Moldeo por inyección termoplástico
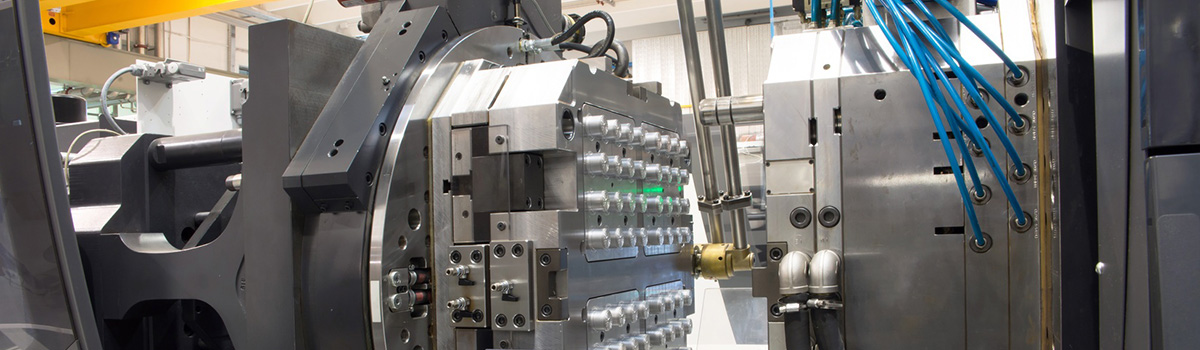
El moldeo por inyección de termoplásticos es un proceso de fabricación popular que se utiliza para crear diversas piezas de plástico para múltiples industrias. Este proceso consiste en derretir gránulos de plástico e inyectarlos en un molde para producir una forma tridimensional. El moldeo por inyección de termoplásticos es altamente eficiente y rentable para producir grandes volúmenes de piezas de plástico de alta calidad con tolerancias estrictas. Esta guía completa explorará los diversos aspectos del moldeo por inyección de termoplásticos, incluidas sus ventajas y desventajas, los tipos de termoplásticos utilizados, el proceso de moldeo por inyección, las consideraciones de diseño y mucho más.
Historia del moldeo por inyección de termoplásticos
La historia del moldeo por inyección de termoplásticos abarca más de un siglo de avances tecnológicos, desarrollos de materiales y aplicaciones industriales. Desde sus humildes comienzos como un proceso de moldeo de celuloide hasta la tecnología sofisticada actual, el moldeo por inyección sigue siendo una técnica de fabricación vital, que impulsa la innovación y da forma a diversas industrias.
- Primeros desarrollos:John Wesley Hyatt y su hermano Isaiah desarrollaron la primera máquina de moldeo por inyección práctica, rastreando los orígenes del moldeo por inyección de termoplásticos hasta finales del siglo XIX. En 19, patentaron un dispositivo que usaba un émbolo para inyectar celuloide en la cavidad de un molde, creando objetos sólidos. Este avance sentó las bases para el moderno proceso de moldeo por inyección.
- Avances en materiales:A principios del siglo XX, la introducción de nuevos polímeros sintéticos abrió nuevas posibilidades para el moldeo por inyección. La baquelita, una resina fenólica, se convirtió en un material popular para moldear debido a sus excelentes propiedades de aislamiento eléctrico. A lo largo de las décadas de 20 y 1930, los avances en la química de los polímeros condujeron al desarrollo de otros termoplásticos, como el poliestireno y el polietileno, que ampliaron aún más la gama de materiales adecuados para el moldeo por inyección.
- Adopción industrial: La adopción generalizada del moldeo por inyección de termoplásticos comenzó en la década de 1950 cuando los fabricantes reconocieron su rentabilidad y versatilidad. La introducción de máquinas de alta presión permitió tiempos de ciclo más rápidos y mayores volúmenes de producción. Como resultado, surgió una diversa selección de productos para uso personal e industrial. Estos incluían componentes de automóviles, electrodomésticos y juguetes.
- Innovaciones tecnológicas:A lo largo de las décadas, la tecnología de moldeo por inyección siguió evolucionando. En la década de 1960, surgieron máquinas controladas por computadora, lo que permitió un control preciso sobre el proceso de moldeo. La introducción de los sistemas de canales calientes en la década de 1980 redujo los desechos y mejoró la eficiencia al eliminar la necesidad de canales y bebederos. En los últimos años, los avances en automatización, robótica e impresión 3D han revolucionado aún más la industria del moldeo por inyección, permitiendo diseños complejos y reduciendo el tiempo de producción.
- Sostenibilidad y Reciclaje:Con las crecientes preocupaciones ambientales, la industria del moldeo por inyección ha adoptado medidas de sostenibilidad. Los fabricantes han desarrollado termoplásticos reciclados y de base biológica, lo que reduce la dependencia de materiales basados en combustibles fósiles. Además, las tecnologías de reciclaje mejoradas han permitido el reprocesamiento de desechos posconsumo y posindustriales, lo que minimiza el impacto ambiental del moldeo por inyección de termoplásticos.
- Perspectivas de futuro:El futuro del moldeo por inyección de termoplásticos parece prometedor. La industria está explorando innovaciones como el moldeado por microinyección para componentes en miniatura, técnicas de sobremoldeo y de múltiples materiales para piezas complejas, e integrando tecnologías inteligentes para el control y la optimización de procesos. Además, los investigadores esperan avances en materiales biodegradables y fabricación aditiva para revolucionar el campo, haciendo que el moldeo por inyección sea aún más sostenible y versátil.
Ventajas del moldeo por inyección de termoplásticos
El moldeo por inyección de termoplásticos ofrece numerosas ventajas para los fabricantes. Proporciona flexibilidad de diseño, lo que permite diseños complejos e intrincados con diversas características. El proceso es rentable, reduce el desperdicio de material y reduce los costos unitarios. El moldeo por inyección de termoplástico admite múltiples materiales, lo que brinda versatilidad para diferentes aplicaciones.
- Flexibilidad de diseño:El moldeo por inyección de termoplásticos permite diseños intrincados y complejos con características como muescas, paredes delgadas y espesores variables, lo que brinda a los diseñadores una libertad inmensa.
- Eficiencia de costo: El proceso es altamente eficiente, reduce el desperdicio de material y reduce los costos unitarios. El moldeo simultáneo de múltiples piezas y los ciclos de producción rápidos contribuyen al ahorro de costos.
- Versatilidad de materiales: El moldeo por inyección de termoplásticos admite una amplia gama de materiales, lo que permite a los fabricantes elegir la opción más adecuada para cada aplicación, incluidos materiales rígidos o flexibles, transparentes u opacos y químicamente resistentes.
- Fuerza y durabilidad:Los termoplásticos moldeados por inyección pueden exhibir excelentes propiedades mecánicas, como alta resistencia, tenacidad y resistencia al impacto. Las opciones de refuerzo, como las fibras de vidrio o de carbono, mejoran aún más estas propiedades.
- Consistencia y Calidad:El moldeo por inyección garantiza una calidad constante de pieza a pieza y precisión dimensional, ofreciendo tolerancias estrictas y productos confiables. El proceso también proporciona un acabado superficial suave y uniforme, eliminando la necesidad de operaciones de acabado adicionales.
- Escalabilidad y producción en masa:El moldeo por inyección es escalable de volúmenes bajos a altos, lo que lo hace adecuado para la producción en masa. Una vez que los fabricantes crean el molde, pueden producir grandes cantidades de piezas idénticas con variaciones mínimas.
- Integración y Montaje:Las piezas moldeadas por inyección pueden incorporar varios componentes en una sola pieza, lo que reduce la necesidad de procesos de ensamblaje adicionales. Esta integración mejora el rendimiento del producto, reduce el tiempo de ensamblaje y reduce los costos.
- Sostenibilidad:La industria del moldeo por inyección está mostrando un enfoque cada vez mayor en la sostenibilidad. La disponibilidad de materiales reciclados y de base biológica permite producir productos respetuosos con el medio ambiente. El uso eficiente de materiales y la reciclabilidad de los termoplásticos contribuyen a un proceso de fabricación más ecológico.
Estos beneficios lo han convertido en un método de fabricación ampliamente adoptado en varias industrias, proporcionando soluciones de alta calidad, rentables y respetuosas con el medio ambiente para requisitos de productos complejos.
Desventajas del moldeo por inyección de termoplásticos
Si bien el moldeo por inyección de termoplásticos ofrece numerosas ventajas, también presenta varias desventajas. Los fabricantes deben evaluar cuidadosamente estos factores y compararlos con los beneficios para determinar la idoneidad del moldeo por inyección de termoplásticos para sus aplicaciones específicas.
- Alta Inversión Inicial: Establecer una operación de moldeo por inyección de termoplásticos requiere una inversión inicial significativa en el diseño y fabricación de moldes y la compra de maquinaria especializada. Los costos asociados con la creación de moldes y herramientas pueden ser sustanciales, especialmente para diseños complejos e intrincados.
- Limitaciones de diseño: Si bien el moldeo por inyección de termoplásticos ofrece flexibilidad de diseño, existen ciertas limitaciones. Por ejemplo, lograr un espesor de pared uniforme en toda la pieza puede ser un desafío, lo que genera variaciones en la distribución del material y posibles debilidades estructurales. Además, la presencia de muescas o geometrías complejas puede requerir el uso de características de molde adicionales u operaciones secundarias, lo que aumenta los costos y el tiempo de producción.
- Plazos de entrega largos:El proceso de diseño y fabricación de moldes para moldeo por inyección puede llevar mucho tiempo, lo que lleva a plazos de entrega más largos para el desarrollo de productos. El proceso de iteración del diseño, la producción de moldes y las pruebas pueden agregar un tiempo significativo a la línea de tiempo de producción general, lo que puede no ser adecuado para proyectos con plazos ajustados.
- Restricciones de selección de materiales:Aunque el moldeo por inyección de termoplásticos admite una amplia gama de materiales, existen ciertas limitaciones y restricciones. Algunos materiales pueden tener requisitos de procesamiento específicos o disponibilidad limitada, lo que afecta las opciones de diseño y la selección de materiales para una aplicación en particular.
- Limitaciones de tamaño de pieza:Las máquinas de moldeo por inyección tienen limitaciones de tamaño, tanto en términos del tamaño físico del dispositivo como del tamaño de los moldes que pueden acomodar. La producción de piezas enormes puede requerir equipos especializados o métodos de fabricación alternativos.
- Impacto medioambiental:Si bien la industria está trabajando hacia la sustentabilidad, el proceso de moldeo por inyección de termoplásticos aún genera material de desecho, incluidos desechos y bebederos. La eliminación y el reciclaje adecuados de estos materiales son necesarios para minimizar el impacto ambiental.
- La complejidad de la Optimización de Procesos:Lograr parámetros de proceso óptimos para el moldeo por inyección de termoplásticos puede ser complejo y llevar mucho tiempo. Los fabricantes deben controlar cuidadosamente y optimizar la temperatura, la presión, las tasas de enfriamiento y los tiempos de ciclo para garantizar una calidad de pieza uniforme y minimizar los defectos.
Tipos de termoplásticos utilizados en el moldeo por inyección
Estos son solo algunos ejemplos de los termoplásticos comúnmente utilizados en el moldeo por inyección. Cada material tiene propiedades únicas, lo que lo hace adecuado para aplicaciones específicas basadas en la fuerza, la flexibilidad, la resistencia química, la transparencia y el costo. Los fabricantes deben tener en cuenta estas propiedades y requisitos al seleccionar el termoplástico apropiado para sus proyectos de moldeo por inyección.
- Polipropileno (PP):El polipropileno es un termoplástico versátil que se usa comúnmente en el moldeo por inyección. Ofrece excelente resistencia química, baja densidad y buena resistencia al impacto. El PP (polipropileno) tiene una amplia gama de aplicaciones en embalajes, componentes de automóviles, electrodomésticos y dispositivos médicos.
- Polietileno (PE):El polietileno es otro termoplástico ampliamente utilizado en el moldeo por inyección. Está disponible en varias formas, como polietileno de alta densidad (HDPE) y polietileno de baja densidad (LDPE). El PE ofrece buena resistencia química, tenacidad y flexibilidad, lo que lo hace adecuado para botellas, contenedores y tuberías.
- Poliestireno (PS):El poliestireno es un termoplástico versátil conocido por su claridad, rigidez y asequibilidad. Encuentra un uso común en envases, bienes de consumo y productos desechables. PS (poliestireno) permite un procesamiento rápido y proporciona una buena estabilidad dimensional, pero puede ser quebradizo y susceptible al agrietamiento por estrés ambiental.
- Acrilonitrilo butadieno estireno (ABS): El ABS es un termoplástico popular conocido por su excelente resistencia al impacto y durabilidad. Combina las propiedades del acrilonitrilo, el butadieno y el estireno para crear un material versátil adecuado para piezas de automóviles, carcasas electrónicas y juguetes.
- Cloruro de polivinilo (PVC): El PVC es un termoplástico ampliamente utilizado conocido por su excelente resistencia química, durabilidad y bajo costo. Puede ser rígido o flexible dependiendo de la formulación y aditivos utilizados. El PVC (cloruro de polivinilo) encuentra un uso común en la construcción, aislamiento eléctrico, productos para el cuidado de la salud y empaques.
- Policarbonato (PC): El policarbonato es un termoplástico transparente con extraordinario impacto y alta resistencia al calor. Encuentra un uso común en aplicaciones que requieren claridad óptica, como componentes automotrices, cascos de seguridad y pantallas electrónicas.
- Nailon (Poliamida):El nailon es un termoplástico fuerte y duradero conocido por sus excelentes propiedades mecánicas y resistencia química. Encuentra un uso común en aplicaciones que exigen alta resistencia, como piezas de automóviles, componentes industriales y bienes de consumo.
- Tereftalato de polietileno (PET):El PET es un termoplástico popular para producir botellas, envases y materiales de empaque. Ofrece buena claridad, resistencia química y propiedades de barrera, lo que lo hace adecuado para aplicaciones de alimentos y bebidas.
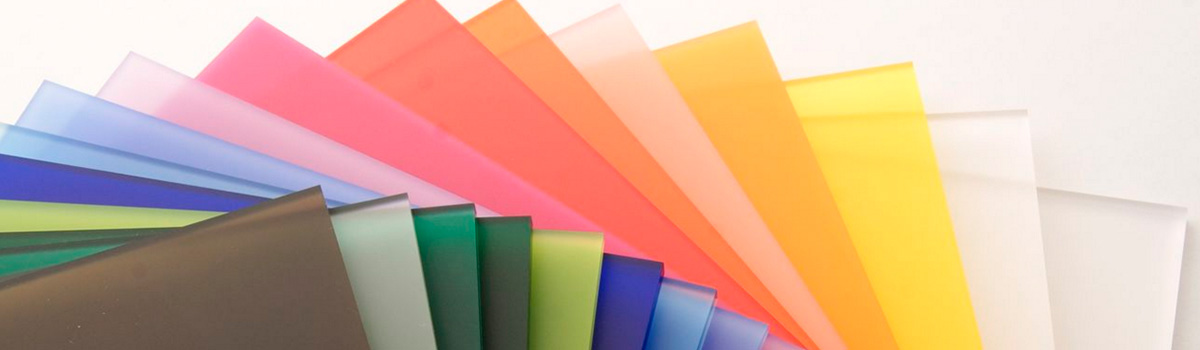
Propiedades de los termoplásticos utilizados en el moldeo por inyección
Estas propiedades de los termoplásticos juegan un papel crucial en la determinación de su idoneidad para aplicaciones específicas de moldeo por inyección. Los fabricantes deben considerar cuidadosamente estas propiedades y seleccionar el termoplástico adecuado según el rendimiento deseado, las condiciones ambientales y los requisitos de costo.
- Propiedades mecánicas:Los termoplásticos utilizados en el moldeo por inyección pueden exhibir varias propiedades mecánicas, que incluyen resistencia a la tracción, resistencia al impacto y resistencia a la flexión. Estas propiedades determinan la capacidad del material para resistir las fuerzas aplicadas y su durabilidad general en diversas aplicaciones.
- Resistencia química:Muchos termoplásticos utilizados en el moldeo por inyección poseen una notable resistencia a los productos químicos, disolventes y aceites. Esta propiedad es crucial para aplicaciones que implican la exposición a entornos hostiles o sustancias corrosivas.
- Estabilidad térmica:La estabilidad térmica de los termoplásticos se refiere a su capacidad para soportar temperaturas elevadas sin una degradación significativa. Algunos termoplásticos presentan una excelente resistencia al calor, lo que les permite mantener sus propiedades mecánicas incluso a altas temperaturas.
- Propiedades electricas:Los termoplásticos utilizados en el moldeo por inyección pueden tener propiedades eléctricas específicas, incluido el aislamiento eléctrico, la conductividad o la rigidez dieléctrica. Estas propiedades son esenciales para las aplicaciones en las industrias eléctrica y electrónica, donde los materiales deben proporcionar un rendimiento eléctrico fiable.
- Transparencia y Claridad:Ciertos termoplásticos, como el policarbonato y el PET, ofrecen una excelente transparencia y claridad, lo que los hace adecuados para aplicaciones que requieren propiedades ópticas. Los fabricantes suelen utilizar estos materiales en productos como ventanas transparentes, lentes y pantallas.
- Flexibilidad y dureza: La flexibilidad y la tenacidad son propiedades esenciales de los termoplásticos utilizados en aplicaciones que requieren resistencia al impacto y durabilidad. Algunos termoplásticos, como el ABS y el nailon, ofrecen una dureza excelente, lo que les permite resistir impactos repetidos sin romperse.
- Estabilidad dimensional:La estabilidad dimensional se refiere a la capacidad de un termoplástico para mantener su forma y tamaño en condiciones variables, incluidos los cambios de temperatura. Los materiales con buena estabilidad dimensional aseguran dimensiones de pieza consistentes, minimizando el riesgo de deformación o distorsión.
- Compatibilidad química:La compatibilidad química de los termoplásticos se refiere a su capacidad para resistir la degradación o la interacción con varios productos químicos, incluidos ácidos, bases y solventes. Para garantizar un rendimiento óptimo, es esencial seleccionar un termoplástico que pueda resistir el entorno químico específico que encontrará en la aplicación prevista.
- Densidad: Los termoplásticos tienen diferentes grosores, lo que puede afectar su peso y las propiedades generales de la pieza. Los materiales de baja densidad, como el polietileno, ofrecen soluciones livianas, mientras que los materiales de alta densidad, como el polipropileno, brindan mayor resistencia y rigidez.
Proceso de moldeo por inyección: paso a paso
El proceso de moldeo por inyección sigue estos pasos, lo que permite la producción eficiente y precisa de piezas termoplásticas de alta calidad. Cada paso requiere un control y una supervisión cuidadosos para garantizar la uniformidad de las dimensiones de las piezas, las propiedades del material y la calidad general.
- Diseño y fabricación de moldes: El primer paso en el proceso de moldeo por inyección es el diseño y fabricación del molde. Los fabricantes deben crear un diseño de molde preciso y detallado para lograr las especificaciones deseadas de la pieza. Luego, los fabricantes fabrican el molde utilizando diversas técnicas, como CNC o mecanizado por descarga eléctrica (EDM).
- Preparación del material: El siguiente paso es la preparación una vez que el molde esté listo. Los gránulos o gránulos termoplásticos se seleccionan en función de las propiedades deseadas del material y se funden en una tolva. Luego, los operadores introducen el material en el barril de la máquina de moldeo por inyección, donde se funde y homogeneiza.
- Inyección:Durante la fase de inyección, los operadores inyectan el termoplástico fundido en la cavidad del molde a alta presión. La unidad de inyección de la máquina empuja el material fundido a través de una boquilla hacia el interior del molde. El material llena la cavidad del molde, tomando la forma de la pieza deseada.
- Enfriamiento y Solidificación:Después de llenar el molde, los operadores dejan que el plástico fundido se enfríe y se solidifique. El enfriamiento es crucial para lograr la estabilidad dimensional y la formación adecuada de la pieza. Los operadores pueden controlar el proceso de enfriamiento haciendo circular el refrigerante a través de los canales dentro del molde o usando placas de enfriamiento.
- Apertura y expulsión del molde:Los operadores abren el molde y expulsan la pieza de la cavidad del molde una vez que el plástico se solidifica. El sistema de expulsión dentro de la máquina utiliza pasadores, placas de expulsión o chorros de aire para retirar la región del molde. El molde está entonces listo para el próximo ciclo de inyección.
- Postprocesamiento: Después de la expulsión, la pieza puede someterse a operaciones de procesamiento posterior, como recorte, desbarbado o acabado superficial. Estos pasos ayudan a eliminar el exceso de material, suavizar los bordes ásperos y mejorar la apariencia final de la pieza.
- Inspeccion de calidad: El paso final consiste en inspeccionar la calidad de las piezas inyectadas y asegurarse de que cumplan con los requisitos especificados. Se pueden emplear diversas técnicas de control de calidad, incluidas la medición dimensional, la inspección visual y las pruebas funcionales, para verificar la calidad e integridad de la pieza.
- Reciclaje y Reutilización de Materiales:Cualquier exceso o material de desecho generado durante el moldeo por inyección se puede reciclar y reutilizar. Reducir el uso de nuevos materiales termoplásticos ayuda a minimizar los residuos y mejorar la sostenibilidad.
Equipos utilizados en el moldeo por inyección
Estos componentes del equipo facilitan el proceso de moldeo por inyección, desde la fusión e inyección del material termoplástico hasta la conformación, enfriamiento y expulsión de la pieza final. La operación y el mantenimiento adecuados de estos componentes del equipo son cruciales para lograr una producción de moldeo por inyección eficiente y de alta calidad.
- Máquina de moldeo por inyección:El equipo principal en el moldeo por inyección es responsable de fundir el material termoplástico, inyectarlo en el molde y controlar el proceso.
- Molde: El molde, diseñado a medida para crear la forma y las características deseadas de la pieza de plástico, consta de dos mitades, la cavidad y el núcleo. Los operadores lo montan en la unidad de sujeción de la máquina de moldeo por inyección.
- Tolva:Recipiente que contiene el material termoplástico en forma de gránulos o gránulos y lo introduce en el cilindro de la máquina de moldeo por inyección para su fusión e inyección.
- Barril y tornillo: El barril, una cámara cilíndrica, funde y homogeneiza el material termoplástico a medida que el tornillo gira dentro de él para fundir, mezclar y estandarizar el material.
- Sistemas de calefacción y refrigeración:Las máquinas de moldeo por inyección cuentan con elementos calefactores, como calentadores eléctricos o calentadores de aceite caliente, para elevar la temperatura del barril, y sistemas de enfriamiento, como circulación de agua o aceite, para enfriar el molde y solidificar la pieza de plástico.
- Sistema eyector:Retira la pieza moldeada de la cavidad del molde después de la solidificación, normalmente utilizando pasadores eyectores, placas o chorros de aire durante la apertura del molde.
- Sistema de control:Supervisa y controla varios parámetros del proceso de moldeo por inyección, lo que permite a los operadores establecer y ajustar parámetros como la velocidad de inyección, la temperatura, la presión y el tiempo de enfriamiento.
Máquinas de Moldeo por Inyección: Tipos y Características
Cada tipo de máquina de moldeo por inyección tiene sus características y ventajas, lo que permite a los fabricantes elegir el dispositivo más adecuado para sus requisitos específicos de producción.
- Máquinas de moldeo por inyección hidráulica: Estas máquinas utilizan sistemas hidráulicos para generar la presión necesaria para inyectar plástico fundido en el molde. Son conocidos por su alta fuerza de sujeción, control preciso y versatilidad en el manejo de varios termoplásticos. Las máquinas hidráulicas son adecuadas para la producción a gran escala y pueden adaptarse a moldes complejos.
- Máquinas eléctricas de moldeo por inyección:Las máquinas eléctricas utilizan servomotores eléctricos para el funcionamiento de la máquina, incluidos los sistemas de inyección, sujeción y expulsión. Ofrecen control preciso, eficiencia energética y tiempos de respuesta más rápidos que las máquinas hidráulicas. Las máquinas eléctricas son ideales para aplicaciones de moldeo de precisión que requieren alta repetibilidad y precisión.
- Máquinas de moldeo por inyección híbridas:Las máquinas híbridas combinan los beneficios de los dispositivos hidráulicos y eléctricos. Utilizan una combinación de servosistemas hidráulicos y eléctricos para lograr alta precisión, eficiencia energética y rentabilidad. Las máquinas híbridas son adecuadas para una amplia gama de aplicaciones y proporcionan un equilibrio entre el rendimiento y los costos operativos.
- Máquinas de moldeo por inyección de dos platos: Las máquinas de dos placas tienen un diseño único con dos placas separadas para sujetar el molde. Este diseño proporciona mayor estabilidad, mejor sincronización de moldes y permite tamaños de moldes más grandes y mayores fuerzas de sujeción. Las máquinas de dos platos son adecuadas para piezas grandes y complejas que requieren un moldeado preciso.
- Máquinas de moldeo por inyección de componentes múltiples:Los fabricantes diseñan estas máquinas para producir piezas con múltiples materiales o colores en un solo ciclo de moldeo. Disponen de varias unidades de inyección y moldes, lo que permite la inyección simultánea de diferentes materiales. Las máquinas multicomponente ofrecen flexibilidad y eficiencia en la fabricación de piezas complejas con características variables.
- Máquinas de moldeo por microinyección:Diseñadas específicamente para producir piezas pequeñas y precisas, las máquinas de moldeo por microinyección ofrecen una precisión y exactitud increíblemente altas. Pueden producir detalles intrincados con tolerancias estrictas y un mínimo desperdicio de material. La electrónica, los dispositivos médicos y la microóptica suelen utilizar máquinas de moldeo por microinyección.
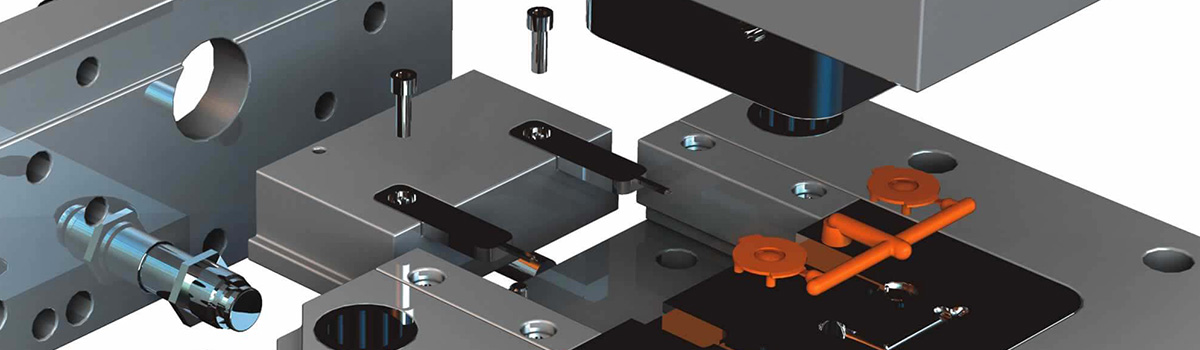
Consideraciones de diseño de moldes para moldeo por inyección
Las consideraciones cuidadosas del diseño del molde son esenciales para una producción exitosa de moldeo por inyección.
- Diseño de parte:El diseño del molde debe adaptarse a los requisitos específicos de la pieza, incluida su forma, dimensiones y características funcionales. Los fabricantes deben considerar adecuadamente los ángulos de desmoldeo, el grosor de la pared, las socavaduras y cualquier elemento necesario para garantizar la facilidad de expulsión y la calidad de la pieza.
- Material del molde: La selección del material del molde es crucial para lograr durabilidad, estabilidad dimensional y resistencia al calor. Los materiales comunes para moldes incluyen aleaciones de acero, aleaciones de aluminio y aceros para herramientas. La elección del material depende de factores como el volumen de producción, la complejidad de la pieza y la vida útil esperada de la herramienta.
- Sistema de refrigeración:El enfriamiento eficiente es esencial para la solidificación adecuada de la pieza y para minimizar el tiempo del ciclo. El diseño del molde debe incorporar canales de enfriamiento o insertos ubicados estratégicamente para garantizar un enfriamiento uniforme del molde. El enfriamiento adecuado reduce el riesgo de deformación, encogimiento y defectos de las piezas.
- Desfogue:Es necesaria una ventilación adecuada para permitir el escape de aire y gases durante el proceso de inyección. Una ventilación insuficiente puede provocar trampas de gas, marcas de quemaduras o llenado de piezas incompleto. Los fabricantes pueden lograr la ventilación incorporando ranuras de ventilación, pasadores u otros mecanismos en el diseño del molde.
- Sistema de expulsión:El diseño del molde debe incluir un sistema de eyección efectivo para retirar de manera segura y eficiente la pieza moldeada de la cavidad del molde. El sistema de eyección puede consistir en pasadores de eyección, manguitos u otros mecanismos, colocados estratégicamente para evitar la interferencia con la función o las características críticas.
- Diseño de puerta:La puerta es donde el plástico fundido ingresa a la cavidad del molde. El diseño de la compuerta debe garantizar el llenado adecuado de la pieza, minimizar las líneas de flujo y evitar la congelación prematura del material. Los diseños estándar de compuertas incluyen compuertas de borde, compuertas de túnel y sistemas de canal caliente, según los requisitos de la pieza y las propiedades del material.
- Línea divisoria:El diseño del molde debe definir una línea de separación adecuada, que es la línea donde se juntan las dos mitades del molde. La colocación correcta de la línea de partición garantiza un desajuste mínimo de la línea de separación y la rebaba, y facilita el montaje eficiente del molde.
- Mantenimiento y capacidad de servicio del molde: Los fabricantes deben considerar la facilidad de mantenimiento, reparación y servicio de moldes. Los componentes del molde deben ser fácilmente accesibles para su limpieza, inspección y reemplazo. La incorporación de características como insertos de cambio rápido o diseños de moldes modulares puede mejorar la capacidad de servicio del molde.
Materiales de molde utilizados en el moldeo por inyección
La colaboración con especialistas en materiales de moldes y la consideración de las necesidades específicas de la aplicación de moldeo pueden ayudar a determinar el material más adecuado para lograr el rendimiento óptimo del molde y la calidad de la pieza.
- Aleaciones de acero: Las aleaciones de acero, como los aceros para herramientas (p. ej., P20, H13) y los aceros inoxidables, se usan comúnmente para moldes de moldeo por inyección debido a su excelente durabilidad, resistencia al calor y resistencia al desgaste. Estos materiales pueden soportar las altas temperaturas y presiones del proceso de moldeo por inyección y ofrecen una buena estabilidad dimensional para producir piezas de alta calidad.
- Aleaciones de aluminio:Las aleaciones de aluminio, como 7075 y 6061, son livianas y ofrecen una buena conductividad térmica, lo que las hace adecuadas para moldes que requieren un enfriamiento eficiente. Los fabricantes suelen utilizar moldes de aluminio para la creación de prototipos, la producción de bajo volumen o aplicaciones en las que la reducción de peso es crítica. Sin embargo, los moldes de aluminio pueden tener una menor durabilidad en comparación con las aleaciones de acero.
- Aleaciones de cobre:Las aleaciones de cobre, como el cobre berilio, muestran una alta conductividad térmica y una buena maquinabilidad. Encuentran uso en moldes que requieren una excelente transferencia de calor para un enfriamiento efectivo. Las aleaciones de cobre pueden ayudar a reducir los tiempos de ciclo al disipar rápidamente el calor de la pieza moldeada, lo que da como resultado una solidificación más rápida.
- Aceros para herramientas:Los aceros para herramientas, incluidos H13, S7 y D2, están diseñados para aplicaciones de herramientas de alto rendimiento. Estos aceros ofrecen una combinación de alta resistencia, dureza y resistencia al desgaste. Los aceros para herramientas se adaptan a moldes con altos volúmenes de producción, materiales abrasivos o condiciones de moldeo exigentes.
- Aleaciones de níquel:Las aleaciones de níquel, como Inconel y Hastelloy, son conocidas por su excepcional resistencia a la corrosión, resistencia a altas temperaturas y estabilidad térmica. Los fabricantes usan estas aleaciones en moldes que manejan materiales corrosivos o requieren resistencia a temperaturas extremas y entornos de moldeo agresivos.
- Materiales compuestos:Los materiales compuestos, como los plásticos reforzados o los compuestos con inserciones de metal, se utilizan ocasionalmente para aplicaciones de moldeo específicas. Estos materiales ofrecen un equilibrio de propiedades, como alta resistencia, estabilidad térmica y peso reducido. Los moldes compuestos pueden ser alternativas rentables para requisitos de producción específicos.
Tipos de moldes de inyección
El moldeo por inyección es un proceso de fabricación versátil y ampliamente utilizado para piezas de plástico.
- Molde de dos platos:El molde de dos placas es el tipo más común de molde de inyección. Consta de dos placas, la placa de cavidades y la placa central, que se separan para permitir la expulsión de la pieza moldeada. La placa de cavidades contiene el lado de la cavidad del molde, mientras que la placa del núcleo alberga el lado del núcleo. Los fabricantes utilizan moldes de dos placas para producir una amplia gama de piezas debido a su diseño relativamente simple.
- Molde de tres platos:El molde de tres placas es una versión avanzada del molde de dos placas. Incluye una placa adicional, la corredera o la placa de bebedero. La placa de corredera crea un canal separado para el bebedero, las correderas y las compuertas, lo que facilita la extracción de la pieza moldeada. Los fabricantes suelen utilizar moldes de tres placas para detalles con sistemas de entrada complejos o cuando es deseable evitar un vestigio de entrada en la pieza.
- Molde de canal caliente:El sistema de canales y compuertas se calienta en moldes de canales calientes, lo que elimina la necesidad de solidificar y volver a fundir el material durante cada ciclo. El sistema de canal caliente consta de colectores y boquillas calientes que mantienen el estado fundido del plástico. Los moldes de colada caliente ofrecen ventajas como un tiempo de ciclo reducido, menos desperdicio de material y una mejor calidad de la pieza al minimizar los vestigios de entrada.
- Molde de canal frío: Los moldes de colada fría tienen un sistema tradicional de colada y compuerta donde el plástico fundido fluye a través de coladas frías que se solidifican con cada ciclo. Posteriormente, los operadores retiran los canales solidificados, lo que genera un desperdicio de material. Los fabricantes suelen utilizar moldes de colada complejos para una producción de menor volumen o cuando los costes de los materiales son menos críticos debido a su diseño más sencillo.
- Insertar molde:Los moldes de inserción incorporan insertos de metal o plástico en la cavidad del molde durante el moldeo por inyección. Los insertos pueden colocarse previamente en el molde o insertarse mediante procesos automatizados. Este molde permite integrar componentes adicionales o elementos de refuerzo en la pieza moldeada, mejorando su funcionalidad o resistencia.
- Sobremoldeado: El sobremoldeo implica moldear un material sobre otro, normalmente uniendo un sustrato de plástico rígido con un elastómero o termoplástico más suave. Este proceso permite la creación de piezas con múltiples materiales o texturas en un solo molde, proporcionando un mejor agarre, amortiguación o características estéticas.
Factores que afectan los costos de moldeo por inyección
Tener en cuenta estos factores puede ayudar a los fabricantes a estimar y optimizar el costo del moldeo por inyección, asegurando un equilibrio entre calidad, eficiencia y rentabilidad para sus requisitos de producción específicos.
- Complejidad de la pieza:La complejidad del diseño de la pieza juega un papel importante en la determinación del costo del moldeo por inyección. Las geometrías intrincadas, los socavados, las paredes delgadas o las características complejas pueden requerir herramientas adicionales, moldes especializados o ciclos más largos, lo que aumenta el costo total de fabricación.
- Selección de materiales:La elección del material termoplástico afecta el costo del moldeo por inyección. Los diferentes materiales tienen diferentes precios por kilogramo, y factores como la disponibilidad del material, las propiedades y los requisitos de procesamiento pueden influir en el costo total del material.
- Diseño de utillajes y moldes: Los costos iniciales de diseño de herramientas y moldes son significativos en los costos de moldeo por inyección. Factores como la complejidad del molde, el número de cavidades, el tamaño del molde y el material del molde contribuyen a los gastos de fabricación de herramientas y moldes. Los moldes más complejos o los moldes que requieren funciones avanzadas pueden aumentar la inversión inicial.
- Volumen de producción: El volumen de producción impacta directamente en el costo por pieza en el moldeo por inyección. Los libros más altos a menudo dan como resultado economías de escala, lo que reduce el costo por pieza. Por el contrario, las corridas de producción de bajo volumen pueden incurrir en cargos más altos debido a la configuración, las herramientas y el desperdicio de material.
- Tiempo del ciclo: El tiempo del ciclo, que incluye las fases de enfriamiento y expulsión, afecta la capacidad de producción y el costo total. Los tiempos de ciclo más largos dan como resultado una producción reducida y precios potencialmente más altos. Optimizar el diseño del molde, el sistema de enfriamiento y los parámetros del proceso puede minimizar los tiempos de ciclo y mejorar la eficiencia.
- Requerimientos de calidad:Los estrictos requisitos de calidad o las certificaciones específicas pueden afectar el costo del moldeo por inyección. Cumplir con las tolerancias exactas, los requisitos de acabado de la superficie o las pruebas adicionales pueden requerir otros recursos, procesos o inspecciones, lo que aumenta el costo total.
- Operaciones secundarias:Si las piezas moldeadas requieren operaciones de procesamiento posterior, como ensamblaje, pintura o pasos de acabado adicionales, estas operaciones pueden aumentar el costo total del moldeo por inyección.
- Proveedor y Ubicación:La elección del proveedor de moldeo por inyección y su ubicación pueden afectar los costos. Los costos de mano de obra, los gastos generales, la logística y los gastos de transporte varían según la ubicación del proveedor, lo que afecta el costo total de fabricación.
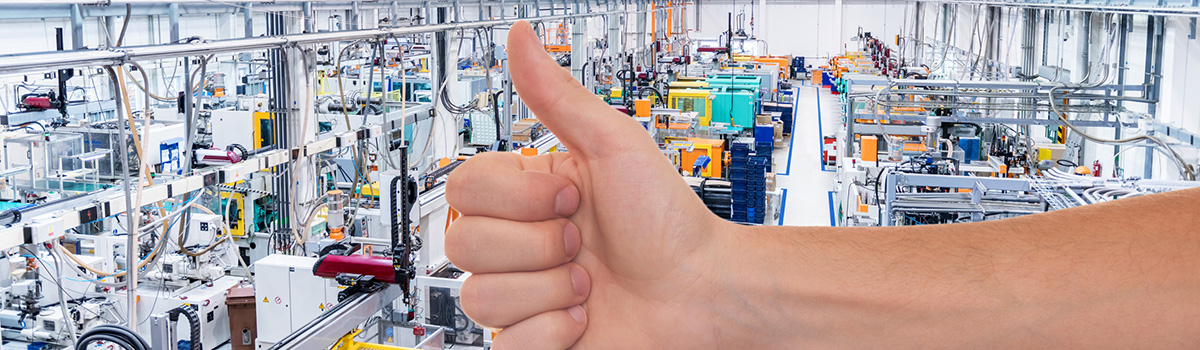
Control de calidad en moldeo por inyección
La implementación de medidas sólidas de control de calidad a lo largo del proceso de moldeo por inyección ayuda a identificar y abordar posibles defectos, desviaciones o inconsistencias, lo que garantiza la producción de piezas de alta calidad que cumplen con las especificaciones y los requisitos del cliente.
- Monitoreo de Procesos: El monitoreo continuo de los parámetros clave del proceso, como la temperatura de fusión, la presión de inyección, el tiempo de enfriamiento y el tiempo del ciclo, garantiza la consistencia y la repetibilidad en la producción de piezas. El monitoreo en tiempo real y los sistemas automatizados pueden detectar variaciones o desviaciones de los parámetros establecidos, lo que permite ajustes oportunos y mantiene la estabilidad del proceso.
- Inspección y Medición:La revisión y medición regulares de las piezas moldeadas son esenciales para verificar la precisión dimensional, la calidad de las piezas y el cumplimiento de las especificaciones. Nuestros servicios cubren una variedad de métodos de control de calidad, como la medición de dimensiones, el análisis de la calidad de la superficie, la realización de inspecciones visuales y la realización de pruebas funcionales. Se emplean varias técnicas de inspección, como máquinas de medición por coordenadas (CMM) y sistemas de inspección óptica y visual, para una evaluación precisa.
- Control Estadístico de Procesos (SPC): SPC implica recopilar y analizar datos de proceso para monitorear y controlar la calidad del moldeo por inyección. Los métodos estadísticos, como los gráficos de control y el análisis de la capacidad del proceso, ayudan a identificar tendencias, detectar variaciones del proceso y garantizar que el proceso permanezca dentro de los límites de control definidos. SPC permite la identificación proactiva de problemas y facilita la optimización de procesos.
- Prueba de materiales: Las pruebas de las materias primas, como los termoplásticos, los aditivos y los colorantes, garantizan su calidad e idoneidad para el moldeo por inyección. Las pruebas de materiales pueden incluir análisis del índice de fluidez (MFI), propiedades mecánicas, características térmicas y composición del material. Verificar la calidad del material ayuda a prevenir defectos e inconsistencias en las piezas moldeadas.
- Mantenimiento e inspección de herramientas:El mantenimiento adecuado y la inspección periódica de los moldes de inyección son cruciales para garantizar la calidad en el moldeo por inyección. La limpieza, lubricación y evaluación regulares de los componentes del molde ayudan a prevenir el desgaste, el daño o la degradación que podría afectar la calidad de la pieza. La reparación o el reemplazo oportunos de los componentes del molde desgastados o dañados es esencial para mantener un rendimiento constante del moldeado.
- Documentación y Trazabilidad:Mantener una documentación completa y registros de trazabilidad es esencial para el control de calidad en el moldeo por inyección. Es vital registrar los parámetros del proceso, los resultados de la inspección, la información del material y cualquier cambio o ajuste realizado durante la producción. La documentación adecuada permite la trazabilidad de las piezas, facilita el análisis de la causa raíz y garantiza la consistencia en la calidad.
- Capacitación y desarrollo de habilidades: Brindar capacitación adecuada y programas de desarrollo de habilidades para operadores, técnicos y personal de control de calidad mejora su comprensión de los procesos de moldeo por inyección, los requisitos de calidad y las técnicas de inspección. El personal bien capacitado puede detectar defectos, solucionar problemas e implementar medidas correctivas de manera efectiva, lo que garantiza una producción de alta calidad.
Defectos comunes de moldeo por inyección y cómo evitarlos
La inspección, el control y el análisis regulares de los procesos de moldeo por inyección y el mantenimiento y ajuste adecuados de los equipos y moldes pueden ayudar a identificar y abordar estos defectos comunes.
- Marcas de hundimiento:Las marcas de hundimiento son depresiones o muescas en la superficie de la pieza moldeada causadas por un enfriamiento o una contracción desiguales. Se debe considerar la ubicación y el diseño adecuados de la compuerta, el diseño óptimo del sistema de enfriamiento y la distribución uniforme del espesor de la pared para evitar marcas de hundimiento. Aumentar la presión de inyección o ajustar el tiempo de enfriamiento también puede ayudar a minimizar las marcas de hundimiento.
- Alabeo:La deformación se refiere a la deformación o flexión de una pieza moldeada después de la expulsión debido a un enfriamiento desigual o tensiones residuales. Mantener un grosor de pared uniforme, usar canales de enfriamiento adecuados y garantizar un llenado y empaquetado equilibrados del molde son cruciales para evitar la deformación. La optimización de la temperatura del molde, el uso de ángulos de inclinación apropiados y el control de la temperatura del material y la velocidad de inyección pueden ayudar a minimizar la deformación.
- Destello:El flash ocurre cuando el exceso de material fluye hacia la línea de partición del molde, lo que resulta en proyecciones delgadas no deseadas o material adicional en la pieza final. Se puede prevenir eficazmente el rebaba asegurando un diseño de molde adecuado, incluida la aplicación de una fuerza de sujeción adecuada, una alineación precisa y el uso de técnicas de ventilación adecuadas. La optimización de los parámetros del proceso, como la presión de inyección, la temperatura y el tiempo de ciclo, reduce el flash.
- Tiro corto:Un disparo rápido ocurre cuando el material inyectado no llena la cavidad del molde, lo que da como resultado una pieza incompleta. La selección adecuada del material, la garantía de una temperatura y viscosidad de fusión adecuadas y el mantenimiento de la presión y el tiempo de inyección adecuados son esenciales para evitar fotografías cortas. Además, verificar que el diseño del molde tenga un tamaño suficiente de canales y compuertas y una ventilación adecuada puede ayudar a evitar disparos rápidos.
- Líneas de soldadura:Las líneas de soldadura se producen cuando dos o más frentes de flujo de material fundido se encuentran y se solidifican, lo que da como resultado una línea o marca visible en la superficie de la pieza. Un buen diseño de compuerta y corredor, temperatura de fusión óptima, velocidad de inyección y ajuste del flujo de material y la geometría de la pieza pueden minimizar las líneas de soldadura. El análisis del flujo del molde y la optimización de la ubicación de las puertas también pueden ayudar a prevenir o mitigar las líneas de soldadura.
- Quemaduras:Las marcas de quemaduras son decoloraciones o manchas negras en la superficie de la pieza moldeada causadas por calor excesivo o sobrecalentamiento del material. Evitar la temperatura de fusión extrema, usar los canales de enfriamiento apropiados y optimizar el tiempo del ciclo puede ayudar a prevenir las marcas de quemaduras. La ventilación adecuada, el diseño adecuado de la compuerta y el control de la temperatura del molde también contribuyen a minimizar las marcas de quemaduras.
Operaciones posteriores al moldeado: acabado y ensamblaje
Después del moldeo por inyección, muchas piezas moldeadas pueden requerir operaciones adicionales de acabado y ensamblaje para lograr el producto final deseado. Estas operaciones posteriores al moldeo pueden incluir:
- Guarnición:Retire cualquier exceso de material o tapajuntas alrededor de la pieza moldeada con herramientas de recorte o corte.
- Tratamiento superficial:Mejorar la apariencia o la funcionalidad de la superficie de la pieza utilizando diversas técnicas, como pintura, revestimiento o texturizado.
- Asamblea:Unir varias piezas moldeadas o agregar componentes como sujetadores, insertos o etiquetas para completar el producto final.
- Pruebas:Verificación de la calidad y la funcionalidad de las piezas a través de varios métodos de prueba, como análisis dimensional, pruebas de propiedades del material o pruebas de rendimiento.
- Embalaje y envío:Embalaje y etiquetado adecuados del producto terminado para su envío a los clientes o usuarios finales.
La selección de operaciones posteriores al moldeo depende de la aplicación específica y las características deseadas del producto final. La estrecha colaboración entre los expertos en moldeo por inyección, los especialistas en acabado y montaje y el cliente es crucial para lograr la calidad y funcionalidad absolutas deseadas del producto. La planificación adecuada y la integración de las operaciones posteriores al moldeado en el proceso de fabricación pueden ayudar a garantizar una producción eficiente y la entrega oportuna de productos de alta calidad.
Moldeo por inyección frente a otros procesos de fabricación de plástico
Cada proceso de fabricación de plástico tiene ventajas y limitaciones, lo que los hace aptos para diferentes aplicaciones.
- Moldeo por inyección: El moldeo por inyección es un proceso de fabricación muy versátil y ampliamente utilizado para producir piezas de plástico. Ofrece ventajas como alta eficiencia de producción, replicación precisa de piezas y la capacidad de crear geometrías complejas. El moldeo por inyección es adecuado para ciclos de producción de gran volumen y permite utilizar una amplia gama de materiales termoplásticos. Ofrece una precisión dimensional y un acabado superficial excelentes, lo que lo hace ideal para diversas industrias, como la automotriz, la de bienes de consumo y la de dispositivos médicos.
- Moldeo por soplado: El moldeo por soplado es un proceso que se utiliza principalmente para producir piezas de plástico huecas, como botellas, recipientes y componentes de automóviles. Implica derretir plástico e inflarlo en una cavidad de molde, creando la forma deseada. El moldeo por soplado es adecuado para la producción de alto volumen y puede producir piezas grandes y livianas con un espesor de pared uniforme. Sin embargo, está limitado en términos de complejidad de la pieza y selección de materiales en comparación con el moldeo por inyección.
- Termoformado:El termoformado es un proceso utilizado para producir piezas de plástico calentando una lámina termoplástica y dándole forma mediante moldes o formación al vacío. Encuentra un uso común en envases, productos desechables y productos a gran escala, como bandejas y cubiertas. El termoformado ofrece una producción rentable para piezas grandes y permite la creación rápida de prototipos. Sin embargo, tiene limitaciones con respecto a la complejidad de las piezas, la selección de materiales y la precisión dimensional en comparación con el moldeo por inyección.
- Extrusión:La extrusión es un proceso continuo para producir perfiles, láminas, tubos y películas de plástico. Se trata de derretir resina plástica y forzarla a través de un troquel para crear la forma deseada. La extrusión es adecuada para producir longitudes largas y continuas de productos de plástico con una sección transversal uniforme. Si bien la extrusión ofrece altas tasas de producción y rentabilidad, está limitada en términos de geometrías de piezas complejas y control dimensional preciso en comparación con el moldeo por inyección.
- Moldeo por compresión:El moldeo por compresión consiste en colocar una cantidad previamente medida de material termoendurecible en una cavidad de molde caliente y comprimirlo a alta presión hasta que se cure. Encuentra un uso común en la producción de piezas con alta resistencia y estabilidad dimensional, como componentes automotrices y aislamiento eléctrico. El moldeo por compresión ofrece una buena consistencia de la pieza, alta eficiencia de producción y la capacidad de utilizar una amplia gama de materiales. Sin embargo, está limitado en términos de complejidad de la pieza y tiempo de ciclo en comparación con el moldeo por inyección.
Aplicaciones del moldeo por inyección de termoplásticos
Varias industrias utilizan ampliamente el moldeo por inyección de termoplásticos debido a su versatilidad, eficiencia y rentabilidad. Algunas de las aplicaciones del moldeo por inyección de termoplásticos incluyen:
- Industria automotriz: La industria automotriz utiliza ampliamente el moldeo por inyección de termoplásticos para fabricar varios componentes, que incluyen molduras interiores y exteriores, tableros, paneles de puertas, parachoques y conectores eléctricos. El proceso permite la replicación precisa de piezas, geometrías complejas y materiales livianos, lo que mejora la eficiencia del combustible y la flexibilidad del diseño.
- Bienes de consumo:El moldeo por inyección encuentra amplias aplicaciones en la producción de bienes de consumo, como electrodomésticos, dispositivos electrónicos, envases y juguetes. El proceso permite la producción en masa de productos duraderos y de alta calidad con dimensiones y acabados superficiales consistentes. También permite opciones de personalización e iteraciones rápidas de productos.
- Dispositivos médicos:El moldeo por inyección juega un papel crucial en la industria médica para producir una amplia gama de dispositivos, incluidas jeringas, instrumentos quirúrgicos, componentes implantables y sistemas de administración de fármacos. El proceso asegura la producción de piezas estériles, precisas y biocompatibles que cumplen con los estrictos requisitos normativos del sector sanitario.
- Industria Electrónica y Eléctrica:La industria electrónica utiliza el moldeo por inyección para fabricar conectores eléctricos, gabinetes, interruptores y otros componentes. El proceso ofrece una alta precisión dimensional, un excelente acabado superficial y la capacidad de incorporar funciones como el moldeado por inserción y el sobremoldeado, lo que permite una producción eficiente de ensamblajes electrónicos complejos.
- Industria del embalaje:Diversas industrias, incluidas las de alimentos y bebidas, productos farmacéuticos y cuidado personal, suelen utilizar el moldeo por inyección para producir envases, tapas, cierres y botellas de plástico. El proceso permite la creación de soluciones de embalaje ligeras, duraderas y estéticamente atractivas con ciclos de fabricación eficientes.
- Industria aeroespacial:El sector aeroespacial emplea el moldeo por inyección para la fabricación de componentes ligeros y de alto rendimiento, como conductos de aire, soportes, paneles interiores y piezas estructurales. El proceso permite el uso de materiales avanzados y geometrías de piezas complejas, lo que contribuye a la reducción de peso y mejora la eficiencia del combustible.
Impacto ambiental del moldeo por inyección de termoplásticos
El moldeo por inyección de termoplásticos es un proceso de fabricación popular debido a sus muchos beneficios, pero también es esencial tener en cuenta su impacto ambiental. Aquí hay algunos puntos a considerar:
- Eficiencia material:El moldeo por inyección de termoplásticos promueve la eficiencia del material al minimizar el desperdicio. El proceso utiliza un control preciso sobre la cantidad de material inyectado en el molde, lo que reduce la necesidad de exceso de material. Los fabricantes también pueden emplear técnicas de rectificado y reciclaje para reutilizar chatarra o piezas rechazadas, lo que reduce aún más el desperdicio de material.
- Consumo de energía:Los fabricantes diseñan máquinas de moldeo por inyección para que sean energéticamente eficientes, con modelos modernos que incorporan tecnologías avanzadas como servomotores y variadores de velocidad. Estas características optimizan el uso de energía al reducir el consumo de energía durante el moldeo, lo que resulta en menores requisitos de energía y un menor impacto ambiental.
- Gestión de residuos:Al tiempo que minimizan el desperdicio de material, los fabricantes deben implementar prácticas adecuadas de manejo de desperdicios para manejar materiales sobrantes, bebederos o canales. Los fabricantes pueden establecer programas de reciclaje para recolectar y reutilizar los desechos plásticos generados durante el moldeo por inyección, reduciendo así los desechos enviados a los vertederos.
- Reduccion de emisiones: El moldeo por inyección de termoplásticos generalmente genera menos emisiones que otros procesos de fabricación. Los fabricantes pueden reducir las emisiones mediante el uso de materiales ecológicos, la implementación de equipos de bajo consumo y el empleo de sistemas avanzados de escape y filtración para capturar las emisiones liberadas.
- Opciones de materiales sostenibles:La selección de materiales termoplásticos puede afectar significativamente la sustentabilidad ambiental del moldeo por inyección. Optar por plásticos biodegradables o de base biológica, así como por materiales reciclados o reciclables, puede ayudar a reducir la huella ecológica general del proceso.
Consideraciones del ciclo de vida: considerar el ciclo de vida completo del producto moldeado es esencial para evaluar su impacto ambiental. Durante las etapas de diseño y selección de materiales, los fabricantes deben considerar factores como la durabilidad de la pieza, su reciclabilidad y el potencial de eliminación o reutilización al final de su vida útil.
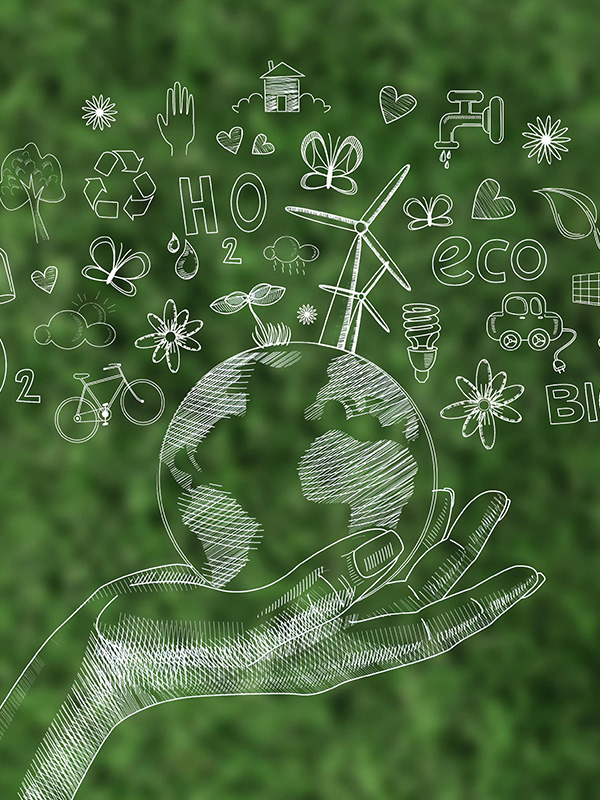
Futuro del moldeo por inyección de termoplásticos
El futuro del moldeo por inyección de termoplásticos parece prometedor, con avances continuos en tecnología y una mayor demanda de piezas de precisión de alta calidad en diversas industrias. Algunos de los desarrollos clave que se esperan para los próximos años incluyen:
- Mayor uso de la automatización y la robótica para mejorar la eficiencia y reducir los costos.
- Los esfuerzos se centran en el desarrollo de nuevos materiales y procesos para mejorar el rendimiento de las piezas y habilitar nuevas aplicaciones.
- Es una adopción creciente de prácticas sostenibles, como el uso de materiales reciclados y la optimización del consumo de energía, para reducir el impacto ambiental del moldeo por inyección.
- Mayor integración de tecnologías digitales, como impresión 3D y software de simulación, para mejorar los procesos de diseño y producción.
El mercado global de moldeo por inyección se está expandiendo, particularmente en las economías emergentes, impulsado por la creciente demanda de productos plásticos en varias industrias.
Elección del socio de moldeo por inyección adecuado
Elegir el socio de moldeo por inyección adecuado es crucial para el éxito de su proyecto. Tómese el tiempo para evaluar múltiples opciones, realizar visitas al sitio y participar en debates exhaustivos para garantizar una asociación compatible y duradera.
- Conocimientos y experiencia:Busque un socio de moldeo por inyección con amplio conocimiento y experiencia en la industria. Deben tener un historial comprobado de entrega de productos y soluciones de alta calidad a clientes en varios sectores. Considere su comprensión de diferentes materiales, diseños de moldes y procesos de fabricación.
- Capacidades de fabricación: Evalúe las capacidades de fabricación del socio de moldeo por inyección. Asegúrese de que tengan una instalación bien equipada con maquinaria y tecnologías modernas para manejar los requisitos de su proyecto. Tenga en cuenta su capacidad de producción, su capacidad para manejar diferentes tamaños y complejidades de piezas, y su capacidad para cumplir con los plazos y los volúmenes de producción deseados.
- Seguro De Calidad:La calidad es primordial en el moldeo por inyección. Evaluar los sistemas de control de calidad y certificaciones del potencial socio. Busque socios que sigan estrictos estándares de calidad, tengan procesos de inspección sólidos y realicen pruebas exhaustivas para garantizar la calidad y la consistencia de las piezas.
- Soporte de diseño e ingeniería:Un socio confiable de moldeo por inyección debe ofrecer soporte de diseño e ingeniería para optimizar el diseño de su pieza para la fabricación. Deben contar con ingenieros calificados que puedan proporcionar información valiosa sobre la selección de materiales, el diseño de moldes y la optimización de procesos para mejorar la calidad y la eficiencia de las piezas.
- Competitividad de costes:Si bien el costo no debe ser el único factor determinante, es esencial evaluar el precio y la competitividad de costos del socio de moldeo por inyección. Solicite cotizaciones detalladas y considere los costos de herramientas, costos de materiales, costos de mano de obra y cualquier servicio adicional que brinden.
- Comunicación y colaboración:La comunicación y la colaboración efectivas son esenciales para una asociación exitosa. Asegúrese de que el socio de moldeo por inyección tenga buenos canales de comunicación, responda a sus consultas y pueda proporcionar actualizaciones periódicas del proyecto. Un enfoque de colaboración ayudará a garantizar que cumplamos con sus requisitos y abordemos rápidamente cualquier desafío.
- Referencias y reseñas de clientes:Busque referencias de clientes o lea reseñas/testimonios para obtener información sobre las experiencias de otros clientes con el socio de moldeo por inyección. La obtención de esta información puede ayudar a determinar su confiabilidad, rapidez y nivel general de satisfacción del cliente.
Conclusión
El moldeo por inyección de termoplásticos es un método versátil y rentable para fabricar piezas de plástico en grandes cantidades. Su capacidad para producir formas complejas con alta precisión y consistencia se ha convertido en una opción popular para varias industrias, incluidas la automotriz, médica, electrónica y de bienes de consumo. Al comprender los diferentes aspectos del moldeo por inyección de termoplásticos, incluidas sus ventajas, desventajas y consideraciones de diseño, puede tomar decisiones informadas sobre la elección del socio de moldeo por inyección adecuado para sus necesidades comerciales.