韓国の事例
韓国自動車会社向けプラスチック射出成形部品の肉厚構造設計
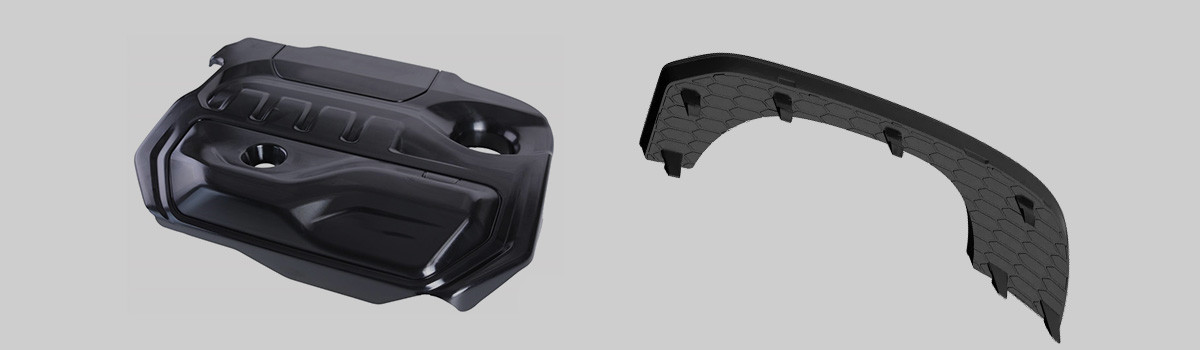
プラスチック部品は自動車にとって非常に輸入品であり、その構造強度は寿命や安全運転に影響するため、韓国の自動車メーカーはプラスチック部品の購入を非常に厳しくしています。 自動車産業は自動車に大量のプラスチック部品を使用することになるが、韓国の現地射出成形会社では大量の供給ができず、これらの自動車メーカーは中国のDJモールディングと同様にプラスチック部品を海外から購入することになるだろう。
プラスチック部品は自動車にとって非常に重要であるため、韓国の自動車会社にとってプラスチック射出成形部品の肉厚構造をどのように設計するのでしょうか? DJmolding は、プラスチック射出成形部品の厚さ構造の設計を示します。
肉厚の定義
肉厚はプラスチック部品の基本的な構造特性です。 プラスチック部品の外面を外壁、内面を内壁と呼ぶ場合、外壁と内壁の間には厚さの値が存在します。 この値を壁厚と呼びます。 構造設計時にソフト上でシェルを抽出する際に入力される値も肉厚と言えます。
壁厚の関数
製品の外壁に
部品の外壁は部品の外皮のようなものです。 内壁は部品の構造骨格です。 部品の外壁の表面処理により、さまざまな外観効果を得ることができます。 内壁は構造(リブ、ネジバー、バックルなど)を接続するだけであり、部品に一定の強度を与えます。 その間、感染成形プロセス中に他の構造が充填される可能性があります。 内壁と外壁 (冷却、組み立て) には特別な要件はありません。 通常、内部の部品を損傷や環境による干渉から保護するために、各部品が十分な強度を持つように全体として作られます。
製品の内部部品について
ベアリングまたは接続ブラケットとして、内壁と外壁に厳密な要件はなく、実際の条件に応じて外壁に他の構造(リブ、ネジバー、バックルなど)を確立できます。 ただし、製造の便宜上(主に前金型と後金型を分離する場合を指します。後金型にプラスチック部品を保持するために、金型の前面の外壁はできるだけシンプルに設計する必要があります)そうでない場合は、前金型と後金型の抜き勾配を調整したり、前金型にシンブルを入れたり、後金型に小さなアンダーカットを入れたりして、内壁に他の構造を設計するのが一般的です。
シェル部品、内部部品を問わず、金型のエジェクターピンの受け面として部品をスムーズに突き出すための肉厚は不可欠です。
壁厚の設計原則:
プラスチック部品の設計では、建物の基礎として不可欠な肉厚が最優先されます。 他の構造はその上に構築する必要があります。 一方で、プラスチック部品の機械的特性、成形性、外観、コストにも影響を与えます。 したがって、肉厚は上記の要素に基づいて設計する必要があります。
壁の厚さは特定の値である必要があると述べました。 値がある場合、それは均一な肉厚を指します。 値が多い場合は不均一な肉厚を指します。 均一か不均一かの違いについては後ほど紹介します。 ここで、肉厚設計の原則に従う必要があることについて説明します。
1. 機械的特性の原理に基づく:
シェル部品であっても内部部品であっても、ある程度の強度が必要であると述べました。 他の要素とは別に、部品の形成を考慮する場合、レジストの剥離力が必要になります。 薄すぎると変形しやすくなります。 一般に、肉厚が厚いほど部品の強度は高くなります(肉厚が 10% 増加すると、強度は約 33% 増加します)。 肉厚が一定の範囲を超えると、肉厚が増すと収縮や気孔率により部品の強度が低下します。 肉厚の増加は、部品の強度の低下と重量の増加、射出成形サークルの延長、コストなどを引き起こすことは明らかであり、肉厚を増やすだけで部品の強度を高めることは最適なプログラムではありません。 剛性を高めるには、リブ、曲線、波形表面、補強材などの幾何学的特徴を利用するのが最善です。
スペースの制限やその他の要因により、一部の部品の強度が主に肉厚によって実現される可能性は排除されません。 したがって、強度が重要な要素である場合は、機械的シミュレーションを模倣して適切な肉厚を決定することをお勧めします。 実際、壁の厚さの値も次の形式原則に従う必要があります。
2. 成形性の原則に基づく:
実際の壁の厚さは、前金型と後金型の間の金型キャビティの厚さです。 溶融樹脂が金型キャビティに充填され、冷却されると肉厚が得られます。
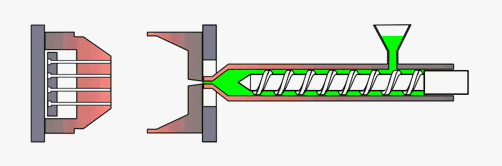
1) 射出・充填の際、溶融樹脂はどのように流れるのでしょうか?
キャビティ内のプラスチックの流れは層流とみなすことができます。 流体力学の理論によれば、層流流体は、せん断力の作用下で滑り合う互いに隣接する液体の層とみなすことができます。
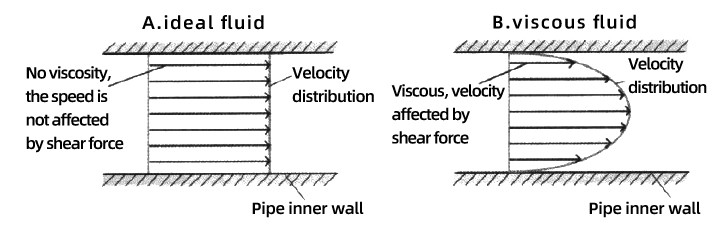
射出成形の際、溶融樹脂はランナー壁(金型キャビティ壁)と接触し、最初に冷却されたランナー壁(または金型キャビティ壁)に流層が付着します。 速度はゼロであり、隣接する液体層との間で摩擦抵抗が生じます。 このまま通過しますが、中流層の速度が一番速いです。 両側のランナー壁(または金型キャビティ壁)付近で層流速度が低下する流れ形状。
中間層は流体層であり、スキン層は固化層です。 冷却時間が経過するにつれて、呪いの層が増加します。 流体層の断面積は徐々に小さくなります。 充填物が硬ければ硬いほど、射出力は大きくなります。 実際、射出を完了するために溶融物を金型キャビティに押し込むことはより困難です。
したがって、肉厚の大きさは射出成形プロセス中の射出成形品の流動と充填に大きな影響を与えるため、その値が小さすぎることはできません。
2) 溶融プラスチックの粘度も流動性に大きく影響します。
溶融物が外部作用を受けており、層間に相対運動がある場合、流体層間の相対運動を妨げる内部摩擦力が発生します。 流体が生み出す内部摩擦力を粘度といいます。 粘度の強さを動粘度(または粘性係数)で評価します。 溶融物のせん断速度に対するせん断応力の比を数値化したもの。
溶融物の粘度は、プラスチック溶融物の流れやすさの特性を反映します。 これはメルトフロー抵抗の尺度です。 粘度が高くなるほど流体抵抗が大きくなり、流れにくくなります。 溶融粘度に影響を与える要因は、分子構造だけでなく、温度、圧力、せん断速度、添加剤なども関係します(プラスチック材料の種類を決定した後、温度、圧力、せん断速度、添加剤など)射出成形工程におけるプラスチックの流動性は、射出成形工程におけるその他の要因を変えることで変化する可能性があります(今後、状況に応じて流動性について記事を書きます)。
一方、実際の用途では、メルトインデックスは加工中のプラスチック材料の流動性を示します。 数値が大きいほど材料の流動性が良くなります。 逆に材料の流動性は悪くなります。
したがって、流動性の良いプラスチックは、特に複雑な構造の射出成形部品の場合、金型キャビティに充填しやすくなります。
一般的に使用されるプラスチックの流動性は、金型設計の要件に応じて大きく XNUMX つのカテゴリーに分類できます。
①流動性良好:PA、PE、PS、PP、CA、ポリ(4)メチルペンチレン。
②中流動性:ポリスチレン系樹脂(ABS、AS等)、PMMA、POM、PPO。
③流動性が悪い:PC、硬質PVC、PPO、PSF、PASF、フッ素樹脂。
上の図からわかるように、流動性が最も低い材料では、最小肉厚の要件が高くなります。 これは層流理論で導入されています。
上記の壁厚の推奨値は、控えめな数値にすぎません。 実際のアプリケーションでは、部品のサイズには小、中、大が含まれますが、上図は基準範囲を指定するものではありません。
3) 流長比から計算できます
プラスチックの流動長比とは、プラスチック溶融流の長さ (L) と壁の厚さ (T) の比を指します。 つまり、特定の壁厚の場合、流動長比が高くなるほど、プラスチック溶融物はより遠くまで流れます。 あるいは、プラスチック溶融流の長さが一定である場合、流れ長さの比率が大きいほど、肉厚を小さくすることができます。 したがって、プラスチックの流動長比は、プラスチック製品の供給数と流通に直接影響します。 また、プラスチックの壁の厚さにも影響します。
より正確には、流動長比を計算することで肉厚の具体的な数値範囲を求めることができます。 実際、この値は材料温度、金型温度、研磨度合いなどに関係します。これはおおよその範囲の値にすぎず、条件が異なると正確にすることは困難ですが、参考値として使用できます。
流れ長さの比率の計算:
L/T (合計) = L1/T1 (メイン チャネル) + L2/T2 (スプリット チャネル) + L3/T3 (積) 計算された流長比は、物性表に示されている値より小さい必要があります。そうでない場合は、充填不良の現象です。
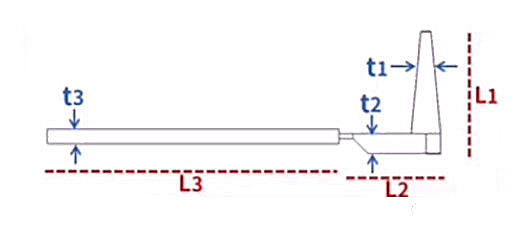
例えば、
ゴムシェル、PC 材料、壁の厚さは 2、充填距離は 200、ランナーは 100、ランナーの直径は 5 です。
Calculation: L/T(total)=100/5+200/2=120
PCの流動長比の基準値は90であり、基準値よりも明らかに高い。 射出が難しいため射出速度と射出圧力を上げる必要があり、さらには特殊な高性能射出成形機が必要になります。 100つの給電点を採用するか、給電点の位置を変更すると、製品の充填距離を100に短縮できます。つまり、L/T(合計)=5/100+2/70=100となります。 長さ比が基準値より小さくなり、射出成形が容易になりました。 肉厚を3にすると、L/T(合計)=100/5+200/3=87となり、通常の射出成形が可能となる。
3. 外観の原則に基づく:
部品の外観に影響を与える肉厚の具体的な性能は次のとおりです。
1) 肉厚不均一:表面の収縮(縮み、穴、印刷の濃淡などの外観不良を含む)、反り変形等。
2) 過度の肉厚: 表面収縮や内部収縮穴などの欠陥。
3) 肉厚が薄すぎる:接着剤の不足、シンブル印刷、反り、変形などの欠陥。
収縮または気孔率
通常、肉厚の厚い部分で収縮や気孔が発生します。 メカニズム: 材料の凝固原理によれば、射出成形プロセス中の内部気孔率と表面収縮は、冷却プロセス中の一定の収縮によるものです。 後方の凍結位置に収縮が集中し、すぐに回復できない場合、内部に収縮や気孔が発生しやすくなります。
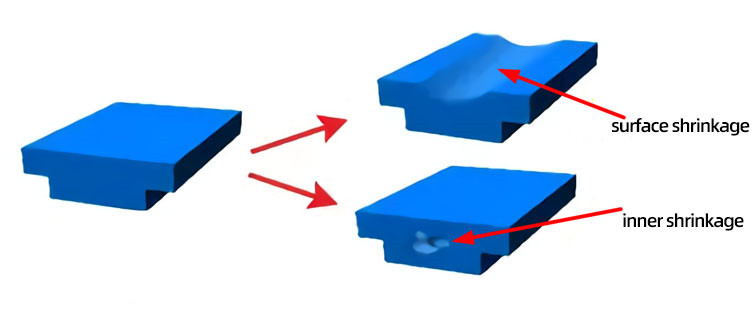
上記の肉厚の設計原則を機械的性質、成形性、外観、コストのXNUMXつの側面から紹介します。 肉厚設計を一言で表すと、機械的特性と加工性能を満足する条件下で、射出成形品の肉厚値をできるだけ小さく、かつ均一にする必要があるということです。 そうでない場合は、一律に移行する必要があります。
DJmolding は、世界的な市場向けにプラスチック部品の設計および製造サービスを提供しています。プロジェクトを開始したい場合は、今すぐお問い合わせください。