Injekzio-moldeketaren ohiko moldaketa-akatsen konponbideak
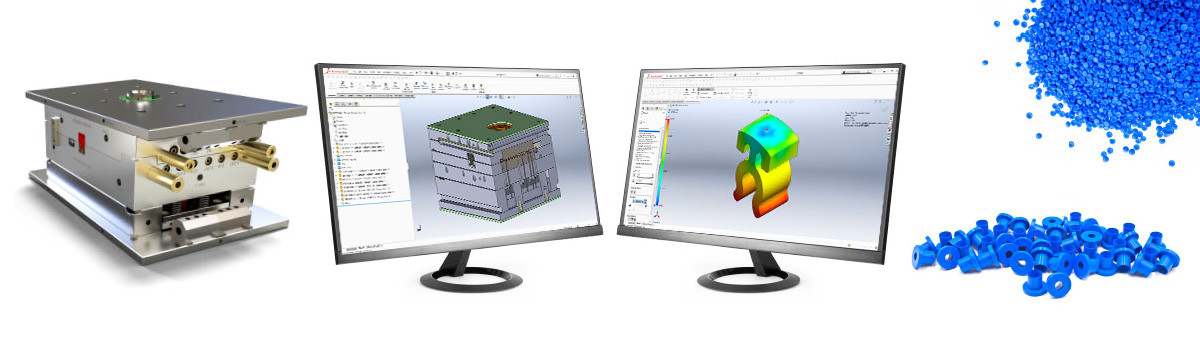
Plastikozko injekziozko piezak prozesatzeko moldeak erabiltzean akatsak ohikoak dira, eta horrek prozesatzeko eraginkortasunari eragiten dio neurri handi batean. Honako hauek plastikozko injekzio-moldeen piezen moldaketa-akats arruntak eta soluzioak dira.
Plano laburrak
Plano laburrak egindako produktuak osatu gabe daudela aipatzen dute, moldeak guztiz beteta ez daudelako.
Akats hori atetik urrunen dagoen tokian edo moldeko eremu estuetatik soilik irits daitezkeen piezetan agertzen da normalean, eremu estuek urtuaren fluxuari eragin diezaioketelako.
Jaurtiketa laburrak mikro-fluxu-markak sor ditzake edo produktuaren zati handi bat falta da, jakina.
eragin:
Plano laburren arrazoiak hauek dira:
Moldean injektatutako lehengaia ez da nahikoa.
Urtutakoen erresistentzia handia da, eta ondorioz ezin da moldea guztiz bete.
Moldearen aireztapena eskasa da eta urtzea blokeatzen duen kavitazio-sorkuntza eragiten du, urtzeak ezin du moldearen eremu batzuetara joan.
burrs
Moldearen barrunbetik produktuari ateratako gehiegizko lehengaien itsaspenetik sortzen dira errebak.
Akats hori produktuaren ertzetan edo moldez osaturiko zati bakoitzean egongo da. Lehengaia moldetik gainezka egin daiteke, edo mugitzeko eta finkatzeko moldeen lotura guneetatik.
Moldearen nukleoan errebak ere aurki daitezke, hau da, presio hidraulikoaren edo pin angelurraren ondorioz.
Erreben larritasuna aldatu egiten da, batzuetan mehea, beste batzuetan lodiagoa.
eragin:
Erreben arrazoiak honako hauek dira:
Lotzeko moldearen gainazala hondatuta dago edo oso higatuta dago.
Mugitzeko moldea eta finkatzeko moldea blokeatuta daudenean desplazatzen dira.
Moldearen lehengaien presioa moldea estutzeko indarra baino handiagoa da.
Goian aipatutako hirugarren baldintza hainbat arrazoiren ondorioz sortuko litzateke. Ondorengo egoeretan, lehengaien presioa moldea estutzeko indarra baino handiagoa da.
Injekzio moldearen lehen fasean (moldeak betetzeko fasean), lehengai gehiegi betetzen da, eta horrek moldearen barruko presioa areagotzen du.
Moldea betetzeko prozesuan, urtze-fluxuaren erresistentzia handiak moldearen barruko presioa ere igoko du.
Moldearen barrunbearen presioa altuegia da presioari eusteko fasean.
Moldea estutzeko indarra ez da nahikoa.
degradazioa
Deskonposizioak emaitza asko ekar ditzake. Arazoaren hedadura eta larritasuna ere aldatu egiten dira. Kasurik larrienean, produktuaren kolore osoa eta propietate mekaniko txarrak eragin ditzake. Tokiko degradazioak marra edo orban ilunak baino ez ditu eragingo.
eragin:
Degradazioa lehengaia hondatuta egoteak eragiten du. Plastikoak osatzen dituzten kate luzeko molekulak deskonposatuko dira gehiegizko beroaren edo gehiegizko ebakidura-tentsioaren eraginez. Molekulen deskonposizioan, gas lurrunkorrak degradazio-prozesua bizkortuko du, eta horrek lehengaiaren deskolorazioa eragingo du. Molekula kopuru handien deskonposizioak lehengaiaren edukia hautsi eta propietate mekanikoetan eragin negatiboa eragingo du.
Tokiko degradazioa materialaren upelaren tenperatura irregularretik sor daiteke.
Degradazioa honako egoera hauetan gerta daiteke:
Lehengaia gehiegi berotzen ari da material upelean edo kanal beroko sisteman.
Lehengaia denbora gehiegi geratzen da upelean.
Injekzio-moldeaketa prozesuan, lehengaiari eragiten dion ebakidura-esfortzua handiegia da. Toberak blokeatzen badira, edo ateak eta korridoreak estuegiak badira, ebakidura-esfortzua handituko da.
deformazio
Egoera normaletan, produktuen formek moldeenarekin bat etorri behar dute. Deformazioak produktuen deformazioari egiten dio erreferentzia.
Egoera okertzen denean, produktuak guztiz deformatuko dira moldetik kanporatzean. Egoera larria ez denean, produktuaren forma irregulartasun txikiak agertuko dira.
Luzeak baina euskarririk gabeko ertz edo plano handirik gabe deformaziorako joera gehien duten eremuak dira.
eragin:
Deformazioaren arrazoiak:
Tenperatura altuegia da moldea askatzen denean.
Hozte-denbora eremu lodietan eta meheetan desberdina denez, edo moldearen tenperatura-aldea mugitzen den moldean eta finkatzeko moldean, produktuen barruko txikizioa desberdina da.
Moldearen fluxua ez da leuna betetzen betetzerakoan («Izozteko orientazioa» deitzen dena) edo moldearen barrunbeko presioa altuegia da presioari eusteko fasean.
ezpurutasun
Ezpurutasunak askotan kolore, adabaki edo marra ezberdinetako orban moduan agertzen dira. Ohikoena puntu beltza da.
Ezpurutasunak orban txikiak izan daitezke, baina larria denean marra nabariak edo decolorazio zati handia ere izan daitezke.
eragin:
Ezpurutasunak lehengaiekin nahasten diren produktuek sortzen dituzte, hala nola:
Lehengaia produktuekin nahasten da upeletara garraiatzen denean.
Lehengaiaren deskonposizioa edozein ebaketa-mekanismoetatik eror daiteke eta lehengaietan nahastu daiteke, hala nola makina-torlojuak, lehortzeko danborraren barruko horma, junturak / toberak.
Ijezketa
Laminazioak "azalaren efektua" sortuko du produktuen gainazalean, produktuen eta beste lehengaien gainazaleko propietateen eta ehunduraren desberdintasunak eragindakoa, eta kendu daitekeen azal zuritu bat eratzen du.
Laminazioa larria denean, gurutze-eremu osoa geruza ezberdinez osatuta dago, eta ez da elkarrekin urtu. Akatsak agerikoak ez direnean, produktuen itxurak baldintzak bete ditzake, baina produktuen propietate mekanikoak hautsiko ditu.
eragin:
Laminaziorako bi arrazoi nagusi daude. Lehenengoa bi lehengai mota gaizki nahasten direnean. Bi lehengaiak presiopean aldi berean ontzira eramango dira. Hala ere, hoztean moldea elkarrekin urtu ezin denean, geruza desberdinak produktuak osatzeko indarrez estutzen diren bezalaxe.
Bigarrena: urtu hotza ate estutik pasatzera behartzen bada, ebakidura-esfortzua sortuko da. Ebakidura-tentsio handiegiak aldez aurretik urtutako geruza guztiz fusionatu ezin izatea eragingo du.
Nahasteko arriskua:
Kontuan izan behar den gauza bat da lehengai batzuek elkarrekin nahastuta erreakzio kimiko indartsua eragingo dutela, hala nola PVC eta Avetal ez direla nahastu behar.
Zilarrezko lineala
Sliver lineala tokiko fenomenoa izan daiteke, baina larria denean azalera osora heda daiteke.
Zilarrezko linealak produktuen itxuran eragina izango du eta produktuen propietate mekanikoak ere kaltetzen ditu.
eragin:
Bi puntu hauek zilarrezko lineala eragiten dute:
Lehengaia bustita dago eta horietako batzuek aireko lurruna xurgatuko dute. Lehengaia hezeegia bada, presio-lurruna upelaren tenperatura eta presio altuetan sor daiteke. Lurrun horiek produktuaren gainazala zeharkatzen dute eta zilarrezko marra osatzen dute.
Urtuak termikoki kaltetu zuen eta tokiko degradazioa sortzen du. Sortutako gas lurrunkorra moldearen gainazalean blokeatuko da eta produktuen gainazalean marra sortuko da.
Hau ez da degradazioa bezain okerragoa. Urtutako tenperatura altua bada edo plastifikazioan zehar ebakidura-esfortzua jasaten badu edo moldean injektatzen bada, hori gerta liteke.
Distira/itzala
Produktuen gainazaleko akabera moldeen berdina izan behar du. Biren gainazaleko akabera desberdina denean, distira/itzal akatsak gertatu dira.
Gainazala iluna izango da akatsak gertatzen direnean, eta gainazal zakarra leuna eta distiratsua da.
eragin:
Distira/itzalen arrazoiak hauek dira:
Urtuak ez du isurtzen edo moldearen gainazalaren tenperatura baxua da, eta ondorioz, moldearen gainazaleko akabera ezin da bikoiztu materiala moldatzen denean.
Presioari eusten zaion bitartean, barrunbean dagoen presioa ez da nahikoa materiala hozteko prozesuan moldearen gainazalera atxikitzeko, uzkurtze-markak utziz.
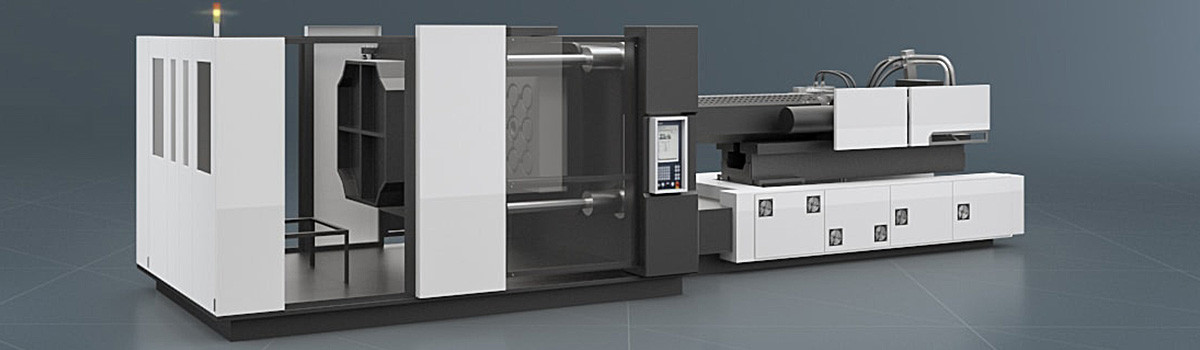
Fluxuak
Fluxu-markak produktuen gainazalean hainbat formatan aurki daitezke. Orokorrean, itzal eremu bat osatuko du.
Fluxu-markek ez dute produktuen gainazalean erlieberik edo depresiorik sortzen, hatzekin sentitu ezin dena. Akats horri arrastatze-markak, mamuak eta itzalak ere esaten zaio.
Fluxu-markak nabariak direnean, zirrikituak sortuko ditu eta produktuen gainazalean markak bezalako akatsak utziko ditu.
eragin:
Fluxu-markak aurki daitezke:
Urtzearen jariakortasuna eskasa da edo moldearen gainazaleko tenperatura baxua da, eta ondorioz plastikoaren fluxuarekiko erresistentzia handia da moldea betetzeko prozesuan.
Moldearen betetzean, erresistentzia duen urtze-fluxua, trokelaren gainazal irregularrak, trokelaren gainazalean inprimatutako markak edo ereduak edo betetze-prozesuan urtutako fluxuaren noranzko aldaketak sor daitezke.
Lotura-lerroa
Lotura-lerroa bi urtze-fronte elkartzen direnean sortzen da moldea betetzean, eta produktuaren gainazalean lerro bat bezala agertuko da.
Lotura-lerroa produktuen gainazaleko pitzadura-lerroa bezalakoa da, detektatzeko begi-bistakoa ez dena.
Moldeak diseinatzerakoan, ikus daitezkeen juntagailu-lerro batzuk saihestezinak dira. Kasu honetan, artikulazio-lerroa ahalik eta gehien laburtzen du, produktuen indarra eta itxura kaltetu ez daitezen.
eragin:
Urtze-frontea sortzeko arrazoi asko daude. Arrazoi posibleena moldearen nukleoaren ertzetan zehar urtutako fluxua izan daiteke. Bi urtzeak elkartzen direnean, juntagailu-lerroak sortzen ditu. Bi urtutako aurrealdeko tenperatura nahikoa altua izan behar da ondo uztar daitezen eta produktuen indarrari eta itxurari eraginik ez izateko.
Bi urtuak guztiz fusionatu ezin direnean, akatsak sortuko dira.
Akatsen arrazoiak:
Moldeak zati lodiagoak eta meheagoak ditu, eta urtzeen fluxu-abiadura desberdina da, urtzea moldearen zati mehetik igarotzen denean, tenperatura baxua da.
Korrikalari bakoitzaren luzera ezberdina da. Korrikalari bakartiak erraz hozten dira.
Moldearen barrunbearen presioa ez da nahikoa presioari eusteko fasean urtzea guztiz fusiona dadin.
Gainerako burbuilek urtze-frontea ezin fusionatu egiten dute, eta horrek ere erre egingo du.
Burning
Erretzea plano laburren antzekoa da, baina lausotzen diren ertz irregularrak eta erre-usain arina ditu. Karbono beltzaren eremuak produktuan agertuko dira, egoera larria denean, plastikozko erre usainarekin batera.
Akatsak ezabatzen ez badira, sarritan deposizio beltza egoten da moldean. Erretzeak sortutako gas edo petrolio substantziak berehala egiaztatzen ez badira, aire-zuloak blokeatu ditzakete. Erretzea, oro har, bideen amaieran aurkitzen da.
eragin:
Erretzea barne-errekuntzaren efektuak eragiten du. Oso denbora gutxian aireko presioa nabarmen handitzen denean, tenperatura igo egingo da eta erredura eragingo du. Bildutako datuen arabera, barne-errekuntzaren efektuak injekzio-moldaketa prozesuan tenperatura altua sor dezake 600 graduraino.
Erretzea gerta daiteke:
Moldea betetzeko abiadura azkarra da, airea moldearen barrunbetik kanporatu ezin dadin, eta aire-burbuilak sortzen ditu sarrerako plastikoaren blokeagatik, eta barne-errekuntza efektua eragiten du konprimitu ondoren.
Aire-zuloak blokeatuta daude edo aireztapena ez da leuna.
Moldearen airea aire-zuloetatik hustu behar da. Aireztapena posizioak, kopuruak, tamainak edo funtzioak eragiten badu, airea moldean geratuko da eta erre egingo du. Moldea estutzeko indar handiak aireztapen eskasa ere ekarriko du.
shrinkage
Uzkurdura produktuen gainazaleko zulo txikiei dagokie.
Akatsak txikiak direnean, produktuen gainazala irregularra da. Larria denean, produktuen eremu handia erori egingo da. Arkuak, heldulekuak eta irtenguneak dituzten produktuek uzkurtze-akatsak izaten dituzte.
eragin:
Uzkurdura hoztean lehengaien eremu handian uzkurtzearen ondorioz sortzen da.
Produktuen eremu lodietan (arkua bezala), materialaren nukleo epela baxua da, beraz, uzkurdura gainazalekoa baino beranduago gertatuko da, eta horrek uzkurdura-indarra sortuko du lehengaiaren barruan, eta kanpoko aldea barruko depresioan sartuko da. uzkurdura sortzeko.
Uzkurdurak egoera hauetan gertatzen dira:
Moldearen barrunbean dagoen presioa hozte-prozesuan lehengaiaren uzkurtzetik sortutako indarra baino txikiagoa da.
Moldearen barrunbearen presio-denbora nahikoa hozte-prozesuan zehar, eta ondorioz, atetik barrunbetik lehengaiak isurtzen dira.
Lehengaiak ez du behar adinako buffering-ahalmena moldatzeko eta presioari eusteko fasean, torlojua guztiz erretiratzen baita gehiegizko lehengaia injektatu aurretik.
Ateen eta korridoreen ebakidura-eremuak produktuen lodiera baino askoz txikiagoak dira, hau da, ateak dagoeneko izoztuta daude produktuak estrusio-prozesuaren aurretik.
Bubbles
Hutseko burbuilak aire burbuilen moduan aurkezten dira, produktu gardenetan erraz aurki daitezkeenak. Produktu opakuen ebakiduran ere ikus daiteke.
eragin:
Aire-burbuilak produktuen hutsunea dira, hozte-prozesuan lehengaia uzkurtzen denean sortzen direnak.
Uzkurduraren antzera, lehengaiaren barneak uzkurtzeko indarra sortzen du. Desberdintasuna da produktuen kanpoko itxura burbuilak sortzen direnean solidotu egin dela eta ez dagoela kolapsorik, beraz, burbuila hutsak sortzen dira.
Burbuilen kausak murrizketaren berberak dira, besteak beste:
Moldearen barrunbearen presioa eraginkorra
Barrunbearen presio-denbora nahikoa ez da
Korrikalariaren eta atearen tamaina txikiegia da
Ihinztatze markak
Ihinztatze markak atearen parean dagoen hariztatutako eremuari dagozkio. Ihinztatze-markek produktuen itxurari eragiten ez ezik, produktuen indarrari ere eragiten diote.
eragin:
Ihinztatze-markak moldeak betetzeko prozesuan kontroletik kanpo dagoen urtze-fluxuaren ondorioz sortzen dira.
Urtutako plastikoa presio handipean sartzen da moldean. Moldea betetzeko abiadura altuegia bada, plastikoa moldearen barrunbeko hutsunetik aterako da eta azkar itzuliko da eta hoztu egingo da. Momentu horretan, hariak sortzen dira, eta horrek blokeatu egiten du urtutako plastikoa ateetan sartzea.
Ihinztatzeko marken kausa nagusia ateen posizio okerra edo atearen diseinua dira. Bi egoera hauek akatsen egoera okerrera egingo dute:
Moldea betetzeko abiadura handia
Moldea betetzean urtze-fluxu eskasa