Что такое литье пластмасс под давлением
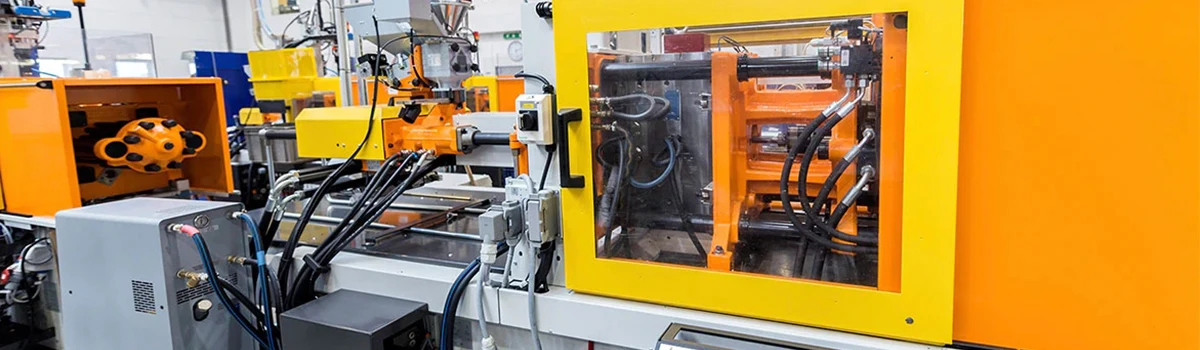
Литье термопластов под давлением — это метод изготовления крупногабаритных деталей из пластиковых материалов. Благодаря своей надежности и гибкости в вариантах дизайна, литье под давлением используется во многих отраслях, в том числе: упаковка, бытовая техника и электроника, автомобилестроение, медицина и многие другие.
Литье под давлением является одним из наиболее широко используемых производственных процессов в мире. Термопласты — это полимеры, которые размягчаются и текут при нагревании и затвердевают при охлаждении.
Приложения
Литье под давлением — наиболее распространенный современный метод изготовления пластиковых деталей; он идеально подходит для производства больших объемов одного и того же объекта. Литье под давлением используется для создания многих вещей, включая катушки с проволокой, упаковку, крышки для бутылок, автомобильные детали и компоненты, игровые приставки, карманные расчески, музыкальные инструменты, стулья и небольшие столы, контейнеры для хранения, механические детали и многие другие изделия из пластика.
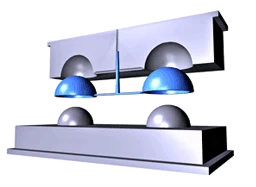
Дизайн пресс-формы
После того, как продукт разработан в программном обеспечении, таком как пакет CAD, формы создаются из металла, обычно из стали или алюминия, и прецизионно обрабатываются, чтобы сформировать элементы желаемой детали. Пресс-форма состоит из двух основных компонентов: пресс-формы для литья под давлением (пластина А) и пресс-формы для эжектора (пластина В). Пластмассовая смола поступает в форму через литник или литник и течет в полость формы через каналы или направляющие, которые врезаны в поверхности пластин A и B.
Процесс литья под давлением
При формовании термопластов обычно гранулированное сырье подается через бункер в нагретую бочку с возвратно-поступательным движением шнека. Шнек подает сырье вперед через обратный клапан, где оно собирается в передней части шнека в объем, известный как дробь.
Впрыск – это количество смолы, необходимое для заполнения литника, направляющей и полостей пресс-формы. Когда достаточное количество материала собрано, материал под высоким давлением и скоростью вдавливается в полость, формирующую деталь.
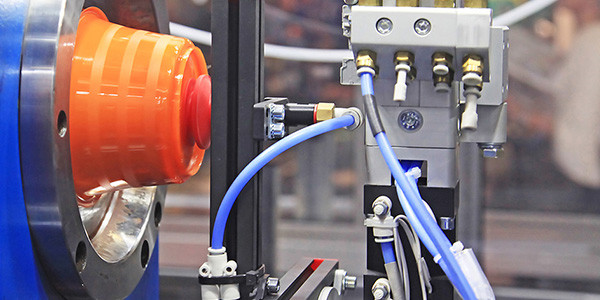
Как работает литье под давлением?
После того, как пластик заполнил форму, включая ее литники, направляющие, ворота и т. д., форму поддерживают при заданной температуре, чтобы обеспечить равномерное затвердевание материала в форме детали. Удерживающее давление поддерживается во время охлаждения, чтобы остановить обратный поток в ствол и уменьшить эффект усадки. В этот момент в бункер добавляются пластиковые гранулы в ожидании следующего цикла (или выстрела). При охлаждении плита открывается и позволяет вытолкнуть готовую деталь, а винт снова оттягивается назад, позволяя материалу попасть в цилиндр и начать процесс заново.
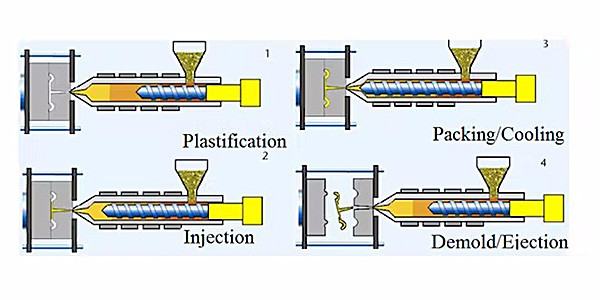
Цикл литья под давлением представляет собой непрерывный процесс: закрытие формы, подача/нагрев пластиковых гранул, их давление в форме, охлаждение до получения твердой детали, извлечение детали и повторное закрытие формы. Эта система позволяет быстро производить пластиковые детали, и за рабочий день можно изготовить до 10,000 XNUMX пластиковых деталей в зависимости от конструкции, размера и материала.
Цикл литья под давлением
Цикл литья под давлением очень короткий, обычно от 2 секунд до 2 минут. Есть несколько этапов:
1. Зажим
Перед введением материала в форму две половины формы надежно закрываются зажимным устройством. Зажимной узел с гидравлическим приводом сталкивает половинки пресс-формы вместе и прилагает достаточную силу, чтобы удерживать пресс-форму закрытой во время впрыска материала.
2. Инъекция
При закрытой форме полимерная дробь впрыскивается в полость формы.
3. охлаждение
Когда полость заполнена, прикладывается удерживающее давление, которое позволяет большему количеству полимера попасть в полость, чтобы компенсировать усадку пластика при его охлаждении. Тем временем винт поворачивается и подает очередной выстрел на передний винт. Это заставляет винт втягиваться, когда готовится следующий выстрел.
4. Выброс
Когда деталь достаточно остынет, форма открывается, деталь выталкивается, и цикл начинается снова.
Преимущества
1. Быстрое производство; 2. Гибкость дизайна; 3.Точность; 4.Низкие затраты на оплату труда; 5. Низкий уровень отходов