ပလပ်စတစ်ဆေးထိုးမှို
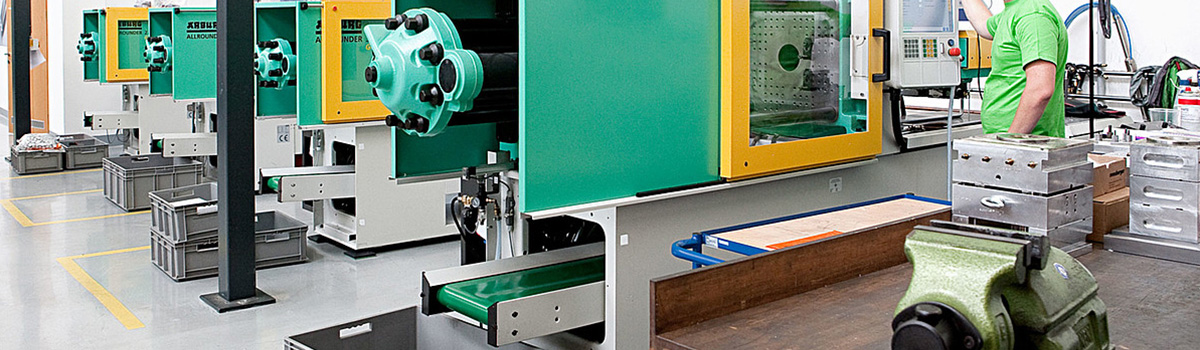
ပလပ်စတစ်ဆေးထိုးခြင်းဆိုသည်မှာ သုံးဖက်မြင်အရာဝတ္ထုတစ်ခုဖန်တီးရန်အတွက် ပလပ်စတစ်အမှုန့်များကို အရည်ပျော်ပြီး မှိုပေါက်အတွင်း ထိုးသွင်းခြင်းပါ၀င်သည့် ထုတ်လုပ်မှုလုပ်ငန်းစဉ်တစ်ခုဖြစ်သည်။ ဤလုပ်ငန်းစဉ်သည် သေးငယ်သောတိကျသောအစိတ်အပိုင်းများမှ သိသာထင်ရှားသော မော်တော်ယာဥ်အစိတ်အပိုင်းများအထိ ထုတ်ကုန်များစွာဖြင့် စတင်သည်။ ပလပ်စတစ်ဆေးထိုးပုံသွင်းခြင်းသည် ထုတ်လုပ်မှုနှုန်းမြင့်မားခြင်း၊ ဒီဇိုင်းပြောင်းလွယ်ပြင်လွယ်နှင့် ကုန်ကျစရိတ်သက်သာခြင်းအပါအဝင် အခြားသောကုန်ထုတ်လုပ်မှုလုပ်ငန်းစဉ်များထက် အားသာချက်များစွာကို ပေးဆောင်ပါသည်။ ဤလမ်းညွှန်ချက်သည် ပလတ်စတစ်ဆေးထိုးခြင်းတွင် နက်ရှိုင်းစွာကြည့်ရှုပြီး ၎င်း၏ အမျိုးမျိုးသော အသုံးချမှု၊ အကျိုးကျေးဇူးများနှင့် ကန့်သတ်ချက်များကို ရှာဖွေမည်ဖြစ်သည်။
Plastic Injection Molding ၏သမိုင်း
ပလပ်စတစ်ဆေးထိုးပုံသွင်းခြင်းဆိုသည်မှာ တိကျသောပုံသဏ္ဍာန်တစ်ခုဖန်တီးရန်အတွက် မှိုပေါက်အတွင်းသို့ သွန်းသောပလပ်စတစ်ကို ထိုးသွင်းခြင်းပါဝင်သည့် ထုတ်လုပ်မှုလုပ်ငန်းစဉ်တစ်ခုဖြစ်သည်။ ပလပ်စတစ်ဆေးထိုးခြင်း၏သမိုင်းကြောင်းကို ဆယ်လူလွိုက်ပလတ်စတစ်အမျိုးအစားကို စတင်တီထွင်ခဲ့ချိန် 1800 ခုနှစ်နှောင်းပိုင်းမှ ပြန်လည်ခြေရာခံနိုင်သည်။ သို့သော် ၁၉၄၀ ပြည့်လွန်နှစ်များတွင် ပလပ်စတစ်ဆေးထိုးခြင်းအား ထုတ်လုပ်မှုနည်းပညာအဖြစ် တွင်ကျယ်စွာအသုံးပြုလာခဲ့သည်။
ဒုတိယကမ္ဘာစစ်အတွင်းတွင် အမြောက်အမြားထုတ်လုပ်သော ပလတ်စတစ်ထုတ်ကုန်များ ၀ယ်လိုအား မြင့်တက်လာပြီး ထုတ်လုပ်သူများသည် ၎င်းတို့ကို ထုတ်လုပ်ရန် ပိုမိုထိရောက်သော နည်းလမ်းသစ်များကို ရှာဖွေခဲ့ကြသည်။ 1946 ခုနှစ်တွင် အမေရိကန်တီထွင်သူ James Watson Hendry သည် ပလတ်စတစ်ဆေးထိုးခြင်းလုပ်ငန်းကို တော်လှန်ပြောင်းလဲခဲ့သည့် ပထမဆုံးဝက်အူဆေးထိုးစက်ကို တီထွင်ခဲ့သည်။ ဤစက်သည် ပိုမိုတိကျပြီး တသမတ်တည်း ဆေးထိုးသည့် လုပ်ငန်းစဉ်ကို ထိန်းချုပ်နိုင်သောကြောင့် ပလတ်စတစ်အစိတ်အပိုင်း အများအပြားကို ပိုမိုရရှိနိုင်ပြီး ထိရောက်မှုရှိသည်။
1950 နှင့် 1960 ခုနှစ်များတစ်လျှောက်တွင် ပလတ်စတစ်နည်းပညာတိုးတက်မှုများသည် ပလတ်စတစ်ဆေးထိုးခြင်းလုပ်ငန်းစဉ်ကို ဆက်လက်တိုးတက်စေခဲ့သည်။ polystyrene နှင့် polyethylene ကဲ့သို့သော ပစ္စည်းအသစ်များကို မိတ်ဆက်ခြင်းဖြင့် ပိုမိုရှုပ်ထွေးပြီး တာရှည်ခံသော ပလပ်စတစ်အစိတ်အပိုင်းများကို ဖန်တီးခဲ့သည်။ ထို့အပြင်၊ ဟိုက်ဒရောလစ်စနစ်များအသုံးပြုခြင်းအပါအဝင် ပုံသွင်းစက်နည်းပညာတိုးတက်မှုများသည် ဆေးထိုးပုံသွင်းခြင်းလုပ်ငန်းစဉ်ကို ပိုမိုထိရောက်ပြီး ကုန်ကျစရိတ်သက်သာစေသည်။
ယနေ့ခေတ်တွင် ပလပ်စတစ်ဆေးထိုးခြင်းဆိုသည်မှာ အရုပ်များနှင့် လူသုံးကုန်ပစ္စည်းများမှ မော်တော်ယာဥ်အစိတ်အပိုင်းများနှင့် ဆေးဘက်ဆိုင်ရာပစ္စည်းများအထိ ပလပ်စတစ်ထုတ်ကုန် အများအပြားကို ထုတ်လုပ်ရန် အသုံးပြုသည့် အလွန်အလိုအလျောက် လုပ်ငန်းစဉ်တစ်ခုဖြစ်သည်။ အသစ်သော ပစ္စည်းများနှင့် နည်းပညာများ ဖွံ့ဖြိုးတိုးတက်လာသည်နှင့်အမျှ၊ ပလပ်စတစ်ဆေးထိုးခြင်း လုပ်ငန်းစဉ်သည် နှစ်ပေါင်းများစွာ အရေးပါသော ထုတ်လုပ်မှုနည်းပညာတစ်ခုအဖြစ် ဆက်လက်တည်ရှိနေမည်ဟု အာမခံပါသည်။
ပလပ်စတစ်ထိုးသွင်းပုံသွင်းခြင်း၏အခြေခံများ
ပလပ်စတစ်ဆေးထိုးခြင်းဆိုသည်မှာ ပလပ်စတစ်ပစ္စည်းများဖြင့် ပြုလုပ်ထားသော အစိတ်အပိုင်းများနှင့် ထုတ်ကုန်များကို ဖန်တီးထုတ်လုပ်သည့် လုပ်ငန်းစဉ်တစ်ခုဖြစ်သည်။ လုပ်ငန်းစဉ်တွင် သွန်းသောပလပ်စတစ်ကို မှိုတစ်ခုထဲသို့ ထိုးသွင်းခြင်းဖြင့် လိုချင်သောပုံသဏ္ဍာန်ကို အေးခဲစေပြီး ခိုင်မာစေပါသည်။
ပလပ်စတစ်ဆေးထိုးခြင်း လုပ်ငန်းစဉ်တွင် ပါဝင်သည့် အခြေခံအဆင့်များမှာ အောက်ပါအတိုင်းဖြစ်သည်။
- မှိုဒီဇိုင်း- လုပ်ငန်းစဉ်၏ ပထမအဆင့်မှာ လိုချင်သောအပိုင်းကို ဖန်တီးရန် အသုံးပြုမည့် မှိုကို ဒီဇိုင်းရေးဆွဲရန်ဖြစ်သည်။ မှိုကို ယေဘုယျအားဖြင့် သတ္တုဖြင့်ပြုလုပ်ထားပြီး ပလပ်စတစ်သည် အေးခဲပြီး ခိုင်မာလာသောအခါ ကျုံ့နိုင်စေရန် ပြင်ဆင်ရမည်ဖြစ်သည်။
- ပစ္စည်းပြင်ဆင်ခြင်း- ဆေးထိုးပုံသွင်းခြင်းလုပ်ငန်းစဉ်တွင် အသုံးပြုသည့် ပလပ်စတစ်ပစ္စည်းသည် အရည်ကျိုပြီး မှိုထဲသို့ ဆေးထိုးရန်အတွက် ပြင်ဆင်ရမည့် အလုံးများ သို့မဟုတ် granules ပုံစံဖြင့် လာပါသည်။ ၎င်းကို ပုံမှန်အားဖြင့် ပလတ်စတစ်ကို သတ်မှတ်ထားသော အပူချိန်တွင် အပူပေးပြီး အရည်အခြေအနေသို့ အရည်ပျော်သွားသည့် hopper တွင် ပြုလုပ်သည်။
- ထိုးဆေး- ပလပ်စတစ်အရည်ပျော်ပြီးသည်နှင့် အထူးပြု ဆေးထိုးပုံသွင်းစက်ကို အသုံးပြု၍ မှိုထဲသို့ ထိုးသွင်းသည်။ စက်သည် သွန်းသောပလပ်စတစ်ကို ဖိအားသက်ရောက်စေပြီး မှို၏ပုံသဏ္ဍာန်ပေါ်ရှိ မှိုပေါက်အတွင်းသို့ တွန်းပို့သည်။
- အအေးခံခြင်းနှင့် အစိုင်အခဲဖြစ်စေခြင်း- ပလပ်စတစ်ကို မှိုထဲသို့ ထိုးသွင်းပြီးနောက်၊ ၎င်းသည် အေးပြီး ခိုင်မာစေနိုင်သည်။ ၎င်းသည် အစိတ်အပိုင်း၏ အရွယ်အစားနှင့် ရှုပ်ထွေးမှုပေါ် မူတည်၍ စက္ကန့်အနည်းငယ်မှ မိနစ်များစွာအထိ ကြာနိုင်သည်။
- ထုတ်ခြင်း- ပလပ်စတစ်သည် အအေးခံပြီး ခိုင်မာသွားသည်နှင့်၊ မှိုပွင့်လာပြီး အစိတ်အပိုင်းကို ထုတ်ပစ်လိုက်သည်။ ပိုလျှံနေသော ပလပ်စတစ် သို့မဟုတ် ကြမ်းတမ်းသောအနားများကို ဖယ်ရှားရန်အတွက် ဖြတ်တောက်ခြင်း သို့မဟုတ် သဲပြုလုပ်ခြင်းကဲ့သို့သော အပိုအချောထည်လုပ်ရန် လိုအပ်နိုင်သည်။
ပလပ်စတစ်ဆေးထိုးပုံသွင်းခြင်းသည် တိကျပြီး ထပ်တလဲလဲလုပ်ဆောင်နိုင်သော လုပ်ငန်းစဉ်ဖြစ်ပြီး ၎င်းသည် အစုလိုက်အပြုံလိုက်ထုတ်လုပ်သည့် အစိတ်အပိုင်းများနှင့် ထုတ်ကုန်များအတွက် စံပြအဖြစ် တသမတ်တည်းဖြစ်စေသည်။ ၎င်းသည် အရွယ်အစားအမျိုးမျိုး၊ ပုံသဏ္ဍာန်များနှင့် ရှုပ်ထွေးမှုများဖြင့် အပိုင်းပိုင်းနှင့် ထုတ်ကုန်များကို ဖန်တီးနိုင်သောကြောင့် အလွန်စွယ်စုံရရှိပါသည်။ ပလတ်စတစ်ဆေးထိုးခြင်း၏ အသုံးအများဆုံး အသုံးချမှုအချို့တွင် အရုပ်များ၊ လူသုံးကုန်ပစ္စည်းများ၊ မော်တော်ယာဥ်အစိတ်အပိုင်းများနှင့် ဆေးဘက်ဆိုင်ရာ ကိရိယာများ ထုတ်လုပ်ခြင်းတို့ ပါဝင်သည်။
ပလပ်စတစ်ထိုးသွင်းပုံသွင်းခြင်းလုပ်ငန်းစဉ်- အဆင့်ဆင့်
ပလပ်စတစ်ဆေးထိုးခြင်းဆိုသည်မှာ အဆင့်များစွာပါဝင်သည့် ရှုပ်ထွေးသောလုပ်ငန်းစဉ်တစ်ခုဖြစ်သည်။ ဤသည်မှာ ပလပ်စတစ်ဆေးထိုးခြင်းလုပ်ငန်းစဉ်အတွက် အဆင့်ဆင့်လမ်းညွှန်ချက်ဖြစ်ပါသည်။
- Mold ကို ဒီဇိုင်းဆွဲခြင်း- ပထမအဆင့်မှာ အစိတ်အပိုင်းကို ဖန်တီးရာတွင် အသုံးပြုသည့် ပုံစံခွက်ကို ဒီဇိုင်းဆွဲရန်ဖြစ်သည်။ မှိုကို ပုံမှန်အားဖြင့် သံမဏိ သို့မဟုတ် အလူမီနီယမ်ဖြင့် ပြုလုပ်ထားပြီး အေးသွားသောအခါ ပလပ်စတစ်ပစ္စည်း၏ ကျုံ့သွားမှုကို လိုက်လျောညီထွေဖြစ်အောင် ပြင်ဆင်ထားရပါမည်။
- မှိုကိုဖန်တီးခြင်း- မှိုဒီဇိုင်းပြီးသည်နှင့်၊ ၎င်းကို ကွန်ပျူတာအထောက်အကူပြု ဒီဇိုင်း (CAD) ဆော့ဖ်ဝဲလ်နှင့် ကွန်ပြူတာအကူအညီဖြင့် ထုတ်လုပ်ခြင်း (CAM) စက်ပစ္စည်းများကို အသုံးပြု၍ ထုတ်လုပ်ပါသည်။ နောက်ဆုံးထုတ်ကုန်၏ တိကျမှုနှင့် ပြီးစီးမှုသေချာစေရန် မှိုကို ဂရုတစိုက် စက်နှင့် ပွတ်ရပါမည်။
- ပစ္စည်းရွေးချယ်ခြင်း- ဆေးထိုးပုံသွင်းခြင်းလုပ်ငန်းစဉ်အတွက် အသုံးပြုသည့် ပလတ်စတစ်အစေးပစ္စည်းအား ၎င်း၏ ကြံ့ခိုင်မှု၊ ပြောင်းလွယ်ပြင်လွယ်၊ အရောင်နှင့် အသွင်အပြင်ကဲ့သို့သော အစိတ်အပိုင်း၏ လိုအပ်ချက်များအပေါ် အခြေခံ၍ ရွေးချယ်ရမည်ဖြစ်သည်။
- ပစ္စည်းပြင်ဆင်ခြင်း- ရွေးချယ်ထားသော ပလပ်စတစ်ပစ္စည်းကို တိကျသောအပူချိန်တစ်ခုတွင် အပူပေးပြီး အရည်အဖြစ် အရည်ပျော်သွားပါသည်။ ထို့နောက် ပစ္စည်းကို ပုံသွင်းစက်၏ hopper ထဲသို့ ထိုးသွင်းသည်။
- ထိုးသွင်းပုံသွင်းခြင်း- သွန်းသောပလပ်စတစ်ပစ္စည်းကို အထူးပြုဆေးထိုးပုံသွင်းစက်ဖြင့် မှိုပေါက်ထဲသို့ ထိုးသွင်းသည်။ စက်သည် မှိုပုံသဏ္ဍာန်ပေါ်ရှိ မှိုပေါက်အတွင်းသို့ တွန်းပို့သော ပလပ်စတစ်ပစ္စည်းကို ဖိအားသက်ရောက်သည်။
- အအေးခံခြင်း- မှိုအပေါက်ကို ပလပ်စတစ်ဖြင့် ပြည့်သွားသည်နှင့် အအေးခံနိုင်ပြီး ခိုင်မာသွားနိုင်သည်။ အအေးခံချိန်ကို ပလပ်စတစ်ပစ္စည်း၏ ဝိသေသလက္ခဏာများ၊ အစိတ်အပိုင်း၏ အရွယ်အစားနှင့် အထူနှင့် မှိုအပူချိန်တို့ဖြင့် ဆုံးဖြတ်သည်။
- ထုတ်ပယ်ခြင်း- ပလပ်စတစ် ခိုင်မာလာပြီးနောက်၊ မှိုပွင့်လာပြီး အစိတ်အပိုင်းကို မှိုပေါက်များမှ ထုတ်လွှတ်သည်။
- အပြီးသတ်ခြင်း- ထုတ်လွှတ်သည့်အပိုင်းသည် ပိုလျှံနေသည့် ပလတ်စတစ် သို့မဟုတ် ကြမ်းတမ်းသောအနားများကို ဖယ်ရှားရန် ဖြတ်တောက်ခြင်း၊ သဲပြုလုပ်ခြင်း သို့မဟုတ် ပန်းချီဆွဲခြင်းကဲ့သို့သော အပိုအချောထည်လုပ်ငန်းများ လိုအပ်နိုင်သည်။
- အရည်အသွေးထိန်းချုပ်မှု- အချောထည်အပိုင်းသည် လိုအပ်သောသတ်မှတ်ချက်များနှင့် အရည်အသွေးစံချိန်စံညွှန်းများပြည့်မီရန် စေ့စေ့စပ်စပ်စစ်ဆေးခြင်းကို လုပ်ဆောင်သည်။
ပလပ်စတစ်ဆေးထိုးပုံသွင်းခြင်းသည် အရွယ်အစားအမျိုးမျိုး၊ ပုံသဏ္ဍာန်မျိုးစုံနှင့် ရှုပ်ထွေးမှုများဖြင့် အစိတ်အပိုင်းအမျိုးမျိုးနှင့် ထုတ်ကုန်များကို ထုတ်လုပ်နိုင်သည်။ အဆိုပါလုပ်ငန်းစဉ်ကို မော်တော်ယာဥ်၊ ဆေးဘက်ဆိုင်ရာ၊ လူသုံးကုန်ပစ္စည်းများနှင့် အီလက်ထရွန်းနစ်ပစ္စည်းများ အပါအဝင် လုပ်ငန်းအများအပြားတွင် တွင်ကျယ်စွာ အသုံးပြုလျက်ရှိသည်။
Injection Molding တွင်အသုံးပြုသော ပလပ်စတစ်အမျိုးအစားများ
ဆေးထိုးခြင်းတွင် ပလတ်စတစ်အမျိုးအစားများစွာကို အသုံးပြုနိုင်ပါသည်။ ပလပ်စတစ်ပစ္စည်းရွေးချယ်မှုသည် ထုတ်ကုန်၏ သီးခြားလိုအပ်ချက် သို့မဟုတ် အစိတ်အပိုင်းများဖြစ်သည့် ခိုင်ခံ့မှု၊ ပြောင်းလွယ်ပြင်လွယ်၊ တာရှည်ခံမှုနှင့် အသွင်အပြင်တို့အပေါ် မူတည်မည်ဖြစ်သည်။ ဆေးထိုးပုံသွင်းရာတွင် အသုံးအများဆုံး ပလပ်စတစ် အမျိုးအစားအချို့မှာ အောက်ပါအတိုင်းဖြစ်သည်။
- Polyethylene (PE): PE သည် ၎င်း၏ ကြံ့ခိုင်မှုနှင့် ပြောင်းလွယ်ပြင်လွယ်ကြောင့် လူသိများသော အသုံးများသော ပလတ်စတစ်ပစ္စည်းဖြစ်သည်။ ထုပ်ပိုးပစ္စည်းများ၊ အရုပ်များနှင့် ဆေးဘက်ဆိုင်ရာ ကိရိယာများ အပါအဝင် အမျိုးမျိုးသော ထုတ်ကုန်များ ထုတ်လုပ်ရန် အသုံးပြုသည်။
- Polypropylene (PP): PP သည် မော်တော်ကားလုပ်ငန်းတွင် အသုံးများသော ပေါ့ပါးပြီး တာရှည်ခံသော ပလတ်စတစ်ပစ္စည်းဖြစ်ပြီး ဒက်ရှ်ဘုတ်များနှင့် တံခါးဘောင်များကဲ့သို့သော အတွင်းပိုင်းအစိတ်အပိုင်းများဖြစ်သည်။ ၎င်းသည် ကွန်တိန်နာများနှင့် ပုလင်းများကဲ့သို့သော ထုပ်ပိုးပစ္စည်းများကိုလည်း ထုတ်လုပ်သည်။
- ပိုလီကာဗွန်နိတ် (PC)- PC သည် ကွန်ပျူတာနှင့် ဖုန်းအိတ်များကဲ့သို့ အီလက်ထရွန်နစ် အစိတ်အပိုင်းများ ထုတ်လုပ်ရန်အတွက် အသုံးများသော အခဲနှင့် ဖောက်ထွင်းမြင်ရသော ပလတ်စတစ်ပစ္စည်းဖြစ်သည်။ ၎င်းကို မော်တော်ယာဥ်လုပ်ငန်းတွင် headlamp lens နှင့် dashboard အစိတ်အပိုင်းများအတွက်လည်း အသုံးပြုပါသည်။
- Acrylonitrile Butadiene Styrene (ABS) - ABS သည် ၎င်း၏ ကြံ့ခိုင်မှု၊ တာရှည်ခံမှုနှင့် အပူဒဏ်ကြောင့် လူသိများသော စွယ်စုံသုံး ပလပ်စတစ်ပစ္စည်းဖြစ်သည်။ ဒက်ရှ်ဘုတ်များ၊ အကာအရံမီးတောက်များ၊ အရုပ်များနှင့် လူသုံးကုန်ပစ္စည်းများကဲ့သို့သော မော်တော်ယာဥ်အစိတ်အပိုင်းများထုတ်လုပ်ရန် မကြာခဏအသုံးပြုသည်။
- Polyamide (PA): နိုင်လွန်ဟုလည်းသိကြသော PA သည် အင်ဂျင်ကာဗာများနှင့် လေဝင်ပေါက်စနစ်များကဲ့သို့သော မော်တော်ယာဥ်အစိတ်အပိုင်းများထုတ်လုပ်ရာတွင် အသုံးများသော ခိုင်ခံ့ပေါ့ပါးသော ပလပ်စတစ်ပစ္စည်းဖြစ်သည်။ နှင်းလျှောစီးဖိနပ်များနှင့် တင်းနစ်ရက်ကက်များကဲ့သို့သော အားကစားပစ္စည်းများကိုလည်း ထုတ်လုပ်သည်။
- Polystyrene (PS) : PS သည် ခွက်များ၊ ခွက်များ၊ နှင့် အစားအသောက်ထည့်သော ဗူးများကဲ့သို့သော ထုပ်ပိုးပစ္စည်းများ ထုတ်လုပ်ရာတွင် အသုံးများသော ပေါ့ပါးပြီး တောင့်တင်းသော ပလတ်စတစ်ပစ္စည်းဖြစ်သည်။ အရုပ်များနှင့် အီလက်ထရွန်နစ် အစိတ်အပိုင်းများကဲ့သို့သော လူသုံးကုန်ပစ္စည်းများကိုလည်း ထုတ်လုပ်သည်။
- Polyethylene Terephthalate (PET) - PET သည် ပုလင်းများနှင့် ကွန်တိန်နာများကဲ့သို့သော ထုပ်ပိုးပစ္စည်းများကို ထုတ်လုပ်ရန်အတွက် အသုံးများသော ခိုင်ခံ့ပြီး ပွင့်လင်းသော ပလတ်စတစ်ပစ္စည်းဖြစ်သည်။ ချည်မျှင်နှင့် အထည်များထုတ်လုပ်ရန် အထည်အလိပ်လုပ်ငန်းတွင်လည်း အသုံးပြုသည်။
၎င်းတို့သည် ဆေးထိုးပုံသွင်းရာတွင် အသုံးအများဆုံး ပလတ်စတစ်အမျိုးအစားအချို့သာဖြစ်သည်။ အခြားပလတ်စတစ်ပစ္စည်းများ အမျိုးအစားများစွာကို ရရှိနိုင်ပြီး တစ်ခုချင်းစီတွင် ထူးခြားသော ဂုဏ်သတ္တိများနှင့် လက္ခဏာများရှိသည်။ ပလတ်စတစ်ပစ္စည်းရွေးချယ်မှုသည် ထုတ်လုပ်သည့်အစိတ်အပိုင်း သို့မဟုတ် ထုတ်ကုန်၏ သီးခြားလိုအပ်ချက်များပေါ်တွင် မူတည်မည်ဖြစ်သည်။
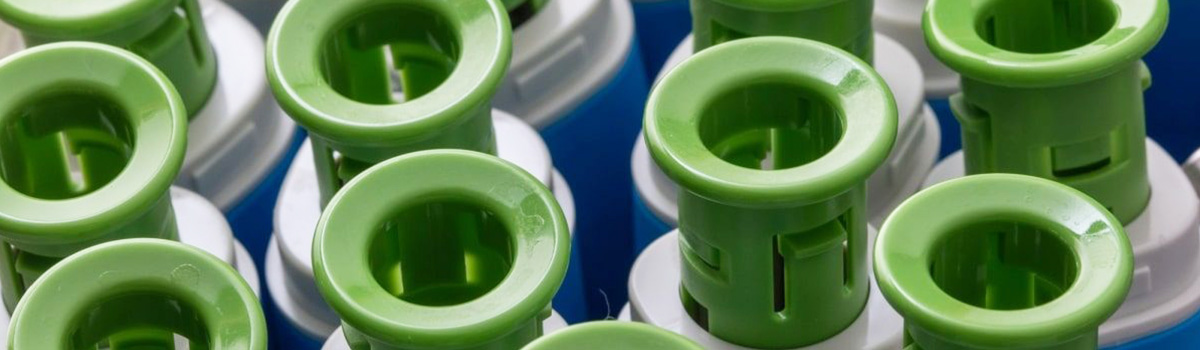
Injection Molding Machine အမျိုးအစားများ
ဆေးထိုးပုံသွင်းစက်များသည် အမျိုးအစားနှင့် အရွယ်အစားအမျိုးမျိုးရှိပြီး၊ တစ်ခုစီသည် သီးခြားထုတ်လုပ်မှုလိုအပ်ချက်များနှင့်ကိုက်ညီစေရန် ဒီဇိုင်းထုတ်ထားသည်။ ဤသည်မှာ ဆေးထိုးပုံသွင်းစက် အမျိုးအစားများထဲမှ အချို့ဖြစ်သည်။
- ဟိုက်ဒရောလစ်ထိုးသွင်းပုံသွင်းစက်- ဤစက်သည် မှိုထဲသို့ ပလပ်စတစ်ထိုးသွင်းရန် ဖိအားထုတ်ပေးရန် ဟိုက်ဒရောလစ်စွမ်းအင်ကို အသုံးပြုသည်။ ဟိုက်ဒရောလစ်စက်များကို ပုံမှန်အားဖြင့် ကုပ်တွယ်မှုအားကောင်းရန် လိုအပ်သော ပိုမိုထင်ရှားသော အစိတ်အပိုင်းများအတွက် အသုံးပြုကြသည်။
- Electric Injection Molding Machine- လျှပ်စစ်စက်များသည် ဆေးထိုးယူနစ်နှင့် ကလစ်ယန္တရားအား ပါဝါပေးရန်အတွက် လျှပ်စစ်မော်တာများကို အသုံးပြုသည်။ ၎င်းတို့သည် ၎င်းတို့၏ မြင့်မားသော တိကျမှုနှင့် စွမ်းအင်ထိရောက်မှုတို့ကြောင့် လူသိများပြီး သေးငယ်ပြီး အနုစိတ်သော အစိတ်အပိုင်းများကို ထုတ်လုပ်သည့်အတွက် ကျော်ကြားသည်။
- Hybrid Injection Molding Machine- Hybrid စက်များသည် လိုအပ်သော ဖိအားနှင့် ပါဝါကို ထုတ်လုပ်ရန် ဟိုက်ဒရောလစ်နှင့် လျှပ်စစ်ပါဝါ နှစ်မျိုးလုံးကို အသုံးပြု၍ ဟိုက်ဒရောလစ်နှင့် လျှပ်စစ်ပါဝါကို အသုံးပြု၍ ဟိုက်ဒရောလစ်နှင့် လျှပ်စစ်ပစ္စည်းများ၏ အကျိုးကျေးဇူးများကို ပေါင်းစပ်ထားသည်။ ဟိုက်ဘရစ်စက်များသည် အမြန်နှုန်း၊ တိကျမှုနှင့် စွမ်းအင်ထိရောက်မှု၏ မျှတမှုကို ပေးဆောင်သည်။
- Vertical Injection Molding Machine- ဒေါင်လိုက် စက်များသည် ထည့်သွင်းပုံသွင်းခြင်း သို့မဟုတ် ပုံသွင်းခြင်း လိုအပ်သော အစိတ်အပိုင်းများကို ထုတ်လုပ်သည်။ ၎င်းတို့တွင် သေးငယ်သော သို့မဟုတ် ရှုပ်ထွေးသော အစိတ်အပိုင်းများကို ဖန်တီးရန် စံပြအဖြစ် ပုံစံခွက်သို့ အလွယ်တကူ ဝင်ရောက်နိုင်စေမည့် ဒေါင်လိုက်ညှပ်ယူနစ်တစ်ခုရှိသည်။
- Two-Shot Injection Molding Machine- နှစ်ချက်ပစ်စက်များသည် မတူညီသော ပစ္စည်း သို့မဟုတ် အရောင်များဖြင့် အစိတ်အပိုင်းများကို ထုတ်လုပ်သည်။ စက်ပစ္စည်းတွင် ဆေးထိုးယူနစ် နှစ်ခုပါရှိပြီး တစ်ခုစီသည် မှိုထဲသို့ နိုင်ငံခြားပစ္စည်းများကို ထိုးသွင်းနိုင်သည်။ ဤစက်အမျိုးအစားကို လက်ကိုင်နှင့် လက်ကိုင်များကဲ့သို့သော မော်တော်ယာဥ်အစိတ်အပိုင်းများ ထုတ်လုပ်ရန်အတွက် အသုံးများသည်။
- Multi-Shot Injection Molding Machine- Multi-shot စက်များသည် ပစ္စည်း နှစ်ခု သို့မဟုတ် အရောင်များထက်ပိုသော အစိတ်အပိုင်းများကို ထုတ်လုပ်သည်။ စက်ပစ္စည်းတွင် ဆေးထိုးယူနစ်များစွာပါရှိပြီး တစ်ခုစီတွင် မတူညီသောပစ္စည်းတစ်ခုကို ပုံစံခွက်ထဲသို့ ထိုးသွင်းနိုင်သည်။ ဤစက်အမျိုးအစားကို သွားတိုက်တံနှင့် သင်တုန်းဓားများကဲ့သို့သော လူသုံးကုန်ပစ္စည်းများ ထုတ်လုပ်ရန်အတွက် အသုံးများသည်။
- All-Electric Injection Molding Machine- လျှပ်စစ်စက်အားလုံးသည် ဆေးထိုးယူနစ်၊ ကလစ်ယန္တရားနှင့် မှိုကို အားဖြည့်ရန်အတွက် လျှပ်စစ်မော်တာများကို အသုံးပြုသည်။ ၎င်းတို့သည် ၎င်းတို့၏ မြင့်မားသော တိကျမှု၊ မြန်နှုန်းနှင့် စွမ်းအင်ထိရောက်မှုတို့ကြောင့် လူသိများပြီး သေးငယ်ပြီး တိကျမှုမြင့်မားသော အစိတ်အပိုင်းများကို ထုတ်လုပ်သည့်အတွက် ကျော်ကြားသည်။
ဤအရာများသည် အတွေ့ရအများဆုံး ဆေးထိုးစက် အမျိုးအစား အနည်းငယ်မျှသာ ဖြစ်သည်။ စက်တစ်ခုစီတွင် ထူးခြားသောအင်္ဂါရပ်များနှင့် အားသာချက်များ ပါရှိသောကြောင့် တိကျသောထုတ်လုပ်မှုလိုအပ်ချက်များအတွက် သင့်လျော်သောစက်ပစ္စည်းကို ရွေးချယ်ရန် လိုအပ်ပါသည်။
Injection Molding Machine ၏ အစိတ်အပိုင်းများ
ဆေးထိုးပုံသွင်းစက်များတွင် ကုန်ကြမ်းများမှ ပလတ်စတစ်အစိတ်အပိုင်းများကို ဖန်တီးသည့် အစိတ်အပိုင်းများစွာရှိသည်။ ဤတွင် ဆေးထိုးစက်၏ အရေးကြီးသော အစိတ်အပိုင်းများ ဖြစ်သည် ။
Hopper- ရေလှောင်ကန်သည် ဆေးထိုးပုံသွင်းစက်ထဲသို့ မထည့်မီ ပလတ်စတစ်ကုန်ကြမ်းကို သိုလှောင်ထားသည်။ ပစ္စည်းသည် အများအားဖြင့် အမှုန့် သို့မဟုတ် အမှုန့်ပုံစံဖြစ်သည်။
စည်- စည်သည် ဆေးထိုးပုံသွင်းစက်၏ ရှည်လျားသော ဆလင်ဒါအစိတ်အပိုင်းဖြစ်ပြီး ဝက်အူများ အရည်ပျော်ကာ ပလပ်စတစ်ပစ္စည်းကို ရောနှောပေးသည့် ဝက်အူကို တည်ဆောက်ပေးသည်။
ဝက်အူ- ဝက်အူသည် ပလပ်စတစ်ပစ္စည်းကို ရှေ့သို့တွန်းထုတ်ကာ ပွတ်တိုက်မှုနှင့် အပူကြောင့် အရည်ပျော်သွားသည့် စည်အတွင်းဘက်လှည့်သည့်ကိရိယာဖြစ်သည်။
ဆေးထိုးယူနစ်- ဆေးထိုးယူနစ်တွင် ခုန်ပေါက်၊ စည်၊ ဝက်အူများ ပါဝင်ပြီး ပလပ်စတစ်အရည်ပျော်ခြင်းနှင့် မှိုထဲသို့ ထိုးသွင်းခြင်းအတွက် တာဝန်ရှိသည်။
Clamping ယူနစ်- ကုပ်ယူနစ်သည် ဆေးထိုးပုံသွင်းခြင်းလုပ်ငန်းစဉ်အတွင်း မှိုကို လုံခြုံစွာ ကိုင်ထားပြီး လိုအပ်သော ဖိအားကို အသုံးပြုရန် တာဝန်ရှိသည်။
မှို- မှိုသည် ပလပ်စတစ်အစိတ်အပိုင်း၏ ပုံသဏ္ဍာန်နှင့် အရွယ်အစားကို ဖန်တီးပေးသည့် ကိရိယာဖြစ်သည်။ ပုံစံခွက်ကို ပုံမှန်အားဖြင့် သံမဏိဖြင့် ပြုလုပ်ထားပြီး လိုက်ဖက်သော အပိုင်းနှစ်ပိုင်း ပါဝင်ပါသည်။
နော်ဇယ်- နော်ဇယ်သည် ဆေးထိုးယူနစ်၏ အစိတ်အပိုင်းဖြစ်ပြီး ဆေးထိုးပုံသွင်းစက်ကို မှိုနှင့် ချိတ်ဆက်ပေးသည်။ အရည်ကျိုထားသော ပလပ်စတစ်ပစ္စည်းကို နော်ဇယ်မှတဆင့် မှိုထဲသို့ ထိုးသွင်းသည်။
အအေးခံစနစ်- အအေးခံစနစ်သည် မှိုထဲသို့ ထိုးသွင်းပြီးသည်နှင့် ပလပ်စတစ်အစိတ်အပိုင်းကို အအေးခံရန် တာဝန်ရှိသည်။ ၎င်းသည် အပိုင်းအစကို ခိုင်မာစေပြီး ပျက်စီးခြင်းမရှိဘဲ မှိုမှဖယ်ရှားနိုင်သည်ကို သေချာစေသည်။
ထိန်းချုပ်အကန့်- ထိန်းချုပ်အကန့်သည် အော်ပရေတာအား အပူချိန်၊ ဖိအားနှင့် စက်ဝန်းအချိန်ကဲ့သို့သော ဆေးထိုးပုံသွင်းစက်၏ ဆက်တင်များကို စောင့်ကြည့် ချိန်ညှိရန် ခွင့်ပြုသည့် အင်တာဖေ့စ်ဖြစ်သည်။
ဤအစိတ်အပိုင်းတစ်ခုစီသည် ဆေးထိုးပုံသွင်းခြင်းလုပ်ငန်းစဉ်တွင် အရေးပါသောအခန်းကဏ္ဍမှပါဝင်ပြီး အရည်အသွေးမြင့်သောအစိတ်အပိုင်းများကို ထိထိရောက်ရောက်ထုတ်လုပ်ကြောင်းသေချာစေရန် အပိုင်းတစ်ခုချင်းစီကို ထိန်းသိမ်းရန်နှင့် အကောင်းဆုံးဖြစ်အောင်ပြုလုပ်ရန် အရေးကြီးပါသည်။
Injection Molding Tooling- ဒီဇိုင်းနှင့် ထုတ်လုပ်ရေး
ဆေးထိုးပုံသွင်းကိရိယာသည် ပလပ်စတစ်အစိတ်အပိုင်းများထုတ်လုပ်ရန်အတွက် ဆေးထိုးပုံသွင်းစက်များတွင် အသုံးပြုသည့်မှိုများကို ဒီဇိုင်းထုတ်ခြင်းနှင့် ထုတ်လုပ်ခြင်းကို ရည်ညွှန်းသည်။ မှိုများ၏ အရည်အသွေးနှင့် ထိရောက်မှုသည် ဆေးထိုးပုံသွင်းခြင်းလုပ်ငန်းစဉ်၏ အရည်အသွေးနှင့် ကုန်ထုတ်စွမ်းအားကို တိုက်ရိုက်ထိခိုက်စေပါသည်။ ဤတွင် ဆေးထိုးပုံသွင်းကိရိယာ၏ ဒီဇိုင်းနှင့် ထုတ်လုပ်ရေးတွင် အရေးကြီးသော အဆင့်များ ဖြစ်သည်-
ထုတ်ကုန်ဒီဇိုင်း- ဆေးထိုးပုံသွင်းကိရိယာ၏ ပထမအဆင့်မှာ ထုတ်ကုန်ထုတ်လုပ်ရန် ဒီဇိုင်းဆွဲခြင်းဖြစ်သည်။ ထုတ်ကုန်ဒီဇိုင်းတွင် အစိတ်အပိုင်း၏ အရွယ်အစား၊ ပုံသဏ္ဍာန်နှင့် ပစ္စည်းကို သတ်မှတ်ခြင်းအပြင် သီးခြားအင်္ဂါရပ်များ သို့မဟုတ် လိုအပ်ချက်များ ပါဝင်သည်။
မှိုဒီဇိုင်း- ထုတ်ကုန်ဒီဇိုင်း အပြီးသတ်ပြီးသည်နှင့် မှိုဒီဇိုင်းလုပ်ငန်းစဉ် စတင်သည်။ မှိုဒီဇိုင်နာသည် အကောင်းဆုံးမှိုအမျိုးအစား၊ လိုအပ်သော အပေါက်အရေအတွက်နှင့် မှို၏အရွယ်အစားနှင့် ပုံသဏ္ဍာန်တို့ကို ဆုံးဖြတ်ပေးမည်ဖြစ်သည်။
မှိုတည်ဆောက်မှု- မှိုကို သံမဏိ သို့မဟုတ် အလူမီနီယမ်ကဲ့သို့သော အရည်အသွေးမြင့်ပစ္စည်းများကို အသုံးပြု၍ မှိုဒီဇိုင်းကို အခြေခံ၍ တည်ဆောက်ထားသည်။ မှိုကို ပုံမှန်အားဖြင့် နှစ်ခြမ်းခွဲထားပြီး တစ်ခုချင်းစီတွင် အပေါက်တစ်ခု သို့မဟုတ် တစ်ခုထက်ပိုသော အပေါက်များပါရှိသည်။
မှိုတပ်ဆင်ခြင်း- မှိုကိုတည်ဆောက်ပြီးသည်နှင့် ၎င်းကို တိကျမှုနှင့် လုပ်ဆောင်နိုင်စွမ်းအတွက် စုစည်းပြီး စမ်းသပ်သည်။ မှိုသည် ဆေးထိုးပုံသွင်းခြင်းလုပ်ငန်းစဉ်၏ ဖိအားနှင့် အပူကို ခံနိုင်ရည်ရှိရမည်။
မှိုစမ်းသပ်ခြင်းနှင့် အတည်ပြုခြင်း- မှိုကို တပ်ဆင်ပြီးနောက်၊ ၎င်းသည် ထုတ်ကုန်သတ်မှတ်ချက်များနှင့် ကိုက်ညီသည့် အရည်အသွေးမြင့် အစိတ်အပိုင်းများကို ထုတ်လုပ်ကြောင်း သေချာစေရန် ၎င်းကို စမ်းသပ်ပြီး တရားဝင်စစ်ဆေးသည်။ မှိုသည် ၎င်း၏စွမ်းဆောင်ရည်ကို မြှင့်တင်ရန် ချိန်ညှိရန် သို့မဟုတ် ပြုပြင်ရန် လိုအပ်နိုင်သည်။
မှိုထိန်းသိမ်းခြင်း- မှို၏ သက်တမ်းနှင့် စွမ်းဆောင်ရည်ကို သေချာစေရန်အတွက် ပုံမှန်ထိန်းသိမ်းခြင်းနှင့် ပြုပြင်ခြင်းသည် အရေးကြီးပါသည်။ သန့်ရှင်းရေး၊ ချောဆီနှင့် ဟောင်းနွမ်းပျက်စီးနေသည့် အစိတ်အပိုင်းများကို အစားထိုးခြင်း ပါဝင်သည်။
ဆေးထိုးပုံသွင်းကိရိယာသည် အရည်အသွေးမြင့် အစိတ်အပိုင်းများကို တသမတ်တည်းနှင့် ထိရောက်စွာ ထုတ်လုပ်နိုင်ရန် တိကျမှုနှင့် ကျွမ်းကျင်မှု လိုအပ်သည်။ ပြီးပြည့်စုံသော ဒီဇိုင်းနှင့် ထုတ်လုပ်ရေး လုပ်ငန်းစဉ်ကို လိုက်နာခြင်းဖြင့် ထုတ်လုပ်သူများသည် ၎င်းတို့၏ ထုတ်ကုန်များ၏ ထူးခြားသော လိုအပ်ချက်များနှင့် ကိုက်ညီသော မှိုများကို ပြုလုပ်နိုင်ပြီး ၎င်းတို့၏ ဆေးထိုးပုံသွင်းခြင်း လုပ်ငန်းစဉ်များကို အကောင်းဆုံးဖြစ်အောင် လုပ်ဆောင်နိုင်သည်။
Injection Molding Tooling အမျိုးအစားများ
Injection molding သည် အစိတ်အပိုင်း အများအပြား ထုတ်လုပ်ရန်အတွက် တွင်ကျယ်စွာ အသုံးပြုသည့် ထုတ်လုပ်မှု လုပ်ငန်းစဉ်တစ်ခု ဖြစ်သည်။ ၎င်းတွင် သွန်းသောပလပ်စတစ်ကို မှိုအပေါက်ထဲသို့ ထိုးသွင်းပြီး ၎င်းကို အေးမြစေပြီး လိုချင်သောပုံစံသို့ ခိုင်မာစေခြင်း ပါဝင်သည်။ Injection molding tooling သည် ဆေးထိုးပုံသွင်းရာတွင် အသုံးပြုသော မှိုများကို ဖန်တီးသည့် လုပ်ငန်းစဉ်ဖြစ်သည်။ ဆေးထိုးပုံသွင်းကိရိယာ အမျိုးအစားများစွာရှိပြီး တစ်ခုစီတွင် ၎င်း၏ အားသာချက်များနှင့် အားနည်းချက်များရှိသည်။
- Two-Plate Molds ပန်းကန်ပြားနှစ်ချပ်မှိုများသည် အရိုးရှင်းဆုံး ဆေးထိုးခြင်းကိရိယာ အမျိုးအစားဖြစ်သည်။ ၎င်းတို့တွင် မှိုအပေါက်တစ်ခုဖြစ်လာစေရန် ပန်းကန်ပြားနှစ်ခုပါ၀င်သည်။ သွန်းသောပလပ်စတစ်ကို တံခါးပေါက်မှတဆင့် အပေါက်ထဲသို့ ထိုးသွင်းပြီး အေးမြစေပြီး ခိုင်မာစေပါသည်။ အပိုင်းကို ဖန်တီးပြီးသည်နှင့် ပန်းကန်ပြားနှစ်ခုကို ခွဲထုတ်ပြီး ပမာဏကို ထုတ်လွှတ်သည်။ ပန်းကန်ပြားနှစ်ချပ်မှိုများကို ရိုးရှင်းသော ဂျီသြမေတြီများဖြင့် အသေးစားမှ အလတ်စား အစိတ်အပိုင်းများအတွက် အသုံးများသည်။
- Three-Plate Molds ပန်းကန်ပြားသုံးချပ်မှိုများသည် ပန်းကန်ပြားနှစ်ချပ်မှိုများနှင့် ဆင်တူသော်လည်း ၎င်းတို့တွင် ပုံသွင်းထားသောအပိုင်းကို အပြေးစနစ်နှင့် ပိုင်းခြားထားသည့် stripper plate ဟုခေါ်သော နောက်ထပ်ပန်းကန်တစ်ခုရှိသည်။ အပြေးသမားစနစ်သည် မှိုပေါက်အတွင်းသို့ သွန်းသောပလပ်စတစ်များကို ပို့ဆောင်ပေးသည့် ချန်နယ်ကွန်ရက်ဖြစ်သည်။ ပိုသိသာထင်ရှားသော အစိတ်အပိုင်းများနှင့် ပိုမိုရှုပ်ထွေးသော ဂျီသြမေတြီများအတွက် သုံးပန်းကန်မှိုများကို အသုံးပြုပါသည်။
- Hot Runner Molds ပူသောအပြေးသမားမှိုများတွင်၊ သွန်းသောပလပ်စတစ်ကို ဂိတ်ပေါက်မှတဆင့်မဟုတ်ဘဲ အပူပေးသောလမ်းကြောင်းများမှတဆင့် မှိုအပေါက်ထဲသို့ တိုက်ရိုက်ထိုးသွင်းပါသည်။ ၎င်းသည် အပြေးစနစ်တွင် စွန့်ပစ်ပစ္စည်းများကို လျော့နည်းစေပြီး ပိုမိုထိရောက်သော လုပ်ငန်းစဉ်ကို ရရှိစေသည်။ ရှုပ်ထွေးသောအစိတ်အပိုင်းများ၏ ထုထည်မြင့်မားသော ထုတ်လုပ်မှုအတွက် အပူပြေးမှိုများကို အသုံးပြုသည်။
- Family Molds မိသားစုမှိုများသည် မှိုတစ်ခုတည်းတွင် အစိတ်အပိုင်းများစွာကို ထုတ်လုပ်သည်။ ၎င်းတို့တွင် များပြားလှသော ဒိုမိန်းများကို တစ်ပြိုင်နက် ထုတ်လုပ်နိုင်စေမည့် နည်းလမ်းဖြင့် စီထားသော အမျိုးမျိုးသော အပေါက်များရှိသည်။ မိသားစုမှိုများကို အများအားဖြင့် အသေးစားမှ အလတ်စား ထုထည်ရှိသော အစိတ်အပိုင်းများအတွက် အသုံးပြုကြသည်။
- မှိုထည့်ခြင်း မှိုထည့်ခြင်း သတ္တု သို့မဟုတ် ပလပ်စတစ်ထည့်ရန် လိုအပ်သော အစိတ်အပိုင်းများကို မှိုထည့်ပါ။ ထည့်သွင်းမှုများကို သွန်းသောပလပ်စတစ်ကို မထိုးသွင်းမီ မှိုအပေါက်ထဲသို့ ထည့်ထားသည်။ ပလပ်စတစ်အအေးခံပြီး ခိုင်မာသွားသောအခါ၊ အစိတ်အပိုင်းနှင့် ပေါင်းထည့်မှုကို အမြဲတမ်း ချည်နှောင်ထားသည်။ မှိုထည့်သွင်းခြင်းကို ခိုင်ခံ့မှု၊ တာရှည်ခံမှု၊ သို့မဟုတ် အလှအပဆိုင်ရာ ဆွဲဆောင်မှု လိုအပ်သော ရာထူးများအတွက် အသုံးပြုသည်။
- Overmolding Overmolding သည် အစိတ်အပိုင်းတစ်ခုကို အခြားတစ်ခုသို့ ပုံသွင်းသည့် လုပ်ငန်းစဉ်တစ်ခုဖြစ်သည်။ နူးညံ့သော အထိအတွေ့ သို့မဟုတ် ပိုမိုကောင်းမွန်သော ဆုပ်ကိုင်မှု လိုအပ်သော အနေအထားများအတွက် ၎င်းကို မကြာခဏ အသုံးပြုသည်။ Overmolding သည် ပထမအလွှာ သို့မဟုတ် အောက်ခံအပိုင်းကို သတ်မှတ်ပြီး ဒုတိယပစ္စည်းကို ပုံသွင်းခြင်းတွင် ပါဝင်ပါသည်။ ဒုတိယပစ္စည်းသည် မတူညီသောပလပ်စတစ်အမျိုးအစား၊ ရော်ဘာကဲ့သို့သောအရာ သို့မဟုတ် သာမိုပလတ်စတစ် အီလက်စတိုမာဖြစ်နိုင်သည်။
နိဂုံးချုပ်အနေနှင့်၊ ဆေးထိုးပုံသွင်းကိရိယာ၏ရွေးချယ်မှုသည် ထုတ်လုပ်သည့်အစိတ်အပိုင်းအမျိုးအစား၊ လိုအပ်သောထုတ်လုပ်မှုပမာဏနှင့် အစိတ်အပိုင်းဒီဇိုင်းတွင်ပါဝင်သော ရှုပ်ထွေးမှုအဆင့်တို့အပေါ် မူတည်ပါသည်။ လုပ်ငန်းစဉ်သည် ထိရောက်ပြီး ကုန်ကျစရိတ်သက်သာကြောင်း သေချာစေရန် သင့်လျော်သောကိရိယာကို ရွေးချယ်ခြင်းသည် မရှိမဖြစ်လိုအပ်ပါသည်။
Injection Molding Design လမ်းညွှန်ချက်များ
Injection molding သည် ပလပ်စတစ် အစိတ်အပိုင်းများ ထုတ်လုပ်ရန်အတွက် တွင်ကျယ်စွာ အသုံးပြုသော ကုန်ထုတ်လုပ်မှု လုပ်ငန်းစဉ်တစ်ခု ဖြစ်သည်။ ဆေးထိုးပုံသွင်းခြင်းအတွက် အစိတ်အပိုင်းများကို ဒီဇိုင်းထုတ်ရာတွင် အသေးစိတ်အချက်အလက်များကို အောင်မြင်စွာထုတ်လုပ်နိုင်စေရန် သေချာစေရန် လုပ်ငန်းစဉ်များ၊ ပစ္စည်းများနှင့် ဒီဇိုင်းလမ်းညွှန်ချက်များကို ကောင်းစွာနားလည်ရန် လိုအပ်ပါသည်။ အောက်ဖော်ပြပါ ဆေးထိုးပုံသွင်းခြင်း ဒီဇိုင်းလမ်းညွှန်ချက်အချို့မှာ အောက်ပါအတိုင်းဖြစ်သည်။
နံရံအထူ၊ အစိတ်အပိုင်း၏ နံရံအထူသည် လိုအပ်သော ကြံ့ခိုင်မှုနှင့် လုပ်ဆောင်နိုင်စွမ်းကို ထိန်းသိမ်းထားစဉ် ဖြစ်နိုင်သမျှ တစ်ပြေးညီဖြစ်ပြီး ပါးလွှာသင့်သည်။ ၎င်းသည် အအေးခံချိန်နှင့် စက်လည်ပတ်ချိန်ကို လျှော့ချပေးကာ warping နှင့် sink marks ဖြစ်နိုင်ခြေကို လျှော့ချပေးသည်။
Ribs နှင့် Bosses Ribs နှင့် Bosses များသည် အစိတ်အပိုင်း၏ ကြံ့ခိုင်မှုနှင့် တောင့်တင်းမှုကို တိုးမြှင့်ရန်အတွက် အသုံးပြုနိုင်သည်။ နံရိုးများသည် အမည်ခံနံရံအထူ၏ 60% ထက်မပိုသင့်ဘဲ အထက်လူကြီးများသည် အမည်ခံနံရံအထူ၏ 1.5 ဆ ဖြစ်သင့်သည်။
Draft Angle၊ တစ်စိတ်တစ်ပိုင်း ထုတ်လွှတ်မှုကို လွယ်ကူချောမွေ့စေပြီး မှိုပျက်စီးမှုကို ကာကွယ်ရန် ဒေါင်လိုက်မျက်နှာပြင်အားလုံးတွင် အနည်းဆုံး 1-2 ဒီဂရီ အကြမ်းထောင့်ကို အသုံးပြုသင့်သည်။
ကွဲအက်ခြင်းနှင့် ပျက်ကွက်ခြင်းတို့ကို ဖြစ်ပေါ်စေနိုင်သည့် ဖိစီးမှုအာရုံစူးစိုက်မှုကို တားဆီးရန် အသားလွှာများနှင့် Radii ချွန်ထက်သောထောင့်များနှင့် အစွန်းများကို ရှောင်ရှားသင့်သည်။ ယင်းအစား၊ အသားလွှာများနှင့် အချင်းများသည် စိတ်ဖိစီးမှုကို ဖြန့်ဝေပေးပြီး အစိတ်အပိုင်း၏ ကြံ့ခိုင်မှုကို မြှင့်တင်ပေးသင့်သည်။
Gates and Runners တံခါးများနှင့် အပြေးသမားများ၏ တည်နေရာနှင့် ဒီဇိုင်းသည် ကောင်းမွန်သော အစိတ်အပိုင်း အရည်အသွေးကို ရရှိရန်အတွက် အရေးကြီးပါသည်။ ဝင်ပေါက်များသည် အစိတ်အပိုင်း၏ အထူဆုံးအပိုင်းတွင် တတ်နိုင်သမျှ သေးငယ်သင့်သည်။ အပြေးသမားများသည် ဖိအားကျဆင်းမှုနှင့် စီးဆင်းမှုကို အမြင့်ဆုံးဖြစ်စေရန် ဒီဇိုင်းထုတ်သင့်သည်။
Surface Finish အစိတ်အပိုင်း၏ မျက်နှာပြင် အပြီးသတ်မှုသည် လျှောက်လွှာလိုအပ်ချက်များအပေါ် အခြေခံ၍ သတ်မှတ်သင့်သည်။ မြင်သာသောအပိုင်းများအတွက် ပိုမိုမြင့်မားသော မျက်နှာပြင်အချောထည် လိုအပ်နိုင်သော်လည်း အောက်မျက်နှာပြင်အချောထည်သည် လျှို့ဝှက်အစိတ်အပိုင်းများအတွက် လက်ခံနိုင်မည်ဖြစ်သည်။
ပစ္စည်းရွေးချယ်ခြင်း အပိုင်းအတွက် ရွေးချယ်ထားသော ပစ္စည်းသည် ဆေးထိုးပုံသွင်းခြင်းအတွက် သင့်လျော်ပြီး လိုအပ်သော စက်ပိုင်းဆိုင်ရာ၊ အပူနှင့် ဓာတုဂုဏ်သတ္တိများနှင့် ကိုက်ညီသင့်ပါသည်။
Injection Molding တွင် Secondary Operations
Injection molding သည် အမျိုးမျိုးသော ပလပ်စတစ် အစိတ်အပိုင်းများ ထုတ်လုပ်ရန် အသုံးပြုသည့် စွယ်စုံသုံး ကုန်ထုတ်လုပ်မှု လုပ်ငန်းစဉ်တစ်ခု ဖြစ်သည်။ ပင်မပုံသွင်းခြင်းလုပ်ငန်းစဉ်အပြင်၊ ရာထူးများစွာသည် လိုချင်သောပုံသဏ္ဍာန်၊ ပြီးစီးမှု သို့မဟုတ် လုပ်ဆောင်နိုင်စွမ်းကိုရရှိရန် ဆင့်ပွားလုပ်ဆောင်မှုများ လိုအပ်သည်။ ဆေးထိုးပုံသွင်းခြင်းတွင် နေ့စဉ် ဆင့်ပွားလုပ်ဆောင်မှုအချို့မှာ အောက်ပါအတိုင်းဖြစ်သည်။
- မှိုမှိုထုတ်ပြီးနောက် ပုံသွင်းထားသောအပိုင်းမှ ပိုလျှံနေသောပစ္စည်းများကို ဖြတ်တောက်ခြင်းသည် ဖယ်ရှားခြင်းဖြစ်သည်။ ၎င်းကို ချုံ့နှိပ်ခြင်း သို့မဟုတ် CNC စက်ဖြင့် ပြုလုပ်လေ့ရှိသည်။ အစိတ်အပိုင်း၏နောက်ဆုံးပုံသဏ္ဍာန်နှင့်အရွယ်အစားကိုရရှိရန်မကြာခဏဖြတ်တောက်ရန်လိုအပ်သည်။
- ဂဟေဆော်ခြင်းသည် အပူ၊ ဖိအား သို့မဟုတ် နှစ်ခုလုံးကို ပေါင်းစပ်အသုံးပြု၍ ပလပ်စတစ် အစိတ်အပိုင်းနှစ်ခု သို့မဟုတ် ထို့ထက်ပိုသော အစိတ်အပိုင်းများကို ပေါင်းစပ်ထားသည်။ ၎င်းကို ပုံစံခွက်တစ်ခုတည်းတွင် မထုတ်လုပ်နိုင်သော ပိုမိုကြီးမားသော သို့မဟုတ် ပိုမိုရှုပ်ထွေးသော အင်္ဂါရပ်များကို ဖန်တီးရန် ၎င်းကို မကြာခဏအသုံးပြုသည်။
- Decorating သည် ပုံသွင်းထားသော အစိတ်အပိုင်း၏ မျက်နှာပြင်တွင် အမြင်အာရုံ သို့မဟုတ် လုပ်ဆောင်နိုင်သော အင်္ဂါရပ်များကို ပေါင်းထည့်သည့် လုပ်ငန်းစဉ်ဖြစ်သည်။ ၎င်းတွင် ပန်းချီ၊ ပုံနှိပ်ခြင်း၊ အညွှန်းတပ်ခြင်း သို့မဟုတ် အသွင်အပြင် သို့မဟုတ် ပုံစံကို အသုံးပြုခြင်းတို့ ပါဝင်နိုင်သည်။
- စည်းဝေးပွဲသည် ပြီးပြည့်စုံသောထုတ်ကုန်တစ်ခုဖန်တီးရန် အစိတ်အပိုင်းများစွာကို ပေါင်းစပ်ခြင်းလုပ်ငန်းစဉ်ဖြစ်သည်။ ၎င်းကို တွယ်ကပ်များ၊ ကော်များ သို့မဟုတ် အခြားသော ပေါင်းစည်းနည်းများကို အသုံးပြု၍ လုပ်ဆောင်နိုင်သည်။
- Insert Molding Insert molding ဆိုသည်မှာ ကြိုတင်ဖွဲ့စည်းထားသော သတ္တု သို့မဟုတ် ပလပ်စတစ် ပတ်ပတ်လည်တွင် ပလပ်စတစ်ပုံသွင်းခြင်း ဖြစ်သည်။ ခိုင်ခံ့မှု သို့မဟုတ် တာရှည်ခံမှု အဆင့်မြင့်မားသော အစိတ်အပိုင်းများကို ဖန်တီးရန် ၎င်းကို မကြာခဏ အသုံးပြုသည်။
- Overmolding Overmolding သည် မဖွဲ့စည်းမီ အစိတ်အပိုင်းတစ်ခုအပေါ် ဒုတိယပစ္စည်းကို ပုံသွင်းသည့် လုပ်ငန်းစဉ်ဖြစ်သည်။ ၎င်းသည် ပျော့ပျောင်းသောထိတွေ့မျက်နှာပြင်ကို ပေါင်းထည့်နိုင်သည်၊ ချုပ်ကိုင်မှုကို ပိုမိုကောင်းမွန်စေသည်၊ သို့မဟုတ် နှစ်ရောင်စပ် သို့မဟုတ် ဘက်စုံပစ္စည်းအပိုင်းအစကို ဖန်တီးနိုင်သည်။
- အပေါ်ယံပိုင်းသည် ၎င်း၏အသွင်အပြင်၊ တာရှည်ခံမှု သို့မဟုတ် အခြားဂုဏ်သတ္တိများကို ပိုမိုကောင်းမွန်စေရန်အတွက် ပါးလွှာသောပစ္စည်းအလွှာကို အသုံးပြုသည်။ ၎င်းတွင် chrome၊ နီကယ် သို့မဟုတ် အမှုန့်အပေါ်ယံအလွှာများ ကဲ့သို့သော coatings များ ပါဝင်နိုင်သည်။
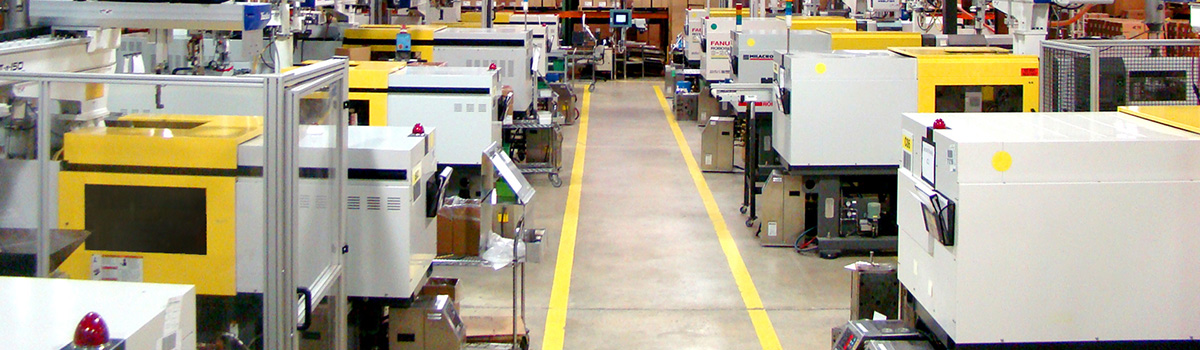
Plastic Injection မှို၏အားသာချက်များ
ပလပ်စတစ်ဆေးထိုးပုံသွင်းခြင်းသည် တိကျမှု၊ ညီညွတ်မှုနှင့် အရည်အသွေးမြင့်မားသော ပလတ်စတစ်အစိတ်အပိုင်းများထုတ်လုပ်ရန်အတွက် တွင်ကျယ်စွာအသုံးပြုသည့် ထုတ်လုပ်မှုလုပ်ငန်းစဉ်တစ်ခုဖြစ်သည်။ ၎င်းတွင် သွန်းသောပလပ်စတစ်ကို မှိုအပေါက်ထဲသို့ ထိုးသွင်းပြီး အေးမြစေပြီး ခိုင်မာစေခြင်း ပါဝင်သည်။ ပလပ်စတစ်ဆေးထိုးခြင်း၏ အားသာချက်အချို့မှာ အောက်ပါအတိုင်းဖြစ်သည်။
- မြင့်မားသော စွမ်းဆောင်ရည်နှင့် ကုန်ထုတ်စွမ်းအားမြင့် ပလပ်စတစ်ဆေးထိုးပုံသွင်းခြင်းသည် မြင့်မားသော လိုက်လျောညီထွေရှိပြီး အရည်အသွေးမြင့်မားသော အစိတ်အပိုင်းအများအပြားကို ထုတ်လုပ်ပေးနိုင်သည့် မြင့်မားသော ထိရောက်ပြီး အလိုအလျောက်လုပ်ဆောင်သည့် လုပ်ငန်းစဉ်တစ်ခုဖြစ်သည်။ အဆင့်မြင့် automation နည်းပညာဖြင့်၊ ထုတ်လုပ်မှုစက်ဝန်းအချိန်ကို စက္ကန့်အထိ လျှော့ချနိုင်ပြီး ရှုပ်ထွေးပြီး အနုစိတ်သော အစိတ်အပိုင်းများကို ထုထည်မြင့်မားစွာ ထုတ်လုပ်နိုင်စေပါသည်။
- မြင့်မားသော တိကျမှုနှင့် တိကျသော ထိုးသွင်းပုံသွင်းခြင်းသည် ရှုပ်ထွေးပြီး အနုစိတ်သော အစိတ်အပိုင်းများကို ထုတ်လုပ်ရာတွင် တိကျမှုနှင့် တိကျမှုကို တိုးစေသည်။ ကွန်ပြူတာထိန်းချုပ်သည့် စက်ယန္တရားများနှင့် အဆင့်မြင့်ဆော့ဖ်ဝဲများသည် ထပ်ခါတလဲလဲဖြစ်နိုင်မှုနှင့် တိကျမှုမြင့်မားသော တင်းကျပ်သောသည်းခံမှုကို ပံ့ပိုးပေးသည်။
- Versatility Injection molding သည် အရွယ်အစားအမျိုးမျိုး၊ ပုံသဏ္ဍာန်များနှင့် ရှုပ်ထွေးမှုအမျိုးမျိုးရှိသော ပလတ်စတစ်အစိတ်အပိုင်းများကို ကျယ်ပြန့်စွာထုတ်လုပ်နိုင်သော စွယ်စုံရ လုပ်ငန်းစဉ်တစ်ခုဖြစ်သည်။ ရှုပ်ထွေးသော ဂျီသြမေတြီများဖြင့် အသေးစိပ်အသေးစိတ်များအထိ အရာခပ်သိမ်းကို သေးငယ်သောအပိုင်းအစများအထိ ပြုလုပ်ရန် လုပ်ငန်းစဉ်ကို အသုံးပြုနိုင်သည်။
- Material Flexibility Injection molding သည် သာမိုပလတ်စတစ်များ၊ သာမိုဆက်ကိရိယာများနှင့် အီလက်စတိုမာများ အပါအဝင် ပလတ်စတစ်ပစ္စည်းများကို ကျယ်ပြန့်စွာ အသုံးပြုနိုင်သည်။ ၎င်းသည် အမျိုးမျိုးသော စက်ပိုင်းဆိုင်ရာ၊ အပူနှင့် ဓာတုဂုဏ်သတ္တိများဖြင့် အစိတ်အပိုင်းများကို ထုတ်လုပ်နိုင်စေပါသည်။
- Low Waste Production Injection Molding သည် ထုတ်လုပ်မှုအတွင်း အမှိုက်အနည်းငယ်သာ ထုတ်ပေးသောကြောင့် အမှိုက်နည်းသော ထုတ်လုပ်မှုလုပ်ငန်းစဉ်တစ်ခုဖြစ်သည်။ ပိုလျှံနေသည့် မည်သည့်ပစ္စည်းမဆို အလွယ်တကူ ပြန်လည်အသုံးပြုနိုင်ပြီး ထုတ်လုပ်မှုတွင် ပြန်လည်အသုံးပြုနိုင်ပြီး ၎င်းကို သဘာဝပတ်ဝန်းကျင်နှင့် သဟဇာတဖြစ်သော ထုတ်လုပ်မှုလုပ်ငန်းစဉ်တစ်ခု ဖြစ်လာစေပါသည်။
- လုပ်သားကုန်ကျစရိတ်များ လျှော့ချပေးခြင်း ဆေးထိုးပုံသွင်းခြင်းတွင် မြင့်မားသော အလိုအလျောက်စနစ်၏ အတိုင်းအတာသည် လုပ်သားအင်အားသုံး လုပ်ငန်းစဉ်များအတွက် လိုအပ်မှုကို နည်းပါးစေပြီး လုပ်သားစရိတ်များကို သိသိသာသာ လျှော့ချပေးသည်။ ၎င်းသည် လူ့အမှား၏အန္တရာယ်ကိုလည်း လျှော့ချပေးကာ နောက်ဆုံးထုတ်ကုန်၏ အရည်အသွေးနှင့် လိုက်လျောညီထွေရှိမှုကို တိုးတက်စေသည်။
- ထုတ်လုပ်မှုပြီးသော လုပ်ဆောင်ချက်များကို လျှော့ချပြီး ထိုးသွင်းပုံသွင်းခြင်းသည် အစိတ်အပိုင်းများကို မြင့်မားသော တိကျမှုနှင့် လိုက်လျောညီထွေဖြစ်စေပြီး ဖြတ်တောက်ခြင်း၊ တူးဖော်ခြင်း သို့မဟုတ် ကြိတ်ခြင်းကဲ့သို့သော ထုတ်လုပ်မှုနောက်ပိုင်း လုပ်ငန်းဆောင်တာများအတွက် လိုအပ်မှုကို လျှော့ချပေးသည်။ ၎င်းသည် နောက်ဆုံးထုတ်ကုန်၏ ထုတ်လုပ်မှုအချိန်နှင့် ကုန်ကျစရိတ်ကို လျော့နည်းစေသည်။
- တသမတ်တည်းနှင့် အရည်အသွေးကို ထိုးသွင်းပုံသွင်းခြင်းသည် လိုက်လျောညီထွေရှိပြီး အရည်အသွေးမြင့်မားသော အစိတ်အပိုင်းများကို ထုတ်လုပ်ပေးပါသည်။ အဆင့်မြင့်နည်းပညာနှင့် ကွန်ပျူတာဖြင့် ထိန်းချုပ်ထားသော စက်ယန္တရားများသည် အသေးစိတ်တစ်ခုချင်းစီ၏ ပုံသဏ္ဍာန်၊ အရွယ်အစားနှင့် အရည်အသွေးတူညီကြောင်း သေချာစေသည်။
- ဒီဇိုင်း Flexibility Injection molding သည် ရှုပ်ထွေးသော ဂျီသြမေတြီများ၊ ဖြတ်တောက်မှုများ၊ ရှုပ်ထွေးသောအသေးစိတ်အချက်များဖြင့် အစိတ်အပိုင်းများကို ထုတ်လုပ်နိုင်သောကြောင့် ဒီဇိုင်းပြောင်းလွယ်ပြင်လွယ် မြင့်မားစွာ ပံ့ပိုးပေးပါသည်။ ၎င်းသည် အခြားကုန်ထုတ်မှုလုပ်ငန်းစဉ်များကို အသုံးပြု၍ ပြုလုပ်၍မရသော ထူးခြားသောပုံစံများနှင့် လုပ်ဆောင်ချက်များဖြင့် ဒီဇိုင်နာများကို ဖန်တီးနိုင်စေမည်ဖြစ်သည်။
- ထုထည်မြင့်မားသော ထုတ်လုပ်မှုအတွက် ကုန်ကျစရိတ်သက်သာပြီး ပလပ်စတစ် အစိတ်အပိုင်းများ ထုတ်လုပ်ရန်အတွက် ကုန်ကျစရိတ်သက်သာသော လုပ်ငန်းစဉ်တစ်ခုဖြစ်သည်။ ကနဦး ကိရိယာ တန်ဆာပလာ ကုန်ကျစရိတ် မြင့်မားသော်လည်း ထုတ်လုပ်မှု ပမာဏ တိုးလာသည်နှင့်အမျှ တစ်စိတ်တစ်ပိုင်း ကုန်ကျစရိတ် ကျဆင်းသွားသည်။ ၎င်းသည် အစိတ်အပိုင်းများစွာကို ထုတ်လုပ်ရန်အတွက် စံပြလုပ်ငန်းစဉ်တစ်ခု ဖြစ်စေသည်။
ပလပ်စတစ်ဆေးထိုးခြင်း သည် အားသာချက်များစွာကိုပေးစွမ်းပြီး ပလတ်စတစ်အစိတ်အပိုင်းများထုတ်လုပ်ရန်အတွက် လူကြိုက်များသောရွေးချယ်မှုတစ်ခုဖြစ်လာသည်။ ၎င်း၏မြင့်မားသောထိရောက်မှု၊ တိကျမှု၊ ဘက်စုံသုံးနိုင်မှု၊ ပစ္စည်းပြောင်းလွယ်ပြင်လွယ်၊ စွန့်ပစ်ပစ္စည်းထုတ်လုပ်မှုနည်းပါးမှု၊ လုပ်သားစရိတ်လျှော့ချမှု၊ ညီညွတ်မှုနှင့် အရည်အသွေးသည် ၎င်းကို အမျိုးမျိုးသောအသုံးချပရိုဂရမ်များအတွက် စံပြလုပ်ငန်းစဉ်တစ်ခုဖြစ်စေသည်။ မြင့်မားသောဒီဇိုင်းပြောင်းလွယ်ပြင်လွယ်နှင့် ကုန်ကျစရိတ်သက်သာမှုဖြင့် ရှုပ်ထွေးပြီး အနုစိတ်သော အစိတ်အပိုင်းများကို ထုတ်လုပ်နိုင်မှုသည် ၎င်းကို အလွန်ရှာဖွေထားသော ထုတ်လုပ်မှုလုပ်ငန်းစဉ်ကို ဖြစ်စေသည်။
Plastic Injection Molding ၏ အားနည်းချက်များ
ပလပ်စတစ်ဆေးထိုးခြင်းဆိုသည်မှာ ပလပ်စတစ်အစိတ်အပိုင်းများနှင့် ထုတ်ကုန်အများအပြားကို ထုတ်လုပ်ရန်အတွက် မှိုပေါက်အတွင်း သွန်းသောပလပ်စတစ်ကို မှိုပေါက်ထဲသို့ ထိုးသွင်းခြင်းပါဝင်သည့် ကျယ်ပြန့်စွာအသုံးပြုသော ကုန်ထုတ်လုပ်မှုလုပ်ငန်းစဉ်တစ်ခုဖြစ်သည်။ ပလပ်စတစ်ဆေးထိုးခြင်းတွင် အကျိုးကျေးဇူးများစွာရှိသော်လည်း အားနည်းချက်များစွာရှိသည်။ ပလပ်စတစ်ဆေးထိုးခြင်း၏ အဓိကအားနည်းချက်အချို့မှာ အောက်ပါအတိုင်းဖြစ်သည်။
- မြင့်မားသော ကိရိယာတန်ဆာပလာ ကုန်ကျစရိတ်- ပလပ်စတစ်ဆေးထိုးပုံသွင်းခြင်းအတွက် မှိုကို ဒီဇိုင်းထုတ်ခြင်းနှင့် ထုတ်လုပ်ခြင်းကုန်ကျစရိတ်သည် အလွန်မြင့်မားနိုင်သည်။ အဘယ်ကြောင့်ဆိုသော် မှိုကို အရည်အသွေးမြင့် ပစ္စည်းများနှင့် ပြုလုပ်ထားရန် လိုအပ်ပြီး အလိုရှိသော အစိတ်အပိုင်းကို ဖန်တီးရန် တိကျစွာ စက်ဖြင့် ပြုလုပ်ထားသောကြောင့် ဖြစ်သည်။ ထို့အပြင် မှိုကို ဒီဇိုင်းဆွဲခြင်းနှင့် ထုတ်လုပ်ခြင်း၏ကုန်ကျစရိတ်သည် အသေးစားထုတ်လုပ်ခြင်းလုပ်ငန်းအတွက် တားမြစ်ထားနိုင်ပြီး ပလပ်စတစ်ဆေးထိုးခြင်းမှိုသည် ထုထည်နည်းသောထုတ်လုပ်မှုအတွက် သက်သာစေပါသည်။
- ကြာမြင့်ချိန်- ပလပ်စတစ်ဆေးထိုးခြင်းအတွက် မှိုကို ဒီဇိုင်းထုတ်ခြင်းနှင့် ထုတ်လုပ်ခြင်းလုပ်ငန်းစဉ်သည် အချိန်ကြာမြင့်နိုင်ပြီး ပလတ်စတစ်အစိတ်အပိုင်းများ ထုတ်လုပ်မှုကို နှောင့်နှေးစေနိုင်သည်။ စျေးကွက်ဝယ်လိုအားပြောင်းလဲမှုများကို လျင်မြန်စွာတုံ့ပြန်ရန် သို့မဟုတ် ထုတ်ကုန်အသစ်များကို လျင်မြန်စွာ တီထွင်ဖန်တီးလိုသည့် စီးပွားရေးလုပ်ငန်းများအတွက် ၎င်းသည် အထူးသဖြင့် ပြဿနာရှိနိုင်သည်။
- အကန့်အသတ်ဖြင့် ပြောင်းလွယ်ပြင်လွယ်- မှိုကို ဒီဇိုင်းထုတ်ပြီး ထုတ်လုပ်သည်နှင့် ဒီဇိုင်းကို ပြောင်းလဲရန် သို့မဟုတ် ထုတ်လုပ်မှုလုပ်ငန်းစဉ်ကို ပြုပြင်ရန် ပိုမိုလွယ်ကူပြီး စျေးသက်သာပါသည်။ ၎င်းသည် ပလပ်စတစ်ဆေးထိုးပုံသွင်းခြင်း၏ ပြောင်းလွယ်ပြင်လွယ်ကို ကန့်သတ်နိုင်ပြီး စိတ်ကြိုက် သို့မဟုတ် တစ်မျိုးတည်းသော ထုတ်ကုန်များထုတ်လုပ်ရန်အတွက် ၎င်းကို သင့်လျော်မှုနည်းပါးစေသည်။
- သဘာဝပတ်ဝန်းကျင်ဆိုင်ရာစိုးရိမ်မှုများ- ပလပ်စတစ်ဆေးထိုးခြင်းလုပ်ငန်းသည် အပျက်သဘောဆောင်သောဂေဟစနစ်ဆိုင်ရာသက်ရောက်မှုများရှိလာနိုင်သည့်ပလတ်စတစ်အမြောက်အမြားပေါ်တွင်မှီခိုနေရပါသည်။ ပလတ်စတစ်အမှိုက်သည် အဓိက ပတ်ဝန်းကျင်ဆိုင်ရာ ပြဿနာဖြစ်ပြီး ပလတ်စတစ်ဆေးထိုးခြင်းမှ ဤပြဿနာကို အထောက်အကူဖြစ်စေနိုင်သည်။ ထို့အပြင် ပလတ်စတစ် ထုတ်ကုန်များ ထုတ်လုပ်သည့် လုပ်ငန်းစဉ်သည် သဘာဝပတ်ဝန်းကျင်ကို ပိုမိုထိခိုက်စေနိုင်သည့် စွမ်းအင်နှင့် သဘာဝအရင်းအမြစ်များကို အသုံးပြုရန် လိုအပ်သည်။
- မြင့်မားသော အပိုင်းအစများ- ပလပ်စတစ်ဆေးထိုးခြင်း သည် စွန့်ပစ်ရန် သို့မဟုတ် ပြန်လည်အသုံးပြုရန် စျေးကြီးသည့် သိသိသာသာ အပိုင်းအစများကို ထုတ်လုပ်နိုင်သည်။ ထို့အပြင်၊ အပိုင်းအစများ ထုတ်လုပ်မှုသည် အလုံးစုံထုတ်လုပ်မှုကုန်ကျစရိတ်ကို တိုးစေပြီး ထုတ်လုပ်မှုလုပ်ငန်းစဉ်၏ ထိရောက်မှုကို လျှော့ချနိုင်သည်။
- အကန့်အသတ်ရှိသော ပစ္စည်းရွေးချယ်မှုများ- သတ္တု သို့မဟုတ် ကြွေထည်ပစ္စည်းများကဲ့သို့သော အခြားပစ္စည်းများနှင့် နှိုင်းယှဉ်ပါက အကန့်အသတ်ရှိသော ဂုဏ်သတ္တိရှိသည့် သာမိုပလတ်စတစ်ပစ္စည်းများမှ အစိတ်အပိုင်းများနှင့် ထုတ်ကုန်များထုတ်လုပ်ရန်အတွက် အဓိကအားဖြင့် အသုံးပြုသည်။ ၎င်းသည် မြင့်မားသော ခွန်အား၊ အပူချိန်ခံနိုင်ရည် သို့မဟုတ် အခြားအဆင့်မြင့် ဂုဏ်သတ္တိများ လိုအပ်သော ပလပ်စတစ်ဆေးထိုးခြင်းလုပ်ငန်းအတွက် သင့်လျော်မှုနည်းစေသည်။
Plastic Injection Molding ၏ ကန့်သတ်ချက်များ
ပလပ်စတစ်ဆေးထိုးပုံသွင်းခြင်းသည် အားသာချက်များစွာကို ပေးစွမ်းသော်လည်း အချို့သောကန့်သတ်ချက်များသည် လုပ်ငန်းစဉ်နှင့် ဆက်စပ်နေပါသည်။ ဤသည်မှာ ပလတ်စတစ်ဆေးထိုးခြင်း၏ ကန့်သတ်ချက်အချို့ဖြစ်သည်။
မြင့်မားသော ကနဦးတူးလ်ကုန်ကျစရိတ်- မှိုကို ဒီဇိုင်းဆွဲခြင်းနှင့် ထုတ်လုပ်ခြင်း၏ ကနဦးကုန်ကျစရိတ် တိုးမြင့်နိုင်သည်။ ထပ်ခါတလဲလဲ ဆေးထိုးပုံသွင်းခြင်းလုပ်ငန်းစဉ်ကို ခံနိုင်ရည်ရှိရန် မှိုသည် တိကျပြီး တာရှည်ခံရန် လိုအပ်ပြီး ၎င်းသည် အထူးသဖြင့် ရှုပ်ထွေးသော သို့မဟုတ် ကြီးမားသောမှိုများအတွက် ကြီးမားသောကြိုတင်ရင်းနှီးမြုပ်နှံမှုတစ်ခု လိုအပ်နိုင်သည်။
ခဲချိန်- မှို၏ ရှုပ်ထွေးမှုနှင့် အရွယ်အစားပေါ်မူတည်၍ မှိုထုတ်လုပ်ရန်အတွက် ပို့ဆောင်ချိန်သည် သိသာထင်ရှားပြီး ရက်သတ္တပတ်များမှ လများအထိ သိသာနိုင်ပါသည်။ ၎င်းသည် အထူးသဖြင့် အချိန်အကဲဆတ်သော ပရောဂျက်များအတွက် ထုတ်လုပ်မှုအချိန်ဇယားတွင် နှောင့်နှေးမှုများ ဖြစ်စေနိုင်သည်။
ဒီဇိုင်းကန့်သတ်ချက်များ- ထိုးသွင်းပုံသွင်းခြင်းတွင် ထည့်သွင်းစဉ်းစားရမည့် ဒီဇိုင်းကန့်သတ်ချက်များရှိသည်။ ဥပမာအားဖြင့်၊ အစိတ်အပိုင်းတလျှောက်လုံး တူညီသော နံရံအထူရရှိရန်မှာ သင့်လျော်သော ဖြည့်သွင်းမှုနှင့် အအေးခံမှုကို သေချာစေရန် အရေးကြီးပါသည်။ ထို့အပြင်၊ ပုံစံခွက်မှ အလွယ်တကူ ထုတ်လွှတ်နိုင်စေရန် ဒေါင်လိုက်မျက်နှာပြင်များပေါ်တွင် မူကြမ်းထောင့်များ လိုအပ်ပါသည်။
အပိုင်းအရွယ်အစားကန့်သတ်ချက်များ- ဆေးထိုးပုံသွင်းခြင်းသည် အသေးစားမှအလတ်စားအစိတ်အပိုင်းများထုတ်လုပ်ရန်အတွက် အသင့်တော်ဆုံးဖြစ်သည်။ ကြီးမားသောအစိတ်အပိုင်းများသည် အထူးပြုစက်ပစ္စည်းများနှင့် ပိုကြီးသောမှိုများကို လိုအပ်နိုင်ပြီး ကုန်ကျစရိတ်နှင့် ရှုပ်ထွေးမှုတို့ကို ပေါင်းထည့်နိုင်သည်။
ပစ္စည်းရွေးချယ်ခြင်း- ဆေးထိုးပုံသွင်းခြင်းသည် ကျယ်ပြန့်သောပလပ်စတစ်ပစ္စည်းများအတွက် ခွင့်ပြုပေးသော်လည်း အခြားကုန်ထုတ်လုပ်မှုလုပ်ငန်းစဉ်များနှင့် နှိုင်းယှဉ်ပါက ပစ္စည်းရွေးချယ်မှုမှာ အကန့်အသတ်ရှိနေဆဲဖြစ်သည်။ အရည်ပျော်မှတ်များ သို့မဟုတ် စီးဆင်းမှုအားနည်းသောလက္ခဏာများရှိသော ပစ္စည်းများသည် ဆေးထိုးခြင်းအတွက် မသင့်လျော်ပါ။
မျက်နှာပြင်အချောသတ်ခြင်း- ဆေးထိုးပုံသွင်းခြင်းလုပ်ငန်းစဉ်သည် အစိတ်အပိုင်း၏မျက်နှာပြင်ပေါ်တွင် မြင်သာသောချည်လိုင်းများ သို့မဟုတ် ပိုင်းခြားထားသည့်လိုင်းများ ဖြစ်ပေါ်နိုင်သည်။ အရည်အသွေးမြင့် မျက်နှာပြင်အချောထည်ကို ရရှိရန် စိန်ခေါ်မှုတစ်ခုဖြစ်နိုင်ပြီး ပွတ်တိုက်ခြင်း သို့မဟုတ် အပေါ်ယံပိုင်းကဲ့သို့သော အခြားနည်းလမ်းများ လိုအပ်နိုင်ပါသည်။
Limited Undercuts- အောက်ခံဖြတ်များသည် ပုံစံခွက်မှ အလွယ်တကူ ဖယ်ရှားခံရခြင်းမှ ကာကွယ်ပေးသည့် အစိတ်အပိုင်းတစ်ခုရှိ အင်္ဂါရပ်များ သို့မဟုတ် အသေးစိတ်အချက်များဖြစ်သည်။ Undercuts များသည် ထုတ်လွှတ်သည့် လုပ်ငန်းစဉ်ကို ရှုပ်ထွေးစေပြီး လိုချင်သောအပိုင်း ဂျီသြမေတြီကို ရရှိရန်အတွက် နောက်ထပ်မှိုအင်္ဂါရပ်များ သို့မဟုတ် ဆင့်ပွားလုပ်ဆောင်မှုများ လိုအပ်ပါသည်။
အကန့်အသတ်ရှိသော ပြုပြင်မှုရွေးချယ်စရာများ- မှိုတစ်ခု ပျက်စီးသွားပါက သို့မဟုတ် ပြုပြင်မွမ်းမံရန် လိုအပ်ပါက၊ ၎င်းသည် ရှိပြီးသားမှိုကို ပြုပြင်ရန် သို့မဟုတ် ပြုပြင်ရန် အချိန်ကုန်ခံနိုင်သည်။ တစ်ခါတစ်ရံတွင် လုံးဝအသစ်သော ပုံစံခွက်ကို ထုတ်လုပ်ရန် လိုအပ်ပြီး အပိုကုန်ကျစရိတ်များနှင့် နှောင့်နှေးမှုများ ဖြစ်စေသည်။
ဤကန့်သတ်ချက်များရှိနေသော်လည်း၊ ပလပ်စတစ်ဆေးထိုးပုံသွင်းခြင်းသည် ပလတ်စတစ်အစိတ်အပိုင်းများထုတ်လုပ်ရန်အတွက် အလွန်အသုံးများပြီး ဘက်စုံသုံးကုန်ထုတ်လုပ်မှုလုပ်ငန်းစဉ်တစ်ခုအဖြစ် ဆက်လက်တည်ရှိနေပါသည်။ ဒီဇိုင်းနှင့် ထုတ်လုပ်မှုအစီအစဥ်အဆင့်များအတွင်း ဤကန့်သတ်ချက်များကို သေချာစဉ်းစားခြင်းဖြင့်၊ ၎င်းတို့၏အကျိုးသက်ရောက်မှုကို လျော့ပါးစေပြီး ဆေးထိုးပုံသွင်းခြင်း၏ အကျိုးကျေးဇူးများကို ထိထိရောက်ရောက် အသုံးချနိုင်မည်ဖြစ်သည်။
Plastic Injection Molding ၏အသုံးချမှုများ
ပလပ်စတစ်ဆေးထိုးခြင်းဆိုသည်မှာ ပလပ်စတစ်အစိတ်အပိုင်းများကို ကျယ်ပြန့်စွာထုတ်လုပ်နိုင်သော စွယ်စုံသုံးကုန်ထုတ်လုပ်ငန်းစဉ်တစ်ခုဖြစ်သည်။ ဤသည်မှာ ပလတ်စတစ်ဆေးထိုးခြင်း၏ အသုံးချမှုအချို့ဖြစ်သည်။
- လူသုံးကုန်ပစ္စည်းများ- အရုပ်များ၊ မီးဖိုချောင်သုံးပစ္စည်းများနှင့် အီလက်ထရွန်းနစ်ပစ္စည်းများကဲ့သို့သော အမျိုးမျိုးသောထုတ်ကုန်များထုတ်လုပ်ရန်အတွက် ဆေးထိုးပုံသွင်းခြင်းကို တွင်ကျယ်စွာအသုံးပြုပါသည်။ လုပ်ငန်းစဉ်သည် ရှုပ်ထွေးသော ဂျီသြမေတြီများနှင့် တိကျသောအတိုင်းအတာများဖြင့် အရည်အသွေးမြင့် အစိတ်အပိုင်းများကို ထုတ်လုပ်နိုင်သောကြောင့် တင်းကျပ်သောသည်းခံမှုနှင့် ရှုပ်ထွေးသောပုံစံများလိုအပ်သော ထုတ်ကုန်များအတွက် စံပြဖြစ်စေပါသည်။
- မော်တော်ကားအစိတ်အပိုင်းများ- ဒက်ရှ်ဘုတ် အစိတ်အပိုင်းများ၊ တံခါးလက်ကိုင်များနှင့် မီးချောင်းများကဲ့သို့သော မော်တော်ကားပလတ်စတစ် အစိတ်အပိုင်းများစွာကို ဆေးထိုးပုံသွင်းခြင်းဖြင့် ထုတ်လုပ်ပါသည်။ လုပ်ငန်းစဉ်သည် မြင့်မားသော ထုတ်လုပ်မှုပမာဏနှင့် တသမတ်တည်း အရည်အသွေးကို ရရှိစေပြီး ၎င်းသည် မော်တော်ယာဥ်ထုတ်လုပ်သူများအတွက် ကုန်ကျစရိတ်သက်သာသော ရွေးချယ်မှုတစ်ခု ဖြစ်လာစေသည်။
- ဆေးဘက်ဆိုင်ရာကိရိယာများ- ထိုးဆေးပုံသွင်းခြင်းအား ဆေးထိုးအပ်များ၊ ရှူသွင်းကိရိယာများနှင့် ရောဂါရှာဖွေရေးကိရိယာများကဲ့သို့သော ဆေးဘက်ဆိုင်ရာကိရိယာများထုတ်လုပ်ရန်အတွက် အများအားဖြင့် အသုံးပြုကြသည်။ လုပ်ငန်းစဉ်သည် စက်ပစ္စည်းများ၏ အရည်အသွေးနှင့် ယုံကြည်စိတ်ချရမှုကို အာမခံပြီး မြင့်မားသောတိကျမှုနှင့် လိုက်လျောညီထွေရှိသော အစိတ်အပိုင်းများကို ထုတ်လုပ်နိုင်သည်။
- ထုပ်ပိုးမှု- ဆေးထိုးပုံသွင်းခြင်းကို ကွန်တိန်နာများ၊ အဖုံးများနှင့် ဦးထုပ်များကဲ့သို့သော ပလပ်စတစ်ထုပ်ပိုးမှုပြုလုပ်ရန် တွင်ကျယ်စွာအသုံးပြုသည်။ လုပ်ငန်းစဉ်တွင် တသမတ်တည်းရှိသော အတိုင်းအတာများနှင့် အရည်အသွေးမြင့်သော အစိတ်အပိုင်းများပါရှိနိုင်ပြီး ဆွဲဆောင်မှုရှိသောအသွင်အပြင်နှင့် လုံခြုံအံဝင်ခွင်ကျရှိသော ထုပ်ပိုးမှုအတွက် စံပြဖြစ်စေပါသည်။
- လေကြောင်းနှင့် ကာကွယ်ရေး- ထိုးသွင်းပုံသွင်းခြင်းသည် လေယာဉ်အတွင်းပိုင်း၊ အလင်းရောင်နှင့် ဆက်သွယ်ရေးစနစ်များကဲ့သို့သော အာကာသနှင့် ကာကွယ်ရေး အစိတ်အပိုင်းများကို ထုတ်လုပ်သည်။ လုပ်ငန်းစဉ်တွင် ပေါ့ပါးပြီး တာရှည်ခံပစ္စည်းများဖြင့် အစိတ်အပိုင်းများပါရှိနိုင်ပြီး ၎င်းတို့အား ခွန်အားနှင့် အလေးချိန်အချိုးမြင့်မားသော အသုံးချပရိုဂရမ်များအတွက် သင့်လျော်စေသည်။
- ဆောက်လုပ်ရေး- ဆေးထိုးပုံသွင်းခြင်းသည် ပလပ်စတစ်ကြွေပြားများ၊ အမိုးမိုးခြင်းနှင့် ဘေးဘောင်များကဲ့သို့သော ဆောက်လုပ်ရေးပစ္စည်းများကို ထုတ်လုပ်နိုင်သည်။ လုပ်ငန်းစဉ်သည် တသမတ်တည်းရှိသော အတိုင်းအတာနှင့် အရည်အသွေးမြင့်သော အစိတ်အပိုင်းများပါရှိနိုင်ပြီး ၎င်းသည် ဆောက်လုပ်ရေးကုမ္ပဏီများအတွက် ဆွဲဆောင်မှုရှိသော ရွေးချယ်မှုတစ်ခု ဖြစ်လာစေသည်။
- အားကစားနှင့် အပန်းဖြေခြင်း- ဆေးထိုးပုံသွင်းခြင်းကို ဂေါက်ကလပ်များ၊ တင်းနစ်ရက်ကက်များနှင့် စက်ဘီးအစိတ်အပိုင်းများကဲ့သို့သော အားကစားပစ္စည်းများ ထုတ်လုပ်ရာတွင် တွင်ကျယ်စွာ အသုံးပြုပါသည်။ လုပ်ငန်းစဉ်သည် ပေါ့ပါးသောပစ္စည်းများနှင့် တိကျသောဂျီသြမေတြီများဖြင့် အစိတ်အပိုင်းများကို ထုတ်လုပ်နိုင်ပြီး ပစ္စည်းများ၏ စွမ်းဆောင်ရည်နှင့် တာရှည်ခံမှုကို အာမခံပါသည်။
ယေဘုယျအားဖြင့်၊ ပလပ်စတစ်ဆေးထိုးပုံသွင်းခြင်းသည် အမျိုးမျိုးသော အသုံးချမှုများအတွက် အရည်အသွေးမြင့် ပလတ်စတစ်အစိတ်အပိုင်းများကို ထုတ်လုပ်ပေးနိုင်သည့် စွယ်စုံရနှင့် တွင်ကျယ်စွာ အသုံးပြုသည့် ကုန်ထုတ်လုပ်မှုလုပ်ငန်းစဉ်တစ်ခုဖြစ်သည်။ လုပ်ငန်းစဉ်သည် တိကျသောဒီဇိုင်းနှင့် ထုတ်လုပ်မှုလိုအပ်ချက်များနှင့်ကိုက်ညီစေရန် အံဝင်ခွင်ကျဖြစ်စေနိုင်ပြီး၊ ၎င်းသည် စက်မှုလုပ်ငန်းမျိုးစုံရှိ ထုတ်လုပ်သူများအတွက် ဆွဲဆောင်မှုတစ်ခုဖြစ်စေပါသည်။
မော်တော်ယာဥ်လုပ်ငန်းနှင့် ပလတ်စတစ်ဆေးထိုးခြင်းလုပ်ငန်း
မော်တော်ကားလုပ်ငန်းသည် ပလတ်စတစ်ဆေးထိုးခြင်းနည်းပညာကို အရေးပါသောအသုံးပြုသူဖြစ်သည်။ ပလပ်စတစ်ဆေးထိုးပုံသွင်းခြင်းလုပ်ငန်းစဉ်သည် မော်တော်ကားအစိတ်အပိုင်းများနှင့် အစိတ်အပိုင်းများထုတ်လုပ်မှုကို တော်လှန်ပြောင်းလဲခဲ့ပြီး ရှုပ်ထွေးသောပုံသဏ္ဍာန်များကို တိကျမှန်ကန်မှုဖြင့် မြင့်မားစွာထုတ်လုပ်နိုင်ခဲ့သည်။ မော်တော်ကားလုပ်ငန်းတွင် ပလပ်စတစ်ဆေးထိုးခြင်းအား အသုံးပြုသည့် နည်းလမ်းအချို့မှာ အောက်ပါအတိုင်းဖြစ်သည်။
- အတွင်းပိုင်းအစိတ်အပိုင်းများ- ပလပ်စတစ်ဆေးထိုးပုံသွင်းခြင်းသည် ဒက်ရှ်ဘုတ်အစိတ်အပိုင်းများ၊ တံခါးပြားများ၊ အပိုင်းအစများနှင့် အခြားအရာများအပါအဝင် အတွင်းပိုင်းအချက်များစွာကို ထုတ်လုပ်ပေးပါသည်။ ဤအစိတ်အပိုင်းများကို အနုစိတ်ပုံသဏ္ဍာန်များနှင့် အသွင်အပြင်များဖြင့် ဒီဇိုင်းထုတ်နိုင်ပြီး ယာဉ်မော်ဒယ်လ်တစ်ခုစီ၏ ပုံစံနှင့် လုပ်ဆောင်နိုင်စွမ်းလိုအပ်ချက်များနှင့် ကိုက်ညီစေရန် စိတ်ကြိုက်ပြင်ဆင်နိုင်သည်။
- အပြင်ပိုင်း အစိတ်အပိုင်းများ- ဘမ်ပါများ၊ မီးကင်များ၊ ဘေးကြည့်မှန်များနှင့် အခြားအရာများအပါအဝင် ပြင်ပအင်္ဂါရပ်များကို ထုတ်လုပ်ရန်အတွက် ပလပ်စတစ်ဆေးထိုးခြင်းကိုလည်း အသုံးပြုပါသည်။ ဤအစိတ်အပိုင်းများသည် ပြင်းထန်သော ရာသီဥတုအခြေအနေများကို ခံနိုင်ရည်ရှိစေရန် ဒီဇိုင်းထုတ်နိုင်ပြီး အရောင်မျိုးစုံနှင့် အချောသတ်ပြုလုပ်ထားသည်။
- ကားခေါင်းအောက်ပိုင်း အစိတ်အပိုင်းများ- ပလပ်စတစ်ဆေးထိုးခြင်းမှ အင်ဂျင်အဖုံးများ၊ လေဝင်စနစ်များနှင့် အအေးပေးစနစ် အစိတ်အပိုင်းများအပါအဝင် ကားခေါင်းအောက်ပိုင်း အင်္ဂါရပ်များစွာကို ထုတ်လုပ်ပေးပါသည်။ ဤအစိတ်အပိုင်းများသည် အပူချိန်မြင့်မားပြီး ဓာတုဗေဒခံနိုင်ရည်ရှိရန် လိုအပ်ပြီး သာမိုပလပ်စတစ်ပစ္စည်းများဖြင့် ရရှိနိုင်သည်။
- လျှပ်စစ်နှင့် အီလက်ထရွန်နစ် အစိတ်အပိုင်းများ- ပလပ်စတစ်ဆေးထိုးခြင်းမှ ချိတ်ဆက်ကိရိယာများ၊ အိမ်များနှင့် အာရုံခံကိရိယာများအပါအဝင် လျှပ်စစ်နှင့် အီလက်ထရွန်နစ် အစိတ်အပိုင်းများကို ထုတ်လုပ်သည်။ ပလပ်စတစ်ဆေးထိုးပုံသွင်းခြင်း၏ တိကျမှုနှင့် လိုက်လျောညီထွေရှိမှုတို့ဖြင့် ရရှိနိုင်သည့် မြင့်မားသောတိကျမှုနှင့် ယုံကြည်စိတ်ချရမှုတို့ လိုအပ်ပါသည်။
- ပေါ့ပါးခြင်း- ပလပ်စတစ်ဆေးထိုးပုံသွင်းခြင်းကို မကြာခဏဆိုသလို ယာဉ်တစ်စီးလုံး၏အလေးချိန်ကို လျှော့ချရန်၊ ဆီစားသက်သာပြီး ဓာတ်ငွေ့ထုတ်လွှတ်မှုကို လျှော့ချရန် ပေါ့ပါးသောအစိတ်အပိုင်းများကို ထုတ်လုပ်ရန် အသုံးပြုသည်။ ပေါ့ပါးမှုသည် ကားတစ်စီး၏ ကိုင်တွယ်မှုနှင့် စွမ်းဆောင်ရည်ကို မြှင့်တင်ပေးနိုင်သည်။
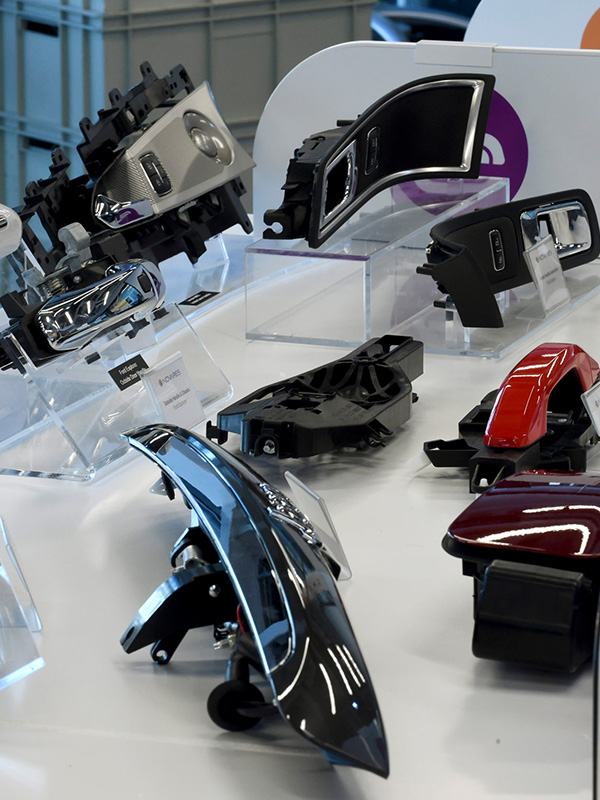
ဆေးဘက်ဆိုင်ရာလုပ်ငန်းနှင့် ပလပ်စတစ်ဆေးထိုးခြင်းလုပ်ငန်း
ပလပ်စတစ်ဆေးထိုးခြင်းလုပ်ငန်းတွင် ဆေးဘက်ဆိုင်ရာစက်ပစ္စည်းများနှင့် အစိတ်အပိုင်းအမျိုးမျိုးကို ထုတ်လုပ်ရန်အတွက် ဆေးဘက်ဆိုင်ရာလုပ်ငန်းတွင် တွင်ကျယ်စွာအသုံးပြုသည်။ ပလပ်စတစ်ဆေးထိုးပုံသွင်းခြင်းလုပ်ငန်းစဉ်သည် မြင့်မားသောတိကျမှုနှင့် တိကျမှုဖြင့် ရှုပ်ထွေးသောပုံသဏ္ဍာန်များကို ထုတ်လုပ်နိုင်စေပြီး ဆေးဘက်ဆိုင်ရာအသုံးချမှုများစွာအတွက် စံပြကုန်ထုတ်နည်းလမ်းတစ်ခုဖြစ်လာသည်။ ဤသည်မှာ ဆေးဘက်ဆိုင်ရာလုပ်ငန်းတွင် ပလပ်စတစ်ဆေးထိုးခြင်းအား အသုံးပြုသည့် နည်းလမ်းအချို့ဖြစ်သည်။
- ဆေးဘက်ဆိုင်ရာကိရိယာများ- ပလပ်စတစ်ဆေးထိုးခြင်းလုပ်ငန်းသည် ခွဲစိတ်ကိရိယာများ၊ ရောဂါရှာဖွေရေးကိရိယာများ၊ ဆေးဝါးပို့ဆောင်မှုစနစ်များ စသည်တို့အပါအဝင် ဆေးဘက်ဆိုင်ရာကိရိယာများကို ထုတ်လုပ်ပေးပါသည်။ ဤကိရိယာများသည် တိကျပြီး တိကျမှုများစွာလိုအပ်ပြီး ပလပ်စတစ်ဆေးထိုးခြင်းသည် အဆိုပါလိုအပ်ချက်များကို ပြည့်မီနိုင်ပါသည်။
- အစားထိုးထည့်သွင်းခြင်း- ပလပ်စတစ်ဆေးထိုးပုံသွင်းခြင်းကို အဆစ်အစားထိုးခြင်း၊ သွားနှင့်ခံတွင်းအစားထိုးခြင်း နှင့် အခြားအရာများအပါအဝင် အမျိုးမျိုးသော အစားထိုးခြင်းများကို ထုတ်လုပ်ရန်အတွက်လည်း အသုံးပြုပါသည်။ ဤ implant များကို လူနာ၏ ခန္ဓာဗေဒနှင့် ကိုက်ညီစေရန် ဒီဇိုင်းထုတ်နိုင်ပြီး ဇီဝသဟဇာတဖြစ်သော ပစ္စည်းများဖြင့် ထုတ်လုပ်နိုင်သည်။
- ဓာတ်ခွဲခန်းသုံးပစ္စည်းများ- ပလပ်စတစ်ဆေးထိုးခြင်းမှ ပိုက်ပြားများ၊ မိုက်ခရိုပြားများနှင့် စမ်းသပ်ပြွန်များကို ထုတ်လုပ်သည်။ ယုံကြည်စိတ်ချရသောရလဒ်များကိုသေချာစေရန် ဤအစိတ်အပိုင်းများသည် မြင့်မားသောတိကျမှုနှင့် တိကျမှုလိုအပ်ပါသည်။
- ထုပ်ပိုးခြင်း- ပိုးမွှားအတားအဆီးစနစ်များနှင့် ထုတ်ကုန်တစ်ခုချင်းစီအတွက် စိတ်ကြိုက်ထုပ်ပိုးခြင်းအပါအဝင် ဆေးဘက်ဆိုင်ရာပစ္စည်းများအတွက် ထုပ်ပိုးမှုပြုလုပ်ရန် ပလပ်စတစ်ဆေးထိုးခြင်းအား အသုံးပြုသည်။ ဤထုပ်ပိုးမှုဖြေရှင်းနည်းများသည် ဆေးဘက်ဆိုင်ရာကိရိယာ၏ မြုံမှုနှင့် ခိုင်မာမှုကို ထိန်းသိမ်းရန် ကူညီပေးနိုင်သည်။
- တစ်ခါသုံးကိရိယာများ- ပလပ်စတစ်ဆေးထိုးခြင်းလုပ်ငန်းသည် ဆေးထိုးအပ်များ၊ ဆေးထိုးအပ်များနှင့် catheters ကဲ့သို့သော တစ်ခါသုံးကိရိယာများကို ထုတ်လုပ်ပေးလေ့ရှိသည်။ ဤစက်ပစ္စည်းများကို စျေးနှုန်းချိုသာစွာဖြင့် အသံအတိုးအကျယ်ဖြင့် ပြုလုပ်နိုင်ပြီး ကျန်းမာရေးစောင့်ရှောက်မှုဆက်တင်များတွင် ရောဂါပိုးများ ပျံ့နှံ့မှုကို တားဆီးရန် ကူညီပေးနိုင်ပါသည်။
လူသုံးကုန်ပစ္စည်းများနှင့် ပလပ်စတစ်ထိုးဆေးပုံသွင်းခြင်း။
ပလပ်စတစ်ဆေးထိုးပုံသွင်းခြင်းကို ၎င်း၏ ဘက်စုံအသုံးပြုနိုင်မှု၊ ထိရောက်မှုနှင့် ကုန်ကျစရိတ်သက်သာမှုတို့ကြောင့် လူသုံးကုန်ပစ္စည်းများ ထုတ်လုပ်မှုတွင် တွင်ကျယ်စွာအသုံးပြုသည်။ ပလပ်စတစ်ဆေးထိုးပုံသွင်းခြင်းလုပ်ငန်းစဉ်သည် မြင့်မားသောတိကျမှုနှင့် တိကျမှုတို့ဖြင့် ရှုပ်ထွေးသောပုံစံများကို ထုတ်လုပ်နိုင်စေကာ သုံးစွဲသူများစွာအတွက် စံပြကုန်ထုတ်နည်းလမ်းတစ်ခုဖြစ်စေသည်။ ဤသည်မှာ လူသုံးကုန်ပစ္စည်းများထုတ်လုပ်ရာတွင် ပလတ်စတစ်ဆေးထိုးခြင်းအား အသုံးပြုသည့်နည်းလမ်းအချို့ဖြစ်သည်။
- အရုပ်များ- ပလပ်စတစ်ဆေးထိုးခြင်း သည် အရုပ်ငယ်များမှ အကြီးစား ကစားစရာများအထိ အရုပ်မျိုးစုံကို ထုတ်လုပ်ပေးပါသည်။ လုပ်ငန်းစဉ်သည် အနုစိတ်သော ဒီဇိုင်းများနှင့် အသေးစိတ်အချက်များ ဖန်တီးခြင်းနှင့် အရောင်မျိုးစုံနှင့် ပစ္စည်းများဖြင့် အရုပ်များ ပြုလုပ်ခြင်းတို့ ပြုလုပ်နိုင်သည်။
- အိမ်သုံးပစ္စည်းများ- ပလပ်စတစ်ဆေးထိုးခြင်းလုပ်ငန်းသည် မီးဖိုချောင်သုံးပစ္စည်းများ၊ သိုလှောင်ရုံများနှင့် သန့်ရှင်းရေးသုံးပစ္စည်းများအပါအဝင် အိမ်သုံးပစ္စည်းများကို ထုတ်လုပ်သည်။ ဤထုတ်ကုန်များသည် တာရှည်ခံ၊ ပေါ့ပါးပြီး အသုံးပြုရလွယ်ကူစေရန် ဒီဇိုင်းထုတ်နိုင်သည်။
- အီလက်ထရွန်နစ်ပစ္စည်းများ- ပလပ်စတစ်ဆေးထိုးခြင်းမှ ကွန်ပျူတာ အိုးအိမ်များ၊ ဖုန်းအိတ်များနှင့် အားသွင်းကိရိယာများ အပါအဝင် အီလက်ထရွန်နစ် အစိတ်အပိုင်းများစွာကို ထုတ်လုပ်ပေးပါသည်။ လုပ်ငန်းစဉ်၏ တိကျမှုနှင့် တိကျမှုသည် ဤအစိတ်အပိုင်းများကို လိုက်လျောညီထွေရှိပြီး ယုံကြည်စိတ်ချရမှုမြင့်မားသော အတိုင်းအတာဖြင့် ပြုလုပ်ထားကြောင်း သေချာစေသည်။
- တစ်ကိုယ်ရေ စောင့်ရှောက်မှု ထုတ်ကုန်များ- ပလပ်စတစ် ဆေးထိုးခြင်း သည် သွားတိုက်တံများ၊ သင်တုန်း နှင့် ဆံပင်ပွတ်တံများ အပါအဝင် ထူးခြားသော စောင့်ရှောက်မှု ထုတ်ကုန်များကို ထုတ်လုပ်ပါသည်။ ဤထုတ်ကုန်များသည် အသုံးပြုရလွယ်ကူပြီး ဘေးကင်းစေရန်အတွက် မြင့်မားသောတိကျမှုနှင့် တိကျမှုလိုအပ်ပါသည်။
- မော်တော်ယာဥ်ဆက်စပ်ပစ္စည်းများ- ပလပ်စတစ်ဆေးထိုးခြင်းမှ ဒက်ရှ်ဘုတ်အစိတ်အပိုင်းများ၊ ခွက်ကိုင်ဆောင်သူများနှင့် အခြားအရာများအပါအဝင် မော်တော်ယာဥ်ဆက်စပ်ပစ္စည်းများကို ထုတ်လုပ်ပေးပါသည်။ ဤအစိတ်အပိုင်းများကို ပေါ့ပါးစွာ၊ တာရှည်ခံရန်နှင့် နေ့စဉ်အသုံးပြုမှု၏ စုတ်ပြဲပျက်စီးမှုကို ခံနိုင်ရည်ရှိစေရန် ဒီဇိုင်းထုတ်နိုင်သည်။
ပလပ်စတစ်ထိုးသွင်းပုံသွင်းခြင်းတွင် သဘာဝပတ်ဝန်းကျင်ဆိုင်ရာ ထည့်သွင်းစဉ်းစားမှုများ
ပလပ်စတစ်ဆေးထိုးပုံသွင်းခြင်းသည် တွင်ကျယ်စွာအသုံးပြုသည့် ထုတ်လုပ်မှုလုပ်ငန်းစဉ်တစ်ခုဖြစ်သော်လည်း သဘာဝပတ်ဝန်းကျင်အပေါ် သက်ရောက်မှုများစွာရှိသည်။ ဤသည်မှာ ပလတ်စတစ်ဆေးထိုးခြင်းတွင် ဂေဟဗေဒဆိုင်ရာ ထည့်သွင်းစဉ်းစားမှုအချို့ဖြစ်သည်။
- ပစ္စည်းရွေးချယ်ခြင်း- ဆေးထိုးပုံသွင်းရာတွင် အသုံးပြုသည့် ပလတ်စတစ်ပစ္စည်းရွေးချယ်မှုသည် သဘာဝပတ်ဝန်းကျင်ကို သိသိသာသာ ထိခိုက်စေနိုင်သည်။ အချို့သောပစ္စည်းများသည် ဇီဝပြိုကွဲပျက်စီးနိုင်သော သို့မဟုတ် ပြန်လည်အသုံးပြု၍ရသော်လည်း အချို့သောပစ္စည်းများမှာ မရှိပေ။ ဇီဝပြိုကွဲပျက်စီးနိုင်သော သို့မဟုတ် ပြန်လည်အသုံးပြုနိုင်သောပစ္စည်းများကို အသုံးပြုခြင်းသည် ပလပ်စတစ်ဆေးထိုးခြင်း၏ သဘာဝပတ်ဝန်းကျင်ဆိုင်ရာ ထိခိုက်မှုကို လျှော့ချနိုင်သည်။
- စွမ်းအင်သုံးစွဲမှု- ပလပ်စတစ်ဆေးထိုးပုံသွင်းခြင်းသည် ပလပ်စတစ်ကို အရည်ပျော်ပြီး မှိုထဲသို့ ထိုးသွင်းရန်အတွက် သိသာထင်ရှားသောစွမ်းအင်လိုအပ်သည်။ လျှပ်စစ်စက်များနှင့် စက်ဝိုင်းပိတ်စနစ်များကဲ့သို့ စွမ်းအင်သက်သာသည့် စက်ပစ္စည်းနှင့် လုပ်ငန်းစဉ်များသည် စွမ်းအင်သုံးစွဲမှုနှင့် သဘာဝပတ်ဝန်းကျင်ဆိုင်ရာ ထိခိုက်မှုကို လျှော့ချနိုင်သည်။
- အမှိုက်စီမံခန့်ခွဲမှု- ပလပ်စတစ်ဆေးထိုးပုံသွင်းခြင်းသည် ပိုလျှံနေသောပစ္စည်း၊ ချို့ယွင်းနေသော အစိတ်အပိုင်းများနှင့် ထုပ်ပိုးမှုတို့မှ စွန့်ပစ်ပစ္စည်းများကို ထုတ်ပေးသည်။ ပြန်လည်အသုံးပြုခြင်းနှင့် စွန့်ပစ်ပစ္စည်းများကို ပြန်လည်အသုံးပြုခြင်းကဲ့သို့သော သင့်လျော်သော စွန့်ပစ်ပစ္စည်းစီမံခန့်ခွဲမှုအလေ့အကျင့်များသည် ပလပ်စတစ်ဆေးထိုးခြင်း၏ သဘာဝပတ်ဝန်းကျင်ဆိုင်ရာ ထိခိုက်မှုကို လျှော့ချရန် ကူညီပေးနိုင်ပါသည်။
- ဓာတုအသုံးပြုမှု- မှိုထုတ်လွှတ်သော အေးဂျင့်များနှင့် သန့်စင်သောအရည်များကဲ့သို့သော ပလပ်စတစ်ဆေးထိုးမှိုများတွင် ဓာတုပစ္စည်းအချို့သည် ပတ်ဝန်းကျင်ကို ထိခိုက်စေနိုင်သည်။ ပတ်ဝန်းကျင်နှင့် သဟဇာတဖြစ်နိုင်သော အခြားရွေးချယ်စရာများကို အသုံးပြုခြင်း သို့မဟုတ် ဤဓာတုပစ္စည်းများအသုံးပြုမှုကို လျှော့ချခြင်းဖြင့် ပတ်ဝန်းကျင်ထိခိုက်မှုကို လျှော့ချရန် ကူညီပေးနိုင်ပါသည်။
- သက်တမ်းကုန်ဆုံးရန် ထည့်သွင်းစဉ်းစားခြင်း- ဆေးထိုးပုံသွင်းခြင်းမှတစ်ဆင့် ထုတ်လုပ်သော ပလတ်စတစ်ပစ္စည်းများသည် ပြိုကွဲပျက်စီးရန် နှစ်ရာနှင့်ချီ၍ ကြာနိုင်သောကြောင့် အမှိုက်ပုံများတွင် မကြာခဏ ဆုံးခန်းသွားလေ့ရှိသည်။ ပြန်လည်သုံးစွဲနိုင်မှု သို့မဟုတ် ဇီဝရုပ်ကြွင်းအတွက် ထုတ်ကုန်များကို ဒီဇိုင်းထုတ်ခြင်းသည် ပလတ်စတစ်ဆေးထိုးခြင်း၏ သဘာဝပတ်ဝန်းကျင်ဆိုင်ရာ ထိခိုက်မှုကို လျှော့ချနိုင်သည်။
ပလပ်စတစ်ဆေးထိုးခြင်း၏အနာဂတ်
နည်းပညာနှင့် ပစ္စည်းများ တိုးတက်လာမှုကြောင့် ပလပ်စတစ်ဆေးထိုးပုံသွင်းခြင်း၏ အနာဂတ်သည် အလားအလာကောင်းပြီး လုပ်ငန်းစဉ်ကို ပိုမိုထိရောက်၊ ကုန်ကျစရိတ်သက်သာကာ ရေရှည်တည်တံ့စေရန် မျှော်လင့်ထားသည်။ ဤသည်မှာ ပလတ်စတစ်ဆေးထိုးပုံသွင်းခြင်း၏ အနာဂတ်ကို ပုံဖော်မည့် ခေတ်ရေစီးကြောင်းနှင့် တိုးတက်မှုအချို့ဖြစ်သည်။
- ထပ်လောင်းထုတ်လုပ်ခြင်း- 3D ပုံနှိပ်ခြင်းဟုလည်း လူသိများသော ပေါင်းစည်းထုတ်လုပ်ခြင်းသည် ပလပ်စတစ်ဆေးထိုးပုံသွင်းခြင်းကို ပြောင်းလဲနိုင်သည့် ပေါ်ထွန်းလာသော နည်းပညာတစ်ခုဖြစ်သည်။ မှိုဖန်တီးရန်အတွက် 3D ပုံနှိပ်စက်ကို အသုံးပြုခြင်းဖြင့် ထုတ်လုပ်သူများသည် ရိုးရာမှိုပြုလုပ်ခြင်းနည်းပညာများနှင့် ဆက်စပ်နေသော အချိန်နှင့် ကုန်ကျစရိတ်ကို သိသိသာသာ လျှော့ချနိုင်သည်။
- စမတ်ကျသောထုတ်လုပ်မှု- အလိုအလျောက်စနစ်၊ ဒေတာခွဲခြမ်းစိတ်ဖြာမှုနှင့် စက်သင်ယူမှုတို့ပါ၀င်သည့် စမတ်ထုတ်လုပ်မှုသည် ပလပ်စတစ်ဆေးထိုးပုံသွင်းခြင်းကို တော်လှန်ရန် မျှော်လင့်ပါသည်။ လုပ်ငန်းစဉ်များကို ပိုမိုကောင်းမွန်အောင်လုပ်ဆောင်ရန် အာရုံခံကိရိယာများနှင့် ဒေတာခွဲခြမ်းစိတ်ဖြာချက်များကို အသုံးပြုခြင်းဖြင့် ထုတ်လုပ်သူများသည် စွမ်းဆောင်ရည်ကို မြှင့်တင်နိုင်ပြီး စွန့်ပစ်ပစ္စည်းများကို လျှော့ချကာ ထုတ်လုပ်မှုစွမ်းအားကို တိုးမြှင့်နိုင်သည်။
- ရေရှည်တည်တံ့နိုင်သောပစ္စည်းများ- ဇီဝပလတ်စတစ်နှင့် ပြန်လည်အသုံးပြုထားသော ပလတ်စတစ်များကဲ့သို့သော စဉ်ဆက်မပြတ်သောပစ္စည်းများသည် ပလတ်စတစ်ဆေးထိုးခြင်းလုပ်ငန်းတွင် လူကြိုက်များလာပါသည်။ ဤပစ္စည်းများသည် သဘာဝပတ်ဝန်းကျင်ဆိုင်ရာ အကျိုးကျေးဇူးများကို ပေးစွမ်းနိုင်ပြီး ထုတ်လုပ်သူများအား ရေရှည်တည်တံ့ခိုင်မြဲမှုပန်းတိုင်များ ပြည့်မီစေရန် ကူညီပေးနိုင်ပါသည်။
- မိုက်ခရိုပုံသွင်းခြင်း- သေးငယ်သော အစိတ်အပိုင်းများကို တိကျမှန်ကန်စွာ ထုတ်လုပ်ခြင်းပါဝင်သည့် မိုက်ခရိုပုံသွင်းခြင်းသည် ကျန်းမာရေးစောင့်ရှောက်မှုနှင့် အီလက်ထရွန်နစ်ပစ္စည်းကဲ့သို့သော လုပ်ငန်းများတွင် ပို၍အရေးပါလာသည်။ နည်းပညာနှင့် ပစ္စည်းများ တိုးတက်လာခြင်းသည် မိုက်ခရိုပုံသွင်းခြင်းကို ပိုမိုရရှိနိုင်ပြီး ကုန်ကျစရိတ်သက်သာစေရန် မျှော်လင့်ပါသည်။
- စိတ်ကြိုက်ပြင်ဆင်ခြင်း- စားသုံးသူများသည် စိတ်ကြိုက်ထုတ်ကုန်များကို ပိုမိုတောင်းဆိုလာသည်နှင့်အမျှ ပလပ်စတစ်ဆေးထိုးမှုပုံစံသည် ပိုမိုပြောင်းလွယ်ပြင်လွယ်နှင့် စိတ်ကြိုက်ပြင်ဆင်နိုင်မည်ဟု မျှော်လင့်ပါသည်။ အချိန်နှင့်တပြေးညီ တုံ့ပြန်ချက်နှင့် စက်သင်ယူခြင်းကဲ့သို့သော နည်းပညာတိုးတက်မှုများသည် ထုတ်လုပ်သူများအား စိတ်ကြိုက်ထုတ်ကုန်များကို လျင်မြန်ထိရောက်စွာ ထုတ်လုပ်နိုင်စေမည်ဖြစ်သည်။
နိဂုံး:
ပလပ်စတစ်ဆေးထိုးပုံသွင်းခြင်းသည် ကျယ်ပြန့်သောထုတ်ကုန်များထုတ်လုပ်မှုကို တော်လှန်ပြောင်းလဲပေးသည့် စွယ်စုံရနှင့် ထိရောက်သောကုန်ထုတ်လုပ်မှုလုပ်ငန်းစဉ်တစ်ခုဖြစ်သည်။ ဆေးဘက်ဆိုင်ရာစက်ပစ္စည်းများမှသည် မော်တော်ယာဥ်အစိတ်အပိုင်းများအထိ၊ ပလပ်စတစ်ဆေးထိုးခြင်းမှ ထုတ်လုပ်မှုနှုန်းမြင့်မားခြင်း၊ ဒီဇိုင်းပြောင်းလွယ်ပြင်လွယ်နှင့် ကုန်ကျစရိတ်သက်သာခြင်းအပါအဝင် အခြားသောကုန်ထုတ်လုပ်မှုလုပ်ငန်းစဉ်များထက် အားသာချက်များစွာကို ပေးဆောင်ပါသည်။ နည်းပညာနှင့် ပစ္စည်းများတွင် စဉ်ဆက်မပြတ် တိုးတက်မှုနှင့်အတူ ပလပ်စတစ်ဆေးထိုးပုံသွင်းခြင်း၏ အနာဂတ်သည် တောက်ပလာကာ ဤလုပ်ငန်းစဉ်သည် လာမည့်နှစ်များတွင် ကုန်ထုတ်လုပ်မှုလုပ်ငန်းတွင် ပို၍ပင် အရေးပါသော အခန်းကဏ္ဍမှ ပါဝင်လာဖွယ်ရှိသည်။