射出成形金型の製造
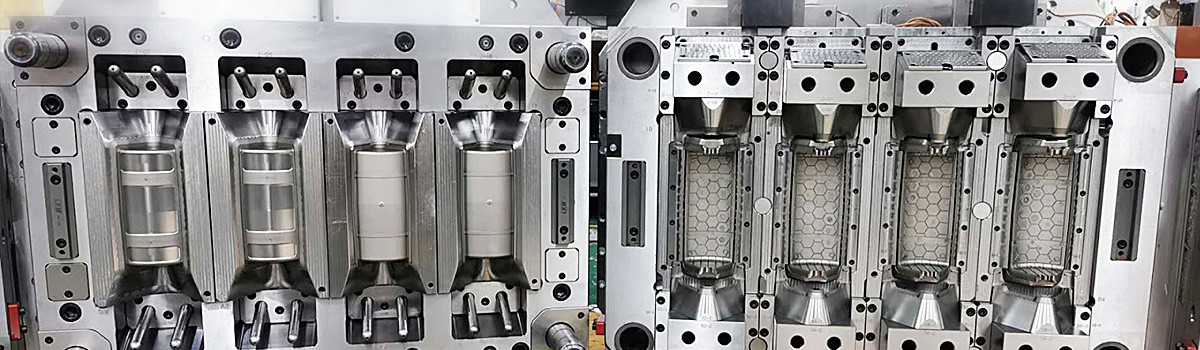
プラスチックは、さまざまな業界の製品に一般的に使用される材料です。 おもちゃ、自動車部品、医療機器、工具などはすべてプラスチックで作られています。 私たちが日常生活で目にするプラスチック製品の多くは、プラスチック射出成形と呼ばれる製造プロセスにより、溶融した樹脂を所定のデザインに操作することによって製造されます。 この非常に効率的なプロセスにより、さまざまなサイズや形状の部品を作成でき、同じ金型を使用して同じ部品を何度も複製できます。 このプロセスの中心となるのは、ツールとも呼ばれる金型です。 高品質の金型製造プロセスは、コスト効率の高いパフォーマンスを維持しながら高品質の部品を製造するために不可欠です。 高品質の金型製造に投資すると、部品の品質が向上し、プロジェクト全体のコストが下がります。
射出成形プロセスの手順
射出成形は、プラスチック製品の製造に使用される最も一般的な製造プロセスの XNUMX つです。 これは、同じ部品を何千回も再現できる要求の高いプロセスです。 このプロセスは、部品のデジタル コピーを含むコンピューター支援設計 (CAD) ファイルから始まります。 CAD ファイルは、金型の製造プロセスを支援する一連の指示として使用されます。 型またはツールは通常、XNUMX つの金属片から作られます。 部品の形状に合わせたキャビティが金型の各側面に切り込まれます。 この型は通常、アルミニウム、鋼、または合金で作られています。
金型の製作が完了したら、次のステップは適切なプラスチック材料を選択することです。 材料の選択は、最終部品がどのように使用されるかによって決まります。 プラスチック材料には、考慮すべきさまざまな特性があります。 これには、あらゆる外観と感触だけでなく、耐薬品性、耐熱性、耐摩耗性も含まれます。 射出成形に利用できるプラスチック材料の詳細については、DJmolding の専門家にお問い合わせください。
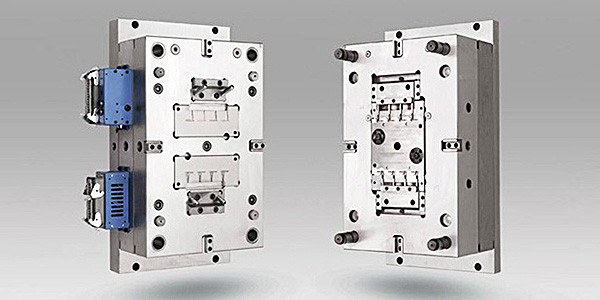
選択された材料は、射出成形機のホッパーに供給されるプラスチック ペレットとして始まります。 ペレットは加熱されたチャンバーを通過し、そこで溶融、圧縮されて金型キャビティに射出されます。 部品が冷えると、金型の XNUMX つの半分が開いて部品が取り出されます。 その後、マシンがリセットされてプロセスが再開されます。
金型の製作に使用される材料は何ですか?
金型の製造は鋼、アルミニウム、または合金で行われます。 DJmolding は金型製造に高品質の鋼材を使用しています。 鋼製金型の製作は、アルミニウムや合金を使用するよりも若干高価になります。 通常、コストが高くても、鋼製金型の寿命がはるかに長くなることで相殺されます。 アルミニウム型は製造コストが安いものの、鋼鉄ほど寿命が短く、頻繁に交換する必要があります。 スチール金型は通常、XNUMX 万サイクルをはるかに超えて耐久します。 アルミニウムの金型は、より頻繁に交換する必要があります。 スチール製の金型の製造では、アルミニウムでは実現できない非常に複雑なデザインを実現できます。 鋼製の型を溶接で修理・改造することも可能です。 アルミニウム金型は、金型が損傷した場合や変更に対応するために、最初から機械加工する必要があります。 高品質の鋼製金型は、数千回、数十万回、場合によっては最大 XNUMX 万回のサイクルで使用できます。
射出成形金型部品
ほとんどの射出成形金型は、A 面と B 面、またはキャビティとコアの XNUMX つの部分で構成されています。 通常、キャビティ側が最良の側ですが、残りの半分であるコアには、完成品を金型から押し出すエジェクター ピンによる視覚的な欠陥がいくつかあります。 射出成形金型には、サポート プレート、エジェクター ボックス、エジェクター バー、エジェクター ピン、エジェクター プレート、スプルー ブッシュ、および位置決めリングも含まれます。
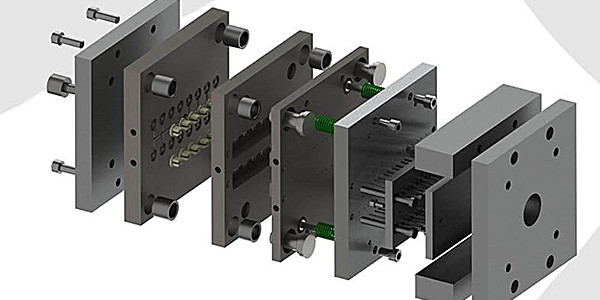
射出成形は、多くの可動部品を伴う製造プロセスです。 以下は、金型の製造と射出成形に必要な部品の多くを説明する用語のリストです。 工具はフレーム内の複数の鋼板で構成されています。 金型フレームは射出成形機に配置され、クランプで所定の位置に保持されます。 射出成形金型の一部を横から見ると、さまざまな層を重ねたサンドイッチのように見えます。 用語の完全なリストについては、射出成形用語集をご覧ください。
モールド フレームまたはモールド ベース: キャビティ、コア、ランナー システム、冷却システム、突き出しシステムなどの金型コンポーネントをまとめて保持する一連の鋼板。
プレート: 金型の半分。 このプレートには可動部品は含まれていません。 キャビティまたはコアのいずれかを含めることができます。
Bプレート: 金型の残り半分。 プレートには可動部品または可動部品が完成部品 (通常はエジェクター ピン) と相互作用できるようにするためのスペースが含まれています。
サポートプレート: 成形プロセス中に安定性を提供する金型フレーム内の鋼板。
エジェクターボックス: 完成した部品を金型から押し出すために使用されるエジェクター システムが含まれています。
エジェクタープレート: エジェクターバーを内蔵する鋼板。 エジェクタプレートが移動して成形後の完成品を突き出します。
エジェクターバー: エジェクタープレートの一部。 エジェクタピンはエジェクタバーに接続されています。
エジェクターピン: 完成品に接触して金型から押し出すスチールピン。 一部の射出成形品にはエジェクター ピンの跡が見られますが、通常は部品の背面に丸い跡が見られます。
スプルーブッシュ: 溶融樹脂がキャビティに入る金型と射出成形機の間の接続部分。
スプルー: 溶融樹脂が金型キャビティに入る金型フレーム上のスポット。
ロケーターリング: 射出成形機のノズルがスプルー ブッシュと適切に接触することを保証する金属リング。
キャビティまたはダイキャビティ: 金型内の凹面の印象。通常、成形品の外面を形成します。 金型は、そのような凹みの数に応じて、単一キャビティまたは複数キャビティとして指定されます。
コア: 金型内の凸状の痕跡。通常、成形品の内面を形成します。 金型の盛り上がった部分です。 それはキャビティの逆です。 溶融樹脂は常にキャビティ内に押し込まれ、空間を満たします。 盛り上がったコアの周囲に溶融樹脂が形成されます。
ランナーまたはランナー システム: 溶融樹脂がスプルーからキャビティへ、またはキャビティからキャビティへ流れることを可能にする金型内のチャネル。
ゲート: 溶融した樹脂が金型キャビティに入るランナーの端。 さまざまな用途に応じてさまざまなゲート設計があります。 一般的に使用されるゲート タイプには、ピン、スポーク、ファン、エッジ、ディスク、ファン、トンネル、バナナまたはカシュー、チゼルなどがあります。 ゲートの設計と配置は、金型の製造プロセスを開始する前に重要な考慮事項です。
冷却システム: 金型の外殻にある一連のチャネル。 これらのチャネルは流体を循環させて冷却プロセスを支援します。 部品が不適切に冷却されると、さまざまな表面または構造上の欠陥が発生する可能性があります。 通常、冷却プロセスは射出成形サイクルの大部分を占めます。 冷却時間を短縮すると、金型の効率が大幅に向上し、コストが削減されます。 Fathom は、金型効率を最大 60% 向上させるコンフォーマル冷却を多くの射出成形用途に提供しています。
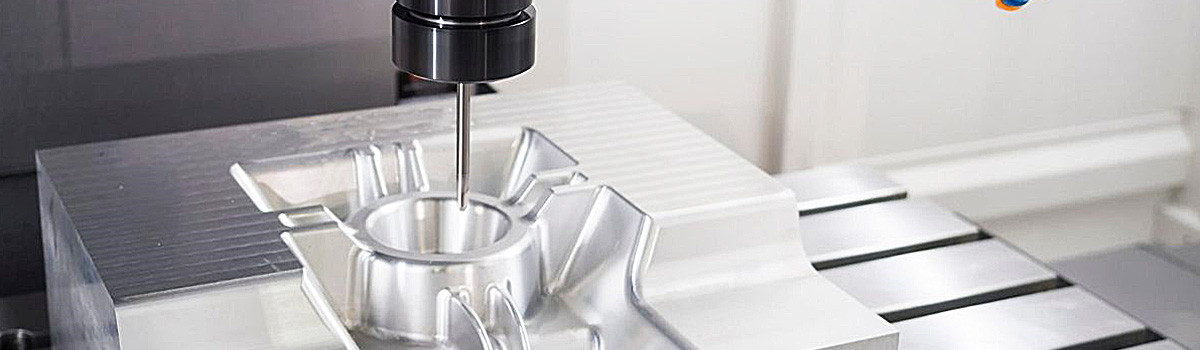
さまざまな成形プロセスに対応した DJmolding 金型の製造
プラスチック射出成形プロセスは、さまざまで複雑なニーズに合わせて調整できます。 単純なプラスチック部品を大量に製造するのに理想的ですが、複雑な形状やアセンブリを持つ非常に複雑な部品の作成にも使用できます。
マルチキャビティまたはファミリーモールド – この金型には、単一の金型フレーム内に複数のキャビティがあり、各射出サイクルで同じ部品または関連部品がいくつか生成されます。 これは、生産量を増やし、XNUMX 個あたりの価格を下げるための理想的な方法です。
オーバーモールディング – この射出成形法は、XNUMX つの異なる種類のプラスチックで作られた部品を作成するために使用されます。 この好例としては、硬い外殻と柔らかいゴム引きグリップを備えたポータブル ドリル本体またはゲーム コントローラーが挙げられます。 以前に成形された部品を特別に作られた金型に再度挿入します。 金型が閉じられ、元の部品の上に別のプラスチックの XNUMX 番目の層が追加されます。 これは、XNUMX つの異なるテクスチャーが必要な場合に理想的なプロセスです。
インサート成形 – 金属、セラミック、またはプラスチック片を最終部品に組み込むことができる射出成形プロセス。 金属またはセラミックの部品を金型に配置し、溶かしたプラスチックを金型に注入して、XNUMX つの異なる材料からなる継ぎ目のない部品を作成します。 インサート成形は、重量を軽減し、金属などの高価な材料を削減する革新的な方法であるため、自動車用途に最適です。 部品全体を金属で作るのではなく、接続部品のみを金属にし、残りの部品をプラスチックで作る必要があります。
共射出成形 – XNUMX つの異なるポリマーがキャビティに順次または同時に注入されます。 このプロセスを使用すると、ある種類のプラスチックの外皮と別の種類のプラスチックのコアを備えた部品を作成できます。
薄肉成形 – サイクルタイムの短縮と生産性の向上に重点を置き、薄く、軽く、安価なプラスチック部品を製造する射出成形の一種。
ゴム射出成形 – プラスチック射出成形と同様のプロセスを使用して、ゴムを金型に射出します。 ゴム部品の射出成形を成功させるには、より多くの圧力が必要です。
セラミック注入 – セラミック材料を利用した射出成形プロセス。 セラミックは、自然に硬く、化学的に不活性な材料であり、さまざまな産業で使用されています。 セラミックの注入にはいくつかの追加の手順が必要です。 特性の耐久性を確保するために、新しく成形された部品の焼結または硬化が含まれます。
低圧プラスチック射出成形 – より低い圧力で製造されるプラスチック部品。 これは、電子機器などの繊細な部品のカプセル化が必要な作業に特に役立ちます。
プラスチック射出成形の詳細については、DJmolding にお問い合わせください。 当社の専門家チームがプラスチック射出成形プロジェクトをお手伝いします。