Termoplastik Enjeksiyon Kalıplama
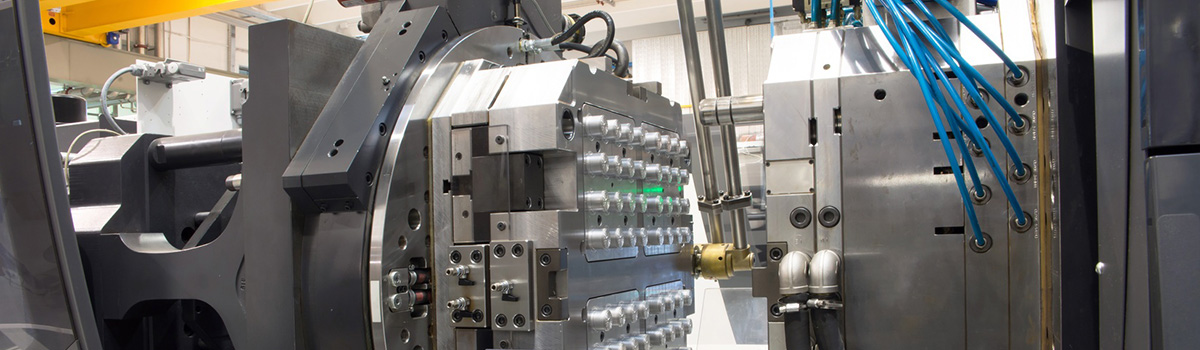
Termoplastik enjeksiyon kalıplama, birden fazla endüstri için çeşitli plastik parçalar oluşturmak için kullanılan popüler bir üretim sürecidir. Bu süreç, plastik peletlerin eritilmesini ve üç boyutlu bir şekil elde etmek için bir kalıba enjekte edilmesini içerir. Termoplastik enjeksiyon kalıplama, sıkı toleranslara sahip büyük hacimli yüksek kaliteli plastik parçalar üretmek için oldukça verimli ve uygun maliyetlidir. Bu kapsamlı kılavuz, avantajları ve dezavantajları, kullanılan termoplastik türleri, enjeksiyon kalıplama işlemi, tasarım hususları ve çok daha fazlası dahil olmak üzere termoplastik enjeksiyon kalıplamanın çeşitli yönlerini keşfedecektir.
Termoplastik Enjeksiyon Kalıplamanın Tarihçesi
Termoplastik enjeksiyon kalıplamanın tarihi, yüzyılı aşkın bir süredir teknolojik gelişmelere, malzeme geliştirmelerine ve endüstriyel uygulamalara dayanmaktadır. Selüloit kalıplama işlemi olarak mütevazi başlangıcından günümüzün sofistike teknolojisine kadar enjeksiyon kalıplama, inovasyonu yönlendiren ve çeşitli endüstrileri şekillendiren hayati bir üretim tekniği olmaya devam ediyor.
- Erken Gelişmeler:John Wesley Hyatt ve kardeşi Isaiah, termoplastik enjeksiyon kalıplamanın kökenlerinin 19. yüzyılın sonlarına kadar izini sürerek ilk pratik enjeksiyon kalıplama makinesini geliştirdiler. 1872'de, bir kalıp boşluğuna selüloit enjekte etmek için piston kullanan ve katı nesneler yaratan bir cihazın patentini aldılar. Bu atılım, modern enjeksiyonlu kalıplama işleminin temelini attı.
- Malzemelerdeki Gelişmeler:20. yüzyılın başlarında, yeni sentetik polimerlerin piyasaya sürülmesi, enjeksiyon kalıplama için yeni olanaklar yarattı. Fenolik bir reçine olan bakalit, mükemmel elektriksel yalıtım özellikleri nedeniyle kalıplama için popüler bir malzeme haline geldi. 1930'lar ve 1940'lar boyunca polimer kimyasındaki gelişmeler, polistiren ve polietilen gibi diğer termoplastiklerin geliştirilmesine yol açtı ve bu da enjeksiyon kalıplamaya uygun malzeme yelpazesini daha da genişletti.
- Endüstriyel Evlat Edinme: Termoplastik enjeksiyon kalıplamanın yaygın olarak benimsenmesi, üreticilerin maliyet etkinliğini ve çok yönlülüğünü fark etmesiyle 1950'lerde başladı. Yüksek basınçlı makinelerin tanıtılması, daha hızlı çevrim süreleri ve artan üretim hacimleri sağladı. Sonuç olarak, hem kişisel hem de endüstriyel kullanım için çok çeşitli ürünler ortaya çıktı. Bunlara araba bileşenleri, ev aletleri ve oyuncaklar dahildir.
- Teknolojik inovasyonlar:On yıllar boyunca, enjeksiyon kalıplama teknolojisi gelişmeye devam etti. 1960'larda, kalıplama işlemi üzerinde hassas kontrol sağlayan bilgisayar kontrollü makineler ortaya çıktı. 1980'lerde sıcak yolluk sistemlerinin piyasaya sürülmesi, yolluklara ve yolluklara olan ihtiyacı ortadan kaldırarak atıkları azalttı ve verimliliği artırdı. Son yıllarda, otomasyon, robotik ve 3D baskı gelişmeleri, enjeksiyon kalıplama endüstrisinde daha da devrim yaratarak karmaşık tasarımları mümkün kıldı ve üretim süresini kısalttı.
- Sürdürülebilirlik ve Geri Dönüşüm:Artan çevresel kaygılarla, plastik enjeksiyon endüstrisi sürdürülebilirlik önlemlerini benimsemiştir. Üreticiler, biyo-bazlı ve geri dönüştürülmüş termoplastikler geliştirerek fosil yakıtı bazlı malzemelere olan bağımlılığı azalttı. Ek olarak, geliştirilmiş geri dönüşüm teknolojileri, tüketici ve sanayi sonrası atıkların yeniden işlenmesini sağlayarak termoplastik enjeksiyon kalıplamanın çevresel etkisini en aza indirmiştir.
- Gelecek görünüşü:Termoplastik enjeksiyon kalıplamanın geleceği umut verici görünüyor. Endüstri, minyatür bileşenler için mikro enjeksiyon kalıplama, karmaşık parçalar için çoklu malzeme ve üst kalıplama teknikleri ve süreç izleme ve optimizasyon için akıllı teknolojileri entegre etme gibi yenilikleri araştırıyor. Ayrıca araştırmacılar, biyobozunur malzemelerdeki ve eklemeli üretimdeki ilerlemelerin bu alanda devrim yaratarak enjeksiyon kalıplamayı daha sürdürülebilir ve çok yönlü hale getirmesini bekliyor.
Termoplastik Enjeksiyon Kalıplamanın Avantajları
Termoplastik enjeksiyon kalıplama, üreticiler için çok sayıda avantaj sunar. Çeşitli özelliklere sahip karmaşık ve girift tasarımlara izin vererek tasarım esnekliği sağlar. Süreç uygun maliyetlidir, malzeme israfını azaltır ve birim maliyetleri düşürür. Termoplastik enjeksiyon kalıplama, farklı uygulamalar için çok yönlülük sağlayan birden fazla malzemeyi destekler.
- Tasarım Esnekliği:Termoplastik enjeksiyon kalıplama, alttan kesmeler, ince duvarlar ve değişen kalınlıklar gibi özelliklere sahip girift ve karmaşık tasarımlara izin vererek tasarımcılara muazzam bir özgürlük sağlar.
- Maliyet Verimliliği: Süreç oldukça verimlidir, malzeme israfını azaltır ve birim maliyetleri düşürür. Birden fazla parçanın eşzamanlı kalıplanması ve hızlı üretim döngüleri, maliyet tasarrufuna katkıda bulunur.
- Malzeme Çok Yönlülüğü: Termoplastik enjeksiyon kalıplama, üreticilerin sert veya esnek, şeffaf veya opak ve kimyasal olarak dayanıklı malzemeler dahil olmak üzere her uygulama için en uygun seçeneği seçmesine olanak tanıyan geniş bir malzeme yelpazesini destekler.
- Mukavemet ve Dayanıklılık:Enjeksiyonla kalıplanmış termoplastikler, yüksek mukavemet, tokluk ve darbe direnci gibi mükemmel mekanik özellikler sergileyebilir. Cam veya karbon fiberler gibi güçlendirme seçenekleri bu özellikleri daha da geliştirir.
- Tutarlılık ve Kalite:Enjeksiyon kalıplama, sıkı toleranslar ve güvenilir ürünler sunarak parçadan parçaya tutarlı kalite ve boyutsal doğruluk sağlar. İşlem ayrıca pürüzsüz ve düzgün bir yüzey kalitesi sağlayarak ek bitirme işlemlerine olan ihtiyacı ortadan kaldırır.
- Ölçeklenebilirlik ve Seri Üretim:Enjeksiyon kalıplama, düşük hacimlerden yüksek hacimlere kadar ölçeklendirilebilir, bu da onu seri üretime uygun hale getirir. Üreticiler kalıbı oluşturduktan sonra, minimum varyasyonlarla büyük miktarlarda aynı parçaları üretebilirler.
- Entegrasyon ve Montaj:Enjeksiyonla kalıplanmış parçalar, birden fazla bileşeni tek parça halinde birleştirerek ek montaj işlemlerine olan ihtiyacı azaltır. Bu entegrasyon, ürün performansını artırır, montaj süresini azaltır ve maliyetleri düşürür.
- Sürdürülebilirlik:Plastik enjeksiyon endüstrisi, sürdürülebilirliğe giderek daha fazla odaklanıyor. Biyolojik bazlı ve geri dönüştürülmüş malzemelerin mevcudiyeti, çevre dostu ürünlerin üretilmesine olanak tanır. Termoplastiklerin verimli malzeme kullanımı ve geri dönüştürülebilirliği, daha yeşil bir üretim sürecine katkıda bulunur.
Bu avantajlar, karmaşık ürün gereksinimleri için yüksek kaliteli, uygun maliyetli ve çevre dostu çözümler sunarak çeşitli endüstrilerde yaygın olarak benimsenen bir üretim yöntemi haline getirmiştir.
Termoplastik Enjeksiyon Kalıplamanın Dezavantajları
Termoplastik enjeksiyon kalıplama çok sayıda avantaj sunarken, birkaç dezavantaj da vardır. Üreticiler, termoplastik enjeksiyon kalıplamanın kendi özel uygulamalarına uygunluğunu belirlemek için bu faktörleri dikkatli bir şekilde değerlendirmeli ve faydalarına karşı tartmalıdır.
- Yüksek İlk Yatırım: Bir termoplastik enjeksiyon kalıplama işlemi kurmak, kalıp tasarımı ve imalatında önemli bir ilk yatırım ve özel makine satın almayı gerektirir. Kalıp oluşturma ve takım oluşturma ile ilgili maliyetler, özellikle karmaşık ve girift tasarımlar için önemli olabilir.
- Tasarım Sınırlamaları: Termoplastik enjeksiyon kalıplama tasarım esnekliği sunarken, belirli sınırlamalar mevcuttur. Örneğin, parça boyunca tekdüze duvar kalınlığı elde etmek zor olabilir, bu da malzeme dağılımında farklılıklara ve potansiyel yapısal zayıflıklara yol açar. Ek olarak, alttan kesmelerin veya karmaşık geometrilerin varlığı, ek kalıp özelliklerinin veya ikincil işlemlerin kullanılmasını gerektirerek maliyetleri ve üretim süresini artırabilir.
- Uzun Teslimat Süreleri:Enjeksiyon kalıplama için kalıp tasarlama ve üretme süreci zaman alıcı olabilir ve bu da ürün geliştirme için daha uzun teslim sürelerine yol açar. Tasarım yineleme süreci, kalıp üretimi ve test etme, genel üretim zaman çizelgesine önemli ölçüde zaman katabilir ve bu, son teslim tarihlerinin kısıtlı olduğu projeler için uygun olmayabilir.
- Malzeme Seçimi Kısıtlamaları:Termoplastik enjeksiyon kalıplama çok çeşitli malzemeleri desteklese de, belirli sınırlamalar ve kısıtlamalar vardır. Bazı malzemeler, belirli bir uygulama için tasarım seçimlerini ve malzeme seçimini etkileyen özel işleme gereksinimlerine veya sınırlı kullanılabilirliğe sahip olabilir.
- Parça Boyutu Sınırlamaları:Enjeksiyon kalıplama makineleri, hem cihazın fiziksel boyutu hem de barındırabilecekleri kalıpların boyutu açısından boyut sınırlamalarına sahiptir. Büyük parçaların üretilmesi, özel ekipman veya alternatif üretim yöntemleri gerektirebilir.
- Çevresel Etki:Endüstri sürdürülebilirlik için çalışırken, termoplastik enjeksiyon kalıplama işlemi hala hurda ve yolluk dahil olmak üzere atık malzeme üretiyor. Çevresel etkiyi en aza indirmek için bu malzemelerin uygun şekilde bertaraf edilmesi ve geri dönüştürülmesi gereklidir.
- Süreç Optimizasyonunun karmaşıklığı:Termoplastik enjeksiyon kalıplama için optimum proses parametrelerine ulaşmak karmaşık ve zaman alıcı olabilir. Üreticiler, tutarlı parça kalitesi sağlamak ve kusurları en aza indirmek için sıcaklık, basınç, soğutma hızları ve döngü sürelerini dikkatli bir şekilde kontrol etmeli ve optimize etmelidir.
Enjeksiyon Kalıplamada Kullanılan Termoplastik Türleri
Bunlar, enjeksiyon kalıplamada yaygın olarak kullanılan termoplastiklerin sadece birkaç örneğidir. Her malzemenin benzersiz özellikleri vardır, bu da onu güç, esneklik, kimyasal direnç, şeffaflık ve maliyete dayalı belirli uygulamalar için uygun hale getirir. Üreticiler, enjeksiyon kalıplama projeleri için uygun termoplastik seçerken bu özellikleri ve gereklilikleri dikkate almalıdır.
- Polipropilen (PP):Polipropilen, enjeksiyon kalıplamada yaygın olarak kullanılan çok yönlü bir termoplastiktir. Mükemmel kimyasal direnç, düşük yoğunluk ve iyi darbe dayanımı sunar. PP (polipropilen) paketleme, otomotiv bileşenleri, ev aletleri ve tıbbi cihazlarda geniş bir uygulama alanına sahiptir.
- Polietilen (PE):Polietilen, enjeksiyon kalıplamada yaygın olarak kullanılan bir başka termoplastiktir. Yüksek yoğunluklu polietilen (HDPE) ve düşük yoğunluklu polietilen (LDPE) gibi çeşitli formlarda mevcuttur. PE, iyi kimyasal direnç, tokluk ve esneklik sunarak onu şişeler, kaplar ve borular için uygun hale getirir.
- Polistiren (PS):Polistiren, berraklığı, sertliği ve satın alınabilirliği ile bilinen çok yönlü bir termoplastiktir. Ambalaj, tüketim malları ve tek kullanımlık ürünlerde yaygın kullanım alanı bulur. PS (polistiren) hızlı işlemeye izin verir ve iyi boyutsal kararlılık sağlar, ancak kırılgan olabilir ve çevresel stres çatlamasına karşı hassas olabilir.
- Akrilonitril Bütadien Stiren (ABS): ABS, mükemmel darbe direnci ve dayanıklılığı ile bilinen popüler bir termoplastiktir. Akrilonitril, bütadien ve stirenin özelliklerini bir araya getirerek otomotiv parçaları, elektronik muhafazalar ve oyuncaklara uygun çok yönlü bir malzeme oluşturur.
- Polivinil Klorür (PVC): PVC, mükemmel kimyasal direnci, dayanıklılığı ve düşük maliyeti ile bilinen yaygın olarak kullanılan bir termoplastiktir. Kullanılan formülasyona ve katkı maddelerine bağlı olarak sert veya esnek olabilir. PVC (polivinil klorür) inşaat, elektrik yalıtımı, sağlık ürünleri ve paketlemede yaygın kullanım alanı bulur.
- Polikarbonat (PC): Polikarbonat, olağanüstü darbe ve yüksek ısı direncine sahip şeffaf bir termoplastiktir. Otomotiv bileşenleri, güvenlik kaskları ve elektronik ekranlar gibi optik netlik gerektiren uygulamalarda yaygın kullanım alanı bulur.
- Naylon (Poliamid):Naylon, mükemmel mekanik özellikleri ve kimyasal direnci ile bilinen güçlü ve dayanıklı bir termoplastiktir. Otomotiv parçaları, endüstriyel bileşenler ve tüketim malları gibi yüksek mukavemet gerektiren uygulamalarda yaygın kullanım alanı bulur.
- Polietilen Tereftalat (PET):PET, şişeler, kaplar ve ambalaj malzemeleri üretmek için popüler bir termoplastiktir. İyi berraklık, kimyasal direnç ve bariyer özellikleri sunarak onu yiyecek ve içecek uygulamaları için uygun hale getirir.
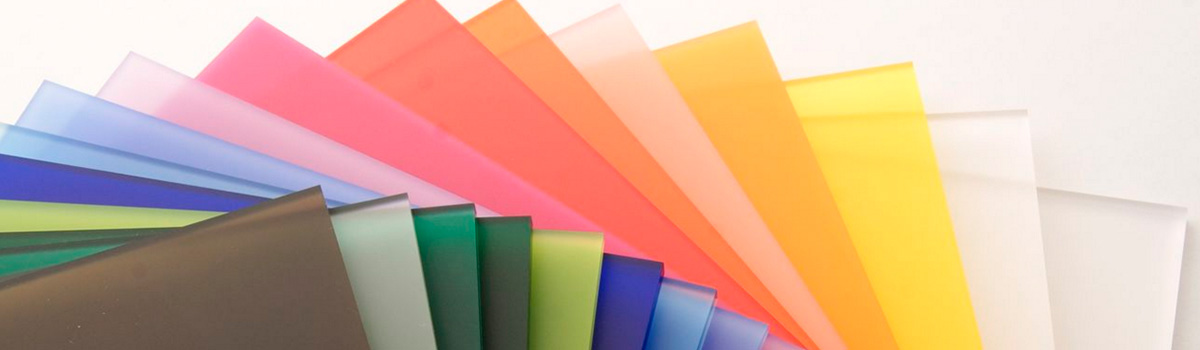
Enjeksiyon Kalıplamada Kullanılan Termoplastiklerin Özellikleri
Termoplastiklerin bu özellikleri, belirli enjeksiyon kalıplama uygulamaları için uygunluklarının belirlenmesinde çok önemli bir rol oynamaktadır. Üreticiler bu özellikleri dikkatlice değerlendirmeli ve istenen performansa, çevre koşullarına ve maliyet gerekliliklerine göre uygun termoplastik seçmelidir.
- Mekanik özellikler:Enjeksiyon kalıplamada kullanılan termoplastikler, çekme mukavemeti, darbe direnci ve eğilme mukavemeti dahil olmak üzere çeşitli mekanik özellikler sergileyebilir. Bu özellikler, malzemenin uygulanan kuvvetlere dayanma yeteneğini ve çeşitli uygulamalarda genel dayanıklılığını belirler.
- Kimyasal direnç:Enjeksiyon kalıplamada kullanılan birçok termoplastik, kimyasallara, solventlere ve yağlara karşı dikkate değer bir dirence sahiptir. Bu özellik, zorlu ortamlara veya aşındırıcı maddelere maruz kalmayı içeren uygulamalar için çok önemlidir.
- Termal kararlılık:Termoplastiklerin termal stabilitesi, önemli bir bozulma olmadan yüksek sıcaklıklara dayanma yeteneklerini ifade eder. Bazı termoplastikler, yüksek sıcaklıklarda bile mekanik özelliklerini korumalarına izin veren mükemmel ısı direnci sergiler.
- Elektriksel Özellikler:Enjeksiyon kalıplamada kullanılan termoplastikler, elektriksel yalıtım, iletkenlik veya dielektrik dayanımı dahil olmak üzere belirli elektriksel özelliklere sahip olabilir. Bu özellikler, malzemelerin güvenilir elektriksel performans sağlaması gereken elektrik ve elektronik endüstrilerindeki uygulamalar için gereklidir.
- Şeffaflık ve Netlik:Polikarbonat ve PET gibi belirli termoplastikler mükemmel şeffaflık ve netlik sunarak onları optik özellikler gerektiren uygulamalar için uygun hale getirir. Üreticiler genellikle bu malzemeleri şeffaf pencereler, lensler ve ekranlar gibi ürünlerde kullanırlar.
- Esneklik ve Dayanıklılık: Esneklik ve tokluk, darbe direnci ve dayanıklılık gerektiren uygulamalarda kullanılan termoplastiklerin temel özellikleridir. ABS ve naylon gibi bazı termoplastikler mükemmel tokluk sunarak tekrarlanan darbelere kırılmadan dayanmalarını sağlar.
- Ölçüsel durağanlık:Boyutsal kararlılık, bir termoplastiğin sıcaklık değişiklikleri de dahil olmak üzere değişen koşullar altında şeklini ve boyutunu koruma yeteneğini ifade eder. İyi boyutsal stabiliteye sahip malzemeler, bükülme veya bozulma riskini en aza indirerek tutarlı parça boyutları sağlar.
- Kimyasal Uyumluluk:Termoplastiklerin kimyasal uyumluluğu, bozunmaya veya asitler, bazlar ve çözücüler dahil olmak üzere çeşitli kimyasallarla etkileşime direnme yeteneklerini ifade eder. Optimum performansı sağlamak için, amaçlanan uygulamada karşılaşacağı belirli kimyasal ortama dayanabilecek bir termoplastik seçmek çok önemlidir.
- Yoğunluk: Termoplastikler, ağırlıklarını ve genel parça özelliklerini etkileyebilecek farklı kalınlıklara sahiptir. Polietilen gibi düşük yoğunluklu malzemeler hafif çözümler sunarken, polipropilen gibi yüksek yoğunluklu malzemeler ek güç ve sağlamlık sağlar.
Enjeksiyon Kalıplama Süreci: Adım Adım
Enjeksiyon kalıplama işlemi, yüksek kaliteli termoplastik parçaların verimli ve hassas bir şekilde üretilmesini sağlayan bu adımları takip eder. Tutarlı parça boyutları, malzeme özellikleri ve genel kalite sağlamak için her adım dikkatli kontrol ve izleme gerektirir.
- Kalıp Tasarımı ve İmalatı: Enjeksiyon kalıplama sürecindeki ilk adım, kalıbın tasarımı ve imalatıdır. Üreticiler, istenen parça özelliklerine ulaşmak için kesin ve ayrıntılı bir kalıp tasarımı oluşturmalıdır. Üreticiler daha sonra kalıbı CNC veya elektrik deşarjlı işleme (EDM) gibi çeşitli teknikler kullanarak imal ederler.
- Malzeme hazırlama: Bir sonraki adım, kalıp hazır olduğunda hazırlıktır. Termoplastik peletler veya granüller, istenen malzeme özelliklerine göre seçilir ve bir haznede eritilir. Operatörler daha sonra malzemeyi eritme ve homojenleştirmeye tabi tutulacağı enjeksiyon kalıplama makinesinin namlusuna besler.
- Enjeksiyon:Enjeksiyon aşamasında, operatörler erimiş termoplastik malzemeyi yüksek basınç altında kalıp boşluğuna enjekte eder. Makinenin enjeksiyon ünitesi, erimiş malzemeyi bir memeden geçirerek kalıba iter. Malzeme istenilen parçanın şeklini alarak kalıp boşluğunu doldurur.
- Soğutma ve Katılaşma:Kalıbı doldurduktan sonra, operatörler erimiş plastiğin soğumasını ve katılaşmasını sağlar. Soğutma, boyutsal stabilite ve uygun parça oluşumu elde etmek için çok önemlidir. Operatörler soğutma sıvısını kalıp içindeki kanallardan geçirerek veya soğutma plakalarını kullanarak soğutma işlemini kontrol edebilirler.
- Kalıp Açma ve Çıkarma:Operatörler kalıbı açar ve plastik katılaştıktan sonra parçayı kalıp boşluğundan çıkarır. Makine içindeki fırlatma sistemi, bölgeyi kalıptan çıkarmak için pimler, ejektör plakaları veya hava üflemeleri kullanır. Kalıp daha sonra bir sonraki enjeksiyon döngüsü için hazırdır.
- Rötuş: Fırlatmadan sonra parça, düzeltme, çapak alma veya yüzey bitirme gibi işlem sonrası işlemlere tabi tutulabilir. Bu adımlar, fazla malzemenin çıkarılmasına, pürüzlü kenarların düzleştirilmesine ve parçanın nihai görünümünün iyileştirilmesine yardımcı olur.
- Kalite Kontrol: Son adım, enjekte edilen parçaların kalite açısından incelenmesini ve belirtilen gereksinimleri karşıladıklarından emin olunmasını içerir. Parçanın kalitesini ve bütünlüğünü doğrulamak için boyutsal ölçüm, görsel inceleme ve fonksiyonel test dahil olmak üzere çeşitli kalite kontrol teknikleri kullanılabilir.
- Geri Dönüşüm ve Malzemenin Yeniden Kullanımı:Enjeksiyon kalıplama sırasında oluşan herhangi bir fazlalık veya hurda malzeme geri dönüştürülebilir ve yeniden kullanılabilir. Yeni termoplastik malzeme kullanımının azaltılması, atığın en aza indirilmesine ve sürdürülebilirliğin iyileştirilmesine yardımcı olur.
Enjeksiyon Kalıplamada Kullanılan Ekipmanlar
Bu ekipman bileşenleri, termoplastik malzemenin eritilmesi ve enjekte edilmesinden nihai parçanın şekillendirilmesi, soğutulması ve çıkarılmasına kadar enjeksiyonlu kalıplama sürecini kolaylaştırır. Bu ekipman bileşenlerinin uygun şekilde çalıştırılması ve bakımı, verimli, yüksek kaliteli plastik enjeksiyon üretimi elde etmek için çok önemlidir.
- Enjeksiyonlu kalıp makinası:Enjeksiyon kalıplamadaki birincil ekipman, termoplastik malzemenin eritilmesinden, kalıba enjekte edilmesinden ve işlemin kontrolünden sorumludur.
- Kalıp: Plastik parçanın istenilen şekil ve özelliklerini oluşturmak için özel olarak tasarlanan kalıp, boşluk ve maça olmak üzere iki yarıdan oluşur. Operatörler bunu plastik enjeksiyon makinesinin kenetleme ünitesine monte eder.
- Hazne:Termoplastik malzemeyi pelet veya granül formda tutan ve eritmek ve enjeksiyon için enjeksiyon kalıplama makinesinin namlusuna besleyen kap.
- Namlu ve Vida: Silindirik bir hazne olan namlu, malzemeyi eritmek, karıştırmak ve standart hale getirmek için vida içinde dönerken termoplastik malzemeyi eritir ve homojenleştirir.
- Isıtma ve Soğutma Sistemleri:Enjeksiyon kalıplama makinelerinde, namlunun sıcaklığını yükseltmek için elektrikli ısıtıcılar veya kızgın yağ kullanan ısıtıcılar gibi ısıtma elemanları ve kalıbı soğutmak ve plastik parçayı katılaştırmak için su veya yağ sirkülasyonu gibi soğutma sistemleri bulunur.
- Ejektör Sistemi:Tipik olarak kalıp açma sırasında ejektör pimleri, plakaları veya hava üflemelerini kullanarak, kalıplanmış parçayı katılaşmadan sonra kalıp boşluğundan çıkarır.
- Kontrol sistemi:Enjeksiyon kalıplama işleminin çeşitli parametrelerini izler ve kontrol ederek operatörlerin enjeksiyon hızı, sıcaklık, basınç ve soğutma süresi gibi parametreleri ayarlamasına ve ayarlamasına olanak tanır.
Enjeksiyon Makineleri: Tipleri ve Özellikleri
Her tip enjeksiyon kalıplama makinesinin kendine has özellikleri ve avantajları vardır, bu da üreticilerin kendi özel üretim gereksinimleri için en uygun cihazı seçmelerine olanak tanır.
- Hidrolik Enjeksiyon Makineleri: Bu makineler, erimiş plastiği kalıba enjekte etmek için gerekli basıncı oluşturmak için hidrolik sistemler kullanır. Yüksek kenetleme kuvvetleri, hassas kontrolleri ve çeşitli termoplastiklerin işlenmesindeki çok yönlülükleri ile tanınırlar. Hidrolik makineler, büyük ölçekli üretim için uygundur ve karmaşık kalıpları barındırabilir.
- Elektrikli Enjeksiyon Makineleri:Elektrikli makineler, enjeksiyon, kenetleme ve ejektör sistemleri dahil olmak üzere makinenin çalışması için elektrikli servo motorlar kullanır. Hassas kontrol, enerji verimliliği ve hidrolik makinelerden daha hızlı yanıt süreleri sunarlar. Elektrikli makineler, yüksek tekrarlanabilirlik ve doğruluk gerektiren hassas kalıplama uygulamaları için idealdir.
- Hibrit Enjeksiyon Makineleri:Hibrit makineler, hem hidrolik hem de elektrikli cihazların faydalarını birleştirir. Yüksek hassasiyet, enerji verimliliği ve maliyet etkinliği elde etmek için hidrolik ve elektrikli servo sistemlerinin bir kombinasyonunu kullanırlar. Hibrit makineler, performans ve işletme maliyetleri arasında bir denge sağlayan çok çeşitli uygulamalar için uygundur.
- İki Plakalı Enjeksiyon Makineleri: İki plakalı makineler, kalıbı sıkıştırmak için iki ayrı plaka ile benzersiz bir tasarıma sahiptir. Bu tasarım, gelişmiş stabilite, gelişmiş kalıp senkronizasyonu sağlar ve daha büyük kalıp boyutları ve daha yüksek sıkıştırma kuvvetleri sağlar. İki plakalı makineler, hassas kalıplama gerektiren büyük ve karmaşık parçalar için uygundur.
- Çok Bileşenli Enjeksiyon Makineleri:Üreticiler, bu makineleri, tek bir kalıplama döngüsünde birden çok malzeme veya renge sahip parçalar üretmek için tasarlar. Farklı malzemelerin aynı anda enjeksiyonunu sağlayan çeşitli enjeksiyon üniteleri ve kalıpları vardır. Çok bileşenli makineler, değişen özelliklere sahip karmaşık parçaların üretiminde esneklik ve verimlilik sunar.
- Mikro Enjeksiyon Makineleri:Küçük ve hassas parçalar üretmek için özel olarak tasarlanmış olan mikro enjeksiyonlu kalıplama makineleri, inanılmaz derecede yüksek hassasiyet ve doğruluk sunar. Dar toleranslar ve minimum malzeme israfı ile karmaşık detaylar üretebilirler. Elektronik, tıbbi cihazlar ve mikro optikler genellikle mikro enjeksiyon kalıplama makinelerini kullanır.
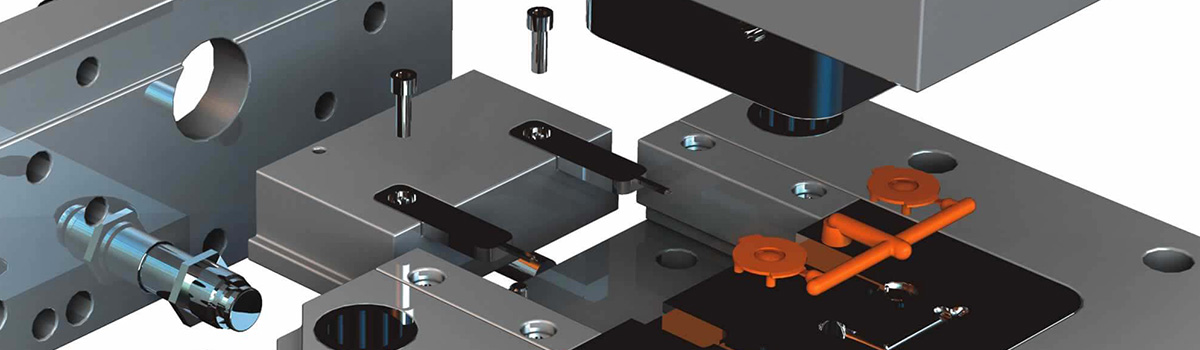
Enjeksiyon Kalıplama için Kalıp Tasarımı Hususları
Başarılı enjeksiyon kalıplama üretimi için dikkatli kalıp tasarımı hususları esastır.
- Parça Tasarımı:Kalıp tasarımı, şekli, boyutları ve işlevsel özellikleri dahil olmak üzere parçanın özel gereksinimlerini karşılamalıdır. Üreticiler, çıkarma kolaylığı ve parça kalitesini sağlamak için taslak açılarını, duvar kalınlığını, alttan kesmeleri ve gerekli tüm öğeleri uygun şekilde dikkate almalıdır.
- Kalıp Malzemesi: Kalıp malzemesi seçimi, dayanıklılık, boyutsal kararlılık ve ısı direnci elde etmek için çok önemlidir. Yaygın kalıp malzemeleri arasında çelik alaşımları, alüminyum alaşımları ve takım çelikleri bulunur. Malzeme seçimi, üretim hacmi, parça karmaşıklığı ve beklenen takım ömrü gibi faktörlere bağlıdır.
- Soğutma Sistemi:Verimli soğutma, uygun parça katılaşması ve döngü süresinin en aza indirilmesi için gereklidir. Kalıp tasarımı, tek tip kalıp soğutması sağlamak için soğutma kanallarını veya stratejik olarak konumlandırılmış ekleri içermelidir. Doğru soğutma, eğilme, çekme ve parça kusurları riskini azaltır.
- Havalandırma:Enjeksiyon işlemi sırasında hava ve gazların kaçmasına izin vermek için yeterli havalandırma gereklidir. Yetersiz havalandırma, gaz tuzaklarına, yanık izlerine veya eksik parça dolumuna yol açabilir. Üreticiler, kalıp tasarımına havalandırma oluklarını, pimleri veya diğer mekanizmaları dahil ederek havalandırma sağlayabilir.
- Fırlatma Sistemi:Kalıp tasarımı, kalıplanmış parçayı kalıp boşluğundan güvenli ve verimli bir şekilde çıkarmak için etkili bir çıkarma sistemi içermelidir. Fırlatma sistemi, işleve veya kritik özelliklere müdahaleyi önlemek için stratejik olarak konumlandırılmış ejektör pimleri, manşonlar veya diğer mekanizmalardan oluşabilir.
- Kapı Tasarımı:Kapı, erimiş plastiğin kalıp boşluğuna girdiği yerdir. Geçit tasarımı, uygun parça dolumunu sağlamalı, akış hatlarını en aza indirmeli ve erken malzeme donmasını önlemelidir. Standart kapı tasarımları, parça gereksinimlerine ve malzeme özelliklerine bağlı olarak kenar kapıları, tünel geçitleri ve sıcak yolluk sistemlerini içerir.
- Ayrılma çizgisi:Kalıp tasarımı, kalıbın iki yarısının bir araya geldiği çizgi olan uygun bir ayırma çizgisini tanımlamalıdır. Doğru ayırma hattı yerleşimi, minimum parlama ve ayırma hattı uyumsuzluğu sağlar ve verimli kalıp montajını kolaylaştırır.
- Kalıp Bakımı ve Servis Verilebilirlik: Üreticiler bakım, onarım ve kalıp servisinin kolaylığını göz önünde bulundurmalıdır. Kalıp bileşenlerine temizlik, inceleme ve değiştirme için kolayca erişilebilir olmalıdır. Hızlı değiştirilebilir kesici uçlar veya modüler kalıp tasarımları gibi özelliklerin birleştirilmesi, kalıbın servis edilebilirliğini artırabilir.
Enjeksiyon Kalıplamada Kullanılan Kalıp Malzemeleri
Kalıp malzemesi uzmanlarıyla işbirliği yapmak ve kalıplama uygulamasının özel ihtiyaçlarını göz önünde bulundurmak, optimum kalıp performansı ve parça kalitesi elde etmek için en uygun malzemenin belirlenmesine yardımcı olabilir.
- Çelik Alaşımları: Takım çelikleri (örneğin, P20, H13) ve paslanmaz çelikler gibi çelik alaşımları, mükemmel dayanıklılıkları, ısı dirençleri ve aşınma dirençleri nedeniyle enjeksiyon kalıplama kalıplarında yaygın olarak kullanılır. Bu malzemeler, enjeksiyon kalıplama işlemindeki yüksek sıcaklıklara ve basınçlara dayanabilir ve yüksek kaliteli parçalar üretmek için iyi bir boyutsal kararlılık sunar.
- Alüminyum Alaşımları:7075 ve 6061 gibi alüminyum alaşımları hafiftir ve iyi termal iletkenlik sunarak onları verimli soğutma gerektiren kalıplar için uygun hale getirir. Üreticiler genellikle prototip oluşturma, düşük hacimli üretim veya ağırlık azaltmanın kritik olduğu uygulamalar için alüminyum kalıplar kullanır. Bununla birlikte, alüminyum kalıplar, çelik alaşımlara kıyasla daha düşük dayanıklılığa sahip olabilir.
- Bakır alaşımları:Berilyum bakır gibi bakır alaşımları, yüksek termal iletkenlik ve iyi işlenebilirlik sergiler. Etkili soğutma için mükemmel ısı transferi gerektiren kalıplarda kullanım alanı bulurlar. Bakır alaşımları, kalıplanmış parçadan ısıyı hızla dağıtarak döngü sürelerini azaltmaya yardımcı olabilir ve bu da daha hızlı katılaşma sağlar.
- Takım Çelikleri:H13, S7 ve D2 dahil olmak üzere takım çelikleri, yüksek performanslı takım uygulamaları için tasarlanmıştır. Bu çelikler, yüksek mukavemet, sertlik ve aşınma direncinin bir kombinasyonunu sunar. Takım çelikleri, yüksek üretim hacimlerine, aşındırıcı malzemelere veya zorlu kalıplama koşullarına sahip kalıplara uygundur.
- Nikel Alaşımları:Inconel ve Hastelloy gibi nikel alaşımları olağanüstü korozyon direnci, yüksek sıcaklık dayanımı ve termal kararlılığı ile bilinir. Üreticiler bu alaşımları aşındırıcı malzemeleri işleyen veya aşırı sıcaklıklara ve agresif kalıplama ortamlarına karşı direnç gerektiren kalıplarda kullanırlar.
- Kompozit Malzemeler:Takviyeli plastikler veya metal uçlu kompozitler gibi kompozit malzemeler bazen özel kalıplama uygulamaları için kullanılır. Bu malzemeler, yüksek mukavemet, termal kararlılık ve azaltılmış ağırlık gibi özellikler dengesi sunar. Kompozit kalıplar, özel üretim gereksinimleri için uygun maliyetli alternatifler olabilir.
Enjeksiyon Kalıp Çeşitleri
Enjeksiyon kalıplama, plastik parçalar için çok yönlü ve yaygın olarak kullanılan bir üretim sürecidir.
- İki Plakalı Kalıp:İki plakalı kalıp, en yaygın enjeksiyon kalıbı türüdür. Kalıplanmış parçanın çıkarılmasına izin vermek için ayrılan iki plakadan, boşluk plakasından ve çekirdek plakasından oluşur. Boşluk plakası, kalıbın boşluk tarafını içerirken, çekirdek plakası, çekirdek tarafını barındırır. Üreticiler, nispeten basit tasarımları nedeniyle geniş bir parça yelpazesi üretmek için iki plakalı kalıplar kullanırlar.
- Üç Plakalı Kalıp:Üç plakalı kalıp, iki plakalı kalıbın gelişmiş bir versiyonudur. Ek bir plaka, yolluk veya yolluk plakası içerir. Yolluk plakası yolluk, yolluklar ve kapılar için ayrı bir kanal oluşturarak kalıplanmış parçanın daha kolay çıkarılmasını sağlar. Üreticiler, karmaşık yolluk sistemleriyle ilgili ayrıntılar için veya parça üzerinde bir kapı izinden kaçınılması istendiğinde genellikle üç plakalı kalıplar kullanırlar.
- Sıcak Yolluk Kalıbı:Yolluk ve geçit sistemi, sıcak yolluk kalıplarında ısıtılarak, her döngüde malzemenin katılaşması ve yeniden eritilmesi ihtiyacını ortadan kaldırır. Sıcak yolluk sistemi, plastiğin erimiş halini koruyan ısıtılmış manifoldlardan ve nozüllerden oluşur. Sıcak yolluk kalıpları, kapı kalıntılarını en aza indirerek azaltılmış döngü süresi, daha az malzeme atığı ve iyileştirilmiş parça kalitesi gibi avantajlar sunar.
- Soğuk Yolluk Kalıbı: Soğuk yolluk kalıpları, erimiş plastiğin her döngüde katılaşan soğuk yolluklardan aktığı geleneksel bir yolluk ve kapı sistemine sahiptir. Operatörler daha sonra katılaşmış yollukları çıkarır ve bu da malzeme israfına neden olur. Üreticiler genellikle daha düşük hacimli üretim için veya daha basit tasarımları nedeniyle malzeme maliyetlerinin daha az kritik olduğu durumlarda karmaşık yolluk kalıpları kullanırlar.
- Kalıp Ekle:Ekleme kalıpları, enjeksiyon kalıplama sırasında kalıp boşluğuna metal veya plastik ekler içerir. Ek parçalar kalıba önceden yerleştirilebilir veya otomatik işlemlerle yerleştirilebilir. Bu kalıp, ek bileşenlerin veya takviye elemanlarının kalıplanmış parçaya entegre edilmesine izin vererek işlevselliğini veya gücünü arttırır.
- aşırı kalıp: Üst kalıplama, tipik olarak sert bir plastik alt tabakayı daha yumuşak bir elastomer veya termoplastik ile birleştirerek, bir malzemenin diğerinin üzerine kalıplanmasını içerir. Bu süreç, tek bir kalıpta birden çok malzeme veya dokuya sahip parçaların oluşturulmasına olanak tanıyarak gelişmiş kavrama, yastıklama veya estetik özellikler sağlar.
Enjeksiyon Kalıplama Maliyetlerini Etkileyen Faktörler
Bu faktörlerin göz önünde bulundurulması, üreticilerin kendi özel üretim gereksinimleri için kalite, verimlilik ve maliyet etkinliği arasında bir denge sağlayarak enjeksiyon kalıplama maliyetini tahmin etmelerine ve optimize etmelerine yardımcı olabilir.
- Parça Karmaşıklığı:Parça tasarımının karmaşıklığı, enjeksiyon kalıplama maliyetinin belirlenmesinde önemli bir rol oynar. Karmaşık geometriler, alttan kesmeler, ince duvarlar veya karmaşık özellikler, genel üretim maliyetini artıran ek takımlar, özel kalıplar veya daha uzun döngüler gerektirebilir.
- Malzeme seçimi:Termoplastik malzeme seçimi enjeksiyon kalıplama maliyetini etkiler. Farklı malzemelerin kilogram başına değişen fiyatları vardır ve malzemenin kullanılabilirliği, özellikleri ve işleme gereksinimleri gibi faktörler genel malzeme maliyetini etkileyebilir.
- Alet ve Kalıp Tasarımı: İlk takım ve kalıp tasarım maliyetleri, enjeksiyon kalıplama maliyetlerinde önemlidir. Kalıp karmaşıklığı, boşluk sayısı, kalıp boyutu ve kalıp malzemesi gibi faktörler takım ve kalıp imalat giderlerine katkıda bulunur. Daha karmaşık kalıplar veya gelişmiş özellikler gerektiren kalıplar ön yatırımı artırabilir.
- Üretim hacmi: Üretim hacmi, enjeksiyon kalıplamada parça başına maliyeti doğrudan etkiler. Daha yüksek kitaplar genellikle parça başına maliyeti düşürerek ölçek ekonomisi sağlar. Tersine, düşük hacimli üretim çalışmaları, kurulum, alet ve malzeme atığı nedeniyle daha yüksek ücretlere neden olabilir.
- Devir süresi: Soğutma ve püskürtme aşamalarını içeren döngü süresi, üretim kapasitesini ve toplam maliyeti etkiler. Daha uzun döngü süreleri, üretim çıktısının azalmasına ve potansiyel olarak daha yüksek fiyatlara neden olur. Kalıp tasarımını, soğutma sistemini ve işlem parametrelerini optimize etmek döngü sürelerini en aza indirebilir ve verimliliği artırabilir.
- Kalite Gereksinimleri:Sıkı kalite gereklilikleri veya özel sertifikalar enjeksiyon kalıplama maliyetini etkileyebilir. Kesin toleransların, yüzey kalitesi gerekliliklerinin veya ek testlerin karşılanması, başka kaynaklar, süreçler veya incelemeler gerektirerek toplam maliyeti artırabilir.
- İkincil İşlemler:Kalıplanmış parçalar montaj, boyama veya ek bitirme adımları gibi işlem sonrası işlemler gerektiriyorsa, bu işlemler genel enjeksiyon kalıplama maliyetine katkıda bulunabilir.
- Tedarikçi ve Konum:Enjeksiyon kalıplama tedarikçisinin seçimi ve konumu maliyetleri etkileyebilir. İşçilik maliyetleri, genel giderler, lojistik ve nakliye giderleri, tedarikçinin konumuna göre değişir ve genel üretim maliyetini etkiler.
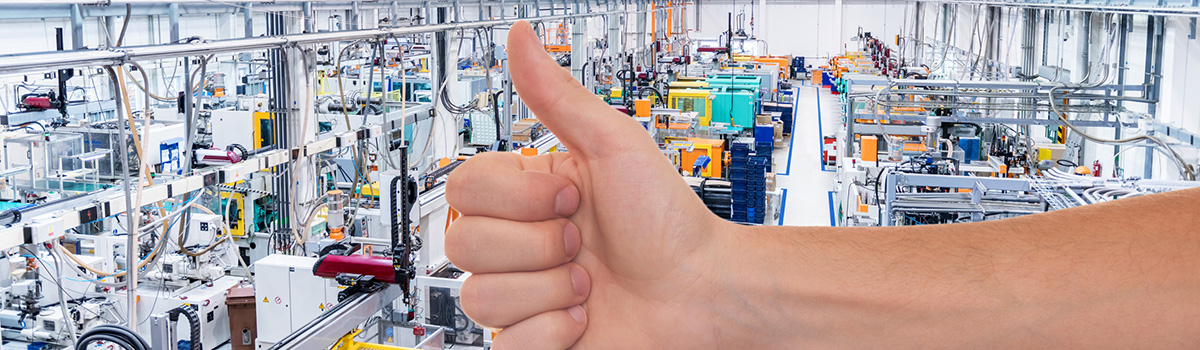
Enjeksiyon Kalıplamada Kalite Kontrol
Enjeksiyon kalıplama işlemi boyunca sağlam kalite kontrol önlemlerinin uygulanması, müşteri spesifikasyonlarını ve gereksinimlerini karşılayan yüksek kaliteli parçaların üretilmesini sağlayarak potansiyel kusurları, sapmaları veya tutarsızlıkları belirlemeye ve ele almaya yardımcı olur.
- Süreç İzleme: Eriyik sıcaklığı, enjeksiyon basıncı, soğutma süresi ve döngü süresi gibi temel işlem parametrelerinin sürekli izlenmesi, parça üretiminde tutarlılık ve tekrarlanabilirlik sağlar. Gerçek zamanlı izleme ve otomatikleştirilmiş sistemler, ayarlanan parametrelerdeki değişimleri veya sapmaları tespit ederek zamanında ayarlamalara ve süreç istikrarının korunmasına olanak tanır.
- Muayene ve Ölçüm:Kalıplanmış parçaların düzenli olarak gözden geçirilmesi ve ölçülmesi, boyutsal doğruluğu, parça kalitesini ve spesifikasyonlara bağlılığı doğrulamak için gereklidir. Hizmetlerimiz boyutları ölçmek, yüzey kalitesini analiz etmek, görsel incelemeler yapmak ve fonksiyonel testler yapmak gibi bir dizi kalite kontrol yöntemini kapsar. Doğru değerlendirme için koordinat ölçüm makineleri (CMM) ve optik ve görsel inceleme sistemleri gibi çeşitli inceleme teknikleri kullanılır.
- İstatistiksel Süreç Kontrolü (SPC): SPC, enjeksiyon kalıplama kalitesini izlemek ve kontrol etmek için proses verilerinin toplanmasını ve analiz edilmesini içerir. Kontrol çizelgeleri ve süreç yetenek analizi gibi istatistiksel yöntemler, eğilimlerin belirlenmesine, süreç varyasyonlarının saptanmasına ve sürecin tanımlanmış kontrol limitleri içinde kalmasının sağlanmasına yardımcı olur. SPC, sorunların proaktif olarak tanımlanmasını sağlar ve süreç optimizasyonunu kolaylaştırır.
- Malzeme Testi: Termoplastikler, katkı maddeleri ve renklendiriciler gibi ham maddelerin test edilmesi, bunların kalitesini ve enjeksiyon kalıplamaya uygunluğunu garanti eder. Malzeme testi, eriyik akış indeksi (MFI) analizini, mekanik özellikleri, termal özellikleri ve malzeme bileşimini içerebilir. Malzeme kalitesinin doğrulanması, kalıplanmış parçalardaki kusurları ve tutarsızlıkları önlemeye yardımcı olur.
- Alet Bakımı ve Muayenesi:Enjeksiyon kalıplarında uygun bakım ve düzenli muayene, enjeksiyon kalıplamada kaliteyi sağlamak için çok önemlidir. Kalıp bileşenlerinin düzenli olarak temizlenmesi, yağlanması ve değerlendirilmesi, parça kalitesini etkileyebilecek aşınma, hasar veya bozulmayı önlemeye yardımcı olur. Aşınmış veya hasar görmüş kalıp bileşenlerinin zamanında onarılması veya değiştirilmesi, tutarlı kalıplama performansını sürdürmek için çok önemlidir.
- Dokümantasyon ve İzlenebilirlik:Enjeksiyon kalıplamada kalite kontrol için kapsamlı dokümantasyon ve izlenebilirlik kayıtlarının tutulması esastır. Proses parametrelerinin, muayene sonuçlarının, malzeme bilgilerinin ve üretim sırasında yapılan her türlü değişikliğin veya ayarlamanın kaydedilmesi hayati önem taşır. Uygun dokümantasyon, parçaların izlenebilirliğini sağlar, temel neden analizini kolaylaştırır ve kalitede tutarlılık sağlar.
- Eğitim ve Beceri Geliştirme: Operatörler, teknisyenler ve kalite kontrol personeli için yeterli eğitim ve beceri geliştirme programları sağlanması, enjeksiyon kalıplama süreçleri, kalite gereksinimleri ve denetim teknikleri konusundaki anlayışlarını geliştirir. İyi eğitimli personel, kusurları tespit edebilir, sorunları giderebilir ve düzeltici önlemleri etkili bir şekilde uygulayarak yüksek kaliteli üretim sağlayabilir.
Yaygın Enjeksiyon Kalıplama Hataları ve Onlardan Nasıl Kaçınılır?
Enjeksiyon kalıplama işlemlerinin düzenli olarak denetlenmesi, izlenmesi ve analizi ile ekipman ve kalıpların uygun şekilde bakımı ve ayarlanması, bu yaygın kusurların belirlenmesine ve giderilmesine yardımcı olabilir.
- Çöküntü izleri:Çökme işaretleri, kalıplanmış parçanın yüzeyinde eşit olmayan soğuma veya çekmenin neden olduğu çöküntüler veya girintilerdir. Çökme izlerini önlemek için uygun kapı konumu ve tasarımı, optimum soğutma sistemi tasarımı ve tek tip duvar kalınlığı dağılımı dikkate alınmalıdır. Enjeksiyon basıncını artırmak veya soğutma süresini ayarlamak da batma izlerini en aza indirmeye yardımcı olabilir.
- Çarpıklık:Eğilme, kalıplanmış bir parçanın dışarı atıldıktan sonra eşit olmayan soğuma veya artık gerilimler nedeniyle deformasyonu veya bükülmesini ifade eder. Düzgün duvar kalınlığını korumak, uygun soğutma kanallarını kullanmak ve kalıbın dengeli doldurulmasını ve paketlenmesini sağlamak, eğrilmeyi önlemek için çok önemlidir. Kalıp sıcaklığını optimize etmek, uygun çekme açılarını kullanmak ve malzeme sıcaklığını ve enjeksiyon hızını kontrol etmek, eğrilmeyi en aza indirmeye yardımcı olabilir.
- Flaş:Fazla malzeme kalıp ayırma hattına aktığında, nihai parça üzerinde ince, istenmeyen çıkıntılara veya fazladan malzemeye neden olduğunda parlama meydana gelir. Yeterli sıkma kuvveti uygulamak, hassas hizalama ve uygun havalandırma tekniklerini kullanmak da dahil olmak üzere uygun kalıp tasarımı sağlanarak parlama etkili bir şekilde önlenebilir. Enjeksiyon basıncı, sıcaklık ve döngü süresi gibi proses parametrelerinin optimize edilmesi parlamayı azaltır.
- Kısa atış:Enjekte edilen malzeme kalıp boşluğunu doldurmadığında, eksik bir parçayla sonuçlandığında hızlı bir çekim gerçekleşir. Kısa fotoğraflardan kaçınmak için uygun malzeme seçimi, yeterli erime sıcaklığı ve viskozitenin sağlanması ve uygun enjeksiyon basıncı ve süresinin sürdürülmesi esastır. Ek olarak, kalıp tasarımının yeterli yolluk ve kapı boyutu ve uygun havalandırma için doğrulanması, hızlı çekimlerin önlenmesine yardımcı olabilir.
- Kaynak Hatları:Kaynak çizgileri, iki veya daha fazla erimiş malzeme akış cephesi buluşup katılaşarak parça yüzeyinde görünür bir çizgi veya işaretle sonuçlandığında meydana gelir. İyi kapı ve yolluk tasarımı, optimum eriyik sıcaklığı, enjeksiyon hızı ve malzeme akışı ile parça geometrisinin ayarlanması kaynak hatlarını en aza indirebilir. Kalıp akışı analizi ve kapı yerleştirme optimizasyonu da kaynak çizgilerini önlemeye veya hafifletmeye yardımcı olabilir.
- Yanık izleri:Yanık izleri, malzemenin aşırı ısınması veya aşırı ısınması nedeniyle kalıplanmış parçanın yüzeyindeki renk değişimleri veya siyah noktalardır. Aşırı erime sıcaklığından kaçınmak, uygun soğutma kanallarını kullanmak ve döngü süresini optimize etmek yanık izlerinin önlenmesine yardımcı olabilir. Yeterli havalandırma, uygun kapı tasarımı ve kalıp sıcaklığının kontrol edilmesi de yanık izlerinin en aza indirilmesine katkıda bulunur.
Kalıplama Sonrası İşlemler: Bitirme ve Montaj
Enjeksiyon kalıplamadan sonra, birçok kalıplanmış parça, istenen nihai ürünü elde etmek için ek bitirme ve montaj işlemleri gerektirebilir. Bu kalıplama sonrası işlemler şunları içerebilir:
- Kırpma:Kırpma veya kesme aletlerini kullanarak kalıplanmış parçanın etrafındaki fazla malzemeyi çıkarın veya parlatın.
- Yüzey İşlem:Boyama, kaplama veya tekstüre etme gibi çeşitli teknikler kullanarak parça yüzeyinin görünümünü veya işlevselliğini geliştirme.
- Montaj:Nihai ürünü tamamlamak için birden fazla kalıplanmış parçanın birleştirilmesi veya bağlantı elemanları, ekler veya etiketler gibi bileşenlerin eklenmesi.
- Test:Boyut analizi, malzeme özellikleri testi veya performans testi gibi çeşitli test yöntemleriyle parça kalitesinin ve işlevselliğinin doğrulanması.
- Ambalaj ve Nakliye:Bitmiş ürünün müşterilere veya son kullanıcılara gönderilmek üzere uygun şekilde paketlenmesi ve etiketlenmesi.
Kalıplama sonrası operasyonların seçimi, spesifik uygulamaya ve istenen nihai ürün özelliklerine bağlıdır. Enjeksiyon döküm uzmanları, bitirme ve montaj uzmanları ile müşteri arasındaki yakın işbirliği, istenen mutlak ürün kalitesi ve işlevselliğini elde etmek için çok önemlidir. Kalıplama sonrası operasyonların uygun şekilde planlanması ve üretim sürecine entegre edilmesi, verimli üretimin ve yüksek kaliteli ürünlerin zamanında tesliminin sağlanmasına yardımcı olabilir.
Enjeksiyon Kalıplama ve Diğer Plastik Üretim Süreçleri
Her plastik üretim sürecinin avantajları ve sınırlamaları vardır, bu da onları farklı uygulamalar için uygun hale getirir.
- Enjeksiyon kalıplama: Enjeksiyon kalıplama, plastik parçalar üretmek için çok yönlü ve yaygın olarak kullanılan bir üretim sürecidir. Yüksek üretim verimliliği, hassas parça çoğaltma ve karmaşık geometriler oluşturma yeteneği gibi avantajlar sunar. Enjeksiyon kalıplama, yüksek hacimli üretim çalışmaları için uygundur ve çok çeşitli termoplastik malzemelerin kullanılmasına izin verir. Mükemmel boyutsal doğruluk ve yüzey kalitesi sunarak otomotiv, tüketim malları ve tıbbi cihazlar gibi çeşitli endüstriler için idealdir.
- Şişirme: Şişirme, öncelikle şişeler, kaplar ve otomotiv bileşenleri gibi içi boş plastik parçalar üretmek için kullanılan bir işlemdir. Plastiğin eritilmesini ve bir kalıp boşluğuna şişirilerek istenen şeklin oluşturulmasını içerir. Şişirme, yüksek hacimli üretim için uygundur ve aynı duvar kalınlığına sahip büyük, hafif parçalar üretebilir. Ancak parça karmaşıklığı ve malzeme seçimi açısından enjeksiyon kalıplamaya göre sınırlıdır.
- termoform:Termoform, termoplastik bir levhayı ısıtarak ve kalıplar veya vakumla şekillendirme kullanarak şekillendirerek plastik parçalar üretmek için kullanılan bir işlemdir. Ambalajlarda, tek kullanımlık ürünlerde ve tepsi, kapak gibi büyük ölçekli ürünlerde yaygın kullanım alanı bulmaktadır. Termoform, büyük parçalar için uygun maliyetli üretim sunar ve hızlı prototipleme sağlar. Bununla birlikte, enjeksiyonla kalıplamaya kıyasla parça karmaşıklığı, malzeme seçimi ve boyutsal doğrulukla ilgili sınırlamaları vardır.
- ekstrüzyon:Ekstrüzyon, plastik profiller, levhalar, tüpler ve filmler üretmek için sürekli bir süreçtir. Plastik reçinenin eritilmesini ve istenen şekli oluşturmak için bir kalıptan geçirilmesini içerir. Ekstrüzyon, tutarlı bir enine kesite sahip uzun, sürekli uzunluklarda plastik ürünler üretmek için uygundur. Ekstrüzyon, yüksek üretim hızları ve maliyet etkinliği sunarken, enjeksiyon kalıplamaya kıyasla karmaşık parça geometrileri ve hassas boyutsal kontrol açısından sınırlıdır.
- Sıkıştırma Kalıplama:Sıkıştırma kalıplama, önceden ölçülmüş miktarda termoset malzemeyi ısıtılmış bir kalıp boşluğuna yerleştirmeyi ve sertleşene kadar yüksek basınç altında sıkıştırmayı içerir. Otomotiv bileşenleri ve elektrik yalıtımı gibi yüksek mukavemete ve boyutsal kararlılığa sahip parçaların üretiminde yaygın kullanım alanı bulur. Sıkıştırma kalıplama, iyi parça tutarlılığı, yüksek üretim verimliliği ve geniş bir malzeme yelpazesi kullanma yeteneği sunar. Bununla birlikte, parça karmaşıklığı ve enjeksiyon kalıplamaya kıyasla döngü süresi açısından sınırlıdır.
Termoplastik Enjeksiyon Kalıplama Uygulamaları
Çeşitli endüstriler, çok yönlülüğü, verimliliği ve maliyet etkinliği nedeniyle yaygın olarak termoplastik enjeksiyon kalıplamayı kullanır. Termoplastik enjeksiyon kalıplama uygulamalarından bazıları şunlardır:
- Otomotiv endüstrisi: Otomotiv endüstrisi, iç ve dış döşeme, panolar, kapı panelleri, tamponlar ve elektrik konektörleri dahil olmak üzere çeşitli bileşenleri üretmek için yaygın olarak termoplastik enjeksiyon kalıplama kullanır. Süreç, hassas parça replikasyonuna, karmaşık geometrilere ve hafif malzemelere izin vererek yakıt verimliliğini ve tasarım esnekliğini artırır.
- Tüketici Malları:Enjeksiyon kalıplama, ev aletleri, elektronik cihazlar, ambalaj kapları ve oyuncaklar gibi tüketim mallarının üretiminde geniş uygulamalar bulur. Süreç, tutarlı boyutlara ve yüzey kalitesine sahip dayanıklı, yüksek kaliteli ürünlerin seri üretimini mümkün kılar. Ayrıca özelleştirme seçeneklerine ve hızlı ürün yinelemelerine olanak tanır.
- Tıbbi cihazlar:Enjeksiyon kalıplama, tıp endüstrisinde şırıngalar, cerrahi aletler, implante edilebilir bileşenler ve ilaç dağıtım sistemleri dahil olmak üzere çok çeşitli cihazların üretilmesinde çok önemli bir rol oynar. Süreç, sağlık sektörünün katı düzenleyici gerekliliklerini karşılayan steril, hassas ve biyouyumlu parçaların üretimini sağlar.
- Elektronik ve Elektrik Endüstrisi:Elektronik endüstrisi, elektrik konektörleri, mahfazalar, anahtarlar ve diğer bileşenleri üretmek için enjeksiyon kalıplama kullanır. İşlem, yüksek boyutsal doğruluk, mükemmel yüzey kalitesi ve ekleme kalıplama ve üst kalıplama gibi özellikleri birleştirme yeteneği sunarak karmaşık elektronik tertibatların verimli üretimine olanak tanır.
- Ambalaj Endüstrisi:Yiyecek ve içecek, ilaç ve kişisel bakım dahil olmak üzere çeşitli endüstriler, plastik ambalaj kapları, kapaklar, kapaklar ve şişeler üretmek için yaygın olarak enjeksiyon kalıplama kullanır. Süreç, verimli üretim döngüleri ile hafif, dayanıklı ve estetik açıdan çekici ambalaj çözümlerinin oluşturulmasını sağlar.
- Havacılık ve Uzay Sanayii:Havacılık sektörü, hava kanalları, braketler, iç paneller ve yapısal parçalar gibi hafif ve yüksek performanslı bileşenlerin imalatı için enjeksiyon kalıplama kullanır. Süreç, gelişmiş malzemelerin ve karmaşık parça geometrilerinin kullanılmasına izin vererek ağırlığın azaltılmasına ve geliştirilmiş yakıt verimliliğine katkıda bulunur.
Termoplastik Enjeksiyon Kalıplamanın Çevresel Etkisi
Termoplastik enjeksiyon kalıplama, birçok faydası nedeniyle popüler bir üretim sürecidir, ancak çevresel etkisini de göz önünde bulundurmak önemlidir. İşte dikkate alınması gereken bazı noktalar:
- Malzeme Verimliliği:Termoplastik enjeksiyon kalıplama, atıkları en aza indirerek malzeme verimliliğini artırır. İşlem, kalıba enjekte edilen malzeme miktarı üzerinde hassas kontrol sağlayarak fazla malzeme ihtiyacını azaltır. Üreticiler ayrıca hurda veya reddedilen parçaları yeniden kullanmak için yeniden öğütme ve geri dönüşüm tekniklerini kullanarak malzeme israfını daha da azaltabilir.
- Enerji tüketimi:Üreticiler, enjeksiyon kalıplama makinelerini servo motorlar ve değişken hızlı sürücüler gibi gelişmiş teknolojileri içeren modern modellerle enerji verimli olacak şekilde tasarlıyor. Bu özellikler, kalıplama sırasında güç tüketimini azaltarak enerji kullanımını optimize eder, bu da daha düşük enerji gereksinimleri ve daha düşük çevresel etki ile sonuçlanır.
- Atık Yönetimi:Üreticiler, malzeme israfını en aza indirirken, artık malzemeleri, yollukları veya yollukları işlemek için uygun atık yönetimi uygulamalarını uygulamalıdır. Üreticiler, enjeksiyon kalıplama sırasında oluşan plastik atıkları toplamak ve yeniden kullanmak için geri dönüşüm programları oluşturabilir, böylece çöplüklere gönderilen atıkları azaltabilir.
- Emisyon Azaltma: Termoplastik enjeksiyon kalıplama genellikle diğer üretim süreçlerine göre daha düşük emisyon üretir. Üreticiler, çevre dostu malzemeler kullanarak, enerji tasarruflu ekipman uygulayarak ve salınan emisyonları yakalamak için gelişmiş egzoz ve filtreleme sistemleri kullanarak emisyonları azaltabilir.
- Sürdürülebilir Malzeme Seçenekleri:Termoplastik malzemelerin seçimi, enjeksiyon kalıplamanın çevresel sürdürülebilirliğini önemli ölçüde etkileyebilir. Biyobozunur veya biyo-bazlı plastiklerin yanı sıra geri dönüştürülmüş veya geri dönüştürülebilir malzemeleri tercih etmek, sürecin genel ekolojik ayak izini azaltmaya yardımcı olabilir.
Yaşam Döngüsü Hususları: Kalıplanmış ürünün tüm yaşam döngüsünü göz önünde bulundurmak, çevresel etkisini değerlendirmek için esastır. Tasarım ve malzeme seçimi aşamalarında üreticiler, parçanın dayanıklılığı, geri dönüştürülebilirliği ve kullanım ömrü sonunda imha veya yeniden kullanım potansiyeli gibi faktörleri göz önünde bulundurmalıdır.
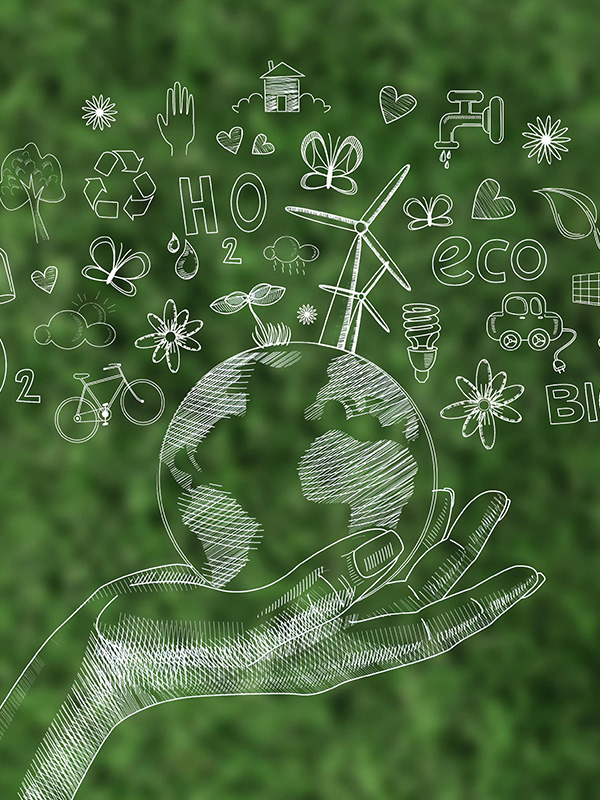
Termoplastik Enjeksiyon Kalıplamanın Geleceği
Termoplastik enjeksiyon kalıplamanın geleceği, teknolojide devam eden ilerlemeler ve çeşitli endüstrilerde yüksek kaliteli, hassas parçalara yönelik artan talep ile umut verici görünüyor. Önümüzdeki yıllarda beklenen önemli gelişmelerden bazıları şunlardır:
- Verimliliği artırmak ve maliyetleri azaltmak için artan otomasyon ve robotik kullanımı.
- Çabalar, parça performansını iyileştirmek ve yeni uygulamalara olanak sağlamak için yeni malzemeler ve süreçler geliştirmeye odaklanmıştır.
- Enjeksiyon kalıplamanın çevresel etkisini azaltmak için geri dönüştürülmüş malzemeler kullanmak ve enerji tüketimini optimize etmek gibi sürdürülebilir uygulamaların giderek daha fazla benimsenmesidir.
- Tasarım ve üretim süreçlerini iyileştirmek için 3D baskı ve simülasyon yazılımı gibi dijital teknolojilerin daha fazla entegrasyonu.
Küresel enjeksiyon kalıplama pazarı, çeşitli sektörlerde plastik ürünlere yönelik artan talebin etkisiyle, özellikle gelişmekte olan ekonomilerde genişlemektedir.
Doğru Enjeksiyon Ortağını Seçmek
Doğru plastik enjeksiyon iş ortağını seçmek, projenizin başarısı için çok önemlidir. Uyumlu ve uzun süreli bir ortaklık sağlamak için birden fazla seçeneği değerlendirmek, saha ziyaretleri yapmak ve kapsamlı tartışmalara katılmak için zaman ayırın.
- Uzmanlık ve Deneyim:Sektörde kapsamlı bilgi ve deneyime sahip bir plastik enjeksiyon ortağı arayın. Çeşitli sektörlerdeki müşterilere yüksek kaliteli ürünler ve çözümler sunma konusunda kanıtlanmış bir sicile sahip olmalıdırlar. Farklı malzemeler, kalıp tasarımları ve üretim süreçleri hakkındaki anlayışlarını göz önünde bulundurun.
- Üretim Yetenekleri: Enjeksiyon kalıplama iş ortağının üretim yeteneklerini değerlendirin. Proje gereksinimlerinizi karşılamak için modern makine ve teknolojilere sahip iyi donanımlı bir tesise sahip olduklarından emin olun. Üretim kapasitelerini, farklı parça boyutlarını ve karmaşıklıklarını işleme yeteneklerini ve istediğiniz üretim hacimlerini ve zaman çizelgelerini karşılama yeteneklerini göz önünde bulundurun.
- Kalite güvencesi:Enjeksiyon kalıplamada kalite çok önemlidir. Potansiyel ortağın kalite kontrol sistemlerini ve sertifikalarını değerlendirin. Katı kalite standartlarını takip eden, sağlam denetim süreçlerine sahip olan ve parça kalitesi ve tutarlılığını sağlamak için kapsamlı testler gerçekleştiren ortaklar arayın.
- Tasarım ve Mühendislik Desteği:Güvenilir bir plastik enjeksiyon iş ortağı, parça tasarımınızı üretilebilirlik açısından optimize etmek için tasarım ve mühendislik desteği sunmalıdır. Parça kalitesini ve verimliliğini artırmak için malzeme seçimi, kalıp tasarımı ve süreç optimizasyonu konularında değerli girdiler sağlayabilecek yetenekli mühendislere sahip olmalıdırlar.
- Maliyet rekabet gücü:Maliyet tek belirleyici faktör olmamakla birlikte, plastik enjeksiyon ortağının fiyatlandırmasını ve maliyet rekabetçiliğini değerlendirmek esastır. Ayrıntılı fiyat teklifleri isteyin ve alet maliyetlerini, malzeme maliyetlerini, işçilik maliyetlerini ve sağladıkları ek hizmetleri göz önünde bulundurun.
- İletişim ve İşbirliği:Başarılı bir ortaklık için etkili iletişim ve işbirliği şarttır. Plastik enjeksiyon iş ortağının iyi iletişim kanallarına sahip olduğundan, sorularınıza yanıt verdiğinden ve düzenli proje güncellemeleri sağlayabildiğinden emin olun. İşbirlikçi bir yaklaşım, gereksinimlerinizi karşılamamıza ve herhangi bir zorluğu derhal ele almamıza yardımcı olacaktır.
- Müşteri Referansları ve Yorumları:Plastik enjeksiyon iş ortağıyla diğer müşterilerin deneyimlerine ilişkin fikir edinmek için müşteri referansları arayın veya incelemeleri/tanıtımları okuyun. Bu bilgileri elde etmek, güvenilirliklerini, çabukluklarını ve genel müşteri memnuniyet düzeylerini belirlemeye yardımcı olabilir.
Sonuç
Termoplastik enjeksiyon kalıplama, büyük miktarlarda plastik parçaların üretilmesi için çok yönlü ve uygun maliyetli bir yöntemdir. Yüksek hassasiyet ve tutarlılıkla karmaşık şekiller üretebilme yeteneği, otomotiv, medikal, elektronik ve tüketim malları dahil olmak üzere çeşitli endüstriler için popüler bir seçim haline geldi. Avantajları, dezavantajları ve tasarım hususları dahil olmak üzere termoplastik enjeksiyon kalıplamanın farklı yönlerini anlayarak, iş ihtiyaçlarınız için doğru enjeksiyon kalıplama ortağını seçme konusunda bilinçli kararlar verebilirsiniz.