インドでの事件
DJmolidng のインド企業向け射出成形サービスにおけるインサート金型
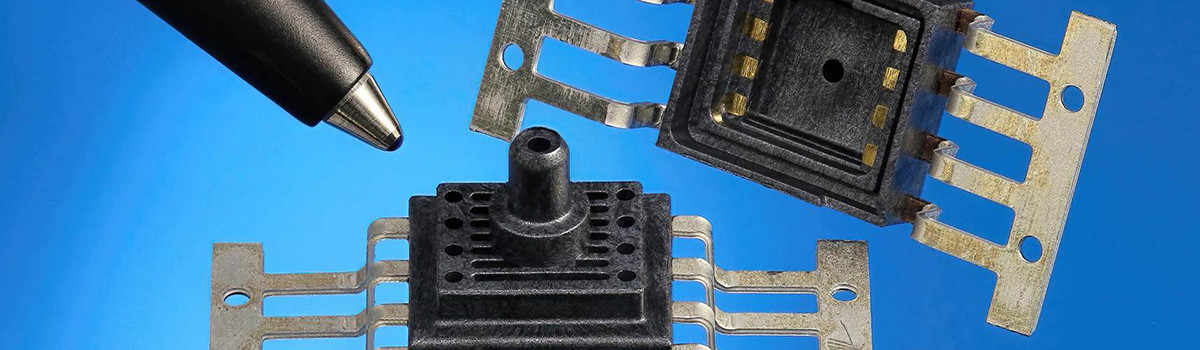
インサート金型は一般に、ナット、金属部品、または硬質プラスチック部品をキャビティ内に固定して射出成形する金型の一種です。
DJmolding はインド市場向けにインサート mlod 射出成形サービスを提供しており、さまざまな業界、特に家電メーカー向けにインサート成形のプラスチック部品を多数生産しています。 インドの一部の家電メーカーは、インサート成形のプラスチック部品を DJmolding から長期にわたって購入しています。 当社はこれらのインド企業と非常に良好なパートナーシップを築いています。
インサートナット射出成形: ナットの材質はステンレス鋼、銅、青銅、鋼があり、一般に銅ナットがよく使用されます。 銅はローレット加工がしやすいため、ナットとプラスチックの接合が容易になります。 ナット内径の公差は0.02mm以内に管理してください。0.02mmを超えるとバリが発生しやすくなります。 金型嵌合ではインサートピンにナットを組み付けてテストする必要があります。 ナットとピンの間がしっかりと嵌合していると、部品をイジェクトするのが難しくなり、イジェクトマークや固着の問題が発生する可能性があります。 緩んでいるとフラッシュの原因となります。
インサート金属部品射出成形:
金属部品には、ステンレス鋼、アルミニウム、銅、鋼などがあります。 金属部品の公差は0.02mm以内に管理する必要があり、それ以外の場合は封止が困難でバリが発生しやすくなります。 金属部品の面積をあまり大きく設計することはできません。
金属部品の充填面積が大きすぎると、金属部品間の温度差が大きくなり、完全に注入することが非常に困難になります。 キャビティは移動しないため、通常、金属部品の位置はキャビティ内で設計されます。これにより、移動中に金属部品が緩むことによるバリ(ひどい場合は金型を損傷する可能性があります)を回避できます。 特殊な場合、金属部品の位置は製品のコアまたは側面のみに設計できます。
硬質プラスチック射出成形のインサート:
通常、PEEK、PA66+30GF、PP+30GF、PA12+30GF、PPSなどの高融点の硬質プラスチックを選択します。 これらの硬質プラスチックの公差は正確である必要があります。 シール領域に収縮、へこみ、変形などの欠陥が存在することはできません。 金型の取り付けでは、テストのために硬質プラスチックを金型の中に入れ、より良いシールを実現するためにシール領域の周囲に 0.05 ~ 0.1 mm のプレプレスを残す必要があります。
硬質プラスチック部品の面積を大きくしすぎないように設計してください。温度差が生じ、射出時の材料の充填が困難になります。 通常、キャビティは動かないため、金型の移動によるバリや金型の損傷を避けるために、硬質プラスチック部品をキャビティの側面に固定します。 特殊な場合、金属部品の位置は製品のコアまたは側面のみに設計できます。
デザインのポイント
1.ナットインサート付きの製品では設計収縮が発生しますが、金属部品や硬質プラスチックインサート付きの製品では設計収縮は不要です。 厳密な公差が必要な領域については、製品のサイズ公差を中央値に変更してください。
2.通常、金型設計では標準ピンポイントゲートを備えた金型ベースを採用し、二次射出では挿入部品を可能な限りキャビティ内に配置します。 インサートをキャビティ内に固定した状態で、射出成形後にコア内に部品を取り出す方法を検討します。 通常、キャビティに弾性ブロックを追加し、パーツがコアに留まるように弾性接着剤を追加します。 弾性ブロックと接着剤の間の距離が大きすぎると、弾性力によって硬質プラスチックや金属部品が変形してしまいます。 通常、この距離は2mm以内に設計されており、金属または硬質プラスチックインサートの面積が比較的大きい場合は、弾性ブロックと弾性接着剤の量を適切に増やします。
3. 材料の厚さは 1.3 ~ 1.8 mm 以内が最適です (1.5 mm 程度が最適です)。そうでない場合は、製品の図面を確認し、顧客に変更を提案する必要があります。 材料の厚みが1.3mmより薄いと材料の充填が難しく、1.8mmより厚いと製造時に収縮が起こりやすくなります。
4.金型においてゲートは非常に重要です。 ゲートポイントへの材料充填バランスには十分な配慮が必要です。金属部品や硬質プラスチック部品が固定されている部分に材料が流れ込むと、インサート抵抗や温度差により材料の充填速度や圧力が低下します。
5.金型エジェクタシステムの場合、突き出しのバランスを考慮する必要があり、突き出し後に変形が発生します。 バランスよく部品を取り出すことができない場合は、構造設計時にバランスの問題を改善するために崩壊を考慮する必要があります。
6.射出成形で突き出された後の部品の外観の品質を保証するために、エジェクタ装置はABSまたはPMMAが挿入された硬質プラスチックの塊である必要があります。 オーバーモールドにスライドシールがある場合は、キャビティ内でスライドすることで金型の嵌合が容易になるため、できる限りキャビティ内でスライドするように設計してください。
7. シーリングSA(縫い代)の強度を確保するため、0.8回射出成形品の場合、シーリングSAの幅は1.0mm以上必要となります。 二次射出材料が硬質プラスチックの場合、シール SA の幅は少なくとも XNUMXmm である必要があります。それ以外の場合は、お客様に製品の変更を提案する必要があります。
8.金型設計では、射出成形機の生産を考慮して、縦型または横型のどちらのタイプの機械が採用されているかを確認する必要があります。 特にコールド ランナーを備えた金型の場合は、キャビティの数が多すぎるとランナーが長くなり、材料が無駄になるだけでなく、高効率の射出を達成するのにも有害であるため、キャビティの数を多すぎないように設計することをお勧めします。 射出成形機にマッチするためには、コンパクトで製品配置に合理的であるかどうかを考慮する必要があります。また、製品を金型に入れるたびに同じ状態になるように製品を固定できる必要があります。 もう XNUMX つの方法は、金型を閉じる前に部品が正しい位置にない場合に警告を発する設計反応システムで、金型の閉じを停止するのに役立ちます。 このようにして、部品が金型内で同じ状態になるため、射出成形における合格率と生産効率が向上します。
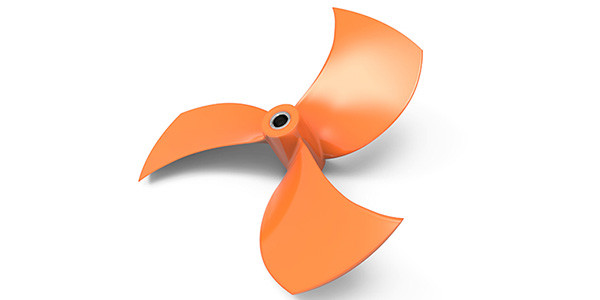
9.金型の射出領域には射出時に大きな圧力がかかるため、鋼製サポートを設計する必要があります (形状とサイズが部品の領域より 5 ~ 10 mm 大きい必要があります)。 オーバーモールド領域の周りの部品の間に隙間を残してはいけません。そうしないと、二次射出後に部品の形状が崩れてしまいます。 SA(縫い代)のないパーツの場合は、この点にさらに注意を払う必要があります。
10.エアトリップが起こりやすい 射出成形ではエアトリップが起こりやすいため、金型設計時にはベントを十分に考慮する必要があります。 死角に材料を充填するのははるかに困難であるため、長距離の水線のすべての死角と位置で、硬質プラスチック部品に通気穴を設計する必要があります。
11. 射出された材料と適切な推力が確実に完全に充填されるようにするための XNUMX つの方法は、部品の角にアンダーカットを設計して接着効果を高め、部品をよりしっかりと接着させることです。
12. シーリング領域とパーティング ライン領域では、金型のクランプ ラインや脱型抜き勾配により金型フィッティングにバリが発生するため、キャビティとコアから金型を取り外すべきではありません。 LISS-OFFで離型してみます。
インサート金型のゲートポイントタイプ
インサート金型のゲートポイントは、ホットスプルーバルブゲート、ホットスプルーピンゲート、ピンポイントゲート、サブゲート、エッジゲートなどを指示するように設計できます。
ホットスプルーバルブゲート: 流動性が良く、位置選択が柔軟で、ゲートポイントが小さい。 大量生産や肉厚の厚い製品に適しています。 材料の節約、ゲートの材料の無駄なし、短納期、高品質に貢献します。 唯一の欠点は、わずかなゲート跡です。
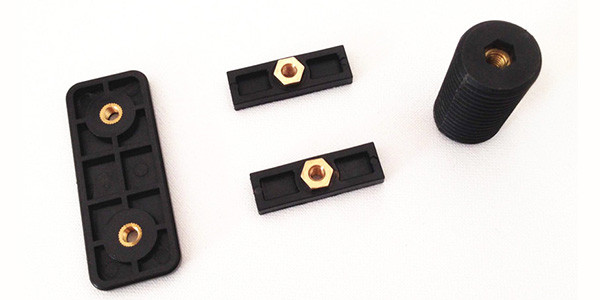
ホット スプルー ピン ゲート: 良好な流動性、柔軟なポジション選択、小さなゲートポイント。 大量生産や肉厚の厚い製品に適しています。 材料の節約、ゲートの材料の無駄なし、短納期、高品質に貢献します。 ただし、ゲートポイント付近に0.1mm程度材料が残り、バリが出やすいなどの欠点があります。 ゲートポイントの周りに残った材料を覆うために溝を作る必要があります。
ピンポイントゲート: 柔軟なポジション選択、弱い流動性、長いランナー距離、小さなゲートポイント。 小ロット生産に適しています。 ゲートポイント付近で廃棄物が増加。 生産時にゲートポイントをクランプする機械アームが必要です。 リードタイムが長い。 欠陥はゲート ポイントの周囲に 0.1 ~ 0.2 mm の材料が残るため、ゲート ポイントの周囲に残った材料を覆うように溝を作成する必要があります。
サブゲート: キャビティ内のリブ、コア、側壁、エジェクターピンに設計できます。 ゲートポイントを柔軟に選択でき、注入ゲートは自動的に部品から分離され、ゲート跡はわずかです。 欠点: ゲートポイント周辺で材料が抜けやすい、ゲート位置に乾燥跡が発生しやすい、材料を手で拭き取る必要がある、キャビティからのゲートポイントのプレスロスが多い。
エッジゲート: 溶融プラスチックはゲートを通って流れ、横方向に均等に割り当てられ、応力が減少します。 空洞に空気が入る可能性を減らし、縞や気泡の発生を防ぎます。 欠陥: 注ぐゲートが部品から自動的に分離できない、部品の端にスプルーの跡が残る、注ぐゲートを平らに加工するには工具が必要。 エッジ ゲートは、射出と圧力保持のバランスを調整するのに役立ち、また圧力保持と供給にも適しているため、エア ラインやフロー マークなどの改善に役立ちます。
インサート金型の加工・嵌合
1.加工前に金型の加工技術を検討します。 高精度加工機、高速加工機、低速送りNCワイヤカット機、ミラー放電加工機などをお選び下さい。
2.プリプレス位置を0.05~0.1mm残すようにデザインします。
3.モールドベース加工の精度要件に注意し、モールドベースを入手した後に公差を検査し、公差が不適格な場合は使用しないでください。
4.金型内にナット、金属部品、硬質プラスチック部品を入れて金型を取り付けます。 金型の取り付けに問題がある場合は、ナット、金属部品、硬質プラスチック部品、金型をチェックして、どれが間違っているかを確認します。 可能な限り図面通りに部品を加工することで、今後のデータ追跡に役立ちます。
5.金型取り付けにはグラインダーは使用できません。 金型のフィッティングが良くない場合は機械に頼って修正します。
6.試用前に動作テストを行い、組み立てミスや組み立て間違いを避けてください。 組み付けを誤るとモールドベースの破損の原因となります。
インサート金型の金型検査
1.金型のテストでは、金型の開閉、取り出しのシーケンスを明確に知っておく必要があります。 金属部品と硬質プラスチック部品の構造的特徴と特性を理解します。
2.金型検査では多くのサンプルが必要となるため、顧客が必要とするサンプルの量を明確に把握し、十分なナット、金属部品、硬質プラスチックを準備します。
3.ナット、金属部品、または硬質プラスチックをインサートせずに金型をテストできるかどうかに注意してください。 インサートナットや金属部品、硬質プラスチックなどが金型に組み付けられていない場合、金型への固着やショートショットなどの不良が発生する可能性があります。
4.多くの場合、金型のウォーターラインプレートを調整する必要がありますが、インサート金型の構造によってはウォーターラインプレートの調整ができない場合や、さらに悪いことに、金型がひどく固着して修正が必要になったり、金型が破損したりする場合があります。オープニング。
5.金型テストでは、ショートショット、エアトリップ、フラッシュ、金型への固着などの問題が発生する可能性があります。 射出成形機で問題が確認できる場合は、それを解決した方がよいでしょう。
DJmolding は 10 年以上のインサート成形の経験があります。ご質問がございましたら、お問い合わせください。