Conceptos básicos del moldeo por inyección de plástico
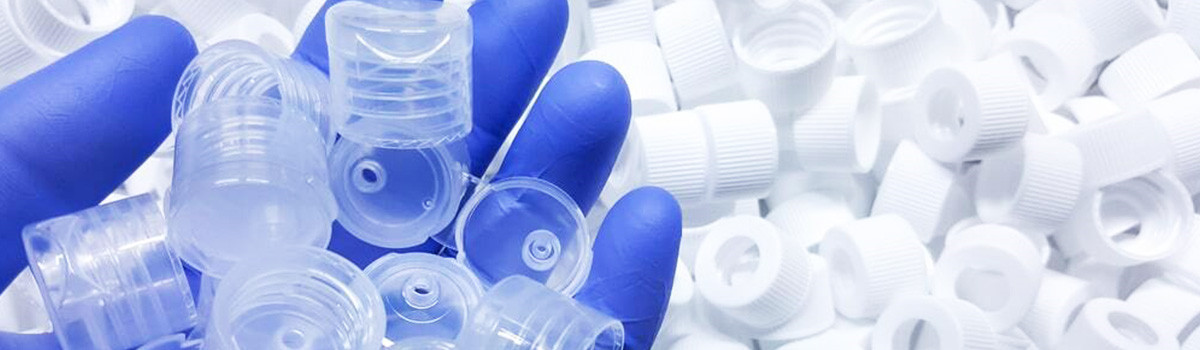
Explore el proceso de moldeo por inyección y cómo funciona.
El moldeo por inyección de plástico es una técnica de fabricación popular en la que los gránulos termoplásticos se convierten en grandes volúmenes de piezas complejas. El proceso de moldeo por inyección es adecuado para una variedad de materiales plásticos y es un aspecto vital de la vida moderna: las carcasas de los teléfonos, las carcasas electrónicas, los juguetes e incluso las piezas de automóviles no serían posibles sin él. Este artículo desglosará los conceptos básicos del moldeo por inyección, describirá cómo funciona el moldeo por inyección e ilustrará en qué se diferencia de la impresión 3D.
¿Cuáles son los fundamentos del moldeo por inyección de plástico?
Los conceptos básicos del proceso de moldeo por inyección de plástico incluyen la creación del diseño del producto, la elaboración de un molde para que se ajuste al diseño del producto, la fusión de los gránulos de resina plástica y el uso de presión para inyectar los gránulos derretidos en el molde.
Vea un desglose de cada paso a continuación:
1. Creación del diseño del producto
Los diseñadores (ingenieros, empresas de fabricación de moldes, etc.) crean una pieza (en forma de archivo CAD u otro formato transferible), siguiendo pautas de diseño fundamentales específicas para el proceso de moldeo por inyección. Los diseñadores deben tratar de incluir las siguientes características en sus diseños para ayudar a aumentar el éxito de un molde de inyección de plástico:
*Protuberancias para insertos roscados/sujetadores
*Espesores de pared constantes o casi constantes
*Transiciones suaves entre espesores de pared variables
*Cavidades huecas en secciones gruesas
*Bordes redondeados
*Ángulos de tiro en paredes verticales
* Costillas para soportes
*Ajustes por fricción, uniones a presión y otras características de unión sin sujetadores
* Bisagras vivas
Además, los diseñadores deben minimizar las siguientes características para reducir los defectos en sus diseños:
*Espesores de pared no uniformes o paredes especialmente delgadas/gruesas
*Paredes verticales sin ángulos de inclinación
*Cambios geométricos repentinos (esquinas, huecos, etc.)
*Ribete mal diseñado
*Socavados/salientes
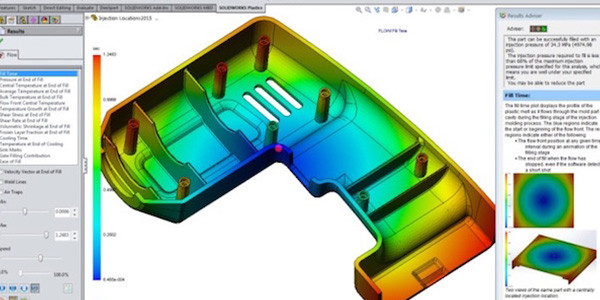
2. Elaboración de un molde de herramientas que se ajuste al diseño del producto
Maquinistas y fabricantes de herramientas altamente calificados, utilizando el diseño del producto, fabrican un molde de herramientas para la máquina de moldeo por inyección. Un molde de herramientas (también conocido simplemente como una herramienta) es el corazón y el alma de la máquina de moldeo por inyección. Están diseñados cuidadosamente para contener la cavidad negativa para el diseño del producto y características adicionales como bebederos, canales, compuertas, ventilaciones, sistemas de eyectores, canales de enfriamiento y componentes móviles. Los moldes de herramientas están hechos de grados específicos de acero y aluminio que pueden soportar decenas de miles (ya veces cientos de miles) de ciclos de calentamiento y enfriamiento, como aluminio 6063, acero P20, acero H13 y acero inoxidable 420. El proceso de fabricación del molde tarda más de 20 semanas en completarse, incluidas la fabricación y la aprobación, lo que convierte a este paso en el aspecto más extenso del moldeo por inyección. También es la parte más costosa del moldeo por inyección, y una vez que se fabrica un molde de herramientas, no se puede cambiar drásticamente sin incurrir en costos adicionales.
3. Derretir los gránulos de resina plástica
Una vez que los operadores obtienen el molde terminado, se inserta en la máquina de moldeo por inyección y el molde se cierra, iniciando el ciclo de moldeo por inyección.
Los gránulos de plástico se introducen en la tolva y en el barril. El tornillo alternativo se retira, lo que permite que los materiales se deslicen en el espacio entre el tornillo y el cilindro. Luego, el tornillo se sumerge hacia adelante, empujando el material hacia el barril y más cerca de las bandas del calentador donde se derrite en plástico fundido. La temperatura de fusión se mantiene constante según las especificaciones del material para que no se produzca degradación en el barril o en el propio molde.
4. Usar presión para inyectar los gránulos derretidos en el molde
El tornillo alternativo fuerza este plástico fundido a través de la boquilla, que está asentada dentro de una depresión en el molde conocida como casquillo del bebedero del molde. La presión de la platina móvil ajusta firmemente el molde y la boquilla, asegurando que no se escape ningún plástico. El plástico derretido se presuriza mediante este proceso, lo que hace que entre en todas las partes de la cavidad del molde y desplace el aire de la cavidad a través de las ventilaciones del molde.
Componentes de la máquina de moldeo por inyección
Los componentes de una máquina de moldeo por inyección incluyen una tolva, un barril, un tornillo alternativo, calentador(es), placa móvil, una boquilla, un molde y una cavidad de molde.
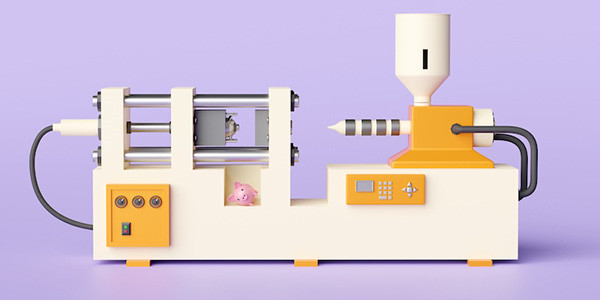
Más información sobre cada uno de los componentes de moldeo por inyección en la lista a continuación:
*Tolva: la abertura por donde se introducen los gránulos de plástico en la máquina.
*Barril: la carcasa exterior de la máquina de moldeo por inyección, que contiene el tornillo alternativo y los gránulos de plástico. El cañón está envuelto en varias bandas calentadoras y tiene una boquilla calentada en la punta.
*Tornillo alternativo: el componente sacacorchos que transporta y presuriza el material plástico a medida que se derrite a través del barril.
*Calentadores: También conocidos como bandas calefactoras, estos componentes proporcionan energía térmica a los gránulos de plástico, convirtiéndolos de una forma sólida a líquida. forma.
*Platina móvil: El componente móvil conectado al núcleo del molde que aplica presión para mantener herméticas ambas mitades del molde y también libera el núcleo del molde al revelar la pieza terminada.
*Boquilla: el componente calentado que proporciona una salida estándar para el plástico fundido en la cavidad del molde, manteniendo la temperatura y la presión lo más estables posible.
*Moho: el componente o los componentes que contienen la cavidad del molde y las características adicionales de soporte como pasadores de expulsión, canales de canales, canales de enfriamiento, ventilaciones, etc. Como mínimo, los moldes se separan en dos mitades: el lado estacionario (más cercano al barril) y el molde núcleo (en el plato móvil).
*Cavidad del molde: el espacio negativo que, al rellenarlo con plástico fundido, le dará la forma final deseada más soportes, compuertas, correderas, bebederos, etc.
¿Cómo funciona el moldeo por inyección?
Una vez que el plástico ha llenado el molde, incluidos los bebederos, canales, compuertas, etc., el molde se mantiene a una temperatura establecida para permitir la solidificación uniforme del material en la forma de la pieza. Se mantiene una presión de retención mientras se enfría para detener el reflujo hacia el barril y reducir los efectos de contracción. En este punto, se agregan más gránulos de plástico a la tolva a la espera del siguiente ciclo (o disparo). Cuando se enfría, la platina se abre y permite que la pieza terminada sea expulsada, y el tornillo se retira una vez más, lo que permite que el material ingrese al barril y comience el proceso nuevamente.
El ciclo de moldeo por inyección funciona mediante este proceso continuo: cerrar el molde, alimentar/calentar los gránulos de plástico, presurizarlos en el molde, enfriarlos hasta convertirlos en una pieza sólida, expulsar la pieza y volver a cerrar el molde. Este sistema permite la producción rápida de piezas de plástico y se pueden fabricar más de 10,000 XNUMX piezas de plástico en un día de trabajo, según el diseño, el tamaño y el material.
Djmolding es una empresa de moldeo por inyección de bajo volumen en China. Nuestro proceso de moldeo por inyección de plástico produce prototipos personalizados y piezas de producción de uso final con plazos de entrega tan rápidos como 1 día, proveedor de piezas de moldeo por inyección de plástico de bajo volumen para hasta 10000 piezas por año