プラスチック射出成形の新展開
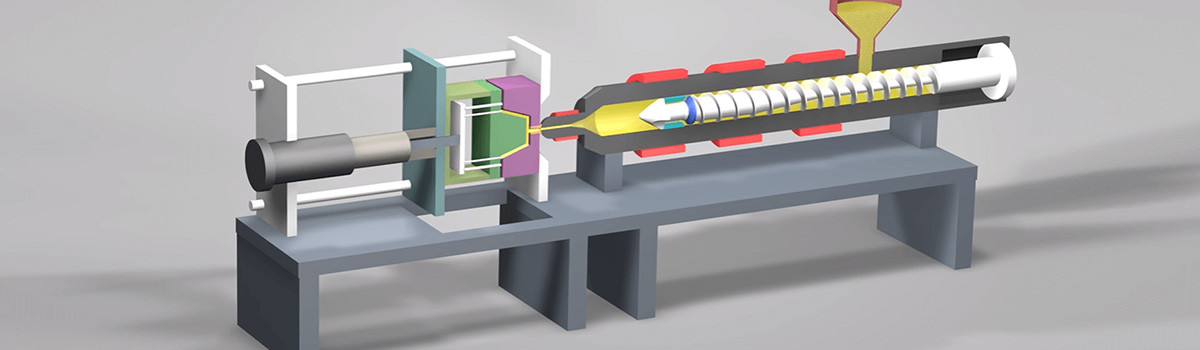
製造技術としてのプラスチック射出成形は、何十年も前から存在しています。 しかし、新しい射出成形のトレンドがこの方法を推進しており、これを選択する企業に前例のない新しい利点をもたらしています。
今後数年間の射出成形の新しいトレンドと、それらを適用することで貴社がどのようなメリットを得ることができるかをご覧ください。
プラスチック射出成形はどのように進化しましたか?
プラスチックは 1850 年代から存在していましたが、より柔軟なタイプのプラスチックが発明されたのは 1870 年代になってからです。 その結果、射出成形プロセスが開発されました。 それ以来、多くの進歩により、プラスチック射出成形の可能性がさらに広がりました。
スクリュー射出成形機の発明により、射出速度の制御が容易になり、最終製品の品質も向上しました。 このプロセスにより、混合材料の使用も可能になり、着色プラスチックや再生プラスチックの使用への扉が開かれました。
ガスアシスト スクリュー マシンは、より複雑で、より柔軟で、より強力な製品の作成も可能にしました。 この方法により、生産時間、廃棄物、および製品の重量がすべて最小限に抑えられたため、経済的なコストも削減されました。
コンピュータ支援製造のおかげで、より複雑な金型が存在するようになり、設計者はより複雑な形状を生成できるようになりました (複数のセクションを持つことも、より詳細で正確なものにすることもできます)。
ガスアシスト射出成形
この形式の射出成形では、典型的な溶融プラスチックの射出は、金型への加圧ガスの射出によって補助されます。このプロセスには一般に窒素が使用されます。 ガスは気泡を生成し、プラスチックを金型の端に向かって押します。 したがって、バブルが拡大すると、さまざまなセクションが満たされます。 プラスチック業界で使用される成形にはいくつかの形式があり、ポリマーを鋳造する際にガスが注入される位置によって区別されます。
より具体的には、ガスは機械のノズルから注入するか、一定の圧力または体積で金型のキャビティに直接注入することができます。 これらの方法の一部は特許によって保護されています。 したがって、それらを使用するには、適切なライセンス契約を締結する必要があります。
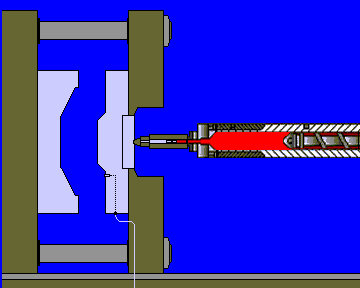
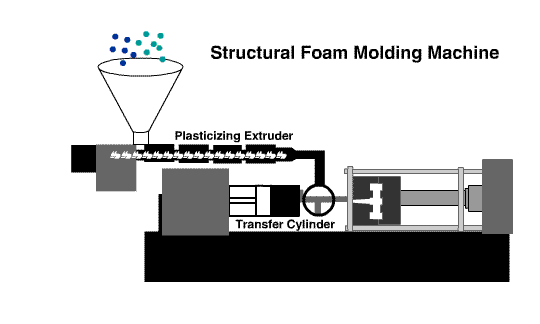
発泡射出成形
この技術は、構造部品で高い抵抗力と剛性を達成するための効果的で手頃な方法を提供します。 この利点に加えて、発泡構造部品は、優れた断熱性、優れた耐薬品性、および改善された電気的および音響的特性を備えています。 この部品には、XNUMX つの層の間にフォーム コアが含まれています。 このコアは、不活性ガスを樹脂に溶解し、金型のキャビティにガス可塑性溶液を射出するときに樹脂を膨張させることによって得られます。 発泡射出成形で製造された部品はどこにありますか? このプロセスは、部品重量を減らすための代替手段として車両パネルで使用されます。
薄肉射出成形
この場合の主な技術革新は、最終結果に関連しています。つまり、非常に薄い壁を持つセクションです。
このプロセスの主な難点は、「薄い壁」と見なされる壁の幅を決定することです。 原則として、幅が 1 mm (50/XNUMX インチ) 未満の部品が製造される場合、それらは薄肉であると見なされます。
壁の幅の縮小に伴う利点は、今日では高く評価され、求められています。
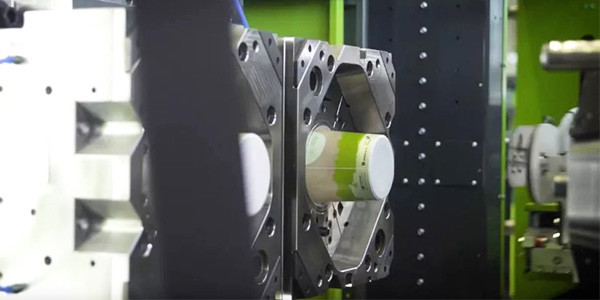
多成分射出成形
射出オーバーモールディングまたはオーバーインジェクション とも呼ばれます。このプロジェクトでは、一般にプラスチックまたは金属のコンポーネントである基材 (基板) の上に硬質または軟質のポリマーをオーバーモールドする必要があるためです。
全体として、この技術は、XNUMX つの同じ金型内に複数のコンポーネントまたは材料を射出し、XNUMX つのプロセスの一部として定義することができ、異なる色、質感、形状を持つ XNUMX つ、XNUMX つ、またはそれ以上の材料の組み合わせを可能にします。
マルチマテリアル射出成形の利点は何ですか?
マルチマテリアル射出成形により、さまざまなタイプのプラスチックで形成される複雑な部品の製造が可能になります。 このプラスチック射出成形プロセスの主な利点は、機械的、熱的、耐薬品性の高い部品が得られることです。
来年のプラスチック射出成形動向
プラスチック射出成形の持続可能性
プラスチック射出成形業界は、特にプラスチック業界がますます監視および規制されている時期に、新しい持続可能性の価値観および規制に迅速に対応しています。 したがって、新しい射出成形の傾向は次の方向を示しています。
また、安全で環境に中立な 100% リサイクル可能なプラスチック素材の使用。
製造中の二酸化炭素排出量を削減するための代替手段を検討しています。 これには、再生可能なエネルギー源の適用や、製造プロセス中のエネルギー損失の最小化に向けた取り組みが含まれる場合があります
同時に、企業は、持続可能なモデルへの移行によって、製品の機械的および物理的特性を含む製品の品質が損なわれないことを保証する必要があります。
軽量素材の需要増
軽量材料は、多くの場合、経済的コスト (輸送に関連するコストなど) の削減と、エネルギー コストの削減 (自動車部品など) につながります。 医療機器の軽量素材は、患者の結果を改善することもできます。
プラスチック射出成形のカスタム ソリューション
プラスチック射出成形におけるより費用対効果の高いオプションの検索は、カスタム ソリューションの優先順位付けにもつながりました。特定のニーズに合わせて技術部品をカスタムメイドすると、ROI が向上することに気付く企業がますます増えています。
プラスチック射出成形の自動化と新技術
AI、機械学習、および高度な分析の導入と同様に、さまざまな自動化ソフトウェア オプションが、プラスチック射出成形の可能性をさらに押し上げています。
これらのテクノロジーにより、機器のダウンタイムと誤動作を最小限に抑え、予知保全プログラムを開発し、生産サイクルを短縮できます。 同時に、新しいソフトウェアにより、企業は設計プロセス中に射出成形サイクルをシミュレートし、不規則な充填パターンなどの問題をテストできます。 これにより、生産プロセスに進む前に問題を修正できるため、時間と費用を節約できます。