Acuan Suntikan Plastik
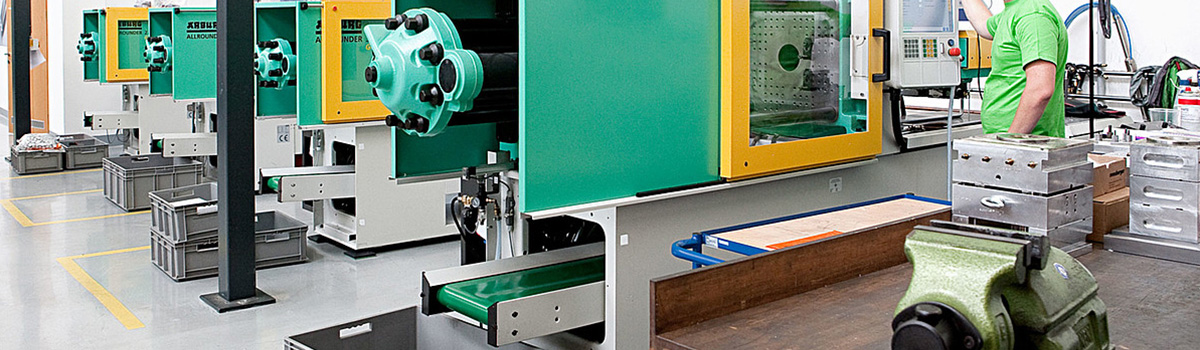
Pengacuan suntikan plastik ialah proses pembuatan yang melibatkan peleburan pelet plastik dan menyuntiknya ke dalam rongga acuan untuk mencipta objek tiga dimensi. Proses ini bermula dengan banyak produk, daripada bahagian ketepatan kecil kepada komponen automotif yang penting. Pengacuan suntikan plastik menawarkan banyak kelebihan berbanding proses pembuatan lain, termasuk kadar pengeluaran yang tinggi, fleksibiliti reka bentuk dan keberkesanan kos. Panduan ini akan melihat secara mendalam pada pengacuan suntikan plastik dan meneroka pelbagai aplikasi, faedah dan batasannya.
Sejarah Pengacuan Suntikan Plastik
Pengacuan suntikan plastik ialah proses pembuatan yang melibatkan suntikan plastik cair ke dalam rongga acuan untuk mencipta bentuk tertentu. Sejarah pengacuan suntikan plastik boleh dikesan kembali pada akhir 1800-an apabila seluloid, sejenis plastik, mula-mula dicipta. Walau bagaimanapun, pada tahun 1940-an pengacuan suntikan plastik digunakan secara meluas sebagai teknik pembuatan.
Semasa Perang Dunia II, permintaan untuk produk plastik yang dihasilkan secara besar-besaran meningkat, dan pengeluar mula mencari cara baharu dan lebih cekap untuk menghasilkannya. Pada tahun 1946, James Watson Hendry, seorang pencipta Amerika, membangunkan mesin pengacuan suntikan skru pertama, yang merevolusikan industri pengacuan suntikan plastik. Mesin ini membenarkan kawalan proses suntikan yang lebih tepat dan konsisten, menjadikan pengeluaran bahagian plastik dalam kuantiti yang banyak lebih mudah diakses dan cekap.
Sepanjang 1950-an dan 1960-an, kemajuan dalam teknologi plastik terus meningkatkan proses pengacuan suntikan plastik. Pengenalan bahan baharu, seperti polistirena dan polietilena, mencipta bahagian plastik yang lebih kompleks dan tahan lama. Selain itu, penambahbaikan dalam teknologi mesin pengacuan, termasuk menggunakan sistem hidraulik, menjadikan proses pengacuan suntikan lebih cekap dan menjimatkan kos.
Hari ini, pengacuan suntikan plastik ialah proses yang sangat automatik yang digunakan untuk menghasilkan pelbagai jenis produk plastik, daripada mainan dan barangan pengguna kepada alat ganti automotif dan peranti perubatan. Dengan pembangunan bahan dan teknologi baharu, proses pengacuan suntikan plastik terus berkembang dan bertambah baik, memastikan ia akan kekal sebagai teknik pembuatan penting selama bertahun-tahun.
Asas Pengacuan Suntikan Plastik
Pengacuan suntikan plastik ialah proses pembuatan untuk mencipta bahagian dan produk yang diperbuat daripada bahan plastik. Proses ini melibatkan suntikan plastik cair ke dalam acuan, yang menyejukkan dan memejal untuk membentuk bentuk yang diingini.
Langkah-langkah asas yang terlibat dalam proses pengacuan suntikan plastik adalah seperti berikut:
- Reka bentuk acuan: Langkah pertama dalam proses adalah untuk mereka bentuk acuan yang akan digunakan untuk membuat bahagian yang dikehendaki. Acuan biasanya dibuat daripada logam dan mesti disediakan untuk mengambil kira pengecutan apabila plastik menyejuk dan memejal.
- Penyediaan bahan: Bahan plastik yang digunakan dalam proses pengacuan suntikan datang dalam bentuk pelet atau butiran, yang mesti dicairkan dan disediakan untuk suntikan ke dalam acuan. Ini biasanya dilakukan dalam corong, di mana plastik dipanaskan pada suhu tertentu dan cair ke dalam keadaan cecair.
- Suntikan: Setelah plastik cair, ia disuntik ke dalam acuan menggunakan mesin pengacuan suntikan khusus. Mesin memberi tekanan pada plastik cair, memaksanya masuk ke dalam rongga acuan, di mana ia mengambil bentuk acuan.
- Penyejukan dan pemejalan: Selepas plastik disuntik ke dalam acuan, ia boleh menyejukkan dan memejal. Ini boleh mengambil masa dari beberapa saat hingga beberapa minit, bergantung pada saiz dan kerumitan bahagian tersebut.
- Ejection: Sebaik sahaja plastik telah sejuk dan pepejal, acuan dibuka, dan bahagiannya dikeluarkan. Kedudukan itu mungkin memerlukan kerja kemasan tambahan, seperti pemangkasan atau pengamplasan, untuk mengeluarkan plastik berlebihan atau tepi kasar.
Pengacuan suntikan plastik ialah proses yang tepat dan boleh diulang, menjadikannya sesuai untuk menghasilkan bahagian dan produk secara besar-besaran dengan kualiti yang konsisten. Ia juga sangat serba boleh, kerana ia boleh mencipta kepingan dan produk dalam pelbagai saiz, bentuk dan kerumitan. Beberapa aplikasi acuan suntikan plastik yang paling biasa termasuk pengeluaran mainan, barangan pengguna, alat ganti automotif dan peranti perubatan.
Proses Pengacuan Suntikan Plastik: Langkah demi Langkah
Pengacuan suntikan plastik adalah proses yang kompleks yang melibatkan beberapa langkah. Berikut ialah panduan langkah demi langkah untuk proses pengacuan suntikan plastik:
- Merekabentuk Acuan: Langkah pertama ialah mereka bentuk acuan yang digunakan untuk membuat bahagian. Acuan biasanya diperbuat daripada keluli atau aluminium dan mesti disediakan untuk menampung pengecutan bahan plastik semasa ia sejuk.
- Mencipta Acuan: Setelah reka bentuk acuan selesai, ia dihasilkan menggunakan perisian reka bentuk bantuan komputer (CAD) dan mesin pembuatan bantuan komputer (CAM). Acuan mesti dimesin dan digilap dengan teliti untuk memastikan ketepatan dan kemasan produk akhir.
- Pemilihan Bahan: Bahan resin plastik yang digunakan untuk proses pengacuan suntikan mesti dipilih berdasarkan keperluan bahagian, seperti kekuatan, fleksibiliti, warna dan teksturnya.
- Penyediaan Bahan: Bahan plastik yang dipilih kemudian dipanaskan pada suhu tertentu dan dicairkan menjadi cecair. Bahan tersebut kemudiannya disuntik ke dalam corong mesin acuan.
- Pengacuan Suntikan: Bahan plastik cair disuntik ke dalam rongga acuan menggunakan mesin pengacuan suntikan khusus. Mesin memberi tekanan pada bahan plastik, memaksanya ke dalam rongga acuan, di mana ia mengambil bentuk acuan.
- Penyejukan: Setelah rongga acuan diisi dengan plastik, ia boleh menyejukkan dan memejal. Masa penyejukan ditentukan oleh ciri-ciri bahan plastik, saiz dan ketebalan bahagian, dan suhu acuan.
- Ejection: Selepas plastik telah pepejal, acuan dibuka, dan bahagian dikeluarkan dari acuan menggunakan pin ejector.
- Kemasan: Bahagian yang dikeluarkan mungkin memerlukan kerja kemasan tambahan, seperti pemangkasan, pengamplasan atau pengecatan, untuk mengeluarkan sebarang plastik berlebihan atau tepi kasar.
- Kawalan Kualiti: Bahagian siap menjalani pemeriksaan menyeluruh untuk memenuhi spesifikasi dan piawaian kualiti yang diperlukan.
Pengacuan suntikan plastik boleh menghasilkan pelbagai bahagian dan produk dalam pelbagai saiz, bentuk dan kerumitan. Proses ini digunakan secara meluas dalam beberapa industri, termasuk automotif, perubatan, barangan pengguna dan elektronik.
Jenis Plastik Yang Digunakan dalam Pengacuan Suntikan
Banyak jenis plastik boleh digunakan dalam pengacuan suntikan. Pilihan bahan plastik akan bergantung pada keperluan khusus produk atau bahagian yang dihasilkan, seperti kekuatan, fleksibiliti, ketahanan dan penampilan. Berikut adalah beberapa jenis plastik yang paling biasa digunakan dalam pengacuan suntikan:
- Polietilena (PE): PE ialah bahan plastik yang digunakan secara meluas yang terkenal dengan kekuatan dan fleksibilitinya. Ia digunakan untuk menghasilkan pelbagai produk, termasuk bahan pembungkusan, mainan, dan peranti perubatan.
- Polipropilena (PP): PP ialah bahan plastik ringan dan tahan lama yang biasa digunakan dalam industri automotif untuk bahagian dalaman, seperti papan pemuka dan panel pintu. Ia juga menghasilkan bahan pembungkusan, seperti bekas dan botol.
- Polikarbonat (PC): PC ialah bahan plastik pepejal dan lutsinar yang biasa digunakan untuk menghasilkan komponen elektronik, seperti sarung komputer dan telefon. Ia juga digunakan untuk kanta lampu depan dan komponen papan pemuka dalam industri automotif.
- Acrylonitrile Butadiene Styrene (ABS): ABS ialah bahan plastik serba boleh yang terkenal dengan kekuatan, ketahanan dan rintangan habanya. Ia biasanya digunakan untuk menghasilkan bahagian automotif, seperti papan pemuka, suar fender, mainan dan barangan pengguna.
- Poliamida (PA): PA, juga dikenali sebagai nilon, ialah bahan plastik yang kuat dan ringan yang biasa digunakan dalam pengeluaran bahagian automotif, seperti penutup enjin dan sistem pengambilan udara. Ia juga menghasilkan peralatan sukan, seperti but ski dan raket tenis.
- Polistirena (PS): PS ialah bahan plastik ringan dan tegar yang biasa digunakan dalam penghasilan bahan pembungkusan, seperti cawan, dulang, dan bekas makanan. Ia juga mengeluarkan barangan pengguna, seperti mainan dan komponen elektronik.
- Polyethylene Terephthalate (PET): PET ialah bahan plastik teguh dan lutsinar yang biasa digunakan untuk menghasilkan bahan pembungkusan, seperti botol dan bekas. Ia juga digunakan dalam industri tekstil untuk menghasilkan gentian dan fabrik.
Ini hanyalah beberapa jenis plastik yang paling biasa digunakan dalam pengacuan suntikan. Banyak jenis bahan plastik lain boleh didapati, masing-masing mempunyai ciri dan ciri unik. Pilihan bahan plastik akan bergantung pada keperluan khusus bahagian atau produk yang dihasilkan.
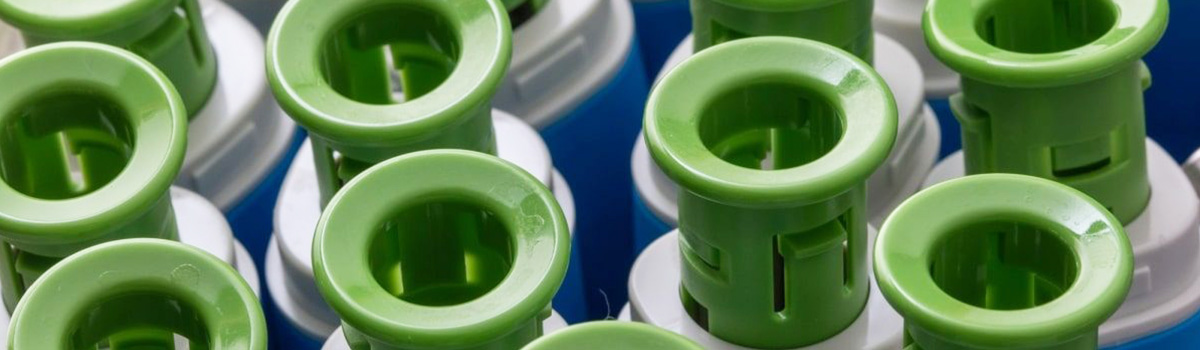
Jenis Mesin Pengacuan Suntikan
Mesin pengacuan suntikan datang dalam pelbagai jenis dan saiz, setiap satu direka untuk memenuhi keperluan pembuatan tertentu. Berikut adalah beberapa jenis mesin pengacuan suntikan yang paling biasa:
- Mesin Pengacuan Suntikan Hidraulik: Mesin ini menggunakan kuasa hidraulik untuk menjana tekanan untuk menyuntik plastik ke dalam acuan. Mesin hidraulik biasanya digunakan untuk bahagian yang lebih penting yang memerlukan daya pengapit yang tinggi.
- Mesin Pengacuan Suntikan Elektrik: Mesin elektrik menggunakan motor elektrik untuk menggerakkan unit suntikan dan mekanisme pengapit. Ia terkenal dengan ketepatan tinggi dan kecekapan tenaga, menjadikannya terkenal kerana menghasilkan bahagian yang kecil dan rumit.
- Mesin Pengacuan Suntikan Hibrid: Mesin hibrid menggabungkan faedah peranti hidraulik dan elektrik, menggunakan kedua-dua kuasa hidraulik dan elektrik untuk menjana tekanan dan kuasa yang diperlukan. Mesin hibrid menawarkan keseimbangan kelajuan, ketepatan dan kecekapan tenaga yang baik.
- Mesin Pengacuan Suntikan Menegak: Mesin menegak menghasilkan bahagian yang memerlukan pengacuan sisipan atau pengacuan berlebihan. Mereka mempunyai unit pengapit menegak yang membolehkan akses mudah kepada acuan, menjadikannya sesuai untuk membuat bahagian kecil atau kompleks.
- Mesin Pengacuan Suntikan Dua Pukulan: Mesin dua pukulan menghasilkan bahagian dengan bahan atau warna yang berbeza. Peranti ini mempunyai dua unit suntikan, setiap satu mampu menyuntik bahan asing ke dalam acuan. Mesin jenis ini biasanya digunakan untuk menghasilkan bahagian automotif, seperti pemegang dan tombol.
- Mesin Pengacuan Suntikan Berbilang Pukulan: Mesin berbilang pukulan menghasilkan bahagian dengan lebih daripada dua bahan atau warna. Peranti ini mempunyai beberapa unit suntikan, setiap satu mampu menyuntik bahan yang berbeza ke dalam acuan. Mesin jenis ini biasanya digunakan untuk menghasilkan barangan pengguna, seperti berus gigi dan pencukur.
- Mesin Pengacuan Suntikan Semua Elektrik: Mesin semua elektrik menggunakan motor elektrik untuk menggerakkan unit suntikan, mekanisme pengapit dan acuan. Ia terkenal dengan ketepatan tinggi, kelajuan dan kecekapan tenaga, menjadikannya terkenal kerana menghasilkan bahagian berketepatan tinggi yang kecil.
Ini hanyalah beberapa jenis mesin pengacuan suntikan yang paling biasa. Setiap mesin mempunyai ciri dan kelebihan yang unik, menjadikannya penting untuk memilih peranti yang sesuai untuk keperluan pembuatan tertentu.
Bahagian Mesin Pengacuan Suntikan
Mesin pengacuan suntikan mempunyai beberapa bahagian yang mencipta bahagian plastik daripada bahan mentah. Berikut ialah komponen kritikal mesin pengacuan suntikan:
Hopper: Takungan menyimpan bahan plastik mentah sebelum dimasukkan ke dalam mesin pengacuan suntikan. Bahan ini biasanya dalam bentuk pelet atau serbuk.
Tong: Tong ialah bahagian silinder yang panjang bagi mesin pengacuan suntikan yang menempatkan skru, yang mencairkan dan mencampurkan bahan plastik.
Skru: Skru ialah peranti berputar di dalam tong yang menolak bahan plastik ke hadapan dan mencairkannya melalui geseran dan haba.
Unit suntikan: Unit suntikan termasuk corong, tong dan skru dan bertanggungjawab untuk mencairkan dan menyuntik plastik ke dalam acuan.
Unit pengapit: Unit pengapit bertanggungjawab untuk memegang acuan dengan selamat dan menggunakan tekanan yang diperlukan semasa proses pengacuan suntikan.
Acuan: Acuan ialah alat yang mencipta bentuk dan saiz bahagian plastik. Acuan biasanya diperbuat daripada keluli dan terdiri daripada dua bahagian yang sesuai bersama.
Muncung: Muncung ialah bahagian unit suntikan yang menyambungkan mesin pengacuan suntikan ke acuan. Bahan plastik cair disuntik melalui muncung dan ke dalam acuan.
Sistem penyejukan: Sistem penyejukan bertanggungjawab untuk menyejukkan bahagian plastik sebaik sahaja disuntik ke dalam acuan. Ini memastikan kepingan itu padat dan boleh dikeluarkan dari acuan tanpa kerosakan.
Panel kawalan: Panel kawalan ialah antara muka yang membolehkan pengendali memantau dan melaraskan tetapan mesin pengacuan suntikan, seperti suhu, tekanan dan masa kitaran.
Setiap bahagian ini memainkan peranan penting dalam proses pengacuan suntikan, dan adalah penting untuk mengekalkan dan mengoptimumkan setiap bahagian untuk memastikan bahagian berkualiti tinggi dihasilkan dengan cekap.
Alat Pengacuan Suntikan: Reka Bentuk dan Pembuatan
Alat pengacuan suntikan merujuk kepada mereka bentuk dan mengeluarkan acuan yang digunakan dalam mesin pengacuan suntikan untuk menghasilkan bahagian plastik. Kualiti dan kecekapan acuan secara langsung mempengaruhi kualiti dan produktiviti proses pengacuan suntikan. Berikut ialah langkah kritikal dalam reka bentuk dan pembuatan alat pengacuan suntikan:
Reka bentuk produk: Langkah pertama dalam alat pengacuan suntikan ialah mereka bentuk produk yang akan dihasilkan. Reka bentuk produk termasuk menentukan saiz, bentuk dan bahan bahagian, serta sebarang ciri atau keperluan khusus.
Reka bentuk acuan: Proses reka bentuk acuan bermula sebaik sahaja reka bentuk produk dimuktamadkan. Pereka bentuk acuan akan menentukan jenis acuan terbaik, bilangan rongga yang diperlukan, dan saiz dan bentuk acuan.
Pembinaan acuan: Acuan dibina berdasarkan reka bentuk acuan, menggunakan bahan berkualiti tinggi seperti keluli atau aluminium. Acuan biasanya dibuat dalam dua bahagian, setiap satu mengandungi satu atau lebih rongga.
Pemasangan acuan: Setelah acuan dibina, ia dipasang dan diuji untuk ketepatan dan kefungsian. Acuan mesti menahan tekanan dan haba proses pengacuan suntikan.
Ujian dan pengesahan acuan: Selepas acuan dipasang, ia diuji dan disahkan untuk memastikan ia menghasilkan bahagian berkualiti tinggi yang memenuhi spesifikasi produk. Acuan mungkin perlu dilaraskan atau diubah suai untuk meningkatkan prestasinya.
Penyelenggaraan acuan: Penyelenggaraan dan pembaikan acuan yang kerap adalah penting untuk memastikan jangka hayat dan prestasinya. Ini termasuk pembersihan, pelinciran dan penggantian mana-mana bahagian yang haus atau rosak.
Alat pengacuan suntikan memerlukan ketepatan dan kepakaran untuk menghasilkan bahagian berkualiti tinggi secara konsisten dan cekap. Dengan mengikuti proses reka bentuk dan pembuatan yang lengkap, pengeluar boleh membuat acuan yang memenuhi keperluan unik produk mereka dan mengoptimumkan proses pengacuan suntikan mereka.
Jenis Alat Pengacuan Suntikan
Pengacuan suntikan ialah proses pembuatan yang digunakan secara meluas untuk menghasilkan bahagian dalam kuantiti yang banyak. Ia melibatkan menyuntik plastik cair ke dalam rongga acuan dan membenarkannya menyejuk dan memejal menjadi bentuk yang diingini. Alat pengacuan suntikan ialah proses mencipta acuan yang digunakan dalam pengacuan suntikan. Terdapat beberapa jenis alat pengacuan suntikan, masing-masing mempunyai kelebihan dan kekurangannya sendiri.
- Acuan Dua Plat Acuan dua plat adalah jenis alat pengacuan suntikan yang paling mudah. Ia terdiri daripada dua plat yang diapit bersama untuk membentuk rongga acuan. Plastik cair disuntik ke dalam lubang melalui pintu dan dibiarkan sejuk dan pepejal. Sebaik sahaja bahagian itu dibuat, kedua-dua plat dipisahkan, dan jumlahnya dikeluarkan. Acuan dua plat biasanya digunakan untuk komponen bersaiz kecil hingga sederhana dengan geometri mudah.
- Acuan Tiga Plat Acuan tiga plat adalah serupa dengan acuan dua plat, tetapi ia mempunyai plat tambahan, dikenali sebagai plat penjalur, yang memisahkan bahagian acuan daripada sistem pelari. Sistem pelari ialah rangkaian saluran yang menghantar plastik cair ke rongga acuan. Acuan tiga plat digunakan untuk bahagian yang lebih penting dan geometri yang lebih kompleks.
- Acuan Hot Runner Dalam acuan hot runner, plastik cair disuntik terus ke dalam rongga acuan melalui satu siri saluran yang dipanaskan dan bukannya melalui pintu pagar. Ini mengurangkan bahan terbuang dalam sistem pelari, menghasilkan proses yang lebih cekap. Acuan pelari panas digunakan untuk pengeluaran volum tinggi bahagian kompleks.
- Acuan Keluarga Acuan keluarga menghasilkan beberapa bahagian dalam satu acuan. Mereka mempunyai pelbagai rongga yang disusun dengan cara yang membolehkan pengeluaran banyak domain secara serentak. Acuan keluarga biasanya digunakan untuk bahagian dengan isipadu kecil hingga sederhana.
- Acuan Masukkan Acuan masukkan menghasilkan bahagian yang memerlukan sisipan logam atau plastik. Sisipan dimasukkan ke dalam rongga acuan sebelum menyuntik plastik cair. Setelah plastik telah sejuk dan pepejal, bahagian dan sisipan diikat secara kekal. Acuan sisip digunakan untuk kedudukan yang memerlukan kekuatan, ketahanan, atau daya tarikan estetik.
- Overacuan Overacuan ialah satu proses di mana satu bahagian dibentuk di atas bahagian yang lain. Ia sering digunakan untuk kedudukan yang memerlukan sentuhan lembut atau cengkaman yang lebih baik. Overacuan melibatkan penetapan substrat atau bahagian asas terlebih dahulu dan kemudian membentuk bahan kedua di atasnya. Bahan kedua boleh menjadi jenis plastik yang berbeza, bahan seperti getah, atau elastomer termoplastik.
Kesimpulannya, pilihan alat pengacuan suntikan bergantung kepada jenis bahagian yang dihasilkan, jumlah pengeluaran yang diperlukan, dan tahap kerumitan yang terlibat dalam reka bentuk bahagian. Memilih alatan yang betul adalah penting untuk memastikan proses itu cekap dan kos efektif.
Garis Panduan Reka Bentuk Pengacuan Suntikan
Pengacuan suntikan ialah proses pembuatan yang digunakan secara meluas untuk menghasilkan bahagian plastik. Mereka bentuk bahagian untuk pengacuan suntikan memerlukan pemahaman yang baik tentang proses, bahan, dan garis panduan reka bentuk yang mesti diikuti untuk memastikan butiran boleh dihasilkan dengan jayanya. Berikut ialah beberapa garis panduan reka bentuk pengacuan suntikan yang perlu diingat:
Ketebalan Dinding, Ketebalan dinding bahagian hendaklah seragam dan setipis mungkin sambil mengekalkan kekuatan dan fungsi yang diperlukan. Ini membantu mengurangkan masa penyejukan dan kitaran serta meminimumkan risiko meledingkan dan tanda tenggelam.
Rusuk dan Bos Rusuk dan bos boleh digunakan untuk meningkatkan kekuatan dan ketegaran bahagian. Rusuk hendaklah tidak lebih daripada 60% daripada ketebalan dinding nominal, dan bos hendaklah 1.5 kali ketebalan dinding nominal.
Sudut Draf, Sudut draf sekurang-kurangnya 1-2 darjah hendaklah digunakan pada semua permukaan menegak untuk memudahkan bahagian lentingan dan mengelakkan kerosakan pada acuan.
Fillet dan Jejari Sudut dan tepi yang tajam harus dielakkan untuk mengelakkan kepekatan tekanan, yang boleh menyebabkan keretakan dan kegagalan. Sebaliknya, fillet dan jejari harus mengedarkan tekanan dan meningkatkan kekuatan bahagian.
Pintu dan Pelari Lokasi dan reka bentuk pintu dan pelari adalah penting untuk mencapai kualiti bahagian yang baik. Pintu masuk hendaklah sekecil mungkin di bahagian paling tebal bahagian itu. Pelari harus direka bentuk untuk meminimumkan penurunan tekanan dan memaksimumkan aliran.
Kemasan Permukaan Kemasan permukaan bahagian hendaklah ditentukan berdasarkan keperluan aplikasi. Kemasan permukaan yang lebih tinggi mungkin diperlukan untuk kepingan yang kelihatan, manakala kemasan permukaan yang lebih rendah mungkin boleh diterima untuk bahagian tersembunyi.
Pemilihan Bahan Bahan yang dipilih untuk bahagian hendaklah sesuai untuk pengacuan suntikan dan memenuhi sifat mekanikal, haba dan kimia yang diperlukan.
Operasi Sekunder dalam Pengacuan Suntikan
Pengacuan suntikan adalah proses pembuatan serba boleh yang digunakan untuk menghasilkan pelbagai bahagian plastik. Sebagai tambahan kepada proses pengacuan utama, banyak kedudukan memerlukan operasi sekunder untuk mencapai bentuk, kemasan atau fungsi yang diingini. Berikut adalah beberapa operasi sekunder harian dalam pengacuan suntikan:
- Pemangkasan adalah mengeluarkan bahan berlebihan dari bahagian acuan selepas ia dikeluarkan dari acuan. Ini biasanya dilakukan menggunakan mesin trim atau mesin CNC. Pemangkasan selalunya diperlukan untuk mencapai bentuk dan saiz akhir bahagian.
- Kimpalan menggabungkan dua atau lebih bahagian plastik menggunakan haba, tekanan, atau gabungan kedua-duanya. Ini sering digunakan untuk mencipta ciri yang lebih besar atau lebih kompleks yang tidak boleh dihasilkan dalam satu acuan.
- Menghias ialah proses menambah ciri visual atau fungsi pada permukaan bahagian yang dibentuk. Ini boleh termasuk mengecat, mencetak, melabel atau menggunakan tekstur atau corak.
- Perhimpunan ialah proses mencantumkan beberapa bahagian untuk mencipta produk yang lengkap. Ini boleh dilakukan menggunakan pengikat, pelekat, atau teknik penyambungan lain.
- Pengacuan Sisipan Pengacuan Sisipan ialah pengacuan plastik di sekeliling sisipan logam atau plastik yang telah dibentuk. Ini sering digunakan untuk mencipta bahagian dengan tahap kekuatan atau ketahanan yang tinggi.
- Overmolding Overmolding ialah proses membentuk bahan kedua di atas bahagian yang telah dibentuk. Ini boleh menambah permukaan sentuhan lembut, meningkatkan cengkaman atau mencipta sekeping dua warna atau berbilang bahan.
- Salutan menggunakan lapisan bahan nipis pada permukaan bahagian untuk meningkatkan penampilan, ketahanan atau sifat lain. Ini boleh termasuk salutan seperti salutan krom, nikel atau serbuk.
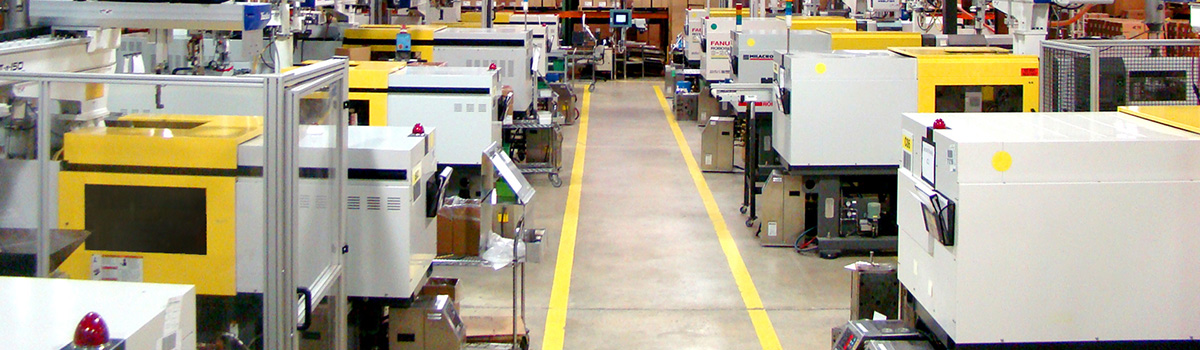
Kelebihan Acuan Suntikan Plastik
Pengacuan suntikan plastik ialah proses pembuatan yang digunakan secara meluas untuk menghasilkan bahagian plastik dengan ketepatan, konsistensi dan kualiti yang tinggi. Ia melibatkan menyuntik plastik cair ke dalam rongga acuan dan membenarkannya menyejuk dan memejal. Berikut adalah beberapa kelebihan pengacuan suntikan plastik:
- Kecekapan dan Produktiviti Tinggi Pengacuan suntikan plastik ialah proses yang sangat cekap dan automatik yang boleh menghasilkan jumlah bahagian yang besar dengan ketekalan dan kualiti yang tinggi. Dengan teknologi automasi canggih, masa kitaran pengeluaran boleh dikurangkan kepada beberapa saat, yang membolehkan pengeluaran volum tinggi bahagian yang kompleks dan rumit.
- Pengacuan Suntikan Ketepatan dan Ketepatan Tinggi meningkatkan ketepatan dan ketepatan dalam menghasilkan bahagian yang kompleks dan rumit. Jentera yang dikawal komputer dan perisian canggih membolehkan toleransi yang ketat dengan kebolehulangan dan ketepatan yang tinggi.
- Pengacuan suntikan serba boleh ialah proses serba boleh yang boleh menghasilkan pelbagai bahagian plastik dengan saiz, bentuk dan kerumitan yang berbeza. Proses ini boleh digunakan untuk membuat segala-galanya daripada kepingan kecil dengan butiran yang rumit kepada jumlah yang besar dengan geometri yang kompleks.
- Pengacuan Suntikan Fleksibiliti Bahan boleh menggunakan pelbagai jenis bahan plastik, termasuk termoplastik, termoset dan elastomer. Ini membolehkan untuk menghasilkan bahagian dengan pelbagai sifat mekanikal, haba dan kimia.
- Pengacuan Suntikan Pengeluaran Sisa Rendah ialah proses pengeluaran sisa rendah kerana ia menghasilkan sisa minimum semasa pengeluaran. Sebarang lebihan bahan boleh dikitar semula dan digunakan semula dengan mudah dalam pengeluaran, menjadikannya proses pembuatan yang mesra alam.
- Mengurangkan Kos Buruh Tahap automasi yang tinggi dalam pengacuan suntikan meminimumkan keperluan untuk proses intensif buruh, dengan ketara mengurangkan kos buruh. Ini juga mengurangkan risiko kesilapan manusia, meningkatkan kualiti dan konsistensi produk akhir.
- Operasi Pasca Pengeluaran Dikurangkan Pengacuan suntikan menghasilkan bahagian dengan ketepatan dan ketekalan yang tinggi, mengurangkan keperluan untuk operasi pasca pengeluaran seperti pemangkasan, penggerudian atau pengilangan. Ini mengurangkan masa pengeluaran dan kos produk akhir.
- Ketekalan dan Kualiti Pengacuan suntikan menghasilkan bahagian dengan tahap ketekalan dan kualiti yang tinggi. Teknologi canggih dan jentera kawalan komputer memastikan setiap butiran adalah sama dalam bentuk, saiz dan kualiti.
- Pengacuan Suntikan Fleksibiliti Reka Bentuk menawarkan tahap fleksibiliti reka bentuk yang tinggi, kerana ia membolehkan untuk menghasilkan bahagian dengan geometri kompleks, potongan bawah dan butiran rumit. Ini akan membolehkan pereka bentuk mencipta kepingan dengan bentuk dan fungsi unik yang tidak boleh dibuat menggunakan proses pembuatan lain.
- Kos efektif untuk pengacuan Suntikan Pengeluaran Volume Tinggi ialah proses kos efektif untuk menghasilkan bahagian plastik. Kos perkakas awal boleh menjadi tinggi, tetapi kos setiap bahagian berkurangan apabila volum pengeluaran meningkat. Ini menjadikannya proses yang ideal untuk menghasilkan kuantiti bahagian yang banyak.
Pengacuan suntikan plastik menawarkan banyak kelebihan, menjadikannya pilihan popular untuk menghasilkan bahagian plastik. Kecekapan tinggi, ketepatan, serba boleh, fleksibiliti bahan, pengeluaran sisa yang rendah, kos buruh yang dikurangkan, serta konsistensi dan kualiti menjadikannya proses yang ideal untuk pelbagai aplikasi. Keupayaan untuk menghasilkan bahagian yang kompleks dan rumit dengan fleksibiliti reka bentuk yang tinggi dan keberkesanan kos untuk pengeluaran volum tinggi menjadikannya proses pembuatan yang sangat dicari.
Kelemahan Pengacuan Suntikan Plastik
Pengacuan suntikan plastik ialah proses pembuatan yang digunakan secara meluas yang melibatkan suntikan plastik cair ke dalam rongga acuan untuk menghasilkan pelbagai jenis bahagian dan produk plastik. Walaupun pengacuan suntikan plastik mempunyai banyak faedah, terdapat juga beberapa kelemahan. Berikut adalah beberapa kelemahan utama pengacuan suntikan plastik:
- Kos perkakas yang tinggi: Kos mereka bentuk dan menghasilkan acuan untuk pengacuan suntikan plastik boleh menjadi sangat tinggi. Ini kerana acuan perlu dibuat daripada bahan yang berkualiti tinggi dan dimesin dengan tepat untuk menghasilkan bahagian yang dikehendaki. Selain itu, kos untuk mereka bentuk dan mengeluarkan acuan mungkin terlalu mahal untuk pengeluaran berskala kecil, menjadikan pengacuan suntikan plastik kurang menjimatkan untuk pembuatan volum rendah.
- Masa pendahuluan yang lama: Proses mereka bentuk dan menghasilkan acuan untuk pengacuan suntikan plastik boleh mengambil masa yang lama, yang boleh melambatkan pengeluaran bahagian plastik. Ini boleh menjadi masalah terutamanya bagi perniagaan yang perlu bertindak balas dengan cepat terhadap perubahan dalam permintaan pasaran atau membangunkan produk baharu dengan pantas.
- Fleksibiliti terhad: Setelah acuan direka bentuk dan dihasilkan, lebih mudah dan lebih murah untuk menukar reka bentuk atau mengubah suai proses pengeluaran. Ini boleh mengehadkan fleksibiliti pengacuan suntikan plastik dan menjadikannya kurang sesuai untuk menghasilkan produk tersuai atau satu-satunya.
- Kebimbangan alam sekitar: Pengacuan suntikan plastik bergantung pada sejumlah besar plastik, yang boleh memberi kesan ekologi negatif. Sisa plastik adalah isu alam sekitar yang utama, dan pengacuan suntikan plastik boleh menyumbang kepada masalah ini. Selain itu, proses pembuatan produk plastik memerlukan penggunaan tenaga dan sumber semula jadi, yang boleh memberi kesan kepada alam sekitar.
- Kadar sekerap yang tinggi: Pengacuan suntikan plastik boleh menghasilkan bahan sekerap yang ketara, yang boleh mahal untuk dilupuskan atau dikitar semula. Selain itu, pengeluaran bahan sekerap boleh meningkatkan kos pengeluaran keseluruhan dan mengurangkan kecekapan proses pembuatan.
- Pilihan bahan terhad: Pengacuan suntikan plastik digunakan terutamanya untuk menghasilkan bahagian dan produk daripada bahan termoplastik, yang mempunyai sifat terhad berbanding bahan lain seperti logam atau seramik. Ini boleh menjadikan pengacuan suntikan plastik kurang sesuai untuk aplikasi yang memerlukan kekuatan tinggi, rintangan suhu atau sifat lanjutan yang lain.
Had Pengacuan Suntikan Plastik
Walaupun pengacuan suntikan plastik menawarkan banyak kelebihan, batasan tertentu juga dikaitkan dengan proses tersebut. Berikut adalah beberapa batasan pengacuan suntikan plastik:
Kos Perkakas Permulaan Tinggi: Kos permulaan mereka bentuk dan mengeluarkan acuan boleh dinaikkan. Acuan perlu tepat dan tahan lama untuk menahan proses pengacuan suntikan berulang, dan ini boleh memerlukan pelaburan pendahuluan yang besar, terutamanya untuk acuan yang kompleks atau besar.
Masa Utama: Masa utama untuk pembuatan acuan boleh menjadi ketara, antara minggu hingga bulan, bergantung pada kerumitan dan saiz acuan. Ini boleh menyebabkan kelewatan dalam garis masa pengeluaran, terutamanya untuk projek sensitif masa.
Kekangan Reka Bentuk: Pengacuan suntikan mempunyai batasan reka bentuk tertentu yang mesti dipertimbangkan. Sebagai contoh, mencapai ketebalan dinding yang seragam di seluruh bahagian adalah penting untuk memastikan pengisian dan penyejukan yang betul. Selain itu, sudut draf diperlukan pada permukaan menegak untuk membolehkan pelepasan mudah daripada acuan.
Had Saiz Bahagian: Pengacuan suntikan paling sesuai untuk menghasilkan bahagian kecil hingga sederhana. Bahagian yang besar mungkin memerlukan peralatan khusus dan acuan yang lebih besar, menambah kos dan kerumitan.
Pemilihan Bahan: Walaupun pengacuan suntikan membolehkan pelbagai jenis bahan plastik, pilihan bahan masih terhad berbanding proses pembuatan lain. Bahan dengan takat lebur yang tinggi atau ciri aliran yang lemah mungkin tidak sesuai untuk pengacuan suntikan.
Kemasan Permukaan: Proses pengacuan suntikan boleh mengakibatkan garisan bersatu atau garisan pemisah yang boleh dilihat pada permukaan bahagian. Mencapai kemasan permukaan berkualiti tinggi mungkin mencabar, dan kaedah lain, seperti penggilap atau salutan, mungkin diperlukan.
Potongan Terhad: Potongan bawah ialah ciri atau butiran pada bahagian yang menghalangnya daripada mudah dikeluarkan daripada acuan. Potongan bawah boleh merumitkan proses lontar dan memerlukan ciri acuan tambahan atau operasi sekunder untuk mencapai geometri bahagian yang dikehendaki.
Pilihan Pembaikan Terhad: Jika acuan rosak atau memerlukan pengubahsuaian, ia boleh memakan kos yang tinggi dan memakan masa untuk membaiki atau mengubah acuan sedia ada. Kadangkala, acuan yang benar-benar baru mungkin perlu dikeluarkan, yang membawa kepada perbelanjaan tambahan dan kelewatan.
Walaupun had ini, pengacuan suntikan plastik kekal sebagai proses pembuatan yang sangat serba boleh dan digunakan secara meluas untuk menghasilkan bahagian plastik. Dengan mempertimbangkan dengan teliti had ini semasa peringkat reka bentuk dan perancangan pengeluaran, adalah mungkin untuk mengurangkan kesannya dan memanfaatkan kelebihan pengacuan suntikan dengan berkesan.
Aplikasi Pengacuan Suntikan Plastik
Pengacuan suntikan plastik adalah proses pembuatan serba boleh yang boleh menghasilkan pelbagai jenis bahagian plastik. Berikut adalah beberapa aplikasi pengacuan suntikan plastik:
- Produk Pengguna: Pengacuan suntikan digunakan secara meluas untuk menghasilkan pelbagai produk, seperti mainan, peralatan dapur dan elektronik. Proses ini boleh menghasilkan bahagian berkualiti tinggi dengan geometri yang rumit dan dimensi yang tepat, menjadikannya sesuai untuk produk yang memerlukan toleransi yang ketat dan bentuk yang kompleks.
- Bahagian Automotif: Banyak komponen plastik kereta, seperti komponen papan pemuka, pemegang pintu dan lampu, dihasilkan menggunakan pengacuan suntikan. Proses ini membolehkan volum pengeluaran yang tinggi dan kualiti yang konsisten, menjadikannya pilihan kos efektif untuk pengeluar automotif.
- Peranti Perubatan: Pengacuan suntikan biasanya digunakan untuk menghasilkan peranti perubatan, seperti picagari, penyedut dan peralatan diagnostik. Proses ini boleh menghasilkan bahagian dengan ketepatan dan konsistensi yang tinggi, memastikan kualiti dan kebolehpercayaan peranti.
- Pembungkusan: Pengacuan suntikan digunakan secara meluas untuk menghasilkan pembungkusan plastik, seperti bekas, penutup dan penutup. Proses ini boleh mempunyai bahagian dengan dimensi yang konsisten dan kemasan berkualiti tinggi, menjadikannya sesuai untuk pembungkusan dengan penampilan yang menarik dan padanan yang selamat.
- Aeroangkasa dan Pertahanan: Pengacuan suntikan menghasilkan pelbagai komponen aeroangkasa dan pertahanan, seperti bahagian dalam pesawat, pencahayaan dan sistem komunikasi. Proses ini boleh mempunyai bahagian dengan bahan ringan dan tahan lama, menjadikannya sesuai untuk aplikasi yang memerlukan nisbah kekuatan kepada berat yang tinggi.
- Pembinaan: Pengacuan suntikan boleh menghasilkan pelbagai bahan binaan, seperti jubin plastik, bumbung, dan berpihak. Proses ini boleh mempunyai bahagian dengan dimensi yang konsisten dan kemasan berkualiti tinggi, menjadikannya pilihan yang menarik untuk syarikat pembinaan.
- Sukan dan Rekreasi: Pengacuan suntikan digunakan secara meluas dalam menghasilkan peralatan sukan, seperti kayu golf, raket tenis dan komponen basikal. Proses ini boleh menghasilkan bahagian dengan bahan ringan dan geometri yang tepat, memastikan prestasi dan ketahanan peralatan.
Secara keseluruhannya, pengacuan suntikan plastik adalah proses pembuatan yang serba boleh dan digunakan secara meluas yang boleh menghasilkan bahagian plastik berkualiti tinggi untuk pelbagai aplikasi. Proses ini boleh disesuaikan untuk memenuhi keperluan reka bentuk dan pengeluaran khusus, menjadikannya pilihan yang menarik untuk pengeluar dalam pelbagai industri.
Industri Automotif dan Pengacuan Suntikan Plastik
Industri automotif adalah pengguna penting teknologi pengacuan suntikan plastik. Proses pengacuan suntikan plastik telah merevolusikan pengeluaran bahagian dan komponen automotif, menjadikannya mungkin untuk menghasilkan bentuk yang kompleks dengan ketepatan dan ketepatan yang tinggi. Berikut ialah beberapa cara pengacuan suntikan plastik digunakan dalam industri automotif:
- Bahagian dalaman: Pengacuan suntikan plastik menghasilkan banyak faktor dalaman, termasuk komponen papan pemuka, panel pintu, kepingan trim dan banyak lagi. Bahagian ini boleh direka bentuk dengan bentuk dan tekstur yang rumit serta disesuaikan untuk dipadankan dengan gaya dan keperluan fungsi setiap model kenderaan.
- Bahagian luar: Pengacuan suntikan plastik juga digunakan untuk menghasilkan pelbagai ciri luaran, termasuk bampar, jeriji, cermin sisi dan banyak lagi. Bahagian ini boleh direka bentuk untuk menahan keadaan cuaca yang melampau dan dibuat dalam pelbagai warna dan kemasan.
- Komponen bawah hud: Pengacuan suntikan plastik menghasilkan banyak ciri bawah hud, termasuk penutup enjin, sistem pengambilan udara dan bahagian sistem penyejukan. Komponen ini memerlukan suhu tinggi dan rintangan kimia, yang boleh dicapai dengan bahan termoplastik.
- Komponen elektrik dan elektronik: Pengacuan suntikan plastik menghasilkan pelbagai komponen elektrik dan elektronik, termasuk penyambung, perumah dan penderia. Komponen ini memerlukan ketepatan dan kebolehpercayaan yang tinggi, yang boleh dicapai dengan ketepatan dan ketekalan pengacuan suntikan plastik.
- Ringan: Pengacuan suntikan plastik sering digunakan untuk menghasilkan bahagian ringan yang membantu mengurangkan berat keseluruhan kenderaan, meningkatkan kecekapan bahan api dan mengurangkan pelepasan. Pemberat ringan juga boleh meningkatkan pengendalian dan prestasi kenderaan.
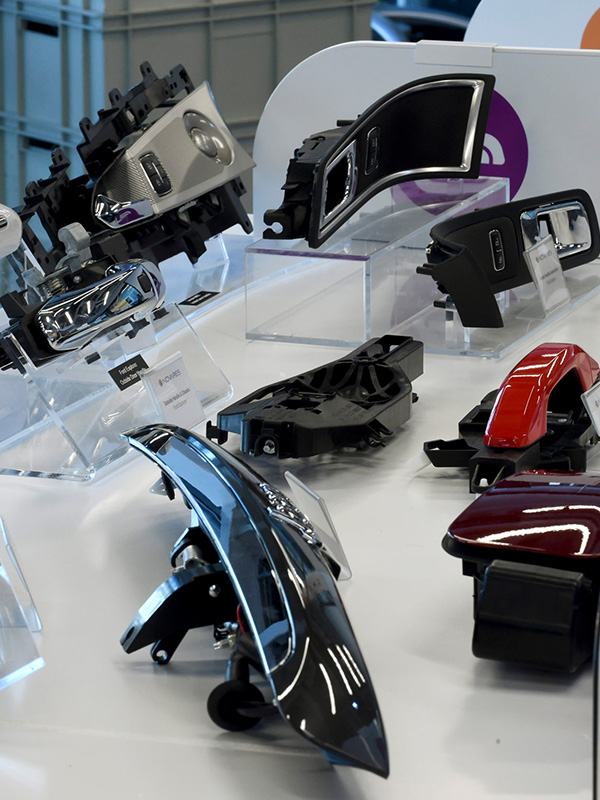
Industri Perubatan dan Pengacuan Suntikan Plastik
Pengacuan suntikan plastik digunakan secara meluas dalam industri perubatan untuk menghasilkan pelbagai peranti dan komponen perubatan. Proses pengacuan suntikan plastik membolehkan penghasilan bentuk kompleks dengan ketepatan dan ketepatan yang tinggi, menjadikannya kaedah pembuatan yang ideal untuk banyak aplikasi perubatan. Berikut ialah beberapa cara pengacuan suntikan plastik digunakan dalam industri perubatan:
- Peranti perubatan: Pengacuan suntikan plastik menghasilkan pelbagai peranti perubatan, termasuk instrumen pembedahan, alat diagnostik, sistem penghantaran ubat, dll. Peranti ini selalunya memerlukan ketepatan dan ketepatan yang tinggi, dan pengacuan suntikan plastik boleh memenuhi keperluan ini.
- Implan: Pengacuan suntikan plastik juga digunakan untuk menghasilkan pelbagai implan, termasuk penggantian sendi, implan pergigian dan banyak lagi. Implan ini boleh direka bentuk untuk memadankan anatomi pesakit dan dihasilkan dengan bahan biokompatibel.
- Peralatan makmal: Pengacuan suntikan plastik menghasilkan pipet, plat mikro, dan tiub uji. Komponen ini memerlukan ketepatan dan ketepatan yang tinggi untuk memastikan hasil yang boleh dipercayai.
- Pembungkusan: Pengacuan suntikan plastik digunakan untuk menghasilkan pembungkusan untuk peranti perubatan, termasuk sistem penghalang steril dan pembungkusan tersuai untuk produk individu. Penyelesaian pembungkusan ini boleh membantu mengekalkan kemandulan dan integriti peranti perubatan.
- Peranti guna tunggal: Pengacuan suntikan plastik selalunya menghasilkan peranti sekali guna seperti picagari, jarum dan kateter. Peranti ini boleh dibuat dalam jumlah tinggi pada kos yang rendah dan boleh membantu untuk mencegah penyebaran jangkitan dalam tetapan penjagaan kesihatan.
Produk Pengguna dan Pengacuan Suntikan Plastik
Pengacuan suntikan plastik digunakan secara meluas dalam pengeluaran produk pengguna kerana kepelbagaian, kecekapan dan keberkesanan kosnya. Proses pengacuan suntikan plastik membolehkan penghasilan bentuk kompleks dengan ketepatan dan ketepatan yang tinggi, menjadikannya kaedah pembuatan yang ideal untuk banyak aplikasi pengguna. Berikut ialah beberapa cara pengacuan suntikan plastik digunakan dalam pengeluaran produk pengguna:
- Mainan: Pengacuan suntikan plastik menghasilkan pelbagai jenis mainan, daripada patung kecil kepada set mainan yang lebih besar. Proses ini membolehkan untuk mencipta reka bentuk dan butiran yang rumit dan membuat mainan dalam pelbagai warna dan bahan.
- Barangan isi rumah: Pengacuan suntikan plastik menghasilkan pelbagai barangan isi rumah, termasuk peralatan dapur, bekas penyimpanan dan bekalan pembersihan. Produk ini boleh direka bentuk untuk tahan lama, ringan dan mudah digunakan.
- Elektronik: Pengacuan suntikan plastik menghasilkan banyak komponen elektronik, termasuk perumah komputer, sarung telefon dan pengecas. Ketepatan dan ketepatan proses memastikan bahawa komponen ini dibuat dengan tahap ketekalan dan kebolehpercayaan yang tinggi.
- Produk penjagaan diri: Pengacuan suntikan plastik menghasilkan produk penjagaan yang unik, termasuk berus gigi, pencukur dan berus rambut. Produk ini memerlukan ketepatan dan ketepatan yang tinggi untuk memastikan kemudahan penggunaan dan keselamatan.
- Aksesori automotif: Pengacuan suntikan plastik menghasilkan pelbagai aksesori automotif, termasuk komponen papan pemuka, pemegang cawan dan banyak lagi. Komponen ini boleh direka bentuk untuk menjadi ringan, tahan lama dan tahan terhadap haus dan lusuh penggunaan harian.
Pertimbangan Alam Sekitar dalam Pengacuan Suntikan Plastik
Pengacuan suntikan plastik ialah proses pembuatan yang digunakan secara meluas tetapi mempunyai implikasi alam sekitar yang ketara. Berikut adalah beberapa pertimbangan ekologi dalam pengacuan suntikan plastik:
- Pemilihan bahan: Pilihan bahan plastik yang digunakan dalam pengacuan suntikan boleh memberi kesan kepada alam sekitar dengan ketara. Sesetengah bahan boleh terbiodegradasi atau boleh dikitar semula, manakala yang lain tidak. Menggunakan bahan biodegradasi atau kitar semula boleh membantu mengurangkan kesan alam sekitar pengacuan suntikan plastik.
- Penggunaan tenaga: Pengacuan suntikan plastik memerlukan tenaga yang ketara untuk mencairkan plastik dan menyuntiknya ke dalam acuan. Peralatan dan proses yang cekap tenaga, seperti mesin elektrik dan sistem gelung tertutup, boleh mengurangkan penggunaan tenaga dan kesan alam sekitar.
- Pengurusan sisa: Pengacuan suntikan plastik menjana sisa daripada bahan berlebihan, bahagian yang rosak dan pembungkusan. Amalan pengurusan sisa yang betul, seperti kitar semula dan menggunakan semula bahan buangan, boleh membantu mengurangkan kesan persekitaran pengacuan suntikan plastik.
- Penggunaan kimia: Sesetengah bahan kimia dalam acuan suntikan plastik, seperti agen pelepas acuan dan pelarut pembersih, boleh membahayakan alam sekitar. Menggunakan alternatif mesra alam atau meminimumkan penggunaan bahan kimia ini boleh membantu mengurangkan kesan alam sekitar.
- Pertimbangan akhir hayat: Produk plastik yang dihasilkan melalui pengacuan suntikan selalunya berakhir di tapak pelupusan sampah, yang boleh mengambil masa ratusan tahun untuk merosot. Mereka bentuk produk untuk kebolehkitar semula atau kebolehbiodegradan boleh mengurangkan kesan alam sekitar pengacuan suntikan plastik.
Masa Depan Pengacuan Suntikan Plastik
Masa depan pengacuan suntikan plastik kelihatan menjanjikan, kerana kemajuan dalam teknologi dan bahan dijangka menjadikan proses itu lebih cekap, kos efektif dan mampan. Berikut ialah beberapa trend dan perkembangan yang mungkin membentuk masa depan pengacuan suntikan plastik:
- Pengilangan aditif: Pengilangan aditif, juga dikenali sebagai percetakan 3D, ialah teknologi baru muncul yang berpotensi mengubah pengacuan suntikan plastik. Dengan menggunakan percetakan 3D untuk mencipta acuan, pengeluar boleh mengurangkan masa dan kos yang berkaitan dengan teknik membuat acuan tradisional dengan ketara.
- Pembuatan pintar: Pembuatan pintar, yang melibatkan automasi, analisis data dan pembelajaran mesin, dijangka merevolusikan pengacuan suntikan plastik. Pengilang boleh meningkatkan kecekapan, mengurangkan pembaziran dan meningkatkan produktiviti dengan menggunakan penderia dan analitik data untuk mengoptimumkan proses.
- Bahan lestari: Bahan lestari, seperti bioplastik dan plastik kitar semula, menjadi semakin popular dalam industri pengacuan suntikan plastik. Bahan ini menawarkan faedah alam sekitar dan boleh membantu pengilang untuk mencapai matlamat kemampanan.
- Pengacuan mikro: Pengacuan mikro, yang melibatkan pengeluaran bahagian kecil dengan ketepatan tinggi, menjadi lebih kritikal dalam industri seperti penjagaan kesihatan dan elektronik. Kemajuan dalam teknologi dan bahan dijangka menjadikan pengacuan mikro lebih mudah diakses dan menjimatkan kos.
- Penyesuaian: Memandangkan pengguna menuntut lebih banyak produk yang diperibadikan, pengacuan suntikan plastik dijangka menjadi lebih fleksibel dan boleh disesuaikan. Kemajuan dalam teknologi, seperti maklum balas masa nyata dan pembelajaran mesin, akan membolehkan pengeluar menghasilkan produk tersuai dengan cepat dan cekap.
Kesimpulan:
Pengacuan suntikan plastik ialah proses pembuatan yang sangat serba boleh dan cekap yang telah merevolusikan pengeluaran pelbagai produk. Daripada peranti perubatan kepada komponen automotif, pengacuan suntikan plastik menawarkan banyak kelebihan berbanding proses pembuatan lain, termasuk kadar pengeluaran yang tinggi, fleksibiliti reka bentuk dan keberkesanan kos. Dengan kemajuan berterusan dalam teknologi dan bahan, masa depan pengacuan suntikan plastik kelihatan cerah, dan proses ini mungkin akan memainkan peranan yang lebih penting dalam industri pembuatan pada tahun-tahun akan datang.