Thermoplastic ynjeksje moulding
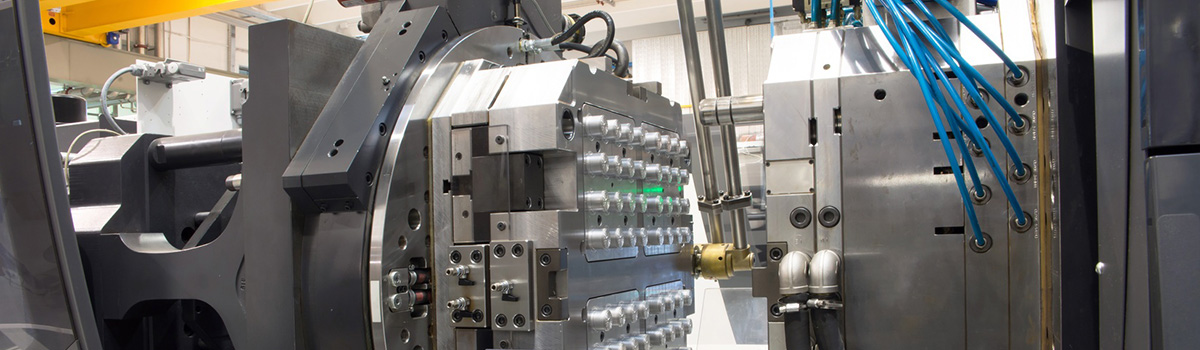
Thermoplastysk ynjeksjefoarmjen is in populêr fabrikaazjeproses dat wurdt brûkt om ferskate plestikdielen te meitsjen foar meardere yndustry. Dit proses omfettet it smelten fan plestik pellets en ynjeksje se yn in skimmel om in trijediminsjonale foarm te meitsjen. Thermoplastysk ynjeksjefoarmjen is heul effisjint en kosten-effektyf foar it produsearjen fan grutte folumes fan heechweardige plestik dielen mei strakke tolerânsjes. Dizze wiidweidige hantlieding sil de ferskate aspekten fan thermoplastysk ynjeksjefoarm ûndersykje, ynklusyf de foardielen en neidielen, de soarten brûkte thermoplastyk, it ynjeksjefoarmproses, ûntwerpoerwagings, en folle mear.
Skiednis fan Thermoplastic Injection Molding
De skiednis fan termoplastysk ynjeksjefoarmjen giet oer in ieu fan technologyske foarútgong, materiaalûntwikkelingen en yndustriële tapassingen. Fan har beskieden begjin as in celluloid-foarmproses oant de hjoeddeiske ferfine technology, bliuwt ynjeksjefoarmjen in fitale produksjetechnyk, dy't ynnovaasje driuwt en ferskate yndustry foarmje.
- Iere ûntjouwings:John Wesley Hyatt en syn broer Jesaja ûntwikkele de earste praktyske ynjeksje moulding masine, tracing de oarsprong fan thermoplastic molding werom nei de lette 19e ieu. Yn 1872 patintearren se in apparaat dat in plunger brûkte om celluloid yn in skimmelholte te ynjeksje, wêrtroch fêste objekten makke wurde. Dizze trochbraak lei de basis foar it moderne spuitgietproses.
- Foarútgong yn materialen:Yn 'e iere 20e ieu iepene de yntroduksje fan nije syntetyske polymers nije mooglikheden foar ynjeksjefoarmjen. Bakelit, in fenolhars, waard in populêr materiaal foar foarmjen troch syn treflike elektryske isolearjende eigenskippen. Yn 'e rin fan' e jierren '1930 en 1940 late foarútgong yn polymearchemie ta de ûntwikkeling fan oare thermoplasten, lykas polystyrene en polyetyleen, dy't it oanbod fan materialen dy't geskikt binne foar ynjeksjefoarmjen fierder útwreide.
- Yndustriële oanname: De wiidferspraat oannimmen fan thermoplastysk ynjeksjefoarmjen begon yn 'e jierren 1950, om't fabrikanten har kosten-effektiviteit en veelzijdigheid erkende. Yntroduksje fan hege druk masines tastien foar flugger syklus tiden en ferhege produksje folume. Dêrtroch ûntstie in ferskaat oan produkten foar sawol persoanlik as yndustrieel gebrûk. Dizze omfette auto-ûnderdielen, húshâldlike apparaten en boartersguod.
- Technologyske ynnovaasjes:Yn 'e rin fan' e desennia bleau de technology foar ynjeksjefoarmjen evoluearje. Yn 'e 1960's ûntstiene komputer-kontroleare masines, wêrtroch't sekuere kontrôle oer it foarmproses mooglik makken. De ynfiering fan hot runner systemen yn de jierren 1980 fermindere ôffal en ferbettere effisjinsje troch elimineren de needsaak foar runners en sprues. Yn 'e ôfrûne jierren hawwe foarútgongen fan automatisearring, robotika en 3D-printsjen de ynjeksjefoarmyndustry fierder revolúsjonearre, wêrtroch komplekse ûntwerpen mooglik binne en produksjetiid ferminderje.
- Duorsumens en Recycling:Mei tanimmende miljeusoarch hat de ynjeksjefoarmsektor duorsumensmaatregels omearme. Fabrikanten hawwe ûntwikkele bio-basearre en recycled thermoplasten, ferminderjen it fertrouwen op fossile brânstof-basearre materialen. Derneist hawwe ferbettere technologyen foar recycling it opnij ferwurke fan post-konsumint en post-yndustrieel ôffal, it minimalisearjen fan de miljeu-ynfloed fan thermoplastysk ynjeksjefoarmjen.
- takomstperspektyf:De takomst fan thermoplastysk ynjeksjefoarmjen sjocht der kânsryk út. De yndustry ûndersiket ynnovaasjes lykas mikro-ynjeksjefoarmjen foar miniatuerkomponinten, multi-materiaal en overmoldingtechniken foar komplekse dielen, en yntegrearjen fan yntelliginte technologyen foar prosesmonitoring en optimisaasje. Fierder ferwachtsje ûndersikers foarútgong yn biologysk ôfbrekbere materialen en additive manufacturing om it fjild te revolúsjonearjen, wêrtroch it ynjeksjefoarmjen noch duorsumer en mearsidiger wurdt.
Foardielen fan Thermoplastic Injection Moulding
Thermoplastysk ynjeksjefoarmjen biedt in protte foardielen foar fabrikanten. It biedt ûntwerpfleksibiliteit, wêrtroch komplekse en yngewikkelde ûntwerpen mei ferskate funksjes mooglik binne. It proses is kosten-effisjint, it ferminderjen fan materiaal ôffal en ferleget ienheid kosten. Thermoplastysk ynjeksjefoarming stipet meardere materialen, en biedt veelzijdigheid foar ferskate tapassingen.
- Designfleksibiliteit:Thermoplastysk ynjeksjefoarm makket yngewikkelde en komplekse ûntwerpen mooglik mei funksjes lykas ûndersnijdingen, tinne muorren en wikseljende dikten, wêrtroch ûntwerpers enoarme frijheid leverje.
- Kosteneffektiviteit: It proses is heul effisjint, it ferminderjen fan materiaalôffal en ferleget ienheidskosten. Tagelyk foarmjen fan meardere dielen en rappe produksjesyklusen drage by oan kostenbesparring.
- Materiaal veelzijdigheid: Thermoplastysk ynjeksjefoarming stipet in breed oanbod fan materialen, wêrtroch fabrikanten de meast geskikte opsje kinne kieze foar elke applikaasje, ynklusyf rigide as fleksibele, transparante of ûntrochsichtige, en gemysk resistinte materialen.
- Sterkte en duorsumens:Ynjeksjefoarmige thermoplasten kinne poerbêste meganyske eigenskippen fertoane, lykas hege sterkte, taaiens en ynfloedresistinsje. Opsjes foar fersterking, lykas glês of koalstoffezels, ferbetterje dizze eigenskippen fierder.
- Konsistinsje en kwaliteit:Molders soarget foar konsekwinte part-to-part kwaliteit en diminsjonele krektens, it leverjen fan strakke tolerânsjes en betroubere produkten. It proses soarget ek foar in glêde en unifoarme oerflakfinish, wêrtroch't de needsaak is foar ekstra finishoperaasjes.
- Skalberens en massaproduksje:Ynjeksjefoarmjen is skalberber fan leech nei hege folumes, wêrtroch it geskikt is foar massaproduksje. Sadree't fabrikanten meitsje de skimmel, se kinne produsearje grutte hoemannichten identike dielen mei minimale fariaasjes.
- Yntegraasje en gearstalling:Ynjeksjefoarmige dielen kinne meardere komponinten yn ien stik opnimme, wat de needsaak foar ekstra assemblageprosessen ferminderje. Dizze yntegraasje ferbettert produktprestaasjes, ferminderet assemblagetiid en ferleget kosten.
- Duorsumens:De yndustry foar spuitgieten toant in tanimmende fokus op duorsumens. De beskikberens fan bio-basearre en recycled materialen makket it mooglik om miljeufreonlike produkten te produsearjen. It effisjinte materiaalgebrûk en recycleberens fan thermoplastyk draacht by oan in griener produksjeproses.
Dizze foardielen hawwe it in breed oannommen produksjemetoade makke yn ferskate yndustry, it leverjen fan hege kwaliteit, kosten-effektive en miljeufreonlike oplossingen foar komplekse produkteasken.
Neidielen fan Thermoplastic Injection Moulding
Wylst thermoplastysk ynjeksjefoarmjen in protte foardielen biedt, binne d'r ek ferskate neidielen. Fabrikanten moatte dizze faktoaren soarchfâldich beoardielje en se weagje tsjin 'e foardielen om de geskiktheid fan thermoplastysk ynjeksjefoarmjen foar har spesifike tapassingen te bepalen.
- Hege earste ynvestearring: It opsetten fan in thermoplastyske ynjeksjefoarmoperaasje fereasket in wichtige earste ynvestearring yn skimmelûntwerp en fabrikaazje en oankeap fan spesjalisearre masines. De kosten ferbûn mei it meitsjen fan mallen en tooling kinne substansjeel wêze, foaral foar komplekse en yngewikkelde ûntwerpen.
- Design beheinings: Wylst thermoplastysk ynjeksjefoarmjen ûntwerpfleksibiliteit biedt, besteane bepaalde beheiningen. Bygelyks, it berikken fan unifoarme muorredikte yn it hiele diel kin útdaagjend wêze, wat liedt ta fariaasjes yn materiaalferdieling en potinsjele strukturele swakkens. Derneist kin de oanwêzigens fan ûndersnijdingen as komplekse geometry's it gebrûk fan ekstra skimmelfunksjes as sekundêre operaasjes fereaskje, tanimmende kosten en produksjetiid.
- Lange liedingstiden:It proses fan it ûntwerpen en fabrisearjen fan mallen foar ynjeksjefoarmjen kin tiidslinend wêze, wat liedt ta langere leadtiden foar produktûntwikkeling. It iteraasjeproses fan ûntwerp, skimmelproduksje en testen kinne wichtige tiid tafoegje oan 'e totale produksjetiidline, dy't miskien net geskikt is foar projekten mei strakke deadlines.
- Materiaal seleksje beheiningen:Hoewol't thermoplastic molding stipet in breed skala oan materialen, der binne bepaalde beheinings en beheinings. Guon materialen kinne spesifike ferwurkingseasken hawwe as beheinde beskikberens, fan ynfloed op ûntwerpkeuzes en materiaalseleksje foar in bepaalde tapassing.
- Beperkingen foar dielgrutte:Ynjeksjefoarmmasines hawwe grutte beheiningen, sawol yn termen fan 'e fysike grutte fan it apparaat as de grutte fan' e mallen dy't se kinne passe. It produsearjen fan enoarme dielen kin spesjalisearre apparatuer as alternative produksjemetoaden fereaskje.
- Miljeu-ynfloed:Wylst de yndustry wurket oan duorsumens, genereart it thermoplastyske ynjeksjefoarmproses noch ôffalmateriaal, ynklusyf skrap en sprues. Goede ôffier en recycling fan dizze materialen binne nedich om de miljeu-ynfloed te minimalisearjen.
- De kompleksiteit fan prosesoptimalisaasje:It berikken fan optimale prosesparameters foar thermoplastysk ynjeksjefoarm kin kompleks en tiidslinend wêze. Fabrikanten moatte temperatuer, druk, koelsnelheden en fytstiden soarchfâldich kontrolearje en optimalisearje om konsekwinte dielkwaliteit te garandearjen en defekten te minimalisearjen.
Soarten termoplastyk brûkt yn ynjeksjefoarmjen
Dit binne mar in pear foarbylden fan 'e thermoplasten dy't gewoanlik brûkt wurde yn spuitfoarmjen. Elk materiaal hat unike eigenskippen, wêrtroch it geskikt is foar spesifike tapassingen basearre op sterkte, fleksibiliteit, gemyske ferset, transparânsje en kosten. Fabrikanten moatte dizze eigenskippen en easken beskôgje by it selektearjen fan de passende thermoplastyk foar har ynjeksjefoarmprojekten.
- Polypropyleen (PP):Polypropyleen is in alsidige thermoplastyk dy't faaks brûkt wurdt yn ynjeksjefoarmjen. It biedt poerbêste gemyske ferset, lege tichtheid, en goede ynfloedsterkte. PP (polypropyleen) hat wiidferspraat tapassingen yn ferpakking, auto-ûnderdielen, húshâldlike apparaten en medyske apparaten.
- Polyetyleen (PE):Polyetyleen is in oare wiidferspraat brûkte thermoplastyk yn ynjeksjefoarmjen. It is beskikber yn ferskate foarmen, lykas polyetyleen mei hege tichtheid (HDPE) en polyetyleen mei lege tichtheid (LDPE). PE biedt goede gemyske ferset, taaiens en fleksibiliteit, wêrtroch it geskikt is foar flessen, konteners en buizen.
- Polystyrene (PS):Polystyrene is in alsidich thermoplastysk bekend om syn dúdlikens, rigiditeit en betelberens. It fynt gewoan gebrûk yn ferpakking, konsuminteguod en wegwerpprodukten. PS (polystyrene) soarget foar flugge ferwurking en jout goede dimensional stabiliteit, mar it kin wêze bros en gefoelich foar miljeu stress cracking.
- Acrylonitril Butadien Styrene (ABS): ABS is in populêr thermoplastysk bekend om syn treflike ynfloedresistinsje en duorsumens. It kombinearret de eigenskippen fan acrylonitrile, butadiene, en styreen om in alsidich materiaal te meitsjen dat geskikt is foar auto-ûnderdielen, elektroanyske behuizingen en boartersguod.
- Polyvinylchloride (PVC): PVC is in soad brûkt thermoplastic bekend om syn treflike gemyske ferset, duorsumens, en lege kosten. It kin stiif of fleksibel wêze ôfhinklik fan 'e formulearring en tafoegings dy't brûkt wurde. PVC (polyvinylchloride) fynt mienskiplik gebrûk yn bou, elektryske isolaasje, sûnenssoarchprodukten en ferpakking.
- Polykarbonat (PC): Polycarbonate is in transparant thermoplastysk mei bûtengewoane ynfloed en hege waarmtebestriding. It fynt gewoan gebrûk yn applikaasjes dy't optyske dúdlikens fereaskje, lykas auto-ûnderdielen, feiligenshelmen en elektroanyske byldskermen.
- Nylon (polyamide):Nylon is in sterk en duorsum thermoplastysk bekend om syn treflike meganyske eigenskippen en gemyske ferset. It fynt gewoan gebrûk yn applikaasjes dy't hege sterkte freegje, lykas auto-ûnderdielen, yndustriële komponinten en konsuminteguod.
- Polyetyleentereftalaat (PET):PET is in populêr thermoplastysk foar it produsearjen fan flessen, konteners en ferpakkingsmaterialen. It biedt goede dúdlikens, gemyske ferset, en barriêre-eigenskippen, wêrtroch it geskikt is foar iten- en drinkapplikaasjes.
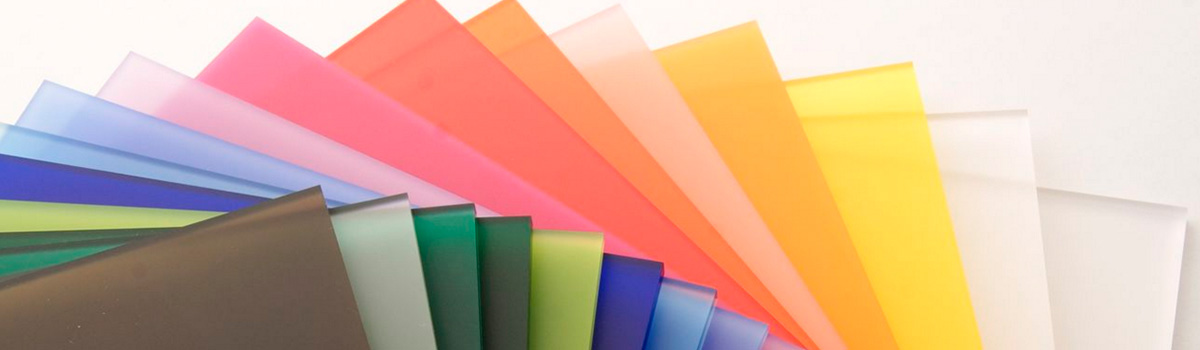
Eigenskippen fan termoplastyk brûkt yn ynjeksjefoarmjen
Dizze eigenskippen fan thermoplasten spylje in krúsjale rol by it bepalen fan har gaadlikens foar spesifike spuitefoarmapplikaasjes. Fabrikanten moatte dizze eigenskippen soarchfâldich beskôgje en de passende thermoplastyk selektearje op basis fan 'e winske prestaasjes, miljeubetingsten en kosteneasken.
- Meganyske eigenskippen:Thermoplastyk brûkt yn ynjeksjefoarmjen kin ferskate meganyske eigenskippen eksposearje, ynklusyf treksterkte, slachbestriding en bûgingssterkte. Dizze eigenskippen bepale it fermogen fan it materiaal om tapaste krêften te wjerstean en syn totale duorsumens yn ferskate tapassingen.
- Gemyske wjerstân:In protte thermoplastyk brûkt yn ynjeksjefoarmjen hawwe opmerklike ferset tsjin gemikaliën, solvents en oaljes. Dit pân is krúsjaal foar tapassingen dy't bleatstelling oan drege omjouwings as korrosive stoffen befetsje.
- Thermyske stabiliteit:De termyske stabiliteit fan thermoplasten ferwiist nei har fermogen om ferhege temperatueren te wjerstean sûnder signifikante degradaasje. Guon thermoplasten hawwe poerbêste waarmtebestriding, wêrtroch se har meganyske eigenskippen sels by hege temperatueren behâlde kinne.
- Elektryske eigenskippen:Thermoplastyk dy't brûkt wurdt yn ynjeksjefoarmjen kin spesifike elektryske eigenskippen hawwe, ynklusyf elektryske isolaasje, konduktiviteit of dielektryske sterkte. Dizze eigenskippen binne essensjeel foar tapassingen yn elektryske en elektroanyske yndustry, wêr't materialen betroubere elektryske prestaasjes moatte leverje.
- Transparânsje en dúdlikens:Bepaalde thermoplasten, lykas polycarbonate en PET, biede poerbêste transparânsje en dúdlikens, wêrtroch se geskikt binne foar tapassingen dy't optyske eigenskippen nedich binne. Fabrikanten brûke dizze materialen gewoanlik yn produkten lykas transparante finsters, linzen en byldskermen.
- Fleksibiliteit en hurdens: Fleksibiliteit en hurdens binne essensjele eigenskippen fan thermoplastyk brûkt yn tapassingen dy't ynfloedresistinsje en duorsumens fereaskje. Guon thermoplasten, lykas ABS en nylon, biede poerbêste taaiens, wêrtroch't se werhelle effekten kinne wjerstean sûnder te brekken.
- Dimensionale stabiliteit:Dimensionale stabiliteit ferwiist nei it fermogen fan in thermoplastyk om syn foarm en grutte te behâlden ûnder wikseljende omstannichheden, ynklusyf temperatuerferoaringen. Materialen mei goede dimensionale stabiliteit soargje foar konsekwint diel ôfmjittings, minimalisearje it risiko fan warping of ferfoarming.
- Gemyske kompatibiliteit:De gemyske kompatibiliteit fan thermoplasten ferwiist nei har fermogen om degradaasje of ynteraksje te wjerstean mei ferskate gemikaliën, ynklusyf soeren, basen en solvents. Om optimale prestaasjes te garandearjen, is it essensjeel om in thermoplastyk te selektearjen dy't de spesifike gemyske omjouwing kin tsjinkomme dy't it sil tsjinkomme yn 'e bedoelde tapassing.
- Density: Thermoplastyk hat ferskate dikten, dy't ynfloed kinne op har gewicht en algemiene dieleigenskippen. Materialen mei lege tichtheid, lykas polyetyleen, biede lichtgewicht oplossingen, wylst materialen mei hege tichtheid, lykas polypropyleen, ekstra sterkte en rigiditeit leverje.
Ynjeksjefoarmproses: stap foar stap
It ynjeksjefoarmproses folget dizze stappen, wêrtroch de effisjinte en krekte produksje fan heechweardige thermoplastyske dielen mooglik is. Elke stap fereasket soarchfâldige kontrôle en tafersjoch om konsekwinte dieldiminsjes, materiaaleigenskippen en algemiene kwaliteit te garandearjen.
- Mouldûntwerp en fabryk: De earste stap yn it ynjeksjefoarmproses is it ûntwerp en fabryk fan 'e skimmel. Fabrikanten moatte in krekte en detaillearre foarm ûntwerp meitsje om de winske dielspesifikaasjes te berikken. Fabrikanten meitsje dan de skimmel mei ferskate techniken, lykas CNC of elektryske ûntslachmasjine (EDM).
- Materiaal tarieding: De folgjende stap is tarieding as de skimmel klear is. Thermoplastyske pellets of korrels wurde selektearre op basis fan 'e winske materiaal eigenskippen en smelt yn in hopper. Operators dan feed it materiaal yn 'e barrel fan' e ynjeksje moulding masine, dêr't it ûndergiet melting en homogenization.
- Ynjeksje:Tidens de ynjeksje faze, operators inject de smelte thermoplastic yn de mal holte ûnder hege druk. De ynjeksje-ienheid fan 'e masine triuwt it gesmolten materiaal troch in mûlestik en yn' e mal. It materiaal follet de skimmelholte, nimt de foarm fan it winske diel.
- Koeling en solidifikaasje:Nei it ynfoljen fan de skimmel litte operators it smelte plestik koelje en fêstigje. Koeling is krúsjaal foar it berikken fan dimensionale stabiliteit en goede dielfoarming. Operators kinne it koelproses kontrolearje troch koelmiddel te sirkulearjen troch kanalen yn 'e skimmel of troch koelplaten te brûken.
- Mold iepening en útwerping:Operators iepenje de skimmel en smyt it diel út 'e skimmelholte as it plestik fersteurt. It útwerpsysteem yn 'e masine brûkt pinnen, ejectorplaten, as luchtblazen om de regio út' e skimmel te ferwiderjen. De skimmel is dan klear foar de folgjende ynjeksjesyklus.
- Post-ferwurking: Nei it útwerpen kin it diel post-ferwurkingsoperaasjes ûndergean, lykas trimmen, ôfbramen of oerflakfinish. Dizze stappen helpe om oerstallich materiaal te ferwiderjen, rûge rânen glêd te meitsjen en it definitive uterlik fan it diel te ferbetterjen.
- Kwaliteitskontrôle: De lêste stap omfettet it ynspektearjen fan de ynjeksjede dielen op kwaliteit en garandearje dat se foldogge oan de spesifisearre easken. Ferskate techniken foar kwaliteitskontrôle, ynklusyf dimensjemjitting, fisuele ynspeksje, en funksjonele testen, kinne wurde brûkt om de kwaliteit en yntegriteit fan it diel te ferifiearjen.
- Recycling en materiaal wergebrûk:Elk oerskot of skrapmateriaal dat wurdt generearre tidens it ynjeksjefoarmjen kin wurde recycled en opnij brûkt. It ferminderjen fan it gebrûk fan nij thermoplastysk materiaal helpt om ôffal te minimalisearjen en duorsumens te ferbetterjen.
Apparatuer brûkt yn Molders
Dizze apparatuerkomponinten fasilitearje it ynjeksjefoarmproses, fan it smelten en ynjeksje fan it thermoplastyske materiaal oant it foarmjen, koeljen en útwerpen fan it lêste diel. Goede eksploitaasje en ûnderhâld fan dizze apparatuerkomponinten binne krúsjaal foar it realisearjen fan effisjinte, heechweardige produksje fan ynjeksjefoarmjen.
- Ynjeksjefoarmmasine:De primêre apparatuer yn ynjeksjefoarmjen is ferantwurdlik foar it smelten fan it thermoplastyske materiaal, it ynjeksje fan it yn 'e skimmel en it kontrolearjen fan it proses.
- Skimmel: De skimmel, op maat ûntworpen om de winske foarm en funksjes fan it plestik diel te meitsjen, bestiet út twa helten, de holte en de kearn. Operators mount it op 'e clamping ienheid fan' e ynjeksje moulding masine.
- Hopper:Container dy't it thermoplastyske materiaal yn pellet of korrelige foarm hâldt en it yn 'e barrel fan' e ynjeksjefoarmmasjine fiert foar smelten en ynjeksje.
- Barrel en skroef: De barrel, in silindryske keamer, smelt en homogenisearret it thermoplastyske materiaal as de skroef deryn draait om it materiaal te smelten, te mingjen en te standerdisearjen.
- Ferwaarming- en koelsystemen:Ynjeksjefoarmmasines hawwe ferwaarmingseleminten, lykas elektryske kachels of kachels dy't hjitte oalje brûke, om de temperatuer fan 'e barrel te ferheegjen, en koelsystemen, lykas wetter- of oaljesirkulaasje, om de skimmel te koelen en it plestik diel te solidisearjen.
- Ejector System:Ferwideret it getten diel út 'e skimmelholte nei fersteviging, typysk mei help fan ejectorpinnen, platen, of luchtblazen tidens de skimmeliepening.
- Kontrôle systeem:Monitors en kontrolearret ferskate parameters fan it ynjeksjefoarmproses, wêrtroch operators parameters kinne ynstelle en oanpasse lykas ynjeksjesnelheid, temperatuer, druk en koeltiid.
Molders Machines: Soarten en skaaimerken
Elk type ynjeksjefoarmmasjine hat syn skaaimerken en foardielen, wêrtroch fabrikanten it meast geskikte apparaat kinne kieze foar har spesifike produksjeeasken.
- Hydraulyske ynjeksjefoarmmasines: Dizze masines brûke hydraulyske systemen om de nedige druk te generearjen om smelte plestik yn 'e mal te ynjeksje. Se binne bekend om har hege klemkrêft, krekte kontrôle en veelzijdigheid by it behanneljen fan ferskate thermoplastyk. Hydraulyske masines binne geskikt foar grutskalige produksje en kinne komplekse mallen bepale.
- Elektryske ynjeksjefoarmmasines:Elektryske masines brûke elektryske servomotoren foar de wurking fan 'e masine, ynklusyf de ynjeksje-, klem- en ejectorsystemen. Se biede krekte kontrôle, enerzjy-effisjinsje, en rappere reaksjetiden dan hydraulyske masines. Elektryske masines binne ideaal foar presys moulding applikaasjes dy't fereaskje hege repeatability en krektens.
- Hybride ynjeksjefoarmmasines:Hybride masines kombinearje de foardielen fan sawol hydraulyske as elektryske apparaten. Se brûke in kombinaasje fan hydraulyske en elektryske servosystemen om hege presyzje, enerzjy-effisjinsje en kosten-effektiviteit te berikken. Hybride masines binne geskikt foar in breed skala oan tapassingen, en jouwe in lykwicht tusken prestaasjes en operasjonele kosten.
- Twa-platen ynjeksjefoarmmasines: Twa-platen masines hawwe in unyk ûntwerp mei twa aparte platen foar clamping de mal. Dit ûntwerp jout ferbettere stabiliteit, ferbettere mal syngronisaasje en makket it mooglik foar gruttere mal maten en hegere clamping krêften. Twa-platen masines binne geskikt foar grutte en komplekse dielen dy't nedich presys moulding.
- Mearkomponinten ynjeksjefoarmmasines:Fabrikanten ûntwerpe dizze masines om dielen te produsearjen mei meardere materialen as kleuren yn ien foarmsyklus. Se hawwe ferskate ynjeksje-ienheden en mallen, wêrtroch simultane ynjeksje fan ferskate materialen mooglik is. Masines mei meardere komponinten biede fleksibiliteit en effisjinsje by it produsearjen fan komplekse dielen mei wikseljende skaaimerken.
- Mikro-ynjeksjefoarmmasines:Spesifyk ûntworpen foar it produsearjen fan lytse en krekte dielen, mikro-ynjeksjefoarmmasines biede ongelooflijk hege presyzje en krektens. Se kinne yngewikkelde details produsearje mei strakke tolerânsjes en minimale materiaalôffal. Elektroanika, medyske apparaten, en mikro-optyk brûke gewoanlik mikro-ynjeksjefoarmmasines.
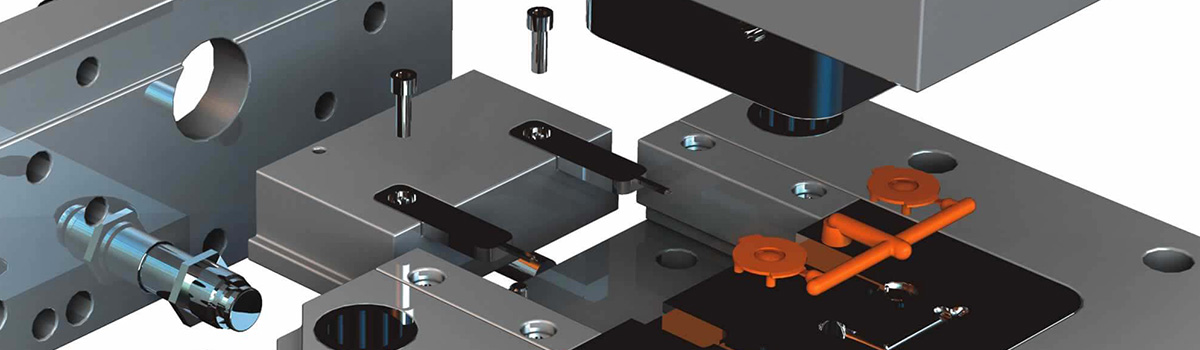
Mould Design ôfwagings foar Molders
Soarch oerwegingen foar foarmûntwerp binne essinsjeel foar suksesfolle produksje fan spuitgietfoarm.
- Part ûntwerp:It skimmelûntwerp moat foldwaan oan de spesifike easken fan it diel, ynklusyf de foarm, dimensjes en funksjonele funksjes. Fabrikanten moatte goed beskôgje konsept hoeken, muorre dikte, undercuts, en alle nedige eleminten te garandearjen gemak fan útstjit en diel kwaliteit.
- Mold Materiaal: De seleksje fan skimmelmateriaal is krúsjaal foar it berikken fan duorsumens, dimensionale stabiliteit en waarmtebestriding. Algemiene skimmelmaterialen omfetsje stiellegeringen, aluminiumlegeringen, en arkstiel. De kar fan materiaal hinget ôf fan faktoaren lykas produksje folume, diel kompleksiteit, en ferwachte tool libben.
- Koelsysteem:Effisjinte koeling is essensjeel foar juste ferharding fan dielen en minimalisearje de syklustiid. It skimmelûntwerp moat koelkanalen of strategysk pleatste ynserts omfetsje om unifoarme skimmelkoeling te garandearjen. Goede koeling ferleget it risiko fan warpage, krimp, en part defekten.
- Fentilaasje:Adekwate ventilaasje is nedich om it ûntkommen fan lucht en gassen mooglik te meitsjen tidens it ynjeksjeproses. Net genôch ventilaasje kin liede ta gasfallen, brânmerken, of ûnfolsleine dielfolling. Fabrikanten kinne ventilaasje berikke troch ventilaasjegroeven, pinnen of oare meganismen yn te nimmen yn it malûntwerp.
- Ejection System:It skimmelûntwerp moat in effektyf útwerpsysteem befetsje om it getten diel út 'e skimmelholte feilich en effisjint te ferwiderjen. It útwerpsysteem kin bestean út ejectorpinnen, mouwen of oare meganismen, strategysk pleatst om ynterferinsje mei de funksje of krityske funksjes te foarkommen.
- Gate Design:De poarte is wêr't gesmolten plestik yn 'e skimmelholte komt. It poarteûntwerp moat soargje foar goede dielfolling, streamlinen minimalisearje en foartiid befriezen fan materiaal foarkomme. Standert poarte-ûntwerpen omfetsje rânepoarten, tunnelpoarten, en hot runner-systemen, ôfhinklik fan de easken fan it diel en materiaaleigenskippen.
- Parting Line:It skimmelûntwerp moat in gaadlike ôfskiedingsline definiearje, dat is de line wêr't de twa helten fan 'e skimmel byinoar komme. De juste pleatsing fan skiedingsline soarget foar minimale flits- en skiedingsline-mismatch en fasilitearret effisjinte skimmelmontage.
- Mold ûnderhâld en tsjinstberens: Fabrikanten moatte beskôgje it gemak fan ûnderhâld, reparaasje, en skimmelservice. Mouldkomponinten moatte maklik tagonklik wêze foar skjinmeitsjen, ynspeksje en ferfanging. It opnimmen fan funksjes lykas ynserts foar snelle feroaring as modulêre foarmûntwerpen kinne de tsjinstberens fan skimmel ferbetterje.
Mouldmaterialen brûkt yn ynjeksjefoarmjen
Gearwurking mei skimmelmateriaal spesjalisten en beskôgje de spesifike behoeften fan 'e moulding applikaasje kin helpe bepale de meast geskikte materiaal foar it berikken fan optimale skimmel prestaasjes en diel kwaliteit.
- Steel Alloys: Stiellegeringen, lykas arkstiel (bgl. P20, H13) en roestfrij stielen, wurde faak brûkt foar spuitgietfoarmen fanwegen har poerbêste duorsumens, waarmtebestriding en slijtresistinsje. Dizze materialen kinne de hege temperatueren en drukken yn it ynjeksjefoarmproses wjerstean en biede goede diminsjonele stabiliteit foar it produsearjen fan heechweardige dielen.
- Aluminiumlegeringen:Aluminiumlegeringen, lykas 7075 en 6061, binne lichtgewicht en biede goede termyske konduktiviteit, wêrtroch't se geskikt binne foar mallen dy't effisjinte koeling nedich binne. Fabrikanten brûke faak aluminium mallen foar prototyping, produksje mei leech folume, as tapassingen wêr't gewichtsreduksje kritysk is. Aluminiumfoarmen kinne lykwols legere duorsumens hawwe yn ferliking mei stiellegeringen.
- Koper Alloys:Koper alloys, lykas beryllium koper, fertoane hege termyske conductivity en goede machinability. Se fine gebrûk yn mallen dy't poerbêste waarmteferfier nedich binne foar effektive koeling. Koperlegeringen kinne helpe om syklustiden te ferleegjen troch waarmte fluch te dissipearjen fan it getten diel, wat resulteart yn flugger solidifikaasje.
- Tool Steels:Tool stielen, ynklusyf H13, S7, en D2, binne ûntwurpen foar hege-optreden tooling applikaasjes. Dizze stielen biede in kombinaasje fan hege sterkte, hurdens en wearbestindich. Tool stielen suit mallen mei hege produksje folume, abrasive materialen, of easket moulding betingsten.
- Nikkellegeringen:Nikkellegeringen, lykas Inconel en Hastelloy, binne bekend om har útsûnderlike korrosjebestriding, hege temperatuersterkte en thermyske stabiliteit. Fabrikanten brûke dizze alloys yn mallen dy't omgean mei corrosive materialen of fereaskje ferset tsjin ekstreme temperatueren en agressive moulding omjouwings.
- Composite materialen:Gearstalde materialen, lykas fersterke plestik of kompositen mei metalen ynserts, wurde soms brûkt foar spesifike mouldapplikaasjes. Dizze materialen biede in lykwicht fan eigenskippen, lykas hege sterkte, thermyske stabiliteit en fermindere gewicht. Gearstalde mallen kinne kosten-effektive alternativen wêze foar spesifike produksjeeasken.
Soarten ynjeksjefoarmen
Ynjeksjefoarmjen is in alsidige en in soad brûkte produksjeproses foar plestik dielen.
- Twa-plaat mal:De twa-plaat skimmel is it meast foarkommende type ynjeksje schimmel. It bestiet út twa platen, de holte plaat, en de kearn plaat, dy't skieden te tastean it útwerpen fan it getten diel. De holte plaat befettet de holte kant fan 'e mal, wylst de kearn plaat herberget de kearn kant. Fabrikanten brûke twa-plaat mallen foar it produsearjen fan in breed skala oan dielen fanwege harren relatyf ienfâldige ûntwerp.
- Trije plaat mal:De trije-plaat mal is in avansearre ferzje fan de twa-plate mal. It omfettet in ekstra plaat, de runner, of de sprueplaat. De runner plaat makket in apart kanaal foar de sprue, runners, en poarten, wêrtroch makliker fuortheljen fan it getten diel. Fabrikanten brûke faaks trije-plaat mallen foar details mei komplekse gating systemen of as it foarkommen fan in poarte vestige op it stik is winsklik.
- Hot Runner Mould:It runner- en poartesysteem wurdt ferwaarme yn hjitte runner-mallen, wêrtroch't de needsaak foar solidifikaasje en opnij smelten fan it materiaal tidens elke syklus. It hot runner systeem bestiet út ferwaarme manifolds en sproeiers dy't behâlde de smelte steat fan it plestik. Hot runner mallen biede foardielen lykas fermindere syklustiid, legere materiaal ôffal, en ferbettere diel kwaliteit troch minimalisearje poarte resten.
- Cold Runner Mold: Kâlde runner mallen hawwe in tradisjoneel runner en poarte systeem dêr't de smelte plestik streamt troch kâlde runners dy't solidify mei elke syklus. Eksploitanten ferwiderje dêrnei de ferhurde rinners, wat resulteart yn materiaalôffal. Fabrikanten brûke typysk komplekse runner-mallen foar produksje fan legere folume as as materiaalkosten minder kritysk binne fanwegen har mear rjochtlinige ûntwerp.
- Mold ynfoegje:Ynfoegje mallen omfetsje metalen of plestik ynserts yn 'e malholte by it ynjeksjefoarmjen. Inserts kinne foarôf pleatst wurde yn 'e mal of ynfoege troch automatisearre prosessen. Dizze skimmel makket it mooglik om ekstra komponinten te yntegrearjen of eleminten te fersterkjen yn it getten diel, it ferbetterjen fan syn funksjonaliteit of sterkte.
- Overmold: Overmolding giet it om it foarmjen fan ien materiaal oer in oar, typysk it ferbinen fan in stive plestik substraat mei in sêfter elastomeer of thermoplastysk. Dit proses makket it mooglik om dielen te meitsjen mei meardere materialen as tekstueren yn ien mal, en biedt ferbettere grip, cushioning of estetyske funksjes.
Faktors dy't ynfloed hawwe op kosten foar spuitgieten
Troch dizze faktoaren te beskôgjen kinne fabrikanten helpe om de kosten fan ynjeksjefoarmjen te skatten en te optimalisearjen, in lykwicht te garandearjen tusken kwaliteit, effisjinsje en kosten-effektiviteit foar har spesifike produksjeeasken.
- Diel kompleksiteit:De kompleksiteit fan it dielûntwerp spilet in wichtige rol by it bepalen fan de kosten fan ynjeksjefoarmjen. Yngewikkelde geometry's, undercuts, tinne muorren, as komplekse funksjes kinne ekstra ark, spesjalisearre mallen, as langere syklusen fereaskje, wat de totale produksjekosten ferheegje.
- Materiaal seleksje:De kar fan thermoplastysk materiaal beynfloedet de kosten foar ynjeksjefoarmjen. Ferskillende materialen hawwe wikseljende prizen per kilogram, en faktoaren lykas materiaal beskikberens, eigenskippen, en ferwurking easken kinne beynfloedzje de totale materiaal kosten.
- Tooling en malûntwerp: De kosten foar inisjele tooling en malûntwerp binne signifikant yn kosten foar ynjeksjefoarmjen. Faktoaren lykas skimmelkompleksiteit, oantal holtes, skimmelgrutte en skimmelmateriaal drage by oan de útjeften foar ark en skimmelfabrikaazje. Mear komplekse mallen as mallen dy't avansearre funksjes fereaskje kinne de foarôf ynvestearring ferheegje.
- Produksje folume: It produksjevolumint hat direkt ynfloed op de kosten per diel yn ynjeksjefoarmjen. Hegere boeken resultearje faak yn skaalfoardielen, wêrtroch't de kosten per diel ferminderje. Oarsom kinne produksjerinnen mei leech folume hegere kosten krije fanwege opset, ark en materiaalôffal.
- Fytstiid: De syklustiid, dy't de fazen fan koeling en útstjit omfettet, hat ynfloed op de produksjekapasiteit en de totale kosten. Langere syklustiden resultearje yn fermindere produksjeútfier en mooglik hegere prizen. Optimalisearjen fan it skimmelûntwerp, koelsysteem en prosesparameters kinne syklustiden minimalisearje en effisjinsje ferbetterje.
- Kwaliteitseasken:Stringe kwaliteitseasken as spesifike sertifikaasjes kinne ynfloed hawwe op de kosten foar spuitgieten. It foldwaan oan krekte tolerânsjes, easken foar oerflakfinish, as oanfoljende testen kinne oare boarnen, prosessen of ynspeksjes fereaskje, wat taheakke oan 'e totale kosten.
- Sekundêre operaasjes:As de getten dielen post-ferwurkingsoperaasjes fereaskje, lykas montage, skilderjen, of ekstra finishstappen, kinne dizze operaasjes tafoegje oan 'e totale kosten foar spuitgieten.
- Oanbieder en lokaasje:De kar fan leveransier foar ynjeksjefoarmjen en har lokaasje kin de kosten beynfloedzje. Arbeidskosten, overheadkosten, logistyk en ferfierkosten fariearje op basis fan 'e lokaasje fan' e leveransier, en beynfloedzje de totale produksjekosten.
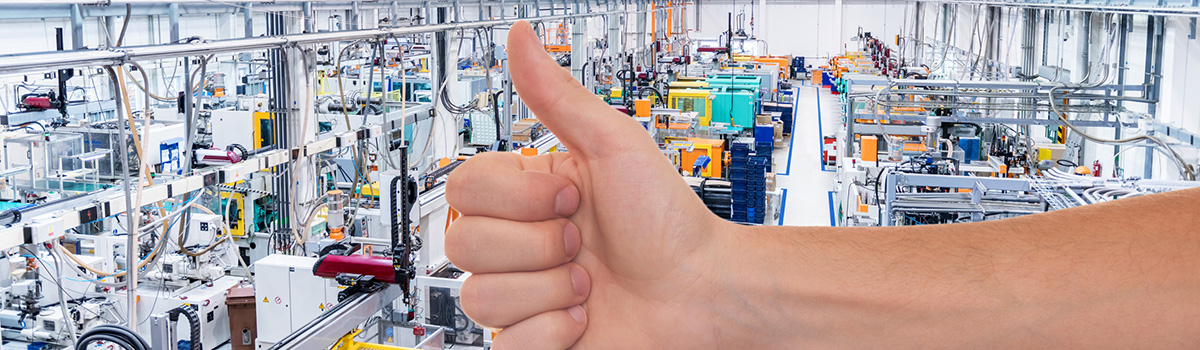
Kwaliteitskontrôle yn Molders
It ymplementearjen fan robúste kwaliteitskontrôlemaatregels yn it heule spuitproses helpt te identifisearjen en oan te pakken potinsjele defekten, ôfwikingen, as inkonsistinsjes, en garandearje de produksje fan heechweardige dielen dy't foldogge oan klantspesifikaasjes en easken.
- Prosesmonitoring: Trochrinnende tafersjoch op wichtige prosesparameters, lykas smelttemperatuer, ynjeksjedruk, koeltiid, en syklustiid, soarget foar konsistinsje en werhelling yn dielproduksje. Real-time tafersjoch en automatisearre systemen kinne detect fariaasjes of ôfwikingen fan ynstelde parameters, wêrtroch't tiidige oanpassings en behâld fan proses stabiliteit.
- Ynspeksje en mjitting:Regelmjittige beoardieling en mjitting fan getten dielen binne essensjeel om dimensjekrektens, dielkwaliteit en neilibjen fan spesifikaasjes te kontrolearjen. Us tsjinsten omfetsje in ferskaat oan metoaden foar kwaliteitskontrôle, lykas dimensjes mjitten, oerflakkwaliteit analysearje, fisuele ynspeksjes útfiere en funksjonele tests útfiere. Ferskate ynspeksjetechniken, lykas koördinearjende mjitmasines (CMM) en optyske en fisuele ynspeksjesystemen, wurde brûkt foar krekte evaluaasje.
- Statistical Process Control (SPC): SPC omfettet it sammeljen en analysearjen fan prosesgegevens om de kwaliteit fan ynjeksje te kontrolearjen en te kontrolearjen. Statistyske metoaden, lykas kontrôlediagrammen en analyse fan prosesfermogen, helpe trends te identifisearjen, prosesfariaasjes te detektearjen en te soargjen dat it proses binnen definieare kontrôlegrinzen bliuwt. SPC makket de proaktive identifikaasje fan problemen mooglik en fasilitearret prosesoptimalisaasje.
- Materiaal testen: It testen fan grûnstoffen, lykas thermoplastyk, tafoegings en kleurstoffen, garandearret har kwaliteit en geskiktheid foar ynjeksjefoarmjen. Materiaaltesten kinne analyse fan meltflow-yndeks (MFI) omfetsje, meganyske eigenskippen, thermyske skaaimerken en materiaalkomposysje. It ferifiearjen fan de materiaalkwaliteit helpt defekten en inkonsistinsjes yn 'e foarme dielen te foarkommen.
- Tooling ûnderhâld en ynspeksje:Goed ûnderhâld en reguliere ynspeksje fan 'e ynjeksjefoarmen binne krúsjaal foar it garandearjen fan kwaliteit yn it ynjeksjefoarmjen. Regelmjittich skjinmeitsjen, smeren en beoardieling fan skimmelkomponinten helpe slijtage, skea of degradaasje te foarkommen dy't de kwaliteit fan dielen kinne beynfloedzje. Tidige reparaasje of ferfanging fan ôfsliten of beskeadige skimmelkomponinten is essinsjeel om konsekwinte foarmprestaasjes te behâlden.
- Dokumintaasje en traceability:It behâld fan wiidweidige dokumintaasje en traceability records is essinsjeel foar kwaliteit kontrôle yn spuitgieten. It is essinsjeel om prosesparameters, ynspeksjeresultaten, materiaalynformaasje, en alle feroaringen as oanpassingen makke tidens produksje op te nimmen. Goede dokumintaasje makket traceerberens fan dielen mooglik, fasilitearret analyse fan woarteloarsaken en soarget foar konsistinsje yn kwaliteit.
- Training en feardigensûntwikkeling: It leverjen fan adekwate opliedings- en feardigensûntwikkelingsprogramma's foar operators, technici en personiel foar kwaliteitskontrôle ferbettert har begryp fan ynjeksjefoarmprosessen, kwaliteitseasken en ynspeksjetechniken. Goed oplaat personiel kin defekten detektearje, problemen oplosse en korrektive maatregels effektyf útfiere, en soargje foar produksje fan hege kwaliteit.
Algemiene ynjeksjefoarmdefekten en hoe't se se kinne foarkomme
Reguliere ynspeksje, tafersjoch en analyse fan ynjeksjefoarmprosessen en goed ûnderhâld en oanpassing fan apparatuer en mallen kinne helpe om dizze mienskiplike defekten te identifisearjen en oan te pakken.
- Sink Marks:Sinkmarken binne depresjes of ynspringingen op it oerflak fan it getten diel dy't feroarsake binne troch unjildich koeljen of krimp. Men moat beskôgje goede poarte lokaasje en ûntwerp, optimaal cooling systeem design, en unifoarm muorre dikte distribúsje te kommen dat sink marks. It fergrutsjen fan de ynjeksjedruk of it oanpassen fan de koeltiid kin ek helpe om sinkmarken te minimalisearjen.
- Warside:Warpage ferwiist nei de ferfoarming of bûgen fan in getten diel nei útstjit fanwege unjildich koeling of oerbleaune spanningen. It behâld fan unifoarme muorredikte, it brûken fan juste koelkanalen, en it garandearjen fan lykwichtige ynfoljen en ynpakken fan 'e skimmel binne krúsjaal om warpage te foarkommen. Optimalisearjen fan skimmeltemperatuer, mei help fan passende ûntwerphoeken, en kontrolearjen fan materiaaltemperatuer en ynjeksjesnelheid kinne helpe om warpage te minimalisearjen.
- Flits:Flash optreedt as oerstallige materiaal streamt yn de mal parting line, resultearret yn tinne, net winske projeksjes of ekstra materiaal op it lêste diel. Men kin effektyf foarkomme flits troch it garandearjen fan goede mal design, ynklusyf it tapassen fan adekwate clamping krêft, sekuere alignment, en mei help fan passende venting techniken. It optimalisearjen fan prosesparameters lykas ynjeksjedruk, temperatuer en syklustiid ferminderet flits.
- Koarte shot:In flugge skot bart as de ynjeksje materiaal net folje de mal holte, resultearret yn in ûnfolsleine diel. Goede materiaal seleksje, soargje foar adekwate melt temperatuer en viscosity, en it behâld fan passende ynjeksje druk en tiid binne essinsjeel om foar te kommen koarte foto's. Derneist kin it ferifiearjen fan it skimmelûntwerp foar genôch rinner- en poartegrutte en juste ventilaasje helpe om rappe shots te foarkommen.
- Weld Lines:Weld rigels foarkomme as twa of mear smelte materiaal flow fronten moetsje en solidify, resultearret yn in sichtbere line of mark op it diel oerflak. Goede poarte- en runner-ûntwerp, optimale smelttemperatuer, ynjeksjesnelheid, en oanpassen fan materiaalstream en dielmjitting kinne weldlinen minimalisearje. Mold flow analyse en poarte pleatsing optimalisaasje kin ek helpe te foarkommen of mitigate weld rigels.
- Burn Marks:Burn marks binne discolorations of swarte plakken op it oerflak fan it getten diel feroarsake troch oermjittige waarmte of oververhitting fan it materiaal. It foarkommen fan ekstreme smelttemperatuer, it brûken fan passende koelkanalen en it optimalisearjen fan de syklustiid kin helpe om brânmerken te foarkommen. Adekwate ventilaasje, juste poarteûntwerp, en it kontrolearjen fan skimmeltemperatuer drage ek by oan it minimalisearjen fan brânmerken.
Post-Moulding Operations: Finishing en gearkomste
Nei it ynjeksjefoarm kinne in protte getten dielen ekstra ôfwurkings- en gearstallingsoperaasjes fereaskje om it winske einprodukt te berikken. Dizze post-molding operaasjes kinne omfetsje:
- Trimmen:Fuortsmite alle oerstallige materiaal of flits om de getten diel mei help trimmen of cutting ark.
- Surface Treatment:Ferbetterjen fan it uterlik of funksjonaliteit fan it diel oerflak mei help fan ferskate techniken lykas skilderjen, coating, of texturing.
- Gearkomste:Joining meardere getten dielen of it tafoegjen fan komponinten lykas Fasteners, Inserts, of labels te foltôgjen it definitive produkt.
- Testing:Ferifikaasje fan kwaliteit en funksjonaliteit fan diel troch ferskate testmetoaden lykas dimensjeanalyse, testen fan materiaaleigenskippen, as prestaasjestesten.
- Ferpakking en ferstjoering:Goede ferpakking en etikettering fan it ôfmakke produkt foar ferstjoering nei klanten as ein-brûkers.
De seleksje fan post-molding operaasjes hinget ôf fan de spesifike tapassing en winske úteinlike produkt skaaimerken. Nauwe gearwurking tusken saakkundigen foar ynjeksjefoarmjen, spesjalisten foar finish en montage, en de klant is krúsjaal foar it berikken fan de winske absolute produktkwaliteit en funksjonaliteit. Goede planning en yntegrearjen fan post-molding operaasjes yn it produksjeproses kin helpe te garandearjen effisjinte produksje en yntiidske levering fan produkten fan hege kwaliteit.
Molders vs Oare Plastic Manufacturing prosessen
Elk plestik produksjeproses hat foardielen en beheiningen, wêrtroch se geskikt binne foar ferskate tapassingen.
- Injection Molding: Ynjeksjefoarmjen is in heul alsidige en in soad brûkte produksjeproses foar it produsearjen fan plestik dielen. It biedt foardielen lykas hege produksje-effisjinsje, krekte dielreplikaasje, en de mooglikheid om komplekse geometryn te meitsjen. Molders is geskikt foar produksjerinnen mei hege folume en makket it mooglik om in breed oanbod fan thermoplastyske materialen te brûken. It biedt poerbêste diminsjonele krektens en oerflakfinish, wêrtroch it ideaal is foar ferskate yndustry lykas automotive, konsuminteguod en medyske apparaten.
- Blow Molding: Blaasfoarmjen is in proses dat primêr wurdt brûkt foar it produsearjen fan holle plestik dielen, lykas flessen, konteners en auto-ûnderdielen. It giet om it smelten fan plestik en it opblazen yn in skimmelholte, wêrtroch de winske foarm ûntstiet. Blow moulding is geskikt foar hege folume produksje en kin produsearje grutte, lichtgewicht dielen mei unifoarm muorre dikte. It is lykwols beheind yn termen fan dielkompleksiteit en materiaalseleksje yn ferliking mei ynjeksjefoarmjen.
- Thermoformaasje:Thermoforming is in proses dat wurdt brûkt om plestik dielen te produsearjen troch in thermoplastysk blêd te ferwaarmjen en it te foarmjen mei mallen of fakuümfoarmjen. It fynt gewoan gebrûk yn ferpakking, wegwerpprodukten, en grutskalige produkten lykas trays en dekken. Thermoforming biedt kosten-effektive produksje foar grutte dielen en soarget foar rappe prototyping. It hat lykwols beheiningen oangeande dielkompleksiteit, materiaalseleksje en diminsjonele krektens yn ferliking mei ynjeksjefoarmjen.
- Extrusion:Extrusion is in kontinu proses foar it produsearjen fan plestik profilen, lekkens, buizen en films. It giet om it smelten fan plestik hars en it twingen troch in die om de winske foarm te meitsjen. Extrusion is geskikt foar it produsearjen fan lange, trochgeande lingten fan plestik produkten mei in konsekwint dwerstrochsneed. Wylst extrusion biedt hege produksje tariven en kosten-effektiviteit, it is beheind yn termen fan komplekse diel geometry en sekuere dimensional kontrôle yn ferliking mei Molders.
- Kompresje moulding:Kompresjefoarmjen giet it om it pleatsen fan in foarôfmjitten hoemannichte thermosetmateriaal yn in ferwaarme skimmelholte en komprimearje it ûnder hege druk oant it genêzen. It fynt gewoan gebrûk by it produsearjen fan dielen mei hege sterkte en dimensjeel stabiliteit, lykas auto-ûnderdielen en elektryske isolaasje. Kompresjefoarmjen biedt goede dielkonsistinsje, hege produksje-effisjinsje, en de mooglikheid om in breed oanbod fan materialen te brûken. It is lykwols beheind yn termen fan dielkompleksiteit en syklustiid yn ferliking mei ynjeksjefoarmjen.
Applikaasjes fan Thermoplastic Injection Moulding
Ferskate yndustry brûke in soad thermoplastyske ynjeksjefoarming fanwegen syn veelzijdigheid, effisjinsje en kosten-effektiviteit. Guon fan 'e tapassingen fan thermoplastysk ynjeksjefoarmjen omfetsje:
- Auto yndustry: De auto-yndustry brûkt in protte thermoplastyske ynjeksjefoarmen om ferskate komponinten te meitsjen, ynklusyf ynterieur- en eksterieurtrimmen, dashboards, doarpanielen, bumpers en elektryske connectors. It proses soarget foar krekte replikaasje fan dielen, komplekse geometryn, en lichtgewicht materialen, ferbetterjen fan brânstof effisjinsje en ûntwerpfleksibiliteit.
- Konsuminte guod:Ynjeksjefoarmjen fynt wiidweidige applikaasjes by it produsearjen fan konsuminteguod lykas húshâldlike apparaten, elektroanyske apparaten, ferpakkingskonteners en boartersguod. It proses makket de massaproduksje mooglik fan duorsume produkten fan hege kwaliteit mei konsekwinte dimensjes en oerflakfinish. It soarget ek foar oanpassingsopsjes en rappe produktiteraasjes.
- Medyske apparaten:Ynjeksjefoarmjen spilet in krúsjale rol yn 'e medyske yndustry foar it produsearjen fan in breed skala oan apparaten, ynklusyf spuiten, sjirurgyske ynstruminten, ymplantbere komponinten, en systemen foar medisynlevering. It proses soarget foar de produksje fan sterile, krekte en biokompatibele dielen dy't foldogge oan de strange regeljouwingseasken fan 'e sûnenssektor.
- Elektroanika en elektryske yndustry:De elektroanika-yndustry brûkt ynjeksjefoarmjen om elektryske connectors, kasten, skeakels en oare komponinten te meitsjen. It proses biedt hege diminsjonele krektens, poerbêste oerflakfinish, en de mooglikheid om funksjes op te nimmen lykas ynfoegje moulding en overmolding, wêrtroch effisjinte produksje fan komplekse elektroanyske assemblies mooglik is.
- Packaging Industry:Ferskate yndustry, ynklusyf iten en drinken, farmaseutyske produkten, en persoanlike fersoarging, brûke gewoanwei ynjeksjefoarmjen foar it produsearjen fan plestik ferpakkingskonteners, doppen, slutingen en flessen. It proses makket it meitsjen fan lichtgewicht, duorsume en estetysk oansprekkende ferpakkingsoplossingen mooglik mei effisjinte produksjesyklusen.
- Aerospace Industry:De loftfeartsektor brûkt ynjeksjefoarmjen foar it produsearjen fan lichtgewicht en hege prestaasjes komponinten lykas luchtkanalen, beugels, ynterieurpanielen en strukturele dielen. It proses makket it mooglik om avansearre materialen en yngewikkelde dielgeometyen te brûken, wat bydraacht oan gewichtsreduksje en ferbettere brânstofeffisjinsje.
Miljeu-ynfloed fan Thermoplastic Injection Moulding
Thermoplastysk ynjeksjefoarmjen is in populêr fabrikaazjeproses fanwegen syn protte foardielen, mar it is ek essinsjeel om de miljeu-ynfloed te beskôgjen. Hjir binne wat punten om te beskôgjen:
- Materiaal effisjinsje:Thermoplastysk ynjeksjefoarmjen befoarderet materiaaleffisjinsje troch ôffal te minimalisearjen. It proses brûkt sekuere kontrôle oer de hoemannichte materiaal yn 'e skimmel ynjeksje, wêrtroch't de needsaak foar oerskot materiaal wurdt fermindere. Fabrikanten kinne ek werslijp- en recyclingtechniken brûke om skrot of ôfwiisde dielen opnij te brûken, wat materiaalôffal fierder ferminderje.
- Enerzjykonsumpsje:Fabrikanten ûntwerpe ynjeksjefoarmmasines om enerzjysunich te wêzen, mei moderne modellen mei avansearre technologyen lykas servomotoren en oandriuwen mei fariabele snelheid. Dizze funksjes optimalisearje enerzjyferbrûk troch it ferminderjen fan enerzjyferbrûk by it foarmjen, wat resulteart yn legere enerzjyeasken en fermindere miljeu-ynfloed.
- Offalbehear:By it minimalisearjen fan materiaalôffal, moatte fabrikanten juste ôffalbehearpraktiken ymplementearje om oerbliuwende materialen, spuiten of runners te behanneljen. Fabrikanten kinne recyclingprogramma's opstelle om plestik ôffal te sammeljen en opnij te brûken dat ûntstiet by spuitgieten, en dêrmei ôffal ferminderje dat nei stoartplakken stjoerd wurdt.
- Emission Reduksje: Thermoplastysk ynjeksjefoarm genereart oer it generaal legere útstjit as oare produksjeprosessen. Fabrikanten kinne emissies ferminderje troch miljeufreonlike materialen te brûken, enerzjysunige apparatuer te ymplementearjen en avansearre útlaat- en filtraasjesystemen te brûken om alle frijlitten emissies op te fangen.
- Duorsume materiaalkeuzes:De seleksje fan thermoplastyske materialen kin de miljeu duorsumens fan spuitgieten signifikant beynfloedzje. Kieze foar biologysk ôfbrekber of bio-basearre plestik, lykas recycled of recyclebere materialen, kin helpe om de algemiene ekologyske foetôfdruk fan it proses te ferminderjen.
Life Cycle Considerations: It beskôgjen fan de heule libbenssyklus fan it getten produkt is essensjeel foar it beoardieljen fan de miljeu-ynfloed. Tidens de fazen fan ûntwerp en materiaalseleksje moatte fabrikanten faktoaren beskôgje lykas de duorsumens fan it diel, de recycleberens, en it potensjeel foar ferwidering of wergebrûk fan it ein fan it libben.
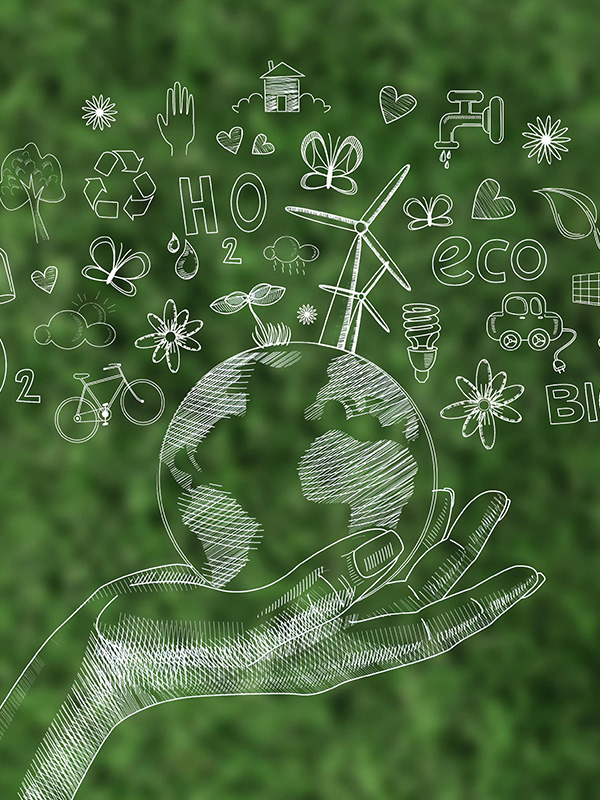
Future of Thermoplastic Injection Molding
De takomst fan thermoplastysk ynjeksjefoarmjen sjocht der kânsryk út, mei oanhâldende foarútgong yn technology en tanommen fraach nei hege kwaliteit, presys dielen yn ferskate yndustry. Guon fan 'e wichtige ûntjouwings dy't yn' e kommende jierren ferwachte wurde omfetsje:
- Ferhege gebrûk fan automatisearring en robotika om effisjinsje te ferbetterjen en kosten te ferminderjen.
- Ynspanningen binne rjochte op it ûntwikkeljen fan nije materialen en prosessen om dielprestaasjes te ferbetterjen en nije applikaasjes mooglik te meitsjen.
- It is in groeiende oannimmen fan duorsume praktiken, lykas it brûken fan recycled materialen en it optimalisearjen fan enerzjyferbrûk, om de miljeu-ynfloed fan spuitgieten te ferminderjen.
- Gruttere yntegraasje fan digitale technologyen, lykas 3D-printsjen en simulaasjesoftware, om ûntwerp- en produksjeprosessen te ferbetterjen.
De wrâldwide merk foar spuitgieten wreidet út, fral yn opkommende ekonomyen, dreaun troch de tanimmende fraach nei plestikprodukten yn ferskate yndustry.
De juste partner foar spuitgieten kieze
De juste partner foar spuitgieten kieze is krúsjaal foar it sukses fan jo projekt. Nim de tiid om meardere opsjes te evaluearjen, sitebesites út te fieren en yngeande diskusjes te dwaan om in kompatibel en lang duorjende partnerskip te garandearjen.
- Expertise en ûnderfining:Sjoch foar in ynjeksje moulding partner mei wiidweidige kennis en ûnderfining yn 'e yndustry. Se moatte in bewezen track record hawwe fan it leverjen fan produkten en oplossingen fan hege kwaliteit oan kliïnten yn ferskate sektoaren. Beskôgje har begryp fan ferskate materialen, skimmelûntwerpen en fabrikaazjeprosessen.
- Manufacturing mooglikheden: Beoardielje de produksjemooglikheden fan 'e ynjeksjefoarmpartner. Soargje derfoar dat se in goed ynrjochte foarsjenning hawwe mei moderne masines en technologyen om jo projekteasken te behanneljen. Beskôgje har produksjekapasiteit, fermogen om ferskate dielgrutte en kompleksiteiten te behanneljen, en fermogen om te foldwaan oan jo winske produksjevoluminten en tiidlinen.
- Kwaliteitssoarch:Kwaliteit is foarop yn ynjeksjefoarmjen. Evaluearje de kwaliteitskontrôlesystemen en sertifikaten fan 'e potensjele partner. Sjoch foar partners dy't strikte kwaliteitsnormen folgje, robúste ynspeksjeprosessen hawwe en wiidweidige testen útfiere om kwaliteit en konsistinsje fan diel te garandearjen.
- Untwerp en technyske stipe:In betroubere ynjeksjefoarmpartner moat ûntwerp- en technykstipe oanbiede om jo dielûntwerp te optimalisearjen foar fabrikaazje. Se moatte betûfte yngenieurs hawwe dy't weardefolle ynput kinne leverje oer materiaalseleksje, skimmelûntwerp en prosesoptimalisaasje om dielkwaliteit en effisjinsje te ferbetterjen.
- Kosten konkurrinsjefermogen:Wylst kosten net de iennichste bepalende faktor moatte wêze, is it essensjeel om de prizen en kostenkonkurrinsjefermogen fan 'e ynjeksjefoarmpartner te evaluearjen. Freegje detaillearre offertes en beskôgje toolingkosten, materiaalkosten, arbeidskosten, en alle ekstra tsjinsten dy't se leverje.
- Kommunikaasje en gearwurking:Effektive kommunikaasje en gearwurking binne essinsjeel foar in suksesfolle partnerskip. Soargje derfoar dat de ynjeksjefoarmpartner goede kommunikaasjekanalen hat, reageart op jo fragen en kin regelmjittige projektupdates leverje. In gearwurkjende oanpak sil helpe om te soargjen dat wy oan jo easken foldwaan en alle útdagings prompt oanpakke.
- Klantreferinsjes en resinsjes:Sykje klantferwizings of lês resinsjes / tsjûgenissen om ynsjoch te krijen yn 'e ûnderfiningen fan oare kliïnten mei de ynjeksjefoarmpartner. It krijen fan dizze ynformaasje kin helpe om har betrouberens, spoed en algemiene nivo fan klanttefredenheid te bepalen.
Konklúzje
Thermoplastysk ynjeksjefoarmjen is in alsidige en kosten-effektive metoade foar it produsearjen fan plestik dielen yn grutte hoemannichten. It fermogen om komplekse foarmen te produsearjen mei hege presyzje en konsistinsje is in populêre kar wurden wurden foar ferskate yndustry, ynklusyf automotive, medyske, elektroanika en konsuminteguod. Troch de ferskate aspekten fan thermoplastysk spuitgieten te begripen, ynklusyf de foardielen, neidielen, en ûntwerp oerwagings, kinne jo ynformeare besluten nimme oer it kiezen fan de juste spuitgietpartner foar jo bedriuwsbehoeften.