Enjeksiyon kalıplamada Yaygın Kalıplama Hatalarına Çözümler
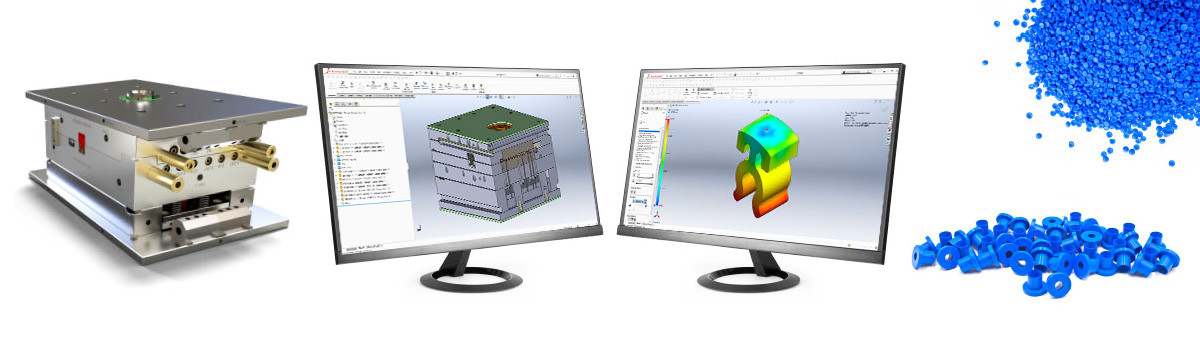
Plastik enjeksiyon kalıplama parçalarını işlemek için kalıpları kullanırken kusurlar yaygındır ve bu, işleme verimliliğini büyük ölçüde etkiler. Aşağıdakiler, plastik enjeksiyon kalıp parçaları için yaygın kalıplama kusurları ve çözümleridir.
Kısa çekimler
Kısa çekimler, kalıpların tam olarak doldurulmaması nedeniyle yapılan ürünlerin eksik olduğunu ifade eder.
Bu kusur genellikle kapıdan en uzak noktada veya sadece kalıp üzerindeki dar alanlardan ulaşılabilen kısımlarda görülür, çünkü dar alanlar eriyiklerin akışını etkileyebilir.
Kısa atış, mikro akış izlerine neden olabilir veya ürünün büyük bir kısmının açıkça kaybolmasına neden olabilir.
Nedeni:
Kısa çekimlerin nedenleri şunları içerir:
Kalıba enjekte edilen hammadde yeterli değildir.
Eriyiklerin direnci büyüktür, bu da kalıbın tamamen doldurulamamasına neden olur.
Kalıbın havalandırması zayıftır ve eriyiği bloke eden kavitasyon oluşumuna neden olarak eriyiğin kalıbın bazı bölgelerine akmasını engeller.
çapak
Çapaklar, kalıp boşluğundan ekstrüde edilen fazla ham maddelerin ürüne yapışmasından kaynaklanır.
Bu kusur, ürünün kenarlarında veya kalıbın oluşturduğu her parçada olacaktır. Hammadde kalıptan veya hareketli ve sabitleyici kalıpların yapıştırma yerlerinden taşabilir.
Kalıp göbeğinde hidrolik basınçtan veya açısal pimden kaynaklanan çapaklar da bulunabilir.
Çapakların şiddeti değişir, bazen ince, bazen daha kalın.
Nedeni:
Çapakların nedenleri şunları içerir:
Sıkıştırma kalıbı yüzeyi hasarlı veya aşırı derecede aşınmış.
Hareketli kalıp ve sabitleme kalıbı kilitlendiğinde yerinden çıkar.
Hammaddenin kalıp içindeki basıncı, kalıp sıkıştırma kuvvetinden daha yüksektir.
Yukarıda belirtilen üçüncü durum, çeşitli sebeplerden kaynaklanacaktır. Aşağıdaki durumlarda hammaddenin basıncı kalıp tutma kuvvetinden yüksektir.
Enjeksiyon kalıbının ilk aşamasında (kalıp doldurma aşaması) çok fazla hammadde doldurulur ve bu da kalıbın içindeki basıncı artırır.
Kalıp doldurma işlemi sırasında, eriyik akışının büyük direnci kalıbın içindeki basıncı da yükseltecektir.
Basınç tutma aşamasında kalıp boşluğu basıncı çok yüksektir.
Kalıp sıkıştırma kuvveti yeterli değil.
bozulma
Ayrışma birçok sonuca yol açabilir. Sorunun boyutu ve ciddiyeti de değişir. En ciddi durumda, ürünün renginin tamamen solmasına ve zayıf mekanik özelliklere neden olabilir. Yerel bozulma yalnızca koyu çizgilere veya noktalara neden olur.
Nedeni:
Bozunma, hammaddenin zarar görmesi sonucu oluşur. Plastik oluşturan uzun zincirli moleküller, aşırı ısı veya aşırı kayma gerilimi etkisi altında ayrışır. Moleküllerin ayrışması sırasında uçucu gaz, bozunma sürecini hızlandıracak ve bu da ham maddenin renginin solmasına neden olacaktır. Büyük miktarda molekülün ayrışması, sonunda ham maddenin içeriğini bozacak ve mekanik özellikler üzerinde olumsuz etkiye neden olacaktır.
Yerel bozunma, malzeme kovanının eşit olmayan sıcaklığından kaynaklanabilir.
Bozulma aşağıdaki durumlarda meydana gelebilir:
Hammadde, malzeme varilinde veya sıcak yolluk sisteminde aşırı ısıtılıyor.
Hammadde varilde çok uzun süre kalır.
Enjeksiyon kalıplama işlemi sırasında ham maddeye uygulanan kesme gerilimi çok fazladır. Püskürtme uçları tıkalıysa veya geçitler ve yolluk çok darsa, kesme gerilimini artıracaktır.
Deformasyon
Normal durumlarda ürünlerin şekilleri kalıpların şekline uygun olmalıdır. Deformasyon, ürünlerin deformasyonunu ifade eder.
Durum kötüleştiğinde ürünler kalıptan çıkarıldığında tamamen deforme olacaktır. Durum ciddi olmadığında, ürün şeklinde küçük düzensizlikler görünecektir.
Uzun ancak desteksiz kenarlar veya geniş düzlemler, deformasyona en yatkın alanlardır.
Nedeni:
Deformasyon nedenleri:
Kalıp serbest bırakıldığında sıcaklık çok yüksektir.
Kalın ve ince bölgelerde soğuma süresi veya hareketli kalıp ile sabitleme kalıbında kalıp sıcaklık farkı farklı olduğundan, ürünlerin iç çekmeleri farklıdır.
Doldurma sırasında kalıp akışı pürüzsüz değildir ("Donma yönü" olarak adlandırılır) veya kalıp boşluğu içindeki basınç, basınç tutma aşamasında çok yüksektir.
Safsızlıklar
Safsızlıklar genellikle farklı renklerde lekeler, yamalar veya şeritler şeklinde görünür. En yaygın olanı siyah noktadır.
Safsızlıklar sadece küçük noktalar olabilir, ancak ciddi olduğunda bariz şeritler veya büyük bir renk bozulması da olabilir.
Nedeni:
Safsızlıklar, aşağıdakiler gibi hammaddelerle karıştırılan çeşitli eşyalardan kaynaklanır:
Hammadde varillere taşınırken çeşitli eşyalarla karıştırılır.
Hammaddenin ayrışması, herhangi bir kesme mekanizmasından düşebilir ve makine cıvataları, kurutma tamburunun iç duvarı, bağlantılar / nozullar gibi hammaddelere karışabilir.
Laminasyon
Laminasyon, ürünlerin yüzeyinde ve diğer hammaddelerin yüzeylerinin özellik ve dokularındaki farklılıktan kaynaklanan “cilt etkisi” yaratacak ve bu, çıkarılabilen bir soyulma kabuğu oluşturacaktır.
Laminasyon ciddi olduğunda, tüm kesit alanı farklı katmanlardan oluşur ve birlikte eritilmemiştir. Kusurlar daha az belirgin olduğunda, ürünlerin görünümü gereksinimleri karşılayabilir ancak ürünlerin mekanik özelliklerini bozar.
Nedeni:
Laminasyonun iki ana nedeni vardır. Birincisi, iki farklı türdeki ham maddenin yanlış karıştırılmasıdır. İki ham madde basınç altında aynı anda varile taşınacaktır. Bununla birlikte, kalıp soğutulduğunda birlikte eritilemediğinde, tıpkı farklı katmanların ürünler oluşturmak için zorla birbirine bastırılması gibi.
İkincisi: eğer soğuk eriyik dar geçitten geçmeye zorlanırsa, kayma gerilimi oluşacaktır. Çok yüksek kayma gerilimi önceden erimiş eriyik tabakasının tamamen kaynaşamamasına neden olacaktır.
Karışım riski:
Dikkat edilmesi gereken bir husus, PVC ve Avetal gibi bazı hammaddelerin karıştırılması güçlü kimyasal reaksiyona neden olacağıdır ve karıştırılmamalıdır.
gümüş lineer
Şerit doğrusal sadece yerel bir fenomen olabilir, ancak ciddi olduğunda tüm yüzeye yayılabilir.
Silver lineer ürünlerin görünümünü etkiler ve ayrıca ürünlerin mekanik özelliklerine de zarar verir.
Nedeni:
Aşağıdaki iki nokta gümüş doğrusala neden olur:
Hammadde ıslaktır ve bir kısmı havadaki buharı emer. Hammadde çok ıslaksa, yüksek sıcaklık ve yüksek varil basıncı altında basınçlı buhar üretilebilir. Bu buharlar ürünün yüzeyinden geçerek gümüş şeritler oluşturur.
Eriyik termal olarak hasar gördü ve yerel bozulmaya neden oldu. Üretilen uçucu gaz, kalıp yüzeyinde bloke edilecek ve ürünlerin yüzeyinde şeritler oluşturacaktır.
Bu, bozulma kadar kötü değil. Eriyik sıcaklığı yüksek olduğu veya plastikleştirme veya kalıba enjeksiyon sırasında kayma gerilimine maruz kaldığı sürece bu olabilir.
Parlaklık/gölge
Ürünlerin yüzey kalitesi kalıplarınki ile aynı olmalıdır. İkisinin yüzey kalitesi farklı olduğunda parlaklık/gölge kusurları oluştu.
Kusurlar meydana geldiğinde yüzey kasvetli olacak ve pürüzlü yüzey pürüzsüz ve parlak olacaktır.
Nedeni:
Parlaklık/gölge nedenleri şunları içerir:
Eriyik düzgün olmayan bir şekilde akar veya kalıp yüzeyinin sıcaklığı düşüktür, bu da malzeme kalıplanırken kalıp yüzeyi kaplamasının kopyalanamamasına neden olur.
Basınç tutma sırasında, boşluktaki basınç, soğutma işleminde malzemenin kalıp yüzeyine yapışmasını ve büzülme izleri bırakmasını sağlayacak kadar yüksek değildir.
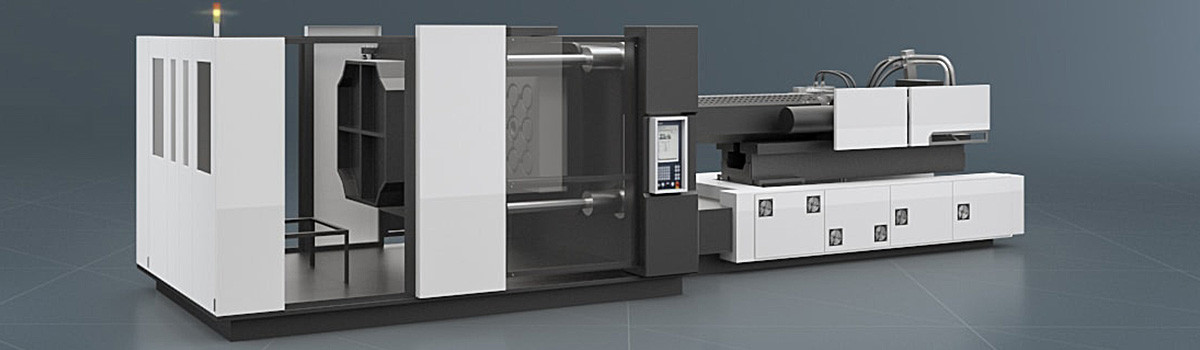
Akış işaretleri
Akış işaretleri, ürünlerin yüzeyinde birden fazla biçimde bulunabilir. Genel olarak, bir gölge alanı oluşturacaktır.
Akış işaretleri, ürünlerin yüzeyinde parmakla hissedilemeyecek herhangi bir kabartma veya çöküntü oluşturmaz. Bu kusur ayrıca sürükleme işaretleri, gölgelenme ve gölgeler olarak da adlandırılır.
Akış işaretleri belirgin olduğunda, oluklar oluşturacak ve ürünlerin yüzeyinde işaretler gibi kusurlar bırakacaktır.
Nedeni:
Akış işaretleri şu durumlarda bulunabilir:
Eriyiğin akışkanlığı zayıftır veya kalıbın yüzey sıcaklığı düşüktür, bu da kalıp doldurma işleminde plastiğin büyük bir akış direncine neden olur.
Kalıp doldurmada, kalıbın pürüzlü yüzeyi, kalıp yüzeyine basılan işaretler veya desenler veya doldurma işlemi sırasında eriyik akış yönünün değişmesinden kaynaklanabilecek dirençli eriyik akışı.
Birleştirme hattı
Birleştirme çizgisi, kalıp dolumu sırasında iki eriyik cephesi birleştiğinde oluşturulur ve ürün yüzeyinde bir çizgi gibi görünür.
Birleştirme çizgisi, ürünlerin yüzeyinde tespit edilmesi kolay olmayan çatlama çizgisi gibidir.
Kalıpları tasarlarken, bazı görünür bağlantı çizgileri kaçınılmazdır. Bu durumda ürünlerin sağlamlığının ve görünümünün bozulmaması için birleştirme hattını olabildiğince kısaltır.
Nedeni:
Erime cephesinin oluşmasının birçok nedeni vardır. En olası neden, kalıp maçasının kenarları boyunca eriyik akışı olabilir. İki eriyik buluştuğunda, birleştirme hatlarını oluşturur. İki eriyik cephesinin sıcaklığı, bunların başarılı bir şekilde kaynaşmasına izin verecek kadar yüksek olmalı ve ürünlerin sağlamlığını ve görünümünü etkilememelidir.
İki eriyik tamamen kaynaşamadığında, kusurlar üretilecektir.
Kusurların nedenleri:
Kalıp daha kalın ve daha ince parçalara sahiptir ve eriyiklerin akış hızı farklıdır, eriyik kalıbın ince kısmından akarken sıcaklık düşüktür.
Her koşucunun uzunluğu farklıdır. Yalnız koşucuları soğutmak kolay olacak.
Kalıp boşluğu basıncı, basınç tutma aşaması sırasında eriyiğin tamamen kaynaşmasına izin verecek kadar yeterli değildir.
Kalan kabarcıklar, eriyik cephesinin kaynaşmasını engeller ve bu da yanmaya neden olur.
Yanan
Yanma kısa atışa benzer, ancak düzensiz solma kenarları ve hafif yanık kokusu vardır. Ürün üzerinde karbon siyahı alanlar, durum ciddi olduğunda yanık plastik kokusu ile birlikte görünecektir.
Kusurlar giderilmezse, kalıp üzerinde genellikle siyah birikme olur. Yanma sonucu oluşan gaz veya petrol maddeleri hemen kontrol edilmezse hava deliklerini tıkayabilir. Yanma genellikle yolların sonunda bulunur.
Nedeni:
Yanma, içten yanma etkisinden kaynaklanır. Havadaki basınç çok kısa sürede keskin bir şekilde arttığında, sıcaklık yükselir ve yanmaya neden olur. Toplanan verilere göre, enjeksiyon kalıplama işlemindeki içten yanma etkisi 600 dereceye kadar yüksek sıcaklık üretebilir.
Yanma şu durumlarda oluşabilir:
Kalıp doldurma hızı yüksektir, böylece hava kalıp boşluğundan boşaltılamaz ve gelen plastiğin bloke edilmesi nedeniyle hava kabarcıkları oluşturur ve sıkıştırıldıktan sonra içten yanma etkisine yol açar.
Hava delikleri tıkalı veya havalandırma düzgün değil.
Hava deliklerinden kalıp içindeki hava boşaltılmalıdır. Havalandırma, konum, sayı, boyut veya işlevden etkilenirse, hava kalıbın içinde kalarak yanmasına neden olur. Büyük kalıp sıkıştırma kuvveti de yetersiz havalandırmaya yol açacaktır.
büzülme
Büzülme, ürünlerin yüzeyindeki hafif oyukları ifade eder.
Kusurlar hafif olduğunda, ürünlerin yüzeyi pürüzlüdür. Ciddiye alınınca geniş ürün alanı çöker. Kemerli, kulplu ve çıkıntılı ürünler genellikle çekme kusurlarından muzdariptir.
Nedeni:
Büzülme, soğutma sırasında ham maddelerin geniş alanlı büzülmesinden kaynaklanır.
Ürünlerin kalın alanında (kemer gibi), malzemenin çekirdek sıcaklığı düşüktür, bu nedenle çekme, yüzeydekinden daha sonra gerçekleşir, bu da hammadde içinde bir daralma kuvveti üretecek ve dış tarafı içe doğru çöküntüye çekecektir. büzülmeyi üretmek için.
Büzülmeler aşağıdaki durumlarda ortaya çıkar:
Kalıp boşluğundaki basınç, soğutma işleminde hammaddenin büzülmesinden kaynaklanan kuvvetten daha düşüktür.
Soğutma işlemi sırasında kalıp boşluğunun yetersiz basınçlandırma süresi, bu da ham maddenin kapıdan boşluktan dışarı akmasına neden olur.
Hammaddenin fazlası enjekte edilmeden önce vida tamamen geri çekildiği için kalıplama ve basınç tutma aşamasında hammadde yeterli tamponlama kapasitesine sahip değildir.
Kapıların ve kızakların enine kesit alanları, ürünlerin kalınlığından çok daha küçüktür, bu, ürünlerin ekstrüzyon işleminden önce kapıların zaten donmuş olduğu anlamına gelir.
Bubbles
Vakum kabarcıkları, şeffaf ürünlerde kolayca bulunabilen hava kabarcıkları şeklinde sunulur. Opak ürünlerin kesitlerinde de görülebilir.
Nedeni:
Hava kabarcıkları, soğutma işlemi sırasında hammaddenin çekmesiyle oluşan ürünlerin vakum kısmıdır.
Büzülmeye benzer şekilde, ham maddenin içi de büzülme kuvvetini üretir. Fark, ürünlerin dış görünümünün baloncuklar oluştuğunda katılaşmış olması ve çökme olmaması, dolayısıyla içi boş baloncukların oluşmasıdır.
Baloncukların nedenleri, aşağıdakiler de dahil olmak üzere, azalma nedenleri ile aynıdır:
Verimsiz kalıp boşluğu basıncı
Yetersiz kavite basınçlandırma süresi
Koşucu ve kapının boyutu çok küçük
Püskürtme işaretleri
Püskürtme işaretleri, kapının karşısındaki dişli alanı ifade eder. Püskürtme izleri, ürünlerin sadece görünümünü etkilemekle kalmaz, aynı zamanda ürünlerin mukavemetini de etkiler.
Nedeni:
Püskürtme izleri, kalıp doldurma işlemi sırasında eriyik akışının kontrolden çıkmasından kaynaklanır.
Erimiş plastik, büyük basınç altında kalıba girer. Kalıp doldurma hızı çok yüksekse, plastik kalıp boşluğunun açık aralığından dışarı çıkar ve hızlı bir şekilde geri yaylanır ve soğur. Bu sırada, erimiş plastiğin kapılara girmesini engelleyen iplikler oluşur.
Püskürtme izlerinin ana nedeni, kapıların yanlış konumlandırılması veya kapının tasarımıdır. Aşağıdaki iki durum, kusurların durumunu daha da kötüleştirecektir:
Yüksek kalıp doldurma hızı
Kalıp doldurma sırasında zayıf eriyik akışı