Литье пластмасс под давлением
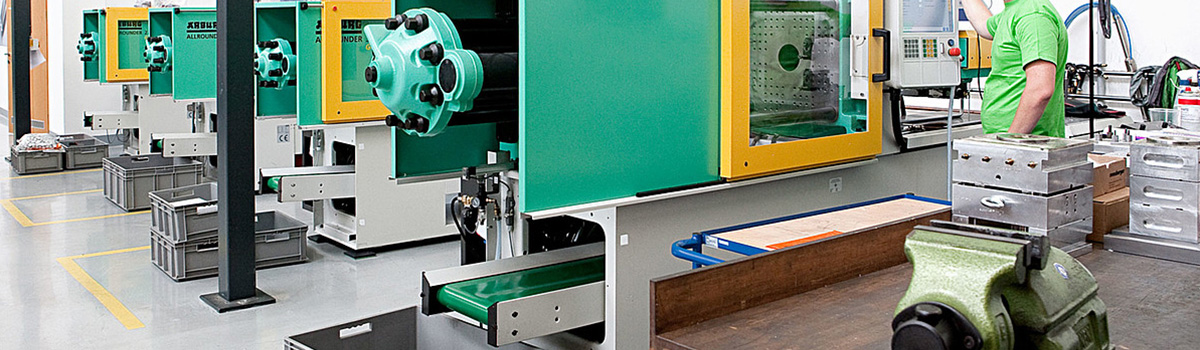
Литье пластмасс под давлением — это производственный процесс, который включает плавление пластиковых гранул и их впрыскивание в полость пресс-формы для создания трехмерного объекта. Этот процесс начинается со многих продуктов, от небольших прецизионных деталей до важных автомобильных компонентов. Литье пластмасс под давлением предлагает множество преимуществ по сравнению с другими производственными процессами, включая высокую производительность, гибкость конструкции и экономичность. В этом руководстве подробно рассматривается литье пластмасс под давлением и исследуются его различные области применения, преимущества и ограничения.
История литья пластмасс под давлением
Литье пластмасс под давлением — это производственный процесс, который включает впрыскивание расплавленного пластика в полость пресс-формы для создания определенной формы. История литья пластмасс под давлением восходит к концу 1800-х годов, когда был впервые изобретен целлулоид, тип пластика. Однако именно в 1940-х годах литье пластмасс под давлением стало широко использоваться в качестве технологии производства.
Во время Второй мировой войны спрос на серийные изделия из пластика увеличился, и производители начали искать новые и более эффективные способы их производства. В 1946 году американский изобретатель Джеймс Уотсон Хендри разработал первую машину для литья под давлением с винтовым литьем, которая произвела революцию в индустрии литья пластмасс под давлением. Эта машина позволила более точно и последовательно контролировать процесс впрыска, сделав производство больших количеств пластиковых деталей более доступным и эффективным.
На протяжении 1950-х и 1960-х годов прогресс в технологии пластмасс продолжал улучшать процесс литья пластмасс под давлением. Внедрение новых материалов, таких как полистирол и полиэтилен, привело к созданию более сложных и прочных пластиковых деталей. Кроме того, усовершенствования в технологии литьевых машин, включая использование гидравлических систем, сделали процесс литья под давлением еще более эффективным и экономичным.
Сегодня литье пластмасс под давлением представляет собой высокоавтоматизированный процесс, используемый для производства широкого спектра пластиковых изделий, от игрушек и потребительских товаров до автомобильных запчастей и медицинских устройств. С развитием новых материалов и технологий процесс литья пластмасс под давлением продолжает развиваться и совершенствоваться, гарантируя, что он останется жизненно важной технологией производства на долгие годы.
Основы литья пластмасс под давлением
Литье пластмасс под давлением — это производственный процесс для создания деталей и изделий из пластмасс. Процесс включает в себя впрыскивание расплавленного пластика в форму, которая охлаждается и затвердевает, придавая желаемую форму.
Основные этапы процесса литья пластмасс под давлением следующие:
- Дизайн пресс-формы. Первым шагом в этом процессе является проектирование пресс-формы, которая будет использоваться для создания желаемой детали. Форма обычно изготавливается из металла и должна быть подготовлена с учетом усадки при охлаждении и затвердевании пластика.
- Подготовка материала: пластиковый материал, используемый в процессе литья под давлением, имеет форму пеллет или гранул, которые необходимо расплавить и подготовить для впрыскивания в форму. Обычно это делается в бункере, где пластик нагревается до определенной температуры и плавится до жидкого состояния.
- Инъекция: после того, как пластик расплавится, он впрыскивается в форму с помощью специальной машины для литья под давлением. Машина оказывает давление на расплавленный пластик, заталкивая его в полость формы, где он принимает форму формы.
- Охлаждение и затвердевание: после того, как пластик впрыснут в форму, он может охладиться и затвердеть. Это может занять от нескольких секунд до нескольких минут, в зависимости от размера и сложности детали.
- Извлечение: когда пластик остынет и затвердеет, форма открывается, и деталь извлекается. Позиция может потребовать дополнительных отделочных работ, таких как обрезка или шлифование, чтобы удалить излишки пластика или шероховатые края.
Литье пластмасс под давлением — это точный и воспроизводимый процесс, что делает его идеальным для массового производства деталей и изделий неизменного качества. Он также очень универсален, так как может создавать изделия и изделия различных размеров, форм и сложности. Некоторые из наиболее распространенных применений литья пластмасс под давлением включают производство игрушек, потребительских товаров, автомобильных запчастей и медицинских устройств.
Процесс литья пластмасс под давлением: шаг за шагом
Литье пластмасс под давлением представляет собой сложный процесс, состоящий из нескольких этапов. Вот пошаговое руководство по процессу литья пластмасс под давлением:
- Проектирование пресс-формы. Первым шагом является проектирование пресс-формы, используемой для создания детали. Форма обычно изготавливается из стали или алюминия и должна быть подготовлена к усадке пластика при его охлаждении.
- Создание пресс-формы: После завершения проектирования пресс-формы она изготавливается с использованием программного обеспечения для автоматизированного проектирования (CAD) и оборудования для автоматизированного производства (CAM). Форма должна быть тщательно обработана и отполирована, чтобы обеспечить точность и качество конечного продукта.
- Выбор материала: пластиковый полимерный материал, используемый для процесса литья под давлением, должен выбираться на основе требований к детали, таких как ее прочность, гибкость, цвет и текстура.
- Подготовка материала: выбранный пластиковый материал затем нагревают до определенной температуры и расплавляют до жидкого состояния. Затем материал впрыскивается в бункер формовочной машины.
- Литье под давлением: расплавленный пластиковый материал впрыскивается в полость пресс-формы с помощью специальной машины для литья под давлением. Машина оказывает давление на пластиковый материал, заталкивая его в полость формы, где он принимает форму формы.
- Охлаждение: как только полость формы заполнена пластиком, он может охладиться и затвердеть. Время охлаждения определяется характеристиками пластика, размером и толщиной детали, а также температурой пресс-формы.
- Выталкивание: после затвердевания пластика форма открывается, и деталь выталкивается из формы с помощью штифтов выталкивателя.
- Финишная обработка: для извлеченной детали может потребоваться дополнительная финишная обработка, например обрезка, шлифовка или покраска, чтобы удалить излишки пластика или шероховатые края.
- Контроль качества: готовая деталь проходит тщательную проверку на соответствие требуемым спецификациям и стандартам качества.
Литье пластмасс под давлением может производить различные детали и изделия разных размеров, форм и сложности. Этот процесс широко используется в нескольких отраслях промышленности, включая автомобилестроение, медицину, производство потребительских товаров и электронику.
Типы пластика, используемые в литье под давлением
Для литья под давлением можно использовать многие виды пластика. Выбор пластикового материала будет зависеть от конкретных требований к изготавливаемому продукту или детали, таких как прочность, гибкость, долговечность и внешний вид. Вот некоторые из наиболее распространенных типов пластика, используемых в литье под давлением:
- Полиэтилен (ПЭ): ПЭ — это широко используемый пластиковый материал, известный своей прочностью и гибкостью. Он используется для производства различной продукции, в том числе упаковочных материалов, игрушек и медицинских изделий.
- Полипропилен (ПП): ПП — это легкий и прочный пластиковый материал, обычно используемый в автомобильной промышленности для изготовления внутренних деталей, таких как приборные панели и дверные панели. Он также производит упаковочные материалы, такие как контейнеры и бутылки.
- Поликарбонат (ПК): ПК — это твердый и прозрачный пластиковый материал, обычно используемый для производства электронных компонентов, таких как корпуса компьютеров и телефонов. Он также используется для линз фар и компонентов приборной панели в автомобильной промышленности.
- Акрилонитрил-бутадиен-стирол (АБС): АБС — универсальный пластик, известный своей прочностью, долговечностью и термостойкостью. Он обычно используется для производства автомобильных деталей, таких как приборные панели, расширители крыльев, игрушки и товары народного потребления.
- Полиамид (ПА): ПА, также известный как нейлон, представляет собой прочный и легкий пластиковый материал, который обычно используется в производстве автомобильных деталей, таких как крышки двигателя и системы впуска воздуха. Он также производит спортивный инвентарь, такой как лыжные ботинки и теннисные ракетки.
- Полистирол (ПС): ПС — это легкий и жесткий пластиковый материал, который обычно используется в производстве упаковочных материалов, таких как чашки, подносы и контейнеры для пищевых продуктов. Он также производит потребительские товары, такие как игрушки и электронные компоненты.
- Полиэтилентерефталат (ПЭТ): ПЭТ представляет собой прочный и прозрачный пластиковый материал, обычно используемый для производства упаковочных материалов, таких как бутылки и контейнеры. Он также используется в текстильной промышленности для производства волокон и тканей.
Это лишь некоторые из наиболее распространенных типов пластика, используемых в литье под давлением. Доступны многие другие типы пластиковых материалов, каждый из которых обладает уникальными свойствами и характеристиками. Выбор пластикового материала будет зависеть от конкретных требований к производимой детали или изделию.
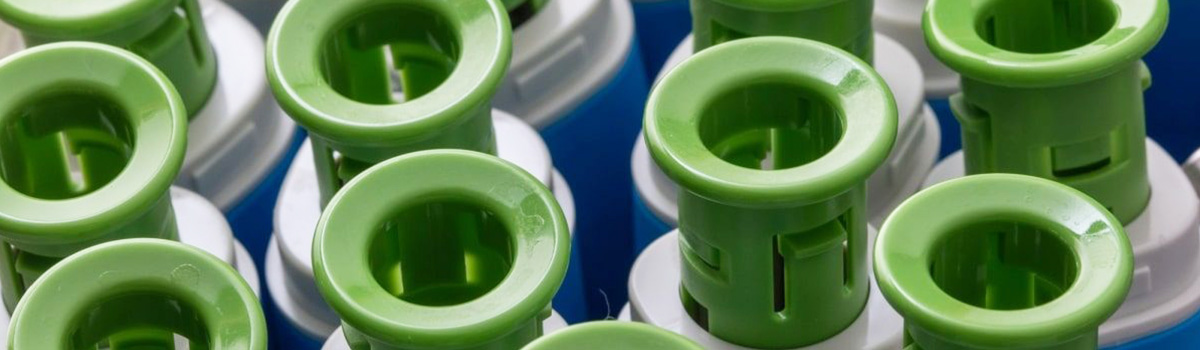
Типы термопластавтоматов
Машины для литья под давлением бывают различных типов и размеров, каждая из которых предназначена для удовлетворения конкретных производственных требований. Вот некоторые из наиболее распространенных типов машин для литья под давлением:
- Гидравлическая машина для литья под давлением: эта машина использует гидравлическую энергию для создания давления для впрыска пластика в форму. Гидравлические машины обычно используются для более важных деталей, требующих высокого усилия зажима.
- Электрическая машина для литья под давлением: электрические машины используют электродвигатели для питания блока впрыска и зажимного механизма. Они известны своей высокой точностью и энергоэффективностью, что делает их известными благодаря производству мелких и сложных деталей.
- Гибридная машина для литья под давлением: Гибридные машины сочетают в себе преимущества гидравлических и электрических устройств, используя как гидравлическую, так и электрическую энергию для создания необходимого давления и мощности. Гибридные машины предлагают хороший баланс скорости, точности и энергоэффективности.
- Вертикальная машина для литья под давлением: Вертикальные машины производят детали, которые требуют литья под давлением или литья под давлением. Они имеют вертикальный зажимной узел, обеспечивающий легкий доступ к пресс-форме, что делает их идеальными для создания небольших или сложных деталей.
- Двухтактная машина для литья под давлением: Двухтактные машины производят детали из разных материалов или цветов. Устройство имеет два узла впрыска, каждый из которых способен впрыскивать в пресс-форму инородный материал. Этот тип машин обычно используется для производства автомобильных деталей, таких как ручки и ручки.
- Многоэтапная машина для литья под давлением: Многоэтапные машины производят детали из более чем двух материалов или цветов. Устройство имеет несколько узлов впрыска, каждый из которых может вводить в форму различный материал. Этот тип машин обычно используется для производства потребительских товаров, таких как зубные щетки и бритвы.
- Полностью электрическая машина для литья под давлением: полностью электрические машины используют электродвигатели для питания узла впрыска, зажимного механизма и пресс-формы. Они известны своей высокой точностью, скоростью и энергоэффективностью, что делает их известными благодаря производству небольших высокоточных деталей.
Это лишь некоторые из наиболее распространенных типов машин для литья под давлением. Каждая машина имеет уникальные характеристики и преимущества, поэтому очень важно выбрать подходящее устройство для конкретных производственных требований.
Части машины для литья под давлением
Машины для литья под давлением имеют несколько частей, которые создают пластиковые детали из сырья. Вот критические компоненты машины для литья под давлением:
Бункер: Резервуар содержит сырьевой пластик перед его подачей в машину для литья под давлением. Материал обычно находится в форме гранул или порошка.
Ствол: Ствол представляет собой длинную цилиндрическую часть машины для литья под давлением, в которой находится шнек, расплавляющий и перемешивающий пластиковый материал.
Винт: Винт представляет собой вращающееся устройство внутри ствола, которое толкает пластиковый материал вперед и плавит его за счет трения и тепла.
Блок впрыска: блок впрыска включает в себя бункер, цилиндр и шнек и отвечает за плавление и впрыскивание пластика в форму.
Зажимной узел: Зажимной узел отвечает за надежное удержание формы и приложение необходимого давления во время процесса литья под давлением.
Форма: Форма — это инструмент, который создает форму и размер пластиковой детали. Форма обычно изготавливается из стали и состоит из двух половин, которые соединяются друг с другом.
Форсунка: Форсунка — это часть узла впрыска, которая соединяет машину для литья под давлением с пресс-формой. Расплавленный пластиковый материал впрыскивается через сопло в форму.
Система охлаждения: система охлаждения отвечает за охлаждение пластиковой детали после впрыска в форму. Это гарантирует, что деталь затвердеет и может быть извлечена из формы без повреждений.
Панель управления: Панель управления — это интерфейс, который позволяет оператору контролировать и регулировать параметры машины для литья под давлением, такие как температура, давление и время цикла.
Каждая из этих деталей играет решающую роль в процессе литья под давлением, и важно поддерживать и оптимизировать каждую деталь, чтобы обеспечить эффективное производство высококачественных деталей.
Инструменты для литья под давлением: проектирование и производство
Инструмент для литья под давлением относится к разработке и производству форм, используемых в машинах для литья под давлением для производства пластиковых деталей. Качество и эффективность пресс-форм напрямую влияют на качество и производительность процесса литья под давлением. Вот важные этапы проектирования и изготовления оснастки для литья под давлением:
Дизайн продукта. Первым шагом в разработке инструментов для литья под давлением является проектирование продукта, который будет производиться. Дизайн продукта включает в себя определение размера, формы и материала детали, а также любых конкретных характеристик или требований.
Дизайн пресс-формы: процесс проектирования пресс-формы начинается после завершения проектирования продукта. Разработчик пресс-формы определит наилучший тип пресс-формы, количество необходимых полостей, а также размер и форму пресс-формы.
Конструкция формы: Форма изготавливается на основе конструкции формы с использованием высококачественных материалов, таких как сталь или алюминий. Форма обычно состоит из двух половин, каждая из которых содержит одну или несколько полостей.
Сборка пресс-формы: после изготовления пресс-формы ее собирают и проверяют на точность и функциональность. Форма должна выдерживать давление и тепло в процессе литья под давлением.
Тестирование и проверка пресс-формы: после того, как пресс-форма собрана, она тестируется и проверяется, чтобы гарантировать, что она производит высококачественные детали, соответствующие спецификациям продукта. Форма может нуждаться в регулировке или модификации для улучшения ее производительности.
Техническое обслуживание пресс-формы. Регулярное техническое обслуживание и ремонт пресс-формы имеют решающее значение для обеспечения ее долговечности и производительности. Это включает чистку, смазку и замену изношенных или поврежденных деталей.
Инструменты для литья под давлением требуют точности и опыта для стабильного и эффективного производства высококачественных деталей. Следуя полному процессу проектирования и производства, производители могут изготавливать пресс-формы, отвечающие уникальным требованиям их продукции, и оптимизировать свои процессы литья под давлением.
Типы инструментов для литья под давлением
Литье под давлением является широко используемым производственным процессом для производства деталей в больших количествах. Он включает в себя впрыск расплавленного пластика в полость формы и позволяет ему остыть и затвердеть до желаемой формы. Инструмент для литья под давлением - это процесс создания форм, используемых в литье под давлением. Существует несколько типов инструментов для литья под давлением, каждый из которых имеет свои преимущества и недостатки.
- Двухпластинчатые пресс-формы Двухпластинчатые пресс-формы являются простейшим типом оснастки для литья под давлением. Они состоят из двух пластин, зажатых вместе, образующих полость пресс-формы. Расплавленный пластик впрыскивается в отверстие через вентиль, где ему дают остыть и затвердеть. Как только деталь создана, две пластины разделяются, и количество выбрасывается. Пресс-формы с двумя плитами обычно используются для изготовления деталей малого и среднего размера с простой геометрией.
- Трехпластинчатые пресс-формы Трехпластинчатые пресс-формы аналогичны двухпластинчатым пресс-формам, но имеют дополнительную пластину, известную как съемная пластина, которая отделяет формованную деталь от литниковой системы. Система желобов представляет собой сеть каналов, по которым расплавленный пластик поступает в полость пресс-формы. Трехпластинчатые пресс-формы используются для более крупных деталей и более сложной геометрии.
- Горячеканальные пресс-формы В горячеканальных пресс-формах расплавленный пластик впрыскивается непосредственно в полость пресс-формы через серию нагретых каналов, а не через вентиль. Это снижает потери материала в литниковой системе, что повышает эффективность процесса. Горячеканальные пресс-формы используются для крупносерийного производства сложных деталей.
- Семейные формы Семейные формы позволяют производить несколько деталей в одной форме. Они имеют различные полости, расположенные таким образом, что позволяют одновременно производить множество доменов. Семейные пресс-формы обычно используются для деталей малых и средних объемов.
- Формы-вкладыши Формы-вкладыши производят детали, для которых требуются металлические или пластиковые вставки. Вставки помещаются в полость формы перед заливкой расплавленного пластика. После того, как пластик остынет и затвердеет, деталь и вставка прочно соединяются. Формы-вкладыши используются для позиций, требующих прочности, долговечности или эстетической привлекательности.
- Многослойное формование Многослойное формование — это процесс, при котором одна деталь отливается поверх другой. Он часто используется для позиций, требующих мягкого прикосновения или улучшенного захвата. Многослойное формование включает в себя сначала установку подложки или базовой части, а затем формование поверх нее второго материала. Второй материал может представлять собой пластик другого типа, резиноподобный материал или термопластичный эластомер.
В заключение, выбор оснастки для литья под давлением зависит от типа изготавливаемой детали, требуемого объема производства и уровня сложности конструкции детали. Выбор правильного инструмента имеет важное значение для обеспечения эффективности и рентабельности процесса.
Руководство по проектированию литья под давлением
Литье под давлением является широко используемым производственным процессом для изготовления пластиковых деталей. Проектирование деталей для литья под давлением требует хорошего понимания процесса, материалов и рекомендаций по проектированию, которым необходимо следовать, чтобы гарантировать успешное изготовление деталей. Вот некоторые рекомендации по проектированию литья под давлением, о которых следует помнить:
Толщина стенки. Толщина стенки детали должна быть однородной и как можно более тонкой при сохранении требуемой прочности и функциональности. Это помогает сократить время охлаждения и время цикла, а также сводит к минимуму риск коробления и утяжек.
Ребра и бобышки Ребра и бобышки можно использовать для увеличения прочности и жесткости детали. Ребра должны составлять не более 60% номинальной толщины стенки, а выступы должны быть в 1.5 раза больше номинальной толщины стенки.
Угол уклона. Угол наклона не менее 1-2 градусов следует использовать на всех вертикальных поверхностях, чтобы облегчить выброс детали и предотвратить повреждение пресс-формы.
Скругления и радиусы Следует избегать острых углов и краев, чтобы предотвратить концентрацию напряжений, которые могут привести к растрескиванию и разрушению. Вместо этого скругления и радиусы должны распределять напряжение и повышать прочность детали.
Ворота и направляющие Расположение и конструкция литников и направляющих имеют решающее значение для достижения хорошего качества деталей. Входы должны быть как можно меньше в самом толстом месте детали. Бегуны должны быть сконструированы таким образом, чтобы свести к минимуму падение давления и максимизировать поток.
Чистота поверхности Чистота поверхности детали должна быть указана на основе требований приложения. Для видимых частей может потребоваться более высокое качество обработки поверхности, тогда как для скрытых частей может быть приемлемо более низкое качество поверхности.
Выбор материала Материал, выбранный для детали, должен подходить для литья под давлением и соответствовать требуемым механическим, термическим и химическим свойствам.
Вторичные операции в литье под давлением
Литье под давлением — это универсальный производственный процесс, используемый для производства различных пластиковых деталей. В дополнение к первичному процессу формования многие положения требуют дополнительных операций для достижения желаемой формы, отделки или функциональности. Вот некоторые повседневные второстепенные операции при литье под давлением:
- Обрезка – это удаление лишнего материала с формованной детали после того, как она была извлечена из формы. Обычно это делается с помощью обрезного пресса или станка с ЧПУ. Обрезка часто требуется для достижения окончательной формы и размера детали.
- Сварка объединяет две или более пластмассовых деталей с использованием тепла, давления или их комбинации. Это часто используется для создания более крупных или сложных элементов, которые невозможно изготовить в одной пресс-форме.
- Декорирование — это процесс добавления визуальных или функциональных элементов на поверхность формованной детали. Это может включать рисование, печать, маркировку или нанесение текстуры или узора.
- Сборка — это процесс соединения нескольких частей для создания законченного продукта. Это можно сделать с помощью крепежа, клея или других методов соединения.
- Литье с вставкой Литье с вставкой – это формование пластика вокруг предварительно сформированной металлической или пластиковой вставки. Это часто используется для создания деталей с высоким уровнем прочности или долговечности.
- Многослойное формование Многослойное формование — это процесс формования второго материала поверх предварительно отформованной детали. Это может добавить поверхность с мягким прикосновением, улучшить сцепление или создать двухцветную или многокомпонентную деталь.
- Покрытие наносит тонкий слой материала на поверхность детали для улучшения ее внешнего вида, долговечности или других свойств. Это может включать такие покрытия, как хром, никель или порошковые покрытия.
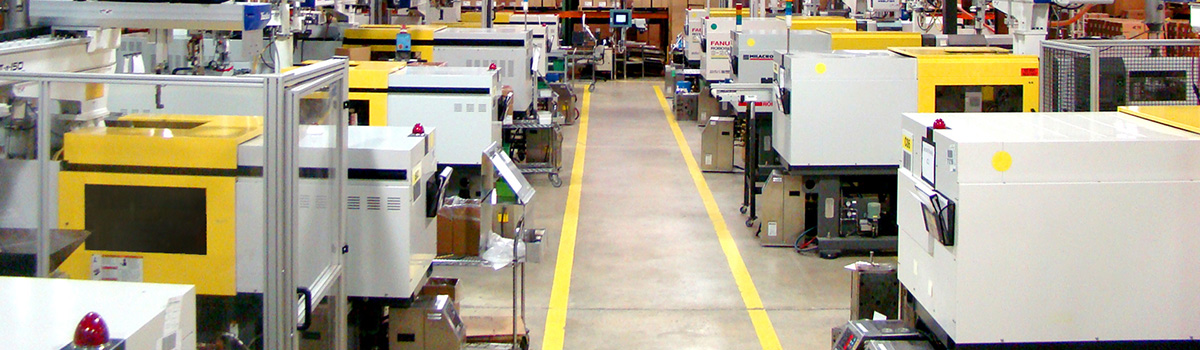
Преимущества литья пластмасс под давлением
Литье пластмасс под давлением — это широко используемый производственный процесс для изготовления пластиковых деталей с высокой точностью, стабильностью и качеством. Он включает в себя впрыскивание расплавленного пластика в полость формы и охлаждение и затвердевание. Вот некоторые преимущества литья пластмасс под давлением:
- Высокая эффективность и производительность Литье пластмасс под давлением — это высокоэффективный и автоматизированный процесс, позволяющий производить большие объемы деталей с высокой консистенцией и качеством. Благодаря передовым технологиям автоматизации время производственного цикла может быть сокращено до секунд, что позволяет производить большие объемы сложных и сложных деталей.
- Высокая точность и точность Литье под давлением повышает точность и точность изготовления сложных и сложных деталей. Машины с компьютерным управлением и передовое программное обеспечение обеспечивают жесткие допуски с высокой повторяемостью и точностью.
- Универсальность Литье под давлением — это универсальный процесс, с помощью которого можно производить широкий спектр пластиковых деталей различных размеров, форм и сложности. Этот процесс можно использовать для изготовления всего: от небольших деталей со сложными деталями до больших объемов со сложной геометрией.
- Гибкость материалов При литье под давлением можно использовать широкий спектр пластиковых материалов, включая термопласты, реактопласты и эластомеры. Это позволяет изготавливать детали с различными механическими, термическими и химическими свойствами.
- Производство с низким уровнем отходов Литье под давлением представляет собой производственный процесс с низким уровнем отходов, поскольку во время производства образуется минимальное количество отходов. Любой излишек материала можно легко переработать и повторно использовать в производстве, что делает производственный процесс экологически безопасным.
- Снижение трудозатрат Высокая степень автоматизации литья под давлением сводит к минимуму потребность в трудоемких процессах, значительно снижая трудозатраты. Это также снижает риск человеческой ошибки, повышая качество и согласованность конечного продукта.
- Сокращение операций постпроизводства При литье под давлением детали производятся с высокой точностью и стабильностью, что снижает потребность в операциях постпроизводства, таких как обрезка, сверление или фрезерование. Это сокращает время производства и стоимость конечного продукта.
- Стабильность и качество Литье под давлением позволяет получать детали с высоким уровнем стабильности и качества. Передовые технологии и оборудование с компьютерным управлением гарантируют, что каждая деталь будет идентична по форме, размеру и качеству.
- Гибкость конструкции Литье под давлением обеспечивает высокую степень гибкости конструкции, поскольку позволяет изготавливать детали со сложной геометрией, выточками и сложными деталями. Это позволит дизайнерам создавать изделия с уникальными формами и функциями, которые невозможно изготовить с использованием других производственных процессов.
- Экономичность для крупносерийного производства Литье под давлением — это экономичный процесс производства пластиковых деталей. Первоначальная стоимость оснастки может быть высокой, но стоимость одной детали снижается по мере увеличения объема производства. Это делает его идеальным процессом для производства больших количеств деталей.
Литье пластмасс под давлением имеет много преимуществ, что делает его популярным выбором для производства пластиковых деталей. Его высокая эффективность, точность, универсальность, гибкость материала, малое количество отходов производства, снижение затрат на рабочую силу, а также постоянство и качество делают его идеальным процессом для различных применений. Возможность производить сложные и сложные детали с высокой гибкостью конструкции и экономичностью для крупносерийного производства делает этот производственный процесс очень востребованным.
Недостатки литья пластмасс под давлением
Литье пластмасс под давлением — это широко используемый производственный процесс, который включает впрыск расплавленного пластика в полость пресс-формы для производства широкого спектра пластиковых деталей и изделий. Хотя литье пластмасс под давлением имеет множество преимуществ, у него есть и несколько недостатков. Вот некоторые из основных недостатков литья пластмасс под давлением:
- Высокие затраты на оснастку: стоимость разработки и изготовления формы для литья пластмасс под давлением может быть очень высокой. Это связано с тем, что пресс-форма должна быть изготовлена из высококачественных материалов и точно обработана для создания желаемой детали. Кроме того, стоимость проектирования и изготовления пресс-формы может быть непомерно высокой для мелкосерийного производства, что делает литье пластмасс под давлением менее экономичным для мелкосерийного производства.
- Длительное время выполнения: процесс проектирования и изготовления пресс-формы для литья пластмасс под давлением может занять много времени, что может привести к задержке производства пластиковых деталей. Это может быть особенно проблематично для предприятий, которым необходимо быстро реагировать на изменения рыночного спроса или быстро разрабатывать новые продукты.
- Ограниченная гибкость: после того, как пресс-форма спроектирована и изготовлена, проще и дешевле изменить конструкцию или модифицировать производственный процесс. Это может ограничить гибкость литья пластмасс под давлением и сделать его менее подходящим для производства нестандартных или единственных в своем роде продуктов.
- Экологические проблемы: литье пластмасс под давлением требует большого количества пластика, что может иметь негативные экологические последствия. Пластиковые отходы представляют собой серьезную экологическую проблему, и литье пластмасс под давлением может усугубить эту проблему. Кроме того, процесс производства пластмассовых изделий требует использования энергии и природных ресурсов, что может дополнительно воздействовать на окружающую среду.
- Высокий уровень брака: при литье пластмасс под давлением может образовываться значительный объем брака, утилизация или переработка которого может быть дорогостоящей. Кроме того, производство лома может увеличить общую стоимость производства и снизить эффективность производственного процесса.
- Ограниченные варианты материалов: литье пластмасс под давлением в основном используется для изготовления деталей и изделий из термопластичных материалов, которые имеют ограниченные свойства по сравнению с другими материалами, такими как металлы или керамика. Это может сделать литье пластмасс под давлением менее подходящим для приложений, требующих высокой прочности, термостойкости или других улучшенных свойств.
Ограничения литья пластмасс под давлением
Хотя литье пластмасс под давлением предлагает многочисленные преимущества, этот процесс также связан с определенными ограничениями. Вот некоторые ограничения литья пластмасс под давлением:
Высокая начальная стоимость оснастки: первоначальная стоимость проектирования и изготовления пресс-формы может быть увеличена. Форма должна быть точной и прочной, чтобы выдерживать повторяющийся процесс литья под давлением, а это может потребовать значительных первоначальных инвестиций, особенно для сложных или больших форм.
Время выполнения: время выполнения заказа на изготовление пресс-формы может быть значительным, от недель до месяцев, в зависимости от сложности и размера пресс-формы. Это может привести к задержке графика производства, особенно для срочных проектов.
Конструктивные ограничения: литье под давлением имеет определенные конструктивные ограничения, которые необходимо учитывать. Например, достижение одинаковой толщины стенки по всей детали имеет решающее значение для обеспечения надлежащего заполнения и охлаждения. Кроме того, на вертикальных поверхностях требуются углы наклона, чтобы обеспечить легкое извлечение из формы.
Ограничения по размеру детали: литье под давлением наиболее подходит для изготовления деталей малого и среднего размера. Для больших деталей может потребоваться специальное оборудование и более крупные формы, что увеличивает стоимость и сложность.
Выбор материала: Хотя литье под давлением позволяет использовать широкий спектр пластиковых материалов, выбор материала по-прежнему ограничен по сравнению с другими производственными процессами. Материалы с высокой температурой плавления или плохими характеристиками текучести могут не подходить для литья под давлением.
Отделка поверхности: в процессе литья под давлением на поверхности детали могут появиться видимые линии переплетения или линии разъема. Достижение высококачественной отделки поверхности может быть сложной задачей, и могут потребоваться другие методы, такие как полировка или покрытие.
Ограниченные поднутрения: поднутрения — это элементы или детали детали, препятствующие ее легкому извлечению из формы. Поднутрения могут усложнить процесс выталкивания и потребовать дополнительных элементов пресс-формы или дополнительных операций для достижения желаемой геометрии детали.
Ограниченные возможности ремонта: если пресс-форма повреждена или нуждается в модификации, ремонт или изменение существующей пресс-формы может быть дорогостоящим и трудоемким. Иногда может потребоваться изготовление совершенно новой пресс-формы, что приводит к дополнительным расходам и задержкам.
Несмотря на эти ограничения, литье пластмасс под давлением остается очень универсальным и широко используемым производственным процессом для изготовления пластиковых деталей. Внимательно учитывая эти ограничения на этапах проектирования и планирования производства, можно смягчить их влияние и эффективно использовать преимущества литья под давлением.
Применение литья пластмасс под давлением
Литье пластмасс под давлением — это универсальный производственный процесс, с помощью которого можно производить широкий спектр пластиковых деталей. Вот некоторые из областей применения литья пластмасс под давлением:
- Потребительские товары: литье под давлением широко используется для производства различных товаров, таких как игрушки, кухонная утварь и электроника. Этот процесс позволяет производить высококачественные детали со сложной геометрией и точными размерами, что делает его идеальным для изделий, требующих жестких допусков и сложных форм.
- Автомобильные детали: многие автомобильные пластиковые компоненты, такие как компоненты приборной панели, дверные ручки и освещение, производятся с использованием литья под давлением. Этот процесс обеспечивает большие объемы производства и стабильное качество, что делает его экономически эффективным вариантом для производителей автомобилей.
- Медицинские устройства: литье под давлением обычно используется для производства медицинских устройств, таких как шприцы, ингаляторы и диагностическое оборудование. Этот процесс позволяет производить детали с высокой точностью и согласованностью, обеспечивая качество и надежность устройств.
- Упаковка: литье под давлением широко используется для производства пластиковой упаковки, такой как контейнеры, крышки и колпачки. В процессе могут использоваться детали с одинаковыми размерами и высококачественной отделкой, что делает его идеальным для упаковки с привлекательным внешним видом и надежной посадкой.
- Аэрокосмическая промышленность и оборона: литье под давлением производит различные аэрокосмические и оборонные компоненты, такие как интерьеры самолетов, освещение и системы связи. В этом процессе могут использоваться детали из легких и прочных материалов, что делает их подходящими для приложений, требующих высокого отношения прочности к весу.
- Строительство: литье под давлением может производить различные строительные материалы, такие как пластиковая черепица, кровля и сайдинг. В этом процессе могут быть детали с одинаковыми размерами и высококачественной отделкой, что делает его привлекательным вариантом для строительных компаний.
- Спорт и отдых: литье под давлением широко используется в производстве спортивного инвентаря, такого как клюшки для гольфа, теннисные ракетки и компоненты для велосипедов. Этот процесс позволяет производить детали из легких материалов и с точной геометрией, обеспечивая производительность и долговечность оборудования.
В целом, литье пластмасс под давлением является универсальным и широко используемым производственным процессом, с помощью которого можно производить высококачественные пластмассовые детали для различных областей применения. Этот процесс может быть адаптирован для удовлетворения конкретных требований к конструкции и производству, что делает его привлекательным вариантом для производителей в различных отраслях.
Автомобильная промышленность и литье пластмасс под давлением
Автомобильная промышленность широко использует технологию литья пластмасс под давлением. Процесс литья пластмасс под давлением произвел революцию в производстве автомобильных деталей и компонентов, позволив изготавливать сложные формы с высокой точностью и аккуратностью. Вот некоторые из способов литья пластмасс под давлением в автомобильной промышленности:
- Детали интерьера: литье пластмасс под давлением создает множество внутренних факторов, включая компоненты приборной панели, дверные панели, элементы отделки и многое другое. Эти детали могут иметь замысловатую форму и текстуру и быть настроены в соответствии со стилем и функциональностью каждой модели автомобиля.
- Внешние детали: литье пластмасс под давлением также используется для изготовления различных элементов экстерьера, включая бамперы, решетки радиатора, боковые зеркала и многое другое. Эти детали могут быть спроектированы таким образом, чтобы выдерживать экстремальные погодные условия, и изготавливаются в различных цветах и с различными покрытиями.
- Компоненты под капотом: литье пластмасс под давлением позволяет производить многие детали под капотом, включая крышки двигателя, системы впуска воздуха и детали системы охлаждения. Эти компоненты требуют высокой термостойкости и химической стойкости, чего можно добиться с помощью термопластичных материалов.
- Электрические и электронные компоненты. Литье пластмасс под давлением позволяет производить различные электрические и электронные компоненты, включая разъемы, корпуса и датчики. Эти компоненты требуют высокой точности и надежности, которые могут быть достигнуты с точностью и постоянством литья пластмасс под давлением.
- Облегчение: литье пластмасс под давлением часто используется для производства легких деталей, которые помогают снизить общий вес автомобиля, повысить эффективность использования топлива и сократить выбросы. Облегчение также может улучшить управляемость и производительность автомобиля.
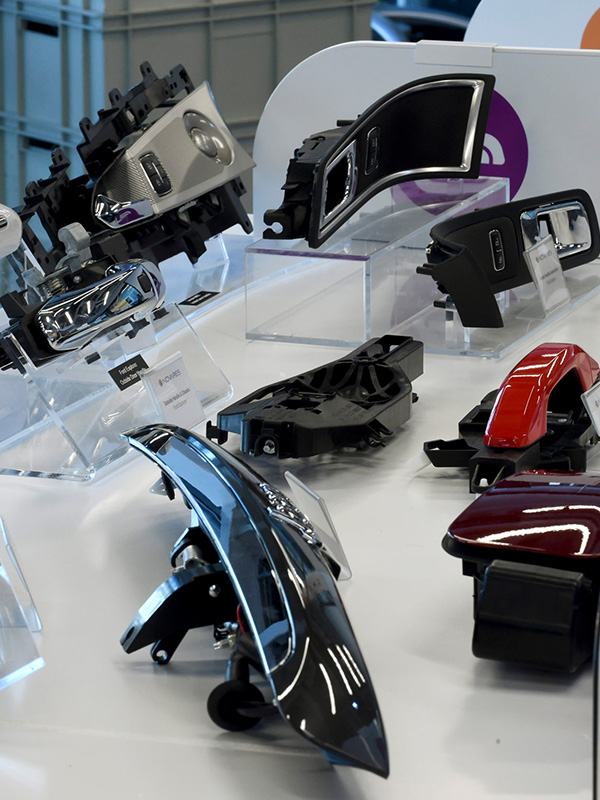
Медицинская промышленность и литье пластмасс под давлением
Литье пластмасс под давлением широко используется в медицинской промышленности для производства различных медицинских устройств и компонентов. Процесс литья пластмасс под давлением позволяет производить сложные формы с высокой точностью, что делает его идеальным методом производства для многих медицинских применений. Вот некоторые из способов литья пластмасс под давлением в медицинской промышленности:
- Медицинские устройства: литье пластмасс под давлением производит различные медицинские устройства, включая хирургические инструменты, диагностические инструменты, системы доставки лекарств и т. д. Эти устройства часто требуют высокой точности и аккуратности, и литье пластмасс под давлением может удовлетворить эти требования.
- Имплантаты: литье пластмасс под давлением также используется для производства различных имплантатов, включая замену суставов, зубные имплантаты и многое другое. Эти имплантаты могут быть разработаны в соответствии с анатомией пациента и изготовлены из биосовместимых материалов.
- Лабораторное оборудование: Литье пластмасс под давлением производит пипетки, микропланшеты и пробирки. Эти компоненты требуют высокой точности и точности для обеспечения надежных результатов.
- Упаковка: литье пластмасс под давлением используется для производства упаковки для медицинских устройств, включая стерильные барьерные системы и нестандартную упаковку для отдельных продуктов. Эти упаковочные решения могут помочь сохранить стерильность и целостность медицинского устройства.
- Одноразовые устройства: при литье пластмасс под давлением часто производятся одноразовые устройства, такие как шприцы, иглы и катетеры. Эти устройства могут производиться в больших объемах по низкой цене и могут помочь предотвратить распространение инфекций в медицинских учреждениях.
Потребительские товары и литье пластмасс под давлением
Литье пластмасс под давлением широко используется в производстве потребительских товаров благодаря своей универсальности, эффективности и экономичности. Процесс литья пластмасс под давлением позволяет производить сложные формы с высокой точностью, что делает его идеальным методом производства для многих потребительских применений. Вот некоторые из способов литья пластмасс под давлением в производстве потребительских товаров:
- Игрушки: литье пластмасс под давлением производит широкий спектр игрушек, от маленьких фигурок до больших игровых наборов. Этот процесс позволяет создавать сложные конструкции и детали, а также делать игрушки различных цветов и материалов.
- Товары для дома: литье пластмасс под давлением производит различные товары для дома, включая кухонную утварь, контейнеры для хранения и чистящие средства. Эти изделия могут быть прочными, легкими и простыми в использовании.
- Электроника: литье пластмасс под давлением производит множество электронных компонентов, включая корпуса компьютеров, чехлы для телефонов и зарядные устройства. Точность и точность процесса гарантируют, что эти компоненты изготовлены с высокой степенью согласованности и надежности.
- Средства личной гигиены: литье пластмасс под давлением производит уникальные средства по уходу, в том числе зубные щетки, бритвы и расчески. Эти продукты требуют высокой точности и точности для обеспечения простоты использования и безопасности.
- Автомобильные аксессуары: литье пластмасс под давлением производит ряд автомобильных аксессуаров, включая компоненты приборной панели, подстаканники и многое другое. Эти компоненты могут быть легкими, прочными и устойчивыми к износу при ежедневном использовании.
Экологические аспекты литья пластмасс под давлением
Литье пластмасс под давлением является широко используемым производственным процессом, но имеет значительные экологические последствия. Вот некоторые из экологических соображений при литье пластмасс под давлением:
- Выбор материала: выбор пластика, используемого при литье под давлением, может существенно повлиять на окружающую среду. Некоторые материалы являются биоразлагаемыми или перерабатываемыми, а другие нет. Использование биоразлагаемых или перерабатываемых материалов может помочь снизить воздействие литья пластмасс под давлением на окружающую среду.
- Потребление энергии: литье пластмасс под давлением требует значительных затрат энергии для плавления пластика и впрыскивания его в форму. Энергоэффективное оборудование и процессы, такие как электрические машины и замкнутые системы, могут снизить потребление энергии и воздействие на окружающую среду.
- Управление отходами: при литье пластмасс под давлением образуются отходы из-за избыточного материала, дефектных деталей и упаковки. Надлежащие методы обращения с отходами, такие как переработка и повторное использование отходов, могут помочь уменьшить воздействие литья пластмасс под давлением на окружающую среду.
- Использование химикатов: некоторые химикаты в литье пластмасс под давлением, такие как смазки для пресс-форм и очищающие растворители, могут нанести вред окружающей среде. Использование экологически чистых альтернатив или минимизация использования этих химикатов может помочь уменьшить воздействие на окружающую среду.
- Соображения, связанные с окончанием срока службы: пластиковые изделия, произведенные методом литья под давлением, часто попадают на свалки, на разложение которых могут уйти сотни лет. Разработка продуктов, пригодных для вторичной переработки или биоразложения, может снизить воздействие литья пластмасс под давлением на окружающую среду.
Будущее литья пластмасс под давлением
Будущее литья пластмасс под давлением выглядит многообещающим, поскольку ожидается, что достижения в области технологий и материалов сделают этот процесс еще более эффективным, рентабельным и устойчивым. Вот некоторые из тенденций и разработок, которые, вероятно, определят будущее литья пластмасс под давлением:
- Аддитивное производство. Аддитивное производство, также известное как 3D-печать, представляет собой новую технологию, которая потенциально может преобразовать литье пластмасс под давлением. Используя 3D-печать для создания форм, производители могут значительно сократить время и затраты, связанные с традиционными методами изготовления форм.
- Интеллектуальное производство. Ожидается, что интеллектуальное производство, которое включает в себя автоматизацию, анализ данных и машинное обучение, произведет революцию в литье пластмасс под давлением. Производители могут повысить эффективность, сократить количество отходов и повысить производительность, используя датчики и средства анализа данных для оптимизации процессов.
- Устойчивые материалы. Устойчивые материалы, такие как биопластик и переработанный пластик, становятся все более популярными в индустрии литья пластмасс под давлением. Эти материалы предлагают экологические преимущества и могут помочь производителям достичь целей устойчивого развития.
- Микроформование: микроформование, которое включает в себя изготовление мелких деталей с высокой точностью, становится все более важным в таких отраслях, как здравоохранение и электроника. Ожидается, что достижения в области технологий и материалов сделают микроформование более доступным и экономически эффективным.
- Индивидуализация: Поскольку потребители требуют более персонализированных продуктов, ожидается, что литье пластмасс под давлением станет более гибким и настраиваемым. Достижения в области технологий, такие как обратная связь в режиме реального времени и машинное обучение, позволят производителям быстро и эффективно производить продукцию на заказ.
Вывод:
Литье пластмасс под давлением — это очень универсальный и эффективный производственный процесс, который произвел революцию в производстве широкого спектра продуктов. От медицинских устройств до автомобильных компонентов, литье пластмасс под давлением предлагает многочисленные преимущества по сравнению с другими производственными процессами, включая высокую производительность, гибкость конструкции и рентабельность. Благодаря постоянному развитию технологий и материалов будущее литья пластмасс под давлением выглядит блестящим, и этот процесс, вероятно, будет играть еще более важную роль в обрабатывающей промышленности в ближайшие годы.