Termoplastické vstřikování
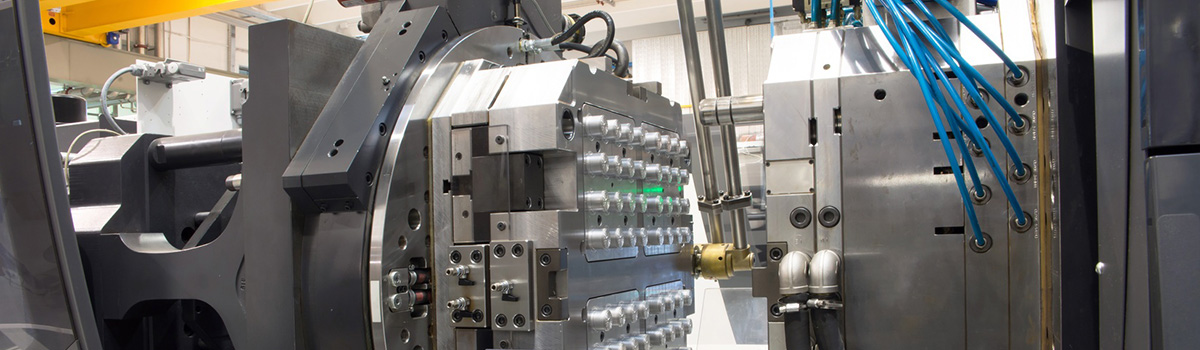
Vstřikování termoplastů je populární výrobní proces používaný k výrobě různých plastových dílů pro různá průmyslová odvětví. Tento proces zahrnuje tavení plastových pelet a jejich vstřikování do formy pro vytvoření trojrozměrného tvaru. Vstřikování termoplastů je vysoce efektivní a nákladově efektivní pro výrobu velkých objemů vysoce kvalitních plastových dílů s úzkými tolerancemi. Tato komplexní příručka prozkoumá různé aspekty vstřikování termoplastů, včetně jeho výhod a nevýhod, typů používaných termoplastů, procesu vstřikování, konstrukčních aspektů a mnoha dalších.
Historie vstřikování termoplastů
Historie vstřikování termoplastů zahrnuje více než století technologického pokroku, vývoje materiálů a průmyslových aplikací. Od svých skromných začátků jako proces lisování celuloidu až po současnou sofistikovanou technologii je vstřikování i nadále životně důležitou výrobní technikou, pohání inovace a formuje různá průmyslová odvětví.
- První vývoj:John Wesley Hyatt a jeho bratr Isaiah vyvinuli první praktický vstřikovací stroj, sledující počátky vstřikování termoplastů až do konce 19. století. V roce 1872 patentovali zařízení, které pomocí pístu vstřikovalo celuloid do dutiny formy a vytvářelo pevné předměty. Tento průlom položil základ pro moderní proces vstřikování.
- Pokroky v materiálech:Na počátku 20. století se zaváděním nových syntetických polymerů otevřely nové možnosti pro vstřikování. Bakelit, fenolová pryskyřice, se stal oblíbeným materiálem pro lisování díky svým vynikajícím elektroizolačním vlastnostem. V průběhu 1930. a 1940. let vedly pokroky v chemii polymerů k vývoji dalších termoplastů, jako je polystyren a polyethylen, které dále rozšířily řadu materiálů vhodných pro vstřikování.
- Průmyslové přijetí: Široké přijetí termoplastického vstřikování začalo v 1950. letech XNUMX. století, kdy výrobci uznali jeho nákladovou efektivitu a všestrannost. Zavedení vysokotlakých strojů umožnilo rychlejší cykly a zvýšení objemu výroby. V důsledku toho vznikl rozmanitý výběr produktů pro osobní i průmyslové použití. Jednalo se o automobilové komponenty, domácí spotřebiče a hračky.
- Technologické inovace:V průběhu desetiletí se technologie vstřikování neustále vyvíjela. V 1960. letech se objevily počítačem řízené stroje, které umožňovaly přesnou kontrolu nad procesem formování. Zavedení systémů horkých vtoků v 1980. letech 3. století snížilo odpad a zlepšilo účinnost odstraněním potřeby vtoků a vtoků. Pokroky v oblasti automatizace, robotiky a XNUMXD tisku v posledních letech způsobily další revoluci v odvětví vstřikování plastů, umožnily komplexní návrhy a zkrátily dobu výroby.
- Udržitelnost a recyklace:S rostoucími obavami o životní prostředí přijal průmysl vstřikování plastů opatření udržitelnosti. Výrobci vyvinuli bio-založené a recyklované termoplasty, což snižuje závislost na materiálech na bázi fosilních paliv. Kromě toho vylepšené recyklační technologie umožnily opětovné zpracování spotřebitelského a postindustriálního odpadu, čímž se minimalizoval dopad termoplastického vstřikování na životní prostředí.
- Budoucí prospekty:Budoucnost vstřikování termoplastů vypadá slibně. Průmysl zkoumá inovace, jako je mikrovstřikování pro miniaturní součástky, vícemateriálové a přestřikovací techniky pro složité díly a integrace inteligentních technologií pro monitorování a optimalizaci procesů. Kromě toho vědci očekávají, že pokroky v biodegradabilních materiálech a výrobě aditiv způsobí revoluci v oboru, díky čemuž bude vstřikování ještě udržitelnější a všestrannější.
Výhody vstřikování termoplastů
Vstřikování termoplastů nabízí výrobcům řadu výhod. Poskytuje flexibilitu návrhu a umožňuje komplexní a složité návrhy s různými funkcemi. Proces je nákladově efektivní, snižuje plýtvání materiálem a snižuje jednotkové náklady. Vstřikování termoplastů podporuje více materiálů a poskytuje všestrannost pro různé aplikace.
- Flexibilita designu:Vstřikování termoplastů umožňuje složité a složité návrhy s vlastnostmi, jako jsou podříznutí, tenké stěny a různé tloušťky, což poskytuje návrhářům obrovskou svobodu.
- Efektivita nákladů: Proces je vysoce účinný, snižuje plýtvání materiálem a snižuje jednotkové náklady. Současné lisování více dílů a rychlé výrobní cykly přispívají k úspoře nákladů.
- Všestrannost materiálu: Vstřikování termoplastů podporuje širokou škálu materiálů, což umožňuje výrobcům vybrat si nejvhodnější variantu pro každou aplikaci, včetně pevných nebo flexibilních, průhledných nebo neprůhledných a chemicky odolných materiálů.
- Síla a odolnost:Vstřikované termoplasty mohou vykazovat vynikající mechanické vlastnosti, jako je vysoká pevnost, houževnatost a odolnost proti nárazu. Možnosti vyztužení, jako jsou skleněná nebo uhlíková vlákna, tyto vlastnosti dále zlepšují.
- Konzistence a kvalita:Vstřikování zajišťuje konzistentní kvalitu jednotlivých dílů a rozměrovou přesnost, poskytuje těsné tolerance a spolehlivé produkty. Tento proces také poskytuje hladkou a jednotnou povrchovou úpravu, což eliminuje potřebu dalších dokončovacích operací.
- Škálovatelnost a hromadná výroba:Vstřikování je škálovatelné od malých po velké objemy, takže je vhodné pro hromadnou výrobu. Jakmile výrobci vytvoří formu, mohou vyrábět velké množství identických dílů s minimálními odchylkami.
- Integrace a montáž:Vstřikované díly mohou obsahovat více součástí do jednoho kusu, což snižuje potřebu dalších montážních procesů. Tato integrace zvyšuje výkon produktu, zkracuje dobu montáže a snižuje náklady.
- Udržitelnost:Průmysl vstřikování se stále více zaměřuje na udržitelnost. Dostupnost biologických a recyklovaných materiálů umožňuje vyrábět produkty šetrné k životnímu prostředí. Efektivní využití materiálů a recyklovatelnost termoplastů přispívá k ekologičtějšímu výrobnímu procesu.
Tyto výhody z něj učinily široce používanou výrobní metodu v různých průmyslových odvětvích, která poskytuje vysoce kvalitní, nákladově efektivní a ekologická řešení pro komplexní požadavky na produkty.
Nevýhody vstřikování termoplastů
Zatímco termoplastické vstřikování nabízí četné výhody, existuje také několik nevýhod. Výrobci musí tyto faktory pečlivě posoudit a porovnat je s výhodami, aby určili vhodnost vstřikování termoplastů pro jejich konkrétní aplikace.
- Vysoká počáteční investice: Nastavení operace vstřikování termoplastů vyžaduje značné počáteční investice do návrhu a výroby formy a nákupu specializovaného strojního zařízení. Náklady spojené s vytvářením forem a nástrojů mohou být značné, zejména u složitých a složitých návrhů.
- Omezení designu: Zatímco vstřikování termoplastů nabízí konstrukční flexibilitu, existují určitá omezení. Například dosažení jednotné tloušťky stěny v celém dílu může být náročné, což vede k odchylkám v distribuci materiálu a potenciálním strukturálním slabinám. Kromě toho přítomnost podříznutí nebo složitých geometrií může vyžadovat použití dalších prvků formy nebo sekundárních operací, což zvyšuje náklady a dobu výroby.
- Dlouhé dodací lhůty:Proces navrhování a výroby forem pro vstřikování může být časově náročný, což vede k delším dodacím lhůtám pro vývoj produktu. Proces iterace návrhu, výroba forem a testování mohou výrazně prodloužit celkovou časovou osu výroby, což nemusí být vhodné pro projekty s krátkými termíny.
- Omezení výběru materiálu:Přestože vstřikování termoplastů podporuje širokou škálu materiálů, existují určitá omezení a omezení. Některé materiály mohou mít specifické požadavky na zpracování nebo omezenou dostupnost, což ovlivňuje výběr designu a výběr materiálu pro konkrétní aplikaci.
- Omezení velikosti dílu:Vstřikovací lisy mají omezení velikosti, a to jak z hlediska fyzické velikosti zařízení, tak velikosti forem, které mohou pojmout. Výroba velkých dílů může vyžadovat specializované vybavení nebo alternativní výrobní metody.
- Zásah do životního prostředí:Zatímco průmysl pracuje na udržitelnosti, proces vstřikování termoplastů stále vytváří odpadní materiál, včetně šrotu a vtoků. Pro minimalizaci dopadu na životní prostředí je nezbytná řádná likvidace a recyklace těchto materiálů.
- Složitost optimalizace procesů:Dosažení optimálních procesních parametrů pro vstřikování termoplastů může být složité a časově náročné. Výrobci musí pečlivě kontrolovat a optimalizovat teplotu, tlak, rychlosti chlazení a doby cyklů, aby zajistili konzistentní kvalitu dílů a minimalizovali závady.
Typy termoplastů používaných při vstřikování
To je jen několik příkladů termoplastů běžně používaných při vstřikování. Každý materiál má jedinečné vlastnosti, díky čemuž je vhodný pro specifické aplikace založené na pevnosti, pružnosti, chemické odolnosti, průhlednosti a ceně. Výrobci by měli vzít v úvahu tyto vlastnosti a požadavky při výběru vhodného termoplastu pro své projekty vstřikování.
- Polypropylen (PP):Polypropylen je všestranný termoplast běžně používaný při vstřikování. Nabízí vynikající chemickou odolnost, nízkou hustotu a dobrou rázovou houževnatost. PP (polypropylen) má široké uplatnění v balení, automobilových součástkách, domácích spotřebičích a lékařských zařízeních.
- Polyetylen (PE):Polyethylen je dalším široce používaným termoplastem při vstřikování. Je k dispozici v různých formách, jako je vysokohustotní polyethylen (HDPE) a nízkohustotní polyethylen (LDPE). PE nabízí dobrou chemickou odolnost, houževnatost a flexibilitu, díky čemuž je vhodný pro láhve, nádoby a potrubí.
- Polystyren (PS):Polystyren je všestranný termoplast známý pro svou čirost, tuhost a cenovou dostupnost. Běžné použití nachází v obalech, spotřebním zboží a jednorázových výrobcích. PS (polystyren) umožňuje rychlé zpracování a poskytuje dobrou rozměrovou stálost, ale může být křehký a náchylný k praskání vlivem okolního prostředí.
- Akrylonitrilbutadienstyren (ABS): ABS je oblíbený termoplast známý pro svou vynikající odolnost proti nárazu a trvanlivost. Kombinuje vlastnosti akrylonitrilu, butadienu a styrenu a vytváří všestranný materiál vhodný pro automobilové díly, pouzdra elektroniky a hračky.
- Polyvinylchlorid (PVC): PVC je široce používaný termoplast známý pro svou vynikající chemickou odolnost, trvanlivost a nízkou cenu. Může být tuhý nebo pružný v závislosti na použitém složení a přísadách. PVC (polyvinylchlorid) nachází běžné použití ve stavebnictví, elektrické izolaci, zdravotnických výrobcích a balení.
- Polykarbonát (PC): Polykarbonát je transparentní termoplast s mimořádnou rázovou houževnatostí a vysokou tepelnou odolností. Běžně se používá v aplikacích, které vyžadují optickou čistotu, jako jsou automobilové komponenty, ochranné přilby a elektronické displeje.
- Nylon (polyamid):Nylon je pevný a odolný termoplast známý pro své vynikající mechanické vlastnosti a chemickou odolnost. Běžně se používá v aplikacích, které vyžadují vysokou pevnost, jako jsou automobilové díly, průmyslové komponenty a spotřební zboží.
- Polyethylentereftalát (PET):PET je oblíbený termoplast pro výrobu lahví, nádob a obalových materiálů. Nabízí dobrou čirost, chemickou odolnost a bariérové vlastnosti, díky čemuž je vhodný pro potravinářské a nápojové aplikace.
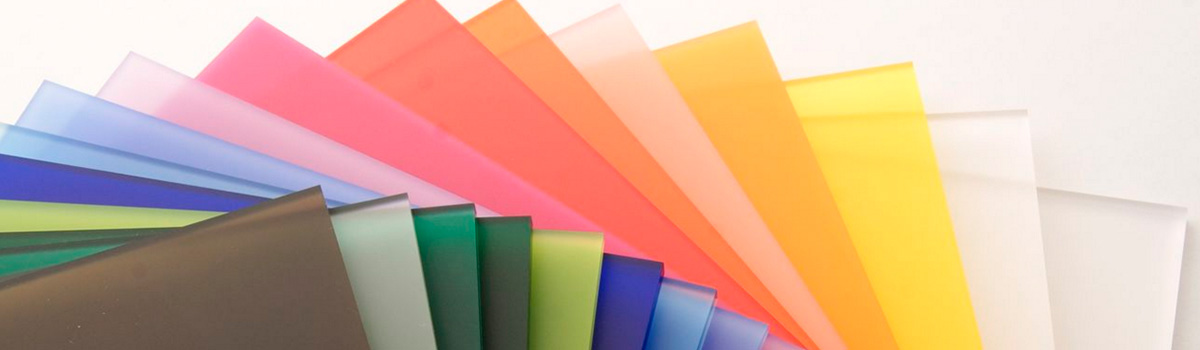
Vlastnosti termoplastů používaných ve vstřikování
Tyto vlastnosti termoplastů hrají zásadní roli při určování jejich vhodnosti pro konkrétní aplikace vstřikování. Výrobci musí pečlivě zvážit tyto vlastnosti a vybrat vhodný termoplast na základě požadovaného výkonu, podmínek prostředí a požadavků na cenu.
- Mechanické vlastnosti:Termoplasty používané při vstřikování mohou vykazovat různé mechanické vlastnosti, včetně pevnosti v tahu, odolnosti proti nárazu a pevnosti v ohybu. Tyto vlastnosti určují schopnost materiálu odolávat aplikovaným silám a jeho celkovou trvanlivost v různých aplikacích.
- Chemická odolnost:Mnoho termoplastů používaných při vstřikování má pozoruhodnou odolnost vůči chemikáliím, rozpouštědlům a olejům. Tato vlastnost je zásadní pro aplikace, které zahrnují vystavení drsnému prostředí nebo korozivním látkám.
- Tepelná stabilita:Tepelná stabilita termoplastů se týká jejich schopnosti odolávat zvýšeným teplotám bez výrazné degradace. Některé termoplasty vykazují vynikající tepelnou odolnost, což jim umožňuje zachovat si své mechanické vlastnosti i při vysokých teplotách.
- Elektrické vlastnosti:Termoplasty používané při vstřikování mohou mít specifické elektrické vlastnosti, včetně elektrické izolace, vodivosti nebo dielektrické pevnosti. Tyto vlastnosti jsou zásadní pro aplikace v elektrotechnickém a elektronickém průmyslu, kde materiály musí poskytovat spolehlivý elektrický výkon.
- Přehlednost a srozumitelnost:Některé termoplasty, jako je polykarbonát a PET, nabízejí vynikající průhlednost a čirost, díky čemuž jsou vhodné pro aplikace, které vyžadují optické vlastnosti. Výrobci běžně používají tyto materiály ve výrobcích, jako jsou průhledná okna, čočky a displeje.
- Pružnost a houževnatost: Pružnost a houževnatost jsou základní vlastnosti termoplastů používaných v aplikacích, které vyžadují odolnost proti nárazu a trvanlivost. Některé termoplasty, jako je ABS a nylon, nabízejí vynikající houževnatost, což jim umožňuje odolat opakovaným nárazům, aniž by se zlomily.
- Prostorová stabilita:Rozměrová stabilita se týká schopnosti termoplastu udržet si svůj tvar a velikost za různých podmínek, včetně teplotních změn. Materiály s dobrou rozměrovou stabilitou zajišťují konzistentní rozměry dílů a minimalizují riziko deformace nebo deformace.
- Chemická kompatibilita:Chemická kompatibilita termoplastů se týká jejich schopnosti odolávat degradaci nebo interakci s různými chemikáliemi, včetně kyselin, zásad a rozpouštědel. Pro zajištění optimálního výkonu je zásadní výběr termoplastu, který odolá specifickému chemickému prostředí, s nímž se při zamýšlené aplikaci setká.
- Hustota: Termoplasty mají různé tloušťky, což může ovlivnit jejich hmotnost a celkové vlastnosti dílů. Materiály s nízkou hustotou, jako je polyethylen, nabízejí lehká řešení, zatímco materiály s vysokou hustotou, jako je polypropylen, poskytují přidanou pevnost a tuhost.
Proces vstřikování: Krok za krokem
Proces vstřikování probíhá po těchto krocích, což umožňuje efektivní a přesnou výrobu vysoce kvalitních termoplastických dílů. Každý krok vyžaduje pečlivou kontrolu a monitorování, aby byly zajištěny konzistentní rozměry dílů, vlastnosti materiálu a celková kvalita.
- Design a výroba formy: Prvním krokem v procesu vstřikování je návrh a výroba formy. Výrobci musí vytvořit přesný a detailní návrh formy, aby dosáhli požadovaných specifikací dílů. Výrobci pak vyrábějí formu pomocí různých technik, jako je CNC nebo elektroerozivní obrábění (EDM).
- Příprava materiálu: Dalším krokem je příprava, jakmile je forma hotová. Termoplastické pelety nebo granule se vybírají na základě požadovaných vlastností materiálu a taví se v násypce. Operátoři pak přivádějí materiál do válce vstřikovacího stroje, kde dochází k jeho roztavení a homogenizaci.
- Injekce:Během fáze vstřikování obsluha vstřikuje roztavený termoplast do dutiny formy pod vysokým tlakem. Vstřikovací jednotka stroje tlačí roztavený materiál tryskou do formy. Materiál vyplňuje dutinu formy a získává tvar požadovaného dílu.
- Chlazení a tuhnutí:Po naplnění formy obsluha nechá roztavený plast vychladnout a ztuhnout. Chlazení je klíčové pro dosažení rozměrové stability a správné formování dílů. Operátoři mohou řídit proces chlazení cirkulací chladicí kapaliny kanálky ve formě nebo pomocí chladicích desek.
- Otevírání a vyhazování formy:Operátoři otevřou formu a vysunou součást z dutiny formy, jakmile plast ztuhne. Vyhazovací systém uvnitř stroje používá kolíky, vyhazovací desky nebo proudy vzduchu k odstranění oblasti z formy. Poté je forma připravena pro další vstřikovací cyklus.
- Následné zpracování: Po vysunutí může díl podstoupit operace následného zpracování, jako je oříznutí, odstranění otřepů nebo povrchová úprava. Tyto kroky pomáhají odstranit přebytečný materiál, vyhladit hrubé hrany a zlepšit konečný vzhled součásti.
- Inspekce kvality: Posledním krokem je kontrola kvality vstřikovaných dílů a zajištění, že splňují stanovené požadavky. K ověření kvality a integrity dílu lze použít různé techniky kontroly kvality, včetně měření rozměrů, vizuální kontroly a funkčního testování.
- Recyklace a opětovné použití materiálu:Jakýkoli přebytečný nebo odpadní materiál vzniklý během vstřikování lze recyklovat a znovu použít. Snížení používání nových termoplastických materiálů pomáhá minimalizovat odpad a zlepšuje udržitelnost.
Zařízení používané při vstřikování
Tyto komponenty zařízení usnadňují proces vstřikování, od tavení a vstřikování termoplastického materiálu až po tvarování, chlazení a vyhazování finálního dílu. Správný provoz a údržba těchto komponentů zařízení jsou klíčové pro dosažení efektivní, vysoce kvalitní výroby vstřikování.
- Vstřikovací stroj:Primární zařízení ve vstřikování je zodpovědné za tavení termoplastického materiálu, jeho vstřikování do formy a řízení procesu.
- Plíseň: Forma, navržená na zakázku pro vytvoření požadovaného tvaru a vlastností plastového dílu, se skládá ze dvou polovin, dutiny a jádra. Operátoři jej namontují na upínací jednotku vstřikovacího stroje.
- Násypka:Nádoba, která drží termoplastický materiál ve formě pelet nebo granulí a přivádí jej do válce vstřikovacího stroje pro roztavení a vstřikování.
- Hlaveň a šroub: Barel, válcová komora, taví a homogenizuje termoplastický materiál, když se v něm šnek otáčí, aby se materiál roztavil, promíchal a standardizoval.
- Systémy vytápění a chlazení:Vstřikovací stroje mají topná tělesa, jako jsou elektrické ohřívače nebo ohřívače využívající horký olej, ke zvýšení teploty barelu, a chladicí systémy, jako je cirkulace vody nebo oleje, pro chlazení formy a tuhnutí plastové části.
- Vyhazovací systém:Odstraňuje výlisek z dutiny formy po ztuhnutí, obvykle pomocí vyhazovacích kolíků, desek nebo proudění vzduchu během otevírání formy.
- Kontrolní systém:Monitoruje a řídí různé parametry procesu vstřikování a umožňuje operátorům nastavovat a upravovat parametry, jako je rychlost vstřikování, teplota, tlak a doba chlazení.
Vstřikovací lisy: Typy a vlastnosti
Každý typ vstřikovacího lisu má své vlastnosti a výhody, což umožňuje výrobcům vybrat si nejvhodnější zařízení pro jejich specifické výrobní požadavky.
- Hydraulické vstřikovací stroje: Tyto stroje využívají hydraulické systémy k vytvoření potřebného tlaku pro vstřikování roztaveného plastu do formy. Jsou známé svou vysokou upínací silou, přesným ovládáním a všestranností při manipulaci s různými termoplasty. Hydraulické stroje jsou vhodné pro velkosériovou výrobu a mohou pojmout složité formy.
- Elektrické vstřikovací stroje:Elektrické stroje využívají k provozu stroje elektrické servomotory včetně vstřikovacích, upínacích a vyhazovacích systémů. Nabízejí přesné ovládání, energetickou účinnost a rychlejší odezvu než hydraulické stroje. Elektrické stroje jsou ideální pro aplikace s přesným lisováním, které vyžadují vysokou opakovatelnost a přesnost.
- Hybridní vstřikovací stroje:Hybridní stroje kombinují výhody hydraulických a elektrických zařízení. Využívají kombinaci hydraulických a elektrických servosystémů k dosažení vysoké přesnosti, energetické účinnosti a hospodárnosti. Hybridní stroje jsou vhodné pro širokou škálu aplikací a poskytují rovnováhu mezi výkonem a provozními náklady.
- Dvoudeskové vstřikovací stroje: Dvoudeskové stroje mají unikátní konstrukci se dvěma samostatnými deskami pro upnutí formy. Tato konstrukce poskytuje zvýšenou stabilitu, zlepšenou synchronizaci formy a umožňuje větší velikosti forem a vyšší upínací síly. Dvoudeskové stroje jsou vhodné pro velké a složité díly, které vyžadují přesné lisování.
- Vícesložkové vstřikovací stroje:Výrobci navrhují tyto stroje tak, aby vyráběly díly s více materiály nebo barvami v jediném lisovacím cyklu. Mají různé vstřikovací jednotky a formy, které umožňují současné vstřikování různých materiálů. Vícesložkové stroje nabízejí flexibilitu a efektivitu při výrobě složitých dílů s různými vlastnostmi.
- Mikrovstřikovací lisy:Mikrovstřikovací stroje, speciálně navržené pro výrobu malých a přesných dílů, nabízejí neuvěřitelně vysokou přesnost a přesnost. Mohou vytvářet složité detaily s úzkými tolerancemi a minimálním odpadem materiálu. Elektronika, lékařská zařízení a mikrooptika běžně používají mikrovstřikovací stroje.
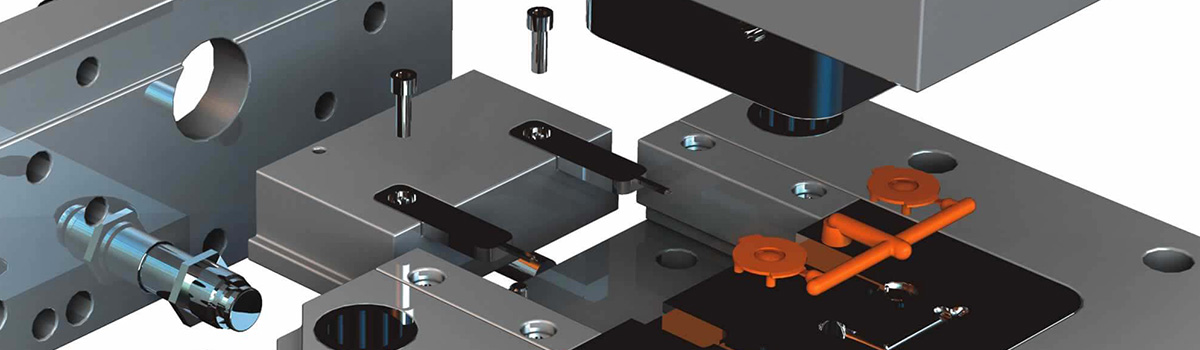
Úvahy o konstrukci formy pro vstřikování
Pro úspěšnou výrobu vstřikovacích forem jsou nezbytné pečlivé úvahy o konstrukci formy.
- Design dílu:Návrh formy by měl odpovídat specifickým požadavkům součásti, včetně jejího tvaru, rozměrů a funkčních vlastností. Výrobci by měli náležitě zvážit úhly úkosu, tloušťku stěny, zářezy a všechny nezbytné prvky, aby zajistili snadné vyhazování a kvalitu dílu.
- Materiál formy: Výběr materiálu formy je rozhodující pro dosažení trvanlivosti, rozměrové stability a tepelné odolnosti. Mezi běžné materiály forem patří ocelové slitiny, hliníkové slitiny a nástrojové oceli. Výběr materiálu závisí na faktorech, jako je objem výroby, složitost součásti a očekávaná životnost nástroje.
- Chladící systém:Efektivní chlazení je nezbytné pro správné tuhnutí součásti a minimalizaci doby cyklu. Konstrukce formy by měla zahrnovat chladicí kanály nebo strategicky umístěné vložky, aby bylo zajištěno rovnoměrné chlazení formy. Správné chlazení snižuje riziko deformace, smrštění a vad dílů.
- Odvětrání:Adekvátní odvětrání je nezbytné, aby se umožnil únik vzduchu a plynů během procesu vstřikování. Nedostatečné odvětrání může vést k lapačům plynu, stopám po popálení nebo neúplnému naplnění součástí. Výrobci mohou dosáhnout odvzdušnění začleněním odvzdušňovacích drážek, čepů nebo jiných mechanismů do konstrukce formy.
- Vyhazovací systém:Konstrukce formy by měla zahrnovat účinný vyhazovací systém pro bezpečné a efektivní vyjmutí lisovaného dílu z dutiny formy. Vyhazovací systém se může skládat z vyhazovacích kolíků, objímek nebo jiných mechanismů, strategicky umístěných tak, aby se zabránilo interferenci s funkcí nebo kritickými funkcemi.
- Design brány:Vrata je místo, kde roztavený plast vstupuje do dutiny formy. Konstrukce uzávěru by měla zajistit správné plnění součástí, minimalizovat průtokové linie a zabránit předčasnému zamrznutí materiálu. Standardní provedení vrat zahrnuje okrajová vrata, tunelová vrata a systémy horkých vtoků v závislosti na požadavcích na součást a vlastnostech materiálu.
- Dělící čára:Návrh formy by měl definovat vhodnou dělicí čáru, což je čára, kde se obě poloviny formy spojují. Správné umístění dělicí čáry zajišťuje minimální záblesk a nesoulad dělicí čáry a usnadňuje efektivní montáž formy.
- Údržba a servis forem: Výrobci by měli zvážit snadnost údržby, oprav a servisu forem. Součásti formy by měly být snadno přístupné pro čištění, kontrolu a výměnu. Začlenění funkcí, jako jsou rychlovýměnné vložky nebo modulární konstrukce forem, může zlepšit použitelnost formy.
Materiály forem používané při vstřikování
Spolupráce se specialisty na formovací materiály a zvážení specifických potřeb lisovací aplikace může pomoci určit nejvhodnější materiál pro dosažení optimálního výkonu formy a kvality dílu.
- Ocelové slitiny: Ocelové slitiny, jako jsou nástrojové oceli (např. P20, H13) a nerezové oceli, se běžně používají pro vstřikovací formy kvůli jejich vynikající životnosti, tepelné odolnosti a odolnosti proti opotřebení. Tyto materiály odolávají vysokým teplotám a tlakům v procesu vstřikování a nabízejí dobrou rozměrovou stabilitu pro výrobu vysoce kvalitních dílů.
- Hliníkové slitiny:Slitiny hliníku, jako jsou 7075 a 6061, jsou lehké a nabízejí dobrou tepelnou vodivost, díky čemuž jsou vhodné pro formy, které vyžadují účinné chlazení. Výrobci často používají hliníkové formy pro prototypování, malosériovou výrobu nebo aplikace, kde je rozhodující snížení hmotnosti. Hliníkové formy však mohou mít nižší trvanlivost ve srovnání s ocelovými slitinami.
- Slitiny mědi:Slitiny mědi, jako je beryliová měď, vykazují vysokou tepelnou vodivost a dobrou obrobitelnost. Používají se ve formách, které vyžadují vynikající přenos tepla pro účinné chlazení. Slitiny mědi mohou pomoci zkrátit doby cyklu tím, že rychle odvádějí teplo z lisovaného dílu, což má za následek rychlejší tuhnutí.
- Nástrojové oceli:Nástrojové oceli, včetně H13, S7 a D2, jsou určeny pro vysoce výkonné nástrojové aplikace. Tyto oceli nabízejí kombinaci vysoké pevnosti, tvrdosti a odolnosti proti opotřebení. Nástrojové oceli jsou vhodné pro formy s vysokými objemy výroby, abrazivní materiály nebo náročné podmínky lisování.
- Slitiny niklu:Slitiny niklu, jako jsou Inconel a Hastelloy, jsou známé pro svou výjimečnou odolnost proti korozi, pevnost při vysokých teplotách a tepelnou stabilitu. Výrobci používají tyto slitiny ve formách, které manipulují s korozivními materiály nebo vyžadují odolnost vůči extrémním teplotám a agresivnímu formovacímu prostředí.
- Kompozitní materiály:Kompozitní materiály, jako jsou vyztužené plasty nebo kompozity s kovovými vložkami, se příležitostně používají pro specifické lisovací aplikace. Tyto materiály nabízejí vyvážené vlastnosti, jako je vysoká pevnost, tepelná stabilita a snížená hmotnost. Kompozitní formy mohou být nákladově efektivní alternativou pro specifické výrobní požadavky.
Typy vstřikovacích forem
Vstřikování je všestranný a široce používaný výrobní proces plastových dílů.
- Dvoudesková forma:Dvoudesková forma je nejběžnějším typem vstřikovací formy. Skládá se ze dvou desek, desky s dutinami a desky jádra, které se oddělují, aby umožnily vysunutí lisovaného dílu. Dutinová deska obsahuje dutinovou stranu formy, zatímco jádrová deska obsahuje stranu jádra. Výrobci používají dvoudeskové formy pro výrobu široké škály dílů díky jejich relativně jednoduché konstrukci.
- Třídesková forma:Třídesková forma je pokročilou verzí dvoudeskové formy. Zahrnuje přídavnou desku, vodicí lištu nebo vtokovou desku. Pojezdová deska vytváří samostatný kanál pro vtokový kanál, vodicí lišty a brány, což umožňuje snazší vyjmutí lisovaného dílu. Výrobci běžně používají třídeskové formy pro detaily se složitými vtokovými systémy nebo když je žádoucí vyhnout se stopě vtoku na kusu.
- Forma horkého vtoku:Systém žlabu a vtoku je vyhříván v horkých vtokových formách, což eliminuje potřebu tuhnutí a opětovného roztavení materiálu během každého cyklu. Systém horkých vtoků se skládá z vyhřívaných rozdělovačů a trysek, které udržují roztavený stav plastu. Formy s horkými vtoky nabízejí výhody, jako je zkrácení doby cyklu, nižší odpad materiálu a zlepšená kvalita dílů díky minimalizaci zbytků vtoků.
- Forma studeného kanálu: Formy se studenými vtoky mají tradiční systém vtoků a vtoků, kde roztavený plast protéká studenými vtoky, které při každém cyklu tuhnou. Obsluha následně odstraní ztuhlé žlaby, což má za následek odpad materiálu. Výrobci obvykle používají složité licí formy pro menší objem výroby nebo když jsou materiálové náklady méně kritické kvůli jejich jednodušší konstrukci.
- Vložit formu:Vkládací formy obsahují kovové nebo plastové vložky do dutiny formy během vstřikování. Vložky mohou být předem umístěny do formy nebo vloženy automatizovanými procesy. Tato forma umožňuje integraci dalších součástí nebo výztužných prvků do lisovaného dílu, čímž se zvyšuje jeho funkčnost nebo pevnost.
- Overmold: Overmolding zahrnuje lisování jednoho materiálu přes druhý, typicky spojení tuhého plastového substrátu s měkčím elastomerem nebo termoplastem. Tento proces umožňuje vytvářet díly s více materiály nebo texturami v jedné formě, což poskytuje lepší přilnavost, odpružení nebo estetické vlastnosti.
Faktory ovlivňující náklady na vstřikování
Zvážení těchto faktorů může výrobcům pomoci odhadnout a optimalizovat náklady na vstřikování a zajistit rovnováhu mezi kvalitou, účinností a nákladovou efektivitou pro jejich specifické výrobní požadavky.
- Složitost dílu:Složitost konstrukce dílu hraje významnou roli při určování nákladů na vstřikování. Složité geometrie, zářezy, tenké stěny nebo složité prvky mohou vyžadovat další nástroje, specializované formy nebo delší cykly, což zvyšuje celkové výrobní náklady.
- Výběr materiálu:Volba termoplastického materiálu ovlivňuje náklady na vstřikování. Různé materiály mají různé ceny za kilogram a faktory jako dostupnost materiálu, vlastnosti a požadavky na zpracování mohou ovlivnit celkovou cenu materiálu.
- Konstrukce nástrojů a forem: Počáteční náklady na nástroje a konstrukci formy jsou významné v nákladech na vstřikování. Faktory jako složitost formy, počet dutin, velikost formy a materiál formy přispívají k nákladům na nástroje a výrobu forem. Složitější formy nebo formy vyžadující pokročilé funkce mohou zvýšit počáteční investici.
- Objem výroby: Objem výroby přímo ovlivňuje náklady na díl při vstřikování. Vyšší knihy často vedou k úsporám z rozsahu, což snižuje náklady na součást. Naopak, nízkoobjemové výrobní série mohou vyžadovat vyšší náklady v důsledku nastavení, nástrojů a plýtvání materiálem.
- Čas cyklu: Doba cyklu, která zahrnuje fázi chlazení a vyhazování, ovlivňuje kapacitu výroby a celkové náklady. Delší doby cyklu mají za následek snížení produkce a potenciálně vyšší ceny. Optimalizace konstrukce formy, chladicího systému a parametrů procesu může minimalizovat doby cyklu a zlepšit efektivitu.
- Požadavky na kvalitu:Přísné požadavky na kvalitu nebo specifické certifikace mohou ovlivnit náklady na vstřikování. Splnění přesných tolerancí, požadavků na povrchovou úpravu nebo dodatečné testování může vyžadovat další zdroje, procesy nebo kontroly, což zvyšuje celkové náklady.
- Sekundární operace:Pokud lisované díly vyžadují operace následného zpracování, jako je montáž, lakování nebo další dokončovací kroky, mohou tyto operace zvýšit celkové náklady na vstřikování.
- Dodavatel a místo:Náklady může ovlivnit výběr dodavatele vstřikovacích forem a jejich umístění. Mzdové náklady, režijní náklady, náklady na logistiku a dopravu se liší v závislosti na lokalitě dodavatele, což má dopad na celkové výrobní náklady.
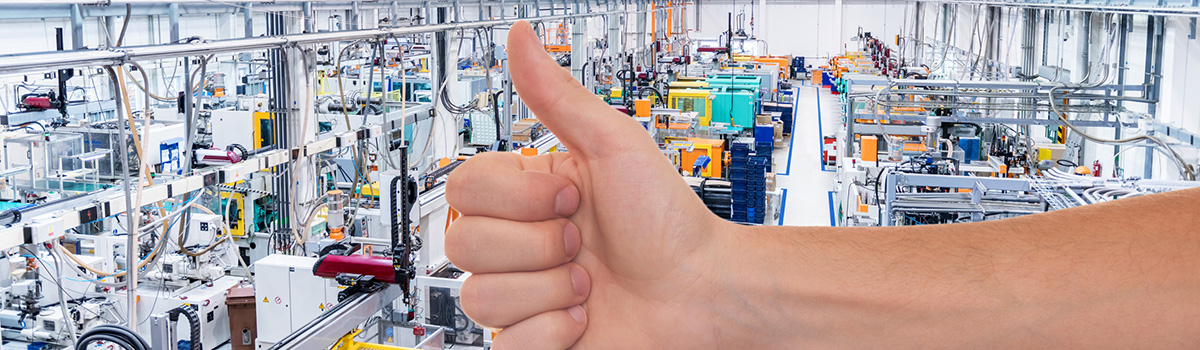
Kontrola kvality ve vstřikování
Implementace robustních opatření pro kontrolu kvality v celém procesu vstřikování pomáhá identifikovat a řešit potenciální vady, odchylky nebo nesrovnalosti a zajistit výrobu vysoce kvalitních dílů, které splňují specifikace a požadavky zákazníků.
- Monitorování procesu: Nepřetržité monitorování klíčových parametrů procesu, jako je teplota taveniny, vstřikovací tlak, doba chlazení a doba cyklu, zajišťuje konzistenci a opakovatelnost výroby dílů. Monitorování v reálném čase a automatizované systémy dokážou detekovat odchylky nebo odchylky od nastavených parametrů, což umožňuje včasné úpravy a udržení stability procesu.
- Kontrola a měření:Pravidelná kontrola a měření lisovaných dílů jsou zásadní pro ověření rozměrové přesnosti, kvality dílů a dodržování specifikací. Naše služby pokrývají řadu metod kontroly kvality, jako je měření rozměrů, analýza kvality povrchu, provádění vizuálních kontrol a provádění funkčních testů. Pro přesné vyhodnocení se používají různé kontrolní techniky, jako jsou souřadnicové měřicí stroje (CMM) a optické a vizuální kontrolní systémy.
- Statistická kontrola procesu (SPC): SPC zahrnuje sběr a analýzu procesních dat pro sledování a kontrolu kvality vstřikování. Statistické metody, jako jsou regulační diagramy a analýza způsobilosti procesu, pomáhají identifikovat trendy, detekovat odchylky procesu a zajistit, aby proces zůstal v definovaných regulačních mezích. SPC umožňuje proaktivní identifikaci problémů a usnadňuje optimalizaci procesů.
- Testování materiálu: Testování surovin, jako jsou termoplasty, aditiva a barviva, zajišťuje jejich kvalitu a vhodnost pro vstřikování. Testování materiálu může zahrnovat analýzu indexu toku taveniny (MFI), mechanické vlastnosti, tepelné charakteristiky a složení materiálu. Ověření kvality materiálu pomáhá předcházet defektům a nesrovnalostem ve formovaných dílech.
- Údržba a kontrola nářadí:Správná údržba a pravidelná kontrola vstřikovacích forem jsou klíčové pro zajištění kvality vstřikování. Pravidelné čištění, mazání a hodnocení součástí forem pomáhá předcházet opotřebení, poškození nebo degradaci, které by mohly ovlivnit kvalitu dílu. Včasná oprava nebo výměna opotřebovaných nebo poškozených součástí formy je nezbytná pro udržení stálého výkonu lisování.
- Dokumentace a sledovatelnost:Vedení komplexní dokumentace a záznamů sledovatelnosti je zásadní pro kontrolu kvality vstřikování. Je životně důležité zaznamenávat parametry procesu, výsledky kontrol, informace o materiálu a jakékoli změny nebo úpravy provedené během výroby. Správná dokumentace umožňuje sledovatelnost dílů, usnadňuje analýzu hlavních příčin a zajišťuje stálost kvality.
- Školení a rozvoj dovedností: Poskytování adekvátního školení a programů rozvoje dovedností pro operátory, techniky a personál kontroly kvality zlepšuje jejich porozumění procesům vstřikování, požadavkům na kvalitu a kontrolním technikám. Dobře vyškolený personál dokáže odhalit závady, odstraňovat problémy a efektivně zavádět nápravná opatření a zajistit tak vysoce kvalitní výrobu.
Běžné vady vstřikování a jak se jim vyhnout
Pravidelná kontrola, sledování a analýza procesů vstřikování a správná údržba a seřizování zařízení a forem může pomoci identifikovat a řešit tyto běžné závady.
- Značky dřezu:Propady jsou prohlubně nebo prohlubně na povrchu lisovaného dílu způsobené nerovnoměrným chlazením nebo smrštěním. Je třeba zvážit správné umístění a design brány, optimální návrh chladicího systému a rovnoměrné rozložení tloušťky stěny, aby se zabránilo stopám po propadu. Zvýšení vstřikovacího tlaku nebo úprava doby chlazení může také pomoci minimalizovat stopy po propadu.
- Warpage:Deformací se rozumí deformace nebo ohnutí lisovaného dílu po vyhození v důsledku nerovnoměrného chlazení nebo zbytkového napětí. Udržování stejnoměrné tloušťky stěny, používání správných chladicích kanálů a zajištění vyváženého plnění a balení formy jsou zásadní pro zabránění deformaci. Optimalizace teploty formy, použití vhodných úhlů úkosu a řízení teploty materiálu a rychlosti vstřikování může pomoci minimalizovat deformaci.
- Blesk:Flash nastává, když přebytečný materiál proudí do dělicí linie formy, což má za následek tenké, nechtěné výstupky nebo další materiál na konečném dílu. Je možné účinně zabránit vzplanutí zajištěním správného návrhu formy, včetně použití adekvátní upínací síly, přesného vyrovnání a použití vhodných odvzdušňovacích technik. Optimalizace procesních parametrů, jako je vstřikovací tlak, teplota a doba cyklu, snižuje záblesky.
- Krátká střela:K rychlému výstřelu dojde, když vstřikovaný materiál nevyplní dutinu formy, což má za následek neúplný díl. Správný výběr materiálu, zajištění adekvátní teploty a viskozity taveniny a udržení vhodného vstřikovacího tlaku a času jsou nezbytné, aby se předešlo krátkým fotografiím. Ověření konstrukce formy pro dostatečnou velikost žlabu a brány a správné odvětrávání může pomoci zabránit rychlým výstřelům.
- Svarové linie:Svarové čáry vznikají, když se dvě nebo více čel toku roztaveného materiálu setkají a ztuhnou, což má za následek viditelnou čáru nebo značku na povrchu součásti. Dobrý design vtoku a žlabu, optimální teplota taveniny, rychlost vstřikování a nastavení toku materiálu a geometrie součásti mohou minimalizovat svarové linie. Analýza toku formy a optimalizace umístění vtoku mohou také pomoci zabránit nebo zmírnit svarové linie.
- Popáleniny:Spáleniny jsou zabarvení nebo černé skvrny na povrchu lisovaného dílu způsobené nadměrným teplem nebo přehřátím materiálu. Vyhýbání se extrémní teplotě taveniny, používání vhodných chladicích kanálů a optimalizace doby cyklu může pomoci předejít stopám po popálení. Adekvátní odvětrávání, správný design vtoku a kontrola teploty formy také přispívají k minimalizaci popálení.
Operace po formování: Dokončení a montáž
Po vstřikování může mnoho lisovaných dílů vyžadovat dodatečné dokončovací a montážní operace k dosažení požadovaného konečného produktu. Tyto operace po formování mohou zahrnovat:
- Ořezávání:Odstraňte veškerý přebytečný materiál nebo odlesky kolem lisovaného dílu pomocí ořezávacích nebo řezných nástrojů.
- Povrchová úprava:Vylepšení vzhledu nebo funkčnosti povrchu součásti pomocí různých technik, jako je malování, potahování nebo texturování.
- Shromáždění:Spojení více lisovaných dílů nebo přidání součástí, jako jsou spojovací prvky, vložky nebo štítky, aby se dokončil konečný produkt.
- Testování:Ověření kvality a funkčnosti dílu pomocí různých testovacích metod, jako je rozměrová analýza, testování vlastností materiálů nebo testování výkonu.
- Balení a doprava:Správné balení a označení hotového výrobku pro odeslání zákazníkům nebo koncovým uživatelům.
Výběr operací po formování závisí na konkrétní aplikaci a požadovaných vlastnostech konečného produktu. Úzká spolupráce mezi odborníky na vstřikování plastů, specialisty na konečnou úpravu a montáž a zákazníkem je zásadní pro dosažení požadované absolutní kvality a funkčnosti produktu. Správné plánování a integrace operací po lisování do výrobního procesu může pomoci zajistit efektivní výrobu a včasné dodání vysoce kvalitních produktů.
Vstřikování vs. jiné procesy výroby plastů
Každý proces výroby plastů má své výhody a omezení, díky čemuž jsou vhodné pro různé aplikace.
- Vstřikování: Vstřikování je vysoce univerzální a široce používaný výrobní proces pro výrobu plastových dílů. Nabízí výhody, jako je vysoká efektivita výroby, přesná replikace dílů a schopnost vytvářet složité geometrie. Vstřikování je vhodné pro velkosériovou výrobu a umožňuje použití široké škály termoplastických materiálů. Nabízí vynikající rozměrovou přesnost a povrchovou úpravu, díky čemuž je ideální pro různá průmyslová odvětví, jako je automobilový průmysl, spotřební zboží a lékařská zařízení.
- Vyfukování: Vyfukování je proces používaný především k výrobě dutých plastových dílů, jako jsou lahve, nádoby a automobilové komponenty. Jedná se o roztavení plastu a jeho nafouknutí do dutiny formy, čímž vznikne požadovaný tvar. Vyfukování je vhodné pro velkosériovou výrobu a může vyrábět velké, lehké díly s rovnoměrnou tloušťkou stěny. Ve srovnání se vstřikováním je však omezena z hlediska složitosti dílu a výběru materiálu.
- Tvarování za tepla:Tepelné tvarování je proces používaný k výrobě plastových dílů zahřátím termoplastické fólie a jejím tvarováním pomocí forem nebo vakuového tvarování. Běžně se používá v obalech, jednorázových produktech a velkoobjemových produktech, jako jsou podnosy a kryty. Tepelné tváření nabízí nákladově efektivní výrobu velkých dílů a umožňuje rychlé prototypování. Má však omezení týkající se složitosti součásti, výběru materiálu a rozměrové přesnosti ve srovnání se vstřikováním.
- Vytlačování:Extruze je kontinuální proces výroby plastových profilů, desek, trubek a fólií. Zahrnuje roztavení plastové pryskyřice a její protlačení matricí, aby se vytvořil požadovaný tvar. Extruze je vhodná pro výrobu dlouhých, souvislých délek plastových výrobků s konzistentním průřezem. Zatímco vytlačování nabízí vysoké výrobní rychlosti a nákladovou efektivitu, je ve srovnání se vstřikováním omezeno z hlediska složitých geometrií součástí a přesné kontroly rozměrů.
- Kompresní lisování:Lisování zahrnuje umístění předem odměřeného množství termosetového materiálu do zahřáté dutiny formy a jeho stlačení pod vysokým tlakem, dokud nevytvrdne. Běžné použití nachází při výrobě dílů s vysokou pevností a rozměrovou stálostí, jako jsou automobilové komponenty a elektrická izolace. Lisování nabízí dobrou konzistenci dílů, vysokou efektivitu výroby a možnost použití široké škály materiálů. Ve srovnání se vstřikováním je však omezena z hlediska složitosti součásti a doby cyklu.
Aplikace vstřikování termoplastů
Různá průmyslová odvětví široce používají vstřikování termoplastů kvůli jeho všestrannosti, účinnosti a hospodárnosti. Některé z aplikací vstřikování termoplastů zahrnují:
- Automobilový průmysl: Automobilový průmysl široce používá vstřikování termoplastů k výrobě různých součástí, včetně vnitřních a vnějších obložení, palubních desek, dveřních panelů, nárazníků a elektrických konektorů. Tento proces umožňuje přesnou replikaci dílů, složité geometrie a lehké materiály, čímž se zlepšuje spotřeba paliva a flexibilita návrhu.
- Spotřební zboží:Vstřikování nachází široké uplatnění při výrobě spotřebního zboží, jako jsou domácí spotřebiče, elektronická zařízení, obalové nádoby a hračky. Tento proces umožňuje hromadnou výrobu odolných, vysoce kvalitních produktů s konzistentními rozměry a povrchovou úpravou. Umožňuje také možnosti přizpůsobení a rychlé iterace produktu.
- Lékařské přístroje:Vstřikování hraje klíčovou roli v lékařském průmyslu pro výrobu široké škály zařízení, včetně injekčních stříkaček, chirurgických nástrojů, implantovatelných komponent a systémů pro podávání léků. Proces zajišťuje výrobu sterilních, přesných a biokompatibilních dílů, které splňují přísné regulační požadavky zdravotnického sektoru.
- Elektronický a elektrotechnický průmysl:Elektronický průmysl využívá vstřikování k výrobě elektrických konektorů, krytů, spínačů a dalších komponent. Tento proces nabízí vysokou rozměrovou přesnost, vynikající povrchovou úpravu a schopnost začlenit funkce, jako je lisování vložek a přelisování, což umožňuje efektivní výrobu složitých elektronických sestav.
- Obalový průmysl:Různá průmyslová odvětví, včetně potravin a nápojů, farmacie a osobní péče, běžně používají vstřikování k výrobě plastových obalových nádob, uzávěrů, uzávěrů a lahví. Tento proces umožňuje vytváření lehkých, odolných a esteticky atraktivních obalových řešení s efektivními výrobními cykly.
- Letecký průmysl:Letecký průmysl využívá vstřikování pro výrobu lehkých a vysoce výkonných součástí, jako jsou vzduchové kanály, držáky, vnitřní panely a konstrukční díly. Tento proces umožňuje použití pokročilých materiálů a složitých geometrií součástí, což přispívá ke snížení hmotnosti a lepší spotřebě paliva.
Vliv vstřikování termoplastů na životní prostředí
Vstřikování termoplastů je oblíbeným výrobním procesem díky mnoha výhodám, ale je také nezbytné vzít v úvahu jeho dopad na životní prostředí. Zde je několik bodů ke zvážení:
- Účinnost materiálu:Vstřikování termoplastů podporuje efektivitu materiálu minimalizací odpadu. Proces využívá přesnou kontrolu nad množstvím materiálu vstřikovaného do formy, což snižuje potřebu přebytečného materiálu. Výrobci mohou také používat techniky přebrušování a recyklace k opětovnému použití šrotu nebo vyřazených dílů, což dále snižuje plýtvání materiálem.
- Spotřeba energie:Výrobci konstruují vstřikovací stroje tak, aby byly energeticky účinné, s moderními modely zahrnujícími pokročilé technologie, jako jsou servomotory a pohony s proměnnými otáčkami. Tyto funkce optimalizují spotřebu energie snížením spotřeby energie během lisování, což má za následek nižší požadavky na energii a nižší dopad na životní prostředí.
- Nakládání s odpady:Při minimalizaci plýtvání materiálem by měli výrobci zavést správné postupy nakládání s odpady, aby nakládali se zbytkovými materiály, vtoky nebo vtoky. Výrobci mohou zavést recyklační programy pro sběr a opětovné použití plastového odpadu vzniklého při vstřikování, čímž se sníží množství odpadu odváženého na skládky.
- Snížení emisí: Vstřikování termoplastů obecně produkuje nižší emise než jiné výrobní procesy. Výrobci mohou snížit emise používáním ekologických materiálů, zaváděním energeticky účinných zařízení a využíváním pokročilých výfukových a filtračních systémů k zachycení jakýchkoli uvolněných emisí.
- Volby udržitelných materiálů:Výběr termoplastických materiálů může významně ovlivnit ekologickou udržitelnost vstřikování. Volba biodegradabilních plastů nebo plastů na biologické bázi, stejně jako recyklovaných nebo recyklovatelných materiálů, může pomoci snížit celkovou ekologickou stopu procesu.
Úvahy o životním cyklu: Zvážení celého životního cyklu lisovaného výrobku je zásadní pro posouzení jeho dopadu na životní prostředí. Během fáze návrhu a výběru materiálu by měli výrobci zvážit faktory, jako je trvanlivost dílu, jeho recyklovatelnost a možnost likvidace nebo opětovného použití na konci životnosti.
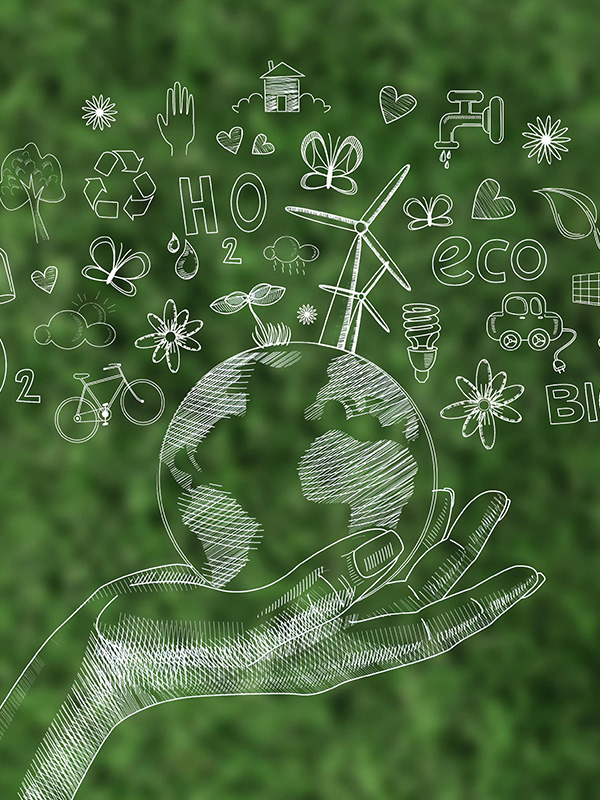
Budoucnost vstřikování termoplastů
Budoucnost vstřikování termoplastů vypadá slibně s neustálým pokrokem v technologii a zvýšenou poptávkou po vysoce kvalitních a přesných dílech v různých průmyslových odvětvích. Mezi klíčové změny očekávané v následujících letech patří:
- Větší využití automatizace a robotiky ke zlepšení efektivity a snížení nákladů.
- Úsilí je zaměřeno na vývoj nových materiálů a procesů pro zlepšení výkonu dílů a umožnění nových aplikací.
- Jde o rostoucí přijetí udržitelných postupů, jako je používání recyklovaných materiálů a optimalizace spotřeby energie, aby se snížil dopad vstřikování na životní prostředí.
- Větší integrace digitálních technologií, jako je 3D tisk a simulační software, pro zlepšení konstrukčních a výrobních procesů.
Globální trh vstřikování se rozšiřuje, zejména v rozvíjejících se ekonomikách, díky rostoucí poptávce po plastových výrobcích v různých průmyslových odvětvích.
Výběr správného partnera pro vstřikování
Výběr správného partnera pro vstřikování je zásadní pro úspěch vašeho projektu. Udělejte si čas na vyhodnocení více možností, proveďte návštěvy na místě a zapojte se do důkladných diskusí, abyste zajistili kompatibilní a dlouhodobé partnerství.
- Odbornost a zkušenosti:Hledejte partnera pro vstřikování s rozsáhlými znalostmi a zkušenostmi v oboru. Měli by mít prokazatelné zkušenosti s poskytováním vysoce kvalitních produktů a řešení klientům v různých odvětvích. Zvažte jejich porozumění různým materiálům, návrhům forem a výrobním procesům.
- Výrobní schopnosti: Posuďte výrobní možnosti partnera pro vstřikování. Zajistěte, aby měli dobře vybavené zařízení s moderními stroji a technologiemi, aby zvládli vaše projektové požadavky. Zvažte jejich výrobní kapacitu, schopnost zvládnout různé velikosti a složitosti dílů a schopnost splnit požadované objemy výroby a časové osy.
- Quality Assurance:Kvalita je u vstřikování prvořadá. Vyhodnoťte systémy kontroly kvality a certifikace potenciálního partnera. Hledejte partnery, kteří dodržují přísné standardy kvality, mají robustní kontrolní procesy a provádějí komplexní testování pro zajištění kvality a konzistence dílů.
- Design a technická podpora:Spolehlivý partner pro vstřikování by měl nabídnout návrhářskou a technickou podporu pro optimalizaci návrhu vašeho dílu z hlediska vyrobitelnosti. Měli by mít zkušené inženýry, kteří mohou poskytnout cenné informace o výběru materiálu, návrhu forem a optimalizaci procesu, aby se zvýšila kvalita a efektivita dílů.
- Cenová konkurenceschopnost:Zatímco náklady by neměly být jediným určujícím faktorem, je nezbytné vyhodnotit cenovou a nákladovou konkurenceschopnost partnera pro vstřikování plastů. Vyžádejte si podrobné nabídky a zvažte náklady na nástroje, materiálové náklady, mzdové náklady a veškeré další služby, které poskytují.
- Komunikace a spolupráce:Pro úspěšné partnerství je nezbytná efektivní komunikace a spolupráce. Ujistěte se, že partner pro vstřikování má dobré komunikační kanály, reaguje na vaše dotazy a může poskytovat pravidelné aktualizace projektu. Přístup založený na spolupráci pomůže zajistit, že splníme vaše požadavky a budeme rychle řešit jakékoli výzvy.
- Zákaznické reference a recenze:Vyhledejte reference zákazníků nebo si přečtěte recenze/osvědčení, abyste získali náhled na zkušenosti ostatních klientů s partnerem pro vstřikování. Získání těchto informací může pomoci určit jejich spolehlivost, rychlost a celkovou úroveň zákaznické spokojenosti.
Proč investovat do čističky vzduchu?
Vstřikování termoplastů je všestranný a nákladově efektivní způsob výroby plastových dílů ve velkém množství. Jeho schopnost vyrábět složité tvary s vysokou přesností a konzistencí se stala oblíbenou volbou pro různá průmyslová odvětví, včetně automobilového průmyslu, lékařství, elektroniky a spotřebního zboží. Pochopením různých aspektů vstřikování termoplastů, včetně jeho výhod, nevýhod a konstrukčních aspektů, můžete činit informovaná rozhodnutí o výběru správného partnera pro vstřikování pro vaše obchodní potřeby.