プラスチック射出成形の基礎
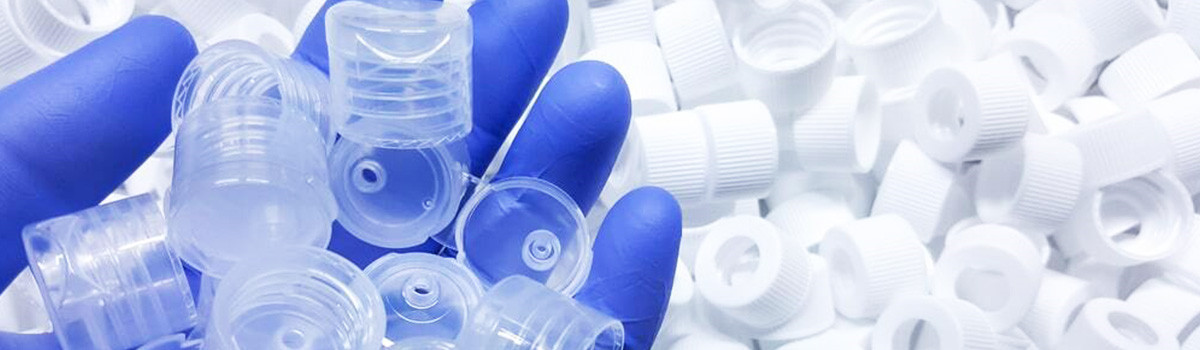
射出成形プロセスとその仕組みを学びましょう。
プラスチック射出成形は、熱可塑性プラスチックのペレットを大量の複雑な部品に変換する一般的な製造技術です。 射出成形プロセスはさまざまなプラスチック材料に適しており、現代生活に不可欠な側面であり、電話ケース、電子機器の筐体、玩具、さらには自動車部品さえも射出成形プロセスなしでは不可能です。 この記事では、射出成形の基本を詳しく説明し、射出成形がどのように機能するかを説明し、3D プリントとの違いを説明します。
プラスチック射出成形の基本とは何ですか?
プラスチック射出成形プロセスの基本には、製品デザインの作成、製品デザインに適合する金型の作成、プラスチック樹脂ペレットの溶解、および圧力を使用して溶解したペレットを金型に射出することが含まれます。
以下の各ステップの内訳をご覧ください。
1. プロダクトデザインの作成
設計者 (エンジニア、金型メーカーなど) は、射出成形プロセスに固有の基本的な設計ガイドラインに従って、部品を (CAD ファイルまたはその他の転送可能な形式で) 作成します。 設計者は、プラスチック射出成形金型の成功率を高めるために、次の機能を設計に組み込むように努める必要があります。
*ねじ付きインサート/ファスナー用のボス
*一定またはほぼ一定の壁厚
*さまざまな壁厚間のスムーズな移行
*厚い部分の中空空洞
*丸みを帯びたエッジ
*垂直壁の抜き勾配
※サポート用リブ
*フリクションフィット、スナップフィットジョイント、その他のノンファスナー接合機能
*リビングヒンジ
さらに、設計者は、設計上の欠陥を減らすために、次の機能を最小限に抑える必要があります。
*壁の厚さが不均一、または特に薄い/厚い壁
*抜き勾配のない垂直壁
※突然の形状変化(角、穴等)
*リブのデザインが不十分
*アンダーカット/オーバーハング
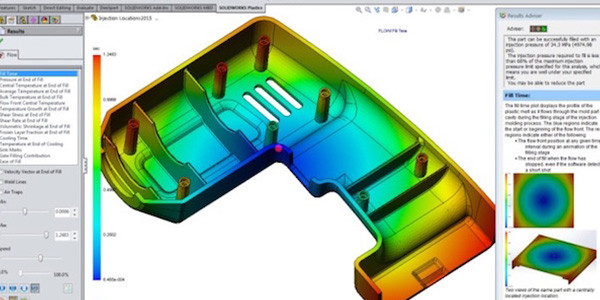
2. 製品設計に合わせた金型の製作
高度なスキルを持った機械工や工具メーカーが、製品設計を使用して、射出成形機用の金型を製造します。 ツーリング金型 (単にツールとも呼ばれます) は、射出成形機の心臓部であり魂です。 これらは、製品設計のためのネガティブ キャビティと、スプルー、ランナー、ゲート、ベント、エジェクター システム、冷却チャネル、可動コンポーネントなどの追加機能を含むように慎重に設計されています。 ツーリング金型は、6063 アルミニウム、P20 鋼、H13 鋼、420 ステンレス鋼など、数万回 (場合によっては数十万回) の加熱および冷却サイクルに耐えられる特定グレードの鋼およびアルミニウムで作られています。 金型の製造プロセスは、製造と承認の両方を含めて完了までに 20 週間以上かかり、このステップは射出成形の中で最も長い部分となります。 これは射出成形の中で最も高価な部分でもあり、金型を一度製造したら、追加コストを発生させずに大幅に変更することはできません。
3. プラスチック樹脂ペレットを溶かす
オペレーターが完成した金型を入手したら、それを射出成形機に挿入し、金型を閉じて射出成形サイクルを開始します。
プラスチック顆粒はホッパーとバレルに供給されます。 往復運動するスクリューが引き戻され、材料がスクリューとバレルの間の空間に滑り込みます。 次に、スクリューが前方に押し込まれ、材料がバレル内に押し込まれ、ヒーターバンドに近づき、そこで材料は溶融プラスチックに溶けます。 溶解温度は材料の仕様に従って一定に保たれるため、バレルや金型自体の劣化は起こりません。
4. 圧力を使用して溶解したペレットを金型に注入する
往復スクリューは、この溶融プラスチックをノズルに押し込みます。ノズルは、金型スプルー ブッシュとして知られる金型のくぼみ内に設置されています。 移動するプラテンの圧力によって金型とノズルがしっかりと密着し、プラスチックが漏れることがありません。 溶融したプラスチックはこのプロセスによって加圧され、金型キャビティのすべての部分に入り込み、キャビティの空気が金型の通気口から排出されます。
射出成形機のコンポーネント
射出成形機のコンポーネントには、ホッパー、バレル、往復スクリュー、ヒーター、可動プラテン、ノズル、金型、金型キャビティが含まれます。
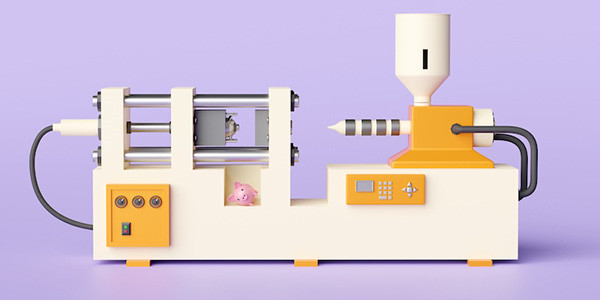
以下のリストにある各射出成形コンポーネントの詳細情報:
*ホッパー: プラスチック顆粒が機械に供給される開口部。
*たる: 射出成形機の外側ハウジング。往復スクリューとプラスチック顆粒が入っています。 バレルはいくつかのヒーターバンドで包まれており、先端には加熱されたノズルが付いています。
※往復ネジ: プラスチック材料がバレル内で溶けるときにプラスチック材料を搬送し、加圧するコルク抜きコンポーネント。
*ヒーター: 加熱バンドとしても知られるこれらのコンポーネントは、プラスチック顆粒に熱エネルギーを提供し、プラスチック顆粒を固体から液体に変えます。 形状。
*可動プラテン: 可動コンポーネントは金型コアに接続されており、両方の金型半部を気密に保つために圧力を加え、完成品が露出するときに金型コアを解放します。
*ノズル: 加熱されたコンポーネントは、金型キャビティへの溶融プラスチックの標準的な出口を提供し、温度と圧力の両方を可能な限り安定に保ちます。
*型: 金型キャビティと、エジェクター ピン、ランナー チャネル、冷却チャネル、ベントなどの追加のサポート機能を含むコンポーネント。少なくとも、金型は、固定側 (バレルに近い) と金型の XNUMX つの半分に分離されます。コア(移動プラテン上)。
*金型キャビティ: ネガティブスペースは、溶融プラスチックで満たされると、サポート、ゲート、ランナー、スプルーなどを含む目的の最終部品に成形されます。
射出成形はどのように機能しますか?
スプルー、ランナー、ゲートなどを含む金型にプラスチックが充填されると、金型は設定温度に保たれ、材料が部品形状に均一に固化します。 冷却中は保持圧力が維持され、バレルへの逆流を止め、収縮効果を軽減します。 この時点で、次のサイクル (またはショット) に備えて、さらに多くのプラスチック顆粒がホッパーに追加されます。 冷却されると、プラテンが開き、完成した部品が排出され、スクリューがもう一度引き戻されて、材料がバレルに入り、プロセスが再び開始されます。
射出成形サイクルは、金型を閉じ、プラスチック顆粒を供給/加熱し、金型内に加圧し、冷却して固体部品にし、部品を取り出し、再び金型を閉じるという連続プロセスによって機能します。 このシステムによりプラスチック部品の迅速な生産が可能になり、設計、サイズ、材料に応じて 10,000 営業日で XNUMX 個以上のプラスチック部品を製造できます。
Djmolding は、中国の少量射出成形会社です。当社のプラスチック射出成形プロセスは、カスタム プロトタイプと最終用途の生産部品を最短 1 日のリードタイムで生産し、年間最大 10000 個の部品を供給する少量プラスチック射出成形部品のサプライヤーです。