プラスチック射出成形とは
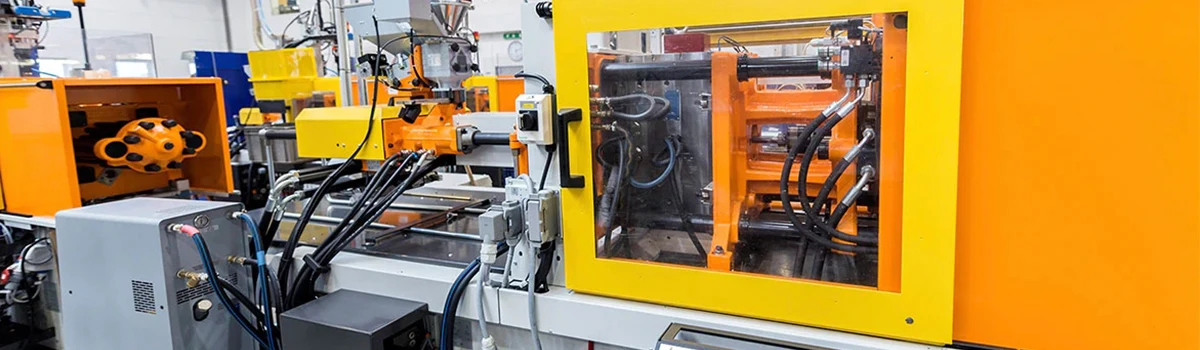
熱可塑性射出成形は、プラスチック材料を使用して大量の部品を製造する方法です。 射出成形は、その信頼性と設計オプションの柔軟性により、パッケージング、消費者および電子機器、自動車、医療などを含む多くの業界で使用されています。
射出成形は、世界で最も広く使用されている製造プロセスの XNUMX つです。 熱可塑性プラスチックは、加熱すると軟化して流動し、冷却すると固化するポリマーです。
アプリケーション
射出成形は、プラスチック部品を製造する最も一般的な最新の方法です。 同じオブジェクトを大量に生産するのに最適です。 射出成形は、ワイヤー スプール、包装、ボトル キャップ、自動車部品およびコンポーネント、ゲーム機、ポケットコーム、楽器、椅子および小さなテーブル、保存容器、機械部品、その他多くのプラスチック製品を含む、多くのものの製造に使用されます。
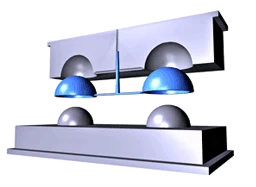
金型設計
製品が CAD パッケージなどのソフトウェアで設計された後、金属 (通常はスチールまたはアルミニウム) から金型が作成され、精密機械加工されて目的の部品の特徴が形成されます。 金型は、射出成形金型 (A プレート) とエジェクター金型 (B プレート) の XNUMX つの主要なコンポーネントで構成されます。 プラスチック樹脂はスプルーまたはゲートを通って金型に入り、A プレートと B プレートの面に機械加工されたチャネルまたはランナーを通って金型キャビティに流れ込みます。
射出成形プロセス
熱可塑性プラスチックを成形する場合、通常、ペレット化された原材料がホッパーを通って往復スクリューで加熱されたバレルに供給されます。 スクリューは原料を逆止弁を通って前方に送り、原料はスクリューの前面でショットと呼ばれる容積に集まります。
ショットとは、金型のスプルー、ランナー、キャビティを満たすのに必要な樹脂の量です。 十分な材料が集まると、材料は高速かつ高圧で部品成形キャビティに押し込まれます。
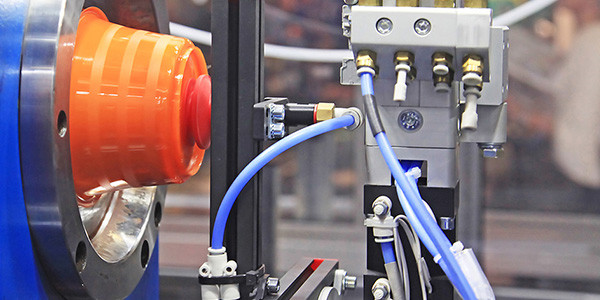
射出成形はどのように機能しますか?
スプルー、ランナー、ゲートなどを含む金型にプラスチックが充填されると、金型は設定温度に保たれ、材料が部品形状に均一に固化します。 冷却中は保持圧力が維持され、バレルへの逆流を止め、収縮効果を軽減します。 この時点で、次のサイクル (またはショット) に備えて、さらに多くのプラスチック顆粒がホッパーに追加されます。 冷却されると、プラテンが開き、完成した部品が排出され、スクリューがもう一度引き戻されて、材料がバレルに入り、プロセスが再び開始されます。
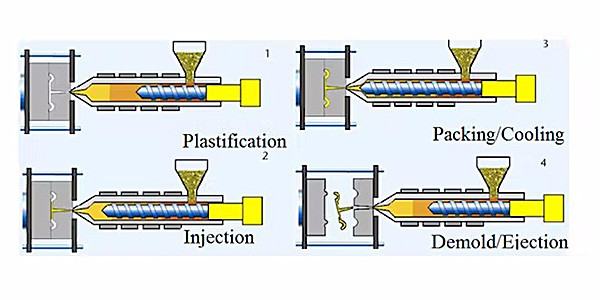
射出成形サイクルは、金型を閉じ、プラスチック顆粒を供給/加熱し、金型内に加圧し、冷却して固体部品にし、部品を取り出し、再び金型を閉じるという連続プロセスによって機能します。 このシステムによりプラスチック部品の迅速な生産が可能になり、設計、サイズ、材料に応じて 10,000 営業日で XNUMX 個以上のプラスチック部品を製造できます。
射出成形サイクル
射出成形サイクルは非常に短く、通常は 2 秒から 2 分の間です。 いくつかの段階があります。
1.クランプ
材料を金型に射出する前に、金型の XNUMX つの半分がクランプ ユニットによってしっかりと閉じられます。 油圧駆動のクランプ ユニットは、金型の半分を一緒に押し、材料の射出中に金型を閉じた状態に保つのに十分な力を発揮します。
2.注射
金型が閉じられた状態で、ポリマー ショットが金型キャビティに射出されます。
3.冷却
キャビティが充填されると、保持圧力が適用され、より多くのポリマーがキャビティに入り、冷却によるプラスチックの収縮を補うことができます。 その間にスクリューが回転し、次のショットを前スクリューに送ります。 これにより、次のショットの準備時にスクリューが後退します。
4.排出
部品が十分に冷却されると、金型が開き、部品が取り出され、サイクルが再び始まります。
Advantages
1.速い生産; 2.設計の柔軟性。 3.精度; 4.人件費が低い。 5.廃棄物が少ない