Литье термопластов под давлением
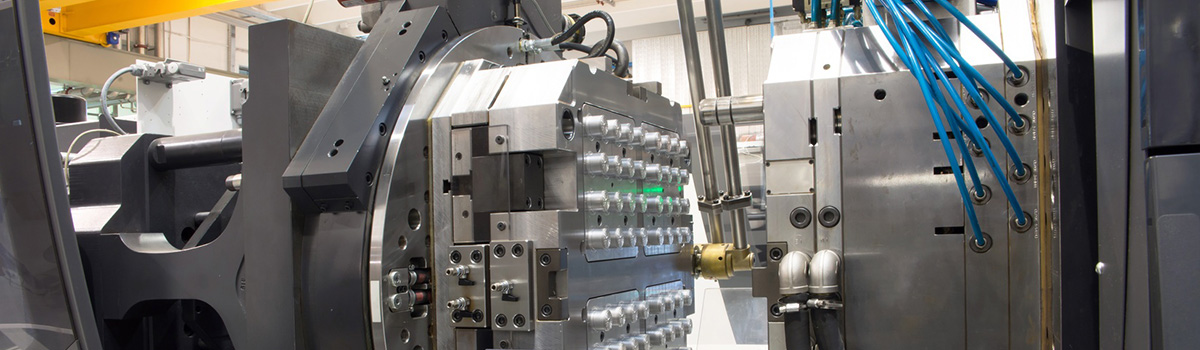
Литье термопластов под давлением — популярный производственный процесс, используемый для создания различных пластиковых деталей для различных отраслей промышленности. Этот процесс включает плавление пластиковых гранул и впрыскивание их в форму для получения трехмерной формы. Литье термопластов под давлением является высокоэффективным и экономичным способом производства больших объемов высококачественных пластиковых деталей с жесткими допусками. В этом подробном руководстве будут рассмотрены различные аспекты литья под давлением термопластов, включая его преимущества и недостатки, типы используемых термопластов, процесс литья под давлением, особенности конструкции и многое другое.
История литья термопластов под давлением
История литья термопластов под давлением насчитывает более века технологических достижений, разработок материалов и промышленного применения. От самого скромного процесса формования из целлулоида до современной сложной технологии литье под давлением продолжает оставаться жизненно важной производственной технологией, стимулирующей инновации и формирующей различные отрасли.
- Ранние разработки:Джон Уэсли Хаятт и его брат Исайя разработали первую практическую машину для литья под давлением, проследив истоки литья термопластов под давлением до конца 19 века. В 1872 году они запатентовали устройство, которое использовало поршень для впрыскивания целлулоида в полость формы, создавая твердые объекты. Этот прорыв заложил основу современного процесса литья под давлением.
- Улучшения в материалах:В начале 20 века появление новых синтетических полимеров открыло новые возможности для литья под давлением. Бакелит, фенольная смола, стал популярным материалом для формования из-за его превосходных электроизоляционных свойств. На протяжении 1930-х и 1940-х годов достижения в области химии полимеров привели к разработке других термопластов, таких как полистирол и полиэтилен, что еще больше расширило диапазон материалов, подходящих для литья под давлением.
- Промышленное внедрение: Широкое распространение литья термопластов под давлением началось в 1950-х годах, когда производители признали его экономичность и универсальность. Внедрение машин высокого давления позволило сократить время цикла и увеличить объемы производства. В результате появился разнообразный выбор продуктов как для личного, так и для промышленного использования. К ним относятся автомобильные компоненты, бытовая техника и игрушки.
- Технологические инновации:На протяжении десятилетий технология литья под давлением продолжала развиваться. В 1960-х годах появились машины с компьютерным управлением, позволяющие точно контролировать процесс формования. Внедрение горячеканальных систем в 1980-х годах уменьшило количество отходов и повысило эффективность за счет устранения необходимости в литниковых каналах и литниках. В последние годы достижения в области автоматизации, робототехники и 3D-печати произвели дальнейшую революцию в индустрии литья под давлением, позволив создавать сложные конструкции и сокращая время производства.
- Устойчивое развитие и переработка:В связи с растущими экологическими проблемами индустрия литья под давлением приняла меры по обеспечению устойчивости. Производители разработали термопласты на биологической основе и переработанные термопласты, что снижает зависимость от материалов на основе ископаемого топлива. Кроме того, усовершенствованные технологии переработки позволили перерабатывать бытовые и промышленные отходы, сводя к минимуму воздействие литья термопластов на окружающую среду.
- Будущие перспективы:Будущее литья термопластов под давлением выглядит многообещающе. В отрасли изучаются такие инновации, как микролитье под давлением для миниатюрных компонентов, методы многокомпонентного литья и многокомпонентного литья для сложных деталей, а также интеграция интеллектуальных технологий для мониторинга и оптимизации процессов. Кроме того, исследователи ожидают, что достижения в области биоразлагаемых материалов и аддитивного производства произведут революцию в этой области, сделав литье под давлением еще более устойчивым и универсальным.
Преимущества литья термопластов под давлением
Литье термопластов под давлением предлагает производителям многочисленные преимущества. Он обеспечивает гибкость дизайна, позволяя создавать сложные и замысловатые конструкции с различными функциями. Этот процесс экономически эффективен, сокращая отходы материалов и снижая удельные затраты. Литье термопластов под давлением поддерживает несколько материалов, обеспечивая универсальность для различных применений.
- Гибкость дизайна:Литье термопластов под давлением позволяет создавать замысловатые и сложные конструкции с такими особенностями, как подрезы, тонкие стенки и различная толщина, предоставляя дизайнерам огромную свободу.
- Эффективность затрат: Этот процесс является высокоэффективным, сокращая отходы материалов и снижая удельные затраты. Одновременное формование нескольких деталей и быстрые производственные циклы способствуют экономии средств.
- Универсальность материала: Литье под давлением термопластов поддерживает широкий спектр материалов, что позволяет производителям выбирать наиболее подходящий вариант для каждого применения, включая жесткие или гибкие, прозрачные или непрозрачные и химически стойкие материалы.
- Прочность и долговечность:Термопласты, полученные литьем под давлением, могут проявлять превосходные механические свойства, такие как высокая прочность, ударная вязкость и ударопрочность. Варианты армирования, такие как стекло или углеродное волокно, еще больше улучшают эти свойства.
- Консистенция и качество:Литье под давлением обеспечивает стабильное качество от детали к детали и точность размеров, обеспечивая жесткие допуски и надежность продукции. Этот процесс также обеспечивает гладкую и однородную поверхность, устраняя необходимость в дополнительных чистовых операциях.
- Масштабируемость и массовое производство:Литье под давлением масштабируется от малых до больших объемов, что делает его пригодным для массового производства. Создав пресс-форму, производители могут производить большое количество идентичных деталей с минимальными вариациями.
- Интеграция и сборка:Детали, полученные литьем под давлением, могут включать несколько компонентов в одну деталь, что снижает потребность в дополнительных процессах сборки. Эта интеграция повышает производительность продукта, сокращает время сборки и снижает затраты.
- Устойчивость:Индустрия литья под давлением все больше внимания уделяет вопросам устойчивого развития. Доступность биоматериалов и переработанных материалов позволяет производить экологически чистую продукцию. Эффективное использование материалов и возможность вторичной переработки термопластов способствуют более экологичному производственному процессу.
Эти преимущества сделали этот метод производства широко распространенным в различных отраслях промышленности, обеспечивая высококачественные, экономичные и экологически безопасные решения для сложных требований к продукту.
Недостатки литья термопластов под давлением
Хотя литье под давлением из термопластов имеет множество преимуществ, у него есть и несколько недостатков. Производители должны тщательно оценить эти факторы и сопоставить их преимущества, чтобы определить пригодность литья термопластов под давлением для их конкретных применений.
- Высокие начальные инвестиции: Создание предприятия по литью термопластов под давлением требует значительных первоначальных инвестиций в проектирование и изготовление пресс-форм, а также приобретение специализированного оборудования. Затраты, связанные с созданием пресс-форм и инструментов, могут быть значительными, особенно для сложных и замысловатых конструкций.
- Ограничения дизайна: Хотя литье термопластов под давлением обеспечивает гибкость дизайна, существуют определенные ограничения. Например, достижение одинаковой толщины стенок по всей детали может быть сложной задачей, что приводит к вариациям в распределении материала и потенциальным конструктивным недостаткам. Кроме того, наличие поднутрений или сложной геометрии может потребовать использования дополнительных функций пресс-формы или дополнительных операций, что увеличивает затраты и время производства.
- Длительные сроки выполнения:Процесс проектирования и изготовления пресс-форм для литья под давлением может занимать много времени, что приводит к увеличению времени разработки продукта. Процесс итерации проектирования, изготовление пресс-форм и тестирование могут значительно увеличить общий график производства, что может не подойти для проектов со сжатыми сроками.
- Ограничения выбора материала:Хотя литье термопластов под давлением поддерживает широкий спектр материалов, существуют определенные ограничения и ограничения. Некоторые материалы могут иметь особые требования к обработке или ограниченную доступность, что влияет на выбор конструкции и выбор материала для конкретного применения.
- Ограничения по размеру детали:Машины для литья под давлением имеют ограничения по размеру как с точки зрения физического размера устройства, так и размера форм, которые они могут вместить. Для производства крупных деталей может потребоваться специальное оборудование или альтернативные методы производства.
- Воздействие на окружающую среду:В то время как промышленность стремится к устойчивому развитию, в процессе литья под давлением термопластов по-прежнему образуются отходы, в том числе лом и литники. Надлежащая утилизация и переработка этих материалов необходимы для сведения к минимуму воздействия на окружающую среду.
- Сложность оптимизации процесса:Достижение оптимальных параметров процесса литья термопластов под давлением может быть сложным и длительным процессом. Производители должны тщательно контролировать и оптимизировать температуру, давление, скорость охлаждения и время цикла, чтобы обеспечить стабильное качество деталей и свести к минимуму дефекты.
Типы термопластов, используемых в литье под давлением
Это всего лишь несколько примеров термопластов, обычно используемых в литье под давлением. Каждый материал обладает уникальными свойствами, что делает его пригодным для конкретных применений в зависимости от прочности, гибкости, химической стойкости, прозрачности и стоимости. Производители должны учитывать эти свойства и требования при выборе подходящего термопластика для своих проектов литья под давлением.
- Полипропилен (ПП):Полипропилен — универсальный термопласт, широко используемый в литье под давлением. Он обладает отличной химической стойкостью, низкой плотностью и хорошей ударной вязкостью. PP (полипропилен) имеет широкое применение в упаковке, автомобильных компонентах, бытовой технике и медицинских устройствах.
- Полиэтилен (ПЭ):Полиэтилен является еще одним широко используемым термопластом в литье под давлением. Он доступен в различных формах, таких как полиэтилен высокой плотности (HDPE) и полиэтилен низкой плотности (LDPE). Полиэтилен обладает хорошей химической стойкостью, прочностью и гибкостью, что делает его пригодным для изготовления бутылок, контейнеров и труб.
- Полистирол (ПС):Полистирол — универсальный термопласт, известный своей прозрачностью, жесткостью и доступной ценой. Он находит широкое применение в упаковке, потребительских товарах и одноразовых продуктах. PS (полистирол) допускает быструю обработку и обеспечивает хорошую размерную стабильность, но может быть хрупким и восприимчивым к растрескиванию под воздействием окружающей среды.
- Акрилонитрилбутадиенстирол (АБС): ABS — популярный термопластик, известный своей превосходной ударопрочностью и долговечностью. Он сочетает в себе свойства акрилонитрила, бутадиена и стирола для создания универсального материала, подходящего для автомобильных деталей, электронных корпусов и игрушек.
- Поливинилхлорид (ПВХ): ПВХ — это широко используемый термопласт, известный своей превосходной химической стойкостью, долговечностью и низкой стоимостью. Он может быть жестким или гибким в зависимости от состава и используемых добавок. ПВХ (поливинилхлорид) находит широкое применение в строительстве, электроизоляции, медицинских изделиях и упаковке.
- Поликарбонат (ПК): Поликарбонат — это прозрачный термопласт с необычайной ударопрочностью и высокой термостойкостью. Он находит широкое применение в приложениях, требующих оптической четкости, таких как автомобильные компоненты, защитные каски и электронные дисплеи.
- Нейлон (полиамид):Нейлон — прочный и долговечный термопласт, известный своими превосходными механическими свойствами и химической стойкостью. Он находит широкое применение в приложениях, требующих высокой прочности, таких как автомобильные детали, промышленные компоненты и товары народного потребления.
- Полиэтилентерефталат (ПЭТ):ПЭТ является популярным термопластом для производства бутылок, контейнеров и упаковочных материалов. Он обладает хорошей прозрачностью, химической стойкостью и барьерными свойствами, что делает его пригодным для пищевых продуктов и напитков.
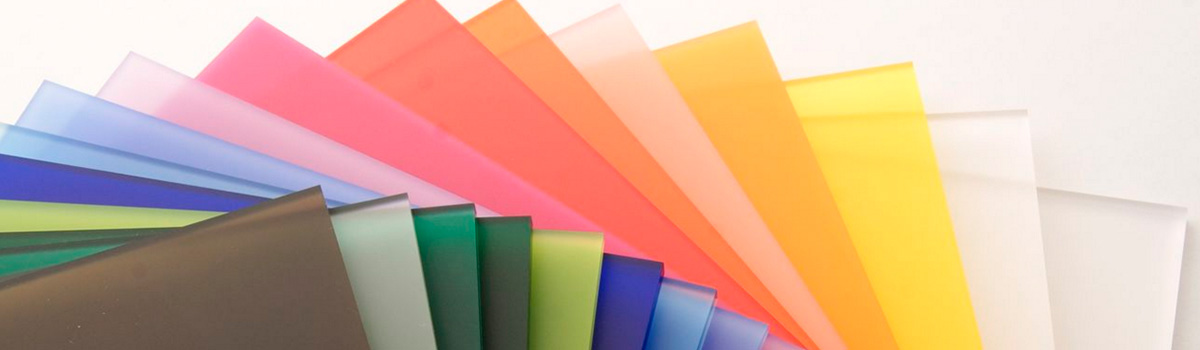
Свойства термопластов, используемых в литье под давлением
Эти свойства термопластов играют решающую роль в определении их пригодности для конкретных применений литья под давлением. Производители должны тщательно учитывать эти свойства и выбирать подходящий термопласт на основе желаемых характеристик, условий окружающей среды и требований к стоимости.
- Механические свойства:Термопласты, используемые в литье под давлением, могут проявлять различные механические свойства, включая прочность на растяжение, ударопрочность и прочность на изгиб. Эти свойства определяют способность материала выдерживать приложенные усилия и его общую долговечность в различных областях применения.
- Химическая устойчивость:Многие термопласты, используемые в литье под давлением, обладают замечательной стойкостью к химическим веществам, растворителям и маслам. Это свойство имеет решающее значение для применений, связанных с воздействием агрессивных сред или агрессивных веществ.
- Термическая стабильность:Термическая стабильность термопластов относится к их способности выдерживать повышенные температуры без существенной деградации. Некоторые термопласты обладают превосходной термостойкостью, что позволяет им сохранять свои механические свойства даже при высоких температурах.
- Электрические свойства:Термопласты, используемые в литье под давлением, могут иметь определенные электрические свойства, включая электрическую изоляцию, проводимость или диэлектрическую прочность. Эти свойства важны для приложений в электротехнической и электронной промышленности, где материалы должны обеспечивать надежные электрические характеристики.
- Прозрачность и ясность:Некоторые термопласты, такие как поликарбонат и ПЭТ, обеспечивают превосходную прозрачность и четкость, что делает их подходящими для приложений, требующих оптических свойств. Производители обычно используют эти материалы в таких продуктах, как прозрачные окна, линзы и дисплеи.
- Гибкость и прочность: Гибкость и ударная вязкость являются важными свойствами термопластов, используемых в приложениях, требующих ударопрочности и долговечности. Некоторые термопласты, такие как АБС и нейлон, обладают превосходной прочностью, что позволяет им выдерживать многократные удары без разрушения.
- Стабильность размеров:Размерная стабильность относится к способности термопластика сохранять свою форму и размер в различных условиях, включая изменения температуры. Материалы с хорошей размерной стабильностью обеспечивают постоянство размеров деталей, сводя к минимуму риск коробления или деформации.
- Химическая совместимость:Химическая совместимость термопластов относится к их способности сопротивляться разложению или взаимодействию с различными химическими веществами, включая кислоты, щелочи и растворители. Для обеспечения оптимальной производительности очень важно выбрать термопластик, способный противостоять специфической химической среде, с которой он столкнется при предполагаемом применении.
- Плотность: Термопласты имеют различную толщину, что может повлиять на их вес и общие свойства деталей. Материалы низкой плотности, такие как полиэтилен, предлагают легкие решения, а материалы высокой плотности, такие как полипропилен, обеспечивают дополнительную прочность и жесткость.
Процесс литья под давлением: шаг за шагом
Процесс литья под давлением следует этим этапам, обеспечивая эффективное и точное производство высококачественных термопластичных деталей. Каждый шаг требует тщательного контроля и мониторинга, чтобы обеспечить согласованные размеры деталей, свойства материалов и общее качество.
- Дизайн и изготовление пресс-форм: Первым шагом в процессе литья под давлением является проектирование и изготовление пресс-формы. Производители должны создать точную и подробную конструкцию пресс-формы для достижения желаемых характеристик детали. Затем производители изготавливают пресс-форму с использованием различных технологий, таких как ЧПУ или электроэрозионная обработка (EDM).
- Подготовка материала: Следующий шаг – подготовка после того, как форма будет готова. Термопластичные пеллеты или гранулы выбираются в зависимости от желаемых свойств материала и расплавляются в бункере. Затем операторы подают материал в цилиндр машины для литья под давлением, где он плавится и гомогенизируется.
- Раствор для инъекций:На этапе впрыска операторы впрыскивают расплавленный термопласт в полость пресс-формы под высоким давлением. Блок впрыска машины проталкивает расплавленный материал через сопло в форму. Материал заполняет полость формы, принимая форму желаемой детали.
- Охлаждение и затвердевание:После заполнения формы операторы позволяют расплавленному пластику остыть и затвердеть. Охлаждение имеет решающее значение для достижения стабильности размеров и правильного формирования детали. Операторы могут контролировать процесс охлаждения, циркулируя охлаждающую жидкость по каналам внутри пресс-формы или используя охлаждающие пластины.
- Открытие пресс-формы и выброс:Операторы открывают форму и извлекают деталь из полости формы после затвердевания пластика. Система выталкивания внутри машины использует штифты, выталкивающие пластины или воздушные потоки для удаления области из формы. После этого форма готова к следующему циклу впрыска.
- Постобработка: После извлечения деталь может подвергаться операциям постобработки, таким как обрезка, удаление заусенцев или обработка поверхности. Эти шаги помогают удалить лишний материал, сгладить шероховатости и улучшить окончательный вид детали.
- Проверка качества: Последний шаг включает в себя проверку качества отлитых деталей и обеспечение их соответствия указанным требованиям. Для проверки качества и целостности детали можно использовать различные методы контроля качества, включая измерение размеров, визуальный осмотр и функциональное тестирование.
- Переработка и повторное использование материалов:Любые излишки или отходы материала, образующиеся во время литья под давлением, могут быть переработаны и использованы повторно. Сокращение использования новых термопластичных материалов помогает свести к минимуму количество отходов и повысить экологичность.
Оборудование, используемое в литье под давлением
Эти компоненты оборудования облегчают процесс литья под давлением, от плавления и впрыска термопластичного материала до формования, охлаждения и выталкивания готовой детали. Надлежащая эксплуатация и техническое обслуживание этих компонентов оборудования имеют решающее значение для достижения эффективного и высококачественного производства литья под давлением.
- Литьевая машина:Основное оборудование в литье под давлением отвечает за плавление термопластичного материала, впрыскивание его в форму и управление процессом.
- Плесень: Форма, специально разработанная для создания желаемой формы и характеристик пластиковой детали, состоит из двух половин: полости и сердцевины. Операторы устанавливают его на узел зажима машины для литья под давлением.
- Хоппер:Контейнер, который содержит термопластический материал в виде гранул или гранул и подает его в цилиндр машины для литья под давлением для плавления и впрыскивания.
- Ствол и винт: Ствол, цилиндрическая камера, плавит и гомогенизирует термопластический материал, когда внутри него вращается шнек для расплавления, смешивания и стандартизации материала.
- Системы отопления и охлаждения:Машины для литья под давлением имеют нагревательные элементы, такие как электрические нагреватели или нагреватели, использующие горячее масло, для повышения температуры цилиндра и системы охлаждения, такие как циркуляция воды или масла, для охлаждения формы и затвердевания пластиковой детали.
- Эжекторная система:Удаляет отформованную деталь из полости формы после затвердевания, обычно используя выталкивающие штифты, пластины или потоки воздуха во время открытия формы.
- Система управления:Отслеживает и контролирует различные параметры процесса литья под давлением, позволяя операторам устанавливать и регулировать такие параметры, как скорость впрыска, температура, давление и время охлаждения.
Термопластавтоматы: типы и характеристики
Каждый тип термопластавтоматов имеет свои характеристики и преимущества, что позволяет производителям выбрать наиболее подходящее устройство для своих конкретных производственных требований.
- Гидравлические литьевые машины: Эти машины используют гидравлические системы для создания необходимого давления для впрыска расплавленного пластика в форму. Они известны своим высоким усилием зажима, точным контролем и универсальностью при работе с различными термопластами. Гидравлические машины подходят для крупносерийного производства и могут работать со сложными формами.
- Электрические термопластавтоматы:В электрических машинах используются электрические серводвигатели для работы машины, включая системы впрыска, зажима и выталкивания. Они обеспечивают точное управление, энергоэффективность и меньшее время отклика, чем гидравлические машины. Электрические машины идеально подходят для прецизионного литья, требующего высокой повторяемости и точности.
- Гибридные литьевые машины:Гибридные машины сочетают в себе преимущества как гидравлических, так и электрических устройств. В них используется комбинация гидравлических и электрических сервосистем для достижения высокой точности, энергоэффективности и экономичности. Гибридные машины подходят для широкого спектра применений, обеспечивая баланс между производительностью и эксплуатационными расходами.
- Машины для литья под давлением с двумя плитами: Двухплитные машины имеют уникальную конструкцию с двумя отдельными пластинами для зажима пресс-формы. Эта конструкция обеспечивает повышенную стабильность, улучшенную синхронизацию пресс-форм и позволяет использовать пресс-формы большего размера и более высокие силы зажима. Двухплитные станки подходят для крупных и сложных деталей, требующих точной формовки.
- Многокомпонентные литьевые машины:Производители проектируют эти машины для производства деталей из нескольких материалов или цветов за один цикл формования. Они имеют различные узлы впрыска и пресс-формы, что позволяет одновременно вводить различные материалы. Многокомпонентные станки обеспечивают гибкость и эффективность при производстве сложных деталей с различными характеристиками.
- Машины для микролитья под давлением:Машины для микролитья под давлением, специально разработанные для производства небольших и точных деталей, обеспечивают невероятно высокую точность и аккуратность. Они могут производить сложные детали с жесткими допусками и минимальными отходами материала. Электроника, медицинские устройства и микрооптика обычно используют машины для микролитья под давлением.
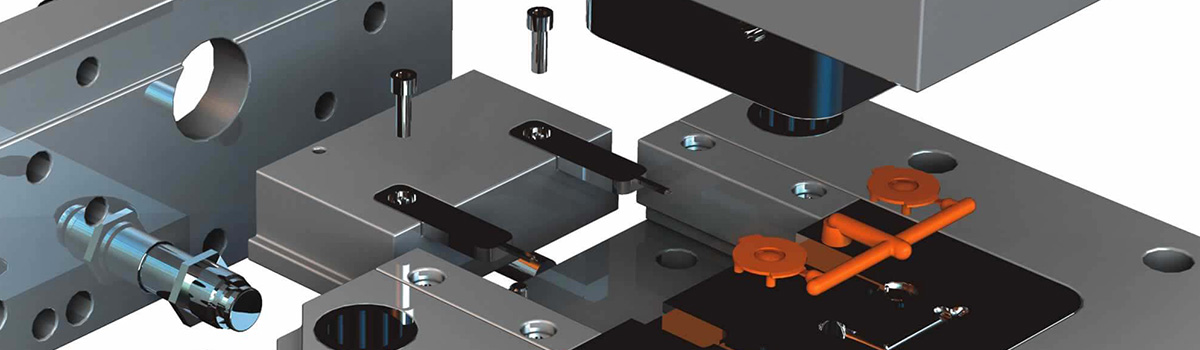
Рекомендации по проектированию пресс-форм для литья под давлением
Тщательное рассмотрение конструкции формы имеет важное значение для успешного производства литья под давлением.
- Дизайн детали:Конструкция пресс-формы должна соответствовать конкретным требованиям детали, включая ее форму, размеры и функциональные характеристики. Производители должны надлежащим образом учитывать углы уклона, толщину стенок, поднутрения и любые необходимые элементы, чтобы обеспечить простоту выталкивания и качество детали.
- Материал прессформы: Выбор материала пресс-формы имеет решающее значение для достижения долговечности, стабильности размеров и термостойкости. Обычные материалы пресс-форм включают стальные сплавы, алюминиевые сплавы и инструментальные стали. Выбор материала зависит от таких факторов, как объем производства, сложность детали и ожидаемый срок службы инструмента.
- Система охлаждения:Эффективное охлаждение необходимо для правильного затвердевания детали и минимизации времени цикла. Конструкция пресс-формы должна включать охлаждающие каналы или стратегически расположенные вставки для обеспечения равномерного охлаждения пресс-формы. Надлежащее охлаждение снижает риск коробления, усадки и дефектов деталей.
- Прокачка:Адекватная вентиляция необходима для выхода воздуха и газов во время процесса впрыска. Недостаточная вентиляция может привести к газоуловителям, следам прогара или неполному заполнению деталей. Производители могут добиться вентиляции, включив в конструкцию пресс-формы вентиляционные канавки, штифты или другие механизмы.
- Система выброса:Конструкция пресс-формы должна включать эффективную систему выталкивания для безопасного и эффективного извлечения формованной детали из полости пресс-формы. Система выброса может состоять из выталкивающих штифтов, втулок или других механизмов, стратегически расположенных так, чтобы не мешать функционированию или критическим функциям.
- Дизайн ворот:Ворота - это место, где расплавленный пластик входит в полость формы. Конструкция затвора должна обеспечивать надлежащее заполнение деталей, минимизировать линии потока и предотвращать преждевременное замерзание материала. Стандартные конструкции затворов включают краевые затворы, туннельные затворы и горячеканальные системы, в зависимости от требований к деталям и свойств материала.
- Линия разъема:Конструкция пресс-формы должна определять подходящую линию разъема, то есть линию, по которой две половины пресс-формы сходятся вместе. Правильное размещение линии разъема обеспечивает минимальное несовпадение заусенцев и линий разъема и облегчает эффективную сборку пресс-формы.
- Техническое обслуживание и ремонтопригодность пресс-формы: Производители должны учитывать простоту обслуживания, ремонта и обслуживания пресс-форм. Компоненты пресс-формы должны быть легко доступны для очистки, осмотра и замены. Включение таких функций, как быстросменные вставки или модульная конструкция пресс-формы, может повысить удобство обслуживания пресс-формы.
Материалы пресс-форм, используемые в литье под давлением
Сотрудничество со специалистами по материалам для пресс-форм и учет конкретных потребностей применения для литья может помочь определить наиболее подходящий материал для достижения оптимальных характеристик пресс-формы и качества деталей.
- Стальные сплавы: Стальные сплавы, такие как инструментальные стали (например, P20, H13) и нержавеющие стали, обычно используются для форм для литья под давлением благодаря их превосходной прочности, термостойкости и износостойкости. Эти материалы могут выдерживать высокие температуры и давление в процессе литья под давлением и обеспечивают хорошую размерную стабильность для производства высококачественных деталей.
- Алюминиевые сплавы:Алюминиевые сплавы, такие как 7075 и 6061, легкие и обладают хорошей теплопроводностью, что делает их подходящими для пресс-форм, требующих эффективного охлаждения. Производители часто используют алюминиевые формы для прототипирования, мелкосерийного производства или приложений, где снижение веса имеет решающее значение. Однако алюминиевые формы могут иметь меньшую долговечность по сравнению со стальными сплавами.
- Медные сплавы:Медные сплавы, такие как бериллиевая медь, обладают высокой теплопроводностью и хорошей обрабатываемостью. Они находят применение в пресс-формах, требующих отличной теплопередачи для эффективного охлаждения. Медные сплавы могут помочь сократить время цикла за счет быстрого рассеивания тепла от формованной детали, что приводит к более быстрому затвердеванию.
- Инструментальные стали:Инструментальные стали, включая H13, S7 и D2, предназначены для высокопроизводительного инструмента. Эти стали сочетают в себе высокую прочность, твердость и износостойкость. Инструментальные стали подходят для пресс-форм с большими объемами производства, абразивными материалами или сложными условиями формования.
- Никелевые сплавы:Никелевые сплавы, такие как Inconel и Hastelloy, известны своей исключительной коррозионной стойкостью, жаропрочностью и термической стабильностью. Производители используют эти сплавы в пресс-формах, которые работают с коррозионно-активными материалами или требуют устойчивости к экстремальным температурам и агрессивным средам формования.
- Композитные материалы:Композитные материалы, такие как армированные пластмассы или композиты с металлическими вставками, иногда используются для специальных формованных изделий. Эти материалы предлагают баланс свойств, таких как высокая прочность, термическая стабильность и малый вес. Композитные формы могут быть экономически эффективными альтернативами для конкретных производственных требований.
Типы литьевых форм
Литье под давлением является универсальным и широко используемым процессом производства пластиковых деталей.
- Двухпластинчатая форма:Двухпластинчатая пресс-форма является наиболее распространенным типом пресс-формы для литья под давлением. Он состоит из двух пластин, пластины с полостью и пластины сердечника, которые разделяются, чтобы обеспечить выброс формованной детали. Пластина с полостью содержит сторону формы с полостью, а пластина с сердечником содержит сторону с сердечником. Изготовители используют двухпластинчатые пресс-формы для изготовления широкого спектра деталей из-за их относительно простой конструкции.
- Трехпластинчатая форма:Трехпластинчатая пресс-форма является усовершенствованной версией двухпластинчатой пресс-формы. Он включает в себя дополнительную пластину, бегунок или литниковую пластину. Пластина направляющей создает отдельный канал для литника, направляющих и литника, что упрощает удаление формованной детали. Производители обычно используют пресс-формы с тремя пластинами для деталей со сложными системами литников или когда желательно избежать следов литника на изделии.
- Горячеканальная пресс-форма:Система желобов и литников нагревается в горячеканальных формах, что устраняет необходимость затвердевания и повторного плавления материала во время каждого цикла. Горячеканальная система состоит из обогреваемых коллекторов и форсунок, которые поддерживают расплавленное состояние пластика. Горячеканальные пресс-формы обладают такими преимуществами, как сокращение времени цикла, сокращение отходов материала и улучшение качества деталей за счет минимизации остатков литника.
- Холодная пресс-форма: Холодноканальные пресс-формы имеют традиционную систему желобов и литников, в которой расплавленный пластик протекает через холодные желоба, которые затвердевают с каждым циклом. Впоследствии операторы удаляют затвердевшие желоба, что приводит к отходам материала. Производители обычно используют сложные литейные формы для небольших объемов производства или когда затраты на материалы менее важны из-за их более простой конструкции.
- Вставьте форму:Формы-вкладыши включают металлические или пластиковые вставки в полость формы во время литья под давлением. Вставки могут быть предварительно помещены в форму или вставлены с помощью автоматизированных процессов. Эта форма позволяет интегрировать дополнительные компоненты или усиливающие элементы в формованную деталь, повышая ее функциональность или прочность.
- Формовка: Многослойное формование включает формование одного материала поверх другого, обычно склеивание жесткой пластиковой подложки с более мягким эластомером или термопластом. Этот процесс позволяет создавать детали из нескольких материалов или текстур в одной форме, обеспечивая улучшенное сцепление, амортизацию или эстетические характеристики.
Факторы, влияющие на стоимость литья под давлением
Учет этих факторов может помочь производителям оценить и оптимизировать стоимость литья под давлением, обеспечив баланс между качеством, эффективностью и рентабельностью для конкретных производственных требований.
- Сложность детали:Сложность конструкции детали играет значительную роль в определении стоимости литья под давлением. Сложная геометрия, подрезы, тонкие стенки или сложные элементы могут потребовать дополнительных инструментов, специальных форм или более длительных циклов, что увеличивает общую стоимость производства.
- Выбор материала:Выбор термопластичного материала влияет на стоимость литья под давлением. Различные материалы имеют разные цены за килограмм, и такие факторы, как доступность материала, свойства и требования к обработке, могут влиять на общую стоимость материала.
- Инструменты и дизайн пресс-форм: Первоначальные затраты на оснастку и проектирование пресс-форм являются значительными в затратах на литье под давлением. Такие факторы, как сложность пресс-формы, количество полостей, размер пресс-формы и материал пресс-формы, влияют на затраты на изготовление инструментов и пресс-форм. Более сложные формы или формы, требующие расширенных функций, могут увеличить первоначальные инвестиции.
- Объем производства: Объем производства напрямую влияет на стоимость детали при литье под давлением. Более высокие книги часто приводят к экономии за счет масштаба, снижая стоимость каждой детали. И наоборот, при малосерийном производстве может взиматься более высокая плата из-за наладки, инструментов и отходов материалов.
- Время цикла: Время цикла, включающее этапы охлаждения и выталкивания, влияет на производительность и общую стоимость. Более длительное время цикла приводит к снижению производительности и потенциально более высоким ценам. Оптимизация конструкции пресс-формы, системы охлаждения и параметров процесса может минимизировать время цикла и повысить эффективность.
- Требования к качеству:Строгие требования к качеству или специальные сертификаты могут повлиять на стоимость литья под давлением. Для соблюдения точных допусков, требований к чистоте поверхности или дополнительных испытаний могут потребоваться другие ресурсы, процессы или проверки, что увеличивает общую стоимость.
- Второстепенные операции:Если формованные детали требуют операций последующей обработки, таких как сборка, покраска или дополнительные этапы отделки, эти операции могут увеличить общую стоимость литья под давлением.
- Поставщик и местоположение:Выбор поставщика оборудования для литья под давлением и его местонахождение могут повлиять на затраты. Затраты на рабочую силу, накладные расходы, логистику и транспортные расходы варьируются в зависимости от местоположения поставщика, что влияет на общую стоимость производства.
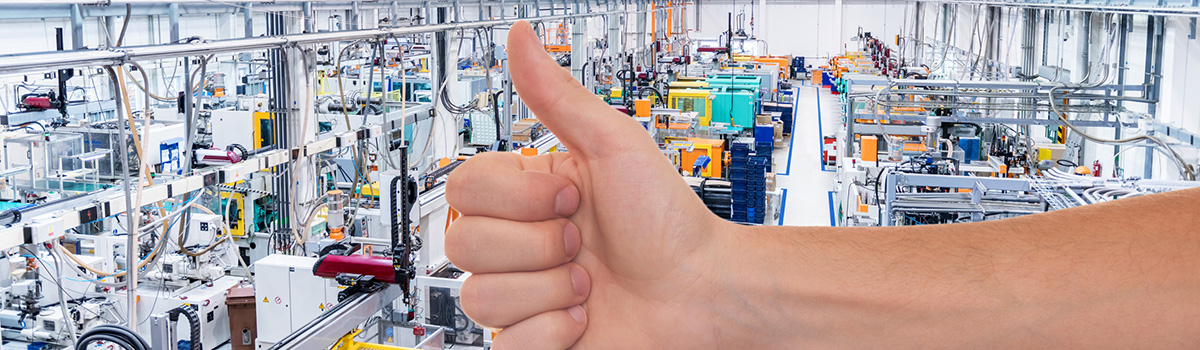
Контроль качества в литье под давлением
Внедрение надежных мер контроля качества на протяжении всего процесса литья под давлением помогает выявлять и устранять потенциальные дефекты, отклонения или несоответствия, обеспечивая производство высококачественных деталей, соответствующих спецификациям и требованиям заказчика.
- Мониторинг процесса: Непрерывный мониторинг ключевых параметров процесса, таких как температура расплава, давление впрыска, время охлаждения и время цикла, обеспечивает согласованность и повторяемость при производстве деталей. Мониторинг в режиме реального времени и автоматизированные системы могут обнаруживать изменения или отклонения от заданных параметров, что позволяет своевременно вносить коррективы и поддерживать стабильность процесса.
- Осмотр и измерение:Регулярный осмотр и измерение формованных деталей необходимы для проверки точности размеров, качества деталей и соблюдения спецификаций. Наши услуги охватывают ряд методов контроля качества, таких как измерение размеров, анализ качества поверхности, визуальный осмотр и выполнение функциональных испытаний. Для точной оценки используются различные методы контроля, такие как координатно-измерительные машины (КИМ) и системы оптического и визуального контроля.
- Статистический контроль процессов (SPC): SPC включает в себя сбор и анализ данных процесса для мониторинга и контроля качества литья под давлением. Статистические методы, такие как контрольные карты и анализ возможностей процесса, помогают выявлять тенденции, выявлять изменения процесса и обеспечивать, чтобы процесс оставался в заданных контрольных пределах. SPC позволяет заблаговременно выявлять проблемы и облегчает оптимизацию процессов.
- Материальные испытания: Тестирование сырья, такого как термопласты, добавки и красители, гарантирует их качество и пригодность для литья под давлением. Испытания материалов могут включать анализ показателя текучести расплава (MFI), механических свойств, тепловых характеристик и состава материала. Проверка качества материала помогает предотвратить дефекты и несоответствия формованных деталей.
- Техническое обслуживание и осмотр инструментов:Надлежащее техническое обслуживание и регулярный осмотр пресс-форм имеют решающее значение для обеспечения качества литья под давлением. Регулярная очистка, смазка и оценка компонентов пресс-формы помогают предотвратить износ, повреждение или деградацию, которые могут повлиять на качество детали. Своевременный ремонт или замена изношенных или поврежденных компонентов пресс-формы имеет важное значение для поддержания стабильной производительности формования.
- Документация и отслеживаемость:Ведение исчерпывающей документации и записей об отслеживаемости имеет важное значение для контроля качества в литье под давлением. Крайне важно записывать параметры процесса, результаты проверки, информацию о материалах и любые изменения или корректировки, сделанные во время производства. Надлежащая документация позволяет отслеживать детали, облегчает анализ первопричин и обеспечивает постоянство качества.
- Обучение и развитие навыков: Предоставление надлежащих программ обучения и повышения квалификации для операторов, техников и персонала по контролю качества улучшает их понимание процессов литья под давлением, требований к качеству и методов контроля. Хорошо обученный персонал может обнаруживать дефекты, устранять неполадки и эффективно принимать корректирующие меры, обеспечивая высокое качество продукции.
Общие дефекты литья под давлением и как их избежать
Регулярный осмотр, мониторинг и анализ процессов литья под давлением, а также надлежащее техническое обслуживание и регулировка оборудования и пресс-форм могут помочь в выявлении и устранении этих распространенных дефектов.
- Следы раковины:Утяжины — это углубления или углубления на поверхности формованной детали, вызванные неравномерным охлаждением или усадкой. Следует учитывать правильное расположение и конструкцию ворот, оптимальную конструкцию системы охлаждения и равномерное распределение толщины стенок, чтобы избежать утяжек. Увеличение давления впрыска или регулировка времени охлаждения также могут помочь свести к минимуму утяжины.
- Деформация:Коробление относится к деформации или изгибу формованной детали после выталкивания из-за неравномерного охлаждения или остаточных напряжений. Поддержание одинаковой толщины стенок, использование надлежащих охлаждающих каналов и обеспечение сбалансированного заполнения и уплотнения пресс-формы имеют решающее значение для предотвращения коробления. Оптимизация температуры пресс-формы, использование соответствующих углов наклона, а также контроль температуры материала и скорости впрыска могут помочь свести к минимуму коробление.
- Flash:Вспышка возникает, когда избыточный материал стекает в линию разъема формы, что приводит к тонким нежелательным выступам или лишнему материалу на готовой детали. Можно эффективно предотвратить облое, обеспечив правильную конструкцию пресс-формы, в том числе применяя соответствующее усилие зажима, точное выравнивание и используя соответствующие методы вентиляции. Оптимизация параметров процесса, таких как давление впрыска, температура и продолжительность цикла, уменьшает вспышку.
- Короткий выстрел:Быстрый выстрел происходит, когда впрыскиваемый материал не заполняет полость формы, что приводит к получению незавершенной детали. Правильный выбор материала, обеспечение соответствующей температуры расплава и вязкости, а также поддержание соответствующего давления и времени впрыска необходимы для того, чтобы избежать коротких фотографий. Кроме того, проверка конструкции пресс-формы на наличие достаточного размера желоба и литника, а также надлежащей вентиляции может помочь предотвратить быстрое впрыскивание.
- Линии сварки:Линии сварки возникают, когда два или более фронта потока расплавленного материала встречаются и затвердевают, что приводит к появлению видимой линии или метки на поверхности детали. Хорошая конструкция литников и направляющих, оптимальная температура расплава, скорость впрыска, а также регулировка потока материала и геометрии детали позволяют свести к минимуму линии сварки. Анализ течения литейной формы и оптимизация размещения литников также могут помочь предотвратить или смягчить линии сварки.
- Следы ожогов:Следы ожогов — это обесцвечивание или черные пятна на поверхности формованной детали, вызванные чрезмерным нагревом или перегревом материала. Избегание экстремальных температур расплава, использование соответствующих охлаждающих каналов и оптимизация времени цикла могут помочь предотвратить прижоги. Адекватная вентиляция, правильная конструкция литника и контроль температуры пресс-формы также способствуют минимизации следов пригара.
Послеформовочные операции: отделка и сборка
После литья под давлением многие формованные детали могут потребовать дополнительных операций по отделке и сборке для получения желаемого конечного продукта. Эти постформовочные операции могут включать:
- Обрезка:Удалите лишний материал или заусенцы вокруг формованной детали с помощью инструментов для обрезки или резки.
- Обработка поверхности:Улучшение внешнего вида или функциональности поверхности детали с помощью различных методов, таких как покраска, покрытие или текстурирование.
- Сборка:Соединение нескольких формованных деталей или добавление компонентов, таких как застежки, вставки или этикетки, для завершения конечного продукта.
- Тестирование:Проверка качества и функциональности деталей с помощью различных методов тестирования, таких как анализ размеров, тестирование свойств материалов или тестирование производительности.
- Упаковка и доставка:Надлежащая упаковка и маркировка готовой продукции для отгрузки клиентам или конечным пользователям.
Выбор операций после формования зависит от конкретного применения и желаемых характеристик конечного продукта. Тесное сотрудничество между специалистами по литью под давлением, специалистами по отделке и сборке и заказчиком имеет решающее значение для достижения желаемого абсолютного качества и функциональности продукта. Надлежащее планирование и интеграция постформовочных операций в производственный процесс может помочь обеспечить эффективное производство и своевременную поставку высококачественной продукции.
Литье под давлением по сравнению с другими процессами производства пластмасс
Каждый процесс производства пластмассы имеет свои преимущества и ограничения, что делает их пригодными для различных применений.
- Литье под давлением: Литье под давлением является очень универсальным и широко используемым производственным процессом для изготовления пластиковых деталей. Он предлагает такие преимущества, как высокая эффективность производства, точное копирование деталей и возможность создавать сложные геометрические формы. Литье под давлением подходит для крупносерийного производства и позволяет использовать широкий спектр термопластичных материалов. Он обеспечивает превосходную точность размеров и чистоту поверхности, что делает его идеальным для различных отраслей промышленности, таких как автомобилестроение, производство потребительских товаров и медицинского оборудования.
- Выдувное формование: Выдувное формование — это процесс, используемый в основном для производства полых пластиковых деталей, таких как бутылки, контейнеры и автомобильные компоненты. Он включает в себя плавление пластика и надувание его в полость формы, создавая желаемую форму. Выдувное формование подходит для крупносерийного производства и позволяет производить большие и легкие детали с одинаковой толщиной стенок. Однако он ограничен с точки зрения сложности деталей и выбора материала по сравнению с литьем под давлением.
- Термоформование:Термоформование — это процесс, используемый для производства пластиковых деталей путем нагрева листа термопласта и придания ему формы с помощью пресс-форм или вакуумного формования. Он находит широкое применение в упаковке, одноразовых продуктах и крупногабаритных продуктах, таких как лотки и крышки. Термоформование обеспечивает рентабельное производство крупных деталей и позволяет быстро создавать прототипы. Однако у него есть ограничения в отношении сложности деталей, выбора материала и точности размеров по сравнению с литьем под давлением.
- Экструзия:Экструзия — это непрерывный процесс производства пластиковых профилей, листов, труб и пленок. Он включает в себя плавление пластиковой смолы и продавливание ее через матрицу для создания желаемой формы. Экструзия подходит для производства длинных непрерывных отрезков пластиковых изделий с постоянным поперечным сечением. Хотя экструзия обеспечивает высокую производительность и экономичность, она имеет ограничения с точки зрения сложной геометрии деталей и точного контроля размеров по сравнению с литьем под давлением.
- Компрессионное формование:Компрессионное формование включает в себя помещение предварительно отмеренного количества термореактивного материала в нагретую полость формы и сжатие его под высоким давлением до отверждения. Он находит широкое применение в производстве деталей с высокой прочностью и стабильностью размеров, таких как автомобильные компоненты и электрическая изоляция. Компрессионное формование обеспечивает хорошую консистенцию деталей, высокую эффективность производства и возможность использования широкого спектра материалов. Однако он ограничен с точки зрения сложности деталей и времени цикла по сравнению с литьем под давлением.
Применение литья термопластов под давлением
В различных отраслях промышленности широко используется литье термопластов под давлением из-за его универсальности, эффективности и экономичности. Некоторые из применений литья термопластов под давлением включают:
- Автоматизированная индустрия: Автомобильная промышленность широко использует литье термопластов под давлением для производства различных компонентов, включая внутреннюю и внешнюю отделку, приборные панели, дверные панели, бамперы и электрические разъемы. Этот процесс позволяет точно воспроизводить детали сложной геометрии и использовать легкие материалы, повышая эффективность использования топлива и гибкость конструкции.
- Потребительские товары:Литье под давлением находит широкое применение в производстве потребительских товаров, таких как бытовая техника, электронные устройства, упаковочные контейнеры и игрушки. Этот процесс обеспечивает массовое производство прочных, высококачественных изделий с постоянными размерами и обработкой поверхности. Это также позволяет использовать параметры настройки и быстрые итерации продукта.
- Медицинское оборудование:Литье под давлением играет решающую роль в медицинской промышленности для производства широкого спектра устройств, включая шприцы, хирургические инструменты, имплантируемые компоненты и системы доставки лекарств. Этот процесс обеспечивает производство стерильных, точных и биосовместимых деталей, отвечающих строгим нормативным требованиям сектора здравоохранения.
- Электроника и электротехническая промышленность:Электронная промышленность использует литье под давлением для производства электрических разъемов, корпусов, переключателей и других компонентов. Этот процесс обеспечивает высокую точность размеров, отличное качество поверхности и возможность включения таких функций, как литье под давлением и литье под давлением, что позволяет эффективно производить сложные электронные сборки.
- Упаковочная промышленность:Различные отрасли промышленности, включая продукты питания и напитки, фармацевтику и средства личной гигиены, обычно используют литье под давлением для производства пластиковых упаковочных контейнеров, крышек, крышек и бутылок. Этот процесс позволяет создавать легкие, прочные и эстетически привлекательные упаковочные решения с эффективными производственными циклами.
- Аэрокосмическая промышленность:В аэрокосмической отрасли литье под давлением используется для производства легких и высокопроизводительных компонентов, таких как воздуховоды, кронштейны, внутренние панели и конструкционные детали. Этот процесс позволяет использовать передовые материалы и детали сложной геометрии, что способствует снижению веса и повышению эффективности использования топлива.
Воздействие литья термопластов под давлением на окружающую среду
Литье термопластов под давлением является популярным производственным процессом из-за его многочисленных преимуществ, но также важно учитывать его воздействие на окружающую среду. Вот несколько моментов, которые следует учитывать:
- Материальная эффективность:Литье термопластов под давлением повышает эффективность материалов за счет минимизации отходов. В процессе используется точный контроль количества материала, впрыскиваемого в форму, что снижает потребность в избыточном материале. Производители также могут использовать методы повторной шлифовки и переработки для повторного использования лома или бракованных деталей, что еще больше сокращает отходы материала.
- Потребление энергии:Производители разрабатывают машины для литья под давлением, чтобы они были энергоэффективными, а современные модели включают передовые технологии, такие как серводвигатели и приводы с регулируемой скоростью. Эти функции оптимизируют использование энергии за счет снижения энергопотребления во время формования, что приводит к снижению энергопотребления и уменьшению воздействия на окружающую среду.
- Управление отходами:Сводя к минимуму отходы материалов, производители должны применять надлежащие методы управления отходами для обработки остатков материалов, литников или направляющих. Производители могут разработать программы утилизации для сбора и повторного использования пластиковых отходов, образующихся при литье под давлением, тем самым сокращая количество отходов, отправляемых на свалки.
- Снижение выбросов: При литье под давлением термопластов выбросы обычно ниже, чем при других производственных процессах. Производители могут сократить выбросы за счет использования экологически чистых материалов, внедрения энергоэффективного оборудования и использования передовых систем выхлопа и фильтрации для улавливания любых выбрасываемых выбросов.
- Экологичный выбор материалов:Выбор термопластичных материалов может существенно повлиять на экологическую устойчивость литья под давлением. Выбор биоразлагаемых пластиков или пластмасс на биологической основе, а также переработанных или перерабатываемых материалов может помочь уменьшить общий экологический след процесса.
Рассмотрение жизненного цикла: Учет всего жизненного цикла формованного изделия необходим для оценки его воздействия на окружающую среду. На этапах проектирования и выбора материала производители должны учитывать такие факторы, как долговечность детали, возможность ее вторичной переработки и возможность утилизации или повторного использования по окончании срока службы.
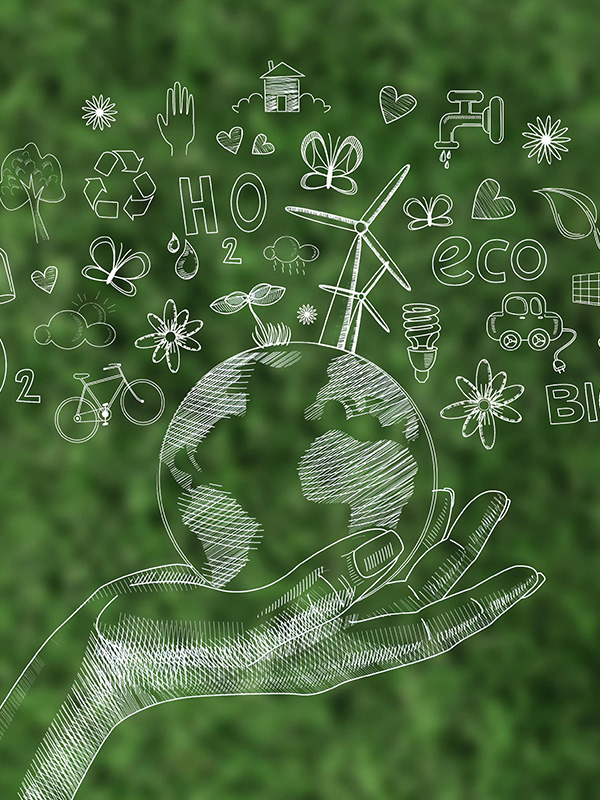
Будущее литья термопластов под давлением
Будущее литья термопластов под давлением выглядит многообещающе благодаря постоянному развитию технологий и увеличению спроса на высококачественные прецизионные детали в различных отраслях промышленности. Некоторые из ключевых событий, ожидаемых в ближайшие годы, включают:
- Более широкое использование автоматизации и робототехники для повышения эффективности и снижения затрат.
- Усилия сосредоточены на разработке новых материалов и процессов для улучшения характеристик деталей и создания новых приложений.
- Это растущее внедрение устойчивых методов, таких как использование переработанных материалов и оптимизация энергопотребления, для снижения воздействия литья под давлением на окружающую среду.
- Более тесная интеграция цифровых технологий, таких как 3D-печать и программное обеспечение для моделирования, для улучшения процессов проектирования и производства.
Мировой рынок литья под давлением расширяется, особенно в странах с развивающейся экономикой, что обусловлено растущим спросом на пластмассовые изделия в различных отраслях.
Выбор правильного партнера по литью под давлением
Выбор правильного партнера по литью под давлением имеет решающее значение для успеха вашего проекта. Потратьте время, чтобы оценить несколько вариантов, посетить объекты и принять участие в тщательных обсуждениях, чтобы обеспечить совместимое и долгосрочное партнерство.
- Компетенция и опыт:Ищите партнера по литью под давлением с обширными знаниями и опытом в отрасли. Они должны иметь проверенный опыт предоставления высококачественных продуктов и решений клиентам в различных секторах. Учитывайте их понимание различных материалов, конструкций пресс-форм и производственных процессов.
- Производственные возможности: Оцените производственные возможности партнера по литью под давлением. Убедитесь, что у них есть хорошо оборудованный объект с современным оборудованием и технологиями для выполнения требований вашего проекта. Примите во внимание их производственные мощности, способность обрабатывать детали различных размеров и сложности, а также способность соответствовать вашим желаемым объемам производства и срокам.
- Гарантия Качества:Качество имеет первостепенное значение в литье под давлением. Оцените системы контроля качества и сертификации потенциального партнера. Ищите партнеров, которые соблюдают строгие стандарты качества, имеют надежные процессы проверки и проводят всестороннее тестирование для обеспечения качества и согласованности деталей.
- Проектно-инженерная поддержка:Надежный партнер по литью под давлением должен предложить проектную и инженерную поддержку, чтобы оптимизировать конструкцию вашей детали для обеспечения технологичности. У них должны быть опытные инженеры, которые могут внести ценный вклад в выбор материалов, проектирование пресс-форм и оптимизацию процессов для повышения качества и эффективности деталей.
- Конкурентоспособность по стоимости:Хотя стоимость не должна быть единственным определяющим фактором, важно оценить ценообразование и ценовую конкурентоспособность партнера по литью под давлением. Запросите подробные расценки и рассмотрите стоимость инструментов, стоимость материалов, затраты на рабочую силу и любые дополнительные услуги, которые они предоставляют.
- Общение и сотрудничество:Эффективное общение и сотрудничество необходимы для успешного партнерства. Убедитесь, что партнер по литью под давлением имеет хорошие каналы связи, отвечает на ваши запросы и может предоставлять регулярные обновления проекта. Совместный подход поможет обеспечить соответствие вашим требованиям и оперативное решение любых проблем.
- Отзывы и отзывы клиентов:Ищите рекомендации клиентов или читайте обзоры/отзывы, чтобы получить представление об опыте других клиентов с партнером по литью под давлением. Получение этой информации может помочь определить их надежность, оперативность и общий уровень удовлетворенности клиентов.
Заключение
Литье термопластов под давлением является универсальным и экономичным методом изготовления пластиковых деталей в больших количествах. Его способность производить сложные формы с высокой точностью и постоянством стала популярным выбором для различных отраслей промышленности, включая автомобилестроение, медицину, электронику и товары народного потребления. Понимая различные аспекты литья термопластов под давлением, включая его преимущества, недостатки и особенности конструкции, вы можете принимать обоснованные решения о выборе подходящего партнера по литью под давлением для нужд вашего бизнеса.