడం వలన అచ్చు సేవలను మెరుగుపరచవచ్చు.
ఇంజెక్షన్ మోల్డింగ్లో ఉపయోగించే అచ్చు పదార్థాలు
మోల్డ్ మెటీరియల్ నిపుణులతో సహకరించడం మరియు మోల్డింగ్ అప్లికేషన్ యొక్క నిర్దిష్ట అవసరాలను పరిగణనలోకి తీసుకోవడం అనేది సరైన అచ్చు పనితీరు మరియు పాక్షిక నాణ్యతను సాధించడానికి అత్యంత అనుకూలమైన మెటీరియల్ని నిర్ణయించడంలో సహాయపడుతుంది.
- ఉక్కు మిశ్రమాలు: టూల్ స్టీల్స్ (ఉదా, P20, H13) మరియు స్టెయిన్లెస్ స్టీల్స్ వంటి ఉక్కు మిశ్రమాలు, వాటి అద్భుతమైన మన్నిక, వేడి నిరోధకత మరియు దుస్తులు నిరోధకత కారణంగా సాధారణంగా ఇంజెక్షన్ మోల్డింగ్ అచ్చులకు ఉపయోగిస్తారు. ఈ పదార్థాలు ఇంజెక్షన్ మౌల్డింగ్ ప్రక్రియలో అధిక ఉష్ణోగ్రతలు మరియు ఒత్తిళ్లను తట్టుకోగలవు మరియు అధిక-నాణ్యత భాగాలను ఉత్పత్తి చేయడానికి మంచి డైమెన్షనల్ స్థిరత్వాన్ని అందిస్తాయి.
- అల్యూమినియం మిశ్రమాలు:7075 మరియు 6061 వంటి అల్యూమినియం మిశ్రమాలు తేలికైనవి మరియు మంచి ఉష్ణ వాహకతను అందిస్తాయి, ఇవి సమర్థవంతమైన శీతలీకరణ అవసరమయ్యే అచ్చులకు అనుకూలంగా ఉంటాయి. తయారీదారులు తరచుగా అల్యూమినియం అచ్చులను ప్రోటోటైపింగ్, తక్కువ-వాల్యూమ్ ఉత్పత్తి లేదా బరువు తగ్గింపు కీలకమైన అనువర్తనాల కోసం ఉపయోగిస్తారు. అయినప్పటికీ, ఉక్కు మిశ్రమాలతో పోలిస్తే అల్యూమినియం అచ్చులు తక్కువ మన్నికను కలిగి ఉండవచ్చు.
- రాగి మిశ్రమాలు:బెరీలియం రాగి వంటి రాగి మిశ్రమాలు అధిక ఉష్ణ వాహకత మరియు మంచి యంత్ర సామర్థ్యాన్ని ప్రదర్శిస్తాయి. సమర్థవంతమైన శీతలీకరణ కోసం అద్భుతమైన ఉష్ణ బదిలీ అవసరమయ్యే అచ్చులలో వారు వినియోగాన్ని కనుగొంటారు. రాగి మిశ్రమాలు అచ్చు భాగం నుండి వేడిని త్వరగా వెదజల్లడం ద్వారా చక్రాల సమయాన్ని తగ్గించడంలో సహాయపడతాయి, ఫలితంగా వేగంగా పటిష్టం అవుతాయి.
- టూల్ స్టీల్స్:H13, S7 మరియు D2తో సహా టూల్ స్టీల్స్ అధిక-పనితీరు గల టూలింగ్ అప్లికేషన్ల కోసం రూపొందించబడ్డాయి. ఈ స్టీల్స్ అధిక బలం, కాఠిన్యం మరియు దుస్తులు నిరోధకత కలయికను అందిస్తాయి. టూల్ స్టీల్స్ అధిక ఉత్పత్తి వాల్యూమ్లు, రాపిడి పదార్థాలు లేదా డిమాండ్ చేసే అచ్చు పరిస్థితులతో అచ్చులకు సరిపోతాయి.
- నికెల్ మిశ్రమాలు:ఇంకోనెల్ మరియు హాస్టెల్లాయ్ వంటి నికెల్ మిశ్రమాలు వాటి అసాధారణమైన తుప్పు నిరోధకత, అధిక-ఉష్ణోగ్రత బలం మరియు ఉష్ణ స్థిరత్వానికి ప్రసిద్ధి చెందాయి. తయారీదారులు ఈ మిశ్రమాలను తినివేయు పదార్థాలను నిర్వహించే అచ్చులలో ఉపయోగిస్తారు లేదా విపరీతమైన ఉష్ణోగ్రతలు మరియు ఉగ్రమైన అచ్చు వాతావరణాలకు నిరోధకత అవసరం.
- మిశ్రమ పదార్థాలు:రీన్ఫోర్స్డ్ ప్లాస్టిక్లు లేదా మెటల్ ఇన్సర్ట్లతో కూడిన మిశ్రమాలు వంటి మిశ్రమ పదార్థాలు అప్పుడప్పుడు నిర్దిష్ట మౌల్డింగ్ అప్లికేషన్ల కోసం ఉపయోగించబడతాయి. ఈ పదార్థాలు అధిక బలం, ఉష్ణ స్థిరత్వం మరియు తగ్గిన బరువు వంటి లక్షణాల సమతుల్యతను అందిస్తాయి. నిర్దిష్ట ఉత్పత్తి అవసరాల కోసం మిశ్రమ అచ్చులు ఖర్చుతో కూడుకున్న ప్రత్యామ్నాయాలు.
ఇంజెక్షన్ అచ్చుల రకాలు
ఇంజెక్షన్ మౌల్డింగ్ అనేది ప్లాస్టిక్ భాగాల కోసం ఒక బహుముఖ మరియు విస్తృతంగా ఉపయోగించే తయారీ ప్రక్రియ.
- రెండు-ప్లేట్ అచ్చు:రెండు-ప్లేట్ అచ్చు అనేది ఇంజెక్షన్ అచ్చు యొక్క అత్యంత సాధారణ రకం. ఇది రెండు ప్లేట్లను కలిగి ఉంటుంది, కుహరం ప్లేట్ మరియు కోర్ ప్లేట్, అచ్చు భాగం యొక్క ఎజెక్షన్ను అనుమతించడానికి విడిగా ఉంటాయి. కుహరం ప్లేట్ అచ్చు యొక్క కుహరం వైపు కలిగి ఉంటుంది, అయితే కోర్ ప్లేట్ కోర్ వైపు ఉంటుంది. తయారీదారులు సాపేక్షంగా సరళమైన డిజైన్ కారణంగా విస్తృత శ్రేణి భాగాలను ఉత్పత్తి చేయడానికి రెండు-ప్లేట్ అచ్చులను ఉపయోగిస్తారు.
- మూడు-ప్లేట్ అచ్చు:మూడు-ప్లేట్ అచ్చు రెండు-ప్లేట్ అచ్చు యొక్క అధునాతన వెర్షన్. ఇది అదనపు ప్లేట్, రన్నర్ లేదా స్ప్రూ ప్లేట్ను కలిగి ఉంటుంది. రన్నర్ ప్లేట్ స్ప్రూ, రన్నర్లు మరియు గేట్ల కోసం ప్రత్యేక ఛానెల్ని సృష్టిస్తుంది, అచ్చు భాగాన్ని సులభంగా తొలగించడానికి అనుమతిస్తుంది. తయారీదారులు సాధారణంగా సంక్లిష్ట గేటింగ్ సిస్టమ్లతో కూడిన వివరాల కోసం మూడు-ప్లేట్ అచ్చులను ఉపయోగిస్తారు లేదా ముక్కపై గేట్ వేస్టేజ్ను నివారించడం మంచిది.
- హాట్ రన్నర్ మోల్డ్:రన్నర్ మరియు గేట్ వ్యవస్థ వేడి రన్నర్ అచ్చులలో వేడి చేయబడుతుంది, ప్రతి చక్రంలో పదార్థాన్ని పటిష్టం చేయడం మరియు మళ్లీ కరిగించే అవసరాన్ని తొలగిస్తుంది. హాట్ రన్నర్ సిస్టమ్లో వేడిచేసిన మానిఫోల్డ్లు మరియు ప్లాస్టిక్ కరిగిన స్థితిని నిర్వహించే నాజిల్లు ఉంటాయి. హాట్ రన్నర్ అచ్చులు తగ్గిన సైకిల్ సమయం, తక్కువ పదార్థ వ్యర్థాలు మరియు గేట్ వెస్టిజ్లను తగ్గించడం ద్వారా పార్ట్ క్వాలిటీని మెరుగుపరచడం వంటి ప్రయోజనాలను అందిస్తాయి.
- కోల్డ్ రన్నర్ మోల్డ్: కోల్డ్ రన్నర్ అచ్చులు సాంప్రదాయ రన్నర్ మరియు గేట్ సిస్టమ్ను కలిగి ఉంటాయి, ఇక్కడ కరిగిన ప్లాస్టిక్ ప్రతి చక్రంతో పటిష్టమయ్యే కోల్డ్ రన్నర్ల ద్వారా ప్రవహిస్తుంది. ఆపరేటర్లు తదనంతరం ఘనీభవించిన రన్నర్లను తొలగిస్తారు, ఫలితంగా పదార్థ వ్యర్థాలు ఏర్పడతాయి. తయారీదారులు సాధారణంగా కాంప్లెక్స్ రన్నర్ మోల్డ్లను తక్కువ వాల్యూమ్ ఉత్పత్తి కోసం ఉపయోగిస్తారు లేదా వాటి మరింత సరళమైన డిజైన్ కారణంగా మెటీరియల్ ఖర్చులు తక్కువగా ఉన్నప్పుడు.
- అచ్చును చొప్పించు:ఇంజెక్షన్ మౌల్డింగ్ సమయంలో అచ్చు కుహరంలోకి మెటల్ లేదా ప్లాస్టిక్ ఇన్సర్ట్లను చొప్పించండి. ఇన్సర్ట్లను అచ్చులో ముందుగా ఉంచవచ్చు లేదా స్వయంచాలక ప్రక్రియల ద్వారా చొప్పించవచ్చు. ఈ అచ్చు అదనపు భాగాలను ఏకీకృతం చేయడానికి లేదా అచ్చు చేయబడిన భాగంలోకి మూలకాలను బలోపేతం చేయడానికి అనుమతిస్తుంది, దాని కార్యాచరణ లేదా బలాన్ని పెంచుతుంది.
- ఓవర్మోల్డ్: ఓవర్మోల్డింగ్లో ఒక పదార్థాన్ని మరొకదానిపై మౌల్డింగ్ చేయడం, సాధారణంగా దృఢమైన ప్లాస్టిక్ సబ్స్ట్రేట్ను మృదువైన ఎలాస్టోమర్ లేదా థర్మోప్లాస్టిక్తో బంధించడం. ఈ ప్రక్రియ ఒకే అచ్చులో బహుళ పదార్థాలు లేదా అల్లికలతో భాగాలను రూపొందించడానికి అనుమతిస్తుంది, మెరుగైన పట్టు, కుషనింగ్ లేదా సౌందర్య లక్షణాలను అందిస్తుంది.
ఇంజెక్షన్ మోల్డింగ్ ఖర్చులను ప్రభావితం చేసే కారకాలు
ఈ కారకాలను పరిగణనలోకి తీసుకుంటే తయారీదారులు ఇంజెక్షన్ మౌల్డింగ్ ధరను అంచనా వేయడంలో మరియు ఆప్టిమైజ్ చేయడంలో సహాయపడుతుంది, వారి నిర్దిష్ట ఉత్పత్తి అవసరాల కోసం నాణ్యత, సామర్థ్యం మరియు వ్యయ-ప్రభావం మధ్య సమతుల్యతను నిర్ధారిస్తుంది.
- భాగం సంక్లిష్టత:ఇంజెక్షన్ మౌల్డింగ్ ఖర్చును నిర్ణయించడంలో పార్ట్ డిజైన్ యొక్క సంక్లిష్టత ముఖ్యమైన పాత్ర పోషిస్తుంది. సంక్లిష్టమైన జ్యామితులు, అండర్కట్లు, సన్నని గోడలు లేదా సంక్లిష్ట లక్షణాలకు అదనపు సాధనాలు, ప్రత్యేకమైన అచ్చులు లేదా పొడవైన చక్రాలు అవసరం కావచ్చు, మొత్తం తయారీ ఖర్చు పెరుగుతుంది.
- మెటీరియల్ ఎంపిక:థర్మోప్లాస్టిక్ పదార్థం యొక్క ఎంపిక ఇంజెక్షన్ మోల్డింగ్ ధరను ప్రభావితం చేస్తుంది. వివిధ పదార్థాలు కిలోగ్రాముకు వేర్వేరు ధరలను కలిగి ఉంటాయి మరియు మెటీరియల్ లభ్యత, లక్షణాలు మరియు ప్రాసెసింగ్ అవసరాలు వంటి అంశాలు మొత్తం పదార్థ ధరను ప్రభావితం చేస్తాయి.
- సాధనం మరియు అచ్చు రూపకల్పన: ప్రారంభ సాధనం మరియు అచ్చు రూపకల్పన ఖర్చులు ఇంజెక్షన్ మోల్డింగ్ ఖర్చులలో ముఖ్యమైనవి. అచ్చు సంక్లిష్టత, కావిటీల సంఖ్య, అచ్చు పరిమాణం మరియు అచ్చు పదార్థం వంటి అంశాలు సాధనం మరియు అచ్చు తయారీ ఖర్చులకు దోహదం చేస్తాయి. అధునాతన ఫీచర్లు అవసరమయ్యే సంక్లిష్టమైన అచ్చులు లేదా అచ్చులు ముందస్తు పెట్టుబడిని పెంచుతాయి.
- ఉత్పత్తి వాల్యూమ్: ఉత్పత్తి పరిమాణం ఇంజెక్షన్ మౌల్డింగ్లో ఒక్కో భాగానికి అయ్యే ఖర్చును నేరుగా ప్రభావితం చేస్తుంది. ఉన్నత పుస్తకాలు తరచుగా ఆర్థిక స్థాయికి దారితీస్తాయి, ఒక్కో భాగానికి ధర తగ్గుతుంది. దీనికి విరుద్ధంగా, తక్కువ-వాల్యూమ్ ఉత్పత్తి పరుగులు సెటప్, టూలింగ్ మరియు మెటీరియల్ వేస్ట్ కారణంగా అధిక ఛార్జీలను కలిగి ఉండవచ్చు.
- సైకిల్ సమయం: శీతలీకరణ మరియు ఎజెక్షన్ దశలను కలిగి ఉన్న చక్రం సమయం, ఉత్పత్తి సామర్థ్యం మరియు మొత్తం వ్యయాన్ని ప్రభావితం చేస్తుంది. ఎక్కువ చక్రాల సమయాలు ఉత్పత్తి ఉత్పత్తి తగ్గడానికి మరియు అధిక ధరలకు దారితీస్తాయి. అచ్చు రూపకల్పన, శీతలీకరణ వ్యవస్థ మరియు ప్రక్రియ పారామితులను ఆప్టిమైజ్ చేయడం వలన చక్రాల సమయాన్ని తగ్గించవచ్చు మరియు సామర్థ్యాన్ని మెరుగుపరుస్తుంది.
- నాణ్యత అవసరాలు:కఠినమైన నాణ్యత అవసరాలు లేదా నిర్దిష్ట ధృవపత్రాలు ఇంజెక్షన్ మోల్డింగ్ ధరను ప్రభావితం చేయవచ్చు. ఖచ్చితమైన టాలరెన్స్లు, ఉపరితల ముగింపు అవసరాలు లేదా అదనపు పరీక్షలకు ఇతర వనరులు, ప్రక్రియలు లేదా తనిఖీలు అవసరం కావచ్చు, ఇది మొత్తం ఖర్చును పెంచుతుంది.
- ద్వితీయ కార్యకలాపాలు:అచ్చు వేయబడిన భాగాలకు అసెంబ్లీ, పెయింటింగ్ లేదా అదనపు ముగింపు దశలు వంటి పోస్ట్-ప్రాసెసింగ్ ఆపరేషన్లు అవసరమైతే, ఈ కార్యకలాపాలు మొత్తం ఇంజెక్షన్ మోల్డింగ్ ధరకు జోడించబడతాయి.
- సరఫరాదారు మరియు స్థానం:ఇంజెక్షన్ మోల్డింగ్ సరఫరాదారు ఎంపిక మరియు వారి స్థానం ఖర్చులను ప్రభావితం చేయవచ్చు. లేబర్ ఖర్చులు, ఓవర్హెడ్లు, లాజిస్టిక్స్ మరియు రవాణా ఖర్చులు సరఫరాదారు స్థానం ఆధారంగా మారుతూ ఉంటాయి, ఇది మొత్తం తయారీ వ్యయంపై ప్రభావం చూపుతుంది.
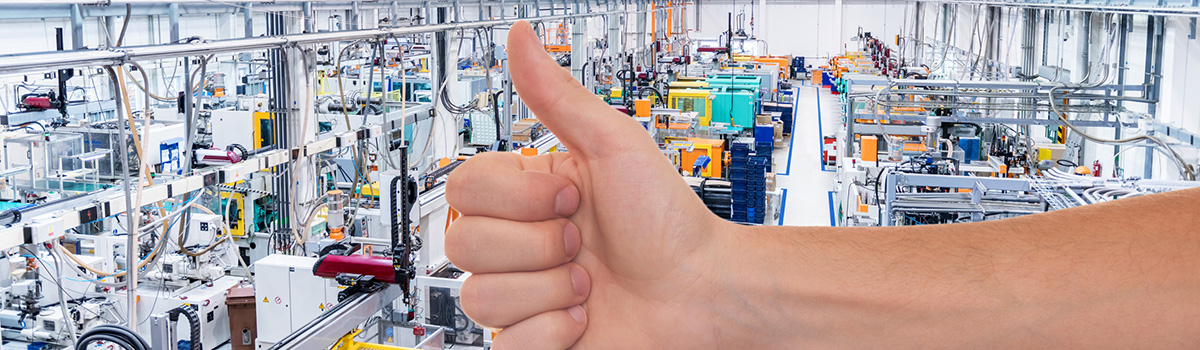
ఇంజెక్షన్ మోల్డింగ్లో నాణ్యత నియంత్రణ
ఇంజెక్షన్ మౌల్డింగ్ ప్రక్రియ అంతటా బలమైన నాణ్యత నియంత్రణ చర్యలను అమలు చేయడం వలన సంభావ్య లోపాలు, విచలనాలు లేదా అసమానతలను గుర్తించి, పరిష్కరించడంలో సహాయపడుతుంది, కస్టమర్ స్పెసిఫికేషన్లు మరియు అవసరాలకు అనుగుణంగా అధిక-నాణ్యత భాగాల ఉత్పత్తిని నిర్ధారిస్తుంది.
- ప్రక్రియ పర్యవేక్షణ: కరిగే ఉష్ణోగ్రత, ఇంజెక్షన్ పీడనం, శీతలీకరణ సమయం మరియు చక్రం సమయం వంటి కీలక ప్రక్రియ పారామితుల యొక్క నిరంతర పర్యవేక్షణ, భాగం ఉత్పత్తిలో స్థిరత్వం మరియు పునరావృతతను నిర్ధారిస్తుంది. రియల్ టైమ్ మానిటరింగ్ మరియు ఆటోమేటెడ్ సిస్టమ్లు సెట్ పారామీటర్ల నుండి వైవిధ్యాలు లేదా వ్యత్యాసాలను గుర్తించగలవు, సకాలంలో సర్దుబాట్లు మరియు ప్రక్రియ స్థిరత్వాన్ని నిర్వహించడం కోసం అనుమతిస్తుంది.
- తనిఖీ మరియు కొలత:డైమెన్షనల్ ఖచ్చితత్వం, పార్ట్ క్వాలిటీ మరియు స్పెసిఫికేషన్లకు కట్టుబడి ఉండటం కోసం క్రమబద్ధమైన సమీక్ష మరియు అచ్చు భాగాల కొలత అవసరం. మా సేవలు కొలతలు కొలవడం, ఉపరితల నాణ్యతను విశ్లేషించడం, దృశ్య తనిఖీలను నిర్వహించడం మరియు క్రియాత్మక పరీక్షలను నిర్వహించడం వంటి నాణ్యత నియంత్రణ పద్ధతుల శ్రేణిని కవర్ చేస్తాయి. ఖచ్చితమైన మూల్యాంకనం కోసం కోఆర్డినేట్ కొలిచే యంత్రాలు (CMM) మరియు ఆప్టికల్ మరియు విజువల్ ఇన్స్పెక్షన్ సిస్టమ్లు వంటి వివిధ తనిఖీ పద్ధతులు ఉపయోగించబడతాయి.
- గణాంక ప్రక్రియ నియంత్రణ (SPC): SPC ఇంజెక్షన్ మోల్డింగ్ నాణ్యతను పర్యవేక్షించడానికి మరియు నియంత్రించడానికి ప్రక్రియ డేటాను సేకరించడం మరియు విశ్లేషించడం. నియంత్రణ చార్ట్లు మరియు ప్రాసెస్ కెపాబిలిటీ విశ్లేషణ వంటి గణాంక పద్ధతులు, ట్రెండ్లను గుర్తించడంలో, ప్రాసెస్ వైవిధ్యాలను గుర్తించడంలో మరియు ప్రక్రియ నిర్వచించిన నియంత్రణ పరిమితుల్లోనే ఉండేలా చేయడంలో సహాయపడతాయి. SPC సమస్యల యొక్క క్రియాశీల గుర్తింపును ప్రారంభిస్తుంది మరియు ప్రక్రియ ఆప్టిమైజేషన్ను సులభతరం చేస్తుంది.
- మెటీరియల్ టెస్టింగ్: థర్మోప్లాస్టిక్లు, సంకలనాలు మరియు రంగులు వంటి ముడి పదార్థాలను పరీక్షించడం, వాటి నాణ్యత మరియు ఇంజెక్షన్ మౌల్డింగ్కు అనుకూలతను నిర్ధారిస్తుంది. మెటీరియల్ టెస్టింగ్లో మెల్ట్ ఫ్లో ఇండెక్స్ (MFI) విశ్లేషణ, మెకానికల్ లక్షణాలు, థర్మల్ లక్షణాలు మరియు మెటీరియల్ కంపోజిషన్ ఉండవచ్చు. మెటీరియల్ నాణ్యతను ధృవీకరించడం అచ్చు భాగాలలో లోపాలు మరియు అసమానతలను నిరోధించడంలో సహాయపడుతుంది.
- సాధనాల నిర్వహణ మరియు తనిఖీ:ఇంజెక్షన్ మౌల్డింగ్లో నాణ్యతను నిర్ధారించడానికి సరైన నిర్వహణ మరియు ఇంజెక్షన్ అచ్చులను క్రమం తప్పకుండా తనిఖీ చేయడం చాలా కీలకం. రెగ్యులర్ క్లీనింగ్, లూబ్రికేషన్ మరియు అచ్చు భాగాల అంచనా భాగం నాణ్యతను ప్రభావితం చేసే దుస్తులు, నష్టం లేదా క్షీణతను నిరోధించడంలో సహాయపడుతుంది. స్థిరమైన అచ్చు పనితీరును నిర్వహించడానికి అరిగిపోయిన లేదా దెబ్బతిన్న అచ్చు భాగాలను సకాలంలో మరమ్మత్తు చేయడం లేదా భర్తీ చేయడం చాలా అవసరం.
- డాక్యుమెంటేషన్ మరియు ట్రేస్బిలిటీ:ఇంజెక్షన్ మోల్డింగ్లో నాణ్యత నియంత్రణ కోసం సమగ్ర డాక్యుమెంటేషన్ మరియు ట్రేస్బిలిటీ రికార్డులను నిర్వహించడం చాలా అవసరం. ప్రక్రియ పారామితులు, తనిఖీ ఫలితాలు, మెటీరియల్ సమాచారం మరియు ఉత్పత్తి సమయంలో చేసిన ఏవైనా మార్పులు లేదా సర్దుబాట్లను రికార్డ్ చేయడం చాలా ముఖ్యం. సరైన డాక్యుమెంటేషన్ భాగాలను గుర్తించడాన్ని అనుమతిస్తుంది, మూలకారణ విశ్లేషణను సులభతరం చేస్తుంది మరియు నాణ్యతలో స్థిరత్వాన్ని నిర్ధారిస్తుంది.
- శిక్షణ మరియు నైపుణ్యాభివృద్ధి: ఆపరేటర్లు, సాంకేతిక నిపుణులు మరియు నాణ్యత నియంత్రణ సిబ్బందికి తగిన శిక్షణ మరియు నైపుణ్య అభివృద్ధి కార్యక్రమాలను అందించడం వలన ఇంజెక్షన్ మౌల్డింగ్ ప్రక్రియలు, నాణ్యత అవసరాలు మరియు తనిఖీ పద్ధతులపై వారి అవగాహన పెరుగుతుంది. సుశిక్షితులైన సిబ్బంది లోపాలను గుర్తించగలరు, సమస్యలను పరిష్కరించగలరు మరియు అధిక-నాణ్యత ఉత్పత్తిని నిర్ధారిస్తూ దిద్దుబాటు చర్యలను సమర్థవంతంగా అమలు చేయగలరు.
సాధారణ ఇంజెక్షన్ మౌల్డింగ్ లోపాలు మరియు వాటిని ఎలా నివారించాలి
ఇంజెక్షన్ మోల్డింగ్ ప్రక్రియల యొక్క రెగ్యులర్ తనిఖీ, పర్యవేక్షణ మరియు విశ్లేషణ మరియు పరికరాలు మరియు అచ్చుల సరైన నిర్వహణ మరియు సర్దుబాటు ఈ సాధారణ లోపాలను గుర్తించి మరియు పరిష్కరించడంలో సహాయపడుతుంది.
- సింక్ గుర్తులు:సింక్ మార్కులు అసమాన శీతలీకరణ లేదా సంకోచం వలన ఏర్పడిన అచ్చు భాగం యొక్క ఉపరితలంపై మాంద్యం లేదా ఇండెంటేషన్లు. సింక్ మార్కులను నివారించడానికి సరైన గేట్ స్థానం మరియు డిజైన్, సరైన శీతలీకరణ వ్యవస్థ రూపకల్పన మరియు ఏకరీతి గోడ మందం పంపిణీని పరిగణించాలి. ఇంజెక్షన్ ఒత్తిడిని పెంచడం లేదా శీతలీకరణ సమయాన్ని సర్దుబాటు చేయడం కూడా సింక్ మార్కులను తగ్గించడంలో సహాయపడుతుంది.
- వార్పేజ్:వార్పేజ్ అనేది అసమాన శీతలీకరణ లేదా అవశేష ఒత్తిళ్ల కారణంగా ఎజెక్షన్ తర్వాత అచ్చు వేయబడిన భాగం యొక్క వైకల్యం లేదా వంగడాన్ని సూచిస్తుంది. వార్పేజ్ను నిరోధించడానికి ఏకరీతి గోడ మందాన్ని నిర్వహించడం, సరైన శీతలీకరణ మార్గాలను ఉపయోగించడం మరియు అచ్చును సమతుల్యంగా నింపడం మరియు ప్యాకింగ్ చేయడం చాలా కీలకం. అచ్చు ఉష్ణోగ్రతను ఆప్టిమైజ్ చేయడం, తగిన డ్రాఫ్ట్ కోణాలను ఉపయోగించడం మరియు మెటీరియల్ ఉష్ణోగ్రత మరియు ఇంజెక్షన్ వేగాన్ని నియంత్రించడం వంటివి వార్పేజ్ను తగ్గించడంలో సహాయపడతాయి.
- ఫ్లాష్:అదనపు పదార్థం అచ్చు విభజన రేఖలోకి ప్రవహించినప్పుడు ఫ్లాష్ ఏర్పడుతుంది, ఫలితంగా సన్నని, అవాంఛిత అంచనాలు లేదా చివరి భాగంలో అదనపు పదార్థం ఏర్పడుతుంది. తగిన బిగింపు శక్తి, ఖచ్చితమైన అమరిక మరియు తగిన వెంటింగ్ పద్ధతులను ఉపయోగించడంతో సహా సరైన అచ్చు రూపకల్పనను నిర్ధారించడం ద్వారా ఫ్లాష్ను సమర్థవంతంగా నిరోధించవచ్చు. ఇంజెక్షన్ ఒత్తిడి, ఉష్ణోగ్రత మరియు సైకిల్ సమయం వంటి ప్రక్రియ పారామితులను ఆప్టిమైజ్ చేయడం ఫ్లాష్ను తగ్గిస్తుంది.
- చిన్న షాట్:ఇంజెక్ట్ చేయబడిన పదార్థం అచ్చు కుహరాన్ని పూరించనప్పుడు త్వరిత షాట్ జరుగుతుంది, ఫలితంగా అసంపూర్ణ భాగం ఏర్పడుతుంది. సరైన పదార్థ ఎంపిక, తగినంత కరిగే ఉష్ణోగ్రత మరియు స్నిగ్ధతను నిర్ధారించడం మరియు తగిన ఇంజెక్షన్ ఒత్తిడి మరియు సమయాన్ని నిర్వహించడం చిన్న ఫోటోలను నివారించడానికి అవసరం. అదనంగా, తగినంత రన్నర్ మరియు గేట్ సైజు కోసం అచ్చు డిజైన్ను ధృవీకరించడం మరియు సరైన వెంటింగు త్వరిత షాట్లను నిరోధించడంలో సహాయపడుతుంది.
- వెల్డ్ లైన్లు:రెండు లేదా అంతకంటే ఎక్కువ కరిగిన మెటీరియల్ ఫ్లో ఫ్రంట్లు కలిసినప్పుడు మరియు పటిష్టం అయినప్పుడు వెల్డ్ లైన్లు ఏర్పడతాయి, ఫలితంగా భాగం ఉపరితలంపై కనిపించే రేఖ లేదా గుర్తు ఏర్పడుతుంది. మంచి గేట్ మరియు రన్నర్ డిజైన్, సరైన మెల్ట్ టెంపరేచర్, ఇంజెక్షన్ స్పీడ్ మరియు మెటీరియల్ ఫ్లో సర్దుబాటు చేయడం మరియు పార్ట్ జ్యామితి వెల్డ్ లైన్లను తగ్గించగలవు. మోల్డ్ ఫ్లో విశ్లేషణ మరియు గేట్ ప్లేస్మెంట్ ఆప్టిమైజేషన్ కూడా వెల్డ్ లైన్లను నిరోధించడంలో లేదా తగ్గించడంలో సహాయపడతాయి.
- కాలిన గుర్తులు:బర్న్ మార్కులు అనేది పదార్థం యొక్క అధిక వేడి లేదా వేడెక్కడం వలన ఏర్పడిన అచ్చు భాగం యొక్క ఉపరితలంపై రంగు మారడం లేదా నల్ల మచ్చలు. విపరీతమైన కరిగే ఉష్ణోగ్రతను నివారించడం, తగిన శీతలీకరణ మార్గాలను ఉపయోగించడం మరియు సైకిల్ సమయాన్ని ఆప్టిమైజ్ చేయడం వంటివి కాలిన గుర్తులను నిరోధించడంలో సహాయపడతాయి. తగినంత వెంటింగ్, సరైన గేట్ డిజైన్ మరియు అచ్చు ఉష్ణోగ్రతను నియంత్రించడం కూడా బర్న్ మార్కులను తగ్గించడానికి దోహదం చేస్తాయి.
పోస్ట్-మోల్డింగ్ ఆపరేషన్స్: ఫినిషింగ్ మరియు అసెంబ్లీ
ఇంజెక్షన్ మౌల్డింగ్ తర్వాత, కావలసిన తుది ఉత్పత్తిని సాధించడానికి అనేక అచ్చు భాగాలకు అదనపు ముగింపు మరియు అసెంబ్లీ కార్యకలాపాలు అవసరం కావచ్చు. ఈ పోస్ట్-మోల్డింగ్ కార్యకలాపాలు వీటిని కలిగి ఉండవచ్చు:
- కత్తిరించడం:ట్రిమ్మింగ్ లేదా కట్టింగ్ టూల్స్ ఉపయోగించి అచ్చు భాగం చుట్టూ ఏదైనా అదనపు పదార్థం లేదా ఫ్లాష్ను తీసివేయండి.
- ఉపరితల చికిత్స:పెయింటింగ్, పూత లేదా ఆకృతి వంటి వివిధ పద్ధతులను ఉపయోగించి భాగం ఉపరితలం యొక్క రూపాన్ని లేదా కార్యాచరణను మెరుగుపరచడం.
- అసెంబ్లీ:బహుళ అచ్చు భాగాలను కలపడం లేదా తుది ఉత్పత్తిని పూర్తి చేయడానికి ఫాస్టెనర్లు, ఇన్సర్ట్లు లేదా లేబుల్ల వంటి భాగాలను జోడించడం.
- టెస్టింగ్:డైమెన్షనల్ అనాలిసిస్, మెటీరియల్ ప్రాపర్టీస్ టెస్టింగ్ లేదా పెర్ఫార్మెన్స్ టెస్టింగ్ వంటి వివిధ టెస్టింగ్ పద్ధతుల ద్వారా పార్ట్ క్వాలిటీ మరియు ఫంక్షనాలిటీని ధృవీకరించడం.
- ప్యాకేజింగ్ మరియు షిప్పింగ్:కస్టమర్లు లేదా తుది-వినియోగదారులకు షిప్మెంట్ కోసం తుది ఉత్పత్తి యొక్క సరైన ప్యాకేజింగ్ మరియు లేబులింగ్.
పోస్ట్-మోల్డింగ్ కార్యకలాపాల ఎంపిక నిర్దిష్ట అప్లికేషన్ మరియు కావలసిన తుది ఉత్పత్తి లక్షణాలపై ఆధారపడి ఉంటుంది. ఇంజెక్షన్ మౌల్డింగ్ నిపుణులు, ఫినిషింగ్ మరియు అసెంబ్లీ నిపుణులు మరియు కస్టమర్ కోరుకున్న సంపూర్ణ ఉత్పత్తి నాణ్యత మరియు కార్యాచరణను సాధించడంలో కస్టమర్ల మధ్య సన్నిహిత సహకారం. సరైన ప్రణాళిక మరియు తయారీ ప్రక్రియలో పోస్ట్-మోల్డింగ్ కార్యకలాపాలను ఏకీకృతం చేయడం వలన సమర్థవంతమైన ఉత్పత్తి మరియు అధిక-నాణ్యత ఉత్పత్తుల యొక్క సకాలంలో డెలివరీని నిర్ధారించడంలో సహాయపడుతుంది.
ఇంజెక్షన్ మోల్డింగ్ vs. ఇతర ప్లాస్టిక్ తయారీ ప్రక్రియలు
ప్రతి ప్లాస్టిక్ తయారీ ప్రక్రియ ప్రయోజనాలు మరియు పరిమితులను కలిగి ఉంటుంది, వాటిని వివిధ అనువర్తనాలకు అనుకూలంగా చేస్తుంది.
- ఇంజెక్షన్ మౌల్డింగ్: ఇంజెక్షన్ మౌల్డింగ్ అనేది ప్లాస్టిక్ భాగాలను ఉత్పత్తి చేయడానికి అత్యంత బహుముఖ మరియు విస్తృతంగా ఉపయోగించే తయారీ ప్రక్రియ. ఇది అధిక ఉత్పత్తి సామర్థ్యం, ఖచ్చితమైన భాగం ప్రతిరూపణ మరియు సంక్లిష్ట జ్యామితిని సృష్టించే సామర్థ్యం వంటి ప్రయోజనాలను అందిస్తుంది. ఇంజెక్షన్ మౌల్డింగ్ అధిక-వాల్యూమ్ ఉత్పత్తి పరుగులకు అనుకూలంగా ఉంటుంది మరియు విస్తృత శ్రేణి థర్మోప్లాస్టిక్ పదార్థాలను ఉపయోగించడానికి అనుమతిస్తుంది. ఇది అద్భుతమైన డైమెన్షనల్ ఖచ్చితత్వం మరియు ఉపరితల ముగింపును అందిస్తుంది, ఇది ఆటోమోటివ్, వినియోగ వస్తువులు మరియు వైద్య పరికరాల వంటి వివిధ పరిశ్రమలకు అనువైనదిగా చేస్తుంది.
- బ్లో మోల్డింగ్: బ్లో మోల్డింగ్ అనేది సీసాలు, కంటైనర్లు మరియు ఆటోమోటివ్ భాగాలు వంటి బోలు ప్లాస్టిక్ భాగాలను ఉత్పత్తి చేయడానికి ప్రధానంగా ఉపయోగించే ప్రక్రియ. ఇది ప్లాస్టిక్ను కరిగించడం మరియు దానిని అచ్చు కుహరంలోకి పెంచడం, కావలసిన ఆకారాన్ని సృష్టించడం. బ్లో మోల్డింగ్ అధిక-వాల్యూమ్ ఉత్పత్తికి అనుకూలంగా ఉంటుంది మరియు ఏకరీతి గోడ మందంతో పెద్ద, తేలికైన భాగాలను ఉత్పత్తి చేయగలదు. అయినప్పటికీ, ఇంజెక్షన్ మౌల్డింగ్తో పోలిస్తే పార్ట్ కాంప్లెక్సిటీ మరియు మెటీరియల్ ఎంపిక పరంగా ఇది పరిమితం చేయబడింది.
- థర్మోఫార్మింగ్:థర్మోఫార్మింగ్ అనేది థర్మోప్లాస్టిక్ షీట్ను వేడి చేయడం మరియు అచ్చులు లేదా వాక్యూమ్ ఫార్మింగ్ని ఉపయోగించి దానిని ఆకృతి చేయడం ద్వారా ప్లాస్టిక్ భాగాలను ఉత్పత్తి చేయడానికి ఉపయోగించే ప్రక్రియ. ఇది ప్యాకేజింగ్, డిస్పోజబుల్ ఉత్పత్తులు మరియు ట్రేలు మరియు కవర్లు వంటి పెద్ద-స్థాయి ఉత్పత్తులలో సాధారణ వినియోగాన్ని కనుగొంటుంది. థర్మోఫార్మింగ్ పెద్ద భాగాలకు తక్కువ ఖర్చుతో కూడిన ఉత్పత్తిని అందిస్తుంది మరియు శీఘ్ర నమూనాను అనుమతిస్తుంది. అయినప్పటికీ, ఇంజెక్షన్ మౌల్డింగ్తో పోలిస్తే ఇది పార్ట్ కాంప్లెక్సిటీ, మెటీరియల్ ఎంపిక మరియు డైమెన్షనల్ ఖచ్చితత్వానికి సంబంధించి పరిమితులను కలిగి ఉంది.
- నూతన:ఎక్స్ట్రాషన్ అనేది ప్లాస్టిక్ ప్రొఫైల్లు, షీట్లు, ట్యూబ్లు మరియు ఫిల్మ్లను ఉత్పత్తి చేయడానికి నిరంతర ప్రక్రియ. ఇది ప్లాస్టిక్ రెసిన్ను కరిగించడం మరియు కావలసిన ఆకారాన్ని సృష్టించడానికి డై ద్వారా బలవంతం చేయడం. ఎక్స్ట్రాషన్ అనేది స్థిరమైన క్రాస్-సెక్షన్తో సుదీర్ఘమైన, నిరంతర ప్లాస్టిక్ ఉత్పత్తులను ఉత్పత్తి చేయడానికి అనుకూలంగా ఉంటుంది. ఎక్స్ట్రాషన్ అధిక ఉత్పత్తి రేట్లు మరియు వ్యయ-ప్రభావాన్ని అందిస్తుంది, ఇంజెక్షన్ మౌల్డింగ్తో పోలిస్తే ఇది సంక్లిష్ట భాగ జ్యామితులు మరియు ఖచ్చితమైన డైమెన్షనల్ నియంత్రణ పరంగా పరిమితం చేయబడింది.
- కంప్రెషన్ మోల్డింగ్:కంప్రెషన్ మోల్డింగ్ అనేది వేడిచేసిన అచ్చు కుహరంలో ముందుగా కొలిచిన మొత్తంలో థర్మోసెట్టింగ్ మెటీరియల్ని ఉంచడం మరియు అది నయమయ్యే వరకు అధిక పీడనం కింద కుదించడం. ఇది ఆటోమోటివ్ కాంపోనెంట్స్ మరియు ఎలక్ట్రికల్ ఇన్సులేషన్ వంటి అధిక బలం మరియు డైమెన్షనల్ స్టెబిలిటీతో భాగాలను ఉత్పత్తి చేయడంలో సాధారణ వినియోగాన్ని కనుగొంటుంది. కంప్రెషన్ మోల్డింగ్ మంచి భాగం అనుగుణ్యత, అధిక ఉత్పత్తి సామర్థ్యం మరియు విస్తృత శ్రేణి పదార్థాలను ఉపయోగించగల సామర్థ్యాన్ని అందిస్తుంది. అయినప్పటికీ, ఇంజెక్షన్ మౌల్డింగ్తో పోలిస్తే ఇది పార్ట్ కాంప్లెక్సిటీ మరియు సైకిల్ టైమ్ పరంగా పరిమితం చేయబడింది.
థర్మోప్లాస్టిక్ ఇంజెక్షన్ మోల్డింగ్ యొక్క అప్లికేషన్స్
వివిధ పరిశ్రమలు థర్మోప్లాస్టిక్ ఇంజెక్షన్ మౌల్డింగ్ను దాని బహుముఖ ప్రజ్ఞ, సామర్థ్యం మరియు వ్యయ-ప్రభావం కారణంగా విస్తృతంగా ఉపయోగిస్తాయి. థర్మోప్లాస్టిక్ ఇంజెక్షన్ మోల్డింగ్ యొక్క కొన్ని అప్లికేషన్లు:
- ఆటోమోటివ్ పరిశ్రమ: ఆటోమోటివ్ పరిశ్రమ అంతర్గత మరియు బాహ్య ట్రిమ్, డాష్బోర్డ్లు, డోర్ ప్యానెల్లు, బంపర్లు మరియు ఎలక్ట్రికల్ కనెక్టర్లతో సహా వివిధ భాగాలను తయారు చేయడానికి థర్మోప్లాస్టిక్ ఇంజెక్షన్ మోల్డింగ్ను విస్తృతంగా ఉపయోగిస్తుంది. ప్రక్రియ ఖచ్చితమైన భాగం ప్రతిరూపణ, సంక్లిష్ట జ్యామితులు మరియు తేలికైన పదార్థాలను అనుమతిస్తుంది, ఇంధన సామర్థ్యాన్ని మరియు డిజైన్ సౌలభ్యాన్ని మెరుగుపరుస్తుంది.
- వినియోగ వస్తువులు:గృహోపకరణాలు, ఎలక్ట్రానిక్ పరికరాలు, ప్యాకేజింగ్ కంటైనర్లు మరియు బొమ్మలు వంటి వినియోగ వస్తువులను ఉత్పత్తి చేయడంలో ఇంజెక్షన్ మౌల్డింగ్ విస్తృతమైన అనువర్తనాలను కనుగొంటుంది. ఈ ప్రక్రియ స్థిరమైన కొలతలు మరియు ఉపరితల ముగింపుతో మన్నికైన, అధిక-నాణ్యత ఉత్పత్తుల యొక్క భారీ ఉత్పత్తిని అనుమతిస్తుంది. ఇది అనుకూలీకరణ ఎంపికలు మరియు శీఘ్ర ఉత్పత్తి పునరావృతాలను కూడా అనుమతిస్తుంది.
- వైద్య పరికరాలు:సిరంజిలు, సర్జికల్ సాధనాలు, అమర్చగల భాగాలు మరియు డ్రగ్ డెలివరీ సిస్టమ్లతో సహా అనేక రకాల పరికరాలను ఉత్పత్తి చేయడానికి వైద్య పరిశ్రమలో ఇంజెక్షన్ మౌల్డింగ్ కీలక పాత్ర పోషిస్తుంది. ఈ ప్రక్రియ ఆరోగ్య సంరక్షణ రంగం యొక్క కఠినమైన నియంత్రణ అవసరాలను తీర్చే శుభ్రమైన, ఖచ్చితమైన మరియు జీవ అనుకూల భాగాల ఉత్పత్తిని నిర్ధారిస్తుంది.
- ఎలక్ట్రానిక్స్ మరియు ఎలక్ట్రికల్ పరిశ్రమ:ఎలక్ట్రానిక్స్ పరిశ్రమ ఎలక్ట్రికల్ కనెక్టర్లు, ఎన్క్లోజర్లు, స్విచ్లు మరియు ఇతర భాగాలను తయారు చేయడానికి ఇంజెక్షన్ మోల్డింగ్ను ఉపయోగిస్తుంది. ఈ ప్రక్రియ అధిక డైమెన్షనల్ ఖచ్చితత్వం, అద్భుతమైన ఉపరితల ముగింపు మరియు ఇన్సర్ట్ మోల్డింగ్ మరియు ఓవర్మోల్డింగ్ వంటి లక్షణాలను పొందుపరచగల సామర్థ్యాన్ని అందిస్తుంది, ఇది సంక్లిష్టమైన ఎలక్ట్రానిక్ అసెంబ్లీలను సమర్థవంతంగా ఉత్పత్తి చేయడానికి అనుమతిస్తుంది.
- ప్యాకేజింగ్ పరిశ్రమ:ఆహారం మరియు పానీయాలు, ఫార్మాస్యూటికల్స్ మరియు వ్యక్తిగత సంరక్షణతో సహా వివిధ పరిశ్రమలు సాధారణంగా ప్లాస్టిక్ ప్యాకేజింగ్ కంటైనర్లు, క్యాప్లు, మూసివేతలు మరియు బాటిళ్లను ఉత్పత్తి చేయడానికి ఇంజెక్షన్ మోల్డింగ్ను ఉపయోగిస్తాయి. ఈ ప్రక్రియ సమర్థవంతమైన తయారీ చక్రాలతో తేలికైన, మన్నికైన మరియు సౌందర్యపరంగా ఆకర్షణీయమైన ప్యాకేజింగ్ సొల్యూషన్ల సృష్టిని అనుమతిస్తుంది.
- ఏరోస్పేస్ ఇండస్ట్రీ:ఏరోస్పేస్ రంగం గాలి నాళాలు, బ్రాకెట్లు, అంతర్గత ప్యానెల్లు మరియు నిర్మాణ భాగాలు వంటి తేలికపాటి మరియు అధిక-పనితీరు గల భాగాలను తయారు చేయడానికి ఇంజెక్షన్ మోల్డింగ్ను ఉపయోగిస్తుంది. ఈ ప్రక్రియ అధునాతన మెటీరియల్స్ మరియు క్లిష్టమైన పార్ట్ జామెట్రీలను ఉపయోగించడానికి అనుమతిస్తుంది, బరువు తగ్గింపు మరియు మెరుగైన ఇంధన సామర్థ్యాన్ని అందించడంలో దోహదపడుతుంది.
థర్మోప్లాస్టిక్ ఇంజెక్షన్ మోల్డింగ్ యొక్క పర్యావరణ ప్రభావం
థర్మోప్లాస్టిక్ ఇంజెక్షన్ మౌల్డింగ్ అనేది దాని అనేక ప్రయోజనాల కారణంగా ఒక ప్రముఖ తయారీ ప్రక్రియ, అయితే దాని పర్యావరణ ప్రభావాన్ని పరిగణనలోకి తీసుకోవడం కూడా చాలా అవసరం. పరిగణించవలసిన కొన్ని అంశాలు ఇక్కడ ఉన్నాయి:
- మెటీరియల్ సమర్థత:థర్మోప్లాస్టిక్ ఇంజెక్షన్ మౌల్డింగ్ వ్యర్థాలను తగ్గించడం ద్వారా మెటీరియల్ సామర్థ్యాన్ని ప్రోత్సహిస్తుంది. ఈ ప్రక్రియ అచ్చులోకి ఇంజెక్ట్ చేయబడిన పదార్థంపై ఖచ్చితమైన నియంత్రణను ఉపయోగిస్తుంది, అదనపు పదార్ధం అవసరాన్ని తగ్గిస్తుంది. తయారీదారులు స్క్రాప్ లేదా తిరస్కరించబడిన భాగాలను తిరిగి ఉపయోగించేందుకు రీగ్రైండింగ్ మరియు రీసైక్లింగ్ పద్ధతులను కూడా ఉపయోగించుకోవచ్చు, దీని వలన పదార్థ వ్యర్థాలను మరింత తగ్గించవచ్చు.
- శక్తి వినియోగం:తయారీదారులు ఇంజెక్షన్ మోల్డింగ్ మెషీన్లను శక్తి-సమర్థవంతంగా రూపొందించారు, ఆధునిక మోడల్లు సర్వో మోటార్లు మరియు వేరియబుల్ స్పీడ్ డ్రైవ్ల వంటి అధునాతన సాంకేతికతలను కలిగి ఉంటాయి. ఈ లక్షణాలు మౌల్డింగ్ సమయంలో విద్యుత్ వినియోగాన్ని తగ్గించడం ద్వారా శక్తి వినియోగాన్ని ఆప్టిమైజ్ చేస్తాయి, ఫలితంగా తక్కువ శక్తి అవసరాలు మరియు పర్యావరణ ప్రభావం తగ్గుతుంది.
- వ్యర్థ పదార్థాల నిర్వహణ:పదార్థ వ్యర్థాలను తగ్గించేటప్పుడు, తయారీదారులు మిగిలిపోయిన పదార్థాలు, స్ప్రూలు లేదా రన్నర్లను నిర్వహించడానికి సరైన వ్యర్థ నిర్వహణ పద్ధతులను అమలు చేయాలి. తయారీదారులు ఇంజెక్షన్ మౌల్డింగ్ సమయంలో ఉత్పత్తి చేయబడిన ప్లాస్టిక్ వ్యర్థాలను సేకరించి, తిరిగి ఉపయోగించేందుకు రీసైక్లింగ్ ప్రోగ్రామ్లను ఏర్పాటు చేయవచ్చు, తద్వారా పల్లపు ప్రాంతాలకు పంపే వ్యర్థాలను తగ్గించవచ్చు.
- ఉద్గార తగ్గింపు: థర్మోప్లాస్టిక్ ఇంజెక్షన్ మౌల్డింగ్ సాధారణంగా ఇతర తయారీ ప్రక్రియల కంటే తక్కువ ఉద్గారాలను ఉత్పత్తి చేస్తుంది. తయారీదారులు పర్యావరణ అనుకూల పదార్థాలను ఉపయోగించడం, శక్తి-సమర్థవంతమైన పరికరాలను అమలు చేయడం మరియు విడుదల చేసిన ఏవైనా ఉద్గారాలను సంగ్రహించడానికి అధునాతన ఎగ్జాస్ట్ మరియు ఫిల్ట్రేషన్ సిస్టమ్లను ఉపయోగించడం ద్వారా ఉద్గారాలను తగ్గించవచ్చు.
- స్థిరమైన మెటీరియల్ ఎంపికలు:థర్మోప్లాస్టిక్ పదార్థాల ఎంపిక ఇంజెక్షన్ మౌల్డింగ్ యొక్క పర్యావరణ స్థిరత్వాన్ని గణనీయంగా ప్రభావితం చేస్తుంది. బయోడిగ్రేడబుల్ లేదా బయో-ఆధారిత ప్లాస్టిక్లను ఎంచుకోవడం, అలాగే రీసైకిల్ చేయబడిన లేదా పునర్వినియోగపరచదగిన పదార్థాలను ఎంచుకోవడం, ప్రక్రియ యొక్క మొత్తం పర్యావరణ పాదముద్రను తగ్గించడంలో సహాయపడుతుంది.
జీవిత చక్రం పరిగణనలు: అచ్చు ఉత్పత్తి యొక్క మొత్తం జీవిత చక్రాన్ని పరిగణనలోకి తీసుకోవడం దాని పర్యావరణ ప్రభావాన్ని అంచనా వేయడానికి అవసరం. డిజైన్ మరియు మెటీరియల్ ఎంపిక దశల సమయంలో, తయారీదారులు భాగం యొక్క మన్నిక, దాని పునర్వినియోగ సామర్థ్యం మరియు జీవితాంతం పారవేయడం లేదా పునర్వినియోగం కోసం సంభావ్యత వంటి అంశాలను పరిగణించాలి.
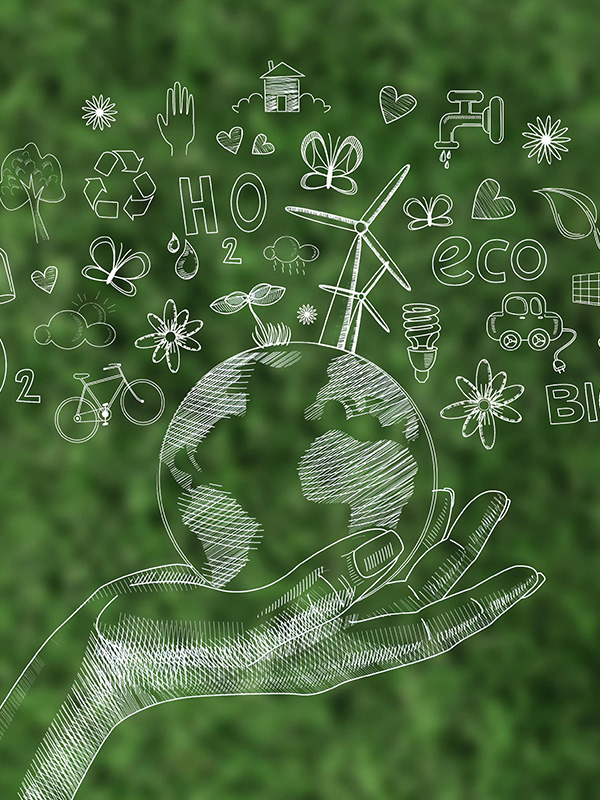
థర్మోప్లాస్టిక్ ఇంజెక్షన్ మోల్డింగ్ యొక్క భవిష్యత్తు
థర్మోప్లాస్టిక్ ఇంజెక్షన్ మౌల్డింగ్ యొక్క భవిష్యత్తు ఆశాజనకంగా కనిపిస్తోంది, సాంకేతికతలో నిరంతర పురోగతులు మరియు వివిధ పరిశ్రమలలో అధిక-నాణ్యత, ఖచ్చితమైన భాగాలకు పెరిగిన డిమాండ్. రాబోయే సంవత్సరాల్లో ఆశించిన కొన్ని కీలక పరిణామాలు:
- సామర్థ్యాన్ని మెరుగుపరచడానికి మరియు ఖర్చులను తగ్గించడానికి ఆటోమేషన్ మరియు రోబోటిక్స్ యొక్క పెరిగిన ఉపయోగం.
- పార్ట్ పనితీరును మెరుగుపరచడానికి మరియు కొత్త అప్లికేషన్లను ప్రారంభించడానికి కొత్త పదార్థాలు మరియు ప్రక్రియలను అభివృద్ధి చేయడంపై ప్రయత్నాలు దృష్టి సారించాయి.
- ఇది ఇంజెక్షన్ మౌల్డింగ్ యొక్క పర్యావరణ ప్రభావాన్ని తగ్గించడానికి రీసైకిల్ చేసిన పదార్థాలను ఉపయోగించడం మరియు శక్తి వినియోగాన్ని ఆప్టిమైజ్ చేయడం వంటి స్థిరమైన పద్ధతుల యొక్క పెరుగుతున్న స్వీకరణ.
- డిజైన్ మరియు ప్రొడక్షన్ ప్రాసెస్లను మెరుగుపరచడానికి 3D ప్రింటింగ్ మరియు సిమ్యులేషన్ సాఫ్ట్వేర్ వంటి డిజిటల్ టెక్నాలజీల యొక్క గొప్ప ఏకీకరణ.
గ్లోబల్ ఇంజెక్షన్ మోల్డింగ్ మార్కెట్ విస్తరిస్తోంది, ముఖ్యంగా అభివృద్ధి చెందుతున్న ఆర్థిక వ్యవస్థలలో, వివిధ పరిశ్రమలలో ప్లాస్టిక్ ఉత్పత్తులకు పెరుగుతున్న డిమాండ్తో నడపబడుతుంది.
సరైన ఇంజెక్షన్ మోల్డింగ్ భాగస్వామిని ఎంచుకోవడం
మీ ప్రాజెక్ట్ విజయవంతం కావడానికి సరైన ఇంజెక్షన్ మోల్డింగ్ భాగస్వామిని ఎంచుకోవడం చాలా ముఖ్యం. అనుకూలమైన మరియు దీర్ఘకాలిక భాగస్వామ్యాన్ని నిర్ధారించడానికి బహుళ ఎంపికలను విశ్లేషించడానికి, సైట్ సందర్శనలను నిర్వహించడానికి మరియు సమగ్ర చర్చలలో పాల్గొనడానికి సమయాన్ని వెచ్చించండి.
- నైపుణ్యం మరియు అనుభవం:పరిశ్రమలో విస్తృతమైన జ్ఞానం మరియు అనుభవం ఉన్న ఇంజెక్షన్ మోల్డింగ్ భాగస్వామి కోసం చూడండి. వారు వివిధ రంగాలలోని ఖాతాదారులకు అధిక-నాణ్యత ఉత్పత్తులు మరియు పరిష్కారాలను అందించడంలో నిరూపితమైన ట్రాక్ రికార్డ్ను కలిగి ఉండాలి. వివిధ పదార్థాలు, అచ్చు నమూనాలు మరియు తయారీ ప్రక్రియలపై వారి అవగాహనను పరిగణించండి.
- తయారీ సామర్థ్యాలు: ఇంజెక్షన్ మోల్డింగ్ భాగస్వామి యొక్క తయారీ సామర్థ్యాలను అంచనా వేయండి. మీ ప్రాజెక్ట్ అవసరాలను నిర్వహించడానికి వారికి ఆధునిక యంత్రాలు మరియు సాంకేతికతలతో కూడిన చక్కటి సదుపాయం ఉందని నిర్ధారించుకోండి. వారి ఉత్పత్తి సామర్థ్యం, విభిన్న భాగాల పరిమాణాలు మరియు సంక్లిష్టతలను నిర్వహించగల సామర్థ్యం మరియు మీరు కోరుకున్న ఉత్పత్తి వాల్యూమ్లు మరియు సమయపాలనలను తీర్చగల సామర్థ్యాన్ని పరిగణించండి.
- నాణ్యత హామీ:ఇంజెక్షన్ మౌల్డింగ్లో నాణ్యత చాలా ముఖ్యమైనది. సంభావ్య భాగస్వామి యొక్క నాణ్యత నియంత్రణ వ్యవస్థలు మరియు ధృవపత్రాలను మూల్యాంకనం చేయండి. ఖచ్చితమైన నాణ్యతా ప్రమాణాలను అనుసరించే, పటిష్టమైన తనిఖీ ప్రక్రియలను కలిగి ఉన్న భాగస్వాముల కోసం చూడండి మరియు భాగం నాణ్యత మరియు అనుగుణ్యతను నిర్ధారించడానికి సమగ్ర పరీక్షను నిర్వహించండి.
- డిజైన్ మరియు ఇంజనీరింగ్ మద్దతు:విశ్వసనీయమైన ఇంజెక్షన్ మౌల్డింగ్ భాగస్వామి, తయారీ సామర్థ్యం కోసం మీ పార్ట్ డిజైన్ను ఆప్టిమైజ్ చేయడానికి డిజైన్ మరియు ఇంజనీరింగ్ మద్దతును అందించాలి. వారు మెటీరియల్ ఎంపిక, అచ్చు రూపకల్పన మరియు పార్ట్ క్వాలిటీ మరియు సామర్థ్యాన్ని మెరుగుపరచడానికి ప్రాసెస్ ఆప్టిమైజేషన్పై విలువైన ఇన్పుట్ను అందించగల నైపుణ్యం కలిగిన ఇంజనీర్లను కలిగి ఉండాలి.
- ఖర్చు పోటీతత్వం:ఖర్చు మాత్రమే నిర్ణయించే అంశం కానప్పటికీ, ఇంజెక్షన్ మోల్డింగ్ భాగస్వామి యొక్క ధర మరియు వ్యయ పోటీతత్వాన్ని అంచనా వేయడం చాలా అవసరం. వివరణాత్మక కోట్లను అభ్యర్థించండి మరియు టూలింగ్ ఖర్చులు, మెటీరియల్ ఖర్చులు, లేబర్ ఖర్చులు మరియు వారు అందించే ఏవైనా అదనపు సేవలను పరిగణించండి.
- కమ్యూనికేషన్ మరియు సహకారం:విజయవంతమైన భాగస్వామ్యానికి సమర్థవంతమైన కమ్యూనికేషన్ మరియు సహకారం అవసరం. ఇంజెక్షన్ మోల్డింగ్ భాగస్వామి మంచి కమ్యూనికేషన్ ఛానెల్లను కలిగి ఉన్నారని, మీ విచారణలకు ప్రతిస్పందిస్తున్నారని మరియు సాధారణ ప్రాజెక్ట్ అప్డేట్లను అందించగలరని నిర్ధారించుకోండి. మేము మీ అవసరాలను తీర్చగలమని మరియు ఏవైనా సవాళ్లను తక్షణమే పరిష్కరించడంలో సహకార విధానం సహాయం చేస్తుంది.
- కస్టమర్ సూచనలు మరియు సమీక్షలు:ఇంజక్షన్ మోల్డింగ్ భాగస్వామితో ఇతర క్లయింట్ల అనుభవాల గురించి అంతర్దృష్టులను పొందడానికి కస్టమర్ సూచనలను వెతకండి లేదా సమీక్షలు/టెస్టిమోనియల్లను చదవండి. ఈ సమాచారాన్ని పొందడం వలన వారి విశ్వసనీయత, సత్వరత్వం మరియు కస్టమర్ సంతృప్తి స్థాయిని గుర్తించడంలో సహాయపడుతుంది.
ముగింపు
థర్మోప్లాస్టిక్ ఇంజెక్షన్ మోల్డింగ్ అనేది ప్లాస్టిక్ భాగాలను పెద్ద పరిమాణంలో తయారు చేయడానికి బహుముఖ మరియు ఖర్చుతో కూడుకున్న పద్ధతి. అధిక ఖచ్చితత్వం మరియు అనుగుణ్యతతో సంక్లిష్టమైన ఆకృతులను ఉత్పత్తి చేయగల దాని సామర్థ్యం ఆటోమోటివ్, మెడికల్, ఎలక్ట్రానిక్స్ మరియు వినియోగ వస్తువులతో సహా వివిధ పరిశ్రమలకు ప్రముఖ ఎంపికగా మారింది. థర్మోప్లాస్టిక్ ఇంజెక్షన్ మౌల్డింగ్ యొక్క వివిధ అంశాలను అర్థం చేసుకోవడం ద్వారా, దాని ప్రయోజనాలు, అప్రయోజనాలు మరియు డిజైన్ పరిగణనలతో సహా, మీ వ్యాపార అవసరాల కోసం సరైన ఇంజెక్షన్ మోల్డింగ్ భాగస్వామిని ఎంచుకోవడం గురించి మీరు సమాచారం నిర్ణయాలు తీసుకోవచ్చు.