Moldeo por inyección de caucho de silicona líquida (LSR)
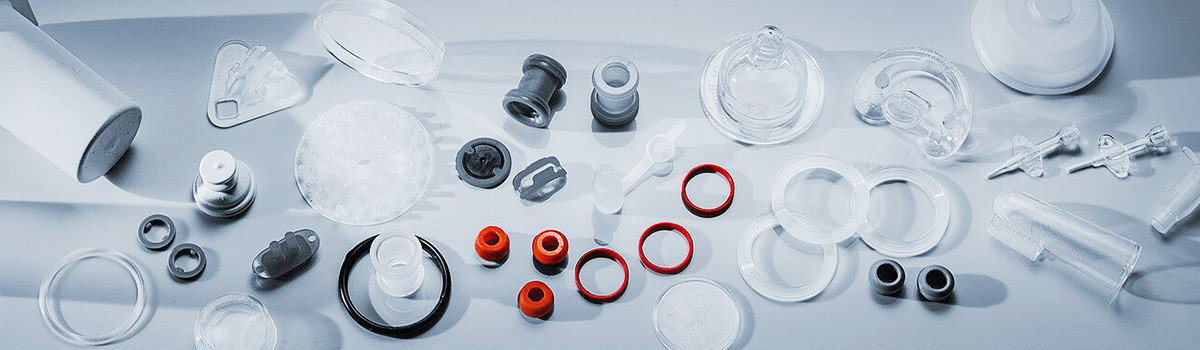
¿Qué es el moldeo por inyección de caucho de silicona líquida (LSR)?
El moldeo por inyección de caucho de silicona líquida (LSR) es un proceso que se utiliza para producir piezas flexibles y duraderas en grandes volúmenes. Durante el proceso son necesarios varios componentes: un inyector, una unidad dosificadora, un tambor de suministro, un mezclador, una boquilla y una abrazadera de molde, entre otros.
El moldeo por inyección de caucho de silicona líquida (LSR) es una tecnología común utilizada para la producción de diferentes productos para aplicaciones médicas y eléctricas, entre otras. Además de las propiedades innatas del material, los parámetros del proceso también son críticos. El moldeo por inyección de LSR es un proceso de varios pasos que se presenta.
El primer paso es la preparación de la mezcla. El LSR generalmente consta de dos componentes, pigmento y aditivos (rellenos, por ejemplo), según las propiedades deseadas del producto final. En este paso, los ingredientes de la mezcla se homogeneizan y se pueden combinar con el sistema de estabilización de temperatura para un mejor control de la temperatura de la silicona (temperatura ambiente o precalentamiento de la silicona).
Hoy en día, el rango de aplicación de los productos de caucho de silicona es cada vez más amplio, y el moldeo por inyección de LSR tiene un papel importante en esta industria.
¿Cómo funciona el moldeo de caucho de silicona líquida?
El moldeo por LSR difiere ligeramente del moldeo por inyección de termoplásticos debido a su flexibilidad. Al igual que una herramienta de aluminio estándar, una herramienta de moldeo LSR se fabrica mediante mecanizado CNC para crear una herramienta de alta temperatura diseñada para soportar el proceso de moldeo LSR. Después del fresado, la herramienta se pule a mano según las especificaciones del cliente, lo que permite seis opciones estándar de acabado superficial.
A partir de ahí, la herramienta terminada se carga en una prensa de moldeo por inyección específica para LSR avanzada que está engranada con precisión para un control exacto del tamaño de la inyección para producir las piezas LSR más uniformes. En Mold-Making, las piezas LSR se extraen manualmente del molde, ya que los pasadores de los inyectores pueden afectar la calidad de la pieza. Los materiales LSR incluyen siliconas estándar y grados específicos para adaptarse a diversas aplicaciones e industrias de piezas, como la médica, la automotriz y la de iluminación. Como el LSR es un polímero termoendurecible, su estado moldeado es permanente: una vez fraguado, no se puede volver a fundir como un termoplástico. Cuando se completa la ejecución, las piezas (o la ejecución de muestra inicial) se empaquetan y se envían poco después.
Aquí vamos a explorarlo, primero, tenemos que hablar sobre el material de caucho de silicona líquida, los puntos principales que debe saber son los siguientes:
El caucho de silicona líquida (LSR) es un excelente aislamiento, adecuado para enchufes electrónicos de alta calidad o alta tecnología.
Los materiales de caucho de silicona líquida (LSR) son adecuados para su uso en entornos de alta o baja temperatura. Las propiedades de aislamiento, las propiedades mecánicas y las propiedades físicas de los materiales permanecen sin cambios a 200 ℃ o tan bajo como -40 ℃.
Es resistente a la gasificación y al envejecimiento, por lo que es adecuado para aplicaciones en exteriores.
El caucho de silicona líquida (LSR) es resistente al aceite, se puede utilizar en la industria minera petrolera. Hay dos modelos: máquina de moldeo por inyección de silicona líquida de doble deslizamiento vertical, máquina de inyección de silicona líquida de deslizamiento simple vertical, que se utiliza para producir todo tipo de productos de caucho de silicona de alta precisión y alta demanda; La máquina de inyección de ángulo de cilindro inferior es la producción de aisladores de suspensión compuestos, aisladores de poste y modelos tradicionales de pararrayos.
Las ventajas del moldeo por inyección LSR (LIM).
El moldeo por inyección LSR (LIM) tiene muchas ventajas. Se compara con el moldeo por compresión de silicona.
El material de caucho de silicona líquida (LSR) es más seguro, el gel de silicona tiene grado alimenticio o grado médico. El moldeo por inyección LSR (LIM) tiene mayor precisión, puede fabricar piezas de caucho de silicona de muy alta precisión. Además, tiene una línea de separación muy fina y un pequeño destello.
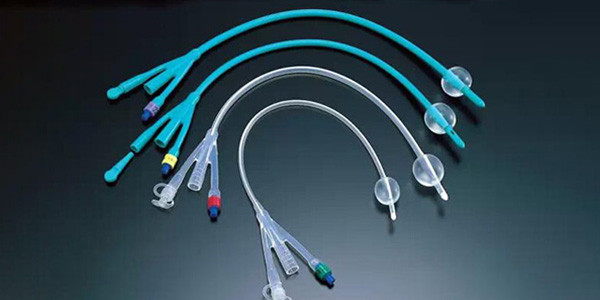
Ventajas de las piezas moldeadas LSR
Diseño ilimitado – Permite la producción de geometrías de piezas y soluciones técnicas que de otro modo no serían posibles
Consistente – Proporciona la más alta consistencia en la dimensión del producto, la precisión y la calidad general
Puro – La silicona es uno de los biomateriales más probados con una larga historia de uso seguro
Preciso – Conceptos de diseño de herramientas sin destellos y sin desperdicio para piezas que pesan desde 0.002 gramos hasta varios cientos de gramos
Confiable – Utilizando la última tecnología en maquinaria, utillaje y automatización
Quality – Nivel de calidad de cero defectos a través de controles en proceso
Rápido – Permite la producción de mayor volumen debido a tiempos de ciclo cortos, de varios miles a millones
Fácil – Utilizando técnicas de procesamiento y producción de última generación en salas limpias de clase 7 y 8
Económico – Ofrece el costo total de propiedad (TCO) más bajo
Moldeo por inyección LSR
Tecnología innovadora que satisface las necesidades del cliente:
El caucho de silicona líquida (LSR) se puede procesar en un proceso de moldeo por inyección de líquido (LIM). La materia prima líquida se mezcla a partir de dos componentes separados en una proporción de 1:1 y se inyecta a través de un sistema de canal frío en un molde caliente. El curado se lleva a cabo en cuestión de segundos, lo que ofrece la ventaja de ciclos rápidos y producción de grandes cantidades.
Debido a la flexibilidad en el diseño y las herramientas, el moldeo por inyección LSR es ideal para producir geometrías complejas y puede consolidar varias características funcionales en una sola pieza. También ofrece ventajas significativas en términos de confiabilidad del producto y costo total de propiedad.
Proceso de moldeo por inyección de caucho de silicona líquida LSR
La máquina de moldeo por inyección de caucho de silicona líquida DJmolding parece una máquina de moldeo por inyección de termoplásticos. Ambos tipos de prensas utilizan las mismas piezas básicas de máquina, unidad de cierre y unidad de inyección.
La unidad de sujeción de la máquina de moldeo por inyección LSR es idéntica para las máquinas termoplásticas y de caucho de silicona líquida. Las máquinas de moldeo por inyección de silicona suelen tener un ariete hidráulico y pueden tener una palanca hidráulica. Algunas prensas están diseñadas con un pistón eléctrico con palanca. A diferencia de las altas presiones utilizadas para moldear piezas termoplásticas, la presión de inyección de silicona líquida está en el rango de 800 PSI. El propósito de la abrazadera es contener la fuerza de expansión del material de silicona, manteniendo el molde cerrado mientras la silicona se cura.
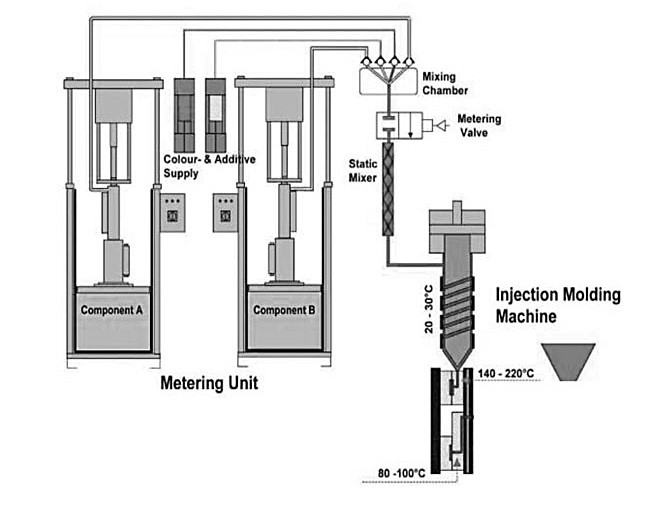
La unidad de inyección de silicona líquida se enfría con un cilindro y una boquilla enfriados por agua para evitar que la silicona líquida se cure. Las unidades de inyección de termoplástico funcionan en sentido contrario, necesitan que el cilindro y la boquilla se calienten a 300 °F o más para mantener el material en movimiento. Las unidades de moldeo por inyección de líquido también funcionan a presiones más bajas (menos de 1,000 PSI), mientras que sus contrapartes termoplásticas funcionan a decenas de miles de PSI.
La silicona líquida generalmente se proporciona en baldes de 5 galones o tambores de 55 galones. Hay una parte A y una parte B. Los colorantes vienen en forma de dispersiones y normalmente tienen un 1-3% en peso de silicona mezclada. La unidad de rociado de silicona bombea una parte de silicona A y una parte B de silicona a través de mangueras separadas al mezclador estático. Además, el color se bombea al mezclador estático a través de otra manguera. A continuación, los componentes mezclados se introducen en la garganta del cilindro de moldeo por inyección a través de una válvula de cierre.
DJmolding es un fabricante profesional de moldeo por inyección de caucho de silicona líquida (LSR) y piezas de caucho de silicona líquida de China.
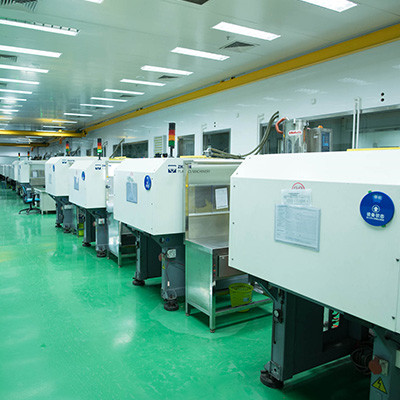
Taller de inyección de caucho de silicona líquida
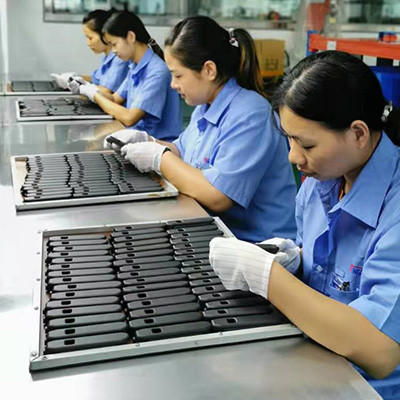
Control de calidad de productos de inyección LSR
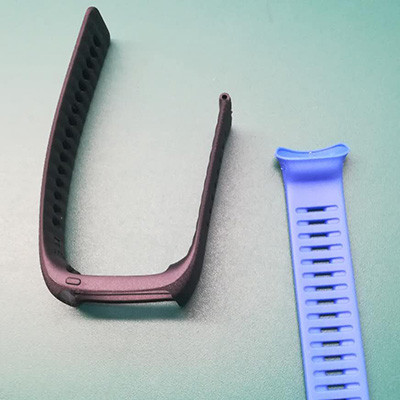
Productos LSR
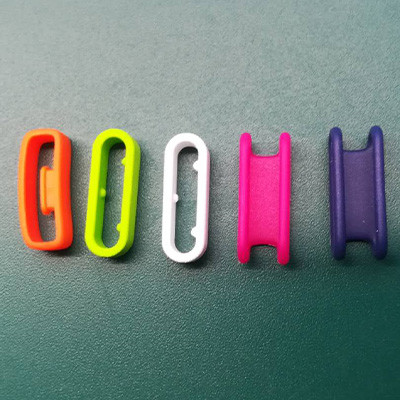
Productos LSR
Nuestro proceso de moldeo de caucho de silicona líquida produce prototipos personalizados y piezas de producción de uso final en 15 días o menos. Usamos moldes de aluminio que ofrecen herramientas rentables y ciclos de fabricación acelerados, y almacenamos varios grados y durómetros de materiales LSR.
Brindando la más alta consistencia en dimensiones, precisión, calidad general.
Nuestro enfoque holístico para el moldeo de caucho de silicona líquida se basa en asociarnos con los clientes para desarrollar soluciones innovadoras basadas en especificaciones y requisitos únicos.
El moldeo por inyección de caucho de silicona líquida (LSR) es un proceso de fabricación que consiste en inyectar caucho de silicona líquida en un molde para crear varios productos. LSR es un material versátil que se ha vuelto cada vez más popular debido a sus propiedades únicas, que incluyen biocompatibilidad, estabilidad térmica y resistencia química. En este artículo, discutiremos los beneficios del moldeo por inyección LSR y exploraremos las diversas aplicaciones de esta tecnología.
¿Cómo funciona el moldeo por inyección LSR?
El moldeo por inyección de LSR (caucho de silicona líquida) es un proceso de fabricación que produce piezas de caucho de silicona de alta calidad y precisión. Es beneficioso para crear formas y diseños complejos con excelente detalle y consistencia. El proceso consiste en inyectar caucho de silicona líquida en la cavidad de un molde, lo que le permite curarse y solidificarse en la forma deseada. Aquí hay una breve descripción de cómo funciona el moldeo por inyección LSR:
Preparación del molde: El proceso comienza con la preparación del molde. El molde generalmente consta de dos mitades, un lado de inyección y un lado de sujeción, que encajan para crear una cavidad para la silicona. Después del curado, el molde se limpia y se recubre con un agente de liberación para facilitar la extracción de la pieza.
Preparación de silicona: El caucho de silicona líquida es un material de dos componentes que consta de una base de silicona y un agente de curado. Estos componentes se mezclan en una proporción precisa. La mezcla se desgasifica para eliminar cualquier burbuja de aire que pueda afectar la calidad de la pieza final.
Inyección: El caucho de silicona líquido mezclado y desgasificado se transfiere a una unidad de inyección. La unidad de inyección calienta el material a una temperatura específica para reducir su viscosidad y facilitar su flujo. El material se inyecta en la cavidad del molde a través de una boquilla o bebedero.
Curado: Una vez que el caucho de silicona líquida se inyecta en la cavidad del molde, comienza a curar. El proceso de curado normalmente se inicia con calor, aunque algunos moldes pueden utilizar otros métodos, como la luz ultravioleta. El calor hace que la silicona se entrecruce y se solidifique, formando la cavidad del molde. El tiempo de curado varía según el diseño de la pieza y el material de silicona.
Enfriamiento y extracción de piezas: después del proceso de curado, el molde se enfría para permitir que la silicona se asiente por completo. El tiempo de enfriamiento puede variar, pero normalmente es más corto que el tiempo de curado. Una vez enfriado, se abre el molde y se retira la pieza terminada. La posición puede requerir pasos adicionales de procesamiento posterior, como recortar el exceso de material o inspeccionar cualquier defecto.
El moldeo por inyección de LSR ofrece varias ventajas, incluida la producción de geometrías intrincadas y complejas, excelente consistencia de piezas, alta precisión y resistencia a temperaturas extremas, productos químicos y envejecimiento. Se usa comúnmente en varias industrias médica, automotriz, electrónica y de productos de consumo.
Es importante tener en cuenta que esta es una explicación simplificada del proceso de moldeo por inyección de LSR y que la operación real puede variar según los requisitos específicos del equipo, los materiales y las piezas.
Ventajas del moldeo por inyección LSR
El moldeo por inyección de LSR (caucho de silicona líquida) es un proceso de fabricación versátil que ofrece varias ventajas sobre los métodos de moldeo tradicionales. El moldeo por inyección de LSR consiste en inyectar silicona líquida en un molde y curarla en una forma sólida para crear un producto terminado. Estas son algunas de las principales ventajas del moldeo por inyección LSR:
Precisión y Consistencia
El moldeo por inyección LSR ofrece una precisión y consistencia excepcionales en la creación de piezas complejas e intrincadas con detalles finos. La silicona líquida se inyecta en un molde a alta presión, llenando incluso las grietas y esquinas más pequeñas para producir piezas altamente complejas. Además, el moldeado LSR permite una mayor consistencia y repetibilidad, lo que reduce la posibilidad de defectos e inconsistencias en el producto final.
Piezas de alta calidad
El moldeo por inyección de LSR puede producir piezas duraderas y de alta calidad resistentes al desgaste, al calor y a la radiación ultravioleta. Los materiales LSR tienen excelentes propiedades físicas, que incluyen alta elasticidad, baja deformación permanente por compresión y resistencia a temperaturas extremas. Esto hace que el moldeo por inyección de LSR sea una opción ideal para producir piezas que requieren alta precisión y durabilidad, como dispositivos médicos, componentes automotrices y productos de consumo.
Económico
El moldeo por inyección de LSR puede ser un método de fabricación rentable para producir piezas grandes. La alta precisión y consistencia del proceso ayudan a reducir el desperdicio y el material de desecho, mientras que los bajos requisitos de mano de obra y los tiempos de producción eficientes minimizan los costos de fabricación. Además, los materiales LSR tienen una larga vida útil, lo que reduce la necesidad de reemplazar o reparar piezas con frecuencia.
Versatilidad
El moldeo por inyección de LSR puede producir varias piezas con diferentes tamaños, formas y geometrías. La silicona líquida se puede moldear en formas intrincadas y complejas con detalles refinados, lo que la hace ideal para producir piezas que requieren alta precisión y exactitud. Además, el moldeo por inyección de LSR puede tener características con diversos grados de dureza y suavidad, lo que permite un diseño de producto y una flexibilidad de funciones más extraordinarios.
Tiempos de ciclo reducidos
El moldeo por inyección de LSR tiene tiempos de ciclo rápidos, lo que permite producir grandes cantidades de piezas en un período relativamente corto. La silicona líquida se inyecta en el molde y se cura en forma sólida en segundos, lo que la convierte en una opción ideal para series de producción de alto volumen.
Baja Generación de Residuos
El moldeo por inyección de LSR produce muy poco material de desecho, ya que la silicona líquida se inyecta directamente en el molde y se cura para obtener la forma deseada. Esto contrasta con otros procesos de fabricación, como el mecanizado o la fundición, que generan un importante material de desecho. Además, los materiales LSR se pueden reciclar y reutilizar, lo que reduce la necesidad de nuevos materiales y reduce la generación de desechos.
Seguridad mejorada
Los materiales LSR generalmente están libres de químicos dañinos como ftalatos, BPA y PVC, lo que los hace más seguros para los trabajadores y los consumidores. Además, el proceso de baja temperatura utilizado en el moldeo por inyección de LSR no requiere solventes dañinos u otros químicos, lo que reduce el riesgo de exposición a materiales peligrosos.
Tiempo de comercialización reducido
El moldeo por inyección de LSR puede reducir el tiempo de comercialización de nuevos productos, ya que permite la creación rápida de prototipos y ciclos de producción rápidos. La alta precisión y consistencia del proceso ayudan a garantizar que el producto final cumpla con las especificaciones deseadas, lo que reduce la necesidad de múltiples rondas de creación de prototipos y pruebas.
Automatización
El moldeo por inyección de LSR se puede automatizar en gran medida, lo que reduce la necesidad de mano de obra y reduce el consumo de energía. Además, la automatización puede mejorar la eficiencia, reducir los costos de mano de obra y mejorar la consistencia y la calidad del producto final.
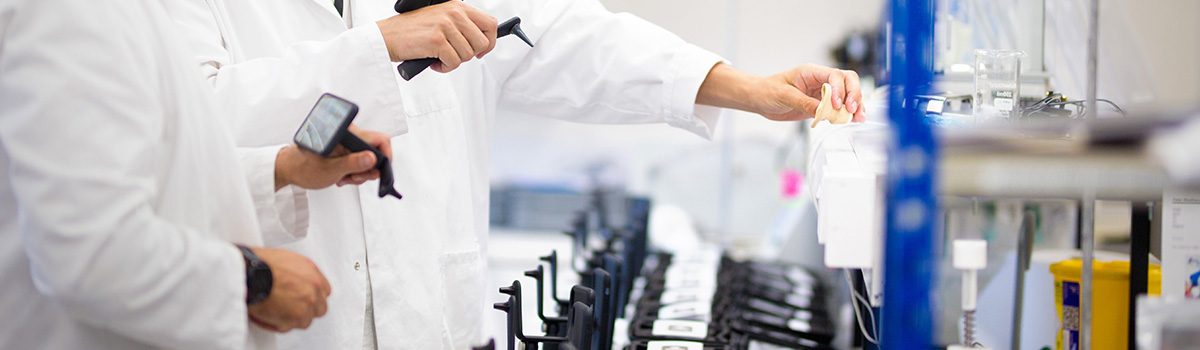
Desventajas del moldeo por inyección LSR
Si bien el moldeo por inyección de LSR (caucho de silicona líquida) ofrece numerosas ventajas, también existen algunas desventajas a tener en cuenta al decidir si utilizar este proceso de fabricación. Estas son algunas de las principales desventajas del moldeo por inyección LSR:
Alta Inversión Inicial
Una de las principales desventajas del moldeo por inyección LSR es la alta inversión inicial requerida para configurar los equipos y moldes. Las máquinas y herramientas de moldeo por inyección LSR pueden ser costosas, especialmente para moldes personalizados o series de producción más pequeñas. Esto puede hacer que el moldeo por inyección de LSR sea menos rentable para empresas con presupuestos reducidos o productos con demanda limitada.
Selección limitada de materiales
Si bien los materiales LSR ofrecen excelentes propiedades físicas, su selección de materiales es limitada. A diferencia de los termoplásticos tradicionales, hay disponible una cantidad limitada de materiales a base de silicona para su uso en el moldeo por inyección de LSR. Encontrar materiales adecuados para aplicaciones o productos específicos puede ser un desafío.
Tiempos de curado más largos
El moldeo por inyección de LSR requiere tiempos de curado más prolongados que los procesos de moldeo por inyección tradicionales. La silicona líquida necesita tiempo para curarse y solidificarse, lo que puede resultar en tiempos de producción más prolongados y una eficiencia reducida. Además, los tiempos de curación más prolongados pueden dificultar la producción de ciertas piezas con geometrías intrincadas o complejas.
Conjunto de habilidades especializadas requeridas
El moldeo por inyección de LSR requiere conocimientos y experiencia especializados, incluida una comprensión profunda de las propiedades y el comportamiento de la silicona líquida. Esto puede dificultar que las empresas encuentren personal calificado para operar y mantener el equipo, particularmente en áreas donde el moldeo por inyección de LSR es menos común.
Desafíos de moldeo
El moldeo por inyección de LSR puede presentar algunos desafíos que deben abordarse para garantizar la producción de piezas de alta calidad. Por ejemplo, la silicona líquida puede ser propensa a destellos o rebabas, lo que afecta la calidad del producto final. Además, es posible que se requieran agentes de desmoldeo para retirar las piezas del molde, lo que puede afectar el acabado de la superficie y las propiedades mecánicas del producto final.
Acabados de superficie limitados
El moldeo por inyección de LSR está limitado en cuanto a acabados superficiales, ya que la silicona líquida es incompatible con ciertos recubrimientos o acabados. Esto puede dificultar el logro de las propiedades estéticas o funcionales deseadas para productos o aplicaciones específicos.
Opciones de color limitadas
El moldeo por inyección de LSR también está limitado en cuanto a opciones de color, ya que el material de silicona líquida suele ser translúcido u opaco. Si bien hay algunos aditivos de color disponibles, puede ser difícil incorporarlos al material sin afectar las propiedades físicas o la consistencia del producto final.
Potencial de contaminación de piezas
El moldeo por inyección de LSR puede presentar un riesgo de contaminación si el equipo o los moldes no se mantienen o limpian adecuadamente. La contaminación puede afectar las propiedades físicas del producto final y provocar defectos o fallas con el tiempo.
Precisión y exactitud en el moldeo por inyección LSR
La precisión y la exactitud son aspectos esenciales del moldeo por inyección de LSR (caucho de silicona líquida), que produce piezas de caucho de silicona de alta calidad con tolerancias estrictas y especificaciones exactas. Estos son algunos factores clave que contribuyen a la precisión y la exactitud en el moldeo por inyección de LSR:
- Diseño y construcción de moldes: el molde es un componente fundamental del proceso de moldeo por inyección de LSR, ya que determina la forma y las dimensiones finales de la pieza. El molde debe diseñarse y construirse con precisión para garantizar que la última pieza cumpla con las especificaciones deseadas. El molde debe estar hecho de materiales de alta calidad y construido con tolerancias estrictas para minimizar los errores y garantizar la precisión.
- Control de la unidad de inyección: La unidad de inyección controla el flujo de caucho de silicona líquida en el molde. El control preciso de la unidad de inyección es fundamental para lograr piezas precisas y consistentes. La unidad de inyección debe calibrarse y controlarse para garantizar que el material se inyecte en la cavidad del molde con la velocidad, la presión y el volumen correctos.
- Control de temperatura: El control de temperatura es un factor crítico en el proceso de moldeo por inyección de LSR, ya que afecta la viscosidad del material y el tiempo de curado. La temperatura debe controlarse cuidadosamente para garantizar que el material fluya suavemente hacia el molde y que el proceso de curado ocurra a la velocidad correcta.
- Calidad del material: La calidad del material LSR es fundamental para lograr precisión y exactitud en la pieza final. Para garantizar un curado y una consistencia adecuados, el material debe estar libre de impurezas y mezclado en la proporción correcta.
- Posprocesamiento: los pasos de posprocesamiento, como el recorte y la inspección, son esenciales para lograr precisión y exactitud en el moldeo por inyección de LSR. La pieza debe recortarse a las dimensiones correctas e inspeccionarse en busca de defectos o imperfecciones.
El moldeo por inyección LSR ofrece una excelente precisión y exactitud, lo que permite la creación de piezas con tolerancias estrictas y especificaciones exactas. Puede producir piezas con una calidad uniforme y variaciones mínimas de una pieza a otra. Esto lo convierte en una opción ideal para aplicaciones donde la precisión y la exactitud son fundamentales, como en dispositivos médicos, componentes de automóviles y productos electrónicos.
Tiempos de producción más rápidos
El moldeo por inyección de caucho de silicona líquida (LSR) es un proceso de fabricación popular que produce productos de silicona de alta calidad con excelentes propiedades como resistencia química, resistencia a la temperatura y biocompatibilidad. Sin embargo, los tiempos de producción para el moldeo por inyección de LSR a veces pueden ser lentos, lo que puede retrasar el proceso de fabricación y aumentar los costos. Aquí hay algunas formas de mejorar los tiempos de producción del moldeo por inyección LSR:
- Utilice una máquina de moldeo por inyección eficiente: Elegir una máquina adecuada es crucial para acelerar la producción. Busque un dispositivo que pueda inyectar LSR rápidamente sin sacrificar la calidad. Considere usar una máquina de alta velocidad de inyección, reduciendo el tiempo de ciclo y mejorando la eficiencia de producción.
- Optimice el diseño del molde: el diseño del molde también es un factor esencial que afecta el tiempo de producción del moldeo por inyección LSR. Optimice el diseño del molde para garantizar que el LSR se inyecte de manera eficiente y uniforme. Considere usar un molde con un tamaño de entrada más grande para mejorar el flujo del LSR y reducir el tiempo del ciclo.
- Utilice un sistema de canal caliente: un sistema de canal caliente puede mejorar la eficiencia del moldeo por inyección de LSR al mantener el LSR a la temperatura ideal durante todo el proceso de inyección. Esto puede reducir el tiempo del ciclo y mejorar la calidad del producto final.
- Precaliente el LSR: precalentar el LSR antes de la inyección también puede ayudar a reducir el tiempo de producción. Precalentar el LSR puede mejorar su flujo y reducir el tiempo de inyección, lo que conduce a tiempos de ciclo más rápidos y una mayor eficiencia.
- Reduzca el tiempo de curado: el tiempo de curado de LSR se puede reducir aumentando la temperatura de curado o usando un agente de curado más rápido. Sin embargo, es esencial mantener la calidad del producto final mientras se reduce el tiempo de curado.
Fabricación rentable
El moldeo por inyección de caucho de silicona líquida (LSR) es un proceso de fabricación popular para producir productos de silicona de alta calidad. Sin embargo, el costo del moldeo por inyección de LSR puede preocupar a los fabricantes, principalmente cuando se producen grandes cantidades. Aquí hay algunas formas de hacer que el moldeo por inyección de LSR sea más rentable:
- Optimice el diseño del producto: el diseño del producto puede afectar significativamente el costo del moldeo por inyección de LSR. Al optimizar el diseño, los fabricantes pueden reducir la cantidad de material utilizado, lo que puede reducir el costo total de producción. Además, la simplificación del procedimiento puede reducir la complejidad del molde, lo que reduce los costos de herramientas.
- Use procesos automatizados: el uso de procesos automatizados puede mejorar la eficiencia del moldeo por inyección de LSR y reducir los costos de mano de obra. Los procesos automatizados, como el manejo robótico y la alimentación automática de materiales, pueden reducir el tiempo del ciclo y mejorar la productividad general.
- Use un molde de alta calidad: un molde de alta calidad puede mejorar la eficiencia del moldeo por inyección de LSR y reducir el desperdicio. El uso de un molde duradero y de alta precisión puede reducir la necesidad de reparaciones o reemplazos frecuentes, lo que ahorra dinero a largo plazo.
- Optimice el proceso de producción: la optimización del proceso de producción puede reducir los desechos y mejorar la eficiencia, reduciendo los costos. Esto puede incluir la optimización de los parámetros de moldeo por inyección, como la velocidad de inyección, la temperatura y la presión, para minimizar el desperdicio de material y reducir el tiempo del ciclo.
- Reduzca el desperdicio de material: Reducir el desperdicio de material puede reducir significativamente el costo del moldeo por inyección de LSR. Esto se puede lograr mediante el uso de un sistema de medición de precisión para controlar el material utilizado, asegurando que el molde esté adecuadamente diseñado y optimizado para minimizar el exceso de material y reciclando el material adicional para uso futuro.
Acabados de superficie de alta calidad
El moldeo por inyección de caucho de silicona líquida (LSR) es un proceso de fabricación popular para producir productos de silicona de alta calidad con excelentes propiedades como resistencia a la temperatura, resistencia química y biocompatibilidad. Además de estas propiedades, lograr un acabado superficial de alta calidad es fundamental para muchas aplicaciones. Aquí hay algunas formas de lograr acabados superficiales de alta calidad en el moldeo por inyección LSR:
- Utilice un molde de alta calidad: un molde de alta calidad es crucial para lograr un acabado superficial de alta calidad. El molde debe estar hecho de materiales de alta calidad y tener un acabado superficial liso. Además, el molde debe diseñarse con ventilación adecuada para evitar la formación de burbujas de aire, que pueden afectar negativamente el acabado de la superficie.
- Use un material LSR de alta calidad: el uso de un material LSR de alta calidad también puede mejorar el acabado de la superficie. Los materiales LSR de alta calidad están formulados para tener una baja viscosidad, lo que puede mejorar el flujo del material y reducir la aparición de marcas de flujo y otras imperfecciones.
- Optimice los parámetros de moldeo por inyección: la optimización de parámetros como la temperatura, la velocidad de inyección y la presión también puede mejorar el acabado de la superficie. La velocidad de inyección debe optimizarse para evitar cualquier acumulación de material o rayas. La temperatura y la presión también deben controlarse cuidadosamente para evitar la degradación o deformación del material.
- Utilice procesos posteriores al moldeado: los procesos posteriores al moldeado, como el recorte, el pulido y el recubrimiento, también pueden mejorar el acabado de la superficie de los productos LSR. El recorte puede eliminar cualquier rebaba o exceso de material de la pieza. El pulido puede suavizar cualquier imperfección en la superficie. El revestimiento puede proporcionar una capa adicional de protección y mejorar la apariencia del personaje.
- Realice un mantenimiento regular de la máquina de moldeo por inyección: el mantenimiento regular es esencial para garantizar una producción constante y de alta calidad. El dispositivo debe limpiarse regularmente para evitar la contaminación, y los moldes deben revisarse en busca de signos de desgaste o daño.
Moldeo por inyección de LSR para aplicaciones médicas
El moldeo por inyección de LSR es un proceso de fabricación que consiste en inyectar caucho de silicona líquida (LSR) en un molde para crear un producto final. Este proceso se usa ampliamente en la industria médica debido a las propiedades únicas de LSR, que lo convierten en un material ideal para aplicaciones médicas.
LSR es un material biocompatible e hipoalergénico que no contiene productos químicos nocivos, lo que lo hace seguro para dispositivos e implantes médicos. También es resistente al crecimiento de bacterias y fácil de esterilizar, lo cual es crucial en entornos médicos donde la limpieza y el control de infecciones son primordiales.
El moldeo por inyección de LSR es un proceso exacto y eficiente que permite la creación de piezas médicas complejas e intrincadas con tolerancias estrictas. Esto es importante en aplicaciones médicas donde la precisión y la exactitud son fundamentales, como en la fabricación de dispositivos implantables como catéteres, componentes de marcapasos y articulaciones artificiales.
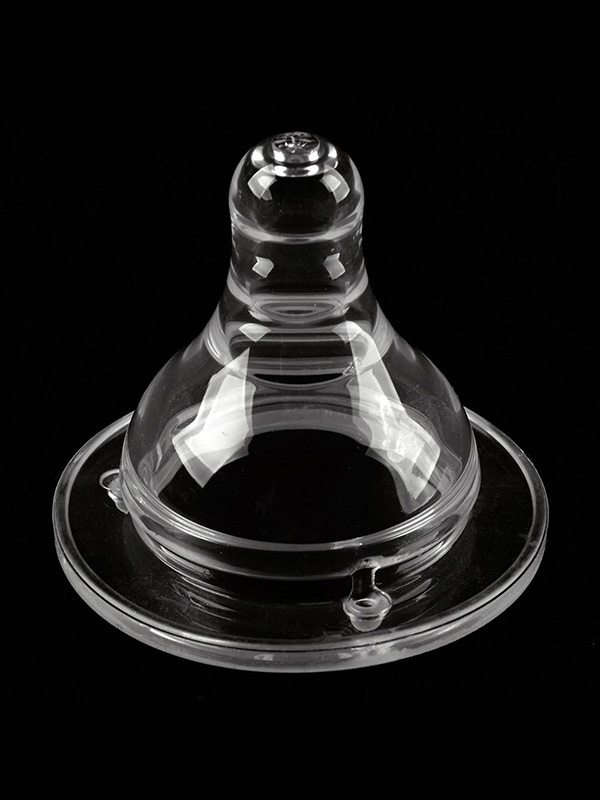
Además de su biocompatibilidad y precisión, LSR tiene excelentes propiedades mecánicas que lo convierten en un material adecuado para aplicaciones médicas. LSR es resistente al desgaste, soporta temperaturas extremas y tiene excelentes propiedades de aislamiento eléctrico. Estas propiedades hacen de LSR un material popular para una amplia gama de aplicaciones médicas, que incluyen:
- Catéteres y tubos: LSR se usa a menudo para fabricar catéteres y tubos debido a su biocompatibilidad, flexibilidad y resistencia a las torceduras.
- Dispositivos implantables: LSR se usa comúnmente para producir dispositivos implantables como articulaciones artificiales, componentes de marcapasos y herramientas quirúrgicas debido a su durabilidad y biocompatibilidad.
- Sellos y juntas médicas: LSR se usa a menudo para fabricarlos debido a su resistencia a temperaturas extremas y su capacidad para mantener sus propiedades a lo largo del tiempo.
El moldeo por inyección de LSR es un proceso muy versátil y eficiente para la fabricación de dispositivos y componentes médicos. Sus propiedades únicas lo convierten en un material ideal para una amplia gama de aplicaciones médicas, y su precisión y exactitud garantizan que los productos cumplan con los más altos estándares de calidad y seguridad.
Uso de LSR en la Industria Automotriz
El caucho de silicona líquida (LSR) se usa cada vez más en la industria automotriz para una amplia gama de aplicaciones debido a las propiedades únicas que lo convierten en un material ideal para piezas de automóviles. LSR es un elastómero sintético formado mediante moldeo por inyección, lo que permite una alta precisión y exactitud en la fabricación de piezas automotrices complejas e intrincadas.
LSR tiene excelentes propiedades mecánicas, lo que lo hace adecuado para piezas de automóviles que requieren durabilidad, resistencia a altas temperaturas y una larga vida útil. LSR es resistente a la abrasión, el desgaste y las roturas, lo que lo hace ideal para piezas de automóviles que experimentan fricción constante, como sellos, juntas y juntas tóricas.
Una de las ventajas más significativas de LSR en la industria automotriz es su capacidad para soportar variaciones extremas de temperatura. LSR puede funcionar de manera eficiente en entornos de alta y baja temperatura, lo que lo convierte en un material ideal para piezas de automóviles expuestas a altas temperaturas, como componentes de motores, sistemas de escape y mangueras de turbocompresores.
Otro beneficio crítico de LSR en la industria automotriz es su capacidad para proporcionar un excelente sellado contra fluidos y gases. LSR es un material altamente resistente que proporciona un sello confiable, incluso bajo alta presión, lo que lo hace ideal para usar en juntas y sellos automotrices.
LSR también tiene excelentes propiedades de aislamiento eléctrico, lo que lo hace ideal para usar en componentes eléctricos en la industria automotriz, como conectores, sensores y sistemas de encendido. LSR puede soportar altos voltajes eléctricos y tiene un bajo riesgo de arcos eléctricos o cortocircuitos, lo que lo convierte en un material confiable para aplicaciones eléctricas.
En general, LSR tiene muchas ventajas que lo convierten en un material ideal para piezas de automóviles, que incluyen durabilidad, resistencia a altas temperaturas, excelentes propiedades de sellado y aislamiento eléctrico. Se espera que el uso de LSR en la industria automotriz crezca en los próximos años a medida que los fabricantes buscan mejorar la confiabilidad, la seguridad y el rendimiento de sus productos al mismo tiempo que reducen los costos y mejoran la eficiencia de la producción.
Aplicaciones de la industria electrónica de LSR
El caucho de silicona líquida (LSR) es un material ampliamente utilizado en la industria electrónica debido a su excelente estabilidad térmica, resistencia química y propiedades de aislamiento eléctrico. Se utiliza en diversas aplicaciones, como encapsulación, sellado y encapsulado de componentes electrónicos.
Una de las principales aplicaciones de LSR en la industria electrónica es la encapsulación de componentes electrónicos, como circuitos integrados (IC), sensores y conectores. La encapsulación protege estos componentes de la humedad, el polvo y otros contaminantes, que pueden causar corrosión y degradar el rendimiento. LSR es un material ideal para la encapsulación debido a su baja viscosidad, alta resistencia al desgarro y excelente adhesión a varios sustratos. También ofrece buenas propiedades dieléctricas, que son esenciales en aplicaciones eléctricas.
LSR también sella los componentes electrónicos para evitar la entrada de humedad y otros contaminantes. El material se puede moldear en formas y tamaños personalizados para adaptarse a varios componentes electrónicos. Los sellos LSR a menudo se usan en entornos hostiles, como aplicaciones marinas y automotrices, donde deben soportar temperaturas extremas y exposición química.
El encapsulado es otra aplicación crítica de LSR en la industria electrónica. El encapsulado consiste en llenar una cavidad alrededor de un componente con un material líquido para protegerlo de factores ambientales como golpes, vibraciones y humedad. LSR es un material ideal para encapsular debido a su baja viscosidad, que le permite fluir fácilmente alrededor de formas complejas, y su alta estabilidad térmica, que asegura que el componente permanezca protegido a altas temperaturas.
LSR también se utiliza para fabricar teclados y botones, componentes estándar en dispositivos electrónicos como controles remotos, calculadoras y teclados. El material altamente personalizable se puede moldear en varias formas y tamaños con diferentes texturas y niveles de dureza.
Aplicaciones de la industria aeroespacial de LSR
El caucho de silicona líquida (LSR) es un material ampliamente utilizado en la industria aeroespacial debido a sus propiedades únicas, como alta estabilidad térmica, resistencia química y excelentes propiedades mecánicas. Se utiliza en diversas aplicaciones aeroespaciales, como el sellado, la unión y el encapsulado de componentes electrónicos y para la fabricación de juntas, juntas tóricas y otros detalles críticos.
Una de las principales aplicaciones de LSR en la industria aeroespacial es sellar y unir componentes de aeronaves. El material se puede moldear fácilmente en formas y tamaños complejos, lo que lo hace ideal para empaquetar y conectar tanques de combustible, componentes de motores y sistemas eléctricos. LSR brinda una excelente adhesión a varios sustratos y puede soportar condiciones ambientales adversas, como temperaturas extremas y exposición química.
LSR también se utiliza en el encapsulado de componentes electrónicos en aplicaciones aeroespaciales. La baja viscosidad del material le permite fluir fácilmente alrededor de formas complejas, brindando una excelente protección para los componentes electrónicos sensibles contra vibraciones, golpes y factores ambientales como la humedad y los cambios de temperatura.
Otra aplicación crítica de LSR en la industria aeroespacial es la fabricación de juntas, juntas tóricas y otros componentes de sellado. El LSR se puede personalizar para cumplir con requisitos específicos, como la temperatura y la resistencia a la presión, y a menudo se usa en aplicaciones de alto rendimiento donde los materiales de caucho tradicionales pueden no ser adecuados.
Además de las aplicaciones de sellado y unión, el LSR también se utiliza para fabricar componentes de iluminación de aeronaves, como lentes y difusores. Las propiedades ópticas del material lo convierten en una opción ideal para estas aplicaciones, proporcionando una excelente transmisión de luz, mientras que sus propiedades mecánicas aseguran durabilidad y resistencia a factores ambientales como la radiación ultravioleta y las fluctuaciones de temperatura.
Moldeo por inyección LSR de grado alimenticio
El caucho de silicona líquida de calidad alimentaria (LSR) es un material especializado que se utiliza en los productos de moldeo por inyección que entran en contacto con los alimentos, como utensilios de cocina, productos para bebés y envases de alimentos. Es un material de alta pureza que cumple con los estrictos estándares regulatorios para la seguridad alimentaria.
Uno de los principales beneficios de Food-Grade LSR es su resistencia a altas temperaturas, lo que lo hace ideal para usar en utensilios de cocina como espátulas, cucharas y moldes para hornear. Puede soportar temperaturas de hasta 450 °F (232 °C), lo que lo hace seguro para aplicaciones de cocción y horneado.
El LSR de grado alimentario también se utiliza para fabricar productos para bebés, como chupetes y tetinas para biberones. Estos productos deben cumplir estrictos estándares de seguridad para garantizar que sean seguros para los bebés. LSR es un material ideal para estas aplicaciones debido a su excelente biocompatibilidad, suavidad y durabilidad.
Otra aplicación importante de LSR de grado alimentario es el envasado de alimentos. El material se puede moldear en varias formas y tamaños, lo que lo hace ideal para la fabricación de recipientes de almacenamiento de alimentos, bandejas de cubitos de hielo y otros productos. LSR es resistente a los productos químicos y tiene excelentes propiedades de sellado, lo que garantiza que el contenido del paquete permanezca fresco y libre de contaminación.
El LSR de grado alimentario también se utiliza para fabricar productos médicos, como materiales de impresión dental y dispositivos protésicos. La biocompatibilidad, la durabilidad y la capacidad del material para replicar detalles finos lo convierten en una opción ideal para estas aplicaciones.
En general, el LSR de grado alimentario es un material especializado ideal para la fabricación de productos que entran en contacto con alimentos, como utensilios de cocina, productos para bebés y envases de alimentos. Su resistencia a altas temperaturas, biocompatibilidad y excelentes propiedades de sellado lo convierten en un material ideal para estas aplicaciones. El material también se utiliza para fabricar productos médicos debido a su biocompatibilidad y capacidad para replicar detalles finos.
Moldeo por inyección LSR para productos para bebés
El moldeo por inyección de LSR (caucho de silicona líquida) es un proceso de fabricación utilizado para producir una amplia gama de productos hechos de caucho de silicona. Una de las aplicaciones más populares del moldeo por inyección de LSR es la producción de productos para bebés, y esto se debe a los muchos beneficios que ofrece LSR para los productos para bebés, incluida la seguridad, la durabilidad y la facilidad de limpieza.
El moldeo por inyección de LSR consiste en inyectar un caucho de silicona líquido en un molde, que luego se cura y solidifica. Este proceso permite la creación de formas y diseños complejos y el uso de diferentes colores y texturas. El resultado es un producto terminado que es suave, flexible y resistente al calor y a los productos químicos.
Una de las principales ventajas del moldeo por inyección de LSR para productos para bebés es la seguridad. El caucho de silicona no es tóxico, es hipoalergénico y no contiene productos químicos nocivos como BPA, ftalatos y PVC. Esto lo convierte en una opción popular para los productos que entran en contacto con los bebés, como chupetes, anillos para la dentición y tetinas para biberones. El moldeo por inyección de LSR también permite la creación de productos sin bordes afilados ni costuras que puedan dañar la delicada piel de un bebé.
La durabilidad es otro beneficio del moldeo por inyección LSR. El caucho de silicona es resistente al desgaste, lo que lo hace ideal para productos de uso frecuente o que se someten a un manejo brusco, como chupetes o mordedores. La naturaleza suave y flexible del material también hace que sea menos probable que se rompa o agriete cuando se cae, lo que reduce el riesgo de lesiones para el bebé.
El moldeo por inyección de LSR también ofrece una fácil limpieza, lo cual es esencial para los productos para bebés que deben desinfectarse con frecuencia. El caucho de silicona no es poroso y puede limpiarse fácilmente con agua y jabón o colocarse en el lavavajillas para una limpieza a fondo.
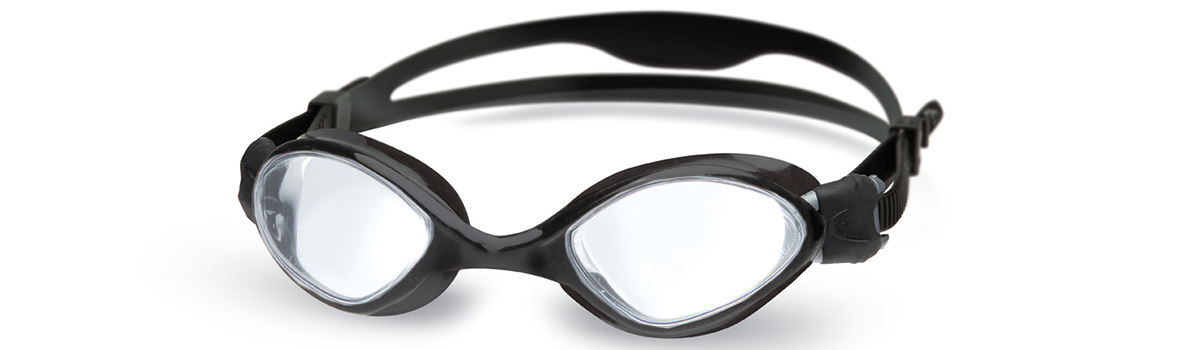
Moldeo por inyección LSR para artículos deportivos
El moldeo por inyección de LSR (caucho de silicona líquida) es un proceso de fabricación popular para varios productos, incluidos los artículos deportivos. El moldeo por inyección de LSR ofrece varios beneficios para la producción de artículos deportivos, que incluyen flexibilidad, durabilidad y resistencia a temperaturas extremas y condiciones ambientales.
Una de las principales ventajas del moldeo por inyección LSR para artículos deportivos es la flexibilidad. El caucho de silicona es un material suave y flexible que se puede moldear en varias formas y diseños. Esto permite crear artículos deportivos que son cómodos de usar y se ajustan al cuerpo, como equipos de protección o empuñaduras para equipos.
La durabilidad es otro beneficio del moldeo por inyección LSR para artículos deportivos. El caucho de silicona es resistente al desgaste, lo que lo hace ideal para productos que se usan con frecuencia o que se someten a un manejo brusco, como pelotas, paletas o raquetas. El material también puede soportar temperaturas y condiciones ambientales extremas, como la exposición a la luz solar o al agua, sin degradarse ni deteriorarse.
El moldeo por inyección LSR también permite crear productos resistentes al impacto y la abrasión. La alta resistencia al desgarro y el alargamiento a la rotura del material lo hacen ideal para producir equipos de protección como revestimientos de cascos, protectores bucales y espinilleras. Además, el moldeo por inyección de LSR permite la creación de superficies o empuñaduras antideslizantes para equipos, como mangos o empuñaduras de raquetas.
Otro beneficio del moldeo por inyección de LSR para artículos deportivos es la creación de productos que son fáciles de limpiar y mantener. El caucho de silicona no es poroso y puede limpiarse fácilmente con un paño húmedo o lavarse con agua y jabón. Esto lo convierte en un material ideal para productos de uso frecuente, como equipos de gimnasia o colchonetas de yoga.
Moldeo por inyección LSR para artículos para el hogar
El moldeo por inyección de LSR es un proceso de fabricación que utiliza caucho de silicona líquida (LSR) para crear piezas moldeadas. Este proceso es ideal para producir artículos para el hogar de alta calidad, como utensilios de cocina, productos para bebés y accesorios para el baño. El moldeo por inyección LSR ofrece varios beneficios, que incluyen alta precisión, consistencia y durabilidad, lo que lo convierte en una excelente opción para productos domésticos que requieren tolerancias estrictas y un rendimiento superior.
El proceso de moldeo por inyección de LSR consiste en inyectar un material de silicona líquida en un molde. Luego, el molde se calienta y el material de silicona líquida se cura y solidifica en la forma deseada. El proceso está altamente automatizado, lo que permite una producción uniforme de piezas con tolerancias estrictas y excelentes acabados superficiales. Este proceso también permite producir geometrías complejas que serían difíciles o imposibles de lograr con otros procesos de moldeo.
Los artículos para el hogar que se producen comúnmente con el moldeo por inyección de LSR incluyen utensilios de cocina, como espátulas y cucharas para cocinar, productos para bebés, como chupetes y tetinas para biberones, y accesorios para el baño, como cabezales de ducha y cepillos de dientes. Estos productos requieren un moldeado preciso para cumplir con los estándares de seguridad y rendimiento, y el moldeo por inyección LSR ofrece la precisión y la consistencia necesarias para producir artículos para el hogar de alta calidad que cumplan con estos estándares.
Uno de los principales beneficios del moldeo por inyección de LSR para artículos para el hogar es su durabilidad. Los materiales LSR son resistentes a altas temperaturas, radiación UV y productos químicos, lo que los hace ideales para productos de larga duración. Además, los materiales LSR son hipoalergénicos, lo que los hace seguros para su uso en productos para bebés y otros artículos para el hogar que entran en contacto con la piel.
Otro beneficio del moldeo por inyección LSR es su capacidad para producir piezas con excelentes acabados superficiales. El proceso permite crear características con un acabado liso y brillante resistente a rayones y rozaduras. Esto hace que el moldeo por inyección de LSR sea una opción perfecta para producir artículos para el hogar que requieren una apariencia atractiva, como utensilios de cocina y accesorios para el baño.
Comparación con otros tipos de molduras de caucho
El moldeo por inyección de LSR (caucho de silicona líquida) es un proceso de fabricación popular para producir varios productos de caucho y ofrece varias ventajas sobre otros tipos de procesos de moldeo de caucho. Aquí hay algunas comparaciones entre el moldeo por inyección LSR y diferentes tipos de moldeo de caucho:
- Moldeo por compresión: el moldeo por compresión es un proceso estándar para producir piezas grandes o piezas con formas complejas. En el moldeo por compresión, se coloca una cantidad previamente medida de caucho en un molde calentado y se aplica presión hasta que se cura el caucho. En comparación con el moldeo por inyección LSR, el moldeo por compresión es un proceso más lento y puede provocar variaciones en las dimensiones de las piezas debido a la distribución desigual de la presión. El moldeo por inyección LSR, por otro lado, permite un control preciso de las dimensiones de la pieza y puede producir formas complejas con tolerancias estrictas.
- Moldeo por transferencia: el moldeo por transferencia es similar al moldeo por compresión, pero implica el uso de un émbolo para transferir el caucho del recipiente de inyección al molde. El moldeo por transferencia puede producir piezas con alta precisión y es adecuado para fabricar piezas de tamaño mediano. Sin embargo, puede ser más lento y costoso que el moldeo por inyección LSR.
- Moldeo por inyección: El moldeo por inyección es un proceso que consiste en inyectar caucho fundido en un molde a alta presión. El moldeo por inyección puede producir piezas de forma rápida y precisa, pero puede no ser adecuado para fabricar piezas con diseños o detalles intrincados. En comparación con el moldeo por inyección, el moldeo por inyección LSR permite la creación de piezas con detalles precisos y diseños y patrones intrincados.
- Extrusión: La extrusión es un proceso utilizado para producir piezas con un perfil transversal continuo, como mangueras, sellos y juntas. La extrusión es un proceso rápido y rentable, pero puede que no sea adecuado para producir formas complejas o piezas con tolerancias estrechas. El moldeo por inyección de LSR, por otro lado, puede tener piezas con formas complejas y tolerancias estrictas, lo que lo hace ideal para producir productos como dispositivos médicos, componentes de automóviles y bienes de consumo.
Consideraciones de diseño para el moldeo por inyección de LSR
Se deben tener en cuenta varias consideraciones vitales al diseñar piezas para el moldeo por inyección de LSR para garantizar un proceso de fabricación exitoso. Estas consideraciones incluyen la selección de materiales, el diseño del molde, la geometría de la pieza y las operaciones posteriores al moldeado.
La selección de materiales es una consideración fundamental al diseñar piezas para el moldeo por inyección de LSR. Los materiales de caucho de silicona líquida vienen en varios durómetros, viscosidades y colores, y seleccionar el material apropiado es esencial para lograr las propiedades deseadas del producto final. La selección del material debe considerar los requisitos de la aplicación, como la resistencia a la temperatura, la resistencia química y la durabilidad.
El diseño del molde es otra consideración crítica para el moldeo por inyección de LSR. El diseño del molde debe optimizarse para producir la geometría de la pieza deseada y tener en cuenta el flujo, el enfriamiento y la eyección del material. El molde debe diseñarse con sistemas de ventilación y entrada adecuados y tener suficientes cavidades para lograr una alta tasa de producción.
La geometría de la pieza también es esencial cuando se diseñan piezas para moldeo por inyección de LSR. La geometría de la pieza debe optimizarse para lograr las propiedades mecánicas y estéticas deseadas del producto final. Esto puede implicar el uso de ángulos de desmoldeo para facilitar la expulsión del molde, el uso de nervaduras para aumentar la rigidez y la colocación de sistemas de compuertas y ventilación para optimizar el flujo de material.
Las operaciones posteriores al moldeo también deben tenerse en cuenta al diseñar piezas para el moldeo por inyección de LSR. Las operaciones posteriores al moldeado pueden incluir operaciones de recorte, desbarbado y ensamblaje secundario. Estas operaciones deben optimizarse para minimizar el desperdicio y reducir los costos de mano de obra.
Otras consideraciones de diseño para el moldeo por inyección de LSR pueden incluir el uso de muescas, la colocación de pasadores eyectores y el uso de líneas de separación. Estos factores deben tenerse en cuenta durante el proceso de diseño para garantizar que el producto final cumpla con las especificaciones deseadas y pueda fabricarse de manera eficiente.
Beneficios ambientales y de sustentabilidad del moldeo por inyección LSR
El moldeo por inyección de LSR ofrece varios beneficios ambientales y de sostenibilidad en comparación con los procesos de fabricación tradicionales, lo que lo convierte en una opción atractiva para las empresas que buscan reducir su huella ecológica.
Uno de los principales beneficios ambientales del moldeo por inyección de LSR es su baja generación de desechos. El proceso produce muy poco material de desecho, ya que el caucho de silicona líquida se inyecta directamente en el molde y se cura para darle la forma deseada. Esto contrasta con otros procesos de fabricación, como el mecanizado o la fundición, que generan un importante material de desecho.
El moldeo por inyección de LSR también tiene el potencial de reducir el consumo de energía y las emisiones de gases de efecto invernadero. El proceso se puede automatizar en gran medida, lo que reduce la necesidad de mano de obra y reduce el consumo de energía. El moldeo por inyección de LSR es un proceso a baja temperatura que requiere menos energía que otros procesos de moldeo, como el moldeo por inyección o el moldeo por soplado. Esto puede resultar en ahorros significativos de energía y reducción de emisiones de gases de efecto invernadero.
Otro beneficio de sostenibilidad del moldeo por inyección de LSR es la posibilidad de utilizar materiales reciclados. Los materiales LSR se pueden reciclar y reutilizar, lo que reduce la necesidad de nuevos materiales y reduce la generación de desechos. Además, la larga vida útil de los productos LSR significa que pueden reutilizarse o readaptarse, lo que reduce aún más los desechos y extiende el ciclo de vida del producto.
El moldeo por inyección de LSR también puede reducir el uso de productos químicos nocivos en la fabricación. Los materiales LSR generalmente están libres de químicos tóxicos como ftalatos, BPA y PVC, lo que los hace más seguros para los trabajadores y los consumidores. Además, el proceso de baja temperatura utilizado en el moldeo por inyección de LSR no requiere solventes nocivos ni otros productos químicos.
Futuro del moldeo por inyección LSR
El futuro del moldeo por inyección de LSR es brillante, y el proceso ofrece varias ventajas sobre los métodos de fabricación tradicionales. El moldeo por inyección de LSR será aún más eficiente, rentable y respetuoso con el medio ambiente a medida que avance la tecnología.
Una de las áreas más prometedoras para el futuro del moldeo por inyección de LSR es el uso de técnicas de fabricación aditiva. La fabricación aditiva, también conocida como impresión 3D, permite la creación de geometrías complejas y piezas personalizadas que serían difíciles o imposibles de producir con los métodos de fabricación tradicionales. A medida que la tecnología mejore, el moldeo por inyección de LSR se integrará más con la fabricación aditiva, lo que permitirá producir productos aún más avanzados e innovadores.
Otra área de desarrollo futuro para el moldeo por inyección de LSR es el uso de materiales avanzados. A medida que se desarrollan nuevos materiales, el moldeo por inyección de LSR puede aprovechar sus propiedades únicas, como una mayor durabilidad, resistencia a la temperatura o biocompatibilidad. Esto permitirá productos aún más especializados, como implantes médicos o componentes industriales de alto rendimiento.
También es probable que la integración continua de la automatización y la robótica en los procesos de moldeo por inyección de LSR sea una tendencia importante en el futuro. La automatización puede mejorar la eficiencia, reducir los costos de mano de obra y mejorar la consistencia y la calidad del producto final. A medida que la tecnología mejore, el moldeo por inyección de LSR se automatizará aún más, y la robótica y la inteligencia artificial desempeñarán un papel más importante en la fabricación.
Finalmente, la sustentabilidad y la responsabilidad ambiental probablemente seguirán siendo impulsores importantes en el futuro del moldeo por inyección de LSR. A medida que los consumidores y las empresas se centren cada vez más en reducir los desechos y minimizar su impacto ecológico, el moldeo por inyección de LSR se convertirá en una opción aún más atractiva para producir productos de alta calidad con una huella ambiental baja. Es probable que el desarrollo de materiales más sostenibles, el reciclaje y la reutilización de materiales y el uso de fuentes de energía renovables desempeñen un papel más importante en el futuro del moldeo por inyección de LSR.
Conclusión:
En conclusión, el moldeo por inyección de LSR es un proceso de fabricación confiable y eficiente con numerosos beneficios para diversas industrias. LSR es un material versátil con características de rendimiento distintivas, lo que lo hace ideal para múltiples aplicaciones. Con los continuos avances en la tecnología LSR y la mayor demanda de prácticas de fabricación sostenibles, el futuro del moldeo por inyección de LSR es brillante.