プラスチック射出成形
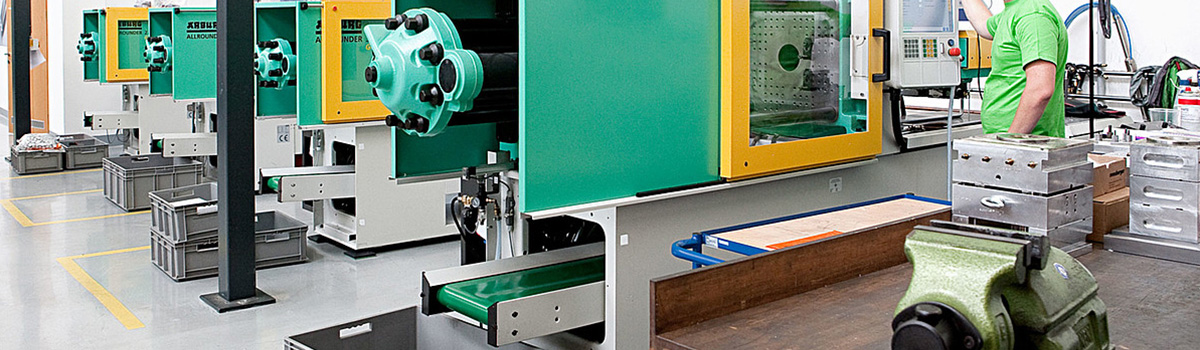
プラスチック射出成形は、プラスチック ペレットを溶かし、金型キャビティに射出して三次元物体を作成する製造プロセスです。 このプロセスは、小さな精密部品から重要な自動車部品に至るまで、多くの製品から始まります。 プラスチック射出成形には、高い生産速度、設計の柔軟性、費用対効果など、他の製造プロセスに比べて多くの利点があります。 このガイドでは、プラスチック射出成形について詳しく説明し、そのさまざまな用途、利点、制限事項を探ります。
プラスチック射出成形の歴史
プラスチック射出成形は、溶融プラスチックを金型キャビティに射出して特定の形状を作成する製造プロセスです。 プラスチック射出成形の歴史は、プラスチックの一種であるセルロイドが初めて発明された 1800 年代後半にまで遡ります。 しかし、プラスチック射出成形が製造技術として広く使用されるようになったのは 1940 年代になってからです。
第二次世界大戦中、大量生産されたプラスチック製品の需要が増加し、製造業者はそれらをより効率的に生産する新しい方法を模索し始めました。 1946 年、アメリカの発明家ジェームス ワトソン ヘンドリーは、プラスチック射出成形業界に革命をもたらした最初のスクリュー射出成形機を開発しました。 この機械により、より正確で一貫した射出プロセス制御が可能になり、大量のプラスチック部品をより利用しやすく効率的に生産できるようになりました。
1950 年代から 1960 年代にかけて、プラスチック技術の進歩により、プラスチック射出成形プロセスが改善され続けました。 ポリスチレンやポリエチレンなどの新素材の導入により、より複雑で耐久性のあるプラスチック部品が作成されました。 さらに、油圧システムの使用を含む成形機技術の向上により、射出成形プロセスはさらに効率的でコスト効率が高くなりました。
現在、プラスチック射出成形は、玩具や消費財から自動車部品や医療機器に至るまで、幅広いプラスチック製品の製造に使用される高度に自動化されたプロセスです。 新しい材料と技術の開発により、プラスチック射出成形プロセスは進化と改善を続けており、長年にわたって重要な製造技術であり続けることが保証されています。
プラスチック射出成形の基礎
プラスチック射出成形は、プラスチック材料から部品や製品を作成する製造プロセスです。 このプロセスでは、溶融したプラスチックを金型に注入し、冷却して固化して目的の形状を形成します。
プラスチック射出成形プロセスに含まれる基本的な手順は次のとおりです。
- 金型設計: プロセスの最初のステップは、目的の部品を作成するために使用される金型を設計することです。 型は通常金属で作られており、プラスチックが冷えて固まるときの収縮を考慮して準備する必要があります。
- 材料の準備: 射出成形プロセスで使用されるプラスチック材料はペレットまたは顆粒の形で提供されます。これらを溶かして金型に射出する準備をする必要があります。 これは通常、ホッパー内で行われ、そこでプラスチックが特定の温度に加熱され、液体状態に溶解されます。
- 射出:プラスチックが溶けたら、専用の射出成形機を使用して金型に射出されます。 機械は溶融プラスチックに圧力を加えて金型キャビティに押し込み、そこで金型の形状をとります。
- 冷却と固化: プラスチックは金型に射出された後、冷却して固化します。 パーツのサイズと複雑さに応じて、これには数秒から数分かかる場合があります。
- 取り出し: プラスチックが冷えて固まると、金型が開かれ、部品が取り出されます。 この位置では、余分なプラスチックや粗いエッジを除去するために、トリミングやサンディングなどの追加の仕上げ作業が必要になる場合があります。
プラスチック射出成形は正確で再現可能なプロセスであるため、安定した品質の部品や製品を大量生産するのに最適です。 また、さまざまなサイズ、形状、複雑さの部品や製品を作成できるため、非常に多用途です。 プラスチック射出成形の最も一般的な用途には、玩具、消費財、自動車部品、医療機器の製造などがあります。
プラスチック射出成形プロセス: ステップバイステップ
プラスチック射出成形は、いくつかのステップを含む複雑なプロセスです。 ここでは、プラスチック射出成形プロセスの段階的なガイドを示します。
- 金型の設計: 最初のステップは、部品の作成に使用する金型を設計することです。 型は通常、スチールまたはアルミニウムで作られており、プラスチック材料が冷えるときの収縮に対応できるように準備する必要があります。
- 金型の作成: 金型の設計が完了すると、コンピュータ支援設計 (CAD) ソフトウェアとコンピュータ支援製造 (CAM) 機械を使用して製造されます。 最終製品の精度と仕上げを確保するには、金型を慎重に機械加工し、研磨する必要があります。
- 材料の選択: 射出成形プロセスに使用されるプラスチック樹脂材料は、強度、柔軟性、色、質感などの部品の要件に基づいて選択する必要があります。
- 材料の準備: 選択したプラスチック材料を特定の温度に加熱し、溶かして液体にします。 次に、材料は成形機のホッパーに注入されます。
- 射出成形: 特殊な射出成形機を使用して、溶融したプラスチック材料を金型キャビティに注入します。 機械はプラスチック材料に圧力を加えて金型キャビティに押し込み、そこで金型の形状を形成します。
- 冷却: 金型キャビティにプラスチックが充填されると、冷却して固化します。 冷却時間は、プラスチック材料の特性、部品のサイズと厚さ、金型の温度によって決まります。
- 取り出し: プラスチックが固まった後、金型が開き、エジェクター ピンを使用して部品が金型から取り出されます。
- 仕上げ: 取り出された部品には、余分なプラスチックや粗いエッジを除去するために、トリミング、サンディング、塗装などの追加の仕上げ作業が必要になる場合があります。
- 品質管理: 完成した部品は、要求された仕様と品質基準を満たすために徹底的な検査を受けます。
プラスチック射出成形では、さまざまなサイズ、形状、複雑さのさまざまな部品や製品を製造できます。 このプロセスは、自動車、医療、消費財、エレクトロニクスなどのいくつかの業界で広く使用されています。
射出成形に使用されるプラスチックの種類
射出成形では多くの種類のプラスチックを使用できます。 プラスチック材料の選択は、強度、柔軟性、耐久性、外観など、製造される製品または部品の特定の要件によって異なります。 射出成形で使用される最も一般的な種類のプラスチックのいくつかを以下に示します。
- ポリエチレン (PE): PE は、強度と柔軟性で知られる広く使用されているプラスチック素材です。 包装材、玩具、医療機器など、さまざまな製品の製造に使用されています。
- ポリプロピレン (PP): PP は、自動車業界でダッシュボードやドアパネルなどの内装部品に一般的に使用されている軽量で耐久性のあるプラスチック素材です。 容器やボトルなどの包装資材も製造しています。
- ポリカーボネート (PC): PC は、コンピュータや電話ケースなどの電子部品の製造に一般的に使用される固体で透明なプラスチック材料です。 自動車業界のヘッドランプレンズやダッシュボードコンポーネントにも使用されています。
- アクリロニトリル ブタジエン スチレン (ABS): ABS は、強度、耐久性、耐熱性で知られる多用途のプラスチック素材です。 一般的に、ダッシュボード、フェンダー フレア、玩具、消費財などの自動車部品の製造に使用されます。
- ポリアミド (PA): ナイロンとしても知られる PA は、エンジン カバーや吸気システムなどの自動車部品の製造に一般的に使用される、強力で軽量のプラスチック材料です。 スキーブーツやテニスラケットなどのスポーツ用品も製造しています。
- ポリスチレン (PS): PS は、カップ、トレイ、食品容器などの包装材料の製造に一般的に使用される軽量で硬いプラスチック材料です。 玩具や電子部品などの消費財も製造しています。
- ポリエチレンテレフタレート (PET): PET は、ボトルや容器などの包装材料の製造に一般的に使用される丈夫で透明なプラスチック素材です。 繊維産業でも繊維や生地を製造するために使用されます。
これらは、射出成形で使用される最も一般的な種類のプラスチックのほんの一部です。 他にも多くの種類のプラスチック材料が利用可能であり、それぞれが独自の特性と特徴を持っています。 プラスチック材料の選択は、製造される部品または製品の特定の要件によって異なります。
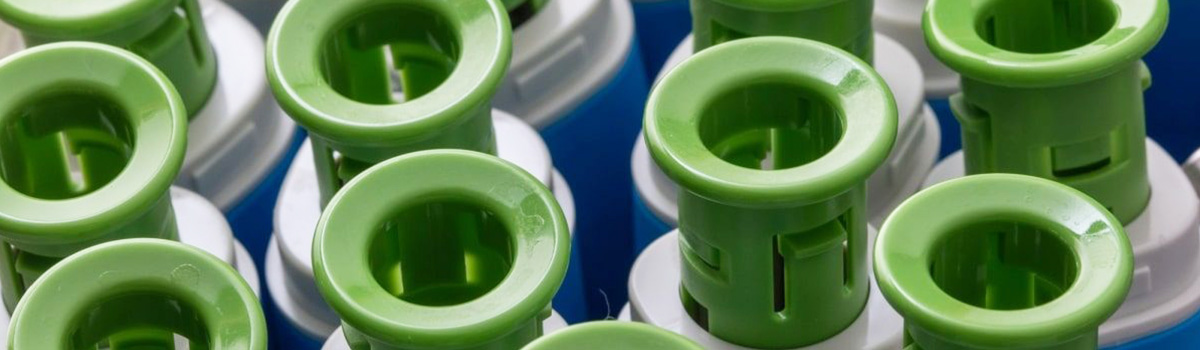
射出成形機の種類
射出成形機にはさまざまなタイプとサイズがあり、それぞれが特定の製造要件を満たすように設計されています。 以下に、最も一般的なタイプの射出成形機をいくつか示します。
- 油圧射出成形機: この機械は、油圧を使用して圧力を生成し、プラスチックを金型に射出します。 油圧機械は通常、高いクランプ力を必要とする重要な部品に使用されます。
- 電動射出成形機: 電動機は、電動モーターを使用して射出ユニットとクランプ機構に電力を供給します。 高い精度とエネルギー効率で知られており、小型で複雑な部品の製造で有名です。
- ハイブリッド射出成形機: ハイブリッド機械は、油圧装置と電気装置の利点を組み合わせ、油圧と電力の両方を使用して必要な圧力と動力を生成します。 ハイブリッド マシンは、速度、精度、エネルギー効率のバランスが優れています。
- 縦型射出成形機: 縦型機械は、インサート成形またはオーバーモールドが必要な部品を製造します。 金型に簡単にアクセスできる垂直クランプ ユニットを備えているため、小型または複雑な部品の作成に最適です。
- ツーショット射出成形機: ツーショット機は、異なる材質または色の部品を製造します。 この装置には XNUMX つの射出ユニットがあり、それぞれが金型に異物を射出することができます。 このタイプの機械は、ハンドルやノブなどの自動車部品の製造によく使用されます。
- マルチショット射出成形機: マルチショット機は、XNUMX つ以上の材料または色を使用して部品を製造します。 この装置には複数の射出ユニットがあり、それぞれが異なる材料を金型に射出することができます。 このタイプの機械は、歯ブラシやカミソリなどの消費財の製造によく使用されます。
- 全電動射出成形機: 全電動機は、電動モーターを使用して射出ユニット、クランプ機構、金型に電力を供給します。 高い精度、スピード、エネルギー効率で知られており、小型で高精度の部品を製造することで有名です。
これらは、最も一般的なタイプの射出成形機のほんの一部です。 各機械には独自の機能と利点があるため、特定の製造要件に適したデバイスを選択することが不可欠です。
射出成形機の部品
射出成形機には、原材料からプラスチック部品を作成するいくつかの部分があります。 射出成形機の重要なコンポーネントは次のとおりです。
ホッパー: リザーバーには、射出成形機に供給される前のプラスチック原料が保持されます。 材料は通常、ペレットまたは粉末の形状です。
バレル: バレルは、プラスチック材料を溶かして混合するスクリューを収容する射出成形機の長い円筒形の部分です。
スクリュー: スクリューはバレル内の回転装置で、プラスチック材料を前方に押し出し、摩擦と熱によってプラスチック材料を溶かします。
射出ユニット: 射出ユニットにはホッパー、バレル、スクリューが含まれており、プラスチックを溶融して金型に射出する役割を果たします。
クランプ ユニット: クランプ ユニットは、金型をしっかりと保持し、射出成形プロセス中に必要な圧力を加える役割を果たします。
金型: 金型は、プラスチック部品の形状とサイズを作成するツールです。 型は通常スチール製で、互いに嵌合する XNUMX つの半分で構成されます。
ノズル: ノズルは、射出成形機を金型に接続する射出ユニットの一部です。 溶けたプラスチック材料がノズルから金型に射出されます。
冷却システム: 冷却システムは、金型に射出されたプラスチック部品を冷却する役割を果たします。 これにより、ピースが確実に固化し、損傷することなく型から取り外すことができます。
コントロール パネル: コントロール パネルは、オペレータが温度、圧力、サイクル タイムなどの射出成形機の設定を監視および調整できるようにするインターフェイスです。
これらの各部品は射出成形プロセスにおいて重要な役割を果たしており、高品質の部品を効率的に生産するには、各部品を保守および最適化することが不可欠です。
射出成形ツール: 設計と製造
射出成形ツールとは、プラスチック部品を製造するために射出成形機で使用される金型の設計および製造を指します。 金型の品質と効率は、射出成形プロセスの品質と生産性に直接影響します。 射出成形ツールの設計と製造における重要な手順は次のとおりです。
製品設計: 射出成形ツールの最初のステップは、製造される製品を設計することです。 製品設計には、部品のサイズ、形状、材質だけでなく、特定の機能や要件の決定も含まれます。
金型設計: 製品設計が完了すると、金型設計プロセスが開始されます。 金型設計者は、最適な金型の種類、必要なキャビティの数、金型のサイズと形状を決定します。
金型の構造: 金型は、鋼やアルミニウムなどの高品質の材料を使用して、金型設計に基づいて構築されます。 型は通常、XNUMX つの半体で作られ、それぞれに XNUMX つ以上のキャビティが含まれます。
金型の組み立て: 金型が構築されると、組み立てられ、精度と機能がテストされます。 金型は、射出成形プロセスの圧力と熱に耐える必要があります。
金型のテストと検証: 金型が組み立てられた後、製品仕様を満たす高品質の部品が製造されていることを確認するためにテストと検証が行われます。 性能を向上させるために、金型を調整または変更する必要がある場合があります。
金型のメンテナンス: 金型の寿命と性能を確保するには、金型の定期的なメンテナンスと修理が重要です。 これには、磨耗または損傷した部品の洗浄、注油、交換が含まれます。
射出成形ツールには、高品質の部品を一貫して効率的に製造するための精度と専門知識が必要です。 完全な設計および製造プロセスに従うことで、メーカーは製品固有の要件を満たす金型を作成し、射出成形プロセスを最適化できます。
射出成形金型の種類
射出成形は、部品を大量に生産するために広く使用されている製造プロセスです。 これには、溶融プラスチックを金型キャビティに注入し、冷却して固化させて目的の形状にすることが含まれます。 射出成形ツールは、射出成形で使用される金型を作成するプロセスです。 射出成形ツールにはいくつかの種類があり、それぞれに独自の長所と短所があります。
- XNUMX プレート金型 XNUMX プレート金型は、最も単純なタイプの射出成形ツールです。 これらは、金型キャビティを形成するために互いにクランプされた XNUMX 枚のプレートで構成されています。 溶融プラスチックはゲートを通して穴に注入され、冷却されて固化します。 パーツが作成されると、XNUMX つのプレートが分離され、その量が排出されます。 XNUMX プレート金型は、単純な形状の小型から中型の部品によく使用されます。
- XNUMX プレート金型 XNUMX プレート金型は XNUMX プレート金型に似ていますが、成形品をランナー システムから分離するストリッパー プレートと呼ばれる追加のプレートがあります。 ランナー システムは、溶融プラスチックを金型キャビティに供給するチャネル ネットワークです。 XNUMX プレート金型は、より重要な部品やより複雑な形状に使用されます。
- ホット ランナー金型 ホット ランナー金型では、溶融プラスチックはゲートではなく、一連の加熱されたチャネルを通じて金型キャビティに直接射出されます。 これにより、ランナー システムでの材料の無駄が削減され、プロセスがより効率的になります。 ホット ランナー金型は、複雑な部品の大量生産に使用されます。
- ファミリー金型 ファミリー金型は、単一の金型で複数の部品を製造します。 それらは、多数のドメインを同時に生成できるように配置されたさまざまな空洞を持っています。 ファミリー金型は、小規模から中規模の部品によく使用されます。
- インサート金型 インサート金型は、金属またはプラスチックのインサートを必要とする部品を製造します。 インサートは、溶融プラスチックを射出する前に金型キャビティに配置されます。 プラスチックが冷えて固まると、部品とインサートは永久的に接着されます。 強度、耐久性、美観が必要な箇所にはインサート金型が使用されます。
- オーバーモールディング オーバーモールディングは、部品を別の部品の上に成形するプロセスです。 ソフトなタッチやグリップ力の向上が必要なポジションによく使用されます。 オーバーモールドでは、最初に基板またはベース部品を設定し、次にその上に XNUMX 番目の材料を成形します。 第 XNUMX の材料は、異なる種類のプラスチック、ゴム状材料、または熱可塑性エラストマーとすることができます。
結論として、射出成形ツールの選択は、生産される部品の種類、必要な生産量、および部品設計に含まれる複雑さのレベルによって異なります。 プロセスの効率性とコスト効率を確保するには、適切なツールを選択することが不可欠です。
射出成形設計ガイドライン
射出成形は、プラスチック部品の製造に広く使用されている製造プロセスです。 射出成形用の部品を設計するには、プロセス、材料、細部を確実に製造できるようにするために従う必要がある設計ガイドラインをよく理解する必要があります。 以下に、留意すべき射出成形設計ガイドラインをいくつか示します。
肉厚: 部品の肉厚は、必要な強度と機能を維持しながら、均一で可能な限り薄くする必要があります。 これにより、冷却時間とサイクル時間が短縮され、反りやヒケのリスクが最小限に抑えられます。
リブとボス リブとボスを使用すると、部品の強度と剛性を高めることができます。 リブは公称肉厚の 60% 以下、ボスは公称肉厚の 1.5 倍でなければなりません。
抜き勾配: 部品の取り出しを容易にし、金型への損傷を防ぐために、すべての垂直面で少なくとも 1 ~ 2 度の抜き勾配を使用する必要があります。
フィレットと半径 亀裂や破損につながる可能性のある応力集中を防ぐために、鋭いコーナーやエッジは避けてください。 代わりに、フィレットと半径によって応力を分散し、部品の強度を向上させる必要があります。
ゲートとランナー ゲートとランナーの位置と設計は、良好な部品品質を実現するために重要です。 成形品の最も厚い部分では、入口はできるだけ小さくする必要があります。 ランナーは、圧力損失を最小限に抑え、流量を最大化するように設計する必要があります。
表面仕上げ 部品の表面仕上げは、アプリケーション要件に基づいて指定する必要があります。 目に見える部分にはより高い表面仕上げが必要になる場合がありますが、隠れた部分にはより低い表面仕上げが許容される場合があります。
材料の選択 部品に選択される材料は、射出成形に適しており、必要な機械的、熱的、化学的特性を満たしている必要があります。
射出成形の二次加工
射出成形は、さまざまなプラスチック部品の製造に使用される多用途の製造プロセスです。 一次成形プロセスに加えて、望ましい形状、仕上げ、または機能を実現するために、多くの位置で二次操作が必要です。 射出成形における日常的な二次作業をいくつか紹介します。
- トリミングとは、成形品を金型から取り出した後、成形品から余分な材料を除去することです。 これは通常、トリム プレスまたは CNC マシンを使用して行われます。 部品の最終的な形状とサイズを実現するには、多くの場合、トリミングが必要になります。
- 溶接では、熱、圧力、またはその両方の組み合わせを使用して、XNUMX つ以上のプラスチック部品を結合します。 これは、単一の金型では製造できない、より大きな、またはより複雑なフィーチャーを作成するためによく使用されます。
- 装飾とは、成形部品の表面に視覚的または機能的な特徴を追加するプロセスです。 これには、ペイント、印刷、ラベル付け、またはテクスチャやパターンの適用が含まれます。
- 組み立てとは、複数の部品を結合して完成品を作成するプロセスです。 これは、ファスナー、接着剤、またはその他の接合技術を使用して行うことができます。
- インサート成形 インサート成形とは、あらかじめ成形された金属またはプラスチックインサートの周囲にプラスチックを成形することです。 これは、高レベルの強度または耐久性を備えた部品を作成するためによく使用されます。
- オーバーモールディング オーバーモールディングは、予備成形された部品の上に XNUMX 番目の材料を成形するプロセスです。 これにより、ソフトタッチの表面を追加したり、グリップを向上させたり、ツートンカラーやマルチマテリアルの作品を作成したりできます。
- コーティングは部品の表面に薄い材料層を適用し、外観、耐久性、その他の特性を向上させます。 これには、クロム、ニッケル、粉体塗装などのコーティングが含まれる場合があります。
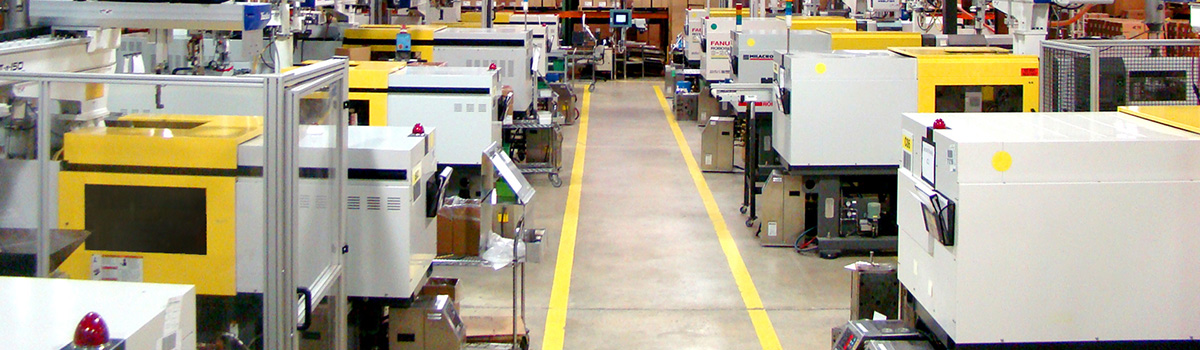
プラスチック射出成形の利点
プラスチック射出成形は、高精度、一貫性、高品質のプラスチック部品を製造するために広く使用されている製造プロセスです。 これには、溶融プラスチックを金型キャビティに注入し、冷却して固化させることが含まれます。 プラスチック射出成形の利点は次のとおりです。
- 高効率と生産性 プラスチック射出成形は、高効率かつ自動化されたプロセスであり、高い一貫性と品質を備えた大量の部品を生産できます。 高度な自動化技術により、生産サイクルタイムを数秒に短縮することができ、複雑で入り組んだ部品の大量生産が可能になります。
- 高精度と高精度 射出成形により、複雑で入り組んだ部品を製造する際の精度と精度が向上します。 コンピュータ制御の機械と高度なソフトウェアにより、高い再現性と精度を備えた厳しい公差が可能になります。
- 汎用性 射出成形は、さまざまなサイズ、形状、複雑さの幅広いプラスチック部品を製造できる汎用性の高いプロセスです。 このプロセスは、複雑なディテールを備えた小さな部品から、複雑な形状を備えた大量の部品まで、あらゆるものを作成するために使用できます。
- 材料の柔軟性 射出成形では、熱可塑性プラスチック、熱硬化性樹脂、エラストマーなどの幅広いプラスチック材料を使用できます。 これにより、さまざまな機械的、熱的、化学的特性を持つ部品の製造が可能になります。
- 低廃棄物の生産 射出成形は、生産中に発生する廃棄物が最小限に抑えられるため、廃棄物の少ない生産プロセスです。 余剰材料は簡単にリサイクルして製造時に再利用できるため、環境に優しい製造プロセスとなります。
- 人件費の削減 射出成形における高度な自動化により、労働集約的なプロセスの必要性が最小限に抑えられ、人件費が大幅に削減されます。 これにより、人的エラーのリスクも軽減され、最終製品の品質と一貫性が向上します。
- 製造後の作業の削減 射出成形では、高精度かつ一貫性のある部品が製造されるため、トリミング、穴あけ、フライス加工などの製造後の作業の必要性が軽減されます。 これにより、最終製品の製造時間とコストが削減されます。
- 一貫性と品質 射出成形では、高レベルの一貫性と品質を備えた部品が製造されます。 高度な技術とコンピューター制御の機械により、形状、サイズ、品質がすべて同一であることが保証されます。
- 設計の柔軟性 射出成形では、複雑な形状、アンダーカット、複雑な詳細を備えた部品を製造できるため、設計の柔軟性が高くなります。 これにより、デザイナーは他の製造プロセスでは作成できない独自の形状や機能を備えた作品を作成できるようになります。
- コスト効率の高い大量生産 射出成形は、プラスチック部品を製造するためのコスト効率の高いプロセスです。 初期の工具コストは高くなる可能性がありますが、生産量が増加するにつれて部品あたりのコストは下がります。 これにより、大量の部品を生産するのに理想的なプロセスとなります。
プラスチック射出成形には多くの利点があるため、プラスチック部品の製造によく選ばれています。 その高効率、精度、多用途性、材料の柔軟性、低廃棄物生産、削減された人件費、一貫性と品質により、さまざまな用途にとって理想的なプロセスとなります。 複雑で入り組んだ部品を高い設計柔軟性と大量生産の費用対効果で製造できるため、非常に人気のある製造プロセスとなっています。
プラスチック射出成形のデメリット
プラスチック射出成形は、溶融プラスチックを金型キャビティに射出して幅広いプラスチック部品や製品を製造する、広く使用されている製造プロセスです。 プラスチック射出成形には多くの利点がありますが、いくつかの欠点もあります。 プラスチック射出成形の主な欠点は次のとおりです。
- 高い金型コスト: プラスチック射出成形用の金型の設計と製造のコストは非常に高くなる可能性があります。 目的の部品を作成するには、金型を高品質の素材で作成し、精密に機械加工する必要があるためです。 さらに、金型の設計と製造のコストは小規模生産では法外に高額になる可能性があり、少量生産ではプラスチック射出成形の経済性が低くなります。
- 長いリードタイム: プラスチック射出成形用の金型の設計と製造のプロセスには長い時間がかかり、プラスチック部品の生産が遅れる可能性があります。 これは、市場の需要の変化に迅速に対応したり、新製品を迅速に開発したりする必要がある企業にとって、特に問題となる可能性があります。
- 柔軟性が限られている: 金型を設計して製造すると、設計の変更や製造プロセスの変更がより簡単かつ低コストになります。 これにより、プラスチック射出成形の柔軟性が制限され、カスタム製品や独自の製品の製造には適さなくなる可能性があります。
- 環境への懸念: プラスチック射出成形は大量のプラスチックに依存しており、環境に悪影響を与える可能性があります。 プラスチック廃棄物は大きな環境問題であり、プラスチック射出成形はこの問題の一因となる可能性があります。 さらに、プラスチック製品の製造プロセスではエネルギーと天然資源の使用が必要となり、環境にさらなる影響を与える可能性があります。
- 高いスクラップ率: プラスチック射出成形では大量のスクラップ材料が発生する可能性があり、廃棄またはリサイクルに費用がかかる可能性があります。 さらに、スクラップ材料の生成により、全体の生産コストが増加し、製造プロセスの効率が低下する可能性があります。
- 材料の選択肢が限られている: プラスチック射出成形は主に、金属やセラミックなどの他の材料と比べて特性が制限されている熱可塑性材料から部品や製品を製造するために使用されます。 このため、プラスチック射出成形は、高強度、耐熱性、またはその他の高度な特性を必要とする用途にはあまり適さない可能性があります。
プラスチック射出成形の限界
プラスチック射出成形には多くの利点がありますが、プロセスには特定の制限もあります。 プラスチック射出成形には次のような制限があります。
初期工具コストが高い: 金型の設計と製造の初期コストが高くなる可能性があります。 金型は、繰り返しの射出成形プロセスに耐えられるように精密かつ耐久性が必要ですが、特に複雑な金型や大型の金型の場合、多額の先行投資が必要となる場合があります。
リードタイム: 金型の製造のリードタイムは、金型の複雑さとサイズに応じて、数週間から数か月に及ぶ場合があります。 これにより、特に時間に敏感なプロジェクトの場合、制作タイムラインに遅れが生じる可能性があります。
設計上の制約: 射出成形には、考慮する必要がある特定の設計上の制約があります。 たとえば、適切な充填と冷却を確保するには、成形品全体で均一な肉厚を実現することが重要です。 さらに、金型からの取り出しを容易にするために、垂直面には抜き勾配が必要です。
部品サイズの制限: 射出成形は、小型から中型の部品の製造に最適です。 大型の部品には特殊な機器と大型の金型が必要となる場合があり、コストと複雑さが増大します。
材料の選択: 射出成形では幅広いプラスチック材料を使用できますが、他の製造プロセスに比べて材料の選択は依然として限られています。 融点が高い材料や流動特性が悪い材料は、射出成形に適さない場合があります。
表面仕上げ: 射出成形プロセスにより、部品の表面にニット ラインやパーティング ラインが目立つ場合があります。 高品質の表面仕上げを達成することは困難な場合があり、研磨やコーティングなどの他の方法が必要になる場合があります。
制限されたアンダーカット: アンダーカットは、金型からの簡単な取り外しを妨げる部品の特徴または詳細です。 アンダーカットがあると、取り出しプロセスが複雑になる可能性があり、目的の部品形状を実現するために追加の金型フィーチャーや二次操作が必要になる場合があります。
限られた修理オプション: 金型が損傷した場合、または修正が必要な場合、既存の金型を修理または変更するには費用と時間がかかる可能性があります。 場合によっては、まったく新しい金型を製造する必要があり、追加費用と遅延が発生することがあります。
これらの制限にもかかわらず、プラスチック射出成形は依然として汎用性が高く、プラスチック部品の製造に広く使用されている製造プロセスです。 設計および生産計画の段階でこれらの制限を慎重に考慮することで、その影響を軽減し、射出成形の利点を効果的に活用することができます。
プラスチック射出成形の応用例
プラスチック射出成形は、幅広いプラスチック部品を製造できる多用途の製造プロセスです。 プラスチック射出成形の用途の一部を以下に示します。
- 消費者製品: 射出成形は、おもちゃ、台所用品、電子機器などのさまざまな製品の製造に広く使用されています。 このプロセスでは、複雑な形状と正確な寸法を備えた高品質の部品を製造できるため、厳しい公差や複雑な形状が必要な製品に最適です。
- 自動車部品: ダッシュボード部品、ドアハンドル、照明などの多くの自動車プラスチック部品は、射出成形を使用して製造されます。 このプロセスにより、大量生産と安定した品質が可能となり、自動車メーカーにとってコスト効率の高いオプションとなります。
- 医療機器: 射出成形は、注射器、吸入器、診断機器などの医療機器の製造に一般的に使用されます。 このプロセスにより、高精度かつ一貫性のある部品を製造でき、デバイスの品質と信頼性が保証されます。
- 包装: 射出成形は、容器、蓋、キャップなどのプラスチック包装の製造に広く使用されています。 このプロセスでは、一貫した寸法と高品質の仕上げを備えた部品が得られるため、魅力的な外観と確実なフィット感を備えたパッケージングに最適です。
- 航空宇宙および防衛: 射出成形では、航空機の内装、照明、通信システムなど、さまざまな航空宇宙および防衛コンポーネントが製造されます。 このプロセスでは、軽量で耐久性のある材料を使用した部品を使用できるため、高い強度対重量比が必要な用途に適しています。
- 建設: 射出成形では、プラスチック タイル、屋根材、サイディングなどのさまざまな建設資材を製造できます。 このプロセスでは、一貫した寸法と高品質の仕上げを備えた部品が得られるため、建設会社にとって魅力的な選択肢となっています。
- スポーツとレクリエーション: 射出成形は、ゴルフクラブ、テニスラケット、自転車部品などのスポーツ用品の製造に広く使用されています。 このプロセスでは、軽量の材料と正確な形状を備えた部品を製造できるため、機器の性能と耐久性が保証されます。
全体として、プラスチック射出成形は多用途で広く使用されている製造プロセスであり、さまざまな用途向けの高品質のプラスチック部品を製造できます。 このプロセスは、特定の設計および製造要件を満たすように調整できるため、複数の業界のメーカーにとって魅力的な選択肢となっています。
自動車産業とプラスチック射出成形
自動車産業は、プラスチック射出成形技術の重要なユーザーです。 プラスチック射出成形のプロセスは、自動車部品やコンポーネントの製造に革命をもたらし、複雑な形状を高精度で製造できるようになりました。 自動車業界におけるプラスチック射出成形の使用方法の一部を以下に示します。
- 内装部品: プラスチック射出成形では、ダッシュボード コンポーネント、ドア パネル、トリム ピースなどを含む多くの内部要素が生成されます。 これらの部品は複雑な形状や質感で設計でき、各車両モデルのスタイルや機能要件に合わせてカスタマイズできます。
- 外装部品: プラスチック射出成形は、バンパー、グリル、サイドミラーなどのさまざまな外装部品の製造にも使用されます。 これらの部品は、極端な気象条件に耐えられるように設計されており、複数の色と仕上げで作られています。
- ボンネット下のコンポーネント: プラスチック射出成形により、エンジン カバー、吸気システム、冷却システム部品などの多くのボンネット下の機能が製造されます。 これらのコンポーネントには高温と耐薬品性が必要ですが、これは熱可塑性プラスチック材料で実現できます。
- 電気および電子部品: プラスチック射出成形により、コネクタ、ハウジング、センサーなどのさまざまな電気および電子部品が製造されます。 これらのコンポーネントには高い精度と信頼性が必要ですが、これはプラスチック射出成形の精度と一貫性によって実現できます。
- 軽量化: プラスチック射出成形は、車両の総重量を軽減し、燃料効率を向上させ、排出ガスを削減する軽量部品の製造によく使用されます。 軽量化により、車両のハンドリングとパフォーマンスも向上します。
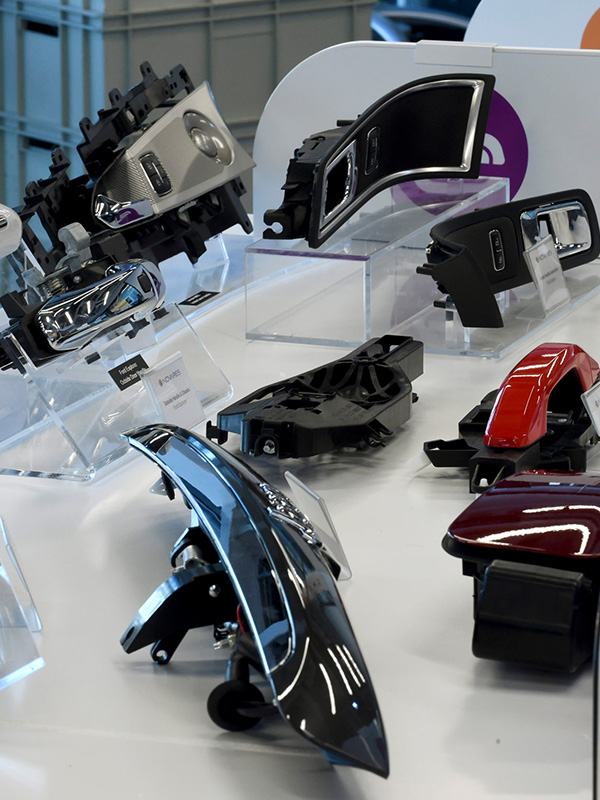
医療産業とプラスチック射出成形
プラスチック射出成形は、医療業界でさまざまな医療機器やコンポーネントを製造するために広く使用されています。 プラスチック射出成形のプロセスでは、複雑な形状を高精度で製造できるため、多くの医療用途にとって理想的な製造方法となっています。 医療業界におけるプラスチック射出成形の使用方法の一部を以下に示します。
- 医療機器: プラスチック射出成形では、手術器具、診断ツール、薬物送達システムなどのさまざまな医療機器が製造されます。これらの機器は多くの場合、高い精度と精度を必要とし、プラスチック射出成形はこれらの要件を満たすことができます。
- インプラント: プラスチック射出成形は、関節置換術や歯科用インプラントなど、さまざまなインプラントの製造にも使用されます。 これらのインプラントは、患者の解剖学的構造に適合するように設計でき、生体適合性の材料で製造できます。
- 研究室用機器: プラスチック射出成形により、ピペット、マイクロプレート、試験管が製造されます。 これらのコンポーネントは、信頼性の高い結果を保証するために、高い精度と精度を必要とします。
- 包装: プラスチック射出成形は、滅菌バリア システムや個々の製品のカスタム包装などの医療機器の包装の製造に使用されます。 これらの包装ソリューションは、医療機器の無菌性と完全性を維持するのに役立ちます。
- 使い捨てデバイス: プラスチック射出成形では、注射器、針、カテーテルなどの使い捨てデバイスが製造されることがよくあります。 これらのデバイスは低コストで大量に製造できるため、医療現場での感染拡大の防止に役立ちます。
消費者製品およびプラスチック射出成形
プラスチック射出成形は、その汎用性、効率性、費用対効果の高さから、消費者製品の製造に広く使用されています。 プラスチック射出成形のプロセスでは、複雑な形状を高精度で製造できるため、多くの民生用途にとって理想的な製造方法となっています。 消費者製品の製造におけるプラスチック射出成形の使用方法の一部を以下に示します。
- おもちゃ: プラスチック射出成形では、小さなフィギュアから大きなプレイセットまで、幅広いおもちゃが製造されます。 このプロセスにより、複雑なデザインや詳細を作成し、さまざまな色や素材でおもちゃを作ることができます。
- 家庭用品: プラスチック射出成形では、キッチン用品、保存容器、掃除用品などのさまざまな家庭用品が製造されます。 これらの製品は、耐久性があり、軽量で使いやすいように設計できます。
- エレクトロニクス: プラスチック射出成形では、コンピューターのハウジング、電話ケース、充電器などの多くの電子部品が製造されます。 プロセスの精度と精度により、これらのコンポーネントは高度な一貫性と信頼性を持って製造されます。
- パーソナルケア製品: プラスチック射出成形により、歯ブラシ、かみそり、ヘアブラシなどのユニークなケア製品が製造されます。 これらの製品は、使いやすさと安全性を確保するために、高い精度と精度が必要です。
- 自動車アクセサリ: プラスチック射出成形では、ダッシュボード コンポーネントやカップ ホルダーなどのさまざまな自動車アクセサリが製造されます。 これらのコンポーネントは、軽量で耐久性があり、日常使用による磨耗に耐えられるように設計できます。
プラスチック射出成形における環境への配慮
プラスチック射出成形は広く使用されている製造プロセスですが、環境に重大な影響を及ぼします。 プラスチック射出成形における環境への考慮事項の一部を以下に示します。
- 材料の選択: 射出成形に使用されるプラスチック材料の選択は、環境に大きな影響を与える可能性があります。 生分解性またはリサイクル可能な材料もあれば、そうでない材料もあります。 生分解性またはリサイクル可能な材料を使用すると、プラスチック射出成形による環境への影響を軽減できます。
- エネルギー消費: プラスチック射出成形では、プラスチックを溶かして金型に射出するために大量のエネルギーが必要です。 電気機械や閉ループ システムなどのエネルギー効率の高い機器とプロセスにより、エネルギー消費と環境への影響を削減できます。
- 廃棄物管理: プラスチック射出成形では、過剰な材料、欠陥部品、梱包などから廃棄物が発生します。 廃棄物のリサイクルや再利用など、適切な廃棄物管理を実践することは、プラスチック射出成形による環境への影響を軽減するのに役立ちます。
- 化学物質の使用: 離型剤や洗浄溶剤など、プラスチック射出成形品に含まれる一部の化学物質は環境に悪影響を与える可能性があります。 環境に優しい代替品を使用するか、これらの化学物質の使用を最小限に抑えると、環境への影響を軽減できます。
- 耐用年数終了に関する考慮事項: 射出成形で製造されたプラスチック製品は最終的に埋め立て地に送られることが多く、劣化するまでに数百年かかる場合があります。 リサイクル性または生分解性を考慮して製品を設計すると、プラスチック射出成形による環境への影響を軽減できます。
プラスチック射出成形の未来
技術と材料の進歩により、プロセスがさらに効率的でコスト効率が高く、持続可能なものになると予想されているため、プラスチック射出成形の将来は有望に見えます。 プラスチック射出成形の将来を形作ると思われるトレンドと発展のいくつかを以下に示します。
- 積層造形: 3D プリンティングとも呼ばれる積層造形は、プラスチック射出成形を変革する可能性のある新興技術です。 3D プリンティングを使用して金型を作成することにより、メーカーは従来の金型作成技術にかかる時間とコストを大幅に削減できます。
- スマート製造: 自動化、データ分析、機械学習を含むスマート製造は、プラスチック射出成形に革命をもたらすと期待されています。 製造業者は、センサーとデータ分析を使用してプロセスを最適化することで、効率を向上させ、無駄を削減し、生産性を向上させることができます。
- 持続可能な材料: バイオプラスチックや再生プラスチックなどの持続可能な材料は、プラスチック射出成形業界でますます人気が高まっています。 これらの材料は環境上の利点をもたらし、メーカーが持続可能性の目標を達成するのに役立ちます。
- マイクロ成形: 小型部品を高精度で製造するマイクロ成形は、ヘルスケアやエレクトロニクスなどの業界でますます重要になっています。 技術と材料の進歩により、マイクロモールディングがより利用しやすくなり、コスト効率も高くなることが期待されています。
- カスタマイズ: 消費者がよりパーソナライズされた製品を要求するにつれて、プラスチック射出成形はより柔軟でカスタマイズ可能になることが予想されます。 リアルタイム フィードバックや機械学習などのテクノロジーの進歩により、メーカーはカスタム製品を迅速かつ効率的に生産できるようになります。
結論:
プラスチック射出成形は、幅広い製品の生産に革命をもたらした、非常に汎用性が高く効率的な製造プロセスです。 医療機器から自動車部品に至るまで、プラスチック射出成形には、高い生産速度、設計の柔軟性、費用対効果など、他の製造プロセスに比べて多くの利点があります。 技術と材料の継続的な進歩により、プラスチック射出成形の将来は明るく、このプロセスは今後数年間で製造業界においてさらに重要な役割を果たすことになるでしょう。