Soluciones a los defectos de moldeo comunes del moldeo por inyección
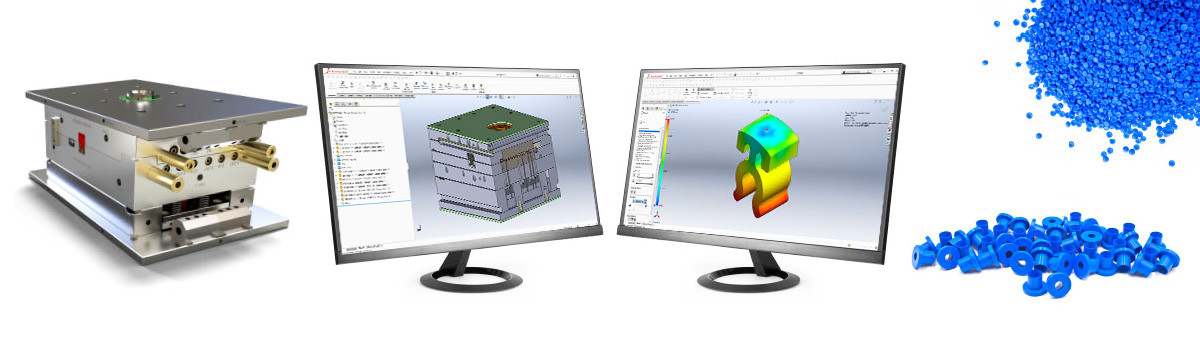
Los defectos son comunes cuando se usan moldes para procesar piezas de moldeo por inyección de plástico, y esto afecta en gran medida la eficiencia del procesamiento. Los siguientes son defectos de moldeo comunes y soluciones para piezas de moldeo por inyección de plástico.
Tiros cortos
Los tiros cortos se refieren a que los productos fabricados están incompletos debido a que los moldes no están completamente llenos.
Este defecto generalmente aparece en el punto más alejado de la entrada o en las partes a las que solo se puede acceder a través de las áreas estrechas del molde porque las áreas estrechas pueden afectar el flujo de la masa fundida.
El tiro corto puede causar micromarcas de flujo o dar como resultado que una gran parte del producto falte obviamente.
Causa:
Las causas de tiros cortos incluyen:
La materia prima inyectada en el molde no es suficiente.
La resistencia de los fundidos es grande, lo que hace que el molde no se pueda llenar por completo.
La ventilación del moho es deficiente y provoca la generación de cavitación que bloquea la masa fundida, lo que hace que la masa fundida no pueda fluir hacia algunas áreas del moho.
Las rebabas
Las rebabas se generan a partir de la adhesión del exceso de materia prima extruida de la cavidad del molde al producto.
Este defecto estará en los bordes del producto o en cada parte compuesta del molde. La materia prima puede desbordarse del molde o de los sitios de unión de los moldes móviles y de fijación.
También se pueden encontrar rebabas en el núcleo del molde, que se deben a la presión hidráulica o al pasador angular.
La gravedad de las rebabas varía, a veces finas, a veces más gruesas.
Causa:
Las causas de las rebabas incluyen:
La superficie del molde de sujeción está dañada o muy desgastada.
El molde móvil y el molde de fijación se dislocan cuando están bloqueados.
La presión de la materia prima en el molde es mayor que la fuerza de sujeción del molde.
La tercera condición mencionada anteriormente sería el resultado de varias razones. En las siguientes situaciones, la presión de la materia prima es mayor que la fuerza de sujeción del molde.
En la primera etapa del molde de inyección (etapa de llenado del molde), se llena demasiada materia prima, lo que aumenta la presión dentro del molde.
Durante el proceso de llenado del molde, la gran resistencia del flujo de fusión también aumentará la presión dentro del molde.
La presión de la cavidad del molde es demasiado alta durante la etapa de mantenimiento de la presión.
La fuerza de sujeción del molde no es suficiente.
degradación
La descomposición podría conducir a muchos resultados. El alcance y la gravedad del problema también varían. En el caso más grave, puede provocar una decoloración completa del producto y malas propiedades mecánicas. La degradación local solo causará rayas o manchas oscuras.
Causa:
La degradación es causada por el daño de la materia prima. Las moléculas de cadena larga que forman los plásticos se descompondrán bajo la acción de un calor excesivo o un esfuerzo cortante excesivo. Durante la descomposición de las moléculas, el gas volátil acelerará el proceso de degradación, lo que provocará la decoloración de la materia prima. La descomposición de una gran cantidad de moléculas finalmente romperá el contenido de la materia prima y causará una influencia negativa en las propiedades mecánicas.
La degradación local puede ser el resultado de la temperatura desigual del barril de material.
La degradación puede ocurrir en las siguientes situaciones:
La materia prima se sobrecalienta en el barril de material o en el sistema de canales calientes.
La materia prima permanece demasiado tiempo en el barril.
Durante el proceso de moldeo por inyección, el esfuerzo cortante ejercido sobre la materia prima es demasiado grande. Si las boquillas están bloqueadas, o las compuertas y el corredor son demasiado angostos, aumentará el esfuerzo cortante.
Deformación
En situaciones normales, las formas de los productos deben estar en línea con las de los moldes. La deformación se refiere a la deformidad de los productos.
Cuando la condición empeora, los productos se deformarán por completo cuando se expulsen del molde. Cuando la condición no es grave, la forma del producto presentará pequeñas irregularidades.
Largas pero sin aristas de apoyo ni grandes planos son las zonas más propensas a deformarse.
Causa:
Causas de la deformación:
La temperatura es demasiado alta cuando se libera el molde.
Como el tiempo de enfriamiento es diferente en áreas gruesas y delgadas, o la diferencia de temperatura del molde al mover el molde y fijar el molde, la contracción dentro de los productos es diferente.
El flujo del molde no es uniforme durante el llenado (la llamada "orientación de congelación") o la presión dentro de la cavidad del molde es demasiado alta en la etapa de retención de presión.
Impurezas
Las impurezas suelen aparecer en forma de manchas de diferentes colores, parches o rayas. El más común es el punto negro.
Las impurezas pueden ser solo puntos diminutos, pero también pueden ser rayas evidentes o una gran parte de la decoloración cuando es grave.
Causa:
Las impurezas son causadas por los diversos mezclados con materias primas, tales como:
La materia prima mezclada con artículos diversos cuando se transporta a los barriles.
La descomposición de la materia prima puede caer de cualquier mecanismo de corte y mezclarse con la materia prima, como pernos de máquinas, paredes internas del tambor de secado, juntas/boquillas.
Laminación
La laminación generará el "efecto piel" en la superficie de los productos, que es causado por la diferencia en las propiedades y texturas de la superficie de los productos y otras materias primas, y forma una piel que se pela y se puede quitar.
Cuando la laminación es seria, toda el área de la sección transversal se compone de diferentes capas y no se ha fundido. Cuando los defectos son menos obvios, la apariencia de los productos puede cumplir con los requisitos, pero romperá las propiedades mecánicas de los productos.
Causa:
Hay dos causas principales para la laminación. El primero es cuando dos tipos diferentes de materias primas se mezclan incorrectamente. Las dos materias primas se transportarán al barril al mismo tiempo bajo presión. Sin embargo, cuando el molde no se puede derretir cuando se enfría, al igual que las diferentes capas se presionan a la fuerza para formar productos.
Segundo: si se obliga a la masa fundida fría a pasar a través de la puerta estrecha, se generará un esfuerzo cortante. Una tensión de cizallamiento demasiado alta hará que la capa fundida fundida de antemano no se pueda fusionar por completo.
Riesgo de mezcla:
Una cosa que debe tener en cuenta es que algunas materias primas mezcladas darán como resultado una fuerte reacción química, como el PVC y el Avetal, no se deben mezclar.
plata lineal
Sliver linear podría ser solo un fenómeno local, pero podría expandirse a toda la superficie cuando es grave.
Silver linear afectará la apariencia de los productos y también dañará las propiedades mecánicas de los productos.
Causa:
Los siguientes dos puntos causan el lineal plateado:
La materia prima está húmeda y algunos de ellos absorberán el vapor en el aire. Si la materia prima está demasiado húmeda, el vapor presurizado podría generarse bajo la alta temperatura y alta presión del barril. Estos vapores atraviesan la superficie del producto y forman franjas plateadas.
El fundido se dañó térmicamente y genera degradación local. El gas volátil generado se bloqueará en la superficie del molde y generará rayas en la superficie de los productos.
Esto no es tan peor como la degradación. Siempre que la temperatura de la masa fundida sea alta o esté sujeta a un esfuerzo cortante durante la plastificación o la inyección en el molde, esto podría suceder.
Brillo/sombra
El acabado superficial de los productos debe ser el mismo que el de los moldes. Cuando el acabado de la superficie de dos es diferente, se produjeron defectos de brillo/sombra.
La superficie será sombría cuando ocurran defectos, y la superficie rugosa será lisa y brillante.
Causa:
Las causas del brillo/sombra incluyen:
El fundido fluye de manera irregular o la temperatura de la superficie del molde es baja, lo que hace que el acabado de la superficie del molde no se pueda duplicar cuando se moldea el material.
Durante el mantenimiento de la presión, la presión en la cavidad no es lo suficientemente alta como para que el material se adhiera a la superficie del molde en el proceso de enfriamiento, dejando marcas de contracción.
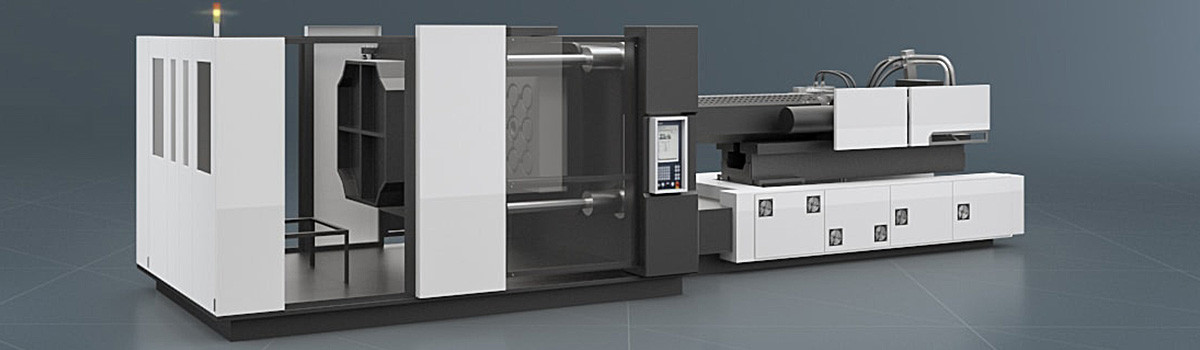
Marcas de flujo
Las marcas de flujo se pueden encontrar en la superficie de los productos en múltiples formas. Generalmente, formará un área de sombra.
Las marcas de flujo no producen ningún relieve o depresión en la superficie de los productos que no se pueda sentir con los dedos. Este defecto también se denomina marcas de arrastre, imágenes fantasma y sombras.
Cuando las marcas de flujo son obvias, generará ranuras y dejará defectos como marcas en la superficie de los productos.
Causa:
Las marcas de flujo se pueden encontrar cuando:
La fluidez del fundido es pobre o la temperatura de la superficie del molde es baja, lo que resulta en una gran resistencia al flujo del plástico en el proceso de llenado del molde.
En el llenado del molde, la masa fundida fluye con resistencia, que puede ser causada por la superficie irregular de la matriz, las marcas o patrones impresos en la superficie de la matriz, o el cambio de dirección del flujo de masa fundida durante el proceso de llenado.
línea de unión
La línea de unión se genera cuando dos frentes de fusión se encuentran durante el llenado del molde y aparecerá en la superficie del producto como una línea.
La línea de unión es como la línea de grietas en la superficie de los productos, que no es evidente de detectar.
Al diseñar moldes, algunas líneas de unión visibles son inevitables. En este caso, acorte lo más posible la línea de unión para evitar que se deteriore la resistencia y el aspecto de los productos.
Causa:
Hay muchas razones para la generación del frente de fusión. La razón más probable podría ser el flujo de fusión a lo largo de los bordes del núcleo del molde. Cuando los dos fundidos se encuentran, se producen las líneas de unión. La temperatura del frente de dos fundidos debe ser lo suficientemente alta para permitir que se fusionen con éxito y no afecte la resistencia y la apariencia de los productos.
Cuando los dos fundidos no pueden fusionarse completamente, se producirán los defectos.
Causas de los defectos:
El molde tiene partes más gruesas y más delgadas, y la velocidad de flujo de la masa fundida es diferente, cuando la masa fundida fluye a través de la parte delgada del molde, la temperatura es baja.
La longitud de cada corredor es diferente. Los corredores solitarios serán fáciles de refrescar.
La presión de la cavidad del molde no es suficiente para permitir que la masa fundida se funda completamente durante la etapa de mantenimiento de la presión.
Las burbujas restantes hacen que el frente de fusión no pueda fusionarse, lo que también provocará la quema.
Quemazón
El ardor es similar al de tiro corto, pero con bordes irregulares de desvanecimiento y ligero olor a quemado. Las áreas de negro de carbón aparecerán en el producto, cuando la condición sea grave, acompañadas por el olor a plástico quemado.
Si no se eliminan los defectos, a menudo hay una deposición negra en el molde. Si las sustancias de gas o petróleo producidas por la quema no se controlan inmediatamente, pueden bloquear los orificios de ventilación. La quema generalmente se encuentra al final de las vías.
Causa:
La quema es causada por el efecto de combustión interna. Cuando la presión en el aire aumenta bruscamente en muy poco tiempo, la temperatura aumentará y provocará quemaduras. Según los datos recopilados, el efecto de combustión interna en el proceso de moldeo por inyección puede producir altas temperaturas de hasta 600 grados.
Se pueden producir quemaduras cuando:
La velocidad de llenado del molde es rápida, por lo que el aire no se puede vaciar de la cavidad del molde y genera burbujas de aire debido al bloqueo del plástico entrante, y provoca un efecto de combustión interna después de comprimirse.
Los agujeros de aire están bloqueados o la ventilación no es uniforme.
El aire en el molde debe vaciarse de los orificios de ventilación. Si la ventilación se ve afectada por la posición, el número, el tamaño o las funciones, el aire permanecerá en el molde y se quemará. Una gran fuerza de sujeción del molde también provocará una mala ventilación.
Contracción
La contracción se refiere a los ligeros huecos en la superficie de los productos.
Cuando los defectos son leves, la superficie de los productos es irregular. Cuando es grave, la gran área de productos colapsará. Los productos con arcos, asas y salientes a menudo sufren defectos de contracción.
Causa:
La contracción es causada por la contracción de gran área de las materias primas durante el enfriamiento.
En el área gruesa de los productos (como el arco), la temperatura central del material es baja, por lo que la contracción ocurrirá más tarde que la de la superficie, lo que producirá una fuerza de contracción dentro de la materia prima y empujará el lado exterior hacia la depresión interna. para producir el encogimiento.
Las contracciones ocurren en las siguientes situaciones:
La presión en la cavidad del molde es menor que la fuerza generada por la contracción de la materia prima en el proceso de enfriamiento.
Tiempo de presurización insuficiente de la cavidad del molde durante el proceso de enfriamiento, lo que provoca que la materia prima fluya fuera de la cavidad desde la compuerta.
La materia prima no tiene suficiente capacidad amortiguadora durante la etapa de moldeo y mantenimiento de la presión, ya que el tornillo se extrae por completo antes de que se inyecte el exceso de materia prima.
Las áreas de la sección transversal de las puertas y canales son mucho más pequeñas que el grosor de los productos, lo que significa que las puertas ya están congeladas antes del proceso de extrusión de los productos.
Burbujas
Las burbujas de vacío se presentan en forma de burbujas de aire, que se pueden encontrar fácilmente en los productos transparentes. También se puede ver en la sección transversal de productos opacos.
Causa:
Las burbujas de aire son la parte de vacío de los productos, que se producen cuando la materia prima se contrae durante el proceso de enfriamiento.
Similar a la contracción, el interior de la materia prima produce la fuerza contráctil. La diferencia es que la apariencia exterior de los productos se ha solidificado cuando se forman las burbujas y no hay colapso, por lo que se generan burbujas huecas.
Las causas de las burbujas son las mismas que las de la reducción, incluyendo:
Presión ineficiente de la cavidad del molde
Tiempo de presurización de la cavidad insuficiente
El tamaño del corredor y la puerta son demasiado pequeños.
Marcas de pulverización
Las marcas de pulverización se refieren al área roscada frente a la puerta. Las marcas de rociado no solo afectan la apariencia de los productos, sino que también afectan la resistencia de los productos.
Causa:
Las marcas de rociado son causadas por el flujo de masa fundida fuera de control durante el proceso de llenado del molde.
El plástico fundido entra en el molde bajo la enorme presión. Si la velocidad de llenado del molde es demasiado alta, el plástico se expulsará del espacio abierto de la cavidad del molde y retrocederá rápidamente y se enfriará. En ese momento, se forman los hilos, lo que bloquea el plástico fundido que ingresa a las compuertas.
La causa principal de las marcas de rociado es la posición incorrecta de las puertas o el diseño de las mismas. Las dos situaciones siguientes agravarán la situación de defectos:
Alta velocidad de llenado de moldes
Mal flujo de fusión durante el llenado del molde