熱可塑性射出成形
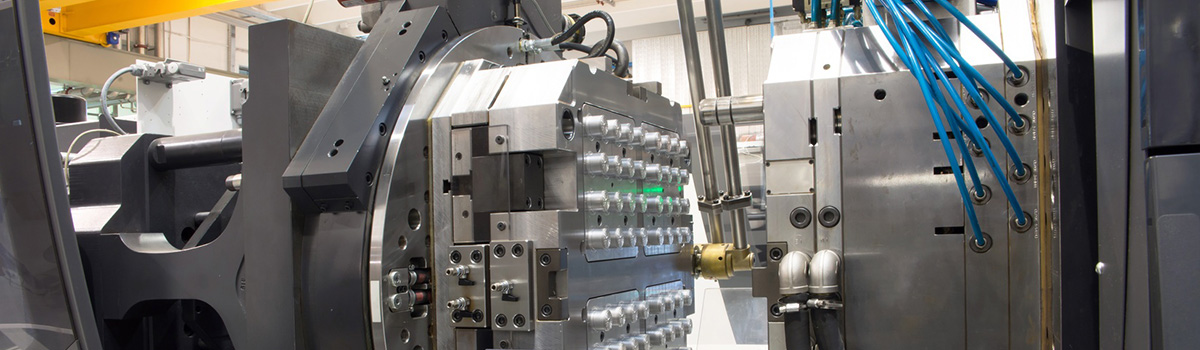
熱可塑性プラスチック射出成形は、複数の業界でさまざまなプラスチック部品を作成するために使用される一般的な製造プロセスです。 プラスチックのペレットを溶かし、金型に射出して立体的な形状を作り出す加工です。 熱可塑性プラスチック射出成形は、公差が厳しい高品質のプラスチック部品を大量に生産するのに非常に効率的でコスト効果が高くなります。 この包括的なガイドでは、長所と短所、使用される熱可塑性プラスチックの種類、射出成形プロセス、設計上の考慮事項など、熱可塑性プラスチック射出成形のさまざまな側面について説明します。
熱可塑性樹脂射出成形の歴史
熱可塑性プラスチック射出成形の歴史は、XNUMX 世紀以上にわたる技術の進歩、材料開発、産業応用に及びます。 セルロイド成形プロセスとしての地味な始まりから、今日の高度な技術に至るまで、射出成形は重要な製造技術であり続け、イノベーションを推進し、さまざまな産業を形成しています。
- 初期の開発:ジョン ウェスリー ハイアットと彼の兄弟イザイアは、熱可塑性プラスチック射出成形の起源を 19 世紀後半まで遡り、最初の実用的な射出成形機を開発しました。 1872 年に、彼らはプランジャーを使用してセルロイドを金型キャビティに注入し、固体物体を作成する装置の特許を取得しました。 この画期的な進歩により、現代の射出成形プロセスの基礎が築かれました。
- 材料の進歩:20 世紀初頭、新しい合成ポリマーの導入により、射出成形の新たな可能性が開かれました。 フェノール樹脂であるベークライトは、その優れた電気絶縁特性により、成形材料として人気がありました。 1930 年代から 1940 年代にかけて、ポリマー化学の進歩により、ポリスチレンやポリエチレンなどの他の熱可塑性プラスチックが開発され、射出成形に適した材料の範囲がさらに拡大しました。
- 産業上の採用: 熱可塑性射出成形は、メーカーがその費用対効果と多用途性を認識したため、1950 年代に広く採用され始めました。 高圧機械の導入により、サイクルタイムが短縮され、生産量が増加しました。 その結果、個人用から産業用まで多彩な製品が誕生しました。 これらには、自動車部品、家電製品、玩具が含まれます。
- 技術革新:数十年にわたり、射出成形技術は進化し続けました。 1960 年代にはコンピューター制御の機械が登場し、成形プロセスを正確に制御できるようになりました。 1980 年代のホット ランナー システムの導入により、ランナーとスプルーが不要になり、無駄が削減され、効率が向上しました。 近年、自動化、ロボット工学、3D プリンティングの進歩により、射出成形業界はさらに革命を起こし、複雑な設計が可能になり、生産時間が短縮されました。
- 持続可能性とリサイクル:環境への懸念が高まる中、射出成形業界は持続可能性への取り組みを進めています。 メーカーはバイオベースおよびリサイクル熱可塑性プラスチックを開発し、化石燃料ベースの材料への依存を減らしています。 さらに、リサイクル技術の向上により、消費者および産業廃棄物の再処理が可能になり、熱可塑性プラスチック射出成形による環境への影響が最小限に抑えられています。
- 将来の展望:熱可塑性射出成形の将来は有望です。 業界は、小型コンポーネントのマイクロ射出成形、複雑な部品のマルチマテリアルおよびオーバーモールディング技術、プロセスの監視と最適化のためのインテリジェント技術の統合などのイノベーションを模索しています。 さらに、研究者らは、生分解性材料と積層造形の進歩によりこの分野に革命が起こり、射出成形がさらに持続可能で汎用性の高いものになると期待しています。
熱可塑性射出成形の利点
熱可塑性プラスチック射出成形は、メーカーに多くの利点をもたらします。 設計の柔軟性が提供され、さまざまな機能を備えた複雑で入り組んだ設計が可能になります。 このプロセスはコスト効率が高く、材料の無駄が減り、単価が下がります。 熱可塑性射出成形は複数の材料をサポートし、さまざまな用途に多用途性を提供します。
- 設計の柔軟性:熱可塑性射出成形では、アンダーカット、薄肉、さまざまな厚さなどの機能を備えた複雑で複雑なデザインが可能となり、設計者に大きな自由をもたらします。
- コスト効率: このプロセスは非常に効率的であり、材料の無駄を削減し、単価を削減します。 複数の部品を同時に成形し、生産サイクルを高速化することでコスト削減に貢献します。
- 材料の多様性: 熱可塑性射出成形は幅広い材料をサポートしているため、メーカーは、硬い材料か柔軟な材料、透明な材料か不透明な材料、耐薬品性の材料など、各用途に最適なオプションを選択できます。
- 強度と耐久性:射出成形された熱可塑性プラスチックは、高強度、靭性、耐衝撃性などの優れた機械的特性を発揮します。 ガラス繊維やカーボン繊維などの強化オプションを使用すると、これらの特性がさらに強化されます。
- 一貫性と品質:射出成形により、部品間の一貫した品質と寸法精度が保証され、厳しい公差と信頼性の高い製品が提供されます。 また、このプロセスにより滑らかで均一な表面仕上げが得られるため、追加の仕上げ作業が不要になります。
- スケーラビリティと大量生産:射出成形は少量から大量まで拡張可能なため、大量生産に適しています。 メーカーは一度金型を作成すると、最小限のばらつきで同一の部品を大量に生産できます。
- 統合と組み立て:射出成形部品は複数のコンポーネントを XNUMX つの部品に組み込むことができるため、追加の組み立てプロセスの必要性が軽減されます。 この統合により、製品のパフォーマンスが向上し、組み立て時間が短縮され、コストが削減されます。
- サステナビリティ:射出成形業界では、持続可能性への注目が高まっています。 バイオベースおよびリサイクル材料を利用できるため、環境に優しい製品の製造が可能になります。 熱可塑性プラスチックの材料の効率的な使用とリサイクル可能性は、より環境に優しい製造プロセスに貢献します。
これらの利点により、この製造方法はさまざまな業界で広く採用されており、複雑な製品要件に対して高品質でコスト効率が高く、環境に優しいソリューションを提供しています。
熱可塑性射出成形の欠点
熱可塑性プラスチック射出成形には多くの利点がありますが、いくつかの欠点もあります。 メーカーは、これらの要因を慎重に評価し、利点と比較して、特定の用途に対する熱可塑性プラスチック射出成形の適合性を判断する必要があります。
- 高額な初期投資: 熱可塑性プラスチック射出成形作業をセットアップするには、金型の設計と製造、および専用機械の購入に多額の初期投資が必要です。 金型や工具の作成に関連するコストは、特に複雑で入り組んだ設計の場合、多額になる可能性があります。
- 設計上の制限: 熱可塑性プラスチック射出成形には設計の柔軟性がありますが、一定の制限が存在します。 たとえば、部品全体で均一な肉厚を実現することは困難な場合があり、材料分布のばらつきや潜在的な構造的弱点につながります。 さらに、アンダーカットや複雑な形状が存在すると、追加の金型フィーチャーの使用や二次加工が必要になる場合があり、コストと生産時間が増加します。
- 長いリードタイム:射出成形用の金型の設計と製作のプロセスには時間がかかり、製品開発のリードタイムが長くなる場合があります。 設計の反復プロセス、金型の製造、およびテストにより、全体の製造スケジュールに大幅な時間がかかる可能性があり、納期が厳しいプロジェクトには適していない可能性があります。
- 材料選択の制約:熱可塑性射出成形は幅広い材料をサポートしていますが、特定の制限と制約があります。 一部の材料には特定の処理要件があったり、入手可能性が限られている場合があり、特定の用途の設計選択や材料の選択に影響を与えます。
- 部品サイズの制限:射出成形機には、装置の物理的なサイズと対応できる金型のサイズの両方の点でサイズ制限があります。 巨大な部品を製造するには、特殊な設備や代替製造方法が必要になる場合があります。
- 環境への影響:業界は持続可能性を目指して取り組んでいますが、熱可塑性プラスチック射出成形プロセスでは依然としてスクラップやスプルーなどの廃棄物が発生します。 環境への影響を最小限に抑えるには、これらの材料の適切な廃棄とリサイクルが必要です。
- プロセス最適化の複雑さ:熱可塑性プラスチック射出成形の最適なプロセスパラメータを達成することは、複雑で時間がかかる場合があります。 メーカーは、一貫した部品の品質を確保し、欠陥を最小限に抑えるために、温度、圧力、冷却速度、サイクル時間を慎重に制御および最適化する必要があります。
射出成形に使用される熱可塑性プラスチックの種類
これらは、射出成形で一般的に使用される熱可塑性プラスチックのほんの一例です。 各材料には独自の特性があり、強度、柔軟性、耐薬品性、透明性、コストに基づいて特定の用途に適しています。 メーカーは、射出成形プロジェクトに適切な熱可塑性プラスチックを選択する際に、これらの特性と要件を考慮する必要があります。
- ポリプロピレン(PP):ポリプロピレンは、射出成形で一般的に使用される多用途の熱可塑性プラスチックです。 優れた耐薬品性、低密度、優れた衝撃強度を備えています。 PP(ポリプロピレン)は、包装、自動車部品、家電、医療機器など幅広い用途に使用されています。
- ポリエチレン(PE):ポリエチレンも射出成形で広く使用されている熱可塑性プラスチックです。 高密度ポリエチレン (HDPE) や低密度ポリエチレン (LDPE) など、さまざまな形状で入手できます。 PEは耐薬品性、靭性、柔軟性に優れているため、ボトル、容器、パイプなどに適しています。
- ポリスチレン(PS):ポリスチレンは、その透明性、剛性、手頃な価格で知られる多用途の熱可塑性プラスチックです。 包装、消費財、使い捨て製品で一般的に使用されています。 PS (ポリスチレン) は迅速な加工を可能にし、優れた寸法安定性を提供しますが、脆くて環境応力亀裂が発生しやすい可能性があります。
- アクリロニトリルブタジエンスチレン(ABS): ABS は、優れた耐衝撃性と耐久性で知られる人気の熱可塑性プラスチックです。 アクリロニトリル、ブタジエン、スチレンの特性を組み合わせて、自動車部品、電子機器の筐体、玩具に適した多用途の材料を作り出します。
- ポリ塩化ビニル(PVC): PVC は、優れた耐薬品性、耐久性、低コストで知られ、広く使用されている熱可塑性プラスチックです。 使用する配合や添加剤に応じて、硬質にも柔軟にもなります。 PVC (ポリ塩化ビニル) は、建築、電気絶縁、ヘルスケア製品、および包装に一般的に使用されています。
- ポリカーボネート(PC): ポリカーボネートは、並外れた耐衝撃性と高い耐熱性を備えた透明な熱可塑性プラスチックです。 自動車部品、安全ヘルメット、電子ディスプレイなど、光学的な透明性が必要な用途で一般的に使用されています。
- ナイロン(ポリアミド):ナイロンは、優れた機械的特性と耐薬品性で知られる、強くて耐久性のある熱可塑性プラスチックです。 自動車部品、産業用部品、消費財など、高い強度が要求される用途で一般的に使用されています。
- ポリエチレンテレフタレート (PET):PET は、ボトル、容器、包装材料の製造によく使われる熱可塑性プラスチックです。 優れた透明性、耐薬品性、バリア性を備えているため、食品や飲料の用途に適しています。
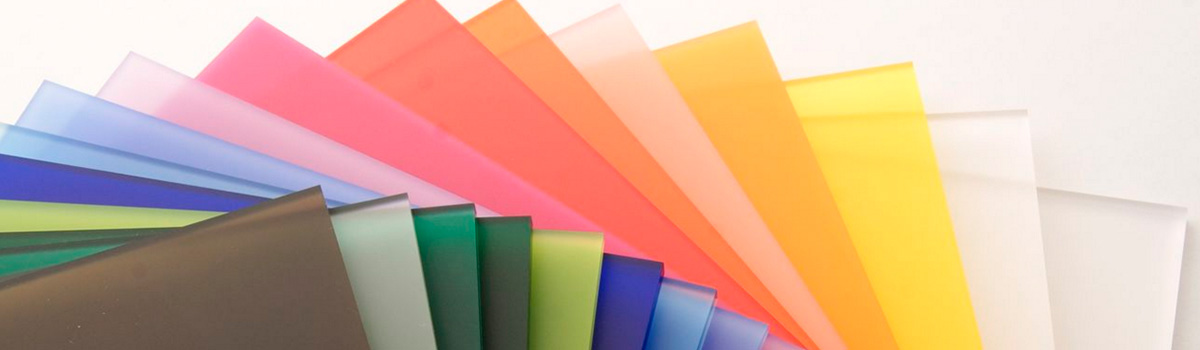
射出成形に使用される熱可塑性プラスチックの特性
熱可塑性プラスチックのこれらの特性は、特定の射出成形用途への適合性を決定する上で重要な役割を果たします。 メーカーはこれらの特性を慎重に検討し、必要な性能、環境条件、コスト要件に基づいて適切な熱可塑性プラスチックを選択する必要があります。
- 機械的性質:射出成形に使用される熱可塑性プラスチックは、引張強度、耐衝撃性、曲げ強度などのさまざまな機械的特性を示すことができます。 これらの特性によって、加えられる力に耐える材料の能力と、さまざまな用途における全体的な耐久性が決まります。
- 耐薬品性:射出成形に使用される熱可塑性プラスチックの多くは、化学薬品、溶剤、油に対して優れた耐性を備えています。 この特性は、過酷な環境や腐食性物質にさらされる用途にとって非常に重要です。
- 熱安定性:熱可塑性プラスチックの熱安定性とは、大きな劣化を起こすことなく高温に耐える能力を指します。 一部の熱可塑性プラスチックは優れた耐熱性を示し、高温でも機械的特性を維持できます。
- 電気的特性:射出成形に使用される熱可塑性プラスチックは、電気絶縁性、導電性、絶縁耐力などの特定の電気的特性を持つ場合があります。 これらの特性は、材料が信頼性の高い電気的性能を提供する必要がある電気および電子産業の用途には不可欠です。
- 透明性と鮮明さ:ポリカーボネートや PET などの特定の熱可塑性プラスチックは、優れた透明性と透明性を備えているため、光学特性が必要な用途に適しています。 メーカーは通常、透明な窓、レンズ、ディスプレイなどの製品にこれらの材料を使用します。
- 柔軟性と靭性: 柔軟性と靭性は、耐衝撃性と耐久性が必要な用途に使用される熱可塑性プラスチックの重要な特性です。 ABS やナイロンなどの一部の熱可塑性プラスチックは優れた靭性を備えており、破損することなく繰り返しの衝撃に耐えることができます。
- 寸法安定性:寸法安定性とは、温度変化などのさまざまな条件下で形状とサイズを維持する熱可塑性樹脂の能力を指します。 寸法安定性に優れた材料により、部品の寸法が一定になり、反りや歪みのリスクが最小限に抑えられます。
- 化学的適合性:熱可塑性プラスチックの化学的適合性とは、酸、塩基、溶剤などのさまざまな化学物質との劣化や相互作用に抵抗する能力を指します。 最適な性能を確保するには、意図した用途で遭遇する特定の化学環境に耐えることができる熱可塑性プラスチックを選択することが不可欠です。
- 密度: 熱可塑性プラスチックの厚さはさまざまで、重量や部品全体の特性に影響を与える可能性があります。 ポリエチレンなどの低密度材料は軽量のソリューションを提供し、一方、ポリプロピレンなどの高密度材料は追加の強度と剛性を提供します。
射出成形プロセス: ステップバイステップ
射出成形プロセスは次の手順に従って行われるため、高品質の熱可塑性プラスチック部品を効率的かつ正確に製造できます。 一貫した部品寸法、材料特性、全体的な品質を確保するには、各ステップで慎重な制御と監視が必要です。
- 金型の設計と製作: 射出成形プロセスの最初のステップは、金型の設計と製作です。 メーカーは、所望の部品仕様を達成するために、正確かつ詳細な金型設計を作成する必要があります。 次に、製造業者は、CNC や放電加工 (EDM) などのさまざまな技術を使用して金型を製造します。
- 材料の準備: 型の準備ができたら、次のステップは準備です。 熱可塑性のペレットまたは顆粒は、必要な材料特性に基づいて選択され、ホッパーで溶解されます。 次に、オペレーターは材料を射出成形機のバレルに供給し、そこで材料の溶解と均質化が行われます。
- 注入:射出段階では、オペレーターは溶融した熱可塑性プラスチックを高圧下で金型キャビティに射出します。 機械の射出ユニットは、溶けた材料をノズルから金型に押し込みます。 材料が金型キャビティに充填され、目的の部品の形状が得られます。
- 冷却と固化:金型に充填した後、オペレーターは溶融プラスチックを冷却して固化させます。 冷却は、寸法安定性と適切な部品形成を達成するために非常に重要です。 オペレーターは、金型内のチャネルに冷媒を循環させるか、冷却プレートを使用することによって、冷却プロセスを制御できます。
- 型開きと取り出し:オペレータは金型を開け、プラスチックが固まったら金型キャビティから部品を取り出します。 機械内の突き出しシステムは、ピン、突き出しプレート、またはエアブラストを使用して、金型から領域を除去します。 これで、金型は次の射出サイクルの準備が整います。
- 後処理: 取り出した後、部品にはトリミング、バリ取り、表面仕上げなどの後処理操作が行われる場合があります。 これらの手順は、余分な材料を除去し、粗いエッジを滑らかにし、部品の最終的な外観を改善するのに役立ちます。
- 品質検査: 最後のステップでは、射出成形された部品の品質を検査し、指定された要件を満たしていることを確認します。 寸法測定、目視検査、機能テストなどのさまざまな品質管理手法を使用して、部品の品質と完全性を検証できます。
- リサイクルと材料の再利用:射出成形時に発生する余剰材料やスクラップ材料はリサイクルして再利用できます。 新しい熱可塑性材料の使用を減らすことで、無駄を最小限に抑え、持続可能性を向上させることができます。
射出成形に使用される設備
これらの装置コンポーネントは、熱可塑性材料の溶解と射出から、最終部品の成形、冷却、取り出しまで、射出成形プロセスを容易にします。 効率的で高品質な射出成形品の生産を実現するには、これらの装置コンポーネントの適切な操作とメンテナンスが不可欠です。
- 射出成形機:射出成形の主要な装置は、熱可塑性プラスチック材料を溶解し、金型に射出してプロセスを制御する役割を果たします。
- 型: プラスチック部品の望ましい形状と特徴を作成するためにカスタム設計された金型は、キャビティとコアの XNUMX つの部分で構成されます。 オペレーターはそれを射出成形機の型締ユニットに取り付けます。
- ホッパー:熱可塑性プラスチック材料をペレットまたは粒状で保持し、溶融および射出のために射出成形機のバレルに供給するコンテナ。
- バレルとスクリュー: 円筒形のチャンバーであるバレルは、スクリューがその中で回転して材料を溶融、混合、標準化するときに、熱可塑性材料を溶融して均質化します。
- 冷暖房システム:射出成形機には、バレルの温度を上げるための電気ヒーターや熱油を使用するヒーターなどの発熱体と、金型を冷却してプラスチック部品を固化させるための水や油の循環などの冷却システムが備えられています。
- エジェクターシステム:固化後に成形品を金型キャビティから取り除きます。通常は、金型を開くときにエジェクター ピン、プレート、またはエアブラストを使用します。
- 制御システム:射出成形プロセスのさまざまなパラメータを監視および制御し、オペレータが射出速度、温度、圧力、冷却時間などのパラメータを設定および調整できるようにします。
射出成形機の種類と特徴
各タイプの射出成形機にはそれぞれの特徴と利点があり、メーカーは特定の生産要件に応じて最適な装置を選択できます。
- 油圧式射出成形機: これらの機械は、油圧システムを使用して、溶融プラスチックを金型に射出するために必要な圧力を生成します。 これらは、高いクランプ力、正確な制御、およびさまざまな熱可塑性プラスチックの取り扱いにおける多用途性で知られています。 油圧機械は大規模生産に適しており、複雑な金型にも対応できます。
- 電動射出成形機:電気機械は、射出、クランプ、エジェクター システムなどの機械の動作に電気サーボ モーターを利用します。 正確な制御、エネルギー効率、油圧機械よりも速い応答時間を実現します。 電気機械は、高い再現性と精度が要求される精密成形用途に最適です。
- ハイブリッド射出成形機:ハイブリッド機械は、油圧装置と電気装置の両方の利点を組み合わせています。 油圧サーボ システムと電気サーボ システムを組み合わせて使用し、高精度、エネルギー効率、費用対効果を実現します。 ハイブリッド マシンは幅広いアプリケーションに適しており、パフォーマンスと運用コストのバランスが取れています。
- XNUMX プラテン射出成形機: XNUMX プラテン マシンは、金型をクランプするための XNUMX つの別個のプレートを備えた独自の設計を採用しています。 この設計により、安定性が向上し、金型の同期性が向上し、より大きな金型サイズとより高い型締力が可能になります。 XNUMX プラテン機械は、精密な成形が必要な大型で複雑な部品に適しています。
- 多部品射出成形機:メーカーは、単一の成形サイクルで複数の材料または色の部品を製造できるようにこれらの機械を設計します。 各種射出装置や金型を備えており、異種材料の同時射出が可能です。 マルチコンポーネント機械は、さまざまな特性を持つ複雑な部品の製造に柔軟性と効率をもたらします。
- マイクロ射出成形機:小型で精密な部品を製造するために特別に設計されたマイクロ射出成形機は、信じられないほど高い精度と精度を実現します。 厳しい公差と最小限の材料無駄で複雑な細部を作成できます。 エレクトロニクス、医療機器、マイクロ光学機器では、通常、マイクロ射出成形機が使用されます。
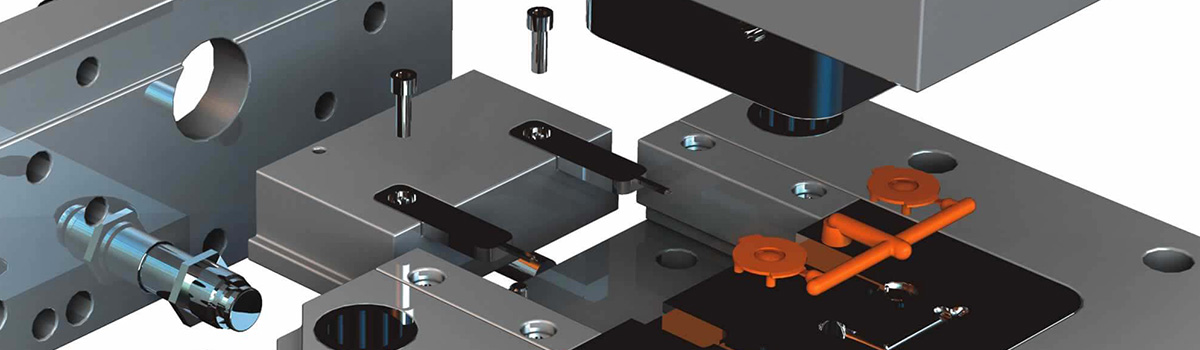
射出成形の金型設計に関する考慮事項
射出成形生産を成功させるには、金型設計を慎重に検討することが不可欠です。
- 部品設計:金型の設計は、形状、寸法、機能的特徴など、部品の特定の要件に対応する必要があります。 メーカーは、取り出しの容易さと部品の品質を確保するために、抜き勾配、肉厚、アンダーカット、および必要な要素を適切に考慮する必要があります。
- モールド材質: 耐久性、寸法安定性、耐熱性を実現するには、金型材料の選択が重要です。 一般的な金型材料には、合金鋼、アルミニウム合金、工具鋼などがあります。 材料の選択は、生産量、部品の複雑さ、予想される工具寿命などの要因によって異なります。
- 冷却システム:部品を適切に固化し、サイクル時間を最小限に抑えるには、効率的な冷却が不可欠です。 金型設計には、均一な金型冷却を確保するために、冷却チャネルまたは戦略的に配置されたインサートを組み込む必要があります。 適切に冷却すると、反り、収縮、部品の欠陥のリスクが軽減されます。
- ベント:射出プロセス中に空気とガスを逃がすには、適切な通気が必要です。 通気が不十分だと、ガストラップ、焼け跡、または部品の充填が不完全になる可能性があります。 メーカーは、通気用の溝、ピン、またはその他の機構を金型設計に組み込むことで通気を実現できます。
- 排出システム:金型の設計には、金型キャビティから成形部品を安全かつ効率的に取り出すための効果的な排出システムが組み込まれている必要があります。 排出システムは、機能や重要な機能との干渉を避けるために戦略的に配置された、排出ピン、スリーブ、またはその他の機構で構成されます。
- ゲートのデザイン:ゲートは、溶融プラスチックが金型キャビティに入る場所です。 ゲートの設計では、成形品の適切な充填を確保し、流線を最小限に抑え、材料の早期凍結を防止する必要があります。 標準的なゲート設計には、部品要件と材料特性に応じて、エッジ ゲート、トンネル ゲート、ホット ランナー システムが含まれます。
- パーティングライン:金型の設計では、金型の XNUMX つの半分が結合するラインである適切なパーティング ラインを定義する必要があります。 パーティング ラインを適切に配置すると、バリとパーティング ラインの不一致が最小限に抑えられ、金型の効率的な組み立てが容易になります。
- 金型のメンテナンスと保守性: メーカーは、メンテナンス、修理、金型の保守のしやすさを考慮する必要があります。 金型コンポーネントは、洗浄、検査、交換のために簡単にアクセスできる必要があります。 クイックチェンジインサートやモジュラー金型設計などの機能を組み込むと、金型の保守性が向上します。
射出成形に使用される金型材料
金型材料の専門家と協力し、成形アプリケーションの特定のニーズを考慮することは、最適な金型の性能と部品の品質を達成するために最適な材料を決定するのに役立ちます。
- 鋼合金: 射出成形金型には、耐久性、耐熱性、耐摩耗性に優れた工具鋼(P20、H13など)やステンレス鋼などの合金鋼がよく使われています。 これらの材料は射出成形プロセスの高温と高圧に耐えることができ、高品質の部品を製造するための良好な寸法安定性を提供します。
- アルミニウム合金:7075 や 6061 などのアルミニウム合金は軽量で熱伝導率が高いため、効率的な冷却が必要な金型に適しています。 メーカーはプロトタイピング、少量生産、または軽量化が重要な用途にアルミニウム金型を使用することがよくあります。 ただし、アルミニウム製の金型は合金鋼に比べて耐久性が低い場合があります。
- 銅合金:ベリリウム銅などの銅合金は、高い熱伝導率と良好な機械加工性を示します。 効果的な冷却のために優れた熱伝達を必要とする金型に使用されます。 銅合金は、成形部品からの熱を素早く放散し、より速く凝固するため、サイクルタイムの短縮に役立ちます。
- 工具鋼:H13、S7、D2 などの工具鋼は、高性能工具用途向けに設計されています。 これらの鋼は、高い強度、硬度、耐摩耗性を兼ね備えています。 工具鋼は、生産量の多い金型、研磨材、または要求の厳しい成形条件に適しています。
- ニッケル合金:インコネルやハステロイなどのニッケル合金は、優れた耐食性、高温強度、熱安定性で知られています。 メーカーはこれらの合金を、腐食性材料を扱う金型や、極端な温度や過酷な成形環境への耐性が必要な金型に使用しています。
- 複合材料:強化プラスチックや金属インサートを備えた複合材料などの複合材料は、特定の成形用途に使用されることがあります。 これらの材料は、高強度、熱安定性、軽量化などの特性のバランスを提供します。 複合金型は、特定の生産要件に対してコスト効率の高い代替手段となります。
射出成形金型の種類
射出成形は、プラスチック部品の多用途で広く使用されている製造プロセスです。
- XNUMX プレート金型:XNUMX プレート金型は最も一般的なタイプの射出成形金型です。 キャビティ プレートとコア プレートの XNUMX つのプレートで構成されており、成形品の取り出しを可能にするために分離されます。 キャビティ プレートには金型のキャビティ側が含まれ、コア プレートにはコア側が含まれます。 メーカーは、設計が比較的シンプルであるため、XNUMX プレート金型をさまざまな部品の製造に使用しています。
- XNUMX プレート金型:XNUMX プレート金型は XNUMX プレート金型の発展版です。 追加のプレート、ランナー、またはスプルー プレートが含まれます。 ランナー プレートは、スプルー、ランナー、ゲート用の個別のチャネルを作成し、成形品の取り外しを容易にします。 メーカーは通常、複雑なゲート システムの詳細を作成する場合、またはピース上のゲートの痕跡を回避する必要がある場合に、XNUMX プレート金型を使用します。
- ホットランナー金型:ランナーとゲート システムはホット ランナー金型内で加熱されるため、各サイクルでの材料の凝固や再溶解の必要がなくなります。 ホット ランナー システムは、プラスチックの溶融状態を維持する加熱されたマニホールドとノズルで構成されています。 ホット ランナー金型には、サイクル タイムの短縮、材料の無駄の削減、ゲートの痕跡を最小限に抑えることによる部品の品質の向上などの利点があります。
- コールド ランナー金型: コールド ランナー金型には従来のランナーとゲート システムがあり、溶融プラスチックがコールド ランナーを通って流れ、サイクルごとに固化します。 その後、オペレーターが固化したランナーを除去するため、材料が無駄になります。 メーカーは通常、少量生産の場合、またはより単純な設計により材料コストがそれほど重要ではない場合に、複雑なランナー金型を使用します。
- インサート金型:インサート金型は、射出成形中に金型キャビティに金属またはプラスチックのインサートを組み込みます。 インサートは、金型に事前に配置することも、自動プロセスによって挿入することもできます。 この金型を使用すると、追加のコンポーネントや強化要素を成形部品に組み込むことができ、その機能や強度が向上します。
- オーバーモールド: オーバーモールドには、ある材料を別の材料の上に成形することが含まれ、通常は硬質プラスチック基板をより柔らかいエラストマーまたは熱可塑性プラスチックと接着します。 このプロセスにより、単一の金型で複数の素材やテクスチャを使用したパーツを作成でき、グリップ、クッション性、または美的特徴が向上します。
射出成形コストに影響を与える要因
これらの要素を考慮することは、メーカーが射出成形のコストを見積もり、最適化し、特定の生産要件に合わせて品質、効率、費用対効果のバランスを確保するのに役立ちます。
- パーツの複雑さ:部品設計の複雑さは、射出成形のコストを決定する上で重要な役割を果たします。 複雑な形状、アンダーカット、薄壁、または複雑な形状では、追加の工具、特殊な金型、またはより長いサイクルが必要になる場合があり、全体の製造コストが増加します。
- 材料の選択:熱可塑性プラスチック材料の選択は、射出成形コストに影響します。 材料が異なればキログラムあたりの価格も異なり、材料の入手可能性、特性、加工要件などの要因が材料全体のコストに影響を与える可能性があります。
- 工具と金型の設計: 射出成形コストの中で、初期工具と金型設計のコストが大きくかかります。 金型の複雑さ、キャビティの数、金型のサイズ、金型の材料などの要因が、工具や金型の製造費用に影響します。 より複雑な金型や高度な機能を必要とする金型では、先行投資が増加する可能性があります。
- 生産量: 生産量は、射出成形における部品あたりのコストに直接影響します。 書籍の価格が高くなると、多くの場合規模の経済が生じ、部品あたりのコストが削減されます。 逆に、少量生産の場合は、セットアップ、工具、材料の無駄により、より高い料金が発生する可能性があります。
- サイクルタイム: 冷却段階と取り出し段階を含むサイクル タイムは、生産能力と全体のコストに影響します。 サイクル時間が長くなると、生産量が減少し、価格が高くなる可能性があります。 金型設計、冷却システム、プロセスパラメータを最適化すると、サイクルタイムを最小限に抑え、効率を向上させることができます。
- 品質要件:厳しい品質要件や特定の認証は、射出成形のコストに影響を与える可能性があります。 正確な公差、表面仕上げ要件を満たす、または追加のテストには、他のリソース、プロセス、または検査が必要となり、全体のコストが増加する場合があります。
- 二次的な操作:成形部品に組み立て、塗装、追加の仕上げステップなどの後処理操作が必要な場合、これらの操作により射出成形全体のコストが増加する可能性があります。
- サプライヤーと所在地:射出成形サプライヤーの選択とその所在地はコストに影響を与える可能性があります。 人件費、諸経費、物流費、輸送費はサプライヤーの所在地によって異なり、全体の製造コストに影響します。
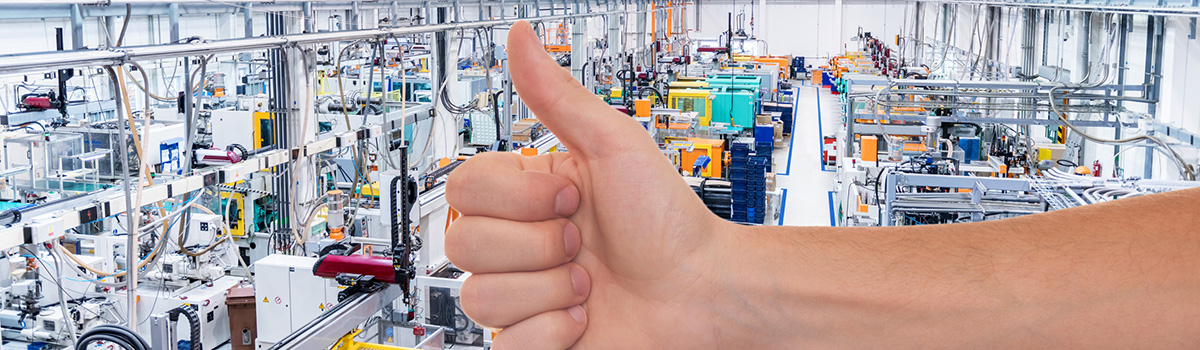
射出成形における品質管理
射出成形プロセス全体にわたって堅牢な品質管理措置を導入することで、潜在的な欠陥、逸脱、または不一致を特定して対処することができ、顧客の仕様と要件を満たす高品質の部品の生産が保証されます。
- プロセス監視: 溶融温度、射出圧力、冷却時間、サイクル時間などの主要なプロセスパラメータを継続的に監視することで、部品製造の一貫性と再現性が保証されます。 リアルタイム監視および自動化システムは、設定パラメータからの変動や逸脱を検出できるため、タイムリーな調整が可能になり、プロセスの安定性が維持されます。
- 検査と測定:寸法精度、部品の品質、仕様への準拠を確認するには、成形部品の定期的なレビューと測定が不可欠です。 当社のサービスは、寸法測定、表面品質分析、外観検査、機能テストの実施など、さまざまな品質管理方法をカバーしています。 正確な評価を行うために、三次元測定機 (CMM) や光学式および外観検査システムなどのさまざまな検査技術が採用されています。
- 統計的プロセス管理 (SPC): SPC には、射出成形の品質を監視および制御するためのプロセス データの収集と分析が含まれます。 管理図や工程能力分析などの統計的手法は、傾向を特定し、プロセスの変動を検出し、プロセスが定義された管理限界内に留まることを確認するのに役立ちます。 SPC により、問題を事前に特定でき、プロセスの最適化が促進されます。
- 材料試験: 熱可塑性プラスチック、添加剤、着色剤などの原材料をテストすることで、その品質と射出成形への適合性が保証されます。 材料試験には、メルト フロー インデックス (MFI) 分析、機械的特性、熱特性、材料組成が含まれる場合があります。 材料の品質を検証することは、成形部品の欠陥や不一致を防ぐのに役立ちます。
- 工具のメンテナンスと検査:射出成形の品質を確保するには、射出成形金型の適切なメンテナンスと定期的な検査が非常に重要です。 金型コンポーネントの定期的な洗浄、潤滑、評価は、部品の品質に影響を与える可能性のある摩耗、損傷、劣化を防ぐのに役立ちます。 一貫した成形性能を維持するには、磨耗または損傷した金型部品を適時に修理または交換することが不可欠です。
- 文書化とトレーサビリティ:射出成形の品質管理には、包括的な文書とトレーサビリティ記録を維持することが不可欠です。 プロセスパラメータ、検査結果、材料情報、および製造中に行われた変更や調整を記録することが重要です。 適切な文書化により、部品のトレーサビリティが可能になり、根本原因の分析が容易になり、品質の一貫性が確保されます。
- トレーニングとスキル開発: オペレーター、技術者、品質管理担当者に適切なトレーニングとスキル開発プログラムを提供することで、射出成形プロセス、品質要件、検査技術に対する理解が深まります。 よく訓練された担当者は、欠陥を検出し、問題のトラブルシューティングを行い、是正措置を効果的に実行して、高品質の生産を保証します。
射出成形の一般的な欠陥とその回避方法
射出成形プロセスの定期的な検査、監視、分析、および機器と金型の適切なメンテナンスと調整は、これらの一般的な欠陥を特定して対処するのに役立ちます。
- ヒケ:ヒケとは、不均一な冷却や収縮によって生じる成形品の表面のくぼみです。 ヒケを避けるために、適切なゲートの位置と設計、最適な冷却システム設計、均一な壁厚分布を考慮する必要があります。 射出圧力を上げるか冷却時間を調整することも、ヒケを最小限に抑えるのに役立ちます。
- 反り:反りとは、不均一な冷却または残留応力による突出後の成形品の変形または曲がりを指します。 均一な肉厚を維持し、適切な冷却チャネルを使用し、金型へのバランスのとれた充填と保圧を確保することが、反りを防ぐために重要です。 金型温度を最適化し、適切な抜き勾配を使用し、材料温度と射出速度を制御すると、反りを最小限に抑えることができます。
- フラッシュ:バリは、余分な材料が金型のパーティング ラインに流れ込むときに発生し、最終部品に薄くて不要な突起や余分な材料が生じます。 適切な型締力の適用、正確な位置合わせ、適切な通気技術の使用など、適切な金型設計を確保することでバリを効果的に防止できます。 射出圧力、温度、サイクルタイムなどのプロセスパラメータを最適化すると、バリが減少します。
- ショートショット:クイック ショットは、射出された材料が金型キャビティを満たさず、その結果、部品が不完全になる場合に発生します。 写真不足を避けるには、適切な材料の選択、適切な溶融温度と粘度の確保、適切な射出圧力と時間を維持することが不可欠です。 さらに、十分なランナーとゲートのサイズと適切な通気のための金型設計を検証することは、クイック ショットの防止に役立ちます。
- ウェルド ライン:ウェルド ラインは、XNUMX つ以上の溶融材料のフロー フロントが出会って固化するときに発生し、その結果、成形品の表面に目に見える線やマークが現れます。 適切なゲートとランナーの設計、最適な溶融温度、射出速度、材料の流れと成形品の形状の調整により、ウェルド ラインを最小限に抑えることができます。 モールド フロー解析とゲート配置の最適化も、ウェルド ラインの防止または軽減に役立ちます。
- 火傷跡:焼け跡とは、材料の過剰な熱や過熱によって生じる成形品の表面の変色や黒い点のことです。 極端な溶融温度を避け、適切な冷却チャネルを使用し、サイクル時間を最適化することで、焼け跡を防ぐことができます。 適切な通気、適切なゲート設計、金型温度の制御も焼け跡を最小限に抑えるのに役立ちます。
成形後の作業: 仕上げと組み立て
射出成形後、所望の最終製品を得るために、多くの成形部品に追加の仕上げおよび組み立て作業が必要になる場合があります。 これらの成形後の操作には次のものが含まれます。
- トリミング:トリミングや切削工具を使用して、成形品の周囲の余分な材料やバリを取り除きます。
- 表面処理:塗装、コーティング、テクスチャリングなどのさまざまな技術を使用して部品表面の外観や機能を強化します。
- アセンブリ:複数の成形部品を結合したり、ファスナー、インサート、ラベルなどのコンポーネントを追加して最終製品を完成させます。
- テスト:寸法分析、材料特性試験、性能試験などのさまざまな試験方法による部品の品質と機能の検証。
- 梱包と配送:顧客またはエンドユーザーに出荷するための最終製品の適切な梱包とラベル付け。
成形後の操作の選択は、特定の用途と望ましい最終製品の特性によって異なります。 望ましい絶対的な製品品質と機能を達成するには、射出成形の専門家、仕上げおよび組立の専門家、そして顧客の間の緊密な協力が不可欠です。 成形後の作業を適切に計画し、製造プロセスに統合することで、効率的な生産と高品質の製品のタイムリーな納品を確保できます。
射出成形と他のプラスチック製造プロセスの比較
各プラスチック製造プロセスには利点と制限があり、さまざまな用途に適しています。
- 射出成形: 射出成形は、プラスチック部品の製造に非常に汎用性が高く、広く使用されている製造プロセスです。 高い生産効率、正確な部品の複製、複雑な形状の作成機能などの利点があります。 射出成形は大量生産に適しており、幅広い熱可塑性プラスチック材料を使用できます。 優れた寸法精度と表面仕上げを備えており、自動車、消費財、医療機器などのさまざまな業界に最適です。
- 中空成形、吹込み成形: ブロー成形は、主にボトル、容器、自動車部品などの中空プラスチック部品の製造に使用されるプロセスです。 プラスチックを溶かし、金型キャビティ内で膨張させて、目的の形状を作成することが含まれます。 ブロー成形は大量生産に適しており、均一な肉厚の大型軽量部品を製造できます。 ただし、射出成形と比較すると、部品の複雑さと材料の選択の点で制限があります。
- 熱成形:熱成形は、熱可塑性プラスチックシートを加熱し、金型または真空成形を使用して成形することによってプラスチック部品を製造するために使用されるプロセスです。 包装、使い捨て製品、トレイやカバーなどの大型製品で一般的に使用されています。 熱成形により、大型部品をコスト効率よく生産でき、迅速なプロトタイピングが可能になります。 ただし、射出成形と比較すると、部品の複雑さ、材料の選択、寸法精度に関して制限があります。
- 押し出し:押出成形は、プラスチックの異形材、シート、チューブ、フィルムを製造する連続プロセスです。 プラスチック樹脂を溶かし、金型に押し込んで目的の形状を作成します。 押出成形は、一貫した断面を持つ長く連続したプラスチック製品の製造に適しています。 押出成形は高い生産速度とコスト効率を実現しますが、射出成形と比較すると複雑な部品形状や正確な寸法制御の点で制限があります。
- 圧縮成形:圧縮成形では、事前に測定した量の熱硬化性材料を加熱した金型キャビティに配置し、硬化するまで高圧下で圧縮します。 自動車部品や電気絶縁体など、高強度と寸法安定性を備えた部品の製造に一般的に使用されています。 圧縮成形では、部品の均一性が高く、生産効率が高く、幅広い材料を使用できます。 ただし、射出成形と比較すると、部品の複雑さとサイクルタイムの点で制限があります。
熱可塑性樹脂射出成形の応用例
熱可塑性射出成形は、その汎用性、効率性、費用対効果の高さから、さまざまな業界で広く使用されています。 熱可塑性射出成形の用途には次のようなものがあります。
- 自動車産業: 自動車業界では、熱可塑性プラスチック射出成形を広く使用して、内外装トリム、ダッシュボード、ドアパネル、バンパー、電気コネクタなどのさまざまなコンポーネントを製造しています。 このプロセスにより、部品の正確な複製、複雑な形状、軽量材料が可能になり、燃料効率と設計の柔軟性が向上します。
- 消費財:射出成形は、家庭用電化製品、電子機器、包装容器、玩具などの消費財の製造に幅広く応用されています。 このプロセスにより、寸法と表面仕上げが安定した耐久性のある高品質の製品の大量生産が可能になります。 また、カスタマイズ オプションや製品の迅速な反復も可能になります。
- 医療機器:射出成形は、注射器、手術器具、埋め込み型コンポーネント、薬物送達システムなどの幅広いデバイスを製造する医療業界で重要な役割を果たしています。 このプロセスにより、医療分野の厳しい規制要件を満たす、滅菌済みで正確な生体適合性のある部品の生産が保証されます。
- エレクトロニクスおよび電気産業:エレクトロニクス産業では、射出成形を利用して電気コネクタ、エンクロージャ、スイッチ、その他のコンポーネントを製造しています。 このプロセスでは、高い寸法精度、優れた表面仕上げ、インサート成形やオーバーモールディングなどの機能を組み込むことができるため、複雑な電子アセンブリの効率的な製造が可能になります。
- 包装業界:食品および飲料、医薬品、パーソナルケアなどのさまざまな業界では、プラスチックの包装容器、キャップ、蓋、ボトルの製造に射出成形が一般的に使用されています。 このプロセスにより、効率的な製造サイクルで、軽量で耐久性があり、見た目にも魅力的なパッケージング ソリューションを作成できます。
- 航空宇宙産業:航空宇宙分野では、エアダクト、ブラケット、内装パネル、構造部品などの軽量で高性能のコンポーネントの製造に射出成形が採用されています。 このプロセスにより、先進的な材料と複雑な部品形状の使用が可能になり、軽量化と燃料効率の向上に貢献します。
熱可塑性プラスチック射出成形の環境への影響
熱可塑性プラスチック射出成形は、多くの利点があるため人気のある製造プロセスですが、環境への影響を考慮することも不可欠です。 考慮すべき点は次のとおりです。
- 材料効率:熱可塑性プラスチック射出成形は、無駄を最小限に抑えて材料効率を高めます。 このプロセスでは、金型に射出される材料の量を正確に制御し、余分な材料の必要性を減らします。 メーカーは、再研磨およびリサイクル技術を採用してスクラップまたは不合格部品を再利用し、材料の無駄をさらに削減することもできます。
- エネルギー消費:メーカーは、エネルギー効率が高くなるように射出成形機を設計しており、最新のモデルにはサーボ モーターや可変速ドライブなどの先進技術が組み込まれています。 これらの機能は、成形時の電力消費を削減することでエネルギー使用を最適化し、その結果、エネルギー要件が低下し、環境への影響が軽減されます。
- 廃棄物管理:メーカーは、材料の無駄を最小限に抑えながら、残りの材料、スプルー、またはランナーを処理する適切な廃棄物管理慣行を実施する必要があります。 メーカーは、射出成形時に発生するプラスチック廃棄物を収集して再利用するためのリサイクル プログラムを確立することで、埋め立て地に送られる廃棄物を削減できます。
- 排出削減: 熱可塑性プラスチック射出成形は一般に、他の製造プロセスよりも排出量が低くなります。 メーカーは、環境に優しい材料を使用し、エネルギー効率の高い機器を導入し、放出される排出物を捕捉する高度な排気および濾過システムを採用することにより、排出量を削減できます。
- 持続可能な素材の選択:熱可塑性プラスチック材料の選択は、射出成形の環境持続可能性に大きな影響を与える可能性があります。 生分解性またはバイオベースのプラスチック、およびリサイクルまたはリサイクル可能な材料を選択すると、プロセス全体のエコロジカル・フットプリントを削減できます。
ライフサイクルの考慮: 環境への影響を評価するには、成形製品のライフサイクル全体を考慮することが不可欠です。 設計および材料の選択段階で、メーカーは部品の耐久性、リサイクル可能性、耐用年数が終了した廃棄または再利用の可能性などの要素を考慮する必要があります。
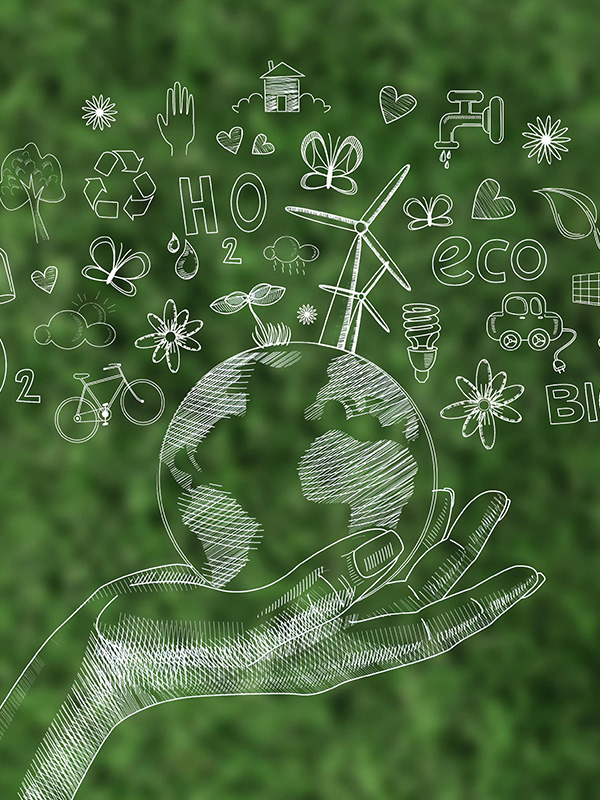
熱可塑性樹脂射出成形の将来
技術の継続的な進歩と、さまざまな業界における高品質で精密な部品の需要の増加により、熱可塑性射出成形の将来は有望に見えます。 今後数年間に予想される主要な発展には次のようなものがあります。
- 効率を向上させ、コストを削減するために、自動化とロボット工学の使用が増加しています。
- 部品の性能を向上させ、新しい用途を可能にする新しい材料とプロセスの開発に努力が注がれています。
- 射出成形による環境への影響を軽減するために、リサイクル材料の使用やエネルギー消費の最適化など、持続可能な手法の採用が増えています。
- 3D プリンティングやシミュレーション ソフトウェアなどのデジタル テクノロジーの統合を強化し、設計や製造プロセスを改善します。
世界の射出成形市場は、さまざまな業界でのプラスチック製品の需要の増加により、特に新興国で拡大しています。
適切な射出成形パートナーの選択
プロジェクトの成功には、適切な射出成形パートナーを選択することが重要です。 時間をかけて複数のオプションを評価し、現場訪問を実施し、徹底的な話し合いを行って、互換性があり長期にわたるパートナーシップを確保してください。
- 専門知識と経験:業界における豊富な知識と経験を持つ射出成形パートナーを探してください。 さまざまな分野のクライアントに高品質の製品とソリューションを提供してきた実績が必要です。 さまざまな材料、金型設計、製造プロセスについての理解を考慮してください。
- 製造能力: 射出成形パートナーの製造能力を評価します。 プロジェクトの要件に対応できる最新の機械とテクノロジーを備えた設備の整った施設を備えていることを確認してください。 生産能力、さまざまな部品サイズと複雑さに対応できる能力、および希望する生産量とスケジュールを満たす能力を考慮してください。
- 品質保証:射出成形では品質が最も重要です。 潜在的なパートナーの品質管理システムと認証を評価します。 厳格な品質基準に従い、堅牢な検査プロセスを備え、包括的なテストを実行して部品の品質と一貫性を保証するパートナーを探してください。
- 設計およびエンジニアリングのサポート:信頼できる射出成形パートナーは、製造可能性を考慮して部品設計を最適化するための設計およびエンジニアリングのサポートを提供する必要があります。 部品の品質と効率を向上させるために、材料の選択、金型設計、プロセスの最適化について貴重な意見を提供できる熟練したエンジニアが必要です。
- コスト競争力:コストだけが決定要因となるべきではありませんが、射出成形パートナーの価格設定とコスト競争力を評価することが不可欠です。 詳細な見積もりをリクエストし、工具費、材料費、人件費、および提供される追加サービスを検討してください。
- コミュニケーションとコラボレーション:パートナーシップを成功させるには、効果的なコミュニケーションとコラボレーションが不可欠です。 射出成形パートナーが良好なコミュニケーション チャネルを持ち、問い合わせに応答し、プロジェクトの最新情報を定期的に提供できることを確認してください。 協力的なアプローチにより、お客様の要件を確実に満たし、あらゆる課題に迅速に対処できるようになります。
- お客様の声とレビュー:顧客の参考資料を探したり、レビュー/体験談を読んで、射出成形パートナーとの他の顧客の経験についての洞察を得ることができます。 この情報を取得すると、信頼性、迅速性、および顧客満足度の全体的なレベルを判断するのに役立ちます。
まとめ
熱可塑性プラスチック射出成形は、プラスチック部品を大量に製造する多用途でコスト効率の高い方法です。 複雑な形状を高い精度と一貫性で製造できるその能力は、自動車、医療、エレクトロニクス、消費財などのさまざまな業界で人気の選択肢となっています。 熱可塑性射出成形の利点、欠点、設計上の考慮事項など、熱可塑性射出成形のさまざまな側面を理解することで、ビジネス ニーズに適した射出成形パートナーの選択について情報に基づいた意思決定を行うことができます。