စိတ်ကြိုက် ပလပ်စတစ် ထိုးဆေးပုံသွင်းခြင်း။
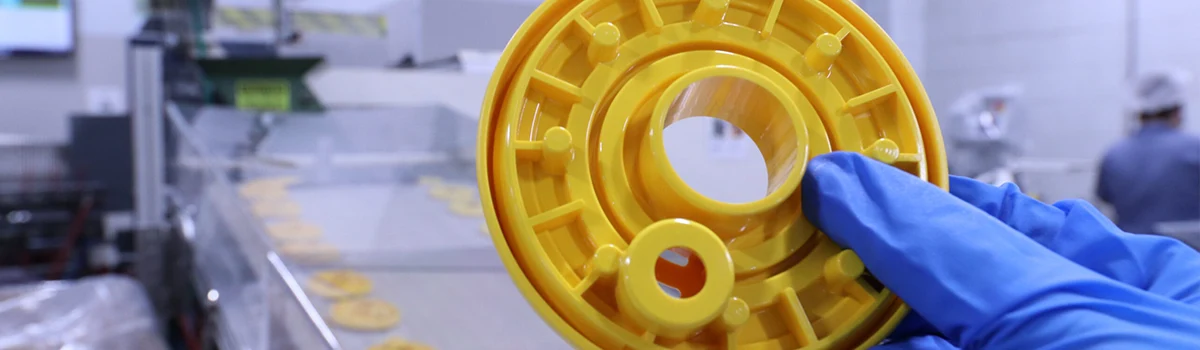
စိတ်ကြိုက်ဆေးထိုးပုံသွင်းခြင်းသည် တိကျသောစက်မှုဆိုင်ရာ သို့မဟုတ် အလှအပဆိုင်ရာအင်္ဂါရပ်များရရှိခြင်းအပေါ်တွင် အားကိုးအားထားပြုသော အောင်မြင်မှုတွင် ပလပ်စတစ်အစိတ်အပိုင်းများအတွက် စံပြဖြစ်သည်။ DJmolding ပလပ်စတစ်ဆေးထိုးပုံသွင်းခြင်းသည် သုံးစွဲသူများအား အကောင်းဆုံးပလတ်စတစ်အစိတ်အပိုင်းများထုတ်လုပ်ရန် ကူညီပေးခြင်း၏ အခြေခံရည်မှန်းချက်ဖြင့် မောင်းနှင်ခြင်းဖြစ်သည်။ ရှုပ်ထွေးမှုတွင် သူစိမ်းမဟုတ်ပါ၊ ဒီဇိုင်းစိန်ခေါ်မှုများသည် သင့်အတွက် ဆန်းသစ်တီထွင်လိုသော ကျွန်ုပ်တို့၏ဆန္ဒကို အမှန်တကယ် တွန်းအားပေးစေသည်။ ကျွန်ုပ်တို့ကို စောစောစီးစီးပါဝင်ခြင်းဖြင့် ဒီဇိုင်းလုပ်ငန်းစဉ်တွင် ကျွန်ုပ်တို့ကို တန်ဖိုးများထည့်ဝင်စေပါသည်။
Plastic Injection Molding ၏ အကျိုးကျေးဇူးများ
အသေးစိတ်အင်္ဂါရပ်များ
သင့်အမှတ်တံဆိပ်ကို မြှင့်တင်ရန်အတွက် အလှအပ သို့မဟုတ် လုပ်ဆောင်နိုင်သော အသေးစိတ်အချက်များ ထည့်သွင်းစဉ်းစားရန်- ပုံနှိပ်ထားသော စာသားများ၊ အလှကုန် သို့မဟုတ် မျက်နှာပြင်များ၊ ပုံသွင်းအလှဆင်ခြင်း၊ လျှပ်တစ်ပြက်အံဝင်ခွင်ကျ၊ ပြောင်းလွယ်ပြင်လွယ်ရှိသော ပတ္တာများ၊ ကွဲပြားသော မာကျောမှု။
မြင့်မားသောစွမ်းရည်
ပလပ်စတစ်ဆေးထိုးပုံသွင်းခြင်း၏ ထိရောက်မှုမှာ တုနှိုင်းမမှီပါ။ ကျွန်ုပ်တို့သည် သင့်အစိတ်အပိုင်းနှင့် ကိရိယာမှ မလိုအပ်သော ကုန်ကျစရိတ်များကို အင်ဂျင်နီယာချုပ်လုပ်ပါသည်။ ကျွန်ုပ်တို့၏ နှစ်ရှည်လများ ဒီဇိုင်းအင်ဂျင်နီယာများနှင့် မာစတာမှိုသမားများသည် ဤအရာကို အမှန်တကယ် ထူးချွန်ပါသည်။
Enhanced စွမ်းဆောင်ရည်
သင့်အပိုင်း၏ ရည်ရွယ်ထားသော လုပ်ဆောင်ချက်များကို နားလည်ရန်နှင့် ရုပ်ပိုင်းဆိုင်ရာသိပ္ပံ၊ ဒီဇိုင်းမူများ၊ ခွဲခြမ်းစိတ်ဖြာမှုကိရိယာများနှင့် လုပ်ငန်းစဉ်ထိန်းချုပ်မှုများကို အသုံးချခြင်းဖြင့် သင်၏ အဓိကရည်မှန်းချက်များကို ပြည့်မီရန် ကျွန်ုပ်တို့ ကြိုးစားလုပ်ဆောင်ပါသည်။
ပစ္စည်းမျိုးစုံ
ပစ္စည်း၊ ကုန်စည်နှင့် အင်ဂျင်နီယာအစေး ၂၀၀ ကျော်မှ ရွေးချယ်ပါ။ စွမ်းဆောင်ရည်နှင့် စျေးနှုန်းကို ဟန်ချက်ညီအောင် ကူညီပေးပြီး ကုန်ကျစရိတ်ကို လျှော့ချရန်အတွက် အခြားပစ္စည်းနှင့် ညီမျှသည့် ပစ္စည်းများကို ခွဲခြားသတ်မှတ်ရန် ကျွန်ုပ်တို့ ကူညီပါမည်။
Injection Molding လုပ်ငန်းစဉ်
ပလပ်စတစ်ဆေးထိုးခြင်းသည် ပလတ်စတစ်များထုတ်လုပ်ခြင်း၏ ရှေးအကျဆုံးနည်းလမ်းများထဲမှတစ်ခုဖြစ်ပြီး ထုတ်ကုန်ထုတ်လုပ်သူများအတွက် အစိတ်အပိုင်းများဖွံ့ဖြိုးတိုးတက်ရေးတွင် အရေးကြီးသောခြေလှမ်းတစ်ခုဖြစ်သည်။ ၎င်းသည် လေးလံသောသတ္တုအစိတ်အပိုင်းများကို ပလပ်စတစ်အဖြစ်သို့ ပြောင်းလဲလိုသော ထုတ်လုပ်သူများအတွက် ကောင်းမွန်သောဖြေရှင်းချက်တစ်ခုလည်းဖြစ်သည်။ ၎င်း၏ အရိုးရှင်းဆုံးပုံစံဖြင့် ရှင်းပြထားသည့် လုပ်ငန်းစဉ်သည် စိတ်ကြိုက်မှိုတစ်ခုသို့ အပူပေးကာ အရည်ပျော်ကာ ဖိအားမြင့်မြင့်ဖြင့် ထိုးသွင်းလိုက်သောအခါတွင် ပိုလီမာ သို့မဟုတ် ပလပ်စတစ်အစေးများကို အသုံးပြုကာ ထုတ်ကုန်ထုတ်လုပ်ရာတွင် အသုံးပြုရန် ပလတ်စတစ်အစိတ်အပိုင်းများ ထွက်လာမည်ဖြစ်သည်။
၎င်းလုပ်ငန်းစဉ်သည် ရိုးရှင်းပုံပေါ်သော်လည်း၊ ၎င်းသည် အမှန်တကယ်ပင် ရှုပ်ထွေးနိုင်ပြီး သင်၏ထူးခြားသောစက်မှုလုပ်ငန်းလိုအပ်ချက်များ၊ သတ်မှတ်ချက်များ၊ အဆုံးအသုံးပြုမှုများနှင့် အချိန်/ဘတ်ဂျက်ကန့်သတ်ချက်များကို ဖြည့်ဆည်းပေးနိုင်သော ဆေးထိုးမှိုလုပ်ဖော်ကိုင်ဖက်ထံမှ အတွေ့အကြုံများစွာ လိုအပ်ပါသည်။ စတင်ရန် အကောင်းဆုံးနေရာမှာ ပလပ်စတစ်ပုံသွင်းခြင်းလုပ်ငန်းစဉ်၏ အခြေခံအသိပညာနှင့် အကောင်းဆုံးအလေ့အကျင့်များကို ဒီဇိုင်းဆွဲခြင်းဖြင့် စတင်ခြင်းဖြစ်သည်။
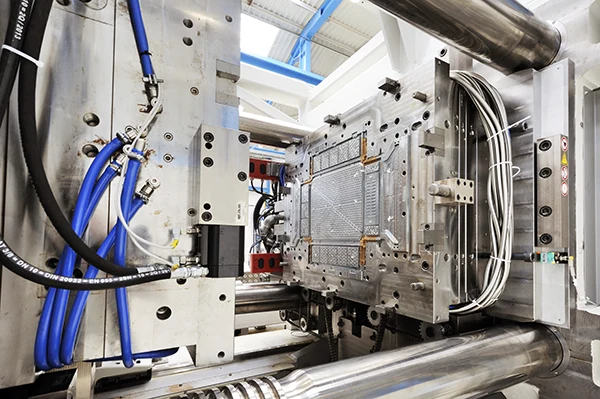
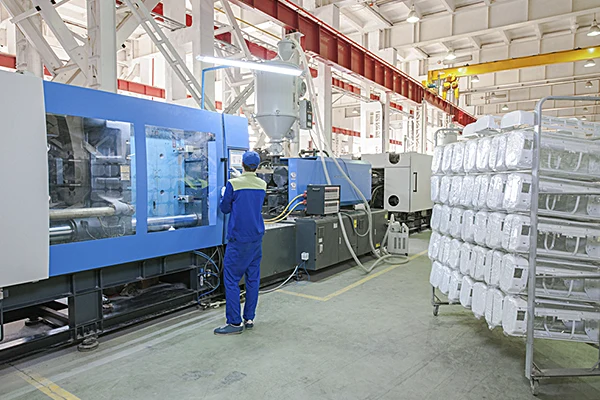
သိပ္ပံနည်းကျ ပုံသွင်းခြင်း
သိပ္ပံနည်းကျ ပုံသွင်းခြင်းနည်းလမ်းသည် တိကျသောစွမ်းဆောင်ရည်နှင့် တိကျမှုမြင့်မားသော အရေးကြီးသောအစိတ်အပိုင်းများထုတ်လုပ်ခြင်းကို အကျိုးကျေးဇူးဖြစ်စေသည်။ ကျွန်ုပ်တို့၏အဆင့်မြင့်ပုံသွင်းနည်းပညာသည် ထပ်ခါတလဲလဲဖြစ်နိုင်စေရန်နှင့် လိုက်လျောညီထွေရှိစေပါသည်။ ဆိုလိုသည်မှာ ယနေ့ကျွန်ုပ်တို့ သင့်အတွက် ထုတ်လုပ်သည့် ထုတ်ကုန်သည် မနက်ဖြန် သင့်အတွက် ကျွန်ုပ်တို့ ပြုလုပ်သော ထုတ်ကုန်ဖြစ်သည်။
ကိရိယာတန်ဆာပလာများ တီထွင်နေစဉ်အတွင်း သိပ္ပံနည်းကျ ဆေးထိုးခြင်း စတင်သည်။ ဖိအား၊ အပူချိန်၊ အစာအိမ်ဖြည့်ချိန်စသည့်အချက်များအား အကောင်းဆုံးဖြစ်အောင် ပြုလုပ်ထားသောကြောင့် ပုံစံခွက်ဒီဇိုင်းသည် ကွဲလွဲမှုများအတွက် အခွင့်အလမ်းများကို အနည်းဆုံးဖြစ်စေသည်။ မှိုစီးဆင်းမှု ပိုင်းခြားစိတ်ဖြာချက်သည် ဖြည့်စွက်ရမည့် အစိတ်အပိုင်း၏ နောက်ဆုံးနေရာများ၊ ပစ္စည်းသည် မှိုသို့ မည်ကဲ့သို့ ဦးတည်မည်၊ အလားအလာရှိသော ကွဲလွဲမှုနှင့် ဖိစီးမှု အမှတ်များကို ဖော်ထုတ်ပြသသည်။ ၎င်းသည် အင်ဂျင်နီယာဆိုင်ရာ ခန့်မှန်းသုံးသပ်ချက်နှင့် တိုင်းတာမှုကို ပံ့ပိုးပေးသည့် တက်ကြွသောအဆင့်တစ်ခုဖြစ်ပြီး အစိတ်အပိုင်း သို့မဟုတ် ပရောဂျက်တစ်ခု၏ အောင်မြင်မှု သို့မဟုတ် ကျရှုံးမှုကို လွယ်ကူစွာ ဆုံးဖြတ်နိုင်စေသည်။
ခိုင်မာသောထုတ်လုပ်မှု လုပ်ငန်းစဉ်များသည် အပိုင်းအစများနှင့် စီမံဆောင်ရွက်ချိန်ကို လျှော့ချပေးသည့် စောင့်ကြည့်စစ်ဆေးခြင်းနှင့် အလိုအလျောက် လုပ်ငန်းစဉ်ထိန်းချုပ်ခြင်းများမှတစ်ဆင့် သိပ္ပံနည်းကျချဉ်းကပ်မှုကို ပိုမိုအသုံးပြုသည်။ ကွဲလွဲမှု သို့မဟုတ် ချွတ်ယွင်းမှုတစ်ခု ဖြစ်ပွားပါက၊ ကိုက်ညီမှုမရှိသော အစိတ်အပိုင်းများ မပြုလုပ်မီ ၎င်းကို လျင်မြန်စွာ ဖော်ထုတ်ပြီး သီးခြားခွဲထုတ်မည်ဖြစ်သည်။
အလွန်အကျွံ
နှစ်ခု (သို့မဟုတ်) ထက်ပိုသောပစ္စည်းများကို overmolding ဖြင့် အစိတ်အပိုင်းတစ်ခုထဲသို့ ပေါင်းစပ်နိုင်သည်။ ဤလုပ်ငန်းစဉ်ကို ပိုမိုပျော့ပျောင်းသော ချုပ်ကိုင်ဧရိယာကဲ့သို့သော ထူးခြားသောထိတွေ့ကိုင်တွယ်နိုင်သော မျက်နှာပြင်အတွက် အသုံးပြုလေ့ရှိသည်။ ပလပ်စတစ်အလွှာအပေါ်မှ ပလပ်စတစ်ကို ဖုံးအုပ်ခြင်း သို့မဟုတ် ပလပ်စတစ်အလွှာအပေါ်မှ ရော်ဘာ ဖြစ်နိုင်သည်၊ ပုံမှန်အားဖြင့် နှစ်ချက်ထိုးဆေးထိုးခြင်းလုပ်ငန်းစဉ်ဖြင့် ပြီးမြောက်နိုင်သည်။ အစေးဖော်မြူလာနှင့် အရောင်ကွဲပြားနိုင်သည်။ overmolding ၏ အလှအပဆိုင်ရာ အားသာချက်များကို သတိပြုမိရန် လွယ်ကူသော်လည်း ၎င်းတို့သည် ဆင့်ပွားလုပ်ဆောင်မှုများကို ဖယ်ရှားပေးပါသည်။ Overmolding သည် လက်ကိုင်၊ လက်ကိုင်ပစ္စည်းများ၊ ရော်ဘာလက်ကိုင်များ လိုအပ်သည့် စက်ရုပ်များ၊ သို့မဟုတ် ကွဲပြားသောအရောင်များဖြင့် အစိတ်အပိုင်းတစ်ခု၏အသွင်အပြင်ကို မြှင့်တင်ရန်အတွက် ပြီးပြည့်စုံသည်။
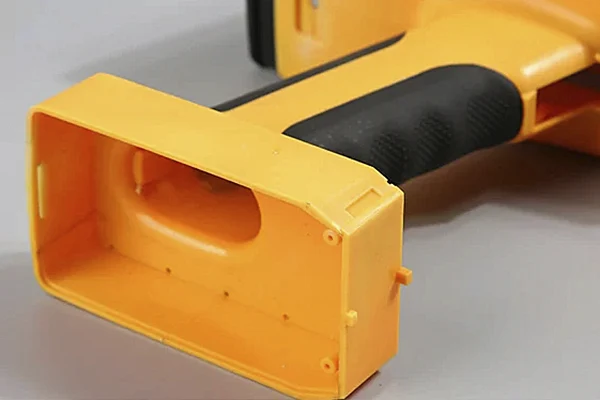
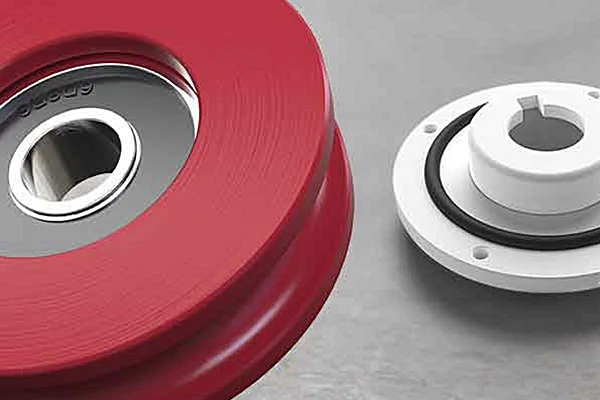
ပုံသွင်းထည့်ပါ။
ထည့်သွင်းပုံသွင်းခြင်းသည် မှိုအပေါက်အတွင်း ထည့်ထားသော အရာဝတ္တုကို overmolding နှင့် ဆင်တူသည်။ ပုံမှန်အားဖြင့် သတ္တု သို့မဟုတ် ပလတ်စတစ်ဖြင့် ထည့်သွင်းရန် ပလပ်စတစ်ကို ပုံသွင်းခြင်းနှောင်ကြိုးများ ထည့်ပါ။ Threaded inserts များသည် အဖြစ်များသည်။ ၎င်းသည် ချည်နှောင်ခြင်း၊ ကော်ကပ်ခြင်း သို့မဟုတ် အပူလောင်းခြင်းအတွက် အစားထိုးအသုံးပြုသည့်အခါ ပင်ပန်းမှုကို ဖယ်ရှားပေးသည်။ အပိုင်းကိုလည်း အားကောင်းအောင် ထည့်သွင်းပါ။ ထည့်သွင်းမှုများကို ကိုယ်တိုင် သို့မဟုတ် စက်ရုပ်အလိုအလျောက်စနစ်ဖြင့် တင်ဆောင်ပါသည်။
အလှဆင်ခြင်းနှင့် တံဆိပ်ကပ်ခြင်းအပိုင်း
ပုံးအတွင်းအလှဆင်ခြင်း (IMD) နှင့် မှိုအတွင်းတံဆိပ်ကပ်ခြင်း (IML) ကို ဂရပ်ဖစ် သို့မဟုတ် အညွှန်းများဖြင့် အမြင်အာရုံကောင်းမွန်သောအသွင်အပြင်ဖန်တီးရန် အသုံးပြုပါသည်။ စက်ရုပ်များနှင့် လျှပ်စစ်စတိတ် သို့မဟုတ် ဖုန်စုပ်စက်ဖြင့် လွယ်ကူချောမွေ့စွာ သွန်းသောပလပ်စတစ်အစေးမထိုးမီ မှိုအပေါက်ထဲသို့ ပုံနှိပ်ထားသော ဖလင်အထပ်လွှာကို ပေါင်းထည့်သည်။ ဤလုပ်ငန်းစဉ်သည် အညွှန်းနှင့် ပြီးသွားသည့်အပိုင်းကြားတွင် အမြဲတမ်းနှောင်ကြိုးကို ဖန်တီးပေးသည်၊ အများအားဖြင့် လုပ်ဆောင်ပြီးနောက် လုပ်ဆောင်ခြင်းလုပ်ငန်းများအတွက် လိုအပ်ချက်များကို ဖယ်ရှားပေးပါသည်။ ကျယ်ပြန့်သော အသွင်အပြင်၊ အရောင်နှင့် မျက်နှာပြင်အပေါ်ယံအလွှာရွေးချယ်မှုများသည် ဖန်တီးမှုဖြစ်နိုင်ခြေအတွက် တံခါးဖွင့်ထားသည်။ သင့်အမှတ်တံဆိပ်ကို မြှင့်တင်ရန် ရွေးချယ်စရာများအကြောင်း သင့်ပရောဂျက်မန်နေဂျာနှင့် ဆွေးနွေးရန် သင့်အား ကျွန်ုပ်တို့ တိုက်တွန်းပါသည်။
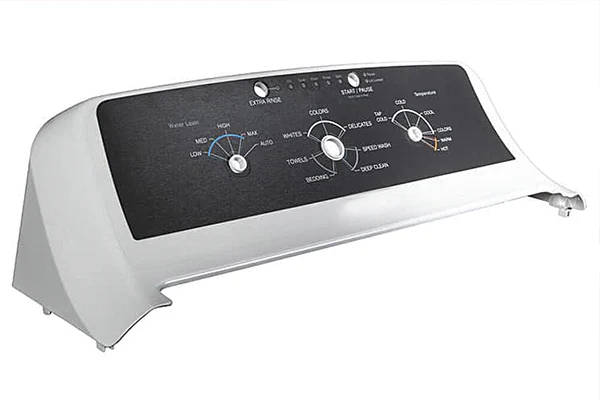
စိတ်ကြိုက်ပလပ်စတစ်ထိုးသွင်းပုံသွင်းခြင်းဝန်ဆောင်မှု China
DJmolding သည် 2010 ကတည်းက စတင်လည်ပတ်နေသည် | AFAQ ISO/TS 16949၊ UL နှင့် ISO အသိအမှတ်ပြုလက်မှတ်များ၊ ယခုကမ္ဘာပေါ်ရှိ 3D ပုံနှိပ်ကုမ္ပဏီများစွာကို အဓိက ပံ့ပိုးပေးနေပါသည်။
Djmolding တွင် ကျွန်ုပ်တို့သည် အရည်အသွေးမြင့် ပလပ်စတစ်ဆေးထိုးပုံသွင်းအစိတ်အပိုင်းများနှင့် မှိုကိရိယာများကို ထုတ်လုပ်ရာတွင် အထူးပြုပါသည်။ ကျွန်ုပ်တို့သည် ကမ္ဘာပေါ်ရှိ 3D ပရင့်ထုတ်သည့်ကုမ္ပဏီများအတွက် ကျွန်ုပ်တို့၏ ပလတ်စတစ်ဆေးထိုးခြင်းလုပ်ငန်းကို အဓိက ပံ့ပိုးပေးပါသည်။ ကျွန်ုပ်တို့တွင် စက်ရုပ်များနှင့် အလိုအလျောက် ပလပ်စတစ်ထိုးဆေး ထုတ်လုပ်ခြင်းအတွက် စက် 55 စက်ရှိသည်။ ကျွန်ုပ်တို့သည် စက်ပစ္စည်းအမျိုးမျိုးမှ စက်ကိရိယာများပြုလုပ်ရန် စက်ယန္တရားနှင့် အချောသတ်ဝန်ဆောင်မှုများအားလုံးကို ပေးဆောင်ထားပြီး အဓိကပလတ်စတစ်အားလုံးတွင် 100 မှ 200k+ အချောထည်အစိတ်အပိုင်းများကို ထုတ်လုပ်နိုင်သည်။ ကျွန်ုပ်တို့ကို အမှန်တကယ်ခြားနားစေသောအရာမှာ သင်၏ အစိတ်အပိုင်းများ ပြည့်မီပြီး သင်၏ အမြင့်ဆုံးမျှော်လင့်ချက်ထက် ကျော်လွန်ကြောင်း သေချာစေရန် ကျွန်ုပ်တို့၏ အဆင့်မြင့်ပစ္စည်းများကို စစ်ဆေးခြင်း၊ စစ်ဆေးခြင်းနှင့် စမ်းသပ်ခြင်းပင်ဖြစ်သည်။ ယနေ့ အခမဲ့ကိုးကားမှုအတွက် ကျွန်ုပ်တို့၏ နိုင်ငံတကာ ဆေးထိုးခြင်းဆိုင်ရာ ကျွမ်းကျင်သူများနှင့် ဆက်သွယ်ပါ။
DJmolding Plastic Injection Molding လုပ်ငန်းစဉ်
သင်၏ပလပ်စတစ်ဆေးထိုးမှိုကိရိယာများ အဆင်သင့်ဖြစ်သောအခါ၊ ပုံသွင်းခြင်းလုပ်ငန်းစဉ်တွင် အောက်ပါအခြေခံအဆင့်များ ပါဝင်ပါသည်။
အဆင့် 1. ပလပ်စတစ်အစေးကို အစိမ်းလိုက် အလုံးလိုက်ဖြင့် ထွက်လာသည်။ ၎င်းတို့ကို မှန်ကန်သော အစိုဓာတ်ပါဝင်မှုဖြင့် အခြောက်ခံပြီး လိုအပ်ပါက ၎င်းတို့ကို ဆိုးဆေး သို့မဟုတ် မာစတာသုတ်အရောင်ခြယ်ဆေးများဖြင့် ရောစပ်နိုင်သည်။
အဆင့် 2. အခြောက်လှန်းထားသော အစေ့များကို ပုံသွင်းစက်၏ hopper ထဲသို့ လောင်းထည့်လိုက်ပါ။ စက်၏စည်အတွင်းရှိအပြန်အလှန်ခံဝက်အူတစ်ခုသည် ဤအမှုန်အမွှားများကို မှိုဆီသို့ပို့ဆောင်ပေးလိမ့်မည်။
အဆင့် 3. စည်အတွင်းမှ အလုံးများကို ရောစပ်ကာ အရည်အစေးများ ဖြစ်ပေါ်လာသည်အထိ ရောစပ်ပြီး အပူပေးသည်။
အဆင့် 4. အပူပေးမှိုသည် အလိုအလျောက်ပိတ်သွားပြီး အစေးကို တံခါးပေါက်မှတဆင့် နှင့် မှိုအပေါက်ထဲသို့ ထိုးသွင်းသည်။
အဆင့် 5. အတွင်းပိုင်းကို ခိုင်မာစေရန် မှိုကို အအေးခံထားပါ။
အဆင့် 6. မှိုပွင့်လာပြီး စက်ဝိုင်းအသစ်တစ်ခုစတင်ရန် အပိုင်းကို ထုတ်ပစ်လိုက်သည်။
Plastic Injection Molding Tolerances
ပလပ်စတစ်ပစ္စည်းအားလုံးသည် အပူနှင့် အစိုဓာတ်၏လွှမ်းမိုးမှုအောက်တွင် ကျယ်လာပြီး ကျုံ့သွားမည်ဖြစ်သည်။ ကျွန်ုပ်တို့၏သည်းခံခြင်းလမ်းညွှန်သည် ပုံမှန်အစိတ်အပိုင်းအင်္ဂါရပ်များအတွက် အသုံးအများဆုံးအစေးအမျိုးအစားများ၏ ဝိသေသလက္ခဏာများဆိုင်ရာ ယေဘုယျအချက်အလက်များကို ပေးပါမည်။
ကုန်ထုတ်လုပ်မှုအတွက် သင့်ဒီဇိုင်းများကို အကောင်းဆုံးဖြစ်အောင် သင်နှင့် အနီးကပ် လုပ်ဆောင်ပါမည်။ ညံ့ဖျင်းသော ဒီဇိုင်းသည် အပူဖိစီးမှု၊ ကျုံ့သွားခြင်း၊ ကွဲထွက်ခြင်း စသည်တို့ကို ဖြစ်ပေါ်စေသည့် မည်သည့်နေရာမဆို ညွှန်ပြပါမည်။ သာမာန်ချို့ယွင်းချက်များအကြောင်း နောက်ထပ်အချက်အလက်များအတွက် ကျွန်ုပ်တို့၏ ဒီဇိုင်းလမ်းညွှန်နှင့် ၎င်းတို့ကို မည်သို့ရှောင်ရှားရမည်နည်း။
အခြားသတ်မှတ်ထားခြင်းမရှိပါက၊ ကျွန်ုပ်တို့သည် ပလပ်စတစ်ဆေးထိုးခြင်းအတွက် DIN 16742 စံနှုန်းများကို လိုက်နာပါသည်။ ဆေးထိုးပုံသွင်းထားသော အစိတ်အပိုင်းများနှင့် သက်ဆိုင်သည့် အမြင်အရည်အသွေး စံနှုန်းများအကြောင်း ဖတ်ပါ။
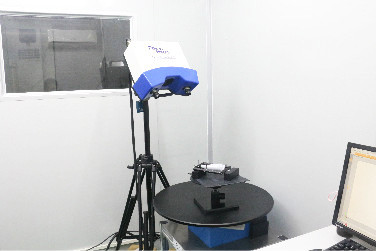
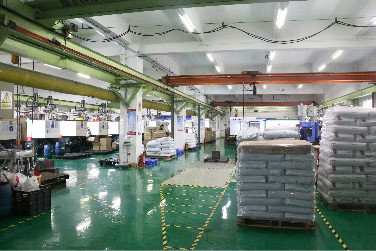
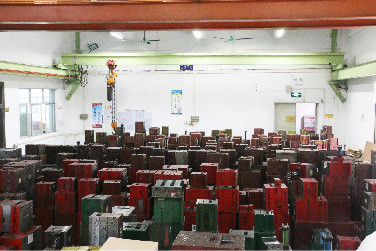
ပလပ်စတစ် ထိုးဆေးပုံသွင်း ပစ္စည်းများ
Djmolding သည် ဆေးထိုးပုံသွင်းကိရိယာများကို ပြုလုပ်ပြီး အလူမီနီယမ် 7075၊ P20 နှင့် NAK80 တစ်ပိုင်းမာကျောသော သံမဏိများနှင့် H13 အပြည့်မာကျောသော သံမဏိများမှ သေဆုံးသည်။ ထို့အပြင်၊ ကျွန်ုပ်တို့သည် စံ SPI အပြီးသတ်မှုများ၊ EDM အသွင်အပြင်နှင့် ထွင်းထုထားသော အသွင်အပြင်များစွာကို ပေးဆောင်ပါသည်။
ဤပစ္စည်းအမျိုးအစားတစ်ခုစီသည် အချို့သောအပလီကေးရှင်းများအတွက် ထူးခြားသောအားသာချက်များရှိသည်။ * ထည့်သွင်းစဉ်းစားချက်များမှာ-
* ကုန်ကြမ်းကုန်ကျစရိတ်
* ကြာရှည်ခံမှုနှင့် ချေးစားခြင်း သို့မဟုတ် ပွန်းပဲ့ခြင်းတို့ကို ခံနိုင်ရည်ရှိသည်။
* စက်ယန္တရား
* မြင့်မားသော မျက်နှာပြင်ကို ပွတ်တိုက်နိုင်မှု
* အပူကုသမှုအတွက်လိုအပ်သောအချိန်
* မျှော်လင့်ထားသောကိရိယာ၏သက်တမ်း
သင့်အတွက် မည်သည့်အရာသည် သင့်အတွက် သင့်လျော်ကြောင်း ပိုမိုလေ့လာရန် ကျွန်ုပ်တို့၏ နည်းပညာကျွမ်းကျင်သူများကို ဆက်သွယ်ပါ။
ပလပ်စတစ်ထိုးထည့်ထားသော အစိတ်အပိုင်းများ
သင့်ပရောဂျက်အတွက် ရွေးချယ်ရန် အပူချိန်ထိန်းညှိခြင်းနှင့် အပူချိန်ထိန်းညှိခြင်း ပလတ်စတစ်များ ထောင်ပေါင်းများစွာရှိသည်။ ထို့အပြင်၊ ဖန်မျှင်များ၊ UV stabilizers နှင့် ချောဆီများကဲ့သို့သော additives များဖြင့် စက်ပိုင်းဆိုင်ရာနှင့် ဓာတုလက္ခဏာများကို မြှင့်တင်နိုင်သည်။ ကျွန်ုပ်တို့၏ စာရွက်စာတမ်းများစာရွက်သည် သင့်အား စံအမျိုးအစားများနှင့် မျှော်လင့်ထားရမည့် ခံနိုင်ရည်များအကြောင်း ပိုမိုအသေးစိတ်အချက်အလက်များကို ပေးပါမည်။
သင်၏ resins ရွေးချယ်မှုသည် အောက်ပါအချက်များထဲမှ တစ်ခု သို့မဟုတ် တစ်ခုထက်ပိုသော ထည့်သွင်းစဉ်းစားမှုအပေါ် မူတည်နိုင်သည်-
* ခရမ်းလွန်ရောင်ခြည်၊ ဓာတု၊ ပွန်းပဲ့မှုနှင့် ထိခိုက်မှုဒဏ်ကို ခံနိုင်ရည်ရှိသည်။
* ကုန်ကြမ်းကုန်ကျစရိတ်
* စက်ပိုင်းဆိုင်ရာအင်အား
* အလေးချိန်နှင့်သိပ်သည်းဆ
* ပြောင်းလွယ်ပြင်လွယ်
*ပွင့်လင်းမြင်သာမှု
* ပြန်လည်အသုံးပြုနိုင်ခြင်း။
ပစ္စည်းဂုဏ်သတ္တိများအကြောင်း ပိုမိုလေ့လာရန် ကျွန်ုပ်တို့၏ နည်းပညာကျွမ်းကျင်သူတစ်ဦးထံ ဆက်သွယ်ပါ။
DJmolding ဆေးထိုးဆိုင်
ပလပ်စတစ်ဆေးထိုးမှိုနှင့် လျင်မြန်သော ပုံတူဖော်ခြင်းဝန်ဆောင်မှုကို ဦးဆောင်ထုတ်လုပ်သူ
Djmolding သည် တရုတ်နိုင်ငံတွင် ပိုမိုလူသိများသော ပလပ်စတစ်ဆေးထိုးခြင်းလုပ်ငန်းကုမ္ပဏီများထဲမှ တစ်ခုဖြစ်သည်။ ကျွန်ုပ်တို့၏ ဆေးထိုးအပ်ဆိုင်တွင် တန်ချိန် 50 မှ 30 တန်အထိ မြင့်မားသော တိကျသော ဆေးထိုးအပ်စက် အစုံ 800 တပ်ဆင်ထားပြီး ၎င်းတို့ကို ထိုင်ဝမ်နှင့် ဂျပန်နိုင်ငံတို့မှ အများဆုံးတင်သွင်းကြပြီး ကျွန်ုပ်တို့၏ ဆေးထိုးဆိုင်သည် တစ်ရက်လျှင် 24 နာရီ ၊ 7 ရက်ပတ်လုံး လည်ပတ်နေပြီး ထုတ်လုပ်ပေးပါသည်။ ဝန်ဆောင်မှုများ။
ကျွန်ုပ်တို့သည် မော်တော်ယာဥ်၊ ဆေးဘက်ဆိုင်ရာ၊ မီးအလင်းရောင်၊ အားကစားပစ္စည်းများ၊ အိမ်သုံးပစ္စည်းများနှင့် စိုက်ပျိုးရေးအပါအဝင် စက်မှုလုပ်ငန်းအများအပြားအတွက် ပလပ်စတစ်ထုတ်ကုန်အမျိုးမျိုးဖြင့် အတွေ့အကြုံရှိပါသည်။ Djmolding သည် 16949 မှစတင်၍ AFAQ ISO/TS 9001၊ UL နှင့် ISO 2010 အသိအမှတ်ပြုလက်မှတ်များကို ဖြတ်ကျော်ထားပြီး၊ ကျွန်ုပ်တို့တွင် IPQC လူ 15 ဦးသည် ကျွန်ုပ်တို့၏ထုတ်လုပ်မှုကို အဆက်မပြတ်ကြည့်ရှုပြီး အစိတ်အပိုင်းအရည်အသွေးကို စစ်ဆေးသည်၊ ၎င်းသည် ကျွန်ုပ်တို့၏ထုတ်လုပ်မှုအရည်အသွေးကို အမြင့်ဆုံးအဆင့်ကို ထိန်းသိမ်းထားကြောင်း သေချာစေသည်။ ပြီးခဲ့သည့် 9 နှစ်အတွင်း၊ Djmolding သည် အရည်အသွေးမြင့်ကိရိယာနှင့် အစိတ်အပိုင်းတစ်ခုကို ကျိုးကြောင်းဆီလျော်သောစျေးနှုန်းဖြင့် ထုတ်လုပ်ခြင်း၏ ခိုင်မာသောဂုဏ်သတင်းကို ထူထောင်ထားသည်။ ကျွန်ုပ်တို့သည် appx နှင့် ခိုင်မာသောစီးပွားရေးဆက်ဆံရေးကို ထိန်းသိမ်းထားသည်။ 50 ဖောက်သည်, အဓိကအားဖြင့်အမေရိကန်နှင့်ဥရောပမှ။
စိတ်ကြိုက် ပလပ်စတစ် ထိုးဆေးပုံသွင်းခြင်း။
စိတ်ကြိုက်ပလပ်စတစ်ဆေးထိုးပုံသွင်းခြင်းသည် အရည်အသွေးမြင့်ပလပ်စတစ်အစိတ်အပိုင်းများထုတ်လုပ်ရန် ဆန်းသစ်ပြီး ထိရောက်သောနည်းလမ်းတစ်ခုဖြစ်သည်။ ဤကုန်ထုတ်လုပ်မှုလုပ်ငန်းစဉ်သည် ပလပ်စတစ်ပစ္စည်းများကို ရှုပ်ထွေးသောပုံသဏ္ဍာန်နှင့် အရွယ်အစားများအဖြစ် ပုံသွင်းရန် မှိုကိုအသုံးပြုပြီး စက်မှုလုပ်ငန်းအမျိုးမျိုးအတွက် စံပြဖြေရှင်းချက်တစ်ခုဖြစ်လာသည်။ ဤဘလော့ဂ်ပို့စ်သည် စိတ်ကြိုက်ပလပ်စတစ်ဆေးထိုးပုံသွင်းခြင်းသို့ နက်နက်ရှိုင်းရှိုင်း ထိုးထွင်းဝင်ရောက်ပြီး ၎င်း၏အကျိုးကျေးဇူးများ၊ အသုံးချမှုများနှင့် အကောင်းဆုံးအလေ့အကျင့်များကို ရှာဖွေပါမည်။
စိတ်ကြိုက် ဆေးထိုးခြင်း လုပ်ငန်းစဉ်ကို နားလည်ခြင်း။
စိတ်ကြိုက်ဆေးထိုးခြင်းဆိုသည်မှာ ထုထည်ကြီးမားသော ပလတ်စတစ်အစိတ်အပိုင်းများထုတ်လုပ်ရန် အသုံးပြုသည့် ကုန်ထုတ်လုပ်မှုလုပ်ငန်းစဉ်တစ်ခုဖြစ်သည်။ ၎င်းတွင် ပလပ်စတစ်အမှုန့်များ သို့မဟုတ် granules များကို အရည်ပျော်စေပြီး ၎င်းတို့ကို ဖိအားများအောက်တွင် မှိုတစ်ခုထဲသို့ ထိုးသွင်းကာ ၎င်းတို့သည် အေးခဲပြီး လိုချင်သောပုံသဏ္ဍာန်ဖြစ်လာစေရန် ခိုင်မာစေပါသည်။ ဆေးထိုးပုံသွင်းခြင်း လုပ်ငန်းစဉ်သည် ဤနေရာတွင် အလုပ်လုပ်ပုံဖြစ်သည် ။
- Clamping- "tool" ဟုခေါ်သော မှို၏နှစ်ခြမ်းကို ဆေးထိုးဖိအားကိုခံနိုင်ရည်လုံလောက်သောအင်အားဖြင့် တွဲချည်ထားသည်။
- ထိုးသွင်းခြင်း- ပလပ်စတစ်အလုံးများကို အပူပေးထားသောစည်တစ်ခုတွင် အရည်ပျော်ပြီး ဖိအားမြင့်သောအပြေးသမားစနစ်မှတစ်ဆင့် မှိုထဲသို့ ထိုးသွင်းသည်။ ပလပ်စတစ်သည် မှိုပေါက်ကို ဖြည့်ပေးပြီး မှိုပုံသဏ္ဍာန်ကို ယူသည်။
- အအေးခံခြင်း- ပလပ်စတစ်သည် အလိုရှိသော ပုံသဏ္ဍာန်ကို ထိန်းသိမ်းရန် မှိုအတွင်းပိုင်းကို အေးစေပြီး ခိုင်မာစေနိုင်သည်။
- ထုတ်ခြင်း- ပလပ်စတစ်အအေးခံပြီး ပြီးသွားသည်နှင့် မှိုပွင့်ပွင့်လာသည်။
- ထပ်တလဲလဲ- တူညီသောအစိတ်အပိုင်းများစွာကိုဖန်တီးရန် လုပ်ငန်းစဉ်ကို ထပ်ခါတလဲလဲပြုလုပ်သည်။
ဆေးထိုးပုံသွင်းခြင်းသည် သေးငယ်သော အစိတ်အပိုင်းများမှ မော်တော်ကားအစိတ်အပိုင်းများနှင့် အိမ်သုံးပစ္စည်းများကဲ့သို့ ကြီးမားသောပစ္စည်းများအထိ ပလပ်စတစ်ထုတ်ကုန်များကို ထုတ်လုပ်သည်။ လုပ်ငန်းစဉ်သည် အလွန်ထိရောက်ပြီး ရှုပ်ထွေးသော ဂျီသြမေတြီများနှင့် တင်းကျပ်သောသည်းခံမှုများဖြင့် အစိတ်အပိုင်းများကို ထုတ်လုပ်နိုင်သည့်အပြင် အမှိုက်အနည်းငယ်မျှသာနှင့် အပိုင်းအစနှုန်းနည်းပါးသော အပိုင်းများကိုလည်း တိကျစွာထုတ်လုပ်နိုင်သည်။
လုပ်ငန်းစဉ်သည် တိကျပြီး တသမတ်တည်း ရလဒ်များကို သေချာစေရန် မှို၊ ဆေးထိုးစက်နှင့် ထိန်းချုပ်မှုစနစ်တို့ အပါအဝင် အထူးပြုကိရိယာများ လိုအပ်ပါသည်။ မှိုကို ပုံမှန်အားဖြင့် သံမဏိဖြင့် ပြုလုပ်ထားပြီး အများအပြား ကပေါက်ပေါက်ပုံသွင်းခြင်းဖြင့် အစိတ်အပိုင်းများစွာကို ထုတ်လုပ်ရန် ဒီဇိုင်းထုတ်နိုင်သည်။
ဆေးထိုးပုံသွင်းခြင်းကို သာမိုပလတ်စတစ်များ၊ သာမိုဆက်ကိရိယာများနှင့် အီလက်စတိုမာများအပါအဝင် အမျိုးမျိုးသော ပစ္စည်းများနှင့်လည်း အသုံးပြုနိုင်သည်။ ပစ္စည်းတစ်ခုစီတွင် ထူးခြားသောဂုဏ်သတ္တိများရှိပြီး သီးခြားအသုံးချမှုများနှင့် အံဝင်ခွင်ကျဖြစ်စေနိုင်သည်။
ယေဘူယျအားဖြင့်၊ ဆေးထိုးပုံသွင်းခြင်းသည် စက်မှုလုပ်ငန်းများစွာတွင် တွင်ကျယ်စွာအသုံးပြုသော စွယ်စုံရနှင့် ထိရောက်သောကုန်ထုတ်လုပ်မှုလုပ်ငန်းစဉ်တစ်ခုဖြစ်သည်။
စိတ်ကြိုက်ပလပ်စတစ်ဆေးထိုးခြင်း၏အားသာချက်များ
စိတ်ကြိုက်ပလပ်စတစ်ဆေးထိုးခြင်းဆိုသည်မှာ ထုထည်ကြီးမားသော စိတ်ကြိုက်ပလပ်စတစ်အစိတ်အပိုင်းများကို ဖန်တီးရန်အတွက် အသုံးပြုသည့် ကုန်ထုတ်လုပ်မှုလုပ်ငန်းစဉ်တစ်ခုဖြစ်သည်။ ဤလုပ်ငန်းစဉ်၏ အားသာချက်အချို့မှာ အောက်ပါအတိုင်းဖြစ်သည်။
မြင့်မားသောစွမ်းဆောင်ရည်နှင့်ကုန်ထုတ်စွမ်းအား- စိတ်ကြိုက်ပလပ်စတစ်ဆေးထိုးပုံသွင်းခြင်းသည် တူညီသောအစိတ်အပိုင်းအများအပြားကို မြန်မြန်ဆန်ဆန်နှင့် တသမတ်တည်းထုတ်လုပ်ပေးနိုင်သည့် အလွန်ထိရောက်သောလုပ်ငန်းစဉ်တစ်ခုဖြစ်သည်။ ၎င်းသည် ပလတ်စတစ် အစိတ်အပိုင်းများ အမြောက်အမြား ထုတ်လုပ်ခြင်းအတွက် စံပြရွေးချယ်မှုတစ်ခု ဖြစ်လာစေသည်။
ဘက်စုံသုံး အဆိုပါလုပ်ငန်းစဉ်ကို သာမိုပလတ်စတစ်များ၊ သာမိုဆက်ကိရိယာများနှင့် အီလက်စတိုမာများ အပါအဝင် ပလတ်စတစ်ပစ္စည်းများ အများအပြားဖြင့် အသုံးပြုနိုင်သည်။ ၎င်းသည် ကျယ်ပြန့်သော အစိတ်အပိုင်း ဒီဇိုင်းများနှင့် အပလီကေးရှင်းများကို ပြုလုပ်နိုင်စေပါသည်။
ကိုက်ညီမှုနှင့် တိကျမှု- ထိုးသွင်းပုံသွင်းခြင်း သည် တစ်သမတ်တည်းနှင့် တိကျသော ရလဒ်များကို ပေးစွမ်းနိုင်ပြီး အစိတ်အပိုင်းများကြားတွင် ကွဲလွဲမှု အနည်းငယ်သာရှိသည်။ ၎င်းသည် အပိုင်းတစ်ခုစီသည် နောက်တစ်ခုနှင့် ထပ်တူကျကြောင်း သေချာစေသည်၊ ၎င်းသည် အက်ပ်များစွာအတွက် မရှိမဖြစ်လိုအပ်သည်။
ကုန်ကျစရိတ်သက်သာခြင်း- စိတ်ကြိုက်ပလပ်စတစ်ဆေးထိုးမှုပုံစံသည် ပမာဏမြင့်မားသောထုတ်လုပ်မှုအတွက် ကုန်ကျစရိတ်သက်သာနိုင်သည်။ ကနဦး ကိရိယာတန်ဆာပလာ ကုန်ကျစရိတ် မြင့်မားသော်လည်း ထုထည် တိုးလာသည်နှင့်အမျှ အစိတ်အပိုင်းအလိုက် ကုန်ကျစရိတ် ကျဆင်းသွားပါသည်။
ရှုပ်ထွေးမှု- ထိုးသွင်းပုံသွင်းခြင်းသည် ပါးလွှာသောနံရံများနှင့် အနုစိတ်သောအင်္ဂါရပ်များအပါအဝင် ရှုပ်ထွေးသောပုံစံများနှင့် ဂျီသြမေတြီများဖြင့် အစိတ်အပိုင်းများကို ထုတ်လုပ်နိုင်သည်။ ၎င်းသည် ပိုမိုကြီးမားသော ဒီဇိုင်းပြောင်းလွယ်ပြင်လွယ်ရှိမှုကို ခွင့်ပြုပေးပြီး အခြားနည်းလမ်းများကို အသုံးပြု၍ ထုတ်လုပ်ရန် ခက်ခဲသော သို့မဟုတ် မဖြစ်နိုင်သည့် အကြောင်းရင်းများကို ထုတ်လုပ်နိုင်စေပါသည်။
အနည်းဆုံး စွန့်ပစ်ပစ္စည်း- ပိုလျှံနေသော ပလတ်စတစ်များကို ပြန်လည်အသုံးပြုပြီး ပြန်လည်အသုံးပြုနိုင်သောကြောင့် ဆေးထိုးပုံသွင်းခြင်းသည် အခြားကုန်ထုတ်လုပ်ငန်းစဉ်များနှင့် နှိုင်းယှဉ်ပါက အမှိုက်အနည်းငယ်ကို ထုတ်ပေးပါသည်။
မျက်နှာပြင် finish ကို: ဆေးထိုးပုံသွင်းခြင်း သည် အပိုလုပ်ဆောင်မှုလွန်ခြင်း သို့မဟုတ် အပြီးသတ်လုပ်ဆောင်ခြင်းမပြုဘဲ အရည်အသွေးမြင့် မျက်နှာပြင်အချောဖြင့် အစိတ်အပိုင်းများကို ထုတ်လုပ်နိုင်သည်။ ၎င်းသည် ချောမွေ့ပြီး ပွတ်သပ်သောအသွင်အပြင်ဖြင့် အပိုင်းများကို ဖန်တီးရန်အတွက် ကုန်ကျစရိတ်သက်သာသော အဖြေတစ်ခုဖြစ်သည်။
အလိုအလျောက်: စက်ရုပ်များမှ အစိတ်အပိုင်းများကို မှိုတင်ခြင်းနှင့် ဖြုတ်ချခြင်းနှင့် စစ်ဆေးခြင်းနှင့် စီခြင်းအင်္ဂါရပ်များဖြင့် ထိုးသွင်းပုံသွင်းခြင်းကို လွယ်ကူစွာ အလိုအလျောက်လုပ်ဆောင်နိုင်သည်။ ၎င်းသည် လက်လုပ်လက်စားလုပ်အား လိုအပ်မှုကို လျော့နည်းစေပြီး စွမ်းဆောင်ရည်ကို တိုးစေသည်။
စိတ်ကြိုက်ပလပ်စတစ်ဆေးထိုးပုံသွင်းခြင်းသည် အခြားနည်းလမ်းများထက် အားသာချက်များစွာကို ပေးဆောင်သည့် စွယ်စုံရနှင့် ထိရောက်သော ကုန်ထုတ်လုပ်မှုလုပ်ငန်းစဉ်တစ်ခုဖြစ်သည်။ အလားတူ အစိတ်အပိုင်းအများအပြားကို လျင်မြန်တိကျစွာ ထုတ်လုပ်နိုင်စွမ်းရှိခြင်းကြောင့် မော်တော်ယာဥ်၊ အာကာသယာဉ်၊ ဆေးဘက်ဆိုင်ရာနှင့် လူသုံးကုန်ပစ္စည်းများအပါအဝင် လုပ်ငန်းများစွာအတွက် စံပြဖြစ်စေသည်။
ဆေးထိုးခြင်းဆိုင်ရာ အသုံးချမှုများ
Injection molding သည် အမျိုးမျိုးသော စက်မှုပလတ်စတစ် ထုတ်ကုန်များကို ဖန်တီးရန်အတွက် တွင်ကျယ်စွာ အသုံးပြုသော ကုန်ထုတ်လုပ်မှု လုပ်ငန်းစဉ်တစ်ခုဖြစ်သည်။ ဤသည်မှာ ဆေးထိုးပုံသွင်းခြင်း၏ အသုံးအများဆုံး အသုံးချမှု အချို့ဖြစ်သည်။
- မော်တော်ယာဥ်လုပ်ငန်း- ဆေးထိုးပုံသွင်းခြင်းသည် အတွင်းပိုင်းနှင့် အပြင်ပိုင်းဖြတ်တောက်မှု၊ ဒက်ရှ်ဘုတ် အစိတ်အပိုင်းများ၊ တံခါးလက်ကိုင်များနှင့် အင်ဂျင်အစိတ်အပိုင်းများအပါအဝင် မော်တော်ကားအစိတ်အပိုင်းများ အမျိုးမျိုးကို ထုတ်လုပ်သည်။ မြင့်မားသော ခွန်အားနှင့် အတိုင်းအတာ တိကျမှုရှိသော အင်္ဂါရပ်များ ရှိနိုင်သောကြောင့် ၎င်းကို ပိုမိုနှစ်သက်သည်။
- လူသုံးကုန်ပစ္စည်းများ- ဆေးထိုးမှုပုံသွင်းခြင်းသည် အရုပ်များ၊ အိမ်သုံးပစ္စည်းများနှင့် အီလက်ထရွန်နစ်ပစ္စည်းများအပါအဝင် လူသုံးကုန်ပစ္စည်းများကို ဖန်တီးပေးသည်။ ၎င်းသည် ရှုပ်ထွေးသော ပုံသဏ္ဍာန်များနှင့် ဂျီသြမေတြီများနှင့် အရည်အသွေးမြင့်မားသော မျက်နှာပြင်များကို ထုတ်လုပ်နိုင်စေပါသည်။
- ဆေးဘက်ဆိုင်ရာကိရိယာများ- ဆေးထိုးအပ်ပုံသွင်းခြင်းကို ဆေးထိုးအပ်များ၊ IV အစိတ်အပိုင်းများနှင့် ရောဂါရှာဖွေရေးကိရိယာများအပါအဝင် ဆေးဘက်ဆိုင်ရာကိရိယာအမျိုးမျိုးကို ထုတ်လုပ်ရန်အတွက် အသုံးပြုပါသည်။ ၎င်းသည် မြင့်မားသောတိကျမှု၊ သန့်ရှင်းသောထုတ်လုပ်မှုနှင့် ဆေးဘက်ဆိုင်ရာလုပ်ငန်းတွင် မရှိမဖြစ်လိုအပ်သည့် ရှုပ်ထွေးသောဂျီသြမေတြီများဖြင့် အစိတ်အပိုင်းများထုတ်လုပ်နိုင်စွမ်းကို ပေးဆောင်သည်။
- ထုပ်ပိုးခြင်းလုပ်ငန်း- ဆေးထိုးပုံသွင်းခြင်းသည် ပုလင်းများ၊ အိုးများနှင့် အဖုံးများအပါအဝင် ထုပ်ပိုးပစ္စည်းများကို ထုတ်လုပ်သည်။ ၎င်းသည် ပေါ့ပါးပြီး တာရှည်ခံသော ကွန်တိန်နာများကို ဖန်တီးရန်နှင့် အရောင်များ၊ အသွင်အပြင်များနှင့် ပုံသဏ္ဍာန်များကို စိတ်ကြိုက်ပြင်ဆင်နိုင်စေပါသည်။
- Aerospace လုပ်ငန်း- ဆေးထိုးပုံသွင်းခြင်းကို တည်ဆောက်ပုံဆိုင်ရာ ဒြပ်စင်များနှင့် အတွင်းပိုင်းဆက်စပ်ပစ္စည်းများ အပါအဝင် အာကာသယာဉ်အစိတ်အပိုင်းများ၏ အစိတ်အပိုင်းအမျိုးမျိုးကို ထုတ်လုပ်ရန် အသုံးပြုပါသည်။ ၎င်းသည် အလွန်အမင်း အပူချိန်နှင့် ဖိအားများကို ခံနိုင်ရည်ရှိသော စွမ်းဆောင်ရည်မြင့် ပစ္စည်းများကို ဖန်တီးနိုင်စေပါသည်။
- ဆောက်လုပ်ရေးလုပ်ငန်း- ဆေးထိုးပုံသွင်းခြင်းသည် PVC ပိုက်များ၊ ရေမြောင်းစနစ်များနှင့် အမိုးအကာပစ္စည်းများအပါအဝင် ဆောက်လုပ်ရေးပစ္စည်းများကို ထုတ်လုပ်သည်။ ၎င်းသည် မြင့်မားသောကြာရှည်ခံမှု၊ ရာသီဥတုနှင့် ဓာတုပစ္စည်းများကို ခံနိုင်ရည်ရှိပြီး အစိတ်အပိုင်းအများအပြားကို ထုတ်လုပ်နိုင်စွမ်းရှိသည်။
- အီလက်ထရွန်နစ်လုပ်ငန်း- ဆေးထိုးပုံသွင်းခြင်းသည် အိမ်ရာ၊ ချိတ်ဆက်ကိရိယာများနှင့် ခလုတ်များအပါအဝင် အမျိုးမျိုးသော အီလက်ထရွန်နစ်အစိတ်အပိုင်းများကို ထုတ်လုပ်သည်။ ၎င်းသည် မြင့်မားသောတိကျမှု၊ ညီညွှတ်မှုနှင့် အီလက်ထရွန်နစ်စက်မှုလုပ်ငန်းတွင် မရှိမဖြစ်လိုအပ်သော ရှုပ်ထွေးသော ဂျီသြမေတြီများဖြင့် အစိတ်အပိုင်းများကို ထုတ်လုပ်နိုင်စွမ်းကို ပေးဆောင်သည်။
ယေဘုယျအားဖြင့်၊ ဆေးထိုးပုံသွင်းခြင်းသည် စက်မှုလုပ်ငန်းများစွာအတွက် ပလတ်စတစ်အစိတ်အပိုင်းများစွာကို ထုတ်လုပ်ပေးနိုင်သည့် စွယ်စုံသုံးကုန်ထုတ်လုပ်မှုလုပ်ငန်းစဉ်တစ်ခုဖြစ်သည်။ ရှုပ်ထွေးသော ဂျီသြမေတြီများ၊ မြင့်မားသော တိကျမှုနှင့် တသမတ်တည်း အရည်အသွေးများဖြင့် အစိတ်အပိုင်းများကို ထုတ်လုပ်နိုင်စွမ်းရှိခြင်းကြောင့် ၎င်းသည် ထုတ်လုပ်သူအများအပြားအတွက် ရေပန်းစားသော ရွေးချယ်မှုတစ်ခုဖြစ်သည်။
ဆေးထိုးပုံသွင်းရာတွင် အသုံးပြုသည့် ပစ္စည်းအမျိုးအစားများ
ဆေးထိုးပုံသွင်းခြင်းဆိုသည်မှာ တိကျသောပုံသဏ္ဍာန်တစ်ခုဖန်တီးရန် မှိုပေါက်အတွင်း သွန်းသောပလပ်စတစ်ကို ထိုးသွင်းခြင်းပါဝင်သည့် ထုတ်လုပ်မှုလုပ်ငန်းစဉ်တစ်ခုဖြစ်သည်။ နောက်ဆုံးထုတ်ကုန်၏အလိုရှိသောဂုဏ်သတ္တိများအပေါ် မူတည်၍ ဆေးထိုးပုံသွင်းခြင်းတွင် မတူညီသောပစ္စည်းများကို အသုံးပြုနိုင်သည်။ ဆေးထိုးပုံသွင်းရာတွင် အသုံးပြုသည့် အသုံးအများဆုံး ပစ္စည်းအမျိုးအစားအချို့မှာ အောက်ပါအတိုင်းဖြစ်သည်။
- သာမိုပလတ်စတစ်များ- ၎င်းတို့သည် ဆေးထိုးပုံသွင်းရာတွင် အသုံးအများဆုံးပစ္စည်းများဖြစ်သည်။ ၎င်းတို့သည် အပူပေးသောအခါတွင် ပျော့ပျောင်းပြီး ပုံသွင်းနိုင်သော ပလတ်စတစ်အမျိုးအစားဖြစ်သည်။ သာမိုပလတ်စတစ်များသည် ၎င်းတို့၏ ဂုဏ်သတ္တိများ မဆုံးရှုံးဘဲ အကြိမ်များစွာ ပုံသွင်းနိုင်ပြီး ပြန်လည်ပုံသွင်းနိုင်သည်။ ဆေးထိုးပုံသွင်းရာတွင် အသုံးပြုလေ့ရှိသော သာမိုပလတ်စတစ်များသည် ပိုလီပပလီလင်း၊ ပိုလီအီသလင်း၊ ပေါ်လီစတီရင်းနှင့် နိုင်လွန်တို့ဖြစ်သည်။
- အပူချိန်ထိန်းကိရိယာများ- ၎င်းတို့သည် တစ်ကြိမ်သာ ပုံသွင်းနိုင်သော ပလတ်စတစ်များဖြစ်သည်။ ၎င်းတို့ကို အပူပေးပြီး သတ်သတ်မှတ်မှတ် ပုံသဏ္ဍာန်တစ်ခုအဖြစ် ဖွံ့ဖြိုးလာကာ ၎င်းတို့သည် မာကျောပြီးသည်နှင့် ၎င်းတို့ကို ပြန်လည်ပုံမသွင်းနိုင်ပေ။ မြင့်မားသော ကြံ့ခိုင်မှုနှင့် တာရှည်ခံမှု လိုအပ်သည့် အပူချိန်ထိန်းကိရိယာများကို အသုံးပြုသည်။ ဆေးထိုးပုံသွင်းရာတွင် အသုံးပြုလေ့ရှိသော အပူချိန်ထိန်းကိရိယာများတွင် epoxy၊ မယ်လမင်းနှင့် ဖီနိုလစ်အစေးများ ပါဝင်သည်။
- Elastomers- ဤပစ္စည်းများသည် ပျော့ပျောင်းသော ဂုဏ်သတ္တိများ ရှိပြီး ၎င်းတို့၏ မူလပုံစံသို့ ပြန်ဆွဲဆန့်နိုင်သည်။ ပျော့ပြောင်းမှုနှင့် တုန်ခါမှုစုပ်ယူမှု လိုအပ်သည့် အပလီကေးရှင်းများအတွက် Elastomers ကို အသုံးပြုသည်။ ဆေးထိုးပုံသွင်းရာတွင် အသုံးပြုသည့် Standard elastomers များတွင် ရော်ဘာ၊ ဆီလီကွန်နှင့် polyurethane တို့ပါဝင်သည်။
- ဇီဝပျက်စီးနိုင်သောပစ္စည်းများ- ၎င်းတို့သည် အန္တရာယ်ရှိသော အကြွင်းအကျန်များကို မချန်ထားဘဲ သဘာဝအတိုင်း ပြိုကွဲသွားနိုင်သည်။ သဘာဝပတ်ဝန်းကျင် ရေရှည်တည်တံ့ရေးသည် စိုးရိမ်စရာရှိသည့် အသုံးချပရိုဂရမ်များအတွက် ၎င်းတို့ကို အသုံးပြုသည်။ ဆေးထိုးပုံသွင်းခြင်းတွင် အသုံးပြုလေ့ရှိသော ဇီဝရုပ်ကြွင်းပစ္စည်းများမှာ polylactic acid (PLA) နှင့် polyhydroxyalkanoates (PHAs) တို့ ပါဝင်သည်။
- ပေါင်းစပ်ပစ္စည်းများသည် တိကျသောဂုဏ်သတ္တိများရှိသော ပစ္စည်းအသစ်တစ်ခုကို ဖန်တီးရန်အတွက် နှစ်ခု သို့မဟုတ် ထို့ထက်ပိုသော မတူညီသောပစ္စည်းများကို ပေါင်းစပ်ခြင်းဖြင့် ပြုလုပ်သောပစ္စည်းများဖြစ်သည်။ မြင့်မားသော ခိုင်ခံ့မှုနှင့် တင်းမာမှု လိုအပ်သည့် ပေါင်းစပ်မှုများကို အသုံးပြုသည်။ ဆေးထိုးပုံသွင်းရာတွင် အသုံးပြုသည့် Standard ပေါင်းစပ်ပစ္စည်းများတွင် ဖန်ဖိုက်ဘာအားဖြည့်ပလတ်စတစ်များ (GRP) နှင့် ကာဗွန်ဖိုက်ဘာအားဖြည့်ပလတ်စတစ်များ (CFRP) ပါဝင်သည်။
- သတ္တုဖြည့်ပလတ်စတစ်များသည် လျှပ်စစ်နှင့် အပူစီးကူးမှု မြင့်မားပြီး အခြားထူးခြားသော ဂုဏ်သတ္တိများရှိသော ပစ္စည်းများ ဖန်တီးရန်အတွက် သတ္တုအမှုန်များဖြင့် ပေါင်းစပ်ထားသော ပလတ်စတစ်များဖြစ်သည်။ သတ္တုဖြည့်ပလတ်စတစ်များကို လိုအပ်သော လျှပ်စစ် သို့မဟုတ် အပူစီးကူးနိုင်သော အသုံးချမှုများအတွက် အသုံးပြုသည်။ ဆေးထိုးပုံသွင်းရာတွင် အသုံးပြုလေ့ရှိသော သတ္တုဖြည့်ပလပ်စတစ်များသည် ကြေးနီဖြည့်ထားသော ပလတ်စတစ်များနှင့် နီကယ်ဖြည့်ထားသော ပလတ်စတစ်များ ပါဝင်သည်။
ယေဘုယျအားဖြင့်၊ ဆေးထိုးပုံသွင်းပစ္စည်းရွေးချယ်မှုသည် ခွန်အား၊ ပြောင်းလွယ်ပြင်လွယ်၊ လျှပ်ကူးနိုင်မှုနှင့် ကြာရှည်ခံမှုအပါအဝင် နောက်ဆုံးထုတ်ကုန်၏ သီးခြားလိုအပ်ချက်များအပေါ် မူတည်ပါသည်။ ထုတ်လုပ်သူများသည် ကုန်ကျစရိတ်၊ ရရှိနိုင်မှု၊ လုပ်ဆောင်ရလွယ်ကူမှုနှင့် နောက်ဆုံးထုတ်ကုန်အတွက် လိုအပ်သည့် ဂုဏ်သတ္တိများအပေါ် အခြေခံ၍ ပစ္စည်းများ ရွေးချယ်လေ့ရှိသည်။
ဆေးထိုးအပ်ပစ္စည်းကို ရွေးချယ်ရာတွင် ထည့်သွင်းစဉ်းစားရမည့်အချက်များ
နောက်ဆုံးထုတ်ကုန်၏ ဂုဏ်သတ္တိနှင့် စွမ်းဆောင်ရည်ကို ထိခိုက်စေနိုင်သောကြောင့် ဆေးထိုးခြင်းတွင် သင့်လျော်သောပစ္စည်းကို ရွေးချယ်ခြင်းသည် အရေးကြီးပါသည်။ ဆေးထိုးပုံသွင်းပစ္စည်းကို ရွေးချယ်ရာတွင် ထည့်သွင်းစဉ်းစားရမည့်အချက်အချို့မှာ အောက်ပါအတိုင်းဖြစ်သည်။
- စက်ပိုင်းဆိုင်ရာ ဂုဏ်သတ္တိများ- ပစ္စည်းတစ်ခုကို ရွေးချယ်ရာတွင် ထည့်သွင်းစဉ်းစားရမည့် အရေးကြီးဆုံးအချက်တစ်ခုမှာ ၎င်း၏စက်ပိုင်းဆိုင်ရာ ဂုဏ်သတ္တိများဖြစ်သည်။ ၎င်းတွင် ၎င်း၏ ကြံ့ခိုင်မှု၊ တောင့်တင်းမှု၊ တောင့်တင်းမှုနှင့် ခံနိုင်ရည်ရှိမှုတို့ ပါဝင်သည်။ နောက်ဆုံး ထုတ်ကုန်အတွက် လိုအပ်သော စက်ပိုင်းဆိုင်ရာ ဂုဏ်သတ္တိများသည် လျှောက်လွှာနှင့် ထုတ်ကုန်ကို ထိတွေ့မည့် ဖိစီးမှုများအပေါ် မူတည်ပါသည်။
- အပူဓာတ်ဂုဏ်သတ္တိများ- ပစ္စည်းတစ်ခု၏ အပူဓာတ်ဂုဏ်သတ္တိများသည်လည်း အရေးကြီးသည်၊ အထူးသဖြင့် နောက်ဆုံးထုတ်ကုန်သည် အပူချိန်မြင့်မားခြင်း သို့မဟုတ် အပူစက်ဘီးစီးခြင်းများနှင့် ထိတွေ့မိပါက အရေးကြီးပါသည်။ ၎င်းတွင် ပစ္စည်း၏ အရည်ပျော်မှတ်၊ အပူစီးကူးမှုနှင့် အပူချဲ့ထွင်မှု ကိန်းဂဏန်းတို့ ပါဝင်သည်။
- Chemical resistance- နောက်ဆုံးထုတ်ကုန်သည် ဓာတုပစ္စည်းများနှင့် ထိတွေ့ပါက၊ ဓာတုပျက်စီးမှုကို ခံနိုင်ရည်ရှိသော ပစ္စည်းကို ရွေးချယ်ခြင်းသည် မရှိမဖြစ်လိုအပ်ပါသည်။ ပစ္စည်းသည် အက်ဆစ်များ၊ အောက်ခံများ၊ ပျော်ရည်များနှင့် အခြားဓာတုပစ္စည်းများနှင့် ၎င်း၏ဂုဏ်သတ္တိများ မဆုံးရှုံးစေဘဲ အက်ဆစ်များနှင့် ထိတွေ့မှုကို ခံနိုင်ရည်ရှိသင့်သည်။
- ပတ်ဝန်းကျင်ဆိုင်ရာအချက်များ- စိုထိုင်းဆနှင့် ခရမ်းလွန်ရောင်ခြည်ထိတွေ့မှုကဲ့သို့သော ပတ်ဝန်းကျင်ဆိုင်ရာအချက်များသည် ပစ္စည်းတစ်ခု၏ ဂုဏ်သတ္တိနှင့် စွမ်းဆောင်ရည်ကို ထိခိုက်စေနိုင်သည်။ နောက်ဆုံးထုတ်ကုန်၏ ပတ်ဝန်းကျင်အခြေအနေများကို ထည့်သွင်းစဉ်းစားပြီး ၎င်းတို့ကို ခံနိုင်ရည်ရှိသော ပစ္စည်းကို ရွေးချယ်ရန် အရေးကြီးသည်။
- ကုန်ကျစရိတ်- ပစ္စည်း၏ကုန်ကျစရိတ်သည် အထူးသဖြင့် ပမာဏမြင့်မားသောထုတ်လုပ်မှုအတွက် အရေးကြီးသောထည့်သွင်းစဉ်းစားမှုတစ်ခုဖြစ်သည်။ နောက်ဆုံးထုတ်ကုန်အတွက် ကုန်ကျစရိတ်သက်သာသော ရွေးချယ်မှုဖြစ်ကြောင်း သေချာစေရန်အတွက် ပစ္စည်း၏ကုန်ကျစရိတ်သည် ၎င်း၏စွမ်းဆောင်ရည်နှင့် ဂုဏ်သတ္တိများကို ချိန်ဆသင့်သည်။
- လုပ်ဆောင်ခြင်းဆိုင်ရာ လိုအပ်ချက်များ- ပစ္စည်းတစ်ခုအတွက် လုပ်ဆောင်ခြင်းဆိုင်ရာ လိုအပ်ချက်များသည် ရွေးချယ်မှုလုပ်ငန်းစဉ်ကို ထိခိုက်စေနိုင်သည်။ အချို့သောပစ္စည်းများသည် တိကျသော ပြုပြင်ရေးကိရိယာ သို့မဟုတ် နည်းစနစ်များ လိုအပ်နိုင်ပြီး အချို့အရာများသည် လုပ်ဆောင်ရန် ပိုမိုခက်ခဲနိုင်သည်။ ဆေးထိုးပုံသွင်းခြင်းလုပ်ငန်းစဉ်တွင် ပစ္စည်းကို အောင်မြင်စွာအသုံးပြုနိုင်ကြောင်း သေချာစေရန် လုပ်ဆောင်ခြင်းဆိုင်ရာ လိုအပ်ချက်များကို ထည့်သွင်းစဉ်းစားသင့်သည်။
- စည်းမျဥ်းစည်းကမ်းလိုက်နာမှု- နောက်ဆုံးတွင်၊ နောက်ဆုံးထုတ်ကုန်နှင့်ကိုက်ညီရမည့် စည်းမျဉ်းစည်းကမ်းသတ်မှတ်ချက်များကို ထည့်သွင်းစဉ်းစားရန် အရေးကြီးပါသည်။ ဆေးဘက်ဆိုင်ရာနှင့် အစားအသောက်လုပ်ငန်းများကဲ့သို့သော အချို့သောစက်မှုလုပ်ငန်းများတွင် ၎င်းတို့၏ထုတ်ကုန်များတွင် အသုံးပြုသည့်ပစ္စည်းများအတွက် သီးခြားစည်းမျဉ်းများရှိသည်။ နောက်ဆုံးထုတ်ကုန်သည် ဘေးကင်းပြီး လိုက်လျောညီထွေရှိစေရန် ဤစည်းမျဉ်းစည်းကမ်းသတ်မှတ်ချက်များနှင့် ကိုက်ညီသည့်ပစ္စည်းကို ရွေးချယ်ခြင်းသည် မရှိမဖြစ်လိုအပ်ပါသည်။
ယေဘုယျအားဖြင့်၊ ဆေးထိုးပုံသွင်းခြင်းအတွက် သင့်လျော်သောပစ္စည်းကို ရွေးချယ်ခြင်းသည် စက်ပိုင်းဆိုင်ရာနှင့် အပူဓာတ်ဂုဏ်သတ္တိများ၊ ဓာတုခံနိုင်ရည်ရှိမှု၊ ပတ်ဝန်းကျင်ဆိုင်ရာအချက်များ၊ ကုန်ကျစရိတ်၊ လုပ်ငန်းစဉ်လိုအပ်ချက်များနှင့် စည်းကမ်းလိုက်နာမှုတို့အပါအဝင် အမျိုးမျိုးသောအချက်များကို ဂရုတစိုက် ထည့်သွင်းစဉ်းစားရန် လိုအပ်ပါသည်။ ထုတ်လုပ်သူသည် နောက်ဆုံးထုတ်ကုန်အတွက် အသင့်တော်ဆုံးပစ္စည်းကို ရွေးချယ်ရန် ဤအချက်များကို အချင်းချင်း ချိန်ဆရပါမည်။
ဆေးထိုးပုံသွင်းခြင်းတွင် မှိုဒီဇိုင်း၏ အရေးပါမှု
မှိုဒီဇိုင်းသည် ဆေးထိုးပုံသွင်းခြင်းလုပ်ငန်းစဉ်၏ အရေးကြီးသော ကဏ္ဍတစ်ခုဖြစ်သည်။ မှို၏ဒီဇိုင်းသည် နောက်ဆုံးထုတ်ကုန်၏အရည်အသွေးအပြင် ထုတ်လုပ်မှုလုပ်ငန်းစဉ်၏ ထိရောက်မှုနှင့် ကုန်ကျစရိတ်သက်သာမှုတို့ကို ထိခိုက်စေနိုင်သည်။ ဆေးထိုးပုံသွင်းခြင်းတွင် မှိုဒီဇိုင်းသည် မရှိမဖြစ်လိုအပ်သော အကြောင်းရင်းအချို့ဖြစ်သည်။
- ထုတ်ကုန်အရည်အသွေး- မှို၏ဒီဇိုင်းသည် နောက်ဆုံးထုတ်ကုန်၏အရည်အသွေးကို ထိခိုက်စေနိုင်သည်။ မှိုကို မှန်ကန်စွာ ဒီဇိုင်းမွမ်းမံထားပါက၊ ၎င်းသည် warping၊ sink marks နှင့် flash ကဲ့သို့သော ချို့ယွင်းချက်များ ဖြစ်ပေါ်နိုင်သည်။ ဤချို့ယွင်းချက်များသည် နောက်ဆုံးထုတ်ကုန်ကို အသုံးမပြုနိုင်စေရန်၊ စွမ်းဆောင်ရည်ကို လျှော့ချနိုင်ပြီး အပိုင်းအစနှုန်းနှင့် ထုတ်လုပ်မှုကုန်ကျစရိတ်များကို တိုးမြင့်စေနိုင်သည်။
- ထုတ်လုပ်မှု ထိရောက်မှု- မှို၏ ဒီဇိုင်းသည် ထုတ်လုပ်မှု လုပ်ငန်းစဉ်၏ ထိရောက်မှုကိုလည်း ထိခိုက်စေနိုင်သည်။ မှိုသည် အကောင်းဆုံး စီးဆင်းမှုနှင့် အအေးခံရန်အတွက် ဒီဇိုင်းထုတ်ထားခြင်း မရှိပါက၊ ၎င်းသည် စက်ဝန်းအချိန်ကြာကြာ၊ စွမ်းအင်သုံးစွဲမှု တိုးလာပြီး ဖြတ်သန်းမှု လျော့ကျသွားနိုင်သည်။ အကောင်းဆုံးမှိုဒီဇိုင်းသည် စွမ်းဆောင်ရည်ကို တိုးတက်စေပြီး ထုတ်လုပ်မှုကုန်ကျစရိတ်ကို လျှော့ချနိုင်သည်။
- ကုန်ကျစရိတ်-ထိရောက်မှု- မှိုဒီဇိုင်းသည် ဆေးထိုးပုံသွင်းခြင်းလုပ်ငန်းစဉ်၏ ကုန်ကျစရိတ်ထိရောက်မှုကိုလည်း ထိခိုက်စေနိုင်သည်။ ကောင်းစွာ ဒီဇိုင်းထုတ်ထားသော မှိုသည် ပစ္စည်းစွန့်ပစ်ပစ္စည်းများကို လျှော့ချနိုင်ပြီး အစိတ်အပိုင်း အရည်အသွေးကို မြှင့်တင်ပေးကာ ထုတ်လုပ်မှု ကုန်ကျစရိတ်ကို တိုးမြင့်စေနိုင်သည်။ ထို့အပြင်၊ ပမာဏမြင့်မားသောထုတ်လုပ်မှုအတွက် ဒီဇိုင်းထုတ်ထားသော မှိုသည် အစိတ်အပိုင်းတစ်ခုစီအတွက် ကုန်ကျစရိတ်ကို လျှော့ချနိုင်ပြီး ရင်းနှီးမြှုပ်နှံမှုအပေါ် ပြန်အမ်းငွေတိုးစေသည်။
- စိတ်ကြိုက်ပြင်ဆင်ခြင်း- မှိုဒီဇိုင်းသည် နောက်ဆုံးထုတ်ကုန်ကို စိတ်ကြိုက်ပြင်ဆင်ခြင်းတွင် အရေးပါသောအခန်းကဏ္ဍမှ ပါဝင်ပါသည်။ သတ်မှတ်ထားသော ပုံသဏ္ဍာန်များနှင့် အင်္ဂါရပ်များအတွက် မှိုကို ဒီဇိုင်းထုတ်ခြင်းဖြင့် ထုတ်လုပ်သူများသည် ၎င်းတို့၏ ဖောက်သည်များ၏ လိုအပ်ချက်နှင့် အံဝင်ခွင်ကျရှိသော ထုတ်ကုန်များကို ဖန်တီးနိုင်သည်။ ၎င်းသည် စျေးကွက်တွင် ပိုမိုပြောင်းလွယ်ပြင်လွယ်နှင့် ကွဲပြားမှုကို ဖြစ်ပေါ်စေပြီး ဖောက်သည်များ၏ စိတ်ကျေနပ်မှုနှင့် သစ္စာစောင့်သိမှုကို တိုးမြှင့်စေသည်။
- ပစ္စည်းရွေးချယ်ခြင်း- မှိုဒီဇိုင်းသည် ဆေးထိုးပုံသွင်းရာတွင် အသုံးပြုသည့် ပစ္စည်းရွေးချယ်မှုအပေါ်လည်း လွှမ်းမိုးနိုင်သည်။ ပုံသွင်းနည်းသည် ပစ္စည်းစီးဆင်းမှုနှင့် အအေးခံမှုကို ထိခိုက်စေနိုင်ပြီး နောက်ဆုံးထုတ်ကုန်၏ စက်ပိုင်းဆိုင်ရာနှင့် အပူဓာတ်ဂုဏ်သတ္တိများကို ထိခိုက်စေနိုင်သည်။ မှန်ကန်သော မှိုဒီဇိုင်းကို ရွေးချယ်ခြင်းဖြင့် ထုတ်လုပ်သူများသည် ပစ္စည်းရွေးချယ်မှုကို အကောင်းဆုံးဖြစ်အောင် လုပ်ဆောင်နိုင်ပြီး နောက်ဆုံးထုတ်ကုန်သည် အလိုရှိသော စွမ်းဆောင်ရည်လိုအပ်ချက်များနှင့် ကိုက်ညီကြောင်း သေချာစေသည်။
ယေဘုယျအားဖြင့်၊ မှိုဒီဇိုင်းသည် ဆေးထိုးပုံသွင်းခြင်းလုပ်ငန်းစဉ်တွင် အရေးကြီးသောအချက်ဖြစ်သည်။ ဒီဇိုင်းကောင်းမွန်သောမှိုသည် ထုတ်ကုန်အရည်အသွေး၊ ထုတ်လုပ်မှုထိရောက်မှု၊ ကုန်ကျစရိတ်သက်သာမှု၊ စိတ်ကြိုက်ပြင်ဆင်မှုနှင့် ပစ္စည်းရွေးချယ်မှုတို့ကို တိုးတက်စေနိုင်သည်။ ထုတ်လုပ်သူများသည် ဆေးထိုးပုံသွင်းခြင်းလုပ်ငန်းစဉ်တွင် အကောင်းဆုံးဖြစ်နိုင်သောရလဒ်များရရှိရန် ၎င်းတို့၏တိကျသောလိုအပ်ချက်များအတွက် အကောင်းဆုံးမှိုများကို ဒီဇိုင်းထုတ်ရာတွင် အချိန်နှင့်အရင်းအမြစ်များကို ရင်းနှီးမြှုပ်နှံရမည်ဖြစ်သည်။
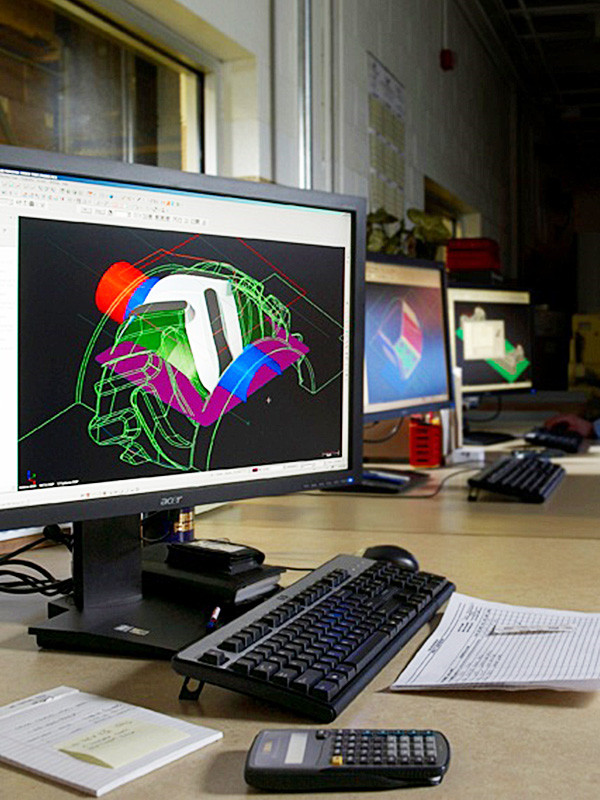
ဆေးထိုးပုံသွင်းရာတွင် အသုံးပြုသော မှိုအမျိုးမျိုး
ဆေးထိုးပုံသွင်းခြင်းသည် အမျိုးမျိုးသော ပလပ်စတစ်ထုတ်ကုန်များကို ထုတ်လုပ်နိုင်သည့် စွယ်စုံသုံးကုန်ထုတ်လုပ်မှုလုပ်ငန်းစဉ်တစ်ခုဖြစ်သည်။ ဆေးထိုးပုံသွင်းခြင်း၏ အရည်အသွေးနှင့် ထိရောက်မှုကို သတ်မှတ်ရန် အရေးကြီးသောအချက်တစ်ခုမှာ အသုံးပြုသောမှိုအမျိုးအစားဖြစ်သည်။ ဆေးထိုးပုံသွင်းရာတွင် အသုံးပြုသည့် မှိုအမျိုးအစားအချို့မှာ အောက်ပါအတိုင်းဖြစ်သည်။
- နှစ်ပြားမှို- နှစ်ပြားမှိုများသည် ဆေးထိုးပုံသွင်းရာတွင် အသုံးအများဆုံးမှိုဖြစ်သည်။ ၎င်းတို့တွင် မှိုပေါက်ဖြင့် ခြားထားသော ပန်းကန်ပြား နှစ်ခုပါရှိသည်။ ပလပ်စတစ်ပစ္စည်းကို အပေါက်ထဲသို့ ထိုးသွင်းပြီး ပန်းကန်ပြားနှစ်ခုကို ပေါင်းစပ်ပြီး နောက်ဆုံးထုတ်ကုန်အဖြစ် ဖန်တီးသည်။
- သုံးပန်းကန်မှို- သုံးပန်းကန်မှိုများသည် ပန်းကန်ပြားနှစ်ချပ်မှိုများနှင့် ဆင်တူသော်လည်း အပြေးသမားစနစ်အား ပုံသွင်းထားသောအပိုင်းနှင့် ပိုင်းခြားထားသော နောက်ထပ်ပန်းကန်တစ်ခုရှိသည်။ ၎င်းသည် အစိတ်အပိုင်းကို ပိုမိုလွယ်ကူစွာ ထုတ်နိုင်စေရန်နှင့် လည်ပတ်ချိန်ကို လျှော့ချနိုင်သည်။
- ပူသောအပြေးသမားမှို- အပူအပြေးသမားမှိုများသည် လည်ပတ်ချိန်နှင့် ပစ္စည်းစွန့်ပစ်မှုကို လျှော့ချနိုင်သောကြောင့် ပမာဏမြင့်မားသော ထုတ်လုပ်မှုအတွက် အသုံးပြုပါသည်။ မှိုတွင် အရည်ပျော်သော ပလပ်စတစ်ကို မှိုအပေါက်ထဲသို့ တိုက်ရိုက် ပို့ဆောင်ပေးသည့် အပူပေး အပြေးသမား စနစ်ပါရှိသည်။
- အပြေးသမားမှို- အအေးခံမှိုများသည် အခြေခံအကျဆုံးမှိုအမျိုးအစားဖြစ်ပြီး တံမှို၊ အပြေးသမားများနှင့် မှိုပေါက်တစ်ခုတို့ပါဝင်သည်။ သွန်းသောပလပ်စတစ်ကို အမှုန်အမွှားထဲသို့ ထိုးသွင်းပြီး ပလတ်စတစ်ကို အပြေးသမားများထဲသို့ ဖြည့်သွင်းကာ မှိုပေါက်ထဲသို့ ထိုးသွင်းသည်။
- မိသားစုမှို- မိသားစုမှိုများသည် စက်ဝိုင်းတစ်ခုတည်းတွင် အစိတ်အပိုင်းများစွာကို ထုတ်လုပ်သည်။ မှိုတွင် အပေါက်များစွာပါဝင်ပြီး တစ်ခုစီတွင် မတူညီသော အစိတ်အပိုင်းတစ်ခုရှိသည်။ မိသားစုမှိုများကို သေးငယ်ပြီး ပမာဏမြင့်သော အစိတ်အပိုင်းများအတွက် အသုံးပြုလေ့ရှိသည်။
- Stack မှို- Stack မှိုများသည် စက်ဝိုင်းတစ်ခုတည်းတွင် ပလပ်စတစ်အလွှာများစွာကို ထုတ်လုပ်သည်။ မှိုတွင် တစ်ခုနှင့်တစ်ခု အပေါ်ထပ်တွင် အထပ်ထပ်ရှိသော အပေါက်များပါရှိသည်။ ပလပ်စတစ်ကို အပေါက်များထဲသို့ ထိုးသွင်းပြီး အလွှာများကို တစ်ခုတည်း၊ အလွှာပေါင်းစုံ ထုတ်ကုန်တစ်ခုအဖြစ် ပေါင်းစပ်ဖွဲ့စည်းသည်။
- မှိုထည့်ခြင်း- ပုံသွင်းခြင်းလုပ်ငန်းစဉ်အတွင်း သတ္တု သို့မဟုတ် ပလပ်စတစ်အစိတ်အပိုင်းများကို ပုံသွင်းထားသောအစိတ်အပိုင်းအတွင်းသို့ ထည့်သွင်းရန်အတွက် မှိုထည့်ခြင်းကို အသုံးပြုသည်။ ပလပ်စတစ်မထိုးမီ မှိုအပေါက်ထဲသို့ ထိုးထည့်ကာ ပလပ်စတစ်ကို ထည့်ပြီး ဝိုင်းရံထားသည်။
ယေဘုယျအားဖြင့် ဆေးထိုးပုံသွင်းရာတွင် အသုံးပြုသည့် မှိုအမျိုးအစားသည် ထုတ်လုပ်သည့် ထုတ်ကုန်၏ သီးခြားလိုအပ်ချက်များပေါ်တွင် မူတည်ပါသည်။ မှန်ကန်သောမှိုအမျိုးအစားကို ရွေးချယ်ခြင်းဖြင့် ထုတ်လုပ်သူများသည် ဆေးထိုးပုံသွင်းခြင်းလုပ်ငန်းစဉ်၏ ထိရောက်မှု၊ အရည်အသွေးနှင့် ကုန်ကျစရိတ်သက်သာမှုကို အကောင်းဆုံးဖြစ်အောင် လုပ်ဆောင်နိုင်သည်။
ဆေးထိုးခြင်းအတွက် အကောင်းဆုံးအလေ့အကျင့်
ဆေးထိုးပုံသွင်းခြင်းသည် အလိုရှိသောရလဒ်များရရှိရန် ဂရုတစိုက်စီစဉ်ခြင်းနှင့် အကောင်အထည်ဖော်ရန် လိုအပ်သော ရှုပ်ထွေးသောထုတ်လုပ်မှုလုပ်ငန်းစဉ်တစ်ခုဖြစ်သည်။ ဤသည်မှာ အကောင်းဆုံးအရည်အသွေး၊ ထိရောက်မှုနှင့် ကုန်ကျစရိတ်သက်သာမှုတို့ကို သေချာစေရန် ကူညီပေးနိုင်သည့် ဆေးထိုးပုံသွင်းခြင်းအတွက် အကောင်းဆုံးအလေ့အကျင့်အချို့ဖြစ်သည်။
- ထုတ်လုပ်နိုင်စွမ်းအတွက် ဒီဇိုင်း- ထုတ်ကုန်၏ ဒီဇိုင်းသည် ဆေးထိုးပုံသွင်းခြင်းအတွက် အကောင်းဆုံးဖြစ်သင့်သည်။ ၎င်းတွင် အစိတ်အပိုင်းအရေအတွက်ကို လျှော့ချခြင်း၊ တူညီသောနံရံအထူရှိစေရန်နှင့် ပုံသွင်းခြင်းကို ရှုပ်ထွေးစေသော အခြားအင်္ဂါရပ်များကို ရှောင်ရှားခြင်းတို့ ပါဝင်သည်။
- ပစ္စည်းရွေးချယ်ခြင်း- ဆေးထိုးပုံသွင်းရာတွင် အသုံးပြုသည့်ပစ္စည်းကို ထုတ်ကုန်၏လိုအပ်ချက်များအပေါ်အခြေခံ၍ ရွေးချယ်သင့်သည်။ စက်ပိုင်းဆိုင်ရာဂုဏ်သတ္တိများ၊ အပူဂုဏ်သတ္တိများနှင့် ပတ်ဝန်းကျင် ခုခံမှုစသည့်အချက်များကို ထည့်သွင်းစဉ်းစားသင့်သည်။
- မှိုဒီဇိုင်း- မှိုဒီဇိုင်းသည် သီးသန့်ထုတ်ကုန်အတွက် အကောင်းဆုံးဖြစ်သင့်သည်။ ၎င်းတွင် သင့်လျော်သော အအေးခံခြင်း၊ လေဝင်လေထွက်နှင့် တံခါးပေါက်များကို သေချာစေခြင်း၊ သင့်လျော်သော မှိုအမျိုးအစားကို ရွေးချယ်ခြင်းတို့ ပါဝင်သည်။
- ဆေးထိုးခြင်းဆိုင်ရာ ကန့်သတ်ချက်များ- ဆေးထိုးဖိအား၊ အပူချိန်နှင့် အရှိန်ကဲ့သို့သော ဆေးထိုးဘောင်များကို အကောင်းမွန်ဆုံး အရည်အသွေးနှင့် လိုက်လျောညီထွေရှိစေရန် ဂရုတစိုက် ထိန်းချုပ်ပြီး စောင့်ကြည့်သင့်သည်။
- ပြုပြင်ထိန်းသိမ်းမှု- ပုံမှန်ဆေးထိုးပုံသွင်းစက်နှင့် မှိုထိန်းသိမ်းခြင်းသည် အကောင်းဆုံးစွမ်းဆောင်ရည်ကိုသေချာစေရန်နှင့် စက်ရပ်ခြင်းကိုကာကွယ်ရန် အရေးကြီးပါသည်။
- အရည်အသွေးထိန်းချုပ်မှု- ဆေးထိုးပုံသွင်းခြင်းလုပ်ငန်းစဉ်တစ်လျှောက်တွင် အရည်အသွေးထိန်းချုပ်မှုကို ဝင်လာသည့်ပစ္စည်းစစ်ဆေးခြင်းမှ နောက်ဆုံးထုတ်ကုန်စစ်ဆေးခြင်းအထိ လုပ်ဆောင်သင့်သည်။ ၎င်းတွင် warpage၊ sink marks နှင့် flash ကဲ့သို့သော စောင့်ကြည့်ရေးချို့ယွင်းချက်များ ပါဝင်သည်။
- လုပ်ငန်းစဉ် ပိုမိုကောင်းမွန်အောင် ပြုလုပ်ခြင်း- စဉ်ဆက်မပြတ် လုပ်ငန်းစဉ် မြှင့်တင်ခြင်းသည် ဆေးထိုးပုံသွင်းခြင်း လုပ်ငန်းများကို အဓိက အာရုံစိုက်သင့်သည်။ ၎င်းတွင် စက်လည်ပတ်ချိန်၊ အပိုင်းအစနှုန်းနှင့် စက်အသုံးပြုမှုကဲ့သို့သော လုပ်ငန်းစဉ်စွမ်းဆောင်ရည်ကို စောင့်ကြည့်စစ်ဆေးခြင်းနှင့် စွမ်းဆောင်ရည်နှင့် အရည်အသွေးကို အကောင်းဆုံးဖြစ်အောင် လိုအပ်သလို ချိန်ညှိခြင်းများ ပါဝင်သည်။
ယေဘုယျအားဖြင့်၊ ဆေးထိုးပုံသွင်းခြင်းတွင် အသေးစိတ်အချက်အလက်များကို ဂရုတစိုက်အာရုံစိုက်ရန်နှင့် စဉ်ဆက်မပြတ်တိုးတက်မှုအပေါ် အာရုံစိုက်ရန် လိုအပ်သည်။ ဆေးထိုးပုံသွင်းခြင်းအတွက် အကောင်းဆုံးအလေ့အကျင့်များကို လိုက်နာခြင်းဖြင့် ထုတ်လုပ်သူများသည် အကောင်းဆုံးအရည်အသွေး၊ ထိရောက်မှုနှင့် ကုန်ကျစရိတ်သက်သာမှုကို သေချာစေပြီး ၎င်းတို့၏ဖောက်သည်များ၏ လိုအပ်ချက်များကို ဖြည့်ဆည်းပေးသည့် အရည်အသွေးမြင့် ပလပ်စတစ်ထုတ်ကုန်များကို ထုတ်လုပ်နိုင်သည်။
ဆေးထိုးပုံသွင်းခြင်းအတွက် အရည်အသွေးထိန်းချုပ်မှုများ
နောက်ဆုံးထုတ်ကုန်သည် လိုအပ်သော သတ်မှတ်ချက်များနှင့် စံချိန်စံညွှန်းများနှင့် ကိုက်ညီကြောင်း သေချာစေသောကြောင့် ဆေးထိုးပုံသွင်းခြင်းတွင် အရည်အသွေးထိန်းချုပ်မှုသည် အရေးကြီးပါသည်။ ဆေးထိုးပုံသွင်းခြင်းအတွက် အရည်အသွေးထိန်းချုပ်မှုအစီအမံအချို့ ဖြစ်သည်-
- ဝင်လာသည့်ပစ္စည်းကို စစ်ဆေးခြင်း- အရည်အသွေးထိန်းချုပ်မှုလုပ်ငန်းစဉ်သည် ဆေးထိုးပုံသွင်းခြင်းအတွက် အသုံးပြုသည့် ကုန်ကြမ်းကို ပြန်လည်သုံးသပ်ခြင်းဖြင့် စတင်သင့်သည်။ ၎င်းတွင် ပစ္စည်းသည် မှန်ကန်သော အမျိုးအစား၊ အဆင့်နှင့် အရောင်ဖြစ်ကြောင်း အတည်ပြုပြီး လိုအပ်သော စက်ပိုင်းဆိုင်ရာနှင့် အပူဓာတ်ဆိုင်ရာ သတ်မှတ်ချက်များနှင့် ကိုက်ညီကြောင်း စစ်ဆေးခြင်း ပါဝင်သည်။
- လုပ်ငန်းစဉ်အတွင်း စစ်ဆေးခြင်း- ဆေးထိုးပုံသွင်းနေစဉ်အတွင်း အရည်အသွေးထိန်းချုပ်ရေးဝန်ထမ်းများသည် ထုတ်ကုန်ကို ပုံသွင်းထားကြောင်း သေချာစေရန် ပုံမှန်စစ်ဆေးသင့်သည်။ ၎င်းတွင် sink marks များ၊ warping နှင့် flash ကဲ့သို့သော ချို့ယွင်းချက်များကို စောင့်ကြည့်ခြင်းနှင့် ထုတ်ကုန်သည် လိုအပ်သောအတိုင်းအတာအထိခံနိုင်ရည်များပြည့်မီကြောင်း စစ်ဆေးခြင်းတို့ပါဝင်သည်။
- နောက်ဆုံးထုတ်ကုန်စစ်ဆေးခြင်း- ဆေးထိုးပုံသွင်းခြင်းလုပ်ငန်းစဉ်ပြီးသည်နှင့်၊ လိုအပ်သောသတ်မှတ်ချက်များနှင့်စံနှုန်းများနှင့်ကိုက်ညီကြောင်းသေချာစေရန်နောက်ဆုံးထုတ်ကုန်ကိုစစ်ဆေးသင့်သည်။ ၎င်းတွင် ထုတ်ကုန်သည် အက်ကွဲများ၊ ပူဖောင်းများနှင့် ပျက်ပြယ်သွားခြင်းကဲ့သို့သော ချို့ယွင်းချက်များနှင့် ကင်းစင်ကြောင်း စစ်ဆေးခြင်း အပါအဝင် လိုအပ်သော အတိုင်းအတာခံနိုင်ရည်များနှင့် ကိုက်ညီပါသည်။
- စာရင်းအင်းဆိုင်ရာ လုပ်ငန်းစဉ်ထိန်းချုပ်မှု- စာရင်းအင်းဆိုင်ရာ လုပ်ငန်းစဉ်ထိန်းချုပ်မှု (SPC) သည် လုပ်ငန်းစဉ်တစ်ခုအား တသမတ်တည်း အရည်အသွေးမြင့်ရလဒ်များထုတ်ပေးကြောင်း သေချာစေရန် စောင့်ကြည့်ထိန်းချုပ်သည့် နည်းလမ်းတစ်ခုဖြစ်သည်။ SPC သည် ဆေးထိုးဖိအားနှင့် အပူချိန်ကဲ့သို့ အရေးကြီးသော လုပ်ငန်းစဉ်ဘောင်များတွင် ဒေတာစုဆောင်းခြင်းနှင့် လုပ်ငန်းစဉ်ကွဲလွဲမှုကို ညွှန်ပြသည့် ခေတ်ရေစီးကြောင်းနှင့် ပုံစံများကို ခွဲခြားသတ်မှတ်ရန် ကိန်းဂဏန်းဆိုင်ရာ ခွဲခြမ်းစိတ်ဖြာမှုကို အသုံးပြုခြင်း။
- စဉ်ဆက်မပြတ် တိုးတက်မှု- အရည်အသွေးထိန်းချုပ်မှုသည် စဉ်ဆက်မပြတ် တိုးတက်မှု၏ လုပ်ငန်းစဉ်တစ်ခု ဖြစ်သင့်သည်။ ၎င်းတွင် လုပ်ငန်းစဉ်စွမ်းဆောင်ရည်အပေါ် ဒေတာခွဲခြမ်းစိတ်ဖြာခြင်း၊ တိုးတက်မှုအတွက် နယ်ပယ်များကို ခွဲခြားသတ်မှတ်ခြင်းနှင့် အရည်အသွေးနှင့် စွမ်းဆောင်ရည်ကို ပိုကောင်းအောင်ပြုလုပ်ရန် လုပ်ငန်းစဉ်ကို ပြောင်းလဲခြင်းများ ပါဝင်သည်။
- စာရွက်စာတမ်းနှင့် ခြေရာခံနိုင်မှု- အရည်အသွေးထိန်းချုပ်ရေးဝန်ထမ်းများသည် ဆေးထိုးပုံသွင်းခြင်းလုပ်ငန်းစဉ်၏ အသေးစိတ်စာရွက်စာတမ်းများကို ထိန်းသိမ်းထားသင့်ပြီး လုပ်ငန်းစဉ်သတ်မှတ်ချက်များ၊ စစ်ဆေးခြင်းရလဒ်များနှင့် မှန်ကန်သောလုပ်ဆောင်ချက်များ ပါဝင်သည်။ ဤစာရွက်စာတမ်းသည် ခြေရာခံနိုင်မှုကို ပေးဆောင်ပြီး အရည်အသွေးဆိုင်ရာ ပြဿနာများကို ဖော်ထုတ်နိုင်ပြီး လျင်မြန်စွာ ပြုပြင်နိုင်ကြောင်း သေချာစေပါသည်။
ယေဘုယျအားဖြင့်၊ အရည်အသွေးထိန်းချုပ်မှုသည် ဆေးထိုးပုံသွင်းခြင်း၏ အရေးကြီးသောကဏ္ဍတစ်ခုဖြစ်ပြီး ထုတ်လုပ်မှုလုပ်ငန်းစဉ်၏ ကဏ္ဍတိုင်းတွင် ပေါင်းစပ်သင့်သည်။ ဤအရည်အသွေးထိန်းချုပ်မှုအစီအမံများကို အကောင်အထည်ဖော်ခြင်းဖြင့် ထုတ်လုပ်သူများသည် ၎င်းတို့၏ဖောက်သည်များ၏လိုအပ်ချက်များနှင့်ကိုက်ညီသည့် အရည်အသွေးမြင့်ပလပ်စတစ်ထုတ်ကုန်များကို ထုတ်လုပ်နိုင်သည်။
ဆေးထိုးပုံသွင်းခြင်းတွင် အဖြစ်များသော ချို့ယွင်းချက်တို့ကို မည်သို့တားဆီးရမည်နည်း
ဆေးထိုးပုံသွင်းခြင်းသည် ရှုပ်ထွေးသောလုပ်ငန်းစဉ်တစ်ခုဖြစ်ပြီး မှားယွင်းစွာလုပ်ဆောင်ပါက ချို့ယွင်းချက်များဖြစ်ပေါ်နိုင်သည်။ ဤသည်မှာ ဆေးထိုးပုံသွင်းခြင်းတွင် ဖြစ်လေ့ရှိသောချို့ယွင်းချက်အချို့နှင့် ၎င်းတို့ကို မည်သို့ကာကွယ်ရမည်နည်း။
- Sink marks များသည် ထုတ်ကုန်၏မျက်နှာပြင်ပေါ်ရှိ စိတ်ဓာတ်ကျခြင်း သို့မဟုတ် အစွန်းအထင်းများဖြစ်သည်။ ၎င်းတို့သည် မညီမညာ အအေးခံခြင်း သို့မဟုတ် ထုပ်ပိုးမှုဖိအား မလုံလောက်ခြင်းကြောင့် ဖြစ်ပေါ်လာခြင်းဖြစ်သည်။ မှိုဒီဇိုင်းတွင် နံရံအထူနှင့် စုပ်ခွက်အမှတ်အသားများကို ကာကွယ်ရန် လုံလောက်သော မူကြမ်းထောင့်များ ပါဝင်ကြောင်း သေချာပါစေ။ ထုပ်ပိုးမှုဖိအားနှင့် အအေးခံချိန်ကို ချိန်ညှိခြင်းသည် နစ်မြုပ်မှုအမှတ်အသားများကို တားဆီးပေးနိုင်သည်။
- Warpage- Warpage သည် ပုံစံခွက်မှဖယ်ရှားပြီးနောက် ထုတ်ကုန်၏ပုံပျက်ခြင်းဖြစ်ပါသည်။ ၎င်းသည် ထုတ်ကုန်အတွင်းရှိ မညီမညာ အအေးခံခြင်း သို့မဟုတ် အတွင်းစိတ်ဖိစီးမှုများကြောင့် ဖြစ်ပေါ်လာခြင်းဖြစ်သည်။ warp ဖြစ်ခြင်းကို ကာကွယ်ရန်၊ မှိုဒီဇိုင်းတွင် တူညီသော နံရံအထူနှင့် အအေးခံချိန် လုံလောက်စွာ ပါဝင်ကြောင်း သေချာပါစေ။ ဖိစီးမှုအမှတ်များကို ဖန်တီးပေးနိုင်သည့် ထုတ်ကုန်ဂျီသြမေတြီတွင် ချွန်ထက်သောထောင့်များ သို့မဟုတ် ရုတ်တရက်ပြောင်းလဲမှုများကို ရှောင်ကြဉ်ပါ။
- ဖလက်ရှ်- ဖလက်ရှ်သည် ပုံမှန်အားဖြင့် မှို၏အစွန်းတစ်ဝိုက်တွင် ဖြစ်ပေါ်လေ့ရှိသော ထုတ်ကုန်နယ်နိမိတ်များထက် ကျော်လွန်သော ပလပ်စတစ်ပိုလျှံသည်။ ဆေးထိုးဖိအားအလွန်အကျွံ၊ ကုပ်ဆွဲအားမလုံလောက်ခြင်း၊ သို့မဟုတ် ပွန်းပဲ့သောမှိုကြောင့်ဖြစ်ရသည်။ ဖလက်ရှ်မီးကို ကာကွယ်ရန်၊ ဆေးထိုးဖိအားနှင့် ကုပ်ကြိုးကို ချိန်ညှိကာ ဝတ်ဆင်မှု လက္ခဏာများအတွက် မှိုကို ပုံမှန်စစ်ဆေးပါ။
- တိုတိုရိုက်ချက်- မှိုသည် ပလတ်စတစ်ဖြင့် တစ်စိတ်တစ်ပိုင်း ပြည့်သွားသောအခါ တိုတောင်းသောရိုက်ချက်များ ဖြစ်ပေါ်သည်။ ၎င်းသည် ဆေးထိုးဖိအား သို့မဟုတ် အပူချိန် မလုံလောက်ခြင်းကြောင့် သို့မဟုတ် ပိတ်ဆို့ထားသော သို့မဟုတ် ကန့်သတ်ထားသော စီးဆင်းမှုလမ်းကြောင်းကြောင့် ဖြစ်နိုင်သည်။ တိုတောင်းသောရိုက်ချက်များကို ကာကွယ်ရန်၊ ဆေးထိုးသည့်ဖိအားနှင့် အပူချိန်ကို ချိန်ညှိကာ စီးဆင်းမှုလမ်းကြောင်းကို ရှင်းလင်းပြီး အတားအဆီးမရှိ သေချာစေရန်။
- မီးလောင်ဒဏ်ရာများ- အပူလွန်ကဲခြင်း သို့မဟုတ် မှိုအတွင်း ပွတ်တိုက်မှုလွန်ကဲခြင်းကြောင့် ဖြစ်ပေါ်လာသော ထုတ်ကုန်၏ မျက်နှာပြင်ပေါ်ရှိ မည်းမှောင်သောအရောင်များ လောင်ကျွမ်းခြင်းအမှတ်အသားများ။ မီးလောင်ဒဏ်ရာများကို ကာကွယ်ရန်၊ မှိုကို လုံလောက်စွာ အအေးခံပြီး ချောဆီသေချာစေရန်၊ ဆေးထိုးနှုန်းနှင့် ဖိအားကို လိုအပ်သလို ချိန်ညှိပါ။
- ပျက်ပြယ်ခြင်းနှင့် ပူဖောင်းများ- အပျက်အစီးများနှင့် ပူဖောင်းများသည် ပစ္စည်းပျောက်နေသော ပစ္စည်း သို့မဟုတ် လေအိတ်များပါရှိသော ထုတ်ကုန်နေရာများဖြစ်သည်။ ၎င်းတို့သည် မှိုထဲတွင် ပိတ်မိနေသော လေ သို့မဟုတ် ဓာတ်ငွေ့ သို့မဟုတ် ပစ္စည်း မလုံလောက်ခြင်းကြောင့် ဖြစ်ပေါ်လာခြင်းဖြစ်သည်။ အပျက်အစီးများနှင့် ပူဖောင်းများကို ကာကွယ်ရန်၊ မှိုကို မှန်ကန်စွာ လေ၀င်လေထွက်ရှိစေရန်နှင့် ဆေးထိုးသည့်အမြန်နှုန်းနှင့် ဖိအားများသည် တူညီသောပစ္စည်းစီးဆင်းမှုကို သေချာစေရန် လုံလောက်ကြောင်း သေချာပါစေ။
ဆေးထိုးပုံသွင်းကိရိယာများအတွက် ပြုပြင်ထိန်းသိမ်းမှု အကြံပြုချက်များ
ဆေးထိုးပုံသွင်းကိရိယာသည် ထုတ်လုပ်သူများအတွက် သိသာထင်ရှားသော ရင်းနှီးမြှုပ်နှံမှုတစ်ခုဖြစ်ပြီး အကောင်းဆုံးစွမ်းဆောင်ရည်နှင့် အသက်ရှည်စေရန်အတွက် သင့်လျော်သော ပြုပြင်ထိန်းသိမ်းမှုသည် မရှိမဖြစ်လိုအပ်ပါသည်။ ဆေးထိုးပုံသွင်းကိရိယာများအတွက် ပြုပြင်ထိန်းသိမ်းမှုဆိုင်ရာ အကြံပြုချက်အချို့မှာ အောက်ပါအတိုင်းဖြစ်သည်။
- ပုံမှန်စစ်ဆေးမှုများလုပ်ဆောင်ပါ- ဝတ်ဆင်ခြင်းနှင့် မျက်ရည်ယိုခြင်း၊ ပျက်စီးခြင်း သို့မဟုတ် အခြားပြဿနာများကို သိရှိနိုင်စေရန် စက်ပစ္စည်းအား ပုံမှန်စစ်ဆေးပါ။ ဟိုက်ဒရောလစ်ပိုက်များ၊ ဖျံများနှင့် အခြားအရေးကြီးသော အစိတ်အပိုင်းများကို အခြေအနေကောင်းမွန်ကြောင်း သေချာစေရန် စစ်ဆေးပါ။
- စက်ပစ္စည်းများကို သန့်စင်ပြီး ချောဆီပေးပါ။- သံချေးတက်ခြင်းနှင့် ဟောင်းနွမ်းခြင်းမှ ကာကွယ်ရန် စက်ကို ပုံမှန်သန့်ရှင်းရေးလုပ်ပြီး ချောဆီပေးပါ။ အကြံပြုထားသော သန့်ရှင်းရေးနှင့် ချောဆီ ထုတ်ကုန်များကို အသုံးပြုကာ ထုတ်လုပ်သူ၏ ညွှန်ကြားချက်များကို လိုက်နာပါ။
- ဟိုက်ဒရောလစ်ဆီအား စောင့်ကြည့်ထိန်းသိမ်းပါ- ၎င်းကို သန့်ရှင်းပြီး မှန်ကန်သော viscosity ရှိစေရန် ပုံမှန်စစ်ဆေးပါ။ ဆီကို လိုအပ်သလို ပြောင်းလဲပြီး အကြံပြုထားသော ဆီအမျိုးအစားကို အသုံးပြုပါ။
- အပူပေးကြိုးများကို ထိန်းသိမ်းပါ- ၎င်းတို့ကို အခြေအနေကောင်းမွန်ပြီး မှန်ကန်စွာ အပူပေးနိုင်ရန် ၎င်းတို့ကို ပုံမှန်စစ်ဆေးပါ။ ပျက်စီးနေသော သို့မဟုတ် ဟောင်းနွမ်းနေသော အပူပေးကြိုးများကို ချက်ချင်း အစားထိုးပါ။
- အအေးခံစနစ်ကို စောင့်ကြည့်ပြီး ထိန်းသိမ်းပါ- အပူလွန်ကဲခြင်းနှင့် စစ်ပွဲဖြစ်ခြင်းတို့ကို ကာကွယ်ပေးသောကြောင့် ဆေးထိုးပုံသွင်းခြင်းအတွက် အရေးကြီးပါသည်။ အအေးပေးစနစ်ကို မှန်ကန်စွာလုပ်ဆောင်နိုင်စေရန်အတွက် ပုံမှန်စစ်ဆေးပြီး အအေးခံလမ်းကြောင်းများကို လိုအပ်သလို သန့်ရှင်းပေးပါ။
- ရထားအော်ပရေတာများ- ပျက်စီးဆုံးရှုံးမှုကိုကာကွယ်ရန်နှင့် အကောင်းဆုံးစွမ်းဆောင်ရည်ကိုသေချာစေရန်အတွက် သင့်လျော်သော စက်ကိရိယာများလည်ပတ်မှုနှင့် ပြုပြင်ထိန်းသိမ်းမှုလုပ်ငန်းစဉ်များကို လေ့ကျင့်ပေးပါသည်။
- ပုံမှန်ပြုပြင်ထိန်းသိမ်းမှုကို အချိန်ဇယားဆွဲပါ- ပြုပြင်ထိန်းသိမ်းမှုအချိန်ဇယားကို ချမှတ်ပြီး ၎င်းကို လိုက်နာပါ။ ချောဆီ နှင့် ဆီ အပြောင်းအလဲများ ကဲ့သို့သော ပုံမှန် ပြုပြင်ထိန်းသိမ်းမှု လုပ်ငန်းများကို အချိန်ဇယားဆွဲပြီး ပြုပြင်ထိန်းသိမ်းမှု လုပ်ဆောင်ချက်အားလုံးကို မှတ်တမ်းတင်ပါ။
- အပိုပစ္စည်းများကို လက်ထဲတွင်ထားရှိပါ- ဟိုက်ဒရောလစ်ပိုက်များ၊ တံဆိပ်များနှင့် အပူပေးကြိုးများကဲ့သို့သော အပိုပစ္စည်းများကို ပေးပါ။ ၎င်းသည် ပျက်စီးနေသော သို့မဟုတ် ဟောင်းနွမ်းနေသော အစိတ်အပိုင်းများကို လျင်မြန်စွာ အစားထိုးနိုင်ပြီး စက်ရပ်ချိန်ကို လျှော့ချနိုင်မည်ဖြစ်သည်။
ဆေးထိုးပုံသွင်းကိရိယာ၏ မှန်ကန်သောထိန်းသိမ်းမှုသည် ထိရောက်စွာလည်ပတ်နိုင်စေရန်၊ အရည်အသွေးမြင့်ထုတ်ကုန်များထုတ်လုပ်ရန်နှင့် တာရှည်သက်တမ်းရှိစေရန် သေချာစေရန်အတွက် မရှိမဖြစ်လိုအပ်ပါသည်။ ဤပြုပြင်ထိန်းသိမ်းမှု အကြံပြုချက်များကို လိုက်နာခြင်းဖြင့် ထုတ်လုပ်သူများသည် ၎င်းတို့၏စက်ပစ္စည်းများကို ထိပ်တန်းအခြေအနေတွင် ထိန်းသိမ်းနိုင်ပြီး စက်ရပ်ချိန်နှင့် ပြုပြင်စရိတ်များကို လျှော့ချနိုင်သည်။
သင့်လျော်သော ဆေးထိုးအပ်ထုတ်လုပ်သူအား မည်သို့ရွေးချယ်မည်နည်း။
သင့်လျော်သော ဆေးထိုးပုံသွင်းထုတ်လုပ်သူအား ရွေးချယ်ခြင်းသည် သင့်ထုတ်ကုန်များ၏ အရည်အသွေးနှင့် ကုန်ကျစရိတ်ကို သိသိသာသာ သက်ရောက်မှုရှိစေမည့် အရေးကြီးသော ဆုံးဖြတ်ချက်တစ်ခုဖြစ်သည်။ ဆေးထိုးပုံသွင်းထုတ်လုပ်သူအား ရွေးချယ်ရာတွင် ထည့်သွင်းစဉ်းစားရမည့်အချက်အချို့မှာ အောက်ပါအတိုင်းဖြစ်သည်။
- အတွေ့အကြုံနှင့် ကျွမ်းကျင်မှု- ဆေးထိုးပုံသွင်းခြင်းတွင် ကျယ်ပြန့်သော အတွေ့အကြုံနှင့် ကျွမ်းကျင်မှုရှိသော ထုတ်လုပ်သူအား ရှာဖွေပါ။ ၎င်းတို့၏ ထုတ်လုပ်မှု လုပ်ငန်းစဉ်များ၊ အရည်အသွေး ထိန်းချုပ်မှု အစီအမံများနှင့် လက်မှတ်များအကြောင်း မေးမြန်းပါ။
- နည်းပညာနှင့် စက်ပစ္စည်း- ခေတ်မီနည်းပညာနှင့် စက်ကိရိယာများကို အသုံးပြုသည့် ထုတ်လုပ်သူအား ရှာဖွေပါ။ ၎င်းသည် တသမတ်တည်း အရည်အသွေး၊ တိုတောင်းသော ပို့ဆောင်ချိန်နှင့် ကုန်ကျစရိတ်သက်သာမှုကို သေချာစေရန် ကူညီပေးနိုင်ပါသည်။
- ပစ္စည်းများနှင့် စွမ်းဆောင်ရည်များ- ထုတ်လုပ်သူနှင့် လုပ်ဆောင်နိုင်သော ပစ္စည်းများ အမျိုးအစားများနှင့် ၎င်းတို့၏ စွမ်းရည်များကို သုံးသပ်ပါ။ အထူးပြုပစ္စည်းများ အပါအဝင် ကျယ်ပြန့်သော ပစ္စည်းများကို ကိုင်တွယ်နိုင်သော ထုတ်လုပ်သူအား ရှာဖွေကာ ထုတ်ကုန်အရွယ်အစားနှင့် ပုံသဏ္ဍာန်အမျိုးမျိုးကို ထုတ်လုပ်နိုင်သည်။
- အရည်အသွေးထိန်းချုပ်မှုအစီအမံများ- အရည်အသွေးထိန်းချုပ်မှုအပေါ် အလေးပေးသော ထုတ်လုပ်သူအား ရှာဖွေပါ။ စစ်ဆေးခြင်းနှင့် စမ်းသပ်ခြင်းလုပ်ထုံးလုပ်နည်းများကဲ့သို့သော ၎င်းတို့၏ အရည်အသွေးထိန်းချုပ်မှုအစီအမံများနှင့် ၎င်းတို့တွင်ရှိသည့် အသိအမှတ်ပြုလက်မှတ်များအကြောင်း မေးမြန်းပါ။
- ဖောက်သည်ဝန်ဆောင်မှု- အလွန်ကောင်းမွန်သော ဖောက်သည်ဝန်ဆောင်မှုပေးသည့် ထုတ်လုပ်သူအား ရှာဖွေပါ။ သင်၏ သီးခြားလိုအပ်ချက်များကို ပြည့်မီစေရန် တုံ့ပြန်မှု၊ ဆက်သွယ်မှုနှင့် လက်တွဲလုပ်ဆောင်လိုစိတ်တို့ကို ထည့်သွင်းစဉ်းစားပါ။
- ကုန်ကျစရိတ်နှင့် ပို့ဆောင်ချိန်- သင့်ပရောဂျက်အတွက် ထုတ်လုပ်သူ၏ကုန်ကျစရိတ်နှင့် ပို့ဆောင်ချိန်ကို ထည့်သွင်းစဉ်းစားပါ။ သင့်လိုအပ်ချက်များနှင့် ကိုက်ညီသော စျေးနှုန်းအပြိုင်အဆိုင်နှင့် လက်တွေ့ကျသော အချိန်များကို ပေးဆောင်သည့် ထုတ်လုပ်သူအား ရှာဖွေပါ။
- အကိုးအကားများနှင့် သုံးသပ်ချက်များ- ကိုးကားချက်တောင်းခံပြီး ထုတ်လုပ်သူ၏ အွန်လိုင်းသုံးသပ်ချက်များကို စစ်ဆေးပါ။ ၎င်းသည် သင့်အား ၎င်းတို့၏ဂုဏ်သတင်းနှင့် အခြားဖောက်သည်များ၏ အတွေ့အကြုံများကို ပိုမိုသိရှိနားလည်စေရန် ကူညီပေးနိုင်ပါသည်။
ဤအချက်များကို ထည့်သွင်းစဉ်းစားပြီး စေ့စေ့စပ်စပ် သုတေသနပြုလုပ်ခြင်းဖြင့် သင့်ပရောဂျက်အတွက် သင့်လျော်သော ဆေးထိုးပုံသွင်းထုတ်လုပ်သူကို ရွေးချယ်နိုင်ပါသည်။ မှန်ကန်သောအတွေ့အကြုံ၊ စွမ်းရည်များနှင့် အရည်အသွေးအပေါ် ကတိကဝတ်ရှိသည့် ကျော်ကြားသောထုတ်လုပ်သူသည် သင့်ထုတ်ကုန်များကို ထိရောက်စွာ၊ ကုန်ကျစရိတ်သက်သာစွာဖြင့် ထုတ်လုပ်ပြီး သင့်တိကျသောသတ်မှတ်ချက်များအတိုင်း သေချာစေရန် ကူညီပေးနိုင်ပါသည်။
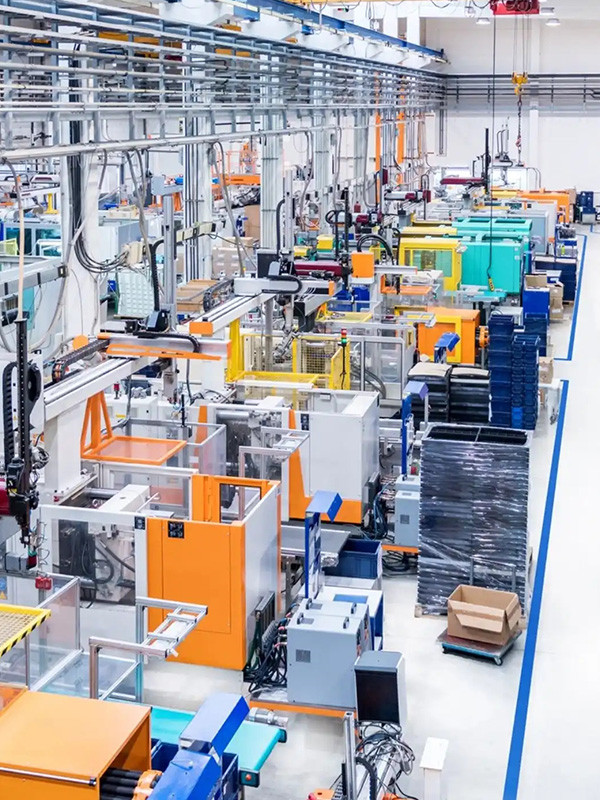
စိတ်ကြိုက် ပလပ်စတစ်ဆေးထိုးခြင်းအတွက် ကုန်ကျစရိတ် ထည့်သွင်းစဉ်းစားခြင်း။
စိတ်ကြိုက်ပလပ်စတစ်ဆေးထိုးပုံသွင်းခြင်းသည် ရှုပ်ထွေးပြီး အရည်အသွေးမြင့် အစိတ်အပိုင်းများကို ထုတ်လုပ်ပေးနိုင်သော စွယ်စုံရထုတ်လုပ်ရေးလုပ်ငန်းစဉ်တစ်ခုဖြစ်သည်။ သို့သော်၊ ကုန်ကျစရိတ်ထည့်သွင်းစဉ်းစားခြင်းသည် ဤကုန်ထုတ်လုပ်မှုလုပ်ငန်းစဉ်ကို အသုံးပြုရာတွင် အရေးကြီးသောအချက်ဖြစ်သည်။ ဤသည်မှာ စိတ်ကြိုက်ပလပ်စတစ်ဆေးထိုးခြင်းအတွက် အဓိကကျသော ကုန်ကျစရိတ် ထည့်သွင်းစဉ်းစားမှုအချို့ဖြစ်သည်။
- ပစ္စည်းကုန်ကျစရိတ်- ဆေးထိုးပုံသွင်းခြင်းလုပ်ငန်းစဉ်တွင် အသုံးပြုသည့် ပစ္စည်းအမျိုးအစားနှင့် အရေအတွက်သည် ဈေးနှုန်းအပေါ် သက်ရောက်မှုရှိမည်ဖြစ်သည်။ စွမ်းဆောင်ရည်မြင့် အင်ဂျင်နီယာ ပလတ်စတစ်ကဲ့သို့သော အချို့သောပစ္စည်းများသည် အခြားပစ္စည်းများထက် ဈေးပိုကြီးသည်။ ပစ္စည်းများ၏ ကုန်ကျစရိတ်သည် ထောက်ပံ့ရေးကွင်းဆက်ပြတ်တောက်မှု၊ စျေးကွက်ဝယ်လိုအားနှင့် ဈေးနှုန်းအတက်အကျများကြောင့်လည်း ထိခိုက်နိုင်သည်။
- ကိရိယာတန်ဆာပလာကုန်ကျစရိတ်- ကိရိယာတန်ဆာပလာကုန်ကျစရိတ် သို့မဟုတ် အစိတ်အပိုင်းများထုတ်လုပ်ရန်အသုံးပြုသည့်မှိုများသည် စိတ်ကြိုက်ပလပ်စတစ်ဆေးထိုးခြင်းတွင် သိသိသာသာကုန်ကျစရိတ်ဖြစ်သည်။ အစိတ်အပိုင်း၏ ရှုပ်ထွေးမှု၊ မှိုအတွင်းရှိ အပေါက်အရေအတွက်နှင့် မှိုကိုဖန်တီးရာတွင် အသုံးပြုသည့် ပစ္စည်းအားလုံးသည် ကိရိယာကုန်ကျစရိတ်အပေါ် သက်ရောက်မှုရှိမည်ဖြစ်သည်။ ကိရိယာတန်ဆာပလာသည် စျေးကြီးသော်လည်း ထုတ်လုပ်မှုစွမ်းဆောင်ရည်ကို မြှင့်တင်ခြင်းဖြင့် အချိန်ကြာလာသည်နှင့်အမျှ ယူနစ်ကုန်ကျစရိတ်ကို သက်သာစေနိုင်သည်။
- ထုတ်လုပ်မှုပမာဏ- ထုတ်လုပ်သည့်အစိတ်အပိုင်းများ၏ ထုထည်ပမာဏသည် ဆေးထိုးပုံသွင်းခြင်းကုန်ကျစရိတ်အပေါ် သက်ရောက်မှုရှိမည်ဖြစ်သည်။ ထုထည်မြင့်မားသောထုတ်လုပ်မှုသည် ယူနစ်ကုန်ကျစရိတ်များကို လျှော့ချနိုင်သော်လည်း ထုထည်နည်းသောထုတ်လုပ်မှုသည် ကိရိယာတန်ဆာပလာနှင့် တပ်ဆင်ချိန်ပိုမိုလိုအပ်ခြင်းကြောင့် ယူနစ်ကုန်ကျစရိတ်ပိုမိုမြင့်မားနိုင်သည်။
- အလုပ်သမားကုန်ကျစရိတ်- လုပ်သားစရိတ်များသည် ဆေးထိုးပုံသွင်းခြင်းတွင် သိသာထင်ရှားသောအချက်ဖြစ်ပြီး အထူးသဖြင့် လက်လုပ်လက်စားလုပ်အားပိုမိုလိုအပ်သော ပိုမိုရှုပ်ထွေးသော အစိတ်အပိုင်းများအတွက် အလုပ်သမားစရိတ်များဖြစ်သည်။ အော်ပရေတာများ၏ ကျွမ်းကျင်မှုအဆင့်နှင့် အစိတ်အပိုင်း၏ ရှုပ်ထွေးမှုသည် ပို့ဆောင်မှုကုန်ကျစရိတ်အပေါ် သက်ရောက်မှုရှိမည်ဖြစ်သည်။
- အရည်အသွေးထိန်းချုပ်မှု ကုန်ကျစရိတ်- အစိတ်အပိုင်းများ၏ ခိုင်မာမှုကိုသေချာစေရန် အရည်အသွေးထိန်းချုပ်မှုကို ထိန်းသိမ်းခြင်းသည် မရှိမဖြစ်လိုအပ်ပါသည်။ အရည်အသွေးထိန်းချုပ်မှု စျေးနှုန်းတွင် စစ်ဆေးရေးကိရိယာများ၊ စမ်းသပ်ခြင်းနှင့် အလုပ်သမားတို့ ပါဝင်နိုင်သည်။
- ပို့ဆောင်ခ- အစိတ်အပိုင်းများကို ဝယ်ယူသူ သို့မဟုတ် အခြားနေရာများသို့ ပို့ဆောင်ခြင်းသည် အထူးသဖြင့် ကြီးမားသော သို့မဟုတ် လေးလံသောအသေးစိတ်အချက်အလက်များအတွက် သိသာထင်ရှားသောကုန်ကျစရိတ်တစ်ခုဖြစ်သည်။
ထုတ်လုပ်သူများသည် ဤကုန်ကျစရိတ်အချက်များကို ထည့်သွင်းစဉ်းစားပြီး ဆေးထိုးပုံသွင်းခြင်းလုပ်ငန်းစဉ်ကို အကောင်းဆုံးဖြစ်အောင်ပြုလုပ်ခြင်းဖြင့် အရည်အသွေးမြင့် အစိတ်အပိုင်းများကို ကုန်ကျစရိတ်သက်သာစွာဖြင့် ထုတ်လုပ်နိုင်သည်။ ပစ္စည်း စွန့်ပစ်ပစ္စည်း လျှော့ချခြင်း၊ ထုတ်လုပ်မှု ထိရောက်မှု တိုးမြင့်လာပြီး စနစ်ထည့်သွင်းခြင်းနှင့် ပြောင်းလဲချိန်များကို လျှော့ချခြင်းဖြင့် ၎င်းကို အောင်မြင်နိုင်သည်။ အတွေ့အကြုံရှိပြီး တတ်ကျွမ်းနားလည်သော ဆေးထိုးပုံသွင်းထုတ်လုပ်သူနှင့် အလုပ်လုပ်ခြင်းသည် လုပ်ငန်းစဉ်ကို အကောင်းဆုံးဖြစ်အောင် လုပ်ပြီး ကုန်ကျစရိတ်ကို လျှော့ချရာတွင်လည်း ကူညီပေးနိုင်ပါသည်။
ဆေးထိုးပုံသွင်းနည်းပညာတွင် ခေတ်ရေစီးကြောင်းနှင့် ဆန်းသစ်တီထွင်မှုများ
ဆေးထိုးပုံသွင်းခြင်းနည်းပညာသည် နှစ်ပေါင်းများစွာကြာခဲ့ပြီဖြစ်သော်လည်း ဤကုန်ထုတ်လုပ်မှုလုပ်ငန်းစဉ်၏အနာဂတ်ကိုပုံဖော်သည့် ဆန်းသစ်တီထွင်မှုများနှင့် ခေတ်ရေစီးကြောင်းများစွာ ရှိပါသေးသည်။ ဤသည်မှာ ဆေးထိုးပုံသွင်းနည်းပညာတွင် ထိပ်တန်းခေတ်ရေစီးကြောင်းနှင့် ဆန်းသစ်တီထွင်မှုအချို့ဖြစ်သည်။
- 3D ပုံနှိပ်ခြင်းနှင့် ပေါင်းထည့်ခြင်း ထုတ်လုပ်မှု- 3D ပုံနှိပ်ခြင်းနှင့် ပေါင်းထည့်ခြင်း ထုတ်လုပ်ခြင်းတို့သည် ဆေးထိုးခြင်းလုပ်ငန်းတွင် လူကြိုက်များလာသည်။ ဤနည်းပညာသည် ရိုးရာဆေးထိုးပုံသွင်းခြင်းဖြင့် အောင်မြင်ရန်ခက်ခဲသော သို့မဟုတ် မဖြစ်နိုင်သော ရှုပ်ထွေးသောပုံသဏ္ဍာန်များနှင့် ဂျီသြမေတြီများကို ဖန်တီးနိုင်စေပါသည်။
- ဘက်စုံဆေးထိုးပုံသွင်းခြင်း- ဘက်စုံဆေးထိုးပုံသွင်းခြင်း သည် တစ်ချက်တည်းတွင် ပစ္စည်းမျိုးစုံ သို့မဟုတ် အရောင်မျိုးစုံဖြင့် အစိတ်အပိုင်းများကို ဖန်တီးနိုင်စေပါသည်။ ဤလုပ်ငန်းစဉ်သည် ထုတ်လုပ်မှုအချိန်နှင့် ကုန်ကျစရိတ်များကို လျှော့ချနိုင်ပြီး ထူးခြားသော ဂုဏ်သတ္တိများနှင့် အသွင်အပြင်များဖြင့် လုပ်ဆောင်ချက်များကို ဖန်တီးနိုင်သည်။
- အလိုအလျောက်စနစ်နှင့်စက်မှုလုပ်ငန်း 4.0- အော်တိုမက်တစ်နှင့် စက်မှုလုပ်ငန်း 4.0 နည်းပညာများဖြစ်သည့် IoT အာရုံခံကိရိယာများနှင့် စက်ရုပ်များကို ဆေးထိုးပုံသွင်းစက်များနှင့် လုပ်ငန်းစဉ်များတွင် ပေါင်းစပ်ထားသည်။ ၎င်းသည် ထုတ်လုပ်မှု စွမ်းဆောင်ရည်ကို မြှင့်တင်နိုင်ပြီး အလုပ်သမား ကုန်ကျစရိတ်များကို လျှော့ချနိုင်ကာ အရည်အသွေး ထိန်းချုပ်မှုကို မြှင့်တင်နိုင်သည်။
- ရေရှည်တည်တံ့နိုင်သော ပစ္စည်းများနှင့် လုပ်ငန်းစဉ်များ- ကုမ္ပဏီများသည် ၎င်းတို့၏ ပတ်ဝန်းကျင်ဆိုင်ရာ ထိခိုက်မှုကို လျှော့ချရန် ကြိုးပမ်းလာသည်နှင့်အမျှ ရေရှည်တည်တံ့သော ပစ္စည်းများနှင့် နည်းလမ်းများသည် ဆေးထိုးခြင်းလုပ်ငန်းတွင် ပို၍အရေးကြီးလာသည်။ ၎င်းတွင် စွန့်ပစ်ပစ္စည်းများနှင့် စွမ်းအင်သုံးစွဲမှု အနည်းဆုံးဖြစ်စေမည့် ဇီဝရုပ်ကြွင်း သို့မဟုတ် ပြန်လည်အသုံးပြုသည့် ပစ္စည်းများ အသုံးပြုခြင်းနှင့် လုပ်ငန်းစဉ်များ ပါဝင်သည်။
- စမတ်ကျသောထုတ်လုပ်မှုနှင့် ကြိုတင်ပြင်ဆင်ထိန်းသိမ်းမှု- စက်သင်ယူခြင်းနှင့် ကြိုတင်ပြင်ဆင်ထိန်းသိမ်းခြင်းကဲ့သို့သော စမတ်ထုတ်လုပ်မှုနည်းပညာများကို ဆေးထိုးပုံသွင်းခြင်းလုပ်ငန်းစဉ်များကို အကောင်းဆုံးဖြစ်အောင်နှင့် စက်ရပ်ချိန်လျှော့ချရန်အတွက် အသုံးပြုလျက်ရှိသည်။ ၎င်းသည် အလုံးစုံစွမ်းဆောင်ရည်ကို တိုးတက်စေပြီး ပြုပြင်ထိန်းသိမ်းမှုကုန်ကျစရိတ်များကို လျှော့ချနိုင်သည်။
- စွမ်းဆောင်ရည်မြင့်မားသောပစ္စည်းများ- စွမ်းဆောင်ရည်မြင့်သောပစ္စည်းများ၊ ဆေးထိုးပုံသွင်းခြင်းအတွက် စွမ်းဆောင်ရည်ကောင်းမွန်သောပစ္စည်းများ၊ တာရှည်ခံမှုနှင့် အပူဒဏ်ခံနိုင်ရည်ရှိသော ပစ္စည်းများအပါအဝင် အသစ်ထုတ်လုပ်ထားပါသည်။ ဤပစ္စည်းများကို မော်တော်ယာဥ် အစိတ်အပိုင်းများမှ ဆေးဘက်ဆိုင်ရာ ကိရိယာများအထိ အမျိုးမျိုးသော အပလီကေးရှင်းများတွင် အသုံးပြုနိုင်သည်။
ဤခေတ်ရေစီးကြောင်းများနှင့် ဆန်းသစ်တီထွင်မှုများအပေါ် ခေတ်မီနေခြင်းဖြင့်၊ ဆေးထိုးပုံသွင်းထုတ်လုပ်သူများသည် အပြိုင်အဆိုင်ရှိနေနိုင်ပြီး ၎င်းတို့၏ဖောက်သည်များအတွက် အရည်အသွေးမြင့် အစိတ်အပိုင်းများကို ဆက်လက်ပံ့ပိုးပေးနိုင်ပါသည်။ နည်းပညာသစ်များနှင့် ပစ္စည်းများ ဖွံ့ဖြိုးတိုးတက်လာသည်နှင့်အမျှ၊ ဆေးထိုးပုံသွင်းလုပ်ငန်းသည် စားသုံးသူများနှင့် စီးပွားရေးလုပ်ငန်းများ၏ ပြောင်းလဲလာသော လိုအပ်ချက်များကို ဖြည့်ဆည်းပေးနိုင်ရန် ဆက်လက်၍ တိုးတက်ပြောင်းလဲကာ လိုက်လျောညီထွေဖြစ်အောင် လုပ်ဆောင်သွားမည်ဖြစ်ပါသည်။
ဆေးထိုးပုံသွင်းခြင်းတွင် ရေရှည်တည်တံ့မှု- စွန့်ပစ်ပစ္စည်းနှင့် စွမ်းအင်သုံးစွဲမှုကို လျှော့ချခြင်း။
ကုမ္ပဏီများသည် ၎င်းတို့၏ သဘာဝပတ်ဝန်းကျင်ဆိုင်ရာ ထိခိုက်မှုကို လျှော့ချရန်နှင့် တိုးပွားလာသော eco-friendly ထုတ်ကုန်များ၏ လိုအပ်ချက်ကို ဖြည့်ဆည်းရန် ကြိုးပမ်းနေသောကြောင့် ဆေးထိုးပုံသွင်းခြင်းလုပ်ငန်းတွင် ရေရှည်တည်တံ့မှုသည် ပို၍အရေးကြီးလာသည်။ ဆေးထိုးပုံသွင်းထုတ်လုပ်သူများသည် အမှိုက်နှင့် စွမ်းအင်သုံးစွဲမှုကို လျှော့ချနိုင်သည့် နည်းလမ်းအချို့ဖြစ်သည်။
- ရေရှည်တည်တံ့ခိုင်မြဲသောပစ္စည်းများကို အသုံးပြုပါ- ပစ္စည်းရွေးချယ်မှုသည် ရေရှည်တည်တံ့မှုအတွက် အရေးကြီးသောအချက်ဖြစ်သည်။ ဆေးထိုးပုံသွင်းထုတ်လုပ်သူများသည် သဘာဝပတ်ဝန်းကျင်ထိခိုက်မှုကို လျှော့ချရန်အတွက် ဇီဝရုပ်ပျက်ဆင်းပျက်နိုင်သော သို့မဟုတ် ပြန်လည်အသုံးပြုသည့်ပစ္စည်းများကို အသုံးပြုနိုင်သည်။ ဥပမာအားဖြင့် ဇီဝပျက်စီးနိုင်သော ပလတ်စတစ်များသည် အချိန်ကြာလာသည်နှင့်အမျှ သဘာဝအတိုင်း ပြိုကွဲနိုင်ပြီး အမှိုက်ပုံများတွင် အမှိုက်ပမာဏကို လျှော့ချနိုင်သည်။ စားသုံးပြီးသား ပလတ်စတစ်များ ကဲ့သို့သော ပြန်လည်အသုံးပြုသည့် ပစ္စည်းများသည် အမှိုက်နှင့် စွမ်းအင်သုံးစွဲမှုကို လျှော့ချရန် ကူညီပေးပါသည်။
- ပစ္စည်းစွန့်ပစ်ခြင်းကို လျှော့ချပါ- ဆေးထိုးပုံသွင်းထုတ်လုပ်သူများသည် အစိတ်အပိုင်းနှင့် မှို၏ဒီဇိုင်းကို ကောင်းမွန်အောင်ပြုလုပ်ခြင်းဖြင့် ပစ္စည်းစွန့်ပစ်ပစ္စည်းများကို လျှော့ချနိုင်သည်။ ၎င်းတွင် အသုံးပြုထားသော ပိုလျှံနေသော ပစ္စည်းပမာဏကို လျှော့ချခြင်း၊ မှိုအတွင်းရှိ အပေါက်အရေအတွက်ကို လျှော့ချခြင်းနှင့် အစိတ်အပိုင်း၏ အလုံးစုံအလေးချိန်ကို လျှော့ချခြင်းတို့ ပါဝင်သည်။ စွန့်ပစ်ပစ္စည်းများကို လျှော့ချခြင်းဖြင့် ထုတ်လုပ်သူသည် ပစ္စည်းကုန်ကျစရိတ်ကို သက်သာစေပြီး ၎င်းတို့၏ ပတ်ဝန်းကျင်ထိခိုက်မှုကို လျှော့ချနိုင်သည်။
- ထုတ်လုပ်မှုစွမ်းဆောင်ရည်ကို ပိုမိုကောင်းမွန်အောင်ပြုလုပ်ပါ- ဆေးထိုးပုံသွင်းထုတ်လုပ်သူများသည် စွမ်းအင်သုံးစွဲမှုကို လျှော့ချရန် ၎င်းတို့၏ ထုတ်လုပ်မှုလုပ်ငန်းစဉ်များကို အကောင်းဆုံးဖြစ်အောင် လုပ်ဆောင်နိုင်သည်။ ၎င်းတွင် ထိရောက်မှုမြင့်မားသော ဆေးထိုးပုံသွင်းစက်များကို အသုံးပြုခြင်း၊ ပုံသွင်းခြင်းလုပ်ငန်းစဉ်ဘောင်များကို ပိုမိုကောင်းမွန်အောင်ပြုလုပ်ခြင်းနှင့် စက်ရပ်ချိန်ကို လျှော့ချခြင်းတို့ ပါဝင်သည်။ စွမ်းအင်သုံးစွဲမှုကို လျှော့ချခြင်းဖြင့် ထုတ်လုပ်သူများသည် စွမ်းအင်ကုန်ကျစရိတ်ကို သက်သာစေပြီး ၎င်းတို့၏ ကာဗွန်ခြေရာကို လျှော့ချနိုင်သည်။
- ရေရှည်တည်တံ့သော အလေ့အကျင့်များကို အကောင်အထည်ဖော်ပါ- ဆေးထိုးပုံသွင်းထုတ်လုပ်သူများသည် ပြန်လည်အသုံးပြုခြင်းနှင့် စွန့်ပစ်ပစ္စည်းများလျှော့ချရေးအစီအစဉ်များ၊ ပြန်လည်ပြည့်ဖြိုးမြဲစွမ်းအင်ရင်းမြစ်များကို အသုံးပြုခြင်းနှင့် ၎င်းတို့၏ဝန်ထမ်းများနှင့် ပေးသွင်းသူများအကြား ရေရှည်တည်တံ့မှုကို မြှင့်တင်ခြင်းကဲ့သို့သော ၎င်းတို့၏လုပ်ငန်းဆောင်တာများတွင် ရေရှည်တည်တံ့သော အလေ့အကျင့်များကို အကောင်အထည်ဖော်နိုင်ပါသည်။ ထောက်ပံ့ရေးကွင်းဆက်တစ်လျှောက် ရေရှည်တည်တံ့သောအလေ့အကျင့်များကို မြှင့်တင်ခြင်းဖြင့် ထုတ်လုပ်သူများသည် ပိုမိုရေရှည်တည်တံ့သောစက်မှုလုပ်ငန်းတစ်ခုလုံးကို ဖန်တီးရန် ကူညီပေးနိုင်ပါသည်။
- ရေရှည်တည်တံ့သော ထုပ်ပိုးမှုကို အသုံးပြုပါ- နောက်ဆုံးတွင်၊ ဆေးထိုးပုံသွင်းထုတ်လုပ်သူများသည် စွန့်ပစ်ပစ္စည်းများနှင့် သဘာဝပတ်ဝန်းကျင်ဆိုင်ရာ ထိခိုက်မှုကို လျှော့ချရန်အတွက် ရေရှည်တည်တံ့သော ထုပ်ပိုးပစ္စည်းများနှင့် ဒီဇိုင်းများကို အသုံးပြုနိုင်သည်။ ၎င်းတွင် ဇီဝချေဖျက်နိုင်သော သို့မဟုတ် ပြန်လည်အသုံးပြုနိုင်သော ထုပ်ပိုးပစ္စည်းများကို အသုံးပြုခြင်း၊ ထုပ်ပိုးမှုစွန့်ပစ်ပစ္စည်းများကို လျှော့ချခြင်းနှင့် ပြန်လည်အသုံးပြုနိုင်သော သို့မဟုတ် ပြန်လည်ဖြည့်နိုင်သော ထုပ်ပိုးမှုပုံစံများ ပါဝင်သည်။
ဤရေရှည်တည်တံ့သော အလေ့အကျင့်များကို အကောင်အထည်ဖော်ခြင်းဖြင့် ဆေးထိုးပုံသွင်းထုတ်လုပ်သူများသည် ၎င်းတို့၏ ပတ်ဝန်းကျင်ဆိုင်ရာ ထိခိုက်မှုကို လျှော့ချနိုင်ပြီး ပိုမိုရေရှည်တည်တံ့သော လုပ်ငန်းတစ်ခုလုံးကို ဖန်တီးနိုင်သည်။ ရေရှည်တည်တံ့ခိုင်မြဲမှုသည် စားသုံးသူများနှင့် စီးပွားရေးလုပ်ငန်းများအတွက် ပို၍အရေးကြီးလာသည်နှင့်အမျှ၊ ရေရှည်တည်တံ့မှုကို ဦးစားပေးသော ဆေးထိုးထုတ်လုပ်သူများသည် တိုးပွားလာသော ဂေဟစနစ်သဟဇာတဖြစ်သော ထုတ်ကုန်များ၏ လိုအပ်ချက်ကို ဖြည့်ဆည်းရန်အတွက် ကောင်းမွန်သောအနေအထားတွင် ရှိနေမည်ဖြစ်ပါသည်။
စိတ်ကြိုက်ပလပ်စတစ်ဆေးထိုးပုံသွင်းခြင်းသည် အခြားကုန်ထုတ်လုပ်ငန်းစဉ်များနှင့် နှိုင်းယှဉ်ပါက မည်သို့နည်း
စိတ်ကြိုက်ပလပ်စတစ်ဆေးထိုးပုံသွင်းခြင်းသည် အရည်အသွေးမြင့်ပလပ်စတစ်အစိတ်အပိုင်းများကို အများအပြားထုတ်လုပ်ရန်အတွက် ရေပန်းစားသောထုတ်လုပ်မှုလုပ်ငန်းစဉ်တစ်ခုဖြစ်သည်။ သို့သော်လည်း ပလပ်စတစ် အစိတ်အပိုင်းများ ပြုလုပ်ရန် အခြားသော ထုတ်လုပ်မှု လုပ်ငန်းစဉ် အများအပြားကို အားသာချက်များနှင့် အားနည်းချက်များ အသီးသီး ပါရှိသည်။ ဤသည်မှာ စိတ်ကြိုက်ပလပ်စတစ်ဆေးထိုးခြင်း၏ အခြားထုတ်လုပ်မှုလုပ်ငန်းစဉ်များနှင့် နှိုင်းယှဉ်ချက်ဖြစ်သည်။
- 3D ပရင့်ထုတ်ခြင်း- 3D ပုံနှိပ်စက်သည် ရှုပ်ထွေးသောပုံသဏ္ဍာန်များနှင့် ဂျီသြမေတြီများကို ဖန်တီးနိုင်စေသည့် လျင်မြန်စွာကြီးထွားလာသော နည်းပညာတစ်ခုဖြစ်သည်။ 3D ပရင့်ထုတ်ခြင်းအား အသေးစားထုတ်လုပ်မှုအတွက်အသုံးပြုနိုင်သော်လည်း ဆေးထိုးပုံသွင်းခြင်းသည် ယေဘူယျအားဖြင့် ကုန်ကျစရိတ်သက်သာပြီး ကြီးမားသောအစိတ်အပိုင်းများထုတ်လုပ်ရန်အတွက် ဆေးထိုးပုံသွင်းခြင်းထက် ယေဘုယျအားဖြင့် သက်သာပါသည်။
- လေမှုတ်ပုံသွင်းခြင်း- လေမှုတ်ပုံသွင်းခြင်းသည် ပုလင်းများနှင့် ကွန်တိန်နာများကဲ့သို့ အခေါင်းပေါက်သော ပလပ်စတစ်အစိတ်အပိုင်းများကို ဖန်တီးသည့် ထုတ်လုပ်မှုလုပ်ငန်းစဉ်တစ်ခုဖြစ်သည်။ လေမှုတ်ပုံသွင်းခြင်းသည် များပြားသောအင်္ဂါရပ်များထုတ်လုပ်ရန်အတွက် သင့်လျော်သော်လည်း၊ ဆေးထိုးပုံသွင်းခြင်းထက် ယေဘုယျအားဖြင့် တိကျမှုနည်းပါးပြီး ပိုမိုရှုပ်ထွေးသောပုံသဏ္ဍာန်များနှင့် ဂျီသြမေတြီများဖန်တီးရန်အတွက် စံပြမဟုတ်ပေ။
- CNC Machining- CNC machining သည် ပစ္စည်းအစိုင်အခဲတုံးတစ်ခုမှ အစိတ်အပိုင်းများကို ဖြတ်တောက်ခြင်းနှင့် ပုံသွင်းခြင်းပါ၀င်သည့် နုတ်ထွက်ကုန်ထုတ်လုပ်မှုလုပ်ငန်းစဉ်တစ်ခုဖြစ်သည်။ CNC စက်သည် သေးငယ်သော တိကျမှုမြင့်မားသော အစိတ်အပိုင်းများကို ထုတ်လုပ်ရန်အတွက် သင့်လျော်သော်လည်း ၎င်းသည် ဆေးထိုးပုံသွင်းခြင်းကဲ့သို့ ယေဘုယျအားဖြင့် ကုန်ကျစရိတ်သက်သာခြင်း သို့မဟုတ် ထိရောက်မှုမရှိပါ။
- Rotational Molding- Rotational Molding သည် မှိုကို အပူပေးနေစဉ် ထောင့်မှန်နှစ်ချောင်း ပတ်ပတ်လည်တွင် မှိုကို လှည့်ပတ်ခြင်း ပါဝင်သည်။ လည်ပတ်ပုံသွင်းခြင်းသည် ရှုပ်ထွေးသောဂျီဩမေတြီများဖြင့် ကြီးမားသောအစိတ်အပိုင်းများကို ထုတ်လုပ်နိုင်သော်လည်း ဆေးထိုးပုံသွင်းခြင်းထက် ယေဘုယျအားဖြင့် တိကျမှုနည်းပါးပြီး သေးငယ်သောအစိတ်အပိုင်းများပြုလုပ်ရန် မသင့်လျော်ပါ။
- Thermoforming- သာမိုပုံစံပြုလုပ်ခြင်းဆိုသည်မှာ ပလပ်စတစ်စာရွက်ကို အပူပေးပြီးမှိုပေါ်တွင် ပုံသွင်းခြင်း ပါ၀င်သည့် ကုန်ထုတ်လုပ်ငန်းစဉ်တစ်ခုဖြစ်သည်။ Thermoforming သည် ရိုးရှင်းသော ဂျီသြမေတြီများဖြင့် ကြီးမားသော အစိတ်အပိုင်းများကို ထုတ်လုပ်နိုင်သော်လည်း ဆေးထိုးပုံသွင်းခြင်းထက် ယေဘုယျအားဖြင့် တိကျမှုနည်းပြီး ပိုမိုရှုပ်ထွေးသော ပုံသဏ္ဍာန်များနှင့် ဂျီသြမေတြီများကို ဖန်တီးရန်အတွက် မသင့်လျော်ပေ။
စိတ်ကြိုက်ပလပ်စတစ်ဆေးထိုးပုံသွင်းခြင်းသည် အရည်အသွေးမြင့်ပလပ်စတစ်အစိတ်အပိုင်းများကို အမြောက်အမြားထုတ်လုပ်ရန်အတွက် စွယ်စုံရနှင့် ကုန်ကျစရိတ်သက်သာသော ကုန်ထုတ်လုပ်မှုလုပ်ငန်းစဉ်တစ်ခုဖြစ်သည်။ အခြားကုန်ထုတ်လုပ်ငန်းစဉ်များသည် တိကျသောအသုံးချပရိုဂရမ်များ သို့မဟုတ် ထုတ်လုပ်မှုပမာဏအတွက် ပိုသင့်လျော်သော်လည်း၊ ဆေးထိုးပုံသွင်းခြင်းသည် ယေဘုယျအားဖြင့် ၎င်း၏မြန်နှုန်း၊ တိကျမှုနှင့် ကုန်ကျစရိတ်သက်သာမှုကြောင့် ထုတ်လုပ်သူအများအပြားအတွက် ဦးစားပေးရွေးချယ်မှုဖြစ်သည်။ အဆုံးစွန်အားဖြင့်၊ ထုတ်လုပ်မှုလုပ်ငန်းစဉ်ရွေးချယ်မှုသည် အစိတ်အပိုင်းဒီဇိုင်း၊ ထုတ်လုပ်မှုပမာဏနှင့် ဘတ်ဂျက်အပါအဝင် အမျိုးမျိုးသောအချက်များပေါ်တွင် မူတည်မည်ဖြစ်သည်။
ဆေးထိုးပုံသွင်းခြင်း၏ အားသာချက်များနှင့် အားနည်းချက်များ
ဆေးထိုးပုံသွင်းခြင်းလုပ်ငန်းသည် ၎င်းတို့၏ကိုယ်ပိုင်ဆေးထိုးပုံသွင်းကိရိယာ သို့မဟုတ် ကျွမ်းကျင်မှုတွင် ရင်းနှီးမြုပ်နှံခြင်းမရှိဘဲ ပလပ်စတစ်အစိတ်အပိုင်းများထုတ်လုပ်ရန် ရှာဖွေနေသည့်ကုမ္ပဏီများအတွက် သာမာန်အလေ့အကျင့်တစ်ခုဖြစ်သည်။ Outsourcing သည် အကျိုးကျေးဇူးများစွာကို ပေးစွမ်းနိုင်သော်လည်း ၎င်းတွင် ဖြစ်နိုင်ချေရှိသော အားနည်းချက်အချို့ရှိသည်။ Outsourcing ဆေးထိုးပုံသွင်းခြင်း၏ ကောင်းကျိုးနှင့် ဆိုးကျိုးအချို့မှာ အောက်ပါအတိုင်းဖြစ်သည်။
Pros:
- ကုန်ကျစရိတ်သက်သာခြင်း- ပြင်ပဆေးထိုးပုံသွင်းခြင်းသည် အိမ်တွင်းထုတ်လုပ်သည့်စက်ရုံကို တည်ဆောက်ခြင်းထက် ကုန်ကျစရိတ်သက်သာလေ့ရှိသည်။ ဤသည်မှာ စျေးကြီးသော စက်ကိရိယာများနှင့် ဝန်ထမ်းများအတွက် ရင်းနှီးမြုပ်နှံရန် အရင်းအနှီးပြုရန် ငွေပမာဏ သို့မဟုတ် ပမာဏ ပိုမိုလိုအပ်သော အသေးစားနှင့် အလတ်စား ကုမ္ပဏီများအတွက် အထူးသဖြင့် မှန်ကန်ပါသည်။
- ကျွမ်းကျင်မှု- ဆေးထိုးပုံသွင်းသည့်ကုမ္ပဏီများသည် ထုတ်လုပ်မှုတွင် အထူးပြုပြီး အစိတ်အပိုင်းများကို အရည်အသွေးမြင့်စံဖြင့် ထုတ်လုပ်ကြောင်း သေချာစေရန် ကျွမ်းကျင်မှုရှိရမည်။ ဆေးထိုးပုံသွင်းခြင်းလုပ်ငန်းကို ပြင်ပမှထုတ်လုပ်ခြင်းဖြင့် ကုမ္ပဏီများသည် အတွေ့အကြုံရှိ ကျွမ်းကျင်ပညာရှင်များ၏ ကျွမ်းကျင်မှုမှ အကျိုးခံစားနိုင်မည်ဖြစ်သည်။
- စွမ်းရည်- ဆေးထိုးပုံသွင်းကုမ္ပဏီများသည် အစိတ်အပိုင်းအများအပြားကို လျင်မြန်ထိရောက်စွာ ထုတ်လုပ်နိုင်သည်။ ၎င်းသည် အင်္ဂါရပ်အများအပြားကို ပုံမှန်ပြုလုပ်ပေးရမည့် ကုမ္ပဏီများအတွက် အထူးအကျိုးရှိသည်။
- ပျော့ပျောင်းမှု- ပြင်ပဆေးထိုးပုံသွင်းခြင်းသည် ကုမ္ပဏီများကို ၎င်းတို့၏ထုတ်လုပ်မှုအချိန်ဇယားများတွင် ပိုမိုပြောင်းလွယ်ပြင်လွယ်ဖြစ်စေသည်။ ကုမ္ပဏီများသည် ၎င်းတို့၏ ထုတ်လုပ်မှုပမာဏကို ချိန်ညှိနိုင်သည် သို့မဟုတ် စက်ပစ္စည်းနှင့် မှိုများပြောင်းလဲခြင်း၏ အရင်းအနှီးကုန်ကျစရိတ်အတွက် စိုးရိမ်စရာမလိုဘဲ မတူညီသော အစိတ်အပိုင်းများသို့ ပြောင်းနိုင်သည်။
Cons:
- ဆက်သွယ်ရေး- Outsourcing ဆေးထိုးပုံသွင်းခြင်းသည် ဖောက်သည်နှင့် ကုမ္ပဏီကြား ဆက်သွယ်ရေးစိန်ခေါ်မှုများကို ဖန်တီးနိုင်သည်။ ဆက်သွယ်ရေးတွင် နားလည်မှုလွဲမှားခြင်း သို့မဟုတ် နှောင့်နှေးမှုများသည် ထုတ်လုပ်မှုတွင် အမှားများ သို့မဟုတ် နှောင့်နှေးမှုများ ဖြစ်စေနိုင်သည်။
- အရည်အသွေးထိန်းချုပ်ရေး- ပြင်ပဆေးထိုးပုံသွင်းခြင်းဆိုသည်မှာ လိုအပ်သော အရည်အသွေးစံနှုန်းများအတိုင်း အစိတ်အပိုင်းများထုတ်လုပ်ရန် ပြင်ပကုမ္ပဏီကို အားကိုးခြင်းဖြစ်ပါသည်။ ပြင်ပကုမ္ပဏီတစ်ခုနှင့် အလုပ်လုပ်သည့်အခါ အရည်အသွေးထိန်းချုပ်မှုသည် စိန်ခေါ်မှုတစ်ခုဖြစ်နိုင်ပြီး လိုအပ်သောသတ်မှတ်ချက်များနှင့် ပြည့်မီရမည့် အင်္ဂါရပ်များကို အမြဲလက်ခံရရှိရန် အန္တရာယ်ရှိပါသည်။
- မှီခိုမှု- Outsourcing ဆေးထိုးပုံသွင်းခြင်းဆိုသည်မှာ ပြင်ပထုတ်လုပ်မှုကုမ္ပဏီတစ်ခုအပေါ် မူတည်သည်။ ၎င်းသည် ပေးသွင်းသူ၏ ယုံကြည်စိတ်ချရမှု၊ တည်ငြိမ်မှုနှင့် ပေးပို့မှုအချိန်များနှင့် ပတ်သက်သော အန္တရာယ်များကို ဖန်တီးနိုင်သည်။
- ဉာဏပစ္စည်းပိုင်ဆိုင်မှု- ပြင်ပဆေးထိုးပုံသွင်းခြင်းသည် ဉာဏပစ္စည်းပိုင်ဆိုင်မှုကို ကာကွယ်ရန်အတွက် အန္တရာယ်များကို ဖန်တီးနိုင်သည်။ ကုမ္ပဏီများသည် ၎င်းတို့၏ ဒီဇိုင်းများနှင့် နည်းပညာများကို သင့်လျော်သော ဥပဒေနည်းလမ်းများဖြင့် အကာအကွယ်ပေးရန် လိုအပ်ပါသည်။
စိတ်ကြိုက် ပလပ်စတစ်ဆေးထိုးခြင်းအတွက် အနာဂတ်အလားအလာ
စိတ်ကြိုက်ပလပ်စတစ်ဆေးထိုးခြင်းသည် ဆယ်စုနှစ်များစွာကြာအောင် ယုံကြည်စိတ်ချရပြီး စွယ်စုံသုံးကုန်ထုတ်လုပ်မှုလုပ်ငန်းစဉ်တစ်ခုဖြစ်သည်။ မကြာသေးမီနှစ်များအတွင်း နည်းပညာနှင့် ပစ္စည်းများဆိုင်ရာ တိုးတက်မှုများသည် ဆေးထိုးပုံသွင်းခြင်း၏ စွမ်းဆောင်ရည်နှင့် အလားအလာများကို ဆက်လက်မြှင့်တင်ပေးခဲ့သည်။ ဤသည်မှာ စိတ်ကြိုက်ပလပ်စတစ်ဆေးထိုးခြင်းအတွက် အနာဂတ်အလားအလာအချို့ဖြစ်သည်။
- စက်မှု 4.0 နည်းပညာများကို လက်ခံကျင့်သုံးခြင်း- ဥာဏ်ရည်တု၊ စက်သင်ယူမှုနှင့် Internet of Things (IoT) ကဲ့သို့သော Industry 4.0 နည်းပညာများ ပေါင်းစပ်ခြင်းသည် အလိုအလျောက်စနစ် တိုးမြင့်လာစေရန်၊ အရည်အသွေးထိန်းချုပ်မှုနှင့် ဆေးထိုးပုံသွင်းခြင်းတွင် ထုတ်လုပ်မှု လုပ်ငန်းစဉ်များကို အကောင်းဆုံးဖြစ်အောင် လုပ်ဆောင်ရန် မျှော်လင့်ပါသည်။
- ဇီဝပြိုကွဲပျက်စီးနိုင်သောပစ္စည်းများကို တိုးမြှင့်အသုံးပြုခြင်း- ပတ်ဝန်းကျင်ဆိုင်ရာစိုးရိမ်မှုများသည် ဆေးထိုးပုံသွင်းခြင်းတွင် ဇီဝပျက်စီးနိုင်သောပစ္စည်းများကို လက်ခံကျင့်သုံးမှုကို တွန်းအားပေးစေသည်။ ဇီဝပြိုကွဲပျက်စီးနိုင်သော ပစ္စည်းများသည် ရိုးရာပလတ်စတစ်များအတွက် ရေရှည်တည်တံ့သော အခြားရွေးချယ်စရာကို ပေးစွမ်းနိုင်ပြီး စွန့်ပစ်ပစ္စည်းများနှင့် သဘာဝပတ်ဝန်းကျင်ဆိုင်ရာ ထိခိုက်မှုကို လျှော့ချပေးနိုင်သည်။
- ဆေးဘက်ဆိုင်ရာကိရိယာများ ထုတ်လုပ်မှုအတွက် ဝယ်လိုအား တိုးလာသည်- သက်ကြီးရွယ်အိုများနှင့် ဆေးဘက်ဆိုင်ရာနည်းပညာများ တိုးတက်လာမှုကြောင့် ဆေးဘက်ဆိုင်ရာ ကိရိယာများ လိုအပ်မှု တိုးလာပါသည်။ ထိုးသွင်းပုံသွင်းခြင်းသည် ၎င်း၏တိကျမှု၊ မြန်ဆန်မှုနှင့် ကုန်ကျစရိတ်သက်သာမှုကြောင့် ဆေးဘက်ဆိုင်ရာပစ္စည်းများအတွက် ရေပန်းစားသောထုတ်လုပ်မှုလုပ်ငန်းစဉ်တစ်ခုဖြစ်သည်။
- 3D ပုံနှိပ်ခြင်းစွမ်းရည်ကို ချဲ့ထွင်ခြင်း- 3D ပုံနှိပ်စက်နည်းပညာ ဖွံ့ဖြိုးတိုးတက်မှုသည် ဆေးထိုးပုံသွင်းခြင်းကို အသုံးပြု၍ ထုတ်လုပ်ရန် ယခင်က မဖြစ်နိုင်ခဲ့သော ရှုပ်ထွေးပြီး အနုစိတ်သော အစိတ်အပိုင်းများ ထုတ်လုပ်မှုကို အထောက်အကူ ပြုစေပါသည်။ သို့သော်လည်း 3D ပရင့်ထုတ်ခြင်းသည် ဆေးထိုးပုံသွင်းခြင်းနှင့် နှိုင်းယှဉ်ပါက အတော်လေးနှေးကွေးပြီး စျေးကြီးနေသေးပြီး နည်းပညာနှစ်ခုသည် တစ်ခုနှင့်တစ်ခု အစားထိုးခြင်းထက် တစ်ခုနှင့်တစ်ခု ဆက်လက်အားဖြည့်နိုင်မည်ဖြစ်သည်။
- ဘက်စုံဆေးထိုးပုံသွင်းခြင်းကို တိုးမြှင့်ခြင်း- ဘက်စုံဆေးထိုးခြင်းလုပ်ငန်းသည် ဆေးထိုးပုံသွင်းခြင်းလုပ်ငန်းစဉ်တစ်ခုတွင် နှစ်ခု သို့မဟုတ် နှစ်ခုထက်ပိုသော မတူညီသောပစ္စည်းများကို အသုံးပြုခြင်းပါဝင်သည်။ ဤနည်းပညာသည် အစိတ်အပိုင်းစွမ်းဆောင်ရည်ကို မြှင့်တင်ပေးခြင်း၊ အလေးချိန်လျှော့ချခြင်းနှင့် ကုန်ကျစရိတ်သက်သာစေခြင်းအပါအဝင် အကျိုးကျေးဇူးများစွာကို ပေးဆောင်သည်။
- ကိရိယာနည်းပညာ တိုးတက်မှု- ကိရိယာတန်ဆာပလာအသစ်များနှင့် ဒီဇိုင်းများကို တီထွင်ခြင်းသည် ဆေးထိုးပုံသွင်းခြင်း၏ အမြန်နှုန်း၊ ထိရောက်မှုနှင့် တိကျမှုကို တိုးမြင့်လာစေရန် မျှော်လင့်ပါသည်။ ဥပမာအားဖြင့်၊ ကိရိယာတန်ဆာပလာတွင် ပုံမှန်အအေးခံလမ်းကြောင်းများသည် စက်လည်ပတ်ချိန်များကို တိုးတက်စေပြီး စွမ်းအင်သုံးစွဲမှုကို လျှော့ချနိုင်သည်။
နိဂုံး:
စိတ်ကြိုက်ပလပ်စတစ်ဆေးထိုးပုံသွင်းခြင်းသည် အရည်အသွေးမြင့် ပလတ်စတစ်အစိတ်အပိုင်းများကို တိကျစွာနှင့် ထိရောက်မှုဖြင့် ထုတ်လုပ်မှုကို အားကောင်းစေသည့် ခိုင်မာသောထုတ်လုပ်မှုလုပ်ငန်းစဉ်တစ်ခုဖြစ်သည်။ ဆေးထိုးပုံသွင်းခြင်းလုပ်ငန်းစဉ်ကို နားလည်သဘောပေါက်ခြင်း၊ သင့်လျော်သောပစ္စည်းများနှင့် မှိုဒီဇိုင်းများကို ရွေးချယ်ခြင်းနှင့် အရည်အသွေးထိန်းချုပ်ခြင်းနှင့် စက်ကိရိယာများထိန်းသိမ်းခြင်းအတွက် အကောင်းဆုံးအလေ့အကျင့်များကို အကောင်အထည်ဖော်ခြင်းဖြင့်၊ စီးပွားရေးလုပ်ငန်းများသည် ၎င်းတို့၏ ဆေးထိုးပုံသွင်းခြင်းလုပ်ငန်းကို အကောင်းဆုံးဖြစ်အောင် လုပ်ဆောင်နိုင်ပြီး ကြီးမားသောအောင်မြင်မှုကို ရရှိနိုင်ပါသည်။ စက်မှုလုပ်ငန်းတွင် ခေတ်ရေစီးကြောင်းအသစ်များနှင့် တီထွင်ဆန်းသစ်မှုများ ပေါ်ပေါက်လာသည်နှင့်အမျှ စိတ်ကြိုက်ပလပ်စတစ်ဆေးထိုးပုံသွင်းခြင်း၏ ရေရှည်တည်တံ့မှု၊ ထိရောက်မှုနှင့် အမြတ်အစွန်းများကို မြှင့်တင်ရန် အခွင့်အလမ်းသစ်များကို အမြဲမပြတ်ရှိနေရန်နှင့် အခွင့်အလမ်းသစ်များကို ရှာဖွေခြင်းသည် မရှိမဖြစ်လိုအပ်ပါသည်။