大量射出成形
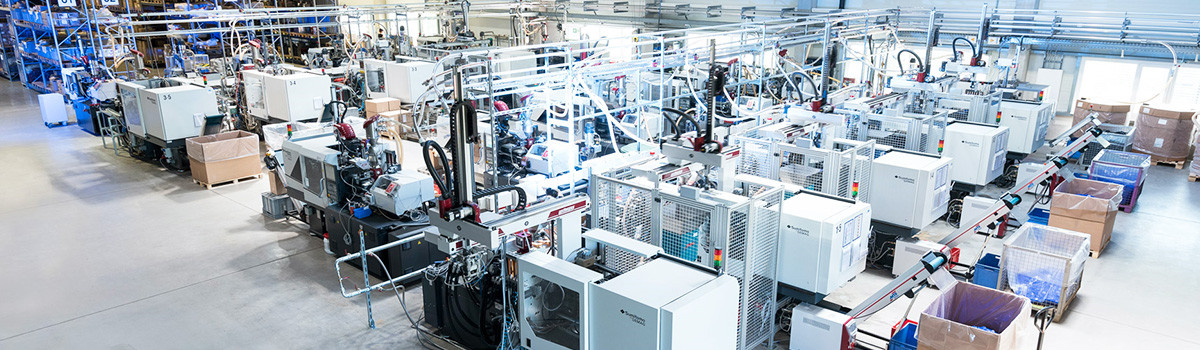
大量射出成形(大量生産):プラスチック射出成形
数千を超えるプラスチック射出成形およびプラスチック製造施設が世界中から選択できますが、成形会社を際立たせる最高の品質の XNUMX つとは何ですか? プロバイダーを選択するときは、多くの要因を考慮する必要があります。 能力、品質保証、会社の評判、コスト、納期など。 ニーズに合った適切なプラスチック射出成形機を見つけるのは時間がかかるように思えるかもしれませんが、最初に少量および大量の要件を特定し、時間の経過とともにそれらがどのように変化するかを判断することが、選択肢を絞り込むのに役立ちます。
DJmolding の大量射出成形サービス
DJmolding の生産施設は、複数の機械と熟練したオペレーターによるハイエンドで効率的な操業です。 多彩な設備により、業種、プラスチックの品質、生産数に応じた幅広い作業に対応できます。 少量から大量の製品まで、設計から製造まで社内で完了できるため、コスト、品質、リードタイムの面でお客様に競争上の優位性を提供します。
DJmolding の射出成形は、実証済みの大量生産プロセス技術です。 これは、完全な量産品質の部品を月に最大数百万個の量で提供する専門サービスです。 大量のプラスチック射出成形により、高公差精度、低スクラップ損失、およびコスト削減が可能になります。
当社の大量成形装置の多くはコンピュータ化されており、機械システムを使用して効率を高め、品質を保護しています。 すべての大量生産に品質管理がどのように組み込まれているかを確認するには、当社の「品質管理システム」を必ずご覧ください。 このタイプの製造は、中規模および大規模企業または大量生産に最適です。
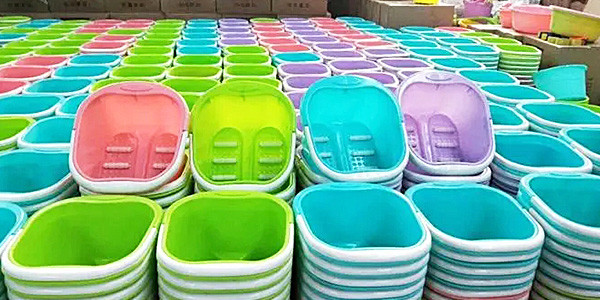
DJmolding の大量射出成形の利点
*より多くの部品をより速いペースで生産します
*メーカーのユニットコストとサイクルタイムを削減
※正確かつ安定した高品質な部品の量産
*多くの場合、生産は、業務時間外であっても、堅牢で信頼性の高い機械を使用して自動化できます。
*最小限のポストプロダクション作業
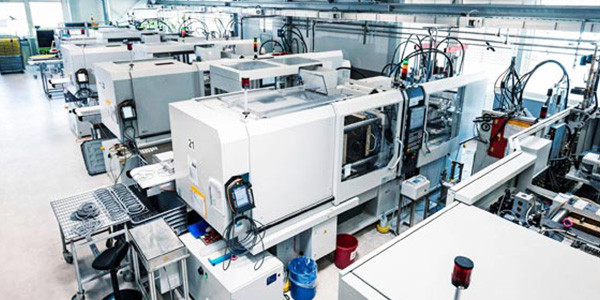
カスタマイズされた大量成形(プラスチック射出製品)
DJmolding のカスタム金型と大量成形には、プロトタイプから量産までのすべてが含まれます。 当社の大量生産金型は、短期生産、大量生産、または複数キャビティのいずれであっても監視および制御されているため、金型の設計と構築のあらゆる側面を安心して行うことができます。 生産の詳細にこのように注意を払うことで、プロセスの各段階を通じて、目標、目的、および事前に設定されたプロジェクトの結果が予定どおりであることが証明されます。 設計から製造までのすべての大量成形は社内で完了し、コスト、品質、納期の面でお客様に競争力のある優位性を提供します。
DJmolding はクライアントと協力して製品の設計とエンジニアリングを行い、コスト効率を高めるために最も効果的な大量の金型を開発します。 当社はプラスチック射出成形業界専用の高品質な大量金型を提供し、幅広いサービスを提供しています。 少量成形からインサート成形、パッド印刷まで、PTI, Inc. はプラスチック射出成形サービスにおいて信頼できるブランドです。
DJmolding は、医療、電気、ハンドツール、通信、自動車産業などのさまざまな分野の顧客向けにプロトタイプコンポーネントを成形します。 85 ~ 500 トンの射出および圧縮プレスを含む、DJmolding の大量成形装置の多くはコンピュータ化されており、機械システムを使用して効率を高め、品質を保護しています。 DJmolding では、あらゆるベンチャーに対してパートナーシップの姿勢をとり、包括的なプラスチック射出成形体験を提供するように設計された施設に長年にわたるプラスチック射出成形の知識と技術的専門知識をもたらします。
大量の金型を構築するには、プラスチック部品のほぼ無限の形状を備えた射出成形金型を迅速に作成するための技術、機器、資格のある金型ビルダーの組み合わせが必要です。
DJmolding は、設計から納品まで、最初から最後までツール構築プログラム全体を調整できます。 PTI の使命は、品質保証プログラムに支えられ、顧客の要件と期待を完全に満たす、またはそれを超える成形製品を提供することです。 会社の経営陣は継続的な品質の向上に取り組んでいます。 優れた品質と効率的な大量成形サービスについては、DJmolding にお問い合わせください。 今日。
多くの企業には、このような包括的な金型製作の最初から最後までの経験を提供する能力がありません。 数個の高速プロトタイプ、数千個の市場投入可能な消費者向けプラスチック、または XNUMX 万個の量産部品を探している場合でも、DJmolding は必要なものを提供します。 少量でも大量でも、私たちは各注文が同じレベルの品質であることを誇りを持って主張します。 今すぐ当社の専門家にお問い合わせください。
DJmolding は、設計から納品まで、最初から最後までツール構築プログラム全体を調整できます。 優れた品質と効率的なサービスをご希望の場合は、以下に情報を送信して見積もりをリクエストしてください。 info@jasonmolding.com
大量射出成形の製造プロセスでは、多数の同一のプラスチック部品が製造されます。 このプロセスは費用対効果が高く、効率的であり、一貫した高品質の製品を提供できるため人気があります。 このブログ投稿では、長所、短所、用途など、大量射出成形について必要なすべてを説明します。
大量射出成形とは何ですか?
大量射出成形は、多数の同一のプラスチック部品を製造する製造プロセスです。 このプロセスでは、溶融したプラスチック材料を高圧および高温で金型キャビティに射出し、冷却して所望の形状に固化させます。 この高度に自動化されたプロセスでは、XNUMX 回の生産で数千、さらには数百万もの同一の部品を生産できます。
大量射出成形を成功させるには、高効率の生産プロセスが鍵となります。 このプロセスには、高速射出成形機と自動化システムの利用が伴い、部品の迅速かつ正確な生産が可能になります。 さらに、メーカーは、高品質の金型を使用し、特定の射出パラメータを適用することで、各要素を仕様どおりに製造することができます。
大量射出成形の最も重要な利点の XNUMX つは、同一の部品を迅速かつコスト効率よく大量に製造できることです。 この製造プロセスは、自動車、消費財、医療機器、エレクトロニクス業界に最適です。
大量射出成形のもう XNUMX つの利点は、公差が厳しい複雑な部品を製造できることです。 射出成形プロセスは正確かつ一貫しているため、部品間のばらつきが最小限に抑えられた複雑なディテールが得られます。
多くの利点があるにもかかわらず、大量射出成形にはいくつかの制限があります。 たとえば、非常に大きな部品や最小限の部品を製造するには、必要な金型のコストと複雑さが法外に高額になる可能性があるため、より良い選択肢がある可能性があります。 さらに、大量のプラスチックは環境に影響を与える可能性があるため、製造業者は持続可能性とリサイクルの取り組みを考慮することが不可欠です。
大量射出成形は、同一のプラスチック部品を迅速かつコスト効率よく大量に生産できる、非常に効率的かつ効果的な製造プロセスです。 これは幅広い業界にとって理想的な選択肢であり、その精度と一貫性により、公差が厳しい複雑な部品の製造に人気があります。 いくつかの制限はありますが、大量射出成形の利点により、高品質のプラスチック部品を大量に生産しようとしているメーカーにとって貴重なツールとなっています。
大量射出成形はどのように行われるのですか?
このプロセスにはいくつかの重要なステップが含まれており、それぞれが高品質の部品を製造するために重要です。 このブログ投稿では、主要な手順や考慮事項など、大量射出成形の仕組みについて概要を説明します。
金型の設計と準備
大量射出成形の最初のステップは、メーカーが部品の製造に使用する金型を設計して準備することです。 必要な部品を製造するために必要なすべての仕様を満たす正確な設計を作成するには、金型メーカーとの協力が必要です。 通常、メーカーはスチールまたはアルミニウムから金型を作成し、射出成形プロセスの高圧と高温に耐えるように設計します。
材料の準備
次のステップは、メーカーが部品の製造に使用するプラスチック材料を準備することです。 使用する樹脂の種類は特定の要件によって異なるため、目的の機能を作成するには、適切なプラスチック樹脂を選択することが重要です。 次に、樹脂を射出成形機に供給し、加熱して溶かして液体にします。
射出成形プロセス
射出成形プロセスは、溶融したプラスチック材料が高圧および高温で金型キャビティに射出されるときに始まります。 プラスチックが冷えて固化するまで、金型は圧力下で閉じた状態に保たれます。 この時点で金型が開かれ、部品が取り出されます。
品質管理
部品が製造されると、要求仕様を満たしていることを確認するために厳格な品質管理プロセスが行われます。 これには、各部品のサイズ、形状、品質が一貫していることを確認するための目視検査、測定、およびテストが含まれる場合があります。
大量射出成形に関する考慮事項
大量射出成形を使用する場合、メーカーは次のような考慮事項を考慮する必要があります。
- マシンの選択: 高速射出成形機は、部品を迅速かつ正確に製造できるため、通常、大量生産に使用されます。
- 金型設計: 金型の設計は、精密であり、プロセスの高圧および高温に耐えることができる必要があるため、射出成形プロセスを成功させるために非常に重要です。
- 材料の選択: プラスチック樹脂の選択は、製造される部品の品質と性能に影響を与える可能性があるため、作業に適した材料を選択することが不可欠です。
- 費用: 大量射出成形はコスト効率の高い製造プロセスですが、金型の設計、材料の選択、製造に関連するコストを考慮する必要があります。
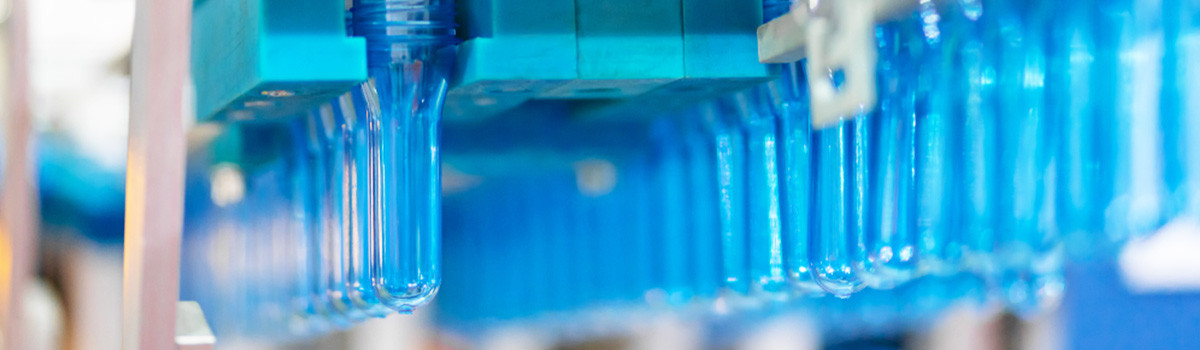
大量射出成形の利点
大量射出成形は、比類のない速度と効率で同一のプラスチック部品を大量に生産できるようにすることで、製造業界に革命をもたらしました。 このプロセスは多くの利点があるためさまざまな分野で人気があり、コストの削減、廃棄物の削減、生産量の増加を目指す企業にとって頼りになる製造方法となっています。
- 費用対効果の高い生産: 大量射出成形は効率が高く自動化されているため、他の製造プロセスに比べてコスト効率が高くなります。 金型を設計して準備したら、生産プロセスを継続的に実行して、最小限の人件費や材料費で数千または数百万の同一部品を生産できます。
- 高い生産性: 高速射出成形機を使用すると、メーカーは正確な部品を短時間で大量に生産できます。 これは、需要の変化に応じて生産量が急速に増減する可能性があることを意味します。
- 一貫した品質: 大量射出成形の精度と一貫性により、公差が厳しく複雑な部品の製造に最適です。 このプロセスにより高い精度が可能になり、製造される各部品が他の部品と同一であることが保証されます。
- 部品設計の多様性: 大量射出成形では、複雑な形状を含む幅広いデザインや形状の部品を製造できます。 これは、メーカーが特定の顧客要件を満たす機能を備え、設計や製品仕様の変更に簡単に対応できることを意味します。
- 廃棄物の削減: 大量射出成形では高品質の金型と正確な射出パラメータを使用することで、製造プロセス中に発生するスクラップや廃棄物の量を最小限に抑えます。 これは、メーカーが材料の無駄を最小限に抑えて部品を製造し、コストと環境への影響を削減できることを意味します。
- 生産効率の向上: 大量の射出成形は高度に自動化されているため、必要な労働力は最小限で、ほとんど介入することなく連続的に実行できます。 これにより、メーカーは手作業や監督を必要とせずに部品を迅速かつ効率的に生産できるため、生産効率の向上につながります。
大量射出成形のデメリット
大量射出成形は、同一のプラスチック部品を迅速かつコスト効率よく大量に製造するために広く使用されている製造プロセスです。 コストパフォーマンスや品質の安定性など多くのメリットがある一方で、デメリットもあります。 このブログ投稿では、大量射出成形の欠点のいくつかを検討します。
- 高額な初期投資: 大量射出成形の主な欠点の XNUMX つは、金型の設計と製造に必要な初期投資の増加です。 このコストは、特に中小企業や特定の部品用にカスタマイズされた金型を必要とする企業にとっては、かなりの額になる可能性があります。
- 長いリードタイム:大量射出成形用の金型の設計と製造のプロセスには数週間、場合によっては数か月かかる場合があり、結果としてリードタイムが長くなります。 これは、部品を迅速に生産したり、需要の変化に対応したりする必要がある企業にとっては不利になる可能性があります。
- 材料の選択肢が限られている: 大量の射出成形には多くの種類のプラスチック樹脂が利用可能ですが、特定の用途によっては選択が制限される場合があります。 一部のプラスチック樹脂はその特性により大量生産に適さない場合があり、材料の選択が制限される可能性があります。
- 設計の柔軟性が限られている: 大量射出成形は、特定の仕様に従って金型を設計する必要がある精密なプロセスです。 これは、特にその位置に複雑な形状やその他の独特の設計要件がある場合、このプロセスで製造される部品の設計に制限がある可能性があることを意味します。
- 高額なメンテナンスと修理のコスト: 大量の射出成形で使用される金型は、最適なパフォーマンスを確保するために定期的にメンテナンスおよび修理する必要があります。 主に金型を頻繁に使用する場合、または長期間使用する場合、メンテナンスと修理のコストが多額になる可能性があります。
これらの欠点にもかかわらず、大量射出成形は依然として、同一のプラスチック部品を大量に生産するための一般的で効果的な製造プロセスです。 このプロセスの長所と短所を慎重に検討することで、メーカーは、このプロセスが自社の特定の生産ニーズにとって正しい選択であるかどうかについて、十分な情報に基づいた意思決定を行うことができます。
大量射出成形に使用される材料
最終製品の品質と性能を確保するには、大量射出成形に適切な材料を選択することが重要です。 この記事では、大量射出成形に使用される材料、その特性、および用途について詳しく説明します。
ポリプロピレン(PP)
ポリプロピレンは、低コスト、強度対重量比、および耐久性により、大量射出成形で一般的に使用される熱可塑性ポリマーです。 PP は自動車、包装、消費財の製造に多用途に使用できます。 PP を射出成形に使用する利点には、軽量であること、耐薬品性、寸法安定性があり、精密部品に最適です。
アクリロニトリルブタジエンスチレン(ABS)
ABS は、靭性、耐衝撃性、高光沢仕上げで知られる熱可塑性ポリマーです。 この材料は、玩具、自動車部品、電子機器の筐体などに一般的に使用されています。 ABS の耐衝撃性により、衝撃や衝撃を受ける細部に適しています。 また、加工が容易で表面仕上げも優れているため、大量生産に最適です。
ポリカーボネート(PC)
ポリカーボネートは、耐衝撃性、光学的に透明、耐熱性に優れた熱可塑性ポリマーです。 自動車、航空宇宙、エレクトロニクス産業で人気のある材料です。 PC の利点には、優れた耐衝撃性、光学的透明性、耐熱性が含まれるため、高温の用途、レンズ、スクリーンに最適です。
ポリエチレン(PE)
ポリエチレンは、柔軟性、強靭性、耐薬品性に優れた熱可塑性ポリマーです。 包装材、ビニール袋、農業用フィルムの製造によく使用されます。 PE の耐薬品性、柔軟性、軽量な性質により、化学処理装置、化学薬品の包装、および部品を曲げたり曲げたりする必要がある用途に最適です。
ポリエチレンテレフタレート(PET)
PET は、高い強度対重量比、透明性、およびバリア特性を備えた熱可塑性ポリマーです。 飲料ボトル、食品容器、包装資材などを製造しています。 PET の利点には、強度と重量のバランス、透明性、バリア特性があり、内容物を湿気や酸素から保護する必要がある飲料ボトルや包装など、強度が必要な用途に最適です。
ポリスチレン(PS)
ポリスチレンは、軽量でコスト効率が高く、優れた断熱特性を備えた熱可塑性ポリマーです。 PS は、使い捨てカップ、包装材料、断熱材の製造に一般的に使用されており、その利点には、低コスト、軽量、優れた断熱特性が含まれます。
大量生産に使用される射出成形機の種類
このプロセスには、溶融したプラスチック材料を金型キャビティに射出することが含まれ、そこで凝固して金型の形状が形成されます。 射出成形機にはさまざまな種類があり、それぞれ特定の種類の生産に適しています。 大量生産に使用される主なタイプの射出成形機は次のとおりです。
- 油圧式射出成形機: これらの機械は、油圧を使用して金型を移動し、溶融プラスチックをキャビティに射出します。 これらは生産量が多いことで知られていますが、サイクルタイムが遅いため、高精度および高速アプリケーションでの使用は制限されています。
- 電動射出成形機: これらの機械は、射出ユニットと金型を駆動するために電気サーボモーターを使用します。 高い精度と速度を実現し、医療機器やエレクトロニクスなどのハイテク産業に最適です。
- ハイブリッド射出成形機: これらのマシンは、両方の長所を組み合わせています。 油圧システムと電気システムを使用して射出ユニットと金型を駆動します。 ハイブリッド エンジンは効率的かつ高速で、高い生産量を実現するため、大量生産に最適です。
- ツーショット射出成形機: これらの機械は、XNUMX つの異なる材料または色を必要とする複雑な部品を製造します。 この装置には XNUMX つの射出ユニットがあり、これらが連携して最終部品を作成します。 ツーショット射出成形機は、複数のコンポーネントを含む高品質の製品を製造するのに最適です。
- 多材料射出成形機:これらの機械は、さまざまな材料で作られた部品を製造します。 複数の射出ユニットを備えており、他の材料を同時に使用できます。 多材料射出成形機は、強度、耐久性、柔軟性などのさまざまな特性が必要な部品の作成に最適です。
- 液体射出成形機: これらの機械は、液体シリコーンゴム (LSR) 製の部品を製造するために使用されます。 機械は LSR を金型キャビティに射出し、そこで固化して金型の形状を形成します。 液体射出成形機は、医療機器や自動車部品など、高い精度と耐久性が要求される部品の製造に最適です。
大量生産のための射出成形プロセスのステップ
このプロセスには、溶融したプラスチック材料を金型キャビティに射出することが含まれ、そこで凝固して金型の形状が形成されます。 大量生産のための射出成形プロセスに含まれる手順は次のとおりです。
- 材料の選択: 射出成形プロセスの最初のステップは、部品の製造に適した材料を選択することです。 選択される材料は、強度、耐久性、柔軟性などの必要な特性を備え、射出成形機と互換性がある必要があります。
- 金型設計: 材料を選択したら、次のステップは金型を設計することです。 金型は、形状、サイズ、機能など、製造される部品の仕様に正確に合わせて準備する必要があります。 金型は、使用する射出成形機の種類と製造プロセスの特定の要件も考慮する必要があります。
- マシンのセットアップ: 金型の設計が完了したら、射出成形機をセットアップします。 これには、金型をデバイスに取り付け、適切な温度と圧力設定を設定し、すべてが正しく動作することを確認することが含まれます。
- 注入: 射出プロセスは、溶融プラスチック材料が金型キャビティに射出されるときに始まります。 これは、特定の速度と圧力で材料を金型に押し込む高圧射出ユニットを使用して行われます。
- 冷却:溶融プラスチック材料が金型キャビティに射出された後、冷却して固化する必要があります。 これは、金型キャビティ内に冷たい空気または水を循環させて材料の温度を下げることによって行われます。
- 排出: プラスチック材料が冷えて固まると、金型が開かれ、部品が取り出されます。 突き出しプロセスでは、機械または油圧システムを使用して部品を金型キャビティから押し出します。
- 品質管理: 部品が取り出された後、品質管理検査が行われ、要求された仕様を満たしているかどうかが確認されます。 これには、部品が高品質で欠陥がないことを確認するための目視検査、測定、テストが含まれる場合があります。
大量射出成形の設計上の考慮事項
大量射出成形用のプラスチック部品を設計するには、部品を効率的かつコスト効率よく製造できるようにするために、いくつかの要素を慎重に考慮する必要があります。 大量射出成形の設計上の考慮事項をいくつか示します。
- 壁の厚さ: プラスチック部品の壁の厚さは、射出成形において重要な考慮事項です。 不均一な冷却やピースの反りを防ぐために、壁の厚さは均一である必要があります。 薄壁は材料の使用量とサイクルタイムを削減できるため、大量生産に最適ですが、厚壁は追加の強度が必要な部品に適しています。
- パーツのサイズと形状: 部品のサイズと形状は射出成形プロセスに影響します。 要素が大きすぎるか複雑すぎると、より長いサイクル時間や特殊な装置が必要となり、生産コストが増加する可能性があります。 シンプルな幾何学的形状は大量生産に最適です。
- 抜き勾配角度: 抜き勾配角度は、部品の取り出しを容易にする金型キャビティ壁の角度です。 部品を金型から素早く取り出すには、部品設計に抜き勾配を含めることが不可欠です。 抜き勾配のない量では、亀裂や変形など、コストのかかる製造上の問題が発生する可能性があります。
- ゲートの位置とサイズ:溶融プラスチック材料が金型キャビティに入るゲートの位置とサイズは、射出成形の設計上の重要な考慮事項です。 ゲートの位置は、部品の構造的完全性に影響を与えない領域に配置する必要があります。 ゲート サイズは、材料が正しく流れるのに十分な大きさである必要がありますが、位置に欠陥が生じるほど大きくない必要があります。
- 材料の選択: 部品を効率的かつコスト効率よく製造できるようにするには、材料の選択が不可欠です。 材料の選択は、強度、耐久性、柔軟性などの部品の特定の要件に基づいて行う必要があります。
- 表面仕上げ: 部品の表面仕上げは、射出成形において重要な考慮事項です。 額の表面仕上げは滑らかで、反りやヒケなどの欠陥がない必要があります。 ゲートの配置、金型設計、材料の選択を適切に行うことで、滑らかな表面仕上げを実現できます。
- 公差: 公差は、部品の寸法に許容される変動の程度です。 部品を正確かつ精密に製造できるように、部品の設計段階で公差を考慮する必要があります。
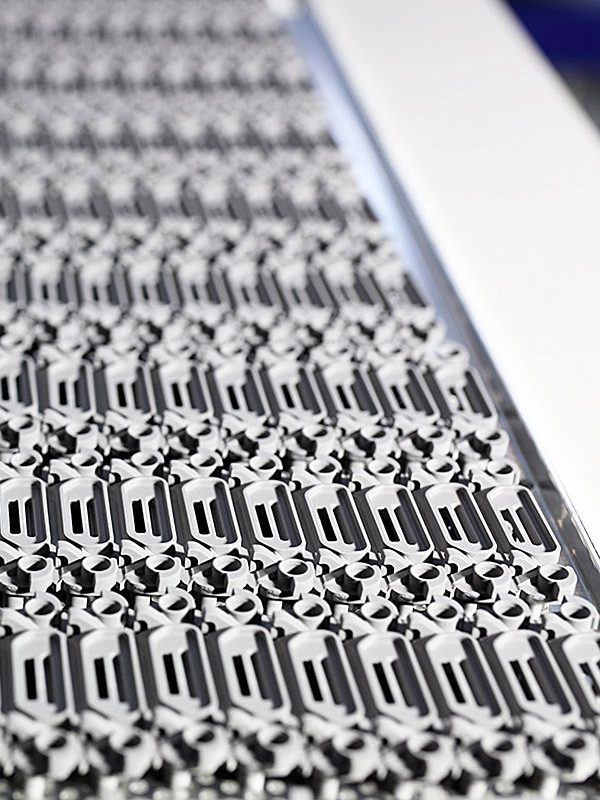
大量射出成形における品質管理対策
品質管理は、生産される部品が要求仕様を満たし、欠陥がないことを保証するため、大量の射出成形には不可欠です。 以下に、大量射出成形で使用される品質管理手段をいくつか示します。
- 製造工程中の検査: 生産プロセス中の定期的なレビューは、欠陥を早期に特定し、より重大な問題になるのを防ぐのに役立ちます。 これには、部品が正しく製造されていることを確認するための目視検査、測定、テストが含まれる場合があります。
- 統計的プロセス管理 (SPC): SPC は、生産プロセスを監視および制御するために使用される統計的手法です。 これには、生産プロセスに関するデータを収集し、それを分析して、プロセスの問題を示す可能性のある傾向とパターンを特定することが含まれます。 SPC は、部品に欠陥が生じる前に問題を検出し、修正するのに役立ちます。
- 自動化された機器の使用: ロボットやセンサーなどの自動化機器は、生産プロセスの一貫性と精度の向上に役立ちます。 機械装置は人的ミスのリスクも軽減し、結果として欠陥が少なくなります。
- 金型のメンテナンス:製造される部品の高品質を確保するには、金型の適切なメンテナンスが重要です。 これには、金型を定期的に洗浄し、金型が正しく機能することを確認するために必要な修理や交換が含まれます。
- 製造後の検査: 部品が製造された後、最終検査を受けて、要求された仕様を満たしていることを確認します。 これには、部品に欠陥がないことを確認するための目視検査、測定、テストが含まれる場合があります。
- トレーニングと教育: 従業員の適切なトレーニングと教育は、生産プロセスの品質を向上させることができます。 従業員は、問題が発生したときに確実に特定して修正できるように、適切な生産技術と品質管理方法についてのトレーニングを受ける必要があります。
- 継続的な改善: 大量射出成形の品質管理には継続的な改善が不可欠です。 製造プロセスを定期的に見直し、改善すべき領域を特定することで、製造業者は欠陥を減らし、製造される部品の品質を向上させることができます。
大量射出成形のコスト分析
大量射出成形は、プラスチック部品を大量に生産するためのコスト効率の高い製造プロセスです。 ただし、射出成形による部品の製造コストは、いくつかの要因によって変動する可能性があります。 大量射出成形のコスト分析に関する考慮事項をいくつか示します。
- 材料費: 原材料のコストは、射出成形の価格に影響を与える最も重要な要素の XNUMX つです。 使用される材料の種類と品質は価格に影響し、一部の材料は他の材料よりも高価です。 メーカーは、部品の特定の要件に基づいて適切な材料を選択する必要があります。
- 工具コスト: 射出成形に必要な金型やその他の機器を含む工具のコストも、生産コストに影響を与える重要な要素です。 工具のコストは、部品の複雑さ、金型のサイズ、金型内のキャビティの数によって異なります。
- 人件費: 射出成形では機械を操作し、生産プロセスを監督する熟練労働者が必要となるため、人件費は重要な要素となります。 人件費は勤務地や労働者の経験によって異なります。
- オーバーヘッドコスト: 光熱費、家賃、その他の経費を含む諸経費も射出成形コストに影響を与える可能性があります。 これらのコストは、製造施設の場所や業務の規模によって異なります。
- 生産量: 生産量は射出成形コストに影響を与える重要な要素です。 生産量が増えると、規模のメリットにより部品あたりのコストが削減されます。
- 部品設計: 設計は射出成形コストにも影響を与える可能性があります。 要素が複雑であったり、特殊な設備が必要な場合は、生産コストが増加する可能性があります。
- 品質管理: 検査やテストなどの品質管理措置のコストも、生産コストに影響を与える可能性があります。 これらの対策は、製造された部品が要求仕様を満たし、欠陥がないことを確認するために必要です。
大量の射出成形を使用する産業
大量射出成形は、大量のプラスチック部品を迅速かつ効率的に生産できる製造プロセスであり、広く使用されています。 大量射出成形に大きく依存している業界を以下に示します。
- 自動車産業: 自動車産業は、大量射出成形の最も重要なユーザーの XNUMX つです。 このプロセスでは、ダッシュボード部品、ドアハンドル、インテリアトリムピースなどのさまざまなプラスチック部品が製造されます。
- 消費財業界: 大量射出成形では、家電製品、玩具、電子機器などのさまざまな消費者製品が製造されます。 このプロセスは、メーカーが大型部品をより安価に製造できるため、好まれています。
- 医療産業: 医療業界では、診断機器、手術器具、使い捨て医療用品など、さまざまな医療機器に高品質で精密なプラスチック部品が必要です。 これらの部品を正確かつ一貫して製造できるため、大量射出成形が推奨されます。.
- 産業:包装業界は、さまざまなプラスチック容器、蓋、クロージャを製造するために大量射出成形に大きく依存しています。 このプロセスはコスト効率が高く、メーカーはさまざまな形状やサイズを迅速に作成できます。
- 航空宇宙産業: 航空宇宙産業では、高温や高圧などの極端な条件に耐えられる高性能プラスチック部品が必要です。 航空機の内外装部品、航空電子機器、電子機器などのコンポーネントは、大量射出成形によって製造されます。
- 建設業: 建設業界では、大量の射出成形を使用して、窓枠、配管、断熱材などのさまざまなプラスチック部品を製造しています。 このプロセスは、耐久性があり、環境要因に耐性のある部品を大量に生産できるため、好まれています。
- スポーツおよびレクリエーション産業: 大量射出成形では、ヘルメット、保護具、玩具など、スポーツおよびレクリエーション産業向けのさまざまなプラスチック部品が製造されます。 このプロセスは、軽量で耐久性があり、見た目にも美しい部品を作成できるため、好まれています。
医療業界における大量射出成形の利点
医療産業は、世界最大かつ急速に成長している産業の XNUMX つです。 技術の進歩と医療機器や医療機器の需要の増加に伴い、高品質のコンポーネントを生産できる効率的な製造プロセスが求められています。 大量射出成形は、医療業界にいくつかのメリットをもたらすプロセスの XNUMX つです。 医療業界における大量射出成形の利点をいくつか見てみましょう。
- 費用対効果の高い: 大量射出成形は、ユニットあたりのコストを抑えて大量のプラスチック部品を生産する、コスト効率の高い製造プロセスです。
- 一貫性: 大量射出成形により、高粘度かつ高精度の部品の製造が可能になり、各部品が必要な仕様を確実に満たすことができます。
- カスタマイズ: このプロセスにより、色、テクスチャ、素材などの特定の要件に合わせて機能をカスタマイズできます。
- その2:シャフトスピード(回転数): 大量の射出成形により、ポジションを迅速に生産できるため、リードタイムが短縮され、効率が向上します。
- 品質: 大量射出成形プロセスにより、医療機器に求められる厳しい基準を満たす高品質の部品が製造されます。
- 無菌性: このプロセスは無菌環境で行われ、製造される部品が汚染されておらず、医療用途に安全であることが保証されます。
- 耐久性: 大量の射出成形を使用して製造された部品は耐久性があり、過酷な環境に耐えることができるため、寿命が長くなり、交換の必要性が減ります。 医療業界では、デバイスや機器が継続的な使用や化学薬品やその他の過酷な要素への潜在的な暴露に耐える必要があるため、耐久性は非常に重要です。
- 複雑: 大量射出成形プロセスにより、複雑なデザインの複雑な部品の製造が可能になり、現代医療の厳しい要件を満たす医療機器を確実に製造できます。 このプロセスは、医療機器や機器に不可欠な独自の機能と設計を備えた複雑なコンポーネントを製造するのに理想的です。
- 汎用性: 大量射出成形では、さまざまな形状やサイズのさまざまな部品を製造できるため、さまざまな医療用途のコンポーネントの作成に最適です。
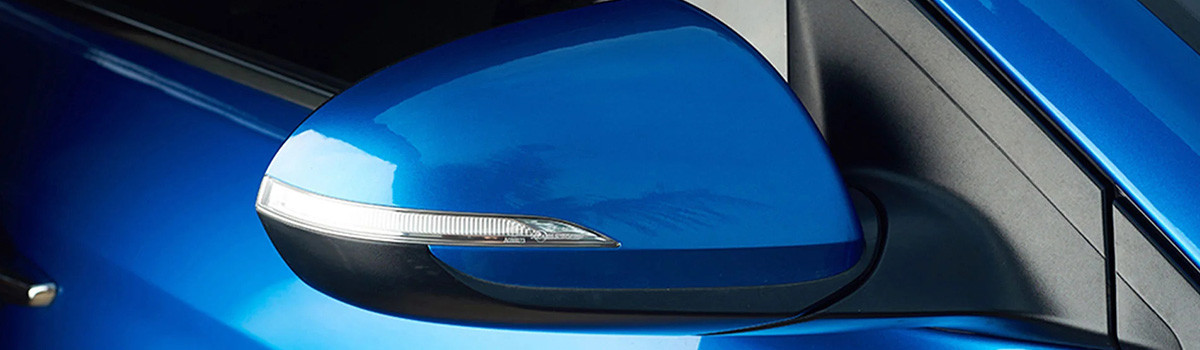
自動車産業向けの大量射出成形
射出成形は、溶融プラスチックを金型キャビティに射出してさまざまなプラスチック部品を作成する製造プロセスです。 このプロセスは、ドアパネル、ダッシュボード、計器パネル、内装トリム、車体外装部品などの複数の部品を製造するために自動車業界で広く使用されています。 大量射出成形は、メーカーが同一の部品を迅速に大量に生産できるようにする特殊な技術です。
大量射出成形は、自動車業界にいくつかの利点をもたらす非常に効率的な製造技術です。 これらの利点には次のようなものがあります。
- 生産コストの削減 – このプロセスは高度に自動化されているため人件費が削減され、金型を使用することでメーカーは同一の部品を低価格で製造できます。
- 部品の一貫性の向上 – 大量の射出成形により、同一部品の製造が可能になり、製造プロセスにおけるばらつきが低減され、質感が向上します。
- 生産時間の短縮 – このプロセスは高度に自動化されているため、メーカーは大量の部品を迅速に生産でき、リードタイムを短縮できます。
- 高品質の部品 – 金型を使用することで、欠陥や不一致が最小限に抑えられた、高品質の部品が製造されることが保証されます。
- 設計の柔軟性 –射出成形を使用すると、複雑な形状やデザインを迅速に作成できるため、設計者の計画に大きな柔軟性が与えられます。
射出成形は、効率の向上、コストの削減、部品の品質の向上といった多くのメリットをもたらすため、自動車産業にとって理想的な製造技術です。 特に大量射出成形は、メーカーが同一の部品を迅速かつ効率的に大量に生産できるようにする特殊な技術です。
自動車産業は、さまざまな自動車や車両部品の製造に射出成形に大きく依存しています。 外装ボディ部品から内装トリムやダッシュボードに至るまで、射出成形は自動車業界において不可欠な製造プロセスとなっています。 大量射出成形を使用すると、メーカーは一貫性と品質が向上し、同一の部品を低コストで大量に生産できます。
消費財業界向けの大量射出成形
大量射出成形は、優れた精度と一貫性で高品質の部品を大量に生産できるため、消費財業界で広く採用されている製造プロセスです。 このプロセスは、玩具、台所用品、包装材などの消費財の製造に一般的に使用されています。 このブログ投稿では、消費財業界における大量射出成形の利点を探ります。
大量射出成形の利点:
- 費用対効果の高い: 大量射出成形の主な利点の XNUMX つは、大量の部品をコスト効率よく製造できる方法であることです。 このプロセスは高度に自動化されているため人件費が削減され、金型は再利用できるため材料費も削減されます。
- 一貫性と精度:射出成形は、部品の製造において優れた精度と一貫性を実現します。 これは、金型が要素の仕様に正確に従って設計されており、すべての部品が同じ品質とサイズであることが保証されるためです。
- 迅速な生産:大量の射出成形は即時プロセスであり、大量の部品を比較的迅速に生産できます。 そのため、素早い納期が必要な消費財の製造に最適です。
- カスタマイズ: 射出成形では、さまざまな材料、色、表面仕上げを使用して部品をカスタマイズできます。 この柔軟性により、消費者の特定のニーズや要件を満たす部品を製造することが可能になります。
消費財業界における大量射出成形の用途:
- 包装材料:射出成形は、ペットボトル、瓶、容器などの包装材料の製造に広く使用されています。
- おもちゃ: 射出成形は、大量の部品を迅速に製造できるため、人気のある玩具製造方法です。
- キッチン用品: 射出成形により、カップ、皿、調理器具などのさまざまなキッチン用品が製造されます。
- エレクトロニクス: 射出成形は、ハウジング、ボタン、スイッチなどのさまざまな電子部品の製造に使用されます。
航空宇宙産業向けの大量射出成形
航空宇宙産業では、航空機の安全性と効率を確保するために、高品質で精密な部品が求められています。 大量射出成形は、安定した品質で高品質の部品を大量に生産するためのコスト効率の高いソリューションを提供するため、航空宇宙産業にとって不可欠なプロセスとなっています。 このブログ投稿では、航空宇宙産業向けの大量射出成形について説明します。
航空宇宙産業における大量射出成形の利点:
航空宇宙産業では、極端な温度や圧力に耐える、軽量で耐久性のあるコンポーネントが必要です。 大量射出成形には、このような要素の製造に次のような多くの利点があります。
- 費用対効果の高い生産: 大量射出成形では、大量の部品を迅速に生産できるため、製造コストが削減されます。
- 一貫した品質: 自動化されたプロセスにより、製造される各部品が同じ高品質であることが保証され、これは航空機部品の安全性と信頼性にとって極めて重要です。
- 複雑な形状: 射出成形プロセスでは、従来の製造方法では実現が難しい複雑な形状や幾何学形状が得られます。
- 材料の選択: 大量射出成形では、航空宇宙用途に最適な複合材料を含む幅広い材料を加工できます。
- 廃棄物の削減: 射出成形プロセスの高度な自動化と精度により、材料の無駄やスクラップが減り、大幅なコスト削減と環境上の利点が得られます。
航空宇宙産業における大量射出成形の用途:
大量射出成形は、航空宇宙産業で次のようなさまざまなコンポーネントの製造に広く使用されています。
- エアダクトと換気システム
- 航空機の内装および外装部品
- ブラケット、クリップ、ハウジングなどの構造要素
- 電気および配線部品
- シールとガスケット
大量射出成形における一般的な欠陥
ただし、他の製造プロセスと同様に、射出成形でも最終製品の品質に影響を及ぼす可能性のある欠陥が発生する場合があります。 このブログ投稿では、大量射出成形における一般的な欠陥とその防止方法について説明します。
- ヒケ: ヒケとは、成形品の表面に発生する可能性のあるくぼみです。 これらはプラスチック材料が冷える際の収縮によって発生し、その結果材料が不均一に分布します。 ヒケを防ぐには、部品の設計を変更し、部品全体にわたって均一な肉厚を確保する必要があります。
- ゆがみ:反りとは、プラスチック材料の不均一な冷却による成形部品の変形です。 部品がねじれたり曲がったりして、要求仕様を満たさなくなります。 反りは、金型温度を一定に保ち、冷却中に部品にかかる応力を最小限に抑える設計機能を組み込むことで防止できます。
- フラッシュ: バリは、金型の接合部からはみ出す余分な材料であり、金型が正しく位置合わせされていない場合やクランプされていない場合に発生する可能性があります。 バリは、金型が適切に位置合わせされていること、および射出中に金型を閉じた状態に保持するのに十分な型締力を確保することによって防止できます。
- ショートショット: ショート ショットは、プラスチック材料が金型キャビティ全体を満たさない場合に発生し、その結果、部品が不完全になります。 これは、不十分な射出圧力、低い樹脂温度、またはゲートのブロックが原因である可能性があります。 ショート ショットは、射出パラメータを最適化し、ゲートが適切に設計および配置されていることを確認することで防止できます。
- ウェルド ライン: ウェルド ラインは、XNUMX つ以上のフロー フロントが合流して固化するときに発生し、その結果、成形品に目に見える線や継ぎ目が生じます。 ウェルド ラインは、金型の設計と射出パラメータを最適化し、プラスチック材料がキャビティ内を均一かつスムーズに流れるようにすることで防止できます。
大量射出成形のトラブルシューティングのヒント
大量射出成形は複雑なプロセスであり、最終製品が最高品質であることを保証するために細部への注意と注意深く監視する必要があります。 射出成形プロセス中に多くの一般的な問題が発生する可能性があり、最終製品の欠陥につながる可能性があります。 この投稿では、大量射出成形に関する最も一般的なトラブルシューティングのヒントをいくつか説明します。
- 射出成形機の設定を確認します。 大量射出成形のトラブルシューティングを行うときに最初に確認することの XNUMX つは、射出成形機の設定です。 使用する特定の材料に対して、温度、圧力、サイクル時間がすべて正しく設定されていることを確認してください。
- マテリアル フローの問題を確認します。 材料の流れの問題も、大量射出成形に共通する問題です。 機械の不適切な設定や射出成形機の詰まりなど、いくつかの要因が原因で発生する可能性があります。 材料がデバイス内をスムーズに流れ、射出成形機内に詰まりがないことを確認してください。
- 反りや収縮をチェックします。 反りや収縮は、大量の射出成形時によく発生する問題です。 これらの問題は、材料の不均一な冷却によって引き起こされることが多く、最終製品の反りや収縮につながる可能性があります。 使用する特定の材料に対して冷却時間が正しく設定されており、システムが適切に機能していることを確認してください。
- エア トラップを確認します。 エアートラップは、大量の射出成形時に発生するもう XNUMX つの一般的な問題です。 これは、金型キャビティ内に空気が閉じ込められると発生し、最終製品にボイドや気泡が発生する可能性があります。 エアトラップの発生を防ぐために、金型の通気が適切に行われていることを確認してください。
- プロセスを監視します。 最後に、問題を確実に発見して迅速に対処するには、射出成形プロセスを注意深く監視することが重要です。 これは、機械の設定、材料の流れ、冷却プロセスを監視することで実行できます。 プロセスを注意深く監視することで、最終製品の欠陥につながる前に問題を特定し、対処することができます。
射出成形機のメンテナンス要件
射出成形機は製造業に欠かせない設備です。 プラスチック部品から金属部品まで、さまざまな製品の製造に使用されています。 ただし、他の機械と同様に、射出成形機も最適なパフォーマンスを確保し、高価な故障を防ぐために定期的なメンテナンスが必要です。 この投稿では、射出成形機のメンテナンス要件のいくつかを検討します。
- 潤滑: 適切な潤滑は、射出成形機のメンテナンスにおいて最も重要な要素の XNUMX つです。 射出ユニットやクランプユニットなどの機械の可動部品は、摩擦や摩耗を防ぐために定期的に潤滑する必要があります。 正しい種類の潤滑剤を使用し、潤滑間隔についてメーカーの推奨事項に従うことが重要です。
- クリーニング: 射出成形機のメンテナンスに欠かせないもう XNUMX つの側面は、定期的な清掃です。 機械は定期的に掃除して、コンポーネントに蓄積する可能性のあるほこり、破片、プラスチックの残留物を取り除く必要があります。 これにより、性能上の問題を引き起こしたり、エンジンに損傷を与えたりする可能性がある、機械のノズルやフィルターの詰まりを防ぐことができます。
- 検査: 機械が良好な状態であることを確認するためには、定期的な検査も必要です。 評価には、亀裂や破損した部品などの摩耗の兆候がないかどうかを確認することが含まれます。 センサーやスイッチなどの電気コンポーネントも定期的にチェックして、正しく機能していることを確認する必要があります。
- キャリブレーション: 射出成形機は、正しいパラメータ内で動作することを確認するための校正も必要です。 これには、マシンの温度、圧力、速度設定をチェックして、それらがメーカーの仕様内であることを確認することが含まれます。 デバイスが最適なレベルで動作していることを確認するために、定期的に校正を実行する必要があります。
- 摩耗した部品の交換: 最後に、摩耗または損傷した部品をできるだけ早く交換することが重要です。 これは、機械へのさらなる損傷を防ぎ、高価な故障のリスクを軽減するのに役立ちます。 交換部品は元の部品と同じ品質であり、資格のある技術者によって取り付けられる必要があります。
持続可能性と大量射出成形
近年、製造業において持続可能性がますます重要な関心事となっています。 産業プロセスが環境に与える影響に対する世界の意識が高まるにつれ、企業は生産性と収益性を維持しながら環境負荷を削減する方法を模索しています。 大量射出成形は、持続可能性が大きな影響を与える可能性がある分野の XNUMX つです。
持続可能性を大量射出成形に組み込む方法はいくつかあります。
- 材料選択:射出成形の持続可能性を達成するには、適切な材料を選択することが不可欠です。 多くのオプションには、バイオプラスチック、再生プラスチック、バイオベースの材料が含まれます。 環境に優しく、二酸化炭素排出量の少ない材料を選択することで、メーカーは環境への影響を大幅に削減できます。
- エネルギー効率: 大量の射出成形の操作には多大なエネルギーが必要です。 メーカーは、エネルギー効率の高いプロセスと装置を導入することで、エネルギー消費を削減し、二酸化炭素排出量を削減できます。 これは、エネルギー効率の高い機械を使用し、生産プロセスを最適化し、再生可能エネルギー源に投資することで実現できます。
- 廃棄物の削減: 射出成形では、大量の廃棄物、特に余分なプラスチックが発生する可能性があります。 廃棄物削減戦略を導入することで、製造業者は発生する廃棄物の量を最小限に抑え、持続可能性を向上させることができます。 これは、材料のリサイクル、再利用、生産プロセスの最適化によって廃棄物を削減することで実現できます。
- ライフサイクル分析: ライフサイクル分析を実施すると、メーカーは自社製品がライフサイクル全体を通じて環境に与える影響を理解することができます。 この分析は、持続可能性を改善できる領域を特定し、より環境に優しい製品を作成するための意思決定に役立ちます。
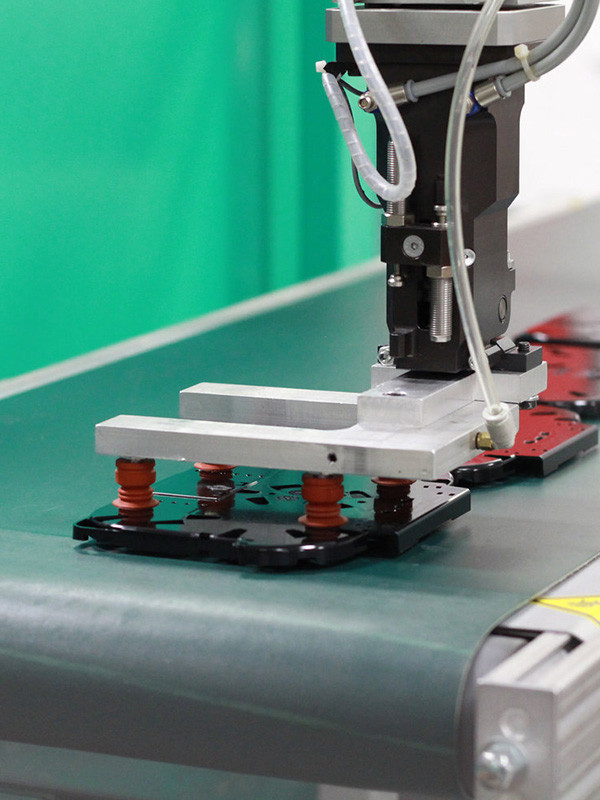
主なポイント:
- 射出成形の持続可能性を達成するには、材料の選択が重要な役割を果たします。
- エネルギー効率の高いプロセスと装置により、エネルギー消費が削減され、炭素排出量が削減されます。
- 材料のリサイクルや再利用などの廃棄物削減戦略により、発生する廃棄物の量を最小限に抑えることができます。
- ライフサイクル分析は、持続可能性を改善できる領域を特定するのに役立ちます。
- 大量射出成形に持続可能性を組み込むことは、コストを削減し、環境に配慮した消費者にアピールすることでメーカーに利益をもたらします。
- 大量射出成形の未来
大量射出成形は、何十年もの間、多くの業界にとって重要な製造プロセスであり、幅広いプラスチック製品の製造において重要な役割を果たし続けています。 技術が進歩し、消費者の需要がより持続可能でカスタマイズ可能な製品へと移行するにつれ、大量射出成形の未来は明るいものとなっています。 この業界の終焉を形作るトレンドとイノベーションのいくつかを以下に示します。
- サステナビリティ: 環境に優しい製品に対する消費者の需要が高まるにつれ、大量射出成形においては持続可能性が重要になっています。 メーカーは、バイオプラスチックやバイオベースの材料などの新しい材料を探索し、製品の環境への影響を最小限に抑えるために廃棄物削減戦略を実施しています。
- カスタマイズ: 消費者は独自のニーズや好みを満たす製品を求めており、大量射出成形はこの需要を満たすのに最適です。 3D プリンティングなどのテクノロジーの進歩により、カスタマイズされた部品や製品を大量に生産することがより簡単かつコスト効率よくなりました。
- オートメーション: 製造業界では自動化がますます普及しており、大量射出成形も例外ではありません。 ロボットアームやコンピュータ支援設計などの自動化されたプロセスにより、生産効率が向上し、コストが削減されます。
- インダストリー 4.0: 第 4.0 次産業革命であるインダストリー XNUMX は、人工知能、モノのインターネット (IoT)、ビッグデータ分析などの先進テクノロジーを統合することにより、製造業を変革しています。 これらのテクノロジーにより、メーカーは生産プロセスを最適化し、製品の品質を向上させることが容易になります。
- 医療業界:大量射出成形は、その精度と一貫性により、医療機器や機器の製造に適しています。 医療製品の需要は成長すると予想されており、射出成形業界にとって重要な分野となっています。
- 電気自動車:電気自動車への移行は、大量射出成形業界に新たなチャンスをもたらします。 バッテリーハウジングや電気コネクタなどのプラスチック部品は電気自動車に不可欠であり、電気自動車の普及が進むにつれてこれらの部品の需要は増加すると予想されます。
結論:
大量のプラスチック部品を生産するには、大量の射出成形が不可欠です。 大量射出成形の長所、短所、材料、機械、方法、設計上の考慮事項、品質管理措置、およびアプリケーションを理解することで、企業は生産プロセスを最適化し、コストを削減し、製品の品質を向上させることができます。 医療、自動車、消費財、航空宇宙産業のいずれにおいても、大量射出成形は一貫した高品質の部品をコスト効率の高い価格で提供することでビジネスに利益をもたらします。