インサート射出成形
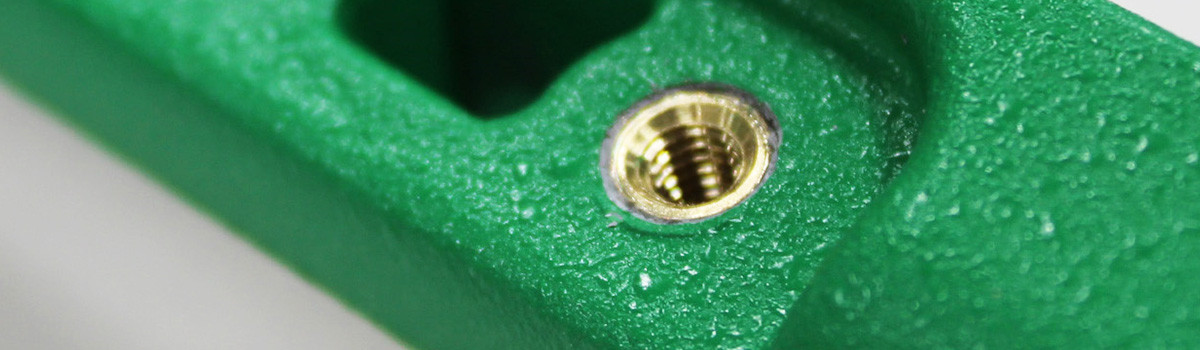
インサート射出成形は、コンポーネントが埋め込まれた複雑なプラスチック部品の製造に広く使用されている製造プロセスです。 この技術では、射出成形プロセスの前に、金型キャビティに金属またはプラスチック部品を挿入します。 次に、溶けた材料が挿入された要素の周りを流れ、XNUMX つの材料間に強固な結合が形成されます。 インサート射出成形には、設計の柔軟性の向上、組み立て時間の短縮、部品の機能の強化など、いくつかの利点があります。 この包括的なガイドでは、インサート射出成形のさまざまな技術、利点、用途について説明します。
インサート射出成形とは何ですか?
射出成形は、さまざまな部品や製品を作成するために使用される製造プロセスです。 インサート射出成形は、成形プロセスを開始する前に、事前に成形された要素またはインサートを金型に挿入できる射出成形の一種です。 この技術により、従来の射出成形法では実現できない特定の機能を必要とする部品の作成が可能になります。
インサート射出成形は、成形プロセスを開始する前に、あらかじめ成形されたインサートを金型キャビティに配置することによって機能します。 インサートには、金属、プラスチック、セラミックなどのさまざまな材料を含めることができます。 成形プロセスは通常どおり、溶融プラスチックが金型キャビティに射出されることから始まります。 プラスチックが冷えて固まると、インサートと融合し、単一の一体化された部品が形成されます。
インサート射出成形を使用することにはいくつかの利点があります。 この技術の主な利点の XNUMX つは、従来の射出成形法では実現できない特定の機能を備えた部品の作成が可能になることです。 たとえば、機能にネジ付きインサートや補強用の金属部品が必要な場合、インサート射出成形を使用できます。 この技術を使用すると、金属インサートを備えたプラスチック部品など、材料を組み合わせた部品を作成することもできます。
インサート射出成形のもう XNUMX つの利点は、時間とコストを節約できることです。 複数のコンポーネントを組み立てる代わりに、インサート射出成形により単一の統合された部品が作成されます。 これにより、企業は組み立てに必要な時間とコストを削減できます。
インサート射出成形は、複雑な部品の作成にも役立ちます。 成形プロセスを開始する前にインサートを金型キャビティに配置できるため、従来の射出成形方法では実現が困難な複雑な形状や機能を備えた部品を製造することができます。
インサート射出成形はどのように行われるのですか?
これは射出成形プロセスの一種であり、成形プロセスを開始する前に、予備成形部品またはインサートを金型に挿入することができます。 この技術により、従来の射出成形法では実現できない特定の機能を備えた部品の作成が可能になり、複雑な部品の作成に特に役立ちます。 ここでは射出成形ワークのインサート方法について説明します。
インサート射出成形プロセスには次の手順が含まれます。
- インサートの配置:インサート射出成形プロセスの最初のステップは、予備成形されたインサートを金型キャビティに配置することです。 メーカーは、金属、プラスチック、セラミックなどのさまざまな材料からこのインサートを製造できます。
- 型締:インサートを所定の位置に配置したら、金型を閉じてクランプで閉じます。 目標は、成形プロセス中にインサートを所定の位置に維持することです。
- 溶融プラスチックの射出:射出成形プロセスでは、溶融プラスチックを金型キャビティに注入します。 メーカーは通常、プラスチックを摂氏 200 ~ 300 度の温度に加熱しますが、その温度は使用する特定のプラスチックに基づいて決定されます。
- 冷却と固化: プラスチックが冷えて固まると、インサートと融合し、単一の一体化された部品が形成されます。 冷却と固化の時間は、使用する特定のプラスチックと製品の製造の複雑さによって異なります。
- 型開きと取り出し: 部品が冷えて固まると、オペレーターは金型を開けて部品を取り出します。 その後、作品を仕上げて使用できるように準備します。
インサート射出成形を使用することにはいくつかの利点があります。 これらの利点には次のようなものがあります。
- 従来の射出成形法では実現できない特定の機能を備えた部品を作成する機能
- 要素は単一の統合部品として作成できるため、組み立て時間とコストが削減されます。
- 複雑な形状や機能を備えた複雑な部品を作成する能力
- 金属、プラスチック、セラミックスなど、さまざまな素材を使用することができます。
- 射出成形は、高効率かつ再現性の高いプロセスであり、高精度で大量の部品を製造できます。
射出成形で使用されるインサートの種類
メーカーは、金属、プラスチック、セラミックなどのさまざまな材料を使用してインサートを作成できます。 これらのインサートを使用すると、従来の射出成形法では達成できなかった特定の機能を備えた部品の作成が可能になります。 ここでは、射出成形で使用されるさまざまなタイプのインサートについて説明します。
- 金属インサート:金属インサートは、プラスチック部品の強度と安定性を高めるために射出成形で一般的に使用されます。 これらは通常、真鍮、鋼、またはアルミニウムで作られており、用途に応じてネジ山付きまたはネジ山なしを選択できます。 メーカーは金属インサートを使用して、高い強度と耐久性を必要とする複雑な形状や要素を備えた部品を作成できます。
- プラスチックインサート: プラスチックインサートは、プラスチック部品をサポートおよび強化するために射出成形でよく使用されます。 通常、ナイロン、ABS、またはポリカーボネート素材で作られており、スナップフィット接続やネジ穴などの特定の機能を備えた部品を作成できます。 メーカーは、軽量でコスト効率の高いソリューションを提供し、さまざまな形状やサイズに簡単に成形できるプラスチック インサートの能力を高く評価しています。
- セラミックインサート: セラミックインサートは、高い強度と耐摩耗性が必要な部品を作成するために射出成形に使用されます。 これらは通常、ジルコニアやアルミナなどの材料で作られており、自動車、航空宇宙、医療産業向けの部品の製造に使用できます。 セラミックインサートは高温、腐食、摩耗に対する耐性が高く、過酷な環境に最適です。
- 複合インサート: メーカーは、金属やプラスチックなどの XNUMX つ以上の材料を組み合わせて複合インサートを作成し、単一の統合部品を作成します。 メーカーはブレンドインサートを利用して、従来の射出成形法では達成できない特定の機能を備えた製品を開発できます。 さらに、これらのインサートを高度にカスタマイズして、特定のアプリケーション固有のニーズを満たすことができます。
- オーバーモールドインサート: 射出成形プロセス中に、メーカーはプラスチック部品にインサートを成形し、その結果、オーバーモールド インサートとして知られるものが得られます。 このプロセスでは、インサートの周囲にプラスチックの最初のショットを作成し、次に最初のショットの上に XNUMX 番目のショットを設定して、単一の一体化された部品を作成します。 メーカーは、プラスチック部品に金属インサートを組み込むなど、材料を組み合わせた部品を作成するためにオーバーモールドインサートを使用することがよくあります。
金属インサートとプラスチックインサート
このプロセスでは、プラスチック射出成形プロセスを開始する前に、金型に配置される予備成形部品またはインサートを使用します。 メーカーは金属やプラスチックなどのさまざまな材料からインサートを製造できますが、それぞれのタイプに独自の長所と短所があります。 この記事では、金属とプラスチックのインサートを比較し、用途に最適なオプションを決定するのに役立ちます。
金属インサート
メーカーは、強度と耐久性が高いため、成形に金属インサートをよく使用します。 これらは通常、真鍮、鋼、またはアルミニウムで作られており、用途に応じてネジ山付きまたはネジ山なしを選択できます。 金属インサートは、プラスチック部品の強度と安定性を高めるために射出成形でよく使用されます。
メタルインサートの利点
- 高強度と耐久性
- 磨耗に強い
- スレッド化を通じて追加機能を提供できます
- 高応力または耐荷重要件のある部品に最適
金属インサートの欠点
- プラスチックインサートよりもコストが高い
- プラスチックインサートよりも成形が難しい
- 重いため、特定のアプリケーションでは懸念される可能性があります
プラスチックインサート
プラスチックインサートは、その汎用性と費用対効果の高さから、成形用に人気があります。 メーカーは通常、ナイロン、ABS、ポリカーボネートなどの材料から製品を製造しており、さまざまな形状やサイズに簡単に成形できます。 プラスチックインサートは軽量で、スナップフィット接続やねじ穴などの特定の機能を備えた部品を作成できます。
プラスチックインサートの利点
- お財布に優しい
- 軽量
- さまざまな形状やサイズに簡単に成形可能
- 応力や耐荷重の要件が低い部品に最適
プラスチックインサートの欠点
- 金属インサートに比べて耐久性が劣る
- 高応力または耐荷重要件のある部品には理想的ではありません
- 時間の経過とともに摩耗しやすくなる可能性があります
金属インサートを選択する場合
金属インサートは、摩耗や損傷に強く、ねじ切り機能も備えているため、高い強度と耐久性が求められる部品に優れています。 金属インサートは、高応力または耐荷重要件が必要な機能にも最適です。 ただし、プラスチックインサートよりも高価であり、成形が難しい場合があります。
金属インサートが必要となる可能性のある用途には次のようなものがあります。
- 自動車および航空宇宙部品
- 医療機器
- 産業機器
- 家電
プラスチックインサートを選択する場合
プラスチックインサートはコスト効率が高く、応力や耐荷重の要件が低い部品に多用途に使用できます。 これらは軽量の特徴を示します。 メーカーはそれらをさまざまな形状やサイズに成形できます。 プラスチックインサートは、スナップフィット接続やネジ穴などの特定の機能が必要な位置にも最適です。 ただし、高応力または耐荷重要件のある細部には、より適したものにする必要がある場合があります。
プラスチックインサートが必要なアプリケーションが含まれています
- 消費財
- 家庭用器具
- おもちゃとゲーム
- 電子
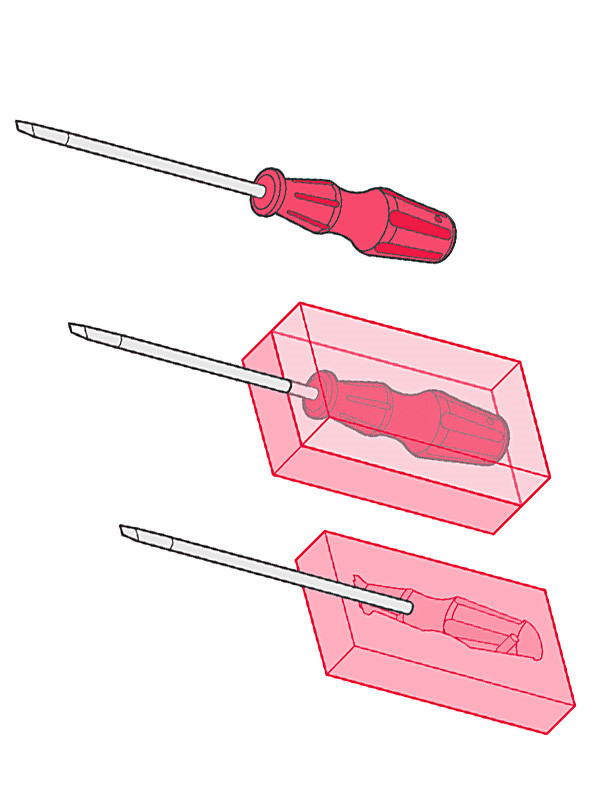
インサート射出成形のメリット
インサート射出成形は、プラスチック射出成形プロセスを開始する前に金型に配置される予備成形部品またはインサートを含む一般的な製造プロセスです。 この技術は従来の成形方法に比べて多くの利点があり、さまざまな用途で人気の選択肢となっています。 この記事では、インサート射出成形の主な利点のいくつかについて説明します。
- 費用対効果の高い: インサート射出成形は、成形後の個別部品の組み立てが不要なため、コスト効率の高い製造ソリューションとなります。 成形時にインサートを統合することで、メーカーは生産効率を高めながら労働力と組み立てコストを削減できます。
- 部品強度の向上: インサート射出成形では、部品のさまざまな領域に異なる材料を使用することで、部品の強度と耐久性を向上させることができます。 この機能は、高い応力や耐荷重の要求に耐えるための詳細を必要とするアプリケーションに特に有益です。
- 設計の柔軟性の向上: インサート射出成形では、複数の特徴や機能を備えた複雑な部品を作成できるため、設計の柔軟性が高まります。 このプロセスは複雑なデザインや形状に適しており、そのような細部に最適です。
- 一貫性と正確性: インサート射出成形は、部品製造において優れた一貫性と精度を実現します。 予備成形されたインサートを金型に正確に配置し、各部品の要件に応じて正確に配置します。 その結果、製造される製品の寸法が均一になり、優れた品質管理が実現されます。
- サイクルタイムの短縮: インサート射出成形では、複数のステップを単一のプロセスに組み合わせることでサイクル タイムを短縮できます。 この方法により、特に大量生産を扱う場合に時間を節約し、生産性を向上させることができます。
- さまざまな素材: インサート射出成形は、プラスチック、金属、セラミックスなどのさまざまな材料に使用できます。 メーカーは、強度、耐久性、コストを考慮して、あらゆる用途に最適な材料を選択できるようになりました。
- 環境上の利点: インサート射出成形は、廃棄物を削減し、材料の使用を最小限に抑えることにより、環境上の利点ももたらします。 インサートを金型に正確に配置するため、従来の成形方法よりも材料の無駄が少なくなります。 これを導入することで、環境負荷の低減や製造コストの削減につながる可能性があります。
インサート成形の設計上の考慮事項
インサート成形は、プリフォームされたインサートをプラスチック射出成形プロセスに統合する一般的な製造プロセスです。 この技術には、部品強度の向上、組み立てコストの削減、設計の柔軟性の向上など、多くの利点があります。 ただし、インサート成形用の部品を設計するには、効率的かつ確実に生産を成功させるために、いくつかの要素を慎重に考慮する必要があります。 この記事では、インサート成形に関する重要な設計上の考慮事項のいくつかについて説明します。
- インサートの配置: 金型内でのインサートの配置は、インサート成形プロセスを成功させるために非常に重要です。 成形プロセス中にインサートがプラスチック材料で完全に封入されるように、インサートは金型内に正確に配置される必要があります。 設計者は、インサートがプラスチック材料の流れを妨げたり、パーティング ラインの問題を引き起こしたりしないことも確認する必要があります。
- 材料の互換性: インサート成形プロセスを成功させるには、インサートとプラスチック材料の両方の材料の選択が重要です。 接着の問題や材料の非互換性を防ぐために、材料は互換性がある必要があります。 設計者は、インサート成形を確実に成功させるために、融点、収縮、熱膨張係数などの材料特性を慎重に考慮する必要があります。
- パーツの形状: 部品の形状もインサート成形の重要な考慮事項です。 設計では、インサートを完全にカプセル化するために、インサートの周囲にプラスチック材料を適切に充填および梱包できるようにする必要があります。 また、部品の形状は、反り、収縮、ヒケの問題を防ぐために、適切な通気と冷却を可能にする必要があります。
- 抜き勾配とアンダーカット: 抜き勾配とアンダーカットの存在は、インサート成形における部品の成形性に影響を与える可能性があります。 設計者は、部品や金型に損傷を与えることなくインサートを金型から簡単に取り外せるように、抜き勾配とアンダーカットの配置と形状を慎重に検討する必要があります。
- ツールに関する考慮事項: インサート成形に必要な工具は、従来の成形方法よりも複雑になる場合があります。 設計者は、インサートの配置と形状、ゲートと通気、必要なサイドアクションを含む金型の設計を慎重に検討する必要があります。 さらに、工具は、適切なインサートの配置を確保し、部品の品質に関する問題を防ぐために、厳しい公差を維持できなければなりません。
インサート射出成形に使用される材料
インサート射出成形は、複雑な部品を正確かつ一貫して製造する高度に専門化されたプロセスです。 このプロセスには、射出成形が行われる前に金型に挿入される、インサートと呼ばれる事前に製造されたフィーチャーの使用が含まれます。 これらのインサートはさまざまな材料から作ることができ、それぞれに独自の特性と利点があります。 ここでは、インサート射出成形で使用される最も一般的な材料とその利点について説明します。
金属
射出成形では、スチール、アルミニウム、真鍮などの金属製のインサートが広く使用されます。 これらの材料は強度と耐久性に優れており、高い耐摩耗性と耐引裂性が要求される部品に最適です。 さらに、金属インサートは高温に耐えることができるため、航空宇宙産業や自動車産業などの要求の厳しい用途での使用に適しています。 射出成形で金属インサートを使用することの具体的な利点には、次のようなものがあります。
- 高強度と耐久性
- 優れた耐熱性
- 耐食性
- 高圧やストレスに耐える能力
プラスチック
プラスチック インサートも射出成形でよく使用され、PEEK、PTFE、UHMW などの材料がよく選ばれます。 これらの材料は、高度な耐熱性、耐薬品性、低摩擦特性を備えています。 これらのコンポーネントは、その高精度と清浄度が医療機器や半導体製造での重要な要素であるため、医療機器や半導体製造での利用に最適です。 射出成形でプラスチックインサートを使用することの具体的な利点には、次のようなものがあります。
- 高い耐薬品性
- 優れた耐熱性
- 低摩擦特性
- 機械加工や形状加工が容易
セラミック
射出成形では、強度、硬度、耐摩耗性が高いセラミックインサートが使用されています。 これらの材料は、部品が高温や過酷な環境に耐える必要がある用途での使用に最適です。 さらに、セラミックインサートは寸法安定性に優れているため、精密工学用途に適しています。 射出成形でセラミックインサートを使用することの具体的な利点には、次のようなものがあります。
- 高強度と硬度
- 優れた耐摩耗性
- 高温耐性
- 寸法安定性
コンポジット
カーボンファイバーやグラスファイバーなどの複合材料は、強度重量比が高いため、射出成形に使用されます。 航空宇宙産業や自動車産業では、軽量化が重要な場合にこれらの材料がよく使用されます。 複合インサートは高い剛性と強度を備えているため、風力タービンや高性能スポーツ用品の用途に最適です。 射出成形で複合インサートを使用することの具体的な利点には、次のようなものがあります。
- 高い強度対重量比
- 高い剛性と強度
- 優れた耐衝撃性
- 低熱膨張係数
ラバー
シリコーンやネオプレンなどのゴム材料は、その柔軟性と密閉性のために射出成形に使用されます。 これらの材料は、シールとクッションが不可欠な医療業界や自動車業界で一般的に使用されています。 ゴムインサートは化学薬品や高温に対する優れた耐性を備えているため、過酷な環境での使用に最適です。 射出成形でゴムインサートを使用することの具体的な利点には、次のようなものがあります。
- 優れたシール性
- 高い柔軟性
- 耐薬品性および耐熱性
- 優れた振動減衰性
泡
ポリウレタンやポリスチレンなどの発泡材料は、軽量で衝撃吸収特性があるため、射出成形に使用されます。 これらの材料は、クッション性と耐衝撃性が不可欠な包装業界や自動車業界でよく使用されます。 フォームインサートは高い断熱性を提供するため、温度に敏感な用途に最適です。 射出成形でフォームインサートを使用する具体的な利点には、次のようなものがあります。
- 軽量で柔軟性
- 優れた衝撃吸収性
- 優れた断熱性
- 複雑な形状に成形する能力
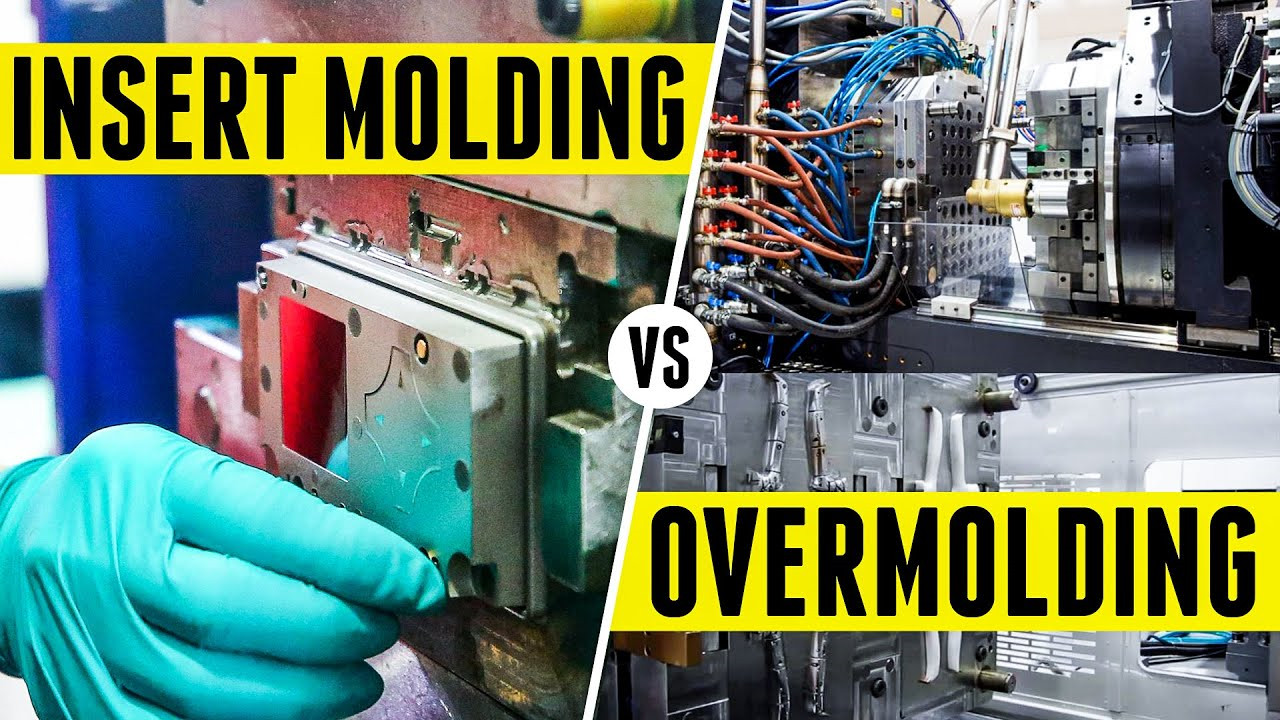
インサート成形とオーバーモールディング: 違いは何ですか?
インサート成形とオーバーモールディングは、複数の材料を使用する射出成形で一般的に使用される XNUMX つのプロセスです。 これらのプロセスは似ているように見えますが、根本的な違いがいくつかあります。 ここではインサート成形とオーバーモールドの違いについて説明します。
インサート成形
インサート成形は、射出成形プロセスが行われる前に、インサートとして知られる事前に製造された部品を金型に挿入するプロセスです。 次に、プラスチック材料がインサートの周囲に射出されて、インサートとプラスチック材料の特性を組み合わせた完成品が作成されます。 このプロセスは、自動車、医療、航空宇宙産業で高精度の部品を作成するために一般的に使用されています。
インサート成形のメリット
- 高精度と精度
- 部品の強度と耐久性の向上
- 組み立て時間とコストの削減
- 異なる特性を持つ材料を組み合わせる能力
オーバーモールディング
オーバーモールディングは、既存の部品の上に XNUMX 番目の材料を射出成形するプロセスです。 メーカーはこのプロセスを使用して、ソフトタッチのハンドル、グリップ、その他の消費者製品を作成します。 オーバーモールドされた材料は通常柔らかくゴム状で、グリップ力と快適性が向上します。 部品の複雑さに応じて、シングルショットまたはツーショットプロセスでオーバーモールドを実行できます。
オーバーモールドのメリット
- 人間工学と美しさの向上
- グリップ力と快適性の向上
- 組み立て時間とコストの削減
- 異なる特性を持つ材料を組み合わせる能力
インサート成形とオーバーモールドの違い
- インサート成形には、事前に製造された部品の挿入が含まれますが、オーバーモールディングは、既存の部品の上に XNUMX 番目の材料を射出成形することで構成されます。
- インサート成形を利用して高精度の部品を作成する一方、オーバーモールディングを利用して製品の人間工学と美観を向上させます。
- インサート成形では特性の異なる材料を組み合わせますが、オーバーモールドではオーバーモールド部分にゴム状の柔らかい材料を使用します。
- インサート成形は自動車、医療、航空宇宙産業でよく使用されますが、オーバー成形は工具、電子機器、パーソナルケア用品などの消費者製品でよく使用されます。
インサート配置のテクニック
インサート成形は、射出成形プロセスが行われる前に、あらかじめ作成された部品またはインサートを金型に配置するプロセスです。 プラスチック材料がインサートの周囲に射出されて完成品が作成されます。 インサートの配置は、インサート成形プロセスを成功させるために非常に重要です。 ここでは、インサートの配置に関するいくつかのテクニックについて説明します。
- 手動配置: この技術では、オペレーターが手動でインサートを金型に配置します。 メーカーは通常、少数のインサートしか必要としない小さな部品や単純な部品にこの技術を使用します。 ただし、時間と労力がかかる可能性があり、手動で配置するためエラーが発生するリスクが高くなります。
- 自動配置: この技術では、ロボットやピックアンドプレース機などのコンピューター化されたシステムを使用して、インサートを金型に配置します。 この技術は手動配置よりも高速かつ正確であるため、大規模な生産工程や複雑な部品に最適です。 ただし、設備への初期投資が必要であり、小規模生産の場合はよりコスト効率が高い必要がある場合があります。
- インサート成形・オーバーモールディング: インサートを XNUMX 番目のオーバーモールド部品に配置し、それを XNUMX 次金型に配置します。 メーカーは通常、複雑な形状や手の届きにくい領域を含むクレームにこの手法を使用します。 また、硬質プラスチックインサートと軟質成形材料など、異なる特性を持つ材料を組み合わせることもできます。
- 接着剤付きインサート:この技術では、インサートを接着剤の裏地でプレコーティングするため、手動または自動配置を必要とせずにインサートを金型に配置できるようになります。 裏面の接着剤は射出成形中に溶けて、インサートをプラスチック材料に接着します。 この技術は小さくて単純な部品によく使用され、製造時間とコストを削減できます。
- ねじ付きインサート: この技術では、ねじ切りされたインサートが金型に配置され、完成品にねじ山を作成するために使用されます。 メーカーは、電子機器や自動車部品など、ネジやボルトの挿入が必要な製品の製造にこの技術をよく使用します。
インサート射出成形機の種類
射出成形プロセスの重要なコンポーネントの XNUMX つは射出成形機です。 これらのマシンにはさまざまなタイプがあり、それぞれに独自の機能と利点があります。 ここでは、さまざまな種類のインサート射出成形機を紹介します。
まず、インサート射出成形機とは何かを定義しましょう。 インサート射出成形機は、プラスチック材料を射出する前に、金属またはプラスチックインサートなどの予備成形部品を金型に挿入できる射出成形機です。 この機能により、ねじ付き開口部や金属サポートなどの追加機能を必要とする複雑な部品の製造が可能になります。
インサート射出成形機の種類は次のとおりです。
- 縦型射出成形機:これらの機械は、金型を垂直に取り付ける垂直方向の設計を採用しています。 インサートを上から金型に簡単に挿入できるため、インサート成形に最適です。 このタイプの機械は必要な床面積も少なく、小規模な生産に適しています。
- 横型射出成形機:これらの機械は、金型を水平に取り付けるフラットな方向の設計を採用しています。 これらは大規模な生産に最適であり、メーカーは通常、より重要な部品の製造にこれらを使用します。 横型機械では、インサートを横から取り付けることができるため、適切な位置合わせを確保することがより困難になります。
- ロータリーテーブル射出成形機:これらの機械には回転テーブルが付いており、複数の金型を取り付けて射出ユニット内に回転させて生産することができます。 このタイプの機械は、金型にさまざまなインサートを挿入して、より複雑な部品を作成できるため、インサート成形に最適です。
- シャトル射出成形機: これらの機械には、射出ユニットと成形領域の間で金型を前後に移動させるシャトルが付いています。 少量の生産に最適であり、インサートの取り付けと取り外しが簡単にできるため、インサート成形に最適です。
インサート成形のプロセスパラメータ
結果として得られる製品は、従来の射出成形と比較して、より優れた強度と耐久性を備えています。 インサート成形のプロセスパラメータは、高品質で一貫した結果を達成するために重要です。 ここではインサート成形のプロセスパラメータを見ていきます。
- 材料の選択: 材料の選択は、インサート成形の重要なプロセスパラメータです。 プラスチック材料は、インサートの材料および用途に適合する必要があります。 互換性があるため、インサートとプラスチック材料がしっかりと接着し、強くて耐久性のある製品が得られます。
- 温度: 温度はインサート成形プロセスにおいて重要な役割を果たします。 プラスチック材料が均一に流れ、ボイドや変形なくキャビティに充填されるように、金型温度を正しく設定する必要があります。 また、熱による損傷を引き起こすことなくプラスチック材料がインサートにしっかりと接着するように、インサートの温度も考慮する必要があります。
- 射出圧力: 射出圧力もインサート成形の重要なパラメータです。 プラスチック材料を金型キャビティに均一かつ迅速に射出するには、張力を正しく設定する必要があります。 射出圧力が高いとインサートまたは金型が変形する可能性があり、射出圧力が低いと金型キャビティの充填が不完全になる可能性があります。
- 射出速度: 射出速度もインサート成形には重要なパラメータです。 プラスチック材料が空隙や変形なく金型キャビティに均一に充填されるように、速度を正しく設定する必要があります。 射出速度が速いと、プラスチック材料に乱流が発生し、最終製品に欠陥が生じる可能性があります。
- 冷却時間: プラスチック材料が固化して最終製品の形状を形成するには、冷却時間が必要です。 最終製品の望ましい形状とサイズを確実に達成するには、冷却時間を正しく設定する必要があります。 冷却時間が短いと変形や収縮が生じる可能性があり、冷却時間が長いとサイクル時間が長くなり、生産性が低下する可能性があります。
- 排出時間: 完成品を金型から取り出すには取り出し時間が必要です。 完成品を損傷や変形なく取り出すには、排出時間を正しく設定する必要があります。 突き出し時間が短いと、突き出しが不完全になったり、製品が損傷したりする可能性があり、突き出し時間が長いと、サイクルタイムが長くなり、生産性が低下する可能性があります。
インサート成形の一般的な欠陥とその回避方法
インサート成形は、プラスチック材料を射出する前に、金属またはプラスチックインサートなどの事前に成形されたコンポーネントを金型に配置する一般的な製造プロセスです。 このプロセスにより、従来の射出成形よりも頑丈で耐久性のある製品が得られます。 ただし、他の製造プロセスと同様に、インサート成形でも最終製品の品質と一貫性に影響を与える欠陥が発生する可能性があります。 ここでは、よくあるインサート成形の欠陥とその回避方法について詳しく見ていきます。
フラッシュ: バリとは、余分なプラスチック材料が金型から漏れ出て、完成品の表面に薄い層を形成するときに発生する欠陥です。 この欠陥は製品の外観や機能に影響を与える可能性があります。 フラッシュを回避するには、次の手順を実行します。
- 射出圧力を下げる
- 型締力の向上
- 離型剤を使用する
- 冷却時間を長くする
ショートショット: ショート ショットは、プラスチック材料が金型キャビティを満たさない場合に発生する欠陥であり、その結果、製品が不完全またはサイズ不足になります。 ショートショットを回避するには、次の手順を実行できます。
- 射出圧力を上げる
- 射出速度を上げる
- 材料温度を上げる
- 金型温度を上げる
反り: 反りは、不均一な冷却や収縮によって完成品が変形したりねじれたりする欠陥です。 反りを回避するには、次の手順を実行します。
- 金型温度を上げる
- 冷却時間を長くする
- 保圧圧力を上げる
- バランスの取れた冷却システムを使用する
ヒケ: ヒケとは、不均一な冷却や収縮によって完成品の表面に生じるくぼみです。 ヒケを避けるには、次の手順を実行できます。
- 金型温度を上げる
- 冷却時間を長くする
- 保圧圧力を上げる
- 製品を強化するには、より厚い壁またはリブを使用します。
はく離: デラミネーションとは、プラスチック材料とインサート材料が適切に接着せず、剥がれたり剥離したりして起こる欠陥のことです。 層間剥離を避けるために、次の手順を実行できます。
- 互換性のあるプラスチック材料を使用し、缶材料を挿入します
- 射出圧力と射出速度を上げる
- インサート温度を上げる
- 金型温度を上げる
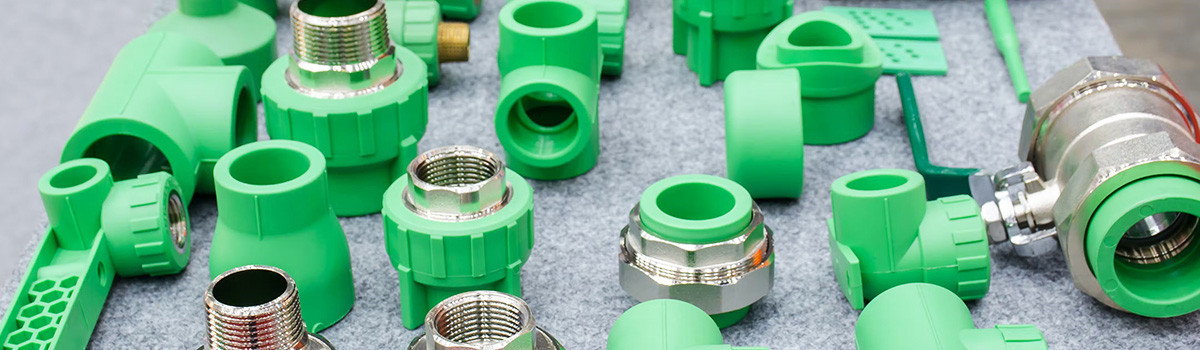
インサート成形の成形後作業
ただし、インサート成形プロセスの完了後、最終製品が希望の仕様を満たしていることを確認するために、いくつかの成形後操作を実行する必要があります。 ここではインサート成形の成形後の作業について詳しく見ていきます。
- バリ取り:バリ取りは、完成品からバリやバリなどの余分な材料を除去するプロセスです。 このプロセスは、製品のサイズと複雑さに応じて、手動または自動で実行できます。
- トリミング:トリミングは、完成品から余分な材料や突起を取り除くプロセスです。 この加工は、製品の形状や大きさに応じて、さまざまな切削工具や工法を使用して行うことができます。
- クリーニング: 洗浄は、完成した製品から汚れ、破片、または汚染物質を除去するプロセスです。 このプロセスは、インサート成形プロセスで使用される材料の種類に応じて、さまざまな洗浄剤または方法を使用して実行できます。
- アセンブリ:組み立ては、複数のコンポーネントを結合して完成品を形成するプロセスです。 このプロセスは、材料の種類や目的の最終製品に応じて、超音波溶接、ホットスタンプ、接着などのさまざまな方法を使用して実行できます。
- テスト: テストは、完成品が望ましい仕様と品質基準を満たしていることを確認するプロセスです。 このプロセスには、製品の種類や用途に応じて、機械的検査、電気的検査、目視検査などのさまざまなテストが含まれる場合があります。
これらの成形後の操作に加えて、成形後の手順の必要性を最小限に抑えるインサート成形プロセスを設計する際に考慮すべき要素もいくつかあります。 これらには次のものが含まれます。
- インサートと成形部品に適した材料の選択
- 成形プロセス中にインサートが適切に配置され、所定の位置に保持されていることを確認します。
- 温度や圧力などの成形パラメータを調整して、欠陥や余分な材料を最小限に抑えます。
- 高品質の金型と設備を使用して、完成品の一貫性と精度を確保します
インサート射出成形の応用例
インサート射出成形は、強度と耐久性に優れた高品質で複雑な部品を製造するために多くの業界で使用されている汎用性の高い製造プロセスです。 ここでは、インサート射出成形の用途とさまざまな業界におけるその利点を詳しく見ていきます。
- 自動車産業:自動車産業は、インサート射出成形の最も重要なユーザーの XNUMX つです。 エアバッグハウジング、シートベルト、エンジン部品など、さまざまな部品の製造に使用されています。 このプロセスにより、自動車の過酷な使用条件に耐えることができる部品の精密かつ正確な成形が可能になります。
- エレクトロニクス産業:エレクトロニクス業界も、スマートフォン、ラップトップ、その他の電子機器などの部品を製造するためにインサート射出成形に大きく依存しています。 このプロセスは、電子部品のコネクタ、スイッチ、ハウジングなどの要素の作成に使用されます。 このプロセスは非常に効率的であり、大量の部品を迅速かつコスト効率よく生産できます。
- 医療産業: 医療業界もインサート射出成形から大きな恩恵を受けています。 このプロセスは、外科器具、薬物送達デバイス、医療インプラントなどのさまざまなコンポーネントの製造に使用されます。 この方法により、医療用途の厳しさに耐えることができる要素の精密な成形が可能になり、大量生産が可能になります。
- 航空宇宙産業: 航空宇宙産業もインサート射出成形を広く使用する産業です。 このプロセスは、エアダクト、ブラケット、航空機部品のハウジングなどの部品の製造に応用されています。 このプロセスにより、航空宇宙用途での高い応力や極端な温度に耐えることができる高強度コンポーネントの作成が可能になります。
- 消費財業界: 消費財業界では、おもちゃ、家電製品、スポーツ用品などの幅広い製品を製造するためにインサート射出成形が広く使用されています。 このプロセスにより、高品質で耐久性があり、軽量で見た目にも美しいコンポーネントの作成が可能になります。
これらの業界に加えて、インサート射出成形は次のような他の多くの用途でも使用されています。
- 包装業界: キャップ、クロージャー、その他の包装コンポーネントの製造用
- 建設業: パイプ、継手、その他の建設コンポーネントの製造用
- 軍事産業: 軍用車両および装備品の部品の製造用
自動車産業のアプリケーション
自動車業界は、プラスチック射出成形が複雑な車両コンポーネントを製造するための費用対効果が高く効率的な方法であるため、プラスチック射出成形を最も重要に使用している国の XNUMX つです。 ここでは、自動車業界におけるプラスチック射出成形のさまざまな用途を詳しく見ていきます。
- 内装部品: 車両の内部は、車両全体の美しさと機能に不可欠ないくつかのプラスチック部品で構成されています。 これらのコンポーネントには、ダッシュボード、ドア パネル、エアコンの通気口、ステアリング ホイールのコンポーネントが含まれます。 射出成形により、高精度を維持しながら、これらの部品を迅速かつコスト効率よく大量生産できます。
- 外装コンポーネント: 車両の外装は、バンパー カバー、ヘッドランプ アセンブリ、テールライト アセンブリなどのいくつかのプラスチック部品で構成されています。 射出成形によりこれらのコンポーネントは高レベルの精度で製造され、自動車業界で要求される厳格な安全性と品質基準を確実に満たします。
- エンジンコンポーネント: 射出成形は、吸気マニホールド、エンジン カバー、オイル フィルターなどのいくつかのエンジン部品の製造にも使用されます。 これらのコンポーネントは厳格な公差と基準に従って製造する必要があり、射出成形によりこれらの要件を満たす高品質の成分の生産が可能になります。
- 電気部品: コネクタ、スイッチ、センサー ハウジングなどの車両の電気部品も射出成形を使用して製造されます。 これらのコンポーネントは耐久性があり、過酷な動作条件に耐える必要があり、射出成形により、これらの条件に耐えられる高品質の材料を製造できます。
- HVAC コンポーネント:射出成形では、空調ダクトや通気口など、車両の HVAC システムに使用されるいくつかのコンポーネントが製造されます。 車内の適切な空気の流れと換気を確保するには、これらのコンポーネントを正確な公差に従って製造する必要があります。
これらの用途に加えて、メーカーは射出成形を使用して、燃料、ブレーキ、サスペンション システムなどの他のいくつかの自動車部品を製造しています。
自動車業界で射出成形を使用することの利点は次のとおりです。
- 高効率:射出成形により、高品質のコンポーネントを迅速に大量生産できるため、生産時間とコストが削減されます。
- 精度:射出成形により、高精度と一貫性を備えたコンポーネントの作成が可能になり、厳格な品質基準を確実に満たすことができます。
- カスタマイズ: 射出成形により複雑な形状や設計を製造できるため、メーカーは特定の設計要件を満たすようにコンポーネントをカスタマイズできます。
医療産業への応用
医療産業は精度と信頼性が最も重要視される分野であり、プラスチック射出成形は医療部品を製造するための理想的な製造プロセスとなっています。 ここでは、医療業界におけるプラスチック射出成形のさまざまな用途を詳しく見ていきます。
- 手術器具: 射出成形では、鉗子、クランプ、メスなどの多くの手術器具が製造されます。 製造業者は、最高の精度と精度を確保するために、これらのコンポーネントを厳格な公差と基準に従って製造する必要があります。
- 医療機器:メーカーは射出成形を使用して、カテーテルや呼吸器部品などの医療機器を製造することもできます。 患者の安全性と信頼性を保証するために、メーカーはこれらのコンポーネントを厳格な基準に従って製造する必要があります。
- 診断コンポーネント: メーカーは射出成形を使用して、ピペット、シリンジ、試験管などの診断機器に使用されるいくつかのコンポーネントを製造しています。 正確なテスト結果を保証するには、これらのコンポーネントを正確な公差に従って製造する必要があります。
- 包装: 射出成形では、滅菌トレイ、容器、包装部品などの医療製品の包装を製造します。 これらのコンポーネントは、医療製品の無菌性と安全性を確保するために、厳格な基準に従って製造される必要があります。
- 歯科用コンポーネント: 射出成形では、マウスガード、トレイ、歯科矯正片などのいくつかの歯科コンポーネントが製造されます。 これらのコンポーネントは、患者への適切なフィット感と快適性を確保するために、正確な公差に従って製造される必要があります。
これらの用途に加えて、メーカーは射出成形を使用して、補綴物、補聴器、実験装置などの他のいくつかの医療部品を製造しています。
医療業界で射出成形を使用することの利点は次のとおりです。
- 高精度:射出成形により、高レベルの精度と一貫性を備えたコンポーネントの製造が可能になり、厳格な品質基準を確実に満たすことができます。
- カスタマイズ:射出成形により複雑な形状や設計を製造できるため、メーカーは特定の設計要件を満たすようにコンポーネントをカスタマイズできます。
- 費用対効果の高い 射出成形は、高品質のコンポーネントを大量に生産する費用対効果の高い製造プロセスであり、生産時間とコストを削減します。
電子産業への応用
エレクトロニクス産業は、正確かつ効率的な製造プロセスに大きく依存する分野です。 プラスチック射出成形は、その精度、多用途性、および速度の点で、電子部品を製造するのに理想的なプロセスです。 ここでは、電子業界におけるプラスチック射出成形のさまざまな用途を詳しく見ていきます。
- コネクタ: 射出成形では、USB コネクタ、HDMI コネクタ、オーディオ ジャックなど、電子産業で使用される幅広いコネクタが製造されます。 これらのコンポーネントは、適切な機能と互換性を確保するために、正確な公差に従って製造される必要があります。
- ハウジングとエンクロージャ: 射出成形では、携帯電話、ラップトップ、その他の家庭用電化製品などの電子機器のハウジングとエンクロージャを製造します。 メーカーは、適切なフィット感と機能を確保するために、これらのコンポーネントを正確な仕様に従って製造する必要があります。
- スイッチ: 射出成形では、ロッカー スイッチ、押しボタン スイッチ、スライド スイッチなど、電子機器に使用されるさまざまな種類のコントロールが製造されます。 信頼性の高い機能を確保するには、これらのコンポーネントを正確な公差に従って製造する必要があります。
- LED コンポーネント:射出成形では、レンズ、反射板、拡散板など、LED 照明に使用されるいくつかの部品が製造されます。 メーカーは、適切な配光と効率を確保するために、これらのコンポーネントを正確な仕様に従って製造する必要があります。
- 電源コンポーネント: 射出成形では、ソケット、プラグ、ケーブル コネクタなど、電源ユニットに使用されるいくつかのコンポーネントが製造されます。 これらのコンポーネントは、安全で信頼性の高い動作を保証するために、正確な公差に従って製造される必要があります。
これらの用途に加えて、製造業者は射出成形を使用して、キーボード、コンピュータ マウス、リモコンなどの他のいくつかの電子部品を製造します。
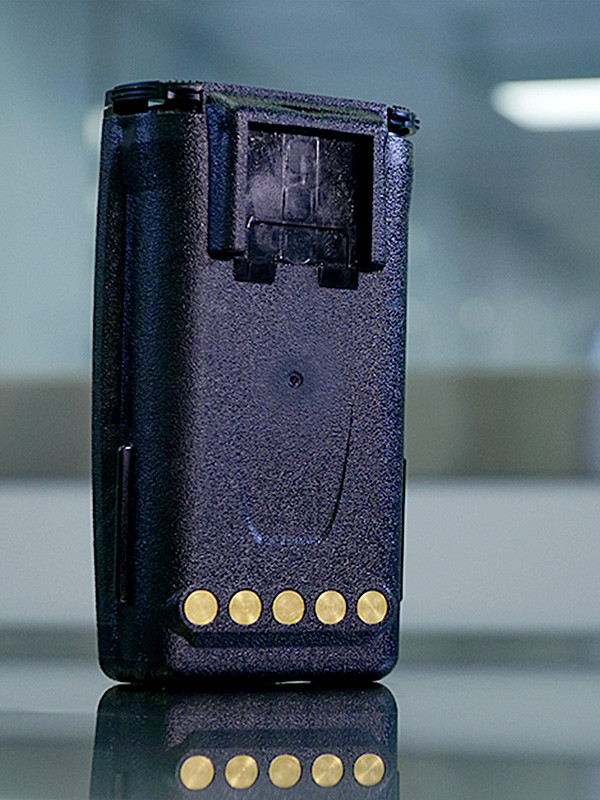
エレクトロニクス業界で射出成形を使用することの利点は次のとおりです。
- 高精度: 射出成形により、高レベルの精度と一貫性を備えたコンポーネントの製造が可能になり、厳格な品質基準を確実に満たすことができます。
- カスタマイズ: 射出成形により複雑な形状や設計を製造できるため、メーカーは特定の設計要件を満たすようにコンポーネントをカスタマイズできます。
- その2:シャフトスピード(回転数):射出成形は高速かつ効率的な製造プロセスであり、高品質のコンポーネントを大量に生産できるため、生産時間とコストが削減されます。
航空宇宙産業のアプリケーション
航空宇宙産業は、すべてのコンポーネントに最高レベルの精度、精度、耐久性が必要な分野です。 航空宇宙産業におけるプラスチック射出成形は、複雑な形状を生成し、重量を軽減し、構造の完全性を高めることができるため、ますます一般的になってきています。 ここでは、航空宇宙産業におけるプラスチック射出成形のさまざまな用途を詳しく見ていきます。
- 内装部品: 射出成形では、シートバック、トレイ テーブル、頭上のコンパートメントなど、航空機のさまざまな内装部品が製造されます。 これらのコンポーネントは軽量で耐久性があり、高い応力や摩耗に耐えることができなければなりません。
- 構造コンポーネント: 射出成形では、翼端、フェアリング、胴体部分などの航空機の構造部品が製造されます。 飛行機の安全性と効率性を確保するには、これらのコンポーネントは軽量で、強度があり、耐久性がなければなりません。
- エンジンコンポーネント:射出成形では、タービンブレード、燃料ノズル、ハウジングなど、航空機エンジン用のいくつかの部品が製造されます。 これらのコンポーネントは、高温、圧力、応力に耐えられるよう、正確な仕様に従って製造する必要があります。
- 電気部品: 射出成形では、コネクタ、スイッチ、ワイヤー ハーネスなどの航空機用の電気部品が製造されます。 適切な機能と信頼性を確保するには、これらのコンポーネントを正確な公差に従って製造する必要があります。
- 計装コンポーネント:射出成形では、コントロール パネルや計器ハウジングなどの航空機用の計器コンポーネントが製造されます。 これらのコンポーネントは耐久性があり、高温、圧力、振動に耐える必要があります。
これらの用途に加えて、メーカーは射出成形を使用して、ブラケット、ファスナー、ガスケットなど、航空宇宙産業向けの他のいくつかのコンポーネントを製造しています。
航空宇宙産業で射出成形を使用することの利点は次のとおりです。
- 減量: 射出成形により、航空機の重量を軽減する軽量コンポーネントの製造が可能になり、燃料消費量が削減され、効率が向上します。
- 精度:射出成形により、高精度かつ一貫性のある部品の製造が可能になり、厳格な品質基準を確実に満たすことができます。
- カスタマイズ:射出成形により複雑な形状や設計を製造できるため、メーカーは特定の設計要件を満たすようにコンポーネントをカスタマイズできます。
- 耐久性:I射出成形により、耐久性があり、高レベルの応力、温度、圧力に耐えることができる部品が製造され、航空機の安全性と信頼性が確保されます。
消費財業界のアプリケーション
消費財産業は、世界経済の最も重要な分野の XNUMX つです。 消費財とは、家庭用品、電子機器、おもちゃ、パーソナルケア製品など、個人が毎日使用する製品です。 消費財業界におけるプラスチック射出成形は、高品質の部品を正確に製造できるため、ますます人気が高まっています。 ここでは、消費財業界におけるプラスチック射出成形のさまざまな用途を詳しく見ていきます。
- 包装: 射出成形は、食品包装、飲料ボトル、化粧品容器などの消費財の包装材料の製造に広く使用されています。 射出成形では複雑な形状やデザインを製造できるため、包装材料の機能性と見た目の魅力が保証されます。
- 家庭用品: 射出成形では、キッチン用品、保存容器、掃除用品などのさまざまな家庭用品が製造されます。 これらのアイテムは耐久性があり、軽量で、毎日の使用に耐えられるものでなければなりません。
- おもちゃ: 射出成形では、アクションフィギュア、人形、ボードゲームなど、さまざまな玩具が製造されます。 これらのおもちゃは、安全性と耐久性を確保するために、正確な仕様に従って製造する必要があります。
- パーソナルケア製品: 射出成形により、歯ブラシ、カミソリ、シャンプー ボトルなどのユニークなケア製品が製造されます。 これらの製品は、見た目が美しく、機能的で、頻繁な使用に耐えられるものでなければなりません。
- エレクトロニクス: 射出成形では、ケース、ボタン、コネクタなど、電子機器用のいくつかの部品が製造されます。 これらのコンポーネントは耐久性があり、軽量であり、高温や高圧に耐える必要があります。
これらの用途に加えて、メーカーは射出成形を使用して、自動車部品、医療機器、産業機器などの消費財業界向けの他のいくつかのコンポーネントを製造しています。
消費財業界で射出成形を使用することの利点は次のとおりです。
- 費用対効果の高い射出成形では、他の製造プロセスよりも低コストで高品質のコンポーネントを製造できます。
- カスタマイズ:I射出成形では、複雑な形状や設計の要素を作成できるため、メーカーは特定の設計要件を満たすように機能をカスタマイズできます。
- 精度: 射出成形は、厳格な品質基準を満たした高精度で一貫したディテールを備えています。
- 耐久性: 射出成形により部品の耐久性が高まり、高レベルの応力、温度、圧力に耐えられるようになり、製品の安全性と信頼性が確保されます。
インサート射出成形の今後の動向
技術の進歩と消費者の需要の変化に伴い、インサート射出成形業界は常に進化しています。 メーカーは常に、効率を向上させ、コストを削減し、より高品質の製品を生産する方法を模索しています。 ここでは、インサート射出成形の今後の動向について見ていきます。
- オートメーション: 製造業界では自動化がますます普及しており、インサート射出成形も例外ではありません。 自動化システムにより、人件費が削減され、生産速度が向上し、品質管理が向上します。
- サステナビリティ: 環境への関心が高まる中、メーカーは廃棄物を削減し、持続可能性を向上させる方法を模索しています。 リサイクル材料を使用し、簡単にリサイクルまたは再利用できる製品を設計することは、メーカーがこの問題に対処する方法のほんの一例にすぎません。
- 3D印刷: インサート射出成形の一部の側面ではすでに 3D プリンティングが使用されていますが、将来的にはさらに普及する可能性があります。 プロトタイプを迅速に作成し、カスタマイズされたコンポーネントを製造できる機能は、3D プリントの利点の XNUMX つにすぎません。
- 先端材料: 研究者や製造業者は、さまざまな温度、圧力、応力に耐える新しい材料を開発しています。
- スマートマニュファクチャリング:スマート製造には、テクノロジーを使用してリアルタイムでデータを収集および分析することが含まれ、より迅速な意思決定とより効率的な生産が可能になります。 このテクノロジーにより、品質管理が向上し、ダウンタイムが削減され、生産性が向上します。
まとめ
インサート射出成形は、コンポーネントが埋め込まれた複雑な部品の作成を可能にする多用途でコスト効率の高い製造プロセスです。 従来の組み立て方法に比べて優れているため、自動車、医療、エレクトロニクス、航空宇宙、消費財などのさまざまな業界で普及しています。 インサート射出成形に関わるさまざまな技術、材料、設計上の考慮事項を理解することで、メーカーは生産プロセスを最適化し、高品質の製品を顧客に提供できます。 技術の進歩に伴い、インサート射出成形のさらに革新的な用途が期待できます。