Thermoplastic Injection Molding ၊
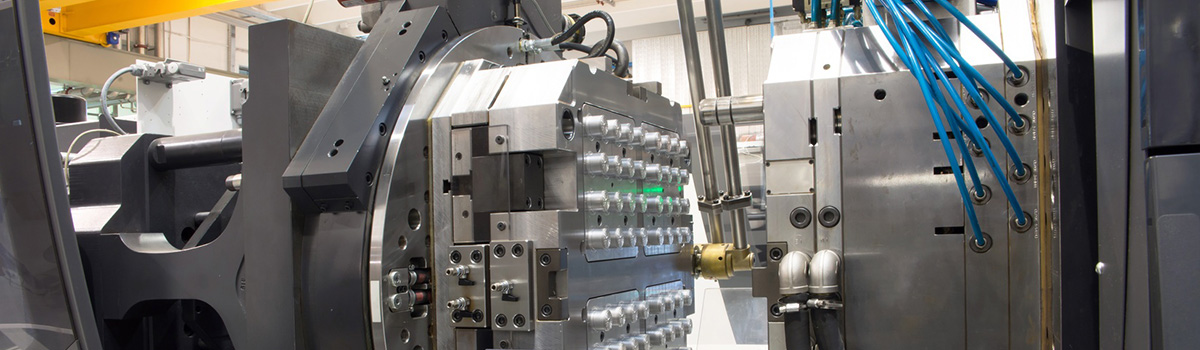
သာမိုပလတ်စတစ်ဆေးထိုးခြင်းဆိုသည်မှာ စက်မှုလုပ်ငန်းမျိုးစုံအတွက် ပလတ်စတစ်အစိတ်အပိုင်းများကို ဖန်တီးရာတွင် အသုံးပြုသည့် ရေပန်းစားသော ကုန်ထုတ်လုပ်မှုလုပ်ငန်းစဉ်တစ်ခုဖြစ်သည်။ ဤလုပ်ငန်းစဉ်တွင် ပလပ်စတစ်အမှုန့်များကို အရည်ပျော်ပြီး သုံးဖက်မြင်ပုံသဏ္ဍာန်တစ်ခုအဖြစ် ပုံဖော်ရန်အတွက် မှိုတစ်ခုထဲသို့ ထိုးသွင်းခြင်းတို့ ပါဝင်ပါသည်။ သာမိုပလပ်စတစ်ဆေးထိုးပုံသွင်းခြင်းသည် တင်းကျပ်စွာခံနိုင်ရည်ရှိသော အရည်အသွေးမြင့်ပလပ်စတစ်အစိတ်အပိုင်းများ အမြောက်အမြားထုတ်လုပ်ရန်အတွက် အလွန်ထိရောက်ပြီး ကုန်ကျစရိတ်သက်သာပါသည်။ ဤပြည့်စုံသောလမ်းညွှန်ချက်သည် ၎င်း၏အားသာချက်များနှင့် အားနည်းချက်များ၊ အသုံးပြုထားသော သာမိုပလတ်စတစ်အမျိုးအစားများ၊ ဆေးထိုးခြင်းလုပ်ငန်းစဉ်၊ ဒီဇိုင်းထည့်သွင်းစဉ်းစားမှုများအပါအဝင် အမျိုးမျိုးသော ရှုထောင့်များကို စူးစမ်းလေ့လာပါမည်။
Thermoplastic Injection Molding ၏သမိုင်း
သာမိုပလတ်စတစ်ဆေးထိုးခြင်း၏သမိုင်းကြောင်းသည် ရာစုနှစ်တစ်ခုကျော်ကြာ နည်းပညာတိုးတက်မှုများ၊ ပစ္စည်းဖွံ့ဖြိုးတိုးတက်မှုနှင့် စက်မှုအသုံးချမှုဆိုင်ရာ အသုံးချမှုများ၏သမိုင်းကြောင်းဖြစ်သည်။ ဆယ်လူလွိုက်ပုံသွင်းခြင်းလုပ်ငန်းစဉ်အဖြစ် ၎င်း၏နှိမ့်ချမှုအစမှ ယနေ့ခေတ် ခေတ်မီဆန်းသစ်သောနည်းပညာအထိ၊ ဆေးထိုးပုံသွင်းခြင်းသည် အရေးပါသောကုန်ထုတ်နည်းစနစ်တစ်ခုအဖြစ် ဆက်လက်တည်ရှိနေကာ ဆန်းသစ်တီထွင်မှုနှင့် စက်မှုလုပ်ငန်းအမျိုးမျိုးကို ပုံဖော်ရန် တွန်းအားပေးလျက်ရှိသည်။
- အစောပိုင်းတိုးတက်မှုများ-John Wesley Hyatt နှင့် သူ၏အစ်ကို Isaiah တို့သည် 19 ရာစုနှောင်းပိုင်းတွင် သာမိုပလတ်စတစ်ဆေးထိုးခြင်း၏ ဇစ်မြစ်ကို ခြေရာခံပြီး ပထမဆုံး လက်တွေ့ဆေးထိုးစက်ကို တီထွင်ခဲ့သည်။ 1872 ခုနှစ်တွင် ၎င်းတို့သည် မှိုအပေါက်ထဲသို့ celluloid ထိုးသွင်းရန် ပလပ်ဂျာကို အသုံးပြု၍ အစိုင်အခဲအရာဝတ္ထုများကို ဖန်တီးခဲ့သည်။ ဤအောင်မြင်မှုသည် ခေတ်မီဆေးထိုးခြင်းလုပ်ငန်းစဉ်အတွက် အုတ်မြစ်ချပေးခဲ့သည်။
- ပစ္စည်းများဆိုင်ရာတိုးတက်မှုများ20 ရာစုအစောပိုင်းတွင်၊ ဓာတုပိုလီမာအသစ်များကို မိတ်ဆက်ခြင်းသည် ဆေးထိုးပုံသွင်းခြင်းအတွက် ဖြစ်နိုင်ခြေအသစ်များကို ဖွင့်လှစ်ပေးခဲ့သည်။ Bakelite၊ ဖီနိုလစ်အစေး၊ ၎င်း၏အလွန်ကောင်းမွန်သောလျှပ်စစ်လျှပ်ကာပစ္စည်းများကြောင့် ပုံသွင်းရန် ရေပန်းစားသောပစ္စည်းဖြစ်လာခဲ့သည်။ 1930 နှင့် 1940 ခုနှစ်များတစ်လျှောက်တွင် ပိုလီမာ ဓာတုဗေဒဆိုင်ရာ တိုးတက်မှုများက ဆေးထိုးပုံသွင်းခြင်းအတွက် သင့်လျော်သော ပစ္စည်းအကွာအဝေးကို ပိုမိုချဲ့ထွင်စေသည့် polystyrene နှင့် polyethylene ကဲ့သို့သော အခြားသော သာမိုပလတ်စတစ်များ ဖွံ့ဖြိုးတိုးတက်လာစေခဲ့သည်။
- စက်မှုမွေးစားခြင်း- ထုတ်လုပ်သူများသည် ၎င်း၏ကုန်ကျစရိတ်ထိရောက်မှုနှင့် ဘက်စုံသုံးနိုင်မှုကို အသိအမှတ်ပြုသောကြောင့် သာမိုပလတ်စတစ်ဆေးထိုးခြင်းအား ကျယ်ကျယ်ပြန့်ပြန့်လက်ခံလာခဲ့သည်။ ပိုမိုမြန်ဆန်သော စက်ဝန်းအချိန်များနှင့် ထုတ်လုပ်မှုပမာဏကို တိုးမြှင့်ရန်အတွက် ခွင့်ပြုထားသော ဖိအားမြင့်စက်များကို မိတ်ဆက်ခြင်း။ ရလဒ်အနေဖြင့် တစ်ကိုယ်ရေသုံးနှင့် စက်မှုလုပ်ငန်းသုံးအတွက် ထုတ်ကုန်မျိုးစုံရွေးချယ်မှု ပေါ်ပေါက်လာသည်။ ၎င်းတို့တွင် ကားအစိတ်အပိုင်းများ၊ အိမ်သုံးပစ္စည်းများနှင့် ကစားစရာများ ပါဝင်သည်။
- နည်းပညာဆိုင်ရာ ဆန်းသစ်တီထွင်မှုများဆယ်စုနှစ်များအတွင်း ဆေးထိုးပုံသွင်းနည်းပညာသည် ဆက်လက်တိုးတက်နေပါသည်။ 1960 ခုနှစ်များတွင် ကွန်ပြူတာ ထိန်းချုပ်စက်များ ပေါ်ပေါက်လာပြီး ပုံသွင်းခြင်း လုပ်ငန်းစဉ်ကို တိကျစွာ ထိန်းချုပ်နိုင်ခဲ့သည်။ 1980 ခုနှစ်များတွင် hot runner systems များကို မိတ်ဆက်ခြင်းသည် အပြေးသမားများနှင့် sprues များလိုအပ်မှုကို ဖယ်ရှားခြင်းဖြင့် အမှိုက်များကို လျှော့ချပြီး စွမ်းဆောင်ရည်ကို တိုးတက်စေသည်။ မကြာသေးမီနှစ်များအတွင်း၊ အလိုအလျောက်စနစ်၊ စက်ရုပ်များနှင့် 3D ပုံနှိပ်ခြင်းဆိုင်ရာ တိုးတက်မှုများသည် ဆေးထိုးပုံသွင်းခြင်းလုပ်ငန်းကို ပိုမိုတော်လှန်ပြောင်းလဲခဲ့ပြီး ရှုပ်ထွေးသောဒီဇိုင်းများကို လုပ်ဆောင်နိုင်ကာ ထုတ်လုပ်မှုအချိန်ကို လျှော့ချပေးခဲ့သည်။
- ရေရှည်တည်တံ့မှုနှင့် ပြန်လည်အသုံးပြုခြင်း-ကြီးထွားလာနေသော သဘာဝပတ်ဝန်းကျင်ဆိုင်ရာ စိုးရိမ်မှုများနှင့်အတူ ဆေးထိုးပုံသွင်းလုပ်ငန်းသည် ရေရှည်တည်တံ့မှုအစီအမံများကို လက်ခံကျင့်သုံးလာခဲ့သည်။ ထုတ်လုပ်သူများသည် ဇီဝအခြေခံနှင့် ပြန်လည်အသုံးပြုသည့် သာမိုပလတ်စတစ်များကို တီထွင်ခဲ့ပြီး ရုပ်ကြွင်းလောင်စာအခြေခံပစ္စည်းများအပေါ် မှီခိုမှုကို လျှော့ချခဲ့သည်။ ထို့အပြင်၊ ပိုမိုကောင်းမွန်သော ပြန်လည်အသုံးပြုသည့်နည်းပညာများသည် စားသုံးသူလွန်နှင့် စက်မှုခေတ်လွန်စွန့်ပစ်ပစ္စည်းများကို ပြန်လည်လုပ်ဆောင်နိုင်စေပြီး သာမိုပလတ်စတစ်ဆေးထိုးခြင်း၏ သဘာဝပတ်ဝန်းကျင်ဆိုင်ရာ ထိခိုက်မှုကို နည်းပါးစေပါသည်။
- အနာဂတ်အလားအလာ-သာမိုပလတ်စတစ်ဆေးထိုးခြင်း၏ အနာဂတ်သည် အလားအလာကောင်းလှသည်။ စက်မှုလုပ်ငန်းသည် အသေးစားအစိတ်အပိုင်းများအတွက် အသေးစားထိုးဆေးပုံသွင်းခြင်း၊ ရှုပ်ထွေးသောအစိတ်အပိုင်းများအတွက် ဘက်စုံနှင့် overmolding နည်းပညာများဖြစ်သည့် ဆန်းသစ်တီထွင်မှုများကို ရှာဖွေနေပြီး လုပ်ငန်းစဉ်စောင့်ကြည့်ခြင်းနှင့် ပိုမိုကောင်းမွန်အောင်လုပ်ဆောင်ခြင်းအတွက် ဉာဏ်ရည်ထက်မြက်သောနည်းပညာများကို ပေါင်းစပ်ထားသည်။ ထို့အပြင်၊ သုတေသီများသည် ဆေးထိုးပုံသွင်းခြင်းကို ပို၍ ရေရှည်တည်တံ့ပြီး စွယ်စုံသုံးနိုင်စေရန် နယ်ပယ်ကို တော်လှန်ပြောင်းလဲရန်အတွက် ဇီဝရုပ်ကြွင်းပစ္စည်းများနှင့် ပေါင်းထည့်ထုတ်လုပ်မှုတို့တွင် တိုးတက်မှုကို မျှော်လင့်ထားသည်။
Thermoplastic Injection Molding ၏ အားသာချက်များ
သာမိုပလတ်စတစ်ဆေးထိုးပုံသွင်းခြင်းသည် ထုတ်လုပ်သူများအတွက် များစွာသော အကျိုးကျေးဇူးများကို ပေးဆောင်သည်။ ၎င်းသည် ဒီဇိုင်းပြောင်းလွယ်ပြင်လွယ်ကို ပံ့ပိုးပေးကာ ရှုပ်ထွေးပြီး အနုစိတ်သော ဒီဇိုင်းများကို အမျိုးမျိုးသောအင်္ဂါရပ်များဖြင့် ပြုလုပ်နိုင်သည်။ လုပ်ငန်းစဉ်သည် ကုန်ကျစရိတ်သက်သာပြီး ပစ္စည်းစွန့်ပစ်မှုနှင့် ယူနစ်ကုန်ကျစရိတ်ကို လျှော့ချပေးသည်။ သာမိုပလပ်စတစ်ဆေးထိုးပုံသွင်းခြင်းသည် အမျိုးမျိုးသောအသုံးအဆောင်များအတွက် ဘက်စုံသုံးနိုင်သော ပစ္စည်းအများအပြားကို ပံ့ပိုးပေးသည်။
- ဒီဇိုင်းပြောင်းလွယ်မှု-သာမိုပလတ်စတစ်ဆေးထိုးပုံသွင်းခြင်း သည် ဒီဇိုင်းပညာရှင်များကို လွတ်လပ်မှုကြီးမားစွာပေးစွမ်းနိုင်သော အောက်ခံညှပ်များ၊ ပါးလွှာသောနံရံများနှင့် ကွဲပြားသောအထူများကဲ့သို့သော အင်္ဂါရပ်များဖြင့် အနုစိတ်ပြီး ရှုပ်ထွေးသော ဒီဇိုင်းများကို ဖန်တီးနိုင်စေပါသည်။
- ကုန်ကျစရိတ်သက်သာခြင်း လုပ်ငန်းစဉ်သည် အလွန်ထိရောက်ပြီး ပစ္စည်းစွန့်ပစ်မှုနှင့် ယူနစ်ကုန်ကျစရိတ်များကို လျှော့ချပေးသည်။ အစိတ်အပိုင်းများစွာကို တစ်ပြိုင်နက် ပုံသွင်းခြင်းနှင့် အမြန်ထုတ်လုပ်မှု လည်ပတ်ခြင်းများသည် ကုန်ကျစရိတ်ကို သက်သာစေပါသည်။
- ဘက်စုံသုံးပစ္စည်း- သာမိုပလတ်စတစ်ဆေးထိုးပုံသွင်းခြင်းသည် ကျယ်ပြန့်သောပစ္စည်းများကို ပံ့ပိုးပေးသောကြောင့် ထုတ်လုပ်သူသည် တောင့်တင်းသော သို့မဟုတ် ပြောင်းလွယ်ပြင်လွယ်၊ ဖောက်ထွင်းမြင်နိုင်သော သို့မဟုတ် ရောင်ပြန်ဟပ်ကာ ဓာတုဗေဒခံနိုင်ရည်ရှိသော ပစ္စည်းများအပါအဝင် အပလီကေးရှင်းတစ်ခုစီအတွက် အသင့်တော်ဆုံးရွေးချယ်မှုကို ရွေးချယ်နိုင်စေပါသည်။
- ကြံ့ခိုင်မှုနှင့် တာရှည်ခံမှု-ထိုးသွင်းပုံသွင်းထားသည့် သာမိုပလပ်စတစ်များသည် မြင့်မားသော ကြံ့ခိုင်မှု၊ တောင့်တင်းမှုနှင့် သက်ရောက်မှုခံနိုင်ရည်စသည့် ကောင်းမွန်သော စက်ပိုင်းဆိုင်ရာ ဂုဏ်သတ္တိများကို ပြသနိုင်သည်။ ဖန် သို့မဟုတ် ကာဗွန်ဖိုင်ဘာများကဲ့သို့ အားဖြည့်ရွေးချယ်မှုများသည် ဤဂုဏ်သတ္တိများကို ပိုမိုတိုးတက်စေပါသည်။
- ညီညွတ်မှုနှင့် အရည်အသွေး-ထိုးသွင်းပုံသွင်းခြင်းသည် တစ်စိတ်တစ်ပိုင်း အရည်အသွေးနှင့် အတိုင်းအတာ တိကျမှုကို သေချာစေပြီး တင်းကျပ်သော သည်းခံမှုနှင့် ယုံကြည်စိတ်ချရသော ထုတ်ကုန်များကို ပေးဆောင်သည်။ လုပ်ငန်းစဉ်သည် ချောမွေ့ပြီး တစ်ပြေးညီသော မျက်နှာပြင်ကို ပံ့ပိုးပေးသည့်အပြင် အပိုအချောသတ်ခြင်းလုပ်ငန်းများအတွက် လိုအပ်မှုကို ဖယ်ရှားပေးပါသည်။
- ချဲ့ထွင်နိုင်မှုနှင့် အစုလိုက်အပြုံလိုက် ထုတ်လုပ်မှု-ဆေးထိုးပုံသွင်းခြင်းအား ထုထည်အနိမ့်မှ အမြင့်အထိ အတိုင်းအတာအထိ ချဲ့ထွင်နိုင်ပြီး အစုလိုက်အပြုံလိုက် ထုတ်လုပ်မှုအတွက် သင့်လျော်သည်။ ထုတ်လုပ်သူများမှိုကို ဖန်တီးပြီးသည်နှင့် ၎င်းတို့သည် ကွဲပြားမှုအနည်းဆုံးဖြင့် ထပ်တူထပ်မျှသော အစိတ်အပိုင်းများစွာကို ထုတ်လုပ်နိုင်သည်။
- ပေါင်းစည်းမှုနှင့် စည်းဝေးပွဲ-ထိုးသွင်းပုံသွင်းထားသော အစိတ်အပိုင်းများသည် အစိတ်အပိုင်းများစွာကို တစ်ပိုင်းတည်းတွင် ပေါင်းစပ်နိုင်ပြီး အပိုတပ်ဆင်ခြင်းလုပ်ငန်းစဉ်များ လိုအပ်မှုကို လျှော့ချနိုင်သည်။ ဤပေါင်းစပ်မှုသည် ထုတ်ကုန်စွမ်းဆောင်ရည်ကို မြှင့်တင်ပေးသည်၊ တပ်ဆင်ချိန်ကို လျှော့ချပေးပြီး ကုန်ကျစရိတ်များကို လျှော့ချပေးသည်။
- သဘာဝပတ်ဝန်းကျင်အားမပျက်စီး:ဆေးထိုးပုံသွင်းခြင်းလုပ်ငန်းသည် ရေရှည်တည်တံ့မှုအပေါ် အာရုံစိုက်မှုကို တိုးမြင့်လာစေသည်။ ဇီဝအခြေခံနှင့် ပြန်လည်အသုံးပြုသည့်ပစ္စည်းများ ရရှိနိုင်မှုသည် ပတ်ဝန်းကျင်နှင့် သဟဇာတဖြစ်သော ထုတ်ကုန်များကို ထုတ်လုပ်နိုင်စေပါသည်။ သာမိုပလတ်စတစ်များကို ထိရောက်စွာအသုံးပြုခြင်းနှင့် ပြန်လည်အသုံးပြုခြင်းသည် ပိုမိုစိမ်းလန်းသောထုတ်လုပ်မှုလုပ်ငန်းစဉ်ကို အထောက်အကူပြုပါသည်။
ဤအကျိုးခံစားခွင့်များသည် ရှုပ်ထွေးသောထုတ်ကုန်လိုအပ်ချက်များအတွက် အရည်အသွေးမြင့်၊ ကုန်ကျစရိတ်သက်သာပြီး သဘာဝပတ်ဝန်းကျင်နှင့် သဟဇာတဖြစ်မှုဖြေရှင်းနည်းများကို အမျိုးမျိုးသောစက်မှုလုပ်ငန်းများတွင် ကျယ်ကျယ်ပြန့်ပြန့် လက်ခံကျင့်သုံးသည့် ကုန်ထုတ်လုပ်မှုနည်းလမ်းတစ်ခု ဖြစ်လာစေသည်။
Thermoplastic Injection Molding ၏ အားနည်းချက်များ
သာမိုပလတ်စတစ်ဆေးထိုးပုံသွင်းခြင်းသည် အားသာချက်များစွာကို ပေးစွမ်းသော်လည်း အားနည်းချက်များစွာရှိသည်။ ထုတ်လုပ်သူများသည် ၎င်းတို့၏ သီးခြားအသုံးချပရိုဂရမ်အတွက် သာမိုပလတ်စတစ်ဆေးထိုးခြင်း၏ သင့်လျော်မှုကို ဆုံးဖြတ်ရန် ဤအချက်များအား ဂရုတစိုက်အကဲဖြတ်ပြီး ၎င်းတို့အား အကျိုးကျေးဇူးများနှင့် ချိန်ညှိရန် လိုအပ်သည်။
- မြင့်မားသော ကနဦးရင်းနှီးမြှုပ်နှံမှု- သာမိုပလတ်စတစ်ဆေးထိုးခြင်းလုပ်ငန်းကို ထူထောင်ခြင်းလုပ်ငန်းသည် မှိုဒီဇိုင်းနှင့် ထုတ်လုပ်ခြင်းနှင့် အထူးပြုစက်ပစ္စည်းများဝယ်ယူခြင်းတွင် သိသာထင်ရှားသော ကနဦးရင်းနှီးမြုပ်နှံမှု လိုအပ်သည်။ မှိုများဖန်တီးခြင်းနှင့် ကိရိယာတန်ဆာပလာများဖန်တီးခြင်းဆိုင်ရာ ကုန်ကျစရိတ်များသည် အထူးသဖြင့် ရှုပ်ထွေးပြီး အနုစိတ်သောဒီဇိုင်းများအတွက် များပြားနိုင်ပါသည်။
- ဒီဇိုင်းကန့်သတ်ချက်များ- သာမိုပလတ်စတစ်ဆေးထိုးပုံသွင်းခြင်းသည် ဒီဇိုင်းပြောင်းလွယ်ပြင်လွယ်ပေးသော်လည်း အချို့သောကန့်သတ်ချက်များရှိသည်။ ဥပမာအားဖြင့်၊ တစ်စိတ်တစ်ပိုင်းလုံးတွင် တူညီသောနံရံအထူရရှိရန် စိန်ခေါ်မှုဖြစ်နိုင်ပြီး ပစ္စည်းဖြန့်ဖြူးမှုတွင် ကွဲပြားမှုများနှင့် ဖြစ်ပေါ်လာနိုင်သည့် ဖွဲ့စည်းပုံဆိုင်ရာ အားနည်းချက်များကို ဖြစ်ပေါ်စေသည်။ ထို့အပြင်၊ အောက်ခံဖြတ်တောက်မှုများ သို့မဟုတ် ရှုပ်ထွေးသော ဂျီသြမေတြီများရှိနေခြင်းသည် အပိုမှိုအင်္ဂါရပ်များ သို့မဟုတ် ဆင့်ပွားလုပ်ဆောင်မှုများကို အသုံးပြုခြင်း၊ ကုန်ကျစရိတ်နှင့် ထုတ်လုပ်မှုအချိန်ကို တိုးမြှင့်ရန် လိုအပ်နိုင်သည်။
- ကြာမြင့်စွာကာလ -ဆေးထိုးပုံသွင်းခြင်းအတွက် မှိုများကို ဒီဇိုင်းထုတ်ခြင်းနှင့် ပုံဖော်ခြင်းလုပ်ငန်းစဉ်သည် အချိန်ကုန်နိုင်ပြီး ထုတ်ကုန်ဖွံ့ဖြိုးတိုးတက်မှုအတွက် ခဲချိန်ပိုကြာစေသည်။ ဒီဇိုင်းပြန်ဆိုခြင်းလုပ်ငန်းစဉ်၊ မှိုထုတ်လုပ်ခြင်းနှင့် စမ်းသပ်ခြင်းသည် အလုံးစုံထုတ်လုပ်မှုအချိန်ဇယားအတွက် သိသာထင်ရှားသောအချိန်ကို ပေါင်းထည့်နိုင်ပြီး၊ တင်းကျပ်သောသတ်မှတ်ရက်များရှိသော ပရောဂျက်များအတွက် မသင့်လျော်နိုင်ပါ။
- ပစ္စည်းရွေးချယ်မှု ကန့်သတ်ချက်များ-သာမိုပလတ်စတစ်ဆေးထိုးပုံသွင်းခြင်းသည် ကျယ်ပြန့်သောပစ္စည်းများကို ပံ့ပိုးပေးသော်လည်း အချို့သောကန့်သတ်ချက်များနှင့် ကန့်သတ်ချက်များရှိသည်။ အချို့သောပစ္စည်းများသည် သီးခြားလုပ်ဆောင်မှုလိုအပ်ချက်များ သို့မဟုတ် ရရှိနိုင်မှုအကန့်အသတ်ရှိနိုင်သည်၊ ဒီဇိုင်းရွေးချယ်မှုနှင့် ပစ္စည်းရွေးချယ်မှုအပေါ် သက်ရောက်မှုရှိနိုင်သည်။
- အပိုင်းအရွယ်အစား ကန့်သတ်ချက်များ-ဆေးထိုးပုံသွင်းစက်များသည် စက်၏ရုပ်ပိုင်းဆိုင်ရာအရွယ်အစားနှင့် ၎င်းတို့လိုက်လျောညီထွေရှိနိုင်သော မှိုအရွယ်အစားနှစ်မျိုးလုံးတွင် အရွယ်အစားကန့်သတ်ချက်များရှိသည်။ ကြီးမားသော အစိတ်အပိုင်းများ ထုတ်လုပ်ရာတွင် အထူးပြု စက်ကိရိယာများ သို့မဟုတ် အစားထိုး ထုတ်လုပ်ရေး နည်းလမ်းများ လိုအပ်နိုင်သည်။
- သဘာဝပတ်ဝန်းကျင် ထိခိုက်မှု-စက်မှုလုပ်ငန်းသည် ရေရှည်တည်တံ့မှုဆီသို့ ဦးတည်လုပ်ဆောင်နေချိန်တွင်၊ သာမိုပလတ်စတစ်ဆေးထိုးခြင်းလုပ်ငန်းစဉ်သည် အပိုင်းအစများနှင့် ကြေးတံများအပါအဝင် စွန့်ပစ်ပစ္စည်းများကို ထုတ်လုပ်နေဆဲဖြစ်သည်။ သဘာဝပတ်ဝန်းကျင် ထိခိုက်မှု အနည်းဆုံးဖြစ်စေရန်အတွက် ဤပစ္စည်းများကို စနစ်တကျ စွန့်ပစ်ခြင်းနှင့် ပြန်လည်အသုံးပြုခြင်းတို့သည် လိုအပ်ပါသည်။
- Process Optimization ၏ရှုပ်ထွေးမှု-သာမိုပလတ်စတစ်ဆေးထိုးခြင်းအတွက် အကောင်းမွန်ဆုံး လုပ်ငန်းစဉ်ဘောင်များကို ရရှိရန်မှာ ရှုပ်ထွေးပြီး အချိန်ကုန်နိုင်သည်။ ထုတ်လုပ်သူများသည် တစ်သမတ်တည်းရှိသော အစိတ်အပိုင်းအရည်အသွေးကို သေချာစေရန်နှင့် ချို့ယွင်းချက်များကို အနည်းဆုံးဖြစ်စေရန် အပူချိန်၊ ဖိအား၊ အအေးနှုန်းနှင့် စက်လည်ပတ်ချိန်များကို ဂရုတစိုက် ထိန်းချုပ်ပြီး အကောင်းဆုံးဖြစ်အောင် လုပ်ဆောင်ရပါမည်။
Injection Molding တွင်အသုံးပြုသော Thermoplastics အမျိုးအစားများ
ဤအရာများသည် ဆေးထိုးပုံသွင်းရာတွင် အသုံးများသော သာမိုပလတ်စတစ်များ၏ နမူနာအနည်းငယ်မျှသာဖြစ်သည်။ ပစ္စည်းတစ်ခုစီတွင် ထူးခြားသောဂုဏ်သတ္တိများရှိပြီး ခွန်အား၊ ပြောင်းလွယ်ပြင်လွယ်၊ ဓာတုခံနိုင်ရည်ရှိမှု၊ ပွင့်လင်းမြင်သာမှုနှင့် ကုန်ကျစရိတ်တို့အပေါ် အခြေခံ၍ သီးခြားအသုံးချမှုများအတွက် သင့်လျော်စေသည်။ ထုတ်လုပ်သူများသည် ၎င်းတို့၏ ဆေးထိုးပုံသွင်းခြင်း ပရောဂျက်များအတွက် သင့်လျော်သော သာမိုပလတ်စတစ်ကို ရွေးချယ်သည့်အခါ ဤဂုဏ်သတ္တိများနှင့် လိုအပ်ချက်များကို ထည့်သွင်းစဉ်းစားသင့်သည်။
- Polypropylene (PP):Polypropylene သည် ဆေးထိုးပုံသွင်းရာတွင် အသုံးများသော ဘက်စုံသုံး သာမိုပလပ်စတစ်ဖြစ်သည်။ ၎င်းသည် အလွန်ကောင်းမွန်သော ဓာတုခံနိုင်ရည်၊ သိပ်သည်းဆနည်းပြီး သက်ရောက်မှုအားကောင်းသည်။ PP (polypropylene) တွင် ထုပ်ပိုးမှု၊ မော်တော်ယာဥ်အစိတ်အပိုင်းများ၊ အိမ်သုံးပစ္စည်းများနှင့် ဆေးဘက်ဆိုင်ရာ ကိရိယာများတွင် ကျယ်ပြန့်သော အသုံးချပရိုဂရမ်များ ပါရှိသည်။
- Polyethylene (PE):Polyethylene သည် ဆေးထိုးပုံသွင်းရာတွင် အသုံးများသော သာမိုပလတ်စတစ်တစ်မျိုးဖြစ်သည်။ High-density polyethylene (HDPE) နှင့် low-density polyethylene (LDPE) ကဲ့သို့သော ပုံစံအမျိုးမျိုးဖြင့် ရရှိနိုင်ပါသည်။ PE သည် ပုလင်းများ၊ ကွန်တိန်နာများနှင့် ပိုက်များအတွက် သင့်လျော်သော ဓာတုခံနိုင်ရည်၊ ခိုင်ခံ့မှုနှင့် ပျော့ပြောင်းမှုတို့ကို ပေးစွမ်းသည်။
- Polystyrene (PS):Polystyrene သည် ၎င်း၏ ရှင်းလင်းပြတ်သားမှု၊ တောင့်တင်းမှုနှင့် တတ်နိုင်မှုတို့ကြောင့် လူသိများသော စွယ်စုံရအပူပလတ်စတစ်တစ်မျိုးဖြစ်သည်။ ထုပ်ပိုးမှု၊ လူသုံးကုန်ပစ္စည်းများနှင့် တစ်ခါသုံးထုတ်ကုန်များတွင် အသုံးများသည်ကို ၎င်းသည် တွေ့ရှိသည်။ PS (polystyrene) သည် လျင်မြန်စွာ စီမံဆောင်ရွက်ပေးနိုင်ပြီး ကောင်းမွန်သော အတိုင်းအတာ တည်ငြိမ်မှုကို ပေးစွမ်းနိုင်သော်လည်း ၎င်းသည် ကြွပ်ဆတ်ပြီး ပတ်ဝန်းကျင်ဆိုင်ရာ ဖိစီးမှုကွဲအက်မှုကို ခံနိုင်ရည်ရှိနိုင်သည်။
- Acrylonitrile Butadiene Styrene (ABS)- ABS သည် ၎င်း၏အလွန်ကောင်းမွန်သော သက်ရောက်မှုခံနိုင်ရည်နှင့် တာရှည်ခံမှုအတွက် လူသိများသော လူကြိုက်များသော သာမိုပလပ်စတစ်ဖြစ်သည်။ ၎င်းသည် မော်တော်ယာဥ်အစိတ်အပိုင်းများ၊ အီလက်ထရွန်းနစ်အိမ်ရာများနှင့် အရုပ်များအတွက် သင့်လျော်သော စွယ်စုံသုံးပစ္စည်းကို ဖန်တီးရန်အတွက် acrylonitrile၊ butadiene နှင့် styrene တို့၏ ဂုဏ်သတ္တိများကို ပေါင်းစပ်ထားသည်။
- Polyvinyl Chloride (PVC)- PVC သည် ၎င်း၏ အလွန်ကောင်းမွန်သော ဓာတုခံနိုင်ရည်၊ တာရှည်ခံမှုနှင့် ကုန်ကျစရိတ် သက်သာခြင်းကြောင့် လူသိများသော အသုံးများသော သာမိုပလပ်စတစ်ဖြစ်သည်။ အသုံးပြုထားသော ဖော်မြူလာနှင့် ဖြည့်စွက်ပစ္စည်းများပေါ်မူတည်၍ ၎င်းသည် တောင့်တင်းခြင်း သို့မဟုတ် ပြောင်းလွယ်ပြင်လွယ်ရှိနိုင်သည်။ PVC (polyvinyl chloride) သည် ဆောက်လုပ်ရေး၊ လျှပ်စစ်ကာရံမှု၊ ကျန်းမာရေးစောင့်ရှောက်မှု ထုတ်ကုန်များနှင့် ထုပ်ပိုးမှုတို့တွင် အသုံးများသည်ကို တွေ့ရှိသည်။
- ပိုလီကာဗွန်နိတ် (PC): ပိုလီကာဗွန်နိတ်သည် ထူးကဲသောအကျိုးသက်ရောက်မှုနှင့် အပူဒဏ်ကို ခံနိုင်ရည်ရှိသော ဖောက်ထွင်းမြင်ရသော သာမိုပလတ်စတစ်ဖြစ်သည်။ မော်တော်ယာဥ်အစိတ်အပိုင်းများ၊ ဘေးကင်းရေးဦးထုပ်ဆောင်းခြင်းနှင့် အီလက်ထရွန်းနစ် မျက်နှာပြင်များကဲ့သို့သော အလင်းပိုင်းရှင်းလင်းမှုလိုအပ်သည့် အက်ပ်များတွင် အသုံးများသောအသုံးပြုမှုများကို တွေ့ရှိရသည်။
- နိုင်လွန် (Polyamide):နိုင်လွန်သည် ခိုင်ခံ့ပြီး တာရှည်ခံသော သာမိုပလတ်စတစ်ဖြစ်ပြီး ၎င်း၏ အလွန်ကောင်းမွန်သော စက်ပိုင်းဆိုင်ရာ ဂုဏ်သတ္တိများနှင့် ဓာတုဗေဒခံနိုင်ရည်အတွက် လူသိများသည်။ မော်တော်ယာဥ်အစိတ်အပိုင်းများ၊ စက်မှုအစိတ်အပိုင်းများနှင့် လူသုံးကုန်ပစ္စည်းများကဲ့သို့ မြင့်မားသော ကြံ့ခိုင်မှုကို လိုအပ်သည့် အပလီကေးရှင်းများတွင် အသုံးများသောအသုံးပြုမှုများကို တွေ့ရှိရသည်။
- Polyethylene Terephthalate (PET)-PET သည် ပုလင်းများ၊ ကွန်တိန်နာများနှင့် ထုပ်ပိုးပစ္စည်းများကို ထုတ်လုပ်ရန်အတွက် ရေပန်းစားသော သာမိုပလတ်စတစ်ဖြစ်သည်။ ၎င်းသည် ကောင်းမွန်သော ရှင်းလင်းပြတ်သားမှု၊ ဓာတုခံနိုင်ရည်နှင့် အတားအဆီးဂုဏ်သတ္တိများကို ပေးစွမ်းသောကြောင့် အစားအစာနှင့် အဖျော်ယမကာအသုံးပြုမှုများအတွက် သင့်လျော်သည်။
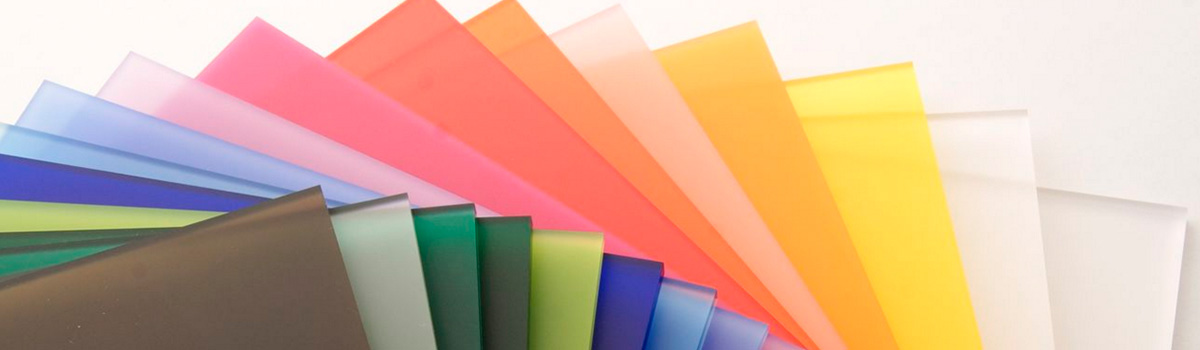
Injection Molding တွင်အသုံးပြုသော သာမိုပလတ်စတစ်များ၏ ဂုဏ်သတ္တိများ
သာမိုပလတ်စတစ်များ၏ ဤဂုဏ်သတ္တိများသည် သတ်သတ်မှတ်မှတ် ဆေးထိုးပုံသွင်းခြင်းလုပ်ငန်းအတွက် ၎င်းတို့၏ သင့်လျော်မှုကို ဆုံးဖြတ်ရာတွင် အရေးကြီးသော အခန်းကဏ္ဍမှ ပါဝင်ပါသည်။ ထုတ်လုပ်သူများသည် ဤဂုဏ်သတ္တိများကို ဂရုတစိုက်စဉ်းစားပြီး အလိုရှိသော စွမ်းဆောင်ရည်၊ ပတ်ဝန်းကျင်အခြေအနေနှင့် ကုန်ကျစရိတ်လိုအပ်ချက်များအပေါ် အခြေခံ၍ သင့်လျော်သော သာမိုပလတ်စတစ်ကို ရွေးချယ်ရပါမည်။
- စက်မှုဂုဏ်သတ္တိများ:ဆေးထိုးပုံသွင်းရာတွင် အသုံးပြုသည့် သာမိုပလပ်စတစ်များသည် ဆန့်နိုင်အား၊ သက်ရောက်မှုခံနိုင်ရည်နှင့် flexural strength အပါအဝင် အမျိုးမျိုးသော စက်ပိုင်းဆိုင်ရာ ဂုဏ်သတ္တိများကို ပြသနိုင်သည်။ ဤဂုဏ်သတ္တိများသည် အသုံးချမှုဆိုင်ရာ တွန်းအားများကို ခံနိုင်ရည်ရှိမှုနှင့် အမျိုးမျိုးသော အသုံးချမှုများတွင် ၎င်း၏ အလုံးစုံကြာရှည်ခံမှုကို ဆုံးဖြတ်ပေးသည်။
- ဓာတုခံနိုင်ရည်:ဆေးထိုးပုံသွင်းရာတွင် အသုံးပြုသည့် သာမိုပလတ်စတစ်အများအပြားသည် ဓာတုဗေဒပစ္စည်းများ၊ အပျော်ရည်များနှင့် ဆီများကို သိသိသာသာ ခံနိုင်ရည်ရှိသည်။ ဤပိုင်ဆိုင်မှုသည် ကြမ်းတမ်းသောပတ်ဝန်းကျင်များ သို့မဟုတ် အဆိပ်ဖြစ်စေသော အရာများနှင့် ထိတွေ့မှုရှိသော အပလီကေးရှင်းများအတွက် အရေးကြီးပါသည်။
- အပူပိုင်းတည်ငြိမ်မှု-သာမိုပလတ်စတစ်များ၏ အပူတည်ငြိမ်မှုသည် သိသိသာသာ ပျက်စီးခြင်းမရှိဘဲ မြင့်မားသောအပူချိန်ကို ခံနိုင်ရည်ရှိခြင်းကို ရည်ညွှန်းသည်။ အချို့သော သာမိုပလပ်စတစ်များသည် အပူချိန်မြင့်မားသည့်တိုင် ၎င်းတို့၏ စက်ပိုင်းဆိုင်ရာ ဂုဏ်သတ္တိများကို ထိန်းသိမ်းထားနိုင်သောကြောင့် အလွန်ကောင်းမွန်သော အပူခံနိုင်ရည်ရှိကြောင်း ပြသသည်။
- လျှပ်စစ်ဂုဏ်သတ္တိများဆေးထိုးပုံသွင်းရာတွင် အသုံးပြုသည့် သာမိုပလတ်စတစ်များသည် လျှပ်စစ်လျှပ်ကာ၊ လျှပ်ကူးနိုင်မှု သို့မဟုတ် လျှပ်စီးအား အပါအဝင် သီးခြားလျှပ်စစ်ဂုဏ်သတ္တိများ ရှိနိုင်သည်။ ဤဂုဏ်သတ္တိများသည် လျှပ်စစ်နှင့် အီလက်ထရွန်းနစ် လုပ်ငန်းများတွင် အသုံးပြုရန်အတွက် မရှိမဖြစ် လိုအပ်ပြီး ပစ္စည်းများသည် ယုံကြည်စိတ်ချရသော လျှပ်စစ်စွမ်းဆောင်ရည်ကို ပေးဆောင်ရမည်ဖြစ်သည်။
- ပွင့်လင်းမြင်သာမှုနှင့် ရှင်းလင်းမှု-ပိုလီကာဗွန်နိတ် နှင့် PET ကဲ့သို့သော အချို့သော သာမိုပလပ်စတစ်များသည် အလွန်ကောင်းမွန်သော ပွင့်လင်းမြင်သာမှုနှင့် ကြည်လင်ပြတ်သားမှုကို ပေးစွမ်းသောကြောင့် ၎င်းတို့သည် အလင်းဆိုင်ရာ ဂုဏ်သတ္တိများ လိုအပ်သည့် အပလီကေးရှင်းများအတွက် သင့်လျော်စေသည်။ ထုတ်လုပ်သူများသည် ဤပစ္စည်းများကို ဖောက်ထွင်းမြင်ရသော ပြတင်းပေါက်များ၊ မှန်ဘီလူးများနှင့် ပြသမှုများကဲ့သို့သော ထုတ်ကုန်များတွင် အသုံးများသည်။
- ပျော့ပြောင်းမှုနှင့် မာကျောမှု- Flexibility and toughness သည် သက်ရောက်မှုခံနိုင်ရည်နှင့် တာရှည်ခံမှု လိုအပ်သော အသုံးချပလပ်စတစ်များတွင် အသုံးပြုသည့် သာမိုပလတ်စတစ်များ၏ မရှိမဖြစ်လိုအပ်သော ဂုဏ်သတ္တိများဖြစ်သည်။ ABS နှင့် နိုင်လွန်ကဲ့သို့သော သာမိုပလတ်စတစ်အချို့သည် ပြင်းထန်သော ခိုင်ခံ့မှုကို ပေးစွမ်းနိုင်ပြီး ၎င်းတို့ကို ထပ်ခါတလဲလဲ ကွဲအက်မှုမရှိဘဲ ခံနိုင်ရည်ရှိစေသည်။
- အတိုင်းအတာ တည်ငြိမ်မှု-Dimensional Stability ဆိုသည်မှာ အပူချိန်ပြောင်းလဲမှုများအပါအဝင် မတူညီသောအခြေအနေများအောက်တွင် ၎င်း၏ပုံသဏ္ဍာန်နှင့် အရွယ်အစားကို ထိန်းသိမ်းထားနိုင်သည့် အပူချိန်ကို ရည်ညွှန်းသည်။ ကောင်းမွန်သော အတိုင်းအတာတည်ငြိမ်မှုရှိသော ပစ္စည်းများသည် တသမတ်တည်းရှိသော အစိတ်အပိုင်းအတိုင်းအတာများကို သေချာစေပြီး ကွဲထွက်ခြင်း သို့မဟုတ် ပုံပျက်ခြင်းအန္တရာယ်ကို လျော့နည်းစေသည်။
- ဓာတုဆိုင်ရာ လိုက်ဖက်မှု-သာမိုပလတ်စတစ်များ၏ ဓာတုသဟဇာတဖြစ်မှုသည် အက်ဆစ်များ၊ ဘေ့စ်များ၊ နှင့် ပျော်ရည်များအပါအဝင် ဓာတုပစ္စည်းအမျိုးမျိုးနှင့် ပြိုကွဲပျက်စီးမှုကို ခုခံနိုင်စွမ်း သို့မဟုတ် အပြန်အလှန်တုံ့ပြန်နိုင်စွမ်းကို ရည်ညွှန်းသည်။ အကောင်းဆုံးစွမ်းဆောင်ရည်သေချာစေရန်၊ ရည်ရွယ်ထားသောအပလီကေးရှင်းတွင်ကြုံတွေ့ရမည့် သီးခြားဓာတုပတ်ဝန်းကျင်ကို ခံနိုင်ရည်ရှိသော သာမိုပလတ်စတစ်ကို ရွေးချယ်ခြင်းသည် မရှိမဖြစ်လိုအပ်ပါသည်။
- သိပ်သည်းဆ: သာမိုပလတ်စတစ်များသည် အထူအမျိုးမျိုးရှိပြီး ၎င်းတို့၏အလေးချိန်နှင့် အစိတ်အပိုင်းတစ်ခုလုံး၏ ဂုဏ်သတ္တိများကို ထိခိုက်စေနိုင်သည်။ polyethylene ကဲ့သို့သော သိပ်သည်းဆနည်းသောပစ္စည်းများသည် ပေါ့ပါးသောဖြေရှင်းနည်းများကို ပေးစွမ်းနိုင်ပြီး၊ ပိုလီပပလီလင်းကဲ့သို့သော သိပ်သည်းဆမြင့်မားသောပစ္စည်းများသည် ခိုင်ခံ့မှုနှင့် တောင့်တင်းမှုကို ပေးစွမ်းသည်။
ထိုးသွင်းပုံသွင်းခြင်းလုပ်ငန်းစဉ်- အဆင့်ဆင့်
ဆေးထိုးပုံသွင်းခြင်းလုပ်ငန်းစဉ်သည် ဤအဆင့်များအတိုင်းလုပ်ဆောင်ပြီး အရည်အသွေးမြင့် သာမိုပလတ်စတစ်အစိတ်အပိုင်းများကို ထိရောက်ပြီး တိကျစွာထုတ်လုပ်နိုင်စေပါသည်။ တစ်စိတ်တစ်ပိုင်းအတိုင်းအတာ၊ ပစ္စည်းဂုဏ်သတ္တိများနှင့် အလုံးစုံအရည်အသွေးတို့ကို သေချာစေရန်အတွက် အဆင့်တစ်ခုစီတိုင်းကို ဂရုတစိုက်ထိန်းချုပ်မှုနှင့် စောင့်ကြည့်စစ်ဆေးရန် လိုအပ်ပါသည်။
- မှိုဒီဇိုင်းနှင့် ထုတ်လုပ်ခြင်း- ဆေးထိုးပုံသွင်းခြင်း လုပ်ငန်းစဉ်၏ ပထမအဆင့်မှာ မှို၏ ဒီဇိုင်းနှင့် ဖန်တီးမှုဖြစ်သည်။ ထုတ်လုပ်သူများသည် လိုချင်သောအစိတ်အပိုင်းသတ်မှတ်ချက်များရရှိရန် တိကျသောအသေးစိတ်ပုံစံကို ဖန်တီးရပါမည်။ ထို့နောက် ထုတ်လုပ်သူများသည် CNC သို့မဟုတ် လျှပ်စစ်ထုတ်လွှတ်မှုစက် (EDM) ကဲ့သို့သော နည်းအမျိုးမျိုးဖြင့် မှိုကို ဖန်တီးသည်။
- ပစ္စည်းပြင်ဆင်မှု- နောက်တစ်ဆင့်ကတော့ ပုံစံခွက်အဆင်သင့်ဖြစ်ပြီဆိုတာနဲ့ ပြင်ဆင်မှုပါ။ လိုချင်သော ပစ္စည်းဂုဏ်သတ္တိများအပေါ် အခြေခံ၍ သာမိုပလတ်စတစ်အလုံး သို့မဟုတ် granules အား ရွေးချယ်ပြီး hopper တွင် အရည်ပျော်သည်။ ထို့နောက် အော်ပရေတာများသည် ပစ္စည်းကို အရည်ပျော်ပြီး တစ်သားတည်းဖြစ်စေသော ဆေးထိုးစက်၏စည်ထဲသို့ ကျွေးသည်။
- ဆေးထိုး:ဆေးထိုးသည့်အဆင့်တွင်၊ အော်ပရေတာများသည် မြင့်မားသောဖိအားအောက်တွင် မှိုအပေါက်ထဲသို့ သွန်းသော သာမိုပလတ်စတစ်ကို ထိုးသွင်းသည်။ စက်၏ဆေးထိုးယူနစ်သည် အရည်ကျိုထားသောပစ္စည်းများကို နော်ဇယ်မှတဆင့် မှိုထဲသို့ တွန်းပို့သည်။ ပစ္စည်းသည် လိုချင်သောအစိတ်အပိုင်း၏ပုံသဏ္ဍာန်ကိုယူပြီး မှိုပေါက်ကိုဖြည့်သည်။
- အအေးခံခြင်းနှင့် ခိုင်မာစေခြင်း-မှိုဖြည့်ပြီးနောက်၊ အော်ပရေတာများသည် သွန်းသောပလပ်စတစ်ကို အေးပြီး ခိုင်မာစေရန် ခွင့်ပြုသည်။ အအေးခံခြင်းသည် အတိုင်းအတာတည်ငြိမ်မှုနှင့် မှန်ကန်သောအစိတ်အပိုင်းဖွဲ့စည်းမှုရရှိရန်အတွက် အရေးကြီးပါသည်။ အော်ပရေတာများသည် မှိုအတွင်းရှိ လမ်းကြောင်းများမှတစ်ဆင့် အအေးခံခြင်း သို့မဟုတ် အအေးခံပြားများကို အသုံးပြုခြင်းဖြင့် အအေးခံခြင်းလုပ်ငန်းစဉ်ကို ထိန်းချုပ်နိုင်သည်။
- မှိုဖွင့်ခြင်းနှင့် ထုတ်ခြင်း-အော်ပရေတာများသည် မှိုကိုဖွင့်ပြီး ပလတ်စတစ်များ ခိုင်မာသွားသည်နှင့် မှိုပေါက်အတွင်းမှ အစိတ်အပိုင်းကို ထုတ်ပစ်ပါ။ စက်အတွင်းမှ ထုတ်လွှတ်သည့်စနစ်သည် မှိုထဲမှ ဧရိယာကို ဖယ်ရှားရန်အတွက် ပင်ချောင်းများ၊ ထုတ်လွှတ်သည့်ပြားများ သို့မဟုတ် လေထုတ်လွှတ်မှုများအား အသုံးပြုသည်။ မှိုသည် နောက်လာမည့် ဆေးထိုးစက်အတွက် အဆင်သင့်ဖြစ်နေပါပြီ။
- လုပ်ဆောင်ပြီးသည်- ထုတ်လွှတ်ပြီးနောက်၊ အပိုင်းသည် ဖြတ်တောက်ခြင်း၊ ဖယ်ရှားခြင်း သို့မဟုတ် မျက်နှာပြင် အလှဆင်ခြင်းကဲ့သို့သော စီမံဆောင်ရွက်ပြီးနောက် လုပ်ဆောင်ခြင်းများကို လုပ်ဆောင်နိုင်သည်။ ဤအဆင့်များသည် ပိုလျှံနေသောပစ္စည်းကို ဖယ်ရှားရန်၊ ကြမ်းတမ်းသောအနားသတ်များကို ချောမွေ့စေပြီး အစိတ်အပိုင်း၏ နောက်ဆုံးအသွင်အပြင်ကို မြှင့်တင်ပေးသည်။
- အရည်အသွေးစစ်ဆေးရေး: နောက်ဆုံးအဆင့်တွင် ထိုးသွင်းထားသော အစိတ်အပိုင်းများကို အရည်အသွေးစစ်ဆေးခြင်းနှင့် သတ်မှတ်ထားသော လိုအပ်ချက်များနှင့် ပြည့်မီကြောင်း သေချာစေခြင်းတို့ ပါဝင်ပါသည်။ အစိတ်အပိုင်း၏ အရည်အသွေးနှင့် သမာဓိရှိမှုကို စစ်ဆေးရန် ဘက်ပေါင်းစုံမှ တိုင်းတာခြင်း၊ အမြင်စစ်ဆေးခြင်းနှင့် လုပ်ဆောင်မှုဆိုင်ရာ စမ်းသပ်ခြင်းအပါအဝင် အမျိုးမျိုးသော အရည်အသွေးထိန်းချုပ်မှုနည်းပညာများကို အသုံးပြုနိုင်ပါသည်။
- ပြန်လည်အသုံးပြုခြင်းနှင့် ပစ္စည်းပြန်လည်အသုံးပြုခြင်း-ဆေးထိုးပုံသွင်းစဉ်အတွင်း ထုတ်ပေးခဲ့သော ပိုလျှံနေသည့် သို့မဟုတ် အပိုင်းအစများကို ပြန်လည်အသုံးပြုပြီး ပြန်လည်အသုံးပြုနိုင်ပါသည်။ သာမိုပလတ်စတစ်ပစ္စည်းအသစ်အသုံးပြုမှုကို လျှော့ချခြင်းဖြင့် စွန့်ပစ်ပစ္စည်းများကို လျော့နည်းစေပြီး ရေရှည်တည်တံ့မှုကို တိုးတက်စေပါသည်။
Injection Molding တွင် အသုံးပြုသည့် စက်ပစ္စည်း
ဤစက်ပစ္စည်းအစိတ်အပိုင်းများသည် ဆေးထိုးပုံသွင်းခြင်းလုပ်ငန်းစဉ်တွင် သာမိုပလတ်စတစ်ပစ္စည်းကို အရည်ပျော်ခြင်းနှင့် ထိုးသွင်းခြင်းမှ ပုံဖော်ခြင်း၊ အအေးခံခြင်းနှင့် နောက်ဆုံးအပိုင်းကို ထုတ်ခြင်းအထိ ကူညီပေးသည်။ ထိရောက်သော၊ အရည်အသွေးမြင့် ဆေးထိုးပုံသွင်းထုတ်လုပ်ခြင်းအတွက် ဤစက်ပစ္စည်းအစိတ်အပိုင်းများကို သင့်လျော်သောလည်ပတ်မှုနှင့် ပြုပြင်ထိန်းသိမ်းမှုသည် အရေးကြီးပါသည်။
- ထိုးဆေးထိုးစက်ဆေးထိုးပုံသွင်းခြင်းတွင် အဓိကစက်ပစ္စည်းသည် သာမိုပလတ်စတစ်ပစ္စည်းကို အရည်ပျော်စေရန်၊ မှိုထဲသို့ ထိုးသွင်းခြင်းနှင့် လုပ်ငန်းစဉ်ကို ထိန်းချုပ်ရန်အတွက် တာဝန်ရှိပါသည်။
- မှို: ပလပ်စတစ် အစိတ်အပိုင်း၏ အလိုရှိသော ပုံသဏ္ဍာန်နှင့် အသွင်သဏ္ဌာန်များကို ဖန်တီးရန် စိတ်တိုင်းကျ ဒီဇိုင်းထုတ်ထားသော မှိုတွင် အပိုင်းနှစ်ပိုင်း၊ အပေါက်နှင့် အူတိုင်တို့ ပါဝင်သည်။ အော်ပရေတာများသည် ၎င်းကို ဆေးထိုးပုံသွင်းစက်၏ ကုပ်ယူနစ်ပေါ်တွင် တပ်ဆင်ကြသည်။
- Hopper-အရည်ကျိုခြင်းနှင့် ဆေးထိုးခြင်းအတွက် ဆေးထိုးစက်၏စည်ထဲသို့ အပူချိန်အမှုန့် သို့မဟုတ် သေးငယ်သောပုံစံဖြင့် ထိန်းထားသော ကွန်တိန်နာ။
- စည်နှင့်ဝက်အူ- ဝက်အူသည် ၎င်းအတွင်းမှ ပစ္စည်းကို အရည်ပျော်ရန်၊ ရောနှောကာ စံချိန်စံညွှန်းသတ်မှတ်ရန် ဝက်အူလှည့်နေသဖြင့် ဘူးခွံ၊ ဆလင်ဒါပုံအခန်းတစ်ခု၊ သည် အပူပလပ်စတစ်ပစ္စည်းကို အရည်ပျော်ပြီး တစ်သားတည်းဖြစ်စေသည်။
- အပူပေးအအေးပေးစနစ်များ-ဆေးထိုးပုံသွင်းစက်များတွင် စည်၏အပူချိန်ကို မြှင့်တင်ရန်အတွက် လျှပ်စစ်အပူပေးစက် သို့မဟုတ် အပူပေးစက်များကဲ့သို့သော အပူပေးစက်များ နှင့် ရေ သို့မဟုတ် ဆီလည်ပတ်မှုကဲ့သို့သော အအေးပေးစနစ်များ၊ မှိုကို အေးမြစေပြီး ပလပ်စတစ်အစိတ်အပိုင်းကို ခိုင်မာစေပါသည်။
- Ejector စနစ်-ပုံမှန်အားဖြင့် မှိုဖွင့်စဉ်အတွင်း ပေါက်တံများ၊ ပန်းကန်ပြားများ သို့မဟုတ် လေပေါက်ကွဲမှုများကို အသုံးပြု၍ မှိုပေါက်အတွင်းမှ ပုံသွင်းထားသော အစိတ်အပိုင်းကို ခိုင်မာစေပြီးနောက် ဖယ်ရှားသည်။
- ထိန်းချုပ်ရေးစနစ်:ဆေးထိုးပုံသွင်းခြင်း လုပ်ငန်းစဉ်၏ အမျိုးမျိုးသော ဘောင်များကို စောင့်ကြည့်ကာ ထိန်းချုပ်ပေးကာ အော်ပရေတာများအား ဆေးထိုးအမြန်နှုန်း၊ အပူချိန်၊ ဖိအားနှင့် အအေးခံချိန်စသည့် ကန့်သတ်ချက်များကို သတ်မှတ်ရန်နှင့် ချိန်ညှိရန် ခွင့်ပြုသည်။
ဆေးထိုးပုံသွင်းစက်များ- အမျိုးအစားများနှင့် လက္ခဏာများ
ဆေးထိုးပုံသွင်းစက် အမျိုးအစား တစ်ခုစီတွင် ၎င်း၏ လက္ခဏာများနှင့် အားသာချက်များ ပါရှိပြီး ထုတ်လုပ်သူသည် ၎င်းတို့၏ တိကျသော ထုတ်လုပ်မှု လိုအပ်ချက်များအတွက် အသင့်တော်ဆုံး ကိရိယာကို ရွေးချယ်နိုင်စေပါသည်။
- ဟိုက်ဒရောလစ် ထိုးဆေး ပုံသွင်းစက်များ ဤစက်များသည် မှိုထဲသို့ သွန်းသောပလပ်စတစ်ကို ထိုးသွင်းရန်အတွက် လိုအပ်သော ဖိအားကိုထုတ်ပေးရန် ဟိုက်ဒရောလစ်စနစ်များကို အသုံးပြုသည်။ အမျိုးမျိုးသော သာမိုပလတ်စတစ်များကို ကိုင်တွယ်ရာတွင် တိကျသောထိန်းချုပ်မှုနှင့် ဘက်စုံလုပ်ဆောင်နိုင်မှုတို့ကြောင့် ၎င်းတို့သည် မြင့်မားသောကုပ်ဆွဲအားကြောင့် လူသိများသည်။ ဟိုက်ဒရောလစ်စက်များသည် အကြီးစားထုတ်လုပ်မှုအတွက် သင့်လျော်ပြီး ရှုပ်ထွေးသောမှိုများကို ထားရှိနိုင်ပါသည်။
- လျှပ်စစ်ထိုးသွင်းပုံသွင်းစက်များလျှပ်စစ်စက်များသည် ဆေးထိုးခြင်း၊ ကုပ်တွယ်ခြင်းနှင့် ထုတ်ပယ်ခြင်းစနစ်များအပါအဝင် စက်၏လည်ပတ်မှုအတွက် လျှပ်စစ်ဆာဗာမော်တာများကို အသုံးပြုသည်။ ၎င်းတို့သည် ဟိုက်ဒရောလစ်စက်များထက် တိကျသော ထိန်းချုပ်မှု၊ စွမ်းအင်ထိရောက်မှုနှင့် တုံ့ပြန်မှုအချိန်များ ပိုမိုမြန်ဆန်စေသည်။ လျှပ်စစ်စက်များသည် ထပ်တလဲလဲနိုင်မှုနှင့် တိကျမှုမြင့်မားရန်လိုအပ်သော တိကျသောပုံသွင်းခြင်းလုပ်ငန်းအတွက် စံပြဖြစ်သည်။
- Hybrid Injection Molding Machines-Hybrid စက်များသည် ဟိုက်ဒရောလစ်နှင့် လျှပ်စစ်ပစ္စည်းများ၏ အကျိုးကျေးဇူးများကို ပေါင်းစပ်ထားသည်။ ၎င်းတို့သည် မြင့်မားသောတိကျမှု၊ စွမ်းအင်ထိရောက်မှုနှင့် ကုန်ကျစရိတ်သက်သာမှုတို့ရရှိရန် ဟိုက်ဒရောလစ်နှင့် လျှပ်စစ်ဆာဗာစနစ်များကို ပေါင်းစပ်အသုံးပြုထားသည်။ Hybrid စက်များသည် စွမ်းဆောင်ရည် နှင့် လုပ်ငန်းလည်ပတ်မှု ကုန်ကျစရိတ်များကြား ချိန်ခွင်လျှာညှိပေးသည့် အသုံးချပရိုဂရမ်များစွာအတွက် သင့်လျော်ပါသည်။
- နှစ်ပြားထိုးဆေးထိုးစက်များ- ပန်းကန်ပြားနှစ်ခု စက်များတွင် မှိုကို ကုပ်ရန် သီးခြားပန်းကန်ပြားနှစ်ခုပါသည့် ထူးခြားသော ဒီဇိုင်းတစ်ခု ရှိသည်။ ဤဒီဇိုင်းသည် ပိုမိုကောင်းမွန်သော တည်ငြိမ်မှု၊ ပိုမိုကောင်းမွန်သော မှိုထပ်တူပြုခြင်းကို ပံ့ပိုးပေးပြီး ပိုကြီးသော မှိုအရွယ်အစားများနှင့် ပိုမိုမြင့်မားသော ကုပ်ကြိုးများကို ထောက်ပံ့ပေးသည်။ ပန်းကန်ပြားနှစ်ချပ်စက်များသည် တိကျသော ပုံသွင်းရန်လိုအပ်သည့် ကြီးမားပြီး ရှုပ်ထွေးသော အစိတ်အပိုင်းများအတွက် သင့်လျော်သည်။
- Multi-Component Injection Molding Machines-ထုတ်လုပ်သူများသည် ပုံသွင်းစက်ဝန်းတစ်ခုတည်းတွင် ပစ္စည်းမျိုးစုံ သို့မဟုတ် အရောင်မျိုးစုံဖြင့် အစိတ်အပိုင်းများကို ထုတ်လုပ်ရန် ဤစက်များကို ဒီဇိုင်းဆွဲသည်။ ၎င်းတို့တွင် အမျိုးမျိုးသော ဆေးထိုးယူနစ်များနှင့် မှိုများပါရှိပြီး မတူညီသော ပစ္စည်းများကို တပြိုင်နက် ထိုးသွင်းနိုင်ပါသည်။ အစိတ်အပိုင်းများစွာရှိသော စက်များသည် ကွဲပြားသောဝိသေသလက္ခဏာများဖြင့် ရှုပ်ထွေးသောအစိတ်အပိုင်းများကို ထုတ်လုပ်ရာတွင် လိုက်လျောညီထွေရှိပြီး ထိရောက်မှုရှိသည်။
- Micro-Injection Molding စက်များ-သေးငယ်ပြီး တိကျသော အစိတ်အပိုင်းများ ထုတ်လုပ်ရန်အတွက် အထူးဒီဇိုင်းထုတ်ထားပြီး မိုက်ခရိုထိုးဆေးပုံသွင်းစက်များသည် မယုံနိုင်လောက်အောင် မြင့်မားသော တိကျမှုနှင့် တိကျမှုကို ပေးစွမ်းသည်။ ၎င်းတို့သည် တင်းတင်းကြပ်ကြပ်သည်းခံနိုင်မှုနှင့် သေးငယ်သောပစ္စည်းစွန့်ပစ်မှုတို့ဖြင့် ရှုပ်ထွေးသောအသေးစိတ်အချက်အလက်များကို ထုတ်လုပ်နိုင်သည်။ အီလက်ထရွန်းနစ်၊ ဆေးဘက်ဆိုင်ရာ ကိရိယာများနှင့် မိုက်ခရိုအော့ပ်စက်များသည် မိုက်ခရိုထိုးဆေး ပုံသွင်းစက်များကို အများအားဖြင့် အသုံးပြုကြသည်။
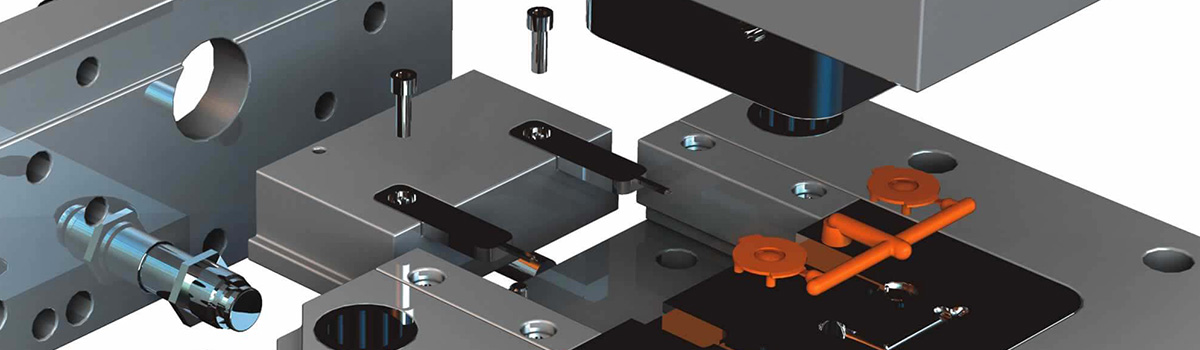
Injection Molding အတွက် Mold Design ထည့်သွင်းစဉ်းစားချက်များ
အောင်မြင်သော ဆေးထိုးပုံသွင်းထုတ်လုပ်ခြင်းအတွက် ဂရုတစိုက် မှိုဒီဇိုင်းထည့်သွင်းစဉ်းစားရန် အရေးကြီးပါသည်။
- အပိုင်းဒီဇိုင်း-မှိုဒီဇိုင်းသည် ၎င်း၏ပုံသဏ္ဍာန်၊ အတိုင်းအတာနှင့် လုပ်ဆောင်နိုင်သောအင်္ဂါရပ်များအပါအဝင် အစိတ်အပိုင်း၏ သီးခြားလိုအပ်ချက်များကို လိုက်လျောညီထွေရှိသင့်သည်။ ထုတ်လုပ်သူသည် အကြမ်းမျဉ်းထောင့်များ၊ နံရံအထူ၊ အောက်ခံဖြတ်ပိုင်းများနှင့် အစိတ်အပိုင်းများ၏ အရည်အသွေးကို လွယ်ကူစွာ ထုတ်လွှတ်နိုင်စေရန်အတွက် လိုအပ်သော အစိတ်အပိုင်းများကို ကောင်းစွာစဉ်းစားသင့်သည်။
- မှိုပစ္စည်း- မှိုပစ္စည်းရွေးချယ်မှုသည် ကြာရှည်ခံမှု၊ အတိုင်းအတာတည်ငြိမ်မှုနှင့် အပူဒဏ်ခံနိုင်ရည်ရရှိရန် အရေးကြီးပါသည်။ အသုံးများသော မှိုပစ္စည်းများတွင် သံမဏိသတ္တုစပ်များ၊ အလူမီနီယမ်သတ္တုစပ်များနှင့် ကိရိယာစတီးလ်များ ပါဝင်သည်။ ပစ္စည်းရွေးချယ်မှုသည် ထုတ်လုပ်မှုပမာဏ၊ တစ်စိတ်တစ်ပိုင်းရှုပ်ထွေးမှုနှင့် မျှော်မှန်းထားသည့်ကိရိယာသက်တမ်းစသည့်အချက်များပေါ်တွင် မူတည်သည်။
- အေး System ကို:သင့်လျော်သောအစိတ်အပိုင်းများ ခိုင်မာစေရန်နှင့် လည်ပတ်ချိန်ကို လျှော့ချရန်အတွက် ထိရောက်သောအအေးပေးခြင်းသည် မရှိမဖြစ်လိုအပ်ပါသည်။ မှိုဒီဇိုင်းသည် မှိုအအေးခံခြင်းကို သေချာစေရန် အအေးခံလမ်းကြောင်းများ သို့မဟုတ် ဗျူဟာကျကျ နေရာယူထားသော ထည့်သွင်းမှုများ ထည့်သွင်းသင့်သည်။ သင့်လျော်သောအအေးပေးခြင်းသည် warpage၊ ကျုံ့သွားခြင်းနှင့် အစိတ်အပိုင်းချို့ယွင်းချက်များ၏အန္တရာယ်ကို လျော့နည်းစေသည်။
- အငြင်းပွားမှု:ဆေးထိုးခြင်း လုပ်ငန်းစဉ်အတွင်း လေနှင့် ဓာတ်ငွေ့များ လွတ်မြောက်ရန် လုံလောက်သော လေဝင်လေထွက် လိုအပ်သည်။ လေဝင်လေထွက်မလုံလောက်ပါက ဓာတ်ငွေ့တွင်းများ၊ မီးလောင်ဒဏ်ရာများ သို့မဟုတ် မပြည့်စုံသော အစိတ်အပိုင်းများကို ဖြည့်သွင်းပေးနိုင်သည်။ ထုတ်လုပ်သူများသည် မှိုဒီဇိုင်းတွင် လေဝင်လေထွက်ပေါက်များ၊ ပင်ချောင်းများ သို့မဟုတ် အခြားယန္တရားများကို ထည့်သွင်းခြင်းဖြင့် လေဝင်လေထွက်ကို ရရှိနိုင်သည်။
- ထုတ်ပယ်စနစ်-မှိုပုံစံဒီဇိုင်းတွင် မှိုအပေါက်မှ ပုံသွင်းထားသော အစိတ်အပိုင်းကို ဘေးကင်းစွာ ထိရောက်စွာ ဖယ်ရှားရန် ထိရောက်သော ထုတ်လွှတ်သည့်စနစ်တစ်ခု ပါဝင်သင့်သည်။ ထုတ်လွှတ်သည့်စနစ်တွင် လုပ်ငန်းဆောင်တာ သို့မဟုတ် အရေးပါသောအင်္ဂါရပ်များကို အနှောင့်အယှက်မဖြစ်စေရန် ဗျူဟာမြောက်နေရာချထားသော ထုတ်ပယ်တံများ၊ လက်စွပ်များ သို့မဟုတ် အခြားယန္တရားများ ပါဝင်နိုင်သည်။
- ဂိတ်ဒီဇိုင်း-တံခါးသည် သွန်းသော ပလပ်စတစ် မှိုပေါက်ထဲသို့ ဝင်လာသော နေရာဖြစ်သည်။ တံခါးဒီဇိုင်းသည် သင့်လျော်သော အစိတ်အပိုင်းအားဖြည့်ရန်၊ စီးဆင်းမှုမျဉ်းများကို လျှော့ချရန်နှင့် အရွယ်မတိုင်မီ ပစ္စည်းအေးခဲခြင်းမှ ကာကွယ်ရန် သေချာသင့်သည်။ ပုံမှန်တံခါးဒီဇိုင်းများတွင် အစိတ်အပိုင်းလိုအပ်ချက်နှင့် ပစ္စည်းဂုဏ်သတ္တိများပေါ်မူတည်၍ အစွန်းတံခါးများ၊ ဥမင်တံခါးများနှင့် အပူပြေးစနစ်များ ပါဝင်ပါသည်။
- ခွဲထွက်ခြင်းလိုင်း-မှိုပုံစံဒီဇိုင်းသည် မှို၏တစ်ဝက်တစ်ပျက်ကို ပေါင်းစည်းသည့်မျဉ်းဖြစ်သည့် သင့်လျော်သောလမ်းခွဲမျဉ်းကို သတ်မှတ်သင့်သည်။ မှန်ကန်သော ခွဲခြင်းလိုင်းနေရာချထားခြင်းသည် ဖလက်ရှ်အနည်းငယ်မျှသာနှင့် ခွဲထွက်သည့်လိုင်း မကိုက်ညီကြောင်း သေချာစေပြီး ထိရောက်သော မှိုစုဝေးမှုကို လွယ်ကူချောမွေ့စေသည်။
- မှိုထိန်းသိမ်းမှုနှင့် ဝန်ဆောင်မှုပေးနိုင်မှု- ထုတ်လုပ်သူသည် ပြုပြင်ထိန်းသိမ်းမှု၊ ပြုပြင်မှုနှင့် မှိုဝန်ဆောင်မှုကို လွယ်ကူစေရန် ထည့်သွင်းစဉ်းစားသင့်သည်။ မှိုအစိတ်အပိုင်းများကို သန့်ရှင်းရေး၊ စစ်ဆေးခြင်းနှင့် အစားထိုးခြင်းအတွက် အလွယ်တကူ လက်လှမ်းမီနိုင်ရမည်။ အပြောင်းအလဲမြန်သော ထည့်သွင်းမှုများ သို့မဟုတ် မော်ဂျူလာမှိုဒီဇိုင်းများကဲ့သို့ အင်္ဂါရပ်များကို ပေါင်းစပ်ထည့်သွင်းခြင်းဖြင့် မှိုဝန်ဆောင်မှုကို မြှင့်တင်ပေးနိုင်ပါသည်။
Injection Molding တွင်အသုံးပြုသော မှိုပစ္စည်းများ
မှိုပစ္စည်း ကျွမ်းကျင်သူများနှင့် ပူးပေါင်း၍ ပုံသွင်းခြင်း လျှောက်လွှာ၏ တိကျသော လိုအပ်ချက်များကို ထည့်သွင်းစဉ်းစားခြင်းဖြင့် အကောင်းဆုံးသော မှိုစွမ်းဆောင်ရည်နှင့် အစိတ်အပိုင်း အရည်အသွေးကို ရရှိရန် အသင့်တော်ဆုံး ပစ္စည်းကို ဆုံးဖြတ်ရန် ကူညီပေးပါသည်။
- သံမဏိသတ္တုစပ်များ တူးလ်သံမဏိများ (ဥပမာ၊ P20၊ H13) နှင့် သံမဏိများကဲ့သို့သော သံမဏိသတ္တုစပ်များကို ၎င်းတို့၏ အလွန်ကောင်းမွန်သော ကြာရှည်ခံမှု၊ အပူခံနိုင်ရည်နှင့် ခံနိုင်ရည်ရှိမှုတို့ကြောင့် ဆေးထိုးပုံသွင်းမှိုများအတွက် အသုံးများသည်။ ဤပစ္စည်းများသည် ဆေးထိုးပုံသွင်းခြင်းလုပ်ငန်းစဉ်တွင် မြင့်မားသောအပူချိန်နှင့် ဖိအားများကို ခံနိုင်ရည်ရှိပြီး အရည်အသွေးမြင့် အစိတ်အပိုင်းများထုတ်လုပ်ရန်အတွက် ကောင်းမွန်သောအတိုင်းအတာတည်ငြိမ်မှုကိုပေးစွမ်းနိုင်သည်။
- အလူမီနီယမ် သတ္တုစပ်များ7075 နှင့် 6061 ကဲ့သို့သော အလူမီနီယမ်သတ္တုစပ်များသည် ပေါ့ပါးပြီး ကောင်းသောအပူစီးကူးမှုကို ပေးစွမ်းသောကြောင့် ထိရောက်သောအအေးခံရန်လိုအပ်သောမှိုများအတွက် သင့်လျော်ပါသည်။ ထုတ်လုပ်သူများသည် ပုံတူပုံတူရိုက်ခြင်း၊ ထုထည်နည်းသောထုတ်လုပ်မှု သို့မဟုတ် အလေးချိန်လျှော့ချရန် အရေးကြီးသည့်အသုံးအဆောင်အတွက် အလူမီနီယံမှိုများကို မကြာခဏအသုံးပြုကြသည်။ သို့သော်၊ အလူမီနီယမ်မှိုများသည် သံမဏိသတ္တုစပ်များနှင့် နှိုင်းယှဉ်ပါက တာရှည်ခံမှု နည်းပါးနိုင်သည်။
- ကြေးနီသတ္တုစပ်များBeryllium ကြေးနီကဲ့သို့သော ကြေးနီသတ္တုစပ်များသည် မြင့်မားသောအပူစီးကူးမှုနှင့် စက်ပိုင်းဆိုင်ရာကောင်းမွန်မှုကို ပြသသည်။ ထိရောက်သော အအေးခံရန်အတွက် အလွန်ကောင်းမွန်သော အပူလွှဲပြောင်းမှု လိုအပ်သော မှိုများတွင် အသုံးပြုမှုကို ရှာဖွေကြသည်။ ကြေးနီသတ္တုစပ်များသည် ပုံသွင်းထားသော အစိတ်အပိုင်းမှ အပူကို လျင်မြန်စွာ ပြေပျောက်စေခြင်းဖြင့် လည်ပတ်ချိန်များကို လျှော့ချနိုင်ပြီး ခိုင်မာမှုကို ပိုမိုရရှိစေသည်။
- တူးလ်သံမဏိများH13၊ S7 နှင့် D2 အပါအဝင် ကိရိယာသံမဏိများကို စွမ်းဆောင်ရည်မြင့်မားသော ကိရိယာအသုံးပြုမှုများအတွက် ဒီဇိုင်းထုတ်ထားသည်။ ဤသံမဏိများသည် မြင့်မားသော ကြံ့ခိုင်မှု၊ မာကျောမှုနှင့် ခံနိုင်ရည်အား ပေါင်းစပ်ပေးသည်။ တူးလ်စတီးများသည် ထုတ်လုပ်မှုပမာဏ မြင့်မားသော ပမာဏ၊ အနုထည်ပစ္စည်းများ၊ သို့မဟုတ် ပုံသွင်းမှု လိုအပ်သော အခြေအနေများနှင့် ကိုက်ညီပါသည်။
- နီကယ်သတ္တုစပ်များInconel နှင့် Hastelloy ကဲ့သို့သော နီကယ်သတ္တုစပ်များသည် ၎င်းတို့၏ ခြွင်းချက်ဖြစ်သော သံချေးတက်ခြင်း၊ အပူချိန်မြင့်ခြင်းနှင့် အပူတည်ငြိမ်ခြင်းတို့ကြောင့် လူသိများသည်။ ထုတ်လုပ်သူများသည် အဆိပ်သင့်သောပစ္စည်းများကို ကိုင်တွယ်နိုင်သော သို့မဟုတ် ပြင်းထန်သောအပူချိန်နှင့် ပြင်းထန်သော ပုံသွင်းပတ်ဝန်းကျင်များကို ခံနိုင်ရည်ရှိရန် လိုအပ်သော မှိုများတွင် ဤသတ္တုစပ်များကို အသုံးပြုကြသည်။
- ပေါင်းစပ်ပစ္စည်းများ-အားဖြည့်ပလပ်စတစ်များ သို့မဟုတ် သတ္တုထည့်သွင်းမှုများကဲ့သို့သော ပေါင်းစပ်ပစ္စည်းများကို တိကျသော ပုံသွင်းခြင်းလုပ်ငန်းအတွက် အခါအားလျော်စွာ အသုံးပြုပါသည်။ ဤပစ္စည်းများသည် မြင့်မားသော ခွန်အား၊ အပူတည်ငြိမ်မှုနှင့် အလေးချိန်လျော့ချခြင်းကဲ့သို့သော ဂုဏ်သတ္တိများ မျှတစေသည်။ ပေါင်းစပ်မှိုများသည် တိကျသောထုတ်လုပ်မှုလိုအပ်ချက်များအတွက် ကုန်ကျစရိတ်သက်သာသော အခြားရွေးချယ်စရာများဖြစ်သည်။
Injection Molds အမျိုးအစားများ
ဆေးထိုးပုံသွင်းခြင်းသည် ပလပ်စတစ်အစိတ်အပိုင်းများအတွက် စွယ်စုံရနှင့် တွင်ကျယ်စွာ အသုံးပြုသည့် ထုတ်လုပ်မှုလုပ်ငန်းစဉ်တစ်ခုဖြစ်သည်။
- နှစ်ပြားမှို-နှစ်ပြားမှိုသည် အသုံးအများဆုံး ဆေးထိုးမှိုအမျိုးအစားဖြစ်သည်။ ၎င်းတွင် ပုံသွင်းထားသော အစိတ်အပိုင်းကို ထုတ်ထုတ်ရန် သီးခြားခွဲထားသော ပန်းကန်ပြား၊ အပေါက်အပြားနှင့် အူတိုင်ပြားတို့ ပါဝင်ပါသည်။ အူတိုင်ပန်းကန်တွင် မှို၏အပေါက်အခြမ်းပါရှိပြီး အူတိုင်ပြားသည် အူတိုင်တွင်တည်ရှိသည်။ ထုတ်လုပ်သူများသည် ၎င်းတို့၏ ရိုးရှင်းသော ဒီဇိုင်းကြောင့် အစိတ်အပိုင်းများစွာကို ကျယ်ပြန့်စွာ ထုတ်လုပ်ရန်အတွက် ပန်းကန်ပြားနှစ်ပြားမှိုများကို အသုံးပြုကြသည်။
- သုံးပန်းကန်မှို-သုံးပန်းကန်မှိုသည် နှစ်ပန်းကန်မှို၏ အဆင့်မြင့်ဗားရှင်းဖြစ်သည်။ ၎င်းတွင် အပိုပန်းကန်ပြား၊ အပြေးသမား သို့မဟုတ် တံမြက်ခင်းပြား ပါဝင်သည်။ အပြေးသမားပန်းကန်သည် တံမြက်ပင်များ၊ အပြေးသမားများနှင့် တံခါးများအတွက် သီးခြားချန်နယ်တစ်ခု ဖန်တီးပေးကာ ပုံသွင်းထားသောအပိုင်းကို ပိုမိုလွယ်ကူစွာ ဖယ်ရှားနိုင်စေပါသည်။ ထုတ်လုပ်သူများသည် ရှုပ်ထွေးသောတံခါးပေါက်စနစ်များဖြင့် အသေးစိတ်အချက်အလက်များအတွက် သို့မဟုတ် အပိုင်းအစပေါ်ရှိ တံခါးအငွေ့အသက်ကို ရှောင်ရှားသည့်အခါတွင် သုံးပန်းကန်မှိုများကို အသုံးပြုလေ့ရှိသည်။
- Hot Runner Mold-အပြေးသမားနှင့် ဂိတ်စနစ်အား ပူသောအပြေးသမားမှိုများဖြင့် အပူပေးကာ စက်ဝန်းတစ်ခုစီအတွင်း ပစ္စည်း၏အစိုင်အခဲနှင့် ပြန်လည် အရည်ပျော်ရန် လိုအပ်မှုကို ဖယ်ရှားပေးသည်။ အပူအပြေးစနစ်တွင် ပလပ်စတစ်၏သွန်းမှုအခြေအနေကို ထိန်းသိမ်းပေးသည့် အပူပေးအ manifolds နှင့် nozzle များပါဝင်သည်။ အပြေးသမား မှိုများသည် လည်ပတ်ချိန်ကို လျှော့ချခြင်း၊ ပစ္စည်းစွန့်ပစ်မှု နည်းပါးခြင်းနှင့် တံခါးအငွေ့အသက်များကို လျှော့ချခြင်းဖြင့် ပိုမိုကောင်းမွန်သော အစိတ်အပိုင်း အရည်အသွေးကို ပေးဆောင်သည်။
- အအေးပြေးသမားမှို- အအေးခံအပြေးသမားမှိုများတွင် သွန်းသောပလပ်စတစ်များသည် လည်ပတ်မှုတစ်ခုစီတိုင်းနှင့် ခိုင်ခံ့စေသော အအေးခန်းအပြေးသမားများမှတစ်ဆင့် ရိုးရာအပြေးသမားနှင့် တံခါးပေါက်စနစ်တစ်ခုရှိသည်။ နောက်ပိုင်းတွင် အော်ပရေတာများသည် ခိုင်ခံ့သော အပြေးသမားများကို ဖယ်ရှားကာ ပစ္စည်းအညစ်အကြေးများကို ဖြစ်ပေါ်စေသည်။ ထုတ်လုပ်သူများသည် ပုံမှန်အားဖြင့် ထုထည်နိမ့်သောထုတ်လုပ်မှုအတွက် ရှုပ်ထွေးသောအပြေးသမားမှိုများကို အသုံးပြုကြသည် သို့မဟုတ် ၎င်းတို့၏ပိုမိုရိုးရှင်းသောဒီဇိုင်းကြောင့် ပစ္စည်းကုန်ကျစရိတ်သည် အရေးပါမှုနည်းသောအခါတွင်ဖြစ်သည်။
- မှိုထည့်ပါ-ဆေးထိုးပုံသွင်းစဉ်အတွင်း မှိုပေါက်အတွင်း သတ္တု သို့မဟုတ် ပလပ်စတစ် ထည့်သွင်းမှုများကို မှိုထည့်ပါ။ ထည့်သွင်းမှုများကို ပုံစံခွက်ထဲသို့ ကြိုတင်ထည့်ထားနိုင်သည် သို့မဟုတ် အလိုအလျောက် လုပ်ငန်းစဉ်များဖြင့် ထည့်သွင်းနိုင်သည်။ ဤမှိုသည် အပိုအစိတ်အပိုင်းများ သို့မဟုတ် ပုံသွင်းထားသောအပိုင်းသို့ အားဖြည့်ပစ္စည်းများကို ပေါင်းစည်းနိုင်စေပြီး ၎င်း၏လုပ်ဆောင်နိုင်စွမ်း သို့မဟုတ် ခွန်အားကို တိုးမြှင့်စေသည်။
- မှို- Overmolding တွင် ပစ္စည်းတစ်ခုအပေါ်တစ်ခု ပုံသွင်းခြင်းတွင် ပုံမှန်အားဖြင့် ပျော့ပျောင်းသော ပလပ်စတစ်အလွှာကို ပျော့ပျောင်းသော အီလက်စတိုမာ သို့မဟုတ် သာမိုပလတ်စတစ်ဖြင့် ချည်နှောင်ထားခြင်းဖြစ်သည်။ ဤလုပ်ငန်းစဉ်သည် မှိုတစ်ခုထဲရှိ ပစ္စည်းမျိုးစုံ သို့မဟုတ် အသွင်အပြင်များဖြင့် အစိတ်အပိုင်းများကို ဖန်တီးနိုင်စေပြီး ပိုမိုကောင်းမွန်သော ချုပ်ကိုင်မှု၊ ကူရှင် သို့မဟုတ် အလှအပဆိုင်ရာအင်္ဂါရပ်များကို ပံ့ပိုးပေးသည်။
ထိုးဆေးပုံသွင်းခြင်းကုန်ကျစရိတ်များကို ထိခိုက်စေသည့်အချက်များ
ဤအချက်များကို ထည့်သွင်းစဉ်းစားခြင်းဖြင့် ထုတ်လုပ်သူသည် ဆေးထိုးပုံသွင်းခြင်း၏ကုန်ကျစရိတ်ကို ခန့်မှန်းကာ ပိုမိုကောင်းမွန်အောင် ကူညီပေးနိုင်ပြီး ၎င်းတို့၏ သီးခြားထုတ်လုပ်မှုလိုအပ်ချက်များအတွက် အရည်အသွေး၊ ထိရောက်မှုနှင့် ကုန်ကျစရိတ်သက်သာမှုတို့ကြား မျှတမှုရှိစေရန် ကူညီပေးနိုင်ပါသည်။
- အပိုင်း ရှုပ်ထွေးမှု-အစိတ်အပိုင်းဒီဇိုင်း၏ ရှုပ်ထွေးမှုသည် ဆေးထိုးပုံသွင်းခြင်း၏ကုန်ကျစရိတ်ကို ဆုံးဖြတ်ရာတွင် အရေးပါသောအခန်းကဏ္ဍမှပါဝင်ပါသည်။ ရှုပ်ထွေးသော ဂျီသြမေတြီများ၊ အောက်ခံဖြတ်တောက်မှုများ၊ ပါးလွှာသောနံရံများ သို့မဟုတ် ရှုပ်ထွေးသောအင်္ဂါရပ်များသည် အပိုကိရိယာတန်ဆာပလာများ၊ အထူးပြုမှိုများ၊ သို့မဟုတ် ပိုရှည်သော စက်ဝန်းများ လိုအပ်ပြီး အလုံးစုံထုတ်လုပ်မှုကုန်ကျစရိတ်ကို တိုးစေသည်။
- ပစ္စည်းရွေးချယ်မှု -သာမိုပလတ်စတစ်ပစ္စည်းရွေးချယ်မှုသည် ဆေးထိုးခြင်းကုန်ကျစရိတ်အပေါ် သက်ရောက်မှုရှိသည်။ မတူညီသောပစ္စည်းများသည် တစ်ကီလိုဂရမ်လျှင် စျေးနှုန်းကွဲပြားကြပြီး ပစ္စည်းရရှိနိုင်မှု၊ ဂုဏ်သတ္တိများနှင့် စီမံဆောင်ရွက်ပေးမှုလိုအပ်ချက်များကဲ့သို့သော အကြောင်းရင်းများသည် အလုံးစုံပစ္စည်းကုန်ကျစရိတ်အပေါ် လွှမ်းမိုးနိုင်သည်။
- တူးလ်နှင့် မှိုဒီဇိုင်း- ကနဦးကိရိယာတန်ဆာပလာနှင့် မှိုဒီဇိုင်းကုန်ကျစရိတ်များသည် ဆေးထိုးပုံသွင်းခြင်းကုန်ကျစရိတ်တွင် သိသိသာသာဖြစ်သည်။ မှိုရှုပ်ထွေးမှု၊ အပေါက်အရေအတွက်၊ မှိုအရွယ်အစားနှင့် မှိုပစ္စည်းများကဲ့သို့သော အကြောင်းရင်းများသည် ကိရိယာတန်ဆာပလာနှင့် မှိုထုတ်လုပ်မှုကုန်ကျစရိတ်ကို အထောက်အကူဖြစ်စေသည်။ အဆင့်မြင့်အင်္ဂါရပ်များလိုအပ်သော ပိုမိုရှုပ်ထွေးသောမှိုများ သို့မဟုတ် မှိုများသည် ရှေ့မှရင်းနှီးမြှုပ်နှံမှုကို တိုးမြှင့်နိုင်သည်။
- ထုတ်လုပ်မှု ပမာဏ- ထုတ်လုပ်မှုပမာဏသည် ဆေးထိုးပုံသွင်းခြင်းတွင် အစိတ်အပိုင်းတစ်ခုချင်းစီ၏ ကုန်ကျစရိတ်ကို တိုက်ရိုက်သက်ရောက်မှုရှိသည်။ မြင့်မားသောစာအုပ်များသည် အစိတ်အပိုင်းအလိုက် ကုန်ကျစရိတ်ကို လျှော့ချပေးလေ့ရှိသည်။ အပြန်အလှန်အားဖြင့်၊ ပမာဏနည်းသော ထုတ်လုပ်မှုလည်ပတ်မှုများသည် စနစ်ထည့်သွင်းမှု၊ ကိရိယာတန်ဆာပလာများနှင့် ပစ္စည်းစွန့်ပစ်မှုများကြောင့် ကုန်ကျစရိတ်ပိုများနိုင်သည်။
- နာရီစက်ဝန်း: အအေးခံခြင်းနှင့် ထုတ်လွှတ်ခြင်းအဆင့်များပါ၀င်သည့် စက်ဝန်းအချိန်သည် ထုတ်လုပ်မှုစွမ်းရည်နှင့် အလုံးစုံကုန်ကျစရိတ်အပေါ် သက်ရောက်မှုရှိသည်။ စက်ဝန်းကြာရှည်ခြင်းကြောင့် ထုတ်လုပ်မှု လျော့ကျလာပြီး ဈေးနှုန်းများ မြင့်မားလာနိုင်သည်။ မှိုဒီဇိုင်း၊ အအေးခံစနစ်နှင့် လုပ်ငန်းစဉ်ဘောင်များကို ပိုမိုကောင်းမွန်အောင်ပြုလုပ်ခြင်းဖြင့် စက်လည်ပတ်ချိန်များကို လျှော့ချနိုင်ပြီး စွမ်းဆောင်ရည်ကို မြှင့်တင်ပေးနိုင်ပါသည်။
- အရည်အသွေး လိုအပ်ချက်များ-တင်းကျပ်သော အရည်အသွေးသတ်မှတ်ချက်များ သို့မဟုတ် တိကျသော အသိအမှတ်ပြုလက်မှတ်များသည် ဆေးထိုးပုံသွင်းခြင်းကုန်ကျစရိတ်အပေါ် သက်ရောက်မှုရှိနိုင်သည်။ တိကျသောသည်းခံနိုင်ရည်များ ပြည့်မီခြင်း၊ မျက်နှာပြင် ပြီးစီးမှုလိုအပ်ချက်များ သို့မဟုတ် ထပ်လောင်းစမ်းသပ်ခြင်းများသည် အခြားအရင်းအမြစ်များ၊ လုပ်ငန်းစဉ်များ သို့မဟုတ် စစ်ဆေးမှုများ လိုအပ်ပြီး အလုံးစုံကုန်ကျစရိတ်ကို ပေါင်းထည့်နိုင်သည်။
- ဒုတိယ လုပ်ဆောင်ချက်များပုံသွင်းထားသော အစိတ်အပိုင်းများသည် တပ်ဆင်ခြင်း၊ ပန်းချီဆွဲခြင်း သို့မဟုတ် အပိုအချောသတ်ခြင်းအဆင့်များကဲ့သို့ လုပ်ဆောင်ပြီးနောက် လုပ်ဆောင်ခြင်းလုပ်ငန်းများကို လိုအပ်ပါက၊ အဆိုပါလုပ်ငန်းများသည် အလုံးစုံ ဆေးထိုးပုံသွင်းခြင်းကုန်ကျစရိတ်ကို ပေါင်းထည့်နိုင်ပါသည်။
- ပေးသွင်းသူနှင့် တည်နေရာ-ဆေးထိုးပုံသွင်းရောင်းချသူရွေးချယ်မှုနှင့် ၎င်းတို့၏တည်နေရာသည် ကုန်ကျစရိတ်များအပေါ် သက်ရောက်မှုရှိနိုင်သည်။ လုပ်သားစရိတ်၊ စရိတ်စကများ၊ ထောက်ပံ့ပို့ဆောင်ရေးနှင့် သယ်ယူပို့ဆောင်ရေးကုန်ကျစရိတ်များသည် ပေးသွင်းသူ၏တည်နေရာပေါ်မူတည်၍ ကွဲပြားပြီး အလုံးစုံကုန်ထုတ်လုပ်မှုကုန်ကျစရိတ်အပေါ် သက်ရောက်မှုရှိသည်။
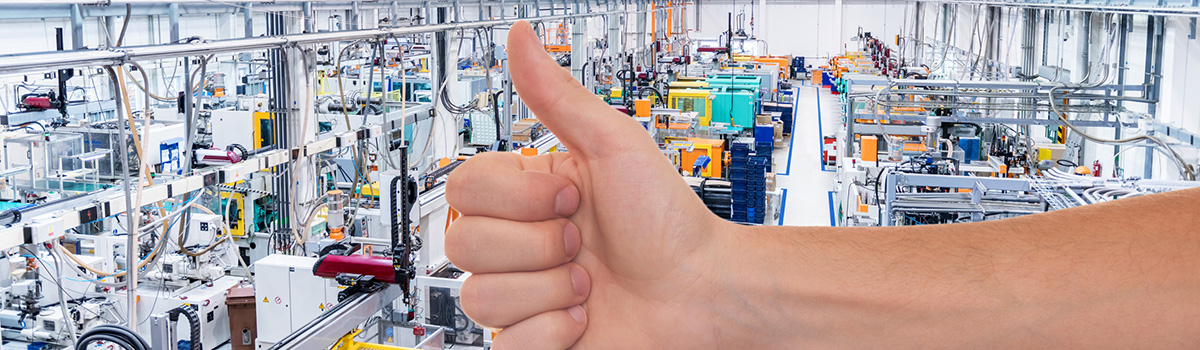
Injection Molding တွင် အရည်အသွေးထိန်းချုပ်ခြင်း။
ဆေးထိုးပုံသွင်းခြင်းလုပ်ငန်းစဉ်တစ်လျှောက် ခိုင်မာသောအရည်အသွေးထိန်းချုပ်မှုအစီအမံများကို အကောင်အထည်ဖော်ခြင်းသည် ဖောက်သည်၏သတ်မှတ်ချက်များနှင့်လိုအပ်ချက်များနှင့်ကိုက်ညီသည့် အရည်အသွေးမြင့်အစိတ်အပိုင်းများထုတ်လုပ်ခြင်းကိုသေချာစေမည့် အလားအလာရှိသောချို့ယွင်းချက်များ၊ သွေဖည်မှုများ သို့မဟုတ် မကိုက်ညီမှုများကိုဖော်ထုတ်ဖြေရှင်းရန်ကူညီပေးသည်။
- လုပ်ငန်းစဉ် စောင့်ကြည့်ခြင်း- အရည်ပျော်သည့်အပူချိန်၊ ဆေးထိုးဖိအား၊ အအေးခံချိန်နှင့် စက်ဝန်းအချိန်ကဲ့သို့သော အဓိက လုပ်ငန်းစဉ်ဘောင်များကို အဆက်မပြတ်စောင့်ကြည့်ခြင်းသည် အစိတ်အပိုင်းထုတ်လုပ်မှုတွင် လိုက်လျောညီထွေရှိပြီး ထပ်တလဲလဲဖြစ်နိုင်မှုကို သေချာစေသည်။ အချိန်နှင့်တပြေးညီ စောင့်ကြည့်စစ်ဆေးခြင်းနှင့် အလိုအလျောက်စနစ်များသည် သတ်မှတ်ဘောင်များမှ ကွဲပြားမှုများ သို့မဟုတ် သွေဖည်မှုများကို သိရှိနိုင်ပြီး အချိန်နှင့်တစ်ပြေးညီ ချိန်ညှိမှုများနှင့် လုပ်ငန်းစဉ်တည်ငြိမ်မှုကို ထိန်းသိမ်းပေးနိုင်သည်။
- စစ်ဆေးခြင်းနှင့် တိုင်းတာခြင်း-ပုံသွင်းထားသော အစိတ်အပိုင်းများကို ပုံမှန်ပြန်လည်သုံးသပ်ခြင်းနှင့် တိုင်းတာခြင်းများသည် အတိုင်းအတာတိကျမှု၊ အစိတ်အပိုင်းအရည်အသွေးနှင့် သတ်မှတ်ချက်များကို လိုက်နာမှုရှိမရှိ စစ်ဆေးရန် အရေးကြီးပါသည်။ ကျွန်ုပ်တို့၏ဝန်ဆောင်မှုများသည် အတိုင်းအတာများကိုတိုင်းတာခြင်း၊ မျက်နှာပြင်အရည်အသွေးကိုခွဲခြမ်းစိတ်ဖြာခြင်း၊ အမြင်အာရုံစစ်ဆေးခြင်းပြုလုပ်ခြင်းနှင့် လုပ်ငန်းဆိုင်ရာစမ်းသပ်မှုများလုပ်ဆောင်ခြင်းကဲ့သို့သော အရည်အသွေးထိန်းချုပ်မှုနည်းလမ်းများစွာကို အကျုံးဝင်ပါသည်။ ညှိနှိုင်းတိုင်းတာရေးစက် (CMM) နှင့် optical နှင့် အမြင်အာရုံစစ်ဆေးခြင်းစနစ်များကဲ့သို့သော အမျိုးမျိုးသော စစ်ဆေးရေးနည်းပညာများကို တိကျစွာအကဲဖြတ်ရန်အတွက် အသုံးပြုပါသည်။
- စာရင်းအင်းဆိုင်ရာ လုပ်ငန်းစဉ်ထိန်းချုပ်မှု (SPC)- SPC တွင် ဆေးထိုးပုံသွင်းခြင်း အရည်အသွေးကို စောင့်ကြည့်ထိန်းချုပ်ရန် လုပ်ငန်းစဉ်ဒေတာများကို စုဆောင်းခြင်းနှင့် ခွဲခြမ်းစိတ်ဖြာခြင်းတို့ ပါဝင်ပါသည်။ ထိန်းချုပ်မှုဇယားများနှင့် လုပ်ငန်းစဉ်ဆိုင်ရာ ခွဲခြမ်းစိတ်ဖြာမှုကဲ့သို့သော ကိန်းဂဏန်းစာရင်းအင်းနည်းလမ်းများ၊ လမ်းကြောင်းများကို ခွဲခြားသတ်မှတ်ရန်၊ လုပ်ငန်းစဉ်ကွဲလွဲချက်များကို ရှာဖွေဖော်ထုတ်ရန်နှင့် လုပ်ငန်းစဉ်သည် သတ်မှတ်ထားသော ထိန်းချုပ်ကန့်သတ်ချက်များအတွင်း ရှိနေကြောင်း သေချာစေရန်။ SPC သည် ပြဿနာများကို တက်ကြွစွာ ဖော်ထုတ်နိုင်စေပြီး လုပ်ငန်းစဉ် ပိုမိုကောင်းမွန်အောင် ဆောင်ရွက်ပေးသည်။
- ပစ္စည်းစစ်ဆေးခြင်း - သာမိုပလတ်စတစ်များ၊ ဖြည့်စွက်ပစ္စည်းများ၊ နှင့် အရောင်ဆိုးဆေးများကဲ့သို့သော ကုန်ကြမ်းများကို စမ်းသပ်ခြင်းသည် ဆေးထိုးပုံသွင်းခြင်းအတွက် ၎င်းတို့၏ အရည်အသွေးနှင့် သင့်လျော်မှုကို သေချာစေသည်။ ပစ္စည်းစမ်းသပ်ရာတွင် အရည်ပျော်ခြင်းအညွှန်းကိန်း (MFI) ခွဲခြမ်းစိတ်ဖြာမှု၊ စက်ပိုင်းဆိုင်ရာ ဂုဏ်သတ္တိများ၊ အပူလက္ခဏာများနှင့် ပစ္စည်းဖွဲ့စည်းမှုတို့ ပါဝင်နိုင်သည်။ ပစ္စည်းအရည်အသွေးကို စစ်ဆေးခြင်းဖြင့် ပုံသွင်းထားသော အစိတ်အပိုင်းများတွင် ချို့ယွင်းချက်များနှင့် ရှေ့နောက်မညီမှုများကို ကာကွယ်ပေးပါသည်။
- ကိရိယာတန်ဆာပလာ ထိန်းသိမ်းခြင်းနှင့် စစ်ဆေးခြင်း-ဆေးထိုးမှိုများကို မှန်ကန်သောထိန်းသိမ်းမှုနှင့် ပုံမှန်စစ်ဆေးခြင်းသည် ဆေးထိုးပုံသွင်းခြင်းတွင် အရည်အသွေးသေချာစေရန်အတွက် အရေးကြီးပါသည်။ ပုံမှန်သန့်ရှင်းရေး၊ ချောဆီနှင့် မှိုအစိတ်အပိုင်းများကို အကဲဖြတ်ခြင်းသည် အစိတ်အပိုင်းအရည်အသွေးကို ထိခိုက်စေနိုင်သည့် ဝတ်ဆင်မှု၊ ပျက်စီးမှု၊ သို့မဟုတ် ပျက်စီးယိုယွင်းမှုတို့ကို တားဆီးရန် ကူညီပေးသည်။ တသမတ်တည်း ပုံသွင်းခြင်းစွမ်းဆောင်ရည်ကို ထိန်းသိမ်းထားရန် ဟောင်းနွမ်းနေသော သို့မဟုတ် ပျက်စီးနေသော မှိုအစိတ်အပိုင်းများကို အချိန်မီ ပြုပြင်ခြင်း သို့မဟုတ် အစားထိုးခြင်းသည် မရှိမဖြစ်လိုအပ်ပါသည်။
- စာရွက်စာတမ်းနှင့် ခြေရာခံနိုင်မှု-ဆေးထိုးပုံသွင်းခြင်းတွင် အရည်အသွေးထိန်းချုပ်မှုအတွက် ပြည့်စုံသောစာရွက်စာတမ်းများနှင့် ခြေရာခံနိုင်မှုမှတ်တမ်းများကို ထိန်းသိမ်းခြင်းသည် မရှိမဖြစ်လိုအပ်ပါသည်။ လုပ်ငန်းစဉ်ကန့်သတ်ချက်များ၊ စစ်ဆေးရေးရလဒ်များ၊ ပစ္စည်းအချက်အလက်များနှင့် ထုတ်လုပ်နေစဉ်အတွင်း ပြုလုပ်ခဲ့သော ပြောင်းလဲမှု သို့မဟုတ် ပြုပြင်ပြောင်းလဲမှုများကို မှတ်တမ်းတင်ရန် အရေးကြီးပါသည်။ သင့်လျော်သောစာရွက်စာတမ်းများသည် အစိတ်အပိုင်းများကို ခြေရာခံနိုင်စေပြီး အရင်းခံအကြောင်းရင်းခွဲခြမ်းစိတ်ဖြာမှုကို လွယ်ကူချောမွေ့စေပြီး အရည်အသွေးတွင် ညီညွတ်မှုကိုသေချာစေသည်။
- လေ့ကျင့်ရေးနှင့် ကျွမ်းကျင်မှု ဖွံ့ဖြိုးတိုးတက်ရေး- အော်ပရေတာများ၊ နည်းပညာရှင်များနှင့် အရည်အသွေးထိန်းချုပ်ရေးဝန်ထမ်းများအတွက် လုံလောက်သောလေ့ကျင့်ရေးနှင့် ကျွမ်းကျင်မှုဖွံ့ဖြိုးတိုးတက်ရေးအစီအစဉ်များကို ပံ့ပိုးပေးခြင်းသည် ဆေးထိုးပုံသွင်းခြင်းလုပ်ငန်းစဉ်များ၊ အရည်အသွေးလိုအပ်ချက်များနှင့် စစ်ဆေးရေးနည်းပညာများကို နားလည်သဘောပေါက်စေပါသည်။ ကောင်းမွန်စွာ လေ့ကျင့်ထားသော ဝန်ထမ်းများသည် ချို့ယွင်းချက်များကို ရှာဖွေတွေ့ရှိနိုင်ပြီး ပြဿနာများကို ဖြေရှင်းနိုင်ပြီး အရည်အသွေးမြင့် ထုတ်လုပ်မှုကို ထိရောက်စွာ ထိရောက်စွာ ပြုပြင်ပေးနိုင်ပါသည်။
အဖြစ်များသော ထိုးဆေးပုံသွင်းခြင်း ချို့ယွင်းချက်တို့ကို မည်သို့ရှောင်ရှားရမည်နည်း
ဆေးထိုးပုံသွင်းခြင်း လုပ်ငန်းစဉ်များကို ပုံမှန်စစ်ဆေးခြင်း၊ စောင့်ကြည့်ခြင်းနှင့် ခွဲခြမ်းစိတ်ဖြာခြင်းနှင့် စက်ကိရိယာနှင့် မှိုများကို သင့်လျော်သော ပြုပြင်ထိန်းသိမ်းခြင်းနှင့် ချိန်ညှိခြင်းတို့သည် အဆိုပါအဖြစ်များသော ချို့ယွင်းချက်များကို ဖော်ထုတ်ဖြေရှင်းရန် ကူညီပေးနိုင်ပါသည်။
- စုပ်ခွက်များ-စုပ်ခွက်အမှတ်အသားများသည် မညီညာသော အေးခဲခြင်း သို့မဟုတ် ကျုံ့သွားခြင်းကြောင့် ပုံသွင်းထားသော အစိတ်အပိုင်း၏ မျက်နှာပြင်ပေါ်တွင် စိတ်ဓာတ်ကျခြင်း သို့မဟုတ် ကုဒ်များဖြစ်သည်။ နစ်မြုပ်မှုအမှတ်အသားများကို ရှောင်ရှားရန် သင့်လျော်သော တံခါးပေါက်တည်နေရာနှင့် ဒီဇိုင်း၊ အကောင်းဆုံး အအေးပေးစနစ် ဒီဇိုင်းနှင့် တူညီသော နံရံအထူဖြန့်ဝေမှုကို ထည့်သွင်းစဉ်းစားသင့်သည်။ ဆေးထိုးဖိအားကို တိုးမြင့်ခြင်း သို့မဟုတ် အအေးခံချိန်ကို ချိန်ညှိခြင်းတို့ကလည်း စုပ်ခွက်အမှတ်အသားများကို နည်းပါးအောင် ကူညီပေးနိုင်သည်။
- Warpage-Warpage သည် မညီမညာ အအေးခံခြင်း သို့မဟုတ် ကျန်နေသော ဖိစီးမှုများကြောင့် ထုတ်လိုက်ပြီးနောက် ပုံသွင်းထားသော အစိတ်အပိုင်း၏ ပုံပျက်ခြင်း သို့မဟုတ် ကွေးခြင်းကို ရည်ညွှန်းသည်။ တူညီသောနံရံအထူကို ထိန်းသိမ်းခြင်း၊ သင့်လျော်သော အအေးခံလမ်းကြောင်းများကို အသုံးပြုခြင်းနှင့် မှို၏ မျှတသော ဖြည့်သွင်းခြင်းနှင့် ထုပ်ပိုးခြင်းတို့သည် warp ဖြစ်ခြင်းမှ ကာကွယ်ရန် အရေးကြီးပါသည်။ မှိုအပူချိန်ကို ကောင်းမွန်အောင်ပြုလုပ်ခြင်း၊ သင့်လျော်သော မူကြမ်းထောင့်များကို အသုံးပြုခြင်းနှင့် ပစ္စည်းအပူချိန်နှင့် ဆေးထိုးခြင်းအမြန်နှုန်းကို ထိန်းချုပ်ခြင်းဖြင့် warpage ကို လျှော့ချရန် ကူညီပေးနိုင်ပါသည်။
- Flash ကို:ပိုလျှံသောပစ္စည်းသည် မှိုခွဲခြင်းမျဉ်းသို့ စီးဆင်းသွားသောအခါ၊ ပါးလွှာသော၊ မလိုလားအပ်သော ပရိုဂရမ်များ သို့မဟုတ် နောက်ဆုံးအပိုင်းရှိ အပိုပစ္စည်းများကို ဖြစ်ပေါ်စေသည်။ လုံလောက်သော clamping force ကိုအသုံးပြုခြင်း၊ တိကျသော ချိန်ညှိခြင်းနှင့် သင့်လျော်သော လေဝင်လေထွက်နည်းများကို အသုံးပြုခြင်း အပါအဝင် သင့်လျော်သော မှိုဒီဇိုင်းကို သေချာစေခြင်းဖြင့် flash ကို ထိထိရောက်ရောက် တားဆီးနိုင်ပါသည်။ ဆေးထိုးဖိအား၊ အပူချိန်နှင့် စက်ဝန်းအချိန်ကဲ့သို့သော လုပ်ငန်းစဉ်ဘောင်များကို ပိုမိုကောင်းမွန်အောင်ပြုလုပ်ခြင်းသည် flash ကို လျော့နည်းစေသည်။
- တိုတိုရိုက်ချက်-ထိုးသွင်းထားသော ပစ္စည်းသည် မှိုအပေါက်ကို မဖြည့်နိုင်သဖြင့် မပြည့်စုံသော အစိတ်အပိုင်းကို ဖြစ်ပေါ်စေသောအခါ အမြန်ရိုက်ချက် ထွက်ပေါ်လာသည်။ သင့်လျော်သောပစ္စည်းရွေးချယ်ခြင်း၊ လုံလောက်သောအရည်ပျော်မှုအပူချိန်နှင့် ပျစ်နိုင်မှုသေချာစေရန်နှင့် သင့်လျော်သောဆေးထိုးခြင်းဖိအားနှင့် အချိန်ကို ထိန်းသိမ်းခြင်းသည် ဓာတ်ပုံတိုများကိုရှောင်ရှားရန် မရှိမဖြစ်လိုအပ်ပါသည်။ ထို့အပြင်၊ လုံလောက်သောအပြေးသမားနှင့် တံခါးအရွယ်အစားအတွက် မှိုဒီဇိုင်းကို စစ်ဆေးအတည်ပြုခြင်းသည် အမြန်ရိုက်ချက်များကို တားဆီးနိုင်မည်ဖြစ်သည်။
- Weld လိုင်းများ-မျက်နှာပြင်နှစ်ခု သို့မဟုတ် နှစ်ခုထက်ပိုသော သွန်းသော အရာများ စီးဆင်းမှု ဆုံပြီး မျက်နှာပြင်ပေါ်၌ မြင်နိုင်သော မျဉ်းကြောင်း သို့မဟုတ် အမှတ်အသား ဖြစ်ပေါ်စေသောအခါ ဂဟေဆက်လိုင်းများ ဖြစ်ပေါ်သည်။ ကောင်းမွန်သောတံခါးနှင့်အပြေးသမားဒီဇိုင်း၊ အကောင်းဆုံးအရည်ပျော်သည့်အပူချိန်၊ ဆေးထိုးသည့်အမြန်နှုန်းနှင့် ပစ္စည်းစီးဆင်းမှုကို ချိန်ညှိခြင်းနှင့် အစိတ်အပိုင်းဂျီသြမေတြီသည် ဂဟေလိုင်းများကို လျှော့ချနိုင်သည်။ မှိုစီးဆင်းမှုကို ခွဲခြမ်းစိတ်ဖြာခြင်းနှင့် တံခါးနေရာချထားခြင်း ပိုမိုကောင်းမွန်အောင်ပြုလုပ်ခြင်းသည် ဂဟေလိုင်းများကို တားဆီးခြင်း သို့မဟုတ် လျော့ပါးစေရန် ကူညီပေးနိုင်သည်။
- မီးလောင်မှု အမှတ်အသားများမီးလောင်မှုအမှတ်အသားများသည် အပူလွန်ကဲခြင်း သို့မဟုတ် အပူလွန်ကဲခြင်းကြောင့် ပုံသွင်းထားသော အစိတ်အပိုင်း၏ မျက်နှာပြင်ပေါ်တွင် အရောင်ပြောင်းခြင်း သို့မဟုတ် အနက်ရောင်အစက်အပြောက်များဖြစ်သည်။ အပူချိန်လွန်ကဲစွာ အရည်ပျော်ခြင်းကို ရှောင်ကြဉ်ခြင်း၊ သင့်လျော်သော အအေးခံလမ်းကြောင်းများကို အသုံးပြုခြင်းနှင့် စက်လည်ပတ်ချိန်ကို အကောင်းဆုံးဖြစ်အောင် ပြုလုပ်ခြင်းဖြင့် မီးလောင်မှု အမှတ်အသားများကို တားဆီးနိုင်ပါသည်။ လုံလောက်သော လေဝင်လေထွက်၊ သင့်လျော်သော တံခါးပေါက်ဒီဇိုင်းနှင့် မှိုအပူချိန်ကို ထိန်းချုပ်ခြင်းသည်လည်း မီးလောင်ဒဏ်ရာများကို လျော့နည်းစေပါသည်။
ပုံသွင်းပြီးသော လုပ်ဆောင်ချက်များ- ပြီးစီးမှုနှင့် စုဝေးမှု
ဆေးထိုးပုံသွင်းပြီးနောက်၊ ပုံသွင်းထားသော အစိတ်အပိုင်းများစွာသည် အလိုရှိသော နောက်ဆုံးထုတ်ကုန်ကိုရရှိရန် အပိုအချောထည်နှင့် တပ်ဆင်ခြင်းလုပ်ငန်းများကို လိုအပ်နိုင်ပါသည်။ ဤပုံသွင်းပြီးနောက် လုပ်ဆောင်မှုများတွင်-
- ချုံ့ခြင်းဖြတ်တောက်ခြင်း သို့မဟုတ် ဖြတ်တောက်ခြင်း ကိရိယာများကို အသုံးပြု၍ ပုံသွင်းထားသော အစိတ်အပိုင်းတစ်ဝိုက်ရှိ ပိုလျှံနေသော အရာများကို ဖယ်ရှားပါ။
- မျက်နှာပြင်ကုသမှု:ပန်းချီ၊ အပေါ်ယံ၊ သို့မဟုတ် အသွေးအသားပေးခြင်းစသည့် နည်းမျိုးစုံကို အသုံးပြု၍ မျက်နှာပြင်၏ အသွင်အပြင် သို့မဟုတ် လုပ်ဆောင်နိုင်စွမ်းကို မြှင့်တင်ပါ။
- ညီလာခံ:ပုံသွင်းထားသော အစိတ်အပိုင်းများစွာကို ချိတ်ဆက်ခြင်း သို့မဟုတ် နောက်ဆုံးထုတ်ကုန်ကို အပြီးသတ်ရန်အတွက် တွယ်ကပ်များ၊ ထည့်သွင်းမှုများ သို့မဟုတ် အညွှန်းများကဲ့သို့သော အစိတ်အပိုင်းများကို ပေါင်းထည့်ခြင်း။
- စမ်းသပ်ခြင်း:အတိုင်းအတာ ခွဲခြမ်းစိတ်ဖြာခြင်း၊ ပစ္စည်းဂုဏ်သတ္တိများ စမ်းသပ်ခြင်း သို့မဟုတ် စွမ်းဆောင်ရည်စမ်းသပ်ခြင်းကဲ့သို့ အမျိုးမျိုးသော စမ်းသပ်မှုနည်းလမ်းများဖြင့် အစိတ်အပိုင်း အရည်အသွေးနှင့် လုပ်ဆောင်နိုင်စွမ်းကို အတည်ပြုခြင်း။
- ထုပ်ပိုးခြင်းနှင့်သင်္ဘောပို့ခြင်း:ဖောက်သည်များ သို့မဟုတ် သုံးစွဲသူများထံ တင်ပို့ရန်အတွက် သင့်လျော်သောထုပ်ပိုးမှုနှင့် တံဆိပ်ကပ်ခြင်း
ပုံသွင်းပြီးသည့်လုပ်ငန်းများကို ရွေးချယ်ခြင်းသည် တိကျသောလျှောက်လွှာနှင့် အလိုရှိသော နောက်ဆုံးထုတ်ကုန်လက္ခဏာများပေါ်တွင် မူတည်သည်။ ဆေးထိုးပုံသွင်းခြင်းဆိုင်ရာ ကျွမ်းကျင်သူများ၊ အချောသပ်ခြင်းနှင့် တပ်ဆင်ခြင်းဆိုင်ရာ ကျွမ်းကျင်သူများအကြား အနီးကပ် ပူးပေါင်းဆောင်ရွက်ခြင်းဖြစ်ပြီး ဖောက်သည်သည် အလိုရှိသော ထုတ်ကုန်အရည်အသွေးနှင့် လုပ်ဆောင်နိုင်စွမ်းကို ရရှိရန် အရေးကြီးပါသည်။ မှန်ကန်သော အစီအစဉ်ဆွဲခြင်းနှင့် မှိုတက်ခြင်းလုပ်ငန်းများကို ထုတ်လုပ်မှုလုပ်ငန်းစဉ်တွင် ပေါင်းစပ်ခြင်းသည် ထိရောက်သောထုတ်လုပ်မှုနှင့် အရည်အသွေးမြင့်ထုတ်ကုန်များကို အချိန်နှင့်တစ်ပြေးညီ ပို့ဆောင်ပေးခြင်းကို သေချာစေနိုင်သည်။
ထိုးသွင်းပုံသွင်းခြင်းနှင့် အခြားပလပ်စတစ်ထုတ်လုပ်ခြင်းလုပ်ငန်းစဉ်များ
ပလတ်စတစ်ထုတ်လုပ်မှု လုပ်ငန်းစဉ်တစ်ခုစီတွင် အားသာချက်များနှင့် ကန့်သတ်ချက်များရှိ၍ မတူညီသော အသုံးချမှုများအတွက် သင့်လျော်စေသည်။
- ဆေးထိုးပုံသွင်းခြင်း- ဆေးထိုးပုံသွင်းခြင်းသည် ပလပ်စတစ်အစိတ်အပိုင်းများထုတ်လုပ်ရန်အတွက် အလွန်အသုံးများပြီး စွယ်စုံရထုတ်လုပ်သည့် လုပ်ငန်းစဉ်တစ်ခုဖြစ်သည်။ ၎င်းသည် မြင့်မားသော ထုတ်လုပ်မှု ထိရောက်မှု၊ တိကျသော အစိတ်အပိုင်း အတုယူမှုနှင့် ရှုပ်ထွေးသော ဂျီသြမေတြီများ ဖန်တီးနိုင်မှု စသည့် အားသာချက်များ ပေးဆောင်သည်။ ထိုးသွင်းပုံသွင်းခြင်းသည် ပမာဏမြင့်မားသော ထုတ်လုပ်မှုလုပ်ငန်းအတွက် သင့်လျော်ပြီး ကျယ်ပြန့်သော သာမိုပလပ်စတစ်ပစ္စည်းများကို အသုံးပြုရန် ခွင့်ပြုသည်။ ၎င်းသည် မော်တော်ကား၊ လူသုံးကုန်ပစ္စည်းများနှင့် ဆေးဘက်ဆိုင်ရာ စက်ပစ္စည်းများကဲ့သို့သော လုပ်ငန်းအမျိုးမျိုးအတွက် သင့်လျော်ကောင်းမွန်သော ဘက်မလိုက်တိကျမှုနှင့် မျက်နှာပြင် အပြီးသတ်မှုကို ပေးစွမ်းသည်။
- လေမှုတ်ပုံသွင်းခြင်း- လေမှုတ်ပုံသွင်းခြင်းသည် ပုလင်းများ၊ ကွန်တိန်နာများနှင့် မော်တော်ယာဥ်အစိတ်အပိုင်းများကဲ့သို့သော အခေါင်းပေါက်ပလပ်စတစ်အစိတ်အပိုင်းများထုတ်လုပ်ရန်အတွက် အဓိကအသုံးပြုသည့်လုပ်ငန်းစဉ်တစ်ခုဖြစ်သည်။ ၎င်းတွင် ပလပ်စတစ်ကို အရည်ပျော်ပြီး မှိုပေါက်ထဲသို့ ဖြည့်သွင်းကာ အလိုရှိသော ပုံသဏ္ဍာန်ကို ဖန်တီးပေးသည်။ Blow molding သည် ထုထည်မြင့်မားသော ထုတ်လုပ်မှုအတွက် သင့်လျော်ပြီး တူညီသော နံရံအထူရှိသော ကြီးမားပြီး ပေါ့ပါးသော အစိတ်အပိုင်းများကို ထုတ်လုပ်နိုင်သည်။ သို့သော်လည်း ဆေးထိုးပုံသွင်းခြင်းနှင့် နှိုင်းယှဉ်ပါက အစိတ်အပိုင်း ရှုပ်ထွေးမှုနှင့် ပစ္စည်းရွေးချယ်မှုတွင် အကန့်အသတ်ရှိသည်။
- အပူချိန်ဖော်ခြင်း-Thermoforming ဆိုသည်မှာ သာမိုပလတ်စတစ်စာရွက်ကို အပူပေးပြီး မှိုများ သို့မဟုတ် ဖုန်စုပ်စက်ဖြင့် ပုံသွင်းခြင်းဖြင့် ပလတ်စတစ်အစိတ်အပိုင်းများ ထုတ်လုပ်ရန် အသုံးပြုသည့် လုပ်ငန်းစဉ်တစ်ခုဖြစ်သည်။ ၎င်းသည် ထုပ်ပိုးခြင်း၊ တစ်ခါသုံးထုတ်ကုန်များနှင့် ဗန်းများနှင့် အဖုံးများကဲ့သို့သော အကြီးစားထုတ်ကုန်များတွင် အသုံးများသည်ကို တွေ့ရှိရသည်။ Thermoforming သည် ကြီးမားသော အစိတ်အပိုင်းများအတွက် ကုန်ကျစရိတ်သက်သာသော ထုတ်လုပ်မှုကို ပေးစွမ်းပြီး လျင်မြန်သော ပုံတူပုံစံကို ပြုလုပ်နိုင်သည်။ သို့သော်၊ ဆေးထိုးပုံသွင်းခြင်းနှင့် နှိုင်းယှဉ်ပါက အစိတ်အပိုင်း ရှုပ်ထွေးမှု၊ ပစ္စည်းရွေးချယ်မှုနှင့် အတိုင်းအတာတိကျမှုတို့နှင့်ပတ်သက်၍ ကန့်သတ်ချက်များရှိသည်။
- Extrusion:Extrusion သည် ပလပ်စတစ်ပရိုဖိုင်များ၊ စာရွက်များ၊ ပြွန်များနှင့် ရုပ်ရှင်များ ထုတ်လုပ်ရန် စဉ်ဆက်မပြတ် လုပ်ငန်းစဉ်တစ်ခုဖြစ်သည်။ ၎င်းတွင် ပလပ်စတစ်အစေးကို အရည်ပျော်ပြီး လိုချင်သောပုံသဏ္ဍာန်ဖန်တီးရန် အသေခံရန် တွန်းအားပေးခြင်း ပါဝင်သည်။ Extrusion သည် တသမတ်တည်း ဖြတ်ပိုင်းဖြင့် ရှည်လျားပြီး အဆက်မပြတ် ပလပ်စတစ် ထုတ်ကုန်များ ထုတ်လုပ်ရန်အတွက် သင့်လျော်သည်။ Extrusion သည် မြင့်မားသော ထုတ်လုပ်မှုနှုန်းထားနှင့် ကုန်ကျစရိတ်-ထိရောက်မှုကို ပေးစွမ်းသော်လည်း၊ ဆေးထိုးပုံသွင်းခြင်းနှင့် နှိုင်းယှဉ်ပါက ရှုပ်ထွေးသောအစိတ်အပိုင်းများ ဂျီသြမေတြီများနှင့် တိကျသောအတိုင်းအတာထိန်းချုပ်မှုတွင် အကန့်အသတ်ရှိသည်။
- ဖိအားပုံသွင်းခြင်း-ဖိသိပ်မှုပုံသွင်းခြင်းတွင် အပူပေးထားသော မှိုအပေါက်အတွင်း ကြိုတင်တိုင်းတာထားသော အပူချိန်ထိန်းပစ္စည်းပမာဏကို ကုသပြီး ပျောက်ကင်းသည်အထိ မြင့်မားသောဖိအားအောက်တွင် ဖိသိပ်ခြင်းပါဝင်သည်။ မော်တော်ယာဥ်အစိတ်အပိုင်းများနှင့် လျှပ်စစ်လျှပ်ကာများကဲ့သို့ မြင့်မားသောကြံ့ခိုင်မှုနှင့် အတိုင်းအတာတည်ငြိမ်မှုရှိသော အစိတ်အပိုင်းများထုတ်လုပ်ရာတွင် အသုံးများသောအသုံးပြုမှုကို တွေ့ရှိရသည်။ Compression molding သည် ကောင်းမွန်သော အစိတ်အပိုင်းများ လိုက်လျောညီထွေရှိမှု၊ မြင့်မားသော ထုတ်လုပ်မှု ထိရောက်မှုနှင့် ကျယ်ပြန့်သော ပစ္စည်းများကို အသုံးပြုနိုင်စွမ်းကို ပေးစွမ်းသည်။ သို့သော်၊ ဆေးထိုးပုံသွင်းခြင်းနှင့် နှိုင်းယှဉ်ပါက အစိတ်အပိုင်းရှုပ်ထွေးမှုနှင့် စက်ဝန်းအချိန်တို့၌ အကန့်အသတ်ရှိသည်။
Thermoplastic Injection Molding ၏အသုံးချမှုများ
အမျိုးမျိုးသောစက်မှုလုပ်ငန်းများသည် ၎င်း၏ဘက်စုံအသုံးပြုနိုင်မှု၊ ထိရောက်မှုနှင့် ကုန်ကျစရိတ်သက်သာမှုတို့ကြောင့် သာမိုပလတ်စတစ်ဆေးထိုးခြင်းကို တွင်ကျယ်စွာအသုံးပြုကြသည်။ သာမိုပလတ်စတစ်ဆေးထိုးခြင်း၏ အသုံးချမှုအချို့တွင်-
- မော်တော်ကားလုပ်ငန်း မော်တော်ယာဥ်လုပ်ငန်းသည် အတွင်းပိုင်းနှင့် အပြင်ပိုင်းဖြတ်ပိုင်း၊ ဒက်ရှ်ဘုတ်များ၊ တံခါးဘောင်များ၊ ဘမ်ဘာများနှင့် လျှပ်စစ်ချိတ်ဆက်ကိရိယာများအပါအဝင် အစိတ်အပိုင်းအမျိုးမျိုးကို ထုတ်လုပ်ရန်အတွက် သာမိုပလတ်စတစ်ဆေးထိုးခြင်းအား ကျယ်ကျယ်ပြန့်ပြန့်အသုံးပြုသည်။ လုပ်ငန်းစဉ်သည် တိကျသောအစိတ်အပိုင်းပုံတူပွားခြင်း၊ ရှုပ်ထွေးသောဂျီသြမေတြီများနှင့် ပေါ့ပါးသောပစ္စည်းများကိုရရှိစေပြီး ဆီစားသက်သာမှုနှင့် ဒီဇိုင်းပြောင်းလွယ်ပြင်လွယ်ကို ပိုမိုကောင်းမွန်စေသည်။
- လူသုံးကုန်:ဆေးထိုးပုံသွင်းခြင်းသည် အိမ်သုံးပစ္စည်းများ၊ အီလက်ထရွန်းနစ်ပစ္စည်းများ၊ ထုပ်ပိုးထားသော ကွန်တိန်နာများနှင့် အရုပ်များကဲ့သို့သော လူသုံးကုန်ပစ္စည်းများထုတ်လုပ်ရာတွင် ကျယ်ပြန့်သောအသုံးချမှုများကို တွေ့ရှိရသည်။ လုပ်ငန်းစဉ်သည် တသမတ်တည်းရှိသော အတိုင်းအတာနှင့် မျက်နှာပြင်အချောထည်များဖြင့် တာရှည်ခံ အရည်အသွေးမြင့် ထုတ်ကုန်များ အစုလိုက်အပြုံလိုက် ထုတ်လုပ်မှုကို ခွင့်ပြုပေးပါသည်။ ၎င်းသည် စိတ်ကြိုက်ရွေးချယ်စရာများနှင့် ထုတ်ကုန်ကို လျင်မြန်စွာ ထပ်တလဲလဲပြုလုပ်နိုင်စေပါသည်။
- ဆေးဘက်ဆိုင်ရာကိရိယာများ-ထိုးဆေးပုံသွင်းခြင်းသည် ဆေးထိုးအပ်များ၊ ခွဲစိတ်ကိရိယာများ၊ စိုက်နိုင်သော အစိတ်အပိုင်းများနှင့် ဆေးဝါးပို့ဆောင်မှုစနစ်များအပါအဝင် စက်ပစ္စည်းအများအပြားကို ထုတ်လုပ်ရန်အတွက် ဆေးလုပ်ငန်းတွင် အရေးပါသောအခန်းကဏ္ဍမှ ပါဝင်ပါသည်။ လုပ်ငန်းစဉ်သည် ကျန်းမာရေးစောင့်ရှောက်မှုကဏ္ဍ၏ တင်းကျပ်သော စည်းမျဉ်းစည်းကမ်းသတ်မှတ်ချက်များနှင့် ကိုက်ညီသည့် ပိုးမွှား၊ တိကျသော၊ နှင့် ဇီဝသဟဇာတရှိသော အစိတ်အပိုင်းများ ထုတ်လုပ်ခြင်းကို သေချာစေသည်။
- အီလက်ထရွန်းနစ်နှင့် လျှပ်စစ်စက်မှုလုပ်ငန်း-အီလက်ထရွန်းနစ်စက်မှုလုပ်ငန်းသည် လျှပ်စစ်ချိတ်ဆက်ကိရိယာများ၊ အကာအရံများ၊ ခလုတ်များနှင့် အခြားအစိတ်အပိုင်းများကို ထုတ်လုပ်ရန်အတွက် ဆေးထိုးပုံသွင်းခြင်းကို အသုံးပြုသည်။ လုပ်ငန်းစဉ်သည် မြင့်မားသော ဘက်မြင်တိကျမှု၊ ကောင်းမွန်သော မျက်နှာပြင်အချောထည်နှင့် ထည့်သွင်းပုံသွင်းခြင်းနှင့် overmolding ကဲ့သို့သော အင်္ဂါရပ်များကို ပေါင်းစပ်နိုင်စေပြီး ရှုပ်ထွေးသော အီလက်ထရွန်နစ် စည်းဝေးပွဲများကို ထိရောက်စွာ ထုတ်လုပ်နိုင်စေမည်ဖြစ်သည်။
- ထုပ်ပိုးမှုလုပ်ငန်းအစားအသောက်နှင့် အဖျော်ယမကာ၊ ဆေးဝါးနှင့် တစ်ကိုယ်ရည် စောင့်ရှောက်မှုများ အပါအဝင် အမျိုးမျိုးသော လုပ်ငန်းများတွင် ပလပ်စတစ်ထုပ်ပိုးမှု ကွန်တိန်နာများ၊ ဦးထုပ်များ၊ အပိတ်များနှင့် ပုလင်းများ ထုတ်လုပ်ရန်အတွက် ဆေးထိုးပုံသွင်းခြင်းကို အများအားဖြင့် အသုံးပြုကြသည်။ လုပ်ငန်းစဉ်သည် ပေါ့ပါးသော၊ တာရှည်ခံကာ ဆွဲဆောင်မှုရှိသော ထုပ်ပိုးမှုဖြေရှင်းချက်များအား ထိရောက်သောထုတ်လုပ်မှုစက်ဝန်းများဖြင့် ဖန်တီးနိုင်စေပါသည်။
- အာကာသလုပ်ငန်း-လေပြွန်ကွင်းများ၊ အတွင်းပိုင်းပြားများနှင့် တည်ဆောက်ပုံဆိုင်ရာ အစိတ်အပိုင်းများကဲ့သို့သော ပေါ့ပါးပြီး စွမ်းဆောင်ရည်မြင့်မားသော အစိတ်အပိုင်းများကို ထုတ်လုပ်ရန်အတွက် အာကာသယာဉ်ကဏ္ဍတွင် ဆေးထိုးပုံသွင်းခြင်းကို အသုံးပြုသည်။ လုပ်ငန်းစဉ်သည် အဆင့်မြင့်ပစ္စည်းများနှင့် အနုစိတ်သော ဂျီသြမေတြီများကို အသုံးပြုနိုင်ပြီး အလေးချိန်လျှော့ချရန်နှင့် ဆီစားသက်သာမှုကို မြှင့်တင်ပေးသည်။
Thermoplastic Injection Molding ၏ ပတ်ဝန်းကျင် ထိခိုက်မှု
သာမိုပလတ်စတစ်ဆေးထိုးပုံသွင်းခြင်းသည် ၎င်း၏အကျိုးကျေးဇူးများစွာကြောင့် လူကြိုက်များသောကုန်ထုတ်လုပ်မှုလုပ်ငန်းစဉ်တစ်ခုဖြစ်သော်လည်း ၎င်း၏ပတ်ဝန်းကျင်ဆိုင်ရာအကျိုးသက်ရောက်မှုကို ထည့်သွင်းစဉ်းစားရန်လည်း မရှိမဖြစ်လိုအပ်ပါသည်။ ဤသည်မှာ ထည့်သွင်းစဉ်းစားရမည့် အချက်အချို့ဖြစ်သည်-
- ပစ္စည်းစွမ်းဆောင်ရည်-သာမိုပလတ်စတစ်ဆေးထိုးပုံသွင်းခြင်းသည် စွန့်ပစ်ပစ္စည်းများကို နည်းပါးအောင်ပြုလုပ်ခြင်းဖြင့် ပစ္စည်း၏ထိရောက်မှုကို မြှင့်တင်ပေးပါသည်။ လုပ်ငန်းစဉ်သည် မှိုထဲသို့ထိုးသွင်းသည့်ပစ္စည်းပမာဏအပေါ် တိကျသောထိန်းချုပ်မှုကိုအသုံးပြုပြီး ပိုလျှံသောပစ္စည်းလိုအပ်မှုကို လျှော့ချပေးသည်။ ထုတ်လုပ်သူများသည် အပိုင်းအစများ သို့မဟုတ် စွန့်ပစ်ထားသော အစိတ်အပိုင်းများကို ပြန်လည်အသုံးပြုရန် ပြန်လည်အသုံးပြုရန်နှင့် စွန့်ပစ်ပစ္စည်းများကို ပိုမိုလျှော့ချရန်အတွက် ပြန်လည်အသုံးပြုရန်နှင့် ပြန်လည်အသုံးပြုသည့်နည်းစနစ်များကိုလည်း အသုံးပြုနိုင်သည်။
- စွမ်းအင်သုံးစွဲမှု့:ထုတ်လုပ်သူများသည် ဆေးထိုးပုံသွင်းစက်များကို စွမ်းအင်သက်သာစေရန် ဒီဇိုင်းထုတ်ကာ servo motors နှင့် variable speed drives ကဲ့သို့သော ခေတ်မီနည်းပညာများပါရှိသော ခေတ်မီမော်ဒယ်များနှင့်အတူ ပုံသွင်းစဉ်အတွင်း ပါဝါသုံးစွဲမှုကို လျှော့ချခြင်းဖြင့် ဤအင်္ဂါရပ်များသည် စွမ်းအင်လိုအပ်ချက်များ နည်းပါးပြီး သဘာဝပတ်ဝန်းကျင်ဆိုင်ရာ ထိခိုက်မှုကို လျှော့ချပေးခြင်းဖြင့် စွမ်းအင်အသုံးပြုမှုကို အကောင်းဆုံးဖြစ်အောင် လုပ်ဆောင်ပေးသည်။
- စွန့်ပစ်ပစ္စည်းစီမံခန့်ခွဲမှု:စွန့်ပစ်ပစ္စည်းများကို လျှော့ချနေစဉ်တွင် ထုတ်လုပ်သူများသည် လက်ကျန်ပစ္စည်းများ၊ တံတွေးများ သို့မဟုတ် အပြေးသမားများကို ကိုင်တွယ်ရန် သင့်လျော်သော စွန့်ပစ်ပစ္စည်းစီမံခန့်ခွဲမှု အလေ့အကျင့်များကို အကောင်အထည်ဖော်သင့်သည်။ ဆေးထိုးပုံသွင်းစဉ်အတွင်း ထုတ်လုပ်သည့် ပလတ်စတစ်အမှိုက်များကို စုဆောင်းပြီး ပြန်လည်အသုံးပြုရန်အတွက် ထုတ်လုပ်သူသည် ပြန်လည်အသုံးပြုသည့် အစီအစဉ်များကို ထူထောင်နိုင်ပြီး၊ ထို့ကြောင့် အမှိုက်ပုံများသို့ ပေးပို့သော အမှိုက်များကို လျှော့ချနိုင်သည်။
- ဓာတ်ငွေ့ထုတ်လွှတ်မှု လျှော့ချရေး- သာမိုပလတ်စတစ်ဆေးထိုးပုံသွင်းခြင်းသည် ယေဘုယျအားဖြင့် အခြားထုတ်လုပ်မှုလုပ်ငန်းစဉ်များထက် ဓာတ်ငွေ့ထုတ်လွှတ်မှု နည်းပါးသည်။ ထုတ်လုပ်သူများသည် eco-friendly ပစ္စည်းများအသုံးပြုခြင်း၊ စွမ်းအင်သက်သာသော စက်ကိရိယာများအသုံးပြုခြင်းနှင့် ထုတ်လွှတ်သည့်ထုတ်လွှတ်မှုအားလုံးကို ဖမ်းယူရန်အတွက် အဆင့်မြင့်အိပ်ဇောနှင့် စစ်ထုတ်ခြင်းစနစ်များကို အသုံးပြုခြင်းဖြင့် ဓာတ်ငွေ့ထုတ်လွှတ်မှုကို လျှော့ချနိုင်သည်။
- ရေရှည်တည်တံ့နိုင်သော ပစ္စည်းရွေးချယ်မှုများ-သာမိုပလတ်စတစ်ပစ္စည်းများကို ရွေးချယ်ခြင်းသည် ဆေးထိုးပုံသွင်းခြင်း၏ သဘာဝပတ်ဝန်းကျင် ရေရှည်တည်တံ့မှုကို သိသိသာသာ သက်ရောက်မှုရှိနိုင်သည်။ ဇီဝပြိုကွဲပျက်စီးနိုင်သော သို့မဟုတ် ဇီဝအခြေခံပလတ်စတစ်များအပြင် ပြန်လည်အသုံးပြုသော သို့မဟုတ် ပြန်လည်အသုံးပြုနိုင်သောပစ္စည်းများကို ရွေးချယ်ခြင်းသည် လုပ်ငန်းစဉ်တစ်ခုလုံး၏ ဂေဟစနစ်ခြေရာကို လျှော့ချရန် ကူညီပေးနိုင်သည်။
Life Cycle ထည့်သွင်းစဉ်းစားချက်များ- ပုံသွင်းထားသောထုတ်ကုန်၏ ဘဝသံသရာတစ်ခုလုံးကို ထည့်သွင်းစဉ်းစားခြင်းသည် ၎င်း၏ပတ်ဝန်းကျင်ဆိုင်ရာ အကျိုးသက်ရောက်မှုကို အကဲဖြတ်ရန်အတွက် မရှိမဖြစ်လိုအပ်ပါသည်။ ဒီဇိုင်းနှင့် ပစ္စည်းရွေးချယ်မှု အဆင့်များအတွင်း ထုတ်လုပ်သူများသည် အစိတ်အပိုင်း၏ တာရှည်ခံမှု၊ ၎င်း၏ ပြန်လည်အသုံးပြုနိုင်မှုနှင့် သက်တမ်းကုန်ဆုံးရန် စွန့်ပစ်ခြင်း သို့မဟုတ် ပြန်လည်အသုံးပြုရန် အလားအလာများကဲ့သို့သော အချက်များကို ထည့်သွင်းစဉ်းစားသင့်သည်။
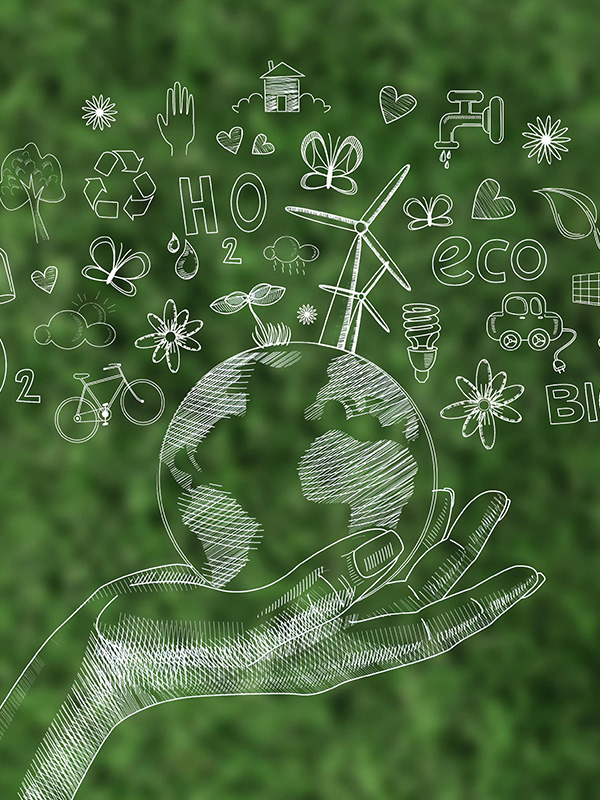
Thermoplastic Injection Molding ၏အနာဂတ်
သာမိုပလပ်စတစ်ဆေးထိုးပုံသွင်းခြင်း၏ အနာဂတ်သည် နည်းပညာတွင် ဆက်လက်တိုးတက်နေပြီး စက်မှုလုပ်ငန်းအမျိုးမျိုးရှိ အရည်အသွေးမြင့်၊ တိကျသောအစိတ်အပိုင်းများအတွက် ၀ယ်လိုအား တိုးလာခြင်းဖြင့် အလားအလာကောင်းနေပါသည်။ လာမည့်နှစ်များတွင် မျှော်မှန်းထားသည့် အဓိကတိုးတက်မှုအချို့ ပါဝင်သည်။
- ထိရောက်မှုနှင့် ကုန်ကျစရိတ်များကို လျှော့ချရန်အတွက် အလိုအလျောက်စနစ်နှင့် စက်ရုပ်များကို တိုးမြှင့်အသုံးပြုခြင်း။
- တစ်စိတ်တစ်ပိုင်းစွမ်းဆောင်ရည်ကို မြှင့်တင်ရန်နှင့် အပလီကေးရှင်းအသစ်များကို အသုံးပြုနိုင်ရန် ကြိုးပမ်းအားထုတ်မှုများသည် အစိတ်အပိုင်းအသစ်များနှင့် လုပ်ငန်းစဉ်များကို ဖော်ဆောင်ရန် အာရုံစိုက်ပါသည်။
- ဆေးထိုးပုံသွင်းခြင်း၏ သဘာဝပတ်ဝန်းကျင်ဆိုင်ရာ ထိခိုက်မှုကို လျှော့ချရန်အတွက် ပြန်လည်အသုံးပြုသည့်ပစ္စည်းများကို အသုံးပြုခြင်းနှင့် စွမ်းအင်သုံးစွဲမှုကို ပိုမိုကောင်းမွန်အောင်ပြုလုပ်ခြင်းကဲ့သို့သော ရေရှည်တည်တံ့သော အလေ့အကျင့်များကို တိုးပွားလာစေပါသည်။
- ဒီဇိုင်းနှင့် ထုတ်လုပ်မှု လုပ်ငန်းစဉ်များ ပိုမိုကောင်းမွန်လာစေရန် 3D ပရင့်ထုတ်ခြင်းနှင့် သရုပ်ဖော်ဆော့ဖ်ဝဲကဲ့သို့ ဒစ်ဂျစ်တယ်နည်းပညာများ ပေါင်းစပ်မှု။
ကမ္ဘာလုံးဆိုင်ရာ ဆေးထိုးပုံသွင်းခြင်းစျေးကွက်သည် အထူးသဖြင့် စက်မှုလုပ်ငန်းအမျိုးမျိုးတွင် ပလတ်စတစ်ထုတ်ကုန်များ ၀ယ်လိုအား တိုးလာခြင်းကြောင့် ထွန်းသစ်စနိုင်ငံများတွင် ကြီးထွားလျက်ရှိသည်။
မှန်ကန်သော ထိုးဆေးပုံသွင်းဖော်ကို ရွေးချယ်ခြင်း။
သင့်ပရောဂျက်၏အောင်မြင်မှုအတွက် မှန်ကန်သော ဆေးထိုးဖော်စပ်သူကို ရွေးချယ်ခြင်းသည် အရေးကြီးပါသည်။ ရွေးချယ်စရာများစွာကို အကဲဖြတ်ရန်၊ ဆိုက်လည်ပတ်မှုများကို လုပ်ဆောင်ရန်နှင့် လိုက်ဖက်ညီပြီး ရေရှည်တည်တံ့သော ပူးပေါင်းဆောင်ရွက်မှုကို သေချာစေရန်အတွက် အချိန်ယူပါ။
- ကျွမ်းကျင်မှုနှင့် အတွေ့အကြုံ-လုပ်ငန်းတွင် ကျယ်ပြန့်သော အသိပညာနှင့် အတွေ့အကြုံရှိသော ဆေးထိုးပုံသွင်းလုပ်ဖော်ကိုင်ဖက်ကို ရှာဖွေပါ။ ၎င်းတို့သည် ကဏ္ဍအသီးသီးရှိ ဖောက်သည်များအား အရည်အသွေးမြင့်ထုတ်ကုန်များနှင့် ဖြေရှင်းချက်များအား ပေးအပ်ခြင်းဆိုင်ရာ သက်သေပြမှတ်တမ်းတစ်ခု ရှိသင့်သည်။ မတူညီသောပစ္စည်းများ၊ မှိုဒီဇိုင်းများနှင့် ထုတ်လုပ်ရေးလုပ်ငန်းစဉ်များကို နားလည်သဘောပေါက်အောင် ဆင်ခြင်ပါ။
- ထုတ်လုပ်မှုစွမ်းရည်- ဆေးထိုးပုံသွင်းဖော်၏ ထုတ်လုပ်မှုစွမ်းရည်ကို အကဲဖြတ်ပါ။ သင့်ပရောဂျက်လိုအပ်ချက်များကို ကိုင်တွယ်ဖြေရှင်းရန် ခေတ်မီစက်ယန္တရားများနှင့် နည်းပညာများဖြင့် ကောင်းစွာ တပ်ဆင်ထားကြောင်း သေချာပါစေ။ ၎င်းတို့၏ ထုတ်လုပ်မှုစွမ်းရည်၊ မတူညီသော အစိတ်အပိုင်းအရွယ်အစားများနှင့် ရှုပ်ထွေးမှုများကို ကိုင်တွယ်နိုင်မှု၊ နှင့် သင်အလိုရှိသော ထုတ်လုပ်မှုပမာဏနှင့် အချိန်ဇယားများကို ပြည့်မီနိုင်မှုကို ထည့်သွင်းစဉ်းစားပါ။
- အရည်အသွေးအာမခံ:ဆေးထိုးခြင်းတွင် အရည်အသွေးသည် အဓိကဖြစ်သည်။ အလားအလာရှိသော လုပ်ဖော်ကိုင်ဖက်များ၏ အရည်အသွေးထိန်းချုပ်မှုစနစ်များနှင့် အသိအမှတ်ပြုလက်မှတ်များကို အကဲဖြတ်ပါ။ တင်းကျပ်သော အရည်အသွေးစံနှုန်းများကို လိုက်နာသော ပါတနာများကို ရှာဖွေပါ၊ ခိုင်မာသော စစ်ဆေးရေး လုပ်ငန်းစဉ်များ ရှိသည်၊ တစ်စိတ်တစ်ပိုင်း အရည်အသွေးနှင့် လိုက်လျောညီထွေရှိစေရန် ပြည့်စုံသော စမ်းသပ်မှုများကို လုပ်ဆောင်ပါ။
- ဒီဇိုင်းနှင့် အင်ဂျင်နီယာပံ့ပိုးမှု-ယုံကြည်စိတ်ချရသော ဆေးထိုးပုံသွင်းလုပ်ဖော်ကိုင်ဖက်တစ်ဦးသည် သင့်အစိတ်အပိုင်းဒီဇိုင်းကို ထုတ်လုပ်နိုင်စေရန်အတွက် အကောင်းဆုံးဖြစ်အောင် ဒီဇိုင်းနှင့် အင်ဂျင်နီယာဆိုင်ရာ ပံ့ပိုးမှုပေးသင့်သည်။ ပစ္စည်းရွေးချယ်မှု၊ ပုံစံခွက်ဒီဇိုင်းနှင့် အစိတ်အပိုင်းအရည်အသွေးနှင့် ထိရောက်မှုတို့ကို မြှင့်တင်ရန် ၎င်းတို့တွင် အဖိုးတန်ထည့်သွင်းမှုများကို ပံ့ပိုးပေးနိုင်သည့် ကျွမ်းကျင်အင်ဂျင်နီယာများ ရှိသင့်သည်။
- ကုန်ကျစရိတ် ယှဉ်ပြိုင်နိုင်စွမ်းကုန်ကျစရိတ်သည် တစ်ခုတည်းသော အဆုံးအဖြတ်ပေးသည့်အချက်မဟုတ်သော်လည်း ဆေးထိုးပုံသွင်းလုပ်ဖော်၏ စျေးနှုန်းနှင့် ကုန်ကျစရိတ်ယှဉ်ပြိုင်နိုင်မှုကို အကဲဖြတ်ရန် အရေးကြီးပါသည်။ အသေးစိတ်ကိုးကားချက်များကို တောင်းဆိုပြီး ကိရိယာကုန်ကျစရိတ်၊ ပစ္စည်းကုန်ကျစရိတ်၊ အလုပ်သမားစရိတ်နှင့် ၎င်းတို့ပေးဆောင်သည့် အပိုဝန်ဆောင်မှုများကို ထည့်သွင်းစဉ်းစားပါ။
- ဆက်သွယ်ရေးနှင့် ပူးပေါင်းဆောင်ရွက်ခြင်း-အောင်မြင်သော မိတ်ဖက်ဆက်ဆံရေးအတွက် ထိရောက်သော ဆက်သွယ်မှုနှင့် ပူးပေါင်းဆောင်ရွက်မှုသည် မရှိမဖြစ်လိုအပ်ပါသည်။ ဆေးထိုးပုံသွင်းလုပ်ဖော်ကိုင်ဖက်တွင် ကောင်းမွန်သော ဆက်သွယ်ရေးလမ်းကြောင်းများရှိပြီး သင့်မေးမြန်းစုံစမ်းမှုများကို တုံ့ပြန်နိုင်ကာ ပုံမှန်ပရောဂျက်အပ်ဒိတ်များကို ပေးနိုင်ကြောင်း သေချာပါစေ။ ပူးပေါင်းလုပ်ဆောင်သောချဉ်းကပ်မှုတစ်ခုသည် ကျွန်ုပ်တို့သည် သင့်လိုအပ်ချက်များနှင့်ကိုက်ညီကြောင်း သေချာစေရန်နှင့် မည်သည့်စိန်ခေါ်မှုများကိုမဆို ဆောလျင်စွာဖြေရှင်းနိုင်စေရန် ကူညီပေးပါမည်။
- ဝယ်ယူသူ အကိုးအကားများနှင့် သုံးသပ်ချက်များ-ဆေးထိုးပုံသွင်းလုပ်ဖော်ကိုင်ဖက်နှင့်အတူ အခြားဖောက်သည်များ၏ အတွေ့အကြုံများကို ထိုးထွင်းသိမြင်နိုင်စေရန် ဖောက်သည်ကိုးကားချက်များကို ရှာပါ သို့မဟုတ် သုံးသပ်ချက်/သက်သေခံချက်များကို ဖတ်ပါ။ ဤအချက်အလက်ကို ရယူခြင်းသည် ၎င်းတို့၏ ယုံကြည်နိုင်မှု၊ လျင်မြန်မှုနှင့် ဖောက်သည်ကျေနပ်မှု၏ အလုံးစုံအဆင့်ကို ဆုံးဖြတ်ရန် ကူညီပေးနိုင်သည်။
ကောက်ချက်
သာမိုပလတ်စတစ်ဆေးထိုးပုံသွင်းခြင်းသည် စွယ်စုံရနှင့် ကုန်ကျစရိတ်သက်သာသော ပလတ်စတစ်အစိတ်အပိုင်းများကို အမြောက်အမြားထုတ်လုပ်ရန် နည်းလမ်းတစ်ခုဖြစ်သည်။ မြင့်မားသောတိကျမှုနှင့် လိုက်လျောညီထွေရှိသော ရှုပ်ထွေးသောပုံစံများကို ထုတ်လုပ်နိုင်စွမ်းသည် မော်တော်ယာဥ်၊ ဆေးဘက်ဆိုင်ရာ၊ အီလက်ထရွန်းနစ်နှင့် လူသုံးကုန်ပစ္စည်းများအပါအဝင် လုပ်ငန်းအမျိုးမျိုးအတွက် ရေပန်းစားသော ရွေးချယ်မှုတစ်ခု ဖြစ်လာခဲ့သည်။ ၎င်း၏အားသာချက်များ၊ အားနည်းချက်များနှင့် ဒီဇိုင်းထည့်သွင်းစဉ်းစားမှုများအပါအဝင် သာမိုပလတ်စတစ်ဆေးထိုးခြင်း၏ မတူညီသောရှုထောင့်များကို နားလည်ခြင်းဖြင့်၊ သင့်လုပ်ငန်းလိုအပ်ချက်အတွက် မှန်ကန်သော ဆေးထိုးပုံဖော်ခြင်းလုပ်ငန်းပါတနာကို ရွေးချယ်ခြင်းနှင့်ပတ်သက်သည့် အသိဉာဏ်ဖြင့် ဆုံးဖြတ်ချက်များချနိုင်ပါသည်။