မော်တော်ကား ပလပ်စတစ် အစိတ်အပိုင်းများ ထိုးသွင်း ပုံသွင်းခြင်း။
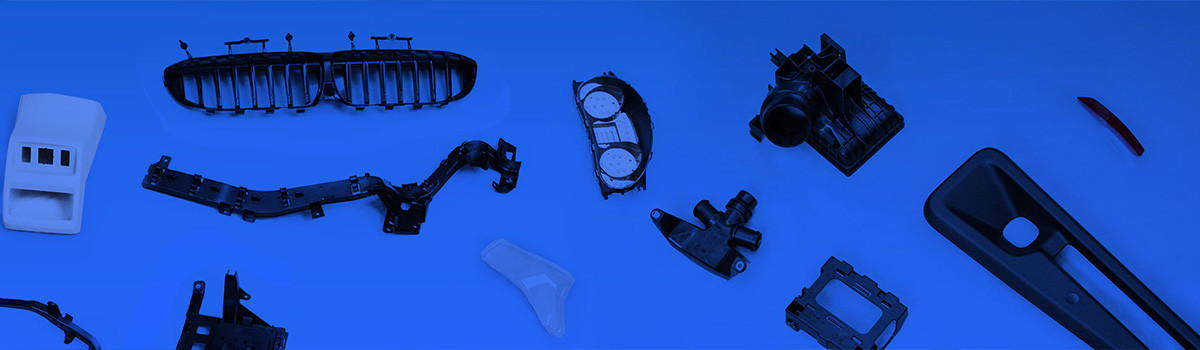
ယနေ့ခေတ် မော်တော်ကား ပလတ်စတစ် အစိတ်အပိုင်းများ
မြင့်မားသော မော်တော်ကား စွမ်းဆောင်ရည်သည် ၎င်းအားလုံးကို ကိုင်တွယ်နိုင်သော အစိတ်အပိုင်းများ လိုအပ်သည်။ ပလတ်စတစ်များသည် အင်ဂျင်မှ ကိုယ်ထည်အထိ လုပ်ဆောင်သည်။ အတွင်းပိုင်းမှ အပြင်ပိုင်းအထိ။ ယနေ့ခေတ်မော်တော်ယာဥ်ပလတ်စတစ်များသည် အပေါ့စားယာဉ်အသစ်၏ ထုထည်၏ ၅၀ ရာခိုင်နှုန်းခန့်ရှိသော်လည်း ၎င်း၏အလေးချိန်၏ ၁၀ ရာခိုင်နှုန်းအောက်သာရှိသည်။
လုံခွုံမှု
ယနေ့ခေတ် ပစ္စည်းများ၏ ဘေးကင်းရေး တိုးတက်မှုများသည် မရေမတွက်နိုင်သော အသက်များကို ကယ်တင်ပါသည်။ လေအိတ်များ၊ လေကာမှန်များ၊ နေကာမိုးများအပြင် စွမ်းအင်စုပ်ယူသည့် တီထွင်ဆန်းသစ်မှုများကြောင့် ယာဉ်သေဆုံးမှုများကို လျှော့ချပေးသည်။ ပလတ်စတစ် ရှေ့ဆုံး မော်ဂျူးများ၊ မော်ဂျူလာထိုင်ခုံများနှင့် စွမ်းအင်စုပ်ယူနိုင်သော ဘမ်ဘာများသည် နှစ်စဉ်နှစ်တိုင်း အသက်များကို ကယ်တင်ရန် ကူညီပေးပါသည်။
ပလပ်စတစ် ပေါင်းစပ်ဖွဲ့စည်းပုံများသည် ဘေးကင်းလုံခြုံရေးအင်္ဂါရပ်များကို ထိန်းသိမ်းထားစဉ် ပေါ့ပါးသောယာဉ်များကို ကူညီပေးနိုင်ပါသည်။ ယာဉ်တိုက်မှုဖြစ်သောအခါ အင်ဂျင်နီယာများသည် တည်ဆောက်ပုံအား ကြိုတင်ခန့်မှန်းနိုင်သောနည်းလမ်းဖြင့် ဖြိုခွင်းစေလိုပါသည်။ မော်တော်ယာဥ်ပစ္စည်းများသည် လူသားများထံ “သက်ရောက်မှုစွမ်းအင်” ကို စုပ်ယူ၊ မလွှဲပြောင်းသင့်ပါ။ စက်မှုလုပ်ငန်းက ၎င်းကို "ထိန်းချုပ်ထားသော နှိပ်စက်ခြင်း" ဟုခေါ်သည်။
ဖိုက်ဘာအားဖြည့် ပေါ်လီမာ ကွန်ပေါင်းများသည် သံမဏိ၏ နှိပ်စက်ခြင်း စွမ်းအင်ထက် လေးဆ စုပ်ယူသည်။ B-pillar သည် ယာဉ်၏အမိုးကို ၎င်း၏ကိုယ်ထည်နှင့် ချိတ်ဆက်ပေးသည့် ထောက်တိုင်ဖြစ်သည်။ ၎င်းသည် ရှေ့တံခါး၏ နောက်ဘက်တွင်ရှိပြီး ယာဉ်တိုက်မှုတစ်ခုအတွင်း ကျူးကျော်ဝင်ရောက်မှုကို ခံနိုင်ရည်ရှိသော အဓိကအရင်းအမြစ်ကို ထောက်ပံ့ပေးသည်။
National Highway Traffic Safety Administration သည် မကြာသေးမီက B-တိုင်များဆိုင်ရာ လေ့လာမှုတစ်ခုကို ရန်ပုံငွေထောက်ပံ့ခဲ့သည်။ လေ့လာမှုသည် ပေါင်းစပ်ပါဝင်မှုအားကောင်းသည့် ကာဗွန်ဖိုက်ဘာ သာမိုပလတ်စတစ် B-တိုင် ဒီဇိုင်းကို အထူးလေ့လာခဲ့သည်။ ရည်ရွယ်ချက်မှာ ဒီဇိုင်း၏အလေးချိန်ကို သက်သာစေပြီး ယာဉ်တိုက်မှုဘေးကင်းရေးအား သတ္တုအခြေခံလိုင်းနှင့် နှိုင်းယှဉ်ဆုံးဖြတ်ရန်ဖြစ်သည်။ B-pillar သည် အလေးချိန် 60 ရာခိုင်နှုန်း သက်သာစေပြီး ဘေးထွက်ထိခိုက်မှု လိုအပ်ချက်များကို ကျေနပ်ကြောင်း ပြသထားသည်။ တွက်ချက်မှုဆိုင်ရာ ကိရိယာများသည် တက်ကြွသော အကျိုးသက်ရောက်မှုနှင့် တုံ့ပြန်မှု B-တိုင်များကို ချေမှုန်းရန် ပုံစံထုတ်ထားသည်။
ပလတ်စတစ်များသည် လမ်းသွားလမ်းလာ ထိခိုက်မှုများအတွင်း လူများ၏အသက်ကို ကယ်တင်ရာတွင်လည်း ကူညီပေးပါသည်။ ပိုလီကာဗွန်နိတ်-ရောစပ်ထားသော ဘမ်ပါများသည် ယာဉ်တိုက်မှုတွင် ခရီးသည်များကို ကာကွယ်ပေးသည်။ ပလတ်စတစ်များသည် Ford ကားများတွင် လမ်းသွားလမ်းလာများကို ပိုမိုကာကွယ်ရန်အတွက် လျင်မြန်စွာ ဖြန့်ကျက်မှုကိုလည်း လုပ်ဆောင်ပေးပါသည်။ လိုက်လျောညီထွေရှိသော လမ်းသွားလမ်းလာ-ယာဉ်တိုက်မှုမှ အကာအကွယ် တိုက်ရိုက်တပ်ဆင်ထားသော ပလပ်စတစ်ဖြင့် ပြုလုပ်ထားသော အာရုံခံကွင်းထိုးဆေးထိုးမှု။ ကျွန်ုပ်တို့၏ “Crumple Zone Blog” နှင့် BMW i3 Carbon Fiber Chassis Safety Components တို့၏ ခရီးစဉ်တွင် ပိုမိုကြည့်ရှုပါ။
လေကာမှန်များ၊ Windows နှင့် Sunroof များ
မြောက်အမေရိကလေကာမှန်များသည် အလွှာပေါင်းစုံယူနစ်အဖြစ် လာပါသည်။ ပါးလွှာသော ဖန်ချပ်နှစ်ခုကြားရှိ ပလပ်စတစ်အလွှာကို ပုံဖော်ပါ။ ပေါင်းစပ်မှုမှာ tempered glass တစ်ခုတည်းထက် ပိုမိုပါးလွှာပြီး၊ ပေါ့ပါးပြီး ခိုင်ခံ့နိုင်ပါသည်။ မျက်ရည်ခံနိုင်ရည်ရှိသော ပလပ်စတစ်အလွှာသည် ပိုင်ရှင်မှ ထုတ်လွှတ်ခြင်းကို တားဆီးပေးသည်။ တကယ်တော့ NHTSA သည် အဆိုပါအလွှာများသည် တစ်နှစ်လျှင် သေဆုံးမှု 300 ကျော်ကို ကာကွယ်ရန် ကူညီပေးသည်။
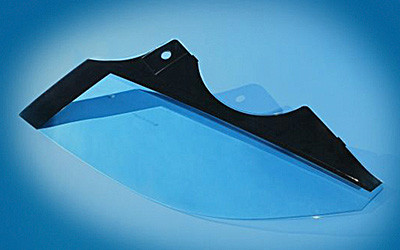
ခေါင်မိုးများအတွက် ပေါ့ပါးသော ပလပ်စတစ် အစိတ်အပိုင်းများသည် မြေဆွဲအား၏ အလယ်ဗဟိုကို နိမ့်ကျစေပြီး နက်ရှိုင်းသော ကွေ့ကောက်သည့် မတော်တဆမှု လှုပ်ရှားမှုများတွင် ထိပ်ဖျားဖြစ်နိုင်ခြေကို လျှော့ချပေးသည်။ ပုံပျက်မသွားသော ကြည်လင်သော polycarbonate သည် ယခုအခါ ခရမ်းလွန်ဒဏ်ခံနိုင်ပြီး ကိုယ်အလေးချိန်ကို သိသိသာသာ လျှော့ချနိုင်ပါပြီ။ အမိုးအကာ တစ်ခုလုံးသည် ပေါ်လီမာကို အခြေခံနိုင်သည်။
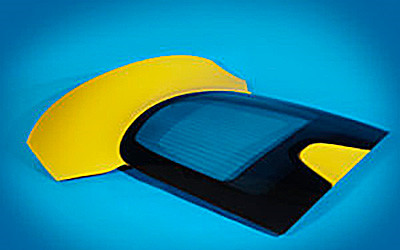
DJmolding ၏ မော်တော်ယာဥ်ပလပ်စတစ် အစိတ်အပိုင်းများ ထိုးသွင်းပုံသွင်းခြင်း။
Djmolding သည် ISO/TS 16949:2009 ပါ မော်တော်ကား ပလပ်စတစ်ဆေးထိုးသည့်ကုမ္ပဏီများဖြစ်ပြီး၊ ကျွန်ုပ်တို့သည် မော်တော်ယာဥ်၊ အာကာသယာဉ်၊ အီလက်ထရွန်နစ်၊ မော်တော်ယာဥ်များအတွက် မော်တော်ယာဥ်၊ အာကာသယာဉ်၊ အီလက်ထရွန်းနစ်၊ မော်တော်ယာဥ်များအတွက် တိကျသောဆေးထိုးမှိုများကို အသုံးပြု၍ စိတ်ကြိုက်ပလပ်စတစ်ဆေးထိုးမှို၊ ဒီဇိုင်နာနှင့် ထုတ်လုပ်သူ တို့ကို ပေးဆောင်ထားပါသည်။ ရေကြောင်း၊ ဆေးဘက်ဆိုင်ရာနှင့် တယ်လီကွန်း အသုံးချပရိုဂရမ်များ။
ကားများထုတ်လုပ်ရာတွင် အသုံးပြုသည့်ပစ္စည်း၏ နှစ်ဆယ်ရာခိုင်နှုန်းသည် မတူညီသောဝိသေသလက္ခဏာများရှိသည့် ပလတ်စတစ်အစိတ်အပိုင်းများပါဝင်သည်။ DJmolding တွင် ကျွန်ုပ်တို့သည် မော်တော်ယာဥ်ကုမ္ပဏီများအတွက်၊ မော်တော်ယာဉ်အတွင်းနှင့် အပြင်ပိုင်းအတွက်သာမက ယာဉ်စက်ပစ္စည်းများအတွက်ပါ ပလတ်စတစ်အစိတ်အပိုင်းများအားလုံးကို ထောက်ပံ့ပေးပါသည်။ ပိုခံနိုင်ရည်ရှိသော၊ ပိုပေါ့ပါးပြီး ပြန်လည်အသုံးပြုရလွယ်ကူသည့် စတီးလ်အစား အမှတ်တံဆိပ်များအသုံးပြုသည့် အမှတ်တံဆိပ်များအသုံးပြုသည့် အစိတ်အပိုင်းများထုတ်လုပ်ရန်အတွက် ပလတ်စတစ်အစိတ်အပိုင်းများကို ထိုးသွင်းခြင်းအတွက် နောက်ဆုံးပေါ်နည်းပညာဖြင့် ကျွန်ုပ်တို့လုပ်ဆောင်ပါသည်။
DJmolding သည် ပလပ်စတစ်ဆေးထိုးပုံသွင်းထုတ်လုပ်သူနှင့် ပေးသွင်းသူအနေဖြင့် သာမိုပလတ်စတစ်ဆေးထိုးခြင်းနည်းပညာကို အထူးပြုပါသည်။ ကျွန်ုပ်တို့၏အသိပညာတွင် ဓာတ်ငွေ့ဆေးထိုးခြင်းနည်းပညာ၊ တောက်ပမှုမြင့်မားခြင်းနှင့် အီးပုံသွင်းခြင်းတို့ ပါဝင်သည်။ ကျွန်ုပ်တို့၏ မော်တော်ယာဥ်လုပ်ငန်းအတွက် ဆေးထိုးပုံသွင်းထားသော အပြင်ပိုင်းနှင့် အတွင်းပိုင်း ကားအစိတ်အပိုင်းများကို အောက်ပါပစ္စည်းများမှ အများစုဖြင့် ပြုပြင်ထားခြင်းဖြစ်သည်- - polystyrene (PS), - polypropylene (PP), - ABS, - PC, - PC / ABS, - PC / PMMA။
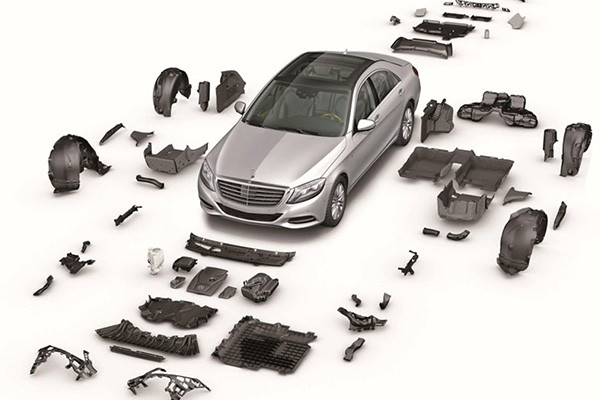
အတွင်းခန်း ဆေးထိုးပုံသွင်းထားသော ကားအစိတ်အပိုင်းများ
တက်ကြွသောမော်တော်ကားလုပ်ငန်းအတွက် ကျွန်ုပ်တို့သည် ဆေးထိုးပုံသွင်းအတွင်းပိုင်းအစိတ်အပိုင်းအမျိုးမျိုးကို ထုတ်လုပ်ရာတွင် ယုံကြည်စိတ်ချရသောမိတ်ဖက်တစ်ဦးဖြစ်သည်။ ကျွန်ုပ်တို့၏ ISO IATF အသိအမှတ်ပြုစက်ရုံများတွင် ကျွန်ုပ်တို့သည် ထိပ်တန်းမော်တော်ယာဥ်ထုတ်လုပ်သူများအတွက် အတွင်းပိုင်းပရောဂျက်များကို လုပ်ဆောင်ပါသည်။ ကျွန်ုပ်တို့သည် အတွေ့အကြုံရှိသော OEM၊ Tier 1 မော်တော်ကားရောင်းချသူနှင့် မော်တော်ယာဥ်အတွင်းပိုင်းနှင့် အပြင်ပိုင်းဖြတ်ပိုင်းအစိတ်အပိုင်းများ ထုတ်လုပ်သူဖြစ်သည်။ ကျွန်ုပ်တို့၏ ထုတ်ကုန်အတွင်းပိုင်းဆေးထိုးခြင်းလုပ်ငန်းစု၏ အစိတ်အပိုင်းများတွင် ပလပ်စတစ်အလိုအလျောက်အစိတ်အပိုင်းများဖြစ်သည့်- ဒက်ရှ်ဘုတ်ဒြပ်စင်များ (ဥပမာ- လက်အိတ်အခန်း၊ တံခါးနှင့် ပြတင်းပေါက်တိုင်များ)၊ စတီယာရင်ကော်လံဖြတ်တောက်မှုများ၊ တံခါးလက်ကိုင်များ၊ လေဝင်ပေါက်များ၊ အလယ်ခလုတ်များ၊ ခေါင်မိုး modules စသည်တို့ဖြစ်သည်။
ပြင်ပဆေးထိုးပုံသွင်းထားသော ကားအစိတ်အပိုင်းများ
ဆေးထိုးပုံသွင်းခြင်းသည် ကျယ်ပြန့်သော ကားအတွင်းပိုင်း အစိတ်အပိုင်းများကို ထုတ်လုပ်ရန် အကောင်းဆုံးနည်းပညာဖြစ်သည်။ ကျွန်ုပ်တို့၏ အတွေ့အကြုံရှိ ဆေးထိုးပုံသွင်းခြင်းဆိုင်ရာ ကျွမ်းကျင်ပညာရှင်များအဖွဲ့သည် မော်တော်ယာဥ် OEMs များနှင့် အဆင့် 1 ဖောက်သည်များနှင့် နီးကပ်စွာ လုပ်ဆောင်ပြီး နည်းပညာဆိုင်ရာ လိုအပ်ချက်အားလုံးကို အကဲဖြတ်ကာ သတ်မှတ်ကာ ထို့ကြောင့် ချွတ်ယွင်းချက်မရှိသော ပြင်ပယာဉ်အစိတ်အပိုင်းများ ထုတ်လုပ်မှုကို အကောင်းဆုံးဖြစ်အောင် လုပ်ဆောင်ပါသည်။ ကျွန်ုပ်တို့သည် မော်တော်ယာဥ်အပြင်ပိုင်း အစိတ်အပိုင်းများ ဥပမာ- ရွှံ့အကာများ (အကာအရံများ)၊ ဘီးခုံးများ၊ မီးကင်များ၊ အာရုံခံကိရိယာများ၊ ကြမ်းပြင်သံလမ်းများ၊ ပင်စည်ဖြတ်တောက်မှုများ၊ ရှေ့နှင့်နောက်ဖုံးများ၊ ဘမ်ဘာများနှင့် အပြင်ဘက်ကားတံခါးအနားကွပ်များ၊ တံခါးဘောင်များ။ ကားများအတွက် ကျွန်ုပ်တို့၏ ဆေးထိုးပလပ်စတစ် အစိတ်အပိုင်းများကို ကမ္ဘာတစ်ဝှမ်းရှိ ကားမော်ဒယ်လ်အမျိုးမျိုးတွင် တွေ့နိုင်ပါသည်။
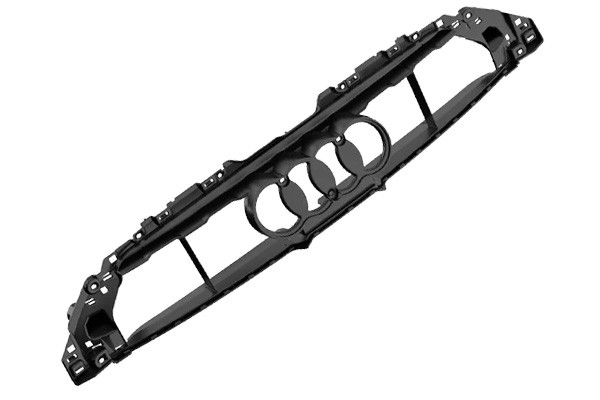
ကျွန်ုပ်တို့၏ ရည်မှန်းချက်မှာ ကျွန်ုပ်တို့၏ဖောက်သည်များအား အကြီးမားဆုံးတန်ဖိုးကို ပေးဆောင်ရန်ဖြစ်သည်။ ပလပ်စတစ် အစိတ်အပိုင်းများ ထုတ်လုပ်ခြင်းအပြင် DJmolding သည် ဆေးထိုးပုံသွင်းခြင်း ဒီဇိုင်းနှင့် ထုတ်လုပ်ရေး ဝန်ဆောင်မှုများကို ပေးဆောင်ပါသည်။ ကျွန်ုပ်တို့၏ဖောက်သည်များအား စျေးကွက်သို့ပို့ဆောင်ရန် အသင့်ရှိသောပုံစံဖြင့် ပလတ်စတစ်အစိတ်အပိုင်းများရရှိရန် ကျွန်ုပ်တို့ကူညီပေးပါသည်။ ကျွန်ုပ်တို့သည် ဆေးထိုးပုံသွင်းခြင်း၊ မော်တော်ယာဥ်ပလတ်စတစ်အစိတ်အပိုင်းများလုပ်ငန်းအတွက် ထုတ်ကုန်အချောထည်များ ပေးပို့ခြင်းမှတစ်ဆင့် လုပ်ငန်းစဉ်တစ်ခုလုံးကို အကျုံးဝင်ပါသည်။
သင်တွေ့မြင်ရသည့်အတိုင်း DJmolding သည် ၎င်း၏ဖောက်သည်များအား ၎င်းတို့ဘာသာ ချန်ထားခဲ့ခြင်းမရှိပေ။ ခြေလှမ်းတိုင်းတွင်၊ ကျယ်ကျယ်ပြန့်ပြန့်ချဉ်းကပ်မှုပေးခြင်းဖြင့် ကျွန်ုပ်တို့၏ဖောက်သည်များအား ကူညီရန် ကျွန်ုပ်တို့ရှိနေပါသည်။ ကျွန်ုပ်တို့သည် အစပိုင်းတွင် ရှုပ်ထွေးသောလုပ်ငန်းစဉ်ဟု ထင်ရသည့်အရာကို အောင်မြင်သောပူးပေါင်းဆောင်ရွက်မှုအဖြစ်သို့ လွယ်ကူစွာပြောင်းလဲနိုင်သည်။
မော်တော်ယာဥ်လုပ်ငန်းသည် ပေါ့ပါးပြီး ထိရောက်သောပစ္စည်းများကို ပြင်းပြင်းထန်ထန် အလေးထားပြီး နှစ်များတစ်လျှောက် ထူးထူးခြားခြား တိုးတက်မှုများကို မြင်တွေ့ခဲ့ရသည်။ ခေတ်မီမော်တော်ယာဉ်ထုတ်လုပ်ရေးတွင် ပလတ်စတစ်အစိတ်အပိုင်းများသည် တာရှည်ခံမှု၊ ဒီဇိုင်းပြောင်းလွယ်ပြင်လွယ်နှင့် ကုန်ကျစရိတ်သက်သာမှုတို့ကို ပေးဆောင်ရန် အရေးကြီးပါသည်။ မော်တော်ကား ပလတ်စတစ် အစိတ်အပိုင်းများ အတွက် အမျိုးမျိုးသော ထုတ်လုပ်မှု လုပ်ငန်းစဉ်များထဲတွင် ဆေးထိုးပုံသွင်းခြင်းကို တွင်ကျယ်စွာ အသုံးပြုပါသည်။ ဤဘလော့ဂ်ပို့စ်သည် မော်တော်ယာဥ်ပလပ်စတစ် အစိတ်အပိုင်းများကို ဆေးထိုးပုံသွင်းခြင်း၊ ၎င်း၏ အကျိုးကျေးဇူးများ၊ အသုံးချမှုများနှင့် ပေါ်ပေါက်လာသော ခေတ်ရေစီးကြောင်းများကို လေ့လာပါမည်။ မော်တော်ယာဥ်ပလတ်စတစ်အစိတ်အပိုင်းများကို ပုံသွင်းခြင်း၏ စွဲမက်ဖွယ်ကမ္ဘာကို စူးစမ်းကြည့်ကြပါစို့။
မော်တော်ယာဥ်လုပ်ငန်းတွင် ဆေးထိုးပုံသွင်းခြင်းကို နားလည်ခြင်း။
မော်တော်ကားလုပ်ငန်းသည် ဒက်ရှ်ဘုတ်များ၊ ဘမ်ဘာများ၊ တူရိယာပြားများ စသည်တို့အပါအဝင် အစိတ်အပိုင်းအမျိုးမျိုးကို ထုတ်လုပ်ရန်အတွက် ဆေးထိုးပုံသွင်းခြင်းကို အသုံးပြုသည်။
မော်တော်ယာဥ်လုပ်ငန်းတွင် ဆေးထိုးပုံသွင်းခြင်းကို နားလည်သောအခါတွင် ထည့်သွင်းစဉ်းစားရမည့်အချက်အချို့မှာ အောက်ပါအတိုင်းဖြစ်သည်။
ဆေးထိုးခြင်းတွင်အသုံးပြုသောပစ္စည်းများ
ထိုးသွင်းပုံသွင်းခြင်း အပါအဝင် ကျယ်ပြန့်သော သာမိုပလတ်စတစ်နှင့် အပူချိန်ထိန်းပစ္စည်းများကို အသုံးပြုသည်-
- polypropylene (PP)
- Polyethylene (PE)
- ပိုလီဗင်နိုင်းကလိုရိုက် (PVC)
- Acrylonitrile-butadiene-styrene (ABS)
- ပိုလီကာဗွန်နိတ် (PC)
- Polyamide (PA)
- Polyurethane (PU)၊
ပစ္စည်းတစ်ခုစီတွင် ပြောင်းလွယ်ပြင်လွယ်၊ ခိုင်ခံ့မှု၊ တာရှည်ခံမှုနှင့် အပူနှင့် ဓာတုပစ္စည်းများကို ခံနိုင်ရည်ရှိခြင်းစသည့် ထူးခြားသောဂုဏ်သတ္တိများနှင့် လက္ခဏာများရှိသည်။ ပစ္စည်းရွေးချယ်မှုသည် ထုတ်လုပ်သည့်အစိတ်အပိုင်း သို့မဟုတ် ထုတ်ကုန်၏ သီးခြားလိုအပ်ချက်များပေါ်တွင် မူတည်သည်။
မော်တော်ယာဥ်လုပ်ငန်းတွင် ဆေးထိုးခြင်း၏ အားသာချက်များ
- မြင့်မားသောထုတ်လုပ်မှုထိရောက်မှု- ဆေးထိုးပုံသွင်းခြင်းသည် အစိတ်အပိုင်းအများအပြားကို လျင်မြန်ထိရောက်စွာ ထုတ်လုပ်နိုင်ပြီး ထုတ်လုပ်မှုအချိန်နှင့် ကုန်ကျစရိတ်များကို လျှော့ချနိုင်သည်။
- တိကျမှုနှင့် လိုက်လျောညီထွေမှု- ဆေးထိုးပုံသွင်းခြင်းသည် အပိုင်းပိုင်းများကြား ကွဲလွဲမှုအနည်းဆုံးဖြင့် တိကျပြီး တသမတ်တည်းရှိသော အစိတ်အပိုင်းများကို ထုတ်လုပ်သည်။
- ဒီဇိုင်းပြောင်းလွယ်ပြင်လွယ်- ထိုးသွင်းပုံသွင်းခြင်းသည် ရှုပ်ထွေးသောဂျီဩမေတြီများနှင့် အနုစိတ်အသေးစိတ်အချက်အလက်များကို အစိတ်အပိုင်းများအတွင်း ထည့်သွင်းနိုင်စေပြီး၊ ဒီဇိုင်နာများသည် တိကျသောလုပ်ငန်းဆောင်တာနှင့် အလှအပဆိုင်ရာလိုအပ်ချက်များနှင့်ကိုက်ညီသည့် အပိုင်းအစများကို ဖန်တီးနိုင်စေပါသည်။
- ကုန်ကျစရိတ်-ထိရောက်မှု- ဆေးထိုးပုံသွင်းခြင်းသည် စက်ဖြင့်ပြုလုပ်ခြင်း သို့မဟုတ် ပုံသွင်းခြင်းကဲ့သို့သော အခြားကုန်ထုတ်နည်းလမ်းများထက် ကုန်ကျစရိတ်သက်သာစွာဖြင့် အစိတ်အပိုင်းများကို ထုတ်လုပ်နိုင်သည်။
မော်တော်ယာဥ်လုပ်ငန်းတွင် ဆေးထိုးခြင်းဆိုင်ရာ စိန်ခေါ်မှုများ
- ကိရိယာတန်ဆာပလာ ကုန်ကျစရိတ်- ဆေးထိုးပုံသွင်းခြင်းသည် ဒီဇိုင်းနှင့် ထုတ်လုပ်ရန် စျေးကြီးနိုင်သည့် မှိုဖန်တီးမှု လိုအပ်သည်။
- ပစ္စည်းရွေးချယ်ခြင်း- အစိတ်အပိုင်းတစ်ခု သို့မဟုတ် ထုတ်ကုန်တစ်ခုအတွက် သင့်လျော်သောပစ္စည်းကို ရွေးချယ်ခြင်းသည် စိန်ခေါ်မှုတစ်ခုဖြစ်နိုင်သည်။
- ပြုပြင်ထိန်းသိမ်းခြင်းနှင့် ပြုပြင်ခြင်း- ဆေးထိုးပုံသွင်းစက်သည် အကောင်းဆုံးစွမ်းဆောင်ရည်ကိုသေချာစေရန်နှင့် စက်ရပ်ခြင်းကိုကာကွယ်ရန် ပုံမှန်ပြုပြင်ထိန်းသိမ်းမှုများ လိုအပ်ပါသည်။
- ပတ်ဝန်းကျင်ထိခိုက်မှု- ဆေးထိုးပုံသွင်းခြင်းမှ ထွက်ရှိလာသော ပလပ်စတစ်အမှိုက်များကို စွန့်ပစ်ခြင်းသည် ပတ်ဝန်းကျင်ဆိုင်ရာ ဆိုးကျိုးများကို ဖြစ်စေနိုင်သည်။
မော်တော်ယာဥ်ပလပ်စတစ် အစိတ်အပိုင်းများ ထိုးသွင်းပုံသွင်းခြင်း၏ အကျိုးကျေးဇူးများ
မော်တော်ကား ပလပ်စတစ် အစိတ်အပိုင်းများ ဆေးထိုးပုံသွင်းခြင်း သည် မှိုနှင့် ပလပ်စတစ် အလုံးများ အသုံးပြုခြင်း အားဖြင့် ရှုပ်ထွေးသော အစိတ်အပိုင်းများ ဖန်တီးခြင်း ပါဝင်သည်။ ဤနည်းလမ်းကို ၎င်း၏ အကျိုးကျေးဇူးများစွာကြောင့် မော်တော်ယာဥ်လုပ်ငန်းတွင် တွင်ကျယ်စွာ အသုံးပြုကြသည်။ ဤဘလော့ဂ်ပို့စ်တွင် ဆေးထိုးပုံသွင်းခြင်း မော်တော်ယာဥ်ပလပ်စတစ်အစိတ်အပိုင်းများ၏ အားသာချက်များကို ဆွေးနွေးပါမည်။
ကုန်ကျစရိတ်သက်သာခြင်း- မော်တော်ကား ပလပ်စတစ် အစိတ်အပိုင်းများ ဆေးထိုးခြင်း၏ အရေးအကြီးဆုံး အကျိုးကျေးဇူးများထဲမှ တစ်ခုမှာ အစိတ်အပိုင်းများ ထုတ်လုပ်ရာတွင် ကုန်ကျစရိတ်သက်သာသော နည်းလမ်းတစ်ခုဖြစ်သည်။ အဘယ်ကြောင့်ဆိုသော် လုပ်ငန်းစဉ်သည် များပြားလှသော အစိတ်အပိုင်းများကို လျင်မြန်ထိရောက်စွာ ဖန်တီးနိုင်သောကြောင့် ဖြစ်သည်။ ၎င်းသည် ထုတ်လုပ်မှုကုန်ကျစရိတ်ကို လျှော့ချစေပြီး ကုန်ကျစရိတ်သည် အမြဲတမ်းစိုးရိမ်စရာရှိသည့် မော်တော်ကားလုပ်ငန်းအတွက် စံပြဖြေရှင်းချက်တစ်ခု ဖြစ်လာစေသည်။
ပေါ့ပါးခြင်း- မော်တော်ယာဥ်လုပ်ငန်းတွင် ပလပ်စတစ်ဆေးထိုးခြင်း၏ နောက်ထပ်ထူးခြားချက်မှာ ပလတ်စတစ်အစိတ်အပိုင်းများသည် ပေါ့ပါးခြင်းပင်ဖြစ်သည်။ သဘာဝပတ်ဝန်းကျင်ဆိုင်ရာ စည်းမျဉ်းများနှင့် သုံးစွဲသူများ၏ မျှော်လင့်ချက်များကို ဖြည့်ဆည်းရာတွင် ကားထုတ်လုပ်သူများအတွက် အရေးကြီးသောအချက်ဖြစ်သည့် မော်တော်ယာဉ်များ၏ ဆီစားသက်သာမှုကို ပိုမိုကောင်းမွန်စေသောကြောင့် ၎င်းသည် အရေးကြီးပါသည်။
ကြံ့ခိုင်မှုနှင့် တာရှည်ခံမှု- ဆေးထိုးပုံသွင်းခြင်းဖြင့် ထုတ်လုပ်သော ပလပ်စတစ် အစိတ်အပိုင်းများသည် အလွန်အစွမ်းထက်ပြီး တာရှည်ခံမှုရှိသည်။ အဘယ်ကြောင့်ဆိုသော် လုပ်ငန်းစဉ်သည် တသမတ်တည်းရှိသော နံရံအထူနှင့် အနည်းငယ်မျှသော ကွဲထွက်မှုရှိသော အစိတ်အပိုင်းများကို ဖန်တီးနိုင်သောကြောင့် ဖြစ်သည်။ ရလဒ်အနေဖြင့် ဆေးထိုးပုံသွင်းခြင်းဖြင့် ထုတ်လုပ်သော ပလတ်စတစ်အစိတ်အပိုင်းများသည် မြင့်မားသောအပူချိန်နှင့် တုန်ခါမှုကဲ့သို့သော မော်တော်ကားပတ်ဝန်းကျင်၏ ပြင်းထန်မှုကို ခံနိုင်ရည်ရှိသည်။
customization: ဆေးထိုးပုံသွင်းခြင်းသည် အရွယ်အစားအမျိုးမျိုးနှင့် ပုံသဏ္ဍာန်အမျိုးမျိုးဖြင့် အစိတ်အပိုင်းများကို ဖန်တီးနိုင်စေပါသည်။ စိတ်ကြိုက်ပြင်ဆင်ခြင်းသည် မရှိမဖြစ်လိုအပ်သော မော်တော်ကားလုပ်ငန်းအတွက် စံပြဖြေရှင်းချက်တစ်ခုဖြစ်သည်။ ဆေးထိုးပုံသွင်းခြင်းဖြင့် ကားထုတ်လုပ်သူများသည် အရွယ်အစား၊ ပုံသဏ္ဍာန်နှင့် အရောင်ကဲ့သို့သော သီးခြားလိုအပ်ချက်များနှင့်ကိုက်ညီသည့် အစိတ်အပိုင်းများကို အလွယ်တကူ ဖန်တီးနိုင်သည်။
စွန့်ပစ်အမှိုက်- ပလပ်စတစ်ဆေးထိုးပုံသွင်းခြင်းသည် သမားရိုးကျကုန်ထုတ်နည်းများထက် စွန့်ပစ်ပစ္စည်းနည်းပါးသည်။ လုပ်ငန်းစဉ်သည် အလွန်ထိရောက်ပြီး အပိုင်းအစအနည်းငယ်မျှဖြင့် ဖန်တီးနိုင်သည်။ ရလဒ်အနေဖြင့်၊ မော်တော်ကားလုပ်ငန်းသည် ပလပ်စတစ်အစိတ်အပိုင်းများထုတ်လုပ်ရန် ဆေးထိုးပုံသွင်းခြင်းကို အသုံးပြုခြင်းဖြင့် ၎င်း၏ကာဗွန်ခြေရာကို လျှော့ချနိုင်သည်။
ပိုမြန်သောထုတ်လုပ်မှု- ဆေးထိုးပုံသွင်းခြင်းသည် ပလပ်စတစ်အစိတ်အပိုင်းများထုတ်လုပ်ရာတွင် မြန်ဆန်ထိရောက်သောနည်းလမ်းတစ်ခုဖြစ်သည်။ လုပ်ငန်းစဉ်သည် စက္ကန့်ပိုင်းအတွင်း အစိတ်အပိုင်းများကို ဖန်တီးနိုင်ပြီး အမြန်ထုတ်လုပ်မှုအချိန်သည် အရေးကြီးသည့် မော်တော်ကားလုပ်ငန်းအတွက် စံပြဖြေရှင်းချက်တစ်ခု ဖြစ်လာစေသည်။
ပိုမိုကောင်းမွန်သော အရည်အသွေး- ဆေးထိုးပုံသွင်းခြင်းဖြင့် ထုတ်လုပ်သော ပလပ်စတစ် အစိတ်အပိုင်းများသည် တသမတ်တည်း အရည်အသွေးရှိသည်။ အဘယ်ကြောင့်ဆိုသော် လုပ်ငန်းစဉ်သည် အပူချိန်၊ ဖိအားနှင့် အအေးခံချိန်ကဲ့သို့သော ပုံသွင်းခြင်းဆိုင်ရာ ကန့်သတ်ချက်များအပေါ် တိကျစွာ ထိန်းချုပ်နိုင်သောကြောင့် ဖြစ်သည်။ ရလဒ်အနေဖြင့် ဆေးထိုးပုံသွင်းခြင်းဖြင့် ထုတ်လုပ်သော ပလပ်စတစ်အစိတ်အပိုင်းများသည် အလွန်ကောင်းမွန်သော Dimension တိကျမှုနှင့် မျက်နှာပြင်အချောထည်များရှိသည်။
Injection Molding တွင် အသုံးများသော ပလတ်စတစ်များကို စူးစမ်းလေ့လာခြင်း။
ထိုးသွင်းပုံသွင်းခြင်းတွင် ပလပ်စတစ်အလုံးများကို အရည်ပျော်ပြီး တိကျသောပုံစံတစ်ခုအဖြစ် ဖန်တီးရန်အတွက် မှိုပေါက်တစ်ခုထဲသို့ ထိုးသွင်းခြင်းပါဝင်သည်။ ဤလုပ်ငန်းစဉ်၏ ဘက်စုံသုံးနိုင်မှုသည် ထုတ်လုပ်သူများအား မြင့်မားသောတိကျမှုနှင့် လိုက်လျောညီထွေရှိသော ရှုပ်ထွေးသောအစိတ်အပိုင်းများကို ဖန်တီးနိုင်စေပါသည်။ အလိုရှိသောဂုဏ်သတ္တိများရရှိရန် ဆေးထိုးပုံသွင်းရာတွင် ပလပ်စတစ်ပစ္စည်းအမျိုးမျိုးကို အသုံးပြုကြသည်။ ဤဘလော့ဂ်ပို့စ်တွင် ဆေးထိုးပုံသွင်းရာတွင် အသုံးများသော ပလတ်စတစ်များနှင့် ၎င်းတို့၏ ဂုဏ်သတ္တိများကို လေ့လာပါမည်။
- Acrylonitrile Butadiene Styrene (ABS) - ABS သည် ၎င်း၏ ကြီးမားသော အကျိုးသက်ရောက်မှု၊ ခိုင်ခံ့မှုနှင့် အပူဒဏ်ခံနိုင်မှုတို့ကြောင့် ဆေးထိုးပုံသွင်းရာတွင် တွင်ကျယ်စွာ အသုံးပြုသည့် သာမိုပလတ်စတစ် ပေါ်လီမာတစ်ခုဖြစ်သည်။ မော်တော်ကား အစိတ်အပိုင်းများ၊ အရုပ်များနှင့် အီလက်ထရွန်းနစ် အိမ်ရာများတွင် အသုံးများသည်။
- ပိုလီကာဗွန်နိတ် (PC)- PC သည် ဘေးကင်းရေးမျက်မှန်များ၊ အီလက်ထရွန်းနစ်အစိတ်အပိုင်းများနှင့် မော်တော်ယာဥ်အစိတ်အပိုင်းများကဲ့သို့သော ထိခိုက်မှုခံနိုင်ရည်ရှိပြီး အလင်းပြတ်သားမှုလိုအပ်သော ထုတ်ကုန်များအတွက် ဆေးထိုးမှိုများတွင် အသုံးပြုသည့် တောင့်တင်းသော၊ ဖောက်ထွင်းမြင်ရသော ပလပ်စတစ်ပစ္စည်းဖြစ်သည်။
- Polypropylene (PP): PP သည် ပြောင်းလွယ်ပြင်လွယ်၊ ခိုင်ခံ့မှုနှင့် ဓာတုခံနိုင်ရည်လိုအပ်သော ထုတ်ကုန်များအတွက် ဆေးထိုးပုံသွင်းရာတွင် အသုံးပြုသည့် စွယ်စုံရပလပ်စတစ်ပစ္စည်းဖြစ်သည်။ ထုပ်ပိုးမှု၊ မော်တော်ကားအစိတ်အပိုင်းများနှင့် လူသုံးကုန်ပစ္စည်းများတွင် အသုံးများသည်။
- Polyethylene (PE): PE သည် ပျော့ပြောင်းမှုနှင့် တာရှည်ခံမှု လိုအပ်သော ထုတ်ကုန်များအတွက် ဆေးထိုးပုံသွင်းရာတွင် အသုံးပြုသည့် ပေါ့ပါးသော ပလပ်စတစ်ပစ္စည်းဖြစ်သည်။ ထုပ်ပိုးမှု၊ အိမ်သုံးပစ္စည်းများနှင့် ကစားစရာများတွင် အသုံးများသည်။
- Polyoxymethylene (POM): POM သည် အတိုင်းအတာတည်ငြိမ်မှုနှင့် ဝတ်ဆင်မှုခံနိုင်ရည်လိုအပ်သော ထုတ်ကုန်များအတွက် ဆေးထိုးပုံသွင်းရာတွင် အသုံးပြုသည့် အခဲနှင့် တောင့်တင်းသော ပလပ်စတစ်ပစ္စည်းဖြစ်သည်။ ဂီယာများ၊ ဝက်ဝံများနှင့် အခြားစက်ပိုင်းဆိုင်ရာ အစိတ်အပိုင်းများတွင် အသုံးများသည်။
- Polystyrene (PS) : PS သည် ကောင်းမွန်သော အတိုင်းအတာ တည်ငြိမ်မှုနှင့် လျှပ်ကာဂုဏ်သတ္တိများ လိုအပ်သော ထုတ်ကုန်များအတွက် ဆေးထိုးပုံသွင်းရာတွင် အသုံးပြုသည့် ပေါ့ပါးပြီး တောင့်တင်းသော ပလပ်စတစ်ပစ္စည်းဖြစ်သည်။ အစားအသောက်ထုပ်ပိုးမှု၊ တစ်ခါသုံးအသုံးအဆောင်များနှင့် CD ဘူးများတွင် အသုံးများသည်။
- Polyethylene Terephthalate (PET) - PET သည် ကြည်လင်ပြတ်သားမှု၊ တောင့်တင်းမှုနှင့် ဓာတုဒဏ်ခံနိုင်မှု မြင့်မားသော ထုတ်ကုန်များအတွက် ဆေးထိုးပုံသွင်းရာတွင် အသုံးပြုသည့် ခိုင်ခံ့ပေါ့ပါးသော ပလပ်စတစ်ပစ္စည်းဖြစ်သည်။ အဖျော်ယမကာပုလင်းများ၊ အစားအသောက်ထုပ်ပိုးခြင်းနှင့် ဆေးဘက်ဆိုင်ရာ ကိရိယာများတွင် အသုံးများသည်။
- နိုင်လွန် (PA) : နိုင်လွန်သည် ပြင်းထန်သော၊ တာရှည်ခံသော ပလပ်စတစ်ပစ္စည်းဖြစ်ပြီး မြင့်မားသော ခွန်အား၊ အပူဒဏ်နှင့် ဓာတုဒဏ်ခံနိုင်မှု လိုအပ်သော ထုတ်ကုန်များအတွက် ဆေးထိုးပုံသွင်းရာတွင် အသုံးပြုသည့် ပစ္စည်းဖြစ်သည်။ မော်တော်ကား အစိတ်အပိုင်းများ၊ အီလက်ထရွန်းနစ် အစိတ်အပိုင်းများနှင့် စက်မှုလုပ်ငန်းသုံး စက်များတွင် အသုံးများသည်။
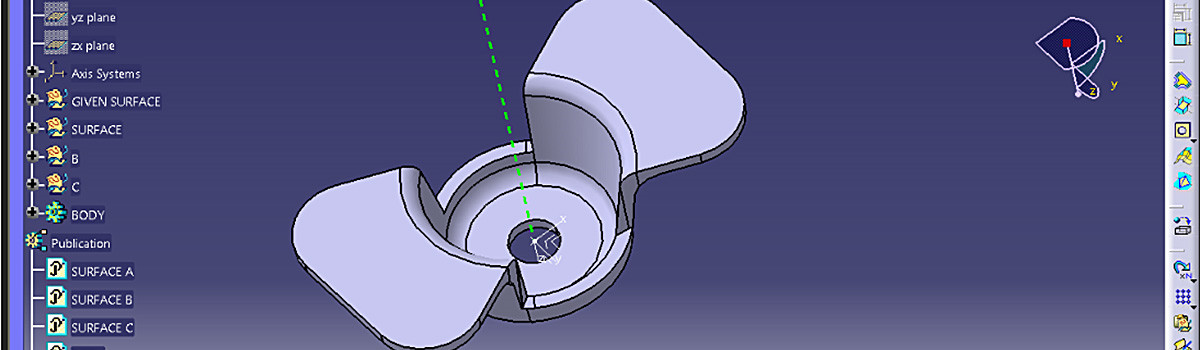
မော်တော်ကား ပလတ်စတစ် အစိတ်အပိုင်းများအတွက် ဒီဇိုင်းထည့်သွင်းစဉ်းစားမှုများ
ဤဘလော့ဂ်ပို့စ်သည် မော်တော်ယာဥ်ပလတ်စတစ်အစိတ်အပိုင်းများအတွက် အရေးကြီးသော ဒီဇိုင်းထည့်သွင်းစဉ်းစားမှုများကို ဆွေးနွေးပါမည်။
ပစ္စည်းရွေးချယ်မှု-
- ပလပ်စတစ် အစိတ်အပိုင်းများကို polypropylene၊ polycarbonate၊ ABS နှင့် အခြားအရာများ အပါအဝင် အမျိုးမျိုးသော ပစ္စည်းများဖြင့် ပြုလုပ်နိုင်သည်။
- ပစ္စည်းတစ်ခုစီတွင် ခိုင်ခံ့မှု၊ တောင့်တင်းမှု၊ အပူတည်ငြိမ်မှုနှင့် ဓာတုပစ္စည်းများနှင့် ခရမ်းလွန်ရောင်ခြည်ကို ခံနိုင်ရည်ရှိခြင်းစသည့် ထူးခြားသောဂုဏ်သတ္တိများရှိသည်။
- တစ်စိတ်တစ်ပိုင်း၏ ရည်ရွယ်အသုံးပြုမှုနှင့် စည်းမျဉ်းစည်းကမ်းစံနှုန်းများနှင့် ကိုက်ညီသော သီးခြားလိုအပ်ချက်များနှင့် ကိုက်ညီသည့် ပစ္စည်းကို ရွေးချယ်ရန် အရေးကြီးပါသည်။
ထုတ်လုပ်မှုနည်းလမ်း
- ပလပ်စတစ်အစိတ်အပိုင်းများကို ဆေးထိုးပုံသွင်းခြင်း၊ လေမှုတ်သွင်းခြင်း၊ အပူချိန်ထိန်းခြင်းနှင့် လှည့်ပုံသွင်းခြင်းအပါအဝင် နည်းလမ်းများစွာဖြင့် ထုတ်လုပ်နိုင်သည်။
- နည်းလမ်းတစ်ခုစီတွင် ကုန်ကျစရိတ်၊ ထုတ်လုပ်မှုအမြန်နှုန်း၊ ရှုပ်ထွေးမှုနှင့် အစိတ်အပိုင်းအရည်အသွေးတို့၌ အားသာချက်များနှင့် အားနည်းချက်များရှိသည်။
- ထုတ်လုပ်မှုနည်းလမ်းကို ၎င်း၏အရွယ်အစား၊ ပုံသဏ္ဍာန်နှင့် ထုထည်၊ တိကျမှုနှင့် လိုက်လျောညီထွေရှိမှုတို့ကဲ့သို့ အစိတ်အပိုင်း၏ သီးခြားလိုအပ်ချက်များအပေါ် အခြေခံ၍ ရွေးချယ်သင့်သည်။
အစိတ်အပိုင်းလုပ်ဆောင်နိုင်စွမ်း-
- ပလပ်စတစ် အစိတ်အပိုင်း၏ လုပ်ဆောင်ချက်ကို ဒီဇိုင်းဆွဲသည့်အခါ ဂရုတစိုက် ထည့်သွင်းစဉ်းစားသင့်သည်။
- စက်ပိုင်းဆိုင်ရာဖိအားများ၊ အပူချိန်အတက်အကျများ၊ ဓာတုထိတွေ့မှုနှင့် အခြားပတ်ဝန်းကျင်ဆိုင်ရာအချက်များအား ခံနိုင်ရည်ရှိရန် အစိတ်အပိုင်းများကို ဒီဇိုင်းထုတ်ရန် လိုအပ်ပါသည်။
- အစိတ်အပိုင်း၏ အံဝင်ခွင်ကျ၊ ပုံစံ၊ လုပ်ဆောင်ချက်နှင့် အလှအပဆိုင်ရာ လိုအပ်ချက်များကိုလည်း ထည့်သွင်းစဉ်းစားသင့်သည်။
တပ်ဆင်မှုအတွက် ဒီဇိုင်း
- ပလပ်စတစ် အစိတ်အပိုင်းများကို တပ်ဆင်ရလွယ်ကူအောင် ဒီဇိုင်းထုတ်သင့်သည်။
- တပ်ဆင်ရန် ခက်ခဲသော သို့မဟုတ် အချိန်ကုန်သော အစိတ်အပိုင်းများသည် ထုတ်လုပ်မှု ကုန်ကျစရိတ်ကို တိုးမြင့်စေပြီး အရည်အသွေးဆိုင်ရာ ပြဿနာများကို ဖြစ်ပေါ်စေနိုင်သည်။
- အပိုပစ္စည်းများ သို့မဟုတ် တွယ်ကပ်ကိရိယာများ လိုအပ်မှု အနည်းဆုံးဖြင့် အစိတ်အပိုင်းများကို အလွယ်တကူနှင့် လုံလုံခြုံခြုံ လိုက်လျောညီထွေဖြစ်အောင် ဒီဇိုင်းထုတ်သင့်သည်။
ထုတ်လုပ်နိုင်စွမ်းအတွက် ဒီဇိုင်း
- ပလတ်စတစ်အစိတ်အပိုင်းများ၏ ဒီဇိုင်းသည် ထုတ်လုပ်မှုလုပ်ငန်းစဉ်နှင့် ကန့်သတ်ချက်များ သို့မဟုတ် ကန့်သတ်ချက်များကိုလည်း ထည့်သွင်းစဉ်းစားသင့်သည်။
- မူကြမ်းထောင့်များ၊ နံရံအထူနှင့် ခွဲထားသောမျဉ်းများကဲ့သို့သော ဒီဇိုင်းအင်္ဂါရပ်များသည် ထုတ်ကုန်အရည်အသွေးနှင့် ကုန်ကျစရိတ်ကို သိသိသာသာ သက်ရောက်မှုရှိနိုင်သည်။
- ထုတ်လုပ်သူနှင့် ပူးပေါင်းဆောင်ရွက်ခြင်းသည် ဒီဇိုင်းကို ထုတ်လုပ်မှုအတွက် အကောင်းဆုံးဖြစ်အောင် သေချာစေနိုင်သည်။
စမ်းသပ်ခြင်းနှင့် အတည်ပြုခြင်း-
- ပလပ်စတစ် အစိတ်အပိုင်း၏ ဒီဇိုင်း ပြီးသည်နှင့်၊ ၎င်းသည် လိုအပ်သော စွမ်းဆောင်ရည်နှင့် ဘေးကင်းရေး လိုအပ်ချက်များနှင့် ကိုက်ညီကြောင်း သေချာစေရန် ၎င်းအား စမ်းသပ်စစ်ဆေးပြီး မှန်ကန်ကြောင်း အတည်ပြုသင့်သည်။
- စမ်းသပ်ခြင်းတွင် စက်ပိုင်းဆိုင်ရာ၊ ဓာတုဗေဒနှင့် အပူပိုင်းစမ်းသပ်ခြင်းနှင့် အံဝင်ခွင်ကျလုပ်ဆောင်မှုများအတွက် စမ်းသပ်ခြင်းများ ပါဝင်နိုင်သည်။
- ကနဦးဒီဇိုင်းမှ နောက်ဆုံးထုတ်ကုန်အထိ ဖွံ့ဖြိုးတိုးတက်ရေး လုပ်ငန်းစဉ်တစ်လျှောက် မှန်ကန်ကြောင်း အတည်ပြုခြင်းကို ပြုလုပ်သင့်သည်။
Injection Molding တွင် Prototyping ၏ အခန်းကဏ္ဍ
ပုံတူရိုက်ခြင်းသည် ဆေးထိုးပုံသွင်းခြင်းလောကတွင် အရေးပါသောအခန်းကဏ္ဍမှ ပါဝင်ပါသည်။ ထုတ်လုပ်မှုတွင် ဒီဇိုင်နာများနှင့် အင်ဂျင်နီယာများအား ၎င်းတို့၏ ဒီဇိုင်းများကို ပြုပြင်ရန်၊ စမ်းသပ်လုပ်ဆောင်နိုင်စွမ်းနှင့် အတိုင်းအတာအပြည့်ထုတ်လုပ်မှုကို ရှေ့မတိုးမီ အလားအလာရှိသော ပြဿနာများကို ရှာဖွေဖော်ထုတ်နိုင်စေမည့် ထုတ်လုပ်မှုတွင် အရေးကြီးသော ခြေလှမ်းတစ်ခုဖြစ်သည်။ ဤတွင်၊ ဆေးထိုးပုံသွင်းခြင်းတွင် ပုံတူရိုက်ခြင်း၏ အရေးပါပုံနှင့် ၎င်း၏မြောက်မြားစွာသော အကျိုးကျေးဇူးများကို လေ့လာပါမည်။
ဒီဇိုင်းအတည်ပြုချက်-
ပုံတူရိုက်ခြင်းသည် ဒီဇိုင်နာများအား ၎င်းတို့၏ ထုတ်ကုန်ဒီဇိုင်းများကို အတည်ပြုနိုင်ပြီး လက်တွေ့ကမ္ဘာတွင် ၎င်းတို့၏ ဖြစ်နိုင်ခြေကို အကဲဖြတ်ရန် ကူညီပေးသည်။ ရုပ်ပိုင်းဆိုင်ရာ ရှေ့ပြေးပုံစံကို ဖန်တီးခြင်းဖြင့်၊ ဒီဇိုင်နာများသည် အစိတ်အပိုင်း ဂျီသြမေတြီ၊ အံဝင်ခွင်ကျနှင့် တပ်ဆင်ခြင်းကဲ့သို့သော အကြောင်းရင်းများကို အကဲဖြတ်နိုင်သည်။ ၎င်းသည် ဒီဇိုင်းချို့ယွင်းချက်များကို ခွဲခြားသတ်မှတ်ရန် ကူညီပေးပြီး နောက်ဆုံးထုတ်ကုန်သည် လိုချင်သောသတ်မှတ်ချက်များနှင့် ကိုက်ညီပြီး ရည်ရွယ်ထားသည့်အတိုင်း လုပ်ဆောင်နိုင်စေရန် ကူညီပေးသည်။
ထပ်ခါထပ်ခါ တိုးတက်မှု-
ပုံတူပုံစံပြုလုပ်ခြင်းသည် ထုတ်ကုန်ဖွံ့ဖြိုးတိုးတက်မှုစက်ဝန်းတစ်လျှောက် ထပ်ခါထပ်ခါ တိုးတက်မှုများကို ခွင့်ပြုပေးသည်။ ရှေ့ပြေးပုံစံများစွာကို ဖန်တီးပြီး ၎င်းတို့ကို စမ်းသပ်ခြင်းဖြင့်၊ ဒီဇိုင်နာများသည် အဖိုးတန်သော အကြံပြုချက်များကို စုဆောင်းနိုင်ပြီး လိုအပ်သော ပြုပြင်ပြောင်းလဲမှုများကို ပြုလုပ်နိုင်သည်။ ဤထပ်တလဲလဲလုပ်ငန်းစဉ်သည် ဒီဇိုင်းကို သန့်စင်အောင်၊ လုပ်ဆောင်နိုင်စွမ်းကို ပိုကောင်းအောင် ကူညီပေးပြီး နောက်ဆုံးထုတ်ကုန်၏ အလုံးစုံစွမ်းဆောင်ရည်ကို မြှင့်တင်ပေးပါသည်။
ကုန်ကျစရိတ်နှင့် အချိန်ကုန်သက်သာခြင်း-
ပုံတူရိုက်နေစဉ်အတွင်း ဒီဇိုင်းချို့ယွင်းချက်များ သို့မဟုတ် လုပ်ဆောင်နိုင်စွမ်းဆိုင်ရာ ပြဿနာများကို ဖော်ထုတ်ခြင်းသည် အစုလိုက်အပြုံလိုက် ထုတ်လုပ်မှုအတွင်း ၎င်းတို့ကို ရှာဖွေတွေ့ရှိခြင်းထက် ကုန်ကျစရိတ် ပိုမိုထိရောက်ပြီး အချိန်ကုန်သက်သာသည်။ ဒီဇိုင်းအပြောင်းအလဲများကို စောစီးစွာပြုလုပ်ခြင်းသည် စျေးကြီးသော ပြန်လည်တူးဆွခြင်းအတွက် လိုအပ်ချက်များကို လျော့နည်းစေပြီး ထုတ်လုပ်မှုနှောင့်နှေးမှုအန္တရာယ်ကို လျော့နည်းစေသည်။ ပုံတူရိုက်ခြင်းသည် စျေးကြီးသောကိရိယာများနှင့် ထုတ်လုပ်ရေးလုပ်ငန်းစဉ်များကို မလုပ်ဆောင်မီ ထိရောက်သောပြဿနာဖြေရှင်းခြင်းနှင့် ပိုမိုကောင်းမွန်အောင်ပြုလုပ်ခြင်းကို ခွင့်ပြုပေးပါသည်။
ပစ္စည်းရွေးချယ်မှု -
ပုံတူရိုက်ခြင်းသည် ဆေးထိုးပုံသွင်းခြင်းအတွက် သင့်လျော်သောပစ္စည်းများကို ရွေးချယ်ရာတွင် လွယ်ကူစေသည်။ မတူညီသောပစ္စည်းများကို စမ်းသပ်ခြင်းဖြင့်၊ အင်ဂျင်နီယာများသည် ခွန်အား၊ ပြောင်းလွယ်ပြင်လွယ်နှင့် အပူခံနိုင်ရည် အပါအဝင် ၎င်းတို့၏ ဂုဏ်သတ္တိများကို အကဲဖြတ်နိုင်ပြီး အလိုရှိသော လျှောက်လွှာအတွက် အသင့်တော်ဆုံး ပစ္စည်းကို ရွေးချယ်နိုင်သည်။ ထိုသို့လုပ်ဆောင်ခြင်းဖြင့် ရလဒ်သည် စွမ်းဆောင်ရည်နှင့် တာရှည်ခံမှုအတွက် လိုအပ်သောစံနှုန်းများနှင့် ကိုက်ညီကြောင်း ကျွန်ုပ်တို့အာမခံပါသည်။
ထုတ်လုပ်မှု လုပ်ငန်းစဉ်ကို အတည်ပြုခြင်း-
ရှေ့ပြေးပုံစံများသည် ရွေးချယ်ထားသော ကုန်ထုတ်လုပ်မှုလုပ်ငန်းစဉ်၏ ဖြစ်နိုင်ခြေနှင့် ထိရောက်မှုကို အတည်ပြုရန် နည်းလမ်းတစ်ခုအဖြစ် လုပ်ဆောင်သည်။ အစုလိုက်အပြုံလိုက် ထုတ်လုပ်မှုအတွက် ရည်ရွယ်သည့် တူညီသောပစ္စည်းများနှင့် နည်းလမ်းများကို အသုံးပြု၍ ရှေ့ပြေးပုံစံများကို ထုတ်လုပ်ခြင်းဖြင့် အင်ဂျင်နီယာများသည် စိန်ခေါ်မှုများ သို့မဟုတ် ကန့်သတ်ချက်များကို အစောပိုင်းတွင် ရှာဖွေဖော်ထုတ်နိုင်ပါသည်။ ဤအတည်ပြုခြင်းလုပ်ငန်းစဉ်သည် ထုတ်လုပ်မှုကို ချောမွေ့စေပြီး ချို့ယွင်းချက်များကို လျှော့ချရန်နှင့် နောက်ဆုံးထုတ်ကုန်တွင် တသမတ်တည်း အရည်အသွေးရှိစေရန် ကူညီပေးသည်။
ဆက်သွယ်ရေးနှင့် Stakeholder Engagement-
ရှေ့ပြေးပုံစံများသည် ထုတ်ကုန်စိတ်ကူးတစ်ခု၏ မြင်သာထင်သာရှိသော ကိုယ်စားပြုမှုများဖြစ်ပြီး ထိရောက်သောဆက်သွယ်မှုနှင့် အစုရှယ်ယာရှင်များ၏ ထိတွေ့ဆက်ဆံမှုကို လွယ်ကူချောမွေ့စေပါသည်။ ဒီဇိုင်းအယူအဆကို သုံးစွဲသူများထံ တင်ပြခြင်း သို့မဟုတ် အဆုံးအသုံးပြုသူများထံမှ အကြံပြုချက်များကို စုဆောင်းခြင်းဖြစ်စေ၊ ရှေ့ပြေးပုံစံများသည် ထုတ်ကုန်ကို မြင်သာစေရန်၊ ထည့်သွင်းမှုပေးရန်နှင့် အသိဉာဏ်ဖြင့် ဆုံးဖြတ်ချက်များချရန် လူတိုင်းအတွက် ပိုမိုလွယ်ကူစေသည်။ ပိုမိုကောင်းမွန်သောပူးပေါင်းဆောင်ရွက်မှုသည် နားလည်မှုလွဲမှားမှုနည်းပါးစေပြီး အလုံးစုံကျေနပ်မှုကိုဖြစ်စေသည်။
Injection Molding လုပ်ငန်းစဉ်တွင် အရေးကြီးသော အဆင့်များ
ဤဘလော့ဂ်ပို့စ်တွင် ဆေးထိုးပုံသွင်းခြင်းလုပ်ငန်းစဉ်တွင် အရေးကြီးသောအဆင့်များကို ဆွေးနွေးပါမည်။
အဆင့် 1- ပစ္စည်းရွေးချယ်မှု
ဆေးထိုးပုံသွင်းခြင်းလုပ်ငန်းစဉ်၏ ပထမအဆင့်မှာ ပစ္စည်းရွေးချယ်ခြင်း ဖြစ်သည်။
မတူညီသောပလပ်စတစ်ပစ္စည်းများတွင် ခိုင်ခံ့မှု၊ ပြောင်းလွယ်ပြင်လွယ်နှင့် ဓာတုဗေဒခံနိုင်ရည်စသည့် ထူးခြားသောဂုဏ်သတ္တိများရှိသည်။
ပစ္စည်းရွေးချယ်မှုသည် အစိတ်အပိုင်း၏ သီးခြားလိုအပ်ချက်များနှင့် ၎င်း၏ ရည်ရွယ်အသုံးပြုမှုအပေါ် မူတည်မည်ဖြစ်သည်။
အဆင့် 2: Pellet ပြင်ဆင်မှု
ပလတ်စတစ်အမှုန့်များကို လိုအပ်သော သတ်မှတ်ချက်များအတိုင်း အခြောက်ခံပြီး ရောစပ်ခြင်းဖြင့် ပြင်ဆင်ပါသည်။
ဤအဆင့်သည် ပလတ်စတစ်သည် နောက်ဆုံးထုတ်ကုန်၏ အရည်အသွေးကို ထိခိုက်စေနိုင်သည့် အစိုဓာတ်နှင့် ညစ်ညမ်းမှုကင်းကြောင်း သေချာစေရန်အတွက် မရှိမဖြစ်လိုအပ်ပါသည်။
အဆင့် 3: ပလပ်စတစ်အရည်ပျော်
ထို့နောက် ပလပ်စတစ်အမှုန့်များကို ဆေးထိုးစက်တွင် အရည်ပျော်သည်။
အရည်ပျော်မှုဖြစ်စဉ်၏ အပူချိန်နှင့် ဖိအားသည် အသုံးပြုထားသော ပလတ်စတစ်ပစ္စည်းအမျိုးအစားပေါ် မူတည်ပါသည်။
အဆင့် 4: ထိုးဆေး
ထို့နောက် အရည်ကျိုထားသော ပလပ်စတစ်ကို မှိုထဲသို့ ထိုးသွင်းပါ။
မှိုကို များသောအားဖြင့် သံမဏိဖြင့် ပြုလုပ်ထားပြီး နောက်ဆုံးထုတ်ကုန်၏ အလိုရှိသော ပုံသဏ္ဍာန်ကို ဖန်တီးထားသည်။
အဆင့် 5: အအေးခံခြင်းနှင့် ခိုင်မာစေခြင်း။
ပလပ်စတစ်ကို မှိုထဲသို့ ထိုးသွင်းပြီးနောက်၊ ၎င်းသည် အေးပြီး လိုချင်သောပုံစံသို့ ခိုင်မာသွားပါသည်။
အအေးခံချိန်သည် အစိတ်အပိုင်း၏ အထူနှင့် ရှုပ်ထွေးမှုပေါ် မူတည်ပါသည်။
အဆင့် 6- ထုတ်ပယ်ခြင်း။
ပလပ်စတစ်အအေးခံပြီး ခိုင်မာသွားသည်နှင့်၊ မှိုပွင့်လာပြီး အပိုင်းကို ထုတ်ပစ်လိုက်သည်။
အချို့ကိစ္စများတွင် မှိုမှ အစိတ်အပိုင်းကို ဖယ်ရှားရာတွင် ကူညီရန်အတွက် ejector pin များကို အသုံးပြုသည်။
အဆင့် 7- ဖြတ်တောက်ခြင်းနှင့် အပြီးသတ်ခြင်း။
အစိတ်အပိုင်းကို ပုံစံခွက်မှ ထုတ်လွှတ်ပြီးနောက်၊ ပိုလျှံနေသော အရာများကို ဖယ်ရှားပြီး အစွန်းများကို ချောမွေ့စေရန် နောက်ထပ် ဖြတ်တောက်ခြင်းနှင့် အပြီးသတ်ခြင်းများ လိုအပ်နိုင်သည်။
အဆင့် 8: အရည်အသွေးထိန်းချုပ်မှု
အရည်အသွေးထိန်းချုပ်မှုသည် ဆေးထိုးခြင်းလုပ်ငန်းစဉ်တွင် မရှိမဖြစ်လိုအပ်သော အဆင့်တစ်ခုဖြစ်သည်။
နောက်ဆုံးထုတ်ကုန်ကို အရောင်ကွဲခြင်း၊ ကွဲအက်ခြင်း သို့မဟုတ် အရောင်ကွဲခြင်းကဲ့သို့သော ချို့ယွင်းချက်များ ရှိမရှိ စစ်ဆေးထားပါသည်။
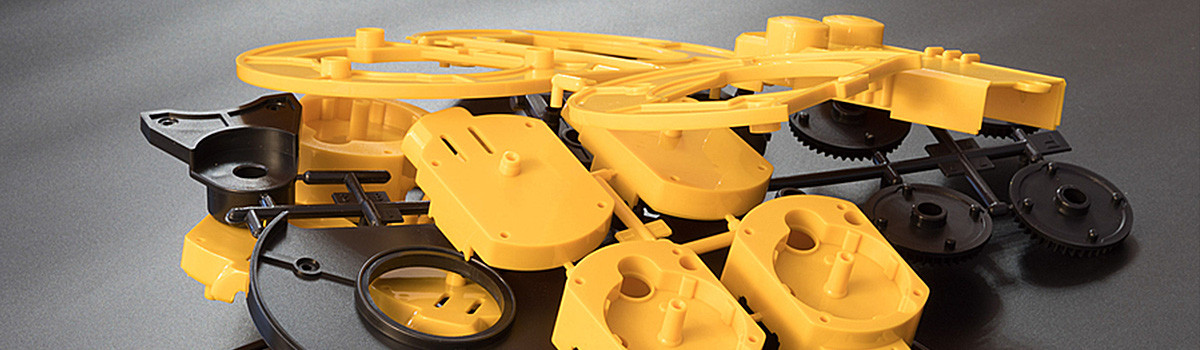
ပလပ်စတစ် အစိတ်အပိုင်းများ၏ ခိုင်ခံ့မှုနှင့် တာရှည်ခံမှုကို မြှင့်တင်ရန် နည်းပညာများ
သို့ရာတွင်၊ အထူးသဖြင့် မြင့်မားသောစိတ်ဖိစီးမှု သို့မဟုတ် ကြမ်းတမ်းသောပတ်ဝန်းကျင်အခြေအနေများနှင့် ထိတွေ့သောအခါတွင် ၎င်းတို့သည် ခိုင်ခံ့မှုနှင့် တာရှည်ခံမှုဆိုင်ရာ စိန်ခေါ်မှုများကို ရင်ဆိုင်ရလေ့ရှိသည်။ ဤဘလော့ဂ်ပို့စ်တွင်၊ ပလပ်စတစ်အစိတ်အပိုင်းများ၏ ခိုင်ခံ့မှုနှင့် တာရှည်ခံမှုကို မြှင့်တင်ရန်အတွက် နည်းပညာအချို့ကို ဆွေးနွေးပါမည်။
ဖြည့်စွက်ပစ္စည်းများဖြင့် အားဖြည့်ပေးခြင်း
- ဖြည့်စွက်ပစ္စည်းများသည် အမျှင်များ၊ ဖြည့်စွက်စာများ၊ သို့မဟုတ် နာနိုအမှုန်များဖြင့် အားဖြည့်ခြင်းဖြင့် ပလတ်စတစ်အစိတ်အပိုင်းများ၏ ခိုင်ခံ့မှုနှင့် တာရှည်ခံမှုကို တိုးတက်စေနိုင်သည်။
- ဖန်မျှင်များ၊ ကာဗွန်ဖိုင်ဘာများ၊ ဆီလီကာ၊ talc နှင့် ရွှံ့စေးတို့ ပါဝင်ပါသည်။
အခြားပစ္စည်းများနှင့်ရောစပ်ပါ။
- ရော်ဘာ သို့မဟုတ် အီလက်စတိုမာများကဲ့သို့သော အခြားပစ္စည်းများနှင့် ပလတ်စတစ်များကို ရောစပ်ခြင်းဖြင့် ၎င်းတို့၏ ခိုင်ခံ့မှုနှင့် တာရှည်ခံမှုကို တိုးမြှင့်ပေးနိုင်သည်။
- ဥပမာအားဖြင့်၊ polypropylene တွင် ရော်ဘာအနည်းငယ်ထည့်ခြင်းဖြင့် ၎င်း၏သက်ရောက်မှုခံနိုင်ရည်ကို တိုးတက်စေနိုင်သည်။
အပူကုသမှု
- အပူကုသမှုသည် အချို့သော ပလတ်စတစ်အစိတ်အပိုင်းများ၏ ခိုင်ခံ့မှုနှင့် တာရှည်ခံမှုကို တိုးမြှင့်ပေးနိုင်သည်။
- ၎င်းတွင် ပလတ်စတစ်ကို ၎င်း၏ ဓာတုနှင့် ရုပ်ပိုင်းဆိုင်ရာ ဂုဏ်သတ္တိများ ပြောင်းလဲစေရန် မြင့်မားသော အပူချိန်နှင့် ထိတွေ့ခြင်း ပါဝင်သည်။
Annealing
- Annealing သည် ပလပ်စတစ်ကို သတ်မှတ်ထားသော အပူချိန်တစ်ခုသို့ အပူပေးပြီး ဖြည်းညှင်းစွာ အအေးပေးခြင်း ပါဝင်သည်။
- ဤနည်းပညာသည် ပလပ်စတစ်အတွင်း အတွင်းပိုင်းဖိစီးမှုများကို လျှော့ချနိုင်ပြီး ၎င်း၏ကြံ့ခိုင်မှုနှင့် တာရှည်ခံမှုကို တိုးတက်စေသည်။
ဆေးထိုးခြင်း လုပ်ငန်းစဉ်ကို ပိုမိုကောင်းမွန်အောင် ပြုလုပ်ခြင်း။
- ဆေးထိုးပုံသွင်းခြင်းလုပ်ငန်းစဉ်ကို ကောင်းမွန်အောင်ပြုလုပ်ခြင်းက ပလပ်စတစ်အစိတ်အပိုင်းများ၏ ခိုင်ခံ့မှုနှင့် တာရှည်ခံမှုကို တိုးမြှင့်ပေးနိုင်သည်။
- ၎င်းတွင် ပုံသွင်းနေစဉ်အတွင်း အပူချိန်၊ ဖိအားနှင့် အအေးခံနှုန်းကို ထိန်းချုပ်ခြင်း ပါဝင်သည်။
မျက်နှာပြင်ကုသမှု
- ကိုရိုနာ၊ ပလာစမာ (သို့) မီးတောက်ကုသခြင်းကဲ့သို့ မျက်နှာပြင် ကုသမှုနည်းပညာများသည် ပလပ်စတစ်နှင့် အခြားပစ္စည်းများကြားတွင် ကပ်တွယ်မှုကို ပိုမိုကောင်းမွန်စေနိုင်သည်။
- ချည်နှောင်ခြင်းသည် အရေးကြီးသော အသုံးချပလပ်စတစ် အစိတ်အပိုင်းများ၏ ခိုင်ခံ့မှုနှင့် တာရှည်ခံမှုကို တိုးမြှင့်ပေးနိုင်သည်။
ကုတ်အင်္ကျီများ
- ထပ်လောင်းအကာအကွယ်အလွှာပေးခြင်းဖြင့် ပလပ်စတစ်အစိတ်အပိုင်းများ၏ ခိုင်ခံ့မှုနှင့် တာရှည်ခံမှုကို မြှင့်တင်ပေးနိုင်သည်။
- ဥပမာအားဖြင့်၊ ကြမ်းတမ်းသောပတ်ဝန်းကျင်တွင် ပလပ်စတစ်အစိတ်အပိုင်းများ ပျက်စီးခြင်းမှ ချေးခံနိုင်ရည်ရှိသော coating သည် ကာကွယ်နိုင်သည်။
မော်တော်ယာဥ် ထိုးဆေးထိုးခြင်းတွင် အရည်အသွေးထိန်းချုပ်မှု အတိုင်းအတာများ
မော်တော်ကားဆေးထိုးပုံသွင်းခြင်းသည် အရည်အသွေးမြင့် မော်တော်ကားအစိတ်အပိုင်းများ ထုတ်လုပ်မှုအတွက် အရေးကြီးသော လုပ်ငန်းစဉ်တစ်ခုဖြစ်သည်။ လုပ်ငန်းစဉ်တွင် တင်းကျပ်သော အရည်အသွေးနှင့် စွမ်းဆောင်ရည် စံချိန်စံညွှန်းများနှင့် ကိုက်ညီသော အစိတ်အပိုင်းများ ထုတ်လုပ်ရန် အထူးပြု စက်များနှင့် မှိုများကို အသုံးပြုခြင်း ပါဝင်သည်။ ဤလုပ်ငန်းစဉ်မှတစ်ဆင့် ပြုလုပ်သော မော်တော်ယာဥ်အစိတ်အပိုင်းများသည် ဤစံနှုန်းများနှင့်ကိုက်ညီကြောင်း အမြဲမပြတ်သေချာစေရန် အရည်အသွေးထိန်းချုပ်မှုအစီအမံများ လိုအပ်ပါသည်။ မော်တော်ယာဥ်ဆေးထိုးပုံသွင်းခြင်းတွင် လုပ်ဆောင်သည့် အရေးကြီးသော အရည်အသွေးထိန်းချုပ်မှုအစီအမံအချို့မှာ အောက်ပါအတိုင်းဖြစ်သည်။
ပစ္စည်းစစ်ဆေးခြင်း- အရည်အသွေးထိန်းချုပ်မှုတွင် ပထမအဆင့်မှာ ပစ္စည်းစစ်ဆေးခြင်း ဖြစ်သည်။ ကုန်ကြမ်းများသည် လိုအပ်သော သတ်မှတ်ချက်များနှင့် ပြည့်မီကြောင်း သေချာစေရန် စစ်ဆေးပါသည်။ ၎င်းတွင် ပစ္စည်းပါဝင်မှု၊ သန့်ရှင်းမှုနှင့် ညီညွတ်မှုကို စစ်ဆေးခြင်း ပါဝင်သည်။
ပုံသွင်းခြင်းလုပ်ငန်းကို စောင့်ကြည့်လေ့လာခြင်း- ပုံသွင်းခြင်းလုပ်ငန်းစဉ်ကို လိုအပ်သော သတ်မှတ်ချက်များအတွင်း အစိတ်အပိုင်းများ ထုတ်လုပ်ကြောင်း သေချာစေရန်အတွက် စဉ်ဆက်မပြတ် စောင့်ကြည့်နေပါသည်။ ၎င်းတွင် အသုံးပြုထားသော ပစ္စည်းများ၏ အပူချိန်၊ ဖိအားနှင့် စီးဆင်းမှုနှုန်းတို့ကို စောင့်ကြည့်ခြင်း ပါဝင်သည်။
အပိုင်းစစ်ဆေးခြင်း- လိုအပ်သောစံချိန်စံညွှန်းများပြည့်မီရန် အစိတ်အပိုင်းများကို ထုတ်လုပ်မှုအပြီးတွင် စစ်ဆေးသည်။ ၎င်းတွင် warping၊ sink marks နှင့် flashing ကဲ့သို့သော ချို့ယွင်းချက်များကို စစ်ဆေးခြင်း ပါဝင်သည်။
စာရင်းအင်းဆိုင်ရာ လုပ်ငန်းစဉ်ထိန်းချုပ်မှု (SPC)- SPC သည် ထုတ်လုပ်မှုလုပ်ငန်းစဉ်ကို စောင့်ကြည့်ထိန်းချုပ်သည့် ကိန်းဂဏန်းဆိုင်ရာကိရိယာတစ်ခုဖြစ်သည်။ ၎င်းတွင် ဒေတာခွဲခြမ်းစိတ်ဖြာရန်နှင့် လုပ်ငန်းစဉ်နှင့် ဖြစ်နိုင်ခြေရှိသော ပြဿနာများကို ညွှန်ပြသည့် လမ်းကြောင်းများ သို့မဟုတ် ပုံစံများကို ခွဲခြားသတ်မှတ်ရန် ကိန်းဂဏန်းနည်းပညာများကို အသုံးပြုခြင်း ပါဝင်သည်။
အရည်အသွေးအာမခံ (QA)- QA သည် နောက်ဆုံးထုတ်ကုန်သည် လိုအပ်သော အရည်အသွေးစံချိန်စံညွှန်းများနှင့် ကိုက်ညီကြောင်း သေချာစေရန် လုပ်ထုံးလုပ်နည်းများနှင့် လမ်းညွှန်ချက်များကို အသုံးပြုခြင်း ပါဝင်သည်။ ၎င်းတွင် လိုအပ်သော သတ်မှတ်ချက်များနှင့် ပြည့်မီကြောင်း သေချာစေရန်အတွက် ကုန်ချောကို စစ်ဆေးခြင်းနှင့် စမ်းသပ်ခြင်းများ ပါဝင်သည်။
ခြေရာခံနိုင်မှု - Traceability သည် ထုတ်ကုန်တစ်ခုအား ၎င်း၏အရင်းအမြစ်သို့ ပြန်လည်ခြေရာခံနိုင်မှုဖြစ်သည်။ မော်တော်ယာဥ် ဆေးထိုးပုံသွင်းခြင်းတွင် ချို့ယွင်းချက် သို့မဟုတ် အရည်အသွေးပြဿနာများကို ၎င်းတို့၏အရင်းအမြစ်သို့ ပြန်၍ခြေရာခံပြီး ပြုပြင်နိုင်ကြောင်း သေချာစေရန် ခြေရာခံနိုင်မှုသည် အရေးကြီးပါသည်။
စဉ်ဆက်မပြတ်တိုးတက်မှု: စဉ်ဆက်မပြတ် တိုးတက်မှုသည် ထုတ်ကုန်အရည်အသွေး မြှင့်တင်ရန် တိုးတက်မှုအတွက် နယ်ပယ်များကို ဖော်ထုတ်ခြင်းနှင့် အပြောင်းအလဲများကို အကောင်အထည်ဖော်ရာတွင် ပါဝင်သည့် ဆက်လက်လုပ်ဆောင်နေသည့် လုပ်ငန်းစဉ်တစ်ခုဖြစ်သည်။ ၎င်းတွင် ဒေတာကို ပိုင်းခြားစိတ်ဖြာခြင်း၊ ခေတ်ရေစီးကြောင်းများကို ခွဲခြားသတ်မှတ်ခြင်းနှင့် ထုတ်ကုန်အရည်အသွေးနှင့် လိုက်လျောညီထွေရှိမှုတို့ကို မြှင့်တင်ရန် လုပ်ငန်းစဉ်ဆိုင်ရာ ပြောင်းလဲမှုများကို အကောင်အထည်ဖော်ခြင်းတို့ ပါဝင်သည်။
ကုန်ကျစရိတ်ခွဲခြမ်းစိတ်ဖြာခြင်း- ဆေးထိုးပုံသွင်းခြင်းနှင့် ရိုးရာကုန်ထုတ်လုပ်မှုနည်းလမ်းများ
ထုတ်လုပ်မှုလုပ်ငန်းတွင် ကုန်ကျစရိတ်ခွဲခြမ်းစိတ်ဖြာခြင်းသည် ဆုံးဖြတ်ချက်ချခြင်း၏ အရေးကြီးသောကဏ္ဍတစ်ခုဖြစ်သည်။ ထုတ်လုပ်သူများသည် ကုန်ကျစရိတ်အသက်သာဆုံးနည်းလမ်းကို ဆုံးဖြတ်ရန် မတူညီသောနည်းလမ်းများကို အသုံးပြု၍ ၎င်းတို့၏ထုတ်ကုန်များထုတ်လုပ်ခြင်း၏ကုန်ကျစရိတ်ကို အကဲဖြတ်ရပါမည်။ ဆေးထိုးပုံသွင်းခြင်းနှင့် ရိုးရာကုန်ထုတ်ခြင်းနည်းလမ်းနှစ်မျိုးကို အသုံးများပြီး ထုတ်လုပ်သူများသည် ၎င်းတို့၏ထုတ်ကုန်များအတွက် ကုန်ကျစရိတ်အသက်သာဆုံးနည်းလမ်းကို ဆုံးဖြတ်ရမည်ဖြစ်သည်။ ဤသည်မှာ ဆေးထိုးပုံသွင်းခြင်း၏ ကုန်ကျစရိတ်နှင့် ရိုးရာကုန်ထုတ်လုပ်မှုနည်းလမ်းများဖြစ်သည်။
ဆေးထိုးပုံသွင်းခြင်း-
Injection molding သည် အစိတ်အပိုင်းများထုတ်လုပ်ရန်အတွက် မှိုထဲသို့ သွန်းသောပလပ်စတစ်ကို ထိုးသွင်းခြင်းပါဝင်သည့် ထုတ်လုပ်မှုနည်းလမ်းတစ်ခုဖြစ်သည်။ ဆေးထိုးခြင်း၏ အားသာချက်များနှင့် အားနည်းချက်အချို့မှာ အောက်ပါအတိုင်းဖြစ်သည်။
အားသာချက်များ:
- မြင့်မားသောထုတ်လုပ်မှုပမာဏ-ဆေးထိုးပုံသွင်းခြင်းသည် တူညီသော အစိတ်အပိုင်းများ မြင့်မားသော စာအုပ်များကို ထုတ်လုပ်ရန်အတွက် စံပြဖြစ်သည်။
- လုပ်အားခ သက်သာသည်-ဆေးထိုးခြင်းလုပ်ငန်းသည် သမားရိုးကျကုန်ထုတ်နည်းလမ်းများနှင့် နှိုင်းယှဉ်ပါက လုပ်သားအနည်းငယ်သာ လိုအပ်ပါသည်။
- ရှေ့နောက်ညီညွတ်မှု: ထိုးသွင်းပုံသွင်းခြင်းသည် လိုက်ဖက်ညီသော အစိတ်အပိုင်းများကို တစ်ခုနှင့်တစ်ခု တူညီစေသည်။
- အောက်ပိုင်း စွန့်ပစ်ပစ္စည်း ဆေးထိုးပုံသွင်းခြင်းတွင် သမားရိုးကျကုန်ထုတ်နည်းများထက် စွန့်ပစ်ပစ္စည်း နည်းပါးသည်။
အားနည်းချက်:
- ပိုမိုမြင့်မားသောကြိုတင်ကုန်ကျစရိတ်-ဆေးထိုးပုံသွင်းခြင်းအတွက် ကုန်ကျစရိတ်သည် သမားရိုးကျကုန်ထုတ်နည်းလမ်းများနှင့် နှိုင်းယှဉ်ပါက ပိုမိုမြင့်မားသည်။
- ကန့်သတ်ပြောင်းလွယ်ပြင်လွယ်- ဆေးထိုးပုံသွင်းခြင်းသည် သမားရိုးကျကုန်ထုတ်လုပ်မှုနည်းလမ်းများထက် ပျော့ပြောင်းမှုနည်းသောကြောင့် စိတ်ကြိုက်အစိတ်အပိုင်းများထုတ်လုပ်ရန်အတွက် စံနမူနာနည်းသည်။
ရိုးရာကုန်ထုတ်လုပ်မှုနည်းလမ်းများ
သမားရိုးကျ ကုန်ထုတ်နည်းများသည် ဆယ်စုနှစ်များစွာ အသုံးပြုခဲ့သည့် သမားရိုးကျ ကုန်ထုတ်လုပ်မှုနည်းပညာများကို ရည်ညွှန်းသည်။ ဤနည်းလမ်းများတွင် ကြိတ်ခွဲခြင်း၊ တူးဖော်ခြင်းနှင့် လှည့်ခြင်းများ ပါဝင်သည်။ ဤသည်မှာ ရိုးရာကုန်ထုတ်နည်းများ၏ အားသာချက်များနှင့် အားနည်းချက်အချို့ဖြစ်သည်။
အားသာချက်များ:
- သက်သာသော၊ ကြိုတင်ကုန်ကျစရိတ်-သမားရိုးကျ ကုန်ထုတ်လုပ်မှုနည်းလမ်းများသည် ကုန်ကျစရိတ်အနည်းငယ်သာ လိုအပ်ပြီး ၎င်းတို့ကို အစိတ်အပိုင်းများ ပမာဏနည်းပါးစွာ ထုတ်လုပ်ရန်အတွက် စံပြဖြစ်စေပါသည်။
- ပြောင်းလွယ်ပြင်လွယ်:သမားရိုးကျကုန်ထုတ်လုပ်မှုနည်းလမ်းများသည် ဆေးထိုးပုံသွင်းခြင်းထက် ပိုမိုပြောင်းလွယ်ပြင်လွယ်ဖြစ်ပြီး ၎င်းတို့ကို စိတ်ကြိုက်အစိတ်အပိုင်းများထုတ်လုပ်ရန်အတွက် စံပြဖြစ်စေပါသည်။
- ကိရိယာတန်ဆာပလာ ကုန်ကျစရိတ် သက်သာသည်-သမားရိုးကျ ထုတ်လုပ်မှုနည်းလမ်းများသည် ဆေးထိုးခြင်းထက် ကိရိယာတန်ဆာပလာများ သက်သာရန် လိုအပ်သည်။
အားနည်းချက်:
- မြင့်မားသောအလုပ်သမားကုန်ကျစရိတ်သမားရိုးကျ ကုန်ထုတ်နည်းများသည် ဆေးထိုးခြင်းထက် လုပ်သားပိုလိုအပ်ပြီး လုပ်သားစရိတ်များ မြင့်မားသည်။
- ပိုမိုမြင့်မားသောပစ္စည်းစွန့်ပစ်:သမားရိုးကျ ကုန်ထုတ်နည်းများသည် ဆေးထိုးခြင်းထက် စွန့်ပစ်ပစ္စည်း ပိုမိုထုတ်လုပ်သည်။
- မကိုက်ညီသော အစိတ်အပိုင်းများ-သမားရိုးကျ ကုန်ထုတ်နည်းများသည် တစ်ခုနှင့်တစ်ခု အနည်းငယ်ကွဲလွဲနိုင်သည့် ပမာဏကို ထုတ်လုပ်သည်။
Injection Molding ၏ ရေရှည်တည်တံ့မှုနှင့် သဘာဝပတ်ဝန်းကျင် ထိခိုက်မှု
ရေရှည်တည်တံ့မှုနှင့် သဘာဝပတ်ဝန်းကျင်ဆိုင်ရာ သက်ရောက်မှုများသည် စီးပွားရေးလုပ်ငန်းများနှင့် ထုတ်လုပ်သူများ ၎င်းတို့၏ ထုတ်လုပ်မှုလုပ်ငန်းစဉ်များတွင် ထည့်သွင်းစဉ်းစားရမည့် အရေးကြီးသောအချက်များဖြစ်သည်။ ရေပန်းစားသော ထုတ်လုပ်မှုနည်းလမ်းတစ်ခုဖြစ်သည့် ဆေးထိုးပုံသွင်းခြင်းသည် အပေါင်းလက္ခဏာဆောင်သော ပတ်ဝန်းကျင်ဆိုင်ရာ သက်ရောက်မှုများရှိသည်။ ဤဘလော့ဂ်ပို့စ်တွင်၊ ဆေးထိုးပုံသွင်းခြင်း၏ ရေရှည်တည်တံ့မှုနှင့် ဂေဟစနစ်ဆိုင်ရာ အကျိုးသက်ရောက်မှုများကို ဆွေးနွေးပါမည်။
သဘာဝပတ်ဝန်းကျင်အားမပျက်စီး:
ရေရှည်တည်တံ့ခိုင်မြဲမှုသည် အနာဂတ်မျိုးဆက်သစ်များ၏ လိုအပ်ချက်များကို ဖြည့်ဆည်းပေးနိုင်စွမ်းကို အလျှော့မပေးဘဲ ပစ္စုပ္ပန်၏ လိုအပ်ချက်များကို ဖြည့်ဆည်းပေးခြင်းကို ရည်ညွှန်းသည်။ ဆေးထိုးပုံသွင်းခြင်းသည် ရေရှည်တည်တံ့ခိုင်မြဲသော အကျိုးကျေးဇူးများစွာရှိသည်။
- ပစ္စည်းထိရောက်မှု-ဆေးထိုးပုံသွင်းခြင်း သည် အစိတ်အပိုင်းများပြုလုပ်ရန် လိုအပ်သောပစ္စည်းကို လျှော့ချပြီး သေးငယ်သော ပစ္စည်းစွန့်ပစ်ပစ္စည်းဖြင့် အစိတ်အပိုင်းများကို ထုတ်လုပ်သည်။
- စွမ်းအင်ထိရောက်မှု-ထိုးသွင်းပုံသွင်းခြင်းသည် စက်နှင့် ပုံသွင်းခြင်းကဲ့သို့သော အခြားကုန်ထုတ်နည်းများထက် အစိတ်အပိုင်းများထုတ်လုပ်ရန် စွမ်းအင်နည်းပါးသည်။
- Long ကသက်တမ်း: ဆေးထိုးပုံသွင်းခြင်းမှ ထုတ်လုပ်သော အစိတ်အပိုင်းများသည် တာရှည်ခံပြီး ကြာရှည်ခံကာ မကြာခဏ အစားထိုးရန် လိုအပ်မှုကို လျှော့ချပေးသည်။
သဘာဝပတ်ဝန်းကျင် ထိခိုက်မှု-
ဆေးထိုးပုံသွင်းခြင်းတွင်လည်း ထည့်သွင်းစဉ်းစားရမည့် သဘာဝပတ်ဝန်းကျင်ဆိုင်ရာ သက်ရောက်မှုများရှိသည်။ ဆေးထိုးပုံသွင်းခြင်း၏ အပြုသဘောဆောင်သော နှင့် အပျက်သဘောဆောင်သော ဂေဟစနစ်ဆိုင်ရာ သက်ရောက်မှုအချို့မှာ အောက်ပါအတိုင်းဖြစ်သည် ။
အပြုသဘောဆောင်သော သဘာဝပတ်ဝန်းကျင်ဆိုင်ရာ သက်ရောက်မှု-
- ပြန်လည်အသုံးပြုခြင်း - ပလတ်စတစ်ကဲ့သို့သော ဆေးထိုးပုံသွင်းပစ္စည်းအများအပြားကို ပြန်လည်အသုံးပြုနိုင်ပြီး အမှိုက်ပုံများဆီသို့ စွန့်ပစ်ပစ္စည်းများကို လျှော့ချနိုင်သည်။
- ကာဗွန်အောက်ခြေ -ထိုးသွင်းပုံသွင်းခြင်းသည် စက်နှင့် ပုံသွင်းခြင်းကဲ့သို့သော အခြားကုန်ထုတ်နည်းလမ်းများထက် ဖန်လုံအိမ်ဓာတ်ငွေ့ထုတ်လွှတ်မှု လျော့နည်းစေသည်။
အနုတ်လက္ခဏာ ပတ်ဝန်းကျင် ထိခိုက်မှု-
- ပြန်လည်ပြည့်ဖြိုးမြဲမဟုတ်သော အရင်းအမြစ်များကို အသုံးပြုခြင်း-ဆေးထိုးခြင်းလုပ်ငန်းသည် ပြန်လည်ပြည့်ဖြိုးမြဲမဟုတ်သော အရင်းအမြစ်များမှရရှိသော ပလပ်စတစ်ကဲ့သို့သော ရေနံအခြေခံပစ္စည်းများကို အသုံးပြုသည်။
- အမှိုက်ထုတ်လုပ်မှုဆေးထိုးပုံသွင်းခြင်းသည် အခြားကုန်ထုတ်နည်းများထက် စွန့်ပစ်ပစ္စည်းနည်းပါးသော်လည်း၊ အမှိုက်နှင့် ထုပ်ပိုးခြင်းကဲ့သို့သော စွန့်ပစ်ပစ္စည်းများကို ထုတ်လုပ်ဆဲဖြစ်သည်။
ဆေးထိုးပုံသွင်းခြင်းတွင် ရေရှည်တည်တံ့သော အလေ့အကျင့်များ
ဆေးထိုးပုံသွင်းခြင်း၏ ဆိုးကျိုးပတ်ဝန်းကျင်ဆိုင်ရာ သက်ရောက်မှုကို လျှော့ချရန်အတွက် ထုတ်လုပ်သူများသည် အောက်ပါကဲ့သို့သော ရေရှည်တည်တံ့သော အလေ့အကျင့်များကို အကောင်အထည်ဖော်နိုင်သည်-
- ပြန်လည်အသုံးပြုသောပစ္စည်းများအသုံးပြုမှု-ထုတ်လုပ်သူများသည် ၎င်းတို့၏ ဆေးထိုးပုံသွင်းခြင်းလုပ်ငန်းစဉ်များတွင် ပြန်လည်အသုံးပြုသည့်ပစ္စည်းများကို အသုံးပြုနိုင်ပြီး အမှိုက်ပုံများဆီသို့ စွန့်ပစ်ပစ္စည်းများကို လျှော့ချနိုင်သည်။
- ပြန်လည်ပြည့်ဖြိုးမြဲစွမ်းအင်အသုံးပြုမှု-ထုတ်လုပ်သူများသည် ၎င်းတို့၏ ဆေးထိုးပုံသွင်းစက်များကို အားဖြည့်ရန်အတွက် ဖန်လုံအိမ်ဓာတ်ငွေ့ထုတ်လွှတ်မှုကို လျှော့ချရန်အတွက် နေရောင်ခြည် သို့မဟုတ် လေစွမ်းအင်ကဲ့သို့သော ပြန်လည်ပြည့်ဖြိုးမြဲစွမ်းအင်ရင်းမြစ်များကို အသုံးပြုနိုင်သည်။
- အမှိုက်လျှော့ချရေး-ထုတ်လုပ်သူများသည် ပြန်သုံးနိုင်သော ထုပ်ပိုးမှုကို အသုံးပြုခြင်းနှင့် စွန့်ပစ်ပစ္စည်း ပမာဏကို လျှော့ချခြင်းကဲ့သို့သော စွန့်ပစ်ပစ္စည်း လျှော့ချရေး အလေ့အကျင့်များကို အကောင်အထည်ဖော်နိုင်သည်။
ထိရောက်မှုအတွက် အလိုအလျောက် ထိုးသွင်းပုံသွင်းခြင်း လုပ်ငန်းစဉ်များ
ကုန်ထုတ်လုပ်ငန်းတွင် ပြိုင်ဆိုင်မှုနှင့် အမြတ်အစွန်းရရှိရန် စွမ်းဆောင်ရည်သည် အရေးကြီးပါသည်။ ဆေးထိုးပုံသွင်းခြင်းသည် မှိုထဲသို့ သွန်းသောပစ္စည်းကို ထိုးသွင်းခြင်းဖြင့် အစိတ်အပိုင်းများထုတ်လုပ်ခြင်းတွင် ပါဝင်သည့် ရေပန်းစားသော ကုန်ထုတ်လုပ်မှုနည်းလမ်းတစ်ခုဖြစ်သည်။ အလိုအလျောက် ဆေးထိုးပုံသွင်းခြင်း လုပ်ငန်းစဉ်များသည် ထိရောက်မှုနှင့် ကုန်ထုတ်စွမ်းအားကို သိသိသာသာ တိုးတက်စေနိုင်သည်။ ဤဘလော့ဂ်ပို့စ်တွင်၊ ထိရောက်မှုအတွက် အလိုအလျောက်ဆေးထိုးခြင်းလုပ်ငန်းစဉ်များ၏ အကျိုးကျေးဇူးများကို ဆွေးနွေးပါမည်။
အလိုအလျောက် ထိုးသွင်းပုံသွင်းခြင်း လုပ်ငန်းစဉ်များ၏ အကျိုးကျေးဇူးများ
ဤသည်မှာ အလိုအလျောက် ဆေးထိုးပုံသွင်းခြင်း လုပ်ငန်းစဉ်များ၏ အကျိုးကျေးဇူးအချို့ဖြစ်သည်။
- အရှိန်မြှင့်သည်-အလိုအလျောက်စနစ်သည် ဆေးထိုးပုံသွင်းခြင်းလုပ်ငန်းစဉ်များကို သိသိသာသာ အရှိန်မြှင့်ပေးနိုင်သည်။ အလိုအလျောက်စက်များသည် manual machines များထက် ပိုမိုမြန်ဆန်သောနှုန်းဖြင့် အစိတ်အပိုင်းများကို ထုတ်လုပ်နိုင်သည်။
- ရှေ့နောက်ညီညွတ်မှု:အလိုအလျောက် ဆေးထိုးပုံသွင်းစက်များသည် အရည်အသွေးနှင့် ယုံကြည်စိတ်ချရမှုကို အာမခံချက် အနည်းငယ်မျှသာ ကွဲပြားမှုဖြင့် တသမတ်တည်း အစိတ်အပိုင်းများကို ထုတ်လုပ်သည်။
- ပိုမိုကောင်းမွန်သော တိကျမှု-အလိုအလျောက်စက်များသည် မြင့်မားသောတိကျမှုနှင့် တိကျမှုရှိပြီး တင်းကျပ်သောသည်းခံနိုင်မှုနှင့် ရှုပ်ထွေးသောဂျီသြမေတြီများဖြင့် အစိတ်အပိုင်းများကို ထုတ်လုပ်ပေးသည်။
- လုပ်အားခ လျှော့ချခြင်း-ဆေးထိုးပုံသွင်းခြင်းလုပ်ငန်းစဉ်များကို အလိုအလျောက်ပြုလုပ်ခြင်းဖြင့် လက်လုပ်လက်စားလိုအပ်မှုကို လျှော့ချနိုင်ပြီး လုပ်သားကုန်ကျစရိတ်ကို လျှော့ချနိုင်သည်။
- ပိုမိုကောင်းမွန်သော ဘေးကင်းရေး-အလိုအလျောက်စက်များသည် လူသားများအတွက် အန္တရာယ်ရှိသော အလုပ်များကို လုပ်ဆောင်နိုင်ပြီး ထုတ်လုပ်မှုပတ်ဝန်းကျင်တွင် ဘေးကင်းစေပါသည်။
- ပစ္စည်း စွန့်ပစ်ပစ္စည်း လျှော့ချခြင်း-အလိုအလျောက် စက်များသည် အစိတ်အပိုင်းများကို စွန့်ပစ်ပစ္စည်း အနည်းဆုံးဖြင့် ထုတ်လုပ်နိုင်ပြီး ပစ္စည်းကုန်ကျစရိတ်နှင့် သဘာဝပတ်ဝန်းကျင် ထိခိုက်မှုကို လျှော့ချနိုင်သည်။
အလိုအလျောက် ထိုးသွင်းပုံသွင်းခြင်း လုပ်ငန်းစဉ်များ-
ဤသည်မှာ ဆေးထိုးပုံသွင်းခြင်းလုပ်ငန်းစဉ်များကို အလိုအလျောက်ဖြစ်စေရန် နည်းလမ်းအချို့ဖြစ်သည်။
- စက်ရုပ်အလိုအလျောက်စနစ်-စက်ရုပ်များသည် အစိတ်အပိုင်းများကို သယ်ဆောင်ခြင်းနှင့် ဖြုတ်ချခြင်း၊ အစိတ်အပိုင်းများကို စစ်ဆေးခြင်းနှင့် ကုန်ချောထုတ်ပိုးခြင်းစသည့် အလုပ်များကို လုပ်ဆောင်နိုင်သည်။ စက်ရုပ်အလိုအလျောက်စနစ်သည် ဆေးထိုးပုံသွင်းခြင်းလုပ်ငန်းစဉ်များ၏ အမြန်နှုန်းနှင့် တိကျမှုကို သိသာထင်ရှားစွာ တိုးမြှင့်နိုင်သည်။
- အလိုအလျောက် ပစ္စည်းကိုင်တွယ်ခြင်း-အလိုအလျောက် ပစ္စည်းများ ကိုင်တွယ်မှုစနစ်များသည် ဆေးထိုးစက်သို့ ပစ္စည်းများ ပို့ဆောင်နိုင်ပြီး လက်လုပ်လက်စား လိုအပ်မှုကို လျှော့ချနိုင်သည်။
- အလိုအလျောက် အရည်အသွေးထိန်းချုပ်မှု-အလိုအလျောက်အရည်အသွေးထိန်းချုပ်မှုစနစ်များသည် ချို့ယွင်းချက်များနှင့် သွေဖည်မှုများအတွက် အစိတ်အပိုင်းများကို စစ်ဆေးနိုင်ပြီး တစ်သမတ်တည်းအရည်အသွေးကို အာမခံကာ လက်ဖြင့်စစ်ဆေးရန် လိုအပ်မှုကို လျှော့ချနိုင်သည်။
- အချိန်နှင့်တပြေးညီစောင့်ကြည့်စစ်ဆေးခြင်း - ဤစနစ်များသည် စက်စွမ်းဆောင်ရည်ကို ခြေရာခံနိုင်ပြီး အချိန်နှင့်တပြေးညီ ပြဿနာများကို ရှာဖွေဖော်ထုတ်နိုင်ပြီး စက်ရပ်ချိန်ကို လျှော့ချကာ စွမ်းဆောင်ရည်ကို မြှင့်တင်ပေးနိုင်သည်။
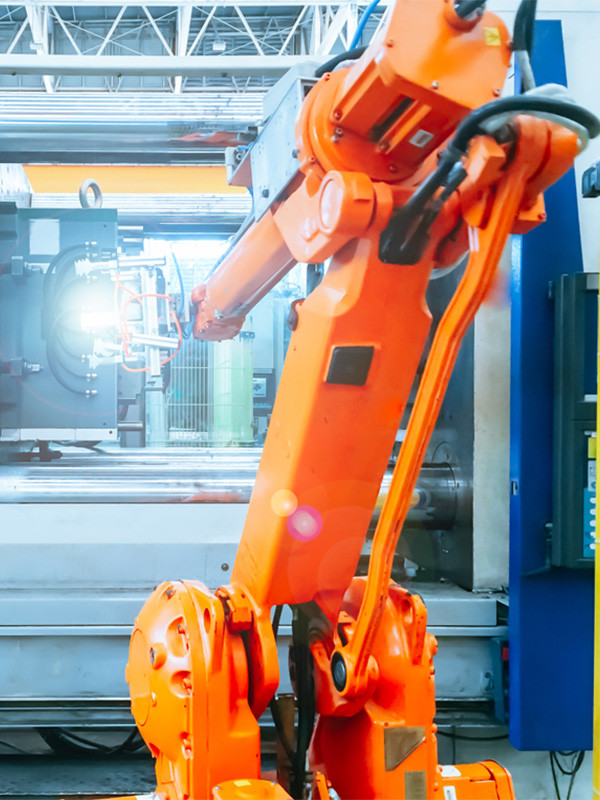
အလိုအလျောက် ထိုးဆေးပုံသွင်းခြင်း လုပ်ငန်းစဉ်များ၏ စိန်ခေါ်မှုများ
အလိုအလျောက် ဆေးထိုးပုံသွင်းခြင်း လုပ်ငန်းစဉ်များသည် များစွာသော အကျိုးကျေးဇူးများ ရှိသော်လည်း၊ ၎င်းသည် စိန်ခေါ်မှုအချို့ကိုလည်း တင်ပြသည်-
- ပိုမိုမြင့်မားသောကြိုတင်ကုန်ကျစရိတ်-စက်ကိရိယာနှင့် အကောင်အထည်ဖော်မှုကုန်ကျစရိတ်ကြောင့် အလိုအလျောက်ဆေးထိုးခြင်းလုပ်ငန်းစဉ်များ စျေးကြီးနိုင်ပါသည်။
- တိုးပွားလာသော ရှုပ်ထွေးမှု-အလိုအလျောက်စနစ်များသည် အထူးပြုလေ့ကျင့်မှုနှင့် ပြုပြင်ထိန်းသိမ်းမှုလိုအပ်သော လက်စွဲစနစ်များထက် ပိုမိုရှုပ်ထွေးပါသည်။
- ပြောင်းလွယ်ပြင်လွယ် လျှော့ချသည်-အလိုအလျောက်စနစ်များသည် လက်စွဲစနစ်များထက် ပျော့ပြောင်းမှုနည်းသောကြောင့် ထုတ်လုပ်မှုလိုအပ်ချက်ပြောင်းလဲမှုများကို လိုက်လျောညီထွေဖြစ်စေရန် စိန်ခေါ်မှုဖြစ်စေသည်။
မော်တော်ကား ပလပ်စတစ် အစိတ်အပိုင်းများ ထိုးသွင်းပုံသွင်းခြင်း၏ စိန်ခေါ်မှုများနှင့် ကန့်သတ်ချက်များ
သို့ရာတွင်၊ မော်တော်ယာဥ်ပလတ်စတစ်အစိတ်အပိုင်းများအတွက် ဆေးထိုးပုံသွင်းခြင်းကို အသုံးပြုသည့်အခါ အချို့သောစိန်ခေါ်မှုများနှင့် ကန့်သတ်ချက်များကို ထည့်သွင်းစဉ်းစားရပါမည်။ ဤဘလော့ဂ်ပို့စ်တွင်၊ မော်တော်ယာဥ်ပလပ်စတစ်အစိတ်အပိုင်းများကို ဆေးထိုးခြင်း၏ စိန်ခေါ်မှုများနှင့် ကန့်သတ်ချက်အချို့ကို ဆွေးနွေးပါမည်။
မော်တော်ကား ပလပ်စတစ် အစိတ်အပိုင်းများ ထိုးသွင်းပုံသွင်းခြင်း၏ စိန်ခေါ်မှုများ
ဤသည်မှာ မော်တော်ယာဥ်ပလပ်စတစ် အစိတ်အပိုင်းများကို ဆေးထိုးခြင်း၏ စိန်ခေါ်မှုအချို့ဖြစ်သည်။
- ပစ္စည်းရွေးချယ်မှု-ဆေးထိုးပုံသွင်းခြင်း မော်တော်ယာဥ်ပလပ်စတစ်အစိတ်အပိုင်းများကို မှန်ကန်သောပစ္စည်းကို ရွေးချယ်ခြင်းသည် စိန်ခေါ်မှုဖြစ်နိုင်သည်။ ပစ္စည်းသည် ခိုင်ခံ့ပြီး တာရှည်ခံကာ ပြင်းထန်သောအပူချိန်နှင့် ကြမ်းတမ်းသောပတ်ဝန်းကျင်အခြေအနေများကို ခံနိုင်ရည်ရှိရပါမည်။
- စက်ပစ္စည်းကုန်ကျစရိတ်-ဆေးထိုးပုံသွင်းခြင်းအတွက် ကိရိယာတန်ဆာပလာကုန်ကျစရိတ်သည် အထူးသဖြင့် ရှုပ်ထွေးရှုပ်ထွေးသော အစိတ်အပိုင်းများအတွက် စျေးကြီးနိုင်သည်။
- အပိုင်းဒီဇိုင်း-ဆေးထိုးပုံသွင်းခြင်းအတွက် အစိတ်အပိုင်းများကို ဒီဇိုင်းထုတ်ရာတွင် ခက်ခဲနိုင်သည်
- အရည်အသွေးထိန်းချုပ်မှု:ဆေးထိုးပုံသွင်းထားသော မော်တော်ယာဥ်ပလပ်စတစ်အစိတ်အပိုင်းများ၏ တစ်သမတ်တည်းအရည်အသွေးနှင့် စွမ်းဆောင်ရည်ကို သေချာစေရန် ပစ္စည်း၊ လုပ်ငန်းစဉ်နှင့် ကိရိယာပုံစံကွဲပြားမှုများကြောင့် စိန်ခေါ်မှုဖြစ်နိုင်သည်။
မော်တော်ကား ပလပ်စတစ် အစိတ်အပိုင်းများ ထိုးသွင်းပုံသွင်းခြင်း၏ ကန့်သတ်ချက်များ
ဤသည်မှာ မော်တော်ယာဥ်ပလပ်စတစ် အစိတ်အပိုင်းများကို ဆေးထိုးခြင်း၏ ကန့်သတ်ချက်အချို့ဖြစ်သည်။
- အရွယ်အစား ကန့်သတ်ချက်များ-ဆေးထိုးပုံသွင်းခြင်းတွင် အရွယ်အစားကန့်သတ်ချက်များရှိပြီး ဆေးထိုးပုံသွင်းခြင်းကို အသုံးပြု၍ ကြီးမားသောမော်တော်ယာဥ်ပလပ်စတစ်အစိတ်အပိုင်းများကို ထုတ်လုပ်ရန် မဖြစ်နိုင်ပါ။
- ထုတ်လုပ်မှုပမာဏ-ဆေးထိုးပုံသွင်းခြင်းသည် ပမာဏမြင့်မားသောထုတ်လုပ်မှုအတွက် အသင့်တော်ဆုံးဖြစ်ပြီး ပမာဏနည်းသောထုတ်လုပ်မှုအတွက် တွက်ချေကိုက်မှုမဖြစ်နိုင်ပါ။
- ရှုပ်ထွေးမှု-ဆေးထိုးပုံသွင်းခြင်းသည် ရှုပ်ထွေးသော ဂျီသြမေတြီများ သို့မဟုတ် ဒီဇိုင်းများစွာရှိသော အစိတ်အပိုင်းများအတွက် မသင့်လျော်ပါ။
- သဘာဝပတ်ဝန်းကျင် ထိခိုက်မှု-ဆေးထိုးပုံသွင်းခြင်းသည် စွန့်ပစ်ပစ္စည်းများကို ထုတ်လုပ်ပြီး ပြန်လည်ပြည့်ဖြိုးမြဲမဟုတ်သော အရင်းအမြစ်များကို အသုံးပြုကာ သဘာဝပတ်ဝန်းကျင်ကို ထိခိုက်နိုင်သည်။
စိန်ခေါ်မှုများနှင့် ကန့်သတ်ချက်များကို ကျော်လွှားခြင်း-
ဤသည်မှာ မော်တော်ကား ပလတ်စတစ် အစိတ်အပိုင်းများ ဆေးထိုးခြင်း၏ စိန်ခေါ်မှုများနှင့် ကန့်သတ်ချက်များကို ကျော်လွှားရန် နည်းလမ်းအချို့ ဖြစ်သည်-
- ပစ္စည်းရွေးချယ်မှု-ဆေးထိုးပုံသွင်းခြင်းအတွက် မှန်ကန်သောပစ္စည်းကိုရွေးချယ်ခြင်းသည် အစိတ်အပိုင်း၏လိုအပ်ချက်များနှင့် စွမ်းဆောင်ရည်ကို ဂရုတစိုက်ထည့်သွင်းစဉ်းစားရန် လိုအပ်သည်။ ထုတ်လုပ်သူသည် အစိတ်အပိုင်း၏ သီးခြားလိုအပ်ချက်များနှင့် ကိုက်ညီသော ပစ္စည်းများကို ရွေးချယ်ရန် ပေးသွင်းသူများနှင့် လက်တွဲနိုင်သည်။
- စက်ပစ္စည်းကုန်ကျစရိတ်-အရည်အသွေးမြင့်ကိရိယာများတွင် ရင်းနှီးမြုပ်နှံခြင်းသည် အချိန်ကုန်သက်သာစေပြီး ကုန်ထုတ်စွမ်းအားတိုးစေခြင်းဖြင့် ရေရှည်တွင် ကုန်ကျစရိတ်ကို လျှော့ချနိုင်သည်။
- အပိုင်းဒီဇိုင်း-ဆေးထိုးပုံသွင်းခြင်းအတွက် တစ်စိတ်တစ်ပိုင်း ဒီဇိုင်းကို ကောင်းမွန်အောင်ပြုလုပ်ရန် ဒီဇိုင်နာများ၊ အင်ဂျင်နီယာများနှင့် ကုန်ထုတ်လုပ်မှု ကျွမ်းကျင်သူများအကြား ပူးပေါင်း၍ ဆေးထိုးပုံသွင်းခြင်းကို အသုံးပြု၍ အစိတ်အပိုင်းကို ထိထိရောက်ရောက်နှင့် ထိထိရောက်ရောက် ထုတ်လုပ်နိုင်စေရန်အတွက် လိုအပ်ပါသည်။
- အရည်အသွေးထိန်းချုပ်မှု:အလိုအလျောက် အရည်အသွေးထိန်းချုပ်မှုစနစ်များကို အကောင်အထည်ဖော်ခြင်းသည် လိုက်လျောညီထွေရှိမှုကို မြှင့်တင်နိုင်ပြီး အရည်အသွေးပိုင်း၌ ကွဲပြားမှုကို လျှော့ချနိုင်သည်။
Injection Molding Technology တွင် ဆန်းသစ်တီထွင်မှုများ
ဆေးထိုးပုံသွင်းခြင်းသည် ရှုပ်ထွေးသော ပလပ်စတစ်အစိတ်အပိုင်းများထုတ်လုပ်ရန်အတွက် တွင်ကျယ်စွာအသုံးပြုသည့်ကုန်ထုတ်လုပ်မှုလုပ်ငန်းစဉ်တစ်ခုဖြစ်သည်။ ၎င်းတွင် သွန်းသောပလပ်စတစ်ပစ္စည်းကို ဖိအားမြင့်မြင့်အောက်တွင် မှိုထဲသို့ ထိုးသွင်းပြီး လိုချင်သောပုံသဏ္ဍာန်ဖြစ်လာစေရန် အအေးပေးခြင်း ပါဝင်သည်။ ထုတ်လုပ်မှုစက်မှုလုပ်ငန်းတွင် တိကျမှုနှင့် ထိရောက်မှုလိုအပ်ချက်များ တိုးပွားလာသည်နှင့်အမျှ ဆေးထိုးပုံသွင်းနည်းပညာတွင် ဆန်းသစ်တီထွင်မှုများသည် အဆိုပါလိုအပ်ချက်များကို ဖြည့်ဆည်းရာတွင် အရေးပါသောအခန်းကဏ္ဍမှ ပါဝင်ခဲ့သည်။ ဤဘလော့ဂ်ပို့စ်တွင်၊ ဆေးထိုးပုံသွင်းနည်းပညာ၏ နောက်ဆုံးပေါ်တိုးတက်မှုအချို့ကို လေ့လာပါမည်။
- မိုက်ခရိုဆေးထိုးခြင်း- ဤနည်းပညာသည် အလွန်သေးငယ်သော အစိတ်အပိုင်းများကို မိုက်ခရိုအနည်းငယ်အထိ ခံနိုင်ရည်နည်းပါးစွာဖြင့် ထုတ်လုပ်နိုင်စေပါသည်။ သေးငယ်၍ ရှုပ်ထွေးသော အစိတ်အပိုင်းများ ဝယ်လိုအား တိုးလာနေသည့် ဆေးနှင့် အီလက်ထရွန်းနစ် လုပ်ငန်းများတွင် မိုက်ခရိုဆေးထိုးခြင်းသည် အထူးအသုံးဝင်သည်။
- အစိတ်အပိုင်းပေါင်းများစွာ ပုံသွင်းခြင်း- ဤလုပ်ငန်းစဉ်တွင် မတူညီသောပစ္စည်းများကို တူညီသောမှိုထဲသို့ ထိုးသွင်းခြင်းဖြင့် အရောင်မျိုးစုံ သို့မဟုတ် ပစ္စည်းများစွာဖြင့် အစိတ်အပိုင်းများကို ထုတ်လုပ်နိုင်စေပါသည်။ ဒီနည်းပညာကို မော်တော်ကားနဲ့ လူသုံးကုန် လုပ်ငန်းတွေမှာ အသုံးများပါတယ်။
- ပုံသွင်းအလှဆင်ခြင်း-ဤနည်းပညာတွင် ဆေးထိုးပုံသွင်းစဉ်အတွင်း ပုံသွင်းထားသောအစိတ်အပိုင်းများသို့ ဂရပ်ဖစ်များ၊ အသွင်အပြင်များနှင့် ပုံစံများကို ပေါင်းထည့်ခြင်းတို့ပါဝင်သည်။ မှိုအတွင်းအလှဆင်ခြင်းသည် အပိုလုပ်ဆောင်ခြင်းမပြုဘဲ အရည်အသွေးမြင့် ပြီးမြောက်မှုရရှိရန် စရိတ်သက်သာသောနည်းလမ်းဖြစ်သည်။
- တွဲဖက်ဆေးထိုးခြင်း- ဤနည်းပညာသည် ပစ္စည်းနှစ်ခုကို တစ်ပြိုင်နက် ထိုးသွင်းပြီး အရေပြားတစ်ခုနှင့် ပင်မပစ္စည်းတစ်ခု ဖန်တီးသည်။ တွဲဖက်ထိုးသွင်းပုံသွင်းခြင်းသည် နူးညံ့သောထိတွေ့ခံစားမှု သို့မဟုတ် ပိုမိုကောင်းမွန်သော စက်ပိုင်းဆိုင်ရာ ဂုဏ်သတ္တိများဖြင့် အစိတ်အပိုင်းများကို ဖန်တီးရန်အတွက် အသုံးဝင်သည်။
- ဓာတ်ငွေ့အကူအညီဖြင့် ဆေးထိုးခြင်း-ဤနည်းပညာတွင် ပုံမှန်အားဖြင့် နိုက်ထရိုဂျင်ဓာတ်ငွေ့ကို ဆေးထိုးပုံသွင်းနေစဉ် မှိုထဲသို့ ထိုးသွင်းခြင်း ပါဝင်သည်။ ဓာတ်ငွေ့သည် အစိတ်အပိုင်းအတွင်း လမ်းကြောင်းများကို ဖြစ်ပေါ်စေပြီး ပစ္စည်းအသုံးပြုမှုကို လျှော့ချကာ ထုတ်ကုန်စွမ်းဆောင်ရည်ကို မြှင့်တင်ပေးသည်။
- မြန်နှုန်းမြင့် ဆေးထိုးခြင်း-ဤနည်းပညာသည် ဆေးထိုးအမြန်နှုန်းနှင့် စက်လည်ပတ်ချိန်များကို ပိုမိုမြန်ဆန်စေပြီး ထုတ်လုပ်မှုထိရောက်မှုနှင့် ကုန်ကျစရိတ်များကို လျှော့ချပေးသည်။ မြန်နှုန်းမြင့် ဆေးထိုးပုံသွင်းခြင်းသည် ပါးလွှာသော နံရံအစိတ်အပိုင်းများ ထုတ်လုပ်ရာတွင် အထူးအသုံးဝင်သည်။
- အသိဉာဏ်ပုံသွင်းခြင်း- ဤနည်းပညာသည် ဆေးထိုးပုံသွင်းခြင်းလုပ်ငန်းစဉ်ကို အကောင်းဆုံးဖြစ်အောင်ပြုလုပ်ရန် အာရုံခံကိရိယာများနှင့် ဒေတာခွဲခြမ်းစိတ်ဖြာမှုများကို အသုံးပြုသည်။ ဉာဏ်ရည်ထက်မြက်သော ပုံသွင်းခြင်းသည် အပူချိန်၊ ဖိအားနှင့် ပစ္စည်းစီးဆင်းမှုစသည့် စောင့်ကြည့်ရေးအချက်များအားဖြင့် ထုတ်ကုန်အရည်အသွေးကို တိုးတက်စေပြီး စွန့်ပစ်ပစ္စည်းများကို လျှော့ချနိုင်သည်။
အသုံးချမှု အထူးအဆန်း- အတွင်းခန်း ပလတ်စတစ် အစိတ်အပိုင်းများ
မော်တော်ယာဥ်လုပ်ငန်းတွင် သာလွန်ကောင်းမွန်သောမောင်းနှင်မှုအတွေ့အကြုံကိုပေးဆောင်ရန်အတွက် အတွင်းပိုင်းဒီဇိုင်းနှင့် လုပ်ဆောင်နိုင်စွမ်းများသည် မရှိမဖြစ်လိုအပ်ပါသည်။ အတွင်းခန်းပလတ်စတစ် အစိတ်အပိုင်းများသည် ဤရည်မှန်းချက်ကို အကောင်အထည်ဖော်ရာတွင် သက်တောင့်သက်သာ၊ စတိုင်လ်ကျကျနှင့် တာရှည်ခံမှုကို ပေးဆောင်ရန် အရေးကြီးသော အခန်းကဏ္ဍမှ ပါဝင်ပါသည်။ ဤဘလော့ဂ်ပို့စ်သည် မော်တော်ယာဥ်အတွင်းပိုင်း၌ အသုံးအများဆုံး ပလတ်စတစ်အစိတ်အပိုင်းအချို့ကို လေ့လာပါမည်။
- dashboard ကို: ဒက်ရှ်ဘုတ်သည် တိုင်းထွာချက်များ၊ လေဝင်ပေါက်များ၊ ဖျော်ဖြေရေးစနစ်များနှင့် အခြားအရေးကြီးသော ထိန်းချုပ်မှုများပါ၀င်သည့် ထင်ရှားသောအတွင်းခန်းအင်္ဂါရပ်တစ်ခုဖြစ်သည်။ တာရှည်ခံခြင်း၊ ဒီဇိုင်းပြောင်းလွယ်ပြင်လွယ်နှင့် စီမံဆောင်ရွက်ရလွယ်ကူခြင်းတို့ကြောင့် ပလတ်စတစ်အစိတ်အပိုင်းများကို ဒက်ရှ်ဘုတ်များထုတ်လုပ်ရာတွင် အများအားဖြင့် အသုံးပြုကြသည်။
- တံခါးပြားများ-တံခါးဘောင်များသည် အတွင်းပိုင်းဒီဇိုင်းအတွက် မရှိမဖြစ်လိုအပ်ပြီး အကာအကွယ်နှင့် သက်တောင့်သက်သာဖြစ်စေသည်။ ထိခိုက်မှုကိုခံနိုင်ရည်ရှိခြင်း၊ ဆူညံသံလျော့ပါးခြင်းနှင့် ပေါ့ပါးသောဂုဏ်သတ္တိများကြောင့် တံခါးအကန့်များဖန်တီးရန် ပလတ်စတစ်အစိတ်အပိုင်းများကို အသုံးပြုကြသည်။
- ထိုင်ခုံ:မော်တော်ကားထိုင်ခုံများသည် သက်တောင့်သက်သာနှင့် ပံ့ပိုးပေးသည့် စွမ်းဆောင်ရည်မြင့်ပစ္စည်းများ လိုအပ်ပါသည်။ ပလပ်စတစ် အစိတ်အပိုင်းများကို ထိုင်ခုံနောက်ကျော၊ လက်စွပ်နှင့် ထိုင်ခုံဖွဲ့စည်းပုံ၏ အခြားအစိတ်အပိုင်းများ ဖန်တီးရန် အသုံးပြုသည်။ ဤအစိတ်အပိုင်းများသည် ခိုင်ခံ့မှုနှင့် ပျော့ပြောင်းမှုကို ပေးစွမ်းပြီး မတူညီသော ဒီဇိုင်းများနှင့် လိုက်လျောညီထွေဖြစ်စေရန် အလွယ်တကူ ပုံသွင်းနိုင်သည်။
- အလယ်ခလုတ်-ဗဟိုကွန်ဆိုးလ်သည် ရာသီဥတုထိန်းချုပ်မှု၊ အသံစနစ်များနှင့် သိုလှောင်မှုကဲ့သို့သော မရှိမဖြစ်လိုအပ်သော ထိန်းချုပ်မှုများအတွက် အချက်အချာကျသည်။ အပူ၊ စိုထိုင်းဆ နှင့် အခြားပတ်ဝန်းကျင်ဆိုင်ရာအချက်များ ခံနိုင်ရည်ရှိသောကြောင့် ဗဟိုကွန်ဆိုးလ်များ ဖန်တီးရန် ပလတ်စတစ် အစိတ်အပိုင်းများကို အများအားဖြင့် အသုံးပြုကြသည်။
- အကွက်များကို ချုံ့ပါ။: တိုင်များ၊ ခေါင်းစီးများနှင့် ထိုင်ခုံနောက်ကျောများကဲ့သို့သော ယာဉ်၏အတွင်းပိုင်းဧရိယာများကို ဖုံးအုပ်ရန် အကန့်အကန့်များကို အသုံးပြုသည်။ ပလပ်စတစ် အစိတ်အပိုင်းများကို ၎င်းတို့၏ ဒီဇိုင်းပြောင်းလွယ်ပြင်လွယ်၊ အရောင်အသွေး အမျိုးမျိုးနှင့် လုပ်ဆောင်ရလွယ်ကူသောကြောင့် ဤအကန့်များကို ဖန်တီးရန် အသုံးပြုပါသည်။
အပလီကေးရှင်း အထူးအဆန်း- အပြင်ပလပ်စတစ် အစိတ်အပိုင်းများ
မော်တော်ယာဥ်လုပ်ငန်းတွင် ပြင်ပပလတ်စတစ် အစိတ်အပိုင်းများသည် ပို၍အဖြစ်များလာသည်။ ပေါ့ပါးသောပစ္စည်းများဝယ်လိုအား၊ ပိုမိုကောင်းမွန်သောဆီစားသက်သာမှုနှင့် ဆန်းသစ်သောဒီဇိုင်းဖြင့်၊ ပလတ်စတစ်အစိတ်အပိုင်းများသည် မော်တော်ကားများ၏ အပြင်ပိုင်းအစိတ်အပိုင်းအမျိုးမျိုးကို ထုတ်လုပ်ရန်အတွက် ရေပန်းစားသောရွေးချယ်မှုတစ်ခုဖြစ်လာသည်။ ဤဘလော့ဂ်ပို့စ်တွင်၊ မော်တော်ယာဥ်လုပ်ငန်းတွင် အသုံးအများဆုံး အပြင်ပန်း ပလတ်စတစ်အစိတ်အပိုင်းအချို့ကို လေ့လာပါမည်။
- ဘန်ပါများ- ဘန်ပါများသည် ယာဉ်တိုက်မှုဖြစ်လျှင် အကာအကွယ်ပေးသော အရေးကြီးသော အပြင်ပိုင်း အစိတ်အပိုင်းတစ်ခုဖြစ်သည်။ ပလပ်စတစ် အစိတ်အပိုင်းများကို ပေါ့ပါးသော၊ သက်ရောက်မှုခံနိုင်ရည်ရှိပြီး ကုန်ကျစရိတ်သက်သာသောကြောင့် ဘမ်ဘာများထုတ်လုပ်ရန် မကြာခဏအသုံးပြုကြသည်။
- အသားကင်များ- Grille သည် ကား၏ ထင်ရှားသော အပြင်ပိုင်းအင်္ဂါရပ်တစ်ခုဖြစ်ပြီး ၎င်း၏ အလုံးစုံဒီဇိုင်းနှင့် လေခွင်းအားအတွက် အရေးကြီးသော အခန်းကဏ္ဍမှ ပါဝင်ပါသည်။ ပလပ်စတစ် အစိတ်အပိုင်းများကို ၎င်းတို့၏ ဒီဇိုင်း ပျော့ပြောင်းမှုနှင့် ရှုပ်ထွေးသော ပုံသဏ္ဍာန်များအဖြစ် ပုံသွင်းနိုင်ခြင်းကြောင့် အကင်များ ထုတ်လုပ်ရာတွင် အများအားဖြင့် အသုံးပြုကြသည်။
- အပြင်ပိုင်းဖြတ်ပိုင်းများ-အပြင်ပိုင်းဖြတ်ပိုင်းများတွင် ပုံသွင်းခြင်း၊ အကာအရံမီးတောက်များနှင့် ယာဉ်၏အသွင်အပြင်ကို မြှင့်တင်ပေးသည့် အခြားအလှဆင်ပစ္စည်းများပါဝင်သည်။ ပလတ်စတစ် အစိတ်အပိုင်းများကို အရောင်အသွေး စုံအောင် ဖန်တီးနိုင်သောကြောင့် ဒီဇိုင်းရွေးချယ်စရာ အများအပြားကို ပေးစွမ်းနိုင်သောကြောင့် အဆိုပါ ညှပ်များကို ထုတ်လုပ်ရန် မကြာခဏ အသုံးပြုကြသည်။
- ကြေးမုံ: မှန်များသည် မြင်နိုင်စွမ်းနှင့် ဘေးကင်းမှုကို ပေးစွမ်းနိုင်သော မည်သည့်ယာဉ်အတွက်မဆို မရှိမဖြစ်လိုအပ်သော အစိတ်အပိုင်းတစ်ခုဖြစ်သည်။ ပလပ်စတစ် အစိတ်အပိုင်းများကို ၎င်းတို့၏ ပေါ့ပါးသော ဂုဏ်သတ္တိများ၊ သက်ရောက်မှုခံနိုင်ရည်နှင့် ဒီဇိုင်းပြောင်းလွယ်ပြင်လွယ်ကြောင့် မှန်အိမ်များကို ထုတ်လုပ်ရန် မကြာခဏ အသုံးပြုကြသည်။
- ဖျက်လိုဖျက်ဆီး: Spoiler များသည် ယာဉ်အများအပြားတွင် ရေပန်းစားသော အပိုပစ္စည်းတစ်ခုဖြစ်ပြီး လေခွင်းအားကောင်းမွန်စေကာ အလုံးစုံအသွင်အပြင်ကို မြှင့်တင်ပေးပါသည်။ ပလပ်စတစ် အစိတ်အပိုင်းများကို ၎င်းတို့၏ ပေါ့ပါးပြီး ဒီဇိုင်းပြောင်းလွယ်ပြင်လွယ်ကြောင့် spoiler များ ထုတ်လုပ်ရန် မကြာခဏ အသုံးပြုကြသည်။
မော်တော်ယာဥ် ပလပ်စတစ် အစိတ်အပိုင်းများ ထိုးထည့်ခြင်း၏ အနာဂတ်
မော်တော်ယာဥ်ပလပ်စတစ် အစိတ်အပိုင်းများကို ဆေးထိုးခြင်းလုပ်ငန်းသည် မော်တော်ကားလုပ်ငန်းတွင် ပို၍အရေးကြီးလာပါသည်။ နည်းပညာတွေ တိုးတက်လာတာနဲ့အမျှ ဒီလုပ်ငန်းစဉ်ရဲ့ အနာဂတ်ဟာ အလားအလာကောင်းတွေ ရှိနေပါတယ်။ ဤသည်မှာ မော်တော်ယာဥ်ပလပ်စတစ် အစိတ်အပိုင်းများကို ဆေးထိုးပုံသွင်းခြင်း၏ အနာဂတ်အတွက် ခေတ်ရေစီးကြောင်းနှင့် ခန့်မှန်းချက်အချို့ဖြစ်သည်။
- ပေါ့ပါးသောပစ္စည်းများကို တိုးမြှင့်အသုံးပြုခြင်း။: ကာဗွန်ဖိုက်ဘာနှင့် သာမိုပလတ်စတစ်များကဲ့သို့ ပေါ့ပါးသောပစ္စည်းများသည် မော်တော်ယာဥ်လုပ်ငန်းတွင် လူကြိုက်များလာသည်။ ယင်းမှာ ဆီစားသက်သာခြင်း၊ စွမ်းဆောင်ရည်နှင့် ဓာတ်ငွေ့ထုတ်လွှတ်မှု လျှော့ချခြင်းဆိုင်ရာ အကျိုးကျေးဇူးများကြောင့် ဖြစ်သည်။ ရလဒ်အနေဖြင့် မော်တော်ကား ပလပ်စတစ် အစိတ်အပိုင်းများကို ဆေးထိုးပုံသွင်းခြင်းသည် အဆိုပါ ပေါ့ပါးသော ပစ္စည်းများကို ထုတ်လုပ်ရာတွင် အရေးပါသော အခန်းကဏ္ဍမှ ပါဝင်မည်ဖြစ်သည်။
- Additive Manufacturing ပေါင်းစပ်ခြင်း-3D ပရင့်ထုတ်ခြင်းဟုလည်း လူသိများသော ပေါင်းစည်းထုတ်လုပ်မှုသည် မော်တော်ယာဥ်လုပ်ငန်းတွင် ပို၍အဖြစ်များလာသည်။ ဤနည်းပညာသည် ရိုးရာဆေးထိုးပုံသွင်းခြင်းကို အသုံးပြု၍ ထုတ်လုပ်ရန် ခက်ခဲသော သို့မဟုတ် မဖြစ်နိုင်သော ရှုပ်ထွေးသော ဂျီသြမေတြီများနှင့် ပုံသဏ္ဍာန်များကို ဖန်တီးနိုင်စေပါသည်။ အနာဂတ်တွင်၊ မော်တော်ယာဥ်ပလပ်စတစ် အစိတ်အပိုင်းများကို ဆေးထိုးပုံသွင်းခြင်းသည် ပိုမိုရှုပ်ထွေးသော ဒီဇိုင်းများဖန်တီးရန်အတွက် ပေါင်းစပ်ထုတ်လုပ်ခြင်းသို့ ပေါင်းစပ်ထုတ်လုပ်နိုင်မည်ဖြစ်သည်။
- တိုးမြှင့်ထားသော အလိုအလျောက်စနစ်- နည်းပညာတိုးတက်လာသည်နှင့်အမျှ၊ ဆေးထိုးပုံသွင်းခြင်းလုပ်ငန်းစဉ်တွင် အလိုအလျောက်လုပ်ဆောင်မှုကို ပိုမိုမြင်တွေ့လာရန် ကျွန်ုပ်တို့ မျှော်လင့်နိုင်သည်။ ၎င်းသည် စွမ်းဆောင်ရည် တိုးမြင့်လာပြီး ထုတ်လုပ်မှုအချိန်များကို လျှော့ချပေးမည်ဖြစ်သည်။ ထို့အပြင်၊ အလိုအလျောက်စနစ်သည် လူ့အမှားဖြစ်နိုင်ခြေကို လျှော့ချနိုင်ပြီး အရည်အသွေးမြင့် ထုတ်ကုန်များကို ဖြစ်ပေါ်စေသည်။
- ပိုမိုရေရှည်တည်တံ့နိုင်သောပစ္စည်းများ- မော်တော်ကားလုပ်ငန်းတွင် ရေရှည်တည်တံ့ခိုင်မြဲရေးသည် ပို၍အရေးကြီးသော ပြဿနာတစ်ရပ်ဖြစ်လာသည်။ မော်တော်ကား ပလတ်စတစ် အစိတ်အပိုင်းများ ဆေးထိုးခြင်း သည် ပိုမိုရေရှည်တည်တံ့သော ပစ္စည်းများကို အသုံးပြုခြင်းဖြင့် ဤလမ်းကြောင်းနှင့် လိုက်လျောညီထွေရှိရန် လိုအပ်မည်ဖြစ်ပါသည်။ ဥပမာအားဖြင့်၊ ဇီဝအခြေခံပလတ်စတစ်များနှင့် ပြန်လည်အသုံးပြုသည့်ပစ္စည်းများကို ဆေးထိုးပုံသွင်းခြင်းလုပ်ငန်းစဉ်တွင် စွန့်ပစ်ပစ္စည်းများနှင့် ကာဗွန်ထုတ်လွှတ်မှုလျှော့ချရန် အသုံးပြုနိုင်သည်။
- တိုးမြှင့်ထားသော စိတ်ကြိုက်ပြင်ဆင်မှု-စိတ်ကြိုက်ပြင်ဆင်ခြင်းနှင့် စိတ်ကြိုက်ပြင်ဆင်ခြင်းများတွင် စားသုံးသူများသည် ပိုမိုတောင်းဆိုလာကြသည်။ အနာဂတ်တွင်၊ မော်တော်ယာဥ်ပလပ်စတစ် အစိတ်အပိုင်းများကို ဆေးထိုးပုံသွင်းခြင်းသည် ထုတ်ကုန်များကို ပိုမိုစိတ်ကြိုက်ပြင်ဆင်နိုင်စေမည့် နည်းပညာများကို ပေါင်းစပ်ထည့်သွင်းနိုင်မည်ဖြစ်သည်။ ၎င်းတွင် ပလပ်စတစ် အစိတ်အပိုင်းများ၏ ဒီဇိုင်း၊ အရောင်နှင့် အသွင်အပြင်ကို စိတ်ကြိုက်ပြင်ဆင်နိုင်မှု ပါဝင်သည်။
- စမတ်နည်းပညာများ ပေါင်းစပ်ခြင်း- အာရုံခံကိရိယာများနှင့် Internet of Things (IoT) ကိရိယာများကဲ့သို့သော စမတ်နည်းပညာများသည် မော်တော်ယာဥ်လုပ်ငန်းတွင် ပို၍အဖြစ်များလာသည်။ အနာဂတ်တွင်၊ မော်တော်ယာဥ်ပလပ်စတစ် အစိတ်အပိုင်းများကို ဆေးထိုးပုံသွင်းခြင်းသည် အဆိုပါနည်းပညာများကို ထုတ်လုပ်မှုတွင် ထည့်သွင်းနိုင်မည်ဖြစ်သည်။ ၎င်းသည် ယာဉ်၏ အခြားအစိတ်အပိုင်းများနှင့် ယာဉ်မောင်းနှင့် ဆက်သွယ်နိုင်သည့် အစိတ်အပိုင်းများကို ဖန်တီးနိုင်စေနိုင်သည်။
Case Study- မော်တော်ယာဥ်လုပ်ငန်းတွင် ဆေးထိုးပုံသွင်းခြင်းကို အောင်မြင်စွာ အကောင်အထည်ဖော်ခြင်း။
Injection molding သည် မော်တော်ယာဥ်လုပ်ငန်းတွင် ပိုမိုရေပန်းစားလာကာ တွင်ကျယ်စွာအသုံးပြုသည့် ကုန်ထုတ်လုပ်မှုလုပ်ငန်းစဉ်တစ်ခုဖြစ်သည်။ ဤဘလော့ဂ်ပို့စ်တွင်၊ မော်တော်ယာဥ်လုပ်ငန်းတွင် ဆေးထိုးပုံသွင်းခြင်းအား အောင်မြင်စွာ အကောင်အထည်ဖော်ခြင်းဆိုင်ရာ ဖြစ်ရပ်မှန်လေ့လာချက်ကို ဆွေးနွေးပါမည်။
Case- မော်တော်ကား မီးအလင်းရောင်
မော်တော်ယာဥ်လုပ်ငန်းတွင် အထူးအောင်မြင်သော ဆေးထိုးခြင်းလုပ်ငန်းသည် မော်တော်ယာဥ်အလင်းရောင် အစိတ်အပိုင်းများ ထုတ်လုပ်ခြင်းပင်ဖြစ်သည်။ ဤကိစ္စရပ်တွင် လေ့လာမှုတွင်၊ လူကြိုက်များသော ဆီဒင်မော်ဒယ်အတွက် နောက်မီးမှန်ဘီလူးကို ထုတ်လုပ်ရန်အတွက် ဆေးထိုးပုံသွင်းခြင်းအား အာရုံစိုက်လုပ်ဆောင်ပါမည်။
စိန်ခေါ်မှုများ:
နောက်မီးမှန်ဘီလူးသည် အောက်ပါလိုအပ်ချက်များနှင့် ကိုက်ညီရမည်-
- ခရမ်းလွန်ရောင်ခြည်နှင့် ရာသီဥတုဒဏ်ကို ခံနိုင်ရည်ရှိသည်။
- အလင်းအမှောင် ကြည်လင်ပြတ်သားမှု ကောင်းပါတယ်။
- ကြာရှည်ခံမှု
- ဗေဒနှစ်သက်ဖွယ်ဒီဇိုင်းကို
- ထိရောက်သောထုတ်လုပ်မှုအချိန်
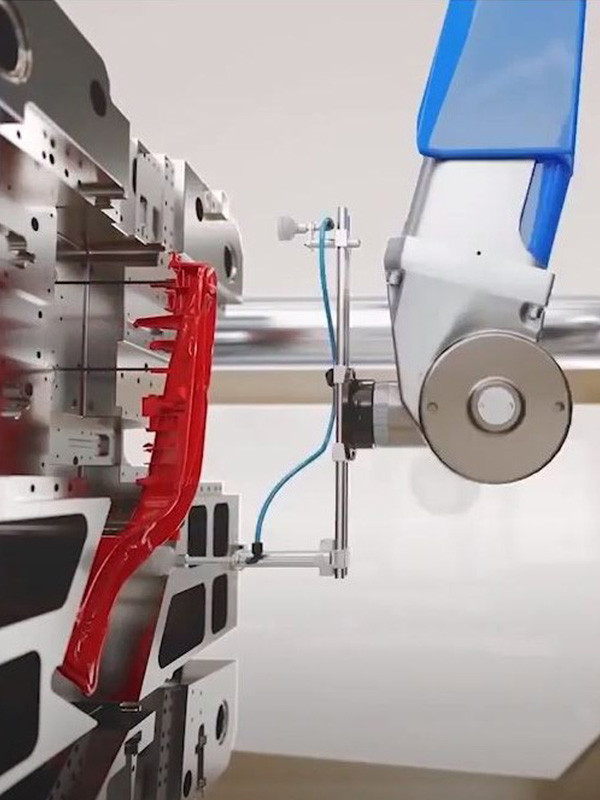
ဖြေရှင်းချက်:
လိုအပ်ချက်များနှင့် စိန်ခေါ်မှုများကို ခွဲခြမ်းစိတ်ဖြာပြီးနောက်၊ မော်တော်ကားအလင်းရောင်ထုတ်လုပ်သူသည် နောက်မီးမှန်ဘီလူးကိုထုတ်လုပ်ရန်အတွက် အကောင်းဆုံးဖြေရှင်းချက်အဖြစ် ဆေးထိုးပုံသွင်းခြင်းကို ရွေးချယ်ခဲ့သည်။ ထုတ်လုပ်သူသည် အရည်အသွေးမြင့် မော်တော်ယာဥ်အစိတ်အပိုင်းများကို ထုတ်လုပ်သည့် စံချိန်တင်ထားသော အတွေ့အကြုံရှိသော ဆေးထိုးပုံသွင်းကုမ္ပဏီနှင့် ပူးပေါင်းခဲ့သည်။
ဆေးထိုးခြင်းလုပ်ငန်းစဉ်တွင် အောက်ပါအဆင့်များ ပါဝင်ပါသည်။
- ပစ္စည်းရွေးချယ်မှု-နောက်မီးမှန်ဘီလူးအတွက် UV-ခံနိုင်ရည်ရှိသော polycarbonate ပစ္စည်းကို ရွေးချယ်ခဲ့သည်။
- မှိုဒီဇိုင်းဆေးထိုးပုံသွင်းသည့်ကုမ္ပဏီသည် လိုအပ်သောသတ်မှတ်ချက်များနှင့်ကိုက်ညီစေရန် နောက်မီးမှန်ဘီလူးကိုထုတ်လုပ်ရန်အတွက် စိတ်ကြိုက်မှိုကို ဒီဇိုင်းထုတ်ပါသည်။
- ဆေးထိုးခြင်း-ထို့နောက် မှိုကို နောက်မီးမှန်ဘီလူးထုတ်လုပ်ရန်အတွက် ဆေးထိုးပုံသွင်းခြင်းလုပ်ငန်းစဉ်တွင် အသုံးပြုခဲ့သည်။
- အရည်အသွေးထိန်းချုပ်မှု:နောက်မီးမှန်ဘီလူးသည် လိုအပ်သောစံချိန်စံညွှန်းများနှင့်ကိုက်ညီကြောင်း သေချာစေရန် တိကျသောအရည်အသွေးထိန်းချုပ်မှုအစီအမံများပြုလုပ်ထားသည်။
ရလဒ်များ:
taillight မှန်ဘီလူးများ ထုတ်လုပ်မှုအတွက် ဆေးထိုးပုံသွင်းခြင်း အကောင်အထည်ဖော်မှုသည် အောင်မြင်ကြောင်း သက်သေပြခဲ့သည်။ မော်တော်ကားအလင်းရောင်ထုတ်လုပ်သူသည် လိုအပ်သောသတ်မှတ်ချက်အားလုံးနှင့်ကိုက်ညီသည့် အရည်အသွေးမြင့် နောက်မီးမှန်ဘီလူးကို ထုတ်လုပ်ခဲ့သည်။
ဤအပလီကေးရှင်းအတွက် ဆေးထိုးပုံသွင်းအသုံးပြုခြင်း၏ အကျိုးကျေးဇူးများ ပါဝင်သည်။
- တသမတ်တည်း အရည်အသွေး-ထိုးသွင်းပုံသွင်းခြင်းသည် လိုအပ်သော စံချိန်စံညွှန်းများနှင့် ကိုက်ညီသည့် နောက်မီးမှန်၏ အရည်အသွေးကို အာမခံပါသည်။
- ထိရောက်သောထုတ်လုပ်မှု- ဆေးထိုးပုံသွင်းခြင်းလုပ်ငန်းစဉ်သည် taillight မှန်ဘီလူးကို ထိရောက်စွာထုတ်လုပ်နိုင်စေပြီး ထုတ်လုပ်မှုအချိန်နှင့် ကုန်ကျစရိတ်များကို လျှော့ချပေးသည်။
- လှပသောဒီဇိုင်းနောက်မီးမှန်ဘီလူးအတွက် သာယာလှပသော ဒီဇိုင်းကို ဖန်တီးရန်အတွက် ဆေးထိုးပုံသွင်းခြင်းကို ခွင့်ပြုထားသည်။
- အကြမ်းခံ: ဆေးထိုးပုံသွင်းခြင်းဖြင့် ထုတ်လုပ်သော နောက်မီးမှန်ဘီလူးသည် ခရမ်းလွန်ရောင်ခြည်နှင့် ရာသီဥတုဒဏ်ကို ခံနိုင်ရည်ရှိသည်။
Injection Molding နှင့် ပတ်သက်၍ အဖြစ်များသော အထင်အမြင်လွဲမှားမှုများ
ဆေးထိုးပုံသွင်းခြင်းဆိုသည်မှာ လိုချင်သောပုံသဏ္ဍာန်ကိုဖန်တီးရန်အတွက် မှိုထဲသို့ သွန်းသောပစ္စည်းကို မှိုထဲသို့ ထိုးသွင်းခြင်းပါ၀င်သော တွင်ကျယ်စွာအသုံးပြုသည့်ကုန်ထုတ်လုပ်မှုလုပ်ငန်းစဉ်တစ်ခုဖြစ်သည်။ သို့သော်လည်း ဆေးထိုးပုံသွင်းခြင်းဆိုင်ရာ အထင်အမြင်လွဲမှားမှုများသည် လုပ်ငန်းစဉ်နှင့် ပတ်သက်၍ နားလည်မှုလွဲမှားမှုများ ဖြစ်စေနိုင်သည်။ ဤဘလော့ဂ်ပို့စ်သည် ဆေးထိုးပုံသွင်းခြင်းနှင့်ပတ်သက်၍ အများအားဖြင့် အထင်အမြင်လွဲမှားမှုအချို့ကို ဆွေးနွေးပါမည်။
အထင်အမြင်လွဲခြင်း 1- ဆေးထိုးပုံသွင်းခြင်းသည် ထုတ်ကုန်အမြောက်အမြားထုတ်လုပ်ရန်အတွက်သာ သင့်လျော်သည်။
ဆေးထိုးပုံသွင်းခြင်းသည် ထုတ်ကုန်အမြောက်အမြားထုတ်လုပ်ရန်အတွက်သာ သင့်လျော်သည်ဟု လူအများက ယုံကြည်ကြသည်။ ဆေးထိုးပုံသွင်းခြင်းသည် ထုတ်ကုန်အမြောက်အမြားကို ထုတ်လုပ်နိုင်သော်လည်း သေးငယ်သော ထုတ်လုပ်မှုလုပ်ငန်းများအတွက်လည်း အသုံးပြုနိုင်သည်။ ဆေးထိုးပုံသွင်းခြင်းသည် အသေးစားနှင့် အလတ်စား ထုတ်လုပ်မှုလုပ်ငန်းများကို ထုတ်လုပ်ရန်အတွက် ထိရောက်ပြီး ကုန်ကျစရိတ်သက်သာနိုင်သည်။
အထင်အမြင်လွဲခြင်း 2- ဆေးထိုးခြင်းသည် နှေးကွေးသော လုပ်ငန်းစဉ်ဖြစ်သည်။
ဆေးထိုးပုံသွင်းခြင်းဆိုင်ရာ နောက်ထပ် အထင်အမြင်လွဲမှားမှုတစ်ခုမှာ ၎င်းသည် နှေးကွေးသော လုပ်ငန်းစဉ်ဖြစ်သည်။ ဆေးထိုးပုံသွင်းခြင်းသည် သတ်မှတ်ထားသော အချိန်အတိုင်းအတာတစ်ခု လိုအပ်သည်မှန်သော်လည်း၊ လုပ်ငန်းစဉ်စတင်ပြီးသည်နှင့် ၎င်းသည် ထုတ်ကုန်အမြောက်အမြားကို လျင်မြန်ထိရောက်စွာ ထုတ်လုပ်နိုင်သည်။ ထို့အပြင် နည်းပညာတိုးတက်မှုများက ဆေးထိုးပုံသွင်းစက်များနှင့် လုပ်ငန်းစဉ်များကို ပိုမိုမြန်ဆန်စွာ ပြုလုပ်နိုင်စေပါသည်။
အထင်အမြင်လွဲခြင်း 3- Injection molding သည် ရိုးရှင်းသော ပုံသဏ္ဍာန်များ ထုတ်လုပ်ရန်အတွက်သာ သင့်လျော်ပါသည်။
ဆေးထိုးပုံသွင်းခြင်းသည် ရိုးရှင်းသော ပုံသဏ္ဍာန်များ ထုတ်လုပ်ခြင်းနှင့် မကြာခဏ ဆက်စပ်နေသော်လည်း ၎င်းသည် သေချာပေါက် မမှန်ပါ။ မှိုဒီဇိုင်းနှင့် ပစ္စည်းရွေးချယ်မှုတွင် တိုးတက်မှုများသည် ဆေးထိုးပုံသွင်းခြင်းမှတစ်ဆင့် ပိုမိုရှုပ်ထွေးသောပုံစံများနှင့် ဒီဇိုင်းများကို ထုတ်လုပ်နိုင်စေခဲ့သည်။ ထို့အပြင် 3D ပုံနှိပ်ခြင်းနှင့် အခြားနည်းပညာများ ပေါင်းစပ်ခြင်းသည် ဆေးထိုးပုံသွင်းခြင်းအတွက် ဖြစ်နိုင်ခြေများကို ပိုမိုကျယ်ပြန့်စေသည်။
အထင်အမြင်လွဲခြင်း 4- ဆေးထိုးပုံသွင်းခြင်းသည် ပတ်ဝန်းကျင်နှင့် မကိုက်ညီပါ။
ဆေးထိုးပုံသွင်းခြင်းသည် ပတ်ဝန်းကျင်နှင့် သဟဇာတမဖြစ်ခြင်းကြောင့် ဝေဖန်ခံရလေ့ရှိသည်။ ဆေးထိုးပုံသွင်းခြင်းသည် စွန့်ပစ်ပစ္စည်းအချို့ကို ဖန်တီးသည်မှန်သော်လည်း၊ ပစ္စည်းရွေးချယ်ခြင်းနှင့် ပြန်လည်အသုံးပြုခြင်းနည်းပညာများတွင် တိုးတက်မှုများက ဆေးထိုးပုံသွင်းခြင်းမှတစ်ဆင့် ပတ်ဝန်းကျင်နှင့် သဟဇာတဖြစ်သော ထုတ်ကုန်များကို ပိုမိုထုတ်လုပ်နိုင်စေပါသည်။ ထို့အပြင် ဆေးထိုးပုံသွင်းခြင်းသည် ထုတ်ကုန်များ၏ ကာဗွန်ခြေရာကို လျှော့ချပေးနိုင်သော ပေါ့ပါးပြီး ရေရှည်တည်တံ့သော ပစ္စည်းများကို ထုတ်လုပ်နိုင်စေပါသည်။
အထင်အမြင်လွဲခြင်း 5- ဆေးထိုးတာက ဈေးကြီးတယ်။
ဆေးထိုးပုံသွင်းခြင်းသည် စျေးကြီးသော ထုတ်လုပ်မှုလုပ်ငန်းစဉ်တစ်ခုဟု လူအများက ယုံကြည်ကြသည်။ မှိုဒီဇိုင်းထုတ်ခြင်းနှင့် မှိုထုတ်လုပ်ခြင်းကဲ့သို့သော ဆေးထိုးပုံသွင်းခြင်းနှင့် ဆက်စပ်သော ကုန်ကျစရိတ်အချို့ရှိသော်လည်း ထုတ်လုပ်မှုပမာဏ တိုးလာသည်နှင့်အမျှ တစ်ယူနစ်ကုန်ကျစရိတ် ကျဆင်းသွားပါသည်။ ထို့အပြင်၊ နည်းပညာတိုးတက်မှုများသည် ဆေးထိုးပုံသွင်းခြင်းကို ယခင်ကထက် ကုန်ကျစရိတ်သက်သာပြီး ထိရောက်မှုရှိစေပါသည်။
Injection Molding တွင် အဖြစ်များသော ပြဿနာများကို ဖြေရှင်းခြင်း။
Injection molding သည် လုပ်ငန်းအမျိုးမျိုးအတွက် အရည်အသွေးမြင့် ပလပ်စတစ်အစိတ်အပိုင်းများကို ထုတ်လုပ်ပေးသည့် တွင်ကျယ်စွာ အသုံးပြုသည့် ထုတ်လုပ်မှုလုပ်ငန်းစဉ်တစ်ခုဖြစ်သည်။ သို့သော်၊ မည်သည့်ကုန်ထုတ်လုပ်မှုလုပ်ငန်းစဉ်ကဲ့သို့ပင်၊ ဆေးထိုးပုံသွင်းခြင်းသည် နောက်ဆုံးထုတ်ကုန်ကို ထိခိုက်စေနိုင်သော ဘုံပြဿနာများကို ကြုံတွေ့ရနိုင်သည်။ ဤဘလော့ဂ်ပို့စ်တွင်၊ ဆေးထိုးခြင်းတွင် အဖြစ်များသော ပြဿနာအချို့နှင့် ၎င်းတို့ကို မည်သို့ဖြေရှင်းရမည်ကို ဆွေးနွေးပါမည်။
ပြဿနာ 1- Burn Marks
ဆေးထိုးပုံသွင်းထားသော အစိတ်အပိုင်းများ၏ မျက်နှာပြင်ပေါ်တွင် မီးလောင်ဒဏ်ရာများ ပေါ်လာနိုင်ပြီး အစေးများ ပျက်စီးခြင်းနှင့် အရောင်ပြောင်းခြင်းတို့ကို ဖြစ်စေသည်။ ဤပြဿနာသည် အပါအဝင် အကြောင်းရင်းများစွာကြောင့် ဖြစ်နိုင်သည်-
- မြင့်မားသောအရည်ပျော်အပူချိန်
- ကြာရှည်နေထိုင်ချိန်
- အအေးခံချိန် မလုံလောက်ခြင်း။
- မြင့်မားသောထိုးဆေးအရှိန်
မီးလောင်မှု အမှတ်အသားများကို ဖြေရှင်းရန် ထုတ်လုပ်သူသည် အောက်ပါအဆင့်များကို ထည့်သွင်းစဉ်းစားသင့်သည်-
- အရည်ပျော်သောအပူချိန်ကိုလျှော့ချပါ။
- နေထိုင်ချိန်ကို လျှော့ချပါ။
- အအေးခံချိန်ကို တိုးပေးပါ။
- ဆေးထိုးနှုန်းကို လျှော့ချပါ။
ပြဿနာ 2- Warping
Warping သည် ပစ္စည်း၏ မညီမညာ အအေးခံခြင်းကြောင့် ဖြစ်ပွားနိုင်သော ဆေးထိုးပုံသွင်းခြင်းတွင် အဖြစ်များသော ပြဿနာတစ်ခုဖြစ်သည်။ ၎င်းသည် နောက်ဆုံးထုတ်ကုန်ကို ကွဲလွဲခြင်း သို့မဟုတ် ပုံပျက်ခြင်းဖြစ်စေနိုင်ပြီး ၎င်း၏လုပ်ဆောင်နိုင်စွမ်းကို ထိခိုက်စေနိုင်သည်။ ဤပြဿနာသည် အကြောင်းရင်းများစွာကြောင့် ဖြစ်နိုင်သည်-
- မညီမညာ အအေးခံခြင်း။
- ထုပ်ပိုးမှုဖိအား မလုံလောက်ပါ။
- မသင့်လျော်သောပုံစံခွက်
warping ပြဿနာကိုဖြေရှင်းရန်၊ ထုတ်လုပ်သူများသည် အောက်ပါအဆင့်များကို ထည့်သွင်းစဉ်းစားသင့်သည်-
- မှိုတစ်လျှောက်လုံး အအေးခံကြောင်း သေချာပါစေ။
- ထုပ်ပိုးမှုဖိအားကို မြှင့်တင်ပါ။
- ဂျီသြမေတြီအပိုင်း တိုးတက်စေရန် မှိုဒီဇိုင်းကို မွမ်းမံပါ။
ပြဿနာ 3- Sink Marks
Sink marks များသည် မညီမညာ အအေးခံခြင်း သို့မဟုတ် ထုပ်ပိုးခြင်းများကြောင့် ဆေးထိုးပုံသွင်းထားသော အစိတ်အပိုင်းများ၏ မျက်နှာပြင်ပေါ်တွင် ဖြစ်ပေါ်နိုင်သည့် စိတ်ဓာတ်ကျခြင်းများဖြစ်သည်။ ဤပြဿနာသည် အကြောင်းရင်းများစွာကြောင့် ဖြစ်နိုင်သည်-
- မြင့်မားသောထိုးဆေးအရှိန်
- ထုပ်ပိုးမှုဖိအား မလုံလောက်ပါ။
- မြင့်မားသောအရည်ပျော်အပူချိန်
- ကြာရှည်နေထိုင်ချိန်
sink marks ပြဿနာဖြေရှင်းရန်၊ ထုတ်လုပ်သူများသည် အောက်ပါအဆင့်များကို ထည့်သွင်းစဉ်းစားသင့်သည်-
- ဆေးထိုးနှုန်းကို လျှော့ချပါ။
- ထုပ်ပိုးမှုဖိအားကို မြှင့်တင်ပါ။
- အရည်ပျော်သောအပူချိန်ကိုလျှော့ချပါ။
- နေထိုင်ချိန်ကို လျှော့ချပါ။
ပြဿနာ 4- Flashing
ပိုလျှံနေသော ပစ္စည်းကို မှိုမှ ညှစ်ထုတ်သောအခါတွင် ရောင်ရမ်းခြင်းသည် ဆေးထိုးပုံသွင်းခြင်းတွင် အဖြစ်များသော ပြဿနာတစ်ခုဖြစ်သည်။ ၎င်းသည် နောက်ဆုံးထုတ်ကုန်၏ အစွန်းတစ်ဝိုက်တွင် ပိုလျှံနေသော ပစ္စည်းကို ဖြစ်ပေါ်စေနိုင်ပြီး ၎င်း၏ အလှအပနှင့် လုပ်ဆောင်နိုင်စွမ်းကို ထိခိုက်စေနိုင်သည်။ ဤပြဿနာသည် အကြောင်းရင်းများစွာကြောင့် ဖြစ်နိုင်သည်-
- ဟောင်းနွမ်းနေသောမှိုအစိတ်အပိုင်းများ
- ကုပ်ဆွဲအား မလုံလောက်ခြင်း။
- အအေးခံချိန် မလုံလောက်ခြင်း။
Flashing ပြဿနာကို ဖြေရှင်းရန် ထုတ်လုပ်သူသည် အောက်ပါအဆင့်များကို ထည့်သွင်းစဉ်းစားသင့်သည်-
- ဟောင်းနွမ်းနေသော မှိုအစိတ်အပိုင်းများကို အစားထိုးပါ။
- တွန်းအားကို တိုးပေးပါ။
- အအေးခံချိန်ကို တိုးပေးပါ။
ကျွမ်းကျင်သော ထိုးထွင်းသိမြင်မှု- မော်တော်ယာဥ် ထိုးဆေးထိုးခြင်းတွင် စက်မှုလုပ်ငန်းကျွမ်းကျင်ပညာရှင်များနှင့် တွေ့ဆုံမေးမြန်းခြင်း။
ထိုးသွင်းပုံသွင်းခြင်းသည် မော်တော်ယာဥ်လုပ်ငန်းတွင် အရေးပါသောလုပ်ငန်းစဉ်ဖြစ်ပြီး မော်တော်ယာဉ်အစိတ်အပိုင်းအမျိုးမျိုးတွင် အရည်အသွေးမြင့် ပလပ်စတစ်အစိတ်အပိုင်းများကို ထုတ်လုပ်ပါသည်။ စက်မှုလုပ်ငန်းနှင့် ၎င်း၏လက်ရှိအခြေအနေတို့ကို ထိုးထွင်းသိမြင်နိုင်ရန် မော်တော်ယာဥ်ဆေးထိုးပုံသွင်းခြင်းဆိုင်ရာ ကျွမ်းကျင်သောအမြင်များနှင့် ထိုးထွင်းသိမြင်မှုများကို မျှဝေပေးသည့် လုပ်ငန်းကျွမ်းကျင်ပညာရှင်များနှင့် ဟောပြောခဲ့ပါသည်။
ကျွမ်းကျင်သူ 1- Injection Molding Company ၏ CEO ဖြစ်သူ John Doe
- မော်တော်ယာဥ်လုပ်ငန်းတွင် ဇီဝပလတ်စတစ်အသုံးပြုမှုသည် ပိုမိုရေပန်းစားလာကြောင်း Doe က ပြောပြသည်။ ဤပလတ်စတစ်များသည် ပတ်ဝန်းကျင်နှင့် သဟဇာတဖြစ်ပြီး ကားတစ်စီး၏ ကာဗွန်ခြေရာကို လျှော့ချနိုင်ပြီး ၎င်းတို့ကို ကားထုတ်လုပ်သူများအတွက် ဆွဲဆောင်မှုတစ်ခုဖြစ်စေသည်။
- 3D ပုံနှိပ်ခြင်းတွင် တိုးတက်မှုများက ပိုမိုရှုပ်ထွေးသော မှိုဒီဇိုင်းများကို ဖန်တီးနိုင်စေပြီး အရည်အသွေးမြင့် နောက်ဆုံးထုတ်ကုန်များကို ဖြစ်ပေါ်စေကြောင်း ၎င်းက မှတ်ချက်ပြုခဲ့သည်။
- စိန်ခေါ်မှုများတွင် ကျွမ်းကျင်လုပ်သားရှားပါးမှုသည် စက်မှုလုပ်ငန်းတွင် သိသာထင်ရှားသောပြဿနာတစ်ခုဖြစ်ပြီး လုပ်သားစရိတ်များ မြင့်မားလာစေသည်ဟု ၎င်းက ဆိုသည်။
ကျွမ်းကျင်ပညာရှင် ၂- ဂျိန်းစမစ်၊ မော်တော်ကားကုမ္ပဏီတစ်ခုမှ ဒီဇိုင်းအင်ဂျင်နီယာ
- လောင်စာဆီထိရောက်မှုနှင့် ဓာတ်ငွေ့ထုတ်လွှတ်မှုကို လျှော့ချရန် ကွန်ပေါင်းနှင့် ပလတ်စတစ်များကဲ့သို့ ပေါ့ပါးသောပစ္စည်းများဆီသို့ အရှိန်အဟုန်မြင့်လာစေရန် Smith မှ ပြောကြားခဲ့ပါသည်။
- ဒီဇိုင်းလုပ်ငန်းစဉ်တွင် Simulation ဆော့ဖ်ဝဲလ်ကို အသုံးပြုခြင်းသည် ပိုမိုထိရောက်ပြီး ကုန်ကျစရိတ်သက်သာသော ထုတ်ကုန်ဖွံ့ဖြိုးတိုးတက်မှုကို ရရှိစေခြင်းဖြင့် ပိုမိုရေပန်းစားလာကြောင်း သူမက မှတ်ချက်ပြုခဲ့သည်။
- စိန်ခေါ်မှုများနှင့် ပတ်သက်၍ မော်တော်ယာဥ်အစိတ်အပိုင်းများ၏ ရှုပ်ထွေးမှုများ တိုးလာခြင်းနှင့် ပိုမိုတိကျသော ထုတ်လုပ်မှုလုပ်ငန်းစဉ်များ လိုအပ်ကြောင်း သူမက ပြောကြားခဲ့သည်။
ကျွမ်းကျင်သူ 3- Injection Molding Company မှ အရည်အသွေးထိန်းချုပ်ရေးမန်နေဂျာ Bob Johnson
- မော်တော်ယာဥ်လုပ်ငန်းတွင် အရည်အသွေးထိန်းချုပ်မှုသည် အရေးကြီးကြောင်း Johnson မှ ပြောကြားခဲ့ပါသည်။ အသေးစားချို့ယွင်းချက်များပင်လျှင် ဘေးကင်းမှုနှင့် လုပ်ဆောင်နိုင်စွမ်းကို ထိခိုက်နိုင်သည်။
- အလိုအလျောက် စစ်ဆေးရေးစနစ်များကဲ့သို့သော နည်းပညာဆိုင်ရာ တိုးတက်မှုများသည် ပိုမိုထိရောက်ပြီး တိကျသော အရည်အသွေးထိန်းချုပ်မှုလုပ်ငန်းစဉ်များကို ခွင့်ပြုပေးထားကြောင်း ၎င်းက မှတ်ချက်ပြုခဲ့သည်။
- စိန်ခေါ်မှုများနှင့် ပတ်သက်၍ ၎င်းက အရည်အသွေးမြင့် စံချိန်စံညွှန်းများကို ထိန်းသိမ်းထားစဉ် ထုတ်လုပ်မှု မြန်ဆန်သည့် လိုအပ်ချက် တိုးလာကြောင်း ၎င်းက ပြောကြားခဲ့သည်။
ကျွမ်းကျင်ပညာရှင် 4- ဆာရာလီ၊ Injection Molding ကုမ္ပဏီတစ်ခုမှ အရောင်းကိုယ်စားလှယ်
- ရေရှည်တည်တံ့မှုနှင့် ကုန်ကျစရိတ်သက်သာမှုတို့ကို ကြီးထွားလာစေရန် အာရုံစိုက်ခြင်းဖြင့် ဖောက်သည်များ၏ တောင်းဆိုမှုများ အဆက်မပြတ် တိုးတက်ပြောင်းလဲလာကြောင်း Lee က ပြောကြားခဲ့သည်။
- နောက်ဆုံးထုတ်ကုန်သည် လိုအပ်သော စံချိန်စံညွှန်းများနှင့် မျှော်မှန်းချက်များ ပြည့်မီကြောင်း သေချာစေရန် ထုတ်လုပ်သူနှင့် ဖောက်သည်များကြား ဆက်သွယ်ရေးနှင့် ပူးပေါင်းဆောင်ရွက်ခြင်းသည် အရေးကြီးကြောင်း သူမက မှတ်ချက်ပြုခဲ့သည်။ စိန်ခေါ်မှုများနှင့် ပတ်သက်၍ လုပ်ငန်းနယ်ပယ်တွင် ပြိုင်ဆိုင်မှုများ တိုးလာခြင်းနှင့် တီထွင်ဆန်းသစ်မှုနှင့် အရည်အသွေးအားဖြင့် ၎င်းတို့ကိုယ်သူတို့ ကွဲပြားစေရန် ဆေးထိုးပုံသွင်းသည့်ကုမ္ပဏီများ လိုအပ်ကြောင်း ပြောကြားခဲ့သည်။
ကောက်ချက်
မော်တော်ယာဥ်လုပ်ငန်းသည် ဆက်လက်တိုးတက်ပြောင်းလဲလာသည်နှင့်အမျှ ဆေးထိုးပုံသွင်းခြင်းသည် အရည်အသွေးမြင့်ပလပ်စတစ်အစိတ်အပိုင်းများထုတ်လုပ်ရန်အတွက် အရေးကြီးသောကုန်ထုတ်လုပ်ငန်းစဉ်တစ်ခုအဖြစ် ဆက်လက်တည်ရှိနေပါသည်။ အတွင်းပိုင်း သို့မဟုတ် အပြင်ပိုင်းပဲဖြစ်ဖြစ်၊ ဆေးထိုးပုံသွင်းခြင်းသည် ထူးထူးခြားခြား ဒီဇိုင်းလွတ်လပ်မှု၊ ကုန်ကျစရိတ်သက်သာမှုနှင့် ရေရှည်တည်တံ့မှု အကျိုးကျေးဇူးများကို ပေးဆောင်သည်။ ထုတ်လုပ်သူများသည် မော်တော်ယာဥ်ပလပ်စတစ် အစိတ်အပိုင်းများကို ဆေးထိုးပုံသွင်းခြင်း၏ ရှုပ်ထွေးရှုပ်ထွေးမှုများကို နားလည်ခြင်းဖြင့် ဆန်းသစ်ပြီး ယုံကြည်စိတ်ချရသော မော်တော်ကားများကို ဖန်တီးရန်အတွက် ဖြစ်နိုင်ခြေအသစ်များကို သော့ဖွင့်နိုင်ပါသည်။ ဆေးထိုးပုံသွင်းခြင်းလောကနှင့် မော်တော်ယာဥ်လုပ်ငန်းအပေါ် ၎င်း၏အကျိုးသက်ရောက်မှုများကို နောက်ထပ်ထိုးထွင်းသိမြင်နိုင်စေရန်အတွက် ဤဘလော့ဂ်ကို ဆက်လက်နားဆင်ပါ။