Pengacuan Suntikan Termoplastik
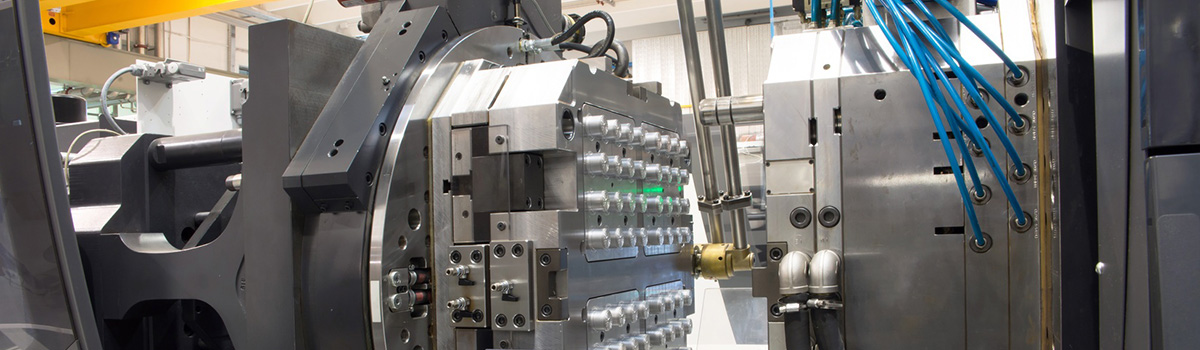
Pengacuan suntikan termoplastik ialah proses pembuatan popular yang digunakan untuk mencipta pelbagai bahagian plastik untuk pelbagai industri. Proses ini melibatkan peleburan plastik pelet dan menyuntiknya ke dalam acuan untuk menghasilkan bentuk tiga dimensi. Pengacuan suntikan termoplastik sangat cekap dan menjimatkan kos untuk menghasilkan bahagian plastik berkualiti tinggi dalam jumlah besar dengan toleransi yang ketat. Panduan komprehensif ini akan meneroka pelbagai aspek pengacuan suntikan termoplastik, termasuk kelebihan dan kekurangannya, jenis termoplastik yang digunakan, proses pengacuan suntikan, pertimbangan reka bentuk dan banyak lagi.
Sejarah Pengacuan Suntikan Termoplastik
Sejarah pengacuan suntikan termoplastik menjangkau lebih satu abad kemajuan teknologi, perkembangan bahan dan aplikasi perindustrian. Dari permulaannya yang sederhana sebagai proses pengacuan seluloid kepada teknologi canggih masa kini, pengacuan suntikan terus menjadi teknik pembuatan yang penting, memacu inovasi dan membentuk pelbagai industri.
- Perkembangan Awal:John Wesley Hyatt dan abangnya Isaiah membangunkan mesin pengacuan suntikan praktikal yang pertama, menjejaki asal-usul pengacuan suntikan termoplastik kembali ke penghujung abad ke-19. Pada tahun 1872, mereka mempatenkan peranti yang menggunakan pelocok untuk menyuntik seluloid ke dalam rongga acuan, mencipta objek pepejal. Kejayaan ini meletakkan asas untuk proses pengacuan suntikan moden.
- Kemajuan dalam Bahan:Pada awal abad ke-20, memperkenalkan polimer sintetik baru membuka kemungkinan baru untuk pengacuan suntikan. Bakelite, resin fenolik, menjadi bahan yang popular untuk pengacuan kerana sifat penebat elektrik yang sangat baik. Sepanjang tahun 1930-an dan 1940-an, kemajuan dalam kimia polimer membawa kepada pembangunan termoplastik lain, seperti polistirena dan polietilena, yang meluaskan lagi rangkaian bahan yang sesuai untuk pengacuan suntikan.
- Penggunaan Industri: Penerimaan meluas pengacuan suntikan termoplastik bermula pada tahun 1950-an apabila pengeluar mengiktiraf keberkesanan kos dan serba boleh. Memperkenalkan mesin tekanan tinggi dibenarkan untuk masa kitaran yang lebih cepat dan meningkatkan jumlah pengeluaran. Hasilnya, pelbagai pilihan produk untuk kegunaan peribadi dan industri telah wujud. Ini termasuk komponen kereta, peralatan rumah dan alat permainan.
- Inovasi Teknologi:Sepanjang beberapa dekad, teknologi pengacuan suntikan terus berkembang. Pada tahun 1960-an, mesin terkawal komputer muncul, membolehkan kawalan tepat ke atas proses pengacuan. Pengenalan sistem pelari panas pada tahun 1980-an mengurangkan sisa dan meningkatkan kecekapan dengan menghapuskan keperluan untuk pelari dan sprue. Dalam beberapa tahun kebelakangan ini, kemajuan automasi, robotik dan pencetakan 3D telah merevolusikan lagi industri pengacuan suntikan, membolehkan reka bentuk yang kompleks dan mengurangkan masa pengeluaran.
- Kemampanan dan Kitar Semula:Dengan kebimbangan alam sekitar yang semakin meningkat, industri pengacuan suntikan telah menerima langkah kemampanan. Pengilang telah membangunkan termoplastik berasaskan bio dan kitar semula, mengurangkan pergantungan pada bahan berasaskan bahan api fosil. Selain itu, teknologi kitar semula yang dipertingkatkan telah membolehkan pemprosesan semula sisa pasca pengguna dan pasca industri, meminimumkan kesan alam sekitar pengacuan suntikan termoplastik.
- Prospek Masa Depan:Masa depan pengacuan suntikan termoplastik kelihatan menjanjikan. Industri sedang meneroka inovasi seperti pengacuan suntikan mikro untuk komponen kecil, teknik berbilang bahan dan acuan untuk bahagian yang kompleks, dan menyepadukan teknologi pintar untuk pemantauan dan pengoptimuman proses. Tambahan pula, penyelidik menjangkakan kemajuan dalam bahan terbiodegradasi dan pembuatan aditif untuk merevolusikan bidang tersebut, menjadikan pengacuan suntikan lebih mampan dan serba boleh.
Kelebihan Pengacuan Suntikan Termoplastik
Pengacuan suntikan termoplastik menawarkan banyak kelebihan untuk pengilang. Ia menyediakan fleksibiliti reka bentuk, membolehkan reka bentuk yang kompleks dan rumit dengan pelbagai ciri. Proses ini menjimatkan kos, mengurangkan sisa bahan dan mengurangkan kos unit. Pengacuan suntikan termoplastik menyokong pelbagai bahan, menyediakan serba boleh untuk aplikasi yang berbeza.
- Fleksibiliti Reka Bentuk:Pengacuan suntikan termoplastik membolehkan reka bentuk yang rumit dan kompleks dengan ciri seperti potongan bawah, dinding nipis dan ketebalan yang berbeza-beza, memberikan pereka kebebasan yang besar.
- Kecekapan Kos: Proses ini sangat cekap, mengurangkan sisa bahan dan mengurangkan kos unit. Pengacuan serentak pelbagai bahagian dan kitaran pengeluaran pantas menyumbang kepada penjimatan kos.
- Kepelbagaian Bahan: Pengacuan suntikan termoplastik menyokong pelbagai jenis bahan, membolehkan pengeluar memilih pilihan yang paling sesuai untuk setiap aplikasi, termasuk bahan tegar atau fleksibel, lutsinar atau legap dan tahan kimia.
- Kekuatan dan Ketahanan:Termoplastik acuan suntikan boleh mempamerkan sifat mekanikal yang sangat baik, seperti kekuatan tinggi, keliatan dan rintangan hentaman. Pilihan tetulang, seperti gentian kaca atau karbon, meningkatkan lagi sifat ini.
- Ketekalan dan Kualiti:Pengacuan suntikan memastikan kualiti bahagian-ke-bahagian yang konsisten dan ketepatan dimensi, memberikan toleransi yang ketat dan produk yang boleh dipercayai. Proses ini juga menyediakan kemasan permukaan yang licin dan seragam, menghapuskan keperluan untuk operasi kemasan tambahan.
- Kebolehskalaan dan Pengeluaran Besar-besaran:Pengacuan suntikan boleh berskala daripada volum rendah ke tinggi, menjadikannya sesuai untuk pengeluaran besar-besaran. Sebaik sahaja pengeluar mencipta acuan, mereka boleh menghasilkan kuantiti yang banyak bahagian yang sama dengan variasi yang minimum.
- Integrasi dan Perhimpunan:Bahagian acuan suntikan boleh menggabungkan beberapa komponen ke dalam satu bahagian, mengurangkan keperluan untuk proses pemasangan tambahan. Penyepaduan ini meningkatkan prestasi produk, mengurangkan masa pemasangan dan mengurangkan kos.
- Kemapanan:Industri pengacuan suntikan menunjukkan tumpuan yang semakin meningkat terhadap kemampanan. Ketersediaan bahan berasaskan bio dan kitar semula membolehkan untuk menghasilkan produk mesra alam. Penggunaan bahan yang cekap dan kebolehkitar semula termoplastik menyumbang kepada proses pembuatan yang lebih hijau.
Faedah ini telah menjadikannya kaedah pembuatan yang diterima pakai secara meluas merentasi pelbagai industri, menyediakan penyelesaian berkualiti tinggi, kos efektif dan mesra alam untuk keperluan produk yang kompleks.
Kelemahan Pengacuan Suntikan Termoplastik
Walaupun pengacuan suntikan termoplastik menawarkan banyak kelebihan, terdapat juga beberapa kelemahan. Pengilang perlu menilai dengan teliti faktor-faktor ini dan menimbangnya dengan faedah untuk menentukan kesesuaian pengacuan suntikan termoplastik untuk aplikasi khusus mereka.
- Pelaburan Permulaan yang Tinggi: Menyediakan operasi pengacuan suntikan termoplastik memerlukan pelaburan awal yang ketara dalam reka bentuk acuan dan fabrikasi serta pembelian jentera khusus. Kos yang berkaitan dengan mencipta acuan dan perkakas boleh menjadi besar, terutamanya untuk reka bentuk yang kompleks dan rumit.
- Had Reka Bentuk: Walaupun pengacuan suntikan termoplastik menawarkan fleksibiliti reka bentuk, batasan tertentu wujud. Sebagai contoh, mencapai ketebalan dinding yang seragam di seluruh bahagian boleh mencabar, yang membawa kepada variasi dalam pengedaran bahan dan potensi kelemahan struktur. Selain itu, kehadiran potongan bawah atau geometri kompleks mungkin memerlukan penggunaan ciri acuan tambahan atau operasi sekunder, meningkatkan kos dan masa pengeluaran.
- Masa Memimpin yang Panjang:Proses mereka bentuk dan membuat acuan untuk pengacuan suntikan boleh memakan masa, yang membawa kepada masa memimpin yang lebih lama untuk pembangunan produk. Proses lelaran reka bentuk, pengeluaran acuan dan ujian boleh menambah masa yang ketara pada garis masa pengeluaran keseluruhan, yang mungkin tidak sesuai untuk projek dengan tarikh akhir yang ketat.
- Kekangan Pemilihan Bahan:Walaupun pengacuan suntikan termoplastik menyokong pelbagai jenis bahan, terdapat batasan dan kekangan tertentu. Sesetengah bahan mungkin mempunyai keperluan pemprosesan khusus atau ketersediaan terhad, memberi kesan kepada pilihan reka bentuk dan pemilihan bahan untuk aplikasi tertentu.
- Had Saiz Bahagian:Mesin pengacuan suntikan mempunyai had saiz, baik dari segi saiz fizikal peranti dan saiz acuan yang boleh mereka tampung. Menghasilkan bahagian yang besar mungkin memerlukan peralatan khusus atau kaedah pembuatan alternatif.
- Kesan alam sekitar:Walaupun industri sedang berusaha ke arah kemampanan, proses pengacuan suntikan termoplastik masih menghasilkan bahan buangan, termasuk sekerap dan sprue. Pelupusan dan kitar semula yang betul bagi bahan-bahan ini adalah perlu untuk meminimumkan kesan alam sekitar.
- Kerumitan Pengoptimuman Proses:Mencapai parameter proses optimum untuk pengacuan suntikan termoplastik boleh menjadi rumit dan memakan masa. Pengilang mesti mengawal dan mengoptimumkan suhu, tekanan, kadar penyejukan dan masa kitaran dengan teliti untuk memastikan kualiti bahagian yang konsisten dan meminimumkan kecacatan.
Jenis Termoplastik yang Digunakan dalam Pengacuan Suntikan
Ini hanyalah beberapa contoh termoplastik yang biasa digunakan dalam pengacuan suntikan. Setiap bahan mempunyai sifat unik, menjadikannya sesuai untuk aplikasi khusus berdasarkan kekuatan, fleksibiliti, rintangan kimia, ketelusan dan kos. Pengilang harus mempertimbangkan sifat dan keperluan ini apabila memilih termoplastik yang sesuai untuk projek pengacuan suntikan mereka.
- Polipropilena (PP):Polipropilena ialah termoplastik serba boleh yang biasa digunakan dalam pengacuan suntikan. Ia menawarkan rintangan kimia yang sangat baik, ketumpatan rendah, dan kekuatan impak yang baik. PP (polipropilena) mempunyai aplikasi yang luas dalam pembungkusan, komponen automotif, perkakas rumah dan peranti perubatan.
- Polietilena (PE):Polietilena adalah satu lagi termoplastik yang digunakan secara meluas dalam pengacuan suntikan. Ia boleh didapati dalam pelbagai bentuk, seperti polietilena berketumpatan tinggi (HDPE) dan polietilena berketumpatan rendah (LDPE). PE menawarkan rintangan kimia yang baik, keliatan dan fleksibiliti, menjadikannya sesuai untuk botol, bekas dan paip.
- Polistirena (PS):Polistirena ialah termoplastik serba boleh yang terkenal dengan kejelasan, ketegaran dan keterjangkauannya. Ia mendapati penggunaan biasa dalam pembungkusan, barangan pengguna dan produk pakai buang. PS (polistirena) membolehkan pemprosesan cepat dan memberikan kestabilan dimensi yang baik, tetapi ia boleh rapuh dan terdedah kepada keretakan tekanan persekitaran.
- Akrilonitril Butadiene Stirena (ABS): ABS ialah termoplastik popular yang terkenal dengan rintangan hentaman dan ketahanan yang sangat baik. Ia menggabungkan sifat akrilonitril, butadiena dan stirena untuk mencipta bahan serba boleh yang sesuai untuk bahagian automotif, perumah elektronik dan mainan.
- Polivinil Klorida (PVC): PVC ialah termoplastik yang digunakan secara meluas yang terkenal dengan rintangan kimia yang sangat baik, ketahanan, dan kos rendah. Ia boleh menjadi tegar atau fleksibel bergantung pada formulasi dan bahan tambahan yang digunakan. PVC (polivinil klorida) menemui kegunaan biasa dalam pembinaan, penebat elektrik, produk penjagaan kesihatan dan pembungkusan.
- Polikarbonat (PC): Polikarbonat ialah termoplastik lutsinar dengan impak luar biasa dan rintangan haba yang tinggi. Ia menemui penggunaan biasa dalam aplikasi yang memerlukan kejelasan optik, seperti komponen automotif, topi keledar keselamatan dan paparan elektronik.
- Nilon (Poliamida):Nylon ialah termoplastik yang kuat dan tahan lama yang terkenal dengan sifat mekanikal yang sangat baik dan rintangan kimia. Ia menemui penggunaan biasa dalam aplikasi yang menuntut kekuatan tinggi, seperti bahagian automotif, komponen industri dan barangan pengguna.
- Polietilena Tereftalat (PET):PET ialah termoplastik yang popular untuk menghasilkan botol, bekas dan bahan pembungkusan. Ia menawarkan kejelasan yang baik, rintangan kimia dan sifat penghalang, menjadikannya sesuai untuk aplikasi makanan dan minuman.
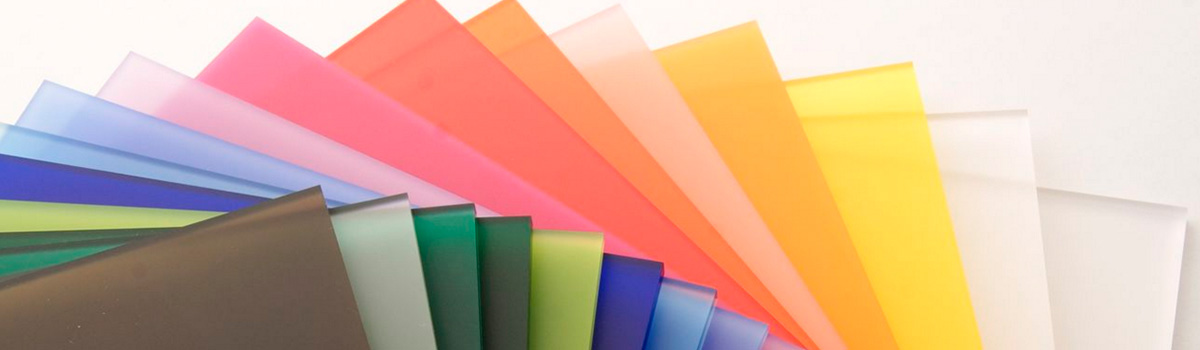
Sifat Termoplastik yang Digunakan dalam Pengacuan Suntikan
Sifat termoplastik ini memainkan peranan penting dalam menentukan kesesuaian mereka untuk aplikasi pengacuan suntikan tertentu. Pengilang mesti mempertimbangkan dengan teliti sifat-sifat ini dan memilih termoplastik yang sesuai berdasarkan prestasi yang diingini, keadaan persekitaran dan keperluan kos.
- Sifat Mekanikal:Termoplastik yang digunakan dalam pengacuan suntikan boleh mempamerkan pelbagai sifat mekanikal, termasuk kekuatan tegangan, rintangan hentaman dan kekuatan lentur. Sifat-sifat ini menentukan keupayaan bahan untuk menahan daya yang dikenakan dan ketahanan keseluruhannya dalam pelbagai aplikasi.
- Rintangan Kimia:Banyak termoplastik yang digunakan dalam pengacuan suntikan mempunyai ketahanan yang luar biasa terhadap bahan kimia, pelarut, dan minyak. Sifat ini penting untuk aplikasi yang melibatkan pendedahan kepada persekitaran yang keras atau bahan menghakis.
- Kestabilan Terma:Kestabilan terma termoplastik merujuk kepada keupayaan mereka untuk menahan suhu tinggi tanpa degradasi yang ketara. Sesetengah termoplastik mempamerkan rintangan haba yang sangat baik, membolehkan mereka mengekalkan sifat mekanikalnya walaupun pada suhu tinggi.
- Sifat Elektrik:Termoplastik yang digunakan dalam pengacuan suntikan boleh mempunyai sifat elektrik tertentu, termasuk penebat elektrik, kekonduksian, atau kekuatan dielektrik. Sifat ini penting untuk aplikasi dalam industri elektrik dan elektronik, di mana bahan mesti memberikan prestasi elektrik yang boleh dipercayai.
- Ketelusan dan Kejelasan:Termoplastik tertentu, seperti polikarbonat dan PET, menawarkan ketelusan dan kejelasan yang sangat baik, menjadikannya sesuai untuk aplikasi yang memerlukan sifat optik. Pengilang biasanya menggunakan bahan ini dalam produk seperti tingkap lutsinar, kanta dan paparan.
- Fleksibiliti dan Ketangguhan: Fleksibiliti dan keliatan adalah sifat penting termoplastik yang digunakan dalam aplikasi yang memerlukan rintangan hentaman dan ketahanan. Sesetengah termoplastik, seperti ABS dan nilon, menawarkan keliatan yang sangat baik, membolehkan mereka menahan hentaman berulang tanpa pecah.
- Kestabilan dimensi:Kestabilan dimensi merujuk kepada keupayaan termoplastik untuk mengekalkan bentuk dan saiznya dalam keadaan yang berbeza-beza, termasuk perubahan suhu. Bahan dengan kestabilan dimensi yang baik memastikan dimensi bahagian yang konsisten, meminimumkan risiko meledingkan atau herotan.
- Keserasian Kimia:Keserasian kimia termoplastik merujuk kepada keupayaan mereka untuk menentang degradasi atau interaksi dengan pelbagai bahan kimia, termasuk asid, bes dan pelarut. Untuk memastikan prestasi optimum, memilih termoplastik yang boleh menahan persekitaran kimia tertentu yang akan ditemui dalam aplikasi yang dimaksudkan adalah penting.
- Kepadatan: Termoplastik mempunyai ketebalan yang berbeza-beza, yang boleh memberi kesan kepada berat dan sifat bahagian keseluruhannya. Bahan berketumpatan rendah, seperti polietilena, menawarkan penyelesaian ringan, manakala bahan berketumpatan tinggi, seperti polipropilena, memberikan kekuatan dan ketegaran tambahan.
Proses Pengacuan Suntikan: Langkah demi Langkah
Proses pengacuan suntikan mengikut langkah-langkah ini, membolehkan pengeluaran bahagian termoplastik berkualiti tinggi yang cekap dan tepat. Setiap langkah memerlukan kawalan dan pemantauan yang teliti untuk memastikan dimensi bahagian, sifat bahan dan kualiti keseluruhan yang konsisten.
- Reka bentuk dan Fabrikasi Acuan: Langkah pertama dalam proses pengacuan suntikan ialah reka bentuk dan fabrikasi acuan. Pengilang mesti mencipta reka bentuk acuan yang tepat dan terperinci untuk mencapai spesifikasi bahagian yang dikehendaki. Pengilang kemudian membuat acuan menggunakan pelbagai teknik, seperti CNC atau pemesinan nyahcas elektrik (EDM).
- Penyediaan Bahan: Langkah seterusnya ialah penyediaan setelah acuan siap. Pelet termoplastik atau butiran dipilih berdasarkan sifat bahan yang dikehendaki dan dicairkan dalam corong. Operator kemudian menyuap bahan ke dalam tong mesin pengacuan suntikan, di mana ia mengalami lebur dan homogenisasi.
- Suntikan:Semasa fasa suntikan, pengendali menyuntik termoplastik cair ke dalam rongga acuan di bawah tekanan tinggi. Unit suntikan mesin menolak bahan cair melalui muncung dan masuk ke dalam acuan. Bahan mengisi rongga acuan, mengambil bentuk bahagian yang dikehendaki.
- Penyejukan dan Pemejalan:Selepas mengisi acuan, pengendali membenarkan plastik cair menyejuk dan memejal. Penyejukan adalah penting untuk mencapai kestabilan dimensi dan pembentukan bahagian yang betul. Operator boleh mengawal proses penyejukan dengan mengedarkan penyejuk melalui saluran dalam acuan atau dengan menggunakan plat penyejuk.
- Pembukaan dan Pelepasan Acuan:Operator membuka acuan dan mengeluarkan bahagian dari rongga acuan sebaik sahaja plastik mengeras. Sistem lontar dalam mesin menggunakan pin, plat ejektor, atau letupan udara untuk mengeluarkan kawasan daripada acuan. Acuan kemudiannya sedia untuk kitaran suntikan seterusnya.
- Pemprosesan Selepas: Selepas lontar, bahagian itu mungkin menjalani operasi pasca pemprosesan, seperti pemangkasan, deburring, atau kemasan permukaan. Langkah-langkah ini membantu mengeluarkan bahan berlebihan, licin tepi kasar dan menambah baik penampilan akhir bahagian.
- Pemeriksaan Kualiti: Langkah terakhir melibatkan pemeriksaan bahagian yang disuntik untuk kualiti dan memastikan ia memenuhi keperluan yang ditetapkan. Pelbagai teknik kawalan kualiti, termasuk pengukuran dimensi, pemeriksaan visual, dan ujian kefungsian, boleh digunakan untuk mengesahkan kualiti dan integriti bahagian tersebut.
- Kitar Semula dan Penggunaan Semula Bahan:Sebarang lebihan atau bahan sekerap yang dihasilkan semasa pengacuan suntikan boleh dikitar semula dan digunakan semula. Mengurangkan penggunaan bahan termoplastik baharu membantu meminimumkan sisa dan meningkatkan kemampanan.
Peralatan yang Digunakan dalam Pengacuan Suntikan
Komponen peralatan ini memudahkan proses pengacuan suntikan, daripada mencairkan dan menyuntik bahan termoplastik kepada membentuk, menyejukkan dan mengeluarkan bahagian akhir. Operasi dan penyelenggaraan yang betul bagi komponen peralatan ini adalah penting untuk mencapai pengeluaran acuan suntikan yang cekap dan berkualiti tinggi.
- Mesin Pengacuan Suntikan:Peralatan utama dalam pengacuan suntikan bertanggungjawab untuk mencairkan bahan termoplastik, menyuntiknya ke dalam acuan, dan mengawal proses.
- Acuan: Acuan, direka khas untuk mencipta bentuk dan ciri bahagian plastik yang diingini, terdiri daripada dua bahagian, rongga dan teras. Operator memasangnya pada unit pengapit mesin pengacuan suntikan.
- Hopper:Bekas yang menyimpan bahan termoplastik dalam bentuk pelet atau berbutir dan memasukkannya ke dalam tong mesin pengacuan suntikan untuk mencairkan dan menyuntik.
- Tong dan Skru: Tong, ruang silinder, mencairkan dan menghomogenkan bahan termoplastik apabila skru berputar di dalamnya untuk mencairkan, mencampur dan menyeragamkan bahan.
- Sistem Pemanasan dan Penyejukan:Mesin pengacuan suntikan mempunyai elemen pemanasan, seperti pemanas elektrik atau pemanas menggunakan minyak panas, untuk menaikkan suhu tong, dan sistem penyejukan, seperti peredaran air atau minyak, untuk menyejukkan acuan dan memejalkan bahagian plastik.
- Sistem Ejector:Mengeluarkan bahagian acuan dari rongga acuan selepas pemejalan, biasanya menggunakan pin ejektor, plat atau letupan udara semasa pembukaan acuan.
- Sistem kawalan:Memantau dan mengawal pelbagai parameter proses pengacuan suntikan, membolehkan pengendali menetapkan dan melaraskan parameter seperti kelajuan suntikan, suhu, tekanan dan masa penyejukan.
Mesin Pengacuan Suntikan: Jenis dan Ciri
Setiap jenis mesin pengacuan suntikan mempunyai ciri dan kelebihannya, membolehkan pengeluar memilih peranti yang paling sesuai untuk keperluan pengeluaran khusus mereka.
- Mesin Pengacuan Suntikan Hidraulik: Mesin ini menggunakan sistem hidraulik untuk menjana tekanan yang diperlukan untuk menyuntik plastik cair ke dalam acuan. Mereka terkenal dengan daya pengapit yang tinggi, kawalan yang tepat dan serba boleh dalam mengendalikan pelbagai termoplastik. Mesin hidraulik sesuai untuk pengeluaran berskala besar dan boleh menampung acuan yang kompleks.
- Mesin Pengacuan Suntikan Elektrik:Mesin elektrik menggunakan motor servo elektrik untuk operasi mesin, termasuk sistem suntikan, pengapit dan ejektor. Mereka menawarkan kawalan yang tepat, kecekapan tenaga dan masa tindak balas yang lebih pantas daripada mesin hidraulik. Mesin elektrik sesuai untuk aplikasi pengacuan ketepatan yang memerlukan kebolehulangan dan ketepatan yang tinggi.
- Mesin Pengacuan Suntikan Hibrid:Mesin hibrid menggabungkan faedah kedua-dua peranti hidraulik dan elektrik. Mereka menggunakan gabungan sistem servo hidraulik dan elektrik untuk mencapai ketepatan tinggi, kecekapan tenaga dan keberkesanan kos. Mesin hibrid sesuai untuk pelbagai aplikasi, memberikan keseimbangan antara prestasi dan kos operasi.
- Mesin Pengacuan Suntikan Dua Plat: Mesin dua plat mempunyai reka bentuk yang unik dengan dua plat berasingan untuk mengapit acuan. Reka bentuk ini memberikan kestabilan yang dipertingkatkan, penyegerakan acuan yang lebih baik dan membolehkan saiz acuan yang lebih besar dan daya pengapit yang lebih tinggi. Mesin dua plat sesuai untuk bahagian yang besar dan kompleks yang memerlukan pengacuan yang tepat.
- Mesin Pengacuan Suntikan Berbilang Komponen:Pengilang mereka bentuk mesin ini untuk menghasilkan bahagian dengan pelbagai bahan atau warna dalam satu kitaran pengacuan. Mereka mempunyai pelbagai unit suntikan dan acuan, membolehkan suntikan serentak bahan berbeza. Mesin berbilang komponen menawarkan fleksibiliti dan kecekapan dalam pembuatan bahagian kompleks dengan ciri yang berbeza-beza.
- Mesin Pengacuan Suntikan Mikro:Direka khusus untuk menghasilkan bahagian yang kecil dan tepat, mesin pengacuan suntikan mikro menawarkan ketepatan dan ketepatan yang sangat tinggi. Mereka boleh menghasilkan butiran yang rumit dengan toleransi yang ketat dan sisa bahan yang minimum. Elektronik, peranti perubatan dan mikro-optik biasanya menggunakan mesin pengacuan suntikan mikro.
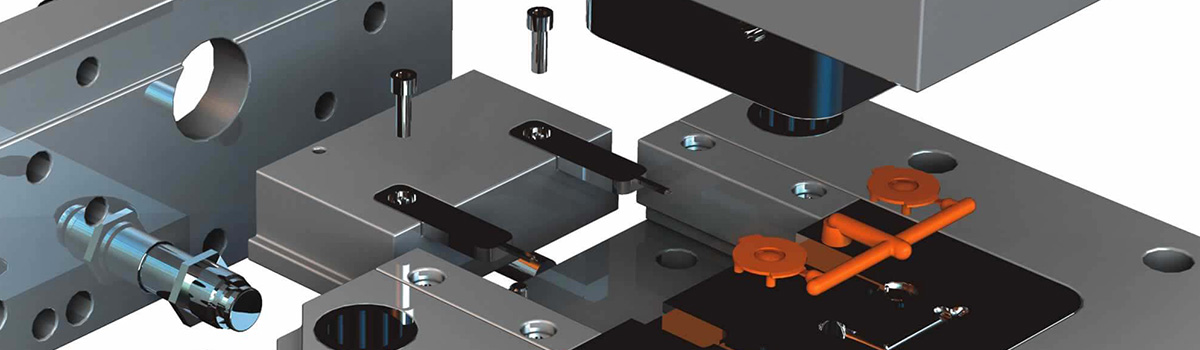
Pertimbangan Reka Bentuk Acuan untuk Pengacuan Suntikan
Pertimbangan reka bentuk acuan yang teliti adalah penting untuk penghasilan acuan suntikan yang berjaya.
- Reka Bentuk Bahagian:Reka bentuk acuan harus menampung keperluan khusus bahagian, termasuk bentuk, dimensi, dan ciri fungsinya. Pengilang harus mempertimbangkan dengan betul sudut draf, ketebalan dinding, potongan bawah, dan sebarang elemen yang diperlukan untuk memastikan kemudahan pelepasan dan kualiti bahagian.
- Bahan acuan: Pemilihan bahan acuan adalah penting untuk mencapai ketahanan, kestabilan dimensi, dan rintangan haba. Bahan acuan biasa termasuk aloi keluli, aloi aluminium dan keluli alat. Pilihan bahan bergantung pada faktor seperti volum pengeluaran, kerumitan bahagian, dan jangka hayat alat.
- Sistem penyejuk:Penyejukan yang cekap adalah penting untuk pemejalan bahagian yang betul dan meminimumkan masa kitaran. Reka bentuk acuan harus menggabungkan saluran penyejukan atau sisipan yang diposisikan secara strategik untuk memastikan penyejukan acuan seragam. Penyejukan yang betul mengurangkan risiko melengkung, pengecutan, dan kecacatan bahagian.
- Pengudaraan:Pembuangan yang mencukupi adalah perlu untuk membolehkan udara dan gas keluar semasa proses suntikan. Pembuangan yang tidak mencukupi boleh menyebabkan perangkap gas, kesan terbakar, atau pengisian bahagian yang tidak lengkap. Pengilang boleh mencapai pengudaraan dengan memasukkan alur pengudaraan, pin atau mekanisme lain ke dalam reka bentuk acuan.
- Sistem Ejection:Reka bentuk acuan harus merangkumi sistem lenting yang berkesan untuk mengeluarkan bahagian acuan dari rongga acuan dengan selamat dan cekap. Sistem lenting boleh terdiri daripada pin ejektor, lengan atau mekanisme lain, diposisikan secara strategik untuk mengelakkan gangguan terhadap fungsi atau ciri kritikal.
- Reka Bentuk Pintu:Pintu adalah tempat plastik cair memasuki rongga acuan. Reka bentuk pagar harus memastikan pengisian bahagian yang betul, meminimumkan garis aliran, dan mencegah pembekuan bahan pramatang. Reka bentuk gerbang standard termasuk pintu tepi, pintu terowong dan sistem pelari panas, bergantung pada keperluan bahagian dan sifat bahan.
- Garis Perpisahan:Reka bentuk acuan harus menentukan garis perpisahan yang sesuai, iaitu garisan di mana kedua-dua bahagian acuan bersatu. Peletakan garis perpisahan yang betul memastikan ketidakpadanan denyar dan garis perpisahan yang minimum serta memudahkan pemasangan acuan yang cekap.
- Penyelenggaraan Acuan dan Kebolehgunaan: Pengilang harus mempertimbangkan kemudahan penyelenggaraan, pembaikan dan servis acuan. Komponen acuan hendaklah mudah diakses untuk pembersihan, pemeriksaan dan penggantian. Menggabungkan ciri seperti sisipan perubahan pantas atau reka bentuk acuan modular boleh meningkatkan kebolehgunaan acuan.
Bahan Acuan Digunakan dalam Pengacuan Suntikan
Bekerjasama dengan pakar bahan acuan dan mempertimbangkan keperluan khusus aplikasi acuan boleh membantu menentukan bahan yang paling sesuai untuk mencapai prestasi acuan dan kualiti bahagian yang optimum.
- Aloi Keluli: Aloi keluli, seperti keluli alat (cth, P20, H13) dan keluli tahan karat, biasanya digunakan untuk acuan pengacuan suntikan kerana ketahanannya yang sangat baik, rintangan haba dan rintangan haus. Bahan ini boleh menahan suhu dan tekanan tinggi dalam proses pengacuan suntikan dan menawarkan kestabilan dimensi yang baik untuk menghasilkan bahagian berkualiti tinggi.
- Aloi aluminium:Aloi aluminium, seperti 7075 dan 6061, adalah ringan dan menawarkan kekonduksian terma yang baik, menjadikannya sesuai untuk acuan yang memerlukan penyejukan yang cekap. Pengilang sering menggunakan acuan aluminium untuk prototaip, pengeluaran volum rendah, atau aplikasi yang mengurangkan berat badan adalah kritikal. Walau bagaimanapun, acuan aluminium mungkin mempunyai ketahanan yang lebih rendah berbanding aloi keluli.
- Aloi Tembaga:Aloi kuprum, seperti kuprum berilium, mempamerkan kekonduksian terma yang tinggi dan kebolehmesinan yang baik. Mereka mendapati penggunaan dalam acuan yang memerlukan pemindahan haba yang sangat baik untuk penyejukan yang berkesan. Aloi kuprum boleh membantu mengurangkan masa kitaran dengan cepat menghilangkan haba dari bahagian yang dibentuk, menghasilkan pemejalan yang lebih cepat.
- Keluli Alat:Keluli alat, termasuk H13, S7, dan D2, direka bentuk untuk aplikasi perkakas berprestasi tinggi. Keluli ini menawarkan gabungan kekuatan tinggi, kekerasan, dan rintangan haus. Keluli alat sesuai dengan acuan dengan jumlah pengeluaran yang tinggi, bahan yang melelas, atau keadaan pengacuan yang menuntut.
- Aloi Nikel:Aloi nikel, seperti Inconel dan Hastelloy, terkenal dengan rintangan kakisan yang luar biasa, kekuatan suhu tinggi dan kestabilan terma. Pengilang menggunakan aloi ini dalam acuan yang mengendalikan bahan menghakis atau memerlukan ketahanan terhadap suhu yang melampau dan persekitaran acuan yang agresif.
- Bahan Komposit:Bahan komposit, seperti plastik bertetulang atau komposit dengan sisipan logam, kadangkala digunakan untuk aplikasi pengacuan tertentu. Bahan-bahan ini menawarkan keseimbangan sifat, seperti kekuatan tinggi, kestabilan terma, dan pengurangan berat. Acuan komposit boleh menjadi alternatif kos efektif untuk keperluan pengeluaran tertentu.
Jenis Acuan Suntikan
Pengacuan suntikan adalah proses pembuatan yang serba boleh dan digunakan secara meluas untuk bahagian plastik.
- Acuan Dua Plat:Acuan dua plat adalah jenis acuan suntikan yang paling biasa. Ia terdiri daripada dua plat, plat rongga, dan plat teras, yang memisahkan untuk membolehkan lonjakan bahagian acuan. Plat rongga mengandungi bahagian rongga acuan, manakala plat teras menempatkan bahagian teras. Pengilang menggunakan acuan dua plat untuk menghasilkan pelbagai bahagian kerana reka bentuknya yang agak mudah.
- Acuan Tiga Plat:Acuan tiga plat adalah versi lanjutan acuan dua plat. Ia termasuk plat tambahan, pelari, atau plat sprue. Plat pelari mencipta saluran berasingan untuk sprue, pelari, dan pintu pagar, membolehkan penyingkiran lebih mudah bahagian acuan. Pengilang biasanya menggunakan acuan tiga plat untuk perincian dengan sistem gating yang kompleks atau apabila mengelak sisa pintu pada bahagian adalah wajar.
- Acuan Pelari Panas:Sistem pelari dan gerbang dipanaskan dalam acuan pelari panas, menghapuskan keperluan untuk pemejalan dan pencairan semula bahan semasa setiap kitaran. Sistem pelari panas terdiri daripada manifold dan muncung yang dipanaskan yang mengekalkan keadaan cair plastik. Acuan pelari panas menawarkan kelebihan seperti mengurangkan masa kitaran, mengurangkan sisa bahan dan kualiti bahagian yang dipertingkatkan dengan meminimumkan sisa pintu.
- Acuan Pelari Sejuk: Acuan pelari sejuk mempunyai sistem pelari dan pintu tradisional di mana plastik cair mengalir melalui pelari sejuk yang menjadi pejal dengan setiap kitaran. Operator kemudiannya mengeluarkan pelari pepejal, mengakibatkan sisa bahan. Pengilang biasanya menggunakan acuan pelari yang kompleks untuk pengeluaran volum yang lebih rendah atau apabila kos bahan kurang kritikal disebabkan reka bentuknya yang lebih mudah.
- Masukkan Acuan:Masukkan acuan memasukkan sisipan logam atau plastik ke dalam rongga acuan semasa pengacuan suntikan. Sisipan boleh diletakkan terlebih dahulu ke dalam acuan atau dimasukkan melalui proses automatik. Acuan ini membolehkan untuk menyepadukan komponen tambahan atau elemen pengukuhan ke dalam bahagian acuan, meningkatkan fungsi atau kekuatannya.
- Overacuan: Pengacuan berlebihan melibatkan pengacuan satu bahan di atas bahan lain, biasanya mengikat substrat plastik tegar dengan elastomer atau termoplastik yang lebih lembut. Proses ini membolehkan penciptaan bahagian dengan berbilang bahan atau tekstur dalam satu acuan, memberikan cengkaman, kusyen atau ciri estetik yang lebih baik.
Faktor-faktor yang Mempengaruhi Kos Pengacuan Suntikan
Memandangkan faktor ini boleh membantu pengeluar menganggar dan mengoptimumkan kos pengacuan suntikan, memastikan keseimbangan antara kualiti, kecekapan dan keberkesanan kos untuk keperluan pengeluaran khusus mereka.
- Kerumitan Bahagian:Kerumitan reka bentuk bahagian memainkan peranan penting dalam menentukan kos pengacuan suntikan. Geometri rumit, potongan bawah, dinding nipis atau ciri kompleks mungkin memerlukan perkakas tambahan, acuan khusus atau kitaran yang lebih panjang, meningkatkan kos pembuatan keseluruhan.
- Pemilihan Bahan:Pemilihan bahan termoplastik mempengaruhi kos pengacuan suntikan. Bahan yang berbeza mempunyai harga yang berbeza bagi setiap kilogram, dan faktor seperti ketersediaan bahan, sifat dan keperluan pemprosesan boleh mempengaruhi kos bahan keseluruhan.
- Alatan dan Reka Bentuk Acuan: Kos perkakasan awal dan reka bentuk acuan adalah penting dalam kos pengacuan suntikan. Faktor-faktor seperti kerumitan acuan, bilangan rongga, saiz acuan, dan bahan acuan menyumbang kepada perbelanjaan pembuatan perkakas dan acuan. Acuan atau acuan yang lebih kompleks yang memerlukan ciri lanjutan boleh meningkatkan pelaburan pendahuluan.
- Jumlah Pengeluaran: Jumlah pengeluaran secara langsung memberi kesan kepada kos setiap bahagian dalam pengacuan suntikan. Buku yang lebih tinggi selalunya menghasilkan skala ekonomi, mengurangkan kos setiap bahagian. Sebaliknya, pengeluaran volum rendah mungkin dikenakan caj yang lebih tinggi disebabkan oleh persediaan, perkakas dan sisa bahan.
- Kitaran masa: Masa kitaran, yang merangkumi fasa penyejukan dan lontar, mempengaruhi kapasiti pengeluaran dan kos keseluruhan. Masa kitaran yang lebih panjang mengakibatkan pengeluaran pengeluaran berkurangan dan harga yang berpotensi lebih tinggi. Mengoptimumkan reka bentuk acuan, sistem penyejukan dan parameter proses boleh meminimumkan masa kitaran dan meningkatkan kecekapan.
- Keperluan Kualiti:Keperluan kualiti yang ketat atau pensijilan khusus boleh memberi kesan kepada kos pengacuan suntikan. Memenuhi toleransi yang tepat, keperluan kemasan permukaan atau ujian tambahan mungkin memerlukan sumber, proses atau pemeriksaan lain, menambah kos keseluruhan.
- Operasi Sekunder:Jika bahagian acuan memerlukan operasi pasca pemprosesan seperti pemasangan, pengecatan atau langkah kemasan tambahan, operasi ini boleh menambah kos pengacuan suntikan keseluruhan.
- Pembekal dan Lokasi:Pilihan pembekal acuan suntikan dan lokasinya boleh menjejaskan kos. Kos buruh, overhed, logistik dan perbelanjaan pengangkutan berbeza-beza berdasarkan lokasi pembekal, memberi kesan kepada kos pembuatan keseluruhan.
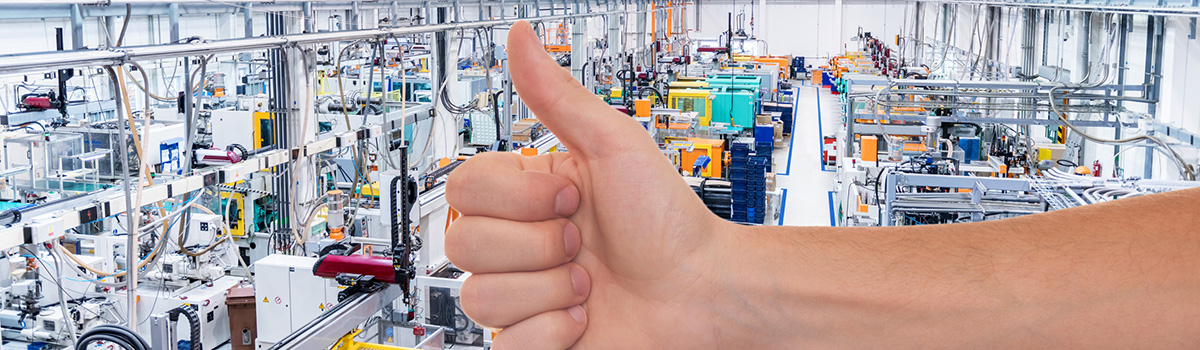
Kawalan Kualiti dalam Pengacuan Suntikan
Melaksanakan langkah kawalan kualiti yang teguh sepanjang proses pengacuan suntikan membantu mengenal pasti dan menangani potensi kecacatan, penyelewengan atau ketidakkonsistenan, memastikan pengeluaran bahagian berkualiti tinggi yang memenuhi spesifikasi dan keperluan pelanggan.
- Pemantauan Proses: Pemantauan berterusan parameter proses utama, seperti suhu cair, tekanan suntikan, masa penyejukan, dan masa kitaran, memastikan konsistensi dan kebolehulangan dalam pengeluaran sebahagian. Pemantauan masa nyata dan sistem automatik boleh mengesan variasi atau sisihan daripada parameter yang ditetapkan, membolehkan pelarasan tepat pada masanya dan mengekalkan kestabilan proses.
- Pemeriksaan dan Pengukuran:Semakan dan pengukuran bahagian acuan yang kerap adalah penting untuk mengesahkan ketepatan dimensi, kualiti bahagian dan pematuhan kepada spesifikasi. Perkhidmatan kami meliputi pelbagai kaedah kawalan kualiti, seperti mengukur dimensi, menganalisis kualiti permukaan, menjalankan pemeriksaan visual dan melaksanakan ujian kefungsian. Pelbagai teknik pemeriksaan, seperti mesin pengukur koordinat (CMM) dan sistem pemeriksaan optik dan visual, digunakan untuk penilaian yang tepat.
- Kawalan Proses Statistik (SPC): SPC melibatkan pengumpulan dan menganalisis data proses untuk memantau dan mengawal kualiti pengacuan suntikan. Kaedah statistik, seperti carta kawalan dan analisis keupayaan proses, membantu mengenal pasti arah aliran, mengesan variasi proses dan memastikan proses kekal dalam had kawalan yang ditetapkan. SPC membolehkan pengenalpastian isu secara proaktif dan memudahkan pengoptimuman proses.
- Ujian Bahan: Menguji bahan mentah, seperti termoplastik, bahan tambahan, dan pewarna, memastikan kualiti dan kesesuaiannya untuk pengacuan suntikan. Ujian bahan mungkin termasuk analisis indeks aliran cair (MFI), sifat mekanikal, ciri terma dan komposisi bahan. Mengesahkan kualiti bahan membantu mengelakkan kecacatan dan ketidakkonsistenan pada bahagian yang dibentuk.
- Penyelenggaraan dan Pemeriksaan Perkakas:Penyelenggaraan yang betul dan pemeriksaan biasa acuan suntikan adalah penting untuk memastikan kualiti dalam pengacuan suntikan. Pembersihan, pelinciran dan penilaian yang kerap komponen acuan membantu mengelakkan haus, kerosakan atau kemerosotan yang boleh menjejaskan kualiti bahagian. Pembaikan atau penggantian komponen acuan yang haus atau rosak tepat pada masanya adalah penting untuk mengekalkan prestasi pengacuan yang konsisten.
- Dokumentasi dan Kebolehkesanan:Mengekalkan dokumentasi komprehensif dan rekod kebolehkesanan adalah penting untuk kawalan kualiti dalam pengacuan suntikan. Adalah penting untuk merekodkan parameter proses, keputusan pemeriksaan, maklumat material, dan sebarang perubahan atau pelarasan yang dibuat semasa pengeluaran. Dokumentasi yang betul membolehkan kebolehkesanan bahagian, memudahkan analisis punca punca, dan memastikan konsistensi dalam kualiti.
- Latihan dan Pembangunan Kemahiran: Menyediakan program latihan dan pembangunan kemahiran yang mencukupi untuk pengendali, juruteknik dan kakitangan kawalan kualiti meningkatkan pemahaman mereka tentang proses pengacuan suntikan, keperluan kualiti dan teknik pemeriksaan. Kakitangan yang terlatih boleh mengesan kecacatan, menyelesaikan masalah dan melaksanakan langkah pembetulan dengan berkesan, memastikan pengeluaran berkualiti tinggi.
Kecacatan Pengacuan Suntikan Biasa dan Cara Mengelakkannya
Pemeriksaan berkala, pemantauan dan analisis proses pengacuan suntikan dan penyelenggaraan serta pelarasan peralatan dan acuan yang betul boleh membantu mengenal pasti dan menangani kecacatan biasa ini.
- Tanda Sinki:Tanda sinki ialah lekukan atau lekukan pada permukaan bahagian acuan yang disebabkan oleh penyejukan atau pengecutan yang tidak sekata. Seseorang harus mempertimbangkan lokasi dan reka bentuk pintu pagar yang betul, reka bentuk sistem penyejukan yang optimum, dan pengedaran ketebalan dinding yang seragam untuk mengelakkan tanda sinki. Meningkatkan tekanan suntikan atau melaraskan masa penyejukan juga boleh membantu meminimumkan tanda sinki.
- Warpage:Warpage merujuk kepada ubah bentuk atau lenturan bahagian yang dibentuk selepas lontar akibat penyejukan yang tidak sekata atau tegasan sisa. Mengekalkan ketebalan dinding yang seragam, menggunakan saluran penyejukan yang betul, dan memastikan pengisian dan pembungkusan yang seimbang bagi acuan adalah penting untuk mengelakkan letupan. Mengoptimumkan suhu acuan, menggunakan sudut draf yang sesuai, dan mengawal suhu bahan dan kelajuan suntikan boleh membantu meminimumkan lengkokan.
- Flash:Denyar berlaku apabila lebihan bahan mengalir ke dalam garisan pemisah acuan, mengakibatkan unjuran nipis yang tidak diingini atau bahan tambahan pada bahagian akhir. Seseorang boleh menghalang denyar dengan berkesan dengan memastikan reka bentuk acuan yang betul, termasuk menggunakan daya pengapit yang mencukupi, penjajaran yang tepat dan menggunakan teknik pengudaraan yang sesuai. Mengoptimumkan parameter proses seperti tekanan suntikan, suhu dan masa kitaran mengurangkan denyar.
- Pukulan Pendek:Pukulan pantas berlaku apabila bahan yang disuntik tidak memenuhi rongga acuan, mengakibatkan bahagian yang tidak lengkap. Pemilihan bahan yang betul, memastikan suhu cair dan kelikatan yang mencukupi, dan mengekalkan tekanan dan masa suntikan yang sesuai adalah penting untuk mengelakkan gambar pendek. Di samping itu, mengesahkan reka bentuk acuan untuk saiz pelari dan pintu pagar yang mencukupi serta pengudaraan yang betul boleh membantu menghalang pukulan pantas.
- Talian Kimpalan:Garisan kimpalan berlaku apabila dua atau lebih bahagian hadapan aliran bahan cair bertemu dan memejal, menghasilkan garisan atau tanda yang kelihatan pada permukaan bahagian. Reka bentuk gerbang dan pelari yang baik, suhu cair optimum, kelajuan suntikan, dan pelarasan aliran bahan dan geometri bahagian boleh meminimumkan garisan kimpalan. Analisis aliran acuan dan pengoptimuman peletakan pintu juga boleh membantu mencegah atau mengurangkan garisan kimpalan.
- Tanda Terbakar:Tanda terbakar ialah perubahan warna atau bintik hitam pada permukaan bahagian acuan yang disebabkan oleh haba yang berlebihan atau terlalu panas bahan. Mengelakkan suhu cair yang melampau, menggunakan saluran penyejukan yang sesuai dan mengoptimumkan masa kitaran boleh membantu mengelakkan kesan terbakar. Pembuangan yang mencukupi, reka bentuk pintu pagar yang betul, dan mengawal suhu acuan juga menyumbang kepada meminimumkan kesan terbakar.
Operasi Selepas Pengacuan: Kemasan dan Pemasangan
Selepas pengacuan suntikan, banyak bahagian acuan mungkin memerlukan operasi kemasan dan pemasangan tambahan untuk mencapai produk akhir yang diingini. Operasi pasca pengacuan ini mungkin termasuk:
- Pemangkasan:Keluarkan sebarang bahan berlebihan atau kilat di sekeliling bahagian acuan menggunakan alat pemangkasan atau pemotongan.
- Rawatan permukaan:Mempertingkatkan rupa atau kefungsian permukaan bahagian menggunakan pelbagai teknik seperti mengecat, menyalut atau mentekstur.
- Perhimpunan:Mencantumkan berbilang bahagian acuan atau menambah komponen seperti pengikat, sisipan atau label untuk melengkapkan produk akhir.
- ujian:Pengesahan kualiti dan kefungsian bahagian melalui pelbagai kaedah ujian seperti analisis dimensi, ujian sifat bahan atau ujian prestasi.
- Pembungkusan dan Penghantaran:Pembungkusan dan pelabelan yang betul bagi produk siap untuk dihantar kepada pelanggan atau pengguna akhir.
Pemilihan operasi pasca pengacuan bergantung pada aplikasi khusus dan ciri produk akhir yang dikehendaki. Kerjasama rapat antara pakar pengacuan suntikan, pakar kemasan dan pemasangan, dan pelanggan adalah penting untuk mencapai kualiti dan fungsi produk mutlak yang diingini. Perancangan yang betul dan penyepaduan operasi pasca pengacuan ke dalam proses pembuatan boleh membantu memastikan pengeluaran yang cekap dan penghantaran produk berkualiti tinggi tepat pada masanya.
Pengacuan Suntikan lwn. Proses Pengilangan Plastik Lain
Setiap proses pembuatan plastik mempunyai kelebihan dan batasan, menjadikannya sesuai untuk aplikasi yang berbeza.
- Acuan suntikan: Pengacuan suntikan adalah proses pembuatan yang sangat serba boleh dan digunakan secara meluas untuk menghasilkan bahagian plastik. Ia menawarkan kelebihan seperti kecekapan pengeluaran yang tinggi, replikasi bahagian yang tepat, dan keupayaan untuk mencipta geometri yang kompleks. Pengacuan suntikan sesuai untuk larian pengeluaran volum tinggi dan membolehkan penggunaan pelbagai bahan termoplastik. Ia menawarkan ketepatan dimensi dan kemasan permukaan yang sangat baik, menjadikannya sesuai untuk pelbagai industri seperti automotif, barangan pengguna dan peranti perubatan.
- Pengacuan tiupan: Pengacuan tiupan ialah proses yang digunakan terutamanya untuk menghasilkan bahagian plastik berongga, seperti botol, bekas, dan komponen automotif. Ia melibatkan peleburan plastik dan mengembungkannya ke dalam rongga acuan, menghasilkan bentuk yang diingini. Pengacuan tiupan sesuai untuk pengeluaran volum tinggi dan boleh menghasilkan bahagian yang besar dan ringan dengan ketebalan dinding yang seragam. Walau bagaimanapun, ia terhad dari segi kerumitan bahagian dan pemilihan bahan berbanding dengan pengacuan suntikan.
- Pembentukan termo:Thermoforming ialah satu proses yang digunakan untuk menghasilkan bahagian plastik dengan memanaskan kepingan termoplastik dan membentuknya menggunakan acuan atau pembentuk vakum. Ia mendapati penggunaan biasa dalam pembungkusan, produk pakai buang dan produk berskala besar seperti dulang dan penutup. Thermoforming menawarkan pengeluaran kos efektif untuk bahagian besar dan membolehkan prototaip pantas. Walau bagaimanapun, ia mempunyai had mengenai kerumitan bahagian, pemilihan bahan, dan ketepatan dimensi berbanding dengan pengacuan suntikan.
- Penyemperitan:Penyemperitan ialah proses berterusan untuk menghasilkan profil plastik, kepingan, tiub, dan filem. Ia melibatkan peleburan resin plastik dan memaksanya melalui acuan untuk menghasilkan bentuk yang diingini. Penyemperitan sesuai untuk menghasilkan produk plastik yang panjang dan berterusan dengan keratan rentas yang konsisten. Walaupun penyemperitan menawarkan kadar pengeluaran yang tinggi dan keberkesanan kos, ia terhad dari segi geometri bahagian kompleks dan kawalan dimensi yang tepat berbanding dengan pengacuan suntikan.
- Pengacuan Mampatan:Pengacuan mampatan melibatkan meletakkan jumlah bahan termoset yang telah diukur sebelumnya dalam rongga acuan yang dipanaskan dan memampatkannya di bawah tekanan tinggi sehingga ia sembuh. Ia mendapati penggunaan biasa dalam menghasilkan bahagian dengan kekuatan tinggi dan kestabilan dimensi, seperti komponen automotif dan penebat elektrik. Pengacuan mampatan menawarkan konsistensi bahagian yang baik, kecekapan pengeluaran yang tinggi, dan keupayaan untuk menggunakan pelbagai jenis bahan. Walau bagaimanapun, ia terhad dari segi kerumitan bahagian dan masa kitaran berbanding dengan pengacuan suntikan.
Aplikasi Pengacuan Suntikan Termoplastik
Pelbagai industri menggunakan pengacuan suntikan termoplastik secara meluas kerana kepelbagaian, kecekapan dan keberkesanan kosnya. Beberapa aplikasi pengacuan suntikan termoplastik termasuk:
- Industri automotif: Industri automotif secara meluas menggunakan pengacuan suntikan termoplastik untuk mengeluarkan pelbagai komponen, termasuk kemasan dalaman dan luaran, papan pemuka, panel pintu, bampar dan penyambung elektrik. Proses ini membolehkan replikasi bahagian yang tepat, geometri kompleks, dan bahan ringan, meningkatkan kecekapan bahan api dan fleksibiliti reka bentuk.
- Barangan Pengguna:Pengacuan suntikan menemui aplikasi yang meluas dalam menghasilkan barangan pengguna seperti perkakas rumah, peranti elektronik, bekas pembungkusan dan mainan. Proses ini membolehkan pengeluaran besar-besaran produk tahan lama, berkualiti tinggi dengan dimensi dan kemasan permukaan yang konsisten. Ia juga membenarkan pilihan penyesuaian dan lelaran produk yang cepat.
- Peralatan perubatan:Pengacuan suntikan memainkan peranan penting dalam industri perubatan untuk menghasilkan pelbagai jenis peranti, termasuk picagari, instrumen pembedahan, komponen boleh implan dan sistem penghantaran ubat. Proses ini memastikan pengeluaran bahagian steril, tepat dan biokompatibel yang memenuhi keperluan pengawalseliaan ketat sektor penjagaan kesihatan.
- Industri Elektronik dan Elektrik:Industri elektronik menggunakan pengacuan suntikan untuk mengeluarkan penyambung elektrik, penutup, suis dan komponen lain. Proses ini menawarkan ketepatan dimensi yang tinggi, kemasan permukaan yang sangat baik, dan keupayaan untuk menggabungkan ciri-ciri seperti pengacuan sisipan dan pengacuan berlebihan, membolehkan pengeluaran pemasangan elektronik kompleks yang cekap.
- Industri Pembungkusan:Pelbagai industri, termasuk makanan dan minuman, farmaseutikal dan penjagaan diri, biasanya menggunakan pengacuan suntikan untuk menghasilkan bekas pembungkusan plastik, penutup, penutup dan botol. Proses ini membolehkan penciptaan penyelesaian pembungkusan yang ringan, tahan lama dan menarik dari segi estetik dengan kitaran pembuatan yang cekap.
- Industri Aeroangkasa:Sektor aeroangkasa menggunakan pengacuan suntikan untuk pembuatan komponen ringan dan berprestasi tinggi seperti saluran udara, kurungan, panel dalaman dan bahagian struktur. Proses ini membolehkan penggunaan bahan termaju dan geometri bahagian yang rumit, menyumbang kepada pengurangan berat dan kecekapan bahan api yang lebih baik.
Kesan Alam Sekitar Pengacuan Suntikan Termoplastik
Pengacuan suntikan termoplastik ialah proses pembuatan yang popular kerana banyak faedahnya, tetapi ia juga penting untuk mempertimbangkan kesan alam sekitar. Berikut adalah beberapa perkara yang perlu dipertimbangkan:
- Kecekapan Bahan:Pengacuan suntikan termoplastik menggalakkan kecekapan bahan dengan meminimumkan sisa. Proses ini menggunakan kawalan tepat ke atas jumlah bahan yang disuntik ke dalam acuan, mengurangkan keperluan untuk bahan berlebihan. Pengilang juga boleh menggunakan teknik pengisaran semula dan kitar semula untuk menggunakan semula sekerap atau bahagian yang ditolak, seterusnya mengurangkan sisa bahan.
- Penggunaan tenaga:Pengilang mereka bentuk mesin pengacuan suntikan supaya cekap tenaga, dengan model moden yang menggabungkan teknologi canggih seperti motor servo dan pemacu kelajuan berubah-ubah. Ciri-ciri ini mengoptimumkan penggunaan tenaga dengan mengurangkan penggunaan kuasa semasa pengacuan, menghasilkan keperluan tenaga yang lebih rendah dan mengurangkan kesan alam sekitar.
- Pengurusan sisa:Sambil meminimumkan sisa bahan, pengilang harus melaksanakan amalan pengurusan sisa yang betul untuk mengendalikan sisa bahan, spru atau pelari. Pengilang boleh mewujudkan program kitar semula untuk mengumpul dan menggunakan semula sisa plastik yang dihasilkan semasa pengacuan suntikan, dengan itu mengurangkan sisa yang dihantar ke tapak pelupusan sampah.
- Pengurangan pelepasan: Pengacuan suntikan termoplastik secara amnya menghasilkan pelepasan yang lebih rendah daripada proses pembuatan lain. Pengilang boleh mengurangkan pelepasan dengan menggunakan bahan mesra alam, melaksanakan peralatan cekap tenaga, dan menggunakan sistem ekzos dan penapisan canggih untuk menangkap sebarang pelepasan yang dikeluarkan.
- Pilihan Bahan Mampan:Pemilihan bahan termoplastik boleh memberi kesan ketara kepada kemampanan alam sekitar pengacuan suntikan. Memilih untuk plastik biodegradasi atau berasaskan bio, serta bahan kitar semula atau kitar semula, boleh membantu mengurangkan keseluruhan jejak ekologi proses tersebut.
Pertimbangan Kitaran Hayat: Mengambil kira keseluruhan kitaran hayat produk acuan adalah penting untuk menilai kesan alam sekitarnya. Semasa peringkat reka bentuk dan pemilihan bahan, pengilang harus mempertimbangkan faktor seperti ketahanan bahagian, kebolehkitar semulanya dan potensi untuk pelupusan atau penggunaan semula akhir hayat.
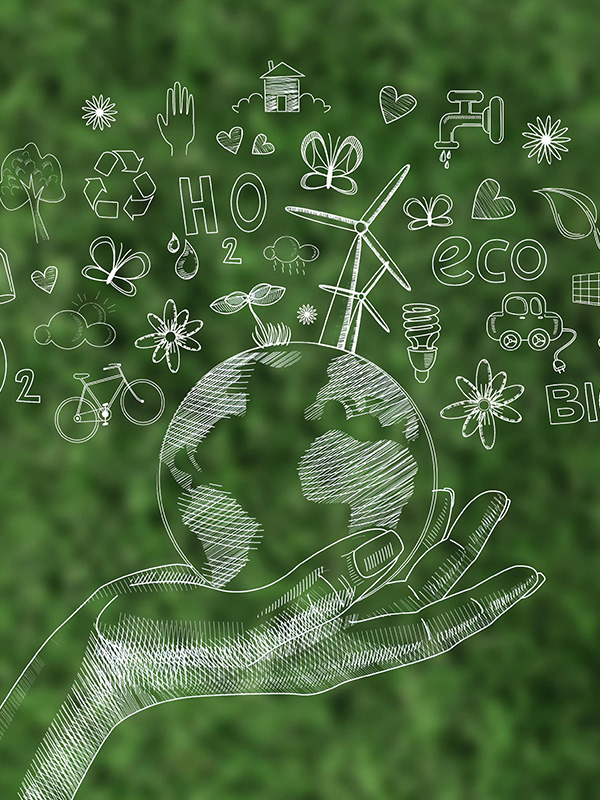
Masa Depan Pengacuan Suntikan Termoplastik
Masa depan pengacuan suntikan termoplastik kelihatan menjanjikan, dengan kemajuan berterusan dalam teknologi dan peningkatan permintaan untuk bahagian berkualiti tinggi dan ketepatan merentas pelbagai industri. Beberapa perkembangan utama yang dijangkakan pada tahun-tahun akan datang termasuk:
- Peningkatan penggunaan automasi dan robotik untuk meningkatkan kecekapan dan mengurangkan kos.
- Usaha ditumpukan pada pembangunan bahan dan proses baharu untuk meningkatkan prestasi bahagian dan membolehkan aplikasi baharu.
- Ia adalah penggunaan amalan lestari yang semakin meningkat, seperti menggunakan bahan kitar semula dan mengoptimumkan penggunaan tenaga, untuk mengurangkan kesan pengacuan suntikan kepada alam sekitar.
- Penyepaduan teknologi digital yang lebih baik, seperti percetakan 3D dan perisian simulasi, untuk menambah baik proses reka bentuk dan pengeluaran.
Pasaran acuan suntikan global berkembang, terutamanya dalam ekonomi sedang pesat membangun, didorong oleh peningkatan permintaan untuk produk plastik dalam pelbagai industri.
Memilih Rakan Pengacuan Suntikan yang Tepat
Memilih rakan pengacuan suntikan yang betul adalah penting untuk kejayaan projek anda. Luangkan masa untuk menilai pelbagai pilihan, jalankan lawatan tapak dan libatkan diri dalam perbincangan menyeluruh untuk memastikan perkongsian yang serasi dan berkekalan.
- Kepakaran dan Pengalaman:Cari rakan pengacuan suntikan dengan pengetahuan dan pengalaman luas dalam industri. Mereka harus mempunyai rekod prestasi yang terbukti dalam menyampaikan produk dan penyelesaian berkualiti tinggi kepada pelanggan dalam pelbagai sektor. Pertimbangkan pemahaman mereka tentang bahan yang berbeza, reka bentuk acuan dan proses pembuatan.
- Keupayaan Pengilangan: Menilai keupayaan pembuatan rakan pengacuan suntikan. Pastikan mereka mempunyai kemudahan yang lengkap dengan jentera dan teknologi moden untuk mengendalikan keperluan projek anda. Pertimbangkan kapasiti pengeluaran mereka, keupayaan untuk mengendalikan saiz bahagian dan kerumitan yang berbeza, dan keupayaan untuk memenuhi volum pengeluaran dan garis masa yang anda inginkan.
- Jaminan kualiti:Kualiti adalah terpenting dalam pengacuan suntikan. Menilai sistem kawalan kualiti dan pensijilan bakal rakan kongsi. Cari rakan kongsi yang mengikut piawaian kualiti yang ketat, mempunyai proses pemeriksaan yang teguh dan melaksanakan ujian komprehensif untuk memastikan kualiti dan konsistensi bahagian.
- Sokongan Reka Bentuk dan Kejuruteraan:Rakan pengacuan suntikan yang boleh dipercayai harus menawarkan sokongan reka bentuk dan kejuruteraan untuk mengoptimumkan reka bentuk bahagian anda untuk kebolehkilangan. Mereka harus mempunyai jurutera mahir yang boleh memberikan input berharga mengenai pemilihan bahan, reka bentuk acuan, dan pengoptimuman proses untuk meningkatkan kualiti dan kecekapan bahagian.
- Daya Saing Kos:Walaupun kos tidak seharusnya menjadi satu-satunya faktor penentu, adalah penting untuk menilai harga dan daya saing kos rakan pengacuan suntikan. Minta sebut harga terperinci dan pertimbangkan kos perkakas, kos bahan, kos buruh dan sebarang perkhidmatan tambahan yang mereka sediakan.
- Komunikasi dan Kerjasama:Komunikasi dan kerjasama yang berkesan adalah penting untuk perkongsian yang berjaya. Pastikan rakan pengacuan suntikan mempunyai saluran komunikasi yang baik, responsif terhadap pertanyaan anda dan boleh memberikan kemas kini projek secara tetap. Pendekatan kolaboratif akan membantu memastikan kami memenuhi keperluan anda dan menangani sebarang cabaran dengan segera.
- Rujukan dan Ulasan Pelanggan:Dapatkan rujukan pelanggan atau baca ulasan/testimoni untuk mendapatkan pandangan tentang pengalaman pelanggan lain dengan rakan pengacuan suntikan. Mendapatkan maklumat ini boleh membantu menentukan kebolehpercayaan, kepantasan dan tahap keseluruhan kepuasan pelanggan mereka.
Kesimpulan
Pengacuan suntikan termoplastik adalah kaedah yang serba boleh dan kos efektif untuk mengeluarkan bahagian plastik dalam kuantiti yang banyak. Keupayaannya untuk menghasilkan bentuk kompleks dengan ketepatan dan ketekalan tinggi telah menjadi pilihan popular untuk pelbagai industri, termasuk automotif, perubatan, elektronik dan barangan pengguna. Dengan memahami pelbagai aspek pengacuan suntikan termoplastik, termasuk kelebihan, kelemahan dan pertimbangan reka bentuknya, anda boleh membuat keputusan termaklum tentang memilih rakan pengacuan suntikan yang betul untuk keperluan perniagaan anda.