自動車用プラスチック部品の射出成形
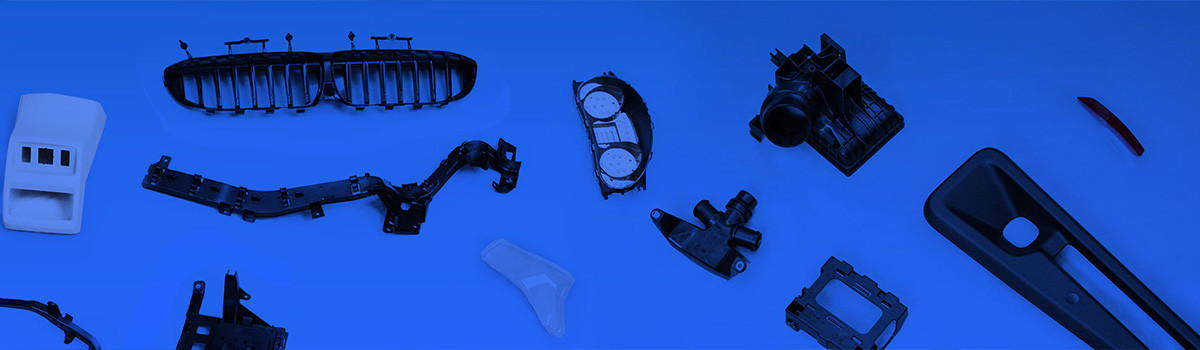
現在の自動車用プラスチック部品
高い自動車性能には、すべてを処理する部品が必要です。 プラスチックはエンジンからシャーシまで機能します。 インテリアからエクステリアまで。 今日の自動車用プラスチックは、新しい軽自動車の体積の約 50% を占めていますが、重量の 10% 未満です。
安全性
今日の材料の安全性の進歩により、数え切れないほどの命が救われています。 エアバッグ、フロントガラス、サンルーフとエネルギー吸収の革新により、車両死亡事故が減少します。 プラスチック製のフロントエンド モジュール、モジュラー シート、エネルギー吸収バンパーは、毎年人命を救っています。
プラスチック複合構造は、安全機能を維持しながら車両の軽量化に役立ちます。 車両が衝突するとき、エンジニアは構造が予測可能な方法で破壊されることを望んでいます。 自動車材料は、人間への「衝撃エネルギー」を伝達するのではなく、吸収する必要があります。 業界ではこれを「コントロールされたクラッシュ」と呼んでいます。
繊維強化ポリマー複合材料は、鋼鉄の XNUMX 倍の粉砕エネルギーを吸収します。 B ピラーは、車両のルーフとボディを接続する支柱です。 フロントドアの後部にあり、衝突時の侵入に対する主な抵抗源となります。
米国道路交通安全局は最近、B ピラーに関する研究に資金を提供しました。 この研究では、複合強化カーボンファイバー熱可塑性 B ピラーの設計に特に注目しました。 目標は、金属ベースラインと比較して、デザインの軽量化と車両衝突安全性を判断することでした。 B ピラーは 60% の重量削減を示し、側面衝突時の要件を満たしました。 計算ツールは、B ピラーの動的衝撃と衝突反応をモデル化しました。
プラスチックは歩行者との衝突時にも命を救うのに役立ちます。 ポリカーボネート混合バンパーは衝突時に乗員を保護します。 プラスチックはまた、フォード車の歩行者保護を強化するための迅速な展開を可能にします。 プラスチックで射出成形された、柔軟な歩行者保護衝突直接取り付けセンサー ブラケット。 詳細については、「クランプル ゾーン ブログ」および BMW i3 カーボンファイバー シャーシ安全コンポーネントのツアーをご覧ください。
フロントガラス、窓、サンルーフ
北米のフロントガラスは多層ユニットとして提供されます。 300 枚の薄いガラスの間にあるプラスチックの薄い層を想像してください。 この組み合わせにより、強化ガラスのみを使用するよりも薄く、軽く、強度を高めることができます。 引き裂き耐性のあるプラスチック層は、乗員の飛び出しを防止します。 実際、NHTSA は、これらの層が年間 XNUMX 人以上の死亡事故を防ぐのに役立っていると推定しています。
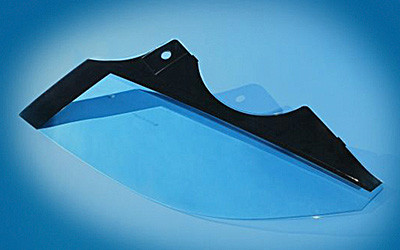
ルーフの軽量プラスチックコンポーネントにより重心が下がり、深いコーナリング時の事故操作時の転倒の可能性が軽減されます。 透明で歪みのないポリカーボネートは、耐紫外線性を備え、重量を大幅に削減できるようになりました。 屋根アセンブリ全体をポリマーベースにすることができます。
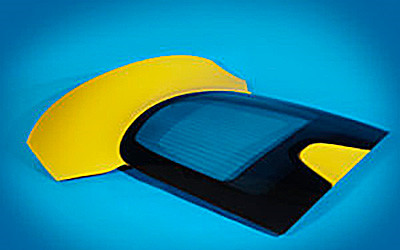
DJmolding の自動車用プラスチック部品射出成形
Djmolding は、ISO/TS 16949:2009 を取得した自動車用プラスチック射出成形会社です。自動車、航空宇宙、電子機器向けに、エンジニアリング グレードの樹脂、ガラス、タングステン、カーボン、鉄充填材料を使用した精密射出成形金型のカスタム プラスチック射出成形機、設計、製造を提供しています。海洋、医療、通信アプリケーション。
自動車の製造に使用される材料の XNUMX% は、さまざまな特性を持つプラスチック部品で構成されています。 DJmolding では、自動車会社に車両の内外装や車載機器向けのあらゆるプラスチック部品を供給しています。 当社は、プラスチック部品の射出成形のための最新技術と、ブランドがスチールの代わりに使用する部品の製造のためのエンジニアリング材料を使用しています。これらの部品は、より耐久性があり、より軽量で、リサイクルが容易です。
DJmolding は、プラスチック射出成形メーカーおよびサプライヤーとして、熱可塑性プラスチック射出成形技術を専門としています。 当社のノウハウには、ガス射出成形技術、高光沢、電子成形も含まれます。 当社の自動車産業向けの射出成形された外装および内装部品は、主に次の材料で設計されています: – ポリスチレン (PS)、 – ポリプロピレン (PP)、 – ABS、 – PC、 – PC / ABS、 – PC / PMMA。
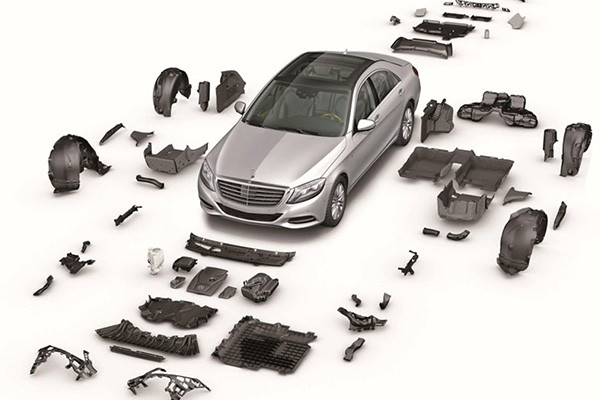
自動車の射出成形内装部品
ダイナミックな自動車産業にとって、当社はさまざまな射出成形内装部品の製造における信頼できるパートナーです。 ISO IATF 認定工場では、大手自動車メーカー向けの内装部品プロジェクトを実施しています。 当社は経験豊富な OEM、ティア 1 自動車サプライヤー、自動車内装および外装トリム部品のメーカーです。 当社のインテリア射出成形部品の製品ポートフォリオは、ダッシュボード要素 (例: グローブ コンパートメント、ドアおよびウィンドウ ピラー)、ステアリング コラム トリム、ドア ハンドル、通気口、センター コンソール、ルーフ モジュールなどのプラスチック自動車部品で構成されています。
射出成形自動車外装部品
射出成形は、幅広い自動車外装部品を製造するのに理想的な技術です。 当社の経験豊富な射出成形専門家チームは、自動車 OEM および Tier 1 クライアントと緊密に連携して、すべての技術要件を評価および定義し、非の打ち所のない車両外装部品の生産を最適化します。 当社は、マッドガード(フェンダー)、ホイールアーチ、グリル、センサーホルダー、フロアレール、トランクトリム前後カバー、バンパーおよび車外装ドアトリム、ドアパネルなどの自動車外装部品のプラスチック射出成形メーカーです。 当社の自動車用射出プラスチック部品は、世界中のさまざまな車種に使用されています。
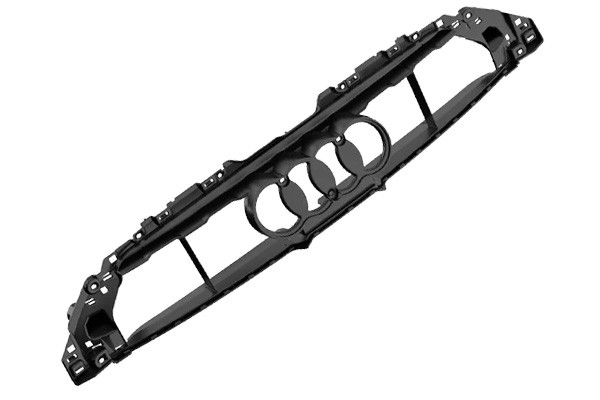
私たちの目標は、お客様に最大の価値を提供することです。 DJmolding は、プラスチック部品の製造に加えて、射出成形の設計および製造サービスも提供しています。 私たちは、お客様がすぐに市場に出荷できる形でプラスチック部品を受け取るお手伝いをします。 自動車用プラスチック部品業界向けに、アイデアから射出成形、最終製品の納品までの全プロセスをカバーします。
ご覧のとおり、DJmolding はクライアントを放っておくことはありません。 あらゆる段階で、当社は包括的なアプローチを提供することでお客様をサポートします。 最初は複雑に見えるプロセスを、大きな成果を生み出す成功した協力へと簡単に変えることができます。
自動車産業は長年にわたり目覚ましい進歩を遂げ、軽量で効率的な素材が重視されてきました。 プラスチック部品は現代の自動車製造において不可欠であり、耐久性、設計の柔軟性、費用対効果を提供します。 自動車用プラスチック部品の製造プロセスの中で、射出成形が広く使用されています。 このブログ投稿では、自動車用プラスチック部品の射出成形、その利点、用途、新たなトレンドについて探ります。 自動車プラスチック部品成形の魅力的な世界を探検しましょう!
自動車産業における射出成形について理解する
自動車産業では、射出成形を使用して、ダッシュボード、バンパー、インストルメントパネルなどのさまざまなコンポーネントを製造しています。
自動車産業における射出成形を理解する際に考慮すべき重要な側面をいくつか示します。
射出成形に使用される材料
射出成形では、次のような幅広い熱可塑性および熱硬化性材料が使用されます。
- ポリプロピレン(PP)
- ポリエチレン(PE)
- ポリ塩化ビニル(PVC)
- アクリロニトリル-ブタジエン-スチレン(ABS)
- ポリカーボネート(PC)
- ポリアミド(PA)
- ポリウレタン(PU)
それぞれの素材は、柔軟性、強度、耐久性、耐熱性、耐薬品性など、独自の特性と特性を持っています。 材料の選択は、製造される部品または製品の特定の要件によって異なります。
自動車産業における射出成形の利点
- 高い生産効率: 射出成形では大量の部品を迅速かつ効率的に生産できるため、生産時間とコストが削減されます。
- 精度と一貫性: 射出成形により、部品間のばらつきが最小限に抑えられた、正確で一貫性のある部品が製造されます。
- 設計の柔軟性: 射出成形により、複雑な形状や複雑な詳細を部品に組み込むことができるため、設計者は特定の機能的および美的要件を満たす部品を作成できます。
- 費用対効果: 射出成形は、機械加工や鋳造などの他の製造方法よりも低コストで部品を製造できます。
自動車産業における射出成形の課題
- 金型のコスト: 射出成形には金型の作成が必要であり、設計と製造に費用がかかる場合があります。
- 材料の選択: 材料が異なれば特性も異なり、追加の加工条件が必要になる場合があるため、部品や製品に適した材料を選択することは困難な場合があります。
- メンテナンスと修理: 射出成形装置は、最適なパフォーマンスを確保し、ダウンタイムを防ぐために定期的なメンテナンスと修理が必要です。
- 環境への影響: 射出成形から発生するプラスチック廃棄物の処理は、環境に悪影響を与える可能性があります。
自動車用プラスチック部品射出成形の利点
自動車プラスチック部品の射出成形は、金型とプラスチック ペレットを使用して複雑な部品を作成するプロセスです。 この方法は多くの利点があるため、自動車業界で広く使用されています。 このブログ投稿では、自動車用プラスチック部品の射出成形の利点について説明します。
費用対効果が高い: 自動車用プラスチック部品射出成形の最も重要な利点の XNUMX つは、費用対効果の高い部品製造方法であることです。 これは、このプロセスにより複雑な部品を迅速かつ効率的に大量に作成できるためです。 これにより生産コストが削減され、コストが常に懸念される自動車業界にとって理想的なソリューションとなります。
軽量: 自動車産業におけるプラスチック射出成形のもう XNUMX つの大きな利点は、プラスチック コンポーネントが軽量であることです。 これは車両の燃費を向上させるため重要であり、自動車メーカーにとって環境規制や顧客の期待を満たす上で重要な要素となります。
強度と耐久性: 射出成形により製造されるプラスチック部品は、強度と耐久性に優れています。 これは、このプロセスにより、肉厚が均一で反りを最小限に抑えた部品を作成できるためです。 その結果、射出成形で製造されたプラスチック部品は、高温や振動などの厳しい自動車環境に耐えることができます。
カスタマイズ: 射出成形では、さまざまなサイズや形状の部品を作成できます。 これにより、カスタマイズが不可欠な自動車業界にとって理想的なソリューションとなります。 自動車メーカーは、射出成形を通じて、サイズ、形状、色などの特定の要件を満たす部品を簡単に作成できます。
廃棄物の削減: プラスチック射出成形は、従来の製造方法よりも廃棄物が少なくなります。 このプロセスは非常に効率的であり、スクラップを最小限に抑えて部品を作成できます。 その結果、自動車業界は射出成形を使用してプラスチック部品を製造することで、二酸化炭素排出量を削減できます。
より迅速な生産: 射出成形は、プラスチック部品を迅速かつ効率的に製造する方法です。 このプロセスでは数秒で部品を作成できるため、迅速な生産時間が重要な自動車業界にとって理想的なソリューションとなります。
改善された品質: 射出成形で製造されるプラスチック部品は安定した品質を誇ります。 これは、このプロセスにより、温度、圧力、冷却時間などの成形パラメータを正確に制御できるためです。 その結果、射出成形により製造されるプラスチック部品は、優れた寸法精度と表面仕上げを実現します。
射出成形で一般的に使用されるプラスチックを調べる
射出成形では、プラスチック ペレットを溶かし、金型キャビティに射出して特定の形状を形成します。 このプロセスの多用途性により、メーカーは高い精度と一貫性を備えた複雑な部品を作成できます。 所望の特性を達成するために、射出成形ではさまざまなプラスチック材料が使用されます。 このブログ投稿では、射出成形で一般的に使用されるプラスチックとその特性について説明します。
- アクリロニトリル ブタジエン スチレン (ABS): ABS は、その多大な衝撃性、靭性、耐熱性により、射出成形に広く使用されている熱可塑性ポリマーです。 自動車部品、玩具、電子機器の筐体などによく使用されています。
- ポリカーボネート (PC): PC は、安全メガネ、電子部品、自動車部品など、耐衝撃性と光学的透明性が必要な製品の射出成形に使用される硬質の透明なプラスチック材料です。
- ポリプロピレン (PP): PP は、柔軟性、強度、耐薬品性が必要な製品の射出成形に使用される多用途のプラスチック材料です。 包装、自動車部品、消費財によく使用されます。
- ポリエチレン (PE): PE は、柔軟性と耐久性が必要な製品の射出成形に使用される軽量のプラスチック材料です。 包装、家庭用品、玩具などによく使用されます。
- ポリオキシメチレン (POM): POM は、寸法安定性と耐摩耗性が必要な製品の射出成形に使用される固体で硬いプラスチック材料です。 ギア、ベアリング、その他の機械部品によく使用されます。
- ポリスチレン (PS): PS は、優れた寸法安定性と絶縁特性を必要とする製品の射出成形に使用される軽量で硬いプラスチック材料です。 食品包装、使い捨て器具、CDケースなどによく使われています。
- ポリエチレン テレフタレート (PET): PET は、高い透明性、剛性、耐薬品性が必要な製品の射出成形に使用される、強力で軽量のプラスチック素材です。 飲料ボトル、食品包装、医療機器などによく使用されています。
- ナイロン (PA): ナイロンは、高い強度、耐熱性、耐薬品性が要求される製品の射出成形に使用される、強くて耐久性のあるプラスチック材料です。 自動車部品、電子部品、産業機械などに多く使用されています。
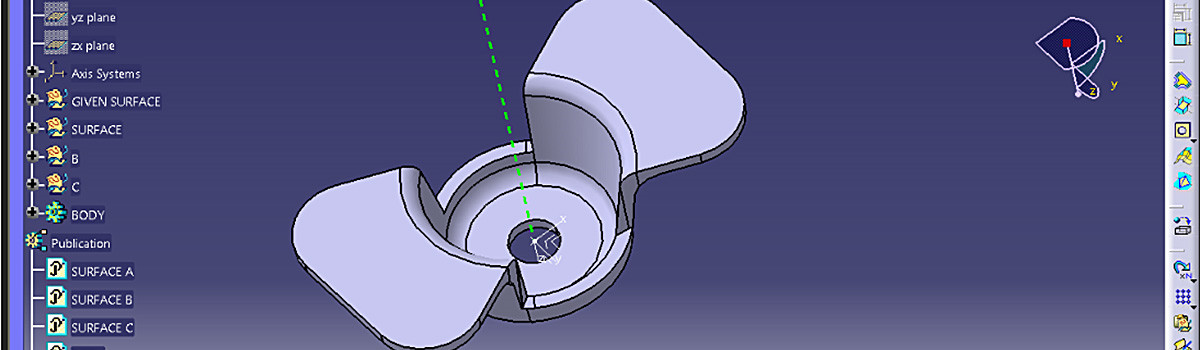
自動車用プラスチック部品の設計上の考慮事項
このブログ投稿では、自動車のプラスチック部品に関する重要な設計上の考慮事項について説明します。
材料選択:
- プラスチック コンポーネントは、ポリプロピレン、ポリカーボネート、ABS など、さまざまな材料から作成できます。
- 各材料には、強度、剛性、熱安定性、化学薬品や紫外線に対する耐性などの固有の特性があります。
- 部品の使用目的と規制基準の特定の要件を満たす材料を選択することが重要です。
生産方法:
- プラスチック部品は、射出成形、ブロー成形、熱成形、回転成形などのいくつかの方法を使用して製造できます。
- 各方法には、コスト、生産速度、複雑さ、部品の品質の点で長所と短所があります。
- 製造方法は、部品のサイズ、形状、体積などの部品の特定のニーズに基づいて選択する必要があります。また、必要な精度や一貫性のレベルも考慮してください。
パーツの機能:
- プラスチック部品を設計する際には、その機能を慎重に考慮する必要があります。
- 部品は、機械的ストレス、温度変動、化学薬品への曝露、その他の環境要因に耐えるように設計する必要がある場合があります。
- 部品のフィット感、形状、機能、および美的要件も考慮する必要があります。
組み立て用の設計:
- プラスチックコンポーネントは、組み立ての容易さを念頭に置いて設計する必要があります。
- 組み立てが困難または時間がかかるコンポーネントは、生産コストを増加させ、品質上の問題を引き起こす可能性があります。
- 部品は、追加のハードウェアや留め具の必要性を最小限に抑え、簡単かつ確実に結合できるように設計する必要があります。
製造可能性を考慮した設計:
- プラスチック部品の設計では、製造プロセスと制限や制約も考慮する必要があります。
- 抜き勾配、肉厚、パーティング ラインなどの設計機能は、製品の品質とコストに大きな影響を与える可能性があります。
- メーカーと協力することで、設計が生産に合わせて最適化されるようにすることができます。
テストと検証:
- プラスチック部品の設計が完了したら、必要な性能と安全性の要件を満たしていることを確認するために、テストおよび検証を行う必要があります。
- テストには、機械的、化学的、熱的テスト、フィット感と機能のテストが含まれます。
- 検証は、初期設計から最終製品に至るまで、開発プロセス全体を通じて実施する必要があります。
射出成形における試作の役割
プロトタイピングは射出成形の世界において重要な役割を果たします。 これは製造において重要なステップであり、デザイナーやエンジニアが本格的な生産に進む前に、設計を改良し、機能をテストし、潜在的な問題を特定できるようになります。 ここでは、射出成形におけるプロトタイピングの重要性とその多くの利点について探っていきます。
設計の検証:
プロトタイピングにより、デザイナーは製品設計を検証し、現実世界での実現可能性を評価できます。 物理的なプロトタイプを作成することで、設計者は部品の形状、フィット感、組み立てなどの要素を評価できます。 設計上の欠陥を特定し、最終製品が望ましい仕様を満たし、意図したとおりに動作することを確認するのに役立ちます。
反復的な改善:
プロトタイピングにより、製品開発サイクル全体にわたって反復的な改善が可能になります。 複数のプロトタイプを作成してテストすることで、設計者は貴重なフィードバックを収集し、必要な変更を加えることができます。 この反復プロセスは、設計を改良し、機能を最適化し、最終製品の全体的なパフォーマンスを向上させるのに役立ちます。
コストと時間の節約:
プロトタイピング中に設計上の欠陥や機能上の問題を特定することは、量産中に発見するよりもはるかにコスト効率が高く、時間を節約できます。 設計変更を早期に行うことで、高価な設備変更の必要性が減り、生産遅延のリスクが軽減されます。 プロトタイピングにより、高価なツールや製造プロセスに着手する前に、効率的な問題解決と最適化が可能になります。
材料の選択:
プロトタイピングにより、射出成形に適した材料の選択が容易になります。 エンジニアはさまざまな材料をテストすることで、強度、柔軟性、耐熱性などの特性を評価し、目的の用途に最適な材料を選択できます。 これにより、結果がパフォーマンスと耐久性の必要な基準を満たしていることを保証します。
製造プロセスの検証:
プロトタイプは、選択した製造プロセスの実現可能性と有効性を検証する手段として機能します。 量産用と同じ材料と方法を使用してプロトタイプを作成することで、エンジニアは課題や限界を早い段階で特定できます。 この検証プロセスは、生産を合理化し、欠陥を減らし、最終製品の一貫した品質を確保するのに役立ちます。
コミュニケーションと利害関係者の関与:
プロトタイプは製品のアイデアを具体的に表現したもので、効果的なコミュニケーションと関係者の関与を促進します。 クライアントにデザインコンセプトを提示する場合でも、エンドユーザーからフィードバックを収集する場合でも、プロトタイプを使用すると、関係者全員が製品を視覚化し、意見を提供し、情報に基づいた意思決定を行うことが容易になります。 コラボレーションが改善されると、誤解が減り、全体的な満足度が高まります。
射出成形プロセスの重要なステップ
このブログ投稿では、射出成形プロセスの重要なステップについて説明します。
ステップ 1: 材料の選択
射出成形プロセスの最初のステップは材料の選択です。
さまざまなプラスチック材料には、強度、柔軟性、耐薬品性などの固有の特性があります。
材料の選択は、部品の特定のニーズとその用途によって異なります。
ステップ 2: ペレットの準備
プラスチックペレットは、必要な仕様に合わせて乾燥および混合することによって調製されます。
このステップは、最終製品の品質に影響を与える可能性のある湿気や汚染物質がプラスチックに含まれていないことを確認するために不可欠です。
ステップ 3: プラスチックを溶かす
プラスチックペレットは射出成形機で溶かされます。
溶解プロセスの温度と圧力は、使用するプラスチック材料の種類によって異なります。
ステップ4:注射
溶けたプラスチックは金型に射出されます。
金型は通常スチールで作られ、最終製品の望ましい形状を作成するように設計されています。
ステップ5:冷却固化
プラスチックを金型に注入した後、冷却して固化させて目的の形状にします。
冷却時間は部品の厚さと複雑さによって異なります。
ステップ 6: 排出
プラスチックが冷えて固まると、金型が開かれ、部品が取り出されます。
場合によっては、金型から部品を取り外すのにエジェクター ピンが使用されます。
ステップ7: トリミングと仕上げ
部品が金型から取り出された後、余分な材料を除去してエッジを滑らかにするために、追加のトリミングと仕上げが必要になる場合があります。
ステップ 8: 品質管理
品質管理は射出成形プロセスにおいて重要なステップです。
最終製品に反りやひび割れ、色や質感のムラなどの欠陥がないか検査されます。
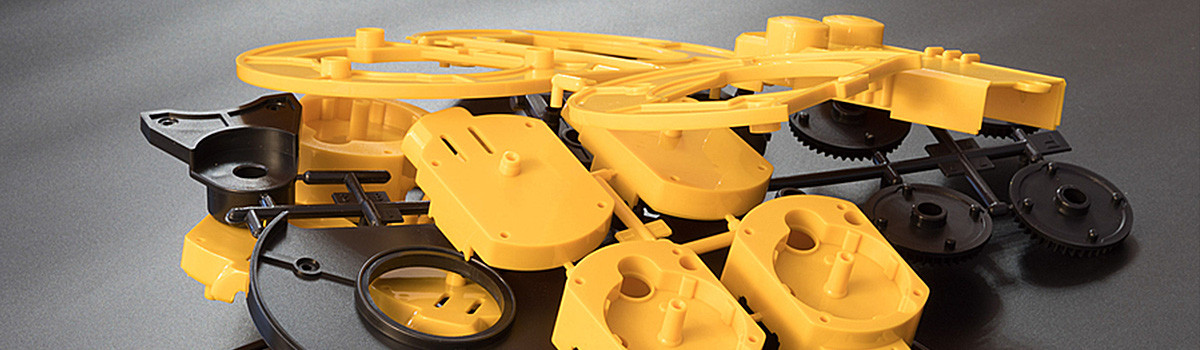
プラスチック部品の強度・耐久性を高める技術
ただし、特に高いストレスや過酷な環境条件にさらされた場合、強度と耐久性の面で課題に直面することがよくあります。 このブログ投稿では、プラスチック コンポーネントの強度と耐久性を向上させるためのいくつかのテクニックについて説明します。
添加剤による補強
- 添加剤は、繊維、フィラー、またはナノ粒子でプラスチック部品を強化することで、プラスチック部品の強度と耐久性を向上させることができます。
- 一般的な添加剤には、ガラス繊維、炭素繊維、シリカ、タルク、粘土などがあります。
他の素材とのブレンド
- プラスチックをゴムやエラストマーなどの他の材料とブレンドすると、強度と耐久性が向上します。
- たとえば、ポリプロピレンに少量のゴムを添加すると、耐衝撃性が向上します。
熱処理
- 熱処理により、特定の種類のプラスチック部品の強度と耐久性が向上します。
- これには、プラスチックを高温にさらして化学的および物理的特性を変化させることが含まれます。
アニーリング
- アニーリングは、プラスチックを特定の温度に加熱し、ゆっくりと冷却する熱処理技術です。
- この技術により、プラスチックの内部応力が軽減され、強度と耐久性が向上します。
射出成形プロセスの最適化
- 射出成形プロセスを最適化することで、プラスチック部品の強度と耐久性を向上させることができます。
- これには、成形中の温度、圧力、冷却速度の制御が含まれます。
表面処理
- コロナ処理、プラズマ処理、火炎処理などの表面処理技術により、プラスチックと他の材料との接着を向上させることができます。
- これにより、接着が重要な用途におけるプラスチック部品の強度と耐久性を向上させることができます。
コーティング
- コーティングは追加の保護層を提供することで、プラスチック部品の強度と耐久性を向上させることができます。
- たとえば、耐食性コーティングは、過酷な環境での損傷からプラスチック部品を保護できます。
自動車射出成形における品質管理対策
自動車射出成形は、高品質の自動車部品の製造に不可欠なプロセスです。 このプロセスには、厳格な品質と性能基準を満たす部品を製造するための専用の機械と金型の使用が含まれます。 このプロセスで製造された自動車部品がこれらの基準を満たしていることを一貫して確認するには、品質管理対策が必要です。 自動車射出成形で実施される重要な品質管理措置の一部を以下に示します。
材料検査: 品質管理の最初のステップは材料検査です。 原材料が要求仕様を満たしていることを確認するために検査されます。 これには、材料の組成、純度、一貫性のチェックが含まれます。
成形プロセスの監視: 成形プロセスは継続的に監視され、部品が要求された仕様内で製造されていることを確認します。 これには、使用済み材料の温度、圧力、流量の監視が含まれます。
部品検査: 部品は製造後に検査され、必要な基準を満たしています。 これには、反り、ヒケ、バリなどの欠陥のチェックが含まれます。
統計的プロセス管理 (SPC): SPC は、生産プロセスを監視および制御する統計ツールです。 これには、統計手法を使用してデータを分析し、プロセスの潜在的な問題を示す傾向やパターンを特定することが含まれます。
品質保証 (QA): QA では、一連の手順とガイドラインを使用して、最終製品が必要な品質基準を満たしていることを確認します。 これには、完成品が要求仕様を満たしていることを確認するための検査とテストが含まれます。
トレーサビリティ: トレーサビリティとは、製品をその出所まで遡って追跡できる機能です。 自動車の射出成形では、欠陥や品質上の問題を発生源まで遡って修正できるようにするためのトレーサビリティが非常に重要です。
継続的な改善: 継続的改善は、改善領域を特定し、製品の品質を向上させるための変更を実装する継続的なプロセスです。 これには、データの分析、傾向の特定、製品の品質と一貫性を向上させるためのプロセスへの変更の実装が含まれます。
コスト分析: 射出成形と従来の製造方法
製造業では、コスト分析は意思決定の重要な側面です。 メーカーは、さまざまな方法を使用して製品の製造コストを評価し、最も費用対効果の高い方法を決定する必要があります。 射出成形と従来の製造方法の XNUMX つが一般的に使用されており、メーカーはどちらの方法が自社の製品にとって最もコスト効率が高いかを決定する必要があります。 ここでは、射出成形と従来の製造方法のコスト分析を示します。
射出成形:
射出成形とは、溶かしたプラスチックを金型に射出して部品を製造する製造方法です。 射出成形の長所と短所は次のとおりです。
Advantages:
- 高い生産量:射出成形は、同一部品のハイブックの製造に最適です。
- 人件費の削減:射出成形は、従来の製造方法と比較して最小限の労力で済みます。
- 一貫性: 射出成形により、互いに同一の互換性のある部品が作成されます。
- 材料廃棄物の削減: 射出成形は従来の製造方法に比べて材料の無駄が少なくなります。
短所:
- 初期費用が高い:射出成形のセットアップコストは、従来の製造方法と比較して高くなります。
- 限られた柔軟性: 射出成形は従来の製造方法に比べて柔軟性が低いため、カスタム部品の製造にはあまり適していません。
伝統的な製造方法:
伝統的な製造方法とは、数十年にわたって使用されてきた従来の製造技術を指します。 これらの方法には、フライス加工、穴あけ、旋削などが含まれます。 従来の製造方法の長所と短所は次のとおりです。
Advantages:
- 低い初期費用:従来の製造方法では、初期費用が最小限で済むため、少量の部品を生産するのに最適です。
- 柔軟性:従来の製造方法は射出成形よりも柔軟性があり、カスタム部品の製造に最適です。
- 工具コストの削減:従来の製造方法では、射出成形よりも低い金型コストが必要です。
短所:
- 人件費の上昇:従来の製造方法では射出成形よりも多くの労力が必要となるため、人件費が高くなります。
- 材料廃棄物の増加:従来の製造方法では、射出成形よりも多くの廃棄物が発生します。
- 矛盾している部分:伝統的な製造方法では、製造量に若干の差異が生じる場合があります。
射出成形の持続可能性と環境への影響
持続可能性と環境への影響は、企業や製造業者が生産プロセスで考慮する必要がある重要な要素です。 一般的な製造方法である射出成形には、プラスとマイナスの環境への影響があります。 このブログ投稿では、射出成形の持続可能性と環境への影響について説明します。
サステナビリティ:
持続可能性とは、将来の世代のニーズを満たす能力を損なうことなく、現在のニーズを満たすことを指します。 射出成形には、持続可能性に関するいくつかの利点があります。
- 材料効率:射出成形では、材料の無駄を最小限に抑えて部品を製造し、部品の製造に必要な材料を削減します。
- エネルギー効率:射出成形では、機械加工や鋳造などの他の製造方法よりも部品の製造に必要なエネルギーが少なくなります。
- 長寿命: 射出成形で製造された部品は耐久性と寿命が長く、頻繁な交換の必要性が軽減されます。
環境への影響:
射出成形には環境への影響も考慮する必要があります。 以下に、射出成形による生態学的にプラスとマイナスの影響をいくつか示します。
環境へのプラスの影響:
- リサイクル: プラスチックなどの射出成形材料の多くはリサイクル可能であり、埋め立て地に送られる廃棄物を削減します。
- 二酸化炭素排出量の削減:射出成形は、機械加工や鋳造などの他の製造方法に比べて、温室効果ガスの排出量が少なくなります。
環境への悪影響:
- 再生不可能な資源の使用:射出成形では、再生不可能な資源に由来するプラスチックなどの石油ベースの材料が使用されます。
- 廃棄物の発生:射出成形は他の製造方法に比べて廃棄物の発生量は少ないですが、それでもスクラップ材料や梱包廃棄物などの廃棄物が発生します。
射出成形における持続可能な実践:
射出成形による環境への悪影響を最小限に抑えるために、メーカーは次のような持続可能な慣行を実行できます。
- リサイクル材料の使用:メーカーは射出成形プロセスでリサイクル材料を使用できるため、埋め立て地に送られる廃棄物を削減できます。
- 再生可能エネルギーの利用:メーカーは太陽光や風力などの再生可能エネルギー源を射出成形機の動力として使用することができ、温室効果ガスの排出量を削減できます。
- 廃棄物の削減:メーカーは、再利用可能なパッケージの使用や、発生するスクラップ材料の量の削減など、廃棄物削減の実践を実行できます。
射出成形プロセスを自動化して効率化
製造業では、競争力と収益性を維持するために効率が非常に重要です。 射出成形は、溶融した材料を金型に射出して部品を製造する一般的な製造方法です。 射出成形プロセスを自動化すると、効率と生産性が大幅に向上します。 このブログ投稿では、射出成形プロセスを自動化して効率化するメリットについて説明します。
射出成形プロセスを自動化する利点:
射出成形プロセスを自動化する利点の一部を次に示します。
- 速度の向上:自動化により、射出成形プロセスの速度が大幅に向上します。 自動機械は手動機械よりもはるかに速い速度で部品を生産できます。
- 一貫性:自動射出成形機は、ばらつきを最小限に抑えた一貫した部品を生産し、品質と信頼性を保証します。
- 精度の向上:自動機械は高い精度と精度を備え、厳しい公差と複雑な形状の部品を製造します。
- 人件費の削減:射出成形プロセスを自動化すると、手作業の必要性が減り、人件費が削減されます。
- 安全性の向上:自動機械は人間にとって危険な作業を実行できるため、製造環境の安全性が向上します。
- 材料廃棄物の削減:自動機械は材料の無駄を最小限に抑えて部品を生産し、材料コストと環境への影響を削減します。
射出成形プロセスの自動化:
射出成形プロセスを自動化する方法のいくつかを次に示します。
- ロボットによる自動化:ロボットは、部品の積み下ろし、部品の検査、完成品の梱包などの作業を実行できます。 ロボットによる自動化により、射出成形プロセスの速度と精度が大幅に向上します。
- 自動マテリアルハンドリング:自動マテリアルハンドリングシステムにより、材料を射出成形機に輸送できるため、手作業の必要性が軽減されます。
- 自動化された品質管理:自動化された品質管理システムは、部品の欠陥や逸脱を検査して、一貫した品質を確保し、手動検査の必要性を減らします。
- リアルタイム監視: これらのシステムはマシンのパフォーマンスを追跡し、問題をリアルタイムで特定し、ダウンタイムを削減し、効率を向上させることができます。
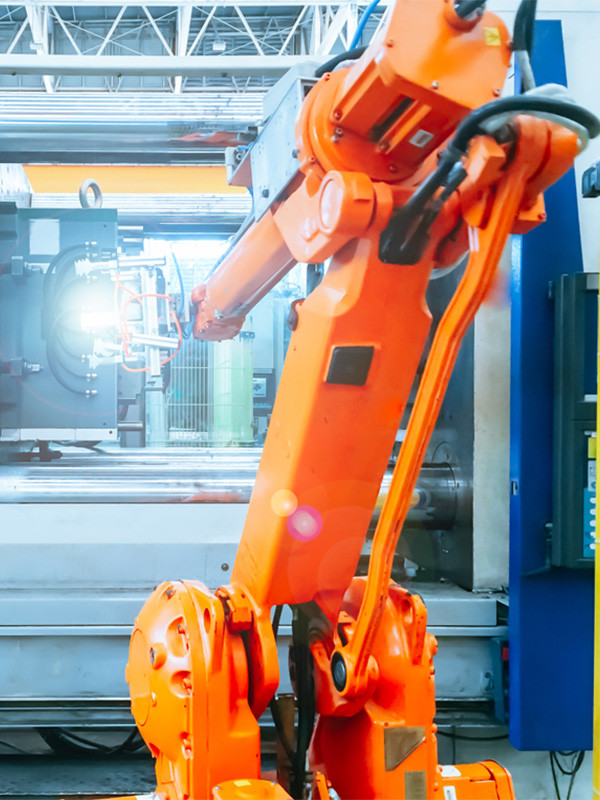
射出成形プロセスの自動化の課題:
射出成形プロセスの自動化には多くの利点がありますが、いくつかの課題もあります。
- 初期費用が高くつく:射出成形プロセスの自動化は、設備と実装のコストにより高価になる場合があります。
- 複雑さの増大:自動化システムは手動システムよりも複雑であり、専門的なトレーニングとメンテナンスが必要です。
- 柔軟性の低下:自動化システムは手動システムに比べて柔軟性が低いため、生産ニーズの変化に適応することが困難になります。
自動車用プラスチック部品射出成形の課題と限界
ただし、自動車用プラスチック部品に射出成形を使用する場合は、いくつかの課題と制限を考慮する必要があります。 このブログ投稿では、自動車プラスチック部品射出成形の課題と限界について説明します。
自動車用プラスチック部品射出成形の課題:
自動車用プラスチック部品の射出成形における課題の一部を以下に示します。
- 材料選択:自動車用プラスチック部品の射出成形に適切な材料を選択するのは難しい場合があります。 材料は強くて耐久性があり、極端な温度や過酷な環境条件に耐える必要があります。
- 工具費:射出成形用の工具のコストは、特に複雑な設計の複雑な部品の場合、高価になる場合があります。
- 部品設計:射出成形用の部品の設計は、成形性、収縮、反りなどの要素を考慮する必要があるため、困難な場合があります。
- 品質管理:射出成形された自動車用プラスチック部品の一貫した品質と性能を確保することは、材料、プロセス、工具の変動により困難になる場合があります。
自動車用プラスチック部品射出成形の限界:
自動車用プラスチック部品射出成形の制限の一部を以下に示します。
- サイズ制限:射出成形にはサイズ制限があり、射出成形を使用して大型の自動車用プラスチック部品を製造できない場合があります。
- 生産量:射出成形は大量生産に最適ですが、少量生産では費用対効果が低い場合があります。
- 複雑:射出成形は、複数の材料やアセンブリを必要とする複雑な形状や設計の部品には適していません。
- 環境への影響:射出成形では廃棄物が発生し、再生不可能な資源が使用されるため、環境に悪影響を与える可能性があります。
課題と限界を克服する:
自動車プラスチック部品射出成形の課題と限界を克服する方法をいくつか紹介します。
- 材料選択:射出成形に適切な材料を選択するには、部品の要件と性能を慎重に考慮する必要があります。 メーカーはサプライヤーと協力して、部品の特定のニーズを満たす材料を選択できます。
- 工具費:高品質のツールに投資すると、ダウンタイムが減少し、生産性が向上するため、長期的にコストを削減できます。
- 部品設計:射出成形用の部品設計を最適化するには、射出成形を使用して部品を効率的かつ効果的に製造できるように、設計者、エンジニア、製造専門家が協力する必要があります。
- 品質管理:自動品質管理システムを導入すると、一貫性が向上し、部品の品質のばらつきが軽減されます。
射出成形技術の革新
射出成形は、複雑なプラスチック部品を製造するために広く使用されている製造プロセスです。 これには、溶融したプラスチック材料を高圧下で金型に注入し、冷却して目的の形状を形成することが含まれます。 製造業における精度と効率への需要が高まる中、射出成形技術の革新はこれらの要件を満たす上で重要な役割を果たしています。 このブログ投稿では、射出成形技術の最新開発のいくつかを探っていきます。
- マイクロ射出成形: この技術により、公差が数ミクロンという極めて小さい部品の製造が可能になります。 マイクロ射出成形は、小型で複雑な部品の需要が高まっている医療業界やエレクトロニクス業界で特に役立ちます。
- 多部品成形: このプロセスでは、同じ金型に異なる材料を射出することが含まれ、複数の色や材料を使用した部品の製造が可能になります。 この技術は自動車および消費財業界で一般的に使用されています。
- インモールド装飾:この技術には、射出成形中に成形部品にグラフィックス、テクスチャ、パターンを追加することが含まれます。 インモールド装飾は、追加の加工を行わずに高品質の仕上げを実現するコスト効率の高い方法です。
- 共射出成形: この技術は XNUMX つの材料を同時に射出して、スキン材料とコア材料を持つ部品を作成します。 共射出成形は、ソフトな感触や機械的特性を強化した部品の作成に役立ちます。
- ガスアシスト射出成形:この技術では、射出成形中にガス (通常は窒素) を金型に注入します。 ガスは部品内にチャネルを形成し、材料の使用量を削減し、製品の性能を向上させます。
- 高速射出成形:このテクノロジーにより、射出速度とサイクルタイムが高速化され、生産効率が向上し、コストが削減されます。 高速射出成形は、薄肉部品の製造に特に役立ちます。
- インテリジェントな成形: このテクノロジーは、センサーとデータ分析を使用して射出成形プロセスを最適化します。 インテリジェントな成形では、温度、圧力、材料の流れなどの要因を監視することで、製品の品質を向上させ、無駄を削減できます。
アプリケーションのスポットライト: 内装プラスチック部品
自動車業界では、優れた運転体験を提供するためにインテリア デザインと機能が不可欠です。 内部のプラスチック部品はこの目的を達成する上で重要な役割を果たし、快適性、スタイル、耐久性を提供します。 このブログ投稿では、自動車の内装で最も一般的に使用されるプラスチック部品のいくつかについて説明します。
- ダッシュボード: ダッシュボードは、計器、通気口、インフォテインメント システム、その他の重要な制御装置を備えた顕著なインテリア機能です。 プラスチック部品は、その耐久性、設計の柔軟性、加工の容易さから、ダッシュボードの製造によく使用されます。
- ドアパネル:ドアパネルはインテリアデザインに不可欠であり、保護と快適さを提供します。 プラスチック部品は、耐衝撃性、騒音低減、軽量特性のため、ドアパネルの製造によく使用されます。
- 席:自動車シートには、快適さとサポートを提供する高性能素材が必要です。 プラスチック部品は、シートバック、アームレスト、およびシート構造のその他の部分を作成するために使用されます。 これらのコンポーネントは強度と柔軟性を提供し、さまざまなデザインに合わせて簡単に成形できます。
- センターコンソール:センターコンソールは、空調制御、オーディオシステム、ストレージなどの重要な制御のハブです。 プラスチック部品は、熱、湿気、その他の環境要因に耐えられるため、センター コンソールの作成によく使用されます。
- トリムパネル: トリムパネルは、ピラー、ヘッドライナー、シートバックなどの車両の室内領域をカバーするために使用されます。 デザインの柔軟性、色の多様性、加工の容易さのため、これらのパネルの作成にはプラスチック部品が使用されます。
アプリケーションのスポットライト: 外装プラスチック部品
自動車業界では、外装プラスチック部品がますます一般的になってきています。 軽量材料、燃費の向上、革新的なデザインの需要により、プラスチック部品は車両のさまざまな外装部品の製造に一般的な選択肢となっています。 このブログ投稿では、自動車業界で最も一般的に使用されている外装プラスチック部品のいくつかについて説明します。
- バンパー: バンパーは衝突時に車両を保護する重要な外装部品です。 プラスチック部品は軽量で耐衝撃性があり、コスト効率が高いため、バンパーの製造によく使用されます。
- グリル: グリルは車両の顕著な外観特徴であり、車両全体のデザインと空気力学において重要な役割を果たします。 プラスチック部品は、設計の柔軟性と複雑な形状に成形できるため、グリルの製造に一般的に使用されます。
- 外装トリム:外装トリムには、車両の外観を向上させるモールディング、フェンダー フレア、その他の装飾コンポーネントが含まれます。 これらのトリムの製造にはプラスチック部品がよく使用されます。これは、プラスチック部品に色や質感を付けることができ、幅広いデザインのオプションが提供されるためです。
- ミラー: ミラーはあらゆる車両に不可欠なコンポーネントであり、視認性と安全性を提供します。 プラスチック部品は、その軽量特性、耐衝撃性、設計の柔軟性により、ミラーハウジングの製造によく使用されます。
- ネタバレ: スポイラーは、空気力学を改善し、全体的な外観を向上させるために、多くの車両に人気のある追加物です。 プラスチック部品は、軽量で設計の柔軟性があるため、スポイラーの製造によく使用されます。
自動車用プラスチック部品射出成形の未来
自動車プラスチック部品の射出成形は、自動車業界においてますます重要になっています。 テクノロジーが進歩し続けるにつれて、このプロセスの将来は有望に見えます。 以下に、自動車プラスチック部品射出成形の将来の傾向と予測をいくつか示します。
- 軽量素材の使用量の増加: カーボンファイバーや熱可塑性プラスチックなどの軽量素材は、自動車業界でますます人気が高まっています。 これは、燃料効率、パフォーマンス、排出ガスの削減という点での利点によるものです。 その結果、自動車用プラスチック部品の射出成形は、これらの軽量材料の製造において重要な役割を果たすことになります。
- 積層造形の統合:3D プリンティングとも呼ばれる積層造形は、自動車業界で一般的になりつつあります。 この技術により、従来の射出成形では製造が困難または不可能だった複雑な幾何学形状や形状の作成が可能になります。 将来的には、自動車プラスチック部品の射出成形では積層造形が生産に統合され、より複雑なデザインが作成される可能性があります。
- 自動化の向上: 技術の進歩に伴い、射出成形プロセスの自動化がさらに進むことが予想されます。 これにより、効率が向上し、生産時間の短縮につながります。 さらに、自動化により人的エラーの可能性が低減され、より高品質の製品が得られます。
- より持続可能な素材: 持続可能性は自動車業界においてますます重要な問題となっています。 自動車プラスチック部品の射出成形では、より持続可能な材料を使用してこの傾向に適応する必要があります。 たとえば、バイオベースのプラスチックやリサイクル材料を射出成形プロセスで使用して、廃棄物や炭素排出量を削減できます。
- カスタマイズ性の向上:消費者のカスタマイズとパーソナライゼーションに対する要求はますます高まっています。 将来的には、自動車用プラスチック部品の射出成形に、製品のさらなるカスタマイズを可能にする技術が組み込まれる可能性があります。 これには、プラスチック部品のデザイン、色、質感をカスタマイズする機能が含まれる可能性があります。
- スマートテクノロジーの統合: 自動車業界では、センサーやモノのインターネット (IoT) デバイスなどのスマート テクノロジーが一般的になりつつあります。 将来的には、自動車用プラスチック部品の射出成形にこれらの技術が組み込まれる可能性があります。 これにより、車両の他の部分やドライバーと通信できるコンポーネントの作成が可能になる可能性があります。
ケーススタディ: 自動車産業における射出成形の導入の成功
射出成形は広く使用されている製造プロセスであり、自動車業界でますます人気が高まっています。 このブログ投稿では、自動車業界における射出成形の成功事例について説明します。
事例: 自動車照明
自動車産業において射出成形が特に成功を収めている分野の XNUMX つは、自動車照明部品の製造です。 このケース スタディでは、人気のセダン モデルのテールライト レンズを製造するための射出成形の実装に焦点を当てます。
課題:
テールライトのレンズは次の要件を満たす必要がありました。
- 紫外線および耐候性に対する耐性
- 良好な光学的透明性
- 耐久性
- 審美的に楽しいデザイン
- 効率的な生産時間
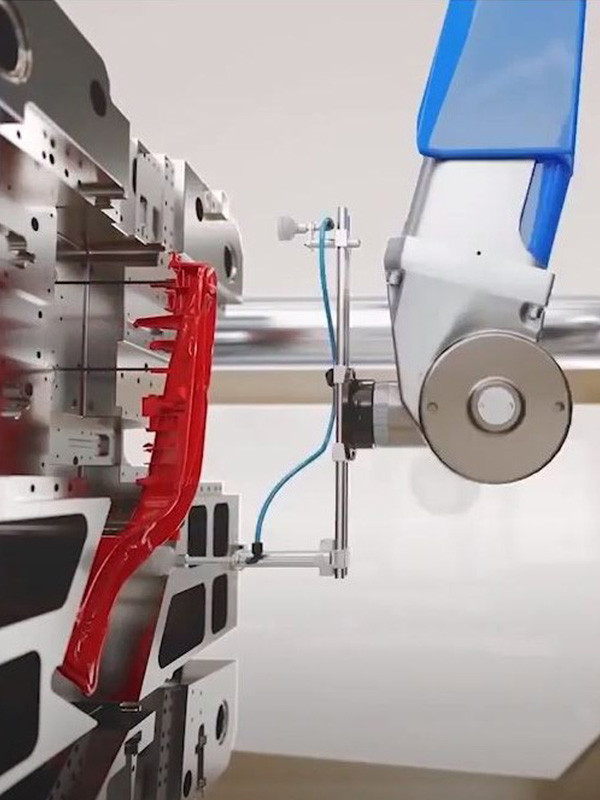
解決法:
要件と課題を分析した後、この自動車照明メーカーはテールライト レンズを製造するための最適なソリューションとして射出成形を選択しました。 このメーカーは、高品質の自動車部品の製造実績を持つ経験豊富な射出成形会社と提携しました。
射出成形プロセスには次の手順が含まれます。
- 材料選択:テールライトレンズには耐紫外線性のポリカーボネート素材が選択されました。
- 金型設計:射出成形会社は、要求仕様を満たすテールライト レンズを製造するためのカスタム金型を設計しました。
- 射出成形:次に、この金型を射出成形プロセスで使用して、テールライト レンズを製造しました。
- 品質管理:テールライトのレンズは、必要な基準を満たしていることを確認するために、厳格な品質管理措置が実施されました。
結果について
テールライトレンズの製造に射出成形を導入したことが成功を収めました。 自動車照明メーカーは、要求される仕様をすべて満たした高品質のテールライト レンズを製造しました。
この用途に射出成形を使用する利点は次のとおりです。
- 一貫した品質:射出成形により、要求基準を満たしたテールライト レンズの安定した品質が確保されました。
- 効率的な生産: 射出成形プロセスによりテールライト レンズの効率的な生産が可能になり、生産時間とコストが削減されました。
- 見た目にも美しいデザイン:射出成形により、テールライト レンズの美しいデザインを作成することができました。
- 耐久性: 射出成形によって製造されたテールライト レンズは耐久性があり、紫外線や風化に強いです。
射出成形に関するよくある誤解
射出成形は、溶融した材料を金型に射出して目的の形状を作成する、広く使用されている製造プロセスです。 ただし、射出成形に関する多くの誤解が、プロセスに関する誤解につながる可能性があります。 このブログ投稿では、射出成形に関するよくある誤解について説明します。
誤解1: 射出成形は、大量の製品を生産する場合にのみ適しています。
多くの人は、射出成形は大量の製品の生産にのみ適していると考えています。 射出成形は大量の製品を生産できますが、小規模な生産にも使用できます。 射出成形は、小規模から中規模の生産を行う場合、効率的かつコスト効率の高い方法となります。
誤解2: 射出成形は時間がかかるプロセスです。
射出成形に関するもう XNUMX つのよくある誤解は、射出成形は時間がかかるプロセスであるということです。 射出成形にはある程度のセットアップ時間が必要であるのは事実ですが、一度プロセスが起動して実行されると、大量の製品を迅速かつ効率的に生産できます。 さらに、技術の進歩により、射出成形機とプロセスの高速化が可能になりました。
誤解3: 射出成形は単純な形状の製造にのみ適しています。
射出成形は単純な形状を製造することを連想させることが多いですが、必ずしもそうではありません。 金型設計と材料選択の進歩により、射出成形によるより複雑な形状やデザインの製造が可能になりました。 さらに、3D プリンティングとその他のテクノロジーの統合により、射出成形の可能性がさらに広がりました。
誤解4: 射出成形は環境に優しくありません。
射出成形は環境に優しくないと批判されることがよくあります。 射出成形によってある程度の廃棄物が発生するのは事実ですが、材料の選択とリサイクル技術の進歩により、射出成形によるより環境に優しい製品の生産が可能になりました。 さらに、射出成形により、製品の二酸化炭素排出量の削減に役立つ軽量で持続可能な材料の生産が可能になります。
誤解5: 射出成形は高価です。
多くの人は、射出成形は高価な製造プロセスであると信じています。 確かに、射出成形には金型の設計や製造のコストなどの初期費用がかかりますが、生産量が増加するにつれてユニットあたりのコストは減少します。 さらに、技術の進歩により、射出成形はこれまで以上にコスト効率と効率が向上しました。
射出成形における一般的な問題のトラブルシューティング
射出成形は、さまざまな業界で高品質のプラスチック部品を製造するために広く使用されている製造プロセスです。 ただし、他の製造プロセスと同様に、射出成形でも最終製品に悪影響を及ぼす可能性のある一般的な問題が発生する可能性があります。 このブログ投稿では、射出成形におけるいくつかの一般的な問題とそのトラブルシューティング方法について説明します。
問題 1: 火傷の跡
材料の過熱により射出成形品の表面に焼け跡が現れ、樹脂の劣化や変色を引き起こすことがあります。 この問題は、次のようなさまざまな要因によって発生する可能性があります。
- 高い溶融温度
- 長い滞在時間
- 冷却時間が不十分である
- 高い射出速度
焼け跡のトラブルシューティングを行うには、メーカーは次の手順を検討する必要があります。
- 溶融温度を下げる
- 滞在時間を短縮する
- 冷却時間を長くする
- 射出速度を下げる
問題 2: 反り
反りは射出成形における一般的な問題で、材料の不均一な冷却によって発生する可能性があります。 これにより、最終製品に歪みや歪みが生じ、機能に悪影響を及ぼす可能性があります。 この問題は、次のようないくつかの要因によって発生する可能性があります。
- 不均一な冷却
- 不十分な保圧
- 不適切な金型設計
反りをトラブルシューティングするには、メーカーは次の手順を検討する必要があります。
- 金型全体を均一に冷却する
- 保圧を高める
- 金型設計を変更して部品の形状を改善する
問題 3: ヒケ
ヒケは、不均一な冷却または保圧によって射出成形品の表面に発生する可能性のあるくぼみです。 この問題は、次のようないくつかの要因によって発生する可能性があります。
- 高い射出速度
- 不十分な保圧
- 高い溶融温度
- 長い滞在時間
ヒケのトラブルシューティングを行うには、メーカーは次の手順を検討する必要があります。
- 射出速度を下げる
- 保圧を高める
- 溶融温度を下げる
- 滞在時間を短縮する
問題 4: 点滅
フラッシングは射出成形でよく発生する問題で、余分な材料が金型から絞り出されるときに発生します。 その結果、最終製品の端の周りに余分な材料が現れ、美観や機能に悪影響を与える可能性があります。 この問題は、次のようないくつかの要因によって発生する可能性があります。
- 磨耗した金型部品
- クランプ力不足
- 冷却時間が不十分である
フラッシュのトラブルシューティングを行うには、メーカーは次の手順を検討する必要があります。
- 磨耗した金型部品を交換する
- クランプ力の増加
- 冷却時間を長くする
専門家の洞察: 自動車射出成形業界の専門家へのインタビュー
射出成形は自動車産業において重要なプロセスであり、さまざまな車両部品の高品質プラスチック部品を製造します。 私たちは業界の専門家に話を聞き、自動車射出成形に関する専門的な意見や洞察を共有し、業界とその現状についての洞察を得ました。
専門家 1: John Doe、射出成形会社 CEO
- ドウ氏は、自動車業界におけるバイオプラスチックの使用がますます一般的になってきていると語った。 これらのプラスチックは環境に優しく、車両の二酸化炭素排出量を削減できるため、自動車メーカーにとって魅力的な選択肢となっています。
- 同氏はまた、3Dプリンティングの進歩により、より複雑な金型設計が可能になり、最終製品の品質がより高くなったと指摘した。
- 課題に関して同氏は、熟練労働者の不足が業界の重大な問題であり、人件費の上昇につながっていると述べた。
専門家 2: ジェーン・スミス、自動車会社の設計エンジニア
- スミス氏は、燃料効率を向上させ、排出ガスを削減するために、複合材料やプラスチックなどの軽量材料を求める業界の傾向が高まっていると語った。
- 同氏はまた、設計プロセスでシミュレーション ソフトウェアを使用することがますます一般的になってきており、より効率的でコスト効率の高い製品開発が可能になっていると述べました。
- 課題について、同氏は自動車部品の複雑さの増大と、より精密な製造プロセスの必要性について言及した。
専門家 3: Bob Johnson 氏、射出成形会社の品質管理マネージャー
- ジョンソン氏は、自動車業界では品質管理が重要であると語った。 軽微な欠陥であっても、安全性と機能性が損なわれる可能性があります。
- 同氏は、自動検査システムなどの技術の進歩により、より効率的で正確な品質管理プロセスが可能になったと指摘した。
- 課題に関しては、高品質基準を維持しながら生産時間を短縮するという要求が高まっていることについて言及しました。
専門家 4: サラ・リー氏、射出成形会社の営業担当者
- Lee 氏は、顧客の要求は常に進化しており、持続可能性と費用対効果への注目が高まっていると共有しました。
- 彼女は、最終製品が必要な基準と期待を確実に満たすためには、メーカーと顧客の間のコミュニケーションとコラボレーションが重要であると述べました。 課題の観点から、同氏は業界内での競争の激化と、射出成形会社がイノベーションと品質を通じて差別化を図る必要性について言及した。
まとめ
自動車産業が進化し続ける中、射出成形は高品質のプラスチック部品を製造するための重要な製造プロセスであり続けています。 内装部品でも外装部品でも、射出成形は驚くべき設計の自由度、コスト効率、持続可能性の利点をもたらします。 メーカーは、自動車用プラスチック部品の射出成形の複雑さを理解することで、革新的で信頼性の高い車両を製造するための新たな可能性を解き放つことができます。 射出成形の世界とそれが自動車産業に与える影響についてのさらなる洞察については、このブログにご注目ください。