Kore'deki vaka
Kore Otomobil Şirketleri için Plastik Enjeksiyon Parçalarının Et Kalınlığı Yapısal Tasarımı
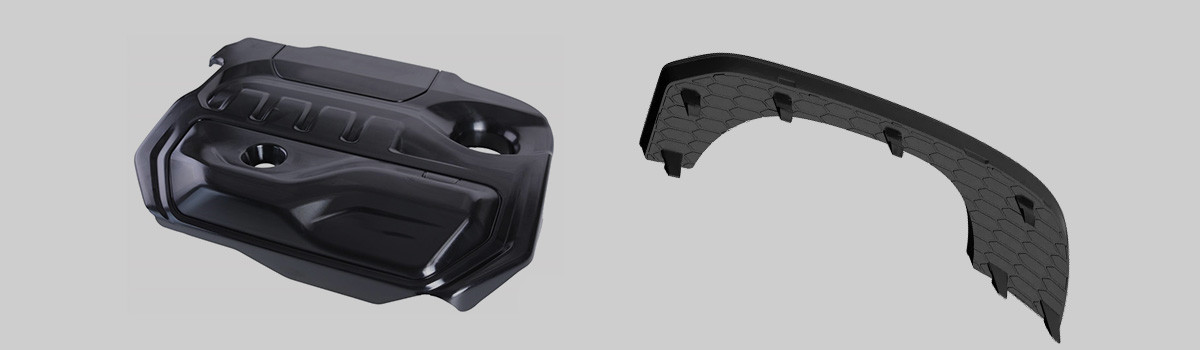
Plastik parçalar bir araba için çok ithaldir ve yapısal sağlamlığı kullanım ömrü üzerinde etkili olacak ve güvenli sürüş sağlayacaktır, bu nedenle Koreli Otomobil üreticileri plastik parçaları çok katı bir şekilde satın almaktadır. Otomobil endüstrisi bir arabada çok fazla plastik parça kullanacak, Kore yerel enjeksiyon şirketleri büyük tedarik sağlayamıyor ve bu Otomobil üreticileri, tıpkı Çin'den DJmolding gibi denizaşırı plastik parçalar satın alacak.
Plastik parçalar bir araba için çok önemlidir, peki Koreli Otomobil şirketleri için plastik enjeksiyon parçalarının duvar kalınlığı yapısal olarak nasıl tasarlanır? Şimdi, DJmolding size plastik enjeksiyon parçalarının yapısal kalınlık tasarımını gösterecek.
duvar kalınlığı tanımı
Duvar kalınlığı, plastik parçaların temel bir yapısal özelliğidir. Plastik parçaların dış yüzeyine dış cidar, iç yüzeyine iç cidar deniliyorsa o zaman dış cidar ile iç cidar arasında bir kalınlık değeri vardır. Değere duvar kalınlığı denir. Yapısal tasarım sırasında yazılım üzerinden kabuk çıkarıldığında girilen değere de duvar kalınlığı denilebilir.
Duvar kalınlığının işlevi
Ürünlerin dış duvarı için
Parçaların dış duvarı, parçaların dış kabuğu gibidir. İç duvar, parçaların yapısal iskeletleridir. Parçaların dış duvarlarının yüzey işlemleriyle farklı görünüm efektleri elde edilebilir. İç duvar sadece yapıları (nervür, vidalı çubuk, toka vb.) birbirine bağlar ve parçalara belirli bir sağlamlık sağlar. Bu arada, enfeksiyon kalıplama işlemi sırasında diğer yapılar doldurulabilir. İç ve dış duvarlar (soğutma, montaj) için özel gereksinimler yoktur. Normalde, parçaların iç kısımları çevre tarafından zarar görmesini veya müdahale etmesini önlemek için yeterli güce sahip olabilmesi için bir bütün haline getirilir.
Ürünün iç parçaları için
Bir yatak veya bağlantı braketi olarak, gerçek koşullara göre dış duvarda başka yapılar (nervürler, vida çubukları, tokalar vb.) oluşturabilen iç ve dış duvarlar için katı gereklilikler yoktur. Bununla birlikte, uygun imalat uğruna (esas olarak, ön ve arka kalıpların ayrıldığında, plastik parçaların arka kalıpta tutulması için, dış duvarın olabildiğince basit tasarlanması gereken kalıbın ön yüzü anlamına gelir. . Değilse, ön ve arka kalıpların çekim açısını ayarlayarak, hatta ön kalıpta bir yüksük veya arka kalıpta belirli bir küçük alt kesim yapın) ve genellikle diğer yapıları iç duvarda tasarlayın.
Kabuk parçaları veya iç parçalar fark etmeksizin, kalıbın ejektör piminin alıcı yüzeyi olarak duvar kalınlığı esastır ve parçaların sorunsuz bir şekilde çıkarılmasını sağlar.
Duvar kalınlığının tasarım ilkeleri:
Plastik aksamların tasarımında, bir binanın temeli olarak esas olan duvar kalınlığı önceliklidir. Diğer yapıların üzerine inşa edilmesi gerekiyor. Bu arada plastik parçaların mekanik özelliklerini, şekillendirilebilirliğini, görünümünü, maliyetini de etkiler. Bu nedenle, duvar kalınlığı, tasarım için yukarıdaki faktörlere dayanmalıdır.
Duvar kalınlığının belirli bir değer olması gerektiğinden bahsetmiştir. Bir değer varsa, eşit duvar kalınlığını ifade eder. Birçok değer varsa, eşit olmayan duvar kalınlığını ifade eder. Çift veya düzensiz arasındaki fark daha sonra tanıtılacaktır. Şimdi, izlenecek duvar kalınlığı tasarımı ilkesinden bahsedeceğiz.
1. Mekanik özellikler ilkesine dayalı olarak:
Kabuk parçaları veya iç parçalar fark etmeksizin her ikisinin de belirli bir güç seviyesine ihtiyacı olduğundan bahsetmiştir. Diğer faktörlerin yanı sıra, parçaların oluşumu göz önünde bulundurulduğunda direnç serbest bırakma kuvveti gereklidir. Parça çok ince ise kolayca deforme olur. Genel olarak, duvar kalınlığı ne kadar kalınsa, parçaların mukavemeti de o kadar yüksek olur (duvar kalınlığı %10 artar, mukavemet yaklaşık %33 artar). Et kalınlığının belirli bir aralığı aşması durumunda, et kalınlığına eklemek, büzülme ve gözeneklilik nedeniyle parçaların mukavemetini düşürecektir. Duvar kalınlığının artması, parçaların mukavemetini azaltacak ve ağırlığı artıracaktır, enjeksiyon kalıplama dairesini, maliyeti vb. Sertliği artırmak için nervürler, eğriler, oluklu yüzeyler, sertleştiriciler vb. gibi geometrik özelliklerin kullanılması en iyisidir.
Alan sınırlamaları ve diğer faktörler nedeniyle, bazı parçaların mukavemetinin esas olarak duvar kalınlığı tarafından gerçekleştirildiği göz ardı edilmemektedir. Bu nedenle, mukavemet önemli bir faktör ise, mekanik simülasyon taklit edilerek uygun bir duvar kalınlığının belirlenmesi önerilir. Nitekim duvar kalınlığı değeri aşağıdaki formalite ilkelerine de uyulmalıdır.
2. Şekillendirilebilirlik ilkesine dayalı olarak:
Gerçek duvar kalınlığı, ön ve arka kalıplar arasındaki kalıp boşluğunun kalınlığıdır. Erimiş reçine kalıp boşluğunu doldurup soğuduğunda duvar kalınlığı elde edilir.
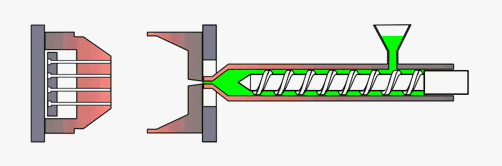
1) Enjeksiyon ve doldurma işlemi sırasında erimiş reçine nasıl akar?
Boşluğun içindeki plastiğin akışı, laminer akış olarak kabul edilebilir. Akışkanlar mekaniği teorisine göre, laminer akışkan, kesme kuvvetinin etkisi altında kayan yan yana sıvı tabakaları olarak kabul edilebilir.
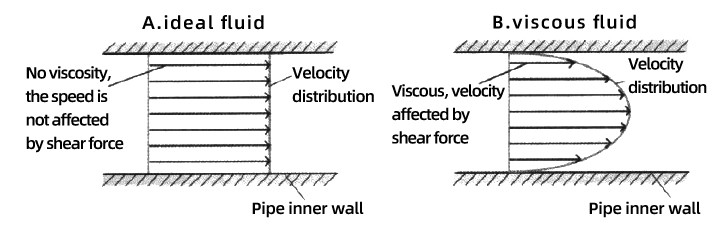
Enjeksiyon kalıplama işlemi sırasında, erimiş reçine yollukların duvarı (kalıp boşluğunun duvarı) ile temas eder ve akış katmanlarının ilk olarak soğutulan yollukların duvarına (veya kalıp boşluğunun duvarına) yapışmasını sağlar. Hız sıfırdır ve bitişik sıvı tabakası ile üretilen sürtünme direnci vardır. Bu şekilde ilet, orta akış katmanının hızı en yüksektir. Her iki tarafta yolluk duvarının (veya kalıp boşluğu duvarının) yakınında laminer hızın azaldığı akış şekli.
Orta tabaka akışkan tabakadır ve deri tabakası katılaşmış tabakadır. Soğuma süresi geçtikçe lanet tabakası artacaktır. Akışkan tabakasının enine kesit alanı kademeli olarak küçülecektir. Dolgu ne kadar sert olursa, enjeksiyon kuvveti o kadar büyük olur. Aslında, enjeksiyonu gerçekleştirmek için eriyiği kalıp boşluğuna itmek daha zordur.
Bu nedenle, duvar kalınlığının boyutunun, enjeksiyon kalıplama işlemi sırasında enjeksiyon kalıplanmış parçaların akışı ve doldurulması üzerinde büyük bir etkisi vardır ve değeri çok küçük olamaz.
2) Plastik eriyiğin viskozitesi de akışkanlık üzerinde büyük bir etkiye sahiptir.
Eriyik dış etki altındayken ve katmanlar arasında göreli hareket olduğunda, sıvı katmanları arasındaki göreli harekete müdahale etmek için üretilen dahili sürtünme kuvveti olacaktır. Akışkan tarafından üretilen iç sürtünme kuvvetine viskozite denir. Viskozite kuvvetinin dinamik viskozite (veya viskozite katsayısı) ile değerlendirilmesi. Kayma geriliminin eriyiğin kayma hızına sayısal olarak oranı.
Eriyiklerin viskozitesi, plastik eriyiğin akma kolaylığının özelliklerini yansıtır. Eriyik akış direncinin bir ölçüsüdür. Viskozite ne kadar yüksek olursa, sıvı direnci o kadar büyük olur ve akış o kadar zor olur. Eriyik viskozitesini etkileyen etkili faktörler yalnızca moleküler yapı ile ilişkili değildir, aynı zamanda sıcaklık, basınç, kayma hızı, katkı maddeleri vb. ve enjeksiyon kalıplama işlemi sırasındaki diğer faktörler, enjeksiyon kalıplama işleminde plastiğin akışkanlığını değiştirmek için değiştirilebilir.Gelecekte, duruma bağlı olarak likidite konusunda bir makale yazacağız.)
Gerçek uygulamada ise eriyik İndeksi, plastik malzemelerin işleme sırasındaki akışkanlığını gösterir. Değer ne kadar yüksek olursa, malzemenin akışkanlığı o kadar iyi olur. Aksine, malzemenin akışkanlığı daha kötü olacaktır.
Bu nedenle, özellikle karmaşık yapılara sahip enjeksiyon kalıplama parçaları için, iyi akışkanlığa sahip plastiğin kalıp boşluğunu doldurması daha kolaydır.
Yaygın olarak kullanılan plastiklerin akışkanlığı, kalıp tasarım gereksinimlerine göre kabaca üç kategoriye ayrılabilir:
①İyi akışkanlık: PA, PE, PS, PP, CA, poli(4) metil pentilen;
②Orta akışkanlık: polistiren serisi reçineler (ABS, AS gibi), PMMA, POM, PPO;
③Zayıf akışkanlık: PC, sert PVC, PPO, PSF, PASF, floroplastikler.
Yukarıdaki Şekilden de görebileceğimiz gibi, akışkanlığı en düşük olan malzeme, minimum duvar kalınlığı gereksinimleri daha yüksek olacaktır. Bu, laminer akış teorisinde tanıtıldı.
Yukarıda tavsiye edilen duvar kalınlığı değeri sadece ihtiyatlı bir sayıdır. Gerçek uygulamada, parçaların boyutları küçük, orta ve büyük içerir, yukarıdaki resim referans aralığını belirtmez.
3) Akış uzunluğu oranına göre hesaplayabiliriz
Plastiğin akış uzunluğu oranı, plastik eriyik akışının uzunluğunun (L) duvar kalınlığına (T) oranını ifade eder. Bu, belirli bir duvar kalınlığı için, akış uzunluğu oranı ne kadar yüksekse, plastik eriyiğin o kadar uzağa aktığı anlamına gelir. Veya plastik eriyik akışının uzunluğu belli olduğunda, akış uzunluğu oranı ne kadar büyük olursa, duvar kalınlığı o kadar küçük olabilir. Böylece, plastiğin akış uzunluğu oranı, plastik ürünlerin beslenme sayısını ve dağıtımını doğrudan etkiler. Ayrıca plastiğin duvar kalınlığını da etkiler.
Daha doğru olmak gerekirse, duvar kalınlığının spesifik değer aralığı, akış uzunluğu oranının hesaplanmasıyla elde edilebilir. Aslında bu değer malzeme sıcaklığı, kalıp sıcaklığı, parlatma derecesi vs. ile alakalıdır. sadece yaklaşık bir aralık değeridir, farklı koşullar farklıdır, kesin olması zordur ama referans değer olarak kullanılabilir.
Akış uzunluğu oranının hesaplanması:
L/T (toplam) = L1/T1 (ana kanal) + L2/T2 (bölünmüş kanal) + L3/T3 (ürün) Hesaplanan akış uzunluğu oranı, fiziksel özellik tablosunda verilen değerden küçük olmalıdır, aksi takdirde Kötü doldurma fenomeni olmak.
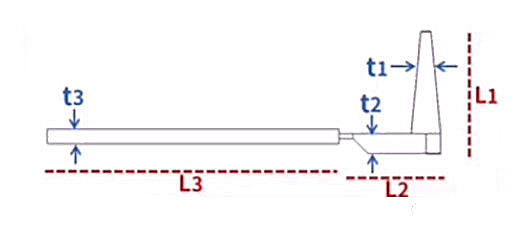
Örneğin
Kauçuk kabuk, PC malzeme, et kalınlığı 2, dolum mesafesi 200, yolluk 100, yolluk çapı 5'dir.
Calculation: L/T(total)=100/5+200/2=120
PC'nin akış uzunluğu oranı için referans değeri 90'dır ve bu, referans değerinden açıkça daha yüksektir. Enjeksiyonun zor olması ve hatta özel yüksek performanslı enjeksiyon kalıplama makineleri gerektirmesi nedeniyle enjeksiyon hızının ve basıncının artırılması gerekir. İki besleme noktası kullanırsa veya besleme noktası konumunu değiştirirse, ürünlerin dolum mesafesi 100'e düşürülebilir, bu da L/T(toplam)=100/5+100/2=70'tir. Uzunluk oranı artık referans değerinden daha azdır ve enjeksiyon kalıplama için kolaydır. Duvar kalınlığı 100 olarak değiştirildiğinde L/T(toplam)=5/200+3/87=3, bu da normal enjeksiyon kalıplamaya izin verir.
3. Görünüm ilkesine göre:
Parçaların görünümünü etkileyen duvar kalınlığının spesifik performansı aşağıdaki gibidir:
1) Düzensiz duvar kalınlığı: yüzey büzülmesi (büzülme, çukurlar, kalın ve ince baskılar gibi görünüm kusurları dahil), eğilme deformasyonu, vb.
2) Aşırı duvar kalınlığı: Yüzey büzülmesi ve iç büzülme delikleri gibi kusurlar.
3) Duvar kalınlığı çok küçük: tutkal eksikliği, yüksük baskı, çarpılma ve deformasyon gibi kusurlar.
büzülme veya gözeneklilik
büzülme veya gözeneklilik normalde kalın et kalınlığı alanlarında meydana gelir. Mekanizma: malzeme katılaşma prensibine göre enjeksiyon kalıplama işlemi sırasında iç gözeneklilik ve yüzey büzülmesi, soğutma işlemi sırasındaki sürekli büzülmeden kaynaklanır. Büzülme, arkadaki donmuş konumda yoğunlaştığı, ancak hemen telafi edilemediği durumlarda, iç kısımda çekme ve gözeneklenme olasılığı daha yüksektir.
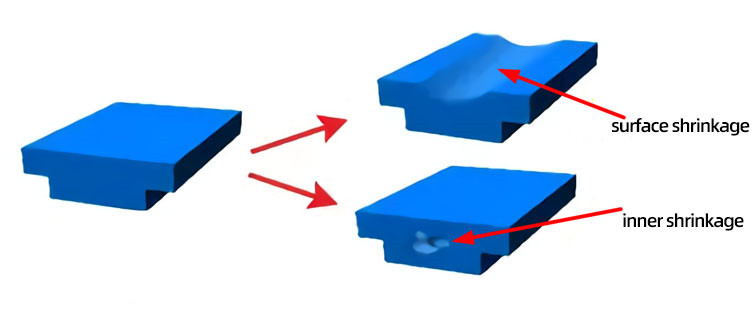
Yukarıdaki duvar kalınlığının tasarım ilkeleri, mekanik özellikler, şekillendirilebilirlik, görünüm, maliyet olmak üzere dört açıdan tanıtılmaktadır. Duvar kalınlığının tasarımını açıklamak için bir cümle kullanırsanız, yani enjeksiyonla kalıplanmış parçaların duvar kalınlığının değeri, mekanik özelliklerin ve işleme performansının karşılanması koşulu altında mümkün olduğu kadar küçük ve mümkün olduğunca tekdüze olmalıdır. Değilse, düzgün bir şekilde geçiş yapılmalıdır.
DJmolding, global pazar için plastik parçaların tasarım ve üretim hizmetlerini sunuyor, projenize başlamak istiyorsanız, lütfen hemen bizimle iletişime geçin.