液状シリコーンゴム(LSR)射出成形
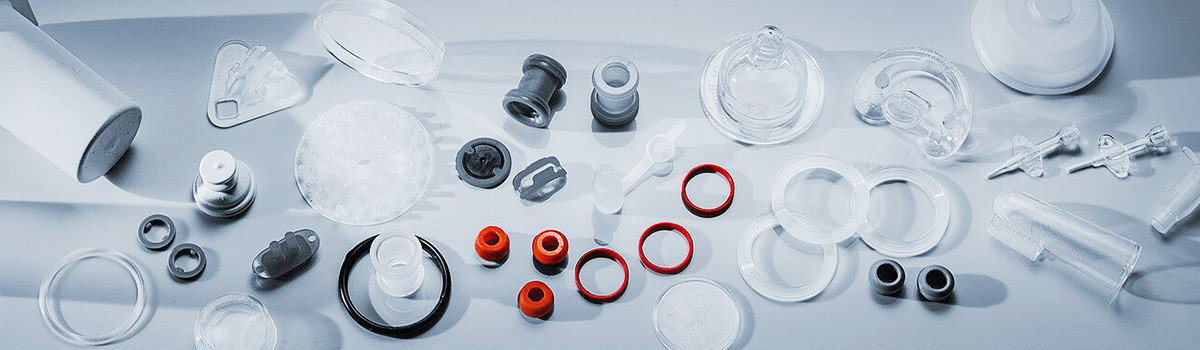
液状シリコーンゴム(LSR)射出成形とは何ですか?
液体シリコーンゴム (LSR) の射出成形は、柔軟で耐久性のある部品を大量生産するために使用されるプロセスです。 プロセス中には、インジェクター、計量ユニット、供給ドラム、ミキサー、ノズル、金型クランプなど、いくつかのコンポーネントが必要です。
液状シリコーンゴム (LSR) の射出成形は、医療用途や電気用途などのさまざまな製品の製造に使用される一般的な技術です。 材料本来の特性に加えて、プロセスのパラメーターも重要です。 LSR 射出成形は複数のステップからなるプロセスです。
最初のステップは混合物の調製です。 LSR は通常、最終製品の望ましい特性に応じて、顔料と添加剤 (充填剤など) の XNUMX つの成分で構成されます。 このステップでは、混合物の成分が均質化され、シリコーン温度(周囲温度またはシリコーンの予熱)をより適切に制御するために温度安定化システムと組み合わせることができます。
現在、シリコーンゴム製品の応用範囲はますます広がっており、LSR射出成形はこの業界で重要な役割を果たしています。
液状シリコーンゴム成形はどのように機能しますか?
LSR 成形は、その柔軟性の点で熱可塑性プラスチック射出成形とは若干異なります。 標準のアルミニウム工具と同様に、LSR 成形工具は CNC 機械加工を使用して製造され、LSR 成形プロセスに耐えるように構築された高温工具を作成します。 フライス加工後、工具は顧客の仕様に合わせて手作業で研磨され、XNUMX つの標準的な表面仕上げオプションが可能になります。
そこから、完成したツールは高度な LSR 専用射出成形プレスにロードされ、ショット サイズを正確に制御できるように精密に調整され、最も一貫した LSR 部品を製造します。 インジェクターピンは部品の品質に影響を与える可能性があるため、金型製造では LSR 部品を金型から手動で取り外します。 LSR 材料には、医療、自動車、照明などのさまざまな部品用途や業界に適合する標準シリコーンと特定グレードが含まれます。 LSR は熱硬化性ポリマーであるため、その成形状態は永続的であり、一度硬化すると、熱可塑性プラスチックのように再び溶かすことはできません。 実行が完了すると、部品 (または最初のサンプル実行) は箱詰めされ、その後すぐに発送されます。
ここでは、それについて調べてみましょう。まず、液状シリコーンゴム材料について説明する必要があります。次のような知っておくべき主な点があります。
液状シリコーンゴム(LSR)は絶縁性に優れ、高級電子プラグやハイテク電子プラグに適しています。
液状シリコーンゴム(LSR)材料は、高温または低温環境での使用に適しています。 材料の絶縁特性、機械的特性、物理的特性は、200℃でも-40℃の低温でも変化しません。
ガス化や劣化に強いので屋外での使用に適しています。
液状シリコーンゴム(LSR)は耐油性があり、石油採掘産業で使用できます。 縦型ダブルスライド液体シリコーン射出成形機、縦型シングルスライド液体シリコーン射出成形機のXNUMXつのモデルがあり、あらゆる種類の需要の高い高精度シリコーンゴム製品の生産に使用されます。 下部シリンダーアングル射出機は、複合サスペンションインシュレーター、ポストインシュレーター、避雷器の伝統的なモデルの生産です。
LSR 射出成形 (LIM) の利点。
LSR 射出成形 (LIM) には多くの利点があります。 シリコーン圧縮成形との比較です。
液体シリコーンゴム(LSR)材料はより安全であり、シリコーンゲルは食品グレードまたは医療グレードです。 LSR射出成形(LIM)は精度が高く、非常に高精度のシリコーンゴム部品を製造することができます。 また、パーティングラインが非常に薄く、バリも少ないです。
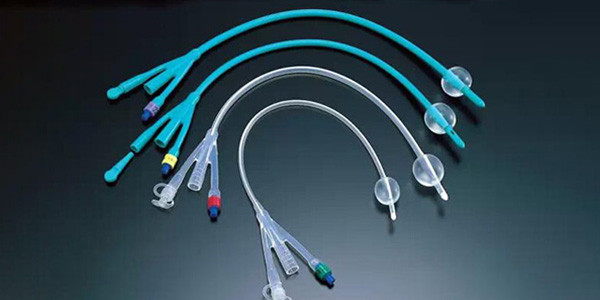
LSR成形品のメリット
無限のデザイン – 他では不可能な部品形状や技術的ソリューションの製造が可能
一貫性のある – 製品の寸法、精度、全体的な品質において最高の一貫性を実現します。
清(ピュア) – シリコーンは、安全に使用されてきた長い歴史を持つ、最も広範囲にテストされた生体材料の XNUMX つです。
正確な – 0.002グラムから数百グラムまでの重量の部品に対応する、フラッシュレス、無駄のない工具設計コンセプト
高信頼性 – 機械、ツーリング、オートメーションにおける最新テクノロジーの使用
品質 – 工程内管理による欠陥ゼロの品質レベル
尊大 – サイクルタイムが短いため、数千から数百万の大量生産が可能
石斑魚 – 最先端の加工技術を活用し、クラス 7 および 8 のクリーンルームで生産
お財布に優しい – 最低の総所有コスト (TCO) を実現
LSR射出成形
顧客のニーズに応える革新的な技術:
液体シリコーンゴム (LSR) は、液体射出成形 (LIM) プロセスで加工できます。 液体原料は 1 つの別々の成分から 1:XNUMX の比率で混合され、コールド ランナー システムを介して加熱された金型に射出されます。 硬化は数秒以内に行われるため、サイクルが速く、大量に生産できるという利点があります。
LSR 射出成形は設計とツールの柔軟性により、複雑な形状の製造に最適であり、さまざまな機能特徴を XNUMX つの部品に統合できます。 また、製品の信頼性と総所有コストの点でも大きな利点があります。
LSR 液状シリコーンゴム射出成形プロセス
DJmolding 液体シリコーンゴム射出成形機は、見た目は熱可塑性プラスチック射出成形機と同じです。 どちらのタイプのプレスも、基本的な機械部品であるクランプユニットと射出ユニットを使用します。
LSR 射出成形機のクランプ ユニットは、液体シリコーンゴムと熱可塑性プラスチックの機械に共通です。 シリコーン射出成形機は通常、油圧ラムを備えており、油圧トグルを備えている場合もあります。 一部の印刷機は、トグル付きの電気ラムを使用して設計されています。 熱可塑性プラスチック部品の成形に使用される高圧とは異なり、液体シリコーンの射出圧力は 800 PSI の範囲です。 クランプの目的は、シリコーンが硬化するときに金型を閉じたままにし、シリコーン材料の膨張力を抑えることです。
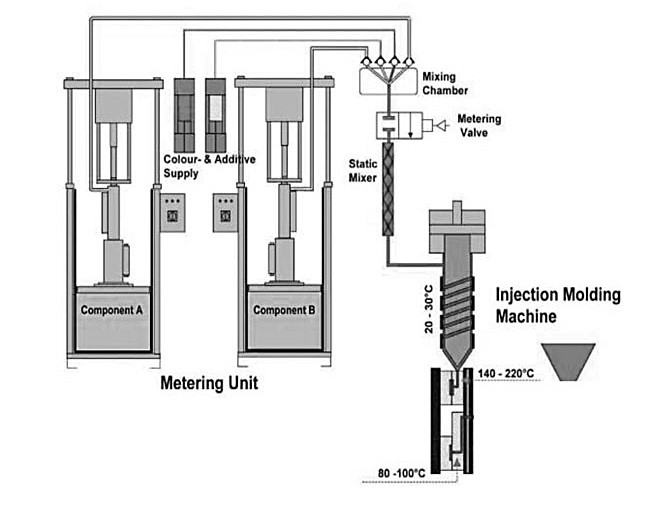
液体シリコーンの射出ユニットは、水冷バレルとノズルにより冷却され、液体シリコーンの硬化を防ぎます。 熱可塑性プラスチック射出ユニットは逆方向に動作し、材料を動かし続けるためにバレルとノズルを 300F 以上に加熱する必要があります。 液体射出成形ユニットもより低い圧力 (1,000 PSI 未満) で動作しますが、熱可塑性プラスチックの対応するユニットは数万 PSI で動作します。
液体シリコーンは通常、5 ガロンのペール缶または 55 ガロンのドラム缶で提供されます。 パート A とパート B があります。着色剤は分散液の形で提供され、通常は混合シリコーンの 1 ~ 3 重量% です。 シリコーン注入ユニットは、XNUMX つのパート A シリコーンと XNUMX つのパート B シリコーンを別々のホースを介してスタティック ミキサーにポンプで送ります。 さらに、色は別のホースを介してスタティック ミキサーに送られます。 混合された成分は、遮断弁を介して射出成形バレルのスロートに供給されます。
DJmolding は、中国の液状シリコーンゴム (LSR) 射出成形および液状シリコーンゴム部品の専門メーカーです。
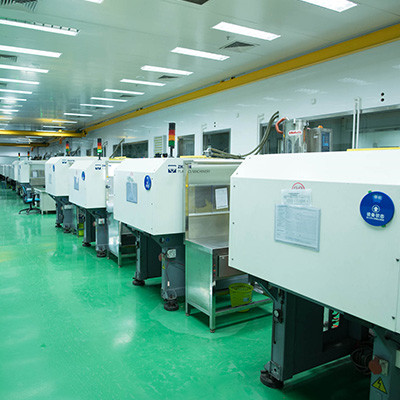
液状シリコーンゴム射出ワークショップ
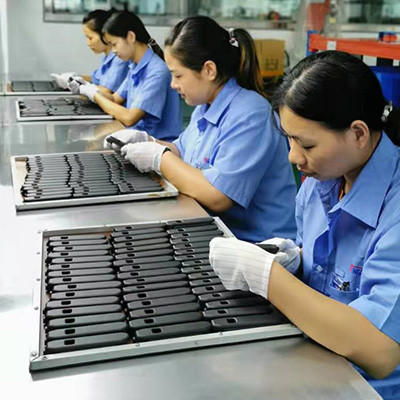
LSR射出製品のQC
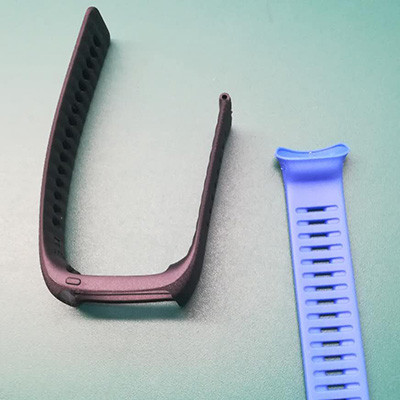
LSR製品
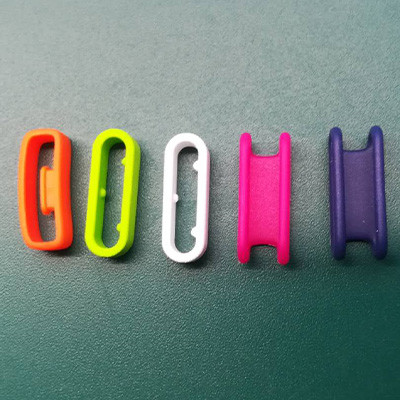
LSR製品
当社の液体シリコーン ゴム成形プロセスでは、カスタム プロトタイプと最終用途の量産部品を 15 日以内に製造します。 当社では、コスト効率の高い工具と製造サイクルの加速を実現するアルミニウム金型を使用し、さまざまなグレードとデュロメーターの LSR 材料を在庫しています。
寸法、精度、全体的な品質において最高の一貫性を提供します。
液状シリコーン ゴム成形に対する当社の総合的なアプローチは、お客様と提携して独自の仕様と要件に基づいた革新的なソリューションを開発することにかかっています。
液状シリコーンゴム(LSR)射出成形は、液状シリコーンゴムを金型に注入してさまざまな製品を作成する製造プロセスです。 LSR は、生体適合性、熱安定性、耐薬品性などのユニークな特性により、ますます人気が高まっている多用途の材料です。 この記事では、LSR 射出成形の利点について説明し、この技術のさまざまなアプリケーションを検討します。
LSR 射出成形はどのように機能しますか?
LSR(液体シリコーンゴム)射出成形は、高品質で精密なシリコーンゴム部品を製造する製造プロセスです。 優れたディテールと一貫性を備えた複雑な形状やデザインを作成するのに役立ちます。 このプロセスでは、液体シリコーンゴムを金型キャビティに注入し、硬化して所望の形状に固化させます。 LSR 射出成形の仕組みの概要を以下に示します。
金型の準備: プロセスは金型の準備から始まります。 型は通常、射出側とクランプ側の XNUMX つの半分で構成され、これらが互いに嵌合してシリコーン用のキャビティを形成します。 硬化後、金型は洗浄され、部品の取り外しが容易になるように離型剤が塗布されます。
シリコーンの準備: 液状シリコーンゴムは、主剤シリコーンと硬化剤からなる XNUMX 成分材料です。 これらの成分は正確な比率で混合されます。 混合物は脱気され、最終部品の品質に影響を与える可能性のある気泡が除去されます。
射出:混合・脱気した液状シリコーンゴムを射出装置に移送します。 射出ユニットは材料を特定の温度に加熱して粘度を下げ、流れやすくします。 材料は、ノズルまたはスプルーを通じて金型キャビティに射出されます。
硬化: 液体シリコーンゴムが金型キャビティに注入されると、硬化が始まります。 硬化プロセスは通常、熱によって開始されますが、一部の型では UV 光などの他の方法を利用する場合もあります。 熱によりシリコーンが架橋して固化し、金型キャビティが形成されます。 硬化時間はパーツの設計やシリコン素材によって異なります。
冷却と部品の取り外し: 硬化プロセスの後、金型を冷却してシリコンを完全に硬化させます。 冷却時間はさまざまですが、通常は硬化時間よりも短くなります。 冷却したら金型を開き、完成した部品を取り出します。 この位置では、余分な材料のトリミングや欠陥の検査など、追加の後処理ステップが必要になる場合があります。
LSR 射出成形には、複雑で複雑な形状の製造、優れた部品の一貫性、高精度、極端な温度、化学薬品、経年変化に対する耐性など、いくつかの利点があります。 さまざまな医療、自動車、エレクトロニクス、消費者製品業界で一般的に使用されています。
これは LSR 射出成形プロセスの簡略化した説明であり、実際の操作は特定の装置、材料、および部品の要件によって異なる場合があることに注意することが重要です。
LSR射出成形のメリット
LSR (液体シリコーンゴム) 射出成形は、従来の成形方法に比べていくつかの利点がある多用途の製造プロセスです。 LSR射出成形では、液状シリコーンを金型に注入し、硬化させて固体として完成品を作ります。 LSR 射出成形の主な利点の一部を以下に示します。
精度と一貫性
LSR 射出成形は、細部にまでこだわった複雑で入り組んだ部品の作成において、優れた精度と一貫性を実現します。 液体シリコーンは高圧下で金型に注入され、最も小さな隙間や隅まで充填され、非常に複雑な部品が製造されます。 さらに、LSR 成形により一貫性と再現性が向上し、最終製品の欠陥や不一致の可能性が減少します。
高品質の部品
LSR 射出成形では、磨耗、熱、紫外線に強い、高品質で耐久性のある部品を製造できます。 LSR 材料は、高弾性、低圧縮永久歪み、極端な温度に対する耐性などの優れた物理的特性を備えています。 このため、LSR 射出成形は、医療機器、自動車部品、消費者製品など、高精度と耐久性が必要な部品の製造に理想的な選択肢となります。
高い費用対効果
LSR 射出成形は、大型部品を製造するためのコスト効率の高い製造方法です。 このプロセスの高い精度と一貫性により、廃棄物やスクラップ材料の削減に貢献するとともに、必要な労働力が低く、生産時間が効率的であるため、製造コストが最小限に抑えられます。 さらに、LSR 材料は寿命が長いため、頻繁に部品を交換したり修理したりする必要性が軽減されます。
多才
LSR 射出成形では、さまざまなサイズ、形状、幾何学形状のさまざまな部品を製造できます。 液状シリコーンは、緻密で複雑な形状を成型することができるため、高い精度と精度が要求される部品の製造に最適です。 さらに、LSR 射出成形には、さまざまな程度の硬さと柔らかさの特徴を持たせることができるため、より優れた製品設計と機能の柔軟性が可能になります。
サイクルタイムの短縮
LSR 射出成形はサイクルタイムが速いため、比較的短期間で大量の部品を生産できます。 液体シリコーンは金型に注入され、数秒で固体の形に硬化するため、大量生産に最適です。
廃棄物の発生量の削減
LSR 射出成形では、液体シリコーンを金型に直接注入し、硬化して目的の形状を形成するため、廃棄物がほとんど発生しません。 これは、大量のスクラップ材料が発生する機械加工や鋳造などの他の製造プロセスとは対照的です。 さらに、LSR 材料はリサイクルして再利用できるため、新しい材料の必要性が減り、廃棄物の発生が削減されます。
安全性の向上
LSR 材料には通常、フタル酸エステル、BPA、PVC などの有害な化学物質が含まれていないため、労働者や消費者にとってより安全です。 さらに、LSR 射出成形で使用される低温プロセスでは、有害な溶剤やその他の化学物質が必要ないため、有害物質にさらされるリスクが軽減されます。
市場展開までの時間の短縮
LSR 射出成形では、迅速なプロトタイピングと迅速な生産が可能になるため、新製品の市場投入までの時間を短縮できます。 このプロセスの高い精度と一貫性により、最終製品が希望の仕様を確実に満たすことができ、複数回のプロトタイピングとテストの必要性が軽減されます。
オートメーション
LSR 射出成形は高度に自動化できるため、手作業の必要性が減り、エネルギー消費が削減されます。 さらに、自動化により効率が向上し、人件費が削減され、最終製品の一貫性と品質が向上します。
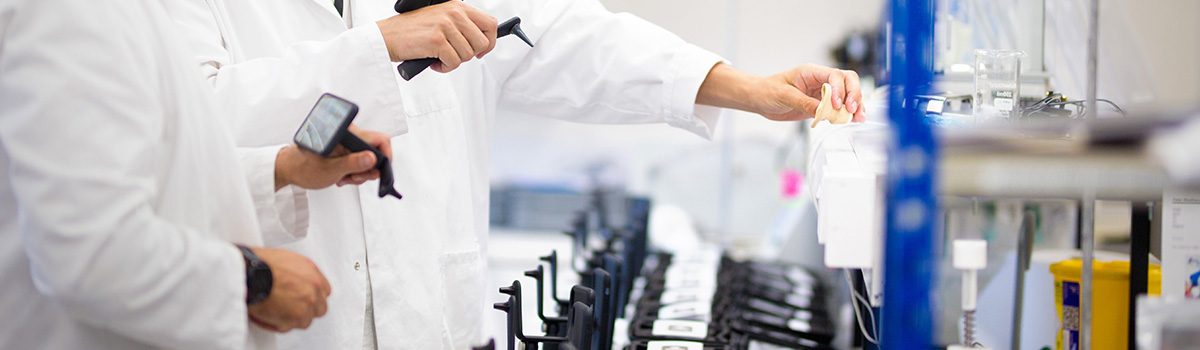
LSR射出成形のデメリット
LSR (液体シリコーンゴム) 射出成形には多くの利点がありますが、この製造プロセスを使用するかどうかを決定する際に考慮すべき欠点もいくつかあります。 LSR 射出成形の主な欠点をいくつか示します。
高い初期投資
LSR 射出成形の主な欠点の XNUMX つは、装置と金型のセットアップに必要な初期投資が高額であることです。 LSR 射出成形機と工具は、特にカスタム金型や小規模生産の場合、高価になる可能性があります。 このため、予算が少ない企業や需要が限られている製品では、LSR 射出成形の費用対効果が低くなる可能性があります。
限られた材料の選択
LSR 材料は優れた物理的特性を備えていますが、材料の選択は限られています。 従来の熱可塑性プラスチックとは異なり、LSR 射出成形で使用できるシリコーンベースの材料は限られています。 特定の用途や製品に適した材料を見つけるのは困難な場合があります。
より長い硬化時間
LSR 射出成形には、従来の射出成形プロセスよりも長い硬化時間が必要です。 液体シリコーンは硬化して固化するのに時間がかかるため、生産時間が長くなり、効率が低下する可能性があります。 さらに、修復時間が長くなると、複雑または複雑な形状の特定の部品の製造が困難になる可能性があります。
専門的なスキルセットが必要
LSR 射出成形には、液体シリコーンの特性と挙動についての深い理解など、専門的な知識と専門知識が必要です。 このため、企業にとって、特に LSR 射出成形があまり一般的ではない地域では、装置の操作と保守を行う資格のある人材を見つけることが困難になる可能性があります。
成形の課題
LSR 射出成形には、高品質の部品を確実に製造するために対処しなければならないいくつかの課題が存在します。 たとえば、液体シリコーンはバリやバリが発生しやすく、最終製品の品質に影響を与えます。 さらに、部品を金型から取り外すために離型剤が必要になる場合があり、最終製品の表面仕上げや機械的特性に影響を与える可能性があります。
限定された表面仕上げ
液体シリコーンは特定のコーティングや仕上げと互換性がないため、LSR 射出成形では表面仕上げが制限されます。 このため、特定の製品や用途に対して望ましい美的特性や機能的特性を達成することが困難になる可能性があります。
限られた色のオプション
LSR 射出成形では、液体シリコーン材料が一般的に半透明または不透明であるため、色の選択肢も限られています。 いくつかの着色添加剤は入手可能ですが、最終製品の物理的特性や一貫性に影響を与えずに材料に組み込むのは難しい場合があります。
部品汚染の可能性
LSR 射出成形では、装置や金型が適切にメンテナンスまたは洗浄されていない場合、汚染のリスクが生じる可能性があります。 汚染は最終製品の物理的特性に影響を与え、時間の経過とともに欠陥や故障につながる可能性があります。
LSR射出成形の精度と精度
LSR (液体シリコーン ラバー) 射出成形では、精度と正確さが重要な要素であり、厳しい公差と厳格な仕様を備えた高品質のシリコーン ラバー部品が製造されます。 LSR 射出成形の精度と精度に寄与する重要な要素をいくつか示します。
- 金型の設計と構築: 金型は、部品の最終的な形状と寸法を決定するため、LSR 射出成形プロセスの重要なコンポーネントです。 最終部品が所望の仕様を確実に満たすように、金型は正確に設計および構築されなければなりません。 誤差を最小限に抑えて精度を確保するには、金型は高品質の素材で作られ、厳しい公差に従って構築される必要があります。
- 射出ユニット制御: 射出ユニットは、金型への液状シリコーンゴムの流れを制御します。 正確で一貫性のある部品を製造するには、射出ユニットの正確な制御が不可欠です。 材料が正しい速度、圧力、量で金型キャビティに射出されるように、射出ユニットを校正および制御する必要があります。
- 温度制御: 温度制御は、材料の粘度と硬化時間に影響を与えるため、LSR 射出成形プロセスでは重要な要素です。 材料が金型にスムーズに流れ込み、正しい速度で硬化プロセスが行われるように、温度を注意深く制御する必要があります。
- 材料品質: LSR 材料の品質は、最終部品の精度と精度を達成するために非常に重要です。 適切な硬化と一貫性を確保するには、材料に不純物が含まれておらず、正しい比率で混合されている必要があります。
- 後処理: LSR 射出成形の精度と精度を達成するには、トリミングや検査などの後処理ステップが不可欠です。 部品を正しい寸法にトリミングし、欠陥や欠陥がないか検査する必要があります。
LSR 射出成形は優れた精度と精度を提供し、厳しい公差と厳密な仕様の部品の作成を可能にします。 一貫した品質で、部品から細部までのばらつきを最小限に抑えた部品を製造できます。 このため、医療機器、自動車部品、電子製品など、精度と精度が重要な用途に最適です。
生産時間の短縮
液状シリコーンゴム (LSR) 射出成形は、耐薬品性、耐温度性、生体適合性などの優れた特性を備えた高品質のシリコーン製品を製造する一般的な製造プロセスです。 ただし、LSR 射出成形の生産時間が遅くなる場合があり、そのため製造プロセスが遅れ、コストが増加する可能性があります。 LSR 射出成形の生産時間を短縮する方法をいくつか紹介します。
- 効率的な射出成形機を使用する: 生産をスピードアップするには、適切な機械を選択することが重要です。 品質を犠牲にすることなく、LSR を迅速に注入できるデバイスを探してください。 サイクルタイムを短縮し、生産効率を向上させるために、射出速度の高いマシンの使用を検討してください。
- 金型設計の最適化: 金型設計も、LSR 射出成形の生産時間に影響を与える重要な要素です。 LSR が効率的かつ均一に射出されるように金型設計を最適化します。 LSR の流れを改善し、サイクル タイムを短縮するには、より大きなゲート サイズの金型の使用を検討してください。
- ホット ランナー システムを使用する: ホット ランナー システムは、射出プロセス全体を通じて LSR を理想的な温度に保つことで、LSR 射出成形の効率を向上させることができます。 これにより、サイクルタイムが短縮され、最終製品の品質が向上します。
- LSR を予熱する: 射出前に LSR を予熱すると、生産時間の短縮にも役立ちます。 LSR を予熱すると、流れが改善され射出時間が短縮され、サイクル タイムの短縮と効率の向上につながります。
- 硬化時間を短縮する: LSR の硬化時間を短縮するには、硬化温度を上げるか、より速い硬化剤を使用します。 ただし、硬化時間を短縮しながら最終製品の品質を維持することが不可欠です。
費用効果の高い製造
液体シリコーン ゴム (LSR) 射出成形は、高品質のシリコーン製品を製造するための一般的な製造プロセスです。 ただし、LSR 射出成形のコストは、主に大量生産する場合にメーカーにとって懸念されることがあります。 LSR 射出成形をよりコスト効率よく行う方法をいくつか紹介します。
- 製品設計の最適化: 製品設計は、LSR 射出成形のコストに大きな影響を与える可能性があります。 設計を最適化することで、メーカーは使用する材料の量を削減でき、全体の生産コストを下げることができます。 さらに、手順を簡素化することで金型の複雑さが軽減され、工具コストも削減できます。
- 自動化プロセスの使用: 自動化プロセスを使用すると、LSR 射出成形の効率が向上し、人件費を削減できます。 ロボットハンドリングや自動材料供給などの自動プロセスにより、サイクルタイムが短縮され、全体的な生産性が向上します。
- 高品質の金型を使用する: 高品質の金型を使用すると、LSR 射出成形の効率が向上し、無駄が削減されます。 耐久性があり高精度の金型を使用すると、頻繁な修理や交換の必要性が減り、長期的にはコストを節約できます。
- 生産プロセスの最適化: 生産プロセスを最適化すると、無駄が削減され、効率が向上し、コストが削減されます。 これには、材料の無駄を最小限に抑え、サイクル タイムを短縮するために、射出速度、温度、圧力などの射出成形パラメータを最適化することが含まれます。
- 材料の無駄を削減: 材料の無駄を削減すると、LSR 射出成形のコストを大幅に削減できます。 これは、精密計量システムを使用して使用する材料を制御し、金型が適切に設計および最適化されて余分な材料が最小限に抑えられるようにし、余分な材料を将来の使用のためにリサイクルすることによって実現できます。
高品質な表面仕上げ
液状シリコーンゴム (LSR) 射出成形は、耐熱性、耐薬品性、生体適合性などの優れた特性を備えた高品質のシリコーン製品を製造するための一般的な製造プロセスです。 これらの特性に加えて、高品質の表面仕上げを達成することは、多くの用途にとって不可欠です。 LSR 射出成形で高品質の表面仕上げを実現する方法をいくつか紹介します。
- 高品質の金型を使用する: 高品質の表面仕上げを実現するには、高品質の金型が不可欠です。 型は高品質の素材で作られ、表面が滑らかに仕上げられている必要があります。 さらに、表面仕上げに悪影響を与える可能性のある気泡の形成を防ぐために、適切な通気を備えた金型を設計する必要があります。
- 高品質の LSR 材料を使用する: 高品質の LSR 材料を使用すると、表面仕上げも向上します。 高品質の LSR 材料は粘度が低くなるように配合されているため、材料の流れが改善され、フロー マークやその他の欠陥の発生が軽減されます。
- 射出成形パラメータの最適化: 温度、射出速度、圧力などのパラメータを最適化すると、表面仕上げも改善できます。 射出速度は、材料の蓄積や縞模様を防ぐために最適化する必要があります。 材料の劣化や反りを避けるために、温度と圧力も注意深く制御する必要があります。
- 成形後のプロセスを使用する: トリミング、研磨、コーティングなどの成形後のプロセスによっても、LSR 製品の表面仕上げを向上させることができます。 トリムでは、パーツからバリや余分な材料を取り除くことができます。 研磨すると、表面の欠陥を滑らかにすることができます。 コーティングは追加の保護層を提供し、キャラクターの外観を向上させることができます。
- 射出成形機の定期メンテナンスを実施する: 安定した高品質の生産を確保するには、定期的なメンテナンスが不可欠です。 汚染を防ぐためにデバイスを定期的に清掃し、金型に摩耗や損傷の兆候がないか確認する必要があります。
医療用途向けLSR射出成形
LSR 射出成形は、液状シリコーンゴム (LSR) を金型に射出して最終製品を作成する製造プロセスです。 このプロセスは、LSR のユニークな特性により医療業界で広く使用されており、医療用途に理想的な素材となっています。
LSR は生体適合性があり、低刺激性の素材であり、有害な化学物質を含まないため、医療機器やインプラントに安全です。 また、細菌の増殖に強く、滅菌が容易であるため、清潔さと感染制御が最重要視される医療現場では非常に重要です。
LSR 射出成形は、正確かつ効率的なプロセスであり、公差が厳しい複雑で入り組んだ医療部品の作成を可能にします。 これは、カテーテル、ペースメーカー部品、人工関節などの埋め込み型デバイスの製造など、精度と精度が重要な医療用途において重要です。
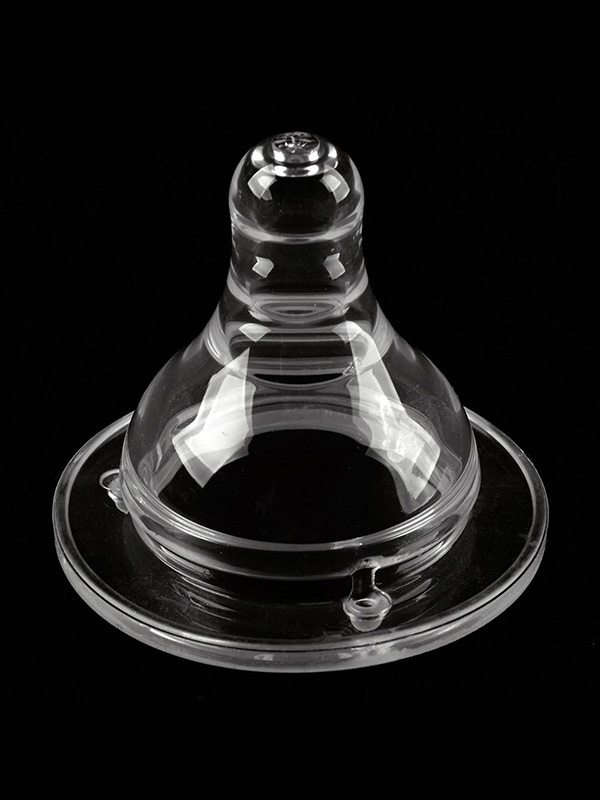
生体適合性と精度に加えて、LSR は優れた機械的特性を備えており、医療用途に適した材料です。 LSR は摩耗や損傷に強く、極端な温度に耐え、優れた電気絶縁特性を備えています。 これらの特性により、LSR は次のような幅広い医療用途で人気のある材料となっています。
- カテーテルとチューブ: LSR は、その生体適合性、柔軟性、耐ねじれ性により、カテーテルとチューブの製造によく使用されます。
- 埋め込み型デバイス: LSR は、その耐久性と生体適合性により、人工関節、ペースメーカー コンポーネント、手術器具などの埋め込み型デバイスの製造に一般的に使用されています。
- 医療用シールとガスケット: LSR は、極端な温度に対する耐性と長期にわたってその特性を維持できるため、それらの製造によく使用されます。
LSR 射出成形は、医療機器およびコンポーネントを製造するための非常に多用途かつ効率的なプロセスです。 そのユニークな特性により、幅広い医療用途に理想的な材料となっており、その精度と正確さにより、製品が最高の品質と安全性基準を満たしていることが保証されます。
自動車産業におけるLSRの使用
液状シリコーンゴム (LSR) は、自動車部品に理想的な材料となる独自の特性により、自動車業界で幅広い用途に使用されることが増えています。 LSR は射出成形によって形成される合成エラストマーであり、複雑で複雑な自動車部品の製造において高い精度と精度を実現します。
LSRは機械的特性に優れており、耐久性、耐高温性、長寿命が要求される自動車部品に適しています。 LSR は摩耗、磨耗、引き裂きに強いため、シール、ガスケット、O リングなど、絶えず摩擦を受ける自動車部品に最適です。
自動車業界における LSR の最も重要な利点の XNUMX つは、極端な温度変化に耐えられる能力です。 LSRは高温環境でも低温環境でも効率よく作動するため、エンジン部品、排気システム、ターボチャージャーホースなど、高温にさらされる自動車部品に最適な材料です。
自動車産業における LSR のもう XNUMX つの重要な利点は、液体やガスに対して優れたシールを提供できることです。 LSR は、高圧下でも信頼性の高いシールを提供する耐久性の高い材料であり、自動車のガスケットやシールでの使用に最適です。
LSR は優れた電気絶縁特性も備えているため、コネクタ、センサー、点火システムなどの自動車産業の電気部品での使用に最適です。 LSR は高電圧に耐えることができ、アーク放電や短絡のリスクが低いため、電気用途にとって信頼できる材料となります。
全体として、LSR には、耐久性、高温耐性、優れたシール性、電気絶縁性など、自動車部品に理想的な材料となる多くの利点があります。 メーカーがコスト削減と生産効率の向上を図りながら自社製品の信頼性、安全性、性能を向上させることを目指しているため、自動車業界におけるLSRの使用は今後数年間で増加すると予想されます。
エレクトロニクス産業におけるLSRの応用例
液状シリコーンゴム (LSR) は、その優れた熱安定性、耐薬品性、電気絶縁特性により、エレクトロニクス産業で広く使用されている材料です。 電子部品の封止、封止、ポッティングなど様々な用途に使用されています。
エレクトロニクス業界における LSR の主な用途の XNUMX つは、集積回路 (IC)、センサー、コネクタなどの電子コンポーネントのカプセル化です。 カプセル化は、腐食や性能低下の原因となる湿気、埃、その他の汚染物質からこれらのコンポーネントを保護します。 LSR は、粘度が低く、引き裂き強度が高く、さまざまな基材に対する優れた接着力を備えているため、カプセル化に理想的な材料です。 また、電気用途に不可欠な優れた誘電特性も備えています。
LSR はまた、電子部品を密閉して湿気の侵入やその他の汚染物質を防ぎます。 この材料は、さまざまな電子部品に合わせてカスタムの形状やサイズに成形できます。 LSR シールは、海洋や自動車用途など、極端な温度や化学物質への曝露に耐える必要がある過酷な環境でよく使用されます。
ポッティングは、エレクトロニクス業界における LSR のもう XNUMX つの重要な用途です。 ポッティングでは、衝撃、振動、湿気などの環境要因からコンポーネントを保護するために、コンポーネントの周囲の空洞を液体材料で満たします。 LSR は、粘度が低いため複雑な形状の周囲に容易に流れることができ、熱安定性が高く、高温でもコンポーネントが確実に保護されるため、ポッティングに理想的な材料です。
LSR は、リモコン、電卓、キーボードなどの電子機器の標準コンポーネントであるキーパッドやボタンの製造にも使用されます。 高度にカスタマイズ可能なこの材料は、異なる質感や硬度レベルを備えたさまざまな形状やサイズに成形できます。
航空宇宙産業における LSR の応用
液体シリコーンゴム (LSR) は、高い熱安定性、耐薬品性、優れた機械的特性などの独特の特性により、航空宇宙産業で広く使用されている材料です。 電子部品のシール、接着、ポッティングなどのさまざまな航空宇宙用途や、ガスケット、O リング、その他の重要な部品の製造に使用されています。
航空宇宙産業における LSR の主な用途の XNUMX つは、航空機コンポーネントのシールと接着です。 この材料は複雑な形状やサイズに簡単に成形できるため、燃料タンク、エンジン部品、電気システムの梱包や接続に最適です。 LSR はさまざまな基材に優れた接着力を発揮し、極端な温度や化学物質への曝露などの過酷な環境条件に耐えることができます。
LSR は、航空宇宙用途の電子部品のポッティングにも使用されます。 この材料は粘度が低いため、複雑な形状の周囲でも容易に流れることができ、敏感な電子部品を振動、衝撃、湿度や温度の変化などの環境要因から優れた保護を提供します。
航空宇宙産業における LSR のもう XNUMX つの重要な用途は、ガスケット、O リング、その他のシール部品の製造です。 LSR は、温度や耐圧などの特定の要件を満たすようにカスタマイズでき、従来のゴム材料が適さない高性能アプリケーションでよく使用されます。
LSR は、シールや接着の用途に加えて、レンズやディフューザーなどの航空機の照明コンポーネントの製造にも使用されます。 この材料の光学的特性は、優れた光透過性を提供するため、これらの用途に理想的な選択肢となり、その機械的特性により、耐久性と、紫外線や温度変動などの環境要因に対する耐性が保証されます。
食品グレードの LSR 射出成形
食品グレードの液状シリコーンゴム (LSR) は、キッチン用品、ベビー用品、食品包装など、食品と接触する射出成形製品に使用される特殊な材料です。 食品安全に関する厳しい規制基準を満たした高純度の素材です。
食品グレード LSR の主な利点の 450 つは高温に対する耐性であり、ヘラ、スプーン、焼き型などのキッチン用品での使用に最適です。 最大 232°F (XNUMX°C) の温度に耐えることができるため、調理やベーキング用途にも安全です。
食品グレードの LSR は、おしゃぶりや哺乳瓶の乳首などのベビー用品の製造にも使用されています。 これらの製品は、幼児にとって安全であることを保証するために、厳格な安全基準を満たしている必要があります。 LSR は、優れた生体適合性、柔らかさ、耐久性を備えているため、これらの用途に理想的な素材です。
食品グレード LSR のもう XNUMX つの重要な用途は、食品包装です。 さまざまな形状や大きさに成形できるため、食品保存容器や製氷皿などの製造に最適です。 LSR は耐薬品性と優れた密封特性を備えており、パッケージの内容物を新鮮に保ち、汚染を防ぎます。
食品グレードの LSR は、歯科印象材や補綴装置などの医療製品の製造にも使用されます。 この材料の生体適合性、耐久性、細部の再現能力により、これらの用途には理想的な選択肢となります。
全体として、食品グレード LSR は、キッチン用品、ベビー用品、食品包装など、食品と接触する製品の製造に最適な特殊素材です。 高温に対する耐性、生体適合性、優れたシール特性により、これらの用途に理想的な材料となっています。 この材料は生体適合性があり、細部まで再現できるため、医療製品の製造にも使用されています。
LSR ベビー用品用射出成形
LSR(液体シリコーンゴム)射出成形は、シリコーンゴム製の幅広い製品の製造に使用される製造プロセスです。 LSR 射出成形の最も人気のある用途の XNUMX つはベビー用品の製造です。これは、安全性、耐久性、掃除のしやすさなど、LSR がベビー用品に提供する多くの利点によるものです。
LSR射出成形は、液状のシリコーンゴムを金型に注入し、硬化・固化させます。 このプロセスにより、複雑な形状やデザインの作成、さまざまな色やテクスチャの使用が可能になります。 その結果、柔らかく、柔軟性があり、熱や化学薬品に耐性のある完成品が得られます。
ベビー用品向け LSR 射出成形の主な利点の XNUMX つは安全性です。 シリコーンゴムは非毒性、低刺激性で、BPA、フタル酸エステル、PVC などの有害な化学物質を含みません。 そのため、おしゃぶり、おしゃぶり、哺乳瓶の乳首など、赤ちゃんが触れる製品によく選ばれています。 LSR 射出成形では、赤ちゃんのデリケートな肌を傷つける可能性のある鋭いエッジや継ぎ目のない製品を作成することもできます。
耐久性も LSR 射出成形の利点です。 シリコーンゴムは摩耗や破れに強いため、おしゃぶりやおしゃぶりなど、頻繁に使用したり乱暴に扱われる製品に最適です。 柔らかく柔軟な素材なので、落としても割れたりひび割れたりしにくく、赤ちゃんの怪我のリスクを軽減します。
LSR 射出成形では洗浄も簡単で、頻繁に消毒する必要があるベビー用品には不可欠です。 シリコーンゴムは非多孔質で、石鹸と水で簡単に洗浄でき、食器洗い機に入れて徹底的に洗浄できます。
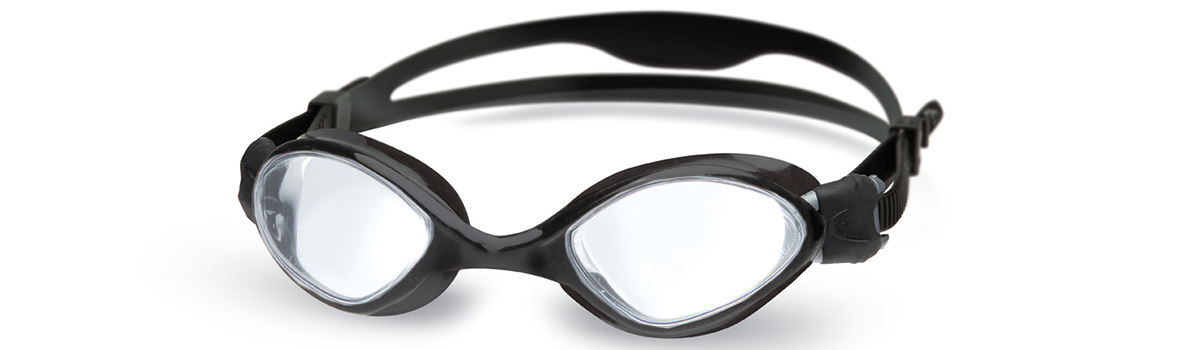
LSR スポーツ用品用射出成形
LSR (液体シリコーンゴム) 射出成形は、スポーツ用品を含むさまざまな製品で一般的な製造プロセスです。 LSR 射出成形は、柔軟性、耐久性、極端な温度や環境条件への耐性など、スポーツ用品の製造にいくつかの利点をもたらします。
スポーツ用品における LSR 射出成形の主な利点の XNUMX つは柔軟性です。 シリコーンゴムは柔らかくて柔軟性のある素材で、さまざまな形状やデザインに成形できます。 防具や用具のグリップなど、身体にフィットした使い心地の良いスポーツ用品の製作が可能になります。
スポーツ用品における LSR 射出成形のもう XNUMX つの利点は、耐久性です。 シリコーンゴムは摩耗や損傷に強いため、ボール、パドル、ラケットなど、頻繁に使用したり乱暴に扱われる製品に最適です。 この素材は、極端な温度や日光や水への暴露などの環境条件にも、劣化したり劣化したりすることなく耐えることができます。
LSR 射出成形では、衝撃や摩耗に強い製品の作成も可能です。 この材料の高い引き裂き強度と破断伸びは、ヘルメットライナー、マウスガード、すね当てなどの保護具の製造に最適です。 さらに、LSR 射出成形により、ハンドルやラケット グリップなどの用具の滑り止め表面やグリップを作成することができます。
スポーツ用品向け LSR 射出成形のもう XNUMX つの利点は、洗浄とメンテナンスが簡単な製品を作成できることです。 シリコーンゴムは非多孔質で、湿らせた布で簡単に拭き取るか、石鹸と水で洗うことができます。 そのため、ジム用品やヨガマットなど、頻繁に使用する製品に最適な素材です。
LSR 家庭用品射出成形
LSR 射出成形は、液体シリコーンゴム (LSR) を使用して成形部品を作成する製造プロセスです。 このプロセスは、キッチン用品、ベビー用品、バスルームアクセサリーなどの高品質の家庭用品の製造に最適です。 LSR 射出成形には、高精度、一貫性、耐久性などの利点があり、厳しい公差と優れた性能を必要とする家庭用製品に最適です。
LSR 射出成形プロセスには、液体シリコーン材料を金型に射出することが含まれます。 次に、金型を加熱すると、液体シリコーン材料が硬化して目的の形状に固まります。 このプロセスは高度に自動化されており、厳しい公差と優れた表面仕上げを備えた一貫した部品生産が可能になります。 このプロセスでは、他の成形プロセスでは達成が困難または不可能な複雑な形状の製造も可能になります。
LSR 射出成形を使用して一般的に製造される家庭用品には、スパチュラや調理用スプーンなどの台所用品、おしゃぶりや哺乳瓶の乳首などのベビー用品、シャワーヘッドや歯ブラシなどのバスルーム付属品などがあります。 これらの製品には、安全性と性能基準を満たすために精密な成形が必要ですが、LSR 射出成形は、これらの基準を満たす高品質の家庭用品を製造するために必要な精度と一貫性を提供します。
家庭用品における LSR 射出成形の主な利点の XNUMX つは、その耐久性です。 LSR 材料は高温、紫外線、化学物質に対する耐性があり、長期耐久性のある製品に最適です。 さらに、LSR素材は低刺激性なので、肌に触れるベビー用品やその他の家庭用品にも安心してご使用いただけます。
LSR 射出成形のもう XNUMX つの利点は、優れた表面仕上げの部品を製造できることです。 このプロセスにより、傷や擦り傷に強い、滑らかで光沢のある仕上げの機能を作成できます。 このため、LSR 射出成形は、キッチン用品やバスルーム付属品など、魅力的な外観が必要な家庭用品の製造に最適です。
他のゴム成形品との比較
LSR (液体シリコーンゴム) 射出成形は、さまざまなゴム製品を製造するための一般的な製造プロセスであり、他のタイプのゴム成形プロセスに比べていくつかの利点があります。 LSR 射出成形とさまざまな種類のゴム成形の比較を以下に示します。
- 圧縮成形: 圧縮成形は、大型部品や複雑な形状の部品を製造するための標準プロセスです。 圧縮成形では、加熱した金型にあらかじめ計量したゴムを入れ、ゴムが硬化するまで圧力を加えます。 LSR 射出成形と比較して、圧縮成形はプロセスに時間がかかり、不均一な圧力分布により部品の寸法にばらつきが生じる可能性があります。 一方、LSR 射出成形では、部品の寸法を正確に制御でき、公差が厳しい複雑な形状を製造できます。
- トランスファー成形: トランスファー成形は圧縮成形に似ていますが、プランジャーを使用してゴムを射出ポットから金型に移す必要があります。 トランスファーモールドは高精度な部品を製造することができ、中型部品の製造に適しています。 ただし、LSR 射出成形よりも時間がかかり、コストも高くなります。
- 射出成形: 射出成形は、溶融したゴムを高圧で金型に射出するプロセスです。 射出成形は部品を迅速かつ正確に製造できますが、複雑なデザインや詳細を備えた部品の製造には適さない場合があります。 射出成形と比較して、LSR 射出成形では、正確な詳細と複雑なデザインやパターンを備えた部品を作成できます。
- 押出成形: 押出成形は、ホース、シール、ガスケットなどの連続断面プロファイルを持つ部品を製造するために使用されるプロセスです。 押出成形は高速でコスト効率の高いプロセスですが、複雑な形状や公差が厳しい部品の製造には適さない場合があります。 一方、LSR 射出成形は、複雑な形状と厳しい公差を持つ部品を作成できるため、医療機器、自動車部品、消費財などの製品の製造に最適です。
LSR 射出成形の設計上の考慮事項
LSR 射出成形用の部品を設計する際には、製造プロセスを確実に成功させるために、いくつかの重要な考慮事項を考慮する必要があります。 これらの考慮事項には、材料の選択、金型設計、部品の形状、成形後の操作が含まれます。
LSR 射出成形用の部品を設計する場合、材料の選択は重要な考慮事項です。 液状シリコーンゴム材料にはさまざまなデュロメーター、粘度、色があり、最終製品の望ましい特性を達成するには、適切な材料を選択することが不可欠です。 材料の選択では、耐熱性、耐薬品性、耐久性などの用途要件を考慮する必要があります。
LSR 射出成形では、金型の設計も重要な考慮事項です。 金型の設計は、必要な部品形状を生成し、材料の流れ、冷却、取り出しを考慮して最適化する必要があります。 金型は、適切なゲートおよび通気システムを備えて設計され、高い生産率を達成するために十分なキャビティを備えている必要があります。
LSR 射出成形用の部品を設計する場合、部品の形状も重要です。 最終製品の望ましい機械的特性と美観を実現するには、部品の形状を最適化する必要があります。 これには、抜き勾配を使用して金型からの取り出しを容易にし、リブを使用して剛性を高め、ゲートおよび通気システムを配置して材料の流れを最適化することが含まれます。
LSR 射出成形用の部品を設計する場合は、成形後の操作も考慮する必要があります。 成形後の作業には、トリミング、バリ取り、二次組立作業が含まれる場合があります。 これらの操作は、無駄を最小限に抑え、人件費を削減するために最適化する必要があります。
LSR 射出成形のその他の設計上の考慮事項には、アンダーカットの使用、エジェクター ピンの配置、パーティング ラインの使用などが含まれる場合があります。 最終製品が希望の仕様を満たし、効率的に製造できるようにするには、設計プロセス中にこれらの要素を考慮する必要があります。
LSR 射出成形の環境と持続可能性の利点
LSR 射出成形は、従来の製造プロセスに比べて環境および持続可能性に関するいくつかの利点をもたらし、環境フットプリントの削減を目指す企業にとって魅力的な選択肢となっています。
LSR 射出成形の主な環境上の利点の XNUMX つは、廃棄物の発生が少ないことです。 液体シリコーンゴムを金型に直接注入し、硬化して目的の形状を形成するため、このプロセスでは廃棄物がほとんど発生しません。 これは、大量のスクラップ材料が発生する機械加工や鋳造などの他の製造プロセスとは対照的です。
LSR 射出成形には、エネルギー消費と温室効果ガスの排出を削減する可能性もあります。 このプロセスは高度に自動化できるため、手作業の必要性が減り、エネルギー消費が削減されます。 LSR 射出成形は、射出成形やブロー成形などの他の成形プロセスよりも必要なエネルギーが少ない低温プロセスです。 これにより、大幅なエネルギー節約と温室効果ガス排出量の削減が可能になります。
LSR 射出成形の持続可能性に関するもう XNUMX つの利点は、リサイクル材料を使用できる可能性があることです。 LSR 材料はリサイクルして再利用できるため、新しい材料の必要性が減り、廃棄物の発生が削減されます。 さらに、LSR 製品の寿命が長いということは、再利用または再利用が可能であることを意味し、廃棄物がさらに削減され、製品のライフサイクルが延長されます。
LSR 射出成形では、製造における有害な化学物質の使用も削減できます。 LSR 材料には通常、フタル酸エステル、BPA、PVC などの有毒化学物質が含まれていないため、労働者や消費者にとってより安全です。 さらに、LSR 射出成形で使用される低温プロセスには、有害な溶剤やその他の化学物質が必要ありません。
LSR 射出成形の将来
LSR 射出成形の将来は明るいです。このプロセスには従来の製造方法に比べていくつかの利点があります。 LSR 射出成形は、技術の進歩に伴い、さらに効率的でコスト効率が高く、環境に優しいものになります。
LSR 射出成形の将来にとって最も有望な分野の 3 つは、積層造形技術の使用です。 XNUMXD プリンティングとも呼ばれる積層造形では、従来の製造方法では製造が困難または不可能だった複雑な形状やカスタマイズされた部品の作成が可能になります。 技術が向上するにつれて、LSR 射出成形は積層造形とより統合され、より高度で革新的な製品の製造が可能になります。
LSR 射出成形の今後の開発分野のもう XNUMX つは、先端材料の使用です。 新しい材料が開発されると、LSR 射出成形では、耐久性、耐熱性、生体適合性の向上など、その独自の特性を活用できます。 これにより、医療用インプラントや高性能産業用コンポーネントなど、さらに特殊な製品が可能になります。
LSR 射出成形プロセスへの自動化とロボット工学の継続的な統合も、将来的には重要なトレンドとなる可能性があります。 自動化により、効率が向上し、人件費が削減され、最終製品の一貫性と品質が向上します。 技術が向上するにつれて、LSR 射出成形はさらに自動化され、ロボット工学と人工知能が製造においてより重要な役割を果たすようになるでしょう。
最後に、持続可能性と環境への責任は、今後も LSR 射出成形の重要な推進力となるでしょう。 消費者や企業が廃棄物の削減と環境への影響を最小限に抑えることにますます注目するようになり、LSR射出成形は、環境負荷が低く高品質の製品を製造するためのさらに魅力的な選択肢になるでしょう。 より持続可能な材料の開発、材料のリサイクルと再利用、再生可能エネルギー源の使用は、LSR 射出成形の将来においてより重要な役割を果たす可能性があります。
結論:
結論として、LSR 射出成形は信頼性が高く効率的な製造プロセスであり、さまざまな業界にとって多くの利点があります。 LSR は独特の性能特性を備えた多用途の材料であり、複数の用途に最適です。 LSR テクノロジーの継続的な進歩と持続可能な製造方法への需要の増加により、LSR 射出成形の将来は明るいです。