少量射出成形 — 少量製造サービス
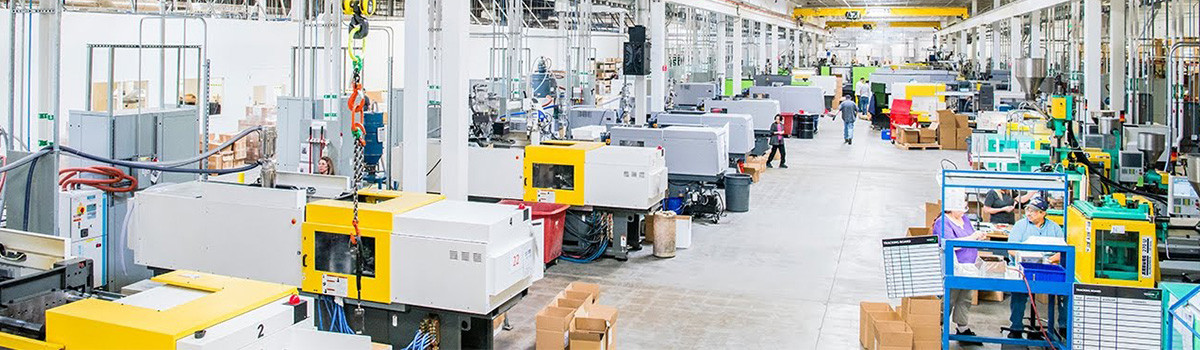
少量射出成形の活用方法(少量生産サービス)
オンデマンド製造を使用して生産コストを削減し、需要の変動を緩和します
救命医療機器を設計する場合でも、高空飛行するドローンを設計する場合でも、大量生産の鋼製工具に 100,000 万ドル以上 (多くの場合それよりも高額) を投資することは、大規模生産への移行に伴う固有の財務リスクとなります。 リスクをさらに悪化させるのは、部品の設計を繰り返したり、収益を生み出す製品を製造したりするときに、鋼製工具の準備が整うまで待機する数か月のアイドル時間です。 もっと良い方法があります。オンデマンド製造です。
オンデマンド製造(少量射出成形)とは何ですか?
DJmolding では、アルミニウム金型を使用する射出成形によるオンデマンドの少量生産サービスを提供しており、数十万の最終用途の成形部品を迅速かつ費用対効果の高い方法で生産できます。
このプロセスを製品の主要な製造方法として使用してください。 オンデマンド製造は、成形部品の試作から少量生産に移行するための優れた方法でもあります。 DJmolding は実際にはフルサービスの製造プロバイダーです。 少量生産は、部品設計を検証し、需要に応じて部品を生産する在庫オーバーヘッドを管理するのにも役立ちます。 さらに、最終的にプラスチック部品の量産に移行する必要がある場合でも、スチール製工具の資本支出に着手する前に、費用対効果の高い当社のアルミニウム製工具を橋渡しとして使用できます。 最後に、このオンデマンドのアプローチによりサプライ チェーンも最適化され、需要の変動性の管理がより適切になります。
品質にとって重要な機能を呼び出す
当社のオンデマンド製造オプションを使用すると、部品の機能にとって最も重要な寸法を部品設計で指定できます。 3D CAD モデルでこれらの重要品質 (CTQ) 機能を呼び出すことにより、注文した部品がモデルと一致していることを保証できます。 さらに、これは、次回それらの部品を注文するときに、その正確な手順に従って、CTQ 仕様に準拠した一貫した再現可能な部品を製造できることを意味します。
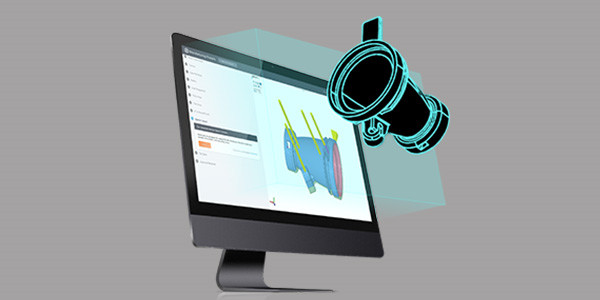
検査は、この CTQ プロセスの重要な部分です。 したがって、当社のアプリケーション エンジニアリング チームがモデルをレビューし、検査作業明細書 (ISOW) を電子メールで送信します。これにより、丸で囲んだフィーチャに公差や成形性に問題があるかどうかがわかります。 ISOW を送信したら、ご注文の製造と検査を行います。
成形プロセスの開発が完了すると、高品質の部品を製造するための一貫した再現可能なプロセスが保証され、自動三次元測定機 (CMM) を使用してツールからの最初の XNUMX つのショットを検査し、XNUMX つのショットをお客様に提供します。 -part First Article Inspection (FAI) レポートおよびプロセス能力レポート。
DJmolding の少量射出成形サービスによりサプライ チェーンの柔軟性を獲得
現在、私たち全員が世界的なパンデミックを乗り越え続けているため、サプライチェーンを考慮することが重要になっています。 オンデマンド製造アプローチは、以下によってより迅速なサプライ チェーンの構築に役立ちます。
* 最小発注数量 (MOQ) を設けず、オンデマンドで部品を調達します。
* オンデマンド調達により在庫コストと倉庫費用を削減
* バックオーダーを発生させずに需要のボラティリティの増大を管理する
* 国内および世界的な配送遅延のリスクを軽減します。
* 大型ツールの修理時のダウンタイムを最小限に抑え、在庫切れのリスクを軽減します。
DJmolding の少量生産
これは完全な量産品質の部品を提供する専門的なサービスですが、使用されるプロセスに応じて、数量は通常 10,000 個以下に制限されます。 当社の少量成形(ショートランとも呼ばれます)は監視および制御されているため、金型の設計と製造のあらゆる側面を安心して行うことができます。 このタイプの生産は、中小企業または小規模バッチ製造に最適です。
少量生産は、部品、製品、材料をサードパーティにアウトソーシングする製造業界のかなり新しい分野です。
これにより、中小企業が製品のデザインとブランディングを担当しながら、あなたの会社は生産面により集中することができます。 中小企業が他社にアウトソーシングしてコストを抑えることでビジネスを成長させようとするため、この成長傾向はあらゆる業界で広まるでしょう。
DJmoldingの少量射出成形
多くの人は「中国」と「カビ」という言葉を同じ文章で聞くと、最悪の事態を想定します。 彼らは、労働者の命を危険にさらす、標準以下の製造方法で作られた、安価で低品質の製品について考えています。
しかし、常にそうとは限りません。
中国の DJmolding は、輸出向けに高品質の製品を生産してきた長い歴史があります。 実際、世界で最も優れた製品のいくつかは中国から来ています。 そして、プラスチック射出成形に関して言えば、中国は実際に世界で最も洗練された国の一つです。
射出成形は、プラスチック部品やデバイスを製造する一般的な方法です。 DJmolding は、人件費が米国やヨーロッパよりもはるかに安いため、少量の射出成形金型を製造するのに適したメーカーです。 DJmolding の最小注文数量 (MOQ) はわずか 1,000 個で、リードタイムは 3 ~ 4 週間と短いです。 これは、独自の製品ラインを開始したいが、事前にツールや生産コストに多額の資金を投資したくない小規模企業にとって非常に役立ちます。
では、信頼できるサプライヤーと取引しているかどうかをどうやって判断すればよいのでしょうか? 詳細を見る必要があります
最小注文数量 (MOQ) – 評判の良いサプライヤーは、お客様と面談したり、お客様の製品を確認したりする前に、大量の注文を要求することはありません。 その代わりに、時間やお金を注ぎすぎる前に、あなたがプロジェクトに真剣に取り組んでいることを確認したいと考えています。
リードタイム – 最良のサプライヤーはリードタイムが短いため、製品をできるだけ早く納品できます (品質基準も満たしています)。
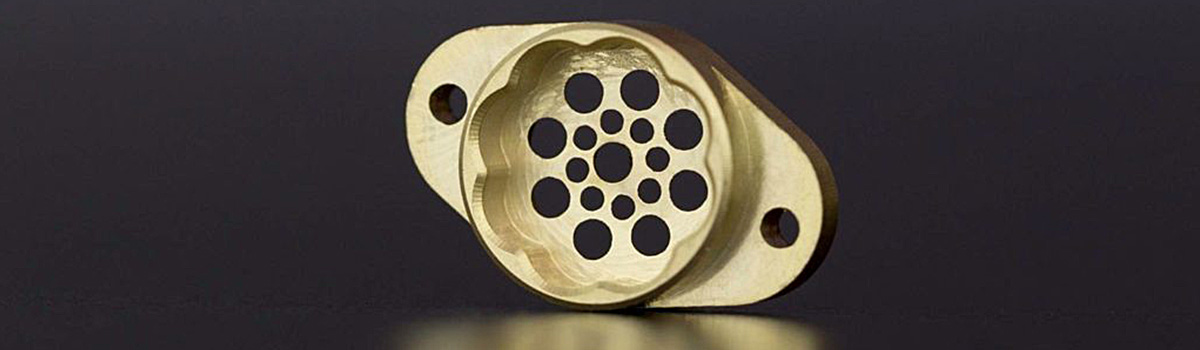
射出成形はプラスチック製品の大量生産によく使われる製造プロセスですが、プロジェクトに少数の部品が必要な場合はどうすればよいでしょうか? そこで少量射出成形の出番です。これは、大金を掛けずに少量のプラスチック部品を製造するためのコスト効率の高い方法です。 このブログ投稿では、少量射出成形の利点と用途、大量射出成形との違い、およびそれがビジネスにどのようなメリットをもたらすかについて詳しく説明します。
少量射出成形について理解する
少量射出成形は、少量のプラスチック部品の生産を可能にする製造プロセスです。 これは、小規模な生産を必要とする企業や予算が限られている企業にとって、効率的でコスト効率の高いソリューションです。
- 少量射出成形のプロセスは、金型の作成から始まります。 通常、メーカーはスチールまたはアルミニウムから金型を作成し、プラスチック部品の望ましい形状を実現するように設計します。 射出成形プロセス中、メーカーは金型の XNUMX つの部分、つまりキャビティとコアを一緒に保持します。
- 射出成形が行われる前に、プラスチック材料は別のチャンバーで加熱され、溶解されます。 メーカーは、プラスチックが望ましい温度に達したら、高圧下で金型にプラスチックを注入します。 プラスチックがキャビティを満たし、金型の形状になります。
- プラスチックが冷えて固まった後、メーカーは金型を開け、完成した部品を取り出します。 少量射出成形のサイクルタイムは比較的短く、他の製造プロセスよりも迅速な生産が可能です。
- 少量の射出成形にはいくつかの利点があります。 まず、複雑で入り組んだ部品を高い精度と再現性で製造できるようになります。 自動車、電子機器、医療機器などの複雑なコンポーネントを必要とする業界では、このオプションを選択すると有益です。
- さらに、少量射出成形により、従来の大量生産方法と比較してコストを削減できます。 ツールへの初期投資が低いため、中小企業や新興企業にとっても利用しやすくなります。 また、工具のリードタイムが短縮されるため、市場投入までの時間が短縮されます。
- 少量射出成形のもう XNUMX つの利点は、その柔軟性です。 大幅な追加コストを発生させることなく、設計の変更や反復が可能になります。 そのため、初期段階で予想される設計変更は、製品開発とプロトタイピングに大きな利益をもたらします。
- その利点にもかかわらず、少量の射出成形にはいくつかの制限があります。 名前が示すように、大量生産には適していません。 工具やセットアップのコストが高いため、部品あたりのコストは大量生産方法よりも高くなる可能性があります。 したがって、小規模から中規模の生産作業に適しています。
- 少量の射出成形では、材料の選択も考慮事項となります。 大量生産プロセスに比べて、利用できる材料の選択肢は限られています。 ただし、ABS、ポリカーボネート、ナイロン、ポリプロピレンなどの多くの熱可塑性材料は引き続き使用できます。
- 少量生産には、経験と知識のある射出成形メーカーと協力することが不可欠です。 材料の選択、金型設計、プロセスの最適化をガイドして、最良の結果を確実に得ることができます。
少量射出成形の利点
少量射出成形には、小規模から中規模の生産ニーズがある企業にいくつかの利点があります。 この製造プロセスの主な利点には次のようなものがあります。
費用対効果の高い生産
- 従来の大量生産方法と比較して、工具への初期投資が少なくて済みます。中小企業や新興企業でも利用可能です。
- 工具のリードタイムが短縮されるため、市場投入までの時間が短縮され、全体の生産コストが削減されます。
複雑かつ精密な部品
- このプロセスにより、複雑で入り組んだ部品を高い精度と再現性で製造できます。 複雑なコンポーネントを必要とする自動車、エレクトロニクス、医療機器などの業界に最適です。
- このプロセスにより、厳しい公差が可能になり、デザインに細かいディテールを組み込むことができます。
設計の柔軟性
- このプロセスにより、大幅な追加コストを発生させることなく、設計の変更や反復が容易になります。
- 初期段階で設計の調整や改良が標準となる製品開発やプロトタイピングに特に有益です。
材料の多様性
- このプロセスでは、ABS、ポリカーボネート、ナイロン、ポリプロピレンなどのさまざまな熱可塑性材料が提供されます。
- 最終製品の特定の要件と望ましい特性を満たします。
生産サイクルの高速化
- このプロセスは比較的短いサイクルタイムを誇り、他の製造プロセスよりも高速な生産を可能にします。
- 厳しいプロジェクトの期限を守ったり、市場の需要に迅速に対応したりするのに役立ちます。
- 生産性が向上し、納期が短縮されます。
廃棄物と環境への影響の削減
- このプロセスでは、必要な量のプラスチックのみを使用することで、材料の無駄を最小限に抑えます。
- このプロセスでは、大量生産方法と比較してエネルギー消費と排出量が削減されます。
- 環境に優しい製造オプション。
品質と一貫性
- このプロセスにより、一貫した寸法と特性を備えた高品質の部品が保証されます。
- このプロセスでは、温度、圧力、冷却の変数を優れた制御できます。
- 製品のパフォーマンスと信頼性が重要な要素となる業界で信頼性を発揮します。
カスタマイズとパーソナライゼーション
- このプロセスは、製品のカスタマイズとパーソナライズの機会を提供します。
- 特定の顧客の要件に合わせた独自の部品の製造。
- このプロセスにより、製品の差別化と顧客満足度が向上します。
リスク軽減と市場テスト
- このプロセスは、新製品開発または市場テストにとってはリスクの低いオプションです。
- このプロセスでは、テスト、検証、市場フィードバック用に限られた部品が製造されます。
- 改造が必要な部品や市場の需要を満たさない部品を大量に投資するリスクを最小限に抑えます。
少量射出成形と大量射出成形の比較
射出成形という汎用性の高い製造プロセスを、さまざまな生産ニーズに合わせて適応させることができます。 射出成形の一般的な XNUMX つのバリエーションは、少量生産と大量生産です。 これら XNUMX つのアプローチを比較し、その違いを調べてみましょう。
少量射出成形
- 小規模から中規模の生産ニーズがある企業に適しています。
- コスト効率の高い生産を提供し、中小企業や新興企業も利用しやすくなります。
- このプロセスでは、大量生産に比べて工具への初期投資が少なくて済みます。
- 工具のリードタイムが短縮されるため、市場投入までの時間が短縮され、全体的な生産コストが削減されます。
- このプロセスにより、複雑で入り組んだ部品を高い精度と再現性で製造できます。
- 設計の柔軟性を提供し、大幅な追加コストをかけずに設計の変更や反復を容易に行うことができます。
- 材料の多様性をサポートし、特定の要件を満たす幅広い熱可塑性材料を提供します。
- 他の製造プロセスと比較してより速い生産サイクルを実現し、生産性の向上と納期の短縮に貢献します。
- 必要な量のプラスチックのみを使用することで材料の無駄を最小限に抑え、環境への影響を軽減します。
- 製品の性能と信頼性が重要な業界では、一貫した寸法と特性を備えた高品質の部品を確保することが重要です。
- カスタマイズおよびパーソナライゼーションのオプションを提供し、特定の顧客の要件に合わせた独自の部品の製造を可能にします。
- 新製品開発や市場テスト中のリスクを軽減し、企業が本格的な生産に着手する前に、検証とフィードバックのために限られた数量の部品を生産できるようにします。
大量射出成形
- 大規模な生産ニーズがある企業に適しています。
- 生産量が増えると、工具や金型への初期投資が増加します。
- 工具のリードタイムが長くなり、市場投入までの時間が長くなる可能性があります。
- 量が増えると固定費がより大きなユニットに分散されるため、規模の経済によりコスト上の利点が得られます。
- このプロセスにより、大型部品を短期間で効率的に生産することが可能になります。
- 需要の高い製品や市場での存在感を確立している業界に最適です。
- 少量の射出成形と比較して、提供できる材料の選択肢が狭い場合があります。
- 生産効率を最適化し、無駄を最小限に抑えるには、慎重な計画と予測が必要です。
- このプロセスは、大量生産プロセス全体を通じて一貫した品質管理と仕様の順守をサポートします。
- 設計変更には大幅な追加コストが発生する可能性があるため、設計の柔軟性は限られています。
少量射出成形の応用例
少量射出成形は、さまざまな業界で応用できる多用途の製造プロセスです。 コスト効率の高い生産、設計の柔軟性、カスタマイズ オプションを提供できるため、複数のアプリケーションに適しています。 少量射出成形の典型的な用途をいくつか見てみましょう。
自動車産業
- 自動車の内装、外装、ボンネット下の用途向けの複雑かつ精密なコンポーネントの製造。
- カスタムダッシュボードパネル、トリムピース、ノブ、スイッチの製造。
- 特定の材料特性を備えた特殊な自動車部品の試作と製造。
- 車両 HVAC システム用の通気口、ダクト、コネクタの作成。
電子および電気産業
- スマートフォン、タブレット、ラップトップなどの家庭用電化製品用の複雑なコンポーネントの製造。
- 電子機器用のコネクタ、ハウジング、エンクロージャの製造。
- キーパッド、ボタン、スイッチをさまざまなテクスチャや色でカスタマイズします。
- 産業機器用の電気コネクタおよびソケットの製造。
- 微小電気機械システム (MEMS) デバイスの試作と製造。
医療およびヘルスケア産業
- 注射器バレル、IV コネクタ、手術器具などの医療機器コンポーネントの製造。
- 医療機器・診断機器向けのカスタム部品の製作。
- 医療用インプラントおよび補綴物用の生体適合性部品の試作および製造。
- ドラッグデリバリーデバイスおよびパッケージングコンポーネントの製造。
- カスタムトレイ、歯科矯正用アライナー、サージカルガイドなどの歯科用製品の製造。
消費財
- おもちゃ、家電製品、パーソナルケア用品などの消費者向け製品のカスタマイズ。
- ブランド要素を盛り込んだユニークなパッケージデザインの制作。
- 限定版製品やニッチ市場向けの小規模生産品の製造。
- 室内装飾品用の複雑な装飾部品の製造。
- カスタマイズされた販促品や景品の作成。
産業機器
- 産業用機械・装置の特殊部品の試作・製作。
- ツーリング部品、治具、治具の製造。
- 特定の要件に合わせて産業機器部品をカスタマイズします。
- ヘビーデューティ用途向けの耐久性と高性能コンポーネントの製造。
- 機械の保護カバー、ガード、マウントの製作。
スポーツとレクリエーション
- ハンドル、グリップ、保護具などの機器部品の製造。
- 自転車、カヤック、その他スポーツ用品のカスタムパーツの製造。
- フィットネス機器に特化したコンポーネントの作成。
- アウトドアレクリエーション製品のコンポーネントの試作と製造。

少量射出成形の恩恵を受ける業界
少量射出成形は、医療機器、航空宇宙、自動車、エレクトロニクス、消費財、産業機器、プロトタイピング、特殊製品、交換部品などのいくつかの業界に大きな利点をもたらします。 この多用途な製造プロセスにより、コスト効率の高い少量生産が容易になり、カスタマイズ、イノベーション、効率的な製品開発が可能になります。
- 医療機器:少量射出成形は、正確な仕様でカスタマイズされた医療機器やコンポーネントを製造するのに最適です。 コスト効率の高い少量生産が可能となり、医療メーカーは患者の多様なニーズに応えることができます。
- 航空宇宙:航空宇宙産業では、高精度と厳しい品質基準を備えた複雑な部品が必要です。 少量の射出成形により、軽量で耐久性のあるコンポーネントの製造が可能になり、航空機の重量が軽減され、燃料効率が向上します。
- オートモーティブ・ソリューション :少量射出成形は、特殊な自動車部品のプロトタイピングと生産に価値があります。 これにより、メーカーは設計を迅速に反復して改良し、本格的な生産前に最適なパフォーマンスと機能を確保できます。
- エレクトロニクス:エレクトロニクス業界は、コネクタやケーシングなどの複雑な部品を製造するための少量射出成形の恩恵を受けています。 このプロセスにより、小バッチの効率的な生産が可能になり、エレクトロニクス製造のペースの速い性質に対応できます。
- 消費財: 少量の射出成形は、独自のデザインと機能を備えたカスタマイズされた消費者製品を作成するのに有利です。 これにより、少量の迅速な生産が可能になり、市場テストや消費者の好みに合わせたカスタマイズが容易になります。
- 産業機器: 少量の射出成形では、ギア、バルブ、ハウジングなどの産業機器コンポーネントが製造されます。 このプロセスにより、少量のコスト効率の高い製造が可能になり、産業用途の特定の要件を満たします。
- プロトタイピングと製品開発: 企業は、試作段階や製品開発段階で少量射出成形を広く使用しています。 これにより、機能的なプロトタイプを作成するためのコスト効率の高い方法が提供され、量産前に設計の検証、テスト、改良が可能になります。
- 特産品: 多くのニッチ産業では、大量生産されない特殊な部品が必要です。 少量射出成形は、これらのユニークなコンポーネントを効率的に作成し、特定の市場の需要に応えるための実行可能なソリューションを提供します。
- 交換部品:少量射出成形は、さまざまな業界の交換部品の製造に有益です。 これにより、少量のオンデマンド生産が可能になり、大量の在庫を必要とせずに重要なコンポーネントの安定した供給が確保されます。
少量射出成形で使用される材料の種類
少量射出成形ではさまざまな材料を利用して、多様な製造ニーズに対応します。
- 熱可塑性プラスチック: 熱可塑性プラスチックは、少量の射出成形で最も一般的に使用される材料です。 性質を大きく変えることなく、何度でも溶解、冷却、再溶解することができます。 熱可塑性プラスチックの例には、ポリエチレン (PE)、ポリプロピレン (PP)、ポリスチレン (PS)、およびポリカーボネート (PC) が含まれます。
- エラストマー:ゴム状材料としても知られるエラストマーは、少量の射出成形で柔軟なコンポーネントを製造します。 弾力性、復元力、耐衝撃性に優れています。 標準的なエラストマーには、シリコーン、ポリウレタン (PU)、および熱可塑性エラストマー (TPE) が含まれます。
- エンジニアリングプラスチック:エンジニアリング プラスチックは、優れた機械的、熱的、化学的特性を示す高性能材料です。 強くて耐久性のある部品として業界で広く使用されています。 少量の射出成形で一般的に使用されるエンジニアリング プラスチックには、アクリロニトリル ブタジエン スチレン (ABS)、ナイロン (PA)、ポリエチレン テレフタレート (PET)、およびポリオキシメチレン (POM) があります。
- 生分解性で持続可能な素材: 持続可能性がますます重視されるようになり、少量の射出成形でも生分解性で持続可能な材料が使用されます。 これらの材料は再生可能資源から得ることができ、環境上の利点をもたらします。 例には、ポリ乳酸 (PLA)、バイオベースのポリエチレン (PE)、およびバイオベースのポリプロピレン (PP) が含まれます。
- 金属およびセラミック粉末: プラスチックに加えて、少量の射出成形では金属およびセラミック粉末を組み込んで金属またはセラミック部品を製造できます。 金属射出成形 (MIM) またはセラミック射出成形 (CIM) として知られるこのプロセスには、粉末をバインダーと混合し、金型に射出することが含まれます。 その後、部品は脱バインダと焼結を経て、最終的な特性が得られます。
- 複合材料:複合材料は、さまざまな材料を組み合わせて、望ましい特性を実現します。 混合材料により、少量の射出成形における強度、剛性、または耐熱性を向上させることができます。 例としては、炭素繊維強化ポリマー (CFRP)、ガラス繊維強化ポリマー (GFRP)、鉱物充填ポリマーなどがあります。
- 液状シリコーンゴム (LSR): LSR は、柔軟性、耐熱性、生体適合性を備えた部品を製造するための特殊な材料です。 医療産業や自動車産業など、優れたシール性が要求される用途に特に適しています。
少量射出成形のしくみ
少量射出成形は、さまざまな業界に利益をもたらす製造プロセスであり、少量のカスタマイズされた部品の生産を可能にします。 これには、金型の設計と製造、および材料の準備が含まれます。その後、材料を溶かして高圧下で金型キャビティに注入します。
- 金型設計:このプロセスは、所望の部品形状に対応する金型を設計および製造することから始まります。 金型はキャビティとコアの XNUMX つの部分で構成されており、これらを組み合わせると最終部品の形状が形成されます。
- 材料の準備: 選択された材料は通常ペレットの形でホッパーに入れられ、射出成形機に供給されます。 次にシェルは加熱され、溶融状態まで溶解されます。
- 注入:溶融した材料は、往復スクリューまたはプランジャーを使用して高圧下で金型キャビティに射出されます。 この圧力により、材料が金型の複雑な細部すべてに確実に充填され、固化中にその形状が維持されます。
- 冷却と固化:金型キャビティを充填した後、溶融した材料は金型内で冷却されて固化します。 金型に組み込まれた冷却チャネルが熱を放散し、凝固プロセスを加速します。
- 型開きと取り出し:材料が十分に固まると型が開き、XNUMX つの半分が分離されます。 エジェクター ピンまたはプレートは、成形品を金型キャビティから押し出し、収集ビンまたはコンベア ベルト上に押し込みます。
- 仕上げ:取り出された部品は、望ましい表面仕上げと寸法精度を達成するためにさまざまなプロセスを受けることがあります。 これらの作業には、余分な材料のトリミング、バリやバリの除去、機械加工や塗装などの二次作業の実行が含まれる場合があります。
- プロセスを繰り返す:金型が閉じられ、このサイクルが繰り返されて次の部品が製造されます。 少量の射出成形では、金型とプロセスを複数回繰り返して調整できるため、生産と設計の改善を柔軟に行うことができます。
- 品質管理:製造された部品が要求仕様を確実に満たすように、プロセス全体にわたって品質管理措置が実施されます。 これらの活動には、定期的な検査、寸法測定、機能テストが含まれる場合があります。
- スケーラビリティ:少量射出成形は主に少量生産に重点を置いていますが、大規模生産への足がかりとしても機能します。企業は、需要が増加した場合、より大型の機械や複数の金型を採用することで、より大量生産に向けてプロセスを最適化できます。
少量射出成形機の種類
さまざまな少量生産射出成形機が利用可能で、さまざまな製造ニーズに応えるように設計されています。 使用する材料、部品の製造の複雑さ、必要な精度と効率などの要因によって、機械の選択が決まります。 望ましい結果を達成し、生産における費用対効果を確保するには、正しいタイプの機械を選択することが重要です。
- 油圧機械:油圧式少量射出成形機は、油圧ポンプを利用して、材料を金型キャビティに射出するのに必要な圧力を生成します。 高い精度と再現性で部品を製造でき、さまざまな材質に対応できます。
- 電気機械:電気少量射出成形機は、油圧ポンプの代わりに電気モーターを使用して射出プロセスを駆動します。 油圧機械よりも優れたエネルギー効率、メンテナンスの軽減、静かな動作を実現します。
- ハイブリッドマシン:ハイブリッド少量射出成形機は、油圧装置と電気装置の両方の利点を組み合わせています。 油圧駆動と電気駆動を組み合わせて、精度、エネルギー効率を向上させ、騒音レベルを低減します。
- 縦型マシン:縦型少量射出成形機は、重力を利用して材料を金型キャビティに供給し、金型は垂直に取り付けられます。 複雑な形状の部品の製造に最適で、製造施設の床面積を節約できます。
- マイクロ成形機:マイクロモールディング少量射出成形機は、小さな寸法と高精度の部品を製造するために特別に設計されています。 彼らは、マイクロインジェクションユニットやマイクロモールドキャビティなどの特殊な装置を使用して、望ましい結果を達成します。
- マルチショットマシン:マルチショット少量射出成形機は、複数の射出ユニットを利用して、さまざまな材料や色の部品を製造します。 この機能により、さまざまなテクスチャや仕上げを備えた複雑なパーツを作成できます。
- クリーンルームマシン:設計者は、医療または医薬品の製造施設などの無菌環境で使用するクリーンルームの少量射出成形機を作成します。 メーカーは、掃除や消毒が簡単な素材で製品を製造し、汚染を最小限に抑える機能を組み込んでいます。
少量射出成形に影響を与える要因
少量射出成形の結果と効率には、いくつかの要因が影響します。 これらの要素を考慮し、プロセスの各側面を最適化することで、少量の射出成形生産を確実に成功させることができます。
- 設計上の考慮事項:部品の設計は、少量の射出成形において重要な役割を果たします。 壁の厚さ、抜き勾配、アンダーカットの存在などの要因は、部品の成形性と全体の品質に影響を与えます。 適切な形状を備えた適切に設計されたフィーチャーは、より良い結果を達成するのに役立ちます。
- 材料の選択:少量の射出成形では材料の選択が重要です。 材料が異なれば、メルトフロー特性、収縮率、温度感受性などの特性も異なります。 成形を成功させるには、機能要件と望ましい美観を満たした適切な材料が不可欠です。
- 金型の設計と構築:金型の設計と構造は、少量射出成形の品質と実現可能性に直接影響します。 部品の適切な充填、冷却、取り出しを確実に行うには、金型材料、冷却チャネル、通気、ゲート システムを慎重に検討する必要があります。
- プロセスパラメータ:少量の射出成形では、射出速度、温度、圧力、冷却時間などのいくつかのプロセス パラメーターを最適化する必要があります。 これらのパラメータの適切なバランスを見つけることは、部品の最適な品質を達成し、欠陥を最小限に抑え、一貫した生産を確保するために非常に重要です。
- 品質管理:少量射出成形プロセス全体にわたって品質管理対策を実施することが不可欠です。 定期的な検査、寸法チェック、機能テストにより、問題や欠陥を早期に特定して対処し、製造された部品が必要な仕様を満たしていることを確認します。
- 工具と機器のメンテナンス:一貫した効率的な生産には、射出成形機と金型の定期的なメンテナンスとメンテナンスが必要です。 機器と金型の適切な洗浄、潤滑、検査は、故障を防止し、ダウンタイムを削減し、工具の寿命を確保するのに役立ちます。
- 生産量:メーカーが少量の射出成形を設計しても、生産量は部品あたりのコスト、リードタイム、工具オプションなどの要素に影響を与える可能性があります。 予想される生産量を理解することは、プロセスを最適化し、適切な製造戦略を選択するために不可欠です。
- コストに関する考慮事項: 少量射出成形のコストには、材料費、金型製作費、機械のセットアップと運用費、後処理費用など、さまざまな要因が関係します。 少量生産を成功させるには、コスト効率と部品の望ましい品質および機能のバランスをとることが重要です。
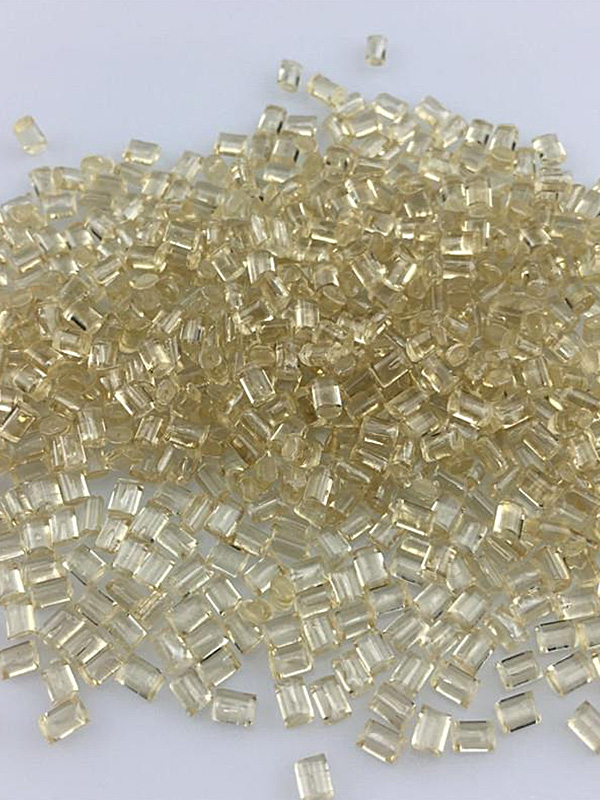
少量射出成形の設計上の考慮事項
少量射出成形用の部品を設計するには、さまざまな要素を慎重に考慮する必要があります。 これらには次のものが含まれます。
壁の厚さ
- 一貫した適切な壁厚を維持することが重要です
- 壁が厚いと冷却時間が長くなり、反りが生じる可能性があります。
- 壁が薄いと、部品の強度が低下する可能性があります。
- 均一な肉厚の設計により、適切な材料の流れと最適な部品品質が保証されます。
抜き勾配角度
- 部品の取り出しを容易にするためには、設計に抜き勾配を組み込むことが不可欠です
- 抜き勾配により、損傷を与えることなくパーツをスムーズに取り外すことができます。
- 適切な抜き勾配は固着を防止し、効率的な生産を促進します。
アンダーカットとサイドアクション
- アンダーカットとサイドアクションを最小限に抑えることをお勧めします
- アンダーカットがあると取り出しが難しくなり、複雑な金型設計や二次加工が必要になる場合があります。
- 部品の形状を簡素化し、複雑な形状を避けることで、成形性が向上し、コストが削減されます。
ゲートの配置
- 材料の流れを最適化し、欠陥を最小限に抑えるには、ゲートを適切に配置することが重要です
- ゲートの位置は、パーツの外観、強度、反りに影響します。
- ゲートを適切な位置に配置すると、部品の品質と美観が向上します。
パーティング ラインとパーティング サーフェス
- 金型の設計と組み立てには、適切なパーティング ラインとサーフェスを定義することが必要です
- きれいで明確なパーティング ラインにより、金型の構築が容易になり、欠陥のリスクが軽減されます。
リブとボス
- リブとボスを組み込むことで、構造の完全性と機能性が向上します
- リブは薄い部分に強度と剛性を与えます。
- ボスは、二次操作のための接続ポイントまたはインサートとして機能します。
表面仕上げと質感
- 希望する表面仕上げと質感を考慮することが重要です
- モールド処理またはキャビティ テクスチャーにより、滑らかなまたはテクスチャーのある表面を実現できます。
- 表面仕上げ要件を適切に選択し、伝達することで、望ましい美観と機能性が実現されます。
公差と寸法精度
- 適切な公差と寸法精度を指定することが重要です
- 少量射出成形の機能を理解することが不可欠です。
これらの設計要素を考慮することで、メーカーは少量の射出成形を最適化し、高品質の部品、効率的な生産、コスト効率を実現できます。
少量射出成形における品質管理
要求仕様を満たす高品質の部品を確実に生産するために、少量の射出成形では品質管理が重要です。 少量射出成形における効果的な品質管理のために考慮すべき重要な要素をいくつか示します。
- 検査とテスト:製造全体を通じて定期的な検査とテストを行うことで、欠陥や問題を早期に特定できます。 部品が仕様を満たしていることを確認するには、寸法検査、目視検査、機能テストを実行する必要があります。
- 材質の検証: 少量の射出成形で使用される材料の品質と一貫性を確保することは非常に重要です。 材料検証には、メルトフロー、粘度、色などの材料特性をチェックして、それらが所望の仕様と一致していることを確認することが含まれます。
- 金型のメンテナンス:一貫した高品質の生産には、金型の適切なメンテナンスと維持が不可欠です。 金型の定期的な洗浄、潤滑、検査は、欠陥を防止し、ダウンタイムを削減し、金型の寿命を延ばすのに役立ちます。
- プロセス監視:射出成形プロセスのパラメータを継続的に監視することは、品質を維持するために不可欠です。 温度、圧力、サイクルタイムなどの変数が指定の範囲内にあることを確認し、逸脱や異常を検出するために監視する必要があります。
- 統計的プロセス管理 (SPC):SPC 技術の導入は、製造プロセスの変動を監視および制御するのに役立ちます。 これには、生産プロセスからデータを収集および分析して、傾向、パターン、変動の潜在的な原因を特定し、事前の調整と改善を可能にすることが含まれます。
- 是正措置と予防措置:品質問題や不適合に対処するには、是正措置と予防措置の実施が非常に重要です。 欠陥や逸脱を特定すると、チームは直ちにそれらの修正と再発防止に努め、製造プロセスの継続的な改善を保証します。
- 文書化とトレーサビリティ:製造プロセスの適切な文書化と追跡可能性を維持することは、品質管理にとって不可欠です。 トレーサビリティと品質保証を促進するには、製造された各部品の履歴を追跡するだけでなく、プロセスパラメータ、検査結果、材料情報を記録することが不可欠です。
- サプライヤーの品質管理:サプライヤーから調達されるコンポーネントと材料の品質を保証することは不可欠です。 認定、評価、継続的なモニタリングを含む堅牢なサプライヤー品質管理プロセスを確立することで、製造において高品質の原材料のみを確実に使用することができます。
効果的な品質管理措置を導入することで、メーカーは少量の射出成形を通じて高品質で一貫性のある信頼性の高い部品を生産できます。
少量射出成形用のツーリング
少量射出成形用の工具は、金型材料の選択、設計、構造、メンテナンス、修理、インサート、テスト、保管について慎重に検討する必要があります。
金型材料の選択
少量の射出成形では、適切な金型材料を選択することが重要です。 耐久性、耐熱性、適合性などを考慮して材質を選択してください。 一般的な金型材料には、鋼合金、アルミニウム合金、複合材料などがあります。
金型設計
少量射出成形用の金型を設計するには、部品の形状、ゲート システム、冷却チャネル、排出機構などの要素を慎重に考慮する必要があります。
- 最適な部品形状により、部品の適切な充填、冷却、取り出しが容易になります。
- 適切に設計されたゲート システムにより、材料の流れが効率的になり、欠陥が最小限に抑えられます。
- 適切に設計された冷却チャネルは、サイクル時間を制御し、一貫した部品品質を保証するのに役立ちます。
- 効果的な排出機構により、金型から部品を簡単に取り外すことができます。
金型の構造
細部にまでこだわって精密に金型製作を行います。
- 熟練した工具メーカーは、機械加工、CNC フライス加工、EDM (放電加工) 技術を使用して金型コンポーネントを作成します。
- 最適な性能と部品の品質を得るには、金型コンポーネントの慎重な組み立てと位置合わせが不可欠です。
金型のメンテナンスと修理
金型の寿命と一貫した性能を確保するには、金型の定期的なメンテナンスと適時の修理が重要です。
- オペレーターは、問題を防止し、生産を最適化するために、定期的な清掃、潤滑、および検査を実施する必要があります。
- 金型コンポーネントの損傷や摩耗を迅速に修復することで、欠陥や生産の中断を回避できます。
金型インサートと交換可能なコンポーネント
金型インサートと交換可能なコンポーネントを使用すると、少量の射出成形での柔軟性とコスト効率が向上します。
- オペレータは、設計変更やその他の要件、つまり部品のバリエーションに合わせてインサートを変更または交換できます。
- 交換可能なコンポーネントにより、金型の迅速な交換が可能になり、ダウンタイムが削減され、生産効率が向上します。
金型のテストと検証
生産を開始する前に、金型の徹底的なテストと検証が不可欠です。
- 当社では、プロセスパラメータを最適化し、部品の品質を確保し、必要な調整を特定するために金型のトライアルを実施します。
- 当社では、成形プロセスを予測および最適化するために、金型流動解析とコンピューター シミュレーションを実行する場合があります。
金型の保管と保存
金型を使用しない場合の品質と性能を維持するには、適切な保管と保存方法が不可欠です。
- 金型は、温度変動、湿度、汚染物質による損傷を防ぐために、管理された環境で保管する必要があります。
- 使用しない期間であっても、定期的に点検・整備を行ってください。
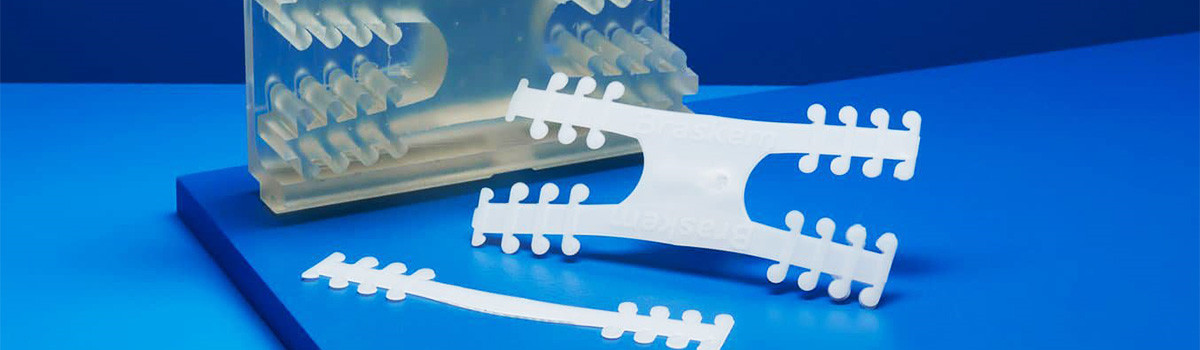
少量射出成形のためのコスト効率の高い戦略
少量射出成形に費用対効果の高い戦略を採用するには、金型設計、材料の選択、プロセスの最適化、自動化、サプライヤーとのパートナーシップを含む総合的なアプローチが必要です。 これらの戦略を実行することで、企業はコストを最小限に抑え、少量生産業務の効率を最大化しながら、高品質の結果を達成することができます。
- 効率的な金型設計:少量の射出成形用に金型を効率的に設計すると、コストを大幅に削減できます。 金型設計を簡素化し、キャビティの数を最小限に抑えることで、工具コストを削減し、生産時間を短縮できます。
- 材料選択:コスト効率の高い少量射出成形には、適切な材料を選択することが重要です。 より安価な樹脂を選択するか、必要な仕様を満たす代替材料を検討することで、品質を損なうことなく大幅なコスト削減につながる可能性があります。
- オートメーションとロボティクス:射出成形に自動化とロボット工学を導入すると、効率が向上し、人件費が削減されます。 自動化システムは、反復的なタスクを処理し、エラーを最小限に抑え、生産量を増やすことができるため、少量生産に最適です。
- プロセスの最適化:射出成形プロセスを微調整すると、コストを削減できます。 温度、圧力、サイクルタイムなどのパラメータを分析および最適化することで、材料の無駄を削減し、部品の品質を向上させ、生産性を向上させることができます。
- オンデマンド製造:オンデマンド製造を採用することで、少量の射出成形における柔軟性とコスト効率が向上します。 必要な場合にのみ部品を生産することで、企業は過剰な在庫コストを回避し、陳腐化のリスクを最小限に抑えることができます。
- 代替ツール:3D プリント金型やソフト ツールなどの代替ツール オプションを検討すると、少量生産の場合はコスト効率が高くなります。 これらの代替品は、多くの場合、従来の鋼製金型よりも初期費用が低く、リードタイムが短くなります。
- サプライヤーとのパートナーシップ:信頼できる経験豊富な射出成形サプライヤーと緊密に連携することで、コストの最適化に役立ちます。 少量生産の専門知識を持つサプライヤーは、貴重な洞察を提供し、コスト削減策を提案し、材料と工具に関して競争力のある価格を提供できます。
- 後処理の最適化:トリミング、組み立て、仕上げなどの後処理作業を合理化することで、コストを削減できます。 効率的な後処理装置と技術に投資すると、労働力の必要性が減り、二次作業の費用を最小限に抑えることができます。
少量の射出成形に 3D プリントを使用する利点
少量の射出成形に 3D プリントを利用すると、いくつかの利点があります。 これにより、迅速なプロトタイピングが可能になり、迅速な反復と設計エラーの削減が可能になります。 3D プリンティングは廃棄物の発生を最小限に抑え、本格的な生産に着手する前にテストと検証を可能にすることでリスクの軽減に役立ちます。
- ラピッドプロトタイピング: 3D プリントにはラピッド プロトタイピングという利点があり、デザイナーは製品デザインを迅速に反復して改良することができます。 このアプローチにより、企業は製品をより迅速に市場に投入し、高価な設計ミスを回避できるようになります。
- 費用対効果の高いツール:3D プリンティングは、少量の射出成形ツールのコスト効率の高い代替手段となり得ます。 3D プリントされた金型またはインサートを使用することで、企業は、特に小規模生産の場合、従来の鋼製金型にかかる初期費用を節約できます。
- 設計の柔軟性: 3D プリントを使用すると、従来の機械加工方法では実現不可能な複雑で複雑なデザインが可能になります。 この柔軟性により、特定の顧客の要件に応えて、カスタマイズされた独自の部品の製造が可能になります。
- リードタイムの短縮: 3D プリンティングを利用することで、メーカーは従来の製造方法と比較してリードタイムを大幅に短縮できます。 工具が不要で、オンデマンドで部品を生産できるため、生産プロセスが迅速化され、顧客へのより迅速な納品が可能になります。
- 素材の種類:3D プリントでは、熱可塑性プラスチック、樹脂、複合材料などの幅広い材料が提供されます。 この材料の多用途性により、特定の機能的および美的要件に応える、さまざまな特性を持つ部品の製造が可能になります。
- 廃棄物の削減:3D プリントは積層造形プロセスであり、パーツの構築に必要な材料のみを使用するため、廃棄物の発生が最小限に抑えられます。 材料コストの削減は、持続可能性への取り組みの促進にも役立ちます。
- リスクの軽減: 少量の射出成形に 3D プリンティングを使用することで、企業は、実証されていない設計や不確実な市場需要のための高価な工具への投資に伴うリスクを軽減できます。 これにより、本格的な生産に着手する前に、より少ない生産量で市場をテストすることが可能になります。
- 本番環境への橋渡し:3D プリンティングは生産への橋渡しとして機能するため、企業は高価な射出成形ツールに投資する前に、設計を迅速に検証し、部品の機能をテストできるようになります。 設計上の欠陥を早期に特定することで、長期的にはコストを節約できます。
少量射出成形の持続可能性
少量の射出成形は、環境に配慮した方法で取り組むと、持続可能な製造オプションとなります。
- 材料効率:少量射出成形では、必要な部品のみを生産することで材料効率を高め、廃棄物の発生を最小限に抑えます。 このアプローチは、過剰な材料消費に伴う環境への影響を軽減するのに役立ちます。
- エネルギー資源の保護:大量生産方法と比較して、少量射出成形では生産時間が短縮され、機械の稼働時間が短縮されるため、消費エネルギーが少なくなります。 これにより、エネルギーを節約し、温室効果ガスの排出を削減することができます。
- 廃棄物の削減:少量の射出成形により、正確な生産数量が可能になり、過剰在庫の必要性が減り、無駄が最小限に抑えられます。 企業は、生産計画を最適化し、需要を予測することで、廃棄物の発生と廃棄のコストを削減できます。
- リサイクルの機会:少量の射出成形では、多くの場合、熱可塑性プラスチックなどのリサイクル可能な材料が使用されます。 リサイクルの実践を生産プロセスに統合することで、材料を再利用し、未使用資源への依存を減らすことができます。 リサイクルの実践を生産プロセスに組み込むことで、材料の再利用が可能になり、純粋な資源への依存が軽減されます。
- 持続可能な素材の選択:企業は、少量の射出成形において持続可能で環境に優しい材料の使用を優先できます。 バイオベースのプラスチック、リサイクル材料、生分解性樹脂は、環境への影響を軽減し、循環経済を促進する実行可能な代替手段を提供します。
- ローカライズされた生産:少量の射出成形により、現地での生産が可能になり、輸送距離とそれに伴う炭素排出量が削減されます。 最終市場に近いところで生産することで、企業はサプライチェーンの環境フットプリントを最小限に抑えることができます。
- 持続可能性を考慮したデザイン:少量の射出成形により、持続可能な設計原則を組み込むことができます。 軽量構造、最適化された形状、材料の効率的な使用を備えた部品を設計することで、製造プロセスの持続可能性をさらに高めることができます。
- ライフサイクル評価:少量射出成形プロセスのライフサイクル評価を実施すると、改善と持続可能性の最適化が必要な領域を特定するのに役立ちます。 原材料の採取から耐用年数終了後の廃棄までの各段階で環境への影響を分析することで、企業は情報に基づいた意思決定を行い、持続可能な実践を実行できるようになります。
少量射出成形に関する規制と基準
少量射出成形における規制と基準を順守することは、製品の安全性、環境責任、職場の安全性、および法的要件と業界要件の遵守を確保するために不可欠です。 企業は、適用される規制や基準について常に最新の情報を入手し、それらを自社の製造プロセスに組み込む必要があります。
- 製品安全基準:少量射出成形では、製造される部品が品質と安全性の要件を満たしていることを保証するために、関連する製品安全基準に準拠する必要があります。 これらの規格は、自動車、医療、消費財などの業界によって異なる場合があります。
- 材料規制:適切な製造プロセスを確保するには、少量射出成形用の材料を選択および使用する際に特定のルールと基準に従うことが必要です。 これらの規制は、材料の組成、毒性レベル、環境への影響を管理します。 REACH (化学物質の登録、評価、認可、制限) などの法律の遵守は、安全で持続可能な材料の使用を確保するために非常に重要です。
- 環境規制:少量の射出成形作業では、環境への影響を最小限に抑えるために環境規制に準拠する必要があります。 これらの規制は、大気排出、廃水管理、廃棄物処理、エネルギー消費などの問題に対処します。 ISO 14001 (環境マネジメントシステム) などの制限を遵守することは、環境責任への取り組みを示しています。
- 労働安全衛生基準:少量生産の射出成形施設では、安全な作業環境を確保することが不可欠です。 OSHA (労働安全衛生局) 規制などの労働安全衛生基準を遵守することは、機械、材料、プロセスに関連する潜在的な危険から労働者を保護するのに役立ちます。
- 品質管理システム:ISO 9001 などの品質管理システムの導入は、少量の射出成形作業には不可欠です。 これらのシステムは、顧客の要件を満たし、適用される規制や基準に準拠した製品を一貫して提供するためのフレームワークを提供します。
- トレーサビリティとラベルの要件:少量の射出成形では、生産に使用される材料やコンポーネントの起源を追跡するためのトレーサビリティ対策が必要になる場合があります。 製品識別、バッチ番号、安全警告などのラベル要件により、明確なコミュニケーションと関連規制の遵守が保証されます。
- 知的財産に関する考慮事項:知的財産権の保護は、主に独自製品の部品を製造する場合など、少量の射出成形において非常に重要です。 企業は特許権を尊重し、製造プロセスが知的財産を侵害していないことを確認する必要があります。
- 国際貿易規制:国際貿易に従事する場合、少量の射出成形作業は、関係国固有の貿易規制および基準に準拠する必要があります。 国際貿易協定を確実に遵守するには、以下の関税規制や輸出入制限が必要となる場合があります。
適切な少量射出成形サービスプロバイダーの選択
信頼できる有能なパートナーは、貴社の少量生産の取り組みの成功に貢献します。
- 専門知識と経験:同様の規模と複雑さのプロジェクトを扱う知識と経験を備えた、少量射出成形を専門とするサービス プロバイダーを探してください。 実績のあるプロバイダーは、貴重な洞察、効率的なプロセス、高品質の結果を提供できます。
- カスタマイズ機能: プロジェクトの要件に合わせてカスタマイズされたソリューションを提供するプロバイダーの能力を評価します。 カスタマイズされたアプローチを実現するために、設計の変更、材料のオプション、生産量に柔軟に対応できるかどうかを確認してください。
- 品質保証:サービスプロバイダーが堅牢な品質保証プロセスを備えていることを確認してください。 部品の信頼性と一貫性を確保するために、当社は業界標準と認証 (ISO 9001 など) を遵守し、徹底した検査とテストを実施しています。
- 生産能力と拡張性:少量生産のニーズを満たすサービスプロバイダーの能力と拡張性を評価します。 小規模でも中規模でも、希望する生産量を処理でき、必要に応じてスケールアップできる必要があります。
- 技術と設備:プロバイダーの技術力と採用している最先端の機器を評価します。 高度な射出成形機械と技術により、プロセス効率、部品の一貫性、生産サイクルの短縮が向上します。
- 重要な専門知識:少量射出成形に適した幅広い材料を扱うサービスプロバイダーの専門知識を検討してください。 彼らはさまざまな樹脂とその特性を理解しており、プロジェクトの要件を満たす材料のオプションを提案できる必要があります。
- 付加価値サービス:後処理、組み立て、仕上げなど、プロバイダーが提供する追加サービスを評価します。 付加価値サービスは、生産プロセスを合理化し、物流の複雑さを軽減し、最初から最後まで包括的なソリューションを提供します。
- サプライチェーンマネジメント:材料やコンポーネントの調達など、プロバイダーのサプライ チェーン管理能力を評価します。 適切に管理されたサプライ チェーンにより、材料をタイムリーに入手できるようになり、生産の遅延が軽減され、コスト効率が最適化されます。
- 顧客サポートとコミュニケーション:サービスプロバイダーのカスタマーサポートとコミュニケーションレベルを考慮してください。 パートナーシップを成功させるには、正確かつ即応性のあるコミュニケーション、プロジェクトの定期的な更新、協力的なアプローチが不可欠です。
- 費用対効果:コストだけが決定要因となるべきではありませんが、プロバイダーの料金体系と全体的な費用対効果を評価することが不可欠です。 見積もりを比較し、金額に見合った価値を評価し、追加料金や料金に関する透明性を確保します。
少量射出成形における一般的な課題
少量射出成形におけるこれらの課題に対処するには、プロジェクトの要件を徹底的に理解し、サプライヤーやパートナーと緊密に連携し、プロセスを継続的に改善する必要があります。
- 工具費:少量の射出成形では生産工程が小規模になることが多く、初期の金型コストが大きな課題となります。 金型の設計と製造は、大量生産に比べて部品あたりのコストが比例して高くなる可能性があるため、慎重なコスト分析と最適化が必要になります。
- 設計の複雑さ:少量生産では、複雑で複雑な設計が必要となる場合があります。 課題は、この方法が射出成形に実行可能であること、および金型が所望の形状を正確に再現できることを保証することにあります。 最適な結果を得るには、設計の変更と反復が必要になる場合があります。
- 材料選択:少量の射出成形に適切な材料を選択するのは困難な場合があります。 コスト、機能性、耐久性、可用性を考慮する必要があります。 望ましい品質と性能を達成するには、材料特性とプロジェクト要件の間のバランスを見つけることが不可欠です。
- 部品品質の一貫性:少量生産を通じて一貫した部品品質を維持することは困難な場合があります。 プロセスパラメータ、金型の摩耗、材料特性の変動は、部品の寸法、表面仕上げ、機械的特性に影響を与える可能性があります。 変動を軽減するには、厳格な品質管理措置と継続的な監視が必要です。
- 納期:少量の射出成形では、多くの場合、大量生産よりも短いリードタイムが必要です。 生産スケジュールを最適化し、ダウンタイムを最小限に抑え、部品をタイムリーに納品するには、効率的な計画と調整が不可欠です。 厳しいスケジュールを守るには、サプライヤーやパートナーとの効果的なコミュニケーションが不可欠です。
- スケーラビリティの制限:少量の射出成形プロセスでは、拡張性に関して制限がある場合があります。 少量生産から大量生産に移行するには、工具、機器、プロセスの調整が必要になる場合があります。 スケーラビリティの課題を予測し、将来の生産ニーズに備えて計画を立てることが不可欠です。
- 部品あたりのコスト:少量の射出成形では、工具のコストをより小さな部品に分散させるため、大量生産に比べて部品あたりのコストが高くなる傾向があります。 品質基準を維持し、プロジェクト要件を満たしながら、コストを考慮するバランスをとることが重要です。
- 陳腐化のリスク:少量生産では、ニッチな市場や特定の製品バリエーションに対応することがよくあります。 部品が陳腐化するリスクや需要が変動するリスクが課題となる可能性があります。 陳腐化のリスクを最小限に抑えるには、慎重な市場分析、需要予測、在庫管理戦略が必要です。
少量射出成形の将来
自動化、積層造形、持続可能な材料とプロセス、カスタマイズ、デジタル化の進歩によって新たな機会が生まれており、少量射出成形の未来は明るいです。 これらのトレンドを受け入れ、新しい技術や手順に投資するメーカーは、急速に進化する市場で成功する有利な立場にあるでしょう。
- オートメーションとインダストリー 4.0:少量射出成形は、ロボット工学、人工知能、IoT などの自動化およびインダストリー 4.0 テクノロジーの恩恵を受ける態勢が整っています。 自動化は、人件費を最小限に抑えながら、リードタイムの短縮、品質の一貫性の向上、生産性の向上に役立ちます。
- 積層造形とハイブリッド プロセス: 少量生産の能力をさらに高めるために、積層造形や、3D プリンティングと射出成形の組み合わせなどのハイブリッド プロセスを採用できます。 これらのテクノロジーにより、プロトタイピングの迅速化、設計の自由度の向上、部品の品質の向上が可能になります。
- 持続可能な材料とプロセス:持続可能性は製造業にとってますます注目されています。 少量射出成形の未来は、持続可能な材料とプロセスの採用にあります。 生分解性および再生可能な材料は環境への影響を軽減し、環境に優しい加工技術により廃棄物とエネルギー消費を最小限に抑えることができます。
- カスタマイズとパーソナライゼーション:カスタマイズとパーソナライゼーションに対する消費者の需要により、少量射出成形の革新が促進されます。 高度なソフトウェアおよび自動化テクノロジーにより、最小限の工具コストで部品の大量カスタマイズが可能になり、ニッチ市場に新たな機会が生まれます。
- デジタル化と接続性:デジタル化と接続性は、少量射出成形の未来です。 メーカーは、データ分析とクラウドベースのプラットフォームを活用することで、生産を最適化し、品質を向上させ、サプライチェーンの透明性を高めることができます。 これらのテクノロジーにより、リモート監視や予知保全も可能になります。
まとめ
少量の射出成形は、少量生産に大きな利点をもたらします。 3D プリント技術により、迅速なプロトタイピング、コスト効率の高いツール、および設計の柔軟性が可能になります。 これにより、企業はリードタイムを短縮し、幅広い材料から選択し、無駄を最小限に抑え、リスクを軽減することができます。 これらの利点を活用することで、中小企業は製造プロセスを最適化し、顧客の要求を満たし、市場での競争力を維持できます。 少量射出成形は、今日のダイナミックな製造環境で少量生産を成功させる、効率的でコスト効率の高いソリューションを提供します。