さまざまな方法でのプラスチック射出成形: 他の方法よりも射出
さまざまな方法でのプラスチック成形: 他の方法よりも射出成形
プラスチック材料の製造では、硬化して望ましい形状を維持しながら、プラスチックの塊の境界を定めるさまざまなタイプの型が使用されます。これらの金型は、金型を開閉するプレスに取り付けられており、必要に応じて大きな圧力が加えられ、外部手段による金型への負荷が容易になります。
プラスチック材料は圧力下で金型内に保持され、十分に硬化するため、取り外した後もその形状が保持されます。
金型の加熱には蒸気、熱水、油、電気が使用されます。特定の作業で使用される暖房の種類は、利用可能な手段と作業自体の性質によって決まります。
場合によっては、金型の温度を一定に保つために、水やその他の冷媒を循環させて金型を冷却する必要がある場合、そのための装置が利用可能です。
プラスチックコンパウンドは互いに大きく異なり、さまざまな成形方法に適しています。各材料はいずれかの方法に適していますが、多くの材料は複数の方法で製造できます。成形材料は粒状の粉末ですが、使用前に予備成形を行うものもあります。
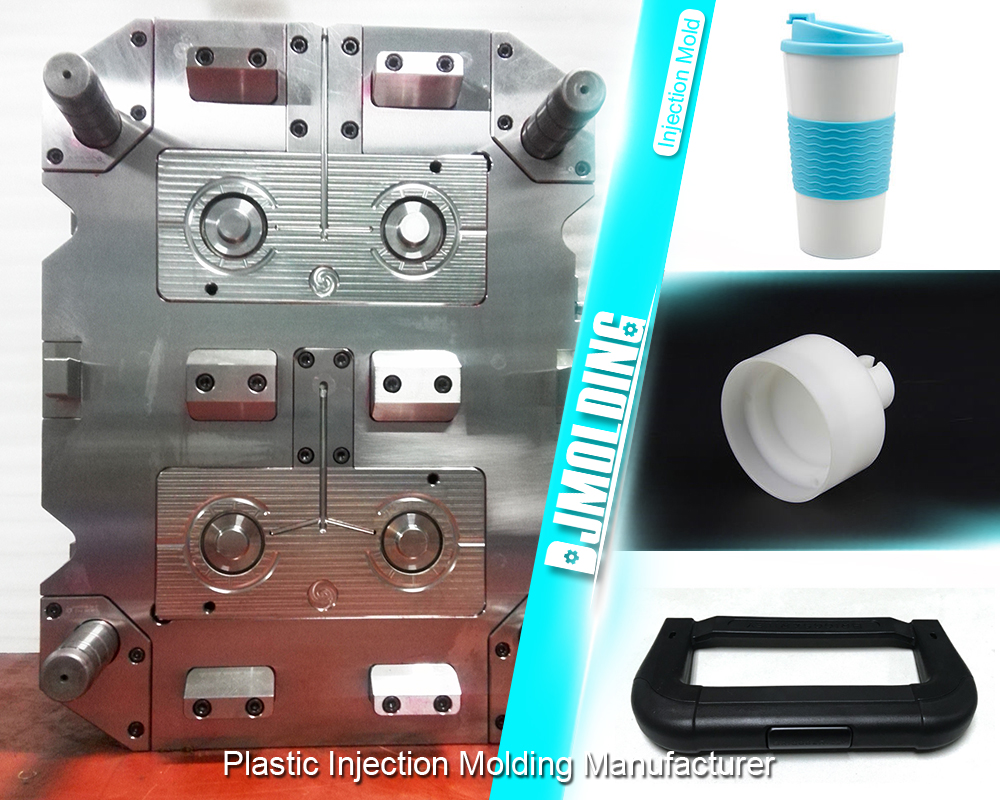
最適なプロセスとしてのインジェクション
射出成形 熱可塑性プラスチック部品の製造に最も広く使用されているプロセスです。このプロセスでは、所望の製品形状に機械加工された金型のキャビティに溶融プラスチックが押し込まれます。
プラスチックが十分に固まったら、金型を開けて部品を取り出します。プラスチック原料はペレットの形で機械のホッパーに入れられます。それからヒーターに入り、そこで溶けます。次に、液圧または機械的圧力を直接加えることにより、溶融プラスチックが金型キャビティに押し込まれます。
大容量 射出成形 機械は数百トンの圧力をかけることができ、大きなプラスチックを一体で製造することができます。例には、アセンブリ、ボンネット、フェンダー、バンパー、グリルなどの自動車の車体コンポーネントが含まれます。
注入プロセスは 5 つのステップに要約できます。
ステップ 1: 金型の部品を閉じます。
ステップ 2: ピストンが前進して材料を加熱シリンダー内に押し込み、同時に可塑化された材料を金型に射出します。
ステップ 3: ピストンはしばらくこの位置に留まり、ノズルを通る圧力を維持します。この間、材料は金型の形状を維持するために必要に応じて冷却および固化します。
ステップ 4: ピストンは反動しますが、金型は閉じたままであり、新しい量の材料がフィーダー ホッパーから落ちます。
ステップ 5: ドリルの動作により、成形部品を拒否すると同時に金型が開きます。
このプロセスの利点は次のとおりです。
- 材料、製造スペース、製造時間の節約。
- 射出成形された部品の形状と寸法の精度。
- 穴を形成し、他の材料から要素を挿入して製造が完了する可能性。
- 射出成形品の表面は滑らかできれいです。
- 良好な抵抗特性。
- 大量の部品を迅速に生産します。
このプロセスの欠点は次のとおりです。
- 工具コストが高いため、少量生産にはお勧めできません。
- 非常に薄い部分を扱う場合、金型に充填する前に樹脂が固化する可能性があります。
- 部品が複雑になると工具コストが増加します。
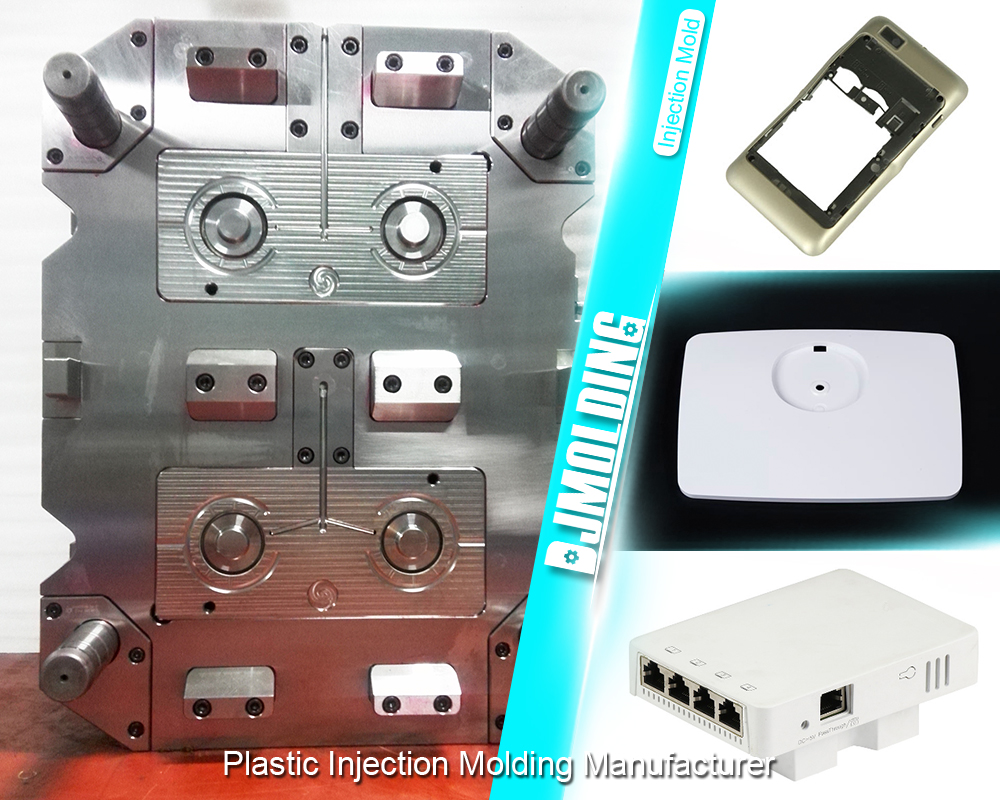
についての詳細 プラスチック射出成形 さまざまな方法: 他の方法よりも注入。次の場所で Djmolding にアクセスできます。 https://www.djmolding.com/ 詳細はこちら