Nozioni di base sullo stampaggio ad iniezione di materie plastiche
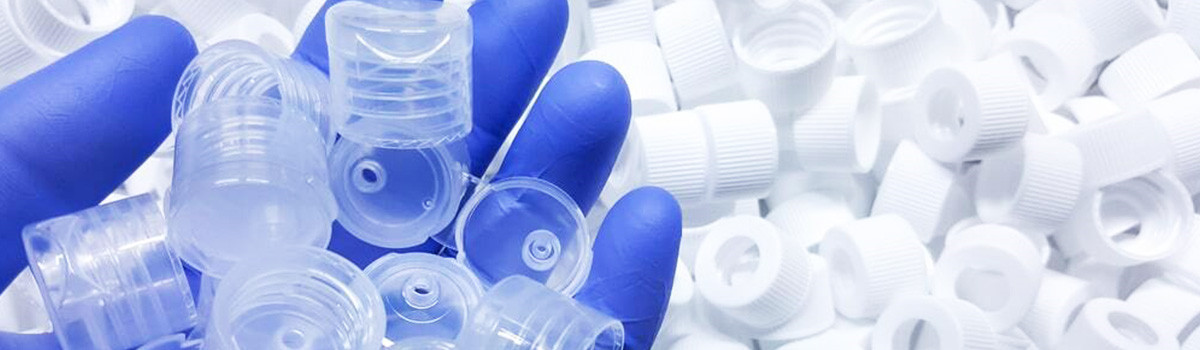
Esplora il processo di stampaggio a iniezione e come funziona.
Lo stampaggio a iniezione di plastica è una tecnica di produzione popolare in cui i pellet termoplastici vengono convertiti in volumi elevati di parti complesse. Il processo di stampaggio a iniezione è adatto a una varietà di materiali plastici ed è un aspetto vitale della vita moderna: custodie per telefoni, custodie elettroniche, giocattoli e persino parti di automobili non sarebbero possibili senza di esso. Questo articolo analizzerà le basi dello stampaggio a iniezione, descriverà come funziona lo stampaggio a iniezione e illustrerà come è diverso dalla stampa 3D.
Quali sono le basi dello stampaggio ad iniezione di materie plastiche?
Le basi del processo di stampaggio a iniezione di materie plastiche includono la creazione del design del prodotto, la realizzazione di uno stampo per adattarsi al design del prodotto, la fusione dei pellet di resina plastica e l'utilizzo della pressione per iniettare i pellet fusi nello stampo.
Vedi una ripartizione di ogni passaggio di seguito:
1. Creazione del design del prodotto
I progettisti (ingegneri, aziende produttrici di stampi, ecc.) creano una parte (sotto forma di file CAD o altro formato trasferibile), seguendo le linee guida di progettazione fondamentali specifiche per il processo di stampaggio a iniezione. I progettisti dovrebbero provare a includere le seguenti caratteristiche nei loro progetti per contribuire ad aumentare il successo di uno stampo a iniezione di plastica:
*Borse per inserti filettati/viteria
*Spessore delle pareti costante o quasi costante
* Transizioni fluide tra spessori di parete variabili
* Cavità cave in sezioni spesse
*Bordi arrotondati
*Angoli di sformo su pareti verticali
*Nelle per supporti
*Adattamenti per attrito, giunzioni a scatto e altre caratteristiche di giunzione senza elementi di fissaggio
* Cerniere viventi
Inoltre, i progettisti dovrebbero ridurre al minimo le seguenti funzionalità per ridurre i difetti nei loro progetti:
*Spessore parete non uniforme o pareti particolarmente sottili/spesse
* Pareti verticali senza angoli di sformo
*Cambiamenti geometrici improvvisi (angoli, fori, ecc.)
* Nervature mal progettate
*Sottosquadri/sporgenze
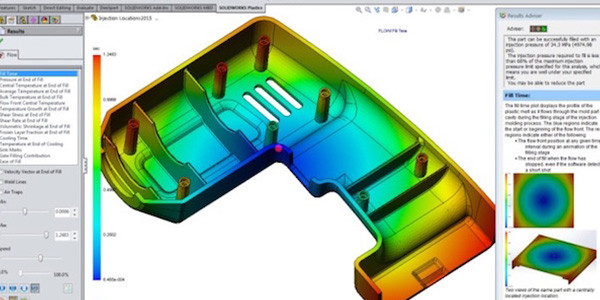
2. Realizzazione di uno stampo per utensili adatto al design del prodotto
Macchinisti e attrezzisti altamente qualificati, utilizzando il design del prodotto, fabbricano uno stampo per utensili per la macchina per lo stampaggio a iniezione. Uno stampo per utensili (noto anche semplicemente come uno strumento) è il cuore e l'anima della macchina per lo stampaggio a iniezione. Sono accuratamente progettati per contenere la cavità negativa per il design del prodotto e caratteristiche aggiuntive come materozze, guide, cancelli, sfiati, sistemi di espulsione, canali di raffreddamento e componenti mobili. Gli stampi per utensili sono realizzati con tipi specifici di acciaio e alluminio in grado di resistere a decine di migliaia (e talvolta centinaia di migliaia) di cicli di riscaldamento e raffreddamento, come alluminio 6063, acciaio P20, acciaio H13 e acciaio inossidabile 420. Il processo di fabbricazione dello stampo richiede fino a 20 settimane per essere completato, inclusa la fabbricazione e l'approvazione, rendendo questo passaggio l'aspetto più esteso dello stampaggio a iniezione. È anche la parte più costosa dello stampaggio a iniezione e, una volta fabbricato uno stampo per utensili, non può essere drasticamente modificato senza incorrere in costi aggiuntivi.
3. Fusione dei pellet di resina plastica
Dopo che gli operatori ottengono lo stampo finito, viene inserito nella pressa ad iniezione e lo stampo si chiude, avviando il ciclo di stampaggio ad iniezione.
I granuli di plastica vengono immessi nella tramoggia e nel fusto. La vite alternativa viene tirata indietro, consentendo ai materiali di scivolare nello spazio tra la vite e la canna. La vite quindi si immerge in avanti, forzando il materiale nella canna e più vicino alle fasce del riscaldatore dove si scioglie in plastica fusa. La temperatura di fusione viene mantenuta costante secondo le specifiche del materiale in modo che non si verifichi alcun degrado nel cilindro o nello stampo stesso.
4. Utilizzo della pressione per iniettare i pellet fusi nello stampo
La vite alternativa forza questa plastica fusa attraverso l'ugello, che si trova all'interno di una depressione nello stampo nota come boccola di colata dello stampo. La pressione della piastra mobile si adatta saldamente allo stampo e all'ugello, assicurando che la plastica non possa fuoriuscire. La plastica fusa viene pressurizzata da questo processo, facendola entrare in tutte le parti della cavità dello stampo e spostando l'aria della cavità attraverso le prese d'aria dello stampo.
Componenti per macchine per lo stampaggio ad iniezione
I componenti di una macchina per lo stampaggio a iniezione includono tramoggia, un cilindro, una vite alternativa, uno o più riscaldatori, una piastra mobile, un ugello, uno stampo e una cavità dello stampo.
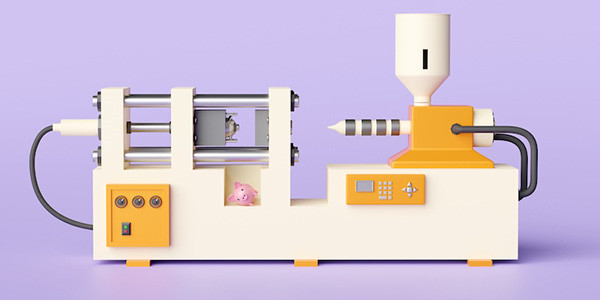
Maggiori informazioni su ciascuno dei componenti dello stampaggio a iniezione nell'elenco seguente:
*Tramoggia: l'apertura in cui i granuli di plastica vengono immessi nella macchina.
*Barile: l'alloggiamento esterno della pressa ad iniezione, che contiene la vite alternativa e i granuli di plastica. La canna è avvolta in diverse fasce riscaldanti ed è dotata di un ugello riscaldato.
* Vite alternativa: il componente del cavatappi che convoglia e pressurizza il materiale plastico mentre fonde attraverso la canna.
*Riscaldatori: noti anche come bande riscaldanti, questi componenti forniscono energia termica ai granuli di plastica, trasformandoli da una forma solida in un liquido. modulo.
*Piano mobile: Il componente mobile collegato all'anima dello stampo che applica pressione per mantenere entrambe le metà dello stampo ermetiche e rilascia anche l'anima dello stampo quando rivela la parte finita.
*Ugello: il componente riscaldato che fornisce un'uscita standard per la plastica fusa nella cavità dello stampo, mantenendo la temperatura e la pressione il più stabili possibile.
*Muffa: il componente o i componenti che contengono la cavità dello stampo e le caratteristiche di supporto aggiuntive come perni di espulsione, canali di guida, canali di raffreddamento, prese d'aria, ecc. Come minimo, gli stampi sono separati in due metà: il lato fisso (più vicino al cilindro) e lo stampo anima (sul piano mobile).
* Cavità dello stampo: lo spazio negativo che, una volta riempito di plastica fusa, lo modellerà nella parte finale desiderata più supporti, cancelli, guide, materozze, ecc.
Come funziona lo stampaggio a iniezione?
Una volta che la plastica ha riempito lo stampo, comprese le sue materozze, guide, cancelli, ecc., lo stampo viene mantenuto a una temperatura prestabilita per consentire una solidificazione uniforme del materiale nella forma del pezzo. Durante il raffreddamento viene mantenuta una pressione di tenuta per arrestare il riflusso nel cilindro e ridurre gli effetti del restringimento. A questo punto, nella tramoggia vengono aggiunti altri granuli di plastica in attesa del ciclo (o sparo) successivo. Una volta raffreddato, il piano si apre e consente l'espulsione del pezzo finito e la vite viene nuovamente tirata indietro, consentendo al materiale di entrare nel cilindro e ricominciare il processo.
Il ciclo di stampaggio a iniezione funziona con questo processo continuo: chiusura dello stampo, alimentazione/riscaldamento dei granuli di plastica, pressurizzazione nello stampo, raffreddamento in una parte solida, espulsione della parte e chiusura dello stampo. Questo sistema consente la produzione rapida di parti in plastica e in una giornata lavorativa è possibile realizzare oltre 10,000 parti in plastica, a seconda del design, delle dimensioni e del materiale.
Djmolding è un'azienda di stampaggio a iniezione a basso volume in Cina. Il nostro processo di stampaggio a iniezione di plastica produce prototipi personalizzati e parti di produzione per uso finale con tempi di consegna fino a 1 giorno, fornitore di parti di stampaggio a iniezione di plastica a basso volume per un massimo di 10000 parti all'anno