Caso en la India
Molde de inserción de DJmolidng en el servicio de moldeo por inyección para empresas indias
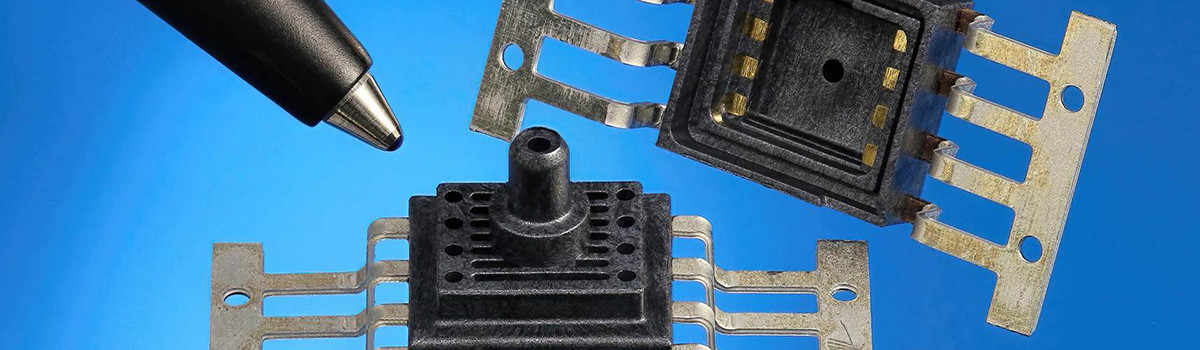
El molde de inserción generalmente es un tipo de molde que fabrica tuercas, piezas de metal o piezas de plástico duro fijadas dentro de cavidades para moldeo por inyección.
DJmolding ofrece el servicio de moldeo por inyección de inserto mlod para el mercado de la India, y producimos muchas piezas de plástico de moldeo por inserción para diferentes industrias, especialmente para fabricantes de electrodomésticos. Algunos fabricantes indios de electrodomésticos compran las piezas de plástico del moldeo por inserción durante mucho tiempo a DJmolding. Tenemos una muy buena asociación con estas empresas de la India.
Moldeo por inyección de tuercas de inserción: el material de las tuercas puede ser acero inoxidable, cobre, bronce y acero, generalmente se usan comúnmente tuercas de cobre. El cobre es fácil de moletear, lo que ayuda a que las tuercas y los plásticos se empalmen mejor. La tolerancia de los orificios internos de las tuercas debe controlarse dentro de los 0.02 mm; de lo contrario, se producirá un flash fácilmente si la tolerancia supera los 0.02 mm. En el ajuste del molde, es necesario ensamblar las tuercas en los pasadores de inserción para la prueba. Si está ajustado entre las tuercas y los pasadores, sería difícil expulsar la pieza y causar marcas de expulsión o problemas de adherencia. Si está holgado, causaría destellos.
Insertar piezas de metal moldeado por inyección:
Las piezas metálicas pueden ser de acero inoxidable, aluminio, cobre, acero…etc. La tolerancia de las piezas metálicas debe controlarse dentro de los 0.02 mm; de lo contrario, es difícil sellar el material y es fácil que se destelle. La superficie de las piezas metálicas no puede diseñarse demasiado grande.
Si la superficie de llenado para las piezas metálicas es demasiado grande, sería muy difícil lograr una inyección completa debido a la gran diferencia de temperatura entre las piezas metálicas. Las posiciones de las partes metálicas generalmente se diseñan en la cavidad, ya que la cavidad no se mueve, lo que ayuda a evitar que las partes metálicas se suelten al moverse (en casos severos, pueden dañar el molde). En casos particulares, las posiciones de las partes metálicas solo pueden diseñarse en el núcleo o en la superficie lateral del producto.
Insertar moldeo por inyección de plástico duro:
Por lo general, elija plásticos duros con un alto punto de fusión, como PEEK, PA66+30GF, PP+30GF, PA12+30GF, PPS….etc. La tolerancia para estos plásticos duros debe ser precisa. Defectos como contracción, abolladura y deformación no pueden existir en el área de sellado. En el ajuste del molde, el plástico duro debe colocarse dentro del molde para probarlo y dejarse 0.05-0.1 mm de presión previa alrededor del área de sellado para lograr un mejor sellado.
La parte de plástico duro no debe diseñarse para una superficie demasiado grande, lo que provocará una diferencia de temperatura y dificultará el llenado del material en la inyección. Por lo general, haga que la parte de plástico duro se fije en el costado de la cavidad, porque la cavidad no se mueve, para evitar destellos o incluso dañar el molde en movimiento. En casos particulares, las posiciones de las partes metálicas solo pueden diseñarse en el núcleo o en la superficie lateral del producto.
Puntos clave del diseño
1. Diseño de contracción para productos con insertos de tuercas, mientras que no es necesario diseño de contracción para productos con piezas metálicas e insertos de plástico duro. Para las áreas que necesitan una tolerancia estricta, modifique la tolerancia de tamaño de los productos a la mediana.
2. Por lo general, adopte la base del molde con una compuerta de punta de alfiler estándar en el diseño del molde y, en la inyección secundaria, coloque las piezas de inserción en la cavidad tanto como sea posible. Con la condición de hacer que los insertos se fijen en la cavidad, considere cómo hacer que la parte quede en el núcleo después del moldeo por inyección, de esta manera, la parte puede ser expulsada. Por lo general, agregue bloques elásticos en la cavidad y pegamento elástico para que la pieza permanezca en el núcleo. La distancia entre los bloques elásticos y el pegamento no puede ser demasiado grande, de lo contrario, la fuerza elástica causará la deformación de las piezas de plástico duro o metal. La distancia generalmente se diseña dentro de los 2 mm y aumenta adecuadamente la cantidad de bloques elásticos y pegamento elástico cuando las inserciones de metal o plástico duro tienen una superficie relativamente grande.
3. El grosor del material es mejor dentro de 1.3-1.8 mm (alrededor de 1.5 mm es el mejor), si no, debe revisar los dibujos del producto y sugerir al cliente que lo modifique. Si el grosor del material es más delgado que 1.3 mm, es difícil para el relleno del material, mientras que el grosor del material es más grueso que 1.8 mm, es fácil que se produzca una contracción en la producción.
4. La compuerta es muy importante en el molde. El equilibrio del llenado de material para el punto de compuerta debe considerarse completamente. Cuando el material corre hacia el área donde se fijan piezas de metal o plástico duro, la velocidad de llenado del material y la presión disminuirán debido a la resistencia de los insertos y la diferencia de temperatura.
5. Para el sistema de expulsión de moldes, se debe considerar el equilibrio de la expulsión o la deformación ocurrirá después de la expulsión. Para las piezas que no pueden expulsarse en equilibrio, es necesario considerar colapsar para mejorar el problema de equilibrio en el diseño de la estructura.
6. Para asegurar la calificación de la apariencia de las piezas después de ser expulsadas en el moldeo por inyección, el dispositivo eyector debe ser un trozo de plástico duro insertado con ABS o PMMA. Si el sobremolde tiene sellado de deslizamiento, diseñe los deslizamientos en la cavidad tanto como sea posible, ya que los deslizamientos en la cavidad facilitan el ajuste del molde.
7. Para asegurar la resistencia del sellado SA (margen de costura), para productos fabricados con doble moldeo por inyección, el ancho del sellado SA debe ser de al menos 0.8 mm. Para que el material de inyección secundario sea plástico duro, el ancho del sellado SA debe ser de al menos 1.0 mm; de lo contrario, se debe sugerir al cliente que modifique el producto.
8. En el diseño de moldes, debemos tener en cuenta las máquinas de moldeo por inyección para la producción para ver qué tipo de máquina adopta, vertical u horizontal. Se sugiere no diseñar demasiadas cavidades, especialmente para moldes con canales fríos, ya que demasiadas cavidades hacen que el canal sea más largo, desperdiciando material y también es perjudicial para lograr una inyección de alta eficiencia. Para que coincida con la máquina de moldeo por inyección, debemos considerar si es compacta y razonable para los arreglos del producto. Los productos deben poder repararse para garantizar que estén en la misma situación cada vez que se moldean. Otra forma es el sistema de reacción del diseño para alertar si la pieza no está en el lugar correcto antes del cierre del molde, lo que ayuda a detener el cierre del molde. De esta forma, las piezas se encuentran en la misma situación en el molde, lo que eleva los índices calificados y la eficiencia productiva en el moldeo por inyección.
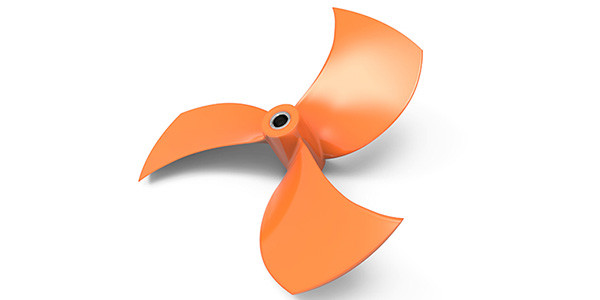
9. Se debe diseñar un soporte de acero ya que el área de inyección del molde soporta una gran presión al inyectar (debe ser 5-10 mm más grande que la de la pieza en forma y tamaño). No debe dejar espacio entre las piezas alrededor del área de sobremoldeo, de lo contrario, la pieza perderá su forma después de la inyección secundaria. Para piezas sin SA (margen de costura) deberá prestar mucha más atención a este aspecto.
10. El viaje aéreo es fácil El viaje aéreo ocurre fácilmente en el moldeo por inyección, por lo que debe considerar completamente la ventilación en el diseño del molde. En todos los ángulos ciegos y posiciones para líneas de agua de larga distancia, se deben diseñar orificios de ventilación en la pieza de plástico duro, ya que es mucho más difícil llenar los ángulos ciegos con material.
11. Para asegurar que el material inyectado y el empuje calificado estén completamente llenos, una forma es diseñar muescas en las esquinas de la pieza para mejorar el resultado del adhesivo y luego hacer que las piezas se adhieran con más fuerza.
12. En el área de sellado y el área de la línea de partición, no debemos desmoldar de la cavidad y el núcleo, ya que las líneas de sujeción en el molde y el desmoldeo provocarán un rebaje en el ajuste del molde. Prueba a desmoldar con LISS-OFF.
Tipos de punto de entrada de molde de inserción
El punto de compuerta para el molde de inserción se puede diseñar para dirigir la compuerta de válvula de bebedero caliente, la compuerta de pasador de bebedero caliente, la compuerta de punta, la subcompuerta, la compuerta de borde, etc.
Compuerta de válvula de bebedero caliente: buena liquidez, selección de posición flexible, punto de compuerta pequeño. Trajes para producción masiva y para productos con espesor de pared grueso. Puede ayudar a ahorrar material, sin desperdicio de material para la puerta, tiempo de entrega corto y alta calidad. El único defecto es el ligero rastro de activación.
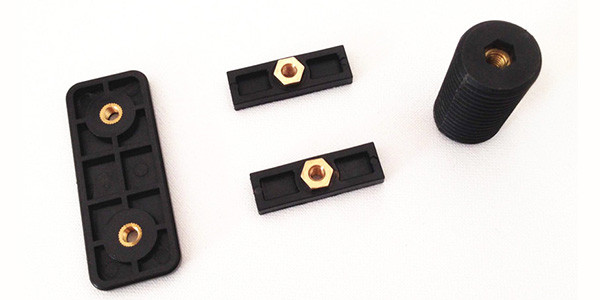
Compuerta del pasador del bebedero caliente: buena liquidez, selección de posiciones punto de puerta pequeño y flexible. Trajes para producción masiva y para productos con espesor de pared grueso. Puede ayudar a ahorrar material, sin desperdicio de material para la puerta, tiempo de entrega corto y alta calidad. Pero hay defectos, como material de 0.1 mm que queda alrededor de la punta de la puerta, y es fácil de rebabar. Necesita hacer surcos para cubrir el material izquierdo alrededor del punto de la puerta.
Puerta de punta de alfiler: selección de posición flexible, liquidez débil, distancia de corredor larga, punto de puerta pequeño. Trajes para la producción de lotes pequeños. Más material de desecho alrededor del punto de entrada. Necesita brazos mecánicos para sujetar el punto de compuerta en producción. Largo plazo de entrega. El defecto es 0.1-0.2 mm de material que queda alrededor de la punta de la puerta, es necesario hacer ranuras para cubrir el material que queda alrededor de la punta de la puerta.
Puerta secundaria: se puede diseñar en nervaduras en la cavidad, el núcleo, las paredes laterales y los pasadores de expulsión. Puede seleccionar el punto de compuerta de manera flexible, la compuerta de vertido se separa de la parte automáticamente, leve rastro de compuerta. Defectos: fácil de sacar material alrededor del punto de entrada, fácil de causar marcas de secado en la posición de entrada, es necesario limpiar el material a mano, mucha pérdida de presión desde el punto de entrada debido a las cavidades.
Puerta de borde: el plástico fundido fluye a través de la compuerta, se les asigna lateralmente de manera uniforme, disminuye la tensión; disminuya la posibilidad de que entre aire en la cavidad, evite causar rayas y burbujas. Defectos: la puerta de vertido no puede separarse de la pieza automáticamente, dejó marcas de bebedero en los bordes de la pieza, se necesitan herramientas para procesar la puerta de vertido plana. La compuerta de borde puede ayudar a dosificar la inyección y el mantenimiento de la presión, y también es bueno para mantener y alimentar la presión, de esta manera, es mejor para mejorar las líneas de aire, las marcas de flujo, etc.
Procesamiento y ajuste para molde de inserción.
1.Antes del procesamiento, determine la tecnología de procesamiento del molde. Elija máquinas de procesamiento de alta precisión, máquinas de alta velocidad, máquinas de corte de alambre NC de alimentación lenta, máquinas de EDM (mecanizado por descarga eléctrica) de espejo, etc.
2.Diseñe 0.05-0.1 mm a la izquierda en la ubicación de preprensado.
3. Tenga en cuenta los requisitos de precisión en el procesamiento de la base del molde, inspeccione la tolerancia después de obtener la base del molde y no la use si la tolerancia no está calificada.
4. Coloque tuercas, piezas de metal y piezas de plástico duro dentro del molde para colocarlo. Si encuentra problemas en el ajuste del molde, revise las tuercas, las piezas de metal, las piezas de plástico duro y los moldes para ver cuál está mal. Procese la pieza de acuerdo con el dibujo en la medida de lo posible, lo que ayuda a rastrear datos en el futuro.
5. No se puede usar la amoladora para el ajuste del molde. Recurra a las máquinas para corregir donde el ajuste del molde no es bueno.
6. Realice pruebas de acción antes del juicio, evite el montaje incorrecto y el montaje incorrecto. Un montaje erróneo dañará la base del molde.
Prueba de molde para molde de inserción
1.En una prueba de molde, uno necesita saber claramente sobre las secuencias de apertura, cierre y expulsión de un molde. Comprender las características y propiedades estructurales de las piezas metálicas y las piezas de plástico duro.
2. Conozca claramente la cantidad de muestras que necesita el cliente, prepare suficientes tuercas, piezas metálicas y plásticos duros, ya que necesita muchas muestras en las pruebas de molde.
3. Tenga en cuenta si puede probar el molde sin insertos de tuercas, piezas metálicas o plásticos duros. Si las tuercas de inserción, las piezas metálicas y los plásticos duros no se ensamblan en el molde, la pieza puede tener defectos como adherencia al molde o tiro corto.
4. En muchos casos, es necesario ajustar la placa de la línea de agua en el molde, pero a veces no se puede ajustar la placa de la línea de agua en algunos moldes de inserción en función de su estructura o, lo que es peor, el molde está muy atascado y es necesario modificarlo, o el molde se daña en el apertura.
5. Pueden ocurrir problemas en las pruebas de molde, como disparos cortos, viajes aéreos, destellos o adherencia al molde. Si los problemas se pueden verificar en una máquina de moldeo por inyección, es mejor resolverlos.
DJmolding tiene más de 10 años de experiencia en moldeo por inserción, si tiene alguna pregunta, contáctenos.