射出成形のよくある成形欠陥の解決策
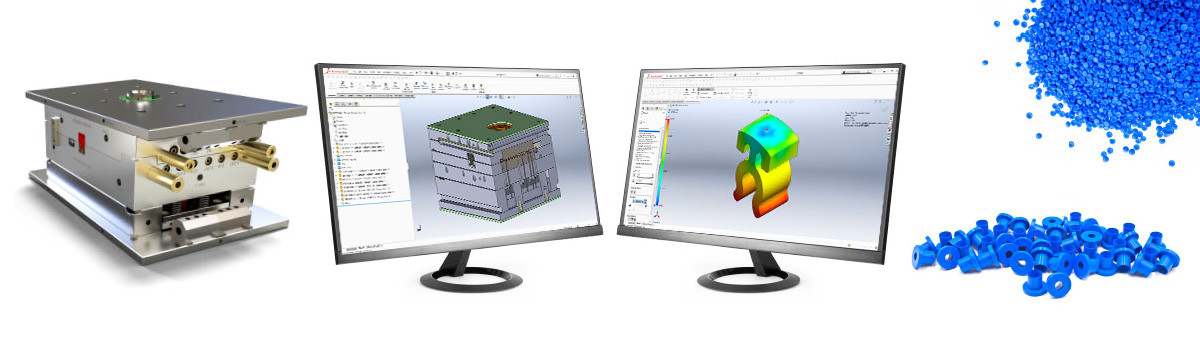
金型を使用してプラスチック射出成形部品を加工する場合、欠陥が発生することが多く、これは加工効率に大きく影響します。 以下は、プラスチック射出成形部品の一般的な成形欠陥と解決策です。
ショートショット
ショートショットとは、金型が完全に充填されていないために製造された製品が不完全であることを指します。
この欠陥は通常、ゲートから最も遠い場所、または金型上の狭い領域からのみ到達できる部品に発生します。これは、狭い領域が溶湯の流れに影響を与える可能性があるためです。
ショートショットにより、マイクロフローマークが発生したり、製品の大部分が明らかに欠落したりする可能性があります。
原因:
ショートショットの原因には次のようなものがあります。
金型に注入された原料が十分ではありません。
溶湯の抵抗が大きく、金型に完全に充填できない場合があります。
金型の通気性が悪く、キャビテーションが発生して溶融物がブロックされ、溶融物が金型の一部の領域に流れなくなります。
バリは、金型キャビティから押し出された余分な原材料が製品に付着することで発生します。
この欠陥は製品のエッジや金型の各構成部品に発生します。 原料が金型から溢れたり、移動型と固定型の接合部分から溢れたりする場合があります。
また、金型コアにバリが見られる場合がありますが、これは油圧やアンギュラーピンが原因です。
バリの程度はさまざまで、薄い場合もあれば厚い場合もあります。
原因:
バリの原因には次のようなものがあります。
型締金型の表面が損傷しているか、ひどく磨耗しています。
移動型と固定型はロック時にずれてしまいます。
金型内の原料圧力は型締力よりも高くなります。
上記の XNUMX 番目の状態は、さまざまな理由から発生します。 次の場合、型締力よりも原料の圧力の方が高くなります。
射出成形金型の最初の段階(金型充填段階)では、原料が過剰に充填され、金型内の圧力が上昇します。
金型充填プロセス中、メルト フローの大きな抵抗により、金型内の圧力も上昇します。
圧力保持段階中の金型キャビティの圧力が高すぎます。
型締力が不足している。
劣化
分解すると多くの結果が得られる可能性があります。 問題の程度や深刻度も異なります。 最も深刻な場合、製品が完全に変色し、機械的特性が低下する可能性があります。 局所的な劣化では、黒い縞模様や斑点が生じるだけです。
原因:
劣化は原材料が傷つくことによって起こります。 プラスチックを形成する長鎖分子は、過度の熱や過度のせん断応力の作用により分解します。 分子の分解中に、揮発性ガスにより分解プロセスが加速され、原材料の脱色が発生します。 大量の分子が分解すると、最終的には原料の内容が破壊され、機械的特性に悪影響を及ぼします。
材料バレルの温度が不均一であるため、局所的な劣化が発生する可能性があります。
劣化は次の状況で発生する可能性があります。
原材料が材料バレルまたはホット ランナー システム内で過熱されています。
原料が樽内に長く留まりすぎます。
射出成形プロセス中に、原材料にかかるせん断応力が大きすぎます。 ノズルが詰まっている場合、またはゲートとランナーが狭すぎる場合は、せん断応力が増加します。
変形
通常、製品の形状は金型の形状と一致しているはずです。 変形とは製品の変形を指します。
状態が悪化すると、金型から取り出す際に製品が完全に変形してしまいます。 状態が深刻でない場合、製品の形状に小さな凹凸が現れます。
長いがサポート エッジがない、または大きな平面は、最も変形しやすい領域です。
原因:
変形の原因:
離型時の温度が高すぎます。
厚い部分と薄い部分では冷却時間が異なることや、金型を移動するときと固定するときの金型温度の違いにより、製品内部の収縮率が異なります。
充填時に金型の流れがスムーズでないか(いわゆる「凍結配向」)、または保圧段階で金型キャビティ内の圧力が高すぎます。
不純物
不純物は、さまざまな色の斑点、パッチ、またはストライプの形で現れることがよくあります。 最も一般的なのは黒い斑点です。
不純物は単なる小さな斑点である可能性もありますが、明らかな縞模様になったり、深刻な場合には脱色の大部分を占める可能性もあります。
原因:
不純物は、以下のような原材料が混入した雑貨によって引き起こされます。
原料が樽に運ばれる際に雑貨と混ざります。
原材料の分解は、あらゆる切断機構から落下し、マシンボルト、乾燥ドラム内壁、ジョイント/ノズルなどの原材料に混入する可能性があります。
ラミネート加工
ラミネート加工により、製品表面と他の原材料の性質や質感の違いから生じる「表皮効果」が製品表面に発生し、剥離可能な皮が形成されます。
積層が本格的である場合、断面領域全体が異なる層で構成されており、互いに溶け合っていません。 欠陥があまり目立たない場合、製品の外観は要件を満たしている可能性がありますが、製品の機械的特性は損なわれます。
原因:
ラミネートの主な原因は XNUMX つあります。 XNUMXつ目は、XNUMX種類の異なる原料を誤って混合した場合です。 XNUMX つの原料は圧力下で同時にバレル内に輸送されます。 ただし、異なる層を強制的に押し合わせて製品を形成するのと同じように、冷却時に金型を一緒に溶かすことができない場合。
第二に、コールドメルトが狭いゲートを強制的に通過すると、せん断応力が発生します。 せん断応力が高すぎると、あらかじめ溶融した溶融層が完全に溶融できなくなります。
混合の危険性:
注意すべきことの XNUMX つは、PVC とアベタールなど、一部の原材料を混合すると強い化学反応を引き起こすため、混合してはいけないことです。
シルバーリニア
線状のスライバーは局所的な現象かもしれませんが、深刻な場合には表面全体に拡大する可能性があります。
シルバーリニアは製品の外観に影響を与えるだけでなく、製品の機械的特性にもダメージを与えます。
原因:
シルバーリニアの原因は次の XNUMX 点です。
原料が湿っているため、空気中の蒸気を吸収してしまうものもあります。 原料が湿りすぎると、バレル内の高温高圧により加圧蒸気が発生する可能性があります。 これらの蒸気は製品の表面を突き破り、銀色の縞模様を形成します。
溶融物が熱損傷を受け、局所的な劣化が発生します。 発生した揮発性ガスは金型表面でブロックされ、製品表面に縞模様が発生します。
これは劣化ほどひどいものではありません。 溶融物の温度が高いか、可塑化中または金型への射出中にせん断応力を受ける限り、この問題が発生する可能性があります。
グロス/シャドウ
製品の表面仕上げは金型の表面仕上げと同じである必要があります。 両者の表面仕上げが異なる場合、光沢・影不良が発生しました。
欠陥が発生すると表面は暗くなりますが、粗い表面は滑らかで光沢があります。
原因:
光沢や影の原因には次のようなものがあります。
湯流れが悪かったり、金型表面の温度が低く、材料成形時の金型表面の仕上がりが再現できません。
保圧中は、キャビティ内の圧力が低く、冷却過程で材料が金型表面に張り付き、収縮跡が残ります。
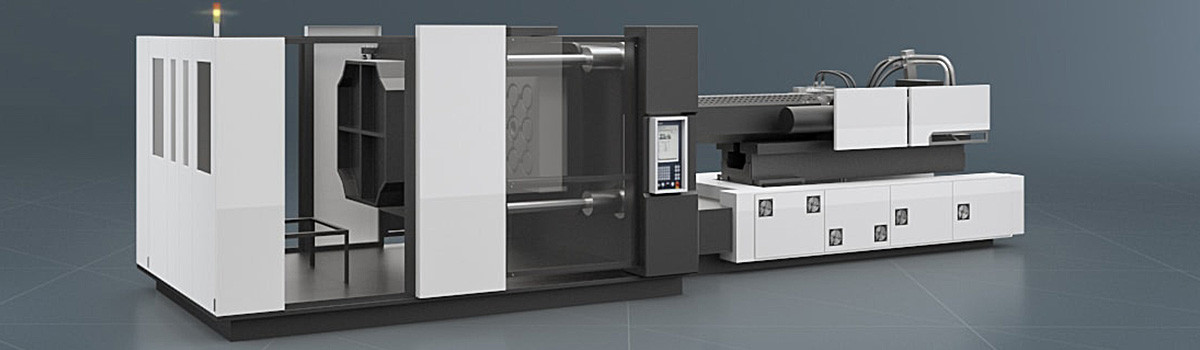
フローマーク
フローマークは製品の表面にさまざまな形で見られます。 通常、影の領域が形成されます。
フローマークは、製品の表面に指で触ることができないような凹凸や凹みを生じさせません。 この欠陥は、ドラッグ マーク、ゴースト、シャドウとも呼ばれます。
フローマークが目立つと溝が発生し、製品の表面にマークのような欠陥が残ります。
原因:
フローマークは次の場合に発生します。
メルトの流動性が悪い、または金型表面温度が低いため、金型充填時のプラスチックの流動抵抗が大きくなります。
金型の充填では、金型表面の凹凸、金型表面に印刷されたマークや模様、充填工程中の湯流れ方向の変化などにより、湯流れに抵抗が生じます。
ジョイントライン
接合線は、金型充填時に XNUMX つのメルト フロントが接触するときに発生し、製品の表面に線のように現れます。
接合線とは製品表面のひび割れ線のようなもので、目に見えないものです。
金型を設計する場合、目に見える接合線の発生は避けられません。 この場合、製品の強度や外観を損ねないよう、接合ラインを極力短くしてください。
原因:
メルトフロントの生成にはさまざまな理由があります。 最も考えられる原因は、金型コアのエッジに沿った溶融物の流動です。 XNUMX つの溶融物が接触すると、接合線が生成されます。 XNUMX つのメルトフロントの温度は、製品の強度と外観に影響を与えず、うまく融合できるように十分に高くする必要があります。
XNUMX つの溶融物が完全に融合できない場合、欠陥が生成されます。
欠陥の原因:
金型には厚い部分と薄い部分があり、溶湯の流速が異なり、金型の薄い部分を溶湯が流れるときは温度が低くなります。
各ランナーの長さが異なります。 孤独なランナーは冷めやすいでしょう。
金型キャビティの圧力は、圧力保持段階で溶融物を完全に融合させるのに十分ではありません。
残った気泡によりメルトフロントが融合できなくなり、これも燃焼の原因となります。
バーニング
焼き上がりはショートショットと似ていますが、エッジが不規則に色褪せし、わずかに焼けるような匂いがします。 状態がひどい場合には、プラスチックの焼ける臭いとともにカーボンブラックの部分が製品に現れます。
欠陥が除去されていない場合、金型に黒い堆積物が発生することがよくあります。 燃焼により発生するガスや油物質はすぐに確認しないと空気穴を塞いでしまう可能性があります。 焼けは通常、通路の端で見られます。
原因:
燃焼は内部燃焼効果によって引き起こされます。 空気中の圧力が非常に短時間に急激に上昇すると、温度が上昇し、燃焼を引き起こします。 収集されたデータによると、射出成形プロセスにおける内燃効果により、最大 600 度の高温が発生する可能性があります。
焼けは次の場合に発生する可能性があります。
金型の充填速度が速いため、金型キャビティから空気を抜くことができず、流入するプラスチックのブロックにより気泡が発生し、圧縮後に内部燃焼効果を引き起こします。
空気穴がふさがれている、または通気がスムーズでありません。
金型内の空気を空気穴から排除する必要があります。 位置、数、大きさ、機能により通気に影響が出る場合、金型内に空気が滞留し、焦げの原因となります。 型締力が大きいと通気性も悪くなります。
収縮
収縮とは、製品の表面に生じるわずかな空洞のことを指します。
欠陥がわずかな場合、製品の表面は凹凸があります。 ひどい場合には広範囲の製品が崩壊してしまいます。 アーチ、ハンドル、突起のある製品は、多くの場合、収縮欠陥に悩まされます。
原因:
収縮は、冷却中に原材料が広範囲に収縮することによって引き起こされます。
製品の厚い部分(アーチなど)では、材料の中心温度が低いため、収縮は表面よりも遅く発生し、原材料の内部に収縮力が生じ、外側が内側のくぼみに引き込まれます収縮を生じさせます。
収縮は次の状況で発生します。
金型キャビティ内の圧力は、冷却過程での素材の収縮によって発生する力よりも低くなります。
冷却工程における金型キャビティの加圧時間が不十分であり、ゲートから原料がキャビティ外に流出してしまう。
過剰な原料が注入される前にスクリューが完全に引き抜かれるため、成形および保圧段階では原料の緩衝能力が十分ではありません。
ゲートとランナーの断面積は製品の厚さよりもはるかに小さいため、製品の押出プロセス前にゲートがすでに凍結していることを意味します。
バブル
真空気泡は気泡の形で表示され、透明な製品上で簡単に見つけることができます。 不透明な製品の断面にも見られます。
原因:
気泡とは製品の真空部分であり、冷却過程で原料が収縮する際に発生します。
収縮と同様に、素材の内部でも収縮力が生じます。 違いは、気泡が発生した時点で製品の外観が固まっており、崩れることなく中空の気泡が発生することです。
気泡の原因は還元の原因と同じで、次のようなものがあります。
非効率的な金型キャビティ圧力
キャビティ加圧時間が不十分
ランナーとゲートのサイズが小さすぎる
吹き付け跡
スプレーマークは、ゲートの反対側のネジ部分を指します。 スプレー痕は製品の外観に影響を与えるだけでなく、製品の強度にも影響します。
原因:
スプレー マークは、金型充填プロセス中に制御不能になった溶融物の流れによって発生します。
溶けたプラスチックは大きな圧力の下で金型に入ります。 金型の充填速度が速すぎると、プラスチックが金型キャビティの開いた隙間から排出され、すぐに跳ね返って冷却されます。 このとき、ねじ山が形成され、溶融プラスチックがゲートに入るのを妨げます。
スプレーマークの主な原因は、ゲートの位置やゲートの設計が間違っていることです。 次の XNUMX つの状況は、欠陥の状況を悪化させます。
高い金型充填速度
金型充填時のメルトフロー不良