Problemi e soluzioni comuni nel processo di produzione dello stampaggio a iniezione di materie plastiche
Problemi e soluzioni comuni nel processo di produzione dello stampaggio a iniezione di materie plastiche
Ad un certo punto, tutto stampaggio a iniezione gli impianti riscontrano problemi durante la produzione.
Pertanto oggi presentiamo una guida con i 3 problemi più comuni con le relative 3 soluzioni.
Cominciamo!
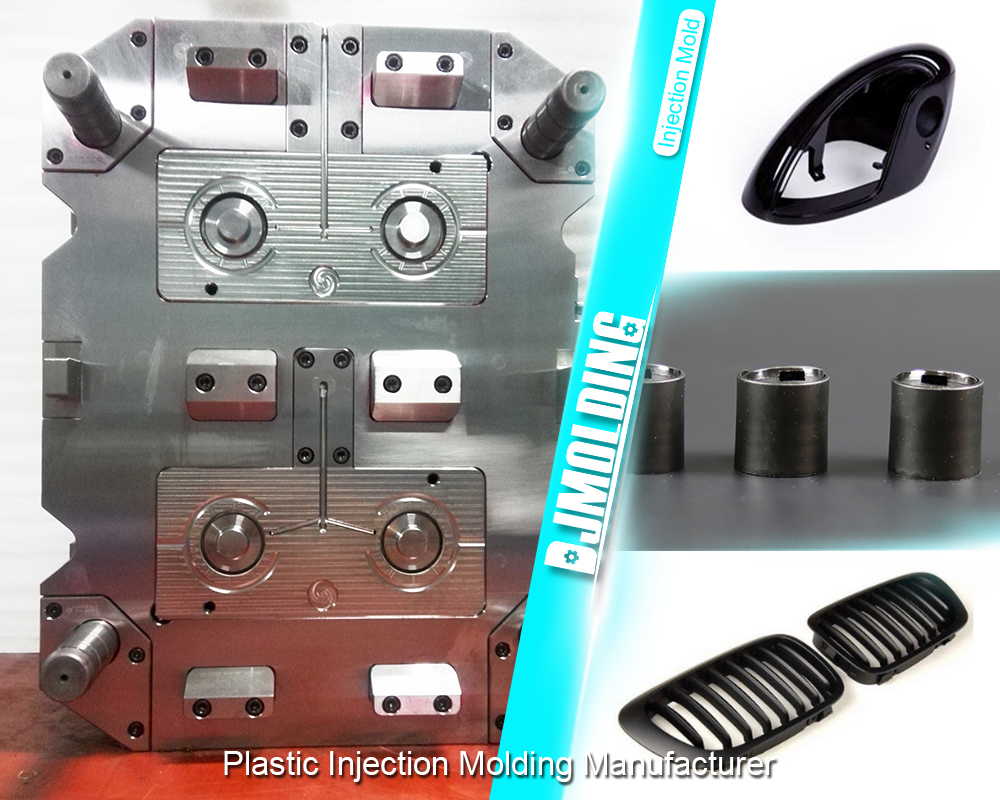
Problema n. 1: segni di graffi sul prodotto
Questi segni sono difetti che compaiono nei pezzi stampati a causa della carenza della materia prima o di un elevato gradiente termico all'interno del pezzo.
Fa sì che il materiale al centro si contragga e “tiri” verso se stesso il materiale sulla superficie, senza compensazione per questa contrazione di volume.
Soluzione:
1) Imballare più plastica nella cavità
Può darsi che la quantità di materia prima disponibile nel ciclo non sia sufficiente.
Ciò si ottiene aumentando il livello o la durata della post-pressione o migliorando il cuscino di iniezione, o anche aumentando il diametro del canale di iniezione o modificando la posizione del stampaggio a iniezione punto della parte.
Si consiglia sempre di riempire dall'estremità più spessa a quella più sottile del pezzo.
2) Ottenere un maggiore flusso di calore
Invece di consentire il raffreddamento a temperatura ambiente, in cui si genera la libera convezione dell'aria, si consiglia di utilizzare la convezione forzata (ad esempio, il raffreddamento con acqua).
Se la planarità del pezzo lo consente, è possibile posizionarlo tra fogli di alluminio1, che dissipano efficacemente il calore per conduzione.
Problema n. 2: il materiale è troppo freddo
Il fluido freddo che esce dall'ugello e va all'interno dello stampo, può provocare aloni indesiderati e diffondersi nel pezzo.
Ciò può anche causare la comparsa di linee di saldatura, causando la spaccatura dell'impasto.
Soluzione
- Controllare la temperatura dello stampo.
Problema n. 3: sbavatura eccessiva
Quando il polimero fuso entra nella superficie di separazione tra le parti dello stampo, si avrà una bava eccessiva.
Generalmente è causato da una pressione di iniezione molto elevata rispetto alla forza di bloccaggio, da un carico eccessivo, da usura o da una scarsa tenuta nelle cavità.
Ciò che è considerato bava eccessiva?
Parti in cui la bava è maggiore di 0.15 mm (0.006”) o che si estende nelle aree di contatto.
Soluzione:
- Ridurre le dimensioni dell'iniezione
- Pressioni di iniezione inferiori
- Aumentare la temperatura dell'impasto aumentando la contropressione e/o la temperatura del tamburo
- Aumentare la temperatura dello stampo o, se possibile, aumentare il tonnellaggio di chiusura
Problema n. 4: linee di flusso visibili presenti sulla superficie della parte mentre la cavità veniva riempita
Sono comunemente causati da una scarsa dispersione del concentrato di colore della resina.
Sono particolarmente visibili su parti nere o trasparenti, su superfici lisce o con finiture metalliche.
Un'altra causa potrebbe essere che la temperatura alla quale si sta lavorando è troppo bassa, perché se non è sufficientemente alta, gli angoli dei fronti di flusso non si svilupperanno completamente, facendo apparire una linea di flusso.
Soluzione
- Aumentare la velocità di iniezione, la pressione di iniezione o la manutenzione.
- Ridurre la temperatura dello stampo o della massa abbassando la contropressione e/o la temperatura del tamburo.
- Aumentare la dimensione della voce e, se possibile, riposizionarla.
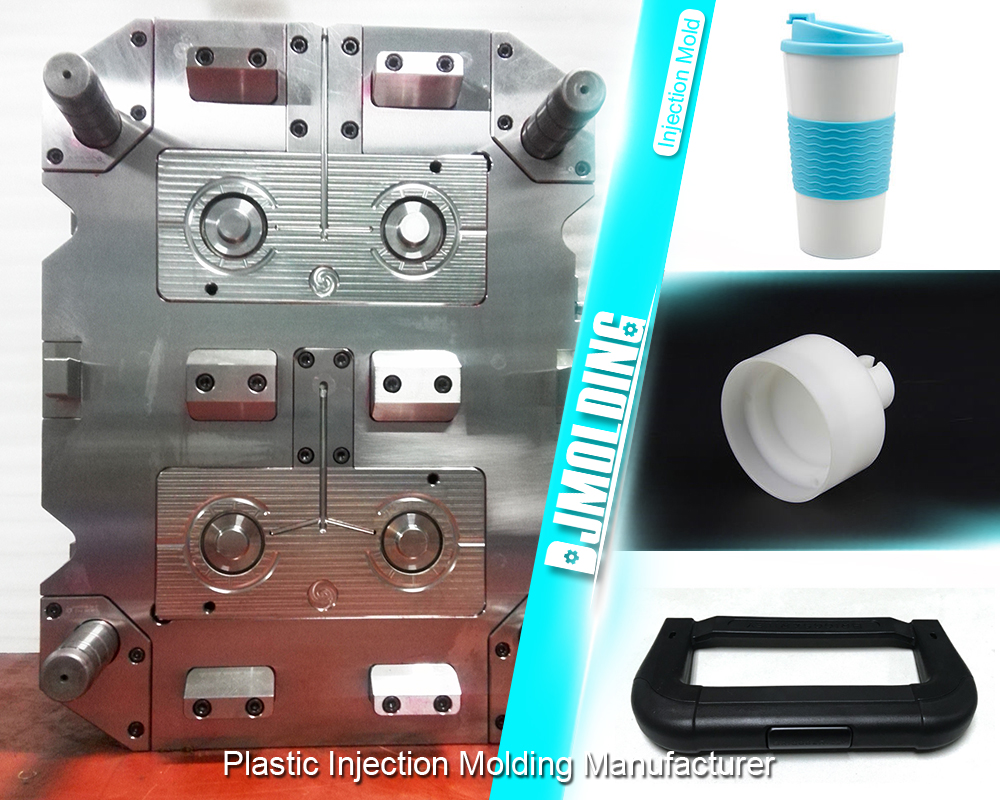
Per ulteriori informazioni sui problemi comuni e sulle soluzioni nel tuo stampaggio ad iniezione di plastica processo di produzione, puoi visitare Djmolding a https://www.djmolding.com/about/ per maggiori informazioni.