カスタムプラスチック射出成形
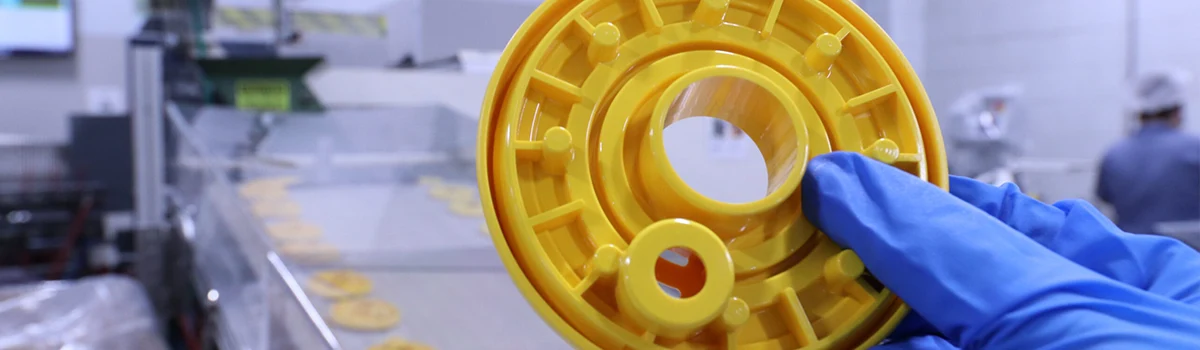
カスタム射出成形は、特定の機械的または美的特徴を実現することが成功の鍵となるプラスチック部品に最適です。 DJmolding プラスチック射出成形は、お客様が最高のプラスチック部品を製造できるように支援するという基本的な目標によって推進されています。 複雑さとは無縁ではありませんが、設計上の課題は、お客様のためにイノベーションを起こしたいという私たちの願望を本当に駆り立てるものです。 早期から参加していただくことで、設計プロセスに付加価値を加えることができます。
プラスチック射出成形の利点
詳細な機能
ブランドを強化するために、美的または機能的な詳細を考慮してください。刻印されたテキスト、化粧品またはテクスチャード加工された表面、インモールド装飾、スナップフィット、柔軟なヒンジ、さまざまな硬度などです。
高効率
プラスチック射出成形の効率は比類のないものです。 お客様の部品やツールから不必要なコストを削減します。 長年勤務している当社の設計エンジニアとマスターモールダーは、この点で非常に優れています。
強化されたパフォーマンス
当社は、材料科学、設計原理、分析ツール、プロセス制御を適用することで、お客様の部品の意図された機能を理解し、お客様の主要な目的を達成するよう努めています。
材料の多様性
200 を超える材料、汎用樹脂、エンジニアリング樹脂からお選びいただけます。 当社は、パフォーマンスと価格のバランスをとり、コストを削減するために同等の代替材料を特定するお手伝いをします。
射出成形プロセス
プラスチック射出成形は、プラスチックを製造する最も古い方法の XNUMX つであり、製品メーカーの部品開発における重要なステップです。 また、重金属部品をプラスチックに変換しようとしているメーカーにとっても優れたソリューションです。 最も簡単な形で説明すると、このプロセスではポリマーまたはプラスチック樹脂を使用し、加熱、溶融、高圧下でカスタム金型に射出すると、製品製造に使用されるプラスチック部品が製造されます。
そのプロセスは単純に見えますが、実際には非常に複雑になる可能性があり、業界固有のニーズ、仕様、最終用途、および時間/予算の制約に対応できる射出成形パートナーからの高度な経験が必要です。 開始するのに最適な場所は、プラスチック成形プロセスと設計のベスト プラクティスに関する基本的な知識を得ることです。
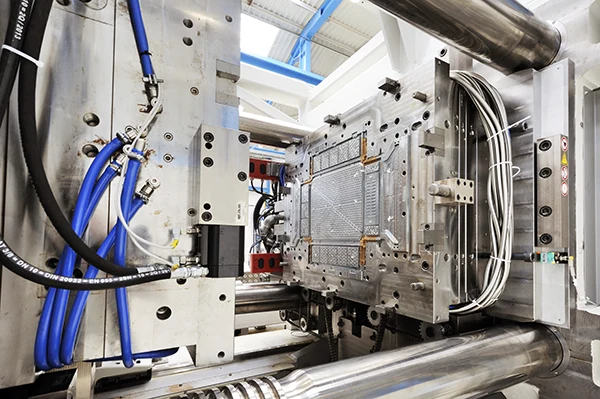
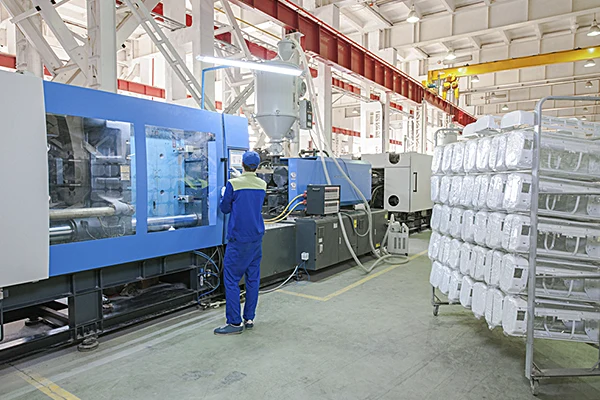
科学成形
科学的な成形アプローチは、特定の性能と高精度を必要とする重要な部品の製造に役立ちます。 当社の高度な成形技術により、再現性と一貫性が保証されます。 つまり、私たちが今日お客様のために作る製品は、明日もお客様のために作られるということです。
科学的な射出成形は、金型の開発中に始まります。 圧力、温度、キャビティ充填時間などの要素が最適化されるため、金型設計の変動の可能性が最小限に抑えられます。 モールド フロー解析では、成形品の最後に充填する領域、材料が金型に対してどのように配向するかを示し、潜在的な反りや応力点を明らかにします。 これは、エンジニアリングの予測分析と測定を提供する予防的なステップであり、部品やプロジェクトの成功または失敗を簡単に判断できるようになります。
堅牢な生産プロセスでは、モニタリングと自動プロセス制御による科学的アプローチをさらに活用し、スクラップと処理時間を削減します。 万が一、ばらつきや不具合が発生した場合は、不適合部品が製造される前に迅速に特定・隔離されます。
オーバーモールディング
オーバーモールディングを使用すると、XNUMX つ (またはそれ以上) の材料を単一の部品に組み合わせることができます。 このプロセスは、柔らかいグリップ領域など、独特の触感のある表面によく使用されます。 オーバーモールドは、プラスチック基板上にプラスチック、またはプラスチック基板上にゴムを重ねて行うことができ、通常は XNUMX ショット射出成形プロセスによって実現されます。 樹脂の配合と色は異なる場合があります。 オーバーモールディングの美的利点はすぐにわかりますが、二次加工も不要になります。 オーバーモールディングは、ハンドグリップ付きのツール、手持ちの物体、ゴム製グリップが必要なロボット工学、または単純に部品の外観を独特の色で向上させる場合に最適です。
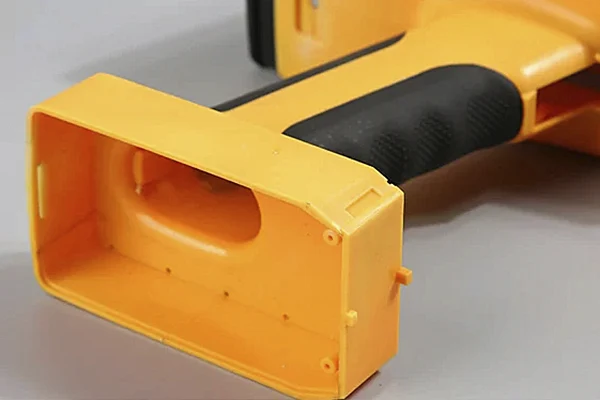
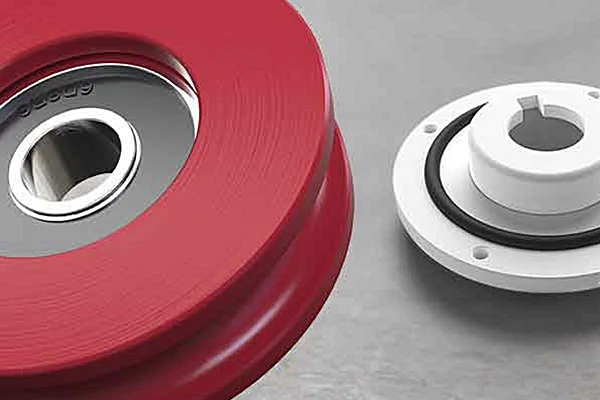
インサート成形
インサート成形はオーバーモールディングに似ていますが、金型キャビティ内に配置されるオブジェクトを組み込みます。 インサート成形は、プラスチックをインサート (通常は金属またはプラスチック) に接着します。 ねじ付きインサートが一般的です。 これにより、ファスナー、接着剤、または熱かしめの代替として使用する際の労力が軽減されます。 インサートは部品の強度も高めます。 インサートは手動またはロボット自動化によってロードされます。
部品の装飾とラベル付け
インモールド装飾 (IMD) とインモールドラベリング (IML) は、グラフィックやラベルで視覚的に注目に値する外観を作成するために使用されます。 ロボット工学と静電グリップまたは真空グリップによって促進され、溶融プラスチック樹脂を射出する前に、印刷されたフィルム オーバーレイが金型キャビティに追加されます。 このプロセスにより、ラベルと完成品の間に永久的な接着が形成され、通常は後処理操作が不要になります。 質感、色、表面コーティングの幅広い選択肢により、創造的な可能性への扉が開かれています。 ブランドを強化するためのオプションについてプロジェクト マネージャーに相談することをお勧めします。
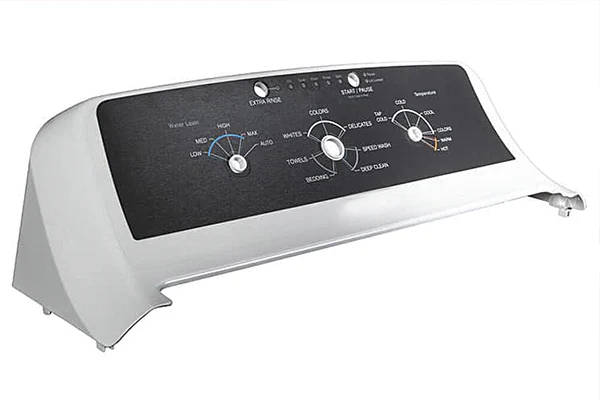
カスタムプラスチック射出成形サービス中国
DJmolding 2010年より運営 | AFAQ ISO/TS 16949、UL、ISO 認証を取得しており、主に世界中の多くの 3D プリンティング会社に供給されています。
Djmolding では、高品質のプラスチック射出成形部品と金型ツールの製造を専門としています。 当社は主に、世界中の多くの 3D プリント会社にプラスチック射出製造を供給しています。 当社は、ロボット工学および自動プラスチック射出製造用の機械を 55 台備えています。当社は、さまざまな材料から工具を作成するためのすべての機械加工および仕上げサービスを提供しており、すべての主要なプラスチックで 100 万から 200 万以上の完成部品を生産できます。 当社を本当に際立たせているのは、お客様の部品がお客様の最高の期待を満たし、それを超えていることを確認するための高度な材料検証、検査、テストです。 無料の見積もりについては、当社の国際的な射出成形の専門家に今すぐお問い合わせください。
DJmolding プラスチック射出成形プロセス
プラスチック射出成形ツールの準備ができたら、成形プロセスは次の基本的な手順で構成されます。
ステップ 1. プラスチック樹脂は生のペレットで提供されます。 これらは適切な水分含有量まで乾燥され、必要に応じて顔料またはマスターバッチ着色剤とブレンドできます。
ステップ2. 乾燥したペレットを成形機のホッパーに流し込みます。 機械のバレル内の往復スクリューがこれらのペレットを金型に向かって輸送します。
ステップ 3. バレル内でペレットが混合され、完全に溶融するまで加熱され、液体樹脂が形成されます。
ステップ 4. 加熱された金型が自動的に閉じ、樹脂が大きな圧力の下でゲートを通って金型キャビティに注入されます。
ステップ 5. 金型を冷却して内部の部品を固化させます。
ステップ 6. 金型が開き、部品が取り出され、新しいサイクルが始まります。
プラスチック射出成形の公差
すべてのプラスチック素材は、熱と湿気の影響で膨張および収縮します。 当社の公差ガイドでは、典型的な部品の特徴に対する最も一般的な樹脂タイプの特性に関するより一般的な情報を提供します。
当社はお客様と緊密に連携して、製造用の設計を最適化します。 不適切な設計により熱応力、収縮、反りなどが発生する可能性がある領域を示します。一般的な欠陥とその回避方法の詳細については、設計ガイドを参照してください。
特に指定がない限り、当社はプラスチック射出成形品の DIN 16742 標準公差に準拠します。 当社が射出成形部品に適用する外観品質基準についてお読みください。
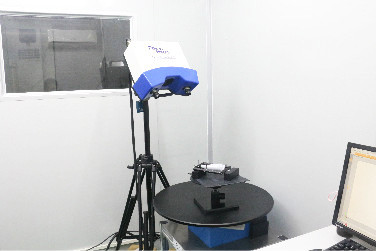
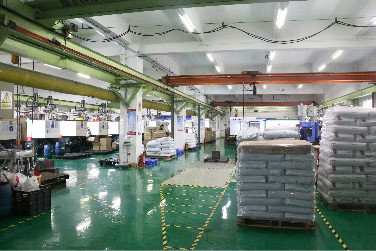
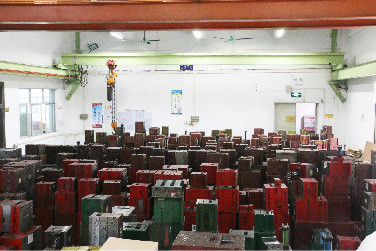
プラスチック射出成形材料
Djmolding は、アルミニウム 7075、P20、NAK80 半硬化鋼、および H13 完全硬化鋼から射出成形ツールと金型を製造しています。 さらに、標準の SPI 仕上げ、EDM テクスチャリング、およびさまざまなエッチング テクスチャも提供しています。
これらの材料タイプにはそれぞれ、特定の用途に対して明確な利点があります。 *考慮事項には次のものが含まれます。
※原材料費
*耐久性と耐腐食性または耐摩耗性
※被削性
*高度な表面研磨能力
※熱処理に要する時間
※予想工具寿命
どちらがお客様に適しているかについて詳しくは、当社の技術スペシャリストにお問い合わせください。
プラスチック射出成形品
プロジェクトに合わせて選択できる熱成形および熱硬化性プラスチックは何千もあります。 さらに、ガラス繊維、UV 安定剤、潤滑剤などの添加剤を使用して、機械的および化学的特性を強化することもできます。 当社の材料シートには、標準タイプとそれぞれに予想される公差に関する詳細情報が記載されています。
樹脂の選択は、次の XNUMX つ以上の考慮事項に依存します。
*耐紫外線性、耐薬品性、耐摩耗性、耐衝撃性
※原材料費
*機械的強度
*重量と密度
*柔軟性
*透明性
※リサイクル性
材料特性の詳細については、当社の技術専門家にお問い合わせください。
DJモールディング射出ショップ:
プラスチック射出成形金型およびラピッドプロトタイピングサービスの大手メーカー
Djmolding は、中国で最も有名なプラスチック射出成形会社の 50 つです。 当社の射出成形工場には、30トンから800トンまでの高精度射出成形機が24台設置されています。それらは主に台湾と日本から輸入されており、当社の射出成形工場は7時間、年中無休で稼働し、生産を提供しています。サービス。
当社は、自動車、医療、照明、スポーツ用品、家電、農業など、多くの産業向けのさまざまなプラスチック製品の経験があります。 Djmolding は 16949 年以来、AFAQ ISO/TS 9001、UL、ISO 2010 認証を取得しています。また、15 人の IPQC 担当者が当社の生産を常に監視し、部品の品質をチェックしています。これにより、当社の生産が最高レベルの品質を維持することが保証されます。 過去 9 年間、Djmolding は高品質のツールと部品を手頃な価格で製造するという高い評判を確立してきました。当社は appx との強力なビジネス関係を維持しています。 顧客数は主にアメリカとヨーロッパからで50名。
カスタムプラスチック射出成形
カスタムプラスチック射出成形は、高品質のプラスチック部品を製造する革新的かつ効率的な方法です。 この製造プロセスでは、金型を使用してプラスチック材料を複雑な形状やサイズに成形するため、さまざまな業界にとって理想的なソリューションとなります。 このブログ投稿では、カスタム プラスチック射出成形について深く掘り下げ、その利点、用途、ベスト プラクティスを探ります。
カスタム射出成形プロセスを理解する
カスタム射出成形は、プラスチック部品を大量に生産するために使用される製造プロセスです。 これには、プラスチックのペレットまたは顆粒を溶かし、高圧下で金型に注入し、冷却して固化させて目的の形状を形成することが含まれます。 射出成形プロセスの仕組みは次のとおりです。
- クランプ: 「ツール」と呼ばれる金型の XNUMX つの半分は、射出圧力に耐えるのに十分な力で一緒にクランプされます。
- 射出: プラスチック ペレットは加熱されたバレル内で溶かされ、高圧下でランナー システムを通じて金型に射出されます。 プラスチックが金型のキャビティを満たし、金型の形状が形成されます。
- 冷却: プラスチックは金型内で冷えて固まり、望ましい形状を維持します。
- 取り出し: プラスチックが冷えると金型が開き、完成した部品が取り出されます。
- 繰り返し: このプロセスを繰り返して、複数の同一のパーツを作成します。
射出成形では、小さな部品から自動車部品や家電製品などの大型製品に至るまで、プラスチック製品が製造されます。 このプロセスは非常に効率的で、複雑な形状と厳しい公差を持つ部品を製造でき、また正確であり、無駄が最小限に抑えられ、スクラップ率も低くなります。
このプロセスには、正確で一貫した結果を保証するための金型、射出成形機、制御システムなどの特殊な機器が必要です。 金型は通常スチールで作られており、マルチキャビティ成形を使用して複数の部品を製造するように設計できます。
射出成形は、熱可塑性プラスチック、熱硬化性樹脂、エラストマーなどのさまざまな材料にも使用できます。 各材料には独自の特性があり、特定の用途に合わせて調整できます。
全体として、射出成形は汎用性が高く効率的な製造プロセスであり、多くの業界で広く使用されています。
カスタムプラスチック射出成形の利点
カスタムプラスチック射出成形は、カスタムプラスチック部品を大量に作成するために使用される製造プロセスです。 このプロセスの利点の一部を次に示します。
高い効率と生産性: カスタムプラスチック射出成形は、同一の部品を大量に迅速かつ一貫して生産できる非常に効率的なプロセスです。 このため、プラスチック部品の大量生産に理想的な選択肢となります。
汎用性: このプロセスは、熱可塑性プラスチック、熱硬化性樹脂、エラストマーなどの幅広いプラスチック材料に使用できます。 これにより、さまざまな部品の設計や用途が可能になります。
一貫性と精度: 射出成形では、公差が厳しく、部品間のばらつきが最小限に抑えられ、一貫した正確な結果が得られます。 これにより、各部分が次の部分と同一であることが保証され、これは多くのアプリケーションにとって不可欠です。
費用対効果の高い: カスタムのプラスチック射出成形は、大量生産において費用対効果が高くなります。 初期の工具コストは高くなる可能性がありますが、量が増えるにつれて部品あたりのコストは下がります。
複雑: 射出成形では、薄肉や複雑な形状など、複雑な形状や幾何学形状の部品を製造できます。 これにより、設計の柔軟性が向上し、他の方法では製造が困難または不可能な要素の製造が可能になります。
最小限の廃棄物: 射出成形では、余分なプラスチックをリサイクルして再利用できるため、他の製造プロセスに比べて廃棄物の発生が最小限に抑えられます。
表面仕上げ: 射出成形では、追加の後処理や仕上げ操作を行わずに、高品質の表面仕上げを備えた部品を製造できます。 これにより、滑らかで洗練された外観の作品を作成するためのコスト効率の高いソリューションになります。
オートメーション: 射出成形は、ロボットによる金型への部品のロードおよびアンロード、検査および仕分け機能により、簡単に自動化できます。 これにより、手作業の必要性が減り、効率が向上します。
カスタムプラスチック射出成形は、汎用性が高く効率的な製造プロセスであり、他の方法に比べて多くの利点があります。 同一の部品を大量に迅速かつ正確に生産できるため、自動車、航空宇宙、医療、消費財などの多くの業界にとって理想的です。
射出成形の用途
射出成形は、さまざまな工業用プラスチック製品を製造するために広く使用されている製造プロセスです。 射出成形の最も一般的な用途のいくつかを以下に示します。
- 自動車産業: 射出成形では、内外装トリム、ダッシュボード部品、ドアハンドル、エンジン部品など、さまざまな自動車部品が製造されます。 強度や寸法精度が高い特徴が得られるため好ましい。
- 消費者製品: 射出成形により、おもちゃ、家電製品、電子機器などのさまざまな消費者製品が作成されます。 これにより、複雑な形状や幾何学形状、高品質の表面仕上げを実現できます。
- 医療機器: 射出成形は、注射器、IV コンポーネント、診断機器などのさまざまな医療機器の製造に使用されます。 高精度、クリーンな製造、および医療業界に不可欠な複雑な形状の部品を製造する能力を提供します。
- 包装産業: 射出成形により、ボトル、瓶、蓋などの包装材料が製造されます。 軽量で耐久性のあるコンテナを作成し、色、テクスチャ、形状をカスタマイズすることができます。
- 航空宇宙産業: 射出成形は、構造要素や内装部品など、航空宇宙部品のさまざまなコンポーネントの製造に使用されます。 これにより、極端な温度や圧力に耐えられる高性能材料の作成が可能になります。
- 建設業界: 射出成形により、PVC パイプ、雨樋システム、屋根材などのさまざまな建設資材が製造されます。 耐久性、耐候性、耐薬品性が高く、部品の大量生産が可能です。
- エレクトロニクス産業: 射出成形では、ハウジング、コネクタ、スイッチなどのさまざまな電子部品が製造されます。 これは、エレクトロニクス産業に不可欠な高精度、均一性、および複雑な形状の部品を製造する能力を提供します。
全体として、射出成形は多用途の製造プロセスであり、多くの業界で多くのプラスチック部品を製造できます。 複雑な形状、高精度、安定した品質の部品を製造できるため、多くのメーカーに人気があります。
射出成形に使用される材料の種類
射出成形は、溶融プラスチックを金型キャビティに射出して特定の形状を作成する製造プロセスです。 最終製品の望ましい特性に応じて、射出成形ではさまざまな材料を使用できます。 射出成形で使用される最も一般的な種類の材料の一部を以下に示します。
- 熱可塑性プラスチック: 射出成形で最も一般的に使用される材料です。 加熱すると柔らかく成型可能になり、冷却すると硬化するプラスチックの一種です。 熱可塑性プラスチックは、その特性を失うことなく、何度でも成形および再成形できます。 射出成形で使用される一般的な熱可塑性プラスチックには、ポリプロピレン、ポリエチレン、ポリスチレン、ナイロンなどがあります。
- 熱硬化性樹脂: 一度しか成形できないプラスチックです。 加熱して特定の形状に発展させ、一度硬化すると再成形することはできません。 熱硬化性樹脂は、高い強度と耐久性が必要な用途に使用されます。 射出成形で使用される一般的な熱硬化性樹脂には、エポキシ、メラミン、フェノール樹脂などがあります。
- エラストマー: これらの素材は弾性特性があり、伸びて元の形状に戻ることができます。 エラストマーは、柔軟性と衝撃吸収性が必要な用途に使用されます。 射出成形で使用される標準的なエラストマーには、ゴム、シリコーン、ポリウレタンなどがあります。
- 生分解性材料: 有害な残留物を残さずに環境中で自然に分解されます。 これらは、環境の持続可能性が懸念される用途に使用されます。 射出成形で使用される一般的な生分解性材料には、ポリ乳酸 (PLA) やポリヒドロキシアルカノエート (PHA) などがあります。
- 複合材料は、XNUMX つ以上の異なる材料を組み合わせて特定の特性を持つ新しい材料を作成することによって作られた材料です。 複合材料は、高い強度と剛性が必要な用途に使用されます。 射出成形で使用される標準的な複合材料には、ガラス繊維強化プラスチック (GRP) と炭素繊維強化プラスチック (CFRP) が含まれます。
- 金属充填プラスチックは、高い電気伝導率、熱伝導率、およびその他の特定の特性を備えた材料を作成するために金属粒子が注入されたプラスチックです。 金属充填プラスチックは、必要な電気伝導性または熱伝導性を備えた用途に使用されます。 射出成形で使用される一般的な金属入りプラスチックには、銅入りプラスチックやニッケル入りプラスチックなどがあります。
全体として、射出成形材料の選択は、強度、柔軟性、導電性、耐久性などの最終製品の特定の要件によって異なります。 メーカーは多くの場合、コスト、入手可能性、加工のしやすさ、最終製品に必要な特性に基づいて材料を選択します。
射出成形材料を選択する際の考慮事項
射出成形に関しては、最終製品の特性や性能に影響を与える可能性があるため、適切な材料を選択することが非常に重要です。 射出成形材料を選択する際に考慮すべき要素のいくつかを以下に示します。
- 機械的特性: 材料を選択する際に考慮すべき最も重要な要素の XNUMX つは、その機械的特性です。 これには、強度、剛性、靱性、耐摩耗性、耐摩耗性が含まれます。 最終製品に必要な機械的特性は、用途と製品がさらされる応力によって異なります。
- 熱特性: 特に最終製品が高温や熱サイクルにさらされる場合、材料の熱特性も重要です。 これには、材料の融点、熱伝導率、熱膨張係数が含まれます。
- 耐薬品性: 最終製品が化学物質にさらされる場合は、化学的劣化に耐えられる材料を選択することが重要です。 材料は、酸、塩基、溶剤、その他の化学薬品にさらされても、その特性が分解したり失われたりすることなく耐えることができます。
- 環境要因: 湿度や紫外線暴露などの環境要因も、材料の特性や性能に影響を与える可能性があります。 最終製品の環境条件を考慮し、それに耐えられる材料を選択することが重要です。
- コスト: 材料のコストも、特に大量生産の場合には重要な考慮事項です。 材料のコストは、最終製品にとって費用対効果の高い選択肢となるように、その性能と特性を比較検討する必要があります。
- 加工要件: 材料の加工要件も選択プロセスに影響を与える可能性があります。 材料によっては、特定の処理装置や技術が必要な場合や、処理がより難しい場合があります。 射出成形プロセスで材料を確実に使用できるようにするには、加工要件を考慮する必要があります。
- 規制への準拠: 最後に、最終製品が満たさなければならない規制要件を考慮することが重要です。 医療業界や食品業界などの一部の業界では、製品に使用される材料に対して特定の規制が設けられています。 最終製品が安全で準拠していることを保証するには、これらの規制要件を満たす材料を選択することが不可欠です。
全体として、射出成形に適した材料を選択するには、機械的および熱的特性、耐薬品性、環境要因、コスト、加工要件、規制遵守などのさまざまな要因を慎重に考慮する必要があります。 メーカーはこれらの要素を相互に比較検討して、最終製品に最適な材料を選択する必要があります。
射出成形における金型設計の重要性
金型の設計は、射出成形プロセスの重要な側面です。 金型の設計は、最終製品の品質だけでなく、製造プロセスの効率と費用対効果にも影響を与える可能性があります。 射出成形において金型設計が不可欠である理由のいくつかを以下に示します。
- 製品の品質: 金型の設計は最終製品の品質に影響を与える可能性があります。 金型の設計が適切でないと、反り、ヒケ、バリなどの不良が発生する可能性があります。 これらの欠陥により、最終製品が使用できなくなり、性能が低下し、スクラップ率や生産コストが増加する可能性があります。
- 製造効率: 金型の設計も製造プロセスの効率に影響を与える可能性があります。 金型が最適な流動と冷却を実現するように設計されていない場合、サイクル時間が長くなり、エネルギー消費が増加し、スループットが低下する可能性があります。 最適化された金型設計により、効率が向上し、生産コストが削減されます。
- 費用対効果: 金型の設計も射出成形プロセスの費用対効果に影響を与える可能性があります。 適切に設計された金型は、材料の無駄を削減し、部品の品質を向上させ、スループットを向上させ、生産コストを削減します。 さらに、大量生産向けに設計された金型により、部品あたりのコストが削減され、投資収益率が向上します。
- カスタマイズ: 金型の設計は、最終製品のカスタマイズにも重要な役割を果たします。 特定の形状や機能に合わせて金型を設計することで、メーカーは顧客のニーズに合わせた製品を作成できます。 これにより、市場における柔軟性と差別化が向上し、顧客満足度とロイヤリティの向上につながります。
- 材料の選択: 金型の設計も、射出成形で使用される材料の選択に影響を与える可能性があります。 成形方法は材料の流れと冷却に影響を与える可能性があり、最終製品の機械的および熱的特性に影響を与える可能性があります。 適切な金型設計を選択することで、メーカーは材料の選択を最適化し、最終製品が望ましい性能要件を確実に満たすことができます。
全体として、金型設計は射出成形プロセスにおいて重要な要素です。 適切に設計された金型は、製品の品質、製造効率、費用対効果、カスタマイズ性、および材料の選択を向上させることができます。 メーカーは、射出成形プロセスで可能な限り最高の結果を達成するために、特定のニーズに合わせて最適化された金型の設計に時間とリソースを投資する必要があります。
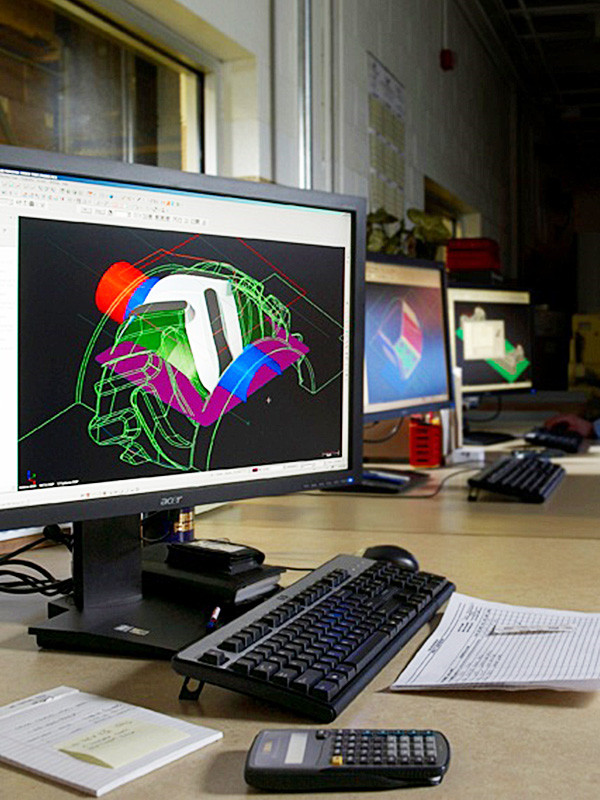
射出成形で使用されるさまざまな種類の金型
射出成形は、さまざまなプラスチック製品を製造できる汎用性の高い製造プロセスです。 射出成形の品質と効率を決定する重要な要素の XNUMX つは、使用する金型の種類です。 射出成形で使用されるさまざまな種類の金型をいくつか紹介します。
- XNUMX プレート金型: XNUMX プレート金型は、射出成形で使用される最も一般的な金型です。 これらは、金型キャビティによって分離された XNUMX つのプレートで構成されます。 プラスチック材料がキャビティに射出され、XNUMX つのプレートが結合されて最終製品が形成されます。
- XNUMX プレート金型: XNUMX プレート金型は XNUMX プレート金型に似ていますが、ランナー システムを成形品から分離する追加のプレートがあります。 これにより、部品の取り出しが容易になり、サイクル タイムを短縮できます。
- ホット ランナー 金型: ホット ランナー 金型は、サイクル タイムと材料の無駄を削減できるため、大量生産に使用されます。 金型には、溶融プラスチックを金型キャビティに直接供給する加熱ランナー システムが組み込まれているため、コールド ランナーが不要になります。
- コールド ランナー金型: コールド ランナー金型は最も基本的なタイプの金型であり、スプルー、ランナー、および金型キャビティで構成されます。 溶融プラスチックはスプルーに射出され、プラスチックがランナーに供給され、次に金型キャビティに供給されます。
- ファミリー金型: ファミリー金型は、単一サイクルで複数の部品を製造します。 金型には複数のキャビティが含まれており、それぞれに異なる部品が含まれています。 ファミリー金型は、小型で大量の部品によく使用されます。
- スタック金型: スタック金型は、単一サイクルで複数のプラスチック層を製造します。 モールドには、互いに積み重ねられた多数のキャビティ層が含まれています。 プラスチックが穴に注入され、層が結合されて単一の多層製品が形成されます。
- インサート金型: インサート金型は、成形プロセス中に金属またはプラスチックの部品を成形品に挿入するために使用されます。 インサートは、プラスチックが射出される前に金型キャビティ内に配置され、プラスチックがインサートを取り囲みます。
全体として、射出成形で使用される金型の種類は、製造される製品の特定の要件によって異なります。 正しいタイプの金型を選択することで、メーカーは射出成形プロセスの効率、品質、費用対効果を最適化できます。
射出成形のベストプラクティス
射出成形は複雑な製造プロセスであり、望ましい結果を達成するには慎重な計画と実行が必要です。 最適な品質、効率、費用対効果を確保するのに役立つ射出成形のベスト プラクティスをいくつか紹介します。
- 製造可能性を考慮した設計: 製品の設計は射出成形用に最適化する必要があります。 これには、部品の数を最小限に抑え、均一な肉厚を確保し、成形を複雑にするアンダーカットやその他の特徴を回避することが含まれます。
- 材料の選択: 射出成形に使用される材料は、製品の要件に基づいて選択する必要があります。 機械的特性、熱的特性、耐環境性などの要素を考慮する必要があります。
- 金型設計: 金型設計は、特定の製品に合わせて最適化する必要があります。 これには、適切なタイプの金型の選択だけでなく、適切な冷却、通気、ゲートの確保が含まれます。
- 射出パラメータ: 射出圧力、温度、速度などの射出パラメータは、最適な品質と一貫性を確保するために慎重に制御および監視する必要があります。
- メンテナンス: 射出成形機と金型の定期的なメンテナンスは、最適なパフォーマンスを確保し、ダウンタイムを防ぐために重要です。
- 品質管理: 品質管理は、材料の入荷検査から最終製品の検査まで、射出成形プロセス全体にわたって実施する必要があります。 これには、反り、ヒケ、バリなどの欠陥の監視が含まれます。
- プロセスの最適化: 継続的なプロセスの改善が射出成形作業の主要な焦点である必要があります。 これには、サイクルタイム、スクラップ率、機械使用率などのプロセスパフォーマンス指標の監視と、効率と品質を最適化するために必要に応じて調整を行うことが含まれます。
全体として、射出成形には細部にまで細心の注意を払い、継続的な改善に注力する必要があります。 射出成形のベストプラクティスに従うことで、メーカーは最適な品質、効率、費用対効果を確保し、顧客のニーズを満たす高品質のプラスチック製品を生産できます。
射出成形の品質管理対策
品質管理は、最終製品が要求される仕様と基準を確実に満たすことを保証するため、射出成形にとって非常に重要です。 射出成形の品質管理手段は次のとおりです。
- 受入材料検査: 品質管理プロセスは、射出成形に使用される原材料のレビューから始める必要があります。 これには、材料のタイプ、グレード、色が正しいこと、および必要な機械的および熱的特性の仕様を満たしていることの検証が含まれます。
- 工程内検査: 射出成形中、品質管理担当者は製品が正しく成形されていることを確認するために定期的に検査する必要があります。 これには、ヒケ、反り、バリなどの欠陥の監視や、製品が必要な寸法公差を満たしているかどうかの検証が含まれます。
- 最終製品検査: 射出成形プロセスが完了したら、最終製品を検査して、必要な仕様と基準を満たしていることを確認する必要があります。 これには、製品に亀裂、気泡、ボイドなどの欠陥がなく、必要な寸法公差を満たしていることの検証が含まれます。
- 統計的プロセス制御: 統計的プロセス制御 (SPC) は、一貫して高品質の結果が得られるようにプロセスを監視および制御する方法です。 SPC では、射出圧力や温度などの重要なプロセス パラメーターに関するデータを収集し、統計分析を使用してプロセスの変動性を示す傾向とパターンを特定します。
- 継続的な改善: 品質管理は、継続的な改善のプロセスである必要があります。 これには、プロセスのパフォーマンスに関するデータの分析、改善領域の特定、品質と効率を最適化するためのプロセスの変更が含まれます。
- 文書化とトレーサビリティ: 品質管理担当者は、プロセスパラメータ、検査結果、是正措置など、射出成形プロセスの詳細な文書を維持する必要があります。 この文書はトレーサビリティを提供し、品質上の問題を迅速に特定して修正できるようにします。
全体として、品質管理は射出成形の重要な側面であり、製造プロセスのあらゆる側面に統合される必要があります。 これらの品質管理対策を実施することで、メーカーは顧客のニーズを満たす高品質のプラスチック製品を生産することができます。
射出成形でよくある欠陥とその防止方法
射出成形は複雑なプロセスであり、不適切に実行されると欠陥が生じる可能性があります。 ここでは、射出成形における一般的な欠陥とその防止方法をいくつか紹介します。
- ヒケとは製品表面のくぼみのことです。 これらは、不均一な冷却または不十分な保圧によって発生します。 ヒケを防ぐために、金型の設計に均一な肉厚と十分な抜き勾配が含まれていることを確認してください。 保圧圧力と冷却時間を調整することもヒケの防止に役立ちます。
- 反り: 反りは、金型から取り出した後の製品の歪みです。 これは、不均一な冷却または製品の内部応力によって発生します。 反りを防ぐには、金型の設計に均一な肉厚と十分な冷却時間を含めるようにしてください。 応力点が生じる可能性があるので、鋭利な角や製品形状の突然の変化を避けてください。
- バリ: バリは、製品の境界を越えて広がる余分なプラスチックであり、通常は金型のエッジの周囲に発生します。 過剰な射出圧力、不十分な型締力、または金型の摩耗が原因で発生します。 バリを防ぐには、射出圧力と型締力を調整し、金型に摩耗の兆候がないか定期的に検査してください。
- ショート ショット: ショート ショットは、金型にプラスチックが部分的に充填されている場合に発生します。 これは、不十分な射出圧力または温度、あるいは流路の閉塞または制限が原因で発生する可能性があります。 ショートショットを防ぐには、射出圧力と温度を調整し、フロー チャネルに障害物がないことを確認してください。
- 焼け跡: 焼け跡は、金型内の過熱や過度の摩擦によって生じる製品表面の暗い変色です。 焼け跡を防ぐために、金型が適切に冷却され潤滑されていることを確認し、必要に応じて射出速度と圧力を調整してください。
- ボイドと気泡: ボイドと気泡は、材料が欠落しているか、エアポケットが含まれている製品領域です。 これらは、金型内に閉じ込められた空気やガス、または材料の流れが不十分なことが原因で発生します。 空隙や気泡を防ぐには、金型の通気が正しく行われていること、および射出速度と圧力が材料の流れを均一にするのに十分であることを確認してください。
射出成形装置のメンテナンスのヒント
射出成形装置はメーカーにとって多大な投資であり、最適なパフォーマンスと寿命を確保するには適切なメンテナンスが不可欠です。 射出成形装置のメンテナンスに関するヒントをいくつか紹介します。
- 定期検査の実施: 機器を定期的に検査して、磨耗、損傷、その他の問題を特定してください。 油圧ホース、シール、その他の重要なコンポーネントを検査して、それらが良好な状態であることを確認します。
- 機器の清掃と潤滑:腐食や摩耗を防ぐために、機器を定期的に清掃して潤滑してください。 推奨される洗浄剤および潤滑剤を使用し、製造元の指示に従ってください。
- 作動油の監視と維持: 定期的に作動油を監視して、作動油が清浄で正しい粘度であることを確認してください。 必要に応じてオイルを交換し、推奨オイルの種類を使用してください。
- ヒーターバンドのメンテナンス: 定期的にチェックして、良好な状態にあり、正しく加熱されていることを確認してください。 損傷または磨耗したヒーター バンドはすぐに交換してください。
- 冷却システムの監視とメンテナンス: 過熱や反りを防ぐため、射出成形にとって非常に重要です。 冷却システムを定期的に監視して正しく機能していることを確認し、必要に応じて冷却チャネルを清掃してください。
- 列車の運転士: 損傷を防ぎ、最適なパフォーマンスを確保するために、適切な機器の操作とメンテナンスの手順について運転員を訓練します。
- 定期的なメンテナンスのスケジュールを設定する: メンテナンス スケジュールを確立し、それを遵守します。 潤滑やオイル交換などの定期的なメンテナンス作業をスケジュールし、すべてのメンテナンス作業を文書化します。
- スペアパーツを手元に用意してください: 油圧ホース、シール、ヒーターバンドなどのスペアパーツを用意してください。 これにより、損傷または磨耗した部品を迅速に交換し、ダウンタイムを最小限に抑えることができます。
射出成形装置を効率的に稼働させ、高品質の製品を生産し、長寿命を確保するには、射出成形装置の適切なメンテナンスが不可欠です。 これらのメンテナンスのヒントに従うことで、メーカーは機器を最高の状態に保ち、ダウンタイムと修理コストを最小限に抑えることができます。
適切な射出成形メーカーの選び方
適切な射出成形メーカーを選択することは、製品の品質とコストに大きな影響を与える可能性がある重要な決定です。 射出成形メーカーを選択する際に考慮すべきいくつかの要素を次に示します。
- 経験と専門知識: 射出成形に関する豊富な経験と専門知識を持つメーカーを探します。 製造プロセス、品質管理措置、認証について尋ねてください。
- 技術と設備: 最新の技術と設備を使用するメーカーを探してください。 これにより、一貫した品質、リードタイムの短縮、コスト効率の確保が可能になります。
- 材料と能力: メーカーが扱うことができる材料の種類とその能力を考慮してください。 特殊な材料を含む幅広い材料を扱い、さまざまなサイズや形状の製品を生産できるメーカーを探します。
- 品質管理対策: 品質管理に重点を置いているメーカーを探してください。 検査やテスト手順などの品質管理措置や、取得している認証について尋ねてください。
- カスタマーサービス: 優れたカスタマーサービスを提供するメーカーを探してください。 対応力、コミュニケーション、特定のニーズを満たすために協力する意欲を考慮してください。
- コストとリードタイム: プロジェクトのメーカーのコストとリードタイムを考慮します。 お客様の要件を満たす、競争力のある価格設定と現実的なリードタイムを提供するメーカーを探してください。
- 参考文献とレビュー: 参考文献を求め、製造元のオンライン レビューを確認してください。 これは、顧客の評判や他の顧客の経験をより深く理解するのに役立ちます。
これらの要素を考慮し、徹底的な調査を行うことで、プロジェクトに適切な射出成形メーカーを選択できます。 適切な経験、能力、品質への取り組みを備えた評判の良いメーカーは、お客様の製品が効率的かつコスト効率よく、正確な仕様に従って生産されることを保証します。
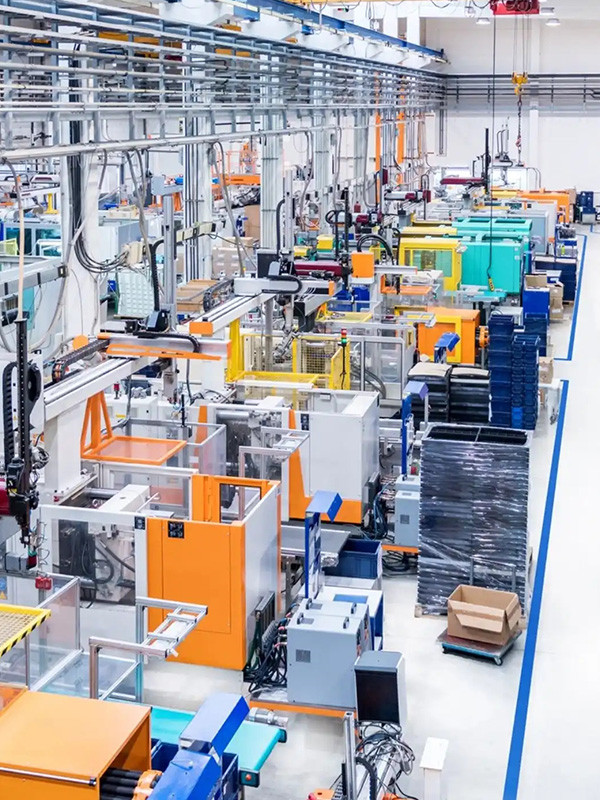
カスタムプラスチック射出成形におけるコストの考慮事項
カスタムプラスチック射出成形は、複雑で高品質の部品を大規模に製造できる、非常に汎用性の高い製造プロセスです。 ただし、この製造プロセスを使用する場合、コストを考慮することが重要な要素になります。 カスタムプラスチック射出成形における主なコストの考慮事項は次のとおりです。
- 材料費: 射出成形プロセスで使用される材料の種類と量は価格に影響します。 高性能エンジニアリング プラスチックなどの一部の材料は、他の材料よりも高価です。 材料のコストは、サプライチェーンの混乱、市場の需要、価格変動によっても影響を受ける可能性があります。
- 金型のコスト: カスタムのプラスチック射出成形では、金型、つまり部品の製造に使用される金型のコストが多額の費用となります。 部品の複雑さ、金型内のキャビティの数、金型の作成に使用される材料はすべて、工具コストに影響します。 工具は初期費用がかかる可能性がありますが、生産効率が向上するため、時間の経過とともに単価を下げることができます。
- 生産量: 生産される部品の量は、射出成形コストに影響します。 大量生産は単価の削減に役立ちますが、少量生産ではより多くの工具とセットアップ時間が必要となるため、単価が高くなる可能性があります。
- 人件費: 人件費は、特に手作業が多く必要となる複雑な部品の場合、射出成形において重要な要素です。 オペレーターのスキルレベルと部品の複雑さは配送コストに影響します。
- 品質管理コスト: 部品の完全性を確保するには、品質管理を維持することが不可欠です。 品質管理の価格には、検査機器、テスト、人件費が含まれる場合があります。
- 配送コスト: 部品を顧客または他の場所に配送すると、特に大型または重量のある部品の場合、多額の費用がかかる可能性があります。
メーカーは、これらのコスト要素を考慮し、射出成形プロセスを最適化することで、高品質の部品を低コストで製造できます。 これは、材料の無駄を削減し、生産効率を高め、セットアップと切り替え時間を最小限に抑えることによって達成できます。 経験と知識のある射出成形メーカーと協力することも、プロセスの最適化とコスト削減に役立ちます。
射出成形技術の動向と革新
射出成形技術は何年も前から存在していますが、この製造プロセスの将来を形作る多くの革新とトレンドがまだあります。 射出成形技術の主なトレンドと革新の一部を以下に示します。
- 3D プリンティングと積層造形: 射出成形業界では、3D プリンティングと積層造形の人気が高まっています。 この技術により、従来の射出成形では実現が困難または不可能だった複雑な形状や形状の作成が可能になります。
- マルチマテリアル射出成形: マルチマテリアル射出成形により、複数の材料または色の部品をワンショットで作成できます。 このプロセスにより、製造時間とコストが削減され、独自の特性と外観を備えた機能を作成できます。
- オートメーションとインダストリー 4.0: IoT センサーやロボティクスなどのオートメーションとインダストリー 4.0 テクノロジーは、射出成形機とプロセスに統合されています。 これにより、生産効率が向上し、人件費が削減され、品質管理が向上します。
- 持続可能な材料とプロセス: 企業が環境への影響を削減しようとする中、射出成形業界では持続可能な材料と方法の重要性が高まっています。 これには、廃棄物とエネルギー消費を最小限に抑える生分解性またはリサイクルされた材料とプロセスの使用が含まれます。
- スマート製造と予知保全: 機械学習や予知保全などのスマート製造テクノロジは、射出成形プロセスを最適化し、ダウンタイムを削減するために使用されています。 これにより、全体的な効率が向上し、メンテナンスコストが削減されます。
- 高機能材料: 強度、耐久性、耐熱性を向上させた材料など、射出成形用の新しい高機能材料が開発されています。 これらの材料は自動車部品から医療機器までさまざまな用途に使用できます。
これらのトレンドやイノベーションを常に最新の状態に保つことで、射出成形メーカーは競争力を維持し、顧客に高品質の部品を提供し続けることができます。 新しい技術や材料が開発されるにつれて、射出成形業界は消費者や企業の変化するニーズを満たすために進化し、適応し続けます。
射出成形における持続可能性: 廃棄物とエネルギー消費の削減
企業が環境への影響を削減し、環境に優しい製品への需要の高まりに応えるため、射出成形業界では持続可能性の重要性がますます高まっています。 射出成形メーカーが廃棄物とエネルギー消費を削減できる方法をいくつか紹介します。
- 持続可能な素材を使用する: 素材の選択は持続可能性にとって重要な要素です。 射出成形メーカーは、生分解性材料またはリサイクル材料を使用して、環境への影響を軽減できます。 たとえば、生分解性プラスチックは時間の経過とともに自然に分解され、埋め立て地の廃棄物の量を減らすことができます。 使用済みリサイクルプラスチックなどのリサイクル材料も、廃棄物とエネルギー消費の削減に役立ちます。
- 材料の無駄を削減: 射出成形メーカーは、部品と金型の設計を最適化することで材料の無駄を削減することもできます。 これには、使用する余分な材料の量を減らし、金型内のキャビティの数を最小限に抑え、部品の総重量を減らすことが含まれます。 材料の無駄を削減することで、メーカーは材料コストを節約し、環境への影響を減らすことができます。
- 生産効率の最適化: 射出成形メーカーは、生産プロセスを最適化してエネルギー消費を削減できます。 これには、高効率の射出成形機の使用、成形プロセスパラメータの最適化、ダウンタイムの最小限化が含まれます。 エネルギー消費を削減することで、メーカーはエネルギーコストを節約し、二酸化炭素排出量を削減できます。
- 持続可能な慣行の導入: 射出成形メーカーは、リサイクルおよび廃棄物削減プログラム、再生可能エネルギー源の使用、従業員やサプライヤーの間での持続可能性の促進など、自社の業務において持続可能な慣行を導入することもできます。 サプライチェーン全体で持続可能な慣行を推進することで、メーカーは業界全体のより持続可能な構築を支援できます。
- 持続可能な包装を使用する: 最後に、射出成形メーカーは持続可能な包装材料と設計を使用して、廃棄物と環境への影響を削減できます。 これには、生分解性またはリサイクル可能な包装材料の使用、包装廃棄物の最小限化、再利用可能または詰め替え可能な包装の設計が含まれます。
これらの持続可能な実践を実行することで、射出成形メーカーは環境への影響を軽減し、業界全体をより持続可能なものにすることができます。 消費者や企業にとって持続可能性の重要性がますます高まる中、持続可能性を優先する射出成形メーカーは、環境に優しい製品に対する需要の高まりに応える有利な立場にあると考えられます。
カスタムプラスチック射出成形を他の製造プロセスと比較する方法
カスタムプラスチック射出成形は、高品質のプラスチック部品を大量に生産するための一般的な製造プロセスです。 ただし、プラスチック部品の製造には他の製造プロセスもいくつか使用できますが、それぞれに長所と短所があります。 以下は、カスタムプラスチック射出成形と他の製造プロセスの比較です。
- 3D プリンティング: 3D プリンティングは、複雑な形状や幾何学形状の作成を可能にする急速に成長しているテクノロジーです。 3D プリンティングは小規模生産に使用できますが、射出成形は一般に、大型部品の生産には射出成形よりもコスト効率と効率が低くなります。
- ブロー成形: ブロー成形は、ボトルや容器などの中空のプラスチック部品を作成する製造プロセスです。 ブロー成形は大量のフィーチャーを製造するのに適していますが、射出成形は一般に射出成形よりも精度が低く、より複雑な形状や形状の作成には理想的ではない可能性があります。
- CNC 加工: CNC 加工は、材料の固体ブロックから部品を切断して成形するサブトラクティブ製造プロセスです。 CNC 機械加工は高精度の部品を少量生産するのに適していますが、一般に射出成形ほど費用対効果や効率が高くありません。
- 回転成形: 回転成形は、金型を加熱しながら直交する XNUMX つの軸の周りを回転させる製造プロセスです。 回転成形では複雑な形状の大型部品を製造できますが、射出成形は一般に射出成形よりも精度が低く、小型部品の製造には適さない場合があります。
- 熱成形: 熱成形は、プラスチック シートを加熱し、金型上で成形する製造プロセスです。 熱成形では単純な形状の大型部品を製造できますが、射出成形は一般に射出成形よりも精度が低く、より複雑な形状や形状の作成には適さない場合があります。
カスタムプラスチック射出成形は、高品質のプラスチック部品を大量に生産するための、非常に多用途でコスト効率の高い製造プロセスです。 特定の用途や生産量には他の製造プロセスの方が適している場合もありますが、速度、精度、費用対効果の点から射出成形が一般に多くの製造業者にとって好まれる選択肢です。 最終的に、製造プロセスの選択は、部品の設計、生産量、予算などのさまざまな要因によって決まります。
射出成形を外注するメリットとデメリット
射出成形をアウトソーシングすることは、独自の射出成形装置や専門知識に投資せずにプラスチック部品の製造を検討している企業にとって一般的な方法です。 アウトソーシングにはいくつかの利点がありますが、潜在的な欠点もいくつかあります。 射出成形をアウトソーシングするメリットとデメリットは次のとおりです。
長所:
- コスト削減: 射出成形を外部委託することは、多くの場合、社内に生産施設を設置するよりもコスト効率が高くなります。 これは、高価な設備や人材への投資を正当化するために、より多くの資金や量が必要な中小企業に特に当てはまります。
- 専門知識: 射出成形会社は製造を専門としており、部品が高品質基準で製造されることを保証する専門知識を持っています。 射出成形をアウトソーシングすることで、企業は経験豊富な専門家の専門知識から恩恵を受けることができます。
- 生産能力: 射出成形会社は大量の部品を迅速かつ効率的に生産できます。 これは、大量の機能を定期的に作成する必要がある企業にとって特に有益です。
- 柔軟性: 射出成形をアウトソーシングすることで、企業は生産スケジュールをより柔軟に行うことができます。 企業は、設備や金型の変更にかかる資本コストを心配することなく、生産量を調整したり、別の部品に切り替えたりすることができます。
短所:
- コミュニケーション: 射出成形をアウトソーシングすると、顧客と会社の間にコミュニケーションの問題が生じる可能性があります。 コミュニケーションの誤解や遅れは、生産のミスや遅れにつながる可能性があります。
- 品質管理: 射出成形のアウトソーシングとは、必要な品質基準を満たす部品の製造を外部の会社に依存することを意味します。 外部企業と協力する場合、品質管理は困難になる可能性があり、必要な仕様を満たす必要がある機能を受け取るリスクが常にあります。
- 依存:射出成形の外注とは、外部の生産会社に依存することを意味します。 これにより、サプライヤーの信頼性、安定性、納期に関するリスクが生じる可能性があります。
- 知的財産: 射出成形を外部委託すると、知的財産の保護にリスクが生じる可能性があります。 企業は、自社の設計と技術が適切な法的措置によって保護されていることを確認する必要があります。
カスタムプラスチック射出成形の今後の展望
カスタムプラスチック射出成形は、数十年にわたって信頼性が高く多用途な製造プロセスです。 近年、技術と材料の進歩により、射出成形の能力と可能性が高まり続けています。 カスタムプラスチック射出成形の将来の展望は次のとおりです。
- インダストリー 4.0 テクノロジーの採用: 人工知能、機械学習、モノのインターネット (IoT) などのインダストリー 4.0 テクノロジーの統合により、射出成形における自動化の推進、品質管理の向上、生産プロセスの最適化が期待されています。
- 生分解性材料の使用の増加: 環境への懸念により、射出成形における生分解性材料の採用が促進されています。 生分解性材料は、従来のプラスチックに代わる持続可能な代替品を提供し、廃棄物と環境への影響の削減に役立ちます。
- 医療機器製造の需要の拡大:高齢化と医療技術の進歩により、医療機器の必要性が高まっています。 射出成形は、その精度、速度、費用対効果の高さから、医療機器の製造プロセスとしてよく使われています。
- 3D プリンティング機能の拡張: 3D プリンティング技術の発展により、これまで射出成形では製造できなかった複雑で複雑な部品の製造が可能になりました。 ただし、3D プリンティングは射出成形に比べてまだ比較的時間がかかり、高価であるため、XNUMX つの技術は相互に置き換えるのではなく、今後も相互に補完していく可能性があります。
- 複数材料射出成形の増加: 複数材料射出成形では、XNUMX つの射出成形プロセスで XNUMX つ以上の異なる材料を使用します。 このテクノロジーは、部品の性能の向上、重量の軽減、コストの削減など、いくつかの利点をもたらします。
- 金型技術の進歩: 新しい金型材料と設計の開発により、射出成形の速度、効率、精度が向上すると予想されます。 たとえば、ツーリングのコンフォーマル冷却チャネルにより、サイクルタイムが改善され、エネルギー消費が削減されます。
結論:
カスタムプラスチック射出成形は、高品質のプラスチック部品を高い精度と効率で生産できる堅牢な製造プロセスです。 射出成形プロセスを理解し、適切な材料と金型設計を選択し、品質管理と装置メンテナンスのベスト プラクティスを実装することで、企業は射出成形操作を最適化し、大きな成功を収めることができます。 業界に新たなトレンドやイノベーションが出現するにつれ、カスタムプラスチック射出成形の持続可能性、効率性、収益性を高めるために常に最新情報を入手し、新たな機会を模索することが不可欠です。